10 推式与拉式生产系统
推式和拉式的定义

推式和拉式的定义|工厂物理学来源|让工厂管理变简单全文总计1012字,需阅读3分钟,以下为正文:注:做生产计划的人,经常会说“推”、“拉”,但如何定义“推”、“拉”且没有明确的,今天分享一下《工厂物理学》的标准定义。
实际中对 jit 的描述都采用了推式(push)与拉式(pull)生产系统这两个术语。
然而,推和拉的定义常常不是很精确,并因此在美国产生了一些对于 jit 的困惑。
定义:推式系统根据外部需求规划产品发布,拉式系统根据自身状态授权产品发布。
另一种有益于考察推与拉区别的方式是,推式系统由其内在属性而决定了是接单生产make-to-order),而拉式系统则为备货生产(make-to-stock)。
也就是说,推动推式系统计划的是订单(或预测)而不是系统状态。
拉式系统将系统中某处的库存短缺作为批准供应的信号。
从这个角度看,基准库存点模型(base stock model)当库存降低到某一特定水平之下即触发订单,是拉的方法;mrp 根据客户订单建立规划然后根据规划投放订单,是推的方法。
当然,大多数现实世界的系统都包括推和拉。
例如,如果一件任务由 mrp排配投放,但是因为考虑到产线的拥堵又保持了这个任务,那么这种效果就是一个混合式推-拉系统。
(340|341)相反地,如果一个看板系统生成批准生产的卡片,但实际的任务触发却因为对部件的预计需求不足(即,没有在主生产计划中体现)而推迟,那么,这也是一个混合式系统(如,见 wight 1970,deelersnyder 等 1988,suri 1998)。
要不要用,怎么用只是蓝图的一部分,用在哪里也很重要。
即使在单一生产系统中,部分拉动式操作也是可能的。
推-拉界面(push-pull interface)是确定何处放置拉式过程时的一个有用概念,它将生产流程分成推段与拉段2。
成功地选择这个接口的位置将使系统能够利用拉的优势来获得战略优势,同时保持推系统的客户驱动特性。
生产模式简介
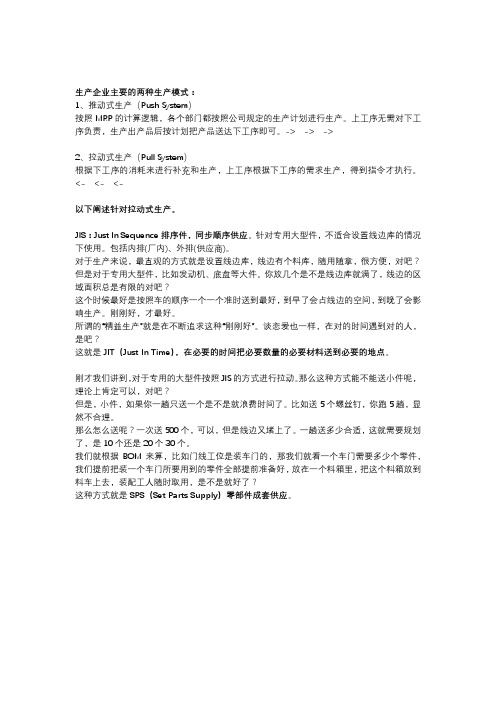
生产企业主要的两种生产模式:1、推动式生产(Push System)按照MRP的计算逻辑,各个部门都按照公司规定的生产计划进行生产。
上工序无需对下工序负责,生产出产品后按计划把产品送达下工序即可。
-> -> ->2、拉动式生产(Pull System)根据下工序的消耗来进行补充和生产,上工序根据下工序的需求生产,得到指令才执行。
<- <- <-以下阐述针对拉动式生产。
JIS:Just In Sequence排序件,同步顺序供应。
针对专用大型件,不适合设置线边库的情况下使用。
包括内排(厂内)、外排(供应商)。
对于生产来说,最直观的方式就是设置线边库,线边有个料库,随用随拿,很方便,对吧?但是对于专用大型件,比如发动机、底盘等大件。
你放几个是不是线边库就满了,线边的区域面积总是有限的对吧?这个时候最好是按照车的顺序一个一个准时送到最好,到早了会占线边的空间,到晚了会影响生产。
刚刚好,才最好。
所谓的“精益生产”就是在不断追求这种“刚刚好”。
谈恋爱也一样,在对的时间遇到对的人,是吧?这就是JIT(Just In Time),在必要的时间把必要数量的必要材料送到必要的地点。
刚才我们讲到,对于专用的大型件按照JIS的方式进行拉动。
那么这种方式能不能送小件呢,理论上肯定可以,对吧?但是,小件,如果你一趟只送一个是不是就浪费时间了。
比如送5个螺丝钉,你跑5趟,显然不合理。
那么怎么送呢?一次送500个,可以,但是线边又堵上了。
一趟送多少合适,这就需要规划了,是10个还是20个30个。
我们就根据BOM来算,比如门线工位是装车门的,那我们就看一个车门需要多少个零件,我们提前把装一个车门所要用到的零件全部提前准备好,放在一个料箱里,把这个料箱放到料车上去,装配工人随时取用,是不是就好了?这种方式就是SPS(Set Parts Supply)零部件成套供应。
根据线体的设计,左侧怎么做?右侧怎么做?比如在门线左侧,可以根据前后车的关系,在一辆料车上同时放前车的左后门和后车的左前门。
拉动式与推进式生产模式资料讲解
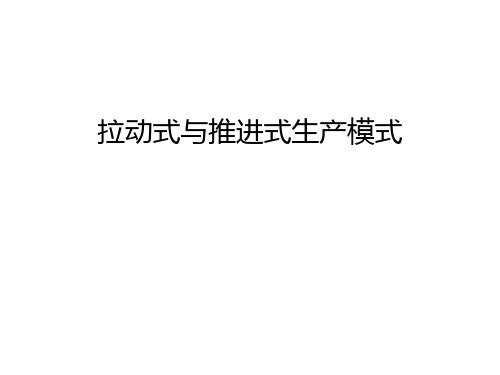
2、拉动式模式
拉动式模式是以日本制造业提出的JIT技术为核心的生产物流管 理模式。
基本思想:强调物流同步管理:
第一,在必要的时间将必要数量的物料送到必要的地点,整个 企业按同一节拍根据后道工序的需要进行生产。
第二,必要的生产工具、工位器具要按位置摆放挂牌明示,以 保持现场无杂物。
在管理手段上,把计算机管理与看板管理相结合
在生产物流方式上,以零件为中心,要求前一道工 序加工完的零件步。
在生产物流计划编制和控制上,以零件为中心,计 算机编制物料生产计划,并运用看板系统执行和控 制,以实施为中心,工作的重点在制造现场。
在对待库存的态度上,认为库存掩盖了生产系统中 的各种缺陷,所以将生产中的一切库存都视为浪费, 要消灭一切浪费。
总结
推动式强调的是市场供应量 拉动式强调的是市场需求量 两者适用于不同的企业类型
此课件下载可自行编辑修改,仅供参考! 感谢您的支持,我们努力做得更好!谢谢
第三,从最终市场需求出发,每道工序、每个车间都按照当时 的需要,根据看板向前道工序、上游车间下达生产指令,前道工 序、上游车间只能生产后道工序、下游车间所需要数量的物品。
看板(Kanban),是一个从日本引进的外来语,意 思是卡片或者某种形式的可见记录。
拉动式模式物流管理的特色
在管理标准化和制度方面重点采用标准化作业
精益生产之看板管理

二、特殊形式看板
名称 彩色乒乓球 容器 方格标识
信号灯
电子看板
说明
应用彩色乒乓球作为信息传递手段
容器本身也可以作为发出信号的工具
在地面或作业台面上画出标识方格明确存放什么零 部件 在墙上设置若干信号灯,某灯开启后即表示需要提 供某种物料 把信息系统引入传统的看板系统
规则二:前工序仅按被后工序领取的物品和数量进行生产 生产数量不能超过看板规定的数量,没有看板不进行生产。 当前工序生产多种零部件时,必须按各看板送达的顺序进 行生产。
规则三:不合格品绝对不能送到后工序
规则四:必须把看板数量减少到最小程度
规则五:通过看板对生产进行的微调
四、看板数量计算
看板数量就是在生产现场实施拉动生产所必须的看板数量。 1、理论基础——订货点理论
1、指示的功能
只按照看板指示的数量进行生产与搬运,这是看板的最基本功能。
2、目视管理的功能 起到物料标识的作用。 自动控制生产过量、搬运过量的作用。 按必要的物品、必要的时间、必要的量进行生产。
3、现场改善的功能
通过看板管理者容易发现异常,并及时采取措施来减少事故发生 及对异常问题的改善。
3.3 工序内看板和工序间领取看板
二、信号看板的使用方法
以冲压工序为例,介绍信号看板的运行方法。
三、信号看板位置计算
三角看板的位置计算和工序内看板数量计算相同:
N DL(1)
C
上图,三角看板位置为?。 材料领取看板的位置计算和工序间领取看板数量的计算相同:
N D (L T TS ) C
上图,材料领取看板位置为?。
3.5 外协领取看板
3.7 看板使用问题
关于拉动式生产体系的描述
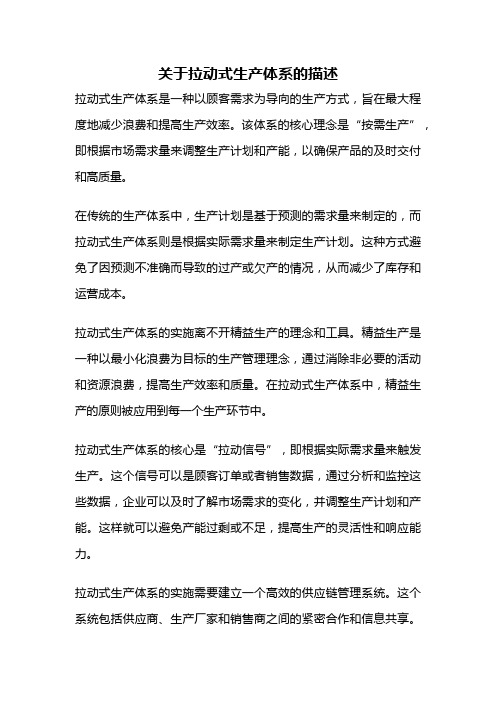
关于拉动式生产体系的描述拉动式生产体系是一种以顾客需求为导向的生产方式,旨在最大程度地减少浪费和提高生产效率。
该体系的核心理念是“按需生产”,即根据市场需求量来调整生产计划和产能,以确保产品的及时交付和高质量。
在传统的生产体系中,生产计划是基于预测的需求量来制定的,而拉动式生产体系则是根据实际需求量来制定生产计划。
这种方式避免了因预测不准确而导致的过产或欠产的情况,从而减少了库存和运营成本。
拉动式生产体系的实施离不开精益生产的理念和工具。
精益生产是一种以最小化浪费为目标的生产管理理念,通过消除非必要的活动和资源浪费,提高生产效率和质量。
在拉动式生产体系中,精益生产的原则被应用到每一个生产环节中。
拉动式生产体系的核心是“拉动信号”,即根据实际需求量来触发生产。
这个信号可以是顾客订单或者销售数据,通过分析和监控这些数据,企业可以及时了解市场需求的变化,并调整生产计划和产能。
这样就可以避免产能过剩或不足,提高生产的灵活性和响应能力。
拉动式生产体系的实施需要建立一个高效的供应链管理系统。
这个系统包括供应商、生产厂家和销售商之间的紧密合作和信息共享。
通过共享销售数据和生产计划,供应链各环节可以更好地协调和调整自己的生产和库存,以满足市场需求。
为了实现拉动式生产体系,企业需要进行一系列的改进和优化。
首先,要优化生产流程,消除不必要的环节和活动,以提高生产效率和质量。
其次,要建立一个高效的物料管理系统,确保原材料和零部件的及时供应,避免缺货和库存积压。
同时,企业还需要培养一支高素质的员工队伍,提高员工的技能和能力,以适应拉动式生产的需求。
拉动式生产体系的好处是显而易见的。
首先,它可以减少生产过程中的浪费,包括时间、人力和物料的浪费。
其次,它可以提高生产的灵活性和响应能力,使企业能够更快地适应市场需求的变化。
最后,它可以提高产品的交付速度和质量,增强客户的满意度和忠诚度。
拉动式生产体系是一种以顾客需求为导向的生产方式,通过按需生产和精益生产的理念和工具,最大程度地减少浪费和提高生产效率。
推-拉式生产的基本概念

最近,拉式生产是工业界最时髦的话题,无论是精益生产还是敏捷供应链都以拉式生产快速反应为核心。
我们大多企业都准备转向按单生产,随需而动。
难道按单计划生产就是拉式生产了吗?本文就是想探讨推拉的本质,来阐述拉式生产的基本规律。
一,推-拉的基本概念这里有两个概念必须澄清,不能混淆:第一个是MRP和看板比较,MRP是推,看板是拉,这主要是指执行层。
MRP是按生产订单执行。
看板是前工序是按后工序的指令或消耗执行。
第二个是计划的推拉概念,计划可以是推也可以是拉,也可以推拉结合,如ATO模式就是前推后拉模式:如按单装配(拉,MTO),一些关键装配件用MPS(推,MTS)。
我这里重点讨论的推-拉是指执行层的。
推拉的关键区别主要体现在执行层,而不是计划层。
计划强调远瞻性和透明性。
根据市场竞争性可以按实际需求计划,也可以按预测需求计划。
那么什么是推式系统呢?它是依赖批量计划来执行,成批送到下游工序或仓库排队。
集中控制,不考虑下一个工序的实际节拍,独立的工序控制,关注资源能力。
没有形成连续流。
那么什么是拉式系统呢?它是实时响应实际需求或消耗来执行,一种由下游向上游提出实际生产需求的生产控制方法。
分散控制,灵活和容易的适应性,关注物料的流动。
二,MRP和看板的本质区别(1),为什么MRP是推式系统?这里不是指的计划而是指的是执行过程,它是利用客户的订单发货和预测来决定将要供应和生产的需求。
生产车间用生产订单和工序段排程来沟通。
在车间没有真正优先级的方法来执行。
(2),为什么看板是连续拉式系统?看板是一个卡或传票,是一套执行规则的系统,可视化的连续拉动,通过消耗点移动物料,是精益生产理想的拉式方法用于车间执行的工具。
MRP计算需求运行要求采购和生产。
精益用MRP的毛需求严格地作为看板需求的计算的投入。
只有出现需要生产的信号,精益实际才生产。
举个例子:假设MRP算出今天需要500个,在MRP系统里,产生一个生产订单500个。
什么是拉动式生产系统

什么是拉动式生产系统
从市场需求动身,由市场需求资讯打算产品组装,再由产品组装拉动零部件加工。
每道工序、每个车间都根据当时的需要向前一道工序、上游车间提出需求,发出工作指令,前道工序、上游车间完全按这些指令进行生产。
物流和资讯流是结合在一起的。
整个过程相当于从后(后道工序)向前(前道工序)拉动,故这种方式被称为拉动式生产方式。
「销售一个,制造一个」是拉动式生产方式的形象说法。
在生产线上,就意味着后道工序每消耗一个零部件,就向前道工序发出制造指令。
精益生产方式采纳的就是拉动式生产系统。
生产方案部门制订主生产方案,其他车间及工序依据主生产方案,按下一道工序、下游车间的需求来制订生产方案。
采纳拉动式生产系统可以真正实现按需生产。
假如每道工序都按下一道工序的要求,在适当的时间按需要的品种与数量生产,就不会发生不需要的零部件被生产出来的状况。
生产企业的管理过程很简单。
不同行业、规模的企业在其管理上都有区分。
即使在同一企业生产同一产品,由于管理者不同,生产的方式、管理方法和制度也有差异。
生产管理制度的基本架构同生产方案的功能有亲密关联,由于生产方案的功能能够大致打算生产管理制度的基本架构。
所以不同的企业应当结合本企业的管理制度,选择切合自身的生产方案掌握系统。
1。
精益生产术语
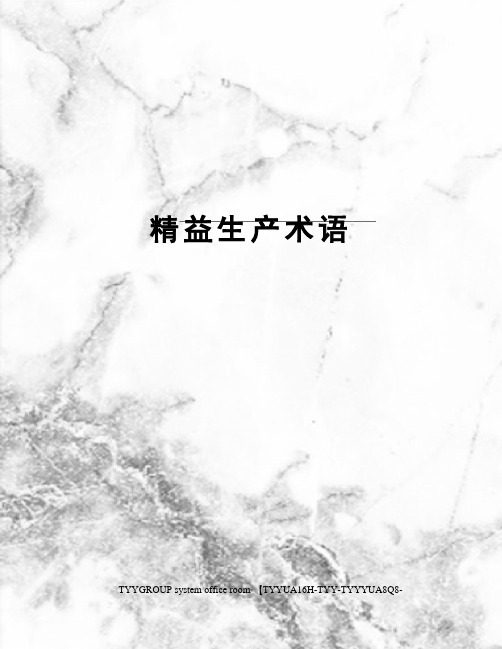
精益生产术语TYYGROUP system office room 【TYYUA16H-TYY-TYYYUA8Q8-精益生产术语为了便于大家进一步学习精益生产,并作为实践的指南,特选用与精益生产有关的术语66条,并加以解释.1.精益生产(Lean Production)含义:精益生产起源于日本的丰田生产方式,美国学者对这种生产方式的理论上加以概括与总结,命名为“Lean Production”,中文翻译为“精益生产”。
“ Lean”的意思是没有脂肪。
这种生产哲学将库存比喻为人体的脂肪,认为动作良好的企业应该是没有库存的,因此命名为“Lean Production”。
2.附加价值(Value Added)含义:附加价值是企业本身创造出的价值。
附加价值愈高则获得能力愈强。
附加价值=销售额-(材料费+委外加工费+折旧费+工资)。
附加价值率的计算方式为:(附加价值/营业收入)*100%。
比率越高则贡献越大,显示获利能力愈强,精益企业应达到30%以上。
3.7种浪费(Seven Wastes)含义:精益生产方式将所有浪费归纳成七种——(1)等待的浪费;(2)搬运的浪费;(3)不良品的浪费;(4)动作的浪费;(5)加工的浪费;(6)库存的浪费;(7)制造过多(早)的浪费。
4.价值流图(Value Stream Mapping)含义:所谓价值流,是指一个产品/服务在流程中所必须要经过的一组特定活动(包括增值活动和非增值活动).识别价值流,是在这组特定活动中识别浪费和寻找改善机会.识别价值流的常用工具,就是价值流图.价值流图把产品或者服务所涉及的所有物流与信息流相关内容用目视图表的方法绘制出来,作为随后即将展开的精益改造的依据.5.丰田生产方式(Toyota Production System)含义:一般认为,丰田生产方式的支柱有两个,一是"自动化",二是“及时生产”。
根据大野耐一的描述,丰田生产方式的现场管理,有两个特点,一是流水化制造,二是拉动式计划方法,也就是看板方式。
推式和拉式的区别
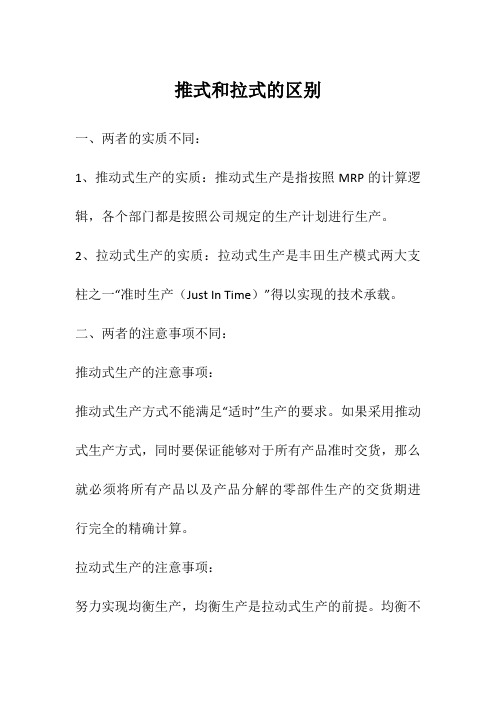
推式和拉式的区别
一、两者的实质不同:
1、推动式生产的实质:推动式生产是指按照MRP的计算逻辑,各个部门都是按照公司规定的生产计划进行生产。
2、拉动式生产的实质:拉动式生产是丰田生产模式两大支柱之一“准时生产(Just In Time)”得以实现的技术承载。
二、两者的注意事项不同:
推动式生产的注意事项:
推动式生产方式不能满足“适时”生产的要求。
如果采用推动式生产方式,同时要保证能够对于所有产品准时交货,那么就必须将所有产品以及产品分解的零部件生产的交货期进行完全的精确计算。
拉动式生产的注意事项:
努力实现均衡生产,均衡生产是拉动式生产的前提。
均衡不
仅是数量,而且包括品种、工时、设备负荷的全部均衡。
设备、工装始终处于良好状态,材料、毛坯供应准时,工人技术平和出勤率良好、稳定等都是重要条件。
三、两者的性质不同:
1、推动式生产的性质:推进式生产中,每一工序都根据生产计划,尽其所能地生产,尽快完成生产任务,不管下一工序当时是否需要。
传统的生产系统一般为推进式生产,推进式生产将造成物品的堆积。
2、拉动式生产的性质:相对于过去的推动式生产,前一作业将零件生产出来“推给”后一作业加工,在拉式生产中,是后一作业根据需要加工多少产品,要求前一作业制造正好需要的零件。
推式生产和拉式生产的本质区别
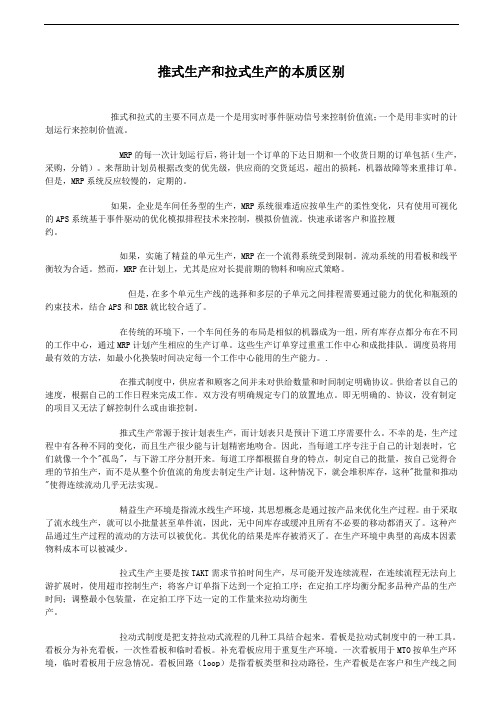
推式生产和拉式生产的本质区别推式和拉式的主要不同点是一个是用实时事件驱动信号来控制价值流;一个是用非实时的计划运行来控制价值流。
MRP的每一次计划运行后,将计划一个订单的下达日期和一个收货日期的订单包括(生产,采购,分销)。
来帮助计划员根据改变的优先级,供应商的交货延迟,超出的损耗,机器故障等来重排订单。
但是,MRP系统反应较慢的,定期的。
如果,企业是车间任务型的生产,MRP系统很难适应按单生产的柔性变化,只有使用可视化的APS系统基于事件驱动的优化模拟排程技术来控制,模拟价值流。
快速承诺客户和监控履约。
如果,实施了精益的单元生产,MRP在一个流得系统受到限制。
流动系统的用看板和线平衡较为合适。
然而,MRP在计划上,尤其是应对长提前期的物料和响应式策略。
但是,在多个单元生产线的选择和多层的子单元之间排程需要通过能力的优化和瓶颈的约束技术,结合APS和DBR就比较合适了。
在传统的环境下,一个车间任务的布局是相似的机器成为一组,所有库存点都分布在不同的工作中心,通过MRP计划产生相应的生产订单。
这些生产订单穿过重重工作中心和成批排队。
调度员将用最有效的方法,如最小化换装时间决定每一个工作中心能用的生产能力。
.在推式制度中,供应者和顾客之间并未对供给数量和时间制定明确协议。
供给者以自己的速度,根据自己的工作日程来完成工作。
双方没有明确规定专门的放置地点。
即无明确的、协议,没有制定的项目又无法了解控制什么或由谁控制。
推式生产常源于按计划表生产,而计划表只是预计下道工序需要什么。
不幸的是,生产过程中有各种不同的变化,而且生产很少能与计划精密地吻合。
因此,当每道工序专注于自己的计划表时,它们就像一个个"孤岛",与下游工序分割开来。
每道工序都根据自身的特点,制定自己的批量,按自己觉得合理的节拍生产,而不是从整个价值流的角度去制定生产计划。
这种情况下,就会堆积库存,这种"批量和推动"使得连续流动几乎无法实现。
精益生产JIT的两种(推和拉)生产方式

拉)生产方式
1
两种(推和拉)生产系统
生产模式演变 精益生产整合界面 推进式(Push)控制系统 拉动式(Pull)控制系统 精益生产计划 追求的管理指标
2
生产模式演变
少品种 大批量
流水线生产
多品种 小批量
多品种 小批量
多品种 小批量
精益生产
3
生产模式演变:案例
11
推进式(Push)生产系统的管理指标
超产好 阿!
库存太多, 受不了
注意
12
拉动式(Pull)生产系统的管理指标
准时
库存 超产 欠产
单位生产时间 单位生产成本
13
思考题:
我们的生产系统属于哪种方式? 各有何优缺点? 该如何改进?
14
培训内容
(一)IPQC工作的意义 (二)IPQC工作内容 (三)制程不良统计区分 (四)过程检验三种形式
看板 均衡化
一个流 作业切换
5S
JIT 品质保证 标准作业
多能工
目视管理 设备保养
自动化 品质保证
5
推进式(Push)控制系统
生产计划部门
1
2
3
信息流 物料流 工作点
N-1
N
6
推进式(Push)控制系统
产品订单
A车间生产 计划 X车间生产 计划
甲供应商
7
拉动式(Pull)控制系统
生产计划部门
1
15
假设1次作业准备切换时间为1H,单位产品加工 时间为1Min,生产批量为3000个,求此批产品 总的作业时间。
如果压缩作业准备切换时间为1/10即6Min,生 产批量也减小为1/10即300个,求此批产品总的 作业时间。
推动式与拉动式[精彩]
![推动式与拉动式[精彩]](https://img.taocdn.com/s3/m/c90045253868011ca300a6c30c2259010202f319.png)
物流管理作业9.什么叫推进式计划方法和拉动式计划方法?它们有什么区别?哪些是拉动式计划方法?哪些是推进式计划方法?答:(1)推进式即用MRP系统制定生产计划和采购计划,然后由主生产进度计划和主产品的层次结构逐层逐个地求出产品所有零部件的出产时间、出产数量,从而形成加工任务单或采购任务单。
拉动式模式是以日本制造业提出的JIT技术为核心的生产物流管理模式,即从生产线末端的需求计划,往前拉动供应生产计划。
(2)推进式计划方法的特色:1.在管理标准化和制度方面重点处理突发事件;2.在管理手段上大量运用计算机管理,数据多,计算复杂;3.在生产物流方式上,以零件为中心,强调严格执行计划,维持一定量的在制品库存,且认为必要的库存是合理的;4.在生产物流计划编制和控制上,以零件需求为依据,计算机编制主生产计划、物料需求计划、生产作业计划,执行中以计划为中心,灵活机动性差,一旦某个环节出现纰漏,则整个计划就必须大变动。
拉动式模式物流管理的特色:1.在管理标准化和制度方面重点采用标准化作业;2.在管理手段上,把计算机管理与看板管理相结合,强调物流与市场需求同步;3.在生产物流方式上,从生产线末端的需求计划,一级一级往前拉动各个生产供应环节,做出切合实际的生产和采购计划,强调物流平衡而没有在制品库存;4.拉动式计划方法的出发点是不断消除生产系统中的一切浪费,最大特点是市场供需关系的工序化,它以外部市场独立需求为源点,拉动相关物料需求的生产和供应。
区别:1.推进式强调的是市场供应量,拉动式强调的是市场需求量;2.推进式适用于大众化的产品,比如方便面等,这种方式要求预测的准确性,拉动式适用于那些消费者个性化定制程度较高的,比如电脑,根据用户的不同配制需求,进行订单生产,这样没有库存,但是要求较强的客户响应能力;3.推进式库存管理是基于每个仓库的预测需求将剩余产能分配给每个仓库,拉动式库存管理是基于每个仓库的特定需求以一定的订货批量补足库存;(3)适用范围:一般来说,当采购或生产的规模经济收益超过拉动式库存管理方式实现的最低总库存水平带来的收益时,就可以采用推进式库存管理方式。
拉动式与推进式生产模式课件
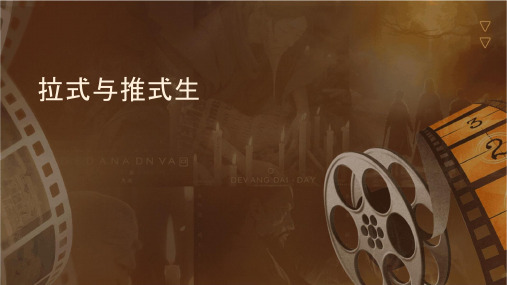
策略三:建立快速响应机制
总结词详细描述THAK YOU06拉动式生产模式的实施策略
策略一:运用看板系 统
总结词
详细描述
策略二:以需求为导向的生产计划管理
要点一
总结词
要点二
详细描述
以需求为导向的生产计划管理,可确保生产与市场需求保 持一致,降低库存风险。
在拉动式生产模式下,生产计划应以市场需求为导向,根 据销售数据和库存情况制定。通过及时调整生产计划,可 以降低库存积压和避免生产过剩的风险。此外,以需求为 导向的生产计划管理还能提高生产的灵活性,更好地适应 市场变化。
VS
详细描述
在推进式生产模式中,提高设备利用率是 关键。这可以通过制定合理的维护计划、 确保设备正常运行以及优化设备的布局等 方式实现。此外,对设备进行定期的检测 和维护也是必要的,以避免设备出现故障 或性能下降的情况。
策略二:优化生产流程
总结词
详细描述
策略三:建立高效的生产计划体系
总结词
详细描述
拉动式生产模式
是指根据客户实际订单来安排生产,由市场需求拉动生产,即“按需生产”。这种模式注重对市场需求的快速响 应和灵活调整。
对比两者优缺点和应用场景
根据企业实际情况选择合适的生产模式
05
推进式生产模式的实施策略
策略一:提高设备利用率
总结词
通过提高设备的利用率,可以降低生产 成本,提高生产效率。
02
推进式生产模式
定义及特点
推进式生产模式的优缺点
优点
1. 生产效率高:由于生产集中在同一地点或少数几个地点,推进式生产模式可以更 有效地利用资源和设备,从而提高生产效率。
2. 库存管理优化:通过预测市场需求并保持适当数量的库存,推进式生产模式可以 减少库存积压和缺货的风险。
拉式生产-高仁义

当工程接到计划下的母盘单之后开始制作母盘,而物 控计划等待工程制作完母盘才能开单排线,然后前加工 拷贝根据指令单领取母盘进行作业。
这样形成了一个不相关的作业之间建立拉式制度;
方正科技集团股份有限公司 Founder Technology Group Co.,Ltd.
5、无间断流程-拉动-降低库存-杜绝浪费
方正科技集团股份有限公司 Founder Technology Group Co.,Ltd.
案例:资料盒 之前资料包装是在接收到前端计划部门的指令后开始包
装,包装好的半成品暂放到规定区域内,后段包装根据需 求进行领用。由于资料包装的单组产能大于后段包装单线 的产能,所以对应关系没有采用一对一。
资料包装事实上是为了后段包装的需求进行作业的, 但目前是与生产流程前段同步接受指令,并且作业时间比 实际需求时间提前了5个小时,从而导致资料盒大量积压。
方正科技集团股份有限公司 Founder Technology Group Co.,Ltd.
2、“推动式” 与“拉动式”生产区别:
在推动式生产中,一个加工工序按照已制定好的生产 计划和排序对某一种生产物料加工完后,该种物料被“推” 向下一个工序,然后再按照此工序已制定好的生产计划和 排序进行加工,如此类推,该种物料被一步步从上游工序 “推”向下游工序。而在拉动式生产中,上游工序的生产 只按照由下游工序传递来的生产量、生产种类和排序等指 令进行生产,生产被下游工序“拉”动进行 。
4.3应该建立保全制度确保在生产出现故障的情况下,能继 续运行。拉动生产系统建立起来,必然有生产信号在各 个工序和生产车间之间传递,生产信号为电子看板,或 者卡片,这些都需要人来操作完成,因此,应该编写操 作说明,或者进行操作培训,确保拉动系统能够平稳运 行。
推式拉式解释
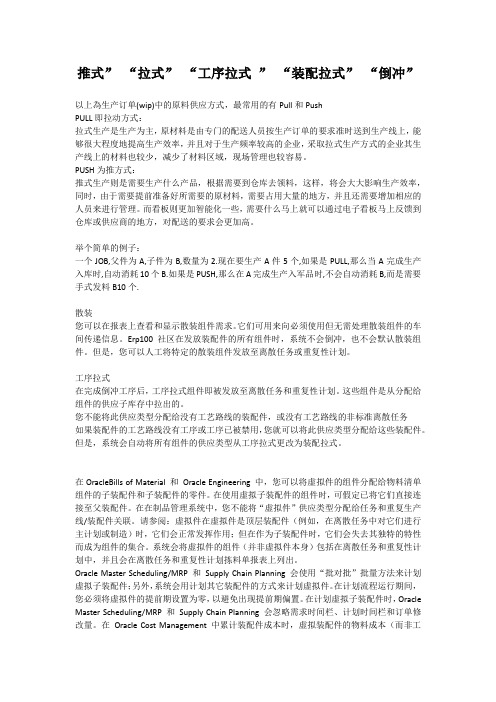
推式”“拉式”“工序拉式”“装配拉式”“倒冲”以上為生产订单(wip)中的原料供应方式,最常用的有Pull和PushPULL即拉动方式:拉式生产是生产为主,原材料是由专门的配送人员按生产订单的要求准时送到生产线上,能够很大程度地提高生产效率,并且对于生产频率较高的企业,采取拉式生产方式的企业其生产线上的材料也较少,减少了材料区域,现场管理也较容易。
PUSH为推方式:推式生产则是需要生产什么产品,根据需要到仓库去领料,这样,将会大大影响生产效率,同时,由于需要提前准备好所需要的原材料,需要占用大量的地方,并且还需要增加相应的人员来进行管理。
而看板则更加智能化一些,需要什么马上就可以通过电子看板马上反馈到仓库或供应商的地方,对配送的要求会更加高。
举个简单的例子:一个JOB,父件为A,子件为B,数量为2.现在要生产A件5个,如果是PULL,那么当A完成生产入库时,自动消耗10个B.如果是PUSH,那么在A完成生产入军品时,不会自动消耗B,而是需要手式发料B10个.散装您可以在报表上查看和显示散装组件需求。
它们可用来向必须使用但无需处理散装组件的车间传递信息。
Erp100社区在发放装配件的所有组件时,系统不会倒冲,也不会默认散装组件。
但是,您可以人工将特定的散装组件发放至离散任务或重复性计划。
工序拉式在完成倒冲工序后,工序拉式组件即被发放至离散任务和重复性计划。
这些组件是从分配给组件的供应子库存中拉出的。
您不能将此供应类型分配给没有工艺路线的装配件,或没有工艺路线的非标准离散任务如果装配件的工艺路线没有工序或工序已被禁用,您就可以将此供应类型分配给这些装配件。
但是,系统会自动将所有组件的供应类型从工序拉式更改为装配拉式。
在OracleBills of Material 和Oracle Engineering 中,您可以将虚拟件的组件分配给物料清单组件的子装配件和子装配件的零件。
在使用虚拟子装配件的组件时,可假定已将它们直接连接至父装配件。
基于Anylogic的推式与拉式生产系统对比研究
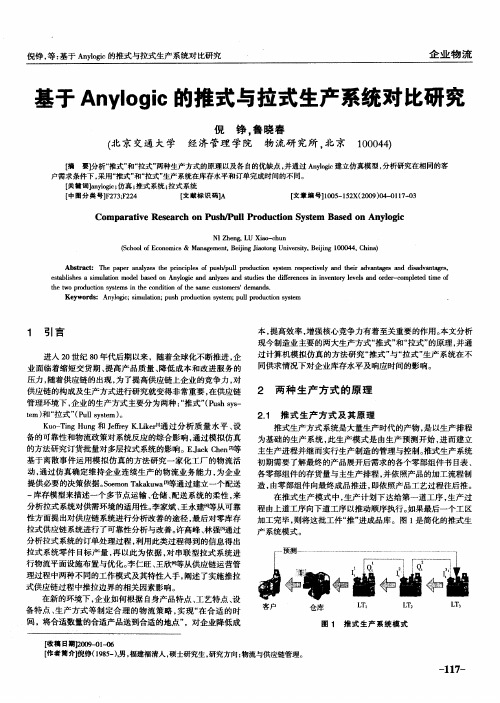
K o Tn u g和 Jfe Lk r通过 分析质 量水平 、 u— igH n e r K. et y i 】 设 备的可靠性和物流政策对 系统反应的综合影响 , 通过模拟仿真 的方法研究订货批量对 多层拉式系统的影响 。 . c h n2 EJ kC e 【 a 】 等 基于离散事件运用模拟仿真 的方法研究一家化工厂 的物流活 动, 通过仿真确定维 持企业 连续生产 的物流业务 能力 , 为企业
同供求情况下对企业库存水平及响应时间的影响。
2 两 种 生 产 方 式 的原 理
21 推式 生产 方式及 其原理 ቤተ መጻሕፍቲ ባይዱ
推式生产方式系统是大量生产时代 的产物 , 以生产排程 是 为基础的生产系统 , 此生产模式 是由生产预测开始 , 而建立 进 主 生 产进 程 并 继 而 实行 生产 制 造 的 管理 与控 制 。 式 生 产 系统 推 初期需要 了解最终的产 品展开后需求的各个零部组件 书目表 、 各零 部组件 的存货量与主生产排程 , 并依照产 品的加工流程制 造, 由零部组件向最终成品推进 , 即依 照产品工艺过程往后推。 在推式生 产模 式中 , 生产计划 下达 给第 一道 工序 , 生产过
t 和 “ 式 ”p uss m) e m) 拉 ( yt 。 u e
本, 提高效率 , 增强核心竞争力有着至关重要 的作用。 本文分析 现 今 制 造 业 主要 的两 大 生产 方 式 “ 式 ” “ 式 ” 推 和 拉 的原 理 , 并通 过计算机模拟仿真的方法研究“ 推式” 拉式” 与“ 生产 系统 在不
提供必要的决策依据。omo au a蹲 通过建立一个配送 Se n Iw p 【 库存模型来描述一个多节点运输 、 仓储 、 配送系统的柔性 , 来 分析拉式系统对供需环境 的适用性 。 李家斌 、 王永建l q 等从可靠
推拉式供应链的区别
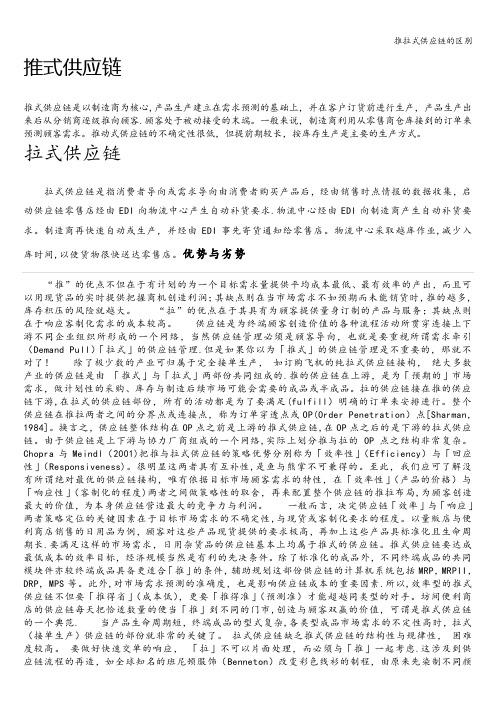
推式供应链推式供应链是以制造商为核心,产品生产建立在需求预测的基础上,并在客户订货前进行生产,产品生产出来后从分销商逐级推向顾客.顾客处于被动接受的末端。
一般来说,制造商利用从零售商仓库接到的订单来预测顾客需求。
推动式供应链的不确定性很低,但提前期较长,按库存生产是主要的生产方式。
拉式供应链拉式供应链是指消费者导向或需求导向由消费者购买产品后,经由销售时点情报的数据收集,启动供应链零售店经由EDI向物流中心产生自动补货要求.物流中心经由EDI向制造商产生自动补货要求。
制造商再快速自动或生产,并经由EDI事先寄货通知给零售店。
物流中心采取越库作业,减少入库时间,以使货物很快送达零售店。
优势与劣势“推”的优点不但在于有计划的为一个目标需求量提供平均成本最低、最有效率的产出,而且可以用现货品的实时提供把握商机创造利润;其缺点则在当市场需求不如预期而未能销货时,推的越多,库存积压的风险就越大。
“拉”的优点在于其具有为顾客提供量身订制的产品与服务;其缺点则在于响应客制化需求的成本较高。
供应链是为终端顾客创造价值的各种流程活动所贯穿连接上下游不同企业组织所形成的一个网络,当然供应链管理必须是顾客导向,也就是要重视所谓需求牵引(Demand Pull)「拉式」的供应链管理.但是如果你以为「推式」的供应链管理是不重要的,那就不对了!除了极少数的产业可归属于完全接单生产,如订购飞机的纯拉式供应链接构,绝大多数产业的供应链是由「推式」与「拉式」两部份共同组成的.推的供应链在上游,是为「预期的」市场需求,做计划性的采购、库存与制造后续市场可能会需要的成品或半成品。
拉的供应链接在推的供应链下游,在拉式的供应链部份,所有的活动都是为了要满足(fulfill)明确的订单来安排进行。
整个供应链在推拉两者之间的分界点或连接点,称为订单穿透点或OP(Order Penetration)点[Sharman,1984]。
换言之,供应链整体结构在OP点之前是上游的推式供应链,在OP点之后的是下游的拉式供应链。
- 1、下载文档前请自行甄别文档内容的完整性,平台不提供额外的编辑、内容补充、找答案等附加服务。
- 2、"仅部分预览"的文档,不可在线预览部分如存在完整性等问题,可反馈申请退款(可完整预览的文档不适用该条件!)。
- 3、如文档侵犯您的权益,请联系客服反馈,我们会尽快为您处理(人工客服工作时间:9:00-18:30)。
XJTU-IE, 2007.9-2008.9, M: xuchen.xuchen@(徐琛), lucifer_tcl@(李慰祖)第十章 推式与拉式生产系统You say yes.I say no.You say stop,And I say go, go, go!——约翰·列侬与保罗·麦卡特尼《Hello goodbye》10.1 引言实际中对JIT的描述都采用了推式(push)与拉式(pull)生产系统这两个术语。
然而,推和拉的定义常常不是很精确,并因此在美国产生了一些对于JIT的困惑。
在这一章,我们从概念水平上提供一个推和拉的正式定义。
通过它们的具体实施来区别推和拉的概念,我们说现实中的系统往往是推和拉的混合。
更进一步地,对比分别处于两个极端的“纯粹的拉”生产系统与“纯粹的推”生产系统,我们获得了使拉式生产系统运行更有效的因素。
这种见解暗示出存在着许多种实现拉式生产的益处的方法。
究竟哪一种最好,取决于一系列的环境因素,正如我们在本章讨论,并将在第三篇中进一步探讨的那样。
10.2 定义JIT之父,大野耐一(Taiichi Ohno),只在非常广泛的意义上使用拉这个术语:制造商与生产车间不能再仅仅将生产建立在桌上那一纸计划的基础上,然后再将产品分配,或者推到市场上。
它已经成为持有不同价值系统的客户或使用者站在市场前沿的必然结果;他们认为,以需要的数量、在需要的时刻拉出他们需要的产品,理所当然。
Hall(1983,39),在美国关于JIT的最著名的教科书之一中,更加具体地用事实来定义了拉式生产系统,“使用者因为需要而取物料”。
(339|340)虽然他承认可能有不同的拉式系统,但是唯一详细描述的系统是我们曾经在第四章中讨论过的丰田的看板。
1 Schonberger (1982),在美国另一本关于JIT的主流书籍中,严格在丰田式的看板系统的背景下谈及拉式系统。
因此,拉这种形式被认为与看板(kanban)类似也就不足为奇了。
然而,我们不认为这么狭窄的定义是大野耐一先生所希望的。
我们认为,将拉仅仅解释为看板是对预期目标的彻底颠覆:赋予拉更多具体说明的同时,它掩盖了拉的精髓。
它混淆了概念(拉)与执行(看板)。
为了从工厂物理学的角度来讨论拉的概念,给推拉系统一个全面而简单的定义是很重要的。
1霍尔又将拉式系统表述为广播(broadcast)系统,在这个系统中总装进度计划(FAS)被广播到产线中所有的起始点来触发加工任务的投放。
但是,他提醒到因为FAS是外生的,这个系统不能严格限制其中的库存总数。
通过提出将FAS信号作为宽松的拉式信号(loose pull signals),他区别了广播系统与看板系统中的控制。
因为广播系统限制WIP的失败,我们根本不能确信它是否能被称作拉式系统。
10.2.1 推与拉的关键区别将推与拉区分开的是引起制品在系统中运动的机制。
根本性地,投料触发来自推式系统之外,拉式系统之内。
更正式地,我们定义推式和拉式系统如下:定义:推式系统根据外部需求计划制品投放,而拉式系统则根据系统自身的状态授权制品投放。
图10.1中简略地描绘了推与拉的对比。
严格地说,推式系统是被外生计划要求时精确地将制品投入生产流程(工厂、产线、或工站),投料时间不会因为制程自身发生了什么事情而调整。
与之相反,只有接到产线状态改变而产生需要开始的信号时,拉式系统才会允许物料进入流程。
典型地,像在丰田的看板系统中,这些授权信号是产线中某些点制品加工完成的结果。
值得注意的是,这个定义与实际上操作任务的人没有关系。
如果下游作业员自上游流程收到制品,但这一举动是根据外部排配,那么这就是推;而如果上游作业员将制品递交给下游流程,但这一举动是对下游流程状态改变的反应,那么这就是拉。
图10.1 推式与拉式系统的投料触发另一种有益于考察推与拉区别的方式是,推式系统由其内在属性而决定了是接单生产(make-to-order),而拉式系统则为备货生产(make-to-stock)。
也就是说,是订单(或预测),而不是系统状态驱动着推式系统的计划。
拉式系统则以系统某处库存不足为批准投料的信号。
从这个角度看,基准库存点模型(base stock model)当库存降低到某一特定水平之下即触发订单,是拉的方法;MRP根据客户订单建立规划然后根据规划投放订单,是推的方法。
当然,大多数现实世界中的系统包含了推和拉两个方面。
例如,如果一件任务由MRP 排配投放,但是因为考虑到产线的拥堵又保持了这个任务,那么这种效果就是一个混合式推-拉系统。
(340|341)相反地,如果一个看板系统生成批准生产的卡片,但实际的任务触发却因为对部件的预计需求不足(即,没有在主生产计划中体现)而推迟,那么,这也是一个混合式系统(如,见Wight 1970,Deelersnyder等 1988,Suri 1998)。
我们将在第三篇中讨论混合式系统的优点,并提供一种实用方法。
我们列出推与拉的显著区别不是建议使用者们严格地选择其中一个或另一个。
秉着工厂物理学的精神,我们更愿意用自己的详细说明来解析拉式系统的好处并探究其根源。
在某种意义上,我们采用了与物理学类似的方法——将机械系统放在无摩擦的理想环境中去考虑。
并不是说理想环境是普遍存在的,而是说在这样一种理想环境下,地球引力、加速度、速度等概念会变得更清晰。
就像在理想环境中探究经典力学是现实物理系统分析的基础一样,我们对于纯粹的拉式与推式生产系统的观察将会提供一个分析现实生产系统的基础。
10.2.2 推-拉界面是否要用、怎么使用拉只是蓝图的一部分,在哪儿用也很重要。
甚至在一个单独的生产系统中,部分按照拉式操作都是可能的。
推-拉界面(push-pull interface)是确定何处放置拉式过程时的一个有用概念,它将生产流程分成推段与拉段2。
成功地选择这个界面的位置能使系统利用拉的优点而取得战略优势,同时还能保持推式系统的客户驱动的特征。
(341|342)图10.2 推-拉界面的位置图示为了理解推-拉界面的概念,不妨将推定义为“接单生产”的形式来,而将拉定义为“备货生产”的形式。
为了理解如何将相似的产线有区别地分成推段和拉段,我们考察图10.2所示的两个生产系统。
在QuickTaco的前端,玉米煎饼备货生产以维持加热台的固定库存水平,使得这一部分表现为拉式;产线的后端只有在客户订单触发后才会移动制品,因此这一部分表现为推式。
推-拉界面位于加热台处。
相反地,在TacoUltimo中,玉米煎饼的移动只能由客户订单来触发,因而它完全是一个推式系统。
推-拉界面位于冰箱处,在那里按照库存目标来储存原材料。
对比QuickTaco与 TacoUltimo的相对优势,我们可以获得权衡推-拉界面位置的洞察力。
2“推-拉界面”这个术语,我们受益于HP的Corey Billington;它被创造来辅助描述HP“供应链管理纲要”之中的部分实践活动。
见Lee与Billington(1995)对HP供应链创新的概述。
TacoUltimo,因为它完全由订单驱动并且几乎全部以原材料形式保有库存,所以具有柔性优势(即,它能生产客户想要的任何一种煎饼);QuickTaco,因为它保有成品煎饼库存,所以具有反应能力优势(即,它能向客户提供更短的提前期)。
因此,需要在速度和柔性之间进行权衡。
通过将推-拉界面移近客户,我们可以缩短提前期,而代价是降低柔性。
(342|343)所以对于一个给定的系统应该如何来选择推-拉界面的位置呢?既然它取决于客户的偏好以及生产流程的实质细节,那么这就不是一个简单的问题。
但是,我们能够提供一些观测资料和现实中的例子。
首先,请注意速度是促使我们将推-拉界面移近客户的首要原因。
因此只有在客户看来增加的速度确实显著提高了服务水平时,这么做才是有意义的。
例如,一个线上周期时间为两小时却实行日末出货(end-of-day shipments)的生产系统,通过移动推-拉界面缩短了周期时间,但客户却看不出提前期有任何不同。
甚至在速度显然很关键的快餐行业,也有一些使用TacoUltimo型产线的餐馆。
他们这么做是因为确信整条产线的周期时间已经足够地短,能够使系统满足客户的期望。
然而,在速度压力特别大的就餐高峰期,许多TacoUltimo型餐馆会转向QuickTaco型。
其次,我们观察到推-拉界面的选择受到它自身流程的巨大影响。
例如,在玉米煎饼产线中我们可能会建议将推-拉界面放在装配线中间的某个地方。
那就是说,做好玉米面饼并在里面装上肉,让口开着,等待涂上配料(toppings)。
然而,这会导致存储和质量问题(如,部分叠合的煎饼会散开),因而可能是不可行的。
第三,请注意推-拉界面位置的经济性会受到产品通过系统时是如何被定制化的影响。
在终端品目(end items)非常少的系统(如,一个只有原木和胶水等原材料,并且生产少数集中不同厚度夹板的夹板制造厂)中,将推-拉界面放在制成品(finished goods)处是相当明智的。
然而,在一个有许多终端品目的系统(如,一个零部件可以组合到一系列不同PC 成品的PC装配厂)中,保持制成品库存是非常昂贵的(见8.8.2节中安全库存集结(aggregation)的例子)。
例如,在玉米煎饼生产系统中,将推-拉界面放在包装之后不是个好主意,因为那需要将煎饼按照所有需要的类型(size)和组合(combination)分装成不同的袋来进行储存。
最后,请注意认识到定制化与变动性汇聚(variability pooling)紧密相关,如我们在第八章中的介绍。
在一个越向产线下游产品定制化程度越高的系统中,推-拉界面向上游移动可以降低为应对需求变动性而设立的安全库存的数量。
例如,贝纳通(Benetton)使用这样的系统,没有着色的毛衣进行备货生产,然后按订单进行染色。
也就是说,他们将推-拉界面从染色工序之后移到之前。
通过这样做,他们分担了对不同颜色毛衣的库存,并因此降低了达到给定客户服务水平所需的库存成本。
一些其他的因重新定位推-拉界面位置而提高整体系统绩效的真实例子包括以下这些:IBM有一个印制电路板生产车间,能够将玻璃纤维和一些不同厚度的铜制成150种不 1.同的电路板。
产线的前面部分生产基板(core blanks)——铜片和玻璃纤维,所有的电路板制造都是从这里开始的。
只有八种不同的基板,经由固定的成批叠压制程生产出来,很难将其与客户订单匹配。
管理层对基板储存进行选择(即,将推-拉界面从原材料处移动到叠压制程之后的库存点)。
这样做的结果是从能够被客户感知的提前期中减少一到两天的周期时间,但只需额外增加一点点库存成本。
(343|344)通用汽车引入了一个新的车辆配送系统,从佛罗里达的卡迪拉克开始,在地区配送 2.中心中储存那些受欢迎的型号(《华尔街日报》,1996年10月21日,A1)。