钣金件质量检验报告单
钣金检验标准

钣金检验标准 IMB standardization office【IMB 5AB- IMBK 08- IMB 2C】文件名称:钣金产品检验标准文件编号:WTL-MP-QA-002发行日期:2007年03月01日1. 目的确保零部件的加工质量,防止未经检验和不合格的加工零部件转序或误用。
2. 适用范围本指导书明确规定了钣金制造工序检验的方法和要求。
本指导书适用于公司内对钣金加工零部件的质量控制,当产品有特殊要求涵盖本指导书,请遵照产品特殊要求执行。
3. 职责生产部操作工负责对所加工零部件进行自检和互检。
质量部负责所加工零部件的检验和不良品处理。
工程部负责产品技术支持。
4. 工序检验规范操作工在操作前,要对上道工序加工零件或原材料进行外观和形状检验,如果发现不良品,操作工可以拒收并通知检验员或工程师处理该不良品。
拉丝检验:4.1.1 检验方法a.操作工及检验员对于每班每批次拉丝加工零件都必须进行首件检验,只有当首件检验合格后,方能进行批量生产. 检验员要求一次首件,一次过程检验和一次最终检验。
操作工在领原材料时必须依据生产程序单的要求检查规格尺寸。
b.操作工应对拉丝零件的表面质量进行全数检验。
4.1.2 检验要求:4.1.2.1 按照工程文件,确认拉丝前原材料符合要求。
剪切零件的检验要求:4.1.2. 对第一块剪下来的材料,应仔细测量各尺寸。
对所剪切的零件进行对角线测量:小于2mm 为合格。
单边测量:小于0.5mm为合格。
检验员检验合格后才可以继续剪料。
4.1.2. 对于剪下来的材料,检查材料剪切边缘是否有蜷曲和变形,如有高于表面0.5mm的为不合格。
4.1.3 剪切下来的板材表面优先按照TS文件或者Routing上有规定的要求检验,没要求的一般按照以下4点要求检验:4.1.3.1 不得有长度超过4毫米深划痕(有手感的),特别是正中很明显的位置,或划痕虽浅但很多很密很长,均不允许。
单面刮痕不能超过2条。
面板安装质量检验报告单
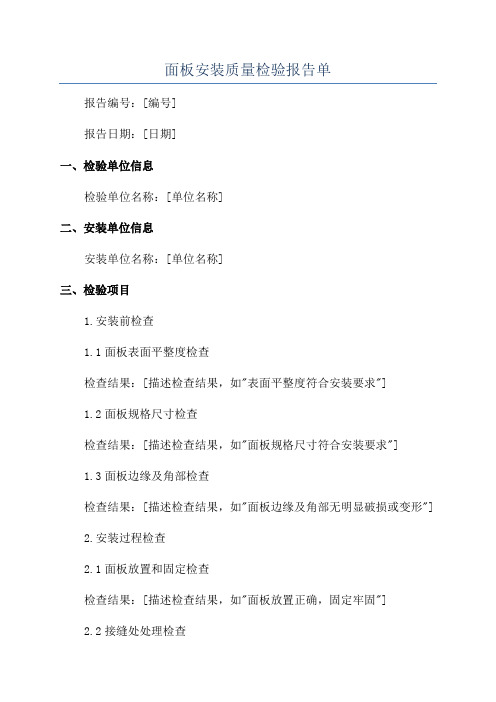
面板安装质量检验报告单报告编号:[编号]报告日期:[日期]一、检验单位信息检验单位名称:[单位名称]二、安装单位信息安装单位名称:[单位名称]三、检验项目1.安装前检查1.1面板表面平整度检查检查结果:[描述检查结果,如"表面平整度符合安装要求"]1.2面板规格尺寸检查检查结果:[描述检查结果,如"面板规格尺寸符合安装要求"]1.3面板边缘及角部检查检查结果:[描述检查结果,如"面板边缘及角部无明显破损或变形"]2.安装过程检查2.1面板放置和固定检查检查结果:[描述检查结果,如"面板放置正确,固定牢固"]2.2接缝处处理检查检查结果:[描述检查结果,如"接缝处处理平整,无明显缝隙"]2.3面板与墙面连接检查检查结果:[描述检查结果,如"面板与墙面连接紧密,无松动现象"]2.4面板与地面连接检查检查结果:[描述检查结果,如"面板与地面连接紧密,无松动现象"]2.5面板与天花板连接检查检查结果:[描述检查结果,如"面板与天花板连接紧密,无松动现象"]3.安装后细节检查3.1表面清洁度检查检查结果:[描述检查结果,如"面板表面清洁度符合要求"]3.2辅助材料使用检查检查结果:[描述检查结果,如"辅助材料使用符合要求"]3.3面板装饰效果检查检查结果:[描述检查结果,如"面板装饰效果符合设计要求"]四、检验结论根据以上检验项目的检查结果,判断面板安装质量情况如下:[描述检验结论,如"面板安装质量良好五、存在问题及改进措施1.问题描述:[描述存在的问题,如"部分面板接缝处有轻微缝隙"]改进措施:[提出改进措施,如"重新处理接缝处,确保接缝无缝隙"]2.问题描述:[描述存在的问题,如"部分面板表面有污渍"]改进措施:[提出改进措施,如"清洁面板表面,确保表面无污渍"]六、检验人员意见检验人员意见:[检验人员意见,如"面板安装质量整体较好,符合要求"]七、附件1.安装前拍照:[安装前的照片,可附图]2.安装后拍照:[安装后的照片,可附图]3.相关检测资料:[如有其他相关检测资料,可附]八、签署检验单位负责人(签名):____________________检验单位负责人(日期):____________________安装单位负责人(签名):____________________。
钣金件加工检验通用标准
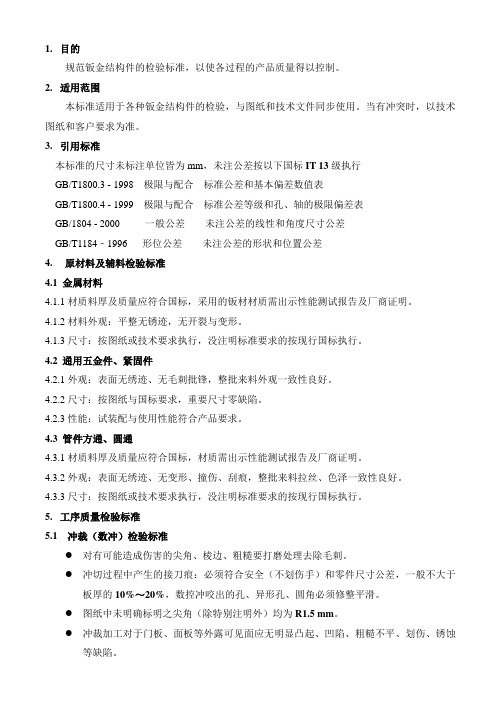
1.目的规范钣金结构件的检验标准,以使各过程的产品质量得以控制。
2.适用范围本标准适用于各种钣金结构件的检验,与图纸和技术文件同步使用。
当有冲突时,以技术图纸和客户要求为准。
3.引用标准本标准的尺寸未标注单位皆为mm,未注公差按以下国标IT 13级执行GB/T1800.3 - 1998 极限与配合标准公差和基本偏差数值表GB/T1800.4 - 1999 极限与配合标准公差等级和孔、轴的极限偏差表GB/1804 - 2000 一般公差未注公差的线性和角度尺寸公差GB/T1184–1996 形位公差未注公差的形状和位置公差4.原材料及辅料检验标准4.1 金属材料4.1.1材质料厚及质量应符合国标,采用的钣材材质需出示性能测试报告及厂商证明。
4.1.2材料外观:平整无锈迹,无开裂与变形。
4.1.3尺寸:按图纸或技术要求执行,没注明标准要求的按现行国标执行。
4.2 通用五金件、紧固件4.2.1外观:表面无绣迹、无毛刺批锋,整批来料外观一致性良好。
4.2.2尺寸:按图纸与国标要求,重要尺寸零缺陷。
4.2.3性能:试装配与使用性能符合产品要求。
4.3 管件方通、圆通4.3.1材质料厚及质量应符合国标,材质需出示性能测试报告及厂商证明。
4.3.2外观:表面无绣迹、无变形、撞伤、刮痕,整批来料拉丝、色泽一致性良好。
4.3.3尺寸:按图纸或技术要求执行,没注明标准要求的按现行国标执行。
5.工序质量检验标准5.1 冲裁(数冲)检验标准●对有可能造成伤害的尖角、棱边、粗糙要打磨处理去除毛刺。
●冲切过程中产生的接刀痕:必须符合安全(不划伤手)和零件尺寸公差,一般不大于板厚的10%~20%,数控冲咬出的孔、异形孔、圆角必须修整平滑。
●图纸中未明确标明之尖角(除特别注明外)均为R1.5 mm。
●冲裁加工对于门板、面板等外露可见面应无明显凸起、凹陷、粗糙不平、划伤、锈蚀等缺陷。
●毛刺:冲裁后毛刺高L ≤5% t(t为板厚)。
钣金结构件检验通用标准

钣金结构件检验通用标准1.目的规范钣金结构件的检验标准,以使各过程的产品质量得以控制。
2.适用范围本标准适用于各种钣金结构件(设备防护、电控柜等)的检验,图纸和技术文件并同使用。
当有冲突时,以技术规范为准。
3.引用标准本标准的尺寸未注单位皆为mm,未注公差按以下国标IT13级执行GB/T1800.3-1998 极限与配合标准公差和基本偏差数值表GB/T1800.4 -1998 极限与配合标准公差等级和孔、轴的极限偏差表GB/1804-2000 一般公差未注公差的线性和角度尺寸的公差未注形位公差按GB/T1184 –1996 形状和位置公差未注公差值执行。
4.原材料检验标准(我司有权对厂家生产用原材料进厂抽检)4.1金属材料4.1.1钣材厚度及质量应符合国标,采用的钣材需出示性能测试报告及厂商证明。
4.1.2 材料外观:平整无锈迹斑痕,无开裂与变形。
4.1.3尺寸:按图纸或技术要求执行,本司未有的按现行国标执行。
4.2通用五金件、紧固件4.2.1外观:表面无绣迹、无毛刺批锋,整批来料外观一致性良好。
4.2.2尺寸:按图纸与国标要求,重要尺寸零缺陷。
4.2.3性能:试装配与使用性能符合产品要求。
5.钣金结构件加工工序质量检验标准5.1下料检验标准5.1.1钣金件表面平整,加工处无毛刺、凸起、裂纹等。
表一、平面度公差要求表面尺寸(mm) 变形尺寸(mm)3以下±0.2以下大于3小于30 ±0.3以下大于30小于315 ±0.5以下大于315小于1000 ±1.0以下大于1000小于2000 ±1.5以下大于2000小于3150 ±2.0以下5.2.1除特别注明外,折弯内圆角为R1。
5.2.2压印:看得到有折痕,但用手触摸感觉不到(可与限度样板相比较)。
5.2.3折弯检验尺寸的选取原则(如图)5.2.3.1 L型表二一次折弯的折弯高度尺寸未注公差值(单位:mm)基本尺寸分段≤30 >30~120 >120~500>500~1000>1000未注公差值±0.2 ±0.3 ±0.5 ±0.8 ±1.0a).压死边的折弯尺寸的未注公差值如图,尺寸H3的未注公差值为(+0.5~0),尺寸H4未注公差值±1。
钣金原材料检验标准

目测
√
√
√
√
编写/日期
审核/日期
批准/日期
标记
处数
更改文件号
签字
日期
A类缺陷: 致命的安全性缺陷; B类缺陷: 严重的功能性缺陷; C类缺陷: 轻微的外观性缺陷
附表
表1 钢带厚度允许偏差 单位:mm
宽度
厚度允许偏差
≤1
≥
≥
≥
≤50-100
±
±
±
±
≤100-500
±
±
±
±
表2 钢带宽度允许偏差 单位:mm
Q255
255
410-550
24
Q275
275
490-630
20
Q295
295
390-570
23
表4
厚度(mm)
最小反复弯曲次数 (圆柱支座半径r=3mm)
<
4
>
3
版本
A/0
零部件名称
冷轧板、镀锌板原材料
共2页第2页
项目
质量标准
质量特性
检验
方法/仪器
检验阶段
样品承认
进料检验
制程检验
成品检验
型式实验
抽样方案:按《统计抽样规定》QY-SIP-80301抽取样品。
镀锌层厚
热镀锌的锌层厚度应≥45μm。用称量法(仲裁方法)测量时,基本测量面为一次测量所去除的区域,不应小于 ㎡,镀层的密度取7.2g/cm3,从单位面积镀层质量可计算出镀层的近似厚度。
钣金原材料检验标准
宁波沁园集团公司
零部件检验标准
产品型号
通用
文件编号
QB/QY11-Z001
来料检验表格填写

来料检验表格填写篇一:来料检验记录单钣金材料来料检验记录单备注: 编号规则按入库单号填写表格生效日期:2011年6月1日铝箔来料检验记录单备注: 编号规则按入库单号填写表格生效日期:2011年6月1日备注: 编号规则按入库单号填写表格生效日期:2011年6月1日备注: 编号规则按入库单号填写表格生效日期:2011年6月1日备注: 编号规则按入库单号填写表格生效日期:2011年6月1日篇二:进料检验规范(含表格)进料检验规范(ISO9001:2015)1.目的:为加强零配件及原材料的质量管理,确保来料质量符合标准,防止不合格品入库,特制定本规范。
2.定义:来料检验又称进料检验,是本公司防止不合格物料进入生产环节的首要控制点。
致命缺陷(CR):凡是对人体或机器产生伤害或危及生命财产的缺点严重缺陷(MA):可能造成产品损坏,功能NG或使用者需要额外加工的缺点轻微缺陷(MI):不影响产品功能的缺点,泛指一般外观轻微不良或差异3.范围:适用于本公司所有进料检验作业。
4:引用标准:抽样计划按MIL-STD-105E单次抽样II级CR:0 MAJ:0.65 MIN:1.5执行5:来料检验流程图:见附件一6.来料检验流程:6.1采购部根据原材料到货日期、品种、规格等通知仓管部和品质部准备来料验收及检验工作。
6.2原材料到厂时,由仓管员,根据采购单,对产品规格、品种、数量、包装方式进行确认,并把来料放置待检区,并通知检验人员对该批物料进行检验,6.3IQC检验PASS合格后,则仓库执行入库处理。
6.4对检测不合格的物料根据《不合格品控制程序》的规定处置,不合格的物料禁止入库,应将其做好相应标识移入不合格品区放置。
6.4.1不合格物料评审,对不合格物料IQC填写IQC检验报告,并附不良样板经品质主管确认后,由公司MRB委员会进行物料评审,最终决定不合格物料的处理方式。
6.4.2评审结果为退货,由IQC在物料上贴不良标签,并注明不良原因和附不良样板,通知采购,由采购开具退货单,由仓库作退货处理。
钣金质量控制QC工程图
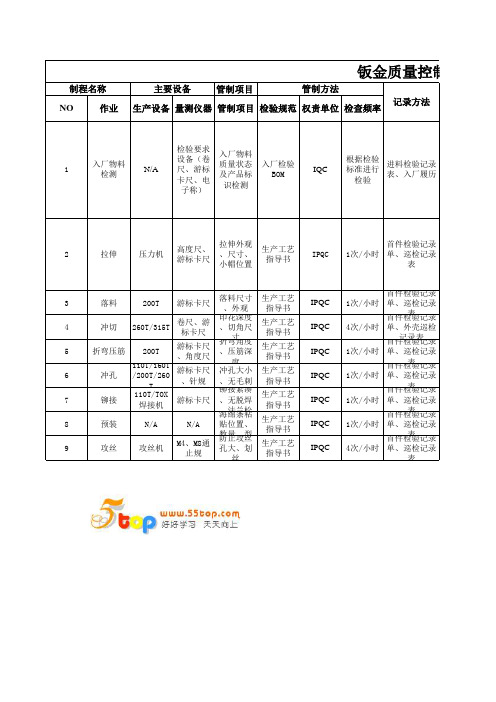
管制项目3落料200T游标卡尺落料尺寸、外观生产工艺指导书IPQC 1次/小时首件检验记录单、巡检记录表4冲切260T/315T卷尺、游标卡尺印花深度、切角尺寸生产工艺指导书IPQC 4次/小时首件检验记录单、外壳巡检记录表5折弯压筋200T游标卡尺、角度尺折弯角度、压筋深度生产工艺指导书IPQC 1次/小时首件检验记录单、巡检记录表6冲孔110T/160T /200T/260T 游标卡尺、针规冲孔大小、无毛刺生产工艺指导书IPQC 1次/小时首件检验记录单、巡检记录表7铆接110T/TOX焊接机游标卡尺铆接紧凑、无脱焊、法兰松生产工艺指导书IPQC 1次/小时首件检验记录单、巡检记录表8预装N/A N/A 海绵条粘贴位置、数量、型生产工艺指导书IPQC 1次/小时首件检验记录单、巡检记录表9攻丝攻丝机M4、M8通止规防止攻丝孔大、划丝生产工艺指导书IPQC4次/小时首件检验记录单、巡检记录表钣金质量控制Q制程名称主要设备管制方法记录方法NO作业生产设备量测仪器管制项目检验规范进料检验记录表、入厂履历权责单位检查频率根据检验标准进行检验首件检验记录单、巡检记录表1入厂物料检测N/A检验要求设备(卷尺、游标卡尺、电子称)入厂物料质量状态及产品标识检测入厂检验BOMIQC2拉伸压力机高度尺、游标卡尺拉伸外观、尺寸、小帽位置生产工艺指导书IPQC1次/小时。
钣金件加工检验通用标准
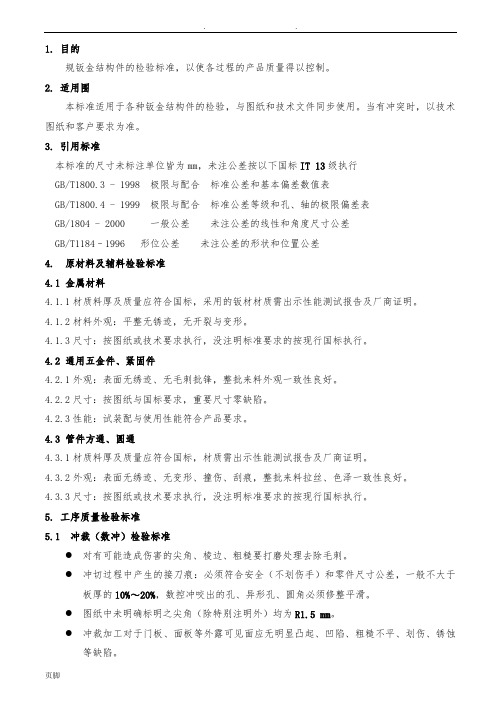
1.目的规钣金结构件的检验标准,以使各过程的产品质量得以控制。
2.适用围本标准适用于各种钣金结构件的检验,与图纸和技术文件同步使用。
当有冲突时,以技术图纸和客户要求为准。
3.引用标准本标准的尺寸未标注单位皆为mm,未注公差按以下国标IT 13级执行GB/T1800.3 - 1998 极限与配合标准公差和基本偏差数值表GB/T1800.4 - 1999 极限与配合标准公差等级和孔、轴的极限偏差表GB/1804 - 2000 一般公差未注公差的线性和角度尺寸公差GB/T1184–1996 形位公差未注公差的形状和位置公差4.原材料及辅料检验标准4.1 金属材料4.1.1材质料厚及质量应符合国标,采用的钣材材质需出示性能测试报告及厂商证明。
4.1.2材料外观:平整无锈迹,无开裂与变形。
4.1.3尺寸:按图纸或技术要求执行,没注明标准要求的按现行国标执行。
4.2 通用五金件、紧固件4.2.1外观:表面无绣迹、无毛刺批锋,整批来料外观一致性良好。
4.2.2尺寸:按图纸与国标要求,重要尺寸零缺陷。
4.2.3性能:试装配与使用性能符合产品要求。
4.3 管件方通、圆通4.3.1材质料厚及质量应符合国标,材质需出示性能测试报告及厂商证明。
4.3.2外观:表面无绣迹、无变形、撞伤、刮痕,整批来料拉丝、色泽一致性良好。
4.3.3尺寸:按图纸或技术要求执行,没注明标准要求的按现行国标执行。
5.工序质量检验标准5.1 冲裁(数冲)检验标准●对有可能造成伤害的尖角、棱边、粗糙要打磨处理去除毛刺。
●冲切过程中产生的接刀痕:必须符合安全(不划伤手)和零件尺寸公差,一般不大于板厚的10%~20%,数控冲咬出的孔、异形孔、圆角必须修整平滑。
●图纸中未明确标明之尖角(除特别注明外)均为R1.5 mm。
●冲裁加工对于门板、面板等外露可见面应无明显凸起、凹陷、粗糙不平、划伤、锈蚀等缺陷。
●毛刺:冲裁后毛刺高L ≤ 5% t(t为板厚)。
钣金件加工检验通用标准

1.目的标准钣金结构件的检验标准,以使各过程的产品质量得以控制。
2.适用范围本标准适用于各种钣金结构件的检验,与图纸和技术文件同步使用。
当有冲突时,以技术图纸和客户要求为准。
3.引用标准本标准的尺寸未标注单位皆为mm,未注公差按以下国标IT 13级执行- 1998 极限与配合标准公差和基本偏差数值表GB/T1800.4 - 1999 极限与配合标准公差等级和孔、轴的极限偏差表GB/1804 - 2000 一般公差未注公差的线性和角度尺寸公差GB/T1184–1996 形位公差未注公差的形状和位置公差4.原材料及辅料检验标准金属材料材质料厚及质量应符合国标,采用的钣材材质需出示性能测试报告及厂商证明。
4.1.2材料外观:平整无锈迹,无开裂与变形。
4.1.3尺寸:按图纸或技术要求执行,没注明标准要求的按现行国标执行。
4.2 通用五金件、紧固件4.2.1外观:外表无绣迹、无毛刺批锋,整批来料外观一致性良好。
4.2.2尺寸:按图纸与国标要求,重要尺寸零缺陷。
4.2.3性能:试装配与使用性能符合产品要求。
4.3 管件方通、圆通4.3.1材质料厚及质量应符合国标,材质需出示性能测试报告及厂商证明。
4.3.2外观:外表无绣迹、无变形、撞伤、刮痕,整批来料拉丝、色泽一致性良好。
4.3.3尺寸:按图纸或技术要求执行,没注明标准要求的按现行国标执行。
5.工序质量检验标准冲裁〔数冲〕检验标准●对有可能造成伤害的尖角、棱边、粗糙要打磨处理去除毛刺。
●冲切过程中产生的接刀痕:必须符合安全〔不划伤手〕和零件尺寸公差,一般不大于板厚的10%~20%,数控冲咬出的孔、异形孔、圆角必须修整平滑。
●图纸中未明确标明之尖角〔除特别注明外〕均为mm。
●冲裁加工对于门板、面板等外露可见面应无明显凸起、凹陷、粗糙不平、划伤、锈蚀等缺陷。
●毛刺:冲裁后毛刺高L ≤5% t〔t为板厚〕。
●划伤、刀痕:以用手触摸不刮手为合格,应≤mm。
●冲裁尺寸符合技术图纸要求,平面度公差要求见表一。
审核检查表(钣金工厂)
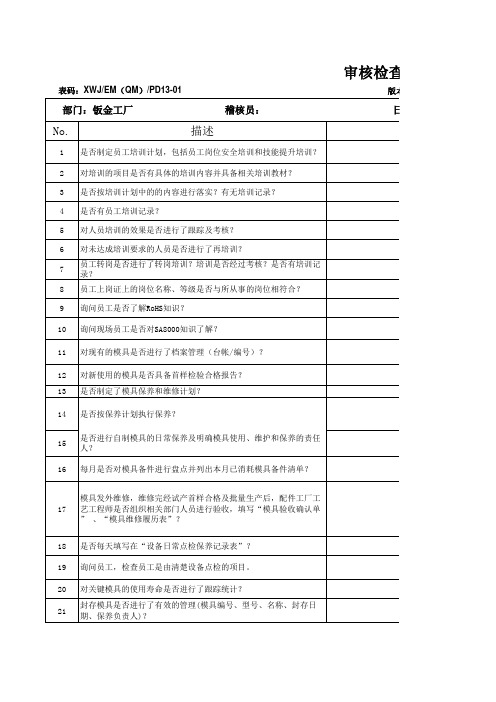
74 75
76
在巡检过程中,是否合格时在“质量跟踪卡”上盖蓝色工号章,不 合格时盖红色工号章,并且当天生产完成后在“冷加工巡检记录表 ”记录检验结果及当天生产状态? PQC检验合格的成品是否直接在“车间成品状态标识卡”上盖合格 蓝色章及检验员对应的工号章 符合停线条件时是否开出停线通知要求停线? 生产过程中品质异常时是否按照品质异常处理流程执行? 员工是否按计划进行了ROHS指令培训和考核,是否有培训记录。抽 查3名新进员工的培训记录。 是否编制了计量仪器台帐对PQC质检员工使用的计量仪器进行归档 管理。 点检发现计量仪器、测试仪器有问题时,PQC员工是否及时将问题 反馈给测试中心仪器管理人员。 对于ROHS订单,如果在首样确认或巡检时,发现非ROHS物料或可疑 物料时,是如何处理?是否有记录? 产品生产过程中是否有检验状态标识。 查看本周的冷加工间首检记录,并查看记录工艺要求,对超差尺寸 首样是否进行了处理,查看是否相关证据证实。 查看冷加工的过程巡检记录,看是否符合要求量跟踪卡上盖蓝色工号章不合格时盖红色工号章并且当天生产完成后在冷加工巡检记录表记录检验结果及当天生产状态
审核检查表
表码: 表码:XWJ/EM(QM)/PD13-01 ( ) 版本号
部门: 部门:钣金工厂
稽核员: 稽核员:
日期
No.
1 2 3 4 5 6 7 8 9 10 11 12 13 14
描述
是否制定员工培训计划,包括员工岗位安全培训和技能提升培训? 对培训的项目是否有具体的培训内容并具备相关培训教材? 是否按培训计划中的的内容进行落实?有无培训记录? 是否有员工培训记录? 对人员培训的效果是否进行了跟踪及考核? 对未达成培训要求的人员是否进行了再培训? 员工转岗是否进行了转岗培训?培训是否经过考核?是否有培训记 录? 员工上岗证上的岗位名称、等级是否与所从事的岗位相符合? 询问员工是否了解RoHS知识? 询问现场员工是否对SA8000知识了解? 对现有的模具是否进行了档案管理(台帐/编号)? 对新使用的模具是否具备首样检验合格报告? 是否制定了模具保养和维修计划? 是否按保养计划执行保养? 是否进行自制模具的日常保养及明确模具使用、维护和保养的责任 人? 每月是否对模具备件进行盘点并列出本月已消耗模具备件清单?
钣金件检验规范标准

#1.目的:规范钣金结构件的检验标准,以使各过程的产品质量得以控制。
2.适用范围:本标准适用于各种钣金结构件的检验,图纸和技术文件同时使用。
当有冲突时,以技术规范和客户要求为准。
3.引用标准:本标准的尺寸未注单位皆为mm,未注公差按以下国标IT13级执行GB/产品几何技术规范极限与配合第1部分:公差、偏差、和配合的基础GB/ -2009产品几何技术规范极限与配合第2部分:标准公差等级和孔、轴极限偏差表GB/1804-2000 一般公差未注公差的线性和角度尺寸的公差未注形位公差按GB/T1184 -1996 形状和位置公差未注公差值执行。
4。
原材料检验标准金属材料:钣材厚度及质量应符合国标,采用钣材需出示性能测试报告及厂商证明。
材料外观:平整无锈迹,无开裂与变形。
尺寸:按图纸或技术要求执行,本司未有的按现行国标执行。
通用五金件、紧固件外观:表面无绣迹、无毛刺批锋,整批来料外观一致性良好。
尺寸:按图纸与国标要求,重要尺寸零缺陷。
性能:试装配与使用性能符合产品要求。
5、工序质量检验标准冲裁检验标准对有可能造成伤害的尖角、棱边、粗糙要做去除毛刺处理。
图纸中未明确标明之尖角(除特别注明外)均为。
冲压加工所产生的毛刺,对于门板、面板等外露可见面应无明显凸起、凹陷、粗糙不平、划伤、锈蚀等缺陷。
毛刺:冲裁后毛刺高L≤5%t(t为板厚)。
划伤、刀痕:以用手触摸不刮手为合格,应≤。
平面度公差要求见表一。
附表一、未注平面度公差要求折弯检验标准毛刺:折弯后挤出毛刺高L≤10%t(t为板厚)。
压印:看得到有折痕,但用手触摸感觉不到。
(有特殊表面要求和镜面除外)折弯变形标准按照《表二》及《表三》。
【附表二:对角线公差要求】折弯方向、尺寸与图纸一致。
钢板在弯、折、卷制作过程中出现的锤击痕迹应予以修复,不得有明显锤窝现象。
钣金加工件检验标准尺寸:尺寸按图纸要求检验,尺寸公差见表三。
【附表三:未注尺寸公差要求】焊接焊缝应牢固、均匀,不得有虚焊、裂纹、未焊透、焊穿、豁口、咬边等缺陷。
钣金件来料检验规范标准(参考材料)
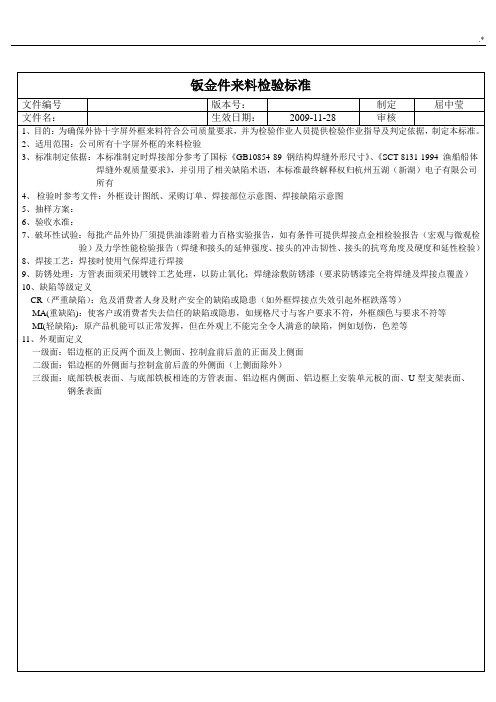
序号
项目
检验方法
检验标准
检验设备
缺陷
缺陷等级
1
包装
检验来料边框物料名称、规格及数量与采购订单是否相符
实物与单据相符
采购订单
实物与单据不相符
MA
目视检验珍珠棉是否将边框完全裹附,且珍珠棉是否用胶纸或扎带紧固于边框
珍珠棉完全裹附边框;珍珠棉被紧固于边框
目视
珍珠棉未被完全裹附边框或未被紧固于边框
MA
设计图纸
位置尺寸超出允许公差;孔径与图纸不符
MA
用卷尺或卡尺测量控制盒前后盖高、宽、厚尺寸及控制盒前后盖定位孔、散热孔、后盖2+2定位孔等位置尺寸;使用卡尺测量孔径
位置尺寸在图纸设计公差范围内;孔径与图纸要求相符
卷尺/卡尺
设计图纸
位置尺寸超出允许公差;孔径与图纸不符
MA
用卷尺或卡尺测量U型支架与钢条在方管上的位置尺寸
目视
有裂缝
CR
26
夹渣
在边框喷漆前进行检查,30cm处自然光线下目视检验焊接点
无夹渣
目视
有夹渣
MA
27
飞溅
在边框喷漆前进行检查,30cm处自然光线下目视检验焊缝两侧
100mm范围内,焊缝每侧≤7个
目视
飞溅数量超出要求
MA
28
弧坑
在边框喷漆前进行检查,30cm处自然光线下目视检验焊接点或用卡尺测量
长度L≤3,深度S≤1的弧坑一个焊接处允许一个
MI
序号
项目
检验方法
检验标准
检验设备
缺陷
缺陷等级
14
表面黑点
在室内光(日光灯45W,光线300-400LUX)下,距边框30CM处以90度视角进行目视检验
钣金检验报告单

□否
□合格
□轻微(局部凸起或脱落) □严重(大范围脱落)□ Leabharlann 格□ 基本合格 □ 不合格
□合格 □轻微(划痕很小或在不明显处)□严重(划痕很大或在很明显处)
□合格
□轻微(用直角尺量会发现但肉眼看不是很明显)
□严重(肉眼直接就能看出)
□ 合格
□ 基本合格 □ 不合格
□合格
□轻微(缝隙在可接受范围内)
□严重(装配后间隙很大,影响产品使用安全)
项目号 检验项目 外形尺寸
3U主控箱 3U配电箱(二) 4U配电箱(一)
配件
钣金件质量检验报告单
检验说明
产品名称 检验数量
LU配电箱
检验结果
备注
数量 颜色 镀锌 喷塑 钣金件强度 划痕 变形 焊接 装配 其他问题 处理意见
说明
检验人
□一致
□不一致
□合格
□单体产品颜色不一致 □成批量产品颜色不一致
□是
□发货
□返工 □报废 1、在检验结果中只能写合格或不合格
2、勾选或涂黑表示评审结论标注,表示选择与不选择 检验日期
钣金件尺寸未注公差检验标准

名称:钣金件尺寸未注公差检验标准图号:DMBM0.402.035I目次1. 范围..................................................................... 12. 规范性引用文件........................................................... 13. 名词解释................................................................. 14. 钣金件尺寸未注公差的检验要求............................................. 24.0 检验尺寸的选取原则............................................. 24.1 折弯高度尺寸的未注公差值....................................... 24.2 冲裁形状尺寸的未注公差值....................................... 34.3 冲裁位置尺寸的未注公差值....................................... 44.4 铆装件的位置尺寸的未注公差值................................... 54.5 角度尺寸的未注公差值........................................... 54.6 局部成形特征的形状和位置尺寸的未注公差值....................... 54.7 丝印形状和位置尺寸的未注公差值................................. 84.8 喷涂保护区域形状和位置尺寸的未注公差值......................... 84.9 装配尺寸的未注公差............................................. 9名称:钣金件尺寸未注公差检验标准图号:DMBM0.402.0351钣金件尺寸未注公差检验标准1. 范围本标准规定了钣金结构件检验中尺寸的未注公差的检验要求。
钣金件检验标准
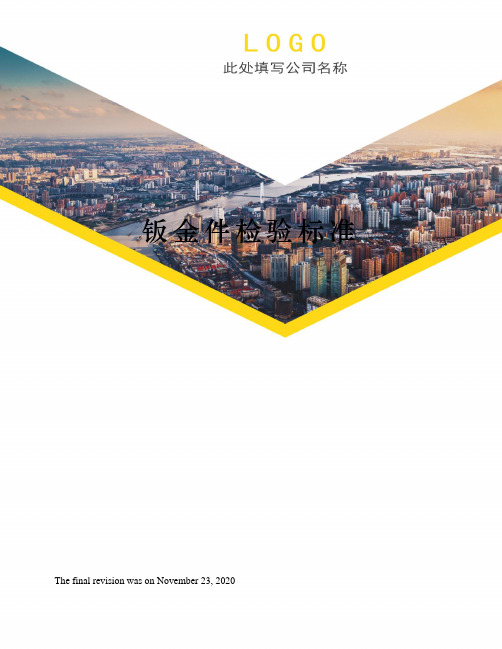
3.箱体内表面检验:
各面允许8点气泡或污点,每点直径1mm以下,点与点距离20mm以上。
4.烤漆厚度30μm-60μm。
5.表面处理后,各螺柱及螺孔表面不允许有漆层覆盖,影响装配。
包装1.每箱数量固定。
2.包装袋内不得有残留毛屑及杂物。
厚度/克重(质量)按xx g/m2计算- √供应商提供报告
参考文件:,附着力1、镀层后任何方向能弯曲180度且弯曲的外径没有任何金属脱落;√参考文件:
耐腐蚀1、盐雾试验后,在距离工件正常距离肉眼可观察到的表面有腐蚀(仅供参考)
仅供参考)√供应商提供报告
参考文件:
根据镀层的厚度选择弯曲内侧的曲率半径,如下表:结构钢冷轧钢
25 30 33/1 33/2 40/1 40/211/2 2 21/2 21/2 3 3
最终处理—镀层要进行以下一种最终处理工艺:类型描述I电镀,不需要后续处理II需要彩色铬酸盐转化镀层后续处理III需要无色铬酸盐转化镀层后续处理IV需要磷酸盐转化镀层后续处理
抗腐蚀要求类型耗时(h)II 96III 12
4.1.1塑性变形:漆膜表面永久的压痕,但没有内聚破坏。
参考GB/T 9286-1998色漆盒清漆漆膜的化格试验,0级为合格,切割边缘完全光滑,无一格脱落。
参考HG 2-1611-85漆膜耐油性测定法
参考GB/T 1771-2007色漆和清漆耐中性盐雾性能的测定
参考GB/T 1865-1997色漆和清漆人工气候老化和人工辐射暴露(滤过的氙弧辐射)
7.外观判定标准,如下表:
判定标准
外观1.表面不得有任何碰伤、开裂、刮伤等严重表面缺陷。如加工过程中有此缺陷,喷涂前须补腻子处理。表面各边、角、焊接部位毛刺均须去除。
钣金件质量检验报告单

□合格√□轻微(用直角尺会量பைடு நூலகம்不垂直但肉眼看不是很明显)
□严重(肉眼直接就能看出)
焊接
√□合格□基本合格□不合格
装配
√□合格 □轻微(缝隙在可接受范围内)
□严重(装配后缝隙很大,影响产品的使用安全)
其他问题
处理意见
√□接收 □让步接收 □返工 □判退
说明
1、在检验结构中只能填写合格或不合格。
2、■/√□、□代表评审结论标注;■/√□:选择;□:不选择;
钣金件质量检验报告单
钣金件质量检验报告单
项目编号
产品名称
检验项目
检验说明
检验数量
检验结果
备注
外形尺寸
配
件
数量
□一致 □不一致
颜色
√□合格□单体产品颜色不一致□成批产品颜色不一致
镀锌
√□是□否
喷塑
√□合格□轻微(局部突起或脱落)□严重(大范围脱落)
钣金件强度
√□合格□基本合格□不合格
划痕
□合格√□轻微(划痕很小或在不明显处)□严重(划痕很大或在明显部位)
检验人
检验日期
来料检验记录单【范本模板】
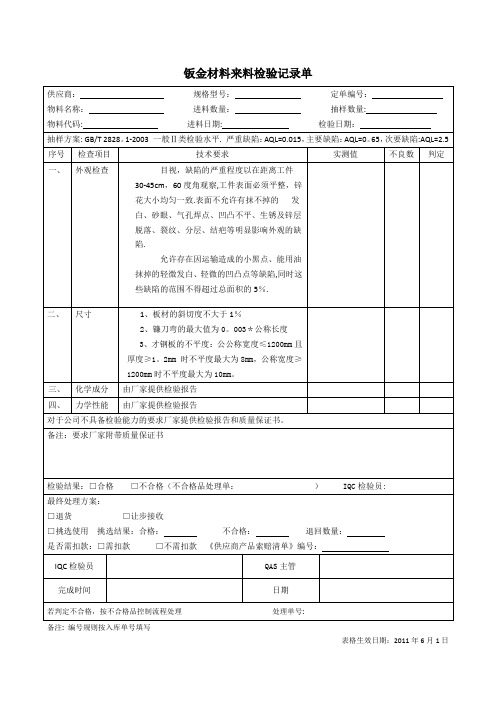
钣金材料来料检验记录单
备注: 编号规则按入库单号填写
表格生效日期:2011年6月1日
铝箔来料检验记录单
备注: 编号规则按入库单号填写
表格生效日期:2011年6月1日
备注: 编号规则按入库单号填写
表格生效日期:2011年6月1日
备注: 编号规则按入库单号填写
表格生效日期:2011年6月1日
备注: 编号规则按入库单号填写
表格生效日期:2011年6月1日
焊条来料检验记录单
备注: 编号规则按入库单号填写
表格生效日期:2011年6月1日
木箱包装来料检验记录单
备注:编号规则按入库单号填写
表格生效日期:2011年6月1日
紧固件来料检验记录单
备注: 编号规则按入库单号填写
表格生效日期:2011年6月1日
塑料件来料检验记录单
备注:编号规则按入库单号填写
表格生效日期:2011年6月1日
钣金喷涂件来料检验记录单
备注:编号规则按入库单号填写
表格生效日期:2011年6月1日。
钣金结构件检验标准

目录1、目的 (1)2、适应范围 (1)3、引用标准 (1)4、原材料检验标准 (1)4.1、金属材料 (1)4.2、塑粉 (1)4.3、通用五金件、紧固件 (1)5、工序质量检验标准 (2)5.1、冲裁检验标准 (2)附:【表一、平面度公差要求】 (2)5.2、折弯检验标准 (2)附:【表二:对角线公差要求】 (2)【表三:角度公差要求】 (3)5.3、钣金加工件检验标准 (3)附:【表四:尺寸公差要求】 (3)5.4、焊接 (3)6、喷涂件检验标准 (4)6.1、外观检验 (4)附:【表五:表面缺陷判定标准】 (5)6.2、涂层厚度检验标准 (6)附:【附表六:喷涂层厚度标准】 (6)6.3、涂层光泽和色泽检测 (6)6.4、涂层附着力检验 (6)6.5、弯板试验法 (7)6.6、涂层抗酒精溶剂性检验 (7)6.7、耐冲击试验 (7)6.8、硬度检验 (7)7、电镀件外观检验标准 (8)公司名称版本状态第版修订次数第次修改文件名称检验标准文件编号页数共 8 页第 1 页钣金结构件检验标准1.目的规范钣金结构件的检验标准,以使各过程的产品质量得以控制。
2.适用范围本标准适用于公司各种钣金结构件的检验,图纸和技术文件并同使用。
当有冲突时,以客户要求和技术标准为准。
3.引用标准本标准的尺寸未注单位皆为mm,未注公差按国家标准IT13级执行GB/T1800.3-1998 极限与配合标准公差和基本偏差数值表GB/T1800.4-1998 极限与配合标准公差等级和孔、轴的极限偏差表GB/1804-2000 一般公差未注公差的线性和角度尺寸的公差未注形位公差按GB/T1184–1996 形状和位置公差未注公差值执行4.原材料检验标准(我司有权对厂家生产用原材料进厂抽检)4.1金属材料4.1.1钣材厚度及质量应符合国标,采用的钣材需出示性能测试报告及厂商证明。
4.1.2材料外观:平整无锈迹,无开裂与变形。
4.1.3尺寸:按图纸或技术要求执行,本司未有的按现行国标执行。
- 1、下载文档前请自行甄别文档内容的完整性,平台不提供额外的编辑、内容补充、找答案等附加服务。
- 2、"仅部分预览"的文档,不可在线预览部分如存在完整性等问题,可反馈申请退款(可完整预览的文档不适用该条件!)。
- 3、如文档侵犯您的权益,请联系客服反馈,我们会尽快为您处理(人工客服工作时间:9:00-18:30)。
项目编号
产品名称
检验项目
检验说明
检验数量
检验结果
备注
外形尺寸
配
件
数量
□一致 □不一致
颜色
√□合格□单体产品颜色不一致□成批产品颜色不一致
镀锌√□是□否喷塑 Nhomakorabea√□合格□轻微(局部突起或脱落)□严重(大范围脱落)
钣金件强度
√□合格□基本合格□不合格
划痕
□合格√□轻微(划痕很小或在不明显处)□严重(划痕很大或在明显部位)
变形
□合格√□轻微(用直角尺会量出不垂直但肉眼看不是很明显)
□严重(肉眼直接就能看出)
焊接
√□合格□基本合格□不合格
装配
√□合格 □轻微(缝隙在可接受范围内)
□严重(装配后缝隙很大,影响产品的使用安全)
其他问题
处理意见
√□接收 □让步接收 □返工 □判退
说明
1、在检验结构中只能填写合格或不合格。
2、■/√□、□代表评审结论标注;■/√□:选择;□:不选择;
检验人
检验日期