热处理工艺参数对热处理变形的影响
钢件热处理变形的原因总结

钢件热处理变形的原因总结一、材料特性:1.材料的塑性变形能力不同:不同类型的钢,具有不同的塑性特性。
一般来说,低碳钢和不锈钢等具有良好的塑性,因此容易出现变形。
而高碳钢、合金钢等则具有较差的塑性,不容易变形。
2.材料的尺寸和形状:钢件的形状和尺寸也会影响热处理的变形程度。
尺寸较大、形状复杂的钢件变形较严重,尤其是在加热和冷却不均匀的情况下。
3.各向异性:钢材具有各向异性,即材料在不同的方向上具有不同的物理性能。
不同方向上的热膨胀系数不同,会导致热处理时钢件的不均匀膨胀和收缩,从而引起变形。
二、加热冷却方式:1.加热方式:钢件的加热方式会影响变形的严重程度。
例如,采用局部加热时,钢件的局部温度差异会导致表面和内部的温度差异,进而引起不均匀的膨胀和收缩。
2.加热速率和温度:加热速率和温度的选择也会对变形产生影响。
加热速率过快会导致钢材的内外温度差异增大,形成应力集中,易引发变形。
加热温度过高或过低也会导致钢件的不均匀热膨胀和变形。
三、操作参数:1.冷却速率:冷却速率的选择会直接影响钢件的变形。
冷却速率过快,会导致表面和内部温度差异增大,进而加剧变形。
冷却速率过慢,会使钢件的内部组织结构不均匀,产生不良的热处理效果。
2.冷却介质:冷却介质的选择也与变形有关。
不同的冷却介质冷却速率不同,从而影响变形的严重程度。
例如,水冷速度较快,容易引发变形;而油冷速度较慢,变形相对较小。
3.外部约束:外部约束也是导致钢件变形的重要因素。
外力的作用会导致钢件产生应力,从而引发变形。
因此,操作过程中要合理设置约束以避免变形的发生。
综上所述,钢件热处理变形是由于材料特性、加热冷却方式和操作参数的影响导致的。
合理选择加热冷却方式和操作参数,并根据钢材的特性进行调整,可以最大限度地减少钢件热处理变形的程度,确保热处理效果的稳定性和一致性。
薄壁件热处理变形
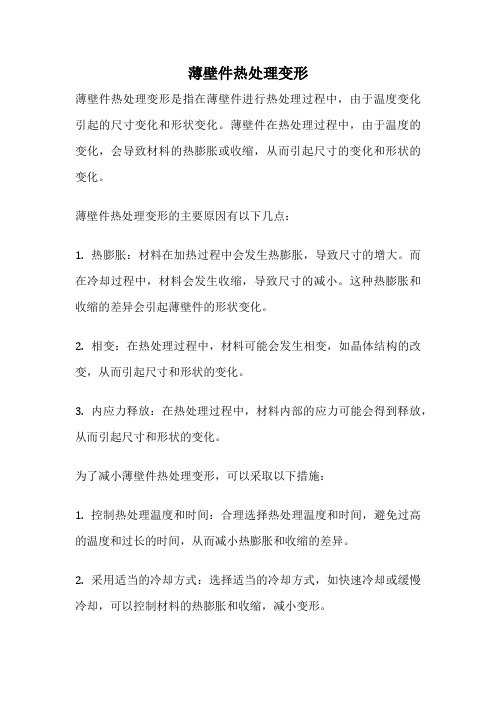
薄壁件热处理变形
薄壁件热处理变形是指在薄壁件进行热处理过程中,由于温度变化引起的尺寸变化和形状变化。
薄壁件在热处理过程中,由于温度的变化,会导致材料的热膨胀或收缩,从而引起尺寸的变化和形状的变化。
薄壁件热处理变形的主要原因有以下几点:
1. 热膨胀:材料在加热过程中会发生热膨胀,导致尺寸的增大。
而在冷却过程中,材料会发生收缩,导致尺寸的减小。
这种热膨胀和收缩的差异会引起薄壁件的形状变化。
2. 相变:在热处理过程中,材料可能会发生相变,如晶体结构的改变,从而引起尺寸和形状的变化。
3. 内应力释放:在热处理过程中,材料内部的应力可能会得到释放,从而引起尺寸和形状的变化。
为了减小薄壁件热处理变形,可以采取以下措施:
1. 控制热处理温度和时间:合理选择热处理温度和时间,避免过高的温度和过长的时间,从而减小热膨胀和收缩的差异。
2. 采用适当的冷却方式:选择适当的冷却方式,如快速冷却或缓慢冷却,可以控制材料的热膨胀和收缩,减小变形。
3. 采用适当的工艺参数:调整热处理的工艺参数,如加热速度、冷却速度等,可以减小薄壁件的变形。
4. 采用适当的夹具和支撑:在热处理过程中,使用适当的夹具和支撑,可以控制薄壁件的形状变化,减小变形。
薄壁件热处理变形是一个复杂的问题,需要综合考虑材料的性质、热处理工艺参数等因素,采取合适的措施来减小变形。
浅析金属材料热处理过程变形及开裂问题
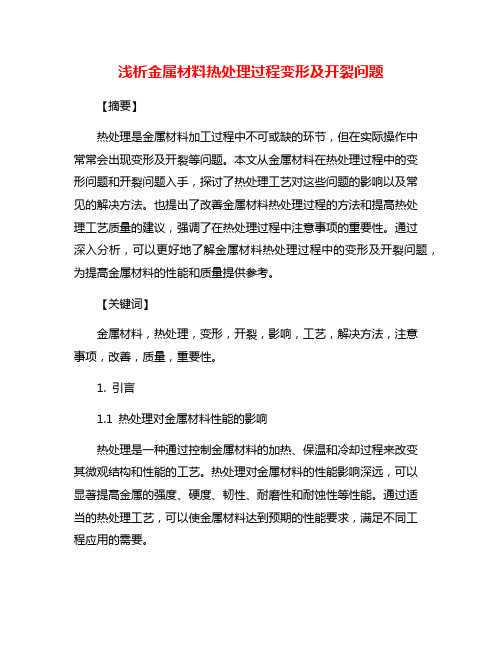
浅析金属材料热处理过程变形及开裂问题【摘要】热处理是金属材料加工过程中不可或缺的环节,但在实际操作中常常会出现变形及开裂等问题。
本文从金属材料在热处理过程中的变形问题和开裂问题入手,探讨了热处理工艺对这些问题的影响以及常见的解决方法。
也提出了改善金属材料热处理过程的方法和提高热处理工艺质量的建议,强调了在热处理过程中注意事项的重要性。
通过深入分析,可以更好地了解金属材料热处理过程中的变形及开裂问题,为提高金属材料的性能和质量提供参考。
【关键词】金属材料,热处理,变形,开裂,影响,工艺,解决方法,注意事项,改善,质量,重要性。
1. 引言1.1 热处理对金属材料性能的影响热处理是一种通过控制金属材料的加热、保温和冷却过程来改变其微观结构和性能的工艺。
热处理对金属材料的性能影响深远,可以显著提高金属的强度、硬度、韧性、耐磨性和耐蚀性等性能。
通过适当的热处理工艺,可以使金属材料达到预期的性能要求,满足不同工程应用的需要。
在热处理过程中,通过控制加热温度、保温时间和冷却速度等参数,可以改变金属的晶粒大小和分布,消除或调整金属内部的残余应力,提高材料的强度和硬度。
热处理还可以消除金属材料中的氧化物、碳化物和其他夹杂物,提高金属的纯度和均匀性。
热处理对金属材料的性能有着显著的影响,可以使材料在各方面性能得到优化和改善。
正确地进行热处理工艺,可以确保金属材料在使用过程中表现出最佳的性能和稳定性。
在实际工程中,热处理是一项非常重要的工艺,需要认真对待和控制。
对于金属材料的性能提升和工程应用具有重要意义。
1.2 变形及开裂问题的定义在金属材料的热处理过程中,变形及开裂问题是不可避免的挑战。
变形是指金属在受热后发生形状或尺寸的改变,造成不同程度的失真。
开裂则是指金属在受热或冷却过程中,出现裂纹或断裂现象。
这些问题可能影响金属材料的性能和使用寿命,甚至会导致制品的废品率增加。
在热处理中,金属材料受到温度、冷却速率、应力等多种因素的影响,容易引起变形及开裂问题。
金属材料热处理变形的影响因素及应对措施
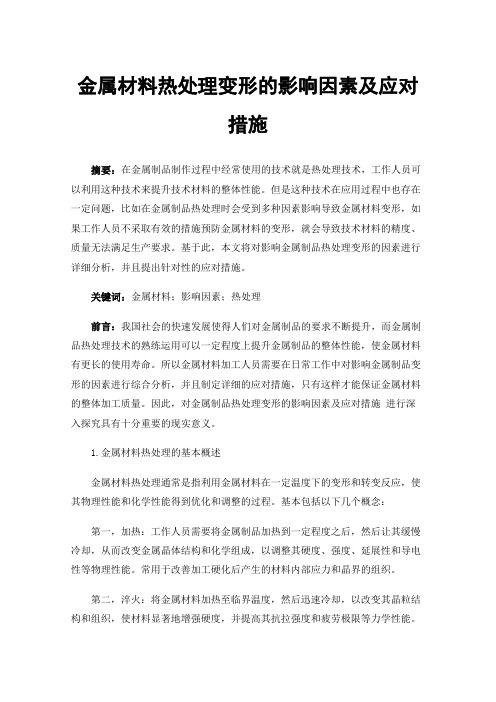
金属材料热处理变形的影响因素及应对措施摘要:在金属制品制作过程中经常使用的技术就是热处理技术,工作人员可以利用这种技术来提升技术材料的整体性能。
但是这种技术在应用过程中也存在一定问题,比如在金属制品热处理时会受到多种因素影响导致金属材料变形,如果工作人员不采取有效的措施预防金属材料的变形,就会导致技术材料的精度、质量无法满足生产要求。
基于此,本文将对影响金属制品热处理变形的因素进行详细分析,并且提出针对性的应对措施。
关键词:金属材料;影响因素;热处理前言:我国社会的快速发展使得人们对金属制品的要求不断提升,而金属制品热处理技术的熟练运用可以一定程度上提升金属制品的整体性能,使金属材料有更长的使用寿命。
所以金属材料加工人员需要在日常工作中对影响金属制品变形的因素进行综合分析,并且制定详细的应对措施,只有这样才能保证金属材料的整体加工质量。
因此,对金属制品热处理变形的影响因素及应对措施进行深入探究具有十分重要的现实意义。
1.金属材料热处理的基本概述金属材料热处理通常是指利用金属材料在一定温度下的变形和转变反应,使其物理性能和化学性能得到优化和调整的过程。
基本包括以下几个概念:第一,加热:工作人员需要将金属制品加热到一定程度之后,然后让其缓慢冷却,从而改变金属晶体结构和化学组成,以调整其硬度、强度、延展性和导电性等物理性能。
常用于改善加工硬化后产生的材料内部应力和晶界的组织。
第二,淬火:将金属材料加热至临界温度,然后迅速冷却,以改变其晶粒结构和组织,使材料显著地增强硬度,并提高其抗拉强度和疲劳极限等力学性能。
第三,固溶处理:这需要工作人员将金属制品的温度保持在一定温度下,使材料中的固溶体或混合物溶解为单一相,然后迅速冷却以避免沉淀形成,从而获得均匀的微观组织结构和化学成分,以增强金属的抗腐蚀性、可加工性和机械性能等。
第四,沉淀强化处理:将金属材料进行固溶处理后,再退火至特定温度下让固溶体于固溶体中析出沉淀相,从而形成分散的硬质相,使材料得到强化。
齿轮加工消除热处理变形的工艺

齿轮是一种常见的机械传动元件,广泛应用于各种机械设备中。
在齿轮加工的过程中,常常会遇到热处理变形的问题,这会影响齿轮的精度和使用寿命。
如何在齿轮加工过程中消除热处理变形成为了重要的技术课题。
一、热处理工艺1. 热处理工艺的种类热处理工艺包括退火、正火、淬火和回火等。
这些工艺对齿轮的硬度、强度和耐磨性都会有不同程度的影响。
2. 热处理变形的原因在热处理过程中,齿轮会受到热膨胀和热应力的影响,从而产生变形。
特别是在淬火过程中,由于齿轮的不均匀冷却会导致变形更为严重。
二、消除热处理变形的工艺1. 预留余量在设计齿轮的尺寸时,可以适当增加一些余量,以便在热处理后进行修磨,从而达到消除变形的效果。
2. 低温回火在淬火后,将齿轮进行低温回火处理,可以有效减少热处理变形的产生。
低温回火可以消除淬火后的残余应力,使齿轮保持较好的形状精度。
3. 调整热处理工艺参数通过调整热处理工艺的温度、时间和速度等参数,可以减小热处理变形的影响。
选择合适的热处理工艺参数对消除变形至关重要。
4. 多次热处理在齿轮加工中,可以采用多次热处理的方法,即在不同阶段对齿轮进行热处理,这样可以减少每次热处理产生的变形量,使齿轮在每次热处理后都能保持尽可能好的形状。
5. 后加工在热处理后进行修磨和整形,可以消除一部分热处理变形,提高齿轮的精度和表面质量。
三、工艺控制1. 设计优化在齿轮的设计阶段,可以通过优化结构和材料选用等,减少热处理变形的产生。
合理的设计能够在一定程度上消除热处理变形。
2. 热处理设备的改进在热处理设备上进行改进,比如采用先进的淬火方式、控制工艺参数等,可以减小热处理变形的产生。
3. 质量控制加强对齿轮加工过程中的质量控制,确保每一道工序都符合要求,这也是避免热处理变形的重要手段。
消除热处理变形的工艺在齿轮加工中至关重要。
通过合理的热处理工艺和工艺控制,可以有效减少热处理变形的影响,提高齿轮的精度和使用寿命。
随着技术的发展,相信在未来会有更多的创新工艺出现,为消除热处理变形提供更多的解决方案。
热处理方法对金属材料的变形性能的影响

热处理方法对金属材料的变形性能的影响热处理是一种通过控制金属材料的加热和冷却过程,改变其晶体结构和组织状态,从而达到改善材料性能的目的的工艺。
在工业生产中,热处理广泛应用于金属材料的加工过程中,它对金属材料的变形性能产生重要影响。
本文将从几个方面探讨热处理方法对金属材料的变形性能的影响。
第一,热处理对金属材料的晶体结构和组织状态的改变对其变形性能产生影响。
金属材料的晶体结构和组织状态直接影响其力学性能,进而影响其变形性能。
通过适当的热处理方法,如退火、正火、淬火等,可以使金属材料的晶体结构和组织状态发生改变,从而改善其变形性能。
第二,热处理可以提高金属材料的硬度和强度,从而改善其变形性能。
通过热处理方法,可以使金属材料中的晶界和位错得到重新排列,从而提高材料的位错密度和晶界能量。
这使得金属材料的塑性减小,硬度和强度增加,从而提高了其变形性能。
第三,热处理可以改变金属材料的内应力状态,从而影响其变形性能。
金属材料在加工过程中会产生内应力,影响其变形行为。
通过热处理方法,可以减轻或消除金属材料中的内应力,提高其变形性能。
例如,通过淬火等方法,可以使金属材料快速冷却,产生较大的残余应力,进而增加材料的抗变形能力。
第四,热处理可以改善金属材料的韧性和延展性,从而影响其变形性能。
金属材料的韧性和延展性是指材料在受力作用下发生塑性变形和断裂的能力。
通过适当的热处理方法,可以改变金属材料中的晶界和位错结构,增加材料的韧性和延展性,从而提高其变形性能。
综上所述,热处理方法对金属材料的变形性能产生重要影响。
通过调整金属材料的晶体结构和组织状态,提高其硬度和强度,改变其内应力状态,改善其韧性和延展性,可以有效地改善金属材料的变形性能。
因此,在金属材料的加工过程中,合理选择适当的热处理方法尤为重要,以达到最佳的变形性能。
热处理变形基础知识
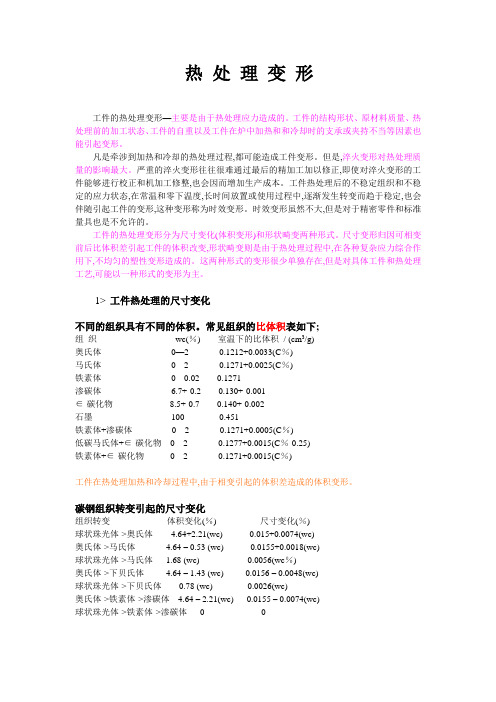
热处理变形工件的热处理变形—主要是由于热处理应力造成的。
工件的结构形状、原材料质量、热处理前的加工状态、工件的自重以及工件在炉中加热和和冷却时的支承或夹持不当等因素也能引起变形。
凡是牵涉到加热和冷却的热处理过程,都可能造成工件变形。
但是,淬火变形对热处理质量的影响最大。
严重的淬火变形往往很难通过最后的精加工加以修正,即使对淬火变形的工件能够进行校正和机加工修整,也会因而增加生产成本。
工件热处理后的不稳定组织和不稳定的应力状态,在常温和零下温度,长时间放置或使用过程中,逐渐发生转变而趋于稳定,也会伴随引起工件的变形,这种变形称为时效变形。
时效变形虽然不大,但是对于精密零件和标准量具也是不允许的。
工件的热处理变形分为尺寸变化(体积变形)和形状畸变两种形式。
尺寸变形归因可相变前后比体积差引起工件的体积改变,形状畸变则是由于热处理过程中,在各种复杂应力综合作用下,不均匀的塑性变形造成的。
这两种形式的变形很少单独存在,但是对具体工件和热处理工艺,可能以一种形式的变形为主。
1>工件热处理的尺寸变化不同的组织具有不同的体积。
常见组织的比体积表如下;组织wc(%) 室温下的比体积/ (cm3/g)奥氏体0—2 0.1212+0.0033(C%)马氏体0---2 0.1271+0.0025(C%)铁素体0---0.02 0.1271渗碳体 6.7+-0.2 0.130+-0.001∈-碳化物8.5+-0.7 0.140+-0.002石墨100 0.451铁素体+渗碳体0---2 0.1271+0.0005(C%)低碳马氏体+∈-碳化物0---2 0.1277+0.0015(C%-0.25)铁素体+∈-碳化物0---2 0.1271+0.0015(C%)工件在热处理加热和冷却过程中,由于相变引起的体积差造成的体积变形。
碳钢组织转变引起的尺寸变化组织转变体积变化(%) 尺寸变化(%)球状珠光体->奥氏体- 4.64+2.21(wc) - 0.015+0.0074(wc)奥氏体->马氏体 4.64 – 0.53 (wc) - 0.0155+0.0018(wc)球状珠光体->马氏体 1.68 (wc) 0.0056(wc%)奥氏体->下贝氏体 4.64 – 1.43 (wc) 0.0156 – 0.0048(wc)球状珠光体->下贝氏体0.78 (wc) 0.0026(wc)奥氏体->铁素体->渗碳体 4.64 – 2.21(wc) 0.0155 – 0.0074(wc)球状珠光体->铁素体->渗碳体0 02>工件热处理的形状畸变工件热处理的形状畸变有多种原因。
热处理变形的影响因素
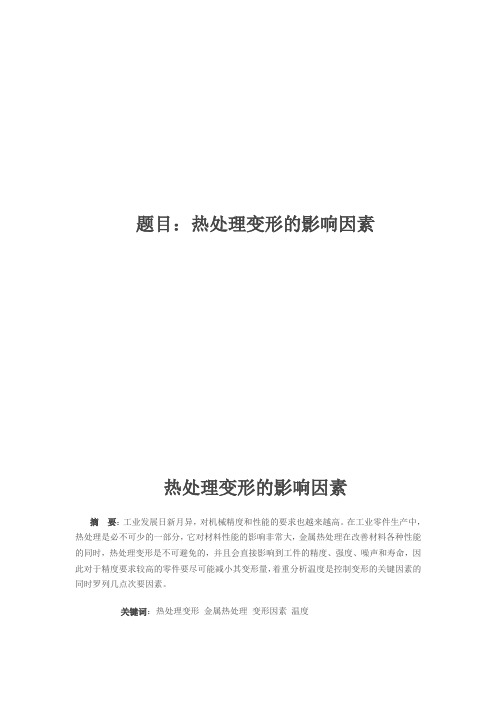
题目:热处理变形的影响因素热处理变形的影响因素摘要:工业发展日新月异,对机械精度和性能的要求也越来越高。
在工业零件生产中,热处理是必不可少的一部分,它对材料性能的影响非常大,金属热处理在改善材料各种性能的同时,热处理变形是不可避免的,并且会直接影响到工件的精度、强度、噪声和寿命,因此对于精度要求较高的零件要尽可能减小其变形量,着重分析温度是控制变形的关键因素的同时罗列几点次要因素。
关键词:热处理变形金属热处理变形因素温度一、引言什么是金属材料的热处理?热处理有什么弊端?(变形等)金属材料的热处理是将固态金属或合金,采用适当的方式进行加热、保温和冷却,有时并兼之以化学作用和机械作用,使金属合金内部的组织和结构发生改变,从而获得改善材料性能的工艺。
热处理工艺是使各种金属材料获得优良性能的重要手段。
很多实际应用中合理选用材料和各种成形工艺并不能满足金属工件所需要的力学性能、物理性能和化学性能,这时热处理工艺是必不可少的。
但是热处理工艺除了具有积极的作用之外,在处理过程中也不可避免地会产生或多或少的变形,而这又是机械加工中必须避免的,两者之间是共存而又需要避免的关系,只能采用相应的方法尽量把变形量控制在尽量小的范围内。
而要减小热处理的变形,我们就需要了解影响热处理变形的因素。
二、温度是变形的关键因素工业生产中实际应用的热处理工艺形式非常多,如退火,正火,回火,淬火等,但是它们的基本过程都是热作用过程,都是由加热、保温和冷却三个阶段组成的。
整个工艺过程都可以用加热速度、加热温度、保温时间、冷却速度以及热处理周期等几个参数来描述。
在热处理工艺中,要用到各种加热炉,金属热处理便在这些加热炉中进行(如基本热处理中的退火、淬火、回火、化学热处理的渗碳、渗氨、渗铝、渗铬或去氢、去氧等等)。
因此,加热炉内的温度测量就成为热处理的重要工艺参数测量。
每一种热处理工艺规范中,温度是很重要的内容。
如果温度测量不准确,热处理工艺规范就得不到正确的执行,以至造成产品质量下降甚至报废。
热处理变形原因与变形控制技术措施论文
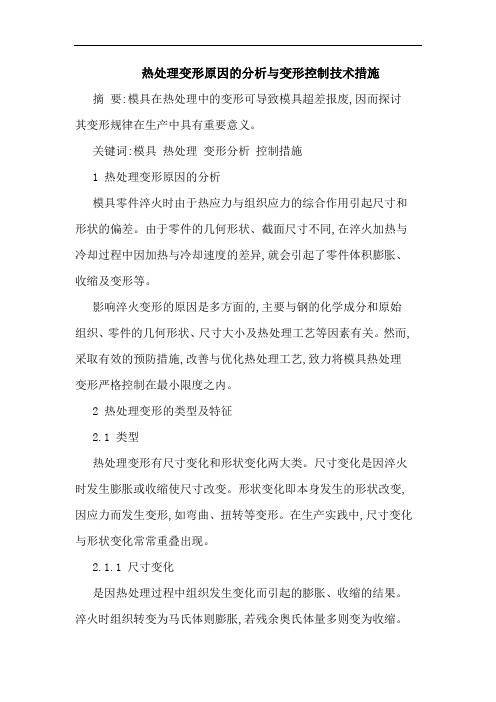
热处理变形原因的分析与变形控制技术措施摘要:模具在热处理中的变形可导致模具超差报废,因而探讨其变形规律在生产中具有重要意义。
关键词:模具热处理变形分析控制措施1 热处理变形原因的分析模具零件淬火时由于热应力与组织应力的综合作用引起尺寸和形状的偏差。
由于零件的几何形状、截面尺寸不同,在淬火加热与冷却过程中因加热与冷却速度的差异,就会引起了零件体积膨胀、收缩及变形等。
影响淬火变形的原因是多方面的,主要与钢的化学成分和原始组织、零件的几何形状、尺寸大小及热处理工艺等因素有关。
然而,采取有效的预防措施,改善与优化热处理工艺,致力将模具热处理变形严格控制在最小限度之内。
2 热处理变形的类型及特征2.1 类型热处理变形有尺寸变化和形状变化两大类。
尺寸变化是因淬火时发生膨胀或收缩使尺寸改变。
形状变化即本身发生的形状改变,因应力而发生变形,如弯曲、扭转等变形。
在生产实践中,尺寸变化与形状变化常常重叠出现。
2.1.1 尺寸变化是因热处理过程中组织发生变化而引起的膨胀、收缩的结果。
淬火时组织转变为马氏体则膨胀,若残余奥氏体量多则变为收缩。
冷处理时因残余奥氏体转变成马氏体又引起膨胀。
马氏体引起的体积膨胀随钢中碳含量增加而变大;其尺寸变化量亦随着增大。
淬火钢回火时马氏体发生分解,而引起收缩;收缩量随马氏体中c%的增多而增大,但若以淬火前的状态为基准,淬火回火后尺寸变化的总合,其结果仍是膨胀。
2.1.2 形状变化是因淬火钢内部的应力及加于外部的力量而引起的。
内部应力是因温度分布不均或因组织转变而引起的。
而外部的力主要是因自重而导致“下垂”。
加热温度越高、保温时间越长,这种因本身重量而引起的“下垂”变形更易发生。
工件加热时,因机械加工或常温加工所产生的残余应力,将发生形状变化。
即使是均匀加热,因钢的屈服点随温度上升而降低之故,此时只要有少许应力存在即发生变形。
因残余应力于外部周围较强。
当温度上升自外部进行时,变形于外部周围特别显著。
40cr调质后加工变形的问题
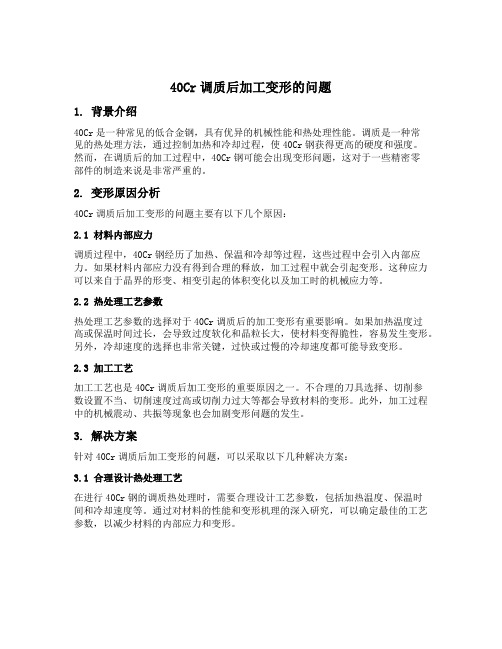
40Cr调质后加工变形的问题1. 背景介绍40Cr是一种常见的低合金钢,具有优异的机械性能和热处理性能。
调质是一种常见的热处理方法,通过控制加热和冷却过程,使40Cr钢获得更高的硬度和强度。
然而,在调质后的加工过程中,40Cr钢可能会出现变形问题,这对于一些精密零部件的制造来说是非常严重的。
2. 变形原因分析40Cr调质后加工变形的问题主要有以下几个原因:2.1 材料内部应力调质过程中,40Cr钢经历了加热、保温和冷却等过程,这些过程中会引入内部应力。
如果材料内部应力没有得到合理的释放,加工过程中就会引起变形。
这种应力可以来自于晶界的形变、相变引起的体积变化以及加工时的机械应力等。
2.2 热处理工艺参数热处理工艺参数的选择对于40Cr调质后的加工变形有重要影响。
如果加热温度过高或保温时间过长,会导致过度软化和晶粒长大,使材料变得脆性,容易发生变形。
另外,冷却速度的选择也非常关键,过快或过慢的冷却速度都可能导致变形。
2.3 加工工艺加工工艺也是40Cr调质后加工变形的重要原因之一。
不合理的刀具选择、切削参数设置不当、切削速度过高或切削力过大等都会导致材料的变形。
此外,加工过程中的机械震动、共振等现象也会加剧变形问题的发生。
3. 解决方案针对40Cr调质后加工变形的问题,可以采取以下几种解决方案:3.1 合理设计热处理工艺在进行40Cr钢的调质热处理时,需要合理设计工艺参数,包括加热温度、保温时间和冷却速度等。
通过对材料的性能和变形机理的深入研究,可以确定最佳的工艺参数,以减少材料的内部应力和变形。
3.2 优化加工工艺在加工过程中,需要选择合适的刀具和切削参数,以减少切削力和切削温度。
合理的刀具几何形状和切削速度可以降低材料的变形风险。
此外,加工过程中要注意减少机械震动和共振现象的发生。
3.3 应力释放热处理对于已经发生变形的40Cr钢材料,可以进行应力释放热处理。
该热处理过程可以通过加热和保温来减少材料的内部应力,并使其趋于平衡。
金属材料热处理变形的影响因素和策略研究
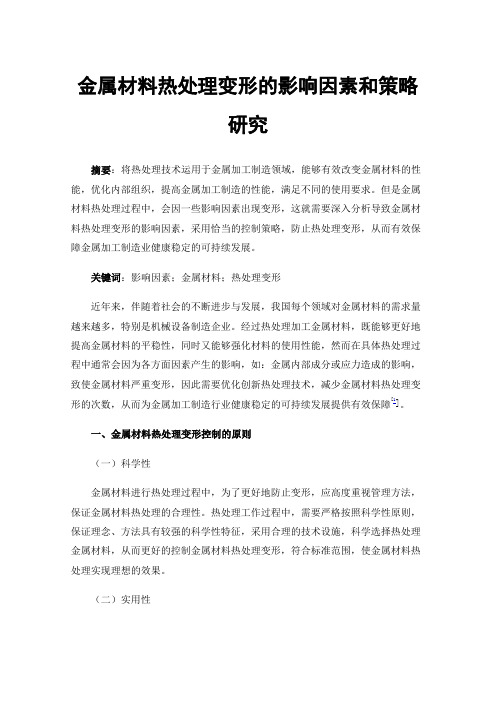
金属材料热处理变形的影响因素和策略研究摘要:将热处理技术运用于金属加工制造领域,能够有效改变金属材料的性能,优化内部组织,提高金属加工制造的性能,满足不同的使用要求。
但是金属材料热处理过程中,会因一些影响因素出现变形,这就需要深入分析导致金属材料热处理变形的影响因素,采用恰当的控制策略,防止热处理变形,从而有效保障金属加工制造业健康稳定的可持续发展。
关键词:影响因素;金属材料;热处理变形近年来,伴随着社会的不断进步与发展,我国每个领域对金属材料的需求量越来越多,特别是机械设备制造企业。
经过热处理加工金属材料,既能够更好地提高金属材料的平稳性,同时又能够强化材料的使用性能,然而在具体热处理过程中通常会因为各方面因素产生的影响,如:金属内部成分或应力造成的影响,致使金属材料严重变形,因此需要优化创新热处理技术,减少金属材料热处理变形的次数,从而为金属加工制造行业健康稳定的可持续发展提供有效保障[1]。
一、金属材料热处理变形控制的原则(一)科学性金属材料进行热处理过程中,为了更好地防止变形,应高度重视管理方法,保证金属材料热处理的合理性。
热处理工作过程中,需要严格按照科学性原则,保证理念、方法具有较强的科学性特征,采用合理的技术设施,科学选择热处理金属材料,从而更好的控制金属材料热处理变形,符合标准范围,使金属材料热处理实现理想的效果。
(二)实用性金属材料不是一种用之不竭的资源,这就需要按照实用性的基本原则使用金属材料,尽量防止金属材料出现浪费的情况。
金属材料热处理过程中,需要有效控制金属材料的变形,实现资源的最大化分配,减少资源,爱护环境,推动社会的长远发展。
另外,按照实用性原则,合理使用金属材料,加强对金属材料质量的控制,全面提升金属材料的使用率。
(三)易操作金属材料进行热处理过程中还需要科学选择操作场地条件,使变形控制精细化和科学化处理的严格要求得到满足。
与此同时,还需要提升变形控制方案的容错率,更好的控制环境因素带来的不良影响。
热处理变形的影响因素

1 引言
金 属 的材 料 热 处理 是 将 固态 的金 属 或者 合 金 , 通 过 高 温加 热 的 方式 , 直接冷却 、 保温冷却 、 突然冷却 的方式将金属 内部 的组织 和结 构 进行 改变 , 在 此 过 程 中为 了 能够 获得 更 好 的结 果 , 经 常 加 入 化 学 材料或者机械工艺材料。热处理工业是获得金属合金的主要方式 , 也是获得大量可靠 、 安全材料性能的主要方式 。在当前不少金属材 料中, 热处理的合金经常能够有着抗高温、 抗变形 、 抗腐蚀等重要 的 作用。 但 是 在 现实 中的 热 处理 工 艺 经常 会 产 生不 少 问题 , 所 加 入 的材 料 和 化 学催 化 剂 作用 不完 全 、 物 理 作用 下 , 金 属 已 经发 生变 形 或 者 内部 发 生 断 裂 等 情 况 ,这 些 都 是 在 机 械 加 工 过 程 中应 当避 免发 生 的 。而 这些 情 况 又 都是 不 可 避免 发 生 。这两 种 相 互作 用 的结 果 将 直 接导致所 出产品的质量和性能 。 如果我们能够在产品的保质温度下 进 行产 品锻 炼 或者 产 品 融合 , 就可 以保 证 在产 品变 形 之前 获 得 较 好 的产 品性 能 和 产 品质 量 。 2 热 量是 工 件 变形 的关 键 工业 中生 产 的产 品 所处 理 的热 工 艺非 常 的多 , 通 过 加热 、 正火 、 回火 、 淬火、 冷却 , 再加热等方式 , 他们之 间互相 的关键其实在于热 作用的过程 , 主要都是通过加热 、 保温 、 冷却三个方式进行。而整个 工作处理的过程中往往可以通过加热速度 、 加热温度 、 保温速度、 保 温 时间、 冷却 速度 、 冷 却 时 间 以及 热 处理 的周 期 等 几 种 重 要 的 工 作 参 数 进 行测 量 和 计算 。 在热处理工艺过程 中,要将材料进入各种加热炉进行加热 , 金 属 热 处 理 的整 个 过程 都 是 会 在这 些 加 热 炉 中进 行 的 。 ( 如基 本 热 处 理 中 的退 火 、 淬火 、 回火 、 化 学热 处 理 的渗 碳 、 渗氨 、 渗铝 、 渗 铬 或 去 氢、 去氧 等 等 ) 。 为 了保 证 金 属 的整 个 加 热效 果 , 测 量 炉 内温度 和炉 内降 温速 度 成 为 了热处 理 的重 要 工艺 参 数 。每 一 种 热 处理 工 艺 规 范 中 , 温度 是 很 重 要 的 内 容 。如果 温 度 测 量不 准 确 , 热 处 理 工艺 规 范 就 得不 到 正 确 的执 行 , 以 至 造成 产 品 质量 下 降 甚 至报 废 。温度 的测 量 与 控制 是 热 处 理 工 艺 的关 键 , 也 是 影 响变 形 的关 键 因素 。 ( 1 ) 工艺温度降低后工件的高温强度损失相对减 少 , 塑性抗力 增强 。 这样工件 的抗应力变形 、 抗淬火变形 、 抗高温蠕变的综合能力 增强 , 变 形 就 会 减少 。 ( 2 ) 工 艺 温度 降 低后 工件 加 热 、 冷 却 的 温度 区间 减少 , 由此 而 引 起 的各 部 位 温度 不 一致 性 也 会 降低 , 由此 而 导 致 的 热应 力 和 组织 应 力也相对减少 , 这样 变 形 就会 减 少 。 ( 3 ) 如 果 工艺 温 度 降 低 、 且 热处 理 工 艺 时 间缩 短 , 则 工 件 的 高温 蠕 变 时 间减 少 , 变形 也 会 减少 。 3变形 的其 它 影 响 因素及 减 小 措施 3 . 1 安排加热的工艺排序和冷却 的方式 不 同的 零件 要 求 对 于其 内部 的结 构 式 不 同 的 , 因此 要 进 行热 处 理必 须 要 对 零件 的 内部结 构 有 着 充分 的 了解 和认 识 , 在 进 行 热处 理 前对 于加 工 材料 的分 析 和计 算 , 并 通 过 实验 结 果 证 明加 工 的温 度 和 冷 却 的方 式 符合 当前 零件 的需 求 。 在 加 工 工艺 工 程 中 , 通过 预 定 的 热 处理 尽 可 能 减少 变 形 的发 生 和, 最终 达 到 变 形量 最 小 的 目的 。 不 过如 此 进行 加 工 , 会 导致 加 工成 本过高 , 加工工艺复杂 , 且浪 费时间 , 因此 在 一 般 的 加 工 工 艺 过 程 中, 除非 有 特 别 要求 进 行 加 工 的零 件 , 才会 采 用 此种 方 式进 行 。 3 . 2 加 工 前 预热 处 理 由于 热 处理 属 于 直接 对 产 品 进行 加 热 , 正 火 的 温度 过 高 、 混晶 、 大量索 氏体或魏 氏组织都很容易导致温度过大 , 零件内部孑 L 长大增 加 空 间 ,如 果直 接 加 入或 者 快 速 加热 很 容 易 当整 个 零 件 直接 断 裂 , 因此加热过程中 , 应 当通过控制温度正火或者等温退火 、 等温加热 的 方式 来 处 理锻 件 。金属 的正 火 、 退 火 工艺 已经 通 过加 热 的材料 和
钢的热处理淬火时工件的变形规律

淬火时,工件发生的变形有两类,一是翘曲变形,一是体积变形。
翘曲变形包括形状变形和扭曲变形。
扭曲变形主要是加热时工件在炉内放置不当,或者淬火前经变形校正后没有定型处理,或者是由于工件冷却时工件各部位冷却不均匀所造成,这种变形可以针对具体情况分析解决。
1、引起各种变形的原因及其变化规律(1)由于淬火前后组织变化而引起的体积变形工件在淬火前的组织状态一般为珠光体型,即铁素体和渗碳体的混合组织,而淬火后为马氏体型组织。
由于这些组织体积不同,淬火前后将引起体积变化,从而产生变形。
这种变形只按比例使工件胀缩,但不改变形状。
淬火前后由此而引起的体积变化,可以计算求得。
(2)热应力引起的形状变形热应力引起的变形发生在钢件屈服强度较低,塑性较高,而表面冷却快,工件内外温差最大的高温区。
此时瞬时热应力是表面张应力,心部压应力,心部温度高,屈服强度比表面低很多,易于变形。
因此表现为在多向压应力作用下的变形,即立方体向呈球形方向变化。
由此导致尺寸较大的一方缩小,而尺寸较小的一方则胀大。
(3)组织应力引起的形状变形组织应力引起的变形也产生在早期组织应力最大时刻。
此时截面温度较大,心部温度较高,仍处于奥氏体状态,塑性较好,屈服强度较低。
瞬时组织应力是表面压应力,心部拉应力;其变形表现为心部在多向拉应力作用下的拉长。
由此导致的结果为在组织应力作用下,工件中尺寸较大的一方伸长,而尺寸较小的一方缩短。
2、影响淬火变形的因素(1)影响体积变形和形状变形的因素。
凡是影响淬火前后组织比体积变化的因素均影响体积变形。
(2)其他影响淬火变形的因素。
影响淬火变形的因素有两种,一种是夹杂物和带状组织对淬火变形的影响。
(3)淬火前残存应力及加热冷却不均匀对变形的影响。
淬火前工件内残余应力没有消除,淬火加热装炉不当,淬火冷却不当均引起工件的扭曲变形。
热处理变形的因素
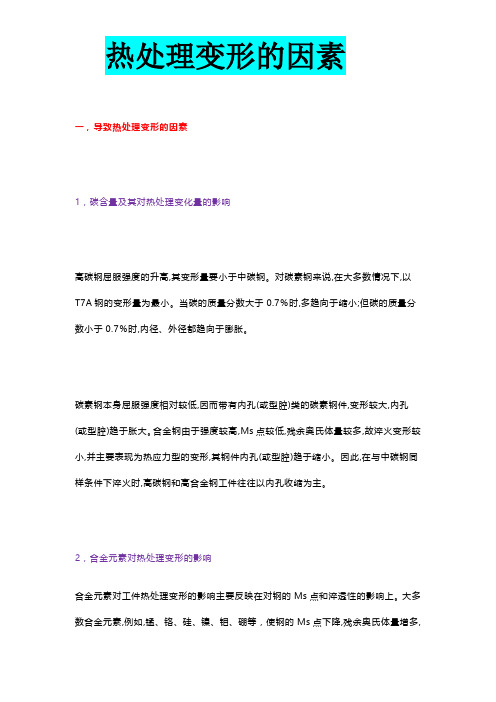
一,导致热处理变形的因素1,碳含量及其对热处理变化量的影响高碳钢屈服强度的升高,其变形量要小于中碳钢。
对碳素钢来说,在大多数情况下,以T7A钢的变形量为最小。
当碳的质量分数大于0.7%时,多趋向于缩小;但碳的质量分数小于0.7%时,内径、外径都趋向于膨胀。
碳素钢本身屈服强度相对较低,因而带有内孔(或型腔)类的碳素钢件,变形较大,内孔(或型腔)趋于胀大。
合金钢由于强度较高,Ms点较低,残余奥氏体量较多,故淬火变形较小,并主要表现为热应力型的变形,其钢件内孔(或型腔)趋于缩小。
因此,在与中碳钢同样条件下淬火时,高碳钢和高合金钢工件往往以内孔收缩为主。
2,合金元素对热处理变形的影响合金元素对工件热处理变形的影响主要反映在对钢的Ms点和淬透性的影响上。
大多数合金元素,例如,锰、铬、硅、镍、钼、硼等,使钢的Ms点下降,残余奥氏体量增多,减小了钢淬火时的比体积变化和组织应力,因此,减小了工件的淬火变形。
合金元素显著提高钢的淬透性,从而增大了钢的体积变形和组织应力,导致工件热处理变形倾向的增大。
此外,由于合金元素提高钢的淬透性,使临界淬火冷却速度降低,实际生产中,可以采用缓和的淬火介质淬火,从而降低了热应力,减小了工件的热处理变形。
硅对Ms点的影响不大,只对试样变形起缩小作用;钨和钒对淬透性和Ms点影响也不大,对工件热处理变形影响较小。
故工业上所谓微变形钢,均含有较多量的硅、钨、钒等合金元素。
3,原始组织和应力状态对热处理变形的影响工件淬火前的原始组织,例如,碳化物的形态、大小、数量及分布,合金元素的偏析,锻造和轧制形成的纤维方向都对工件的热处理变形有一定影响。
球状珠光体比片状珠光体比体积大,强度高,所以经过预先球化处理的工件淬火变形相对要小。
对于一些高碳合金工具钢,例如,9Mn2V、CrWMn和GCr15钢的球化等级对其热处理变形开裂和淬火后变形的校正有很大影响,通常以2.5-5级球化组织为宜。
调质处理不仅使工件变形量的绝对值减小,并使工件的淬火变形更有规律,从而有利于对变形的控制。
各种热处理工艺造成变形的原因总结

各种热处理工艺造成变形的原因总结引言:热处理工艺是一种常见的金属加工方法,它通过对金属材料进行加热和冷却来改变其结构和性能。
然而,热处理过程中往往会导致材料发生变形,这对于一些精密零件的加工和制造带来一定的困扰。
本文将从各种热处理工艺的角度,总结造成变形的原因,并探讨相应的解决方法。
一、淬火过程中的变形原因淬火是一种通过快速冷却来使金属材料达到高强度和硬度的热处理工艺。
然而,淬火过程中常常会出现变形现象。
造成淬火变形的主要原因有以下几点:1. 冷却速度不均匀:淬火过程中,材料表面和内部的冷却速度不一致,导致应力不均匀分布,从而引起变形。
2. 材料内部组织不均匀:金属材料内部的组织不均匀,如晶粒尺寸、相含量等差异,会导致淬火时的收缩和变形不一致。
3. 冷却介质选择不当:不同的冷却介质对材料的冷却速度有不同的影响,选择不当可能导致应力集中和变形。
解决方法:针对淬火过程中的变形问题,可以采取以下措施:1. 控制冷却速度:通过优化冷却介质的选择和控制冷却速度,使材料表面和内部的冷却速度尽可能一致,减少应力的不均匀分布。
2. 优化材料组织:通过调整材料的化学成分和热处理工艺,使材料内部的组织更加均匀,减少淬火时的收缩和变形差异。
3. 采用适当的淬火工艺:根据材料的特性和要求,选择适当的淬火工艺,控制冷却速度和温度,减少变形的发生。
二、退火过程中的变形原因退火是一种通过加热和缓慢冷却来改善材料的性能和结构的热处理工艺。
然而,退火过程中同样存在变形的问题。
造成退火变形的主要原因有以下几点:1. 温度不均匀:退火过程中,材料的温度分布不均匀,导致应力分布不均匀,从而引起变形。
2. 冷却速度过快:退火结束后,如果冷却速度过快,会导致材料内部的残余应力无法得到充分释放,从而引起变形。
3. 材料内部缺陷:金属材料内部存在各种缺陷,如气孔、夹杂物等,这些缺陷在退火过程中会扩散和移动,导致变形的发生。
解决方法:针对退火过程中的变形问题,可以采取以下措施:1. 控制温度均匀性:通过合理设计加热设备和工艺参数,确保材料的温度分布均匀,减少应力的不均匀分布。
热处理对金属材料的残余应力和变形行为的影响分析
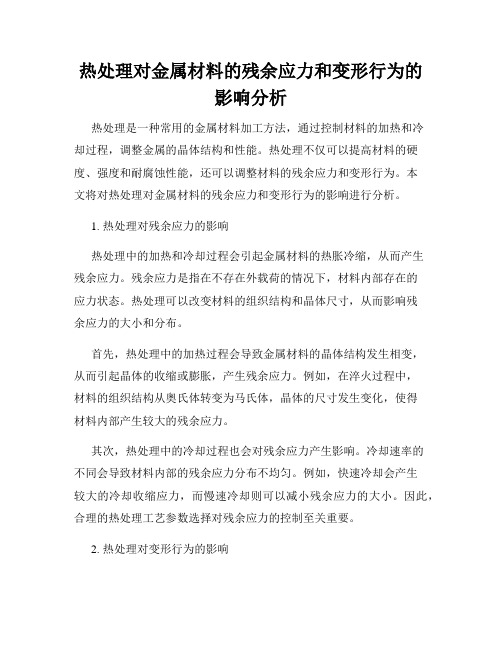
热处理对金属材料的残余应力和变形行为的影响分析热处理是一种常用的金属材料加工方法,通过控制材料的加热和冷却过程,调整金属的晶体结构和性能。
热处理不仅可以提高材料的硬度、强度和耐腐蚀性能,还可以调整材料的残余应力和变形行为。
本文将对热处理对金属材料的残余应力和变形行为的影响进行分析。
1. 热处理对残余应力的影响热处理中的加热和冷却过程会引起金属材料的热胀冷缩,从而产生残余应力。
残余应力是指在不存在外载荷的情况下,材料内部存在的应力状态。
热处理可以改变材料的组织结构和晶体尺寸,从而影响残余应力的大小和分布。
首先,热处理中的加热过程会导致金属材料的晶体结构发生相变,从而引起晶体的收缩或膨胀,产生残余应力。
例如,在淬火过程中,材料的组织结构从奥氏体转变为马氏体,晶体的尺寸发生变化,使得材料内部产生较大的残余应力。
其次,热处理中的冷却过程也会对残余应力产生影响。
冷却速率的不同会导致材料内部的残余应力分布不均匀。
例如,快速冷却会产生较大的冷却收缩应力,而慢速冷却则可以减小残余应力的大小。
因此,合理的热处理工艺参数选择对残余应力的控制至关重要。
2. 热处理对变形行为的影响除了对残余应力的影响外,热处理还可以调整金属材料的变形行为,包括塑性变形和弹性变形。
首先,热处理可以提高金属材料的塑性变形能力。
在热处理过程中,晶体结构的调整可以使材料的晶界和位错运动更加容易,从而提高材料的塑性变形能力。
例如,在退火处理中,材料的晶粒得到了细化,晶界的移动路径减小,增加了材料在塑性变形过程中的滞后与吸收应变的能力。
其次,热处理还可以调整材料的弹性变形行为。
材料经过热处理后,其弹性模量、屈服强度等力学性能会发生变化。
例如,时效处理可以提高合金材料的强度和硬度,使材料具有较高的弹性变形能力。
另外,热处理还可以改善金属材料的应力松弛行为。
材料在热处理后,残余应力会通过应力松弛的方式逐渐减小。
应力松弛是指材料在存在残余应力的情况下,由于位错在晶体中的滑动和扩散,使得部分应力得以释放。
热处理变形的因素

一,导致热处理变形的因素1, 碳含呈及其对热处理变化呈的影响高碳钢屈服强度的升高,其变形呈要小于中碳钢。
对碳素钢来说,在大多数情况下,以T7A钢的变形呈为最小。
当碳的质呈分数大于0.7%时,多趋向于缩小;但碳的质呈分数小于0.7%时,内径、外径都趋向于膨胀。
碳素钢本身屈服强度相对较低,因而带有内孔(或型腔)类的碳素钢件,变形较大,内孔(或型腔)趋于胀大。
合金钢由于强度较高,Ms点较低,残余奥氏体呈较多,故淬火变形较小,并主要表现为热应力型的变形,其钢件内孔(或型腔)趋于缩小。
因此,在与中碳钢同样条件下淬火时,高碳钢和高合金钢工件往往以内孔收缩为主。
2, 合金元素对热处理变形的影响合金元素对工件热处理变形的影响主要反映在对钢的Ms点和淬透性的影响上。
大多数合金元素,例如,锚、错、硅、镇、铝、硼等,使钢的Ms点下降,残余奥氏体星增多, 减小了钢淬火时的比体积变化和组织应力,因此,减小了工件的淬火变形。
合金元素显著提高钢的淬透性,从而增大了钢的体积变形和组织应力,导致工件热处理变形倾向的增大。
此外,由于合金元素提高钢的淬透性,使临界淬火冷却速度降低,实际生产中,可以采用缓和的淬火介质淬火,从而降低了热应力,减小了工件的热处理变形。
硅对Ms点的影响不大,只对试样变形起缩小作用;铸和机对淬透性和Ms点影响也不大,对工件热处理变形影响较小。
故工业上所谓微变形钢,均含有较多呈的硅、餌、机等合金元素。
3, 原始组织和应力状态对热处理变形的影响工件淬火前的原始组织,例如,碳化物的形态、大小、数呈及分布,合金元素的偏析,锻造和轧制形成的纤维方向都对工件的热处理变形有一定影响。
球状珠光体比片状珠光体比体积大,强度高,所以经过预先球化处理的工件淬火变形相对要小。
对于一些高碳合金工具钢,例如,9Mn2V、CrWMn和GCr15钢的球化等级对其热处理变形开裂和淬火后变形的校正有很大影响,通常以2.5-5级球化组织为宜。
调质处理不仅使工件变形呈的绝对值减小,并使工件的淬火变形更有规律,从而有利于对变形的控制。
31crmov9 热处理变形量

31crmov9 热处理变形量
31CrMoV9是一种低合金钢,通常用于制造高强度和耐磨性要求
较高的零件,比如发动机零部件、轴承、齿轮等。
热处理是提高钢
材性能的重要工艺之一,但热处理过程中会产生变形。
热处理变形
量受到多种因素的影响,包括材料的化学成分、热处理工艺参数、
冷却方式等。
首先,化学成分对热处理变形量的影响很大。
31CrMoV9钢的合
金元素含量较高,因此在热处理过程中容易产生变形。
合金元素的
含量会影响钢材的热膨胀系数和晶粒长大速率,进而影响热处理变
形量。
其次,热处理工艺参数的选择也会影响热处理变形量。
比如加
热温度、保温时间、冷却速度等参数的选择都会对变形量产生影响。
合理的工艺参数可以减小热处理变形量,例如采用适当的退火工艺
可以减小变形量。
另外,冷却方式也是影响热处理变形量的重要因素。
快速冷却
容易导致内部应力积聚,从而增加变形量。
因此,合理选择冷却方
式对于减小热处理变形量非常重要。
总的来说,31CrMoV9钢的热处理变形量受到多种因素的影响,
需要综合考虑材料的化学成分、热处理工艺参数和冷却方式等因素,通过合理的工艺控制和参数选择来减小热处理变形量。
同时,对于
特定工件的热处理变形问题,还可以通过模具设计、热处理工艺优
化等手段来减小变形量,以满足工件的使用要求。
- 1、下载文档前请自行甄别文档内容的完整性,平台不提供额外的编辑、内容补充、找答案等附加服务。
- 2、"仅部分预览"的文档,不可在线预览部分如存在完整性等问题,可反馈申请退款(可完整预览的文档不适用该条件!)。
- 3、如文档侵犯您的权益,请联系客服反馈,我们会尽快为您处理(人工客服工作时间:9:00-18:30)。
热处理工艺参数对热处理变形的影响
无论是常规热处理还是特殊热处理,都可能产生热处理变形,分析热处理工艺参数对热处理变形的影响时,最重要的是分析加热过程和冷却过程的影响。
加热过程的主要参数是加热的均匀性、加热温度和加热速度。
冷却过程的主要参数是冷却的均匀性和冷却速度。
不均匀冷却对淬火变形的影响与工件截面形状不对称造成的不均匀冷却情况相同,本文主要讨论其它工艺参数的影响。
一、不均匀加热引起的变形
加热速度过快、加热环境的温度不均匀和加热操作不当均能引起工件的不均匀加热。
加热的不均匀对细长工件或薄片件的变形影响十分显著。
这里说的不均匀加热并不是指工件表面和心部在加热过程中不可避免的温度差,而是特指由于种种原因工件各部分存在的温度梯度的情况。
为了减小不均匀加热引起的变形,对于形状复杂或导热性较差的高合金钢工件,应当缓慢加热或采用预热。
但是应当指出,虽然快速加热能导致长轴类工件和薄片状板件变形度的增加;然而,对于体积变形为主的工件,快速加热往往又能起到减小变形的作用。
这是因为当只有工件的工作部位需要沪淬火强化时,快速加热可使工件心部保持在温度较低强度较高的状态下,工作部分即能达到淬火温度。
这样强度较高的心部就能阻止工件淬火冷却后产生较大变形。
另外,快速加热可以采用较高的加热温度和较短的加热保温时间,从而可以减轻由于在高温阶段长时间停留因工件自重产生的变形。
快速
加热仅使工件表层和局部区域达到相变温度,相应地减小了淬火后的体积变化效应,这也有利于减小淬火变形。
二、加热温度对变形的影响
淬火加热温度通过改变淬火冷却时的温差,改变淬透性、Ms点和残余奥氏体的数量而对淬火变形发生影响。
提高淬火加热温度,增加了残余奥氏体量,使Ms点降低,组织应力引起的变形减小,使套类工件的孔腔趋于缩小;但另一方面,淬火加热温度的提高了淬透性,增大了淬火冷却时的温差,提高了热应力,有使内孔胀大的倾向。
实践证明,对于低碳钢制工件,若正常加热温度淬火后内孔收缩,提高淬火加热温度收缩的更大,为了减小收缩,要降低淬火加热温度;对于中碳合金钢制的工件,若正常加热温度淬火后内孔胀大,则提高淬火加热温度胀的更大,为了减小孔腔的胀大,也需降低淬火加热温度。
对于Cr12型高合金模具钢,提高淬火加热温度,使残余奥氏体量增多,孔腔趋于缩小。
三、淬火冷却速度对变形的影响
一般来说,淬火冷却愈激烈,工件内外和不同部位(截面尺寸不同的部位)温差愈大,产生的内应力愈大,导致热处理变形增大。
(150长*100宽*50高)的热模具钢制试样经不同冷却速度淬火回火的变形情况。
三种介质的冷却速度以油冷最快,热浴冷却次之,空冷最慢。
工件经三种不同冷速淬火后,其长度和宽度的变形皆倾向于收缩,变形量差别不大;但在厚度方向上冷速慢的空冷淬火和热浴淬火引起的变形则小得多,其变形胀大小于0.05%,而油淬发生收缩变形,其最大变形量
达0.28%左右。
然而,当冷却速度的改变使工件的相变发生变化时,冷却速度的增大却并不一定会引起变形的增大,有时反而会使变形减小。
例如,当低碳合金钢淬火后由于心部含有大量铁素体而发生收缩时,增大淬火冷却速度心部得到更多的贝氏体可以有效的减小收缩变形。
相反,若工件淬火后因心部获得马氏体而胀大时,减小冷却速度从而减小心部的马氏体相对量又能使胀大减小。
淬火冷却速度对淬火变形的影响是一个复杂的问题,但原则是在保证要求的组织和性能的前题下,应尽量减小淬火冷却速度。
四、时效与冷处理对热处理变形的影响
对于精密零件和测量工具,为了在长期使用过程中,保持精度和尺寸稳定,往往需要进行冷处理和回火,以便使其组织更加稳定,因此,了解回火工艺和冷处理对工件在时效过程中的变形规律,对于提高这类工件的热处理质量有重要意义。
冷处理使残余奥氏体转变为马氏体导致体积膨胀;低温回火和时效一方面促使∈-碳化物析出和马氏体分解使体积收缩,另一方面引起一定程度的应力松驰导致工件产生形状畸变。
钢的化学成分,回火温度和时效温度是影响时效过程中工作变形的主要因素。