金属工艺学特种铸造课件(PPT38).pptx
合集下载
金属工艺学教学课件第五章铸造
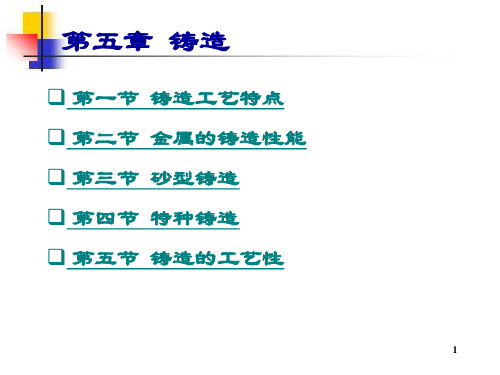
20
第四节 特种铸造
一、熔模铸造 二、金属型铸造 三、压力铸造 四、离心铸造 五、各种铸造方法的比较
21
一、熔模铸造
熔模铸造是用易熔的蜡料制成的和铸件形状相同的 蜡模和浇注系统,在蜡模表面涂挂几层耐火涂料和石英 砂,经硬火、干燥后将蜡模加热熔化,排出蜡液,得到 一个中空的型壳,即获得无分型面的整体铸型,最后进 行浇注,故熔模铸造又称为失蜡铸造。
图5-1 冷隔
9
的流动性可用螺旋线长度来测定,图5-2为螺旋
形试样。将金属液浇注入螺旋形铸型中,在相同的铸造 条件下,获得的螺旋线越长,表明金属液的流动性越好。
图5-2 螺旋形试样
10
一、流动性
(三)影响流动性的因素 合金的种类与化学成分
不同种类的合金具有不同的流动性,根据流动性试 验可测得螺旋线长度,常用铸造合金中,灰铸铁的流动 性较好,而铸钢的流动性相对较差。
11
二、收缩率
收缩是铸造合金从液态凝固和冷却至室温过程中产 生的体积和尺寸的缩减。包括液态收缩、凝固收缩、固 态收缩三个阶段,如图5-3所示。
图5-3 合金收缩的三个阶段
12
二、收缩率
(一)收缩对铸件质量的影响 液态收缩和凝固收缩若得不至到补足,会使铸件产
生缩孔和缩松缺陷;固态收缩若受到阻碍会产生铸造内 应力,导致铸件变形开裂。 缩孔与缩松
离心铸造法的不足之处是铸件内表面较粗糙,尺寸不 易控制,对内孔要切削加工的零件,则应增大加工余量。
离心铸造目前主要用于成批大量生产一般形状的黑色 金属及铜合金的大、中型回转体。如铸铁水管、缸套、活 塞环坯料和输油管等。
25
五、各种铸造方法的比较
各种铸造方法都有其优缺点和最适宜的应用范围。如 砂型铸造尽管有不少缺点,但其适应性强,所用设备比较 简单,因此,它仍然是当前生产中最基本的铸造方法。特 种铸造方法仅在一定条件下,才能显示其优越性。因此, 在选择铸造方法时,必须根据合金种类、铸件大小与形状、 批量、质量、车间设备及技术状况等来进行全面分析,综 合比较,选择经济合理的方法。
第四节 特种铸造
一、熔模铸造 二、金属型铸造 三、压力铸造 四、离心铸造 五、各种铸造方法的比较
21
一、熔模铸造
熔模铸造是用易熔的蜡料制成的和铸件形状相同的 蜡模和浇注系统,在蜡模表面涂挂几层耐火涂料和石英 砂,经硬火、干燥后将蜡模加热熔化,排出蜡液,得到 一个中空的型壳,即获得无分型面的整体铸型,最后进 行浇注,故熔模铸造又称为失蜡铸造。
图5-1 冷隔
9
的流动性可用螺旋线长度来测定,图5-2为螺旋
形试样。将金属液浇注入螺旋形铸型中,在相同的铸造 条件下,获得的螺旋线越长,表明金属液的流动性越好。
图5-2 螺旋形试样
10
一、流动性
(三)影响流动性的因素 合金的种类与化学成分
不同种类的合金具有不同的流动性,根据流动性试 验可测得螺旋线长度,常用铸造合金中,灰铸铁的流动 性较好,而铸钢的流动性相对较差。
11
二、收缩率
收缩是铸造合金从液态凝固和冷却至室温过程中产 生的体积和尺寸的缩减。包括液态收缩、凝固收缩、固 态收缩三个阶段,如图5-3所示。
图5-3 合金收缩的三个阶段
12
二、收缩率
(一)收缩对铸件质量的影响 液态收缩和凝固收缩若得不至到补足,会使铸件产
生缩孔和缩松缺陷;固态收缩若受到阻碍会产生铸造内 应力,导致铸件变形开裂。 缩孔与缩松
离心铸造法的不足之处是铸件内表面较粗糙,尺寸不 易控制,对内孔要切削加工的零件,则应增大加工余量。
离心铸造目前主要用于成批大量生产一般形状的黑色 金属及铜合金的大、中型回转体。如铸铁水管、缸套、活 塞环坯料和输油管等。
25
五、各种铸造方法的比较
各种铸造方法都有其优缺点和最适宜的应用范围。如 砂型铸造尽管有不少缺点,但其适应性强,所用设备比较 简单,因此,它仍然是当前生产中最基本的铸造方法。特 种铸造方法仅在一定条件下,才能显示其优越性。因此, 在选择铸造方法时,必须根据合金种类、铸件大小与形状、 批量、质量、车间设备及技术状况等来进行全面分析,综 合比较,选择经济合理的方法。
特种铸造技术介绍PPT
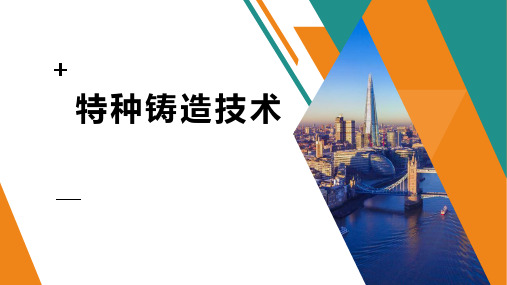
▆ 应用范围
(1)适用于生产形状复杂、精度要求高或难以切削加工成形的各种金属材料(尤其是碳钢及合金 钢)小型零件。如汽轮机、涡轮机的叶片或叶轮,汽车、拖拉机或机床用的各种小件。
2.压力铸造
█ 定义:是指将液态或半液态合金浇入压铸机的压室中,使之在高压和高速 下充填型腔,并在高压下成形结晶而获得铸件的一种铸造方法。常用压射压力 为5-70MPa,压射速度0.5-5m/s,充填时间很短,约0.01-02s。
6、适于有色金属薄壁复杂铸件的大批量生产。
3.低压铸造
█ 定义:是指液态金属在低的气体压力作用下从坩埚中自下而上地充填型腔 并凝固而获得铸件的一种铸造方法。常用压力为0.02~0.06MPa,介于重力和 压力铸造之间。
➢ 工艺过程:
3.低压铸造
3.低压铸造
特点和应用:
1、液态金属自下而上平稳的充填型腔, 型腔中的液流的方向与气体排出的方向一 致,避免了液态金属对型壁、型芯的冲刷 以及气体和氧化物,从而防止了铸件产生 气孔和非金属夹杂物;
3.应用范围
离心铸造是生产管套类铸件的主要方法,广泛应用于生产铸铁水管、缸套、轴套等。
各种铸造方法与砂型铸造加工精度对比:
结束
1.熔模铸造
◆◆ 熔模精密铸造:是指利用易熔材料制成模样,并在模样表面粘结一定厚度的耐火材料,然
后将模样熔化而使金属液充满型腔的一种铸造方法。(也称失蜡铸造)
熔 模 铸 造 工 艺 过 程
1.熔模铸造(1)熔模铸源自的工艺过程① 制作压型 压型根据铸件图制作,压型是压制蜡模的中间铸型。对高精度或大批量生产的铸件,常用机 械加工制成的钢或铝合金压型;对精度要求不高或生产批量不大的铸件常用低熔点合金(锡、铅、 铋)直接浇注的压型;对单件小批量的铸件可用石膏或塑料制作的压型。 ② 制作蜡模 将低熔点熔融态蜡料(常用50%的石蜡+50%的硬脂酸)压入压型中,冷凝后取出,得到单个蜡 模。将若干拉模粘到预制的蜡质浇口棒上,成为蜡模组。 ③ 制作壳型 将蜡模组浸入石英粉与水玻璃配成的浆料中,取出后在其表面撒上一层细石英砂,再浸入氯 化铵的溶液中硬化。如此由细到粗反复涂挂4-5次,指导表面结成5-10mm厚的硬壳后,放入8590℃的热水中,熔去蜡模而得到型腔与蜡模组一致的壳型。
(1)适用于生产形状复杂、精度要求高或难以切削加工成形的各种金属材料(尤其是碳钢及合金 钢)小型零件。如汽轮机、涡轮机的叶片或叶轮,汽车、拖拉机或机床用的各种小件。
2.压力铸造
█ 定义:是指将液态或半液态合金浇入压铸机的压室中,使之在高压和高速 下充填型腔,并在高压下成形结晶而获得铸件的一种铸造方法。常用压射压力 为5-70MPa,压射速度0.5-5m/s,充填时间很短,约0.01-02s。
6、适于有色金属薄壁复杂铸件的大批量生产。
3.低压铸造
█ 定义:是指液态金属在低的气体压力作用下从坩埚中自下而上地充填型腔 并凝固而获得铸件的一种铸造方法。常用压力为0.02~0.06MPa,介于重力和 压力铸造之间。
➢ 工艺过程:
3.低压铸造
3.低压铸造
特点和应用:
1、液态金属自下而上平稳的充填型腔, 型腔中的液流的方向与气体排出的方向一 致,避免了液态金属对型壁、型芯的冲刷 以及气体和氧化物,从而防止了铸件产生 气孔和非金属夹杂物;
3.应用范围
离心铸造是生产管套类铸件的主要方法,广泛应用于生产铸铁水管、缸套、轴套等。
各种铸造方法与砂型铸造加工精度对比:
结束
1.熔模铸造
◆◆ 熔模精密铸造:是指利用易熔材料制成模样,并在模样表面粘结一定厚度的耐火材料,然
后将模样熔化而使金属液充满型腔的一种铸造方法。(也称失蜡铸造)
熔 模 铸 造 工 艺 过 程
1.熔模铸造(1)熔模铸源自的工艺过程① 制作压型 压型根据铸件图制作,压型是压制蜡模的中间铸型。对高精度或大批量生产的铸件,常用机 械加工制成的钢或铝合金压型;对精度要求不高或生产批量不大的铸件常用低熔点合金(锡、铅、 铋)直接浇注的压型;对单件小批量的铸件可用石膏或塑料制作的压型。 ② 制作蜡模 将低熔点熔融态蜡料(常用50%的石蜡+50%的硬脂酸)压入压型中,冷凝后取出,得到单个蜡 模。将若干拉模粘到预制的蜡质浇口棒上,成为蜡模组。 ③ 制作壳型 将蜡模组浸入石英粉与水玻璃配成的浆料中,取出后在其表面撒上一层细石英砂,再浸入氯 化铵的溶液中硬化。如此由细到粗反复涂挂4-5次,指导表面结成5-10mm厚的硬壳后,放入8590℃的热水中,熔去蜡模而得到型腔与蜡模组一致的壳型。
第四章特种铸造介绍PPT课件

制造母模→制造压型→制造熔模→型壳的制造→浇注
熔模铸造动画演示
熔模铸造过程示意图
2 制蜡模设备
压型是用来制造熔模的重要工艺装备。压型要求: 制出的熔模能达到要求的尺寸精度和表面粗糙度;
压蜡机
压 型
蜡 模
3 压制熔模
(1)常用的模料
低熔点模料:由石蜡和硬脂酸各50%配制而成。 优点:熔点低(50~60℃),制备简单,流动性好; 缺点:其热稳定性差,强度低,焊接性和涂挂性差, 收缩率大。
第三章 特种铸造
特种铸造是指砂型铸造方法以外的铸造方法。 常见特种铸造主要有:
1 熔模铸造 2 金属型铸造 3 压力铸造 4 低压铸造 5 离心铸造 6 实型铸造
一 熔模铸造
1概述
采用蜡质材料制成模型,在模样上涂挂 若干层耐火涂料制成型壳,经硬化后再将模 样熔化,排出型外获得无分型面的铸型。铸 型经过低温烘烤和高温焙烧后进行液体金属 的浇注。
5 离心铸造的应用
离心铸造主要用来生产大批套、管类铸件,如 铸铁管、铜套、缸套、双金属钢背铜套等铸件的制 造。
最大重量达几公斤到十多吨,离心 铸件最大直径可达3米,最大长度8 米
六 实型铸造
1 概述
实型铸造又称“气化模造型”或“消失模铸 造”,采用聚苯乙烯发泡材料制得的模型(气化 模)代替木模造型,造型后不用起模直接将金属 液浇注到气化模上,使其气化并形成空腔来容纳 金属液,从而冷却凝固后获得铸件的方法。
涂料机械手
涂料机械手正在涂料制壳
自动化制壳过程
制备好的模壳
焙烧,浇注
5 熔模铸造的特点及适用范围
❖ 铸件尺寸公差可达IT11~IT13;表面粗糙度 Ra值为12.5~1.6μm。 ❖ 适合各种合金的铸件。尤其是熔点高、难切 削的高合金铸钢件的制造。 ❖ 可铸出形状较复杂、不能分型的铸件。 ❖ 工艺过程复杂、工序多,生产周期长 ❖ 铸件的重量一般不超过25kg。 ❖ 冷却速度慢,铸件晶粒粗大。 ❖ 某些原材料,如硅酸乙酯、刚玉粉等价格贵, 来源少
熔模铸造动画演示
熔模铸造过程示意图
2 制蜡模设备
压型是用来制造熔模的重要工艺装备。压型要求: 制出的熔模能达到要求的尺寸精度和表面粗糙度;
压蜡机
压 型
蜡 模
3 压制熔模
(1)常用的模料
低熔点模料:由石蜡和硬脂酸各50%配制而成。 优点:熔点低(50~60℃),制备简单,流动性好; 缺点:其热稳定性差,强度低,焊接性和涂挂性差, 收缩率大。
第三章 特种铸造
特种铸造是指砂型铸造方法以外的铸造方法。 常见特种铸造主要有:
1 熔模铸造 2 金属型铸造 3 压力铸造 4 低压铸造 5 离心铸造 6 实型铸造
一 熔模铸造
1概述
采用蜡质材料制成模型,在模样上涂挂 若干层耐火涂料制成型壳,经硬化后再将模 样熔化,排出型外获得无分型面的铸型。铸 型经过低温烘烤和高温焙烧后进行液体金属 的浇注。
5 离心铸造的应用
离心铸造主要用来生产大批套、管类铸件,如 铸铁管、铜套、缸套、双金属钢背铜套等铸件的制 造。
最大重量达几公斤到十多吨,离心 铸件最大直径可达3米,最大长度8 米
六 实型铸造
1 概述
实型铸造又称“气化模造型”或“消失模铸 造”,采用聚苯乙烯发泡材料制得的模型(气化 模)代替木模造型,造型后不用起模直接将金属 液浇注到气化模上,使其气化并形成空腔来容纳 金属液,从而冷却凝固后获得铸件的方法。
涂料机械手
涂料机械手正在涂料制壳
自动化制壳过程
制备好的模壳
焙烧,浇注
5 熔模铸造的特点及适用范围
❖ 铸件尺寸公差可达IT11~IT13;表面粗糙度 Ra值为12.5~1.6μm。 ❖ 适合各种合金的铸件。尤其是熔点高、难切 削的高合金铸钢件的制造。 ❖ 可铸出形状较复杂、不能分型的铸件。 ❖ 工艺过程复杂、工序多,生产周期长 ❖ 铸件的重量一般不超过25kg。 ❖ 冷却速度慢,铸件晶粒粗大。 ❖ 某些原材料,如硅酸乙酯、刚玉粉等价格贵, 来源少
《金属工艺铸造部分》PPT课件

精多,又不可能全部与基准面放在 分型面的同一侧时,则应使加工基准面与大部分加工面 处于分型面的同一侧。
a) 不合理
b) 合理
螺栓塞头的分型面
精选PPT
8
(5)铸件的非加工表面上,尽量避免有披缝。
a) 不正确
b) 正确
分型面的位置应能避免披缝
(6)分型面的选择应尽量与铸型浇注时位置一致。
↑ ↑ 壁厚 →石墨化倾向 易得粗大石墨片、铁素体 ↓ ↓ 壁厚 →石墨化倾向 易得细小石墨片、珠光体 壁厚↓→白口化倾向↑
图2-13 含碳、硅、壁厚与铸铁组织的关系
精选PPT
5
⒊灰铸铁的孕育处理——孕育铸铁 ● 孕育铸铁的生产: 在含碳、硅较低的铁水中加入孕育剂(75%硅铁), 促进入石墨化,增加了石墨结晶核心,使石墨均 匀,细小,并获得珠光体基体。 ● 孕育铸铁的特点:
三、铸件中的缩孔与缩松
1、缩孔与缩松的形成 形成原因 液态合金在冷凝过程中,液态收缩和凝固收缩 的容积得不到补足而行成。(补缩) (1)缩孔 ⊙ 通常在铸件上部,或最后凝固的部分 ⊙ 大小 合金的液态收缩↑,凝固收缩↑ →缩孔容积↑ 浇注温度↑→缩孔容积↑ 铸件较厚→缩孔容积↑ ⊙ 形成:如图
精选PPT
精选PPT
9
§5.2 铸件结构与合金铸造性能的关系
⒈ 合理设计铸件的壁厚 铸造合金流动性各不相同,在相同条件下,不同合金 所能浇注出铸件的最小壁厚也不相同。 厚大截面承载能力并非按截面积成比例增加。
最小壁厚:在各种工艺条下,铸造合金能充满型腔的最小厚度。主要 取决于合金的种类、铸件的大小及形状等因素。
牌号愈高,铸造性能越差,对结构要求越高。但孕育铸 铁可设计成较厚铸件。
铸钢壁厚不宜过薄,因其流动性差,收缩率高。壁厚稍 厚些,利于顺序(定向)凝固。
第4讲特种铸造

的可能性; – 铸件成型性好。金属液在外力作用下强迫流动,
提高了金属的充填能力,有利于形成轮廓清晰, 表面光洁的铸件; – 铸件组织致密,机械性能高; – 金属收得率高(80%~98%)。
© 2006 金工教研室
机械制造基础
© 2006 金工教研室
机械制造基础
© 2006 金工教研室
机械制造基础
卧式离心铸造机
© 2006 金工教研室
机械制造基础
大型管件
© 2006 金工教研室
机械制造基础
更大的管道
© 2006 金工教研室
机械制造基础
最大重量
达几公斤 到十多吨
离心铸件最大直径可 达3米,最大长度8米
© 2006 金工教研室
机械制造基础
立 式 离 心 铸 造 机
© 2006 金工教研室
© 2006 金工教研室
机械制造基础
金属型铸造
© 2006 金工教研室
机械制造基础
金属型铸造的四种分型方式
© 2006 金工教研室
机械制造基础
金属型铸造的缺点和不足
1. 生产成本高,适合大批量生产 2. 铸件易形成浇不足和开裂等缺陷, 3. 工艺过程参数控制严格 4. 采用金属型生产的铸件重量和形状方面
© 2006 金工教研室
机械制造基础
比较
产量
铸件制造成本(元/件) 砂型 金属型 熔模 压力
100
1.75
6.02
6.25 18.75
1000 0.62 1.23 2.67 1.95
10000 0.33 0.37 1.93 0.50
100000 0.30 0.29 1.80 0.16
© 2006 金工教研室
提高了金属的充填能力,有利于形成轮廓清晰, 表面光洁的铸件; – 铸件组织致密,机械性能高; – 金属收得率高(80%~98%)。
© 2006 金工教研室
机械制造基础
© 2006 金工教研室
机械制造基础
© 2006 金工教研室
机械制造基础
卧式离心铸造机
© 2006 金工教研室
机械制造基础
大型管件
© 2006 金工教研室
机械制造基础
更大的管道
© 2006 金工教研室
机械制造基础
最大重量
达几公斤 到十多吨
离心铸件最大直径可 达3米,最大长度8米
© 2006 金工教研室
机械制造基础
立 式 离 心 铸 造 机
© 2006 金工教研室
© 2006 金工教研室
机械制造基础
金属型铸造
© 2006 金工教研室
机械制造基础
金属型铸造的四种分型方式
© 2006 金工教研室
机械制造基础
金属型铸造的缺点和不足
1. 生产成本高,适合大批量生产 2. 铸件易形成浇不足和开裂等缺陷, 3. 工艺过程参数控制严格 4. 采用金属型生产的铸件重量和形状方面
© 2006 金工教研室
机械制造基础
比较
产量
铸件制造成本(元/件) 砂型 金属型 熔模 压力
100
1.75
6.02
6.25 18.75
1000 0.62 1.23 2.67 1.95
10000 0.33 0.37 1.93 0.50
100000 0.30 0.29 1.80 0.16
© 2006 金工教研室
金属型铸造引用PPT(完整版)精选全文
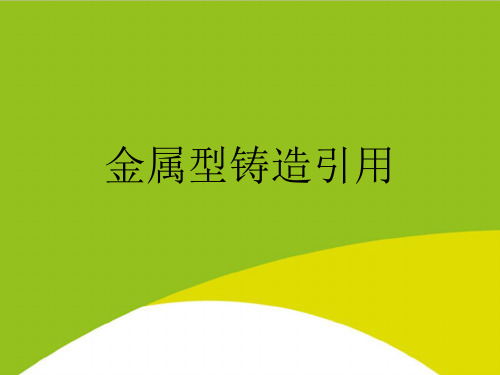
目录
一、概述 二、铸件工艺设计 三、金属型设计 四、铸造工艺 五、金属型铸造机 六、铸件常见缺陷及防止方法
二、铸件工艺设计
1 基准面的选择 2 铸件在金属型中的位置 3 分型面的选择 4 铸件工艺性设计 5 浇注系统 6 冒口设计
1 基准面的选择
基准面决定铸件各部分相对的尺寸位置。 所以选择铸造基准面时,必须和铸件机械 加工的基准面统一,其选择原则为: (1)非全部加工的铸件,应尽量选取非加工 面作为基准面。 (2)采用非加工面作基准面时,应该选尺寸 变动小、最可靠的面作基准面。最好不选 用活块形成的铸件表面作为基准面。
• 金属液充填型腔时易产生飞溅,不利于排气,铸件 易产生氧化夹渣等缺陷。
• 适用于矮而简单的铸件。高度超过100mm的铝、 镁合金铸件宜采用倾斜浇注,倾斜角度为30°~ 50°。
5 浇注系统
(2) 浇注系统的形式及特点 中注式
• 金属液流动比顶注式平稳,能获得比底注式较合理的 热分布,但不能完全避免产生飞溅和涡流。
6 冒口设计
还可将冒口设在内浇道和直浇道之间, 冒口既能补缩又可起集渣的作用。
目录
一、概述 二、铸件工艺设计 三、金属型设计 四、铸造工艺 五、金属型铸造机 六、铸件常见缺陷及防止方法
三、金属型设计
1 金属型结构形式 2 金属型结构设计 3 金属型操纵机构设计 4 金属型加热和冷却 5 金属型用材料及其选用 6 金属型寿命
v也可以根据经验选取。对于铝合金,一般 v<150cm/s;对于镁合金,一般v<130cm/s.
5 浇注系统
(4) 浇注系统的计算 对于铝、镁合金,为防止金属液产生飞
溅,通常采用开放式浇注系统。
大型铸件:A直:A横:A内=1:(2~3):(3~6) 中型铸件:A直:A横:A内=1:(2~3):(2~4) 小型铸件:A直:A横:A内=1:(1.5~3):(1.5~3)
特种铸造课件金属型铸造

3、金属型铸造缺点:
(1)金属型的激冷作用大,充型能力差,易出现 冷隔、浇不足。
(2)金属型本身无退让性,铸件容易产生铸造应 力,发生变形或开裂。
(3)金属型没有透气性,容易卷气。
(4)金属型制作成本较高,不适合单件小批生 产。。
为了防止浇注时金属液流动过程中形成紊流,减 少氧化、夹杂及卷气等缺陷,广泛采用倾转式浇注, 见图2.1
4、金属型应用
金属型铸造主要应用于铝镁等轻有色合金中小型 铸件的生产中,也可用于黑色金属铸件,如磨球、 铸锭等。
金属型铸造在汽车、摩托车、航空航天、农业等 工业领域获得了广泛的应用。
金属型没有透气性,金属液在充型过程中,如果 型腔中的气体排不出去,在型腔中的凹入的死角或金 属液的汇合处形成憋气,阻碍金属液流动充型,或被 金属液卷入进入金属液中形成气孔缺陷,如图2.2所示。
图2-6(a)所示的方案不太合理。原因如下:
a 浇注时金属液通过浇口4直接冲击到砂芯3,导致金属液流紊乱,容 易进渣和卷气。
b 金属型芯2处的厚壁远离冒口,不易得到补缩,易产生缩孔、缩松;
c 上方的冒口偏大,切割工作量大; d 因为有金属型芯2,不设顶出机构或抽芯机构,无法取出铸件。
图2-6(b)所示的方案比较合理。原因如下:
2.3.1.3铸件的工艺性设计
金属型铸件结构工艺性的合理设计是保证铸件质 量,发挥金属型铸造成形优点的先决条件。
铸件工艺性设计应在尽量满足产晶结构要求的前 提下,通过调整机械加工余量、增大铸件拔模斜度、 增加工艺筋和工艺凸台等方法,使铸件结构更加合 理,从而获得优质铸件。铸件工艺性设计原则见表27。
(2)矮的盘形和筒形铸件,分型面应尽量不选在铸 件的轴心上。
(3)分型面应尽可能地选在同一个平面上,尽量避 免曲面分型。
金属工艺学特种铸造课件
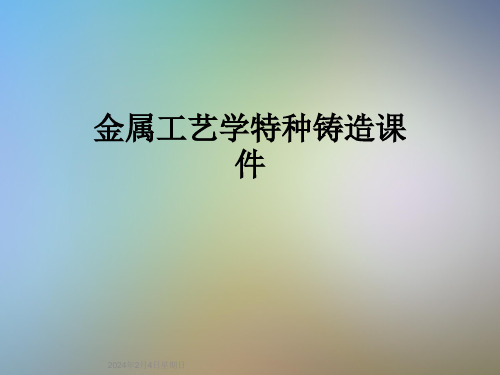
金属工艺学特种铸造课 件
2024年2月4日星期日
第四章 特种铸造
特种铸造方法通常是指区别于普通砂型铸造的一些 方法。其在提高铸件精度和表面质量,改善合金性能, 提高生产率,改善劳动条件和降低铸造成本等方面,各 有优越之处。
❖ 熔模铸造 ❖ 离心铸造 ❖ 压力铸造 ❖ 金属型铸造 ❖ 消失模铸造
熔模铸造
b.制造单个泡沫塑料模 C.组装模样束
(2)上涂料 泡沫塑料模样束表面应上两层
涂料。第一层是用来提高表面光洁度的涂料。第 二层是耐火涂料。
(3)填砂、紧实、浇注 (4)落料、清理
消失模铸造特点
1、铸件尺寸精度高(可达5-7级)
2、铸件表面光洁(Ra6.3-12.5um) 3、铸件加工量小 4、铸件无飞边毛刺,落砂清理容易,清理工时少
❖ 浇注
浇注温度比砂型铸造时高。由根据合金种类、铸件大 小和壁厚决定。
❖ 开型、取出铸件、清理
金属型铸造方法主要用于熔点较低的有色金属或合金铸 件的大批量生产。黑色金属类铸件只限于形状简单的中小零 件。
金属型铸造的特点
❖可承受多次浇注,便于实现机械化生产 ❖铸件精度和表面质量高(铝合金铸件的尺寸公 差等级可达IT7~IT9,表面粗糙度可达 Ra3.2~12.5um) ❖铸件的结晶组织致密,机械性能高
压力铸造的特点和适用范围
❖缺点 ❖ 投资大,生产周期长 ❖ 压铸合金的种类受限制,压铸高熔点合金(铸铁 、铸钢)时,压型寿命低 ❖ 铸件内部常有气孔和缩松,不能进行较多余量的 切削加工 ❖ 压铸件不能用热处理的方法提高性能
❖适用范围
❖主要用于有色合金(如铝合金、锌合金)的中 、小铸件的大量生产。
冷压室卧式压铸(目前应用最多)
工艺过程
2024年2月4日星期日
第四章 特种铸造
特种铸造方法通常是指区别于普通砂型铸造的一些 方法。其在提高铸件精度和表面质量,改善合金性能, 提高生产率,改善劳动条件和降低铸造成本等方面,各 有优越之处。
❖ 熔模铸造 ❖ 离心铸造 ❖ 压力铸造 ❖ 金属型铸造 ❖ 消失模铸造
熔模铸造
b.制造单个泡沫塑料模 C.组装模样束
(2)上涂料 泡沫塑料模样束表面应上两层
涂料。第一层是用来提高表面光洁度的涂料。第 二层是耐火涂料。
(3)填砂、紧实、浇注 (4)落料、清理
消失模铸造特点
1、铸件尺寸精度高(可达5-7级)
2、铸件表面光洁(Ra6.3-12.5um) 3、铸件加工量小 4、铸件无飞边毛刺,落砂清理容易,清理工时少
❖ 浇注
浇注温度比砂型铸造时高。由根据合金种类、铸件大 小和壁厚决定。
❖ 开型、取出铸件、清理
金属型铸造方法主要用于熔点较低的有色金属或合金铸 件的大批量生产。黑色金属类铸件只限于形状简单的中小零 件。
金属型铸造的特点
❖可承受多次浇注,便于实现机械化生产 ❖铸件精度和表面质量高(铝合金铸件的尺寸公 差等级可达IT7~IT9,表面粗糙度可达 Ra3.2~12.5um) ❖铸件的结晶组织致密,机械性能高
压力铸造的特点和适用范围
❖缺点 ❖ 投资大,生产周期长 ❖ 压铸合金的种类受限制,压铸高熔点合金(铸铁 、铸钢)时,压型寿命低 ❖ 铸件内部常有气孔和缩松,不能进行较多余量的 切削加工 ❖ 压铸件不能用热处理的方法提高性能
❖适用范围
❖主要用于有色合金(如铝合金、锌合金)的中 、小铸件的大量生产。
冷压室卧式压铸(目前应用最多)
工艺过程
《金属工艺学铸造》课件
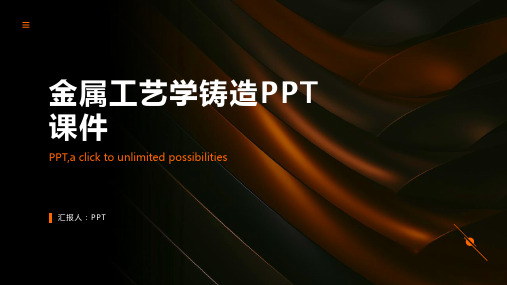
金属材料的可铸造性
流动性:金属材料在铸造过程中流动性 越好,越容易形成均匀的铸件
收缩性:金属材料在冷却过程中收缩性 越小,越容易形成尺寸精确的铸件
热导率:金属材料的热导率越高,越容 易形成表面光滑的铸件
化学稳定性:金属材料在铸造过程中化 学稳定性越好,越不容易产生气孔和裂 纹
机械性能:金属材料的机械性能越好, 越容易形成强度高、耐磨损的铸件
铸造缺陷的检测方法
目视检查:观 察铸件表面是 否有裂纹、气 孔、砂眼等缺
陷
超声波检测: 利用超声波探 头对铸件内部 进行扫描,检
测内部缺陷
射线检测:利 用X射线或γ 射线对铸件进 行照射,通过 观察射线穿透 情况检测内部
缺陷
磁粉检测:利 用磁粉对铸件 表面进行喷涂, 观察磁粉吸附 情况检测表面
缺陷
离心铸造设备: 包括离心铸造 机、离心铸造 模具等,特点 是生产效率高, 精度高,但成
本较高。
连续铸造设备: 包括连续铸造 机、连续铸造 模具等,特点 是生产效率高, 成本低,但精
度较低。
砂型铸造设备的使用和维护
设备类型:砂型铸造设备主要包括砂型铸造机、砂型铸造模具等 使用方法:按照设备说明书进行操作,注意安全操作规程 维护方法:定期检查设备,及时更换磨损部件,保持设备清洁 常见问题及解决方法:如设备故障、模具损坏等问题,应及时解决,确保生产顺利进行
安全设施:包括防护罩、安全门、安全护栏等,确保操作人员安全 环保设施:包括废气处理系统、废水处理系统、噪音控制设备等,减少对环境的影响 使用方法:按照说明书进行操作,定期检查和维护,确保设施正常运行 维护方法:定期进行清洁、润滑、更换易损件等,确保设施使用寿命和效果
铸造生产安全与环保管理的实施
《特种铸造》课件
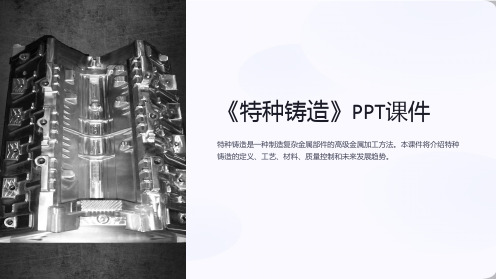
3 金属模铸造
金属模铸造使用金属模具进行铸造,适用于 制造高温、高压和高强度要求的零部件。
4 水玻璃硅溶胶复合型铸造
水玻璃硅溶胶复合型铸造是一种以水玻璃和 硅溶胶为粘结剂的新型铸造工艺,适用于制 造复杂形状和高精度零部件。
特种铸造的材料
金属材料
特种铸造使用多种金属材料,如铁、铝、铜、镁等,以满足不同零部件的要求。
特种铸造中常用的质量控制方法包括材料测试、尺寸测量、表面质量检查和性能 测试等。
特种铸造的未来发展趋势
新材料的不断引入
技术的不断更新与升级
特种铸造将继续引入新材料,如 高温合金、复合材料等,以满足 不断提高的产品性能和功能需求。
特种铸造将借助先进的技术,如 计算机辅助设计、模拟仿真和智 能化制造等,提高生产效率和产 品质量。
《特种铸造》PPT课件
特种铸造是一种制造复杂金属部件的高级金属加工方法。本课件将介绍特种 铸造的定义、工艺、材料、质量控制和未来发展趋势。
简介
什么是特种铸造?特种铸造是一种高级金属加工方法,用于制造复杂的金属部件。它在现代工业中起着重要作 用,并具有丰富的历史和不断发展的前景。
特种铸造的历史和发展:特种铸造技术的起源可以追溯到古代文明时期,经历了多个阶段的演变和改进,如金 属模铸造和水玻璃硅溶胶复合型铸造。
特种铸造在现代工业中的应用:特种铸造广泛应用于航空航天、汽车、能源、工程机械等领域,为各行各业提 供高质量、高精度的零部件。
特种铸造工艺
1 砂型铸造
砂型铸造是最常见的铸造工艺,使用砂型作 为模具,适用于制造大型复杂金属部件。
2 石膏模铸造
石膏模铸造是使用石膏模具进行铸造的工艺, 适用于制造精密细节和表面平整度要求较高 的零部件。
金属材料及工艺课件:特种铸造-

低壓鑄造機
11.4 熔模鑄造
• 熔模鑄造:用易熔材料製成模樣,然後在模樣上塗掛耐 火材料,經硬化之後形成型殼,再將模樣熔化排除型外, 從而獲得無分型面的鑄型。
1. 熔模鑄造的工藝過程
熔模鑄造rongmo[1]
(1)製造蠟模
a 製造壓型; b 壓制蠟模; c 組裝蠟模。
(2)製造型殼
a 浸塗料; b 撒砂; c 硬化; d 重複上述過程。製成5-12㎜的耐火型殼; e 脫蠟。
(2)陶瓷型鑄造的特點及適用範圍 優點: ➢ 尺寸精度高、表面粗糙度低,可澆注高溫合金; ➢ 鑄件的大小不受限制; ➢ 在單件小批生產條件下,需要投資少、生產週期短。 缺點: ➢ 不適合批量大、重量輕或形狀複雜的鑄件; ➢ 難以實現生產過程的機械化和自動化。 應用: ➢ 厚大精密鑄件。如沖模、鍛模、玻璃器皿模、壓鑄模、
1. 壓力鑄造的工藝過程 • 壓鑄機:熱壓室壓鑄機和冷壓室壓鑄機,冷壓室壓鑄機
按其壓室的結構和佈置方式分為臥式和立式壓鑄機。 • 壓鑄型
• 壓鑄過程(以臥式壓鑄機為例),如圖。
壓力鑄造演示yali[1]
• 主要工藝參數:
a 壓鑄壓力和壓鑄速度。 b 澆注溫度 c 壓鑄型溫度。 d 充型、持壓和開型時間, e 塗料。
件。如發動機葉片、齒輪刀具等
典型熔模鑄造鑄件
11.5 離心鑄造
離心鑄造:將液態合金澆入高速旋轉(250~1500r/min) 的鑄型,使金屬液在離心作用下充填鑄型並結晶的鑄造 方法。
5.1 離心鑄造的基本方式
G
2r g
• 立式離心鑄造機:鑄型饒垂直軸旋轉自動形成內腔,壁厚 取決於澆入金屬量
➢ 優點:便於鑄型的固定和金屬的澆注; ➢ 缺點:自由面呈拋物面,上薄下厚; ➢ 應用:高度小於直徑的圓環鑄件、成型鑄件。
第四节特种铸造概要PPT课件
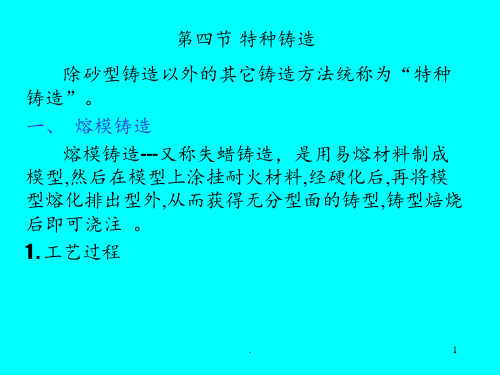
昂贵 模具和精密铸件
尺 寸 精 度 高 、表 面 光 洁 ,但 生 产 率
石膏型铸造
铝、镁、锌 合金
几十克~ 几十公斤
很好
较复杂
高 单件到小批量
低压铸造
有色合金
几十克~ 几十公斤
好
复杂(可 用砂芯)
金属模的制 作费用高
小批量 有色合
,最好 金铸件
是 ,
大批量的大、中型 可生产薄壁铸件
铸 较 率
件组 简单 低
砂型铸造
熔模铸造
金属型铸造
压力铸造
低压铸造
比较项目
适用金属
任意
不限制,以铸钢 不限制,以有色合 铝、锌、镁等低熔 以有色合金为主,
为主
金为主
点合金
也可用于黑色金属
适用铸件大小
任意
小于 25kg,以小 以中、小铸件为主 一般为 l0kg 以下, 以中、小铸件为主
铸件为主
也可用于中型铸件
批量
不限制 用于成批生产, 大批、大量
三、金属型铸造
将液态金属浇入用金属制成的铸型,冷凝后获得 铸件的方法。
1、金属铸型构造 1)铸型材料:多数用铸铁;要求较高用碳钢或低合金钢。 2)型芯材料:形状简单件或有色金属件用金属型芯;薄壁复 杂件或铸铁、铸钢件用砂芯。 3)铸型的种类:按分型面的方位分为垂直分型式、 水平分型 式和整体式、复合分型式。 4)合箱、开箱方式:自动或半自动的连杆机构。
.
23
1、低压铸造的工艺过程:
2、特点及应用
特点:
(1)充型压力和速度便于人为控制,适应各种铸型,包括金属型、砂型、 熔模型壳及适应各种合金铸件,铸件尺寸、形状范围广。
(2)底注充型,减少金属液冲击,平稳易控制。 (3)不用冒口补缩,金属利用率高。 (4)铸件的组织致密,机械性能较高。 (5)易于实现机械化、自动化生产,且设备较压铸简单,但
- 1、下载文档前请自行甄别文档内容的完整性,平台不提供额外的编辑、内容补充、找答案等附加服务。
- 2、"仅部分预览"的文档,不可在线预览部分如存在完整性等问题,可反馈申请退款(可完整预览的文档不适用该条件!)。
- 3、如文档侵犯您的权益,请联系客服反馈,我们会尽快为您处理(人工客服工作时间:9:00-18:30)。
母模
压型
熔蜡
充满压型
一个蜡模
蜡模组
结壳、倒出熔蜡
填砂浇注
与砂型铸造方法对比,熔模精密铸造具有如下优点: 1. 铸件尺寸精度高(IT11~IT13),表面粗糙度值低 (12.5~1.6um)。减少切削加工量,甚至无须切削加工 (涡轮发动机的叶片)。
2.可以铸造薄壁件及重量很小的铸件。
3.擅长制造用砂型铸造、锻压、切削加工等方法难以 制造的形状,复杂、不便分型的零件。如带有精细的 图案、文字、细槽和弯曲细孔的铸件
工艺过程
❖金属型的预热(预热温度一般不低于150°C)
金属型导热性好/液体金属冷却快,铸件易出现 冷隔、浇不足、气孔等缺陷。同时保护铸型。
❖ 涂料(耐火涂料的厚度为0.3~0.4mm)
❖利用涂料层的厚薄,调节铸件的冷却速度; ❖保护金属型,防止高温金属液对型壁的冲蚀和
热击; ❖利用涂料层蓄气排气。
压力铸造的特点和适用范围
❖缺点 ❖ 投资大,生产周期长 ❖ 压铸合金的种类受限制,压铸高熔点合金(铸铁、 铸钢)时,压型寿命低 ❖ 铸件内部常有气孔和缩松,不能进行较多余量的 切削加工 ❖ 压铸件不能用热有色合金(如铝合金、锌合金)的中、 小铸件的大量生产。
冷压室卧式压铸(目前应用最多)
优点
• 利用回转表面生产圆筒形铸件,省去型芯和浇注系统, 大大简化了生产过程,节约了金属
• 离心力的作用,铸件由外向内的顺序凝固,而气体和熔 渣因比重轻向内腔移动而排除,铸件组织致密,极少有 缩孔、气孔、夹渣等缺陷
• 合金的充型能力强,便于流动性差的合金及薄件的生产。
• 便于制造双金属铸件
缺点 • 铸件易产生偏析,铸件内表面较粗糙。内表面尺寸不易控制。
立式离心铸造 铸型绕垂直轴旋转。铸件内表面呈抛物线形。用来
铸造高度小于直径的盘、环类或成形铸件。
❖卧式离心铸造 铸型绕水平轴旋转,铸件壁厚均匀,应用广泛,主 要用来生产圆环类铸件,也用于浇注成形铸件。
离心式实型铸造
离心铸造的生产过程
(1)将金属型型腔清理干净,喷涂料 (2)旋转铸型,浇入定量金属液 (3)凝固后,停止旋转,取出铸件
型腔并凝固 (4)打开铸型,用顶杆顶出铸件
压力铸造的特点和适用范围
❖优点 ❖ 铸件的精度和表面质量都较其他铸造方法高(尺寸公差
等级可达CT4~CT7,表面粗糙度一般可达 Ra1.6~12.5um) ❖ 可压铸出形状复杂的薄壁件、和镶嵌件(铸件最小壁厚 为:锌合金为0.3mm,铝合金为0.5mm) ❖ 铸件强度和硬度高(抗拉强度可比砂型铸件提高 25%~30%,但伸长率有所降低) ❖ 生产率高(一般冷压式压铸机平均每小时压铸600-700次)
b.制造单个泡沫塑料模 C.组装模样束
(2)上涂料 泡沫塑料模样束表面应上两层
第五章 特种铸造
教学重点:每种特种铸造的优越之处和选择原则 教学难点:熔模铸造的工艺过程 教学目标和要求:了解各种铸造方法的特点及应 用范围,每种铸造的优越之处和选择原则。
第四章 特种铸造
特种铸造方法通常是指区别于普通砂型铸造的一些 方法。其在提高铸件精度和表面质量,改善合金性能, 提高生产率,改善劳动条件和降低铸造成本等方面,各 有优越之处。
消失模铸造
也称气化模铸造,国际上称EPC工艺。 真空实型铸造, 用泡沫模型代替金属或木模,造
型后模样不取出,呈实体型腔,浇注时模样气化消失而 得到铸件。
消失模铸造的工艺过程
(1)制造泡沫塑料模
a.制备消失模材料 需经预发泡—将珠粒密度大( 1.05g/cm3)的原材料及发泡剂,经过蒸汽加热、抽真 空,获得符合要求的低密度珠粒、残留发泡剂含量及适当 粒度的珠粒的处理过程。(主要的消失模材料有:可发性 聚苯乙烯(EPS),适用于灰铸铁、球墨铸铁和有色合金 铸件等;可发性聚甲基丙烯甲酯(EPMMA),适用于球 墨铸铁和铸钢件等。这类泡沫塑料的特点:密度小( 0.015~0.025g/cm3),发气量小、导热系数小、产生 气体及残留物少、资源丰富、价格不高。
4.可以制造各种合金材质的铸件,尤其适用于高熔点、 难切削合金的小型复杂铸件的生产
金属型铸造
又称硬模铸造,将液体金属浇入金属铸型,获得铸件 的一种铸造方法。铸型是用金属制成,可以反复使用多次。 金属型的结构有多种形式,(a)是水平分型式金属型,多 用于生产薄壁轮状铸件;(b)为垂直分型式金属型,广泛 应用于复杂铝合金铸件。
❖ 浇注
浇注温度比砂型铸造时高。由根据合金种类、铸件大 小和壁厚决定。
❖ 开型、取出铸件、清理
金属型铸造方法主要用于熔点较低的有色金属或合金铸 件的大批量生产。黑色金属类铸件只限于形状简单的中小零 件。
金属型铸造的特点
❖可承受多次浇注,便于实现机械化生产 ❖铸件精度和表面质量高(铝合金铸件的尺寸公 差等级可达IT7~IT9,表面粗糙度可达 Ra3.2~12.5um) ❖铸件的结晶组织致密,机械性能高
❖金属型成本高,生产周期长 ❖铸造工艺严格, ❖易出现浇不足、冷隔、裂纹 ❖铸件的形状和尺寸受一定的限制
组合金属型结构
金属型和砂型,在性能上有显著的区别
1.透气性差 2.导热性好 3.没有退让性
金属型的这些特点决定了它在铸件形成过程中有自 己的规律。
离心铸造
将液态合金浇入高速旋转的铸型中,使金属液在离心 力作用下充填铸型并结晶。
❖ 熔模铸造 ❖ 离心铸造 ❖ 压力铸造 ❖ 金属型铸造 ❖ 消失模铸造
熔模铸造
熔模铸造用易熔材料制成模型,然后在模型上涂挂 耐火材料,经硬化之后,再将模型熔化、排出型外 ,从而获得无分型面的铸型
由于熔模广泛采用蜡质材料来制造,故又常把它称 为“失蜡铸造”。由于获得的铸件具有较高的尺寸 精度和表面光洁度,故又称“熔模精密铸造”
压力铸造
将熔融的金属在高压下,快速压入金属型,并在 压力下凝固,以获得铸件的方法。(常用压射压力为 几至几十兆帕,充填速度约为0.5~50m/s,充填时间为 0.01~0.2s)
热压室压铸
工艺稳定铸件质量好,压型寿命低
压铸的工艺过程
(1)预热金属铸型,喷涂料 (2)合型、注入金属液 (3)压射冲头在高压下推动金属液充满