外形加工培训教材
FPC工艺培训教材(1)

绝缘层(PI)材料介绍2
聚酰亚胺(PI)有如下特性:㈠具有高度挠曲性, 可立体配线,依空间限制改变形状;㈡耐高低温,耐燃; ㈢可折叠而不影响信号传递功能,可防止静电干扰;㈣化 学变化稳定,安定性、可信赖度高;㈤利于相关产品的设 计,可减少装配工时及错误,并提高有关产品的使用寿命; ㈥良好的绝缘性能㈦优良的介电性能;㈧有良好的黏结性。 但它也有不足之处,那就是吸湿性高,所以PI的FPC应在 干燥的条件下保管以及在进行装配焊接之前必须进行干燥 除湿处理。PET与PI 相比,价格低廉、机械特性优异,但 耐温低,受温度影响的物理性能变化很大。一般都是用在 手工焊或不需要焊接的线路板上,比如电缆线、汽车仪表 上。
(4). 胶厚度 um (5). PI Film 种类代号 : H : Kapton A : Apical T : Taimide P : BOPI
带胶补强结构
补强胶片: 补强FPC 的机械强度, 方便表面 实装作业.常见的厚度有 2mil到9mil. 接着剂:厚度依客戶 需求而定,可以自行备胶。 离形纸:避免接着剂 在压着前沾附异物.
FZ : Fukuda(ED)
ME : Mitsui/S-HTE (ED)
TE : TCF/S-THE(ED) LC : LCY GRLP3(ED)
单面板结构
单面板有胶基材的叠构组成:
a、单面板组成:
铜箔基材+保护膜 b、单面板叠构:
保护膜
铜箔基材
PI 胶 铜箔 胶 PI
备注:与单面无 胶基材相比多了 一层基材胶
10
纯胶结构图
离形紙:避免接
着剂在压着前沾附 异物. 接着剂:厚度依 客戶要求而決定. 功能在于贴合多层 板层与层之间
机械加工表面质量加工培训教材PPT85页课件

1. 磨削用量对表面粗糙度值的影响
*
2. 非几何因素
(1)工件材料的影响
韧性材料:工件材料韧性愈好,金属塑性变形愈大,加工表面愈粗糙。故对中碳钢和低碳钢材料的工件,为改善切削性能,减小表面粗糙度,常在粗加工或精加工前安排正火或调质处理。 脆性材料:加工脆性材料时,其切削呈碎粒状,由于切屑的崩碎而在加工表面留下许多麻点,使表面粗糙。
砂轮硬度。太硬,磨粒脱落↓,表面粗糙度增大;太软,磨粒脱落↑,使表面粗糙度值增大。硬度合适、自励性好↑→Ra↓ 砂轮组织。紧密组织在精密磨获得高精度和较小的表面粗糙度值;疏松组织不易堵塞。
砂轮材料。氧化物(刚玉)砂轮磨钢类零件;碳化物(碳化硅、碳化硼)砂轮磨铸铁、硬质合金等;高硬材料(人造金刚石、立方氮化硼)砂轮可获极小表面粗糙度值,成本高。 磨削液。
(4)其它因素的影响
此外,合理使用冷却润滑液,适当增大刀具的前角,提高刀具的刃磨质量等,均能有效地减小表面粗糙度值。振动
(3)进给量的影响
减小进给量f固然可以减小表面粗糙度值,但进给量过小,表面粗糙度会有增大的趋势。
*
影响切削加工表面粗糙度的因素
刀具几何形状
*
(2)切削速度的影响
加工塑性材料时,切削速度对表面粗糙度的影响(对积屑瘤和鳞刺的影响)。加工脆性材料,切削速度影响不大。 此外,切削速度越高,塑性变形越不充分,表面粗糙度值越小 选择低速宽刀精切和高速精切,可以得到较小的表面粗糙度。
CADCAM 培训教材

目的 去掉铜面钻孔时形成的 占胶 使化学镀铜层与底铜结 合良好 在基材上沉积一层 Pa,作为沉铜的活化层 孔壁沉上 0.05mil0.1mil 铜
方法 不同的 TG 材料采用不同的方法
利用弱蚀刻剂从铜面上蚀刻掉 2-5um. Pa2++Sn2+-(PaSn)2+ (PaSn)2+Pa+ Sn2+ Sn4+ Cu 2+ 2CH2O+OH--Cu + 2CHO2-+H2O+H2 (以 Pa 作为催化剂)
仅作为导通用(不
作插件或焊接),如测 试点和一般导通孔。
用于插件或焊接, 也可导通内外层。
2. NPTH:
(Non-plated through hole) 非电镀孔
N P T H
作用:
一般是作为装配零件的定位孔或工具孔。
3. SMT/SMD
Surface Mounting Technology: 表面贴覆技术 SMT
L1
HOZ
2116X1
L2
47mil 1/1OZ
L3
2116X1
L4
HOZ
压板厚度:压完板后,从铜箔到铜箔上测量的厚度。 压板厚度+电镀铜厚+绿油/保护层厚=完成板厚
第四节 :钻孔 一.工序介绍: 1.冲定位孔:
Target
目的:利用X-Ray读出内层Target, 然后在板边冲出三个孔, 作为钻孔定位孔。保证孔位与内层线路对位一致。
Via Hole
要求:
一般BGA区域VIA孔要求 塞孔
5. Fiducial mark :
作用:
装配时作为对位的标记 Fiducial mark
FMEA_培训教材[1]
![FMEA_培训教材[1]](https://img.taocdn.com/s3/m/3411f1af55270722192ef7c8.png)
PPT文档演模板
FMEA_培训教材[1]
什么是FMEA
在产品设计阶段和过程设计阶段,对构成产 品的子系统、零件,对构成过程的各个工序 逐一进行分析,找出所有潜在的失效模式, 并分析其可能的后果,从而预先采取必要的 措施,以提高产品的质量和可靠性的一种系 统化的活动。
PPT文档演模板
FMEA_培训教材[1]
OEM:分析产品和主机厂装配过程之间的关系对于有效的 FMEA非常关键。
供应链:包括组装、装配、热处理、喷漆、电镀、焊接或其 它精加工服务等。
法规:对安全和环境方面明确要求并监控其实施的政府机构。
明确顾客有助于定义功能、要求和规范,并能帮助确定相关失 效模式的后果。
PPT文档演模板
FMEA_培训教材[1]
PPT文档演模板
FMEA_培训教材[1]
PPT文档演模板
FMEA_培训教材[1]
PPT文档演模板
FMEA_培训教材[1]
缺陷可能性及影响分析
FMEA编号:
产品系统 FMEA
过程系统 FMEA
共 页第 页
类型/型号/生产/批号:
制表:
日期:
系统编号/系统元素: 功能/任务:
零件号
负责人:
部门:
• 由纽约广告代理的老板Alex F Osborn在1930年发 明,其前提是在一般的讨论中,人们害怕别人批评 而约束自己,因此而不能产生有创意的点子。
• 脑力风暴包括创造一种氛围,让人们感到无拘无束, 此时人们可能提出在平时认为不太可能提出的解决 方案,但往往收到意想不到的效果。
PPT文档演模板
FMEA_培训教材[1]
FMEA的类型
SFMEA —— 对产品开发、过程策划综合评估,通过系统、 子系统不同层次展开,自上而下逐级分析,更注重整体性、 逻辑性。
PCB外形加工培训教材

外形加工培训教材
32
外形加工培训教材
33
27
2.4.1.4 斜边不良之原因分析及解决方法
±±º » Ï ß ² À ò Õ ö Ó Ñ ²Í ±±¶ ¸  ù Ç Ï ß µ É Ò ¸ ¶ í æ Õ Ú ±Â ´ ² Ô ¸ ¸ ¦ º á ¸ í ï ¨ Ù õ Ù ù ¾ Ð Ð À ² ³,É Á ´ ³Ê » Ê Á 1. °¹ ² ½ ,Ã Ï °Å ± å ñ º õ ³ § å © ¡ ±±î Ç Ï ß È ¶ , 2. °Æ å ö ù ó ´ ñ ¸ ´ Ò ¹ 3. Ï ß Ê ¶ ² ½ ±±Ù Ç º õ º á ² ³ 4. Ï ß °±Ä ²¾ Ú °Î ±±å ß ø æ ¨Ò å Á à ö ¼ ¨ ¼ ½ ²² ÷ ±±¶ · º Ï ß µ £ ¤Å ¸ ¨ ±Õ ÷ Ð Í 6.5~7.5kg/cm2, ô³ Ú À Ë Ó 600~700NL Ð Â ¾ Õ å ¥ ¿ ±± °· ² ²°µ ¶ Ï ß · å ó Ù ±± ï °¹ Ó Ï ß ´ õ Ç Ù Ç ±± °½ Ó Ê ¶ Ï ß ô ±±Í ò µ º Ï ß ´ Ï
甩金
断金手指
斜边不完全
外形加工培训教材
26
2.4.2.3 板厚误差越大,斜边深度误差越大,因此要对板厚进 行控制,降低报废与返修率将板厚误控制在2mil以 内,斜边深度可完全合符要求。 2.4.2.4 板料弯曲时会使斜边深度严重不平,出现报废, 凡是板弯曲时应将板料拣开经处理后再斜边。
外形加工培训教材
外形加工培训教材
3
2.0各制程流程介绍 2.1 锣板流程 开机 读入资料 参数设定
调零位 锣板
钻管位
上管位钉
钣金安全培训教材

钣金安全培训教材1. 引言钣金行业是一项涉及金属加工、车辆维修和建筑装饰等领域的重要工作。
然而,由于钣金作业涉及高温、高压以及各类危险物质,工作人员面临许多潜在的安全风险。
为了保障钣金工作者的安全,本教材整理了钣金安全培训内容,旨在提升工作人员的安全意识和职业素养。
2. 钣金安全培训的重要性2.1 钣金作业的安全风险钣金涉及使用高温器具、切割设备和重型机械等工具,工作中还有可能接触有毒有害物质,如粉尘、废气等。
这些都给工作人员的生命安全和身体健康带来潜在威胁。
2.2 培养安全意识的必要性通过钣金安全培训,可以帮助工作人员了解各类潜在危险,增强安全意识,减少意外事故的发生。
保障工作人员的安全,有助于提升工作效率和质量,避免潜在的经济损失。
3. 钣金作业安全措施3.1 个人防护装备在进行钣金作业前,工作人员应佩戴安全帽、防护眼镜、防护面罩、手套、防护鞋等个人防护装备,确保自身安全。
3.2 危险品管理合理存储和使用危险品,确保危险品物品标识清晰,防止泄露、蒸发或扩散。
工作人员应定期接受有关危险品的安全培训,提高对危险品的识别和应急处理能力。
3.3 机械设备操作规范使用钣金加工设备时,必须遵守设备操作规范,确保设备的正常运行,并避免操作过程中的伤害风险。
对设备的维护保养也是确保操作安全的关键。
3.4 灭火器和急救设备的配备在钣金作业现场,应配备适量的灭火器和急救设备,并确保人员都具备相应的使用知识和技能,以便应对突发事故和紧急情况。
3.5 通风措施钣金作业往往伴随着高温、有毒气体的产生,因此通风设备的合理设置和正常运行十分必要,以降低工作环境中有害气体的浓度。
4. 钣金安全事故案例为了帮助工作人员认识到安全问题的严重性,本教材列举了一些常见的钣金作业事故案例,并对其进行分析和总结。
通过学习和思考这些案例,工作人员可以加深对工作安全的重视,并提高对潜在危险的警觉性。
5. 结束语本教材对钣金安全培训的重要性进行了阐述,并对工作中需要采取的安全措施进行了介绍。
机械加工工艺培训教材
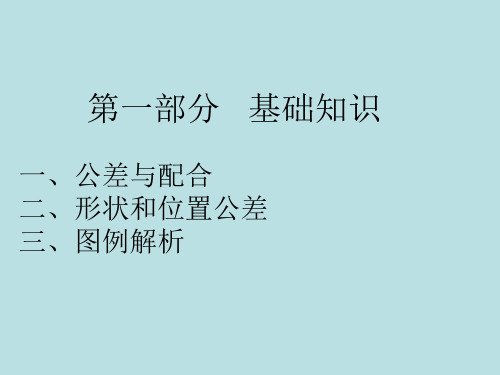
五 加工效率及经济性
A、数控机床(CNC)应用; B、自动化/快换化夹具应用; C、低成本自动化(LCA)应用; D、现场动作/布局优化(IE工程);
第三部分 刀具及冷却液
一、刀具材料及其应用 二、常用冷却液
一 刀具材料及其应用
A、工具钢:手工工具广泛应用 /牌号有:T10A/T8A 如:锉刀/手工锯条/刮刀 B、高速钢/峰钢/白钢:牌号有:W18Cr4V 如:钻头/螺纹刀具/车刀/铣刀 C、硬质合金:牌号有:YT15/YG8/YW1 如:机夹刀片/车刀片/焊接式刀头 D、人造金刚石(PCD)如:修磨砂轮用工具 E、立方氮化硼(CBN)只适宜干切削
> 630 ~1000
2.0
+1 -0.4
表2、镗孔/铰孔加工余量及其偏差(MM)
公称孔径D
≤6
镗孔余量D
/
铰孔余量D
0.05
>6~10 > 10 ~18 >18 ~30 >30 ~50 >50 ~60
0.5-10
0.8-1.4
0.1
0.15
0.2
0.25
0.3
我司现采用的机加工余量一般取0.3~0.5mm。
四 加工质量
加工质量由加工精度和加工表面质量两项指标: A、加工精度:指零件加工后实际几何参数(尺寸、形
状和表面间相互位置)与理想几何参数的符合程度。 B、加工表面质量: 1、已加工表面的结几何形状特征。表面粗糙度/波度/
纹理 2、已加工表面层的物理品质。加工硬化程度/冷硬层深
度/表面层残余应力/表面层金相组织变化
动的切削方式; 四、齿轮加工机床 滚齿机:利用齿轮滚刀按展成法加工齿面的方法。
第一部分 基础知识
一、公差与配合 二、形状和位置公差 三、图例解析
CATIA培训教程-创成式外形设计( GSD)
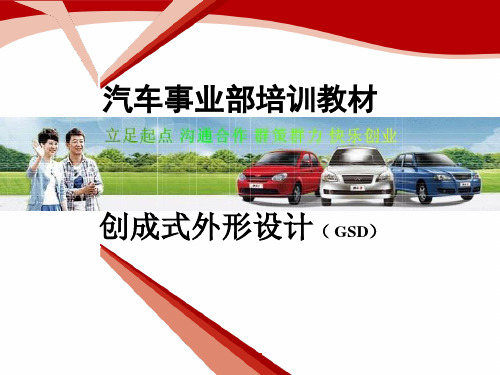
,选择填充曲面
的上表面,选择上述两点作为边界的界限提
取部分上表面的边界,见图13。
图13 提取填充曲面上边界
20
15.单击扫描图标
,在Profile type域选择图标
,Subtype域选择With reference surface,Guide Curve 1
域选择第14步生成的边界,Reference surface域选择第12
图43 剪切拾音槽
49
45.单击合并图标 ,选择上述生成的所有 外表面,将它们合并在一起,见图44。
图44 合并所有的外表曲面
50
45.单击倒棱边圆角图标 ,选择图44所示 棱线,输入圆角半径R=10mm。
图44 倒棱边圆角
51
46.单击变半径倒棱边圆角标 ,选择图45 所示棱边,在圆弧两端点分别点击鼠标,输 入圆角半径R=1mm;在圆弧中点单击鼠标,输 入圆角半径R=10mm。
2.绘制草图1。单击草图图标 ,再选择YZ平面,进入 草图设计模块,绘制一段圆弧,半径为500,包角30度, 中点在原点,如图1所示。
图1在YZ平面绘制草图1
8
3.生成拉伸面1。单击拉伸图标 ,拉伸草 图1,双向拉伸,lim1=lim2=45mm, 单击OK按 钮,得到拉伸面1,见图2。
图2 生成拉伸曲面1
图21 在等距曲面上生成半径为12mm的圆
28
23.单击剪切图标 ,依次选择等距曲面和 上面的圆,剪掉圆的外部,见图22。
图22 剪切圆的外部
29
24.类似第15步,单击扫描图标
,在Profile tith reference surface,Guide
如图24所示的曲面。
图24 剪切曲面
外形工艺培训教材
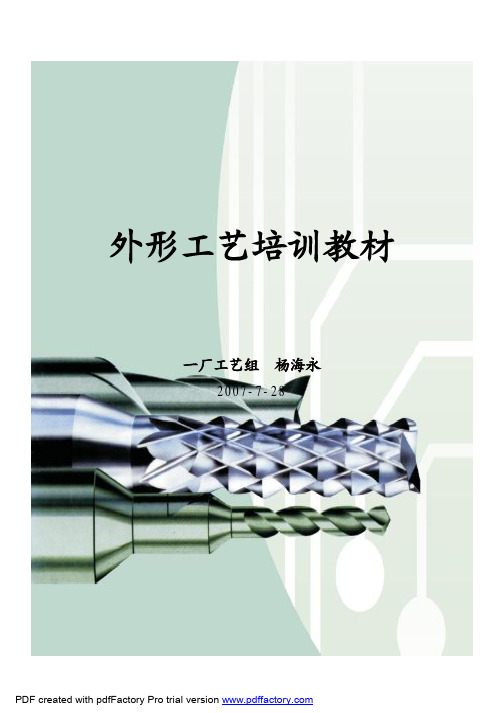
外形工艺培训教材一厂工艺组杨海永2007-7-28目录第一章外形环境了解 (3)一、锣机 (3)二、V-CUT机 (3)三、金手指刨斜边机 (4)四、冲床 (5)第二章外形所用刀具 (6)一、锣刀 (6)二、金手指刨斜边所用刀具 (8)三、V-CUT刀 (10)四、模具和冲针 (11)第三章日立锣机的原理与操作 (16)一、日立锣机的原理 (16)二、日立锣机的操作 (16)第四章外形工艺知识 (21)一、铣外形(Routing) (21)二、冲外形(Punching) (26)三、V-CUT (27)四、金手指刨斜边(Bevelling) (29)第一章外形环境了解一、锣机外形共有10台锣机,日立锣机6台,美国ACC锣机4台,共有SPINDLE 52个。
二、V-CUT机外形共有四台V-CUT机,见下表:如果有漏开V-CUT的板件,已经锣出外形,可以拿一块大约20″×16″大小的报废板,编写锣带,锣出大小与漏开V-CUT板件的出货单元相同的空框,报废板边钻出两个V-CUT管位孔,然后根据外形图纸编出V-CUT程序。
补开V-CUT时,把板件放入空框,然后用胶纸将板件与空框粘牢,就可以补开V-CUT。
三、金手指刨斜边机四、冲床冲床主要有机械冲床和液压冲床。
机械冲床操作简单,行程短,效率高,但因其设备本身的刚度不高,在较大冲力的作用下引起的冲床设备变形容易改变冲模间隙分布,降低模具使用寿命和PCB板件表面质量。
因此,机械冲床只适用于外形简单、尺寸较小、精度要求不高的PCB板件冲外形加工。
已逐渐不能满足目前我司精密板件的加工需求。
而液压冲床结构简单,不易发生超载破坏,可以获得较好的冲裁品质和生产效率,适合于尺寸精度要求高、大尺寸的PCB板件冲外形加工。
目前,一厂的冲床设备有两台40ton的机械冲床,一台110ton的液压冲床。
下图为液压冲床:第二章外形所用刀具一、锣刀锣刀同钻咀的材质相同,在这里不再赘述。
钣金生产安全培训教材
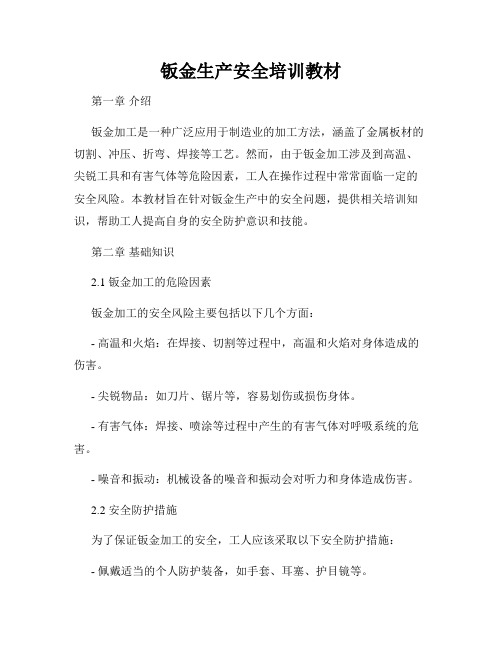
钣金生产安全培训教材第一章介绍钣金加工是一种广泛应用于制造业的加工方法,涵盖了金属板材的切割、冲压、折弯、焊接等工艺。
然而,由于钣金加工涉及到高温、尖锐工具和有害气体等危险因素,工人在操作过程中常常面临一定的安全风险。
本教材旨在针对钣金生产中的安全问题,提供相关培训知识,帮助工人提高自身的安全防护意识和技能。
第二章基础知识2.1 钣金加工的危险因素钣金加工的安全风险主要包括以下几个方面:- 高温和火焰:在焊接、切割等过程中,高温和火焰对身体造成的伤害。
- 尖锐物品:如刀片、锯片等,容易划伤或损伤身体。
- 有害气体:焊接、喷涂等过程中产生的有害气体对呼吸系统的危害。
- 噪音和振动:机械设备的噪音和振动会对听力和身体造成伤害。
2.2 安全防护措施为了保证钣金加工的安全,工人应该采取以下安全防护措施:- 佩戴适当的个人防护装备,如手套、耳塞、护目镜等。
- 确保操作区域的通风良好,避免有害气体滞留。
- 注意机械设备的维护保养,保证其正常运行。
- 操作前进行培训,了解操作规程和安全注意事项。
- 注意工作环境的整洁,避免物品杂乱堆放导致的安全隐患。
第三章钣金加工过程中的安全问题及解决方法3.1 切割过程中的安全问题切割是钣金加工中常见的工艺之一,但也存在一定的安全隐患。
为了确保切割过程的安全,应注意以下事项:- 确保切割区域的安全,附近人员必须保持安全距离。
- 使用锋利的切割刀具,并定期检查和更换刀具。
- 佩戴耐磨、防滑的手套,确保操作时的安全性。
- 避免切割过程中过度疲劳,及时休息。
3.2 折弯过程中的安全问题折弯是钣金加工中常用的成型方法,但也存在一定的安全风险。
为了确保折弯过程的安全,应注意以下事项:- 佩戴适当的手套、护目镜等个人防护用具。
- 确保折弯机床的安全运行状态,及时进行维护保养。
- 熟悉机床的操作规程,按照正确的操作步骤进行折弯。
- 避免操作过程中手指夹伤或被夹住,注意安全距离。
第四章灭火与急救知识4.1 灭火知识在钣金生产过程中,火灾是一种常见的安全事故。
外形加工培训教材
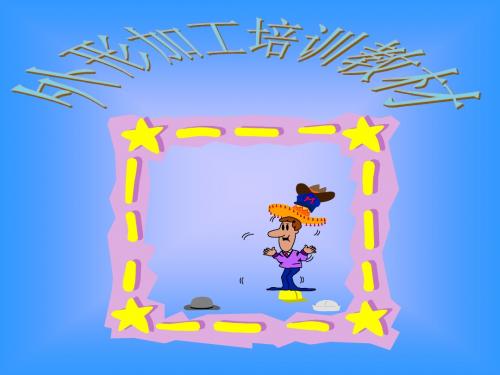
目的: 目的:
清洗板上及孔内的粉尘和杂物
外形制作的工作原理: 六、外形制作的工作原理:
1、锣板的工作原理
由DNC数控电脑系统控制机台移动,按所输入电脑 的资料,制作出客户所要求的轮廓及外形 控制方面分别有X.Y轴坐标及Z轴坐标 电脑控制机台XY轴移动及Z轴锣头带动的锣刀,通 过输入锣板资料及适当的参数,F.N.D.R.C等,机器 会自动按照资料,把所需的轮廓形状制作出来
电木板
作用: 防止损坏锣机台,在电木板上植上管位钉,作为
锣板之用
要求: 电木板厚度3/8”,板面要平直,不变形弯曲
管位钉
作用: 固定每叠板于机台上,不会移动,提高锣板精度 要求: 长度为15mm,钉不能弯曲及松动,直径与管位孔一
致,不能太大或太小
锣刀
作用: 通过锣机在一定的转速及落速带动下割切线路板,使用锣
4、啤机的工艺参数: 啤机的工艺参数: 啤模寿命
啤模每啤20000次便需要翻磨一次
5、啤机的工艺参数: 啤机的工艺参数:
生产能力指引 锣机操作指示 V坑机操作指示 斜边机操作指示 0841-CG-001 0841-25-001 0841-25-001 0841-25-003
6、清洗: 清洗:
流程: 流程:
基板大小设定(XY VALUE Setting) 基板厚度(Thickness) V坑距离(XY Pitch) V坑后剩余厚度(remain thickness) V坑角度(degree)
基板大小
基板大小设定最小为150mm x 150mm 最小为650mm x 650mm
V坑距离
按生产资料的要求设定V坑的距离,分为X-Pitch及 Y-PITCH坑与坑的距离数值,依照生产指示设定
HDI基础知识培训教材1

层压不良
正常盲孔孔形
HDI板工业运用及前景展望
对于不断满足消费者对更小更快更多的便携式电子装置。 如:手机,手提式摄影机,笔记本电脑,个人数字助手等的 要求,从而导 致微孔PCB产品增长的需求. 电子产品朝更轻,更薄,更快方向发展的趋势.对于小尺 寸封装的便携式电子设备和在高密度互连的广泛运用下 减少组成芯片产品需求促使印刷线路板朝着技术高速向 前发展.因此随着电子消费品的发展, 对此类HDI制板的 需求越来越多;
常见2+(N)+2HDI板流程:
开料 → 烤板→内层图形转移→ AOI → 棕化 →第一次排、压板 → X-Ray 及锣边 →烤板→二次元测数据出工具→ 钻埋孔→ 沉 铜 → 板面电镀 →(塞埋孔树脂)→磨板→内层线路干菲林→ AOI → (烤板→ 磨板) → 棕化→第二次排、压板 → X-Ray 及锣边 →烤板→二次元测数据出工具→机械钻管位孔→第一次 conformal mask菲林盲孔开窗次外层→ 酸性蚀刻开窗及褪膜→ AOI开窗→镭射钻孔→沉铜二次→ 板面电镀 →次外层 干菲林→ 图形电镀 → 蚀刻次外层线路→ AOI →烤板→ 磨板 →棕化 → 第二次排压板 → X-Ray 及锣边→烤板 →二次元测数据出工具 →机械钻通孔→第二次conformal mask菲林盲孔开窗外层→ 酸性 蚀刻开窗及褪膜→ AOI开窗→镭射钻孔→沉铜二次→ 板面电镀 →外层 干菲林→ 图形电镀 → 蚀刻外层线路→绿油 → 字符→ 表面处理 → 外型加工 → 测试→FQC→FQA→包装出货
• • • • • • • HDI(High Density Interconnection) 中文意思为高密度互连线路。 凡非机械钻孔,孔径在小于0.2MM镭射孔。 线宽线距4/4MIL以下。 实例:孔径0.2MM H6FA18001A0 H4G997013A0 线,H4G859326A0 H4G859387A0 3.9/3.2MIL 盲孔的定义:使外层导体图形与内层导体图形间相 连的导电孔,它不贯通PCB板的上下表面,仅有一端与 外层相通
加工中心培训教材

加工中心培训教材(基本理论和工艺)一、数控机床刀柄标准及种类目前,数控铣床和镗铣加工中心使用最多的仍是7∶24工具锥柄。
但在高速加工机床上,1∶10空心短锥柄的使用正日益增多。
手动换刀用7∶24工具锥柄的常见标准有国家标准GB3837.3-83和国际标准ISO 297-82,以及机械行业标准JB3381.1-83。
1∶10空心工具锥柄目前已有国家标准GB19449.1-2004“带有法兰接触面的空心圆锥接口第1部分:柄部-尺寸”。
它等同采用了国际标准ISO12164-1:2001的内容。
原德国标准DIN69893-1:1996已被新的标准DIN69873-1:2003代替,新的德国标准也等同采用了国际标准ISO12164-1:2001的内容。
其它常见结构的1∶10工具锥柄基本采用企业标准,具有垄断性,如美国肯纳公司的KM型系列、瑞典山特维克公司的Capto系列、德国瓦尔特公司的NOVEX系列等。
自动换刀机床用7∶24工具锥柄的中国国家标准GB10944-89是参照采用国际标准ISO7388/1:1983制定的,除对极个别项目数据进行了圆整(如尾部螺纹底孔深度13)或未规定数据(如法兰上的键槽根底倒角)外,其它数据完全相同。
而国际标准ISO7388/1:1983又是参照德国标准DIN69871-1的A型工具锥柄制定的,所以这三个标准的外形尺寸相同。
在国内,其工具锥柄的代号为“JT”。
其特征是:法兰厚度较小;有一装刀用的定位缺口;两个端键槽为不对称分布。
自动换刀机床用7∶24工具锥柄在德国标准DIN69871-1中分为A型、AD型和B型三种:A型为螺纹底孔不通的;AD型为螺纹底孔贯通的;B型为法兰端面供水的。
而DIN 69871-2则只有C型一种,为双平行法兰、无V型槽的,现在已很少采用。
其工具锥柄代号虽然标准中未作规定,但在德国其代号通常称为“SK”。
自动换刀机床用7∶24工具锥柄的日本标准JIS B6339:1998虽已替代了日本工作机械工业会标准MAS-403:1975,但由于其主要外形尺寸相同,对使用基本没有影响,所以在不少制造商的样本上仍然标注MAS-403标准代号,而未标注JIS B6339。
外形加工培训教材

5-7mm
外形加工培训教材 17
3.2.2.5 V-Cut角度以使用刀具决定,共有三种:30、45、 60,且磨损后角度逐渐变大。
3.2.2.6 V-Cut刀经V-坑20000mm后必须换刀,刀具过度磨损 会出现V坑角度过大和V坑质量下降(变成圆角V-Cut 线,且常有V坑线变白.严重的会出现报废)。
外形加工培训教材 11
3.1.6.4 锣刀换刀频率规定:根据 “F CNT”之每手板行程及下 表进行换刀:
锣刀直径 锣刀型号 供应商 锣外皮板最大行程 锣坑槽板最大行程
0.8mm 141HF 金洲 /
400
1.6mm 141HF 金洲 900
650
2.4mm 141HF 金洲 1050
/
3.75mm 141HF 金洲 1050
选择“S”输入钻咀或锣刀的落带(单位:100R/min) 选择“F”输入钻咀或锣刀的落速(单位:INCH/min) 选择“R”输入锣刀或钻咀回刀速(单位:INCH/min)
外形加工培训教材 6
3.1.4 调零位程序 3.1.4.1 调零位的作用:使用锣板平台全部覆盖锣板图形 3.1.4.2 读入资料后,按下“ PROGR ”键显示资料程序,同时
外形加工培训教材 4
3.1.1 开机程序
3.1.1.1 打开总气阀
3.1.1.2 打开电源开头
3.1.1.3 设定冷水机温度控制在60-65F范围内
3.1.1.4 打开机器门
电脑出现“CALIB Z”后按一下”CALIB Z”键,则 出
现“CALIB XY”,按下“CALIB XY”键进行机器复
位 3.1.1.5 打开SPINDLES按键
易弯曲而出现夹不住板和碰撞刀架而毁环板料。
mstercam培训教材第08章

图8-23 程序过滤设置
对话框的参数说明见表8-3。
图8-24所示为路径过滤示意图,当图中 的L距离小于或等于过滤误差值时,系统将 会以AC的路径来取代AB和BC的路径,这 样就简化了路径。同样,系统会依照所设定 的误差值来过滤全部的加工路径,使得全部 的刀具路径都在所设定的加工精度内。
(2)精修次数:切削深度方向的精 加工次数。
(3)精修量:精加工时每层切削的 深度,做Z方向精加工时两相邻切削路径 层间的Z方向距离。
(4)不提刀:选中时指每层切削完 毕不提刀。
(5)使用副程式:选中时指分层切削 时调用子程序,以减少NC程序的长度。在 子程序中可选择使用绝对坐标或增量坐标 。
(6)铣斜壁:选中该项,要求输入锥 度角,分层铣削时将按此角度从工件表面 至最后切削深度形成锥度。如图8-16所示, 图8-16(a)的锥度角为0°,而图8-16(b )的锥度角为10°。
mstercam培训教材第 08章
2023/5/31
8.1 外 形 铣 削
外形铣削也称为轮廓铣削,其特点 是沿着零件的外形即轮廓线生成切削加 工的刀具轨迹。轮廓可以是二维的,也 可以是三维的,二维轮廓产生的刀具路 径的切削深度是固定不变的,而三维轮 廓线产生的刀具路径的切削深度是随轮 廓线的高度位置变化的。
(b) 图8-17 轮廓铣削顺序
8.进退刀向量设定
轮廓铣削一般都要求加工表面光滑, 如果在加工时刀具在表面处切削时间过长 (如进刀、退刀、下刀和提刀时),就会 在此处留下刀痕。MasteCAM的进退刀功 能可在刀具切入和切出工件表面时加上进 退引线和圆弧使之与轮廓平滑连接,从而 防止过切或产生毛边。
- 1、下载文档前请自行甄别文档内容的完整性,平台不提供额外的编辑、内容补充、找答案等附加服务。
- 2、"仅部分预览"的文档,不可在线预览部分如存在完整性等问题,可反馈申请退款(可完整预览的文档不适用该条件!)。
- 3、如文档侵犯您的权益,请联系客服反馈,我们会尽快为您处理(人工客服工作时间:9:00-18:30)。
外形加工培训教材
6
3.1.2 读入资料程序 3.1.2.1 进入”FUNTIONS”主菜单内,选择“DATD IN DISKETTE”项,按“LINE FEED”列出文件表 3.1.2.2 选择所需的资料读入 3.1.3 参数设定 3.1.3.1 选择“TOOLS”项进入参数设定画面 3.1.3.2 选择“D”设定钻咀或锣刀的直径大小(IVCH) 选择“S”输入钻咀或锣刀的落带(单位:×100R/min) 选择“F”输入钻咀或锣刀的落速(单位:INCH/min) 选择“R”输入锣刀或钻咀回刀速(单位:INCH/min)
外形加工培训教材
20
3.2.3.3 当发现有异常情况应采取以下措施调整 A 当出现V坑余厚不符合要求时 用V-Cut深度测量仪
应在电脑修改参数调整V-Cut余厚 B 当出现V坑位置精度有异常时 利用绿油窗和V坑对 在电脑
位孔目检 即用OPTEK-V2600测量误差值 调整其位置资料
外形加工培训教材
外形加工培训教材
1
一.目录 1.外形加工制程介绍 2.外形加工机器介绍 3.各制程流程介绍 3.1锣板制程 3.2V-Cut 3.3啤板 3.4斜边 3.5洗板 4.环保 5.工业安全
外形加工培训教材
2
1.0 外形加工制程介绍 外形加工包括 1.1锣板 将半成品线路板切割成客户所需要的尺寸的外形 成品线路板 1.2啤板 将半成品线路板通过压力机剪切成客户所需的尺 寸外形的成品线路板 1.3V-坑 在线路板上加工客户所需“V形坑” 便于客户安装 1.4斜边 1.5洗板 使用线路板 将线路板之金指加工成容易插接的斜面 将外形加工产生的粉尘以及生产过程中产生之油 渍清洗干净 并烘干
外形加工培训教材
3
2.0 外形加工机器介绍
机器名 锣机 型号 Trudril 1440 数量 4 最大产能 1.9K/天/台 备注 每手板用时20分钟 每天工作时间20小时 (去除换板时间)3块/叠 2.7k/panel计算
Trudril104-R4 啤机 J23-40 JH21-80 V-Cut机 斜边机 NVC-650PC OTTER-100
外形加工培训教材
7
3.1.4 调零位程序 3.1.4.1 调零位的作用:使用锣板平台全部覆盖锣板图形 3.1.4.2 读入资料后,按下“ PROGR ”键显示资料程序,同时 按下“ CTRL”+ “G”键进入显示资料的图形 3.1.4.3 按下 “COMM ”键,利用 “X” “ Y” “ +” “- “键 调整零位直至绿色图形没有超出蓝色图形范围为止
外形加工培训教材
31
3.4.2 手动斜边机(MB-001)适用范围 3.4.2.1 手动斜边最大尺寸板:14’长×12’宽 3.4.2.2 加工进退刀槽最小为6mm 3.4.3 OTTER-100自动斜边机空气主轴对生产质量影响 3.4.3.1 空压马达的转速为30000转/分 3.4.3.2 空压压力不足或供气量不足会使空压马达转 速减慢,会出现表面粗糙,断金手指以及斜边 不平的缺陷,因此必须保证供气气压为6.5-7.5 kg/cm2,流量在600-700NL
外形加工培训教材
29
3.3.6 绿油厚度对啤板的质量影响
3.3.6.1 PH3绿油厚度平均为0.8mil,容易出现严重爆油, 因此需要加大绿油窗宽度≥15mil
外形加工培训教材
30
3.4 斜边 3.4.1 自动斜边机(OTTER-100)适用范围 3.4.1.1自动斜边机生产最大板15”×14” 3.4.1.2斜边角度范围 20°-50° 3.4.1.3斜边可进行连续切削和跳越切削两种形式的板 3.4.1.4可进行山形加工,内凹深度≤30cm 3.4.1.5斜边跳刀加工需有进退刀间距不小于20mm 3.4.1.6切削长度不应少于基极总长的2/3,否则会偏斜而 产生坏板,除非另一端设计有凸台与基面相平 3.4.1.7斜边最大深度为2mm
8-15mm
≥2mm
外形加工培训教材
17
3.2.2.3 V-Cut线到定位孔(夹板边)最小距离为2mm距离过于小 或V坑线在定位孔以外(相对板)位置则容易出现刀撞 夹具引起毁坏刀具和夹具 3.2.2.4 V-Cut跳刀加工时,进退刀位应有5-7mm的距离
5-7mm
5-7mm
外形加工培训教材
18
3.2.2.5 V-Cut角度以使用刀具决定,共有三种:30° 45° 60°,且磨损后角度逐渐变大 3.2.2.6 V-Cut刀经V-坑20000mm后必须换刀,刀具过度磨损 会出现V坑角度过大和V坑质量下降(变成圆角V-Cut 线,且常有V坑线变白.严重的会出现报废)
外形加工培训教材
27
3.3.4 啤机对啤板的影响 3.3.4.1啤机公称力不足会使啤板出现披风,粗糙度大和爆 油现象,切割总长度过长时,单位公称力不足而出现 缺陷,此时必须分成两个或两个以上啤模, 增大单位 长度公称力 一般凡有啤坑板均分为坑模与皮模两个 啤模
外形加工培训教材
28
3.3.5 啤板深度调整 3.3.5.1 啤板深度以容易拆板 啤后不脱落为原则 3.3.5.2 调深度时应该由浅入深调整,调整过快,容易出 现过深会出现压伤板面,更严重会损害啤模和 机器
21
C 当出现上下刀对位有异常时 目检
即用OPTEK-V2600测
量有无超出要求范围 若超出要求范围和未达到机器能力 范围 通知维修人员调整达到要求范围 D 当V-Cut线偏转一定角度时 即用OPTEK-V2600测量V-Cut 线 两端有无超出位置精度要求 若超出即由维修人员调 整位针位置至符合要求 E 当出现上 下刀深浅不一 合格 即调整刀架限位螺丝调整至
外形加工培训教材
8
3.1.5 上管位钉程序 3.1.5.1管位钉的作用:将半成品线路板固定在锣板平台,使锣 出精度合符要求的成品 3.5.1.2钻孔:在电木板上钻出管位钉孔 3.1.5.3打管位钉将管位钉打入管位钉孔内,并保证进入后无 松动且垂直 保证板料位置不偏 3.5.1.4管位钉孔深度控制: 钻孔深度应在进入电木板2-3mm,若小于此范围则容易 出现管位钉松动,若大于此范围则管位长度会显不足, 锣板时容易出现吸尘将板吸起而锣坏板
因为
应改用新或翻磨V-Cut
3.3 啤板 3.3.1 啤板的质量与精度与啤模的制作使用有关 3.3.2 啤板单元间距离要求≥30mil
外形加工培训教材
25
3.3.3 啤模制作要求 3.3.3.1 啤模制作的精度要求 S≤0.8(mm) 孔对边误差要求±4mil 边到边误差要求±8mil 0.8≤S≤2.0(mm) 孔对边误差要求±5mil 孔对边误差要求±10mil
外形加工培训教材
4
3.0各制程流程介绍 3.1 锣板流程 开机 读入资料 参数设定 调零位
锣板
上管位钉
钻管位
外形加工培训教材
5
3.1.1 开机程序 3.1.1.1 打开总气阀 3.1.1.2 打开电源开头 3.1.1.3 设定冷水机温度控制在60-65F范围内 3.1.1.4 打开机器门 电脑出现“CALIB Z”后按一下”CALIB Z”键 则出 现“CALIB XY” 按下“CALIB XY”键进行机器复位 3.1.1.5 打开SPINDLES按键
外形加工培训教材
15
3.2.1.3 V-Cut定位孔到板边距离为8-15mm.距离过小会 出现夹板不稳而使V坑偏位,出现报废距离过 大会出现板与夹具相撞而使板偏位.出现报废
3.2.1.4 定位孔数量应为三个成直角三角形孔,且直角 边与V坑线平行或垂直
外形加工培训教材
16
3.2.2 V-Cut制程能力范围 3.2.2.1 V-Cut最大尺寸为650×650(mm) 3.2.2.2 V-Cut板料厚度为0.8-2.4mm厚度小于0.8mm时,板料容 易弯曲而出现夹不住板和碰撞刀架而毁环板料
2 1 1 1 1
1.9K/天/台 6KFT2/天
MB-001(自制) 洗板机 AL-CL5
2 1
每分钟6Units 0.75ft2/unit 每天20小时计算 4 KFT2/天 每分钟4Units 0.75ft2/unit 每天20小时计算, 2/天 4.3 KFT 45秒/Panel 每天工作20h计算 2.7K/panel 2.4 KFT2/天 每天工作16h(去除调刀时间)上 下板, 以P41634板计算(5块/分, 0.5ft2/ unit 1.8 KFT2/天/台 3块/分 0.5 ft2/Unit 每天工作20h 2 12 KFT 10ft2/分,每天开机20小时计算
12
3.1.6.4 锣刀换刀频率规定:根据 “F CNT”之每手板行程及下 表进行换刀
锣刀直径 锣刀型号 供应商 0.8mm 141HF 金洲 1.6mm 141HF 金洲 2.4mm 141HF 金洲 3.75mm 141HF 金洲 锣外皮板最大行程 / 900 1050 1050 锣坑槽板最大行程 400 650 / /
外形加工培训教材
22
3.2.3.4 V-Cut机精度能力范围(NCV-650PC) A V-Cut余厚精度可达到要求值±0.1mm(±4mil) B V-Cut线位置精度可达到 不间断±2mil ±3mil C D V-Cut线上下刀对位偏差可达要求±2mil 跳刀±3mil 跳刀
V-Cut线上下刀深浅误差可达到要求±4mil
外形加工培训教材
9
3.1.6 锣板程序: 3.1.6.1 按一 “COMM”键,把锣刀深度输入,锣板深为BACKUP内, 一般为0.8-1.2mm,过深易出现锣入电木板平台和使锣 刀长度不足而得最上面线路板坏板,过浅则易出现最 底板锣不穿现象
外形加工培训教材
10
3.1.6.2 输入行速: 锣刀直径 0.8 1.6 2.4 3.175 第一次行速(KRPM) 10-50 30-80 30-80 30-80 第二次行速(KRPM) 30-80 50-100 50-100 50-100