铁水预脱硫喷吹系统的优化设计
炼钢厂铁水预处理一键脱硫控制系统

炼钢厂铁水预处理一键脱硫控制系统1 脱硫预处理组成与流程两个脱硫站共用一套氮气供应管路,即石灰和镁粉的储料仓。
为增加系统的灵活性,设置了一套共用的切换阀用于垂直(默认)和交叉(紧急备用)喷吹之间的选择。
喷吹系统、测温取样系统、铁包车、扒渣机和液压系统虽然每个站各自独立,但两站彼此又相同。
每个脱硫站均有两套独立的提升装置,一套用于脱硫喷枪的升降,另一套用于测温取样枪的升降。
为了获得更好的速度和位置控制,喷枪升降驱动装置采用变速调频电机驱动控制(VFD)。
铁水通过铁包车运至脱硫站。
铁包车直接接受原料跨450t天车吊运的铁水,而后从吊/座包位运至喷吹位进行喷吹、扒渣处理,当喷吹、扒渣完成后,再将铁水运至吊/座包位,由原料跨450t天车从车上吊走处理好的铁水,完成一个脱硫周期。
铁水预处理工艺流程如图1。
2 远程I/O通讯主控台包含主控桌,主控桌包含有作为一台HMI和二级客户计算机的操作工作站。
HIMI显示用西门子WINCC可扩充软件设计,并提供了脱硫和除尘系统设备的监控。
操作者报警将显示和公布在控制室的HMI上。
每个脱硫站将包括4个控制柜,每个控制柜均配有远程I/O通讯站,远程I/O 模块通过一个Profibus 网络与PLC进行通讯。
PLC经过采用TCP/IP(工业以太网)协议的以太网与HMI进行通讯。
这种通讯方式在其配置和维护方面具有很大的适应性,并准许过程数据通过远程编程经过OPC服务器进行存取。
脱硫站包括一套用Oracle为数据库的二级系统。
它由一个位于计算机房的服务器和一个客户机组成。
服务器用于数据的储存和管理,客户机作为HMI使用。
3 一键喷吹系统优化每个站控制系统是由一台西门子S7-400系列可编程逻辑控制器(PLC)和一台用于控制两个站共用部件S7-300PLC组成。
每个PLC均有本地和远程数字和模拟I/O接口。
该系统也包括每个脱硫站的人机界面(HMI),人机界面位于主控制操作台上,若必要,每个人机界面均能控制两个站。
铁水预处理喷吹法和搅拌法脱硫分析

ABSTRACT The desulphurization mechanics of hot metal injection and stirring are introduced. The desul2 phurization lim it of injected w ith M g and M g /CaO or stirred with CaO is theoretically calculated. The desulphuriza2 tion capability of every system is 10 - 4 % , 10 - 7 % , 10 - 3 % quantitative rank. The effects of desulphurization and the advantages and disadvantages between injection method and stirring method are compared, in order to guide the steel company choosing suitable desulphurization methods according to their actual situation.
溶解速度 ,提高铁液中镁的溶解度是关系到镁脱硫效果
的关键 。
M gS(g) + [O ] =M gO ( s) + [ S ] ΔG0
= - 210900 + 39. 6T, J /mol
(4)
在冶金温度下 ,镁的各种化合物的稳定性大小顺序 依次为 : M gO、M gS、M gC。式 (4)中 ΔG0 总小于零 ,意味着
— 32 —
冯京跃等 :铁水预处理喷吹法和搅拌法脱硫浅析
铁水预处理脱硫分析
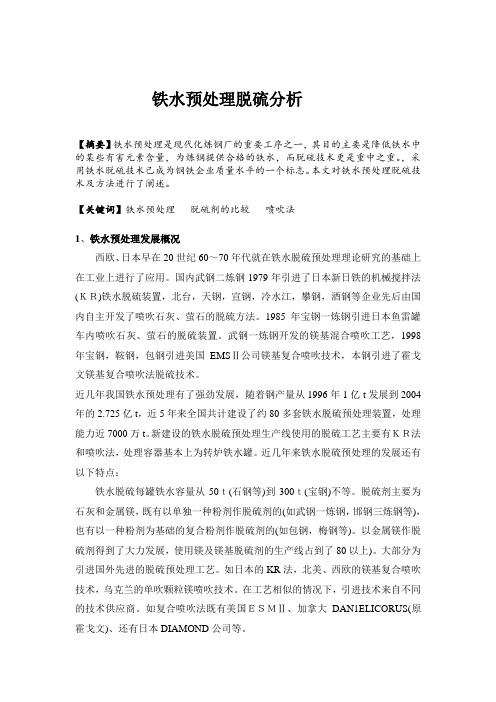
铁水预处理脱硫分析【摘要】铁水预处理是现代化炼钢厂的重要工序之一,其目的主要是降低铁水中的某些有害元素含量,为炼钢提供合格的铁水,而脱硫技术更是重中之重。
,采用铁水脱硫技术已成为钢铁企业质量水平的一个标志。
本文对铁水预处理脱硫技术及方法进行了阐述。
【关键词】铁水预处理脱硫剂的比较喷吹法1、铁水预处理发展概况西欧、日本早在20世纪60~70年代就在铁水脱硫预处理理论研究的基础上在工业上进行了应用。
国内武钢二炼钢1979年引进了日本新日铁的机械搅拌法(KR)铁水脱硫装置,北台,天钢,宣钢,冷水江,攀钢,酒钢等企业先后由国内自主开发了喷吹石灰、萤石的脱硫方法。
1985年宝钢一炼钢引进日本鱼雷罐车内喷吹石灰、萤石的脱硫装置。
武钢一炼钢开发的镁基混合喷吹工艺,1998年宝钢,鞍钢,包钢引进美国EMSⅡ公司镁基复合喷吹技术,本钢引进了霍戈文镁基复合喷吹法脱硫技术。
近几年我国铁水预处理有了强劲发展,随着钢产量从1996年1亿t发展到2004年的2.725亿t,近5年来全国共计建设了约80多套铁水脱硫预处理装置,处理能力近7000万t。
新建设的铁水脱硫预处理生产线使用的脱硫工艺主要有KR法和喷吹法,处理容器基本上为转炉铁水罐。
近几年来铁水脱硫预处理的发展还有以下特点:铁水脱硫每罐铁水容量从50t(石钢等)到300t(宝钢)不等。
脱硫剂主要为石灰和金属镁,既有以单独一种粉剂作脱硫剂的(如武钢一炼钢,邯钢三炼钢等),也有以一种粉剂为基础的复合粉剂作脱硫剂的(如包钢,梅钢等)。
以金属镁作脱硫剂得到了大力发展,使用镁及镁基脱硫剂的生产线占到了80以上)。
大部分为引进国外先进的脱硫预处理工艺。
如日本的KR法,北美、西欧的镁基复合喷吹技术,乌克兰的单吹颗粒镁喷吹技术。
在工艺相似的情况下,引进技术来自不同的技术供应商。
如复合喷吹法既有美国ESMⅡ、加拿大DAN1ELICORUS(原霍戈文)、还有日本DIAMOND公司等。
我国在早期引进国外先进技术的基础上改进的自主知识产权开发技术也在发挥着作用。
铁水预脱硫喷吹系统的优化设计

对于任一套脱硫系统都有其合适的粉气比范 围 , 通常情况下 , 对于混铁车脱硫 , 每立方米载气 的适宜载粉量约为 15 ~ 50kg ;对于铁水罐脱硫 , 由 于易产生喷溅 , 每立方米载气的适宜载粉量约为 20 ~ 40kg 。
虽然复合喷吹设备占地面积大 , 但它能有效 地将因偏析影响脱硫效率的可能性降至最低点 。 从它与应用混合脱硫剂的混合喷粉脱硫技术使用 效果上 看 , 将 270t 铁 水硫 含 量 从 0 .055 %降 至 0 .003 %时 , 复合喷粉镁的消耗量减少 11 %, 当硫 含量降至 0 .014 %时 , 其镁消耗量减少 16 %, 使用 情况见表 2 。
本文根据铁水预脱硫工艺及喷吹技术发展状 况及实践经验 , 从铁水预脱硫喷吹系统设计的角
度出发 , 做一些有益的探讨 。
2 铁水预脱硫工艺的选择
在实际操作中 , 铁水外部脱硫常用的工艺有 4 种 , 这 4 种工艺是 :
(1)苏打或碳酸钠(Na2CO3)工艺 ; (2)石灰/ 煅烧石灰(带添加剂或不带添加剂 的 CaO)工艺 (3)碳化钙工艺 ; (4)钝化镁工艺 。 这 4 种脱硫工艺的对比见表 1 。 从表 1 可看出 , 任何一种工艺单独应用都达 不到全满意的效果 。 最近工业铁水外部脱硫技术的发展主要倾向 于两种工艺 : (1)CaO -Mg 基混合工艺 ; (2)CaC2 -Mg 基混合工艺 。 实践证明 , CaO 和镁基试剂混合使用及碳化 钙和镁基试剂混合使用比单独使用效果好 , 其原 因在于 :
从理论上看 , 脱硫过程可分为孕育期 、脱硫期 及脱硫 后期三个阶段 。 在孕育期硫 含量并无变 化 , 但要造成铁水的强烈搅拌 , 在脱硫期内铁水硫 含量急剧降低 , 脱硫后期硫含量的降低变慢 。
铁水复合喷吹脱硫技术的研究及应用
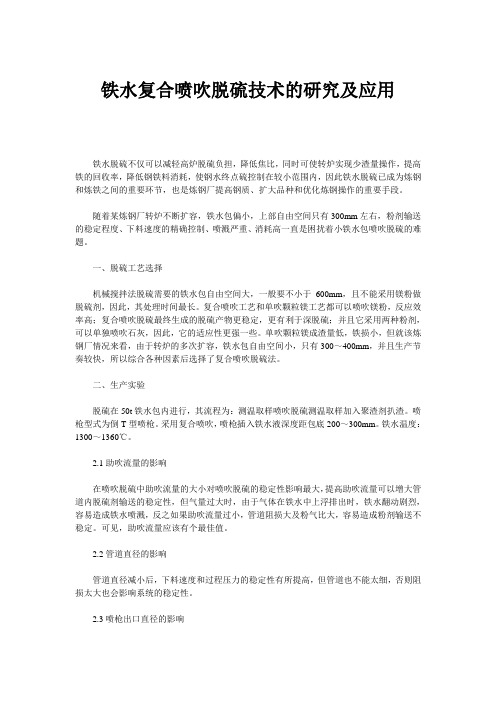
铁水复合喷吹脱硫技术的研究及应用铁水脱硫不仅可以减轻高炉脱硫负担,降低焦比,同时可使转炉实现少渣量操作,提高铁的回收率,降低钢铁料消耗,使钢水终点硫控制在较小范围内,因此铁水脱硫已成为炼钢和炼铁之间的重要环节,也是炼钢厂提高钢质、扩大品种和优化炼钢操作的重要手段。
随着某炼钢厂转炉不断扩容,铁水包偏小,上部自由空间只有300mm左右,粉剂输送的稳定程度、下料速度的精确控制、喷溅严重、消耗高一直是困扰着小铁水包喷吹脱硫的难题。
一、脱硫工艺选择机械搅拌法脱硫需要的铁水包自由空间大,一般要不小于600mm,且不能采用镁粉做脱硫剂,因此,其处理时间最长。
复合喷吹工艺和单吹颗粒镁工艺都可以喷吹镁粉,反应效率高;复合喷吹脱硫最终生成的脱硫产物更稳定,更有利于深脱硫;并且它采用两种粉剂,可以单独喷吹石灰,因此,它的适应性更强一些。
单吹颗粒镁成渣量低,铁损小,但就该炼钢厂情况来看,由于转炉的多次扩容,铁水包自由空间小,只有300~400mm,并且生产节奏较快,所以综合各种因素后选择了复合喷吹脱硫法。
二、生产实验脱硫在50t铁水包内进行,其流程为:测温取样喷吹脱硫测温取样加入聚渣剂扒渣。
喷枪型式为倒T型喷枪。
采用复合喷吹,喷枪插入铁水液深度距包底200~300mm。
铁水温度:1300~1360℃。
2.1助吹流量的影响在喷吹脱硫中助吹流量的大小对喷吹脱硫的稳定性影响最大,提高助吹流量可以增大管道内脱硫剂输送的稳定性,但气量过大时,由于气体在铁水中上浮排出时,铁水翻动剧烈,容易造成铁水喷溅,反之如果助吹流量过小,管道阻损大及粉气比大,容易造成粉剂输送不稳定。
可见,助吹流量应该有个最佳值。
2.2管道直径的影响管道直径减小后,下料速度和过程压力的稳定性有所提高,但管道也不能太细,否则阻损太大也会影响系统的稳定性。
2.3喷枪出口直径的影响喷枪出口直径的大小影响了喷吹罐到喷枪的系统阻损,出口直径从Φ10mm变为Φ12mm时,系统压力从1.66×105Pa降低到了1.31×105Pa,考虑到喷吹过程中,保持足够的出口压力有利于防止喷枪堵塞。
铁水喷镁脱硫工艺优化

铁水喷镁脱硫工艺优化黄群新1,倪红卫1,张 华1,何 航1,墙 蔷1,余新河2,赵继宇2,魏 海2,刘 凯2(1.武汉科技大学钢铁冶金教育部重点实验室,湖北武汉430081;2.武汉钢铁(集团)公司第一炼钢厂,湖北武汉430083)摘 要:采用正交实验方差分析法,通过水模实验和数值模拟计算,研究了喷枪夹角、喷枪喇叭口高度、喷枪枪位、载气流量等因素对100t铁水罐喷镁脱硫时混匀时间及流场的影响。
结果表明,采用夹角为11 、喇叭口高度为705mm的喷枪,在枪位为2150mm、喷吹载气流量为35m3/h的条件下获得了较好的实际生产效果,可使镁脱硫剂的消耗明显降低。
关键词:镁脱硫;水模型;数值模拟中图分类号:T F702.2 文献标识码:A 文章编号:1002 1043(2007)01 0021 03Optimization of hot metal desu lphu rization by Mg injection processH U ANG Qun xin1,NI H ong w ei1,ZH ANG H ua1,H E H ang1,QIANG Qiang1,YU Xin he2,ZH A O Ji y u2,WEI H ai2,LIU Kai2(1.Key Labo rator y for Ferro us m etallurgy and Resource U tilization of the M inistry ofEducation,Wuhan U niv ersity o f Science&T echno logy,w uhan430081,China;2.N o.1Steel m aking Plant of Wuhan Iro n&Steel Co rp.,Wuhan430083,China)Abstract:By means o f orthogonal ex periments,variance analy sis,numerical simulatio n and w ater mo del ex perim ents,the effects of included ang le and heig ht o f the lance's bell mo uth,the level of the lance and the carrier g as flow rate on the blending time and the flow field in the process of desulphurization by M g injectio n in100t hot m etal ladle hav e been studied.Experiments show that better practical r esults hav e been achieved and the consumption coefficient of M g bear ing desulphurizer pro minently cut dow n since11 is cho sen as the included ang le of the lance's bell m outh,705mm as its heig ht,2150mm as the lance's level and35m3/h as the carrier gas flo w rate.Key w ords:desulphurizatio n by M g;Water model;numerical simulation近年来,钝化镁粒作为一种新型的铁水预处理脱硫剂越来越受到众多钢铁生产企业的重视。
复合喷吹法铁水脱硫工艺与设备分析

论风、骚之异同“风”和“骚”是中国古代文学中的两个重要概念,分别指的是《诗经》中的国风和楚辞中的离骚,是古代文学的两种重要文体和风格。
下面将从以下几个方面探讨“风”和“骚”的异同:一、起源和背景“风”起源于《诗经》,是周代各地的歌谣,具有民间性、生活性和现实性。
《诗经》中的国风反映了当时社会的风俗、习惯和思想观念,是周代社会生活的一面镜子。
而“骚”则源于楚辞,是战国时期楚国大夫屈原所创的一种诗歌形式,具有抒情性、想象力和哲理性。
楚辞通过抒发个人情感来表达对人生、社会和自然的感悟,具有深刻的思想和独特的艺术风格。
二、形式和风格“风”以四言为主,句式较为整齐,语言朴素自然,以韵律和音韵的美为主要特点。
而“骚”则是以六言为主,句式较为灵活,语言华美而繁复,追求文学艺术的至高境界。
楚辞中大量运用比喻、象征、夸张等修辞手法,具有浓厚的浪漫主义色彩。
三、表现手法“风”的表现手法主要是以现实生活为基础,通过描绘人物、事件和场景来表现社会生活和人们的思想感情。
而“骚”则更注重抒发个人情感和表现个性,大量运用象征、隐喻等手法,通过塑造意象来表达深刻的思想和情感。
四、思想内容“风”主要反映了周代社会的风俗、习惯和思想观念,表达了人们对生活、爱情、友情等方面的感受和情感。
其思想内容具有普遍性和共同性,能够引起广大读者的共鸣。
而“骚”则更注重表现个体的内心世界和精神追求,关注人类与自然、社会的关系,表达了作者对人生、爱情、政治等方面的独特思考和感悟。
其思想内容具有独特性和深刻性,能够触动读者的内心深处。
五、影响和价值“风”和“骚”在中国古代文学中都具有重要地位和深远影响。
“风”以其朴素自然的语言和生动活泼的风格,深受广大读者的喜爱和传承,对中国古代诗歌的发展产生了深远影响。
“骚”则以其华美而繁复的语言和深刻的思想情感,成为中国古代文学中的一朵奇葩,对中国古代诗歌的发展也产生了重要影响。
同时,“风”和“骚”都具有极高的文化价值和研究价值,能够为我们了解中国古代文化和历史提供重要的资料和启示。
喷镁脱硫法在铸管用铁水中的改进

于 目前各 大钢厂扩 大 产 能 的改 造 , 导致 了低硫 灰 石 和焦 炭资 源 日趋 紧张 , 铁水 含 硫 量不 断 上 升 的情 在
况下 , 为保证 离心球 墨铸铁 管的生 产需要 ,0 8年 6 20 月我们 引进 了铁水 喷吹钝化 颗粒镁 脱硫工 艺 。如何 快速有 效地 提高脱硫 、 降低 镁粉单 耗 、 保证 铸管连续
mea e uf rz to si p o e n e c i ga v r g f8 t ld s lu ia in wa m r v d a d r a h n n a e a e o 2% .Th u l y o o t lme her — e q ai fh tmea tt e t
motn lq i e e , r —etn h a a t r f c mp tr e p  ̄ s se ,t e d s lu iain r t fh t l i u d l v l e s ti g t e p r mee s o o u e x e e ytm h e u f rz t ae o o o
安钢永 通公 司 目前拥 有 4 0 高炉 2座 、 墨 5m 球 离 心铸铁 管生产线 4条 、 整线 2条 、 冷型球 墨铸 精 水 铁管 离心机 6台。产品 主要有炼 钢生铁 、 造生 铁 、 铸 球 墨铸 造用 生铁 、 N 0~1 0 m 水 冷 型离 心球 墨 D 8 0 m 2
铁水预处理脱硫工艺的探讨

铁水预脱硫工艺的探讨摘要:本文重点讨论铁水预处理中脱硫工艺的方法及特点,为国内各个钢厂选择合理有效的工艺,提高铁水质量,增加市场竞争力提供重要的参考信息。
关键词:铁水预处理脱硫剂搅拌法喷吹法扒渣1 前言铁水预脱硫工艺是指铁水进入炼钢炉前的脱硫处理,它是铁水预处理中最先发展成熟的工艺。
对于优化钢铁冶金工艺、提高钢的质量、发展优质钢种、提高钢铁冶金综合效益起着重要作用,是不可缺少的工序。
国内昆钢通过铁水预处理脱硫工艺,铁水中的含硫量从110多个降为15个(含硫量0.001%称为1个硫),使钢材的内在质量得到了提升,明显增加了市场竞争力和经济效益。
2 铁水预脱硫的必要性钢的很多性能都受含硫量及其在钢中形成的硫化物夹的杂物理和化学影响,硫化物—硫化锰夹杂在热轧温度下很容易变形,成为延伸性夹杂,引起钢性能各向异性。
除易切削钢外,硫是影响钢质量和性能主要有害元素,影响钢的加工性能和使用性能。
普通钢:特别是连铸坯内部裂纹和表面质量均与[S]有关,要求[S]≤0.02%;低硫钢:结构钢为实现均匀机械性能,减少各相异性,则要求[S]≤0.011%;极低硫钢:石油和天然气输送管线、海上采油平台、厚船板和航空用钢等要求有更好均匀机械性能和更高冲击韧性,而硅钢要求有良好的磁性,薄钢板则要求良好深冲性能等,都要求[S]≤0.005%。
铁水中硫主要来自加入高炉的焦炭、煤粉和矿石等,高炉内脱硫必须通过增加渣量、提高炉渣碱度和炉温来降低铁水硫含量值,高碱度会增加铁水硅含量,消耗额外热量,导致炼钢石灰耗量增加,对炼钢带来一系列问题,同时降低金属收得率。
所以,一般情况下高炉采用低碱度操作,可以显著降低焦比,减少渣量,降低铁水温度和硅含量,使高炉产量增加。
但产出的铁水含硫较高,如果转炉采用高硫铁水冶炼低硫钢,势必采用造碱度渣,并经多次扒渣、再造渣操作,这样势必带来许多不利影响,严重影响钢的质量,降低炉龄,不能把硫降到较低水平。
所以,只有采用低硫铁水炼钢才能提高钢的质量和各项技术经济指标,降低炼钢成本。
铁水预处理脱硫工艺参数的优化

题 , 出并 实施 了优 化 方案 , 脱硫 工艺基本 上 达到 了正 常化 , 提 使 满足 了生产 的 需要 。
【 关键 词 】 铁 水预 处理周 期
1 前 言 铁水预处理本 是 一项 成熟 的工 艺 , 自 但 我厂投产以来 , 剂脱 硫率 低 、 水 温降 大 、 粉 铁 喷溅严重 、 常堵枪 等 , 使脱 硫 成本 增加 、 经 致 喷 吹 过 程极 不 顺 行 。 成 立 攻 关 组 后 , 技 人 科 员 远 赴 太 钢 考 察 铁 水 脱 硫 工 艺并 认 真 分 析 研 究 了脱 硫 各 项 指标 , 过 调 整 脱 硫 粉 剂 组 成 、 通 配方 、 度 、 装 方 式 , 小 喷 枪 出 粉 孔 径 和 粒 包 减 喷 吹 罐 喉 口直 径 , 低 三 级 减 压 压 力 , 整 喷 调 调 吹罐 罐 顶 、 态 化 、 吹 三 支 管 阀 开 口度 , 流 助 使 石灰 基 脱 硫 粉 剂 脱 硫 率 得 到 大 幅度 提 高 , 铁 水喷溅 有所减 轻 , 堵枪 现象基本解决 , 脱硫 工 艺基 本 正 常化 。 2 铁 水 预 处 理 脱 硫 工 艺 参 数 的 优 化 2 1 脱 硫 粉 剂 . 原脱硫粉剂是 由粉剂生产厂家按 照 自己
出 了很 多切 实 可 行 的 建 议 , 增 加 石 灰 昼 夜 如 出窑 次 数 以 减 少 石 灰 过 烧 率 , 窑 石 灰 石 粒 人
根据有关 资料 的介 绍 , 料 速度 是压 差 下 与 喉 口直 径 的 函数 即 : =A × ̄ P △ ) × / ×( u) 2= F
7 3 7. 0
:
二 :
0. 2 04
墨 : 二曼 Q Q :
8 5 0. 0
维普资讯
KR法与喷吹法在铁水预脱硫中应用的比较
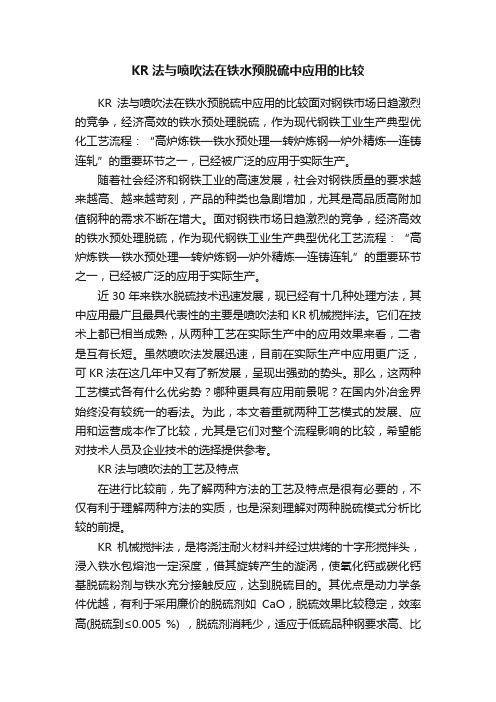
KR法与喷吹法在铁水预脱硫中应用的比较KR法与喷吹法在铁水预脱硫中应用的比较面对钢铁市场日趋激烈的竞争,经济高效的铁水预处理脱硫,作为现代钢铁工业生产典型优化工艺流程:“高炉炼铁—铁水预处理—转炉炼钢—炉外精炼—连铸连轧”的重要环节之一,已经被广泛的应用于实际生产。
随着社会经济和钢铁工业的高速发展,社会对钢铁质量的要求越来越高、越来越苛刻,产品的种类也急剧增加,尤其是高品质高附加值钢种的需求不断在增大。
面对钢铁市场日趋激烈的竞争,经济高效的铁水预处理脱硫,作为现代钢铁工业生产典型优化工艺流程:“高炉炼铁—铁水预处理—转炉炼钢—炉外精炼—连铸连轧”的重要环节之一,已经被广泛的应用于实际生产。
近30年来铁水脱硫技术迅速发展,现已经有十几种处理方法,其中应用最广且最具代表性的主要是喷吹法和KR机械搅拌法。
它们在技术上都已相当成熟,从两种工艺在实际生产中的应用效果来看,二者是互有长短。
虽然喷吹法发展迅速,目前在实际生产中应用更广泛,可KR法在这几年中又有了新发展,呈现出强劲的势头。
那么,这两种工艺模式各有什么优劣势?哪种更具有应用前景呢?在国内外冶金界始终没有较统一的看法。
为此,本文着重就两种工艺模式的发展、应用和运营成本作了比较,尤其是它们对整个流程影响的比较,希望能对技术人员及企业技术的选择提供参考。
KR法与喷吹法的工艺及特点在进行比较前,先了解两种方法的工艺及特点是很有必要的,不仅有利于理解两种方法的实质,也是深刻理解对两种脱硫模式分析比较的前提。
KR机械搅拌法,是将浇注耐火材料并经过烘烤的十字形搅拌头,浸入铁水包熔池一定深度,借其旋转产生的漩涡,使氧化钙或碳化钙基脱硫粉剂与铁水充分接触反应,达到脱硫目的。
其优点是动力学条件优越,有利于采用廉价的脱硫剂如CaO,脱硫效果比较稳定,效率高(脱硫到≤0.005 %) ,脱硫剂消耗少,适应于低硫品种钢要求高、比例大的钢厂采用。
不足是,设备复杂,一次投资较大,脱硫铁水温降较大。
铁水预处理的工艺设计

铁水预处理的工艺设计1、铁水脱硫预处理宜采用喷吹法或机械搅拌法,经预脱硫处理后铁水的硫含量不应高于0.015%,对于生产超低硫钢种用的铁水,硫含量不应高于0.005%。
2、高炉铁水包、鱼雷罐、转炉铁水包均可作为铁水预脱硫的反应容器,宜选用转炉铁水包。
铁水包内铁水面以上自由空间高度,当采用喷吹法时不应小于50 0mm,采用机械搅拌法时不应小于700mm。
3、铁水脱磷预处理应符合下列规定:(1)铁水磷含量高于0.12%,或生产含磷不大于0.005%的超低磷钢种时,应采用铁水包喷吹法、铁水包搅拌法、鱼雷罐喷吹法或转炉炉内预脱磷工艺。
(2)铁水包喷吹法预脱磷时,应采用专用铁水包,铁水面上自由空间高度不应小于1500mm。
处理后的铁水磷含量不应高于0.030%。
(3)铁水包搅拌法预脱磷时,应采用专用铁水包,铁水面上自由空间高度不应小于700mm。
处理后的铁水磷含量不应高于0.040%。
(4)鱼雷罐喷吹法预脱磷时,铁水面上自由空间高度不应小于1000mm。
处理后的铁水磷含量不应高于0.030%。
(5)转炉炉内脱磷预处理后的铁水磷含量不应高于0.030%。
对于超低磷钢种,预处理后铁水磷含量不应高于0.005%。
4、采用转炉炉内脱磷预处理时,加入转炉的废钢比不应大于10%,宜采用轻废钢。
转炉采用氮气进行底吹搅拌,底吹强度不应小于0.2Nm3/(t·min),氮气压力不应小于1.6MPa,每个底吹支路应单独控制。
脱磷转炉宜采用专用氧枪,供氧强度不应大于2.5Nm3/(t·min)。
5、采用铁水包和鱼雷罐内脱磷预处理时,铁水应先进行脱硅预处理,铁水硅含量不应高于0.20%。
6、需要生产超低硫、超低磷钢种的转炉炼钢车间,宜采用铁水三脱(脱硅、脱磷、脱硫)预处理工艺。
7、喷吹法预处理宜采用氮气作为载流气体。
氮气纯度不应低于99.9%,压力不应小于1.0MPa,供气流量应按输送气粉比和供粉强度要求确定。
铁水喷镁脱硫法的改良

铁水喷镁脱硫法的改良铁水采用颗粒镁脱硫效率低与扒渣工序、载气压力、下料速度、计算机专家系统的改进等有关。
具体为:1、扒渣工艺扒渣不净,渣量大会增加渣中的硫与颗粒镁反应的几率,增加镁耗;扒渣不及时,渣中MgS被氧还原,重新进入铁水,造成回硫现象,也降低镁脱硫效率。
2、载气压力镁粉载气压力与下料速度不匹配,粉气比不合理,镁粉下料不顺畅,造成镁粒浪费。
3、下料速度铁水液面过高,为避免喷溅,只能降低喷吹压力和下料速度,受供铁时间限制,导致下料量不足,降低脱硫率;过低,镁气泡来不及溶入,利用率降低。
4、系统设计仅局限于初始硫在0.030%以内,超出此数值,计算的下料量偏低。
改进措施为:1、扒渣工艺针对扒渣不净,优化工艺参数,初次扒渣时间确定为3-5min;单次喷吹时间10-12min;脱硫扒渣分两次,第一次加入稠聚渣剂6袋,第二次加入4袋,时间8-10min。
脱硫工序一个处理时间控制在33-35min。
其次增加铁水进站后的初次扒渣,减少顶渣与镁粉的反应。
2、载气压力通过现场跟踪,确定助吹压力为0.3-0.4MPa,供气量为8-15m3/h,对应下料速度为2-3kg/min。
确保减少喷溅和汽化室粘堵问题,稳定和提高脱硫率。
3、液面高度减少液面过高或过低现象,增加喷枪插入深度,增加镁的蒸气压,提高镁在铁水中的溶解度。
喷枪的插入深度直接关系到颗粒镁在铁水中逗留时间的长短和与铁水接触接触的多少,还影响到脱硫剂的扩散范围大小。
4、系统对实际脱前S、脱后S和下料量进行统计分析,优化专家系统参数,上调初始S设置,下调目标S设置,缩小铁水温度取值范围。
这样优化后,提高了脱硫命中率。
铁水预处理(脱硫)

【本章学习要点】本章学习铁水预处理脱硫的优点,常用脱硫剂种类及其反应特点,脱硫生产指标,KR法脱硫的生产工艺流程和脱硫的基本操作,混铁车喷吹脱硫的工艺特点和工艺操作。
第一节铁水预脱硫的概念和优点铁水预处理,炼钢生产中主要是指铁水在进入转炉之前的脱硫处理。
广义的铁水预处理是指包括对铁水脱硫、脱硅、脱磷的三脱处理,另外还有特殊铁水的预处理,如含V铁水的提V等。
铁水脱硫是二十世纪70年代发展起来的铁水处理工艺技术,它已成为现代钢铁企业优化工艺流程的重要组成部分。
铁水脱硫的主要优点如下:1.铁水中含有大量的硅、碳和锰等还原性的元素,在使用各种脱硫剂时,脱硫剂的烧损少,利用率高,有利于脱硫。
2.铁水中的碳、硅能大大提高铁水中硫的活度系数,改善脱硫的热力学条件,使硫较易脱致较低的水平。
3.铁水中含氧量较低,提高渣铁中硫的分配系数,有利于脱硫。
4.铁水处理温度低,使耐火材料及处理装置的寿命比较高。
5.铁水脱硫的费用低,如在高炉、转炉、炉外精炼装置中脱除一公斤硫,其费用分别是铁水脱硫的2.6、16.9和6.1倍。
6.铁水炉外脱硫的过程中铁水成份的变化,比炼钢或钢水炉外处理过程中钢水成份的变化对最终的钢种成份影响小。
采用铁水脱硫,不仅可以减轻高炉负担,降低焦比,减少渣量和提高生产率,也使转炉也不必为脱硫而采取大渣量高碱度操作,因为在转炉高氧化性炉渣条件下脱硫是相当困难的。
因此铁水脱硫已成为现代钢铁工业优化工艺流程的重要手段,是提高钢质量、扩大品种的主要措施。
早期的铁水脱硫方法有很多种:如将脱硫剂直接加在铁水罐罐底,靠出铁铁流的冲击形成混合而脱硫的铺撒法。
也有将脱硫剂加入装有铁水的铁水罐中,然后将铁水罐偏心旋转或正向反向交换旋转的摇包法。
之后逐步发展至今天采用的KR搅拌法及喷枪插入铁水中的喷吹法。
第二节常用脱硫剂及脱硫指标一、常用脱硫剂经过长期的生产实践,目前选用作为铁水脱硫剂的主要是Ca、Mg、Na等元素的单质或化合物,常用的脱硫剂主要有:Ca系:电石粉(CaC2)、石灰(CaO)、石灰石(CaCO3)等Mg系:金属Mg粉Na系:苏打(Na2CO3)二、常用脱硫剂反应特点1.电石粉碳化钙脱硫反应为用CaC2脱硫有如下特点:1)在高碳系铁水中,CaC2分解出的Ca离子与铁水中的硫有极强的亲和力。
炼钢厂铁水预处理一键脱硫控制系统

炼钢厂铁水预处理一键脱硫控制系统1 脱硫预处理组成与流程两个脱硫站共用一套氮气供应管路,即石灰和镁粉的储料仓。
为增加系统的灵活性,设置了一套共用的切换阀用于垂直(默认)和交叉(紧急备用)喷吹之间的选择。
喷吹系统、测温取样系统、铁包车、扒渣机和液压系统虽然每个站各自独立,但两站彼此又相同。
每个脱硫站均有两套独立的提升装置,一套用于脱硫喷枪的升降,另一套用于测温取样枪的升降。
为了获得更好的速度和位置控制,喷枪升降驱动装置采用变速调频电机驱动控制(vfd)。
铁水通过铁包车运至脱硫站。
铁包车直接接受原料跨450t天车吊运的铁水,而后从吊/座包位运至喷吹位进行喷吹、扒渣处理,当喷吹、扒渣完成后,再将铁水运至吊/座包位,由原料跨450t 天车从车上吊走处理好的铁水,完成一个脱硫周期。
铁水预处理工艺流程如图1。
2 远程i/o通讯主控台包含主控桌,主控桌包含有作为一台hmi和二级客户计算机的操作工作站。
himi显示用西门子wincc可扩充软件设计,并提供了脱硫和除尘系统设备的监控。
操作者报警将显示和公布在控制室的hmi上。
每个脱硫站将包括4个控制柜,每个控制柜均配有远程i/o通讯站,远程i/o模块通过一个profibus 网络与plc进行通讯。
plc 经过采用tcp/ip(工业以太网)协议的以太网与hmi进行通讯。
这种通讯方式在其配置和维护方面具有很大的适应性,并准许过程数据通过远程编程经过opc服务器进行存取。
脱硫站包括一套用oracle为数据库的二级系统。
它由一个位于计算机房的服务器和一个客户机组成。
服务器用于数据的储存和管理,客户机作为hmi使用。
3 一键喷吹系统优化每个站控制系统是由一台西门子s7-400系列可编程逻辑控制器(plc)和一台用于控制两个站共用部件s7-300plc组成。
每个plc 均有本地和远程数字和模拟i/o接口。
该系统也包括每个脱硫站的人机界面(hmi),人机界面位于主控制操作台上,若必要,每个人机界面均能控制两个站。
攀钢铁水预脱硫喷吹系统管径改造合理性论证

攀钢铁水预脱硫喷吹系统管径改造合理性论证由于攀钢Ⅰ、Ⅱ、Ⅴ部铁水预脱硫所使用脱硫剂发生变化,但喷吹管径与喷吹参数保持不变,导致喷吹脱硫过程存在诸多不足,主要表现在以下几个方面:(1)脱硫枪位较高客户机吗,根据实测脱硫枪位在1.6~2.3m 之间,与外厂距罐底0.3m的枪位相比,明显较高,具体表现在脱硫喷溅较大;(2)脱硫处理时间长,目前Ⅰ、Ⅱ、Ⅴ部脱硫平均处理时间在22min左右,造成脱硫铁损及温度损失较大。
为了减少粉剂单耗、缩短处理时间与降低铁水温降,在脱硫剂配方确定的基础上须对喷粉脱硫工艺进行优化。
为此,经过详细分析以及借鉴一些相关实践经验,攀钢提出喷吹管径改造方案:喷吹管径与喷枪内径从32mm减小到25mm,下枪深度从1.2-1.5m增加到2m (铁水液面下),详细参数变化见表1。
攀钢Ⅰ、Ⅱ、Ⅴ部脱硫喷吹系统现行喷吹参数与改造方案中的参数对比见表1。
表1 攀钢Ⅰ、Ⅱ、Ⅴ部脱硫喷吹系统现行喷吹参数与改造方案的参数对比喷吹参数喷吹管径及喷枪内径喷吹速度粉气比下枪深度/铁水液面下助吹压力喷吹粉料罐压力现行喷吹参数 32mm40~60k g/min20kg/ Nm 31.2~1.5m0.3 MPa0.5 MPa管径改造方案的喷吹参数25mm 40~60k g/min20kg/ Nm 32m0.3 MPa0.5 MPa攀钢在管径改造方案的基础上采用管道阻损经验公式0049.00026.0+=∆∑W p 对系统管道压力损失进行了计算,得到系统总压力损失0.33-0.38Mpa ,为了进一步验证改造方案中喷吹参数的合理性,即系统输送压力是否满足喷吹要求,为攀钢管径改造提供更多依据,重大脱硫课题组采用管道阻损理论计算公式(即barth 压力损失理论)对使用改造方案的喷吹参数时的系统压力损失进行了计算分析。
1 系统压力损失计算为保证系统输送压力能满足输送要求,即输送压力大于系统各项压力损失,可以将脱硫剂顺利喷入钢液,系统输送压力p 应至少大于整个系统的各项阻力损失的总与,即管道的阻力损失P 管道阻损,熔池静压力p 熔池静压、大气压力)(a p 与料罐出口压力损失p 料罐出口压损之与。
铁水混合喷吹脱硫喷吹罐工艺参数设计

摘要在现代钢铁冶金生产工艺中,很重要的一门技术就是铁水预处理,又称为铁水炉外处理。
它对于优化钢铁冶金工艺、提高钢的质量、发展优质钢种、提高钢铁冶金企业的综合效益起着重要作用,已发展成为钢铁冶炼中不可缺少的工序。
其中脱硫是最早发展的铁水预处理技术。
喷吹罐是脱硫工艺中的主要设备,常用方式是向上出料和向下出料。
向上出料的喷吹罐对喷吹速率控制能力强,但操作复杂。
向下出料的喷吹罐结构简单,易于操作,但是对喷吹速率控制力弱。
本文主要是设计一种操作简单,且对喷吹速率控制很好的喷吹罐。
本喷吹罐主要包括罐体、机械给料部件、流化室和喉口。
主要参数为罐体体积1.22m3, 旋转给料器转速77.78r/分钟,流化室进气口压强4×105Pa,补气口压强2.2466×105Pa。
关键词铁水预处理,喷吹脱硫、喷吹罐,流化室,喉口ABSTRACTIn modern iron and steel metallurgy in the production process, a very important technology is the hot metal pretreatment, also known as hot metal processing. It is optimized for iron and steel metallurgy process, improve the quality of steel, high-quality steel, iron and steel metallurgy development improve the comprehensive benefit of enterprise plays an important role, has become an indispensable step in steel smelting Which is the earliest development of the desulfurization of hot metal pretreatment.Puffing tank is the main of desulfurization equipment, commonly used method is the material up and down out of the material. Up material puffing tank injection rate control ability, but the operation is complex. Down the material in the puffing tank structure is simple, easy to operate, but the injection rate control is weak. This paper is to design a simple operation, and control the puffing tank injection rate. The puffing tank including tanks, mechanical feeding part, the fluidization chamber and throat. The main parameters for the volume 1.22m3, rotary feeder speed for 77.78r/ min, the fluidizing chamber inlet pressure of 4 × 105Pa, Buqi mouth pressure is2.2466 × 105Pa.Key words The pretreatment of hot metal, blowing desulphurization, puffing tank, a fluidization chamber, throat目录摘要 (1)ABSTRACT ................................................................................................................. I I 1绪论.......................................................................................... 错误!未定义书签。
铁水预处理除尘优化改造

= 跨 尘 吼量 1 ; 0 ‘
密 ,以免被石灰灼伤 , 环 境恶 劣已严 重威胁职工健康 ; 脱硫剂的喷溅 , 造成的不仅是成本的居高不下和原料浪费,更是耗费巨大人力物力的清
不胜清 、堆积如山的废料。
j 藩 尘 风量 i " . 0 n h l 8 】 0 1 h
硫, 【 S 】符合相应钢种要求后,方可兑入转炉冶炼。在不断调整品种
钢结构、提升产品质量的生产要求下 , 3 座K R 预处理的利用率在 7 0 %
以上。
受现场工艺布局 的限制 ,脱硫剂料仓设置位置距离脱硫本体设备
较远,且投料输送管道长、拐点多、助吹少等,从而造成投料过 程中管
图 1 脱硅站 、K R脱琉站除尘 J _ 艺布局
保证 3 座K R脱硫站 的除尘效果。通过优化投料管路及助畎介 质,并借用闲置的脱硅除尘, 增强吸附能力, 提升 K R 区域作业环境。
【 关键司 除尘; 优化;改造
铁水预处理因工艺布局,料仓位置距离脱硫主体设备较远 ,投料时
喷溅区域环境扬粉严重:且除尘风枷设计能力偏小 , 不足以保证 3 座K R
漫、积灰严重的后果 ,这几乎是加料跨乃至厂房 的最大污 染源。脱 硫剂 的主要成分为活性石灰 , 8 5 %以上是 0 . 3 — 1 - 2 mm 的颗粒 ,对人体 身体
损害颇大。 职工于如此恶劣 的环境 ,室内带 口 罩 操作 ,室外作业更是包 裹严
1 O 3 / h 。整改前后 3 座K R除尘风量对比情况见下表
施工结束后,倒罐站除尘仍是独立的系统 ,不受剥离脱硅除尘的
影响 风机 ,除尘 能 力明显 提 高 ;
3 # K R脱硫站单独使用脱硅风机 ,除尘能力 良好。K R区域 的作业环境
- 1、下载文档前请自行甄别文档内容的完整性,平台不提供额外的编辑、内容补充、找答案等附加服务。
- 2、"仅部分预览"的文档,不可在线预览部分如存在完整性等问题,可反馈申请退款(可完整预览的文档不适用该条件!)。
- 3、如文档侵犯您的权益,请联系客服反馈,我们会尽快为您处理(人工客服工作时间:9:00-18:30)。
铁水预脱硫喷吹系统的优化设计翟兴华摘要根据铁水预脱硫工艺和喷吹技术发展状况,结合实践经验,从铁水预脱硫喷吹系统设计的角度出发,对铁水预脱硫工艺、脱硫剂喷吹方式、操作方式、粉气比大小及喷吹控制方式的优化设计做一些有益的探讨。
实践表明,铁水预脱硫喷吹系统的优化设计取得了良好的效果。
关键词脱硫喷吹优化设计Optimum Design of Injection System for Predesulphurization ofHot MetalZhai Xinghua(Wuhan Iron & Steel Design Research Institute)Abstract Based on the development status of desulphurizatin process of hot metal and injection technology, putting emphasis on the design of predesulphurization and injection system, this paper gives discussions on some aspects, such as predesulphurization process of hot metal, injection methods of desulphurizing agents ,operation patterns, ratio of powder and gas, and the optimum design of injection control. It is proved by practice that the optimum design has brought good effects.Keywords desulphurization injection optimum design1 前言随着喷粉技术的出现,铁水外部脱硫迅速发展;由于喷粉冶金克服了反应表面面积小,即渣—金属界面小的问题,以及硫从渣—金属界面向渣整体界面移动困难的两大难点,以喷粉技术为基础发展起来的现代外部脱硫工艺在将铁水硫含量降至很低水平方面非常有用。
由于我国从平炉改造到转炉炼钢比较晚,铁水炉外脱硫到70年代才逐渐发展起来,脱硫工艺设计存在许多不足之处,基本上都是在原有的基础上加以改进,没有大的突破和创新。
80年代初宝钢首次引进新日铁的TDS(顶喷)法,在此基础上,鞍钢、武钢、太钢、攀钢等厂也建立了炉外喷吹脱硫站。
TDS法是新日铁于1971年在ATH法基础上改进而成,一般适用于混铁车脱硫,铁水罐脱硫技术还需进一步完善,以适合我国一些钢铁企业进行炼钢工艺改造的需要。
本文根据铁水预脱硫工艺及喷吹技术发展状况及实践经验,从铁水预脱硫喷吹系统设计的角度出发,做一些有益的探讨。
2 铁水预脱硫工艺的选择在实际操作中,铁水外部脱硫常用的工艺有4种,这4种工艺是:(1)苏打或碳酸钠(Na2CO3)工艺;(2)石灰/煅烧石灰(带添加剂或不带添加剂的CaO)工艺(3)碳化钙工艺;(4)钝化镁工艺。
这4种脱硫工艺的对比见表1。
从表1可看出,任何一种工艺单独应用都达不到全满意的效果。
最近工业铁水外部脱硫技术的发展主要倾向于两种工艺:(1)CaO-Mg基混合工艺;(2)CaC2-Mg基混合工艺。
实践证明,CaO和镁基试剂混合使用及碳化钙和镁基试剂混合使用比单独使用效果好,其原因在于:表1 铁水预脱硫工艺比较(1)镁在混合物中不仅充当一种脱硫剂,还在熔池内起搅拌作用。
(2)在镁粒中掺入一定量的CaO或CaC2,可控制镁的挥发速度,防上镁的挥发损失。
日新制钢公司吴厂第二炼钢车间[1]用CaO-Mg系脱硫剂进行试验,结果证明CaO-Mg系脱硫剂比CaO系脱硫剂脱硫效率显著提高,最大可达86%;铁水温度下降的幅度非常小,约为0.4~0.8℃/min;渣量也明显减少。
新日铁公司八幡厂[2]采用CaO-Mg系脱硫剂进行试验也证明CaO-Mg 系脱硫剂不但比CaO系脱硫剂效率显著提高,而且可获得高的脱硫速度;对铁水中的[S]从0.012%降至0.002%处理的过程中温度下降12℃,与使用CaO系脱硫剂相比大幅度抑制了温降。
在相同脱硫条件下,CaO-Mg基混合工艺不但比CaC-Mg基混合工艺2少产生大约15%的渣,而且考虑到铁损和基建投资的情况下,CaO-Mg基混-Mg混合工艺更便宜。
合工艺比CaC2-Mg 综上所述,在相同的脱硫条件下,CaO-Mg基混合工艺优于CaC2基混合工艺。
但是,由于我国各个钢厂的环境条件和内部要求不同,每个钢厂应根据自己的实际情况选择最经济和最可靠的工艺。
3 铁水预脱硫喷吹方式的选择-Mg基混合工艺而言,脱硫剂喷吹方式可分为对于CaO-Mg基或CaC2复合喷吹和混合喷吹。
在我国一些钢厂为了节省基建投资,常常选用混合喷吹,实际上,这是企业的一种短期行为。
铁水炉外脱硫的费用,除基建投资外,脱硫剂的耗量和脱硫效果也是很重要的因素。
虽然复合喷吹设备占地面积大,但它能有效地将因偏析影响脱硫效率的可能性降至最低点。
从它与应用混合脱硫剂的混合喷粉脱硫技术使用效果上看,将270t铁水硫含量从0.055%降至0.003%时,复合喷粉镁的消耗量减少11%,当硫含量降至0.014%时,其镁消耗量减少16%,使用情况见表2。
表2 脱硫效果比较4 铁水预脱硫操作方式的选择从理论上看,脱硫过程可分为孕育期、脱硫期及脱硫后期三个阶段。
在孕育期硫含量并无变化,但要造成铁水的强烈搅拌,在脱硫期内铁水硫含量急剧降低,脱硫后期硫含量的降低变慢。
利用CaO-Mg基混合工艺脱硫时,镁脱硫剂沸点低,以气相和铁水中的硫反应,故脱硫速度快,但早期加入将很快损失,脱硫后期因镁溶解度增加也会降低其脱硫效率;CaO脱硫剂在铁水中呈固态,要以细粉末状加入,脱硫效率比镁低,价格也较低,粗略估算1kg镁的脱硫效果相当于15kgCaO。
根据脱硫机理及脱硫剂的特点,喷吹操作时,将喷射过程分成三个阶段:第一阶段:先用CaO进行预喷吹,喷入CaO以形成强烈的旋涡,完成融体和渣的脱氧,建立起铁水包中的环流运动。
第二阶段:用选定的Mg(深脱硫)和CaO(浅脱硫)的喷吹速度进行主喷吹。
第三阶段:主喷吹完成后,以高气体量喷入一段时间CaO,以清除夹杂,完成脱硫过程。
在第二阶段喷入最大量的镁(深脱硫时),在此阶段结束时,镁量减至最小,控制喷入物及输送气体流速,使铁水包中形成的旋涡在铁水包边沿高度允许的情况下保持最高,这样可使脱硫剂效果最好而且处理时间最短。
上述操作方式仅对于CaO-Mg基复合喷吹而言,主要目的是在提高脱硫效果的同时最大限度的降低镁的消耗量,以利于降低操作成本。
对于)基或其它喷吹工艺不可机械模仿,可根据上述脱硫过程的机CaO(CaC2理,通过改变喷吹过程的一些参数(如:喷吹压力,二次风流量,喷吹量等)确定自己既简单又经济的操作方式。
5 铁水预脱硫粉气比大小的确定粉气比的大小通常要直接受到喷粉设备的影响。
从工艺操作要求角度出发,在保证一定搅拌力的前提下,应尽可能减少载气,增大粉气比。
运载气体能增快脱硫剂的上浮速度,在气量大的情况下,还会出现脱硫剂尚未发挥作用就被气泡带到液面上去致粉剂接触富硫铁水的机会少。
另外,载气量大时,喷枪粉气出口速度较大,造成气流和气泡对铁水搅拌力强,易出现铁水喷溅现象。
但载气量过小,不但容易堵塞,还会因搅拌力不够影响脱硫效果。
对于任一套脱硫系统都有其合适的粉气比范围,通常情况下,对于混铁车脱硫,每立方米载气的适宜载粉量约为15~50kg;对于铁水罐脱硫,由于易产生喷溅,每立方米载气的适宜载粉量约为20~40kg。
6 铁水预脱硫喷吹控制方式铁水脱硫剂的喷吹量有三种控制方式:旋转给料阀控制、间接控制和计量阀直接控制(见表3)。
表3 喷吹量的三种控制方式喷吹率转子速度被控制保持恒定喷吹量由罐压流化风量和二次风量由阀位控制罐压保持恒定流化风量保持恒定二次风量喷吹率控制根据喷吹量单独控制输送方式稀相稀相浓相浓相6.1 旋转给料阀控制一些喷吹系统通过旋转给料阀或螺旋给料器的转子速度来控制喷吹量。
宝钢80年代引进的第一套新日铁的TDS脱硫喷吹系统,采用旋转给料阀控制喷吹量,因维修费用高、能耗高、难以实现浓相输送而终被淘汰。
6.2 间接控制在喷吹罐与输送管之间不设任何机械给料装置,脱硫剂喷吹量主要取决于:(1)喷吹罐与输粉管之间的压差,受喷吹罐出口布置及横截面积的影响。
(2)喷吹罐底部流化气量。
(3)二次风流量。
喷吹罐压的控制是容易的,但只限于控制范围,不适于大量气体排空或充压的快速反应。
实际控制过程中,喷吹量波动大,不易迅速准确地控制喷吹量,给生产带来很大困难。
罐压一定时,调节喷吹罐底部流化气量和二次风量也可以控制喷吹量。
实际控制过程中,气量的变化往往导致粉气比及输送管内的物料运动状态改变,这些因素又导致铁水脱硫过程不易控制。
6.3 计量阀直接控制[3]通过调整截面积,使用特殊的计量阀可直接控制喷吹罐和输送管道之间的脱硫剂量,该计量阀由开关阀及调节阀组成。
喷吹过程中,罐压和流化气量均保持恒定。
计量阀根据称重信号及本身压降的自适应来准确调节喷粉量。
由于目前国内还没有生产喷吹调节计量阀的厂家,采用计量阀直接控制需引进国外阀门及相关技术,这在一定程度上增加了设备投资,国内的用户应根据自己的经济实力和炼钢工艺系统的要求合理的选择喷吹控制方式。
7 铁水预脱硫系统设计实例武钢一炼钢铁水脱硫(MgO+CaO)工艺。
(1)工艺流程见图1。
图1 武钢一炼钢铁水脱硫站工艺流程图(单系列)(2)脱硫站考虑了1个槽罐车的卸料位置,2条卸料管线。
为了保证工艺一天要求的脱硫剂量,设计采用料仓2个,喷吹罐2个,每个喷吹罐提供的脱硫剂量可满足一个铁水罐脱硫站处理需要。
(3)为了节省投资,根据武钢要求,一期工程采用(MgO+CaO)混合喷吹工艺,予留MgO喷吹设施位置,二期工程考虑采用(MgO+CaO)复合喷吹工艺。
(4)喷吹罐设计时采用计量阀直接控制式喷吹系统,氮气浓相输送,但由于武钢要求设备全部国产化,最后改为改进型压差控制式喷吹系统。
采用罐压、二次风流量、流化风量联合控制方式,最大限度的克服了旧有压差式喷吹控制系统的缺点。
(5)根据系统特点及武钢的实际情况,采用了合理的操作方式。
(6)工艺采用两个铁水罐脱硫台位,为了提高生产的可靠性,任一喷吹系统对应两个铁水罐脱硫台位。
(7)此工程于1998年12月投产,由于MgO供应不到位,投产初期全部采用CaO脱硫,由于喷吹系统设计进行了优化,工艺配置合理,脱硫效率>80%,最高达到91%,脱硫后铁水各项指标全部达到甚至超过设计指标。