湿硫化氢腐蚀(精选)
炼油装置湿硫化氢应力腐蚀分析详解
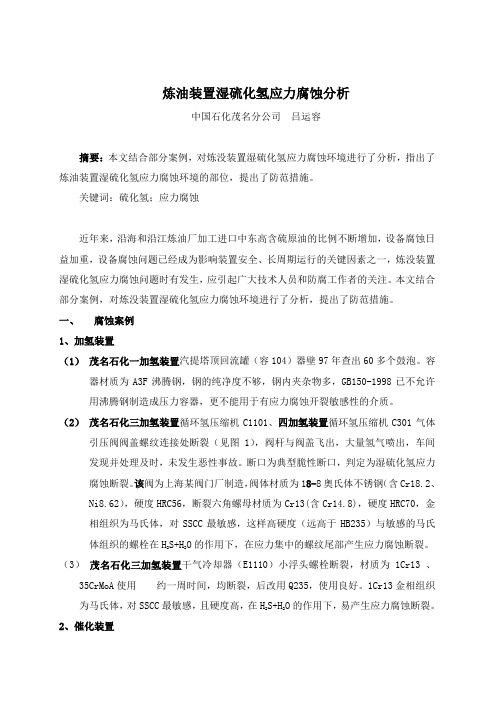
炼油装置湿硫化氢应力腐蚀分析中国石化茂名分公司吕运容摘要:本文结合部分案例,对炼没装置湿硫化氢应力腐蚀环境进行了分析,指出了炼油装置湿硫化氢应力腐蚀环境的部位,提出了防范措施。
关键词:硫化氢;应力腐蚀近年来,沿海和沿江炼油厂加工进口中东高含硫原油的比例不断增加,设备腐蚀日益加重,设备腐蚀问题已经成为影响装置安全、长周期运行的关键因素之一,炼没装置湿硫化氢应力腐蚀问题时有发生,应引起广大技术人员和防腐工作者的关注。
本文结合部分案例,对炼没装置湿硫化氢应力腐蚀环境进行了分析,提出了防范措施。
一、腐蚀案例1、加氢装置(1)茂名石化一加氢装置汽提塔顶回流罐(容104)器壁97年查出60多个鼓泡。
容器材质为A3F沸腾钢,钢的纯净度不够,钢内夹杂物多,GB150-1998已不允许用沸腾钢制造成压力容器,更不能用于有应力腐蚀开裂敏感性的介质。
(2)茂名石化三加氢装置循环氢压缩机C1101、四加氢装置循环氢压缩机C301气体引压阀阀盖螺纹连接处断裂(见图1),阀杆与阀盖飞出,大量氢气喷出,车间发现并处理及时,未发生恶性事故。
断口为典型脆性断口,判定为湿硫化氢应力腐蚀断裂。
该阀为上海某阀门厂制造,阀体材质为18-8奥氏体不锈钢(含Cr18.2、Ni8.62),硬度HRC56,断裂六角螺母材质为Cr13(含Cr14.8),硬度HRC70,金相组织为马氏体,对SSCC最敏感,这样高硬度(远高于HB235)与敏感的马氏体组织的螺栓在H2S+H2O的作用下,在应力集中的螺纹尾部产生应力腐蚀断裂。
(3)茂名石化三加氢装置干气冷却器(E1110)小浮头螺栓断裂,材质为1Cr13 、35CrMoA使用约一周时间,均断裂,后改用Q235,使用良好。
1Cr13金相组织为马氏体,对SSCC最敏感,且硬度高,在H2S+H2O的作用下,易产生应力腐蚀断裂。
2、催化装置(1)茂名石化二催化装置冷305/1、2小浮头螺栓断裂,材质为2Cr13,后改用Q235,使用良好。
h2s对金属的腐蚀
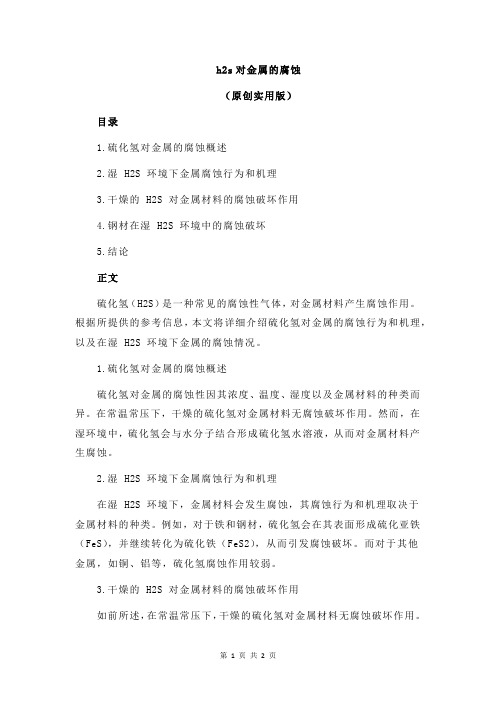
h2s对金属的腐蚀(原创实用版)目录1.硫化氢对金属的腐蚀概述2.湿 H2S 环境下金属腐蚀行为和机理3.干燥的 H2S 对金属材料的腐蚀破坏作用4.钢材在湿 H2S 环境中的腐蚀破坏5.结论正文硫化氢(H2S)是一种常见的腐蚀性气体,对金属材料产生腐蚀作用。
根据所提供的参考信息,本文将详细介绍硫化氢对金属的腐蚀行为和机理,以及在湿 H2S 环境下金属的腐蚀情况。
1.硫化氢对金属的腐蚀概述硫化氢对金属的腐蚀性因其浓度、温度、湿度以及金属材料的种类而异。
在常温常压下,干燥的硫化氢对金属材料无腐蚀破坏作用。
然而,在湿环境中,硫化氢会与水分子结合形成硫化氢水溶液,从而对金属材料产生腐蚀。
2.湿 H2S 环境下金属腐蚀行为和机理在湿 H2S 环境下,金属材料会发生腐蚀,其腐蚀行为和机理取决于金属材料的种类。
例如,对于铁和钢材,硫化氢会在其表面形成硫化亚铁(FeS),并继续转化为硫化铁(FeS2),从而引发腐蚀破坏。
而对于其他金属,如铜、铝等,硫化氢腐蚀作用较弱。
3.干燥的 H2S 对金属材料的腐蚀破坏作用如前所述,在常温常压下,干燥的硫化氢对金属材料无腐蚀破坏作用。
因此,在储存和使用金属材料时,应注意环境湿度的控制,以减少硫化氢腐蚀的可能性。
4.钢材在湿 H2S 环境中的腐蚀破坏钢材在湿 H2S 环境中容易引发腐蚀破坏。
硫化氢与钢材表面的铁发生反应,形成硫化亚铁,并继续转化为硫化铁,导致钢材表面出现锈蚀、脱落等现象。
此外,硫化氢还会加剧钢材的应力腐蚀开裂,从而加速钢材的损坏。
5.结论综上所述,硫化氢对金属材料的腐蚀作用因金属材料种类、环境条件等因素而异。
在湿 H2S 环境下,金属材料容易发生腐蚀,尤其是钢材。
湿硫化氢腐蚀
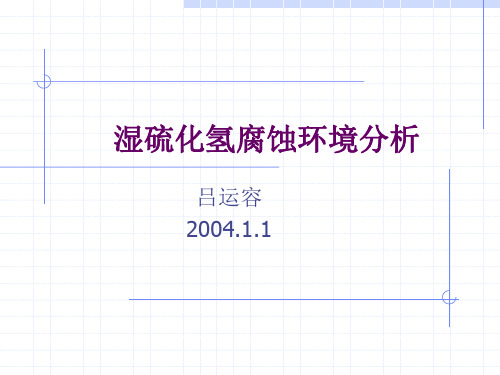
容器内表面HB图
三加氢:1、循环氢压缩机C1101气体引压阀阀杆与 阀体螺纹连接处断裂,上阀杆飞出,大量氢气喷出, 车间发现并处理用时,幸未发生恶性事故。(阀门
结构用材质与四加氢相同,损坏原因一样,断口为
典型脆性断口,判定为湿硫化氢应力腐蚀断裂。
(SSCC、HIC) )
四加氢
循环氢压缩机 C301 气体引压阀阀盖螺纹连接
组织为马氏体,对SSCC最敏感,这样高硬度
(远高于HB235)与敏感的马氏体组织的阀
盖在瓦斯HS+H2O的作用下,在应力集中的螺
纹尾部产生应力腐蚀断裂。
1、1Cr13、2 Cr13、3 Cr13金相组织为马氏体
组织,硬度高,对SCC最敏感,易产生应力腐
蚀断裂。不宜用于湿硫化氢应力腐蚀环境。
2、湿硫化氢应力腐蚀环境下使用时,选购阀
处断裂,阀杆与阀盖飞出,大量氢气喷出,车 间发现并处理用时,幸未发生恶性事故。(已 发生 2 次)断口为典型脆性断口,判定为 湿硫
化氢应力腐蚀断裂。(S质为 18-8奥氏体不锈钢(含Cr18.2、Ni8.62), 硬度HRC56,断裂处材质为Cr13(含Cr14.8), 硬度HRC70,且1Cr13、2 Cr13、3 Cr13金相
三加氢
干气冷却器(E1110)小浮头螺栓断裂,材
质为1Cr13 、35CrMoA使用约一周时间,均
断裂,后改用Q235,使用良好。 1Cr13、2
Cr13、3 Cr13金相组织为马氏体,对SSCC
最敏感,且硬度高,在HS+H2O的作用下,
易产生应力腐蚀断裂。 35CrMoA为中碳调
质低合金钢,硬度约HB280,在HS+H2O的 作用下,易产生应力腐蚀断裂。
硫化氢腐蚀类型及其防护
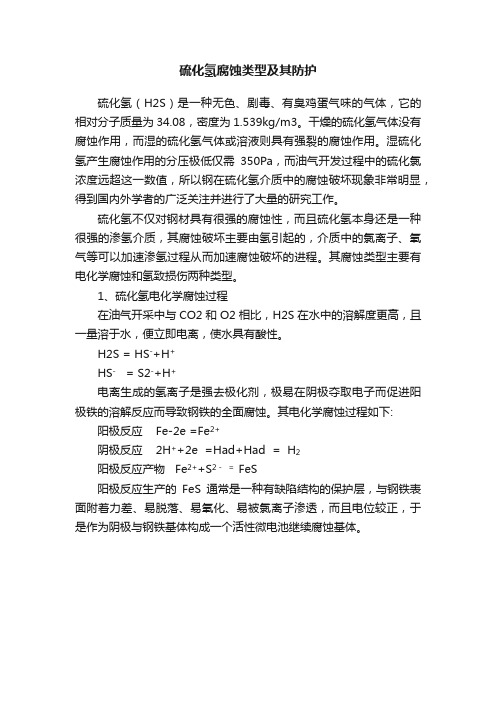
硫化氢腐蚀类型及其防护硫化氢(H2S)是一种无色、剧毒、有臭鸡蛋气味的气体,它的相对分子质量为34.08,密度为1.539kg/m3。
干燥的硫化氢气体没有腐蚀作用,而湿的硫化氢气体或溶液则具有强裂的腐蚀作用。
湿硫化氢产生腐蚀作用的分压极低仅需350Pa,而油气开发过程中的硫化氯浓度远超这一数值,所以钢在硫化氢介质中的腐蚀破坏现象非常明显,得到国内外学者的广泛关注并进行了大量的研究工作。
硫化氢不仅对钢材具有很强的腐蚀性,而且硫化氢本身还是一种很强的渗氢介质,其腐蚀破坏主要由氢引起的,介质中的氯离子、氧气等可以加速渗氢过程从而加速腐蚀破坏的进程。
其腐蚀类型主要有电化学腐蚀和氢致损伤两种类型。
1、硫化氢电化学腐蚀过程在油气开采中与CO2和O2相比,H2S在水中的溶解度更高,且一量溶于水,便立即电离,使水具有酸性。
H2S = HS-+H+HS- = S2-+H+电离生成的氢离子是强去极化剂,极易在阴极夺取电子而促进阳极铁的溶解反应而导致钢铁的全面腐蚀。
其电化学腐蚀过程如下: 阳极反应 Fe-2e =Fe2+阴极反应 2H++2e =Had+Had = H2阳极反应产物 Fe2++S2- = FeS阳极反应生产的FeS通常是一种有缺陷结构的保护层,与钢铁表面附着力差、易脱落、易氧化、易被氯离子渗透,而且电位较正,于是作为阴极与钢铁基体构成一个活性微电池继续腐蚀基体。
2、氢损伤H2S水溶液对钢材电化学腐蚀的另一个产物是氢。
一般认为反应生成的氢有两个去向,一是氢原子间结合生成分子氢而排出,另一个去向就是吸附于钢材表面的氢原子因半径小具有很强的渗透性,可以被钢材吸收进入钢材内部的晶格中,溶于晶格中的氢原子有很强的游离性,在一定条件下引起氢损伤。
在含H2S酸性油气中,氢损伤主要表现为硫化物应力开裂(SSCC)、氢致开裂(HIC)和氢鼓泡(HB)等几种破坏形式。
A、氢鼓泡(Hydrogen bubbling,HB)H2S在电化学腐蚀过程中产生的氢原子具有很强的渗透性,可以向钢材内部渗透,并在晶粒界面、夹杂面、位错、蚀坑等缺陷部位聚集而结合成氢分子。
湿H2S环境金属材料防腐解析
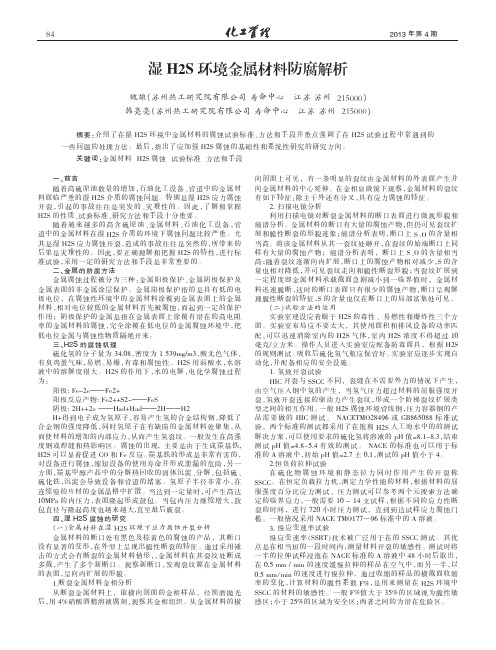
2013年第4期湿H2S环境金属材料防腐解析魏雄(苏州热工研究院有限公司寿命中心江苏苏州215000)韩亮亮(苏州热工研究院有限公司寿命中心江苏苏州215000)摘要:介绍了在湿H2S环境中金属材料的腐蚀试验标准、方法和手段并重点强调了在H2S试验过程中常遇到的一些问题的处理方法。
最后,指出了应加强H2S腐蚀的基础性和系统性研究的研究方向。
关键词:金属材料H2S腐蚀试验标准方法和手段一、前言随着高硫原油数量的增加,石油化工设备、管道中的金属材料面临严重的湿H2S介质的腐蚀问题。
特别是湿H2S应力腐蚀开裂,引起的事故往往是突发的、灾难性的。
因此,了解和掌握H2S的性质、试验标准、研究方法和手段十分重要。
随着越来越多的高含硫原油、金属材料、石油化工设备,管道中的金属材料在湿H2S介质的环境下腐蚀问题比较严重。
尤其是湿H2S应力腐蚀开裂,造成的事故往往是突然的,所带来的后果是灾难性的。
因此,要正确理解和把握H2S的特性,进行标准试验,采用一定的研究方法和手段是非常重要的。
二、金属的防腐方法金属腐蚀过程被分为三种:金属阳极保护、金属阴极保护及金属表面的非金属涂层保护。
金属阳极保护指的是具有低的电极电位,在腐蚀性环境中的金属材料涂覆到金属表面上的金属材料,相对电位较低的金属材料首先被腐蚀,而起到一定的保护作用;阴极保护的金属是指在金属表面上涂覆有潜在的高电阻率的金属材料的腐蚀,完全涂覆在低电位的金属腐蚀环境中,把低电位金属与腐蚀性物质隔绝开来。
三、H2S的腐蚀机理硫化氢的分子量为34.08,密度为1539mg/m3,酸无色气体,有臭鸡蛋气味,易燃、易爆,有毒和腐蚀性。
H2S用弱酸水,水溶液中的溶解度很大。
H2S的作用下,水的电解,电化学腐蚀过程为:阳极:Fe-2e———Fe2+阳极反应产物:Fe2++S2-———FeS阴极:2H++2e———Had+Had———2H———H2H+得到电子成为氢原子,容易产生氢的合金结构钢,降低了合金钢的强度降低,同时氢原子在有缺陷的金属材料处聚集,从而使材料的增加的内部应力,从而产生氢裂纹。
湿硫化氢腐蚀简介
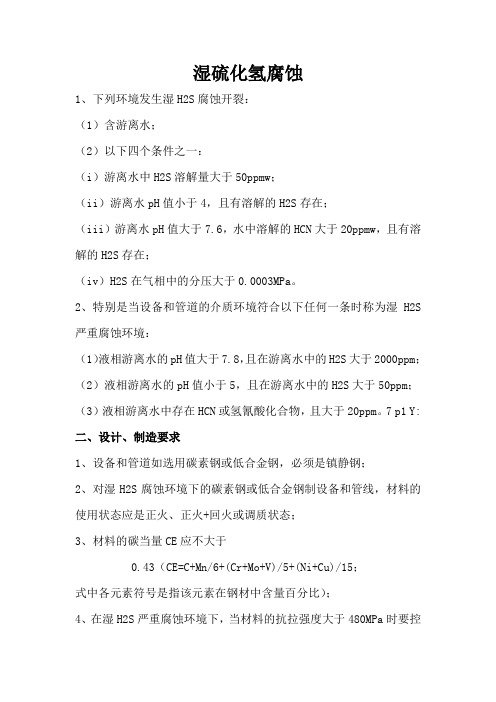
湿硫化氢腐蚀1、下列环境发生湿H2S腐蚀开裂:(1)含游离水;(2)以下四个条件之一:(i)游离水中H2S溶解量大于50ppmw;(ii)游离水pH值小于4,且有溶解的H2S存在;(iii)游离水pH值大于7.6,水中溶解的HCN大于20ppmw,且有溶解的H2S存在;(iv)H2S在气相中的分压大于0.0003MPa。
2、特别是当设备和管道的介质环境符合以下任何一条时称为湿H2S 严重腐蚀环境:(1)液相游离水的pH值大于7.8,且在游离水中的H2S大于2000ppm;(2)液相游离水的pH值小于5,且在游离水中的H2S大于50ppm;(3)液相游离水中存在HCN或氢氰酸化合物,且大于20ppm。
7 p1 Y:二、设计、制造要求1、设备和管道如选用碳素钢或低合金钢,必须是镇静钢;2、对湿H2S腐蚀环境下的碳素钢或低合金钢制设备和管线,材料的使用状态应是正火、正火+回火或调质状态;3、材料的碳当量CE应不大于0.43(CE=C+Mn/6+(Cr+Mo+V)/5+(Ni+Cu)/15;式中各元素符号是指该元素在钢材中含量百分比);4、在湿H2S严重腐蚀环境下,当材料的抗拉强度大于480MPa时要控制其S含量不大于0.002%,P含量不大于0.008%,Mn含量不大于1.30%,且应进行抗HIC性能试验或恒负荷拉伸试验。
5、在湿H2S环境下,应尽量少选择焊接。
如采取焊接,原则上应进行焊后消除应力热处理,热处理温度应按标准要求取上限。
6、热处理后碳素钢或碳锰钢焊接接头的硬度应不大于HB200,其它低合金钢母材和焊接接头的硬度应不大于HB237;7、热加工成形的碳素钢或低合金钢制管道元件,成形后应进行恢复力学性能热处理,且其硬度不大于HB225;8、冷加工成形的碳素钢或低合金钢制设备和管道元件,当冷变形量大于5%时,成形后应进行消除应力热处理,且其硬度不大于HB200。
但对于冷变形量不大于15%且硬度不大于HB190时,可不进行消除应力热处理;9、接触湿硫化氢环境碳素钢螺栓的硬度应不大于HB200,合金钢螺栓的硬度应不大于HB225;10、铬钼钢制设备和管道热处理后母材和焊接接头的硬度应不大于HB225(1Cr-0.5Mo、1.25Cr-0.5Mo)、HB235(2.25Cr-1Mo、5Cr-1Mo)和HB248(9Cr-1Mo);11、铁素体不锈钢、马氏体不锈钢和奥氏体不锈钢的母材和焊接接头的硬度应不大于HRC22,其中奥氏体不锈钢的碳含量不大于0.10%,且经过固溶处理或稳定化处理;12、双相不锈钢的母材和焊接接头的硬度应不大于HRC28,其铁素体含量应在35-65%的范围内;.13、容器内在焊接接头两侧50mm范围内的表面进行防护,可在表面喷锌、喷铝并用非金属涂料封闭的方法;14、不使用承插焊形式的管件;15、结构上应尽量避免应力集中;16、设备壳体或卷制管道用钢板厚度大于12mm时,应按JB/T4730进行超声波检测,符合Ⅱ级要求。
论述炼油设备的湿硫化氢腐蚀与防治方法

论述炼油设备的湿硫化氢腐蚀与防治方法近年来,石油公司大幅度的增加了对含硫或者高含硫原油的加工数量,因而炼油设备也出现比较严重的腐蚀现象。
而在各个种类的腐蚀中,最为严重或者说对设备伤害最大的是高温硫腐蚀以及湿硫化氢造成的设备损坏。
对于高温硫腐蚀只要更换采用适当的耐高温硫腐蚀的设备材料即可大大的缓解此类腐蚀,但是对湿硫化氢所造成的腐蚀进行防治就会有较大的困难。
含硫原油对设备进行腐蚀从而产生硫铁化合物,而硫铁化合物一旦与空气中的氧气接触,它们就会迅速的发生化学反应,也会产生大量的热。
如果这些热量不能够及时的向周边消散,就会导致设备局部迅速升温,而原油属于可燃物质,这就很可能引起具有可怕后果的自燃事故,也会对人类的正常生活及经济活动带来巨大的损失。
下面我们将会着重讨论引起这类事故主要原理及相应的预防治理措施。
1 湿硫化氢对设备的腐蚀机理湿硫化氢在水中极易发生离解,它的腐蚀过程就是一个化学反应,在阳极会出现一般性腐蚀,结果为产生FeS的膜。
从而使金属表面遭到破坏,形成腐蚀坑而出现回路电池的作用,是破坏程度进一步加深。
而在阴极处会出现因化学反应而生成的活性很强的氢,它会在金属比较脆弱的部位比如金属的缺陷处、焊接缺陷处聚集,产生氢鼓包导致金属结构遭到破坏,即使是高强钢也难逃其魔爪。
这种现象我们通常称其为湿硫化氢应力腐蚀开裂。
一般来说,强度越高的钢越容易因此应力而受到损坏,因为强度越高,钢对应力的腐蚀也就越敏感。
碳酸盐或者是湿硫化氢还有氢氧化物等许多无机物质都是我们生产当中比较常见的应力腐蚀环境。
在我国的炼油企业中,大多数都是采用的低合金高强度钢作为其压力容器的主要材料,而之前我们也明确的表述了湿硫化氢对高强度钢的腐蚀是较为厉害的。
湿硫化氢造成的腐蚀最早出现在油田设备和管道设施上,由于近几年出现的几起重大事故,湿硫化氢也自然而然的走进了我们的视野当中,而这几起事故当中发生在1984年的雷蒙特三号炼油厂的事故就是一个最典型的案例。
湿硫化氢环境腐蚀与防护讲解

湿硫化氢环境腐蚀与防护第一章总则1.1 为规范湿硫化氢环境腐蚀与防护工作,防止发生安全事故,依据国家有关法规、标准,制定本指导意见。
1.2石油化工装置在湿硫化氢环境(含有气相或溶解在液相水中,不论是否有氢气存在的酸性工艺环境)使用的静设备,为抵抗硫化物应力腐蚀开裂(SSC)、氢诱导开裂(HIC)和应力导向氢诱导开裂(SOHIC),在设计、材料、试验、制造、检验等方面的要求。
生产、技术、设计、工程、检修、科研等部门应积极参与和配合设备管理部门做好相关工作。
1.3对处于湿硫化氢腐蚀环境中的设备抗 SSC、HIC/SWC 和 SOHIC 损伤的最低要求,其中包括碳钢和低合金钢,以及碳钢及低合金钢加不锈钢的复合钢板制造的设备。
但不包括采用在金属表面(接触介质侧)增加涂层(如喷铝等)防止基体材料腐蚀开裂的设备。
1.4凡处于湿硫化氢环境中的设备在材料选择、设备制造与检验均应满足本标准的要求,否则可能导致设备 SSC、HIC/SWC 和 SOHIC 的破坏。
1.5不包括湿硫化氢引起的电化学失重腐蚀和其他类型的开裂。
1.7 湿硫化氢腐蚀环境的定义与分类:1.7.1 介质在液相中存在游离水,且具备下列条件之一时称为湿硫化氢腐蚀环境:(1)在液相水中总硫化物含量大于 50ppmw;或(2)液相水中 PH 小于 4 且总硫化物含量大于等于 1ppmw;或(3)液相水中 PH 大于 7.6 及氢氰酸(HCN)大于等于 20ppmw,且总硫化物含量大于等于 1ppmw;或(4)气相中含有硫化氢分压大于 0.0003MPa(0.05psia)。
1.7.2 根据湿硫化氢腐蚀环境引起碳钢和低合金钢材料开裂的严重程度以及对设备安全性影响的大小,把湿硫化氢腐蚀环境分为 2 类,在第I 类环境中主要关注 SSC,而在第Ⅱ类环境中,除关注 SSC 外,还要关注HIC 和 SOHIC 等损伤。
具体划分类别如下:第 I 类环境(1)操作介质温度≤ 120℃;(2)游离水中硫化氢含量大于 50ppmw;或(3)游离水的 PH < 4,且含有少量的硫化氢;或(4)气相中硫化氢分压大于 0.0003MPa(绝压);或(5)游离水中含有少量硫化氢,溶解的 HCN 小于 20ppmw,且 PH >7.6。
湿硫化氢腐蚀环境选材要求

湿硫化氢腐蚀环境选材要求
湿硫化氢腐蚀环境对材料的要求非常严格,因为湿硫化氢腐蚀
是一种常见的腐蚀形式,特别是在石油、天然气和化工行业的设备
和管道中。
在这种环境下,材料需要具备以下几个方面的要求:
1. 耐腐蚀性,材料需要具有优异的耐腐蚀性能,能够抵抗湿硫
化氢引起的腐蚀。
通常情况下,不锈钢、镍基合金、钛合金等具有
良好的耐腐蚀性能,因此在湿硫化氢腐蚀环境中被广泛应用。
2. 强度和韧性,材料需要具备足够的强度和韧性,以应对在腐
蚀环境中可能受到的力学应力和冲击。
这对材料的选择和设计提出
了挑战,需要综合考虑材料的力学性能和耐腐蚀性能。
3. 焊接性能,在实际工程中,很多构件需要进行焊接,因此材
料的焊接性能也是考虑的重要因素。
材料需要具有良好的焊接性能,能够确保焊接接头的质量和耐腐蚀性能。
4. 经济性,除了上述性能要求外,材料的成本、加工性能等因
素也需要考虑。
在满足耐腐蚀性能的前提下,尽可能选择成本合理、加工方便的材料,以确保工程的经济性。
总的来说,湿硫化氢腐蚀环境对材料的要求主要集中在耐腐蚀性能、力学性能、焊接性能和经济性等方面。
工程师在选择材料时需要综合考虑这些因素,以确保设备和管道在湿硫化氢腐蚀环境中能够安全、可靠地运行。
湿硫化氢腐蚀类型及机理研
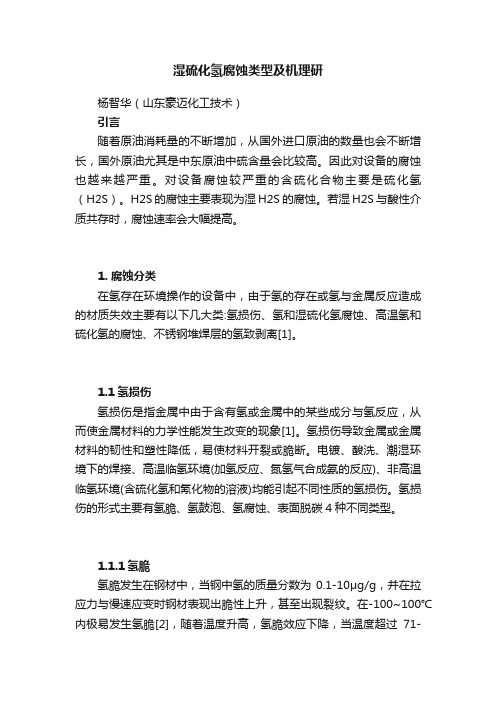
湿硫化氢腐蚀类型及机理研杨智华(山东豪迈化工技术)引言随着原油消耗量的不断增加,从国外进口原油的数量也会不断增长,国外原油尤其是中东原油中硫含量会比较高。
因此对设备的腐蚀也越来越严重。
对设备腐蚀较严重的含硫化合物主要是硫化氢(H2S)。
H2S的腐蚀主要表现为湿H2S的腐蚀。
若湿H2S与酸性介质共存时,腐蚀速率会大幅提高。
1. 腐蚀分类在氢存在环境操作的设备中,由于氢的存在或氢与金属反应造成的材质失效主要有以下几大类:氢损伤、氢和湿硫化氢腐蚀、高温氢和硫化氢的腐蚀、不锈钢堆焊层的氢致剥离[1]。
1.1氢损伤氢损伤是指金属中由于含有氢或金属中的某些成分与氢反应,从而使金属材料的力学性能发生改变的现象[1]。
氢损伤导致金属或金属材料的韧性和塑性降低,易使材料开裂或脆断。
电镀、酸洗、潮湿环境下的焊接、高温临氢环境(加氢反应、氮氢气合成氨的反应)、非高温临氢环境(含硫化氢和氰化物的溶液)均能引起不同性质的氢损伤。
氢损伤的形式主要有氢脆、氢鼓泡、氢腐蚀、表面脱碳4种不同类型。
1.1.1氢脆氢脆发生在钢材中,当钢中氢的质量分数为0.1-10μg/g,并在拉应力与慢速应变时钢材表现出脆性上升,甚至出现裂纹。
在-100~100℃内极易发生氢脆[2],随着温度升高,氢脆效应下降,当温度超过71-82℃时不太容易发生,所以实际氢脆损伤往往都是发生在装置开、停工过程的低温阶段。
若将钢材中的氢释放出来,钢材机械性能仍可恢复,因此氢脆是可逆的。
1.1.2氢鼓泡氢鼓泡形成的两个主要条件:一是存在原子状态的氢;二是金属内部存在“空穴”。
原子状态的氢来源于湿H2S对石油管道钢材表面的腐蚀,而钢材内部的“空穴”则来源于钢材的冶金缺陷和制造缺陷。
腐蚀过程中析出的氢原子向钢中扩散,在钢材的非金属夹杂物、分层和其他不连续处易聚集形成分子氢。
由于氢分子较大,难以从钢的组织内部逸出,从而形成巨大内压导致其周围组织屈服,形成表面层下的平面孔穴结构造成氢鼓泡,其分布平行于钢板表面。
湿硫化氢对金属的腐蚀讲解
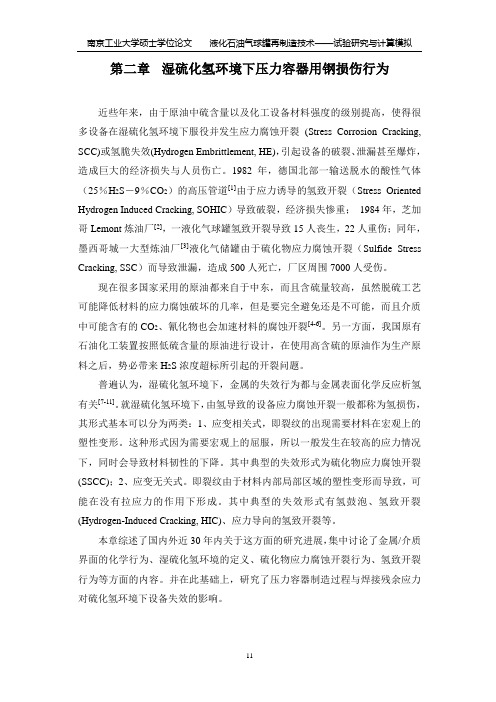
第二章湿硫化氢环境下压力容器用钢损伤行为近些年来,由于原油中硫含量以及化工设备材料强度的级别提高,使得很多设备在湿硫化氢环境下服役并发生应力腐蚀开裂(Stress Corrosion Cracking, SCC)或氢脆失效(Hydrogen Embrittlement, HE),引起设备的破裂、泄漏甚至爆炸,造成巨大的经济损失与人员伤亡。
1982年,德国北部一输送脱水的酸性气体(25%H2S-9%CO2)的高压管道[1]由于应力诱导的氢致开裂(Stress Oriented Hydrogen Induced Cracking, SOHIC)导致破裂,经济损失惨重;1984年,芝加哥Lemont炼油厂[2],一液化气球罐氢致开裂导致15人丧生,22人重伤;同年,墨西哥城一大型炼油厂[3]液化气储罐由于硫化物应力腐蚀开裂(Sulfide Stress Cracking, SSC)而导致泄漏,造成500人死亡,厂区周围7000人受伤。
现在很多国家采用的原油都来自于中东,而且含硫量较高,虽然脱硫工艺可能降低材料的应力腐蚀破坏的几率,但是要完全避免还是不可能,而且介质中可能含有的CO2、氰化物也会加速材料的腐蚀开裂[4-6]。
另一方面,我国原有石油化工装置按照低硫含量的原油进行设计,在使用高含硫的原油作为生产原料之后,势必带来H2S浓度超标所引起的开裂问题。
普遍认为,湿硫化氢环境下,金属的失效行为都与金属表面化学反应析氢有关[7-11]。
就湿硫化氢环境下,由氢导致的设备应力腐蚀开裂一般都称为氢损伤,其形式基本可以分为两类:1、应变相关式,即裂纹的出现需要材料在宏观上的塑性变形。
这种形式因为需要宏观上的屈服,所以一般发生在较高的应力情况下,同时会导致材料韧性的下降。
其中典型的失效形式为硫化物应力腐蚀开裂(SSCC);2、应变无关式。
即裂纹由于材料内部局部区域的塑性变形而导致,可能在没有拉应力的作用下形成。
其中典型的失效形式有氢鼓泡、氢致开裂(Hydrogen-Induced Cracking, HIC)、应力导向的氢致开裂等。
湿硫化氢环境腐蚀与防护讲解

湿硫化氢环境腐蚀与防护第一章总则1.1 为规范湿硫化氢环境腐蚀与防护工作,防止发生安全事故,依据国家有关法规、标准,制定本指导意见。
1.2石油化工装置在湿硫化氢环境(含有气相或溶解在液相水中,不论是否有氢气存在的酸性工艺环境)使用的静设备,为抵抗硫化物应力腐蚀开裂(SSC)、氢诱导开裂(HIC)和应力导向氢诱导开裂(SOHIC),在设计、材料、试验、制造、检验等方面的要求。
生产、技术、设计、工程、检修、科研等部门应积极参与和配合设备管理部门做好相关工作。
1.3对处于湿硫化氢腐蚀环境中的设备抗 SSC、HIC/SWC 和 SOHIC 损伤的最低要求,其中包括碳钢和低合金钢,以及碳钢及低合金钢加不锈钢的复合钢板制造的设备。
但不包括采用在金属表面(接触介质侧)增加涂层(如喷铝等)防止基体材料腐蚀开裂的设备。
1.4凡处于湿硫化氢环境中的设备在材料选择、设备制造与检验均应满足本标准的要求,否则可能导致设备 SSC、HIC/SWC 和 SOHIC 的破坏。
1.5不包括湿硫化氢引起的电化学失重腐蚀和其他类型的开裂。
1.7 湿硫化氢腐蚀环境的定义与分类:1.7.1 介质在液相中存在游离水,且具备下列条件之一时称为湿硫化氢腐蚀环境:(1)在液相水中总硫化物含量大于 50ppmw;或(2)液相水中 PH 小于 4 且总硫化物含量大于等于 1ppmw;或(3)液相水中 PH 大于 7.6 及氢氰酸(HCN)大于等于 20ppmw,且总硫化物含量大于等于 1ppmw;或(4)气相中含有硫化氢分压大于 0.0003MPa(0.05psia)。
1.7.2 根据湿硫化氢腐蚀环境引起碳钢和低合金钢材料开裂的严重程度以及对设备安全性影响的大小,把湿硫化氢腐蚀环境分为 2 类,在第I 类环境中主要关注 SSC,而在第Ⅱ类环境中,除关注 SSC 外,还要关注HIC 和 SOHIC 等损伤。
具体划分类别如下:第 I 类环境(1)操作介质温度≤ 120℃;(2)游离水中硫化氢含量大于 50ppmw;或(3)游离水的 PH < 4,且含有少量的硫化氢;或(4)气相中硫化氢分压大于 0.0003MPa(绝压);或(5)游离水中含有少量硫化氢,溶解的 HCN 小于 20ppmw,且 PH >7.6。
湿硫化氢腐蚀与防护
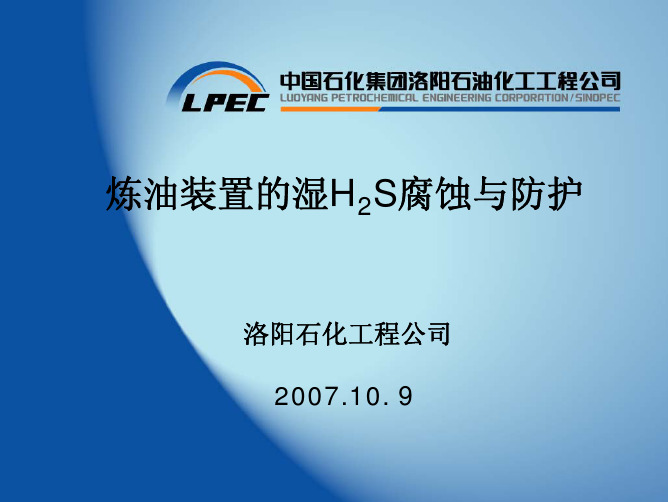
影响H2S-H2O腐蚀的因素:
原料油 温度 H2S含量 氰化物的浓度 氨的浓度 pH值 钢材的显微组织
D防护措施
注水,将氰化物脱出; 注入有机缓蚀剂; 适当提高材质,使用抗HIC钢。
E 腐蚀监测
低温腐蚀探针安装部位为:分馏塔塔顶一级冷却器出口总 管,吸收稳定系统冷凝水集中部位。 腐蚀挂片安装在塔器、冷却器内部腐蚀严重区域。 日常化学分析,分析对象为各塔顶冷凝水。
E 腐蚀监测
腐蚀严重区域还应该采取连续腐蚀监控技术以监测腐蚀 的程度,如果腐蚀高于目标控制值(对于塔顶系行 防治。 原油电脱盐:控制脱后含盐、含水和钠离子含量到规定 指标; 塔器的低温腐蚀部位:采用低温腐蚀探针,腐蚀挂片, 日常化学分析等方法进行监测。
C 腐蚀原因
腐蚀介质主要来源于原油中的氯化物(NaCl、MgCl2、 CaCl2 和有机含氯清蜡剂)和硫化物。 具体腐蚀过程如下:
Fe+2HCl → FeCl2十H2 FeCl2+H2S → FeS↓+HCI FeS+2HCl → FeCl2+H2S
冷凝系统严重腐蚀,尤其是气液两相转变的“露点”部位, 剧烈的腐蚀是由于低pH值的盐酸引起的: Fe+2H+ → Fe2++H2 ↑ FeS+2H+ → Fe2++H2S ↑ 随着冷凝过程的进行,冷凝水量不断增加,HCl水溶液不 断被稀释,pH值提高,腐蚀应有所缓和。但在这一过程 中,H2S的溶解度迅速增加,提供了更多的H+,促进了氢 去极化腐蚀反应: Fe2++H2S → FeS↓十2H+ 这样既破坏了硫化铁膜,又加速了腐蚀进程 。
炼油装置的湿H2S腐蚀与防护
洛阳石化工程公司 2007.10. 9
湿H2S腐蚀破裂的试验方法
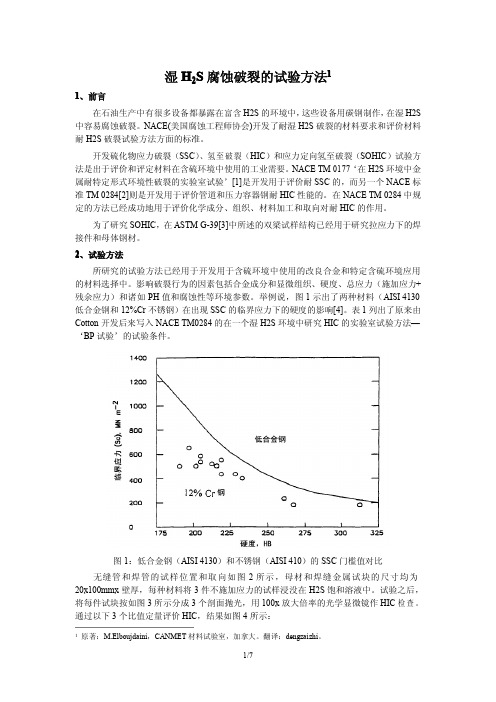
湿H2S腐蚀破裂的试验方法11、前言在石油生产中有很多设备都暴露在富含H2S的环境中,这些设备用碳钢制作,在湿H2S 中容易腐蚀破裂。
NACE(美国腐蚀工程师协会)开发了耐湿H2S破裂的材料要求和评价材料耐H2S破裂试验方法方面的标准。
开发硫化物应力破裂(SSC)、氢至破裂(HIC)和应力定向氢至破裂(SOHIC)试验方法是出于评价和评定材料在含硫环境中使用的工业需要。
NACE TM0177‘在H2S环境中金属耐特定形式环境性破裂的实验室试验’[1]是开发用于评价耐SSC的,而另一个NACE标准TM0284[2]则是开发用于评价管道和压力容器钢耐HIC性能的。
在NACE TM0284中规定的方法已经成功地用于评价化学成分、组织、材料加工和取向对耐HIC的作用。
为了研究SOHIC,在ASTM G-39[3]中所述的双梁试样结构已经用于研究拉应力下的焊接件和母体钢材。
2、试验方法所研究的试验方法已经用于开发用于含硫环境中使用的改良合金和特定含硫环境应用的材料选择中。
影响破裂行为的因素包括合金成分和显微组织、硬度、总应力(施加应力+残余应力)和诸如PH值和腐蚀性等环境参数。
举例说,图1示出了两种材料(AISI4130低合金钢和12%Cr不锈钢)在出现SSC的临界应力下的硬度的影响[4]。
表1列出了原来由Cotton开发后来写入NACE TM0284的在一个湿H2S环境中研究HIC的实验室试验方法—‘BP试验’的试验条件。
图1:低合金钢(AISI4130)和不锈钢(AISI410)的SSC门槛值对比无缝管和焊管的试样位置和取向如图2所示,母材和焊缝金属试块的尺寸均为20x100mmx壁厚,每种材料将3件不施加应力的试样浸没在H2S饱和溶液中。
试验之后,将每件试块按如图3所示分成3个剖面抛光,用100x放大倍率的光学显微镜作HIC检查。
通过以下3个比值定量评价HIC,结果如图4所示:1原著:M.Elboujdaini,CANMET材料试验室,加拿大。
湿硫化氢对金属的腐蚀

第二章 湿硫化氢环境下压力容器用钢损伤行为近些年来,由于原油中硫含量以及化工设备材料强度的级别提高,使得很多设备在湿硫化氢环境下服役并发生应力腐蚀开裂(StressCorrosionCracking,SCC)或氢脆失效(HydrogenEmbrittlement,HE),引起设备的破裂、泄漏甚至爆炸,造成巨大的经济损失与人员伤亡。
1982年,德国北部一输送脱水的酸性气体(25%H 2S -9%CO 2)的高压管道[1]由于应力诱导的氢致开裂(StressOrientedHydrogenInducedCracking,SOHIC )导致破裂,经济损失惨重;1984。
1研究了压力容器制造过程与焊接残余应力对硫化氢环境下设备失效的影响。
2.1湿硫化氢环境下金属/介质界面的化学行为金属材料在湿硫化氢环境下的开裂行为,主要是金属在其表面与介质发生反应生成氢原子向金属内部渗透所导致[12]。
但是金属/介质界面的化学反应十分复杂,现在关于这方面还依然说法不一。
Panasenko [14]提出在低pH 值的酸性溶液中,金属表面发生阳极溶解发应,即ads S H Fe S H Fe )(22→+(2-1)e S H Fe S H Fe ads 2)()(222+→+(2-2)S H Fe S H Fe 2222)(+→++(2-3)而Lofa [8]等人则提出了另一个阳极反应,即+-+→+O H HS Fe O H S H Fe ads 322)(+(2-4) e HS Fe HS Fe ads2)()(+→+-(2-5) O H S H Fe O H HS Fe 2223)(++→++++(2-6)以上的反应中有两个共同的特点,金属材料表面的Fe 向Fe +转化的过程,导致金属/介质界面++Fe 2---+→+2S H e HS (2-12)+-++→+H FeS HS Fe 22222(2-13)但是在经过如何反应获得=HS 离子问题上并没有很好的阐述。
湿硫化氢腐蚀简介

湿硫化氢腐蚀1、下列环境发生湿H2S腐蚀开裂:(1)含游离水;(2)以下四个条件之一:(i)游离水中H2S溶解量大于50ppmw;(ii)游离水pH值小于4,且有溶解的H2S存在;(iii)游离水pH值大于7.6,水中溶解的HCN大于20ppmw,且有溶解的H2S存在;(iv)H2S在气相中的分压大于0.0003MPa。
2、特别是当设备和管道的介质环境符合以下任何一条时称为湿H2S 严重腐蚀环境:(1)液相游离水的pH值大于7.8,且在游离水中的H2S大于2000ppm;(2)液相游离水的pH值小于5,且在游离水中的H2S大于50ppm;(3)液相游离水中存在HCN或氢氰酸化合物,且大于20ppm。
7 p1 Y:二、设计、制造要求1、设备和管道如选用碳素钢或低合金钢,必须是镇静钢;2、对湿H2S腐蚀环境下的碳素钢或低合金钢制设备和管线,材料的使用状态应是正火、正火+回火或调质状态;3、材料的碳当量CE应不大于0.43(CE=C+Mn/6+(Cr+Mo+V)/5+(Ni+Cu)/15;式中各元素符号是指该元素在钢材中含量百分比);4、在湿H2S严重腐蚀环境下,当材料的抗拉强度大于480MPa时要控制其S含量不大于0.002%,P含量不大于0.008%,Mn含量不大于1.30%,且应进行抗HIC性能试验或恒负荷拉伸试验。
5、在湿H2S环境下,应尽量少选择焊接。
如采取焊接,原则上应进行焊后消除应力热处理,热处理温度应按标准要求取上限。
6、热处理后碳素钢或碳锰钢焊接接头的硬度应不大于HB200,其它低合金钢母材和焊接接头的硬度应不大于HB237;7、热加工成形的碳素钢或低合金钢制管道元件,成形后应进行恢复力学性能热处理,且其硬度不大于HB225;8、冷加工成形的碳素钢或低合金钢制设备和管道元件,当冷变形量大于5%时,成形后应进行消除应力热处理,且其硬度不大于HB200。
但对于冷变形量不大于15%且硬度不大于HB190时,可不进行消除应力热处理;9、接触湿硫化氢环境碳素钢螺栓的硬度应不大于HB200,合金钢螺栓的硬度应不大于HB225;10、铬钼钢制设备和管道热处理后母材和焊接接头的硬度应不大于HB225(1Cr-0.5Mo、1.25Cr-0.5Mo)、HB235(2.25Cr-1Mo、5Cr-1Mo)和HB248(9Cr-1Mo);11、铁素体不锈钢、马氏体不锈钢和奥氏体不锈钢的母材和焊接接头的硬度应不大于HRC22,其中奥氏体不锈钢的碳含量不大于0.10%,且经过固溶处理或稳定化处理;12、双相不锈钢的母材和焊接接头的硬度应不大于HRC28,其铁素体含量应在35-65%的范围内;.13、容器内在焊接接头两侧50mm范围内的表面进行防护,可在表面喷锌、喷铝并用非金属涂料封闭的方法;14、不使用承插焊形式的管件;15、结构上应尽量避免应力集中;16、设备壳体或卷制管道用钢板厚度大于12mm时,应按JB/T4730进行超声波检测,符合Ⅱ级要求。
湿硫化氢腐蚀简介

湿硫化氢腐蚀1、下列环境发生湿H2S腐蚀开裂:(1)含游离水;(2)以下四个条件之一:(i)游离水中H2S溶解量大于50ppmw;(ii)游离水pH值小于4,且有溶解的H2S存在;(iii)游离水pH值大于7.6,水中溶解的HCN大于20ppmw,且有溶解的H2S存在;(iv)H2S在气相中的分压大于0.0003MPa。
2、特别是当设备和管道的介质环境符合以下任何一条时称为湿H2S严重腐蚀环境:(1)液相游离水的pH值大于7.8,且在游离水中的H2S大于2000ppm;(2)液相游离水的pH值小于5,且在游离水中的H2S大于50ppm;(3)液相游离水中存在HCN或氢氰酸化合物,且大于20ppm。
7 p1 Y:二、设计、制造要求1、设备和管道如选用碳素钢或低合金钢,必须是镇静钢;2、对湿H2S腐蚀环境下的碳素钢或低合金钢制设备和管线,材料的使用状态应是正火、正火+回火或调质状态;3、材料的碳当量CE应不大于0.43(CE=C+Mn/6+(Cr+Mo+V)/5+(Ni+Cu)/15;式中各元素符号是指该元素在钢材中含量百分比);4、在湿H2S严重腐蚀环境下,当材料的抗拉强度大于480MPa时要控制其S含量不大于0.002%,P含量不大于0.008%,Mn含量不大于1.30%,且应进行抗HIC性能试验或恒负荷拉伸试验。
5、在湿H2S环境下,应尽量少选择焊接。
如采取焊接,原则上应进行焊后消除应力热处理,热处理温度应按标准要求取上限。
6、热处理后碳素钢或碳锰钢焊接接头的硬度应不大于HB200,其它低合金钢母材和焊接接头的硬度应不大于HB237;7、热加工成形的碳素钢或低合金钢制管道元件,成形后应进行恢复力学性能热处理,且其硬度不大于HB225;8、冷加工成形的碳素钢或低合金钢制设备和管道元件,当冷变形量大于5%时,成形后应进行消除应力热处理,且其硬度不大于HB200。
但对于冷变形量不大于15%且硬度不大于HB190时,可不进行消除应力热处理;9、接触湿硫化氢环境碳素钢螺栓的硬度应不大于HB200,合金钢螺栓的硬度应不大于HB225;10、铬钼钢制设备和管道热处理后母材和焊接接头的硬度应不大于HB225(1Cr-0.5Mo、1.25Cr-0.5Mo)、HB235(2.25Cr-1Mo、5Cr-1Mo)和HB248(9Cr-1Mo);11、铁素体不锈钢、马氏体不锈钢和奥氏体不锈钢的母材和焊接接头的硬度应不大于HRC22,其中奥氏体不锈钢的碳含量不大于0.10%,且经过固溶处理或稳定化处理;12、双相不锈钢的母材和焊接接头的硬度应不大于HRC28,其铁素体含量应在35-65%的范围内;.13、容器内在焊接接头两侧50mm范围内的表面进行防护,可在表面喷锌、喷铝并用非金属涂料封闭的方法;14、不使用承插焊形式的管件;15、结构上应尽量避免应力集中;16、设备壳体或卷制管道用钢板厚度大于12mm时,应按JB/T4730进行超声波检测,符合Ⅱ级要求。
湿硫化氢腐蚀

三加氢
干气冷却器(E1110)小浮头螺栓断裂,材 质为1Cr13 、35CrMoA使用约一周时间,均 断裂,后改用Q235,使用良好。 1Cr13、2 Cr13、3 Cr13金相组织为马氏体,对SSCC 最敏感,且硬度高,在HS+H2O的作用下, 易产生应力腐蚀断裂。 35CrMoA为中碳调 质低合金钢,硬度约HB280,在HS+H2O的 作用下,易产生应力腐蚀断裂。
二催化: 冷305/1、2小浮头螺栓断裂,材质为 2Cr13,后改用Q235,使用良好。 1Cr13、2 Cr13、3 Cr13金相组织为马氏 体,对SSCC最敏感,且硬度高,在HS+H2O 的作用下,易产生应力腐蚀断裂。
气 柜:
2#瓦斯压缩机气阀阀座与升程限制器连接螺栓 断裂,气阀阀座与连接螺栓掉入气缸,缸盖及 水套被打烂飞出,大量瓦斯喷出,车间发现并 处理用时,幸未发生恶性事故。
经分析认为:1、大小头开裂属于H2S应力腐蚀开裂; (SSCC)2、SSCC裂纹起源于大小头凹陷处,此处由 于存在涡流产生细小腐蚀坑点,并向外壁抗展。3、大 小头材料为较高纯度的碳钢(S=0.003%,P=0.004%), 硬度也低于HB235,但仍不能防止在这种苛刻条件下 发生SSCC。应采用更高纯度的搞HIC钢。
湿硫化氢腐蚀
腐蚀实例
一加氢:汽提塔顶回流罐(容104)器壁97 年查出60多个鼓泡,该容器报废更新。容 器材质为A3F沸腾钢,钢的纯净度不够,钢 内夹杂物多,在湿硫化氢环境下,形成氢鼓 泡失效(HB)。GB150-1998已不允许用沸 腾钢制造成压力容器,更不能用于有应力腐 蚀开裂敏感性的介质。
容器内表面HB图
17、胜利炼油厂溶剂再生塔顶酸性气冷却器 内浮头盖(材质为12AlMoV,法兰圈材质为 1 Cr13, 焊 条 Cr25Ni13), 使 用 后 在 CO2H2S-H2O一侧,浮头盖与法兰圈的焊缝熔合 线处发生断裂,并延伸至母材。