晶圆制造流程
晶圆制造工艺流程和处理工序

晶圆制造工艺流程和处理工序晶圆制造工艺流程1、表面清洗2、初次氧化3、CVD(Chemical Vapor deposiTIon) 法沉积一层Si3N4 (Hot CVD 或LPCVD) 。
(1)常压CVD (Normal Pressure CVD) (2)低压CVD (Low Pressure CVD) (3)热CVD (Hot CVD)/(thermal CVD) (4)电浆增强CVD (Plasma Enhanced CVD) (5)MOCVD (Metal Organic CVD) 分子磊晶成长(Molecular Beam Epitaxy) (6)外延生长法(LPE)4、涂敷光刻胶(1)光刻胶的涂敷(2)预烘(pre bake) (3)曝光(4)显影(5)后烘(post bake) (6)腐蚀(etching) (7)光刻胶的去除5、此处用干法氧化法将氮化硅去除6 、离子布植将硼离子(B+3) 透过SiO2 膜注入衬底,形成P 型阱7、去除光刻胶,放高温炉中进行退火处理8、用热磷酸去除氮化硅层,掺杂磷(P+5) 离子,形成N 型阱9、退火处理,然后用HF 去除SiO2 层10、干法氧化法生成一层SiO2 层,然后LPCVD 沉积一层氮化硅11、利用光刻技术和离子刻蚀技术,保留下栅隔离层上面的氮化硅层12、湿法氧化,生长未有氮化硅保护的SiO2 层,形成PN 之间的隔离区13、热磷酸去除氮化硅,然后用HF 溶液去除栅隔离层位置的SiO2 ,并重新生成品质更好的SiO2 薄膜, 作为栅极氧化层。
14、LPCVD 沉积多晶硅层,然后涂敷光阻进行光刻,以及等离子蚀刻技术,栅极结构,并氧化生成SiO2 保护层。
15、表面涂敷光阻,去除P 阱区的光阻,注入砷(As) 离子,形成NMOS 的源漏极。
用同样的方法,在N 阱区,注入B 离子形成PMOS 的源漏极。
16、利用PECVD 沉积一层无掺杂氧化层,保护元件,并进行退火处理。
晶圆生产工艺与流程介绍
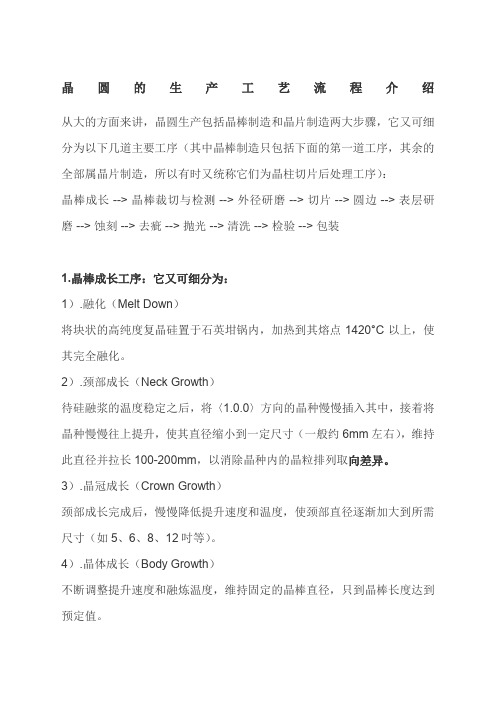
晶圆的生产工艺流程介绍从大的方面来讲,晶圆生产包括晶棒制造和晶片制造两大步骤,它又可细分为以下几道主要工序(其中晶棒制造只包括下面的第一道工序,其余的全部属晶片制造,所以有时又统称它们为晶柱切片后处理工序):晶棒成长 --> 晶棒裁切与检测 --> 外径研磨 --> 切片 --> 圆边 --> 表层研磨 --> 蚀刻 --> 去疵 --> 抛光 --> 清洗 --> 检验 --> 包装1.晶棒成长工序:它又可细分为:1).融化(Melt Down)将块状的高纯度复晶硅置于石英坩锅内,加热到其熔点1420°C以上,使其完全融化。
2).颈部成长(Neck Growth)待硅融浆的温度稳定之后,将〈1.0.0〉方向的晶种慢慢插入其中,接着将晶种慢慢往上提升,使其直径缩小到一定尺寸(一般约6mm左右),维持此直径并拉长100-200mm,以消除晶种内的晶粒排列取向差异。
3).晶冠成长(Crown Growth)颈部成长完成后,慢慢降低提升速度和温度,使颈部直径逐渐加大到所需尺寸(如5、6、8、12吋等)。
4).晶体成长(Body Growth)不断调整提升速度和融炼温度,维持固定的晶棒直径,只到晶棒长度达到预定值。
5).尾部成长(Tail Growth)当晶棒长度达到预定值后再逐渐加快提升速度并提高融炼温度,使晶棒直径逐渐变小,以避免因热应力造成排差和滑移等现象产生,最终使晶棒与液面完全分离。
到此即得到一根完整的晶棒。
2.晶棒裁切与检测(Cutting & Inspection)将长成的晶棒去掉直径偏小的头、尾部分,并对尺寸进行检测,以决定下步加工的工艺参数。
3.外径研磨(Surface Grinding & Shaping)由于在晶棒成长过程中,其外径尺寸和圆度均有一定偏差,其外园柱面也凹凸不平,所以必须对外径进行修整、研磨,使其尺寸、形状误差均小于允许偏差。
晶圆制造工艺流程

晶圆制造工艺流程1、表面清洗2、初次氧化3、 CVD(Chemic al Vapordeposi tion)法沉积一层Si3N4(Hot CVD 或 LPCVD)。
(1)常压 CVD (Normal Pressu re CVD)(2)低压 CVD (Low Pressu re CVD)(3)热 CVD (Hot CVD)/(therma l CVD)(4)电浆增强 CVD (Plasma Enhanc ed CVD)(5)MOCVD(MetalOrgani c CVD) & 分子磊晶成长 (Molecu lar Beam Epitax y)(6)外延生长法(LPE)4、涂敷光刻胶(1)光刻胶的涂敷(2)预烘(pre bake)(3)曝光(4)显影(5)后烘(post bake)(6)腐蚀 (etchin g)(7)光刻胶的去除5、此处用干法氧化法将氮化硅去除6 、离子布植将硼离子(B+3) 透过SiO2 膜注入衬底,形成P 型阱7、去除光刻胶,放高温炉中进行退火处理8、用热磷酸去除氮化硅层,掺杂磷(P+5) 离子,形成N 型阱9、退火处理,然后用HF 去除SiO2 层10、干法氧化法生成一层SiO2 层,然后 LPCVD沉积一层氮化硅11、利用光刻技术和离子刻蚀技术,保留下栅隔离层上面的氮化硅层12、湿法氧化,生长未有氮化硅保护的SiO2 层,形成PN 之间的隔离区13、热磷酸去除氮化硅,然后用HF 溶液去除栅隔离层位置的SiO2 ,并重新生成品质更好的SiO2 薄膜, 作为栅极氧化层。
14、LPCVD沉积多晶硅层,然后涂敷光阻进行光刻,以及等离子蚀刻技术,栅极结构,并氧化生成SiO2 保护层。
15、表面涂敷光阻,去除P 阱区的光阻,注入砷(As) 离子,形成NMOS 的源漏极。
晶圆工艺流程

晶圆工艺流程晶圆工艺流程是指将硅片作为材料,通过一系列的工序制造出用于集成电路的晶圆的过程。
以下是一般的晶圆工艺流程。
首先是硅片的准备。
硅片是晶圆的基本材料,通常是从单晶硅棒中拉制而成。
在准备过程中,硅片需要经过清洗、去除杂质、抛光等操作,确保表面光滑、洁净。
接下来是光刻工艺。
光刻工艺是利用光刻胶和光罩制造芯片图案的过程。
首先,将光刻胶涂覆在硅片表面,然后将光罩对准硅片,并通过紫外线照射。
照射后,将硅片进行显影处理,去除未固化的光刻胶,得到芯片的图案。
然后是离子注入。
离子注入是将掺杂元素注入硅片中,改变硅片的电导性和性能。
首先,在光刻完毕后,通过快速加热将光刻胶去除,然后将硅片放置在离子注入机中,注入所需掺杂元素。
注入后,通过退火处理来激活注入的离子,使其与硅片结合。
接下来是薄膜沉积。
薄膜沉积是将各种材料沉积在硅片上,以形成晶圆上的各种层次和结构。
常见的薄膜沉积方法有化学气相沉积(CVD)和物理气相沉积(PVD)等。
通过这些方法,在硅片上沉积氧化物、金属、聚合物等材料,形成电子器件所需的结构。
然后是刻蚀工艺。
刻蚀工艺是利用化学溶液或等离子体等方法,将不需要的材料从硅片上去除,形成所需的电子器件结构。
通过刻蚀,可以制造出晶圆上细小且复杂的结构。
最后是封装工艺。
封装工艺是将制造好的晶圆进行封装,以保护器件并为其提供连接接口。
在封装过程中,将晶圆切割成单个芯片,并进行焊接、封胶、外壳封装等操作,形成完整的集成电路芯片。
以上是一般的晶圆工艺流程。
当然,实际的制造过程还会包括更多的细节工艺和控制环节,以确保芯片的质量和性能。
随着工艺技术的不断进步,晶圆工艺流程也在不断演进,以满足不断增长的电子器件需求。
晶圆制造工艺流程
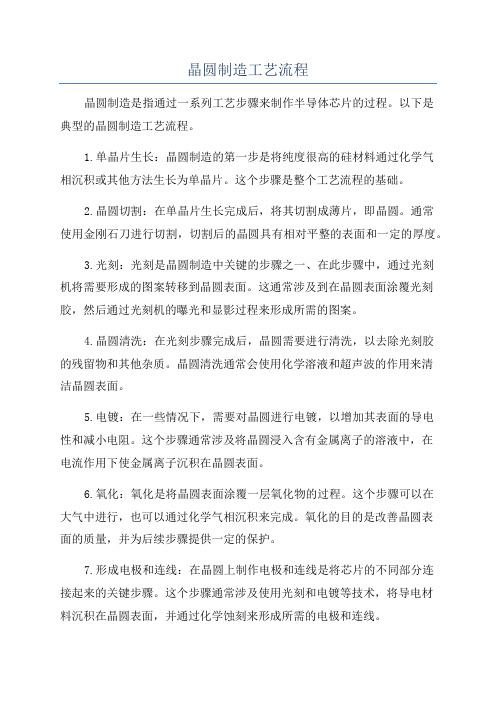
晶圆制造工艺流程晶圆制造是指通过一系列工艺步骤来制作半导体芯片的过程。
以下是典型的晶圆制造工艺流程。
1.单晶片生长:晶圆制造的第一步是将纯度很高的硅材料通过化学气相沉积或其他方法生长为单晶片。
这个步骤是整个工艺流程的基础。
2.晶圆切割:在单晶片生长完成后,将其切割成薄片,即晶圆。
通常使用金刚石刀进行切割,切割后的晶圆具有相对平整的表面和一定的厚度。
3.光刻:光刻是晶圆制造中关键的步骤之一、在此步骤中,通过光刻机将需要形成的图案转移到晶圆表面。
这通常涉及到在晶圆表面涂覆光刻胶,然后通过光刻机的曝光和显影过程来形成所需的图案。
4.晶圆清洗:在光刻步骤完成后,晶圆需要进行清洗,以去除光刻胶的残留物和其他杂质。
晶圆清洗通常会使用化学溶液和超声波的作用来清洁晶圆表面。
5.电镀:在一些情况下,需要对晶圆进行电镀,以增加其表面的导电性和减小电阻。
这个步骤通常涉及将晶圆浸入含有金属离子的溶液中,在电流作用下使金属离子沉积在晶圆表面。
6.氧化:氧化是将晶圆表面涂覆一层氧化物的过程。
这个步骤可以在大气中进行,也可以通过化学气相沉积来完成。
氧化的目的是改善晶圆表面的质量,并为后续步骤提供一定的保护。
7.形成电极和连线:在晶圆上制作电极和连线是将芯片的不同部分连接起来的关键步骤。
这个步骤通常涉及使用光刻和电镀等技术,将导电材料沉积在晶圆表面,并通过化学蚀刻来形成所需的电极和连线。
8.打磨和抛光:在制造晶圆过程中,由于一些原因,晶圆表面可能会有一些不平整和缺陷。
为了修复这些问题,晶圆需要经过打磨和抛光,使其表面更加平整和光滑。
9.测试和封装:在晶圆制造完毕后,需要对芯片进行测试,以确保其正常工作。
测试通常会使用特定的测试设备和测试程序来进行,包括电性能测试、可靠性测试等。
然后,芯片会进行封装,即将其放入塑料或金属封装中,以保护芯片并为其提供适当的引脚。
以上是晶圆制造的典型工艺流程。
当然,实际的晶圆制造可能会因不同应用领域和制造工艺的差异而略有不同。
晶圆的制作流程

晶圆的制作流程
晶圆的制作流程包括以下步骤:
1. 晶圆处理工序:主要工作是在晶圆上制作电路及电子元件(如晶体管、电容、逻辑开关等)。
处理程序通常与产品种类和所使用的技术有关,但一般基本步骤是先将晶圆适当清洗,再在其表面进行氧化及化学气相沉积,然后进行涂膜、曝光、显影、蚀刻、离子植入、金属溅镀等反复步骤,最终在晶圆上完成数层电路及元件加工与制作。
2. 晶圆针测工序:经过上道工序后,晶圆上就形成了一个个的小格,即晶粒。
一般情况下,为便于测试,提高效率,同一片晶圆上制作同一品种、规格的产品;但也可根据需要制作几种不同品种、规格的产品。
在用针测(Probe)仪对每个晶粒检测其电气特性,并将不合格的晶粒标上记号后,将晶圆切开,分割成一颗颗单独的晶粒,再按其电气特性分类,装入不同的托盘中,不合格的晶粒则舍弃。
其目的是用以保护晶粒避免受到机械刮伤或高温破坏。
请注意,这只是大致流程,具体的生产流程可能会根据不同工厂的设备、技术和生产需求有所不同。
(完整版)晶圆的生产工艺流程汇总

晶圆的生产工艺流程:从大的方面来讲,晶圆生产包括晶棒制造和晶片制造两大步骤,它又可细分为以下几道主要工序(其中晶棒制造只包括下面的第一道工序,其余的全部属晶片制造,所以有时又统称它们为晶柱切片后处理工序):晶棒成长 -- 晶棒裁切与检测 -- 外径研磨 -- 切片 -- 圆边-- 表层研磨 -- 蚀刻 -- 去疵 -- 抛光 -- 清洗 -- 检验 -- 包装 1、晶棒成长工序:它又可细分为:1)、融化(Melt Down):将块状的高纯度复晶硅置于石英坩锅内,加热到其熔点1420°C以上,使其完全融化。
2)、颈部成长(Neck Growth):待硅融浆的温度稳定之后,将〈1.0.0〉方向的晶种慢慢插入其中,接着将晶种慢慢往上提升,使其直径缩小到一定尺寸(一般约6mm左右),维持此直径并拉长100-200mm,以消除晶种内的晶粒排列取向差异。
3)、晶冠成长(Crown Growth):颈部成长完成后,慢慢降低提升速度和温度,使颈部直径逐渐加大到所需尺寸(如5、6、8、12吋等)。
4)、晶体成长(Body Growth):不断调整提升速度和融炼温度,维持固定的晶棒直径,只到晶棒长度达到预定值。
5)、尾部成长(Tail Growth):当晶棒长度达到预定值后再逐渐加快提升速度并提高融炼温度,使晶棒直径逐渐变小,以避免因热应力造成排差和滑移等现象产生,最终使晶棒与液面完全分离。
到此即得到一根完整的晶棒。
2、晶棒裁切与检测(Cutting & Inspection):将长成的晶棒去掉直径偏小的头、尾部分,并对尺寸进行检测,以决定下步加工的工艺参数。
3、外径研磨(Surface Grinding & Shaping):由于在晶棒成长过程中,其外径尺寸和圆度均有一定偏差,其外园柱面也凹凸不平,所以必须对外径进行修整、研磨,使其尺寸、形状误差均小于允许偏差。
4、切片(Wire Saw Slicing):由于硅的硬度非常大,所以在本工序里,采用环状、其内径边缘镶嵌有钻石颗粒的薄片锯片将晶棒切割成一片片薄片。
(完整版)晶圆的生产工艺流程汇总

颈部成长
1
待硅融浆的温度安定之后,将〈1.0.0〉方向的晶 种慢慢插入其中。
2
接着将晶种慢慢往上提升,使其直径缩小到一定 尺寸(大凡约6mm左右)。
3
维持此直径并拉长100-200mm,以消除晶种内 的晶粒排列取向差异。
晶冠成长
颈部成长完成后,慢慢降低提升速度 和温度。
使颈部直径逐渐加大到所需尺寸(如5 、6、8、12吋等)。
07
CATALOGUE
蚀刻
蚀刻
要点一
蚀刻的目的
蚀刻是晶圆制造过程中一个重要的步 骤,其目的是去掉晶片表面因加工应 力而产生的一层损伤层。这一层通常 很薄,但如果不将其去除,将会影响 芯片的电气性能和可靠性。因此,蚀 刻是确保晶片表面质量的关键步骤之 一。
要点二
浸泡
将晶片放入化学蚀刻液中,让蚀刻液 与晶片表面发生化学反应。这个过程 通常需要一定时间,以确保蚀刻液能 够充分与晶片表面接触。
抛光的影响因素:抛光处理的效果受 到多个因素的影响,包括抛光设备的 类型和精度、抛光材料的种类和粒度 、化学试剂的种类和浓度、晶片的材 质和厚度等。在抛光处理过程中,要 综合考虑这些因素,以获得最佳的处 理效果。同时,抛光处理还需要注意 保护晶片的边缘部分,避免在处理过 程中对边缘造成损伤或破坏。
06
(完整版)晶圆的 生产工艺流程汇 总
汇报人:XXX 2023-12-01
目录
• 晶棒成长工序 • 晶棒裁切与检测 • 外径研磨 • 切片 • 圆边 • 研磨 • 蚀刻 • 去疵 • 抛光 • 清洗 • 检验 • 包装
01
CATALOGUE
晶棒成长工序
融化
• 将块状的高纯度复晶硅置于石英坩锅内:加热到其 熔点1420°C以上,使其完全融化。待硅融浆的温度 安定之后,将〈1.0.0〉方向的晶种慢慢插入其中。 接着将晶种慢慢往上提升,使其直径缩小到一定尺 寸(大凡约6mm左右)。
晶圆加工流程
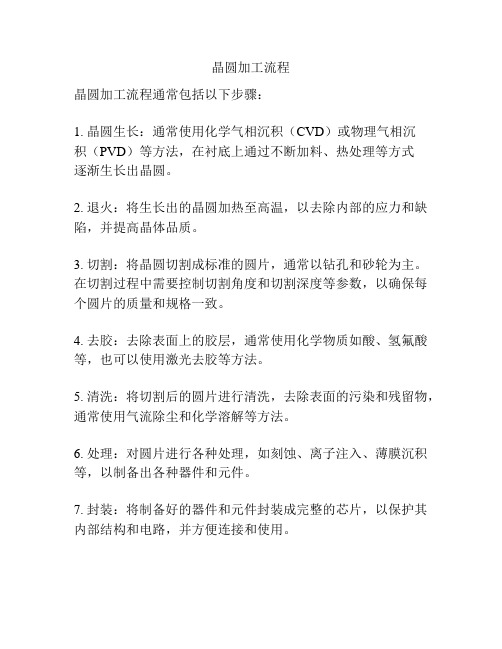
晶圆加工流程
晶圆加工流程通常包括以下步骤:
1. 晶圆生长:通常使用化学气相沉积(CVD)或物理气相沉
积(PVD)等方法,在衬底上通过不断加料、热处理等方式
逐渐生长出晶圆。
2. 退火:将生长出的晶圆加热至高温,以去除内部的应力和缺陷,并提高晶体品质。
3. 切割:将晶圆切割成标准的圆片,通常以钻孔和砂轮为主。
在切割过程中需要控制切割角度和切割深度等参数,以确保每个圆片的质量和规格一致。
4. 去胶:去除表面上的胶层,通常使用化学物质如酸、氢氟酸等,也可以使用激光去胶等方法。
5. 清洗:将切割后的圆片进行清洗,去除表面的污染和残留物,通常使用气流除尘和化学溶解等方法。
6. 处理:对圆片进行各种处理,如刻蚀、离子注入、薄膜沉积等,以制备出各种器件和元件。
7. 封装:将制备好的器件和元件封装成完整的芯片,以保护其内部结构和电路,并方便连接和使用。
以上是典型的晶圆加工流程,不同的应用和工艺还有许多细节和差异。
晶圆制造工艺流程

晶圆制造工艺流程1、表面清洗2、初次氧化3、 CVD(Chemical Vapor deposition) 法沉积一层 Si3N4 (Hot CVD 或 LPCVD) 。
(1)常压 CVD (Normal Pressure CVD)(2)低压 CVD (Low Pressure CVD)(3)热 CVD (Hot CVD)/(thermal CVD)(4)电浆增强 CVD (Plasma Enhanced CVD)(5)MOCVD (Metal Organic?? CVD) & 分子磊晶成长 (Molecular Beam Epitaxy) (6)外延生长法 (LPE)4、涂敷光刻胶(1)光刻胶的涂敷(2)预烘 (pre bake)(3)曝光(4)显影(5)后烘 (post bake)(6)腐蚀 (etching)(7)光刻胶的去除5、此处用干法氧化法将氮化硅去除6 、离子布植将硼离子 (B+3) 透过 SiO2 膜注入衬底,形成 P 型阱7、去除光刻胶,放高温炉中进行退火处理8、用热磷酸去除氮化硅层,掺杂磷 (P+5) 离子,形成 N 型阱9、退火处理,然后用 HF 去除 SiO2 层10、干法氧化法生成一层 SiO2 层,然后 LPCVD 沉积一层氮化硅11、利用光刻技术和离子刻蚀技术,保留下栅隔离层上面的氮化硅层12、湿法氧化,生长未有氮化硅保护的 SiO2 层,形成 PN 之间的隔离区13、热磷酸去除氮化硅,然后用 HF 溶液去除栅隔离层位置的 SiO2 ,并重新生成品质更好的 SiO2 薄膜 , 作为栅极氧化层。
14、LPCVD 沉积多晶硅层,然后涂敷光阻进行光刻,以及等离子蚀刻技术,栅极结构,并氧化生成 SiO2 保护层。
15、表面涂敷光阻,去除 P 阱区的光阻,注入砷 (As) 离子,形成 NMOS 的源漏极。
用同样的方法,在 N 阱区,注入 B 离子形成 PMOS 的源漏极。
晶圆的生产工艺流程汇总

晶圆的生产工艺流程:从大的方面来讲,晶圆生产包括晶棒制造和晶片制造两大步骤,它又可细分为以下几道主要工序(其中晶棒制造只包括下面的第一道工序,其余的全部属晶片制造,所以有时又统称它们为晶柱切片后处理工序):晶棒成长 -- 晶棒裁切与检测 -- 外径研磨 -- 切片 -- 圆边-- 表层研磨 -- 蚀刻 -- 去疵 -- 抛光 -- 清洗 -- 检验 -- 包装 1、晶棒成长工序:它又可细分为:1)、融化(Melt Down):将块状的高纯度复晶硅置于石英坩锅内,加热到其熔点1420°C以上,使其完全融化。
2)、颈部成长(Neck Growth):待硅融浆的温度稳定之后,将〈1.0.0〉方向的晶种慢慢插入其中,接着将晶种慢慢往上提升,使其直径缩小到一定尺寸(一般约6mm左右),维持此直径并拉长100-200mm,以消除晶种内的晶粒排列取向差异。
3)、晶冠成长(Crown Growth):颈部成长完成后,慢慢降低提升速度和温度,使颈部直径逐渐加大到所需尺寸(如5、6、8、12吋等)。
4)、晶体成长(Body Growth):不断调整提升速度和融炼温度,维持固定的晶棒直径,只到晶棒长度达到预定值。
5)、尾部成长(Tail Growth):当晶棒长度达到预定值后再逐渐加快提升速度并提高融炼温度,使晶棒直径逐渐变小,以避免因热应力造成排差和滑移等现象产生,最终使晶棒与液面完全分离。
到此即得到一根完整的晶棒。
2、晶棒裁切与检测(Cutting & Inspection):将长成的晶棒去掉直径偏小的头、尾部分,并对尺寸进行检测,以决定下步加工的工艺参数。
3、外径研磨(Surface Grinding & Shaping):由于在晶棒成长过程中,其外径尺寸和圆度均有一定偏差,其外园柱面也凹凸不平,所以必须对外径进行修整、研磨,使其尺寸、形状误差均小于允许偏差。
4、切片(Wire Saw Slicing):由于硅的硬度非常大,所以在本工序里,采用环状、其内径边缘镶嵌有钻石颗粒的薄片锯片将晶棒切割成一片片薄片。
晶圆生产主要工艺流程
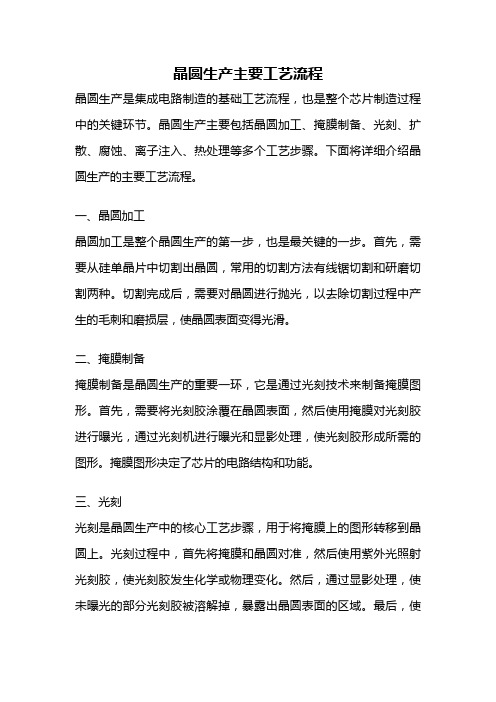
晶圆生产主要工艺流程晶圆生产是集成电路制造的基础工艺流程,也是整个芯片制造过程中的关键环节。
晶圆生产主要包括晶圆加工、掩膜制备、光刻、扩散、腐蚀、离子注入、热处理等多个工艺步骤。
下面将详细介绍晶圆生产的主要工艺流程。
一、晶圆加工晶圆加工是整个晶圆生产的第一步,也是最关键的一步。
首先,需要从硅单晶片中切割出晶圆,常用的切割方法有线锯切割和研磨切割两种。
切割完成后,需要对晶圆进行抛光,以去除切割过程中产生的毛刺和磨损层,使晶圆表面变得光滑。
二、掩膜制备掩膜制备是晶圆生产的重要一环,它是通过光刻技术来制备掩膜图形。
首先,需要将光刻胶涂覆在晶圆表面,然后使用掩膜对光刻胶进行曝光,通过光刻机进行曝光和显影处理,使光刻胶形成所需的图形。
掩膜图形决定了芯片的电路结构和功能。
三、光刻光刻是晶圆生产中的核心工艺步骤,用于将掩膜上的图形转移到晶圆上。
光刻过程中,首先将掩膜和晶圆对准,然后使用紫外光照射光刻胶,使光刻胶发生化学或物理变化。
然后,通过显影处理,使未曝光的部分光刻胶被溶解掉,暴露出晶圆表面的区域。
最后,使用蚀刻或其他加工方法,将暴露出来的晶圆表面进行加工。
四、扩散扩散是晶圆生产中的一种加工方法,用于控制晶圆表面杂质的浓度和分布。
扩散过程中,将晶圆置于高温炉中,与气体或液体中的杂质进行反应,使杂质从液体或气体中扩散到晶圆表面。
扩散后的晶圆表面形成了所需的掺杂区域,用于形成芯片中的电子器件。
五、腐蚀腐蚀是晶圆生产中的一种加工方法,用于去除晶圆表面的氧化层或其他不需要的杂质。
腐蚀过程中,将晶圆放置在腐蚀液中,使腐蚀液与晶圆表面发生化学反应,去除表面的氧化层或杂质。
腐蚀后的晶圆表面更加平整和清洁,有利于后续工艺的进行。
六、离子注入离子注入是晶圆生产中的一种加工方法,用于控制晶圆中杂质的浓度和分布。
离子注入过程中,将晶圆放置在离子注入机中,加速并定向注入离子束到晶圆表面。
注入的离子将与晶体中的原子进行替换或形成杂质,从而改变晶圆的电学性质。
半导体晶圆的生产工艺流程介绍

•从大的方面来讲,晶圆生产包括晶棒制造和晶片制造两大步骤,它又可细分为以下几道主要工序(其中晶棒制造只包括下面的第一道工序,其余的全部属晶片制造,所以有时又统称它们为晶柱切片后处理工序):晶棒成长--> 晶棒裁切与检测--> 外径研磨--> 切片--> 圆边--> 表层研磨--> 蚀刻--> 去疵--> 抛光--> 清洗--> 检验--> 包装1 晶棒成长工序:它又可细分为:1)融化(Melt Down)将块状的高纯度复晶硅置于石英坩锅内,加热到其熔点1420°C以上,使其完全融化。
2)颈部成长(Neck Growth)待硅融浆的温度稳定之后,将〈1.0.0〉方向的晶种慢慢插入其中,接着将晶种慢慢往上提升,使其直径缩小到一定尺寸(一般约6mm左右),维持此直径并拉长100-200mm,以消除晶种内的晶粒排列取向差异。
3)晶冠成长(Crown Growth)颈部成长完成后,慢慢降低提升速度和温度,使颈部直径逐渐加大到所需尺寸(如5、6、8、12吋等)。
4)晶体成长(Body Growth)不断调整提升速度和融炼温度,维持固定的晶棒直径,只到晶棒长度达到预定值。
5)尾部成长(Tail Growth)当晶棒长度达到预定值后再逐渐加快提升速度并提高融炼温度,使晶棒直径逐渐变小,以避免因热应力造成排差和滑移等现象产生,最终使晶棒与液面完全分离。
到此即得到一根完整的晶棒。
2 晶棒裁切与检测(Cutting & Inspection)将长成的晶棒去掉直径偏小的头、尾部分,并对尺寸进行检测,以决定下步加工的工艺参数。
3 外径研磨(Su rf ace Grinding & Shaping)由于在晶棒成长过程中,其外径尺寸和圆度均有一定偏差,其外园柱面也凹凸不平,所以必须对外径进行修整、研磨,使其尺寸、形状误差均小于允许偏差。
晶圆制造流程

晶圆制造流程
晶圆
晶圆是指硅半导体集成电路制作所用的硅晶片,由于其形状为圆形,故称为晶圆;在硅晶片上可加工制作成各种电路元件结构,而成为有特定电性功能之IC产品。
晶圆的原始材料是硅,而地壳表面有用之不竭的二氧化硅。
二氧化硅矿石经由电弧炉提炼,盐酸氯化,并经蒸馏后,制成了高纯度的多晶硅,其纯度高达99.999999999%。
晶圆制造流程
1、脱氧提纯
沙子/石英经过脱氧提纯以后的得到含硅量25%的Si02二氧化硅。
氧化硅经由电弧炉提炼,盐酸氯化,并蒸馏后,得到纯度高达99%以上的晶体硅。
晶体硅的纯度要求非常高,这也是造出晶圆昂贵的原因。
大家知道钻石是个什幺玩意儿吗?钻石就是碳元素经过脱氧以及其他因素形成的元素排列独特且纯度高达99.64%以上的晶体。
大家想想,晶圆比人造钻石便宜多了,感觉还是很划算的。
晶圆的生产工艺流程

晶圆的生产工艺流程:从大的方面来讲,晶圆生产包括晶棒制造和晶片制造两大步骤,它又可细分为以下几道主要工序(其中晶棒制造只包括下面的第一道工序,其余的全部属晶片制造,所以有时又统称它们为晶柱切片后处理工序):晶棒成长 -- 晶棒裁切与检测 -- 外径研磨 -- 切片 -- 圆边-- 表层研磨 -- 蚀刻 -- 去疵 -- 抛光 -- 清洗 -- 检验 -- 包装 1、晶棒成长工序:它又可细分为:1)、融化(Melt Down):将块状的高纯度复晶硅置于石英坩锅内,加热到其熔点1420°C以上,使其完全融化。
2)、颈部成长(Neck Growth):待硅融浆的温度稳定之后,将〈1.0.0〉方向的晶种慢慢插入其中,接着将晶种慢慢往上提升,使其直径缩小到一定尺寸(一般约6mm左右),维持此直径并拉长100-200mm,以消除晶种内的晶粒排列取向差异。
3)、晶冠成长(Crown Growth):颈部成长完成后,慢慢降低提升速度和温度,使颈部直径逐渐加大到所需尺寸(如5、6、8、12吋等)。
4)、晶体成长(Body Growth):不断调整提升速度和融炼温度,维持固定的晶棒直径,只到晶棒长度达到预定值。
5)、尾部成长(Tail Growth):当晶棒长度达到预定值后再逐渐加快提升速度并提高融炼温度,使晶棒直径逐渐变小,以避免因热应力造成排差和滑移等现象产生,最终使晶棒与液面完全分离。
到此即得到一根完整的晶棒。
2、晶棒裁切与检测(Cutting & Inspection):将长成的晶棒去掉直径偏小的头、尾部分,并对尺寸进行检测,以决定下步加工的工艺参数。
3、外径研磨(Surface Grinding & Shaping):由于在晶棒成长过程中,其外径尺寸和圆度均有一定偏差,其外园柱面也凹凸不平,所以必须对外径进行修整、研磨,使其尺寸、形状误差均小于允许偏差。
4、切片(Wire Saw Slicing):由于硅的硬度非常大,所以在本工序里,采用环状、其内径边缘镶嵌有钻石颗粒的薄片锯片将晶棒切割成一片片薄片。
8寸半导体晶圆制造工艺流程

8寸半导体晶圆制造工艺流程
8寸半导体晶圆制造工艺流程主要包括以下几个步骤:
1. 融化(Melt Down):将块状的高纯度复晶硅置于石英坩锅内,加热到
其熔点1420°C以上,使其完全融化。
2. 颈部成长(Neck Growth):待硅融浆的温度稳定之后,将〈〉方向的
晶种慢慢插入其中,接着将晶种慢慢往上提升,使其直径缩小到一定尺寸(一般约6mm左右),维持此直径并拉长mm,以消除晶种内的晶粒排列取向差异。
3. 晶冠成长(Crown Growth):颈部成长完成后,慢慢降低提升速度和温度,使颈部直径逐渐加大到所需尺寸(如5、6、8、12吋等)。
4. 晶圆处理工序:主要工作是在晶圆上制作电路及电子元件(如晶体管、电容、逻辑开关等)。
一般基本步骤是先将晶圆适当清洗,再在其表面进行氧化及化学气相沉积,然后进行涂膜、曝光、显影、蚀刻、离子植入、金属溅镀等反复步骤,最终在晶圆上完成数层电路及元件加工与制作。
5. 晶圆针测工序:经过上道工序后,晶圆上就形成了一个个的小格,即晶粒。
一般情况下,为便于测试,提高效率,同一片晶圆上制作同一品种、规格的产品;但也可根据需要制作几种不同品种、规格的产品。
在用针测(Probe)仪对每个晶粒检测其电气特性,并将不合格的晶粒标上记号后,将晶圆切开,
分割成一颗颗单独的晶粒,再按其电气特性分类,装入不同的托盘中,不合格的晶粒则舍弃。
其目的是用以保护晶粒避免受到机械刮伤或高温破坏。
以上信息仅供参考,如需获取更多详细信息,建议咨询专业半导体技术人员。
晶圆制作工艺流程

晶圆制作工艺流程晶圆是制造半导体芯片的基本材料,半导体集成电路最主要的原料是硅,因此对应的就是硅晶圆。
硅在自然界中以硅酸盐或二氧化硅的形式广泛存在于岩石、砂砾中,硅晶圆的制造可以归纳为三个基本步骤:硅提炼及提纯、单晶硅生长、晶圆成型。
首先是硅提纯,将沙石原料放入一个温度约为2000 ℃,并且有碳源存在的电弧熔炉中,在高温下,碳和沙石中的二氧化硅进行化学反应(碳与氧结合,剩下硅),得到纯度约为98%的纯硅,又称作冶金级硅,这对微电子器件来说不够纯,因为半导体材料的电学特性对杂质的浓度非常敏感,因此对冶金级硅进行进一步提纯:将粉碎的冶金级硅与气态的氯化氢进行氯化反应,生成液态的硅烷,然后通过蒸馏和化学还原工艺,得到了高纯度的多晶硅,其纯度高达99.999999999%,成为电子级硅。
接下来是单晶硅生长,最常用的方法叫直拉法。
如下图所示,高纯度的多晶硅放在石英坩埚中,并用外面围绕着的石墨加热器不断加热,温度维持在大约1400 ℃,炉中的空气通常是惰性气体,使多晶硅熔化,同时又不会产生不需要的化学反应。
为了形成单晶硅,还需要控制晶体的方向:坩埚带着多晶硅熔化物在旋转,把一颗籽晶浸入其中,并且由拉制棒带着籽晶作反方向旋转,同时慢慢地、垂直地由硅熔化物中向上拉出。
熔化的多晶硅会粘在籽晶的底端,按籽晶晶格排列的方向不断地生长上去。
因此所生长的晶体的方向性是由籽晶所决定的,在其被拉出和冷却后就生长成了与籽晶内部晶格方向相同的单晶硅棒。
用直拉法生长后,单晶棒将按适当的尺寸进行切割,然后进行研磨,将凹凸的切痕磨掉,再用化学机械抛光工艺使其至少一面光滑如镜,晶圆片制造就完成了。
单晶硅棒的直径是由籽晶拉出的速度和旋转速度决定的,一般来说,上拉速率越慢,生长的单晶硅棒直径越大。
而切出的晶圆片的厚度与直径有关,虽然半导体器件的制备只在晶圆的顶部几微米的范围内完成,但是晶圆的厚度一般要达到1 mm,才能保证足够的机械应力支撑,因此晶圆的厚度会随直径的增长而增长。
晶圆生产线流程

晶圆生产线流程
晶圆生产线是一种集成电路制造的过程,需要经过多个步骤才能生产出一个完整的晶圆。
晶圆生产线流程包括以下步骤:
1. 晶圆的原材料采购:晶圆的原材料是硅片,它是从石英砂中提取出来的。
硅片的质量对于后续的制造过程非常重要,因此采购方需要选择质量优良的供应商。
2. 晶圆的制备:首先,工人需要将硅片进行清洗和抛光,以保证表面的平整度。
然后,他们会在硅片上加入一层抗反射膜,以减少在制造过程中的反射和折射。
3. 光刻:光刻是制造芯片的关键步骤之一。
它使用光刻机将芯片上的电路图案“印”在光刻胶上。
然后,光刻胶会被化学处理,并使用光刻机将电路图案刻入硅片表面。
4. 蚀刻:蚀刻是将芯片上的电路图案刻入硅片的关键步骤之一。
它使用化学反应将不需要的硅片蚀掉,留下需要的电路图案。
5. 氧化:氧化是将芯片表面涂上一层氧化物的步骤。
这层氧化物可以保护电路图案,同时也可以提高电路的可靠性和稳定性。
6. 金属化:金属化是将芯片上的电路图案涂上一层金属的步骤。
这层金属可以传导电子,同时也可以保护电路图案。
7. 终验和封装:在晶圆生产线的最后一步,芯片会被送到测试和封装区。
在这里,芯片会被测试,以确保它们符合规格。
然后,芯片会被封装在塑料或金属外壳中,以使它们适合在电子设备中使用。
这些步骤组成了晶圆生产线的流程。
在整个过程中,需要严格控
制各种参数,以确保每个晶圆的质量和可靠性。