高炉工艺流程
高炉工艺流程

高炉工艺流程高炉是冶金工业中最重要的设备之一,用于生产炼铁。
高炉工艺流程的主要目标是将铁矿石转化为可用于生产钢铁的铁液。
下面是一个典型的高炉工艺流程:1. 高炉的装料:首先,将适量的炼铁生料(铁矿石,焦炭和石灰石)按照一定比例混合,并通过送料系统连续地装入高炉的上部,即炉缸。
2. 预热和干燥:装料进入高炉后,通过炉顶和鼓风机将燃烧的热风引入高炉。
热风在高炉内升温,并将装料预热和干燥,以使其更容易熔化。
3. 还原反应:高炉内的燃烧和还原反应同时进行。
燃烧产生的热能和还原剂(主要是一氧化碳)使铁矿石发生还原反应,将氧气从铁矿石中脱去,生成铁和一氧化碳。
4. 熔化和铸渣:随着高炉内温度的升高,铁矿石开始融化,并与燃烧产生的一氧化碳反应生成液态的铁液。
在融化的过程中,石灰石被加入以吸收并结合炉渣中的杂质,形成铸渣。
5. 铸渣处理:铸渣是高炉中产生的主要副产品之一。
在高炉底部,温度较低的区域,通过铁口将铁液和铸渣分离。
铁液通过铁口流出,而铸渣则被收集并送入渣铁处理设备进一步处理。
6. 倾吐:当高炉达到预定的操作周期后,铁液将被倾吐到铁水箱中,并通过连铸技术进一步加工成钢坯。
7. 渣铁处理:铸渣中包含着一定量的铁和有价值的金属元素,因此需要对铸渣进行处理。
渣铁处理设备通常包括磁选机、重介质分选机和焦炉等,以回收其中的金属。
8. 炉后处理:通过高炉后处理操作,可以对炼铁过程中产生的废气和废液进行处理。
例如,废气可以通过脱硫和除尘设备进行净化,废液可以通过沉淀和过滤等方法进行处理。
这是一个典型的高炉工艺流程,每个钢铁生产厂商都可能有些许差异。
此外,高炉的操作也需要高度的技术和经验,以确保生产的效率和质量。
高炉的工艺流程是复杂而多变的,需要不断的优化和改进,以降低能耗、提高产量和质量。
高炉炼铁工艺流程及主要设备简介
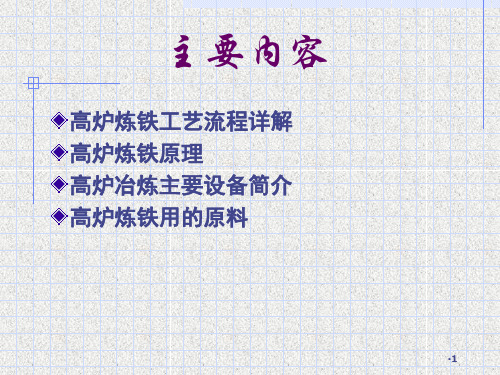
三、高炉冶炼主要设备简介
振动筛(矿): 2BTS1330型号: 2BTS1330 电机型号:Y132M-6 处理量:150T/h 安装倾角:18° 筛孔尺寸:12-6mm 振幅:6.5±1mm 功率:2×4kw 振动筛(焦炭) 型号:TZS1330 电机型号:Y132M2-6 处理量:120T/h 安装倾角:18° 筛孔尺寸:20mm 振幅:7±1mm 功率:2×4kw
缺少的重要组成部分。现代热风炉是一种蓄热式换热 器。目前风温水平为1000℃~1200 ℃ ,高的为1250 ℃~1350 ℃ ,最高可达1450 ℃~1550 ℃。我厂现在 使用的热风风温一般在1180 ℃ 。 提高风温可以通过提高煤气热值、优化热风炉及送风 管道结构、预热煤气和助燃空气、改善热风炉操作等 技术措施来实现。理论研究和生产实践表明,采用优 化的热风炉结构、提高热风炉热效率、延长热风炉寿 命是提高风温的有效途径。现在每座高炉配备一套助 燃风机系统,
冷却塔
鼓风机
热风炉
助燃风机
煤气外网管道
重力 除尘
布袋 除尘
调压阀组 TRT发电
渣池 水渣场
渣泵
•3
二、高炉炼铁原理
高炉是一种竖炉型逆流式反应器。高炉冶炼用的铁矿石 和燃料、熔剂等由炉顶的装料设备装入炉内的,并向 下运动;从下部鼓入的空气燃烧燃料,产生大量的高 温还原性气体向上运动;炉料经过加热、还原、熔化、 滴落、造渣、渗碳、脱硫等一系列物理化学过程,最 终生成液态炉渣和生铁。
•10
三、高炉冶炼主要设备简介
受料斗主 要包括: 受料斗篦 子、受料 斗衬板; 受料斗的 最大容积:
16m³
•11
三、高炉冶炼主要设备简介
挡料阀
上密阀
高炉炼铁工艺流程简介
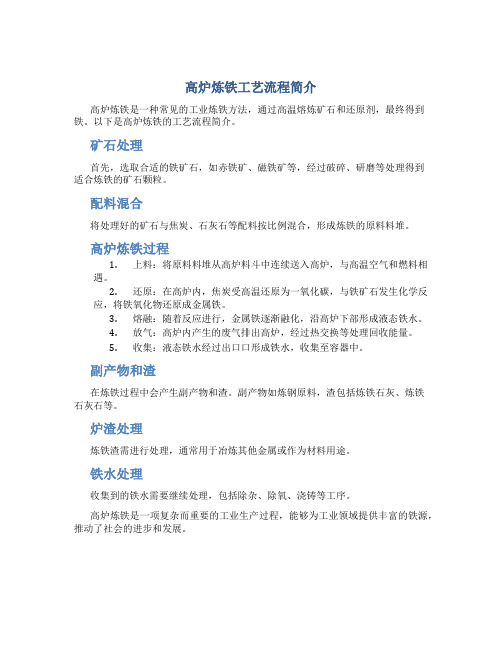
高炉炼铁工艺流程简介
高炉炼铁是一种常见的工业炼铁方法,通过高温熔炼矿石和还原剂,最终得到铁。
以下是高炉炼铁的工艺流程简介。
矿石处理
首先,选取合适的铁矿石,如赤铁矿、磁铁矿等,经过破碎、研磨等处理得到
适合炼铁的矿石颗粒。
配料混合
将处理好的矿石与焦炭、石灰石等配料按比例混合,形成炼铁的原料料堆。
高炉炼铁过程
1.上料:将原料料堆从高炉料斗中连续送入高炉,与高温空气和燃料相
遇。
2.还原:在高炉内,焦炭受高温还原为一氧化碳,与铁矿石发生化学反
应,将铁氧化物还原成金属铁。
3.熔融:随着反应进行,金属铁逐渐融化,沿高炉下部形成液态铁水。
4.放气:高炉内产生的废气排出高炉,经过热交换等处理回收能量。
5.收集:液态铁水经过出口口形成铁水,收集至容器中。
副产物和渣
在炼铁过程中会产生副产物和渣。
副产物如炼钢原料,渣包括炼铁石灰、炼铁
石灰石等。
炉渣处理
炼铁渣需进行处理,通常用于冶炼其他金属或作为材料用途。
铁水处理
收集到的铁水需要继续处理,包括除杂、除氧、浇铸等工序。
高炉炼铁是一项复杂而重要的工业生产过程,能够为工业领域提供丰富的铁源,推动了社会的进步和发展。
高炉炼铁的主要工艺流程

高炉炼铁的主要工艺流程
《高炉炼铁的主要工艺流程》
高炉是钢铁企业中用于炼铁的主要设备,其工艺流程是将铁矿石和焦炭加入高炉内,经过一系列的化学和物理反应,最终得到熔融的生铁。
下面将介绍高炉炼铁的主要工艺流程。
1. 搅拌坩埚法:将原铁矿石和焦炭按一定的比例混合,放入高炉的上部,即炉料层。
在高炉内,炉料层受到高温和高压的影响,发生一系列的物理和化学反应。
2. 燃烧:通过给炉料层加入空气或者氧气,点燃炉料层的顶部,使其燃烧。
燃烧产生的热量使炉料层内的焦炭燃烧,并提供高温条件,促进各种反应的进行。
3. 还原反应:当焦炭燃烧释放出一定量的一氧化碳时,与高炉内的铁矿石发生还原反应,使氧化铁还原为生铁。
4. 精炼:在高温下,生铁中的杂质和一些有害元素(如硫、磷等)会被氧化成气体,并通过炉顶排出。
这一过程称为精炼,是炉料中杂质清除的重要环节。
5. 收得生铁:经过一定时间的冶炼,高炉内的炉料最终产生了熔融的生铁。
生铁通过炉口排除,并进入铁水槽中,成为炼铁的产物。
通过上述简单介绍,可以看出高炉炼铁的主要工艺流程是一个
复杂的过程,包括搅拌坩埚法、燃烧、还原反应、精炼和收得生铁等环节。
这一流程不仅需要科学合理的原料比例和控制方法,还需要高炉操作者的丰富经验和技巧。
只有合理的工艺流程和专业的操作技术,才能保证高炉炼铁的顺利进行和生产出优质的生铁产品。
高炉生产工艺流程

接下来是炉气处理阶段,高炉冶炼过程中产生的炉气中含有一氧化碳、二氧化碳、氮气等物质。这些气体需要被净化和处理,以达到排放标准。常用的方法包括干法除尘、湿法除尘、除硫和除氮等。
最后是余热回收阶段,高炉生产过程中产生了大量的余热,包括炉渣的冷却余热和炉气的余热。这些余热可以通过余热回收系统进行收集和利用,从而提高能源利用效率。
接下来是炉内反应阶段,当炉缸中的炉料逐渐下降时,炉缸内的温度会迅速上升。炉料在高温下被还原成铁,同时产生大量的炉渣。在这个过程中,还会产生大量的一氧化碳和水蒸气。
然后是铁水出炉阶段,当足够的铁被还原出来时,可以通过倾炉孔将铁水从高炉中排出。铁水会流入铁罐中,并冷却凝固成铁块。
之后是炉渣处理阶段,高炉炉渣是由炉料ห้องสมุดไป่ตู้的铁氧化物、石灰石和其他杂质组成的。处理炉渣主要有两个目的:一是回收其中的铁,二是确保炉渣中的有害物质被安全处理。一般会通过氧枪在炉渣中吹氧气,使其中的铁氧化物氧化成铁,并进一步回收。
高炉生产工艺流程
高炉是一种用于冶炼铁的设备,它能够将铁矿石中的铁氧化物还原成纯铁。高炉生产工艺流程包括六个主要步骤:入炉、炉内反应、铁水出炉、炉渣处理、炉气处理和余热回收。
首先是入炉阶段,这个阶段主要是将铁矿石和焦炭按一定比例装入高炉的上料斗中,然后通过料斗控制系统将料物顺次送入炉缸内。在这个过程中,还会加入一定量的石灰石和焦粉,以调节炉料的碱度和流动性。
高炉生产工艺流程

高炉生产工艺流程
《高炉生产工艺流程》
高炉是冶炼铁的主要设备之一,其生产工艺流程复杂而精密。
下面我们就来简要介绍一下高炉生产工艺流程。
首先是原料的准备。
在高炉冶炼过程中,主要原料包括铁矿石、焦炭和石灰石。
这些原料需要进行粉碎和预处理,以便于在高炉中的正常使用。
接下来是原料的投入。
在高炉的顶部,将热风和原料同时注入,而在炉底则通过鼓风机将空气送入,这样可以形成高炉内部的燃烧和还原环境。
然后是炉内反应的进行。
在高炉内部,焦炭先被加热分解形成一定数量的一氧化碳和氢气,然后这些还原气体与熔化的铁矿石发生反应,最终生成液态铁和副产物(例如石灰石渣和炉渣)。
最后是产物的采集和处理。
产生的液态铁会通过出口流出,而炉渣则会流出高炉底部。
这些产物需要进一步加工,例如炉渣用于筑路或者水泥生产,而液态铁则用于钢铁的生产。
总的来说,高炉生产工艺流程是一个复杂而有序的过程,需要严格的管理和运行。
只有良好的生产工艺流程,才能确保高炉的正常生产,同时也能减少资源的浪费和环境的污染。
高炉炼铁工艺流程
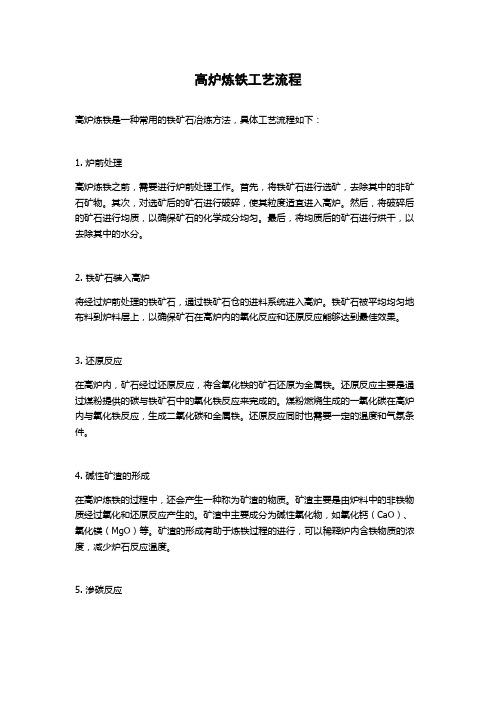
高炉炼铁工艺流程高炉炼铁是一种常用的铁矿石冶炼方法,具体工艺流程如下:1. 炉前处理高炉炼铁之前,需要进行炉前处理工作。
首先,将铁矿石进行选矿,去除其中的非矿石矿物。
其次,对选矿后的矿石进行破碎,使其粒度适宜进入高炉。
然后,将破碎后的矿石进行均质,以确保矿石的化学成分均匀。
最后,将均质后的矿石进行烘干,以去除其中的水分。
2. 铁矿石装入高炉将经过炉前处理的铁矿石,通过铁矿石仓的进料系统进入高炉。
铁矿石被平均均匀地布料到炉料层上,以确保矿石在高炉内的氧化反应和还原反应能够达到最佳效果。
3. 还原反应在高炉内,矿石经过还原反应,将含氧化铁的矿石还原为金属铁。
还原反应主要是通过煤粉提供的碳与铁矿石中的氧化铁反应来完成的。
煤粉燃烧生成的一氧化碳在高炉内与氧化铁反应,生成二氧化碳和金属铁。
还原反应同时也需要一定的温度和气氛条件。
4. 碱性矿渣的形成在高炉炼铁的过程中,还会产生一种称为矿渣的物质。
矿渣主要是由炉料中的非铁物质经过氧化和还原反应产生的。
矿渣中主要成分为碱性氧化物,如氧化钙(CaO)、氧化镁(MgO)等。
矿渣的形成有助于炼铁过程的进行,可以稀释炉内含铁物质的浓度,减少炉石反应温度。
5. 渗碳反应在高炉内,碳通过渗碳反应进一步与铁进行反应,生成碳化物。
这个过程通常需要在高炉底部的温度比较高的炉渣中进行,以确保足够的反应速率。
碳化物生成后,还需要通过进一步的处理来使其转变为可用的铁。
6. 炉缸维护和清理高炉炼铁过程中,会产生一些固体杂质物质,如炉渣和金属铁结晶等。
这些杂质会在高炉底部形成一层坚硬的物质,称为炉缸。
定期对高炉进行炉缸维护和清理是必要的,以保证高炉运行的正常和稳定。
7. 铁水和渣化处理高炉炼铁过程中,会产生两种产品,一种是铁水,另一种是矿渣。
铁水通过高炉底部的铁口流出,进入铁水包。
然后,将铁水通过通道输送到后续的冶金工艺中进行进一步的处理。
矿渣则从高炉底部的渣口流出,进入矿渣车,最终被运到矿渣堆存放。
高炉炼铁的主要工艺流程

高炉炼铁的主要工艺流程高炉炼铁是一种传统的冶炼工艺,通过将铁矿石、焦炭和石灰石等原料投入高炉,经过化学反应和物理过程,最终得到铁水和副产品。
下面将介绍高炉炼铁的主要工艺流程。
1. 原料准备:高炉炼铁的主要原料包括铁矿石、焦炭和石灰石。
首先,铁矿石要经过破碎、磨细的过程,使得颗粒大小适合投入高炉。
焦炭也需要经过破碎、筛分,去除杂质,以提高燃烧效率。
石灰石用于炉渣的形成,防止高炉壁被侵蚀。
2. 加料混合:将经过准备的铁矿石、焦炭和石灰石按一定比例投入到高炉的料斗中。
同时,还需要添加一定的烧结矿和再生焦,以增加炉料的活性和燃烧效率。
混合的原料进入高炉,开始炼铁过程。
3. 预热干燥:原料混合进入高炉后,从上部加入的燃烧空气通过炉体底部的风口喷吹,使混合料堆温度迅速升高。
在预热的同时,水分和挥发物被蒸发除去,使料堆达到干燥状态。
4. 还原反应:当料堆升温到一定程度时,焦炭开始燃烧,释放大量的热能,同时产生一氧化碳(CO)。
在高炉中,一氧化碳与铁矿石中的氧发生还原反应,将铁矿石中的氧还原成金属铁。
这是炼铁过程的关键步骤。
5. 炉渣形成:在还原反应过程中,石灰石与其他杂质反应生成衍生石灰,与铁矿石中的硅和磷等杂质形成炉渣。
炉渣既可以保护高炉炉壁不受侵蚀,还可以促进还原反应的进行,提高金属铁的产率。
6. 铁水收集:经过还原反应后,金属铁被熔化并沉积在高炉底部的铁水中。
在铁水收集器中,铁水与炉渣通过不同的密度分层,并通过铁水口和渣口分别排出。
铁水经过冷却和预处理后,可作为原料用于制造钢铁。
7. 副产品处理:除了铁水以外,高炉炼铁还能产生大量的副产品,如煤气、炉渣和飞灰等。
煤气作为一种重要的燃料和能源资源,可用于发电、加热和炼化等。
炉渣可以用于建筑材料的生产,而飞灰则可以通过处理和综合利用,减少环境污染。
综上所述,高炉炼铁的主要工艺流程包括原料准备、加料混合、预热干燥、还原反应、炉渣形成、铁水收集和副产品处理。
这个工艺流程经过长时间的发展和改进,已经成为一种效率高、成本低、能源利用率较高的冶炼工艺。
钢铁生产高炉操作工作流程

钢铁生产高炉操作工作流程钢铁生产过程是一个复杂而精细的工艺过程,其中高炉操作是整个生产流程中至关重要的一环。
本文将详细介绍钢铁生产高炉操作的工作流程,从原料准备、炉缸布料、点火预热、风温控制、出铁、停炉等环节进行阐述。
一、原料准备钢铁生产的原料主要包括铁矿石、焦炭、石灰石和回收废铁等。
在高炉操作前,首先需要对这些原料进行准备工作。
铁矿石需要破碎、分级、洗选,以确保矿石的质量和粒度符合生产要求。
焦炭则需要经过碳化、煅烧和混合等处理,以提高燃烧效率和炉内温度。
二、炉缸布料炉缸布料是指将预先准备好的原料按一定的比例投入到高炉炉腔内。
在高炉操作中,需要考虑各种原料的配比和进料方式,以达到最佳的冶炼效果。
通常情况下,铁矿石和焦炭按一定比例混合后装入高炉上部的料斗,然后通过布料装置均匀分布到炉缸内。
三、点火预热炉缸布料完成后,需要进行点火预热操作。
点火预热是指将炉内的原料进行燃烧,以使炉内温度逐渐升高到冶炼所需的温度。
点火预热过程通常包括初次点火、次发点火和正常点火等阶段。
在高炉操作中,要注意控制点火的氧气和燃料的配比,以保证点火正常进行。
四、风温控制点火预热完成后,需要进行风温控制。
高炉内需要通过燃烧来提供能量,而风是提供燃烧所需氧气的关键。
在高炉操作过程中,需要根据冶炼条件的要求,控制风温的高低。
通常情况下,风的温度越高,炉内温度也会相应提高。
通过调节风温,可以控制高炉内的温度和冶炼反应的速率。
五、出铁高炉操作的最终目的是生产出高质量的钢铁产品。
在生产过程中,需要定期进行出铁操作,将炉内的铁水抽取出来,并进行冷却和净化处理。
出铁操作需要考虑铁水的温度、速度和清洁度等因素,以确保生产出符合要求的钢铁产品。
六、停炉高炉操作周期结束或需要进行维护时,需要进行停炉操作。
停炉是指将高炉的冶炼过程暂停,进行冷却、清洗和维护等工作。
在停炉期间,需要对高炉进行检查、保养和维修,以保证高炉的正常运行和延长使用寿命。
综上所述,钢铁生产高炉操作是一个复杂而关键的工作环节。
高炉炼铁工艺流程(经典)

高炉炼铁工艺流程(经典)高炉炼铁是冶金行业中的基本工艺之一,主要目的是将矿石加热、还原、融化,以得到铁、钢和其他有价值的金属。
1. 炉料预处理高炉炼铁的第一步是对原料进行预处理,以达到最佳的炉料质量。
这包括:(1)筛选和分类。
矿石会被分类成不同的品级和尺寸,以确保炉料进入高炉的均匀性和稳定性。
(2)磨粉和混合。
矿石和焦炭会被磨成粉末状,并混合在一起。
(3)加湿和固化。
炉料加湿以增加其粘度,使其更容易在高炉中流动。
固化会让炉料更加坚硬,并有利于在炉内定位。
2. 热解和预热炉料进入高炉后,在逐渐升温过程中,炉料中的挥发物和水份被氧化释放,这个过程被称为热解。
热解产生的有害气体,如CO和H2S,通过冷凝和过滤处理后被排出。
预热会将炉料升至高约350°C的温度,以减少在高炉下部的稳定层压力和防止炉底过度损伤。
3. 预还原和加热在高炉内部,还原作用开始发生。
炉料中的铁氧化物被焦炭还原为铁和CO气体。
在高达1000°C的温度下,铁氧化物会形成红热的铁球,并不断向上移动。
在高炉与炉料接触的区域中,铁球受到温度和压力的作用被压加,经过连续的还原作用,最终形成液态铁。
此时,高炉中的温度达到了1400°C左右。
4. 熔融和分层随着炉料和铁的连续加入,高炉内部的温度和压力继续上升,炉料和铁不断熔化。
液态金属以高密度移动到炉底,驱动炉料和熔渣从上层向下层流动。
在高炉的不同高度,会形成不同的物理和化学反应,导致铁、钢和有价值的金属的分离和收集。
5. 出铁和熔渣处理在高炉下部设置有出铁口,铁水通过铁口离开高炉。
铁水一般会被收集在铁包中,并通过滑动放铁的方式输入到下一个工艺站点中。
高炉底部产生的熔渣会通过高炉底部的孔洞排出,并被输送到熔渣池进行处理。
总结:高炉炼铁的工艺流程包括炉料预处理、热解和预热、预还原和加热、熔融和分层以及出铁和熔渣处理等。
整个过程需要高温、高压、长时间的反应,需要准确控制各项参数以保证操作的安全性和炉内炼铁的效率。
高炉炼铁工艺流程
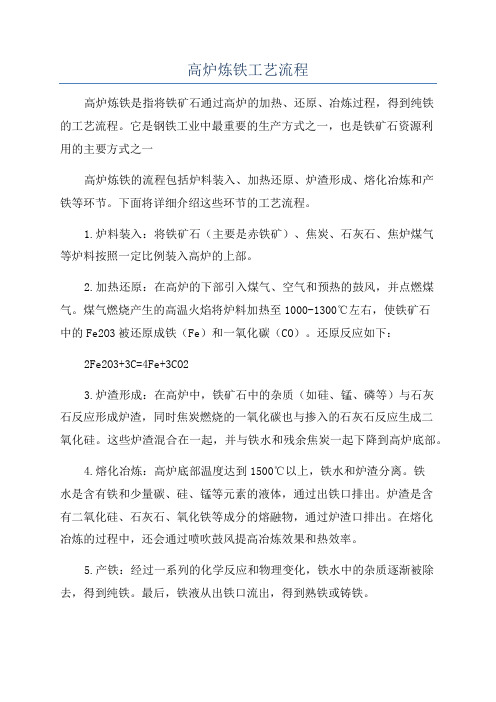
高炉炼铁工艺流程
高炉炼铁是指将铁矿石通过高炉的加热、还原、冶炼过程,得到纯铁
的工艺流程。
它是钢铁工业中最重要的生产方式之一,也是铁矿石资源利
用的主要方式之一
高炉炼铁的流程包括炉料装入、加热还原、炉渣形成、熔化冶炼和产
铁等环节。
下面将详细介绍这些环节的工艺流程。
1.炉料装入:将铁矿石(主要是赤铁矿)、焦炭、石灰石、焦炉煤气
等炉料按照一定比例装入高炉的上部。
2.加热还原:在高炉的下部引入煤气、空气和预热的鼓风,并点燃煤气。
煤气燃烧产生的高温火焰将炉料加热至1000-1300℃左右,使铁矿石
中的Fe2O3被还原成铁(Fe)和一氧化碳(CO)。
还原反应如下:2Fe2O3+3C=4Fe+3CO2
3.炉渣形成:在高炉中,铁矿石中的杂质(如硅、锰、磷等)与石灰
石反应形成炉渣,同时焦炭燃烧的一氧化碳也与掺入的石灰石反应生成二
氧化硅。
这些炉渣混合在一起,并与铁水和残余焦炭一起下降到高炉底部。
4.熔化冶炼:高炉底部温度达到1500℃以上,铁水和炉渣分离。
铁
水是含有铁和少量碳、硅、锰等元素的液体,通过出铁口排出。
炉渣是含
有二氧化硅、石灰石、氧化铁等成分的熔融物,通过炉渣口排出。
在熔化
冶炼的过程中,还会通过喷吹鼓风提高冶炼效果和热效率。
5.产铁:经过一系列的化学反应和物理变化,铁水中的杂质逐渐被除去,得到纯铁。
最后,铁液从出铁口流出,得到熟铁或铸铁。
高炉工艺流程

高炉工艺流程
高炉是冶炼铁的主要设备,其工艺流程包括原料准备、炉料装入、炉内燃烧、还原、熔融和出铁等环节。
下面将详细介绍高炉工艺流程。
首先是原料准备。
高炉的主要原料有焦炭、铁矿石和石灰石。
焦炭是炼铁的燃料,铁矿石是生铁的主要原料,石灰石是用来消耗炉渣中的硅酸和硫。
这些原料需要经过破碎、筛分和配比等工序,确保其化学成分和粒度符合高炉冶炼的要求。
接下来是炉料装入。
在高炉顶部设有料斗,将原料按一定的配比顺序装入料斗,然后通过料斗的开闭装入到高炉内。
炉料的装入顺序和层次对高炉的冶炼过程有着重要的影响,需要根据炉料的性质和冶炼要求进行合理的设计。
然后是炉内燃烧和还原。
在高炉内,焦炭燃烧产生的热量使炉料逐渐升温,矿石中的铁氧化物被还原成金属铁。
同时,燃烧产生的一氧化碳还与矿石中的氧化物发生化学反应,生成二氧化碳和金属铁。
接着是熔融。
随着高炉内温度的升高,金属铁逐渐熔化,与炉渣分离。
炉渣是炼铁过程中产生的一种碱性物质,它能够与矿石中的杂质发生化学反应,形成易于分离的渣滓。
最后是出铁。
经过一系列的冶炼过程,炉内的金属铁和炉渣分离,金属铁在高炉底部聚集,通过出铁口流出。
而炉渣则通过炉渣口排出高炉。
总的来说,高炉工艺流程是一个复杂的物理化学过程,需要严格控制各个环节的操作参数,确保冶炼过程稳定、高效。
同时,高炉的自动化技术和智能化控制也在不断发展,为提高生产效率和降低能耗提供了重要的技术支持。
通过对高炉工艺流程的深入了解,可以更好地指导生产实践,提高炼铁工艺的技术水平,推动炼铁行业的可持续发展。
高炉冶炼工艺流程
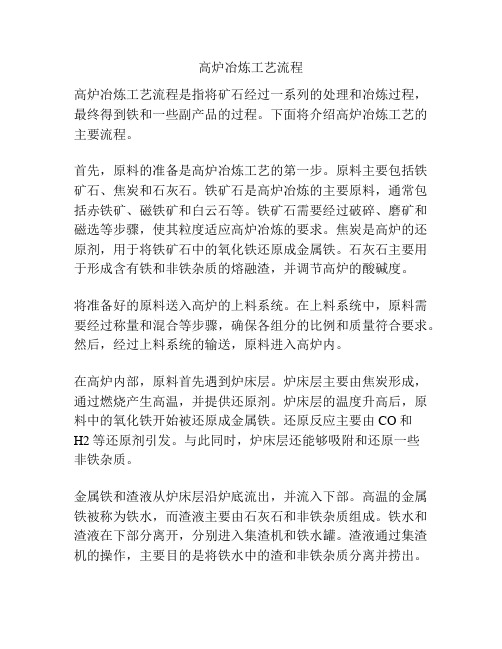
高炉冶炼工艺流程高炉冶炼工艺流程是指将矿石经过一系列的处理和冶炼过程,最终得到铁和一些副产品的过程。
下面将介绍高炉冶炼工艺的主要流程。
首先,原料的准备是高炉冶炼工艺的第一步。
原料主要包括铁矿石、焦炭和石灰石。
铁矿石是高炉冶炼的主要原料,通常包括赤铁矿、磁铁矿和白云石等。
铁矿石需要经过破碎、磨矿和磁选等步骤,使其粒度适应高炉冶炼的要求。
焦炭是高炉的还原剂,用于将铁矿石中的氧化铁还原成金属铁。
石灰石主要用于形成含有铁和非铁杂质的熔融渣,并调节高炉的酸碱度。
将准备好的原料送入高炉的上料系统。
在上料系统中,原料需要经过称量和混合等步骤,确保各组分的比例和质量符合要求。
然后,经过上料系统的输送,原料进入高炉内。
在高炉内部,原料首先遇到炉床层。
炉床层主要由焦炭形成,通过燃烧产生高温,并提供还原剂。
炉床层的温度升高后,原料中的氧化铁开始被还原成金属铁。
还原反应主要由CO和H2等还原剂引发。
与此同时,炉床层还能够吸附和还原一些非铁杂质。
金属铁和渣液从炉床层沿炉底流出,并流入下部。
高温的金属铁被称为铁水,而渣液主要由石灰石和非铁杂质组成。
铁水和渣液在下部分离开,分别进入集渣机和铁水罐。
渣液通过集渣机的操作,主要目的是将铁水中的渣和非铁杂质分离并捞出。
在铁水中,由于与其他金属杂质的存在,铁水内液相中的溶解量较高,此时需要进行脱硫的操作。
脱硫通常是通过给予少量的石灰石进行的,石灰石与脱硫反应生成硫酸钙,并吸附了金属硫化物。
然后,通过浮渣方式将硫酸钙从金属铁中分离出来。
最后,清洗后的铁水进入铁水罐,然后通过铁水输送系统运送到连铸车间,进行铸造最终的铸锭或铸坯。
通过连铸工艺,铸锭或铸坯得以快速冷却,并变成半成品钢。
综上所述,高炉冶炼工艺流程是一个复杂的过程,包括原料准备、上料系统、炉床层、金属铁和渣液的分离以及铁水的处理等。
通过这些工艺步骤,高炉能够将矿石转化为铁和其他副产品,为钢铁工业提供了基础材料。
高炉生产的工艺流程

高炉生产的工艺流程
《高炉生产工艺流程》
高炉是一种生产铁的设备,通常用来从铁矿石中提取铁的过程。
下面是高炉生产的工艺流程。
首先,取得原料。
原料包括铁矿石、焦炭和石灰石。
铁矿石是高炉的主要原料,通常是由含铁量较高的矿石制成。
焦炭是一种煤炭制品,用来加热高炉,使铁矿石中的铁得以提取。
石灰石用来帮助将非铁性杂质从铁矿石中剥离出来。
其次,原料预处理。
铁矿石首先需要经过破碎和磨粉的过程,以便在高炉中更容易被加热。
焦炭也需要进行预处理,以去除其中的杂质和硫。
接下来,原料进入高炉。
铁矿石、焦炭和石灰石被混合在一起,然后送入高炉的顶部。
高炉内部温度达到1500°C以上,原料
在高温下逐渐熔化并产生还原气体。
然后,铁的提取。
在高炉内,还原气体和熔融铁矿石反应,将铁从矿石中提取出来。
非铁性杂质则形成渣,浮在熔融的铁上方。
这样,铁和渣就可以分离了。
最后,产出铁和渣。
经过一系列的处理,从高炉中得到的铁和渣分别被收集起来。
铁经过冷却和成形后,成为各种钢材的生产原料。
而渣通常被用作道路材料或建筑材料。
在整个高炉生产的工艺流程中,需要高温、还原气体和适当的原料配比。
这样才能确保高炉生产出优质的铁和渣。
炼铁高炉工艺流程
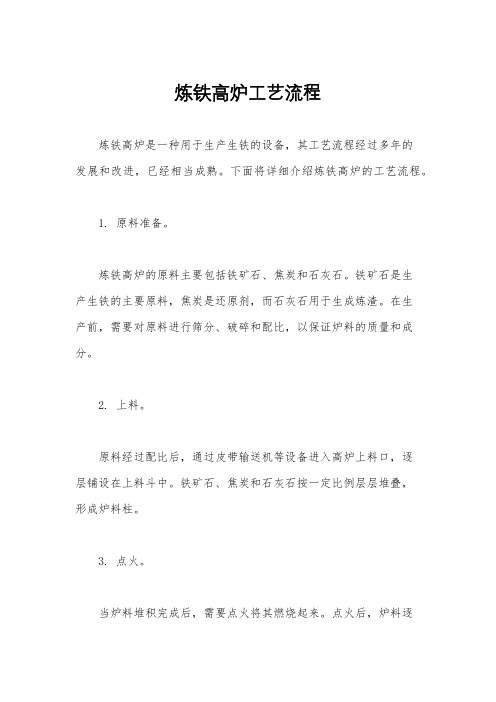
炼铁高炉工艺流程炼铁高炉是一种用于生产生铁的设备,其工艺流程经过多年的发展和改进,已经相当成熟。
下面将详细介绍炼铁高炉的工艺流程。
1. 原料准备。
炼铁高炉的原料主要包括铁矿石、焦炭和石灰石。
铁矿石是生产生铁的主要原料,焦炭是还原剂,而石灰石用于生成炼渣。
在生产前,需要对原料进行筛分、破碎和配比,以保证炉料的质量和成分。
2. 上料。
原料经过配比后,通过皮带输送机等设备进入高炉上料口,逐层铺设在上料斗中。
铁矿石、焦炭和石灰石按一定比例层层堆叠,形成炉料柱。
3. 点火。
当炉料堆积完成后,需要点火将其燃烧起来。
点火后,炉料逐渐升温,煤气和炉渣开始产生,高炉内部温度逐渐升高。
4. 还原。
在高温下,焦炭开始发生还原反应,将铁矿石中的氧化铁还原为金属铁。
还原反应释放出大量的热量,使高炉内部温度进一步升高。
5. 碳氧化反应。
随着温度的升高,炼炉石灰石开始分解,释放出二氧化碳,与铁矿石中的残余氧化物发生碳氧化反应,生成炼渣。
6. 放铁。
当高炉内部温度达到一定程度,炼铁开始熔化,熔化的铁从高炉底部的出铁口流出,经过冷却成型,得到初生铁。
7. 放渣。
除了炼铁外,高炉中还会生成炼渣。
炼渣是一种含有氧化物和矿石杂质的物质,需要定期从高炉炉嘴排出,以保证高炉正常运行。
8. 检修。
高炉在生产过程中需要进行定期检修和维护,以保证设备的正常运行和安全生产。
检修包括炉体、炉缸、炉喉等部位的维护和更换。
总结,炼铁高炉工艺流程经过多年的发展和改进,已经相当成熟。
从原料准备到炉料上料、点火、还原、碳氧化反应、放铁、放渣和检修,每个环节都需要严格控制,以保证高炉的正常运行和生产效率。
炼铁高炉是钢铁行业的重要设备,其工艺流程对于钢铁生产具有重要的意义。
高炉炼铁生产工艺流程简介
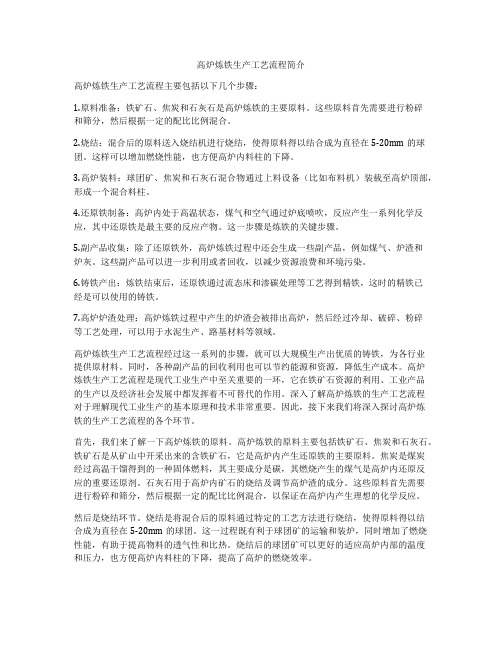
高炉炼铁生产工艺流程简介高炉炼铁生产工艺流程主要包括以下几个步骤:1.原料准备:铁矿石、焦炭和石灰石是高炉炼铁的主要原料。
这些原料首先需要进行粉碎和筛分,然后根据一定的配比比例混合。
2.烧结:混合后的原料送入烧结机进行烧结,使得原料得以结合成为直径在5-20mm的球团。
这样可以增加燃烧性能,也方便高炉内料柱的下降。
3.高炉装料:球团矿、焦炭和石灰石混合物通过上料设备(比如布料机)装载至高炉顶部,形成一个混合料柱。
4.还原铁制备:高炉内处于高温状态,煤气和空气通过炉底喷吹,反应产生一系列化学反应,其中还原铁是最主要的反应产物。
这一步骤是炼铁的关键步骤。
5.副产品收集:除了还原铁外,高炉炼铁过程中还会生成一些副产品,例如煤气、炉渣和炉灰。
这些副产品可以进一步利用或者回收,以减少资源浪费和环境污染。
6.铸铁产出:炼铁结束后,还原铁通过流态床和渗碳处理等工艺得到精铁,这时的精铁已经是可以使用的铸铁。
7.高炉炉渣处理:高炉炼铁过程中产生的炉渣会被排出高炉,然后经过冷却、破碎、粉碎等工艺处理,可以用于水泥生产、路基材料等领域。
高炉炼铁生产工艺流程经过这一系列的步骤,就可以大规模生产出优质的铸铁,为各行业提供原材料。
同时,各种副产品的回收利用也可以节约能源和资源,降低生产成本。
高炉炼铁生产工艺流程是现代工业生产中至关重要的一环,它在铁矿石资源的利用、工业产品的生产以及经济社会发展中都发挥着不可替代的作用。
深入了解高炉炼铁的生产工艺流程对于理解现代工业生产的基本原理和技术非常重要。
因此,接下来我们将深入探讨高炉炼铁的生产工艺流程的各个环节。
首先,我们来了解一下高炉炼铁的原料。
高炉炼铁的原料主要包括铁矿石、焦炭和石灰石。
铁矿石是从矿山中开采出来的含铁矿石,它是高炉内产生还原铁的主要原料。
焦炭是煤炭经过高温干馏得到的一种固体燃料,其主要成分是碳,其燃烧产生的煤气是高炉内还原反应的重要还原剂。
石灰石用于高炉内矿石的烧结及调节高炉渣的成分。
高炉炼铁的原理及工艺流程

高炉炼铁的原理及工艺流程高炉炼铁是一种常用的冶金方法,用于将矿石转化为铁和钢。
它的原理基于铁矿石中铁的还原性质以及高温下不同物质的化学反应。
高炉炼铁的工艺流程大致可以分为以下几个步骤:1. 原料准备:高炉的主要原料是铁矿石、焦炭和石灰石。
铁矿石是高炉的主要还原剂和铁源,焦炭则提供高炉所需的热能和还原剂。
石灰石用于抑制高炉内部的硅和磷的含量。
2. 原料装料:将铁矿石、焦炭和石灰石按照一定比例装入高炉的料斗。
装料过程中要保证各种原料的均匀分布,以便提高炉内反应的效率。
3. 预热煤气和空气:将进入高炉的煤气和空气预热至高温,以增加反应速率和效率。
4. 还原反应:在高炉内,焦炭在高温下与煤气发生还原反应,将铁矿石中的氧气还原成一氧化碳和二氧化碳。
还原反应主要发生在高炉的炉底,炉底以上则发生熔融反应。
5. 熔融反应:一氧化碳和铁矿石中的一些元素熔融成液态铁,并向上移动。
在高炉的中部区域,发生碱性熔融反应,石灰石中的氧化钙与铁矿石中的硅和磷等杂质反应,生成氧化钙和矽酸钙等不溶于铁液的物质,称为渣。
6. 渣铁分离:在高炉的上部,铁液与渣发生不同密度的分离,铁液下流,渣上浮。
由于铁液的密度大于渣,渣可以通过铁液顶部的出渣口排出高炉。
7. 铁水处理:高炉出来的铁液通过钢水包、连铸机等设备进一步处理,以调整铁液的成分和温度,并制造成各种规格和形状的铁坯。
8. 高炉煤气回收:高炉炼铁过程中产生的煤气中含有大量的有价值的气体,如一氧化碳和氢气。
这些煤气被收集后再经过净化和加工,用于供能和制造化学产品等。
通过以上工艺流程,高炉炼铁成功将矿石转化为铁和钢,并产生有价值的煤气。
高炉炼铁工艺有以下几个优点:一是工艺简单,能够处理大量原料;二是可以通过调整原料的配比和炉温等参数,控制铁液的成分和温度;三是能够回收煤气,提高能源利用效率;四是可以用于处理不同种类和品质的铁矿石。
炼钢的工艺流程 高炉炼钢工艺流程
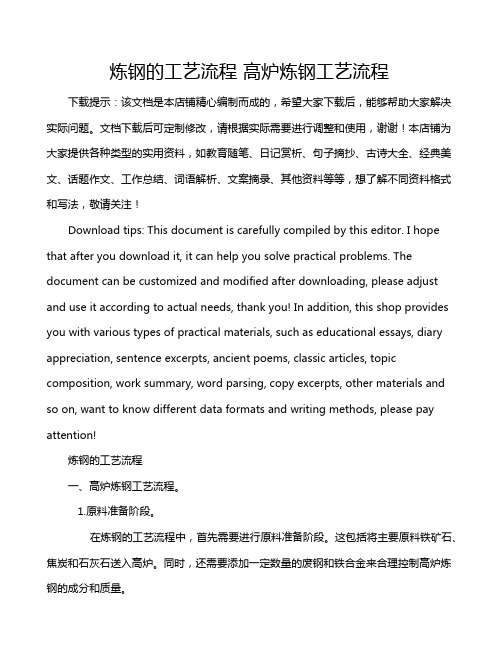
炼钢的工艺流程高炉炼钢工艺流程下载提示:该文档是本店铺精心编制而成的,希望大家下载后,能够帮助大家解决实际问题。
文档下载后可定制修改,请根据实际需要进行调整和使用,谢谢!本店铺为大家提供各种类型的实用资料,如教育随笔、日记赏析、句子摘抄、古诗大全、经典美文、话题作文、工作总结、词语解析、文案摘录、其他资料等等,想了解不同资料格式和写法,敬请关注!Download tips: This document is carefully compiled by this editor. I hope that after you download it, it can help you solve practical problems. The document can be customized and modified after downloading, please adjust and use it according to actual needs, thank you! In addition, this shop provides you with various types of practical materials, such as educational essays, diary appreciation, sentence excerpts, ancient poems, classic articles, topic composition, work summary, word parsing, copy excerpts, other materials and so on, want to know different data formats and writing methods, please pay attention!炼钢的工艺流程一、高炉炼钢工艺流程。
1.原料准备阶段。
高炉生产工艺流程
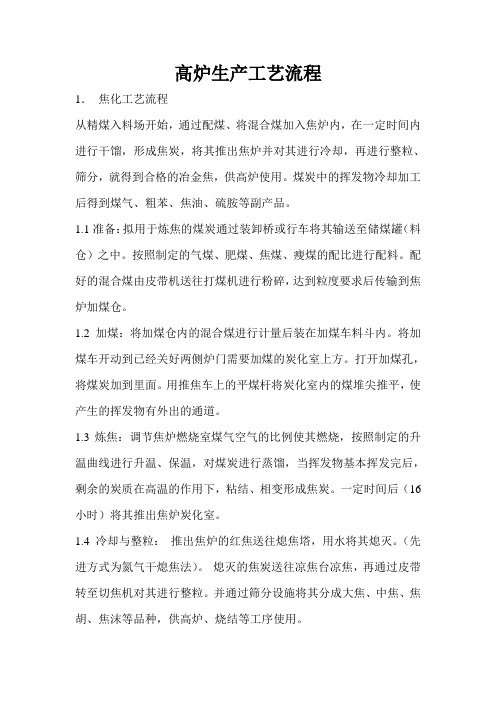
高炉生产工艺流程1.焦化工艺流程从精煤入料场开始,通过配煤、将混合煤加入焦炉内,在一定时间内进行干馏,形成焦炭,将其推出焦炉并对其进行冷却,再进行整粒、筛分,就得到合格的冶金焦,供高炉使用。
煤炭中的挥发物冷却加工后得到煤气、粗苯、焦油、硫胺等副产品。
1.1准备:拟用于炼焦的煤炭通过装卸桥或行车将其输送至储煤罐(料仓)之中。
按照制定的气煤、肥煤、焦煤、瘦煤的配比进行配料。
配好的混合煤由皮带机送往打煤机进行粉碎,达到粒度要求后传输到焦炉加煤仓。
1.2 加煤:将加煤仓内的混合煤进行计量后装在加煤车料斗内。
将加煤车开动到已经关好两侧炉门需要加煤的炭化室上方。
打开加煤孔,将煤炭加到里面。
用推焦车上的平煤杆将炭化室内的煤堆尖推平,使产生的挥发物有外出的通道。
1.3炼焦:调节焦炉燃烧室煤气空气的比例使其燃烧,按照制定的升温曲线进行升温、保温,对煤炭进行蒸馏,当挥发物基本挥发完后,剩余的炭质在高温的作用下,粘结、相变形成焦炭。
一定时间后(16小时)将其推出焦炉炭化室。
1.4 冷却与整粒:推出焦炉的红焦送往熄焦塔,用水将其熄灭。
(先进方式为氮气干熄焦法)。
熄灭的焦炭送往凉焦台凉焦,再通过皮带转至切焦机对其进行整粒。
并通过筛分设施将其分成大焦、中焦、焦胡、焦沫等品种,供高炉、烧结等工序使用。
1.5 化产回收:焦炉炭化室内炼焦蒸馏出的挥发物通过积气罐收集后送往化产回收系统,在其冷却过程中,会析出焦油、粗苯、氨等物质,采用不同工艺将其回收处理。
作为副产品销售。
冷却的煤气供铸管退火炉、烧结点火炉等处使用。
2.烧结工艺流程从原料进入料场开始,通过配料将各种矿粉按比例进行混合,通过胶带输送机将其送到烧结机上进行布料进行烧结,烧成的烧结矿经过破碎、筛分、冷却等工序形成成品烧结矿,成品烧结矿通过皮带输送至高炉料仓这一过程。
它包括原料储存、燃料加工、整粒、配料、一次混合、二次混合、烧结、冷却、整粒的全部工艺过程。
2.1 准备:精矿粉、富矿粉、高炉返矿、云粉等由汽车从原料场转运至烧结配料库。
- 1、下载文档前请自行甄别文档内容的完整性,平台不提供额外的编辑、内容补充、找答案等附加服务。
- 2、"仅部分预览"的文档,不可在线预览部分如存在完整性等问题,可反馈申请退款(可完整预览的文档不适用该条件!)。
- 3、如文档侵犯您的权益,请联系客服反馈,我们会尽快为您处理(人工客服工作时间:9:00-18:30)。
高炉工艺流程炼铁是在高炉内进行还原反应过程,炉料-矿石、燃料和熔剂从无料钟炉顶装入炉内,从鼓风机来的冷风经热风炉后,形成热风从高炉风口鼓入,随着焦炭燃烧,产生热煤气流由下而上运动,而炉料则由上而下运动,互相接触,进行热交换,逐步还原,最后到炉子下部,还原成生铁,同时形成炉渣。
积聚在炉缸的铁水和炉渣分别由出铁口和出渣口放出。
由铁的生产过程可知,高炉除了反应炉本体系统,还包括了热风炉、上料、炉顶、炉前、喷煤、冲渣、给排水、除尘系统等。
其中各系统的工艺流程如下:1.本体高炉本体是利用铁矿石作原料生产铁水的主要设备,是生成铁反应的容器。
高炉也是钢铁联合企业生产线中最重要的基础设备,铁水是转炉炼钢的主要原料,因此高炉生产的优劣直接关系到钢铁联合企业炼钢和钢材的生产,它主要包含了炉基,炉壁,炉喉冷却系统等,且都是利用循环水来冷却的。
2.热风炉热风炉的作用是给高炉提供热风,是炉内反应的必备条件。
1#高炉热风炉采用4个内燃式热风炉为高炉送热风、2个顶燃式热风炉作为预热炉加热助燃空气,同时高炉煤气和助燃空气还通过换热器进行预热。
热风炉是用各种特殊材料建成,可以耐受很高的温度。
炉内砌有许多格子砖,对热风炉的加热,也就是加热这些格子砖。
在加热期间,也被称为“燃烧”状态,高炉煤气和大量的助燃空气混合燃烧,热气到达炉顶,然后通过格子砖,使热风炉被加热,废气从热风炉烟道排出。
当热风炉被加热到一定温度时(顶温1300-1350℃,烟道温度350-400℃),结束燃烧状态,然后准备向高炉提供热风,也就是准备换到“送风“状态。
在送风期间,冷风通过格子砖反向吹进。
砖的热量传递给流过的空气,被加热的空气也称作热风,通过环管送入高炉。
正常生产时,4个热风炉循环送风,一般为2个同时送风,其余2个为燃烧或隔断状态,这样就能满足为高炉提供连续热风的要求。
3.上料上料系统由料仓、输送、给料、排料、筛分、称量等设备组成。
根据冶炼工艺要求,把矿、焦等原燃料配成一定重量和成分的“料批”,然后通过上料运输设备送至炉顶。
1#高炉设计选择胶带机的上料方式。
1#高炉上料系统设计遵循高效、紧凑、清洁、环保、节能、循环经济的技术思想,突破常规的上料模式,两座高炉共用一座联合料仓,焦、矿仓为并列布置。
采用“无中继站”分散筛分和分散称量的直接上料工艺。
采用烧结矿分级入炉技术,可以合理调整入炉原料粒度、控制炉内不同粒度原料的分布,从而提高煤气利用率和炉料的透气性,有利于高炉操作和控制炉墙温度,实现高炉长寿。
5500m3高炉烧结矿选择在烧结厂分级。
烧结矿、球团矿、块矿、杂矿、熔剂、焦炭等原、燃料通过供料系统的胶带机运送至供料转运站。
高炉料仓仓上布置5条带卸料车的配仓胶带机,胶带机在供料转运站内受料后将原、燃料通过卸料车装入料仓内。
焦炭由焦化厂供应输送到高炉料仓, 如高炉焦炭不需要分级入炉时,为避免焦炭的破碎,不进行粒度分级而入炉,如高炉焦炭需要分级入炉时,焦化厂供应系统具有焦炭筛分整粒的功能,筛分整粒后输送到高炉料仓4.炉顶炉顶系统采用无料钟炉顶装料设备。
1#高炉炉顶系统采用的是并罐无料钟技术。
无料钟炉顶设备主要包括:换向溜槽、料罐、阀箱、布料装置。
炉顶系统从工艺上分界是从气密箱往上的部分称为炉顶系统,它包括:上料料罐、垂直探尺、氮气系统、喷水降温系统、水冷气密箱、液压站及部分单个阀的控制。
料罐装满后关上密→开一均阀均压→探尺到值班室规定料线具备放料条件提尺至“0”尺→关一均阀→开二均阀补充压力,均压好后关二均阀→开下密阀→下密开后,启动布料溜槽并找到角度→开节流阀至设定角度放料。
在放料结束后判断实际放料时间与设定时间的差值,根据差值修正下一罐节流的开度设定值→料空信号来后→关节流→关下密→停止溜槽转动→放尺探测料线→料罐根据设定开放散阀放压力(打不开放散,开事故放散)→压力放空后开上密,等待装料。
当皮带上的料进入料罐后,关上密→翻转换向给料器以备装下一罐料→上密关好后开一均阀均压等待料尺到来信号。
5.喷煤喷煤的作用是代替燃烧的焦炭增加热量,以降低焦比,强化冶炼。
它就是把原煤(无烟煤、烟煤)经过烘干、磨细、用氮气输送,将煤粉通过喷煤枪从高炉风口直接喷入炉缸的生产工艺。
喷煤系统工艺部分由以下系统组成,即原煤储运系统、煤粉制备系统、煤粉干燥系统和煤粉喷吹系统。
两个高炉喷煤系统共用一套原煤储运系统,其它三个系统相互独立。
原煤在料场中储存。
原煤在进入喷煤主厂房的原煤仓之前,将无烟煤、烟煤按一定比例(根据生产要求调整)均匀混和。
并通过胶带机输送到喷煤主厂房的原煤仓内。
在进仓之前必须将原煤中的含铁物质清除。
原煤的储存、配煤由原料场来完成,由胶带机(运输量800t/h)运送到原煤仓。
每个高炉每天原煤需求量正常3090t,最大3676t;两座高炉每年原煤需求量208万吨。
煤粉制备系统采用2台大型中速磨煤机制粉,2台高效布袋一级收粉工艺。
设2个有效容积为600m3的原煤仓,可储存原煤1020t,能够满足中速磨连续生产4个小时以上。
原煤仓锥段设计成双曲线形,内衬光滑耐磨衬板,外部设置空气炮,防止堵塞。
原煤通过电子皮带秤给煤机均匀定量给到中速磨,在中速磨中进行研磨,磨细的煤粉由热烟气(由高炉热风炉废气与高温烟气混合而成)携带通过上升管道直接进入到煤粉收集器,在其内进行气固分离,煤粉通过积灰斗下面的卸灰阀均匀地卸到煤粉仓中,尾气经布袋过滤后排入大气,排放浓度小于20 mg/m3。
在系统末端设置2台排粉风机作为整个系统的动力源。
排粉风机出口设置消音器,以减小系统的噪声污染,使噪音指标小于85分贝。
煤粉干燥系统由煤粉干燥混风炉、高炉煤气管道、焦炉煤气管道、助燃空气管道、热风炉废气管道、放散管道、干燥剂管道、废气引风机、助燃风机和各种阀门组成。
采用卧式混风炉,其结构为圆截面钢板外壳全密闭式炉型,内衬耐火砖,具有结构紧凑、容积热强度大、占地面积小,燃烧充分、节约能源,烟气成分和烟气温度易于控制,使用寿命长等特点。
混风炉以高炉煤气作为主要燃料,焦炉煤气用于保温、稳燃、点火和伴烧。
设有自动点火和火焰监测装置,当混风炉熄火时,自动关闭高炉煤气、焦炉煤气供气管道及助燃风机并报警。
喷吹系统采用3个喷煤罐交替进行喷吹、装煤、待喷作业,2根喷煤总管,2个煤粉分配器。
浓相输送,固气比不小于40kg/kg,管道内煤粉流速为2~4m/s。
在每根总管上设置煤粉流量计和调节阀,其调节和计量精度小于4%。
喷煤的倒罐操作、喷吹操作、停止操作、吹扫操作、事故停止操作均为程序自动控制。
6.炉前炉前系统主要包括1# ~ 4#出铁口设备,每个铁口对应一套泥炮机,一套开口机,一套沟盖机。
4套出铁口设备由一套液压系统控制。
液压站:主要由3台主油泵、油箱及2套蓄能器组成。
4套出铁口设备和两套阀站布置在13.05米平台上,其中1#炉前阀站控制1#和4#铁口设备,2#炉前阀站控制2#和3#铁口设备。
出铁场采用双矩形平坦化出铁场,两个出铁场对称布置。
每个出铁场下各设置四条铁水罐车停放线,采用300t铁水罐车运输铁水。
每个出铁场设两个铁口,铁口间夹角77º08'34",每个铁口设有各自独立的泥炮、开口机、移盖机和摆动溜槽等设备。
7.冲渣冲渣系统采用环保型炉渣处理技术,实现蒸气全回收,冲渣水循环使用,减少二氧化硫、硫化氢排放量和水量消耗。
设计按炉渣全部水淬粒化,有利于环保和综合利用,水渣用作生产水泥或超细磨深加工。
设置干渣坑,仅做为事故备用。
一期两座高炉共用一个运输系统,一期一步除“渣1-1”转运站、“渣1-2”转运站、“渣1-1A、B”胶带机通廊、“渣1-2A、B”胶带机通廊、“渣1-3A、B”胶带机通廊外全部建成。
整个运输系统均为双机通廊,每个转运站内都装有三通分料器,正常生产时两座高炉的胶带机互为备用。
两座高炉生产的水渣一部分在渣场堆存后,使用前装机进行装载作业,将水渣装进重载自卸汽车后外运。
另一部分直接装入火车外运。
火车装车线长度为540m,可存放36节车皮。
干渣坑两座高炉的水渣分别由胶带运输机运至“渣—7”转运站后可分两路外运:一路经“渣—9B”胶带机运至水渣堆场暂存后外运,另一路经“渣-9A”胶带机直接装火车外运。
8.给排水给排水系统是给本体、热风炉等岗位提供冷却水,工业水的作用。
它包括:炉体及热风炉软水系统,炉体及热风炉除盐水密闭循环系统,工业水高、中、低压净环系统,加药系统。
除盐水密闭循环冷却系统包括:除盐水炉体A系统,即炉底冷却、炉体各段冷却壁。
它包含有:5台供水泵,1台事故柴油机泵,1#-10#闭式冷却塔。
除盐水炉体B系统,即风口小套、中套、大套冷却系统。
它包含有:4台供水泵,1台事故柴油机泵,1#-4#闭式冷却塔热风炉除盐水密闭循环冷却系统,即热风炉热风阀阀体,阀板冷却系统。
它包括3台供水泵,1它事故柴油机泵,1#-3#闭式冷却塔炉体工业净水开路循环系统包括:高压工业水供水系统,即风口前端、固定测温、炉顶打水等冷却。
它包含有:4台供水泵,1台事故柴油机泵;中压工业水供水系统,即炉喉钢砖、直吹管等冷却,软水备用水。
它包含有:3台供水泵;低压工业水供水系统:3台供水泵。
还有3台工业水上塔泵,2台过滤供水泵9.差压发电(TRT)TRT是利用高炉出口煤气中所蕴含的压力能和热能,使透平膨胀机作功,将其转化为机械能,驱动发电机发电的一种能量回收装置。
从而达到节能、降噪音、环保的目的,是一种节能环保装置。
TRT系统主要分为主煤气系统、润滑油系统、动力油系统、氮气密封系统和循环水系统等几个系统。
高炉产生的煤气,经旋风除尘器,干法除尘后,进入TRT系统。
通过机壳导流使气体转成轴向进入叶栅,气体在静叶栅和动叶栅组成的各自独立的流道中不断膨胀做功,压力和温度逐级降低,并转化为动能作用于工作轮(即转子及动叶片)使之旋转,工作轮通过联轴器带动发电机一起转动而发电。
自透平机出来的煤气,进入低压管网,供用户使用。
TRT与煤气系统中的减压阀组并联。
TRT正常运行时,静叶通过调节自身打开角度来控制通过透平机的煤气流量,从而达到控制高炉顶压的目的。
顶压升高或降低时,调节励磁,以控制发电机的功率因数维持在正常水平(注意不要进相)主煤气系统包括透平机,发电机和励磁机。
实现能的转化:势能→机械能→电能。
润滑油系统主要给透平机、发电机和主轴供油保证其润滑,满足机组在正常工况下及事故状态下润滑油供给,并带走热量。
动力油系统主要给静叶油缸、旁通阀、紧急切断阀等供油,提供压力。
氮气系统主要用来封煤气,氮气压力要略高于煤气压力。
透平机启动时,氮气压力必须大于设定值,否则不允许启动。
检修时,氮气用来吹扫煤气。
将入出口插板阀关闭,放散打开,开始吹扫煤气。
待煤气吹静后,开始检修。
循环水系统主要给润滑油、动力油和发电机冷却系统供水,冷却设备。