我国3D打印技术发展现状及环境分析
3D打印技术的现状和发展趋势

3D打印技术的现状和发展趋势正文:一、3D打印技术的现状3D打印技术是指通过数字化制造技术,将扫描或设计的3D模型数据,利用3D打印机直接切割压缩机床制造而成的物体,并逐层逐层逐渐增加熔化的塑料、金属粉末等原料来形成物体。
目前,3D打印技术的应用范围越来越广泛,主要包括以下几个方面:1.工业制造领域:3D打印技术可以快速制造出零件、模型等,可以节省更多的成本和时间。
2.医疗领域:3D打印技术可以快速制造出人体模型或者人工植入物,大大提高医学效率和成功率。
3.智能科技领域:3D打印技术可以直接制造出智能工具、装置和机器人等,实现智能化和自动化操作。
二、3D打印技术发展趋势1. 宣传力度将会加大随着3D打印技术应用领域的不断拓宽,未来3D打印技术的宣传力度将会越来越大。
因为3D打印技术在医疗、体育、建筑等方面的应用已经日益成熟,人们对于技术的兴趣也越来越高。
2. 材料研究将会更多元化随着3D打印技术的普及和应用,更多的材料研究会呈现多元化的趋势。
3D打印技术可以方便快捷地制造高质量的物品,比如金属、塑料和陶瓷等。
未来,随着材料研究的不断深入,更多的新材料将会被开发出来,供3D打印技术使用。
3. 软件工具将会变得更加强大随着3D打印技术不断的发展,软件工具也将变得更加强大。
3D打印的工程师,为了开发新的打印技术或材料,需要一些能够处理大量信息的软件工具,以确保受到良好的支持并提高他们的工作效率。
4. 3D打印技术将会在更多领域得到广泛应用3D打印技术作为一项高科技技术,其应用领域也将越来越广泛。
未来,3D打印技术将在汽车制造、医疗、建筑、航空航天、交通运输等多个领域实现广泛应用,带来高效、低成本、高效率的制造方式。
结论:随着技术的发展,3D打印技术的应用范围越来越广泛。
未来,3D打印技术将成为一项更加普及且人们所普遍使用的技术,届时3D打印技术将为人们带来更多美好的生活和发展空间。
3D打印技术发展现状及趋势分析
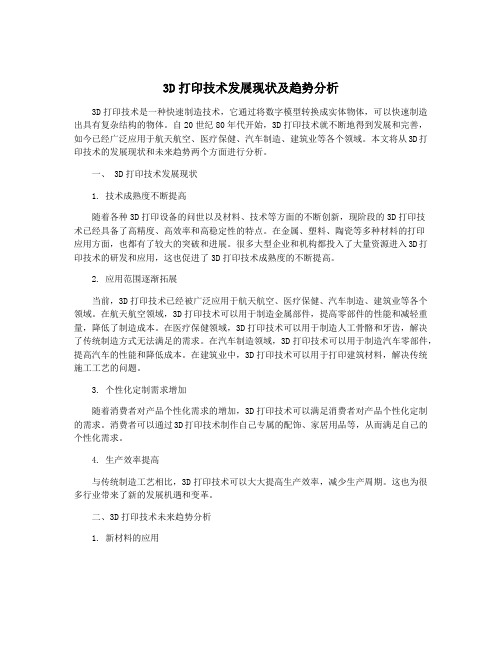
3D打印技术发展现状及趋势分析3D打印技术是一种快速制造技术,它通过将数字模型转换成实体物体,可以快速制造出具有复杂结构的物体。
自20世纪80年代开始,3D打印技术就不断地得到发展和完善,如今已经广泛应用于航天航空、医疗保健、汽车制造、建筑业等各个领域。
本文将从3D打印技术的发展现状和未来趋势两个方面进行分析。
一、 3D打印技术发展现状1. 技术成熟度不断提高随着各种3D打印设备的问世以及材料、技术等方面的不断创新,现阶段的3D打印技术已经具备了高精度、高效率和高稳定性的特点。
在金属、塑料、陶瓷等多种材料的打印应用方面,也都有了较大的突破和进展。
很多大型企业和机构都投入了大量资源进入3D打印技术的研发和应用,这也促进了3D打印技术成熟度的不断提高。
2. 应用范围逐渐拓展当前,3D打印技术已经被广泛应用于航天航空、医疗保健、汽车制造、建筑业等各个领域。
在航天航空领域,3D打印技术可以用于制造金属部件,提高零部件的性能和减轻重量,降低了制造成本。
在医疗保健领域,3D打印技术可以用于制造人工骨骼和牙齿,解决了传统制造方式无法满足的需求。
在汽车制造领域,3D打印技术可以用于制造汽车零部件,提高汽车的性能和降低成本。
在建筑业中,3D打印技术可以用于打印建筑材料,解决传统施工工艺的问题。
3. 个性化定制需求增加随着消费者对产品个性化需求的增加,3D打印技术可以满足消费者对产品个性化定制的需求。
消费者可以通过3D打印技术制作自己专属的配饰、家居用品等,从而满足自己的个性化需求。
4. 生产效率提高与传统制造工艺相比,3D打印技术可以大大提高生产效率,减少生产周期。
这也为很多行业带来了新的发展机遇和变革。
二、3D打印技术未来趋势分析1. 新材料的应用未来,随着新材料的研发和应用,3D打印技术的应用领域将更加广泛。
目前,除了金属、塑料、陶瓷材料外,还有生物材料、纳米材料等,这些新材料的应用将为3D打印技术打开新的应用领域。
3D打印技术的现状和关键技术分析

3D打印技术的现状和关键技术分析3D打印技术是一种快速成型技术,它是一种通过逐层堆叠材料来制作物体的技术。
最初,3D打印技术被用于制造原型,但现在已经广泛应用于各种领域,包括医疗、航天、汽车和消费品制造等。
本文将通过对3D打印技术的现状和关键技术进行分析,探讨3D打印技术的发展趋势和应用前景。
一、3D打印技术的现状1. 发展历程3D打印技术最早可以追溯到20世纪80年代,当时美国麻省理工学院的Charles Hull 发明了第一台3D打印机,并且于1986年申请了第一项3D打印技术的专利。
随后,3D打印技术逐渐向各个领域渗透,不断发展和完善,取得了显著的进展。
目前,全球各种类型的3D打印设备和材料已经不断涌现,3D打印技术已经进入了成熟阶段。
2. 应用领域3D打印技术的应用领域非常广泛,包括医疗、航空航天、汽车、电子产品和消费品制造等。
在医疗领域,3D打印技术被用于制造高精度的人工关节、牙齿和器官模型,为医生提供更精准的手术方案。
在航空航天领域,3D打印技术被用于制造轻量化的航空部件和复杂结构的发动机部件,提高了航空器的性能。
在汽车制造领域,3D打印技术被用于制造汽车零部件和定制化的汽车配件,提高了汽车的安全性和性能。
在消费品制造领域,3D打印技术被用于制造个性化的饰品、家具和玩具,满足了消费者对个性化产品的需求。
3. 发展趋势随着3D打印技术的不断发展,未来它将在更多领域得到应用。
随着3D打印设备的不断升级和成本的不断降低,3D打印技术将逐渐普及,成为工业生产的主流技术。
随着3D打印材料的不断改进和多样化,将能够制造更多种类的产品,包括金属制品、有机材料和复合材料。
随着3D打印技术的结构优化和工艺改进,将能够制造更大尺寸的产品,包括建筑结构、桥梁和飞机机翼等。
二、关键技术分析1. 打印设备3D打印设备是3D打印技术的核心部件,主要包括打印头、打印平台和控制系统。
打印头是用于堆叠材料的部件,可以根据产品的设计要求选择不同的打印头,以打印出不同材料的产品。
3D打印技术的现状与未来发展

3D打印技术的现状与未来发展随着科技的不断进步,3D打印技术越来越受到人们的关注。
3D打印技术可以更加快捷和灵活地生产各种产品,并且在未来的发展中也有着广阔的应用前景。
本文将讨论3D打印技术的现状和未来发展趋势。
一、3D打印技术的现状1、技术原理3D打印技术是一种智能制造技术,是通过计算机将数字化模型转化为具体实物,其工作原理就是通过逐层生长制造构件。
一个3D打印器由液体材料、固体材料、纤维材料和粉末材料等多种材料组成。
3D打印技术的核心是制造构件,构件形态可以通过计算机仿真实现。
在打印构件时,3D打印器将材料按照层次一次一次地堆叠起来,逐层生长打印成型。
因此,有了数字化模型,3D打印技术可以快速、精确地制造出具有各种形状和构型的物品。
2、应用领域3D打印技术已经被广泛应用在医疗、航空、汽车、建筑等领域。
例如,在医疗领域,3D打印技术可以帮助医生更加精确地进行手术,为残疾人提供定制化协助器具,甚至可以为患者生产仿制品。
在航空领域,3D打印技术可以更加快速和精确地生产轻量化部件,减少航空器的重量和增加能效。
在汽车领域,3D打印技术可以通过打印汽车部件,为汽车的制造和改装提供诸多便利。
在建筑领域,3D打印技术可以快速地生产建筑元件,提高建筑施工效率。
二、3D打印技术的未来发展趋势1、应用规模更加广泛随着3D打印技术的发展,其在医疗、教育、文化艺术、消费品、制造业等领域的应用将会越来越广泛。
未来,3D打印技术不仅可以用于生产各种形状、构型的物品,还可以通过多材料多学科交叉融合,打印出对环境、能源以及全球化等方面有纵深研究和贡献的高端产品。
3D打印的规模会越来越大,将会改变传统的生产制造方式,进一步提高生产效率和企业的经济效益。
2、材料与工艺的不断更新目前,3D打印材料主要以ABS、PLA、Nylon、PETG、TPU等塑料为主,而金属材料主要以钛合金、不锈钢、铝合金、镍合金等。
未来,传感器、光电、电黑色材料等新材料的研制将进一步提升3D打印的质量和精度。
3D打印技术发展现状及趋势分析
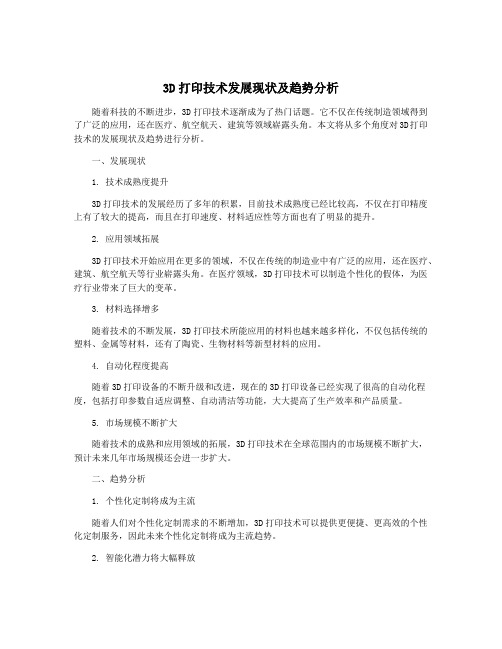
3D打印技术发展现状及趋势分析随着科技的不断进步,3D打印技术逐渐成为了热门话题。
它不仅在传统制造领域得到了广泛的应用,还在医疗、航空航天、建筑等领域崭露头角。
本文将从多个角度对3D打印技术的发展现状及趋势进行分析。
一、发展现状1. 技术成熟度提升3D打印技术的发展经历了多年的积累,目前技术成熟度已经比较高,不仅在打印精度上有了较大的提高,而且在打印速度、材料适应性等方面也有了明显的提升。
2. 应用领域拓展3D打印技术开始应用在更多的领域,不仅在传统的制造业中有广泛的应用,还在医疗、建筑、航空航天等行业崭露头角。
在医疗领域,3D打印技术可以制造个性化的假体,为医疗行业带来了巨大的变革。
3. 材料选择增多随着技术的不断发展,3D打印技术所能应用的材料也越来越多样化,不仅包括传统的塑料、金属等材料,还有了陶瓷、生物材料等新型材料的应用。
4. 自动化程度提高随着3D打印设备的不断升级和改进,现在的3D打印设备已经实现了很高的自动化程度,包括打印参数自适应调整、自动清洁等功能,大大提高了生产效率和产品质量。
5. 市场规模不断扩大随着技术的成熟和应用领域的拓展,3D打印技术在全球范围内的市场规模不断扩大,预计未来几年市场规模还会进一步扩大。
二、趋势分析1. 个性化定制将成为主流随着人们对个性化定制需求的不断增加,3D打印技术可以提供更便捷、更高效的个性化定制服务,因此未来个性化定制将成为主流趋势。
2. 智能化潜力将大幅释放3D打印技术的智能化程度将继续提高,包括智能化设计、智能化打印等,这将大幅提升生产效率和产品质量。
3. 生物材料应用将更加广泛随着医疗领域对生物材料需求的增加,3D打印技术将更加广泛地应用于生物材料的制造,包括人体组织、器官等的打印制造。
4. 可持续发展将成为发展方向随着环境保护意识的提高,可持续发展将成为3D打印技术发展的重要方向,包括资源循环利用、减少废物排放等方面的研究和应用。
5. 工业化生产将逐步成熟随着技术的发展和成熟,3D打印技术的工业化生产将逐步成熟,成为制造业的重要组成部分。
3D打印技术的现状和关键技术分析
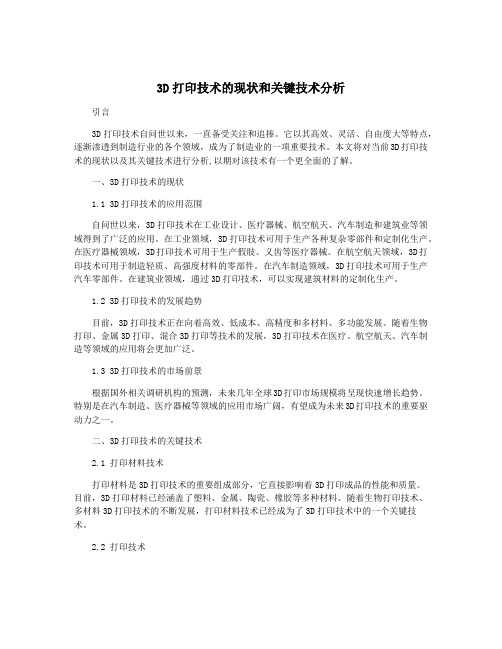
3D打印技术的现状和关键技术分析引言3D打印技术自问世以来,一直备受关注和追捧。
它以其高效、灵活、自由度大等特点,逐渐渗透到制造行业的各个领域,成为了制造业的一项重要技术。
本文将对当前3D打印技术的现状以及其关键技术进行分析,以期对该技术有一个更全面的了解。
一、3D打印技术的现状1.1 3D打印技术的应用范围自问世以来,3D打印技术在工业设计、医疗器械、航空航天、汽车制造和建筑业等领域得到了广泛的应用。
在工业领域,3D打印技术可用于生产各种复杂零部件和定制化生产。
在医疗器械领域,3D打印技术可用于生产假肢、义齿等医疗器械。
在航空航天领域,3D打印技术可用于制造轻质、高强度材料的零部件。
在汽车制造领域,3D打印技术可用于生产汽车零部件。
在建筑业领域,通过3D打印技术,可以实现建筑材料的定制化生产。
1.2 3D打印技术的发展趋势目前,3D打印技术正在向着高效、低成本、高精度和多材料、多功能发展。
随着生物打印、金属3D打印、混合3D打印等技术的发展,3D打印技术在医疗、航空航天、汽车制造等领域的应用将会更加广泛。
1.3 3D打印技术的市场前景根据国外相关调研机构的预测,未来几年全球3D打印市场规模将呈现快速增长趋势。
特别是在汽车制造、医疗器械等领域的应用市场广阔,有望成为未来3D打印技术的重要驱动力之一。
二、3D打印技术的关键技术2.1 打印材料技术打印材料是3D打印技术的重要组成部分,它直接影响着3D打印成品的性能和质量。
目前,3D打印材料已经涵盖了塑料、金属、陶瓷、橡胶等多种材料。
随着生物打印技术、多材料3D打印技术的不断发展,打印材料技术已经成为了3D打印技术中的一个关键技术。
2.2 打印技术打印技术是3D打印技术的核心技术,包括喷墨打印、激光烧结、光固化等多种打印技术。
光固化打印技术是目前最常用的一种3D打印技术,它通过光敏树脂的反应来完成对物体的逐层打印。
2.3 设计软件技术设计软件技术是3D打印技术中的关键技术之一。
3D打印技术的现状与未来发展趋势

3D打印技术的现状与未来发展趋势3D打印技术是一种由计算机控制的逐层堆积物质来创建实体物品的先进制造技术。
这种技术的应用范围十分广泛,从医学、研究、生产、设计到个人娱乐和自助维修等领域均有所涉足。
如今,3D打印技术在不断地发展与突破,本文主要分析其现状与未来发展趋势。
一、3D打印技术发展的现状现在的3D打印技术已经进入了一个全新的时代。
传统的3D打印方法主要有以下几种:1.热塑性制造(FDM)。
FDM是最常见的3D打印技术。
通过热塑性材料的熔融和逐层堆叠,形成三维产品。
FDM 3D打印过程简单,价格低廉,适合家庭、教育、个人创意实现等领域。
2.激光固化(SLA)。
激光固化是在一个坐标轴上利用光线照射重合的区域,使树脂附着并实现固化。
物体制成可以在树脂中自由形成。
能够制造复杂的、内部细节丰富的产品,但制造速度慢,成本高。
3.粉末复合(SLS)。
SLS技术需要使用粉末材料制成原形模型,然后利用激光扫描,经过热熔不断附着形成实体。
SLS技术因为用材相对较广,制作出来的成品非常灵活,可以做到精细的物件。
除此之外,3D打印还可以应用到较高的可视化水平和高精度的材料开发。
一些模具、高复杂度的建筑和大琴等都离不开3D打印技术。
比如医疗方面,在手术之前,在3D打印技术的帮助下,医生可以先打印一个复刻体进行测试,以提高手术的效率,减小手术的风险。
在航空、军工、能源等行业,3D打印技术可以减少零件的制作成本和时间,并可以制造出更耐用的部件。
总之,3D打印技术的发展方向聚焦于更高的速度、更广泛的材料选择、更精确的产品完善,以及人体器官、机械设备和安全用品、自然生物等多个领域的应用。
二、未来3D打印技术发展的趋势1.材料多样性对于3D打印技术而言,最深层次的变化,目前在材料多样性领域里。
几乎每种材料都可以制造出某些产品,包括金属、橡胶和聚合物等。
因此,了解材料特性对于选择最优材料也是非常重要的。
对于3D 打印材料和纳米技术的革新,他们研究各种材料,为每种材料树立各自的应用需求,以满足每个作品的更多定制化。
3d打印的现状及应用前景

3d打印的现状及应用前景3D打印技术是一种以数字模型为基础,通过逐层堆积材料的方式制造物体的新兴技术。
它凭借其快速、低成本、高自由度等优势,进一步改变了传统制造业的格局,被广泛应用于多个领域。
本文将对3D打印的现状和应用前景进行探讨。
一、3D打印的现状1. 技术成熟度:随着3D打印技术的持续发展和工业的普及,3D打印设备、材料和软件等方面都取得了长足的进步。
目前,3D打印技术在快速原型制作、个性化产品定制等领域已经比较成熟,并逐渐向大批量生产和高精度应用拓展。
2. 应用广泛化:3D打印技术不仅适用于传统的制造行业,如航空航天、汽车、医疗器械等,还可以应用于建筑、文化创意、消费品等领域。
例如,3D打印技术可以用于制造复杂的几何结构和薄壁结构,提高产品的性能和效率。
3. 成本下降:随着3D打印技术的发展,打印设备和材料的成本逐渐下降,使得小企业和个人也能够使用3D打印技术。
这降低了产品开发和制造的门槛,促进了创新和创业的活力。
4. 打印材料的多样性:3D打印技术可以使用多种材料,如塑料、金属、陶瓷、复合材料等。
随着材料研发的不断进步,打印出的产品在强度、耐磨性、导热性等方面的性能也得到了提升。
5. 法律和标准的建立:随着3D打印技术的广泛应用,相关的法律和标准也在逐步建立。
这些法律和标准将规范3D打印的行为和产出,保护知识产权,维护市场秩序。
二、3D打印的应用前景1. 制造业变革:3D打印技术可以实现个性化、定制化生产,有效降低产品开发和制造的成本和周期。
它将促使传统制造业转型升级,提高产品的差异化竞争能力。
2. 医疗领域:3D打印技术可应用于医疗器械、人体组织器官等领域。
它可以制造高度定制化的假肢、义肢和矫形器材,帮助残障人士恢复功能。
同时,利用3D打印技术还可以生产复杂的人体器官模型,为手术前的诊断和手术操作提供支持。
3. 文化创意产业:3D打印技术可以帮助艺术家和设计师创造出更加独特、复杂的艺术品和设计作品。
我国3D打印技术的现状与未来发展趋势分析
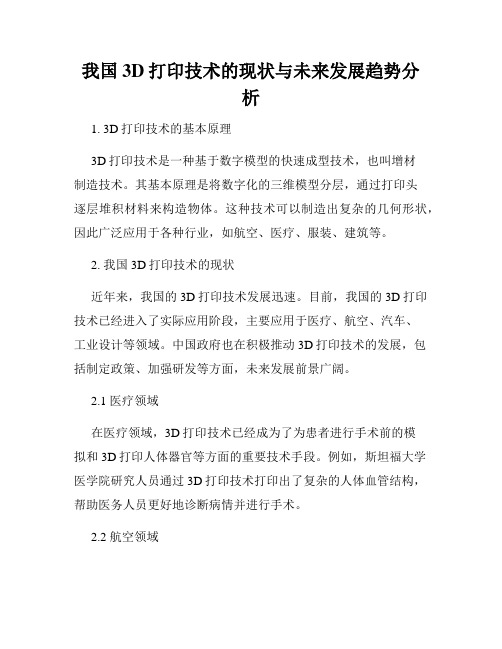
我国3D打印技术的现状与未来发展趋势分析1. 3D打印技术的基本原理3D打印技术是一种基于数字模型的快速成型技术,也叫增材制造技术。
其基本原理是将数字化的三维模型分层,通过打印头逐层堆积材料来构造物体。
这种技术可以制造出复杂的几何形状,因此广泛应用于各种行业,如航空、医疗、服装、建筑等。
2. 我国3D打印技术的现状近年来,我国的3D打印技术发展迅速。
目前,我国的3D打印技术已经进入了实际应用阶段,主要应用于医疗、航空、汽车、工业设计等领域。
中国政府也在积极推动3D打印技术的发展,包括制定政策、加强研发等方面,未来发展前景广阔。
2.1 医疗领域在医疗领域,3D打印技术已经成为了为患者进行手术前的模拟和3D打印人体器官等方面的重要技术手段。
例如,斯坦福大学医学院研究人员通过3D打印技术打印出了复杂的人体血管结构,帮助医务人员更好地诊断病情并进行手术。
2.2 航空领域在航空领域,3D打印技术大幅度降低了部件生产的时间和成本,同时提高了飞机的安全性和性能。
中国商飞公司的C919客机,就采用了大量的3D打印部件,提升了飞机性能,大大缩短了设计和开发周期。
2.3 汽车领域汽车行业也是3D打印技术的主要应用领域之一,通过3D打印技术,厂商可以快速制造出汽车零部件,大大缩短了产品的研发周期,而且还能够降低成本。
例如,捷豹路虎公司通过3D打印技术制造了汽车座椅,在此基础上还进行了重新设计和优化,提升了座椅的舒适性和安全性。
3. 我国3D打印技术的未来发展趋势随着技术的不断进步和市场的推动,未来我国的3D打印技术有望在以下几个方面取得新突破。
3.1 材料多样化目前,3D打印技术使用的材料主要是塑料和金属等,而未来随着材料多样化,人们不仅可以3D打印出生活用品和工业部件,还可以制造出更加复杂的物品,如食品、医疗器械等。
3.2 大型化和智能化未来,3D打印技术有望实现大型化和智能化,使得可以制造更大、更复杂的物品,同时也能够智能地根据用户需求进行设计和制造。
3D打印技术的发展现状与前景

3D打印技术的发展现状与前景近年来,3D打印技术已经成为了各行业的热门话题。
其在设计制造、医疗、教育等领域都有着广泛的应用。
本文将就3D打印技术的发展现状与前景进行探讨。
一、3D打印技术现状3D打印技术,是一种将三维数字模型转化为实体模型的制造技术。
它的原理是将材料通过可控制的方式,逐层积累,最终形成具有特定形状的物体。
在当前,3D打印技术已经经历了数十年的发展,逐渐逐步完善。
1、快速原型技术3D打印技术最初被应用于快速原型技术。
该技术用于制造单例或小批量的产品,可以用来检验或验证新产品的设计。
通过打印出的实体模型,设计师可以在真实物理空间中进行检测和测试,使设计变得更加精确有效。
2、定制化制造3D打印技术还被用于定制化制造,特别是在医学领域。
医生可以通过3D打印技术,制作出患者的外科手术导板、义肢、牙齿以及其他医疗组件。
这种方法可以大大提高医疗器械的准确性和质量,也可以使其更加符合患者的需要。
3、大型打印近年来,3D打印技术开始向大型打印技术发展。
工程师和设计师可以打印出更大、更复杂的建筑构件,甚至可以用于打印大型的工业零部件。
目前,3D打印技术可以应用于各种材料,包括塑料、金属、生物材料、陶瓷等多种材料。
二、3D打印技术前景1、节约成本3D打印技术未来的主要应用之一是节约成本。
它可以用于在研究和开发阶段制造原型,也可以用于制造维修零件和成品。
这种方法可以减少物流和储存成本,减少浪费,减少生产所需的时间。
由于各种材料可以被回收重复使用,也节约了制造成本。
2、推动医疗技术进步3D打印技术还可以推动医疗技术的进步。
医生可以根据患者的身体情况和需要,制作出特定的医疗器械和组件。
这不仅可以提高医疗器械的准确性和质量,也可以促进新型医疗器械和治疗方案的发展,并为研究和开发带来更多机会。
3、创建更具体体验的产品3D打印技术还可以用于创建更具特定体验的产品。
通过制造个性化产品和组件,可以为客户提供更好的用户体验。
3D打印技术的发展现状和未来应用展望分析
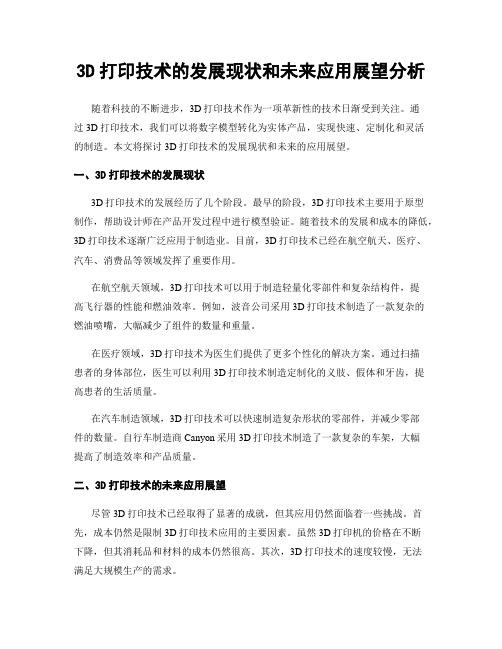
3D打印技术的发展现状和未来应用展望分析随着科技的不断进步,3D打印技术作为一项革新性的技术日渐受到关注。
通过3D打印技术,我们可以将数字模型转化为实体产品,实现快速、定制化和灵活的制造。
本文将探讨3D打印技术的发展现状和未来的应用展望。
一、3D打印技术的发展现状3D打印技术的发展经历了几个阶段。
最早的阶段,3D打印技术主要用于原型制作,帮助设计师在产品开发过程中进行模型验证。
随着技术的发展和成本的降低,3D打印技术逐渐广泛应用于制造业。
目前,3D打印技术已经在航空航天、医疗、汽车、消费品等领域发挥了重要作用。
在航空航天领域,3D打印技术可以用于制造轻量化零部件和复杂结构件,提高飞行器的性能和燃油效率。
例如,波音公司采用3D打印技术制造了一款复杂的燃油喷嘴,大幅减少了组件的数量和重量。
在医疗领域,3D打印技术为医生们提供了更多个性化的解决方案。
通过扫描患者的身体部位,医生可以利用3D打印技术制造定制化的义肢、假体和牙齿,提高患者的生活质量。
在汽车制造领域,3D打印技术可以快速制造复杂形状的零部件,并减少零部件的数量。
自行车制造商Canyon采用3D打印技术制造了一款复杂的车架,大幅提高了制造效率和产品质量。
二、3D打印技术的未来应用展望尽管3D打印技术已经取得了显著的成就,但其应用仍然面临着一些挑战。
首先,成本仍然是限制3D打印技术应用的主要因素。
虽然3D打印机的价格在不断下降,但其消耗品和材料的成本仍然很高。
其次,3D打印技术的速度较慢,无法满足大规模生产的需求。
然而,随着技术的不断进步,这些挑战将逐渐被克服。
首先,随着技术的成熟和竞争的加剧,3D打印机的价格将进一步降低,从而更多企业能够承担起这项技术。
其次,随着材料科学的进步,打印材料的成本也会逐渐降低,更多的材料也会被开发出来。
此外,研究机构和企业正在寻找新的3D打印技术和材料,以提高打印速度。
未来,3D打印技术将在各个领域得到更广阔的应用。
3D打印技术发展现状与未来趋势分析
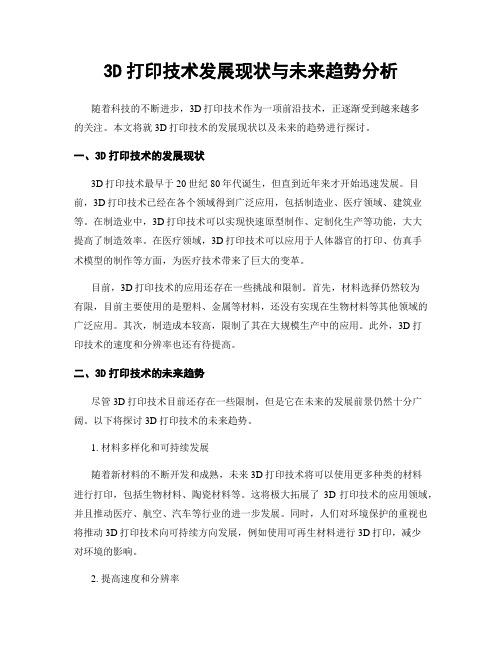
3D打印技术发展现状与未来趋势分析随着科技的不断进步,3D打印技术作为一项前沿技术,正逐渐受到越来越多的关注。
本文将就3D打印技术的发展现状以及未来的趋势进行探讨。
一、3D打印技术的发展现状3D打印技术最早于20世纪80年代诞生,但直到近年来才开始迅速发展。
目前,3D打印技术已经在各个领域得到广泛应用,包括制造业、医疗领域、建筑业等。
在制造业中,3D打印技术可以实现快速原型制作、定制化生产等功能,大大提高了制造效率。
在医疗领域,3D打印技术可以应用于人体器官的打印、仿真手术模型的制作等方面,为医疗技术带来了巨大的变革。
目前,3D打印技术的应用还存在一些挑战和限制。
首先,材料选择仍然较为有限,目前主要使用的是塑料、金属等材料,还没有实现在生物材料等其他领域的广泛应用。
其次,制造成本较高,限制了其在大规模生产中的应用。
此外,3D打印技术的速度和分辨率也还有待提高。
二、3D打印技术的未来趋势尽管3D打印技术目前还存在一些限制,但是它在未来的发展前景仍然十分广阔。
以下将探讨3D打印技术的未来趋势。
1. 材料多样化和可持续发展随着新材料的不断开发和成熟,未来3D打印技术将可以使用更多种类的材料进行打印,包括生物材料、陶瓷材料等。
这将极大拓展了3D打印技术的应用领域,并且推动医疗、航空、汽车等行业的进一步发展。
同时,人们对环境保护的重视也将推动3D打印技术向可持续方向发展,例如使用可再生材料进行3D打印,减少对环境的影响。
2. 提高速度和分辨率目前,3D打印技术的速度和分辨率还有待提高。
未来,随着技术的进步,3D打印设备将能够更快速地完成打印任务,并且能够更精细地打印出细小的结构。
这将使得3D打印技术在更多领域有更广泛的应用,例如微电子器件制造、微创外科手术等。
3. 集成多种技术未来的3D打印技术将会与其他技术进行集成,形成更强大的创新力量。
例如,与人工智能、大数据、虚拟现实等技术的结合,将进一步提高3D打印技术在设计、制造过程中的智能化水平,为用户提供更好的体验和更高效的解决方案。
3D打印技术的发展现状和前景

3D打印技术的发展现状和前景自从3D打印技术被发明以来,它就在不断地发展和创新。
从最开始的手动操作到程序自动化控制,3D打印技术已经取得了巨大的发展进步。
目前,3D打印技术已被广泛应用在各种不同的领域,并且在未来还有着更广泛的应用前景。
一、3D打印技术的现状在当前的产业界,3D打印技术已经成为一项综合性的技术,并且被广泛应用在各种行业领域。
其中,3D打印技术在航空航天、医疗、教育、汽车工业、消费品制造和艺术设计等领域有比较广泛的应用场景。
其中,医疗领域是其最重要的应用领域之一。
医疗科技公司正在使用3D打印技术生产仿制身体组织、骨骼和器官。
随着技术的不断进步,3D打印还被用于生产高质量的牙齿、卡片和人造植入物,为医疗行业带来了变革性的机会。
二、3D打印的优势和劣势3D打印技术的长处在于其可定制性和灵活性。
它可以生产形态复杂的物品,包括几何形状规则的物品和异形物品。
此外,使用3D打印技术可以简化生产或制造流程,因为可以将几个部件组合在一起。
但是,3D打印技术也存在一些劣势。
其生产速度通常比传统方法慢,并且使用的材料往往比传统制造方法更昂贵。
此外,3D打印技术的可操作性还存在一定的限制。
三、3D打印技术的未来前景未来,3D打印技术将会继续发展壮大。
当前,许多3D打印公司正致力于将3D打印应用于医疗行业,包括生产可定制的人工肢体和器官。
此外,3D打印技术还可以用于生产零件和部件,以及制造可持续的产品。
但是,3D打印技术的广泛应用还需要克服一些限制。
其中,3D打印技术的成本和打印速度方面是其关键限制之一。
此外,3D打印技术还需要克服材料选择方面的限制。
如果我们能克服这些限制,那么3D打印技术在未来有机会成为一项更普遍的生产方法,并为国家和企业带来经济利益。
四、结论尽管3D打印技术还存在一些问题和限制,但它依然在未来拥有广泛的应用前景。
未来,无论是在医疗、制造、艺术设计或其他领域,3D打印技术都有可能为我们带来更多的机遇和可能性。
3D打印技术发展现状与未来趋势分析

3D打印技术发展现状与未来趋势分析引言随着科技的不断进步和创新,3D打印技术作为一种革命性的制造方式,正逐渐改变着我们的生活和工业领域。
本文将探讨3D打印技术的发展现状,并分析其未来发展趋势。
一、3D打印技术的发展现状1. 技术成熟度提高3D打印技术自问世以来,经历了多年的发展和完善,现如今已经成为一种相对成熟的制造工艺。
从最初只能打印简单的原型模型到现在可以打印出复杂的功能件和机械部件,3D打印技术已经走过了一段漫长的发展道路。
2. 应用领域不断扩展最初,3D打印技术主要应用于工业设计领域,如制造原型和小批量定制产品。
如今,它已经涉足医疗、建筑、汽车、航空航天等多个领域。
例如,医疗领域的3D打印技术已经用于打印人体器官、牙齿、骨骼等,成为一种重要的医疗手段。
3. 材料选择不断丰富3D打印技术的另一个重要发展是在可用材料选择上的增加。
最初,主要使用的是塑料材料,现如今,金属、陶瓷、纤维等多种材料也被广泛应用于3D打印中。
这使得打印出来的产品性能和质量得以大幅提升。
二、未来趋势分析1. 制造业颠覆随着3D打印技术的日渐成熟,传统制造业将面临巨大的挑战。
传统制造方式通常需要耗费大量的人力和资源,并且产能有限。
而采用3D打印技术可以实现定制化生产,缩短生产周期,并且减少能耗和废物产生。
这将对传统制造业产生颠覆性的影响。
2. 科技与艺术的结合随着3D打印技术的不断进步,人们将更加关注其与艺术的结合。
通过3D 打印技术,艺术家可以设计和打印出更加独特和复杂的艺术作品,从而突破传统的创作界限。
3. 3D打印技术的个人化应用在未来,3D打印技术有望进一步普及,呈现出个人化的应用趋势。
普通消费者将能够利用3D打印机打印出自己需要的产品,如个性化的家居用品、服装和配件等。
这将进一步满足个人需求,推动消费市场的发展。
4. 生物3D打印技术的发展同时,生物3D打印技术也是未来的发展方向。
通过使用细胞和生物材料,可以实现打印出人体组织和器官的目标。
3D打印技术发展现状及趋势分析

3D打印技术发展现状及趋势分析3D打印技术是一种快速增长的制造技术,它利用数字化设计文件直接制造出三维实体物体。
随着技术的不断创新和发展,3D打印技术在各个领域都有着广阔的应用前景。
从工业制造到医疗保健,从航空航天到建筑设计,3D打印技术都能够发挥重要作用。
本文将对3D打印技术的发展现状及未来趋势进行分析。
一、3D打印技术的发展现状1. 技术成熟度目前,3D打印技术已经进入了成熟阶段,各种类型的3D打印设备已经在工业、医疗、教育等领域得到广泛应用。
从传统的尼龙及ABS等材料,到最新的金属和生物材料,3D打印技术的材料种类也不断丰富,满足了不同行业的需求。
2. 应用领域在工业制造领域,3D打印技术可以实现定制化生产,大大缩短产品的研发周期和成本。
在医疗保健领域,医生可以根据患者的具体情况定制医疗器械和假体,提高治疗效果。
在航空航天领域,3D打印技术可以制造复杂结构的零部件,提高飞机的性能和安全性。
3. 创新应用除了传统的材料制造,3D打印技术还被应用于建筑设计、食品制造、纺织品制造等领域。
在建筑领域,研究人员已经成功用3D打印技术制造出了一些建筑物的结构,并且建筑速度相较传统的建筑方式有了大幅度的提高。
在食品制造领域,3D打印技术可以将食材直接制成各种形状的食品,增加了食品的设计性和趣味性。
二、3D打印技术的未来趋势1. 个性化定制随着人们对个性化需求的不断增加,定制化生产将成为3D打印技术的重要发展趋势。
无论是个人消费品还是工业制造品,都可以通过3D打印技术实现定制化生产,满足消费者的个性化需求。
2. 多材料打印目前,3D打印技术主要应用于单一材料的制造,随着材料科学的不断进步,未来3D打印技术将可以实现多种材料的组合打印,提高产品的功能性和质量。
3. 生物打印生物打印是一种利用细胞和生物材料制造组织和器官的技术,它将是未来3D打印技术的重要发展方向。
通过生物打印技术,医生可以根据患者的具体情况制造出合适的人工器官,解决器官移植的瓶颈问题。
3D打印技术发展现状与未来趋势

3D打印技术发展现状与未来趋势随着科技的不断进步和日新月异的创新,各行业都在不断寻找新的突破和发展机会。
而3D打印技术作为一项颠覆性的技术,正在改变着各个行业的生产方式和模式。
本文将探讨3D打印技术的现状以及未来的发展趋势。
一、3D打印技术的现状3D打印技术最早出现于20世纪80年代,但直到近年来才逐渐为人所熟知和应用。
目前,3D打印技术已经被广泛应用于诸多领域,包括医疗、汽车、航空航天、制造业等。
在医疗领域,3D打印技术已经成功应用于个性化医疗器械、人体器官的重建以及手术模拟等方面。
在汽车制造领域,3D打印技术可以实现快速、精准地制造零部件,提高生产效率和产品质量。
在航空航天领域,3D打印技术可以打印出复杂的结构件,减轻了航空器的重量,提高了飞行性能。
然而,目前的3D打印技术还存在一些限制和挑战。
首先是打印速度较慢,尤其在打印大型复杂零部件时,时间成本较高。
其次是材料选择受限,目前可用的3D打印材料种类有限,无法满足一些特殊需求。
再次是设备成本较高,对于一些中小企业来说,经济实力有限。
这些问题使得3D打印技术在某些行业中应用受到限制。
二、3D打印技术的未来趋势尽管存在一些问题,但随着科技的进步和研究的深入,3D打印技术有着广阔的发展前景。
首先,打印速度将会得到提升。
目前,研究人员正在致力于开发更快速的3D打印技术,以满足大规模生产的需求。
利用高效的打印头和更快的打印方法,打印速度将会得到显著提升。
其次,材料选择将会更加丰富。
随着材料科学的发展,研究人员正在不断开发出适用于3D打印的新材料。
例如,金属3D打印技术已经取得了重大突破,可以打印出金属零件,扩大了应用领域。
此外,生物材料和可降解材料的研究也在不断推进,有望在医疗领域实现更多的应用。
再次,设备成本将会逐渐下降。
随着3D打印技术的普及和市场竞争的加剧,设备价格将会逐渐降低。
这将使得更多的中小企业能够负担得起3D打印设备,推动技术在各个行业中的广泛应用。
3D打印技术的发展现状及未来趋势分析

3D打印技术的发展现状及未来趋势分析引言:自从3D打印技术问世以来,它已经在各个领域引起了巨大的变革。
从最初的概念和原型打印到如今的生物医学和航天工业,3D打印已成为一项独具特色的技术。
本文将就3D打印技术的发展现状及未来趋势进行全面分析。
一、3D打印技术的发展现状1.技术成熟度的提高随着科技的不断进步和创新,3D打印技术逐渐成熟起来。
现代3D打印机的精度和打印速度大大提高,使其成为一种可行的生产方式。
此外,3D打印材料的种类也越来越多,包括塑料、金属、陶瓷等。
这些进步使得3D 打印技术在各行各业中得以应用。
2.应用领域的广泛拓展3D打印技术已经逐渐渗透到更多的应用领域。
例如,医学领域的3D打印技术已经可以打印出人体器官和假肢等医疗器械。
建筑和制造业也可以使用3D打印机打印出建筑模型和工业零件等。
此外,文化艺术领域也开始运用3D打印技术来制作雕塑和艺术品等。
3.成本的下降最初的3D打印机价格高昂,限制了其广泛应用。
然而,随着技术的发展和市场竞争的加剧,3D打印机的价格逐渐下降。
这使得中小型企业和个人也可以使用3D打印机,推动了3D打印技术的进一步普及。
二、3D打印技术的未来趋势分析1.大规模生产随着3D打印技术的不断发展和成熟,它有望实现大规模生产。
传统制造业的生产线可能会被3D打印机所取代,因为3D打印可以提高生产效率和灵活性。
未来,我们可能会看到更多的工业品和消费品经由3D打印机量产。
2.材料的多样性目前的3D打印材料主要集中在塑料、金属和陶瓷等几种基础材料上。
然而,随着技术的进一步发展,我们可以预见到更多材料的应用,例如生物材料、纳米材料和复合材料等。
这将使得3D打印技术的应用领域更加广泛。
3.个性化定制3D打印技术的突出优势之一是可以实现个性化定制。
未来,我们可能会看到更多的消费品和医疗器械通过3D打印来满足个人需求。
人们可以根据自己的喜好和需求定制产品,这将带来更多的创意和多样性。
4.生物医学的进一步发展3D打印技术在生物医学领域的应用前景广阔。
3D打印技术的现状和发展趋势

3D打印技术的现状和发展趋势3D打印技术是一项颠覆性的技术,它将互联网、数字化、自动化等多种关键技术融合在一起,可实现快速、准确、灵活地制造物品。
自从1980年代诞生以来,3D打印技术不断发展壮大,已经被广泛应用于生产制造、医疗、文化创意等领域,并拥有了日益充实的应用生态。
本文将从当前3D打印技术的现状、应用场景和发展趋势三个方面探讨其发展的概况。
一、3D打印技术现状3D打印技术是一种利用数字数据通过直接制造物品的快速工艺,也称快速成形技术。
它通过输入数字化模型,将三维模型分层后逐层制造成实体模型,层层堆积最后形成所需物品。
这一过程与传统制造工艺不同,不需要复杂的制造设备,也没有复杂的制造程序,避免了传统制造工艺的许多限制,同时还节省了大量的原材料、时间和人力资源。
3D打印技术的现状主要体现在以下几个方面:1.技术水平:目前,3D打印技术已经非常成熟,涉及的技术领域很广,涵盖了多种技术和工艺,包括喷墨、喷粉、聚合、生长等多种类型。
此外,随着3D打印技术的方法学不断进一步深入,相关的软件设计和机器控制技术也越来越先进。
2.应用领域:当前,3D打印技术已经开始在工业、医疗、文化创意等领域得到广泛应用。
在工业应用方面,3D打印机可以制造出各种模具和零件,以及机器人和空间探测器等,为航空、汽车、船舶、军事等领域提供了不少便利。
在医疗领域,3D打印技术可用于制造人工关节、骨骼和牙齿等,也可用于生物材料和医药等研发,为临床医学带来了飞跃的进展。
在文化创意领域,3D打印技术可以制造出各种小雕像、文化艺术品、游戏工具等,为文化创意产业带来了创新的可能性。
3.市场状况:2019年,全球3D打印市场规模为109.3亿美元。
未来几年,3D打印技术的市场规模将继续增长。
根据市场研究公司IDC发布的《全球3D打印之旅》报告预测,到2024年,全球3D打印市场规模将达到360亿美元,年均复合增长率为25.8%。
二、3D打印技术应用场景3D打印技术在工业、医疗、文化创意等领域得到了广泛应用。
3D打印技术的发展现状及前景分析
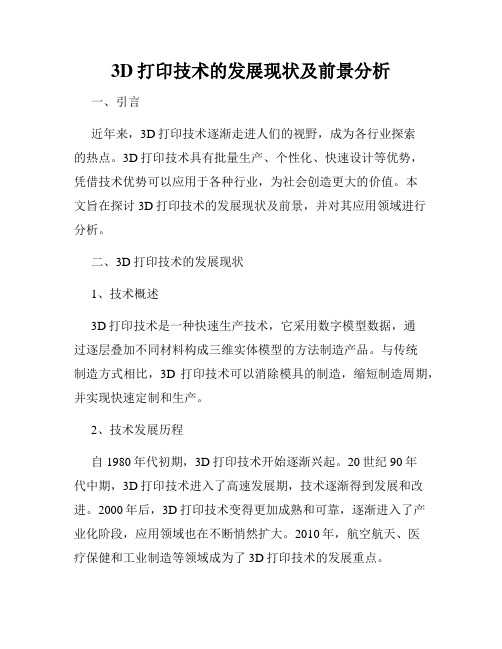
3D打印技术的发展现状及前景分析一、引言近年来,3D打印技术逐渐走进人们的视野,成为各行业探索的热点。
3D打印技术具有批量生产、个性化、快速设计等优势,凭借技术优势可以应用于各种行业,为社会创造更大的价值。
本文旨在探讨3D打印技术的发展现状及前景,并对其应用领域进行分析。
二、3D打印技术的发展现状1、技术概述3D打印技术是一种快速生产技术,它采用数字模型数据,通过逐层叠加不同材料构成三维实体模型的方法制造产品。
与传统制造方式相比,3D打印技术可以消除模具的制造,缩短制造周期,并实现快速定制和生产。
2、技术发展历程自1980年代初期,3D打印技术开始逐渐兴起。
20世纪90年代中期,3D打印技术进入了高速发展期,技术逐渐得到发展和改进。
2000年后,3D打印技术变得更加成熟和可靠,逐渐进入了产业化阶段,应用领域也在不断悄然扩大。
2010年,航空航天、医疗保健和工业制造等领域成为了3D打印技术的发展重点。
3、技术应用3D打印技术可以应用于众多领域,使传统制造方式得到优化和改进。
目前,3D打印技术已经在生产制造、工业设计、医疗保健、教育科研、文化创意等领域得到成熟应用。
(1)生产制造3D打印技术可以实现快速定制、批量生产和高效制造。
例如,某些制造厂商已经开始使用3D打印技术在生产线上制造零部件,加速生产周期和提高产品质量。
(2)工业设计3D打印技术可以优化产品设计和生产过程,提高效率和质量。
例如,汽车、航空航天领域可以在3D打印技术的基础上定制零部件,修正及时、精细化。
(3)医疗保健3D打印技术可以应用于医疗保健领域,例如生产手术工具和医疗设备。
该技术还可以用于生产假肢、人体组织和器官等。
全球很多医疗机构正通过3D打印技术改变患者的生命。
(4)教育科研3D打印技术可以用于教育教学和科学研究,帮助学生和研究人员更好地理解和研究物理原理。
例如,新型教学课件可以使用3D打印模型来展示物体的空间结构和功能特点。
3d打印国内外发展现状
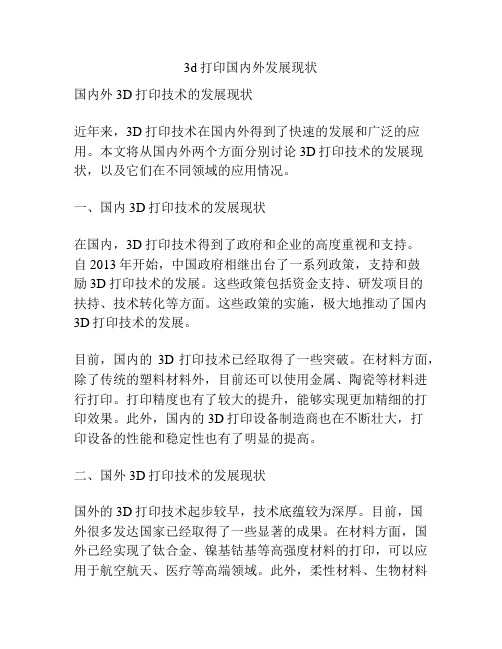
3d打印国内外发展现状国内外3D打印技术的发展现状近年来,3D打印技术在国内外得到了快速的发展和广泛的应用。
本文将从国内外两个方面分别讨论3D打印技术的发展现状,以及它们在不同领域的应用情况。
一、国内3D打印技术的发展现状在国内,3D打印技术得到了政府和企业的高度重视和支持。
自2013年开始,中国政府相继出台了一系列政策,支持和鼓励3D打印技术的发展。
这些政策包括资金支持、研发项目的扶持、技术转化等方面。
这些政策的实施,极大地推动了国内3D打印技术的发展。
目前,国内的3D打印技术已经取得了一些突破。
在材料方面,除了传统的塑料材料外,目前还可以使用金属、陶瓷等材料进行打印。
打印精度也有了较大的提升,能够实现更加精细的打印效果。
此外,国内的3D打印设备制造商也在不断壮大,打印设备的性能和稳定性也有了明显的提高。
二、国外3D打印技术的发展现状国外的3D打印技术起步较早,技术底蕴较为深厚。
目前,国外很多发达国家已经取得了一些显著的成果。
在材料方面,国外已经实现了钛合金、镍基钴基等高强度材料的打印,可以应用于航空航天、医疗等高端领域。
此外,柔性材料、生物材料等领域的打印技术也得到了较大的突破。
在应用方面,国外的3D打印技术已经在多个领域得到了广泛的应用。
例如,在航空航天领域,国外已经成功打印出一些关键零部件,如燃气轮机的涡轮叶片、火箭发动机的燃烧室等。
在医疗领域,3D打印技术可以制造出与患者个体化匹配的假肢、种植物等医疗器械。
此外,3D打印技术还广泛应用于汽车制造、建筑业等众多领域。
总结综上所述,国内外的3D打印技术都取得了较大的发展和突破。
虽然国内与国外在技术水平和应用领域上还存在一定差距,但无论是国内还是国外,3D打印技术都显现出了巨大的潜力和广阔的应用前景。
未来,3D打印技术有望在制造业、医疗领域等方面发挥更加重要的作用。
- 1、下载文档前请自行甄别文档内容的完整性,平台不提供额外的编辑、内容补充、找答案等附加服务。
- 2、"仅部分预览"的文档,不可在线预览部分如存在完整性等问题,可反馈申请退款(可完整预览的文档不适用该条件!)。
- 3、如文档侵犯您的权益,请联系客服反馈,我们会尽快为您处理(人工客服工作时间:9:00-18:30)。
我国3D打印技术发展现状及环境分析摘要:3D打印技术已获得迅速发展,并受到世界各国广泛关注,基于目前3D 打印技术发展的现实情况,着重分析我国3D打印技术发展现状以及面临的环境条件,并提出我国3D打印技术发展与应用的对策建议,以便为我国抢抓3D打印技术发展机遇提供重要技术支撑。
近年来,3D打印技术获得迅速发展,并受到世界各国的广泛关注,美国科学家将3D打印产业列为“美国十大增长最快的工业”之一,有的甚至期望3D打印这种神奇的技术能带来“第三次工业革命”[1][2]。
军事强国加大技术研发力度,3D 打印技术成熟度及性能不断提升,3D打印精度和速度不断提高,打印成本越来越低,打印原材料更加丰富;主要国家积极探索3D打印技术在武器装备设计、制造和维修保障中的应用,已经通过3D打印技术成功“打印”出手枪;美军应用3D打印技术,辅助研制了导弹用的弹出式点火器模型;美国GE集团已应用3D 打印技术制造喷气发动机[3]。
随着世界各国不断加大对3D打印技术的研发与投入,我国也开始高度重视3D打印技术发展与应用,已持续加大对3D打印技术支持,在若干关键技术方向取得了重要突破,在多个领域的应用取得重要进展,3D打印技术发展的支撑环境条件更加完善。
一、我国3D打印技术发展现状我国3D打印技术发展与发达国家相比,虽然在技术标准、技术水平、产业规模和产业链方面还存在大量有待改进和发展的地方,但经过多年的发展,已形成以高校为主体的技术研发力量布局,若干关键技术取得重要突破,产业发展开始起步,形成了小规模产业市场,并在多个领域成功应用,为下一步发展奠定了良好基础。
(一)初步建立以高校为主体的技术研发力量体系自上世纪90年代初开始,航空航天大学、西北工业大学、华中科技大学、交通大学、清华大学等高校相继开展了3D打印技术研究,成为我国开展3D打印技术的主要力量,推动了我国3D打印技术的整体发展。
航空航天大学“大型整体金属构件激光直接制造”教育部工程研究中心的王华明团队,西北工业大学凝固技术国家重点实验室的黄卫东团队主要开展金属材料激光净成形直接制造技术研究。
清华大学生物制造与快速成形技术市重点实验室颜永年团队主要开展熔融沉积制造技术、电子束融化技术、3D生物打印技术研究。
华中科技大学材料成形与模具技术国家重点实验室史玉升团队主要从事塑性成形制造技术与装备、快速成形制造技术与装备、快速三维测量技术与装备等静压近净成形技术研究。
交通大学制造系统工程国家重点实验室,以及快速制造技术及装备国家工程研究中心的卢秉恒院士团队主要从事高分子材料光固化3D打印技术及装备研究。
[4] (二)整体实力不断提升,金属3D打印技术世界领先我国增材制造技术从零起步,在广大科技人员的共同努力下,技术整体实力不断提升,在3D打印的主要技术领域都开展了研究,取得一大批重要的研究成果,特别是在高性能金属零件激光直接成形技术方面取得重大突破,技术水平达到世界领先。
高性能金属零件激光直接成形技术世界领先,攻克了金属材料3D打印的变形、翘曲、开裂等关键问题,成为首个利用选择性激光烧结(SLS)技术制造大型金属零部件的国家。
航空航天大学已掌握使用激光快速成形技术制造超过12平方米的复杂钛合金构件。
西北工业大学的激光立体成形技术可一次打印超过5米的钛金属飞机部件,构件的综合性能达到或超过锻件。
航空航天大学和西北工业大学的高性能金属零件激光直接成形技术已成功应用于制造我国自主研发的大型客机C919的主风挡窗框、大中央翼根肋,以及正在设计的第五代战斗机的钛合金主体结构,成功降低了飞机的结构重量,提高了战机的推重比,缩短了设计时间[5]。
(三)产业化进程加快,初步形成小规模产业市场利用高校、科研院所的研究成果,依托相关技术研究机构,我国已涌现出20多家增材制造设备与服务企业。
隆源自动成型系统,1993年开始研发选区粉末烧结激光快速成型机并取得自主知识产权,广泛应用于航空航天、船舶兵器等行业的设计试制部门;太尔时代科技自主研发了拥有完全自主知识产权的控制系统、机械系统、打印材料等3D打印机核心技术;紫金立德公司专业从事3D打印机及其耗材的开发、生产、销售,并提供相关服务;铂力特激光成形技术是激光快速成形技术的产业化公司,公司产品已在国家多项重点型号研制和生产过程中得到应用,如应用于C919大型商用客机中央翼身缘条钛合金构件的制造,是目前国金属3D打印技术领先者;滨湖机电技术产业主要生产LOM、SLA、SLS、SLM 系列产品并进行技术服务和咨询,1994年就成功开发出我国第一台快速成型装备-薄材叠层快速成形系统,开发生产的大型激光快速制造装备具有国际领先水平,2013年,成功开发出全球首台工作台面1.4m*1.4m的四振镜激光器选择性激光粉末烧结装备,标志着其粉末烧结技术达到国际领先水平。
据中国3D打印技术产业联盟数据,2012年,我国3D打印市场规模约为10亿元,2013年翻一翻达到20亿元,2014年达到50亿元[6]。
未来几年,中国3D打印市场每年将至少以1倍以上的速度成长,规模或达百亿元。
(四)应用取得突破,在多个领域显示了良好的发展前景随着关键技术的不断突破,以及产业的稳步发展,我国3D打印技术的应用也取得较好进展,已成功应用于设计、制造、维修等产品全寿命周期。
一是在设计阶段,已成功将3D打印技术广泛应用于概念设计、原型制作、产品评审、功能验证等,显著缩短了设计时间,节约了研制经费。
在研制歼-15、歼-16和歼-31等战斗机过程中,利用金属3D打印快速制造钛合金主体结构,在一年之连续组装出多款飞机进行飞行实验,显著缩短了研制时间[7]。
运-20在做首飞前的静力试验时发现起落架连接部位一个很复杂的结构件出了问题,需要更换材料,重新加工。
采用3D打印技术,在很短的时间生产出了需要的部件,保证了试验如期进行。
二是在制造领域,已将3D打印技术应用于飞机紧密部件和大型复杂结构件制造。
我国国产大型客机C919的中央翼根肋、主风挡窗框都采用3D打印技术制造,显著降低了成本,节约了时间。
C919主风挡窗框若采用传统工艺制造,国制造能力尚无法满足,必须向国外订购,时间至少需要2年,模具费需要1300万元。
采用激光快速成形3D打印技术制造,时间缩短到2个月,成本降低到120万元。
三是在维修保障领域,3D打印技术已成功应用于飞机部件维修。
当前,我国已将3D打印技术应用于制造过程中报废和使用过程中受损的航空发动机叶片的修复,以及大型齿轮的修复。
以大型舰船伴随保障为背景的3D打印技术973项目成功立项,将对3D打印应用于伴随保障的重大基础问题进行研究。
二、我国3D打印技术发展面临的环境随着技术的不断发展及广泛应用,3D打印技术受到越来越多的重视,我国3D 打印技术发展的机遇和挑战并存。
(一)我国已对3D打印技术高度重视与大力支持,为3D打印技术发展提供了有力的政策支撑环境当前,我国正大力推进经济发展模式转型,高端制造业成为工业发展的重要方向,3D打印已经开始受到国家的高度重视,3D打印技术发展已被提升到国家战略层面,有关部门正在制定支持3D打印产业发展的专项政策。
2013年国庆前夕,中共中央政治局以实施创新驱动发展战略为主题开展第九次集体学习,学习期间,中央领导专门考察了中关村与3D打印相关的研发和生产企业,表明我国上层开始重视3D打印技术的发展。
科技部最新制定的《国家高技术研究发展计划》、《国家科技支撑计划制造领域2014年度备选项目征集指南》中,也明确提出系列支持3D打印技术发展的政策,提出把“3D打印关键技术、装备研制聚焦航空航天、模具领域的需求”作为重点研究,力求突破3D打印制造技术中的核心关键技术。
此外,国家在《2013年产业振兴和技术改造专项重点专题》,《中华人民国国民经济和社会发展第十二个五年规划纲要》,《国务院关于印发工业转型升级规划(2011-2015年)》,《国务院关于加快培育和发展战略性新兴产业的决定》,《高端装备制造业“十二五”发展规划》等文件中,都提出要加大对3D打印技术的支持力度。
随着党和国家的高度重视,必将带动全社会对3D打印技术的重视,政府和企业对3D打印技术的研发投入也必将大幅增长,为我国3D 打印技术的发展提供良好的条件,吸引越来越多的科技工作者投身于3D打印技术的研究,快速攻克制约3D打印技术发展的技术瓶颈,为我国3D打印技术的发展提供不竭的动力。
(二)我国已具备良好的技术基础,为3D打印技术发展与应用奠定了坚实的基础经过多年的发展,我国的3D打印技术已具备较好的基础。
世界上,3D打印技术仍处在技术发展初期,我国与技术先进国家的差距较小,为我国3D打印技术发展提供了难得的历史机遇。
从上世纪末开始3D打印技术研究,经过多年的积累,形成了一批稳定的研究机构和专家队伍,突破了一批关键技术,建成了一批重要的研究基地,创建了一批产业公司,我国3D打印技术发展已经具备赶超发达国家的技术基础。
航空航天大学、西北工业大学的金属材料激光快速成形技术攻克了长期制约金属材料3D打印的关键技术问题,成功应用于航空领域,技术水平居世界领先地位,为下一步发展奠定了技术基础。
航空航天大学、西北工业大学、华中科技大学、交通大学和中航工业航空制造工程研究所等高校和科研结构形成了一批高水平专家队伍,为下一步发展奠定了人才基础。
隆源自动成型系统、太尔时代科技,铂力特激光成形技术、华曙高科和滨湖机电技术产业等3D 打印公司形成了自己的产品特色,业务稳步增长,为3D打印技术的产业化发展奠定了产业基础。
发达国家3D打印技术仍不成熟,为我国3D打印技术留下了赶超的时间窗口。
总体上,3D打印技术仍处于技术积累期,尚有大量核心关键技术待攻克和突破,整体技术水平还有待提升,产业模式还有待拓展,相对传统高级制造业,发达国家在技术上领先幅度并不大,为我国赶超世界先进技术水平留下了机会。
(三)我军武器装备发展模式正在向自主创新转变,对3D打印技术的发展提出了迫切需求当前,新一轮工业革命已经吹响了号角,新型数字化制造特别是3D打印技术的发展为新工业革命的即将来临提供了无限遐想,我国正在按照国防和军队现代化建设“三步走”战略构想,加紧完成机械化和信息化建设双重历史任务,国防科技和武器装备的发展模式正在由跟踪模仿向自主创新转变,对3D打印技术的发展提出了迫切的需求。
3D打印技术是满足武器装备研制对快速制造需求的有效手段。
近年来,新型武器装备的研制显著提速,仅仅在航空领域就有歼-20、歼-15、歼-31、运-20等多种型号军用飞机在同步研制。
复杂武器装备研制是一个重复迭代过程,每一轮设计调整到实验都需要制造原型机,传统制造方式需要制造模具,时间长、花费多,常常造成新型武器装备研制周期长、成本高。