PCB双面板通孔镀铜工艺
PCB工艺电镀一次铜工艺介绍

PANEL PLATING PROCESS
1000
WHAT IS PULSE PLATING? Amps 0
-1000
电流以脉冲的方式输出,达到瞬间
-2000
反电解的效果,使电路板上高电流
-3000
Amps
区造成之差异减至最低。
0.5 sec 10 sec
36
PANEL PLATING PROCESS DC 与 PULSE电镀间的差异
Manganate:
Mn6+ + 4 e- Mn2+
Manganese dioxide:
Mn4+ + 2 e- Mn2+
還原劑可以為 Glyoxal, H2O2 or Hydroxylamine sulfate.
insoluble MnO2
Cu
Mn2+ (soluble)
Cu
9
DESMEAR PROCESS Neutralizer / 中和槽 :
DEBURR设备配置图:
风刀 超音波 风刀 刷磨段
水洗 高压水洗 水洗 超音波 中压 水洗
5
除胶渣(DESMEAR)
WHAT IS SMEAR?
钻孔时树脂产生高温超过Tg
值,而形成融熔状,冷却后
凝固形成胶渣。
Cu
功能 :
去除鑽孔後殘留孔內之基材膠渣 形成孔壁微粗糙度
DESMEAR基本流程:
Sweller
H O
+HNH +HNH +HNH +HNH
Positive charged conditioning polymer
10
DESMEAR PROCESS DESMEAR 后以电子显微镜观察之孔壁粗化清洁情形
PCB电镀铜锡工艺资料
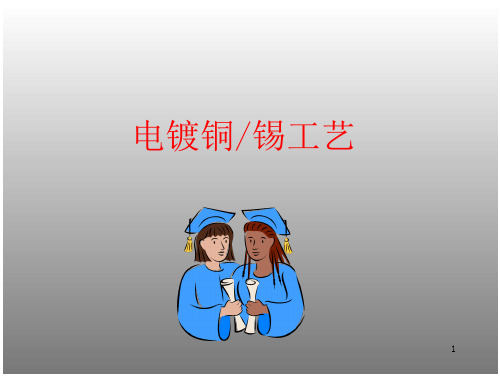
34
电镀铜溶液的控制
n 赫尔槽试验(Hull Cell Test)
n仅高电流密度区烧焦,试片的其它区域仍然正常----Copper Gleam 125T-2(CH) Additive 低 n改正方法:添加1ml/l Copper Gleam 125T-2(CH) Additive
: 濃度太低,Байду номын сангаас液導電性差,鍍液分 散能力差。
濃度太高,降低Cu2+的遷移率,電流 效率反而降低,❹對銅鍍層的延伸 率不利。
: 濃度太低,鍍層出現台階狀的粗糙 鍍層,易出現針孔和燒焦;濃度太 高,導致陽極鈍化,鍍層失去光澤 。
: (後面專題介紹)
11
操作條件對酸性鍍銅效果的影響
溫度
溫度升高,電極反應速度加快,允許電流密度提高,鍍 層沉積速度加快,但加速添加劑分解會增加添加劑消耗,鍍層結 晶粗糙,亮度降低。
31
电镀铜溶液的控制
n 赫尔槽试验 (Hull Cell Test)
阴极-
阳极+
32
电镀铜溶液的控制
n 赫尔槽试验(Hull Cell Test)参数
n — 电流: 2A n — 时间: 10分钟 n — 搅拌: 空气搅拌 n — 温度: 室温
33
电镀铜溶液的控制
n 赫尔槽试验(Hull Cell Test)
28
电镀铜溶液和电镀线的评价
n 热冲击测试
测试步骤
(1) 裁板16""x18"’ (2) 进行钻孔; (3) 经电镀前处理磨刷; (4) Desmear + PTH + 电镀; (5) 经电镀后处理的板清洗烘干; (6) 每片板裁上、中、下3小片100mm x 100mm测试板;
双面板制板流程

双面板制板流程双面板制作流程:1、打印底片或者光绘输出底片2、裁板3、钻孔4、平板机打磨(去除孔内毛刺,要保证孔通透)5、抛光6、沉铜(全自动沉铜:包含预浸与活化二种工艺)7、预浸(约5分钟,除油,除氧化物,调整电荷)8、水洗(水洗都是为除去药水残留)9、活化(约2分钟,纳米碳粒附在孔内)10、透孔11、7至11步工艺在全自动沉铜机里自动完成12、固化(100°C,5~10分钟,使碳粒在孔内附好)13、微蚀(去除覆盖在铜外表的活化液参考时间10~20s)14、镀铜(可以先加速二到四秒钟去除表面氧化物电镀。
最佳时间20分钟,电流约3A/(dm)2)15、水洗16、抛光17、刷线路油墨(较难掌握,多练习)18、烘干(75°C,10~15分钟)19、爆光(爆光时间60~80S,先对孔,用透明胶粘住打印好的菲林膜)20、显影(显影时间不易过长,参考时间30~45s)21、水洗22、烘干23、镀锡(20分钟,铜的有效面积电流约1.5A/(dm)2)24、水洗25、去膜(脱膜机脱膜,一定要用手套,去膜液为强碱性。
)26、水洗27、腐蚀(防止腐蚀过头)28、水洗29、刷阻焊油墨(阻焊油墨中加固化剂,增强固花能力)30、烘干(75°C,5~10分钟)31、爆光(180S)32、显影33、水洗34、烘干固化(150°C,30分钟)35、刷文字油墨(事先配好油墨,油墨一定要配得细腻)36、烘干(75°C,5~10分钟)38、显影固化简易流程:打底片→裁板→钻孔→抛光→(透孔)→预浸→水洗→(透孔)→预先开烘干机↓黑孔→烘干→微蚀→水洗→加速→水洗→(透孔)→镀铜→水洗→配线路油墨配显影液↓↓抛光→刷线路油墨→烘干→爆光→显影→水洗→加速→水洗→镀锡配去膜液配阻焊油墨(配比:固化剂1:油墨3)↓↓→去膜→水洗→腐蚀→水洗→刷阻焊油墨→烘干→爆光→显影配文字油墨(可用油墨稀释剂稀释)(配比:固化剂1:油墨3)↓换网→刷文字油墨→烘干→显影。
pcb双面板的工艺流程

pcb双面板的工艺流程英文回答:PCB (Printed Circuit Board) double-sided fabrication involves several steps in its manufacturing process. Here, I will outline the general process flow for producing double-sided PCBs.1. Design and Layout: The first step is to create a design and layout for the PCB using a computer-aided design (CAD) software. This involves placing components, routing traces, and creating the necessary layers for the PCB.2. Material Selection: Once the design is complete, the next step is to select the appropriate materials for the PCB. This includes choosing the substrate material (usually fiberglass-reinforced epoxy), copper foil for the conductive layers, and solder mask materials.3. Substrate Preparation: The substrate material is cutinto the desired size and shape for the PCB. It is then cleaned and prepared for the subsequent processes.4. Copper Cladding: Copper foil is laminated onto both sides of the substrate using heat and pressure. This provides the conductive layers for the PCB.5. Imaging: A photosensitive material called a photoresist is applied to both sides of the copper-clad substrate. The PCB design is then transferred onto the photoresist using a UV light source and a photomask. The areas exposed to light become either the conductive traces or the pads for component attachment.6. Etching: The unexposed areas of the photoresist are removed, leaving behind the desired conductive traces and pads. The exposed copper is then etched away using an etching solution, leaving only the desired copper pattern on the substrate.7. Drilling: Holes for component mounting and interconnections are drilled into the PCB using a precisiondrilling machine. These holes are typically plated with copper to provide electrical continuity between the layers.8. Plating: A thin layer of copper is electroplatedonto the exposed copper surfaces, including the drilled holes. This helps to improve the conductivity and protect the copper from oxidation.9. Solder Mask Application: A solder mask is applied to both sides of the PCB to protect the copper traces from oxidation and to prevent solder bridges during assembly.The solder mask is typically green in color, but othercolors can also be used.10. Silkscreen Printing: Component designators, logos, and other information are printed onto the solder maskusing a silkscreen printing process. This helps with component placement and identification during assembly.11. Testing and Inspection: The finished PCBs are subjected to various tests and inspections to ensure their quality and functionality. This includes electrical testing,visual inspection, and sometimes, functional testing.12. Assembly: Once the PCBs pass all the tests, theyare ready for component assembly. This involves solderingthe components onto the PCB using either manual or automated assembly processes.13. Final Testing: The assembled PCBs undergo final testing to verify their functionality and performance. This may include functional testing, environmental testing, and reliability testing.中文回答:PCB(Printed Circuit Board)双面板的制造工艺包括多个步骤。
pcb过孔镀铜

pcb过孔镀铜过孔镀铜是在印刷电路板(PCB)制造过程中的关键步骤之一。
它涉及将铜沉积在PCB的过孔内壁,以提供良好的导电性和连接性。
本文将探讨过孔镀铜的工艺和应用。
1. 什么是PCB过孔镀铜过孔是PCB上用于贯穿不同层的电气连接的孔。
它们在电子设备中起到重要的连接作用。
过孔镀铜是指通过电化学方法,在过孔内部形成一层致密、均匀的铜层,从而增加导电能力和强度。
2. PCB过孔镀铜的工艺流程(1)准备工作:包括待镀PCB的清洁、去脂和表面处理等,以确保铜能够牢固附着在过孔内壁上。
(2)化学镀液准备:根据制造要求,配制适当的化学镀液,并调整好温度和PH值等参数。
(3)装载工作:将清洁好的PCB放入镀液槽中,并使用夹具、网篮等装载上下料工具,以保证均匀镀铜。
(4)电化学镀铜:在设定的参数设置下,将PCB浸入镀液中,通电进行电化学反应,将铜离子还原并沉积在过孔内部。
(5)清洗和后处理:将镀好铜的PCB进行清洗、中和和除膜等处理,去除多余的铜和表面残留物。
3. PCB过孔镀铜的优点(1)良好的导电性:通过过孔镀铜,可以在PCB内形成连续的导电路径,保证信号和电力传输的可靠性。
(2)良好的连接性:过孔镀铜可使不同层之间的电气连接更加牢固,增强PCB的机械强度和可靠性。
(3)提高抗氧化性:过孔镀铜还可以有效降低PCB过孔和铜层的氧化水平,延长PCB的使用寿命。
(4)适应多层设计:在多层PCB设计中,过孔镀铜可以实现不同层之间的信号、电力和接地等电路的有效连接。
4. PCB过孔镀铜的应用领域PCB过孔镀铜被广泛应用于电子设备的制造中,特别是以下领域:(1)通信设备:如手机、电视等消费电子产品中,需要通过过孔镀铜实现电路和元件的连接。
(2)计算机和网络设备:作为计算机主板或网络设备的重要组成部分,PCB需要进行过孔镀铜以满足高速信号传输和数据处理的要求。
(3)工业自动化:在工业自动化设备中,PCB的可靠性和耐用性对设备的稳定性至关重要,过孔镀铜可以提供可靠的连接和导电性。
PCB印制电路板电镀铜及镍金工艺
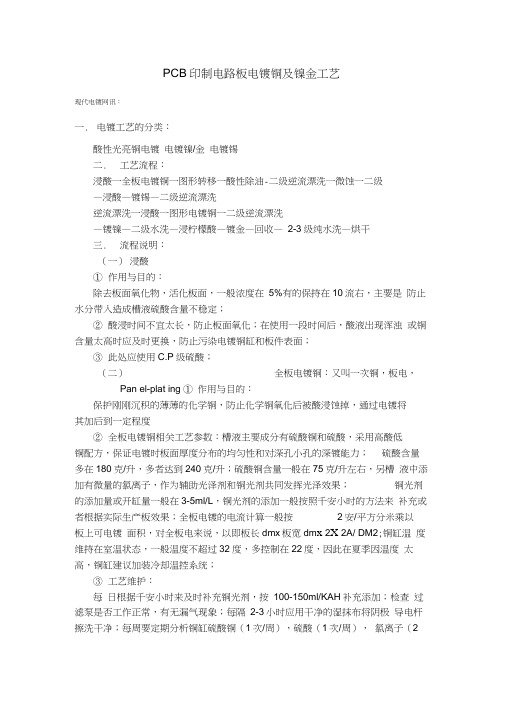
PCB印制电路板电镀铜及镍金工艺现代电镀网讯:一.电镀工艺的分类:酸性光亮铜电镀电镀镍/金电镀锡二.工艺流程:浸酸一全板电镀铜一图形转移一酸性除油-二级逆流漂洗一微蚀一二级—浸酸—镀锡—二级逆流漂洗逆流漂洗一浸酸一图形电镀铜一二级逆流漂洗—镀镍—二级水洗—浸柠檬酸—镀金—回收—2-3级纯水洗—烘干三.流程说明:(一)浸酸①作用与目的:除去板面氧化物,活化板面,一般浓度在5%有的保持在10流右,主要是防止水分带入造成槽液硫酸含量不稳定;②酸浸时间不宜太长,防止板面氧化;在使用一段时间后,酸液出现浑浊或铜含量太高时应及时更换,防止污染电镀铜缸和板件表面;③此处应使用C.P级硫酸;(二)全板电镀铜:又叫一次铜,板电,Pan el-plat ing ① 作用与目的:保护刚刚沉积的薄薄的化学铜,防止化学铜氧化后被酸浸蚀掉,通过电镀将其加后到一定程度②全板电镀铜相关工艺参数:槽液主要成分有硫酸铜和硫酸,采用高酸低铜配方,保证电镀时板面厚度分布的均匀性和对深孔小孔的深镀能力;硫酸含量多在180克/升,多者达到240克/升;硫酸铜含量一般在75克/升左右,另槽液中添加有微量的氯离子,作为辅助光泽剂和铜光剂共同发挥光泽效果;铜光剂的添加量或开缸量一般在3-5ml/L,铜光剂的添加一般按照千安小时的方法来补充或者根据实际生产板效果;全板电镀的电流计算一般按2安/平方分米乘以板上可电镀面积,对全板电来说,以即板长dmx板宽dm x 2X 2A/ DM2;铜缸温度维持在室温状态,一般温度不超过32度,多控制在22度,因此在夏季因温度太高,铜缸建议加装冷却温控系统;③工艺维护:每日根据千安小时来及时补充铜光剂,按100-150ml/KAH补充添加;检查过滤泵是否工作正常,有无漏气现象;每隔2-3小时应用干净的湿抹布将阴极导电杆擦洗干净;每周要定期分析铜缸硫酸铜(1次/周),硫酸(1次/周),氯离子(2次/周)含量,并通过霍尔槽试验来调整光剂含量,并及时补充相关原料;每周要清洗阳极导电杆,槽体两端电接头,及时补充钛篮中的阳极铜球,用低电流0。
PCB电镀铜原理简介电镀工艺
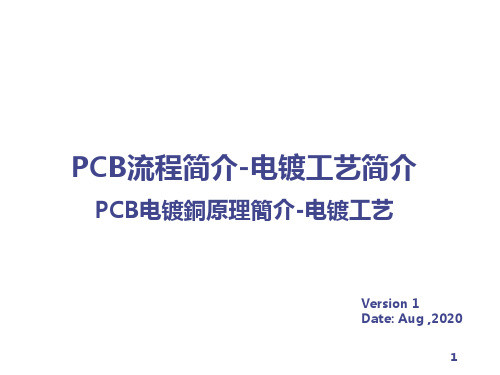
b. 提高Throwing power 的方法很多,包括: (1) 降低ηcts 和ηcth 之差值(△ηct):其方法包括: -改善搅拌效果 -降低IR 值,包括提高酸度及加入导电盐 -强迫孔内对流(降低IR) -添加改变Charge transfer 能力之添加剂包括载体光泽剂等 (2) 修正极化曲线:如之前所提藉降低极化曲线的斜率降低△J
槽液中各成分作用机制
1.提供反应所必须之金属离子,即供给槽液铜离子的主源. 2.配槽时要用化学级之含水硫酸铜结晶溶解使用,平常作业中则由阳极磷铜块解
离补充之,为一盐桥并增加槽液的极限电流密度,配液后要做活性炭处理及假镀 (dummy).
1.增加溶液的导电性及阳极的溶解,镀液在不镀时要关掉吹气(air),以防铜量上升 酸量下降及光泽剂之过度消耗.
双面板以上完成钻孔后即进行镀通孔(Plated Through Hole, PTH) 步骤,其目的使孔壁上之非导体部份之树脂及玻纤束进行金属化 (metalization ),以进行后来之电镀铜制程,完成足够导电及焊接之金属 孔壁。
2
电镀流程
一次铜:
酸洗 → 电镀 → 水洗 → 水洗
二次铜:
清洁剂 → 水洗 → 水洗 → 微蚀 → 水洗 → 水洗 → 酸洗→ 电镀 → 水洗 → 水洗 → 镀锡铅 → 水洗
c. 修正极化曲极化曲线的方法: 降低金属离子浓度: 基本上过电压就是赋予带电离子反应所需能量,以驱使反应进行。因此离子愈少则要 维持定量离子在定时间内反应之难度愈高,因此必须给予较大能量。其结困即使得 J-η曲线愈平,可得几项推论: -CuSO4 浓度愈低,Throwing power 愈好 -上述结果也可推论到二次铜电镀线路不均的板子,其Distribution 也将改善 -必须强调的是随CuSO4 降低,相同电路密度下所消耗的能量更大
PCB生产工艺流程
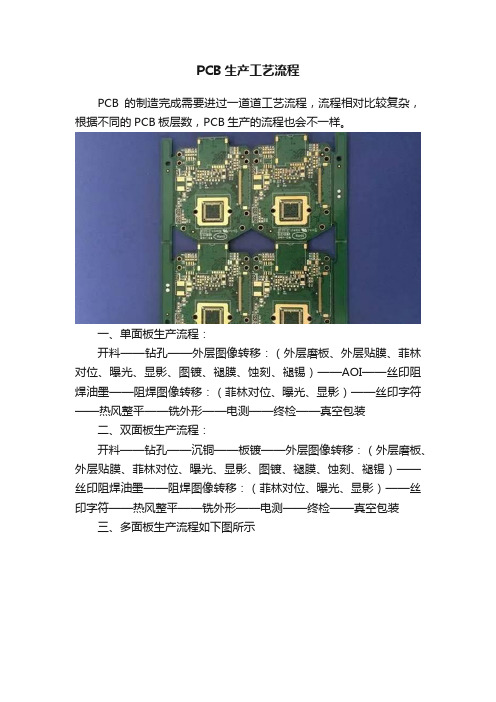
PCB生产工艺流程PCB的制造完成需要进过一道道工艺流程,流程相对比较复杂,根据不同的PCB板层数,PCB生产的流程也会不一样。
一、单面板生产流程:开料——钻孔——外层图像转移:(外层磨板、外层贴膜、菲林对位、曝光、显影、图镀、褪膜、蚀刻、褪锡)——AOI——丝印阻焊油墨——阻焊图像转移:(菲林对位、曝光、显影)——丝印字符——热风整平——铣外形——电测——终检——真空包装二、双面板生产流程:开料——钻孔——沉铜——板镀——外层图像转移:(外层磨板、外层贴膜、菲林对位、曝光、显影、图镀、褪膜、蚀刻、褪锡)——丝印阻焊油墨——阻焊图像转移:(菲林对位、曝光、显影)——丝印字符——热风整平——铣外形——电测——终检——真空包装三、多面板生产流程如下图所示展开剩余77%1、开料目的:根据工程资料MI的要求,在符合要求的大张板材上,裁切成小块生产板件.符合客户要求的小块板料.流程:大板料→按MI要求切板→锔板→啤圆角\磨边→出板2、钻孔目的:根据工程资料(客户资料),在所开符合要求尺寸的板料上,相应的位置钻出所求的孔径.流程:叠板销钉→上板→钻孔→下板→检查\修理3、沉铜目的:沉铜是利用化学方法在绝缘孔壁上沉积上一层薄铜.流程:粗磨→挂板→沉铜自动线→下板→浸1%稀H2SO4→加厚铜4、图形转移目的:图形转移是生产菲林上的图像转移到板上流程:(蓝油流程):磨板→印第一面→烘干→印第二面→烘干→爆光→冲影→检查;(干膜流程):麻板→压膜→静置→对位→曝光→静置→冲影→检查5、图形电镀目的:图形电镀是在线路图形裸露的铜皮上或孔壁上电镀一层达到要求厚度的铜层与要求厚度的金镍或锡层.流程:上板→除油→水洗二次→微蚀→水洗→酸洗→镀铜→水洗→浸酸→镀锡→水洗→下板6、退膜目的:用NaOH溶液退去抗电镀覆盖膜层使非线路铜层裸露出来.流程:水膜:插架→浸碱→冲洗→擦洗→过机;干膜:放板→过机7、蚀刻目的:蚀刻是利用化学反应法将非线路部位的铜层腐蚀去.8、绿油目的:绿油是将绿油菲林的图形转移到板上,起到保护线路和阻止焊接零件时线路上锡的作用流程:磨板→印感光绿油→锔板→曝光→冲影;磨板→印第一面→烘板→印第二面→烘板9、字符目的:字符是提供的一种便于辩认的标记流程:绿油终锔后→冷却静置→调网→印字符→后锔10、镀金手指目的:在插头手指上镀上一层要求厚度的镍\金层,使之更具有硬度的耐磨性流程:上板→除油→水洗两次→微蚀→水洗两次→酸洗→镀铜→水洗→镀镍→水洗→镀金镀锡板(与镀金手指并列的工艺)目的:喷锡是在未覆盖阻焊油的裸露铜面上喷上一层铅锡,以保护铜面不蚀氧化,以保证具有良好的焊接性能.流程:微蚀→风干→预热→松香涂覆→焊锡涂覆→热风平整→风冷→洗涤风干11、成型目的:通过模具冲压或数控锣机锣出客户所需要的形状成型的方法有机锣,啤板,手锣,手切说明:数据锣机板与啤板的精确度较高,手锣其次,手切板最低具只能做一些简单的外形.12、测试目的:通过电子100%测试,检测目视不易发现到的开路,短路等影响功能性之缺陷.流程:上模→放板→测试→合格→FQC目检→不合格→修理→返测试→OK→REJ→报废13、终检目的:通过100%目检板件外观缺陷,并对轻微缺陷进行修理,避免有问题及缺陷板件流出。
PCB电镀工艺流程介绍

PCB电镀工艺介绍线路板的电镀工艺,大约可以分类:酸性光亮铜电镀、电镀镍/金、电镀锡,文章介绍的是关于在线路板加工过程是,电镀工艺的技术以及工艺流程,以及具体操作方法.二.工艺流程:浸酸→全板电镀铜→图形转移→酸性除油→二级逆流漂洗→微蚀→二级逆流漂洗→浸酸→镀锡→二级逆流漂洗→逆流漂洗→浸酸→图形电镀铜→二级逆流漂洗→镀镍→二级水洗→浸柠檬酸→镀金→回收→2-3级纯水洗→烘干三.流程说明:(一)浸酸①作用与目的:除去板面氧化物,活化板面,一般浓度在5%,有的保持在10%左右,主要是防止水分带入造成槽液硫酸含量不稳定;②酸浸时间不宜太长,防止板面氧化;在使用一段时间后,酸液出现浑浊或铜含量太高时应及时更换,防止污染电镀铜缸和板件表面;③此处应使用C.P级硫酸;(二)全板电镀铜:又叫一次铜,板电,Panel-plating①作用与目的:保护刚刚沉积的薄薄的化学铜,防止化学铜氧化后被酸浸蚀掉,通过电镀将其加后到一定程度②全板电镀铜相关工艺参数:槽液主要成分有硫酸铜和硫酸,采用高酸低铜配方,保证电镀时板面厚度分布的均匀性和对深孔小孔的深镀能力;硫酸含量多在180克/升,多者达到240克/升;硫酸铜含量一般在75克/升左右,另槽液中添加有微量的氯离子,作为辅助光泽剂和铜光剂共同发挥光泽效果;铜光剂的添加量或开缸量一般在3-5ml/L,铜光剂的添加一般按照千安小时的方法来补充或者根据实际生产板效果;全板电镀的电流计算一般按2安/平方分米乘以板上可电镀面积,对全板电来说,以即板长dm×板宽dm×2×2A/DM2;铜缸温度维持在室温状态,一般温度不超过32度,多控制在22度,因此在夏季因温度太高,铜缸建议加装冷却温控系统;③工艺维护:每日根据千安小时来及时补充铜光剂,按100-150ml/KAH补充添加;检查过滤泵是否工作正常,有无漏气现象;每隔2-3小时应用干净的湿抹布将阴极导电杆擦洗干净;每周要定期分析铜缸硫酸铜(1次/周),硫酸(1次/周),氯离子(2次/周)含量,并通过霍尔槽试验来调整光剂含量,并及时补充相关原料;每周要清洗阳极导电杆,槽体两端电接头,及时补充钛篮中的阳极铜球,用低电流0。
PCB化学镀铜工艺流程

PCB化学镀铜工艺流程产品检验标准2010-02-03 18:26:16 阅读4 评论0 字号:大中小订阅PCB化学镀铜工艺流程解读(一)化学镀铜(Eletcroless Plating Copper)通常也叫沉铜或孔化(PTH)是一种自身催化性氧化还原反应。
首先用活化剂处理,使绝缘基材表面吸附上一层活性的粒子通常用的是金属钯粒子(钯是一种十分昂贵的金属,价格高且一直在上升,为降低成本现在国外有实用胶体铜工艺在运行),铜离子首先在这些活性的金属钯粒子上被还原,而这些被还原的金属铜晶核本身又成为铜离子的催化层,使铜的还原反应继续在这些新的铜晶核表面上进行。
化学镀铜在我们PCB制造业中得到了广泛的应用,目前最多的是用化学镀铜进行PCB的孔金属化。
PCB孔金属化工艺流程如下:钻孔→磨板去毛刺→上板→整孔清洁处理→双水洗→微蚀化学粗化→双水洗→预浸处理→胶体钯活化处理→双水洗→解胶处理(加速)→双水洗→沉铜→双水洗→下板→上板→浸酸→一次铜→水洗→下板→烘干一、镀前处理1.去毛刺钻孔后的覆铜泊板,其孔口部位不可避免的产生一些小的毛刺,这些毛刺如不去除将会影响金属化孔的质量。
最简单去毛刺的方法是用200~400号水砂纸将钻孔后的铜箔表面磨光。
机械化的去毛刺方法是采用去毛刺机。
去毛刺机的磨辊是采用含有碳化硅磨料的尼龙刷或毡。
一般的去毛刺机在去除毛刺时,在顺着板面移动方向有部分毛刺倒向孔口内壁,改进型的磨板机,具有双向转动带摆动尼龙刷辊,消除了除了这种弊病。
2.整孔清洁处理对多层PCB有整孔要求,目的是除去钻污及孔微蚀处理。
以前多用浓硫酸除钻污,而现在多用碱性高锰酸钾处理法,随后清洁调整处理。
孔金属化时,化学镀铜反应是在孔壁和整个铜箔表面上同时发生的。
如果某些部位不清洁,就会影响化学镀铜层和印制导线铜箔间的结合强度,所以在化学镀铜前必须进行基体的清洁处理。
最常用的清洗液及操作条件列于表如下:3.覆铜箔粗化处理利用化学微蚀刻法对铜表面进行浸蚀处理(蚀刻深度为2-3微米),使铜表面产生凹凸不平的微观粗糙带活性的表面,从而保证化学镀铜层和铜箔基体之间有牢固的结合强度。
PCB化学镀铜工艺流程解读(二)
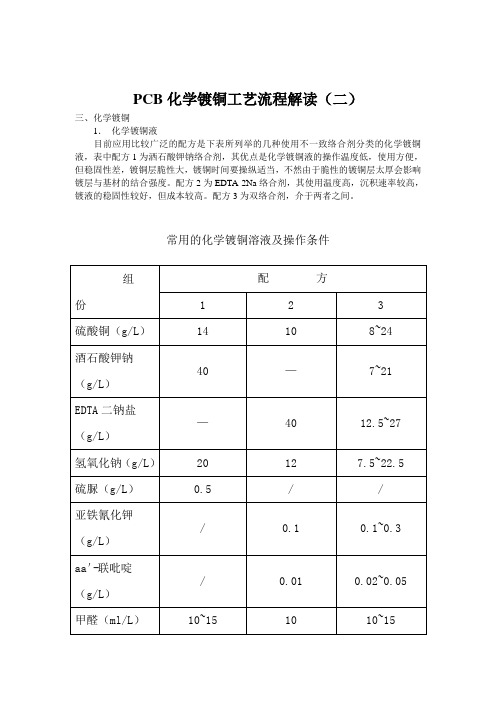
PCB化学镀铜工艺流程解读(二)三、化学镀铜1.化学镀铜液目前应用比较广泛的配方是下表所列举的几种使用不一致络合剂分类的化学镀铜液,表中配方1为洒石酸钾钠络合剂,其优点是化学镀铜液的操作温度低,使用方便,但稳固性差,镀铜层脆性大,镀铜时间要操纵适当,不然由于脆性的镀铜层太厚会影响镀层与基材的结合强度。
配方2为EDTA·2Na络合剂,其使用温度高,沉积速率较高,镀液的稳固性较好,但成本较高。
配方3为双络合剂,介于两者之间。
常用的化学镀铜溶液及操作条件工作温度(℃)21~25 50~60 35~40 沉积速率(µm/h )0.5 4~5 1~2PH值;操作条件12~13;空气搅拌连续过滤12~12.5;空气搅拌连续过滤12~13;空气搅拌连续过滤工作负荷(dm2/L)≤1 ≤1 ≤22.化学镀铜溶液的稳固性(1)化学镀铜溶液不稳固的原因在催化剂存在的条件下,化学镀铜的要紧反应如下:在化学镀铜溶液中除上式的主反应以外,还存在下列几个副反应。
a.甲醛的歧化反应-在浓碱条件下,甲醛一部分被氧化成为甲酸,另一部分被还原成甲醇,反应式为甲醛的歧视化反应除造成甲醛过量的消耗外,还会使镀液过早的"老化",使镀液不稳固。
b.在碱性镀铜溶液中,甲醛还原一部分Cu2+为Cu+,其反应式为反应式(5-3)所生成的Cu2O在碱性溶液中是微溶的:Cu2O+ H2O ===2Cu++2 OH-- (5-4)反应(5-4) 中出现的铜Cu+非常容易发生歧化反应2Cu+=== Cu0↓+ Cu2+ (5-5)反应式(5-5)所生成的铜是极细小的微粒,它们无规则地分散在化学镀铜液中,这些铜微粒具有催化性,假如对这些铜微粒不进行操纵,则迅速地导致整个镀液分解,这是造成化学镀铜液不稳固的要紧原因。
(2)提高化学镀铜溶液稳固性的措施a.加稳固剂所加入的稳固剂对Cu+有极强的络合能力,对溶液中的Cu2+离子络合能力较差,这种溶液中的Cu+离子不能产生歧化反应,因而能起到稳固化学镀铜液的作用。
PCB工艺流程说明

一.双面板工艺流程:覆铜板(CCL)下料(Cut)→钻孔(Drilling)→沉铜(PTH)→全板镀铜(Panel Plating)→图形转移(Pattern)油墨或干膜→图形电镀(Pattern plating)→蚀刻(Etch)→半检IQC→丝印阻焊油墨和字符油墨(SS)或贴阻焊干膜→热风整平或喷锡(HAL)→外形(Pounching)→成检(FQC)→电测试E-TEST→包装(Packaging)二.多层板工艺流程:内层覆铜板(CCL)铜箔(Copper Foil)下料(Cut)→内层图形制作(Inner-layer Pattern)→内层蚀刻(Inner-layer Etch)→内层黑氧化(Black-oxide)→层压or压合制程→钻孔(Drilling)→沉铜(PTH)→全板镀铜(Panel Plating)→外层蚀刻(Outer-layer Etch)→半检IQC→丝印阻焊油墨和字符油墨(SS)或贴阻焊干膜→热风整平或喷锡(HAL)→外形(Pounching)→成检(FQC)→电测试E-TEST→包装(Packaging)=三.流程说明:①下料:从一定板厚和铜箔厚度的整张覆铜板大料上剪出便于加工的尺寸,重量减少大约10-15%;②钻孔:在板上按电脑钻孔程序钻出导电孔或插件孔;板重量大约减少5%;③沉铜:在钻出的孔内沉积一层薄薄的化学铜,厚度大约在0。
3-2um,重量增加较少,目的是在不导电的环氧玻璃布基材(或其他基材)通过化学方法沉上一层铜,便于后面电镀导通形成线路;④全板镀铜:主要是为加厚保护那层薄薄的化学铜以防其在空气中氧化,形成孔内无铜或破洞;⑤图形制作(图形转移):包括内层图形制作,在板上贴上干膜或丝印上图形抗电镀油墨,经曝光,显影后,做出线路图形;重量减少较小。
⑥图形电镀:在已做好图形线路的板上进行线路加厚镀铜,使孔内和线路铜厚达到一定厚度,可以负载一定的电流;重量增加大约15%;⑦蚀刻:包括内层蚀刻,褪掉图形油墨或干膜,蚀刻掉多余的铜箔从而得到导电线路图形;⑧层压:把内层与半固化片,铜箔叠合一起经高温压制成多层板,4层板需要一张内层,两张铜箔;6层板需要两张内层,两张铜箔。
pcb电镀铜工艺参数
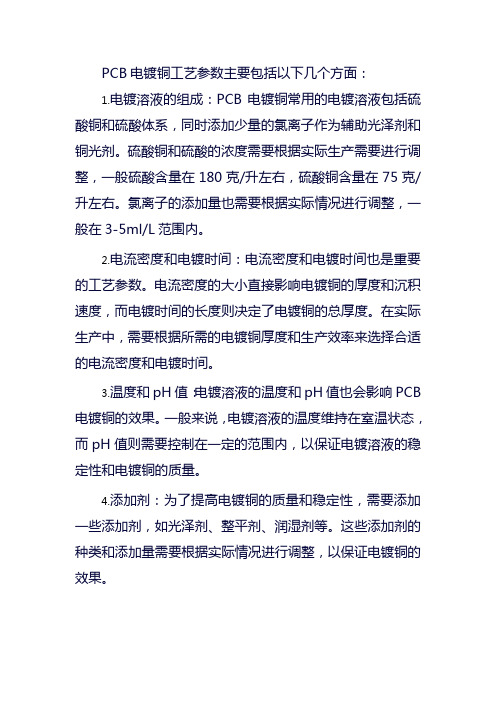
PCB电镀铜工艺参数主要包括以下几个方面:
1.电镀溶液的组成:PCB电镀铜常用的电镀溶液包括硫酸铜和硫酸体系,同时添加少量的氯离子作为辅助光泽剂和铜光剂。
硫酸铜和硫酸的浓度需要根据实际生产需要进行调整,一般硫酸含量在180克/升左右,硫酸铜含量在75克/升左右。
氯离子的添加量也需要根据实际情况进行调整,一般在3-5ml/L范围内。
2.电流密度和电镀时间:电流密度和电镀时间也是重要的工艺参数。
电流密度的大小直接影响电镀铜的厚度和沉积速度,而电镀时间的长度则决定了电镀铜的总厚度。
在实际生产中,需要根据所需的电镀铜厚度和生产效率来选择合适的电流密度和电镀时间。
3.温度和pH值:电镀溶液的温度和pH值也会影响PCB 电镀铜的效果。
一般来说,电镀溶液的温度维持在室温状态,而pH值则需要控制在一定的范围内,以保证电镀溶液的稳定性和电镀铜的质量。
4.添加剂:为了提高电镀铜的质量和稳定性,需要添加一些添加剂,如光泽剂、整平剂、润湿剂等。
这些添加剂的种类和添加量需要根据实际情况进行调整,以保证电镀铜的效果。
5.阴极材料和表面处理:在PCB电镀铜过程中,阴极材料和表面处理也是非常重要的因素。
常用的阴极材料包括纯铜板、镍板等,而表面处理则包括磨光、化学抛光、电抛光等。
这些因素都会影响电镀铜的质量和效果。
总之,PCB电镀铜工艺参数是一个复杂的过程,需要综合考虑多个因素,并根据实际情况进行调整和优化,以保证电镀铜的质量和效果。
PCB化学镀铜工艺
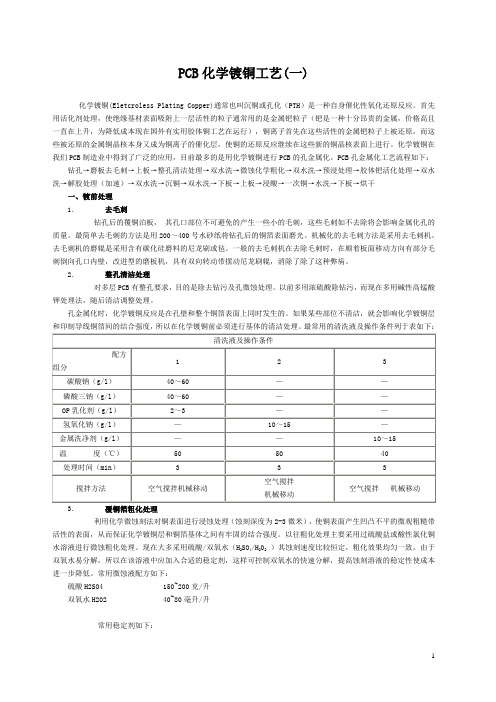
PCB化学镀铜工艺(一)化学镀铜(Eletcroless Plating Copper)通常也叫沉铜或孔化(PTH)是一种自身催化性氧化还原反应。
首先用活化剂处理,使绝缘基材表面吸附上一层活性的粒子通常用的是金属钯粒子(钯是一种十分昂贵的金属,价格高且一直在上升,为降低成本现在国外有实用胶体铜工艺在运行),铜离子首先在这些活性的金属钯粒子上被还原,而这些被还原的金属铜晶核本身又成为铜离子的催化层,使铜的还原反应继续在这些新的铜晶核表面上进行。
化学镀铜在我们PCB制造业中得到了广泛的应用,目前最多的是用化学镀铜进行PCB的孔金属化。
PCB孔金属化工艺流程如下:钻孔→磨板去毛刺→上板→整孔清洁处理→双水洗→微蚀化学粗化→双水洗→预浸处理→胶体钯活化处理→双水洗→解胶处理(加速)→双水洗→沉铜→双水洗→下板→上板→浸酸→一次铜→水洗→下板→烘干一、镀前处理1.去毛刺钻孔后的覆铜泊板,其孔口部位不可避免的产生一些小的毛刺,这些毛刺如不去除将会影响金属化孔的质量。
最简单去毛刺的方法是用200~400号水砂纸将钻孔后的铜箔表面磨光。
机械化的去毛刺方法是采用去毛刺机。
去毛刺机的磨辊是采用含有碳化硅磨料的尼龙刷或毡。
一般的去毛刺机在去除毛刺时,在顺着板面移动方向有部分毛刺倒向孔口内壁,改进型的磨板机,具有双向转动带摆动尼龙刷辊,消除了除了这种弊病。
2.整孔清洁处理对多层PCB有整孔要求,目的是除去钻污及孔微蚀处理。
以前多用浓硫酸除钻污,而现在多用碱性高锰酸钾处理法,随后清洁调整处理。
孔金属化时,化学镀铜反应是在孔壁和整个铜箔表面上同时发生的。
如果某些部位不清洁,就会影响化学镀铜层和印制导线铜箔间的结合强度,所以在化学镀铜前必须进行基体的清洁处理。
最常用的清洗液及操作条件列于表如下:3.覆铜箔粗化处理利用化学微蚀刻法对铜表面进行浸蚀处理(蚀刻深度为2-3微米),使铜表面产生凹凸不平的微观粗糙带活性的表面,从而保证化学镀铜层和铜箔基体之间有牢固的结合强度。
【电镀系列】PCB板——电镀铜
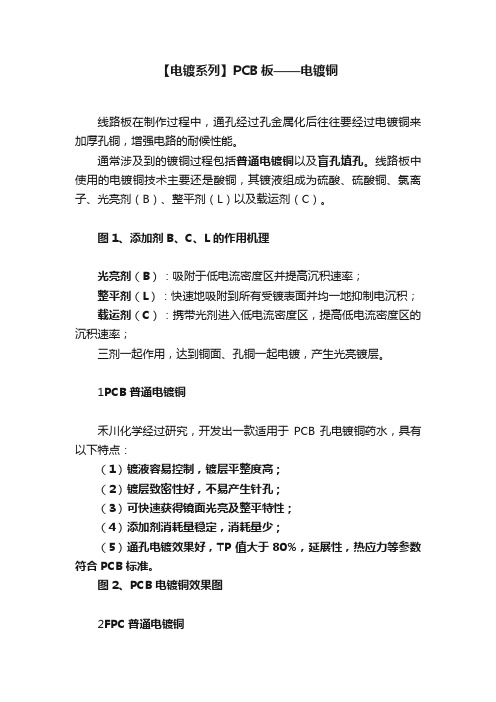
【电镀系列】PCB板——电镀铜线路板在制作过程中,通孔经过孔金属化后往往要经过电镀铜来加厚孔铜,增强电路的耐候性能。
通常涉及到的镀铜过程包括普通电镀铜以及盲孔填孔。
线路板中使用的电镀铜技术主要还是酸铜,其镀液组成为硫酸、硫酸铜、氯离子、光亮剂(B)、整平剂(L)以及载运剂(C)。
图1、添加剂B、C、L的作用机理光亮剂(B):吸附于低电流密度区并提高沉积速率;整平剂(L):快速地吸附到所有受镀表面并均一地抑制电沉积;载运剂(C):携带光剂进入低电流密度区,提高低电流密度区的沉积速率;三剂一起作用,达到铜面、孔铜一起电镀,产生光亮镀层。
1PCB普通电镀铜禾川化学经过研究,开发出一款适用于PCB孔电镀铜药水,具有以下特点:(1)镀液容易控制,镀层平整度高;(2)镀层致密性好,不易产生针孔;(3)可快速获得镜面光亮及整平特性;(4)添加剂消耗量稳定,消耗量少;(5)通孔电镀效果好,TP值大于80%,延展性,热应力等参数符合PCB标准。
图2、PCB电镀铜效果图2FPC普通电镀铜禾川化学经过研究,开发出一款适用于FPC孔铜电镀的药水,具有以下特点:(1)镀液容易控制,镀层平整度高;(2)镀层延展性好,耐折度好;(3)可快速获得镜面光亮及整平特性;(4)添加剂消耗量稳定,消耗量少;(5)通孔电镀效果好,TP值大于120%,延展性,热应力等参数符合PCB标准。
图3、FPC电镀铜效果图3盲孔填孔电镀填孔电镀添加剂的组成:光亮剂(B又称加速剂),其作用减小极化,促进铜的沉积、细化晶粒;载运剂(C又称抑制剂),增加阴极极化,降低表面张力,协助光亮剂作用;整平剂(L),抑制高电流密度区域铜的沉积。
微盲孔孔底和孔内沉积速率的差异主要来源于添加剂在孔内不同位置吸附分布,其分布形成过程如下:a、由于整平剂带正电,最易吸附在孔口电位最负的位置,并且其扩散速率较慢因此在孔底位置整平剂浓度较低;b、加速剂最易在低电流密度区域富集,并且其扩散速率快,因此,孔底加速剂浓度较高;c、在孔口电位最负,同时对流最强烈,整平剂将逐渐替代抑制剂加强对孔口的抑制,最终使得微孔底部的铜沉积速率大于表面沉积速率,从而达到填孔的效果。
PCB电镀工艺流程
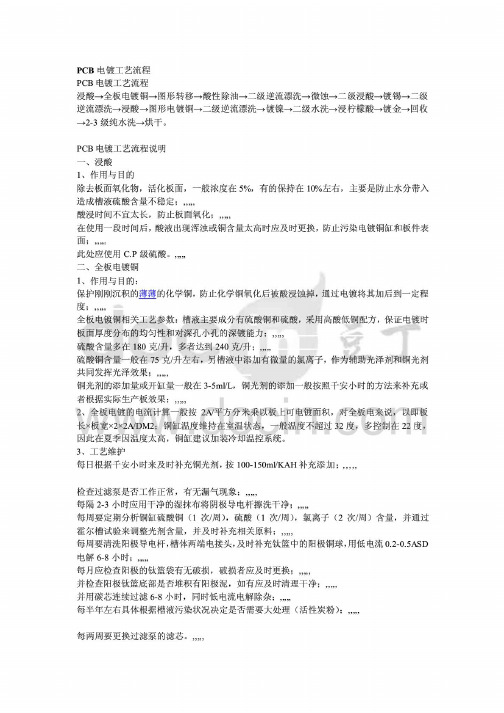
干后备用, "'"
将拙液转移到备用植内,加入 1-3mVL 的 30% 的双氧水,开始加、温,待温度加到 65 度左右
打开空气搅拌,保温空气搅拌 2-4 小时, "'"
关掉空气搅拌,按 3-5 克/升将活性碳粉缓慢溶解到槽液中,待溶解彻底后,打开空气搅拌,
因此在夏季因温度太 高 ,铜缸建议加装冷却温控系统。
3 、 工 艺维护
每日根据千安小时来及时补充铜光剂, 按 100-150mVKAH 补充添加; "'"
检查过滤泵是否 工作正常 , 有无漏气现象;川,
每隔 2-3 小时应用干净的温抹布将阴极导电杆擦洗干净;川"
每周要定期分析铜缸硫酸铜(1次/周) , 硫酸(1次/周) , 氯离子 (2 次/周〉含量,并通过
如此保温 2-4 小时; "'"
关掉空气搅拌 , 加、温,让活性碳粉慢慢沉淀至槽底 ; '"''
待温度降至 40 度左右,用 10um 的 pp 滤芯加助滤粉过滤槽液至清洗干净的 工 作槽'内,打开
空气搅拌,放入阳极,挂入电解板,按 0.2-0.5ASD 电流密度低电流电解 6-8 小时; '"''
每周要清洗阳极导电杆,槽'体两端电接头,及时补充钦篮中的阳极保角,用低电流 0.2-0.5ASD
电解 6-8 小时; "'"
每月应检查阳极的铁篮袋有无破损,破损者应及时更换;并检查阳极钦篮底部是否堆积有阳
PCB填孔电镀制程简介

对于电路板的结构 设计来说,在通盲孔 上直接迭孔的构造 (Via on Via)是获得 最高结构密度可能 性的孔地的平坦性做好,因此填孔就成为必要的技术了
7
总结 填孔的作用:
1.增加PCB的密集度,在最小的面积与体积中,容 纳最大的布线密度与承接最多的主动与被动组件. 2.使镀铜层表面更平滑,避免凹陷产生. 3.避免介电物质及导电物质的不完全填孔. 4.提升微细线路,各项电性及信赖性规范.
A类型
B类型
A类型产生原因
B类型产生原因
24
八.产能统计
電鍍厚度 尺寸(in) 電流密 (mil) 寬 長 度 1.1 21 24 12
電鍍 電鍍時間 線速 保養時 效率 (min) (m/min) 間 90% 109 0.124 1.5
更換料號
時間(min) 次數
40
4
H/DAY 天數 19.8 30
压合 防焊 FQC
雷射 外层 OQC
钻孔 电镀 成仓
5
填孔电镀在电镀制程中的位置
去毛头(DB) 除胶渣(DSM)
水平除胶渣化铜联机 (水平DSM+PTH)
垂直连续电镀线 (VCP)
VCP打底 填孔电镀线
龙门线(PTH+ICu)
后处理
出货
6
三.填孔作用与原理
为什么要用填孔电镀?
在制作传统的印制电路板方面,通孔电镀 一直是业界众所皆知的重要制程,然而随 着时代的进步,电子产品急速往轻薄短小 的趋势发展,印制电路的高密度化要求越 来越高,这时传统制程就无法满足要求了.
2.设备区别
不同点 前处理 阳极
VCP 化铜 无特殊要求
VCP 无微蚀槽 可溶性阳极
填孔线 VCP线打底 与VCP打底时上下方向相反
双面板PCB_制程讲解
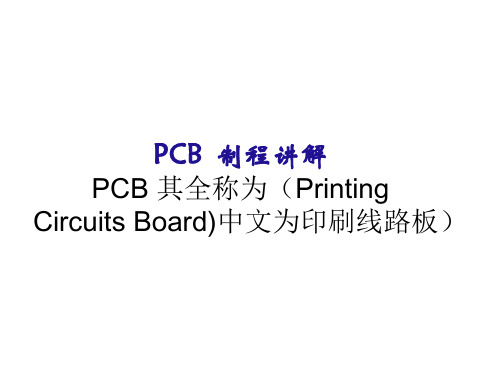
Middle Inspection 蚀检
Solder Mask 绿油
制作工艺流程
Component Mark 白字
测试/FQC 终检
Surface 表面处理
Profiling 成型
FQA 最后稽查
Packing 包装
主要过程图解
Pressing压板 Plating Tin镀锡 Strip Film 褪菲林
PCB所用板料概述
特性:目前用于生产的大多数板材为卤素材料,对人体有害,主要是燃烧时会产 生二恶英(dioxides,戴奥辛TCDD,二氧环环己烷),奔呋喃 (Benz furan)等,发烟量大、高毒性、致癌,人体摄入后无法排除,影响身体健康 。 b、无卤素材料;特性:含卤素比例较少,JPCA-ES-01-2003标准,日本人的定义 :CL、Br、I含量小于0.09%(重量比)称为无卤素,鉴于卤素对人体存在较 大危害,相关法律法规推动禁止使用卤素材料用于板料中(WEEE,ROHS), 1982年瑞士发现在卤化物燃烧后存在二恶英,后20世纪90年代在日本后生省 焚炉废气中发现二恶英。 a、与FR4材料相比,吸水性低,TG约高,DK值约小一点,适用于PCB 阻抗板生产,单价较贵; b、主要应用于电脑、手机、通信设备、医疗设备、仪表、摄象机、 平面液体湿显示器等领域中
Guide Hole 管位孔 Entry盖板
PCB
Back Up Board 垫板
Drilling –钻孔
磨圆角:除去生产板上四角上的尖角,以免擦花、插穿菲 林及伤人。 磨板边:除去生产板周围的纤维丝,防止擦花。 管位钉:将生产板与底板用管位钉固定在一起,以避免钻孔 时板间滑动,造成钻咀断。
生产型号举例:
Duplicate GII Film 复制黄菲林
- 1、下载文档前请自行甄别文档内容的完整性,平台不提供额外的编辑、内容补充、找答案等附加服务。
- 2、"仅部分预览"的文档,不可在线预览部分如存在完整性等问题,可反馈申请退款(可完整预览的文档不适用该条件!)。
- 3、如文档侵犯您的权益,请联系客服反馈,我们会尽快为您处理(人工客服工作时间:9:00-18:30)。
PCB 双面板通孔镀铜工艺7.1 制程目的双面板以上完成钻孔后即进行镀通孔(Plated Through Hole , PTH) 步骤,其目的使孔壁上之非导体部份之树脂及玻纤束进行金属化( metalization ), 以进行后来之电镀铜制程,完成足够导电及焊接之金属孔壁。
1986 年,美国有一家化学公司Hunt 宣布PTH 不再需要传统的贵金属及无电铜的金属化制程,可用碳粉的涂布成为通电的媒介,商名为"Black hole" 。
之后陆续有其他不同base 产品上市, 国内用户非常多. 除传统PTH 外, 直接电镀(direct plating) 本章节也会述及.7.2 制造流程去毛头-除胶渣-PTH 一次铜7.2.1. 去巴里(deburr)钻完孔后,若是钻孔条件不适当,孔边缘有 1.未切断铜丝 2.未切断玻纤的残留,称为burr.因其要断不断,而且粗糙,若不将之去除,可能造成通孔不良及孔小,因此钻孔后会有de-burr 制程.也有de-burr 是放在Desmear 之后才作业.一般de-burr 是用机器刷磨,且会加入超音波及高压冲洗的应用.可参考表4.1.47.2.2. 除胶渣(Desmear)A. 目的:a. Desmearb. Create Micro-rough 增力卩adhesionB. Smear产生的原因:由于钻孔时造成的高温Resin超过Tg值,而形成融熔状,终致产生胶渣。
此胶渣生于内层铜边缘及孔壁区,会造成P.I.(Poor In terco nn ectio n)C. Desmear的四种方法:硫酸法(Sulferic Acid)、电浆法(Plasma)、铬酸法(Cromic Acid)、高锰酸钾法(Perma ngan ate).a. 硫酸法必须保持高浓度,但硫酸本身为脱水剂很难保持高浓度,且咬蚀出的孔面光滑无微孔,并不适用b. 电浆法效率慢且多为批次生产,而处理后大多仍必须配合其他湿制程处理,因此除非生产特殊板大多不予采用。
c. 铬酸法咬蚀速度快,但微孔的产生并不理想,且废水不易处理又有致癌的潜在风险,故渐被淘汰。
d. 高锰酸钾法因配合溶剂制程,可以产生微孔。
同时由于还原电极的推出,使槽液安定性获得较佳控制,因此目前较被普遍使用。
7.2.2.1 高锰酸钾法(KMnO4 Process):A. 膨松剂(Sweller):a. 功能:软化膨松Epoxy,降低Polymer间的键结能,使KMnO4更易咬蚀形成Micro-rough 速率作用Concentrationb. 影响因素:见图7.1c. 安全:不可和KMnO4直接混合,以免产生强烈氧化还原,发生火灾d. 原理解释:(1) 见图7.2叫初期溶出可降低较弱的键结,使其键结间有了明显的差异。
若浸泡过长,强的链结也渐次降低,终致整块成为低链结能的表面。
如果达到如此状态,将无法形成不同强度结面。
若浸泡过短,则无法形成低键结及键结差异,如此将使KMnO4咬蚀难以形成蜂窝面,终致影响到PTH的效果。
(2) Surface Tension 的问题:无论大小孔皆有可能有气泡残留,而表面力对孔内Wetting也影响颇大。
故采用较高温操作有助于降低Surface Tension及去除气泡。
至于浓度的问题,为使Drag out降低减少消耗而使用略低浓度,事实上较高浓度也可操作且速度较快。
在制程中必须先Wetting孔内壁,以后才能使药液进入作用,否则有空气残留后续制程更不易进入孔内,其Smear将不可能去除。
B. 除胶剂(KMnO4 ):a. 使用KMnO4的原因:选KMnO4而未选NaMnO4是因为KMnO4溶解度较佳,单价也较低。
b. 反应原理:4MnO4- + C + 40H- —MnO4= + C02 + 2H2O (此为主反应式)2MnO4- + 20H- —2MnO4= + 1/2 02 + H20 (此为高PH 值时自发性分解反应)Mn04- + H20 —Mn02 + 20H- + 1/2 02 (此为自然反应会造成Mn+4沉淀)c. 作业方式:早期采氧化添加剂的方式,目前多用电极还原的方式操作,不稳定的问题已获解决。
d. 过程中其化学成份状况皆以分析得知,但Mn+7为紫色,Mn+6为绿色,Mn+4为黑色,可由直观的色度来直接判断大略状态。
若有不正常发生,则可能是电极效率出了问题须注意。
e. 咬蚀速率的影响因素:见图7.3f. 电极的好处:(1).使槽液寿命增长(2).质量稳定且无By-product,其两者比较如图7.4:承■-:■--g. KMnO4形成Micro-rough的原因:由于Sweller造成膨松,且有结合力之强弱,如此使咬蚀时产生选择性,而形成所谓的Micro-rough。
但如因过度咬蚀,将再度平滑。
h. 咬蚀能力也会随基材之不同而有所改变i. 电极必须留心保养,电极效率较难定出绝对标准,且也很难确认是否足够应付实际需要。
故平时所得经验及厂商所提供数据,可加一系数做计算,以为电极需求参考。
C. 中和剂(Neutralizer):a. NaHSO3是可用的Neutralizer之一,其原理皆类似Mn+7 or Mm+6 or Mn+4(Neutralizer)-> Mn+2 (Soluable)b. 为免于Pink Ring,在选择Acid base必须考虑。
HCI及H2SO4系列都有,但Cl易攻击Oxide Layer,所以用H2SO4为Base的酸较佳c .药液使用消耗分别以H2SO4及Neutralizer,用Auto-dosing 来补充,7.222 .整条生产线的考虑A. Cycle time :每Rack(Basket)进出某类槽的频率(时间)B. 产能计算:(Working hours / Cycle time)*( FIight Bar / Hoist)*(Racks/FlightBar)*(SF/Rack)= SF/MonC. 除胶渣前Pre-baking对板子的影响:见图7.5MM弓O!a. 由于2.在压合后己经过两次Cure,结构会比1,3 Cure更完全,故Baking会使结构均一,压板不足处得以补偿。
b. 多量的氧,氧化了Resin间的Bon di ng,使咬蚀速率加剧2~3倍。
且使1,2,3区较均一。
c. 释放Stress,减少产生Void的机会.7.2.2.3. 制程内主要反应及化学名称A .化学反应:a . 主要反应4MnO4- + 40H- + Epoxy —4MnO4= + CO2 T + 2H2Ob. 副反应:2MnO4- + 2OH- <--> 2MnO4= + 1/2O2 + H2O (Side reaction)MnO4= + H2O (CI- /SO4= /Catalize Rx.) —MnO2j + 2GH1/2O2(Precipitation formation)2MnO4= + NaOCI + H2O —2MnO4 - + 2OH- + NaCI4MnO4= + NaS2O8 + H2SO4 —4MnO4 - + 2OH- + 2Na2SO44MnO4= + K2S2O8 + H2SO4 —4MnO4 - + 2OH- + 2K2SO4(For Chemical regeneration type process reaction)2MnO4= + 1/2 O2 + H2O <--> 2MnO4 + 2 OH-(Electrolytic reaction: Need replenish air for Oxgen consumption)B. 化学品名称:MnO4- Permanganate NaS2O8 Sodium PersulfateMn04=Mangan ate S2O4-SulfateOH-Hydroxide(Caustic)CO2Carbon DioxideNaOCI Sodium Hydrochloride MnO2 Mangan ese Dioxide7.2.24 典型的Desmear Process:见表7.225. Pocket Void 的解释:A. 说法一:Sweller 残留在Glass fiber 中,在Thermal cycle 时爆开。
B. 说法二:见图7.6a •压板过程不良Stress 积存,上钖过程中力量释出所致b •在膨涨中如果铜结合力强,而 Resin 释出Stress 方向呈Z 轴方向,当Curing 不良而Stress 过大时则易形成a 之断裂,如果孔铜结合力弱则易形成B 之Resin recession ,结合力好而内部树脂不够强轫则出现c 之Pocket voidC •如果爆开而形成铜凸出者称为Pull away 7.2.3 化学铜(PTH)PTH 系统概分为酸性及碱性系统,特性依基本观念而有不同。
723.1酸性系统:A.基本制程:Con diti oner — Microetch — Catalpretreatme nt— Cataldeposit —Accelerator —Electroless DepositB.单一步骤功能说明:a. 整孑L Conditioner :1. Desmear后孔内呈现Bipolar现象,其中Cu呈现高电位正电,Glass fiber、Epoxy 呈负电2. 为使孔内呈现适当状态,Conditioner具有两种基本功能⑴Cleaner : 清洁表面(2)Conditioner :使孔壁呈正电性,以利Pd/Sn Colloid负电离子团吸附3. 一般而言粒子间作用力大小如表因而此类药液系统会有吸附过多或Colloid过多的吸附是否可洗去之顾虑4. Conditioner 若Drag In 至Activator 槽,会使Pd+ 离子团降低b. 微蚀Microetch1. Microetching旨在清除表面之Conditioner所形成的Film2. 此同时亦可清洗铜面残留的氧化物c. 预活化Catalpretreatment1. 为避免Microetch形成的铜离子带入Pd/Sn槽,预浸以减少带入2. 降低孔壁的 Surface Tensiond. 活化 Cataldeposit1. 一般Pd 胶体皆以以下结构存在: 见图7.72. Pd2+ : Sn2+ : Cl- = 1 : 6: 12 较安定3. 一般胶体的架构方式是以以下方式结合:见图 7.8用,且其半径较大使其吸附不易良好,尤其如果孔内的 Roughness 不适当更可 能造成问题4. 孔壁吸附了负离子团,即中和形成中和电性e. 速化 AcceleratorComp ・r © 2030■ 9当吸附时由于Cl 会产生架桥作匕"讪1毎序应丽 Sfi1. Pd胶体吸附后必须去除Sn,使Pd2+曝露,如此才能在未来无电解铜中产生催化作用形成化学铜2. 基本化学反应为:Pd+2/S n+2 (HF) —Pd+2(ad) + Sn+2 (aq)Pd+2(ad) (HCHO) —Pd(s)3. 一般而言Sn 与Pd 特性不同,Pd 为贵金属而Sn 则不然,因此其主反应可如下:Sn+2a Sn+4 + 6F- —SnF6-2 or Sn+2 + 4F- —SnF4-2而Pd 则有两种情形:PH>=4 Pd+2 + 2(OH)- —Pd(OH)2PH<4 Pd+2 + 6F- —PdF6-44. Pd 吸附在本系统中本身就不易均匀,故速化所能发挥的效果就极受限制。