克劳斯硫回收工艺事故整理
克劳斯硫回收工艺生产中存在问题和改进措施研究

克劳斯硫回收工艺生产中存在问题和改进措施研究摘要:本文主要对国能榆林化工有限公司180万t/a甲醇厂现阶段使用的三三级克劳斯转化工艺技术进行论述,根据当下现状,围绕着生产期间引发硫磺回收率提不上来、管线堵塞、反应器床层存在积碳等现象的因素展开深入分析,同时从生产操作参数和原料气控制的角度提出解决办法。
在实行了上述措施后,硫磺的回收率从原先的97.05%飙升到98.10%的水平,并且尾气中的二氧化硫含量也减少了许多。
关键词:克劳斯硫回收工艺;生产环节;存在问题;改进措施;探究与论述引言随着我国煤化工项目数量的连年增长,同时装置也朝着大型化与规模化的方向转变,进一步加剧了国内大气污染的程度。
基于此,近两年我国环保法规已经提高了生产企业的大气污染物排放标准,对各生产企业而言,综合治理废气显然是目前最为紧要的任务之一。
在煤化工的生产期间,废气是燃烧了大量的原料煤、燃料煤才产生的。
我国绝大部分的煤化工生产企业在净化合成气方面,基本都是以低温甲醇洗技术为主,用于分离其中的二氧化硫和二氧化碳等成分,随后再将其转移到硫回收装置当中,完成最后的深度处理环节。
本文就主要针对国能榆林化工有限公司当中的甲醇厂的实际情况,分析了对于克劳斯硫回收的实际工艺情况和生产阶段当中的问题,提出了全新的解决措施和优化方案。
1硫回收的工艺分析现阶段,国内外已经研发出了许多种不同的硫回收工艺技术,其中比较常见的有生物法硫回收、液相直接氧化工艺等等。
液相直接氧化工艺在硫的粗脱环节出现率较高,比如栲胶法脱硫、ADA法脱硫等都是比较典型的工艺技术。
固定床催化氧化工艺、生物法硫回收工艺均可实现高效回收硫磺,尤其是在尾气处理的标准比较严格时就能派上很大用场。
其中,克劳斯回收装置是目前固定床催化氧化硫回收中最具代表性的一项技术。
它主要用在炼厂气和含硫化氢气体回收硫等处理过程中,近年来凭借着回收硫磺纯度高、简单易操作、投资少和占地面积小等优势,在相关领域中极受追捧[1]。
超级克劳斯硫璜回收装置在设计、运行中存在的问题及优化方案

超级克劳斯硫璜回收装置在设计、运行中存在的问题及优化方案超级克劳斯硫璜回收装置在设计、运行中存在的问题及优化方案摘要:超优克劳斯工艺基础是富氧燃烧,通过控制富氧空气与酸性气的比例来控制进入超级克劳斯反应器中硫化氢的浓度。
过量的氧进入下游反应器,也会造成反应器床层温度剧烈波动,严重时会发生燃烧反应,损坏设备。
关键词:废锅液流捕集器过程气工艺管线催化剂床层化学当量燃烧过氧国电赤峰化工有限公司硫回收装置采用的是荷兰荷丰超优/超级克劳斯专利技术,由赛鼎工程有限公司详细设计,日产硫磺25.4吨。
2012年12月17日开车投产,2013年3月20日-3月27日超级克劳斯硫酸盐化结束,超级克斯反应器投用,并成功引入氧气,采用富氧操作模式,至今运行比较稳定,排放达标。
针对超优克劳斯反应特点,就开车中存在的重大安全隐患问题做简单介绍并给出解决方案,以供同行借鉴和参考。
一、硫回收装置在设计中存在的问题我公司硫磺回收装置采用的超优/超级克劳斯工艺,其基础是以比值控制富氧空气流量实现硫化氢部分燃烧。
紧急停车后再开车的燃烧过程中,会造成废锅出口过程气过氧,引起克劳斯反应器催化剂床层温度剧烈波动,从而使催化剂活性降低、烧结、粉碎,减少催化剂使用寿命。
另外过程气工艺管线管道壁会残存硫化亚铁,当过程气中氧含量高时,会引发硫化亚铁与氧气燃烧反应,从而损坏管道、设备。
基于上述安全隐患,必须对原有工艺管线进行改造。
原工艺流程简图如下:改造后的工艺简图:燃料气二、改造方案综合考虑,本着投资少、见效快、大大降低安全隐患的原则,在主体设备不动的情况下,对设备管线进行了如下改造。
1.从废锅出口过程气工艺管线PG61501-400上引一条副线PG61519-300到液流捕集器出口阀后与尾气管线相连接;2.废锅出口过程气工艺管线PG61501-400上增加总阀DN400,并且为夹套蝶阀,使用0.5MPa低压蒸汽伴热;3.废锅出口过程气副线PG61519上两端各增加DN300夹套蝶阀做为隔离使用,并使用使用0.5MPa低压蒸汽伴热;4.废锅出口过程气副线PG61519一定要有倾斜度,保证液体自流;管线使用三根0.5MPa低压蒸汽伴热,防止由于阀门内漏造成硫磺堵塞。
浅谈硫磺回收装置工艺特点与应急救援处置方法

<匕£•矣会•此2021年第21期应急救援或谈硫磺回收装置工艺特点与应急救援处置方法张华东中国石油消防应急救援吉林石化支队吉林市132022摘 要:硫磺回收装置将上游装置排出的硫化氢、氨、一氧化碳等废气利用克劳斯工艺加工回收99. 8%的硫磺。
简述未能回收气体通过循环加氢、反复加工达到完全回收的目的。
简介硫磺回收装置生产过程中存在硫化亚铁、氢气、氨气等危化品的储罐、设备发生火灾爆炸的条件,以及存在硫化氢、氨气泄漏的风险;介绍装置生产中应对各种危险的专项处置方案,明确在火灾爆炸和气体泄漏事故时的工艺处置措施和消防应急措施,以及现场人员如何做好警戒与防护,确保事故状态下应急处置救援在安全可控的状态下进行。
关键词:硫磺回收;硫化氢;工艺特点;应急处置2021年2月份,吉林市某化工厂发生硫化氢泄漏中毒事故,造成5人死亡8人受伤,硫化氢 气体在生产管理与应急处置再次成为舆论热议话题。
国家、地方再次对危化品安全生产企业进行全面风险排查,对有毒气体生产使用企业及不符合污染物国家排放标准的企业进行限期整改。
硫化氢属于高毒性酸性气体,无色,与空 气混合易形成爆炸性混合物,遇明火、高温能形成燃烧爆炸;低浓度时有臭鸡蛋味,因其高浓度时对人体中枢神经有麻醉作用,所以在高浓度硫化氢环境中的人员更不易发觉硫化氢存在,高浓度硫化氢更易发生群体中毒事故。
石油中含硫,含硫量因石油产地不同而各存差异:在原油及炼化中间产品加工过程中,硫经常作为杂质被脱除,而除硫方法经常是以加氢方法将单质硫转化为硫化氢,硫磺回收装置就是将硫化氢以酸性气的形式进行脱除回收,以达到快速除硫的目的;这样既保证原料与成品的纯度,也确保了生产装置长周期运转不被腐蚀。
该方法在化工生产中占比非常高,常减 压、催化裂化、联合芳烃等化工主要生产装置均以该方法脱除生产原料中硫化氢和氨等物质;但脱除的物质必须要实现有效处置,确保作 业环境与生产的安全,这就要求石油化工生产行业合理回收处置硫化氢,在保证安全环保的前提下合理利用硫化氢属性,使其转化为可利用 的产品,切实达到石油化工生产节能创效、安作者简介:张华东,男,主要从事石油化工消防救援技术、全环保的根本目的。
超级克劳斯硫回收装置压力高的原因分析及处理

超级克劳斯硫回收装置压力高的原因分析及处理[日期:2012-05-14] 来源:作者:刘彩锋吕富强[字体:大中小]兖州煤业榆林能化有限责任公司为了实现60万t/a甲醇项目中酸性气处理合格,尾气达标排放,采用了荷兰荷丰公司的超级克劳斯硫磺回收技术。
在装置运行过程中一度出现压力高的问题,给尾气达标排放带来诸多困难,且严重影响了硫回收装置的长周期运转。
为了维持正常的生产,不得不把送至硫回收装置的酸性气部分送至火炬焚烧后放空,既减少了对硫磺的回收,又造成了环境污染。
此外,前系统双炉运行,低温甲醇洗装置送至硫回收的酸性气平均浓度为24.43%,硫回收酸性气主管道流量为1071 m3/h,分流管道流量为379 m3/h,低压氧气流量为302 m3/h,此时装置为超级克劳斯模式运行时系统压力PI17101/02/03为0. 065 MPa左右(设计压力为0.06 MPa时报警,0.075 MPa时装置联锁跳车)。
若酸性气浓度继续提高或送至硫回收装置的酸性气量增加时,系统在超级克劳斯模式运行时,压力将继续上涨至不能满足装置长期运行。
为此,进行了原因分析和整改。
1.来自低温甲醇洗装置的酸性气夹带甲醇多,且我公司曾停用新鲜水约半年,未对酸性气进行洗涤,使酸性气中夹带的碳氢化合物在燃烧过程中形成了大量烟灰,随着酸性气的后移烟灰沉积在瓷球及催化剂上,堵塞了瓷球或催化剂间隙,进而加大了系统阻力,导致系统压力不断升高。
2.硫回收切气后由于主燃烧内空气与燃料气亚当量燃烧时间偏短,空气过量较快,导致废热锅炉后除沫器烧毁,且停车后超级克劳斯仍有大量空气进入,超级硫冷凝器和液硫捕集器、除沫器极易烧毁,烧毁的除沫器和附着的硫磺形成的黑色板结固体是导致系统压力升高的又一原因。
3.系统运行期间硫磺与FeS等腐蚀产物、耐火材料及催化剂碎屑混合时,会产生难以清除的灰色硫磺(混凝土硫磺)堵塞液硫管线,一般位于硫冷凝器与夹套旋塞阀之间的管线及旋塞阀后十字头处,导致系统压力升高。
克劳斯催化剂失活的原因及特征
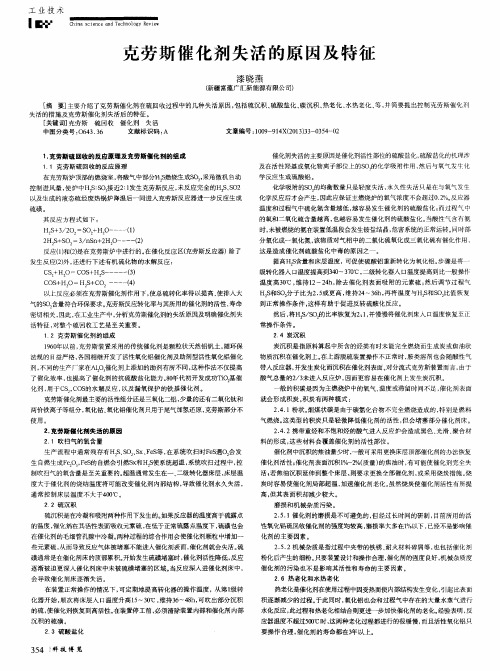
催化剂 失活的主要 原因是催化 剂活性部位 的硫酸盐化 ,硫酸盐化 的机 涉 及在 活性羟基 或氧化 物离 子部位上 的sO 的化 学吸 附作用 ,然后 与氧气 发牛化 学 反应生 成硫酸 铝 。
化学吸 附的SO,的均衡 数量只是 轻度 失活 ,永久性 失活只是 在与氧 气发生 化学 反应后 才会产 生 ,因此应保 证主燃烧 炉 的氧 气浓度 不会超 过0.2%。反 应器 温 度和过程 气 中硫化氢 含量越 低 ,越 容易 发生催化 剂的硫 酸盐化 ;而 过程气 中 的氧和二 氧化硫 含量越 高 ,也越容易 发生催 化剂 的硫酸盐 化 。当酸性 气含有 氨 时 ,未被 燃烧的氨在 装置低温 段会发生铵 盐结 晶,危害系统 的正常运转 。同时部 分 氧化成 一氧 化氮 ,该物质 对气相 中的二 氧化硫 氧化成 三氧化 硫有催 化作用 , 这是造 成催 化剂硫 酸盐 化 中毒 的原 因之一 。
工 业 技பைடு நூலகம்术
I■
克劳 斯 催 化 剂失 活 的 原 因及 特征
漆 晓燕
(新疆 富蕴 广汇新 能源 有 限公司)
[摘 要]主要 介绍 了克 劳 斯催化 剂在 硫 回收过 程 中的几 种失 活原 因 ,包 括硫沉 积 、硫 酸盐化 、碳沉 积 、热老 化 、水热 老化 、等 ,并简 要提 出控制 克劳 斯催 化
克劳斯硫回收操作规程
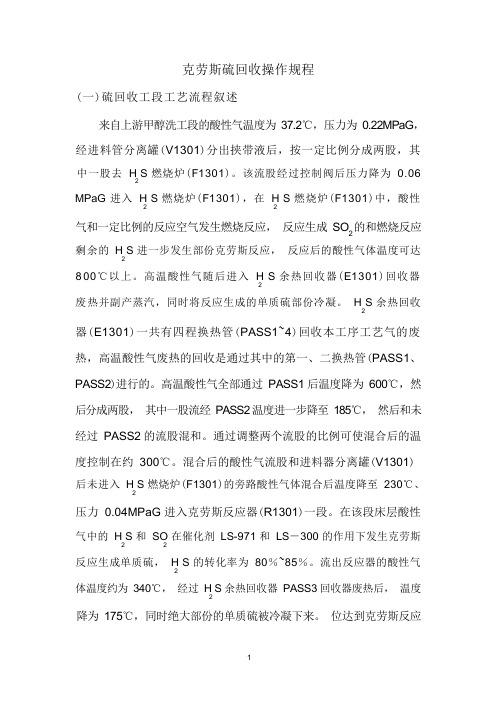
克劳斯硫回收操作规程(一)硫回收工段工艺流程叙述来自上游甲醇洗工段的酸性气温度为37.2℃,压力为0.22MPaG,经进料管分离罐(V1301)分出挟带液后,按一定比例分成两股,其中一股去H S 燃烧炉(F1301)。
该流股经过控制阀后压力降为0.06 2MPaG 进入H S 燃烧炉(F1301),在H S 燃烧炉(F1301)中,酸性2 2气和一定比例的反应空气发生燃烧反应,反应生成SO的和燃烧反应2剩余的H S 进一步发生部份克劳斯反应,反应后的酸性气体温度可达2800℃以上。
高温酸性气随后进入H S 余热回收器(E1301)回收器2废热并副产蒸汽,同时将反应生成的单质硫部份冷凝。
H S 余热回收2器(E1301)一共有四程换热管(PASS1~4)回收本工序工艺气的废热,高温酸性气废热的回收是通过其中的第一、二换热管(PASS1、PASS2)进行的。
高温酸性气全部通过PASS1 后温度降为600℃,然后分成两股,其中一股流经PASS2 温度进一步降至185℃,然后和未经过PASS2 的流股混和。
通过调整两个流股的比例可使混合后的温度控制在约300℃。
混合后的酸性气流股和进料器分离罐(V1301)后未进入H S 燃烧炉(F1301)的旁路酸性气体混合后温度降至230℃、2压力0.04MPaG 进入克劳斯反应器(R1301)一段。
在该段床层酸性气中的H S 和SO 在催化剂LS-971 和LS-300 的作用下发生克劳斯2 2反应生成单质硫,H S 的转化率为80%~85%。
流出反应器的酸性气2体温度约为340℃,经过H S 余热回收器PASS3 回收器废热后,温度2降为175℃,同时绝大部份的单质硫被冷凝下来。
位达到克劳斯反应器二段所需的温度,流程中设置了第一再加热器 (E1302),酸性气进入该加热器预热到约238℃后进入克劳斯反应器二段继续进行克劳斯反应以回收剩余的硫。
在二段反应床中,H S 的转化率约为75%,反2应后的酸性气温度约为255℃。
关于硫回收工艺总结

当前硫回收方法主要有湿法和干法脱硫,干法又分为:传统克劳斯法、亚露点类克劳斯工艺,还原吸收类工艺、直接氧化类克劳斯工艺、富氧克劳斯工艺、和氧化吸收类克劳斯工艺;湿法主要有鲁奇的低、高温冷凝工艺、托普索的WSA工艺。
1干法脱硫1.1常规克劳斯(Claus)法克劳斯法是一种比较成熟的多单元处理技术,是目前应用最为广泛的硫回收工艺。
其工艺过程为:含有硫化氢的酸性气体在克劳斯炉内燃烧,使部分硫化氢氧化为二氧化硫,二氧化硫再与剩余的未反应的硫化氢在催化剂上反应生成硫磺。
传统克劳斯法的特征为:1)控制n(O2):n(H2S)=1:2,若氧气含量过高有SO2溢出,过低则降低H2S的脱除效率;2)需要安装除雾器脱除气流中的硫以提高硫回收量;3)克劳斯法硫总回收率为94%-96%;4)对含可燃性成分的气体如煤气,或当硫质量分数低于40%时不宜用克劳斯法。
1.2亚露点类克劳斯工艺所谓的亚露点工艺是以在低于硫露点的温度下进行克劳斯反应为主要特征的工艺。
主要包括Sulfreen、Hydrosulfreen、Carbonsulfreen、Oxysulfreen、CBA、ULTRA、MCRC、Clauspol 1500、Clauspol 300、Clisulf SDP、ER Claus、Maxisulf等工艺。
1.3还原吸收类工艺还原吸收类工艺由于将有机硫及SO2等转化为H2S再行吸收,故总硫回收率可达99.5%以上。
主要有SCOT、Super-SCOT、LS-SCOT、BSR/Amine、BSR/Wet Oxidation、Resulf、AGE/Dual Solve、HCR、Parsons/BOC Recycle、Sulfcycle和ELSE工艺。
1.4直接氧化类工艺直接氧化是指H2S在固体催化剂上直接氧化成硫,实际上乃是克劳斯原型工艺的新发展。
直接氧化法工艺技术的关键是研制出选择性好、对H2O 和过量O2不敏感的高活性催化剂,目前用铁基金属氧化物的不同混合物制备。
克劳斯硫回收工艺事故整理

克劳斯硫回收工艺事故整理1.硫磺开工烧坏人孔1999年8月15日16:30,某炼油厂硫磺回收装置操作员在巡检时发现炉人孔烧坏。
事故经过:1999年7月10日,硫磺回收装置按计划点炉开工,7月10日点焚烧炉F-202,11日23:25时点燃烧炉F-101,14日点尾气炉F-201,转化器、炉开始烘烤,7月23日烘炉完毕;7月29日至30日R-101、R-102、R-201装催化剂,8月6日重新点火开工,8月13日引酸气入燃烧炉,系统继续升温,8月15日加大酸气入炉量,到16:30发现燃烧炉人孔烧坏而紧急停工。
事故分析:造成主燃烧炉人孔烧坏的主要原因是:1、燃烧炉F-101衬里材料选材错误。
2、风量表偏小,酸气量偏小,造成配风过大,主燃烧炉超温。
3、主要仪表存在不少问题:酸气超声波流量计无指示,H2S/SO2比值分析仪无法投用,SO2、O2分析仪不准,火焰检测仪无法投用等问题。
4、整个人孔被错误用保温材料包得严严实实。
)5、操作人员经验不足。
采取措施:8月20日至9月20日修复衬里,校验风量流量表,更换超声波流量计。
经验教训:“三查四定”时要认真仔细,对各关键设备内衬里选材要严格确认,避免开工后出现衬里不能经受操作温度的纰漏。
2. 开工过程中造成燃烧炉外壁超温1999年10月1日,某炼油厂硫磺回收装置燃烧炉外壁超温。
事故经过:1999年9月20日燃烧炉人孔烧坏处理完毕后,24日重新点火升温,29日产出合格硫磺,10月1日发现主燃烧炉外壁超温而紧急停工。
事故分析:1、燃烧炉衬里问题2、开工引酸气量较大,酸气量波动大,造成炉膛温度过高。
采取措施:紧急停工,修复燃烧炉衬里经验教训:在烘炉完毕后,打开燃烧炉人孔检查衬里时,要严格按照裂缝的条数和尺寸进行审核,不合格就要返工,别把缺陷带到开工后。
3. 停工过程废热锅炉露点腐蚀报废事故经过:2000年3月27日,硫磺回收装置停工,28日发现烟道法兰处漏出铵盐,4月3日拆开F-202人孔,E-202头盖试漏发现废锅E-202内管程穿。
硫磺回收装置、酸性水汽提装置的事故案例

我将我这几天收集到的有关硫磺回收装置、酸性水汽提装置的事故案例进行分享,希望能起到抛砖引玉的效果。
1、大庆石化硫磺回收酸性水原料罐爆炸事故2004年10月27日9时44分,中石油大庆石化分公司炼油厂硫磺回收车间V402原料水罐发生重大爆炸事故,死亡7人,直接经济损失192.27万元。
10月20日,大庆石化分公司所属二级单位炼油厂的硫磺回收车间,64万吨/年酸性水汽提装置V403原料水罐发生撕裂事故,造成该装置停产。
为尽快修复破损设备,恢复生产,炼油厂机动处根据大庆石化分公司与大庆石化总厂关联交易安全生产合同,把抢修作业委托给大庆石化总厂工程公司第一安装工程公司。
该公司接到大庆石化分公司炼油厂硫磺回收车间V403原料水罐维修计划书后,安排下属的四分公司承担该次修复施工任务。
在修复过程中,需要将V406与V407两个水封罐以及原料水罐V402与V403的连接平台吊下。
10月27日8时,四分公司施工员带领16名施工人员到达现场。
8时20分,在炼油厂硫磺回收车间设备主任、设备员等人员的指导配合下,施工员带领两名管工开始在V402罐顶进行安装第17块盲板作业。
8时25分,吊车起吊V406罐和V402罐连接管线,管工将盲板放入法兰内,并在盲板与上法兰之间放入一根电焊条以备吹扫。
硫磺回收车间设备员随后指挥对该管线用氮气进行吹扫。
8时30分,硫磺回收车间开具了二级用火票。
8时45分,吹扫完毕后,管工将法兰螺栓拧紧。
9时20分左右,施工员到硫磺回收车间安全员处取回火票,并叫人把火票送给V402罐顶气焊工。
同时硫磺回收车间设备主任、设备员、监火员和操作工也到达V402罐顶。
9时40分,气焊工开始在V402罐顶排气线0.8米处动火切割。
9时44分,管线切割约一半时,V402罐发生爆炸着火。
事故发生后,大庆石化分公司和大庆石化总厂立即启动了事故应急预案。
大庆石化总厂消防支队迅速调动10多台消防车展开扑救工作。
直到10时45分,大火才被彻底扑灭。
克劳斯硫回收系统常见问题及优化改进措施

克劳斯硫回收系统常见问题及优化改进措施摘要:近年来,随着环保形势日益严峻,煤化工与石油化工企业多采用克劳斯工艺进行对硫化氢酸性气进行处理。
克劳斯硫回收不仅回收了硫单质,创造了经济效益,而且降低了烟气脱硫成本。
但在其运行过程中存在不稳定因素,影响到生产效率的提高,现就常见问题进行原因分析,并提出了优化改进措施。
关键词:克劳斯硫回收;环保设施;经济效益晋煤集团天溪煤制油分公司年产30万t甲醇装置,变换气经低温甲醇洗脱除H2S后,经过再生浓缩生成25%~35%的H2S高浓度酸性气,送往年产0。
8万t克劳斯硫回收装置。
本装置采用分流法三级克劳斯工艺,硫回收率达到98%左右,运行相对稳定。
1克劳斯硫回收工艺介绍按照酸性气中H2S含量的区别,克劳斯法硫回收工艺分三种:直接氧化法、部分燃烧法以及分流法。
通常酸性气里面的H2S体积浓度小于15%时采取直接氧化法;H2S体积浓度超过50%时采取部分燃烧法;H2S浓度位于两者之间采取分流法。
我公司采用分流法:将三分之一的酸性气体通入燃烧炉,加入空气使其燃烧生成SO2,而其余三分之二酸性气走旁路,绕过燃烧室,与燃烧后的气体汇合进入催化剂床层进行反应。
克劳斯硫回收装置工艺流程主要有传统克劳斯工艺、超级克劳斯工艺和带有SCOT尾气处理的克劳斯工艺等。
其中传统克劳斯工艺三级转换,要求H2S、SO2摩尔比值为2的条件下进行;超级克劳斯工艺是在两级普通克劳斯转化之后,第三级改用选择性氧化催化剂,将H2S直接氧化成元素硫,硫回收率可以从98%提升至99。
5%;而带有SCOT尾气处理的克劳斯工艺,通过第三级加氢还原将过程气中的SO2和单质硫转化为H2S,同时将COS和CS2水解为H2S,采用MDEA吸收尾气中的H2S,胺溶液经加热再生循环使用,再生塔顶的酸性气送制硫燃烧炉,吸收塔顶尾气送尾气焚烧炉燃烧后达标排放。
我公司采用传统三级克劳斯工艺,尾气送至锅炉进行焚烧,炉内进行干法脱硫后,通过镁法脱硫,实现环保排放合格。
某化工克劳斯回收硫案例.
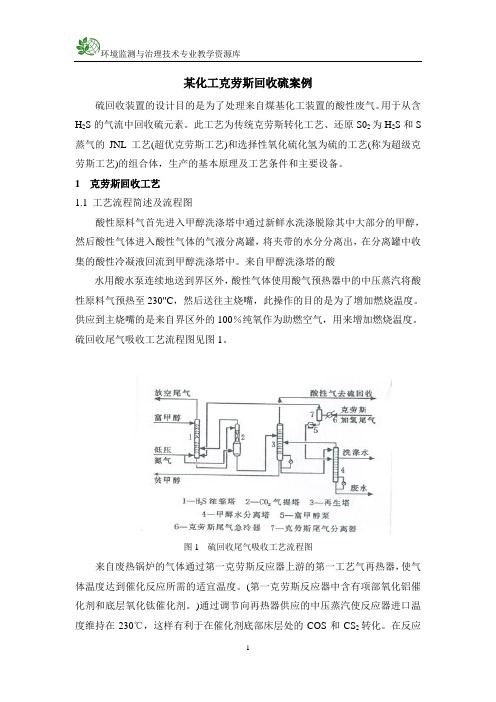
某化工克劳斯回收硫案例硫回收装置的设计目的是为了处理来自煤基化工装置的酸性废气。
用于从含H2S的气流中回收硫元素。
此工艺为传统克劳斯转化工艺、还原S02为H2S和S 蒸气的JNL工艺(超优克劳斯工艺)和选择性氧化硫化氢为硫的工艺(称为超级克劳斯工艺)的组合体,生产的基本原理及工艺条件和主要设备。
1 克劳斯回收工艺1.1 工艺流程简述及流程图酸性原料气首先进入甲醇洗涤塔中通过新鲜水洗涤脱除其中大部分的甲醇,然后酸性气体进入酸性气体的气液分离罐,将夹带的水分分离出,在分离罐中收集的酸性冷凝液回流到甲醇洗涤塔中。
来自甲醇洗涤塔的酸水用酸水泵连续地送到界区外,酸性气体使用酸气预热器中的中压蒸汽将酸性原料气预热至230"C,然后送往主烧嘴,此操作的目的是为了增加燃烧温度。
供应到主烧嘴的是来自界区外的100%纯氧作为助燃空气,用来增加燃烧温度。
硫回收尾气吸收工艺流程图见图1。
图1 硫回收尾气吸收工艺流程图来自废热锅炉的气体通过第一克劳斯反应器上游的第一工艺气再热器,使气体温度达到催化反应所需的适宜温度。
(第一克劳斯反应器中含有项部氧化铝催化剂和底层氧化钛催化剂。
)通过调节向再热器供应的中压蒸汽使反应器进口温度维持在230℃,这样有利于在催化剂底部床层处的COS和CS2转化。
在反应器中,工艺气体中H2S和S02在催化剂上发生反应直到达到平衡。
来自第一反应器的工艺气体进入第一硫冷凝器E-22502中冷却。
工艺气体通过第二工艺气体再热器E-32509,随后在第二克劳斯反应器R-32502(含有氧化钛催化剂,用于COS /CS2的进一步转换)中进行转换。
1.2 焚烧炉超级克劳斯尾气(或旁路操作时的克劳斯尾气)和来自液硫槽的放空气中含有的残留H2S和其它硫化物是不能直接向大气排放的,所以这些气体要在焚烧炉Z-32504中焚烧,使残留的H2S和硫化物在焚烧炉内与过量氧气反应转化为S02。
进焚烧炉的气体与高温废气混合后温度升高,高温气体是在焚烧炉烧嘴Z-32502处燃烧所得的,进烧嘴的燃料气流量是通过控制焚烧炉的温度进行调节的,燃料气燃烧时需要的助燃空气由鼓风机供应。
克劳斯硫回收工艺生产中存在问题和改进措施

进 措施 。
其次 , 剩余 的 H s与生成 的 s 0 。 在催化 剂作 用下 ,
进 行克劳斯 反应 , 生成单 质硫 : 2 H 2 S + S O 2 - -  ̄ 3 S + 2 H 2 0 + Q( 催 化反应 ) 由于受化 学平 衡 的 限制 ,两级 催化 转 化 的常规 C l a u s工艺硫 回收率为 9 0 % ~ 9 5 % ,三级转化 也只能 达
石立军, 井云环
( 神华 宁煤集 团煤炭化学 工业分公司 , 宁夏
摘 要
银川 7 5 0 4 1 1 )
介绍 了神华 宁煤集 团煤炭 化学工业 分公 司 2 5万 t / a甲醇厂 目前采用 的三级 克劳斯转 化 、 三 级冷
凝硫 回收工艺技 术 , 结合 生产 实 际情况 , 分 析 了生产 过程 中管 线堵 塞 、 反 应器 床层 及管 线 积炭 、 硫 磺 回收 率低
到9 5 % 9 8 % , 因此 , 常规 C l a u s工 艺 的尾 气 中硫 化 物
的排 放 量 已不 能 满 足 现 行 环 保 标 准 的要 求 ,所 以
C l a u s硫 回收装置 一般都 配有 相应 的尾气处 理单 元 ,
1 硫 回收 工艺 基 本 概 况
目前 国内外硫 回收工 艺种类 繁多 , 常 用硫 回收工 艺 有液相 直接氧化工艺 、 固定床催 化氧化 工艺 和生物
法 硫 回收工 艺 。液相 直接 氧化 工艺 适用 于硫 的 “ 粗
这 些先进 的尾气处 理 单元 或与 硫 回收装 置组合 为一 个 整体装置 , 或单独成 为一 个后续装 置[ 。
克劳斯硫回收装置产出黑色硫磺原因分析及处理措施
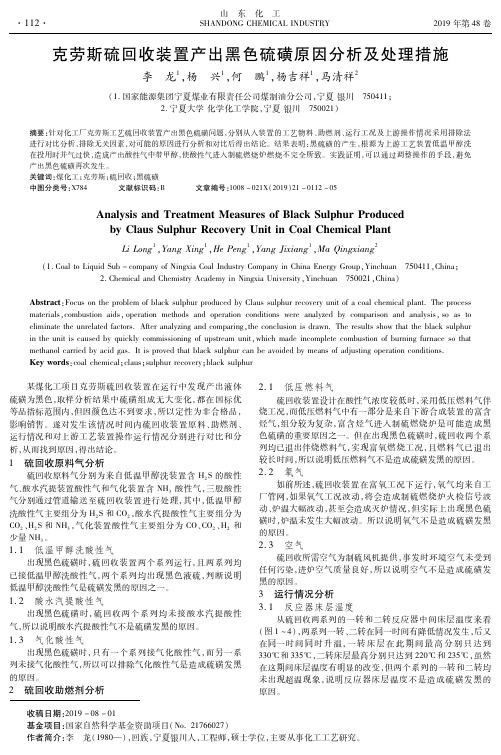
山 东 化 工 收稿日期:2019-08-01基金项目:国家自然科学基金资助项目(No.21766027)作者简介:李 龙(1980—),回族,宁夏银川人,工程师,硕士学位,主要从事化工工艺研究。
克劳斯硫回收装置产出黑色硫磺原因分析及处理措施李 龙1,杨 兴1,何 鹏1,杨吉祥1,马清祥2(1.国家能源集团宁夏煤业有限责任公司煤制油分公司,宁夏银川 750411;2.宁夏大学化学化工学院,宁夏银川 750021)摘要:针对化工厂克劳斯工艺硫回收装置产出黑色硫磺问题,分别从入装置的工艺物料、助燃剂、运行工况及上游操作情况采用排除法进行对比分析,排除无关因素,对可能的原因进行分析和对比后得出结论。
结果表明:黑硫磺的产生,根源为上游工艺装置低温甲醇洗在投用时并气过快,造成产出酸性气中带甲醇,使酸性气进入制硫燃烧炉燃烧不完全所致。
实践证明,可以通过调整操作的手段,避免产出黑色硫磺再次发生。
关键词:煤化工;克劳斯;硫回收;黑硫磺中图分类号:X784 文献标识码:B 文章编号:1008-021X(2019)21-0112-05AnalysisandTreatmentMeasuresofBlackSulphurProducedbyClausSulphurRecoveryUnitinCoalChemicalPlantLiLong1,YangXing1,HePeng1,YangJixiang1,MaQingxiang2(1.CoaltoLiquidSub-companyofNingxiaCoalIndustryCompanyinChinaEnergyGroup,Yinchuan 750411,China;2.ChemicalandChemistryAcademyinNingxiaUniversity,Yinchuan 750021,China)Abstract:FocusontheproblemofblacksulphurproducedbyClaussulphurrecoveryunitofacoalchemicalplant.Theprocessmaterials,combustionaids,operationmethodsandoperationconditionswereanalyzedbycomparisonandanalysis,soastoeliminatetheunrelatedfactors.Afteranalyzingandcomparing,theconclusionisdrawn.Theresultsshowthattheblacksulphurintheunitiscausedbyquicklycommissioningofupstreamunit,whichmadeincompletecombustionofburningfurnacesothatmethanolcarriedbyacidgas.Itisprovedthatblacksulphurcanbeavoidedbymeansofadjustingoperationconditions.Keywords:coalchemical;claus;sulphurrecovery;blacksulphur 某煤化工项目克劳斯硫回收装置在运行中发现产出液体硫磺为黑色,取样分析结果中硫磺组成无大变化,都在国标优等品指标范围内,但因颜色达不到要求,所以定性为非合格品,影响销售。
克劳斯硫回收尾气处理工艺技改总结
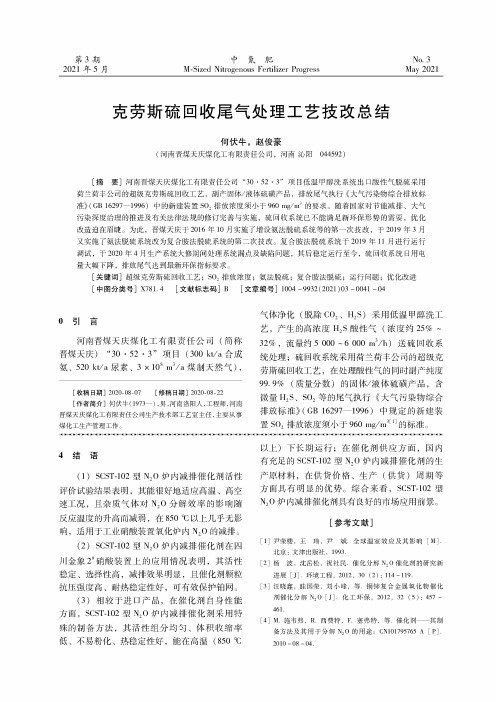
第3期3 2221年5月中3氮3肥M-Sized Nitrogenons Feoilizco ProgressNg933May2221克劳斯硫回收尾气处理工艺技改总结何伏牛,赵俊豪(河南晋煤天庆煤化工有限责任公司,河南沁阳644502)[摘要]河南晋煤天庆煤化工有限责任公司“30•52•3”项目低温甲醇洗系统出口酸性气脱硫采用荷兰荷丰公司的超级克劳斯硫回收工艺,副产固体/液体硫磺产品,排放尾气执行《大气污染物综合排放标准)(GB17227—1996)中的新建装置S02排放浓度须小于96。
m//m8的要求。
随着国家对节能减排、大气污染深度治理的推进及有关法律法规的修订完善与实施,硫回收系统已不能满足新环保形势的需要,优化改造迫在眉睫。
为此,晋煤天庆于2016年5月实施了增设氨法脱硫系统等的第一次技改,于2019年3月又实施了氨法脱硫系统改为复合胺法脱硫系统的第二次技改。
复合胺法脱硫系统于2015年17月进行运行调试,于2020年4月生产系统大修期间处理系统漏点及缺陷问题,其后稳定运行至今,硫回收系统日用电量大幅下降,排放尾气达到最新环保指标要求。
[关键词]超级克劳斯硫回收工艺;S01排放浓度;氨法脱硫;复合胺法脱硫;运行问题;优化改进[中图分类号]X787.4[文献标志码]B[文章编号]1004-9932(2027)03-0047-042引言河南晋煤天庆煤化工有限责任公司(简称晋煤天庆)“32•52•3”项目(322kt/a合成氨、522k/a尿素、3x107m^a煤制天然气),[收稿日期]2729-07-07[修稿日期]2727-07-20[作者简介]何伏牛(1973—)男,可南洛阳人,工程师,可南晋煤天庆煤化工有限责任公司生产技术部工艺室主任,主要从事煤化工生产管理工作。
^-0-4结语(1)SCST-102型NO炉内减排催化剂活性评价试验结果表明,其能很好地适应高温、高空速工况,且杂质气体对NO分解效率的影响随反应温度的升高而减弱,在850C以上几乎无影响,适用于工业硝酸装置氧化炉内NO的减排。
硫回收克劳斯炉事故应急救援预案范本(3篇)
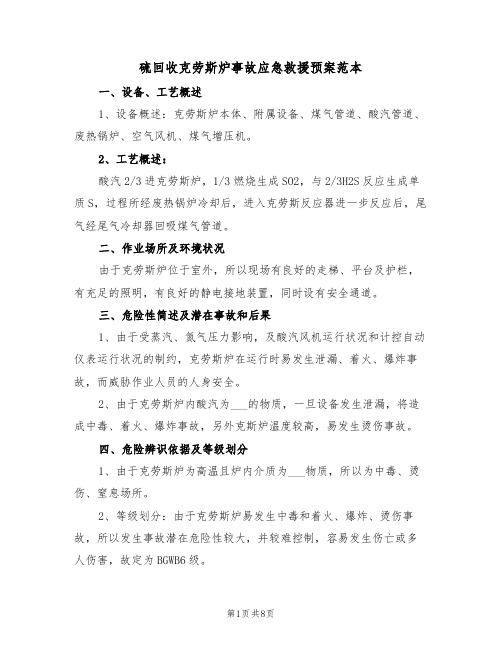
硫回收克劳斯炉事故应急救援预案范本一、设备、工艺概述1、设备概述:克劳斯炉本体、附属设备、煤气管道、酸汽管道、废热锅炉、空气风机、煤气增压机。
2、工艺概述:酸汽2/3进克劳斯炉,1/3燃烧生成SO2,与2/3H2S反应生成单质S,过程所经废热锅炉冷却后,进入克劳斯反应器进一步反应后,尾气经尾气冷却器回吸煤气管道。
二、作业场所及环境状况由于克劳斯炉位于室外,所以现场有良好的走梯、平台及护栏,有充足的照明,有良好的静电接地装置,同时设有安全通道。
三、危险性简述及潜在事故和后果1、由于受蒸汽、氮气压力影响,及酸汽风机运行状况和计控自动仪表运行状况的制约,克劳斯炉在运行时易发生泄漏、着火、爆炸事故,而威胁作业人员的人身安全。
2、由于克劳斯炉内酸汽为___的物质,一旦设备发生泄漏,将造成中毒、着火、爆炸事故,另外克斯炉温度较高,易发生烫伤事故。
四、危险辨识依据及等级划分1、由于克劳斯炉为高温且炉内介质为___物质,所以为中毒、烫伤、窒息场所。
2、等级划分:由于克劳斯炉易发生中毒和着火、爆炸、烫伤事故,所以发生事故潜在危险性较大,并较难控制,容易发生伤亡或多人伤害,故定为BGWB6级。
五、该部位岗位工作内容及人员1、工作内容:⑴控制酸汽、空气、煤气、压力、流量,保证克劳斯炉装置压力、温度。
⑵控制蒸汽压力,保证液硫系统温度,生产合格的硫磺。
2、工作人员:克劳斯炉工硫回收工长六、事前控制措施及负责人1、严格工艺操作,稳定设备运行。
2、认真做好设备维护和保养工作。
3、设备运行每天有专人检查和管理。
4、___职工做好酸汽系统设备着火、中毒事故预防的学习,提高职工自我保护意识。
设备负责人:设备主任生产负责人:生产主任总负责人:行政主任七、事故应急措施1、如克劳斯炉本体发生大量酸汽泄漏及着火事故,现场人员立即通知中控室,指令硫铵停酸汽风机,酸汽停止进炉,改进吸煤气管道。
2、中控室人员调整酸汽、煤气及空气量配比,降低炉温。
克劳斯硫回收装置危险物质分析与安全控制
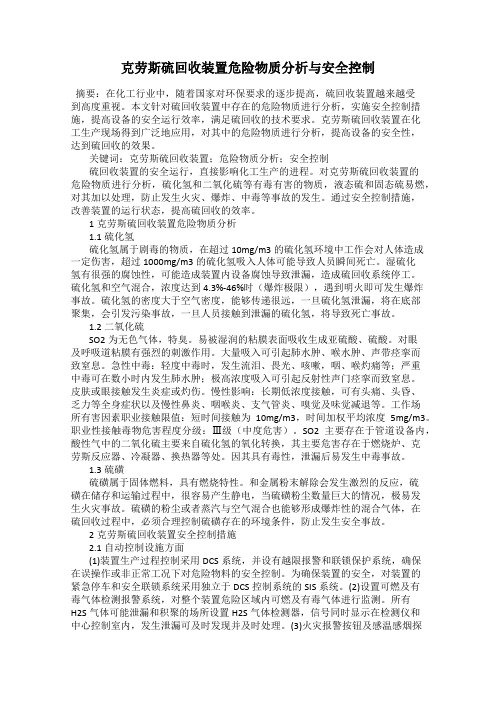
克劳斯硫回收装置危险物质分析与安全控制摘要:在化工行业中,随着国家对环保要求的逐步提高,硫回收装置越来越受到高度重视。
本文针对硫回收装置中存在的危险物质进行分析,实施安全控制措施,提高设备的安全运行效率,满足硫回收的技术要求。
克劳斯硫回收装置在化工生产现场得到广泛地应用,对其中的危险物质进行分析,提高设备的安全性,达到硫回收的效果。
关键词:克劳斯硫回收装置;危险物质分析;安全控制硫回收装置的安全运行,直接影响化工生产的进程。
对克劳斯硫回收装置的危险物质进行分析,硫化氢和二氧化硫等有毒有害的物质,液态硫和固态硫易燃,对其加以处理,防止发生火灾、爆炸、中毒等事故的发生。
通过安全控制措施,改善装置的运行状态,提高硫回收的效率。
1克劳斯硫回收装置危险物质分析1.1硫化氢硫化氢属于剧毒的物质,在超过10mg/m3的硫化氢环境中工作会对人体造成一定伤害,超过1000mg/m3的硫化氢吸入人体可能导致人员瞬间死亡。
湿硫化氢有很强的腐蚀性,可能造成装置内设备腐蚀导致泄漏,造成硫回收系统停工。
硫化氢和空气混合,浓度达到4.3%-46%时(爆炸极限),遇到明火即可发生爆炸事故。
硫化氢的密度大于空气密度,能够传递很远,一旦硫化氢泄漏,将在底部聚集,会引发污染事故,一旦人员接触到泄漏的硫化氢,将导致死亡事故。
1.2二氧化硫SO2为无色气体,特臭。
易被湿润的粘膜表面吸收生成亚硫酸、硫酸。
对眼及呼吸道粘膜有强烈的刺激作用。
大量吸入可引起肺水肿、喉水肿、声带痉挛而致窒息。
急性中毒:轻度中毒时,发生流泪、畏光、咳嗽,咽、喉灼痛等;严重中毒可在数小时内发生肺水肿;极高浓度吸入可引起反射性声门痉挛而致窒息。
皮肤或眼接触发生炎症或灼伤。
慢性影响:长期低浓度接触,可有头痛、头昏、乏力等全身症状以及慢性鼻炎、咽喉炎、支气管炎、嗅觉及味觉减退等。
工作场所有害因素职业接触限值:短时间接触为10mg/m3,时间加权平均浓度5mg/m3。
职业性接触毒物危害程度分级:Ⅲ级(中度危害)。
- 1、下载文档前请自行甄别文档内容的完整性,平台不提供额外的编辑、内容补充、找答案等附加服务。
- 2、"仅部分预览"的文档,不可在线预览部分如存在完整性等问题,可反馈申请退款(可完整预览的文档不适用该条件!)。
- 3、如文档侵犯您的权益,请联系客服反馈,我们会尽快为您处理(人工客服工作时间:9:00-18:30)。
克劳斯硫回收工艺事故整理1.硫磺开工烧坏人孔1999年8月15日16:30,某炼油厂硫磺回收装置操作员在巡检时发现炉人孔烧坏。
事故经过:1999年7月10日,硫磺回收装置按计划点炉开工,7月10日点焚烧炉F-202,11日23:25时点燃烧炉F-101,14日点尾气炉F-201,转化器、炉开始烘烤,7月23日烘炉完毕;7月29日至30日R-101、R-102、R-201装催化剂,8月6日重新点火开工,8月13日引酸气入燃烧炉,系统继续升温,8月15日加大酸气入炉量,到16:30发现燃烧炉人孔烧坏而紧急停工。
事故分析:造成主燃烧炉人孔烧坏的主要原因是:1、燃烧炉F-101衬里材料选材错误。
2、风量表偏小,酸气量偏小,造成配风过大,主燃烧炉超温。
3、主要仪表存在不少问题:酸气超声波流量计无指示,H2S/SO2比值分析仪无法投用,SO2、O2分析仪不准,火焰检测仪无法投用等问题。
4、整个人孔被错误用保温材料包得严严实实。
)5、操作人员经验不足。
采取措施:8月20日至9月20日修复衬里,校验风量流量表,更换超声波流量计。
经验教训:“三查四定”时要认真仔细,对各关键设备内衬里选材要严格确认,避免开工后出现衬里不能经受操作温度的纰漏。
2. 开工过程中造成燃烧炉外壁超温1999年10月1日,某炼油厂硫磺回收装置燃烧炉外壁超温。
事故经过:1999年9月20日燃烧炉人孔烧坏处理完毕后,24日重新点火升温,29日产出合格硫磺,10月1日发现主燃烧炉外壁超温而紧急停工。
事故分析:1、燃烧炉衬里问题2、开工引酸气量较大,酸气量波动大,造成炉膛温度过高。
采取措施:紧急停工,修复燃烧炉衬里经验教训:在烘炉完毕后,打开燃烧炉人孔检查衬里时,要严格按照裂缝的条数和尺寸进行审核,不合格就要返工,别把缺陷带到开工后。
3. 停工过程废热锅炉露点腐蚀报废事故经过:2000年3月27日,硫磺回收装置停工,28日发现烟道法兰处漏出铵盐,4月3日拆开F-202人孔,E-202头盖试漏发现废锅E-202内管程穿。
因设计布局问题,转化器进出口法兰无法加盲板,导致转化器自燃使F-202炉内SO2超标而无法进炉作业,直到4月11日才开始消缺。
造成废锅E-202的管程有一半给铵盐堵上,内侧共堵34根,外侧共堵26根,F-202部分衬里、烟囱衬里部分损坏。
事故分析:造成废锅E-202管束因露点腐蚀报废的原因:1、由于2万吨/年硫磺回收装置开工后,尾气处理部分一直没有开,尾气焚烧炉含硫高,露点腐蚀严重。
2、3月27日停炉后没有及时关闭液硫池蒸汽喷射器造成废锅温度急降,水蒸汽和二氧化硫反应产生H2SO3腐蚀。
采取措施:1、4月11日开始消缺,清通E-202管程,并将腐蚀穿孔的管用堵头堵死。
2001年3月更换E-202废锅。
2、F-202及烟囱修复衬里。
3、烟道处更换热电偶,调校废锅E-202安全阀。
经验教训:开工过程中必须先点焚烧炉,尾气须经尾气处理部分,防止因尾气中二氧化硫含量过高,腐蚀设备。
4.焚烧炉点火闪爆事故事故经过:2003年11月某日晚21时,某硫磺回收装置焚烧炉进行开工点火。
共进行了三次点火。
前两次因为小火嘴没点着,然后拆清火嘴,所用时间较长。
第三次点火时先将辅助燃烧器点着,22:10在点主燃烧器时,没有及时点着主火嘴而发生闪爆,造成尾气中压蒸汽过热器西侧弯头箱鼓起,烟囱内墙体被震塌。
原因分析:1、对炉膛的吹扫时间不够,没有严格按照变更管理程序进行危害识别和风险评估,将吹扫时间由原定的5分钟改为3分钟,导致在点火过程中炉膛吹扫不彻底。
2、点火过程操作不当,没有严格按照操作规程去点火。
点火过程中,进炉膛的瓦斯流量一直是由调节阀控制,该调节阀关不严,导致一定量的瓦斯串入炉膛。
3、点火前没有对火盘进行认真检查,未能及时发现主燃烧器火盘变形,火盘将原应伸出的辅助燃烧器挡住,辅助燃烧器的火焰无法将主火嘴喷出的瓦斯点燃。
防范措施:1、对点火操作开展HSE风险评估,使参加点火操作的职工对点火过程的风险有较深刻的认识。
2、炉子点火过程中的每一个步骤都要严格按照操作规程进行,并且经过岗位、班长及车间三级确认后才能进行下一步骤,要求有确认签名表。
3、点火过程由当班班长统一指挥,装置主管及工艺员监督落实,吹扫时间按原来的5分钟不变,内漏的调节阀要及时处理好,确保仪表完好,符合工艺要求方可进行点火操作。
经验教训:对经过检修的燃烧炉、焚烧炉的主、辅燃烧器的安装情况要加强检查,确保符合设计要求。
5.尾气旁路管线硫化亚铁自燃事件事故经过:硫磺回收装置尾气旁路管线是一条DN800的管线,其作用是当尾气部分需要临时停下抢修的时候,给硫磺装置克劳斯反应后的过程气直接排放到焚烧炉提供通道。
此管线没有任何的监测仪表。
2003年10月27日22:30左右,硫磺装置在停工完成后,装置处于静置状态的第一个晚上,当班操作工在巡检的过程中,发现旁路管线的裸露部分发红,当班人员立即用蒸汽对发红的部位进行掩护,避免了管线的大面积灼烧损坏。
原因分析:1、对硫化亚铁的认识不足,装置在停工的过程中,只认识到硫化亚铁对大型设备的危害,对有可能发生硫化亚铁自燃的大型设备都进行了钝化处理,而忽略了硫化亚铁对管线的危害,没有对管线处理。
(实际上没有办法处理)2、管线在生产过程中,由于硫蒸汽的串入,生成大量的硫化亚铁。
在装置停下静置的时候,由于空气从焚烧炉反串进入,造成管线内的硫化亚铁自燃。
3、由于此管线没有安装任何的仪表,内操无法通过仪表监控。
经验教训:1、停工前对停工过程及设备开展HSE风险识别活动,充分认识可能存在硫化亚铁自燃的设备,从而落实防范措施。
2、装置在停工过程中尽可能对所有的设备管线进行钝化处理,对无法钝化处理的管线应该通入蒸汽或氮气保护,避免当停汽后发生硫化亚铁自燃。
3、给一些大型的管线安装温度检测仪表,便于内操通过计算机监控。
外操在设备停下后要加强巡检,用便携测温计测量设备管线表面温度,以便及时发现有硫化亚铁自燃的管线设备,及时处理,避免烧坏设备。
4、给直径大于DN200的管线安装蒸汽吹扫掩护,以便在发生硫化亚铁自燃的时候可以迅速扑灭。
5、给所有大型设备安装冷水喷淋系统,以便当设备发生硫化亚铁自燃时可以用水浇灭,避免损坏设备。
6. 开工烘炉仪表失灵,炉子烧坏1996年11月20日,某厂3万吨/年硫磺回收装置初次试车烘炉,因反应炉红外线测温仪故障,造成反应炉衬里烧坏,壳体局部烧红,影响开工时间,同时造成了约为二十几万元的经济损失。
事故经过:11月14日,该装置点炉,对反应炉衬里进行干燥,生产车间严格按炉子衬里厂家提供的烘炉曲线进行升温,到11月20日16时,炉子800℃恒温结束,开始以10℃/时的速度升温,当班操作员逐渐增加燃料气和空气流量,但反应炉红外线测温仪表温度指示无上升趋势,于是操作员至现场查找原因,发现反应炉和废热锅炉连接处外壳已烧红。
于是装置做停工处理,反应炉熄火降温,待炉子降至常温后,打开炉子和废热锅炉人孔,发现废热锅炉入口衬里部分烧坏脱落,壳体璧厚减薄,法兰变形。
事故原因:1、红外线测温仪仪表由于反吹风量不够,镜片上积灰,造成检测仪误差。
2、红外线测温仪从国外进口,施工单位没有按照说明书在炉子温度500℃以下安装热电偶,使得在低温段红外仪测量不准时,无热电偶校正,造成红外仪校正误差增大。
3、红外线测温仪安装不当,使得检测发生误差。
经验教训:1、对红外线测温仪这种高精度进口仪器,今后设计施工和用户单位都应了解清楚才能投入使用。
2、加拿大delta公司设计用风机空气作为仪表吹扫介质不合适,应改为仪表风来吹扫。
3、反应炉用单点温度测量不可靠,应增加一点热电偶测温点。
7.开工装剂造成反应器催化剂泄漏1996年10月6日,某厂3万吨/年硫磺回收装置,反应器催化剂泄漏。
事故经过:10月6日,该装置中交后,按计划向反应器装填催化剂,催化剂装填前,国外专家进入反应器进行确认,并按外商要求准备好催化剂装填所需要的用具,在外商监督下对三个反应器催化剂逐一进行装填,当装至第二个反应器时,操作员打开该反应器下部人孔检查,发现有大量催化剂泄漏至反应器底部及硫冷凝器入口管箱,于是停止装催化剂,同时打开第一反应器人孔检查,也发现有类似情况,经过与外商商量,决定把已装入反应器的催化剂全部取出。
事故原因:1、反应器设计不合理,设计时没有把丝网与格栅和反应器衬里内壁固定,催化剂装填时丝网边角有间隙,催化剂从间隙漏至反应器底部。
2、反应器内壁有加强圈,在加强圈周围丝网安装质量差,丝网与加强圈有明显间隙,有部分催化剂从此出漏下。
3、装置采用进口催化剂,其包装为体积约1立方米软包装,因此催化剂装填流速快,造成丝网边角不平,催化剂泄漏。
采取措施:催化剂全部从反应器卸出,过筛后重新装填。
经验教训:1、催化剂装填前应详细检查丝网与反应器衬里内壁是否固定,是否按要求执行。
2、催化剂装填应采用特制的催化剂装填漏斗,均匀控制装填速度。
8.烘炉期间炉子熄火,造成瓦斯轻微爆炸1999年6月13日,某硫磺回收反应炉烘炉期间,由于炉子熄火,瓦斯阀未能及时关闭,造成瓦斯轻微爆炸。
事故经过:6月10日,该装置初次点火烘炉,反应炉和反应器同时用瓦斯燃烧升温,6月13日4时,反应炉由于火焰太小被风吹灭,反应炉此时温度仅为250℃左右,因此温度上升变化不大,操作员未能发现炉子熄火,瓦斯继续通入反应炉。
大约20分钟后,明火造成反应炉发生轻微爆炸,操作员听到爆炸后跑到现场关闭瓦斯阀门,此次事故没有造*员伤亡和财产损失。
事故分析:反应炉熄火没有及时发现,瓦斯继续进入反应炉造成。
采取措施:及时关闭瓦斯现场闸阀及入炉手阀。
经验教训:1、内操监盘认真,能发现重要参数的微小变化,处理事故镇静迅速;.2、现在的新工艺炉子熄火克劳斯部分部分自动停车,瓦斯切断阀门自动关闭;3、为了有效的在装置异常时保护设备,联锁都要按要求投用。
9.废热锅炉放水阀忘记关,造成设备损坏事故经过:1997年2月25日,某硫磺回收紧急停工后开工,25日零点引酸性气入装置,按正常生产进行调节,由于系统温度较低,操作员把废热锅炉底部排污阀打开以降低液面,开阀后便回操作室,忘记关掉阀门。
装置压力逐渐升高,系统温度却逐渐下降,直至反应器入口温度降到69℃,系统压力升至40千帕,装置被迫停工。
停工后进入设备检查发现废热锅炉管焊口开裂。
事故原因:从现状说明,该设备是由于液面过低,上水过急造成的。
废热锅炉开排污是很经常的工作,主要是责任心不强造成,当发现干锅时应该实施“叫水”操作,还有液位的情况下可以加脱氧水,没有液位时应该先缓缓通蒸汽降温,再加水。
采取措施:停工检修:经验教训:操作人员责任心不够强,此类关键设备的操作,最好两人同时到现场,确保操作正确,另外防止忘记关排污阀等类似隐患发生的可能性。