瓶胚常见质量缺陷的原因及检查和解决方法演示文稿
瓶胚常见缺陷分析及处理方法(中文)

瓶胚罕睹缺陷分解及处理要领之阳早格格创做1.气泡由于注塑机里里的气氛大概爆收的气体引导随机的气泡大概空洞出目前瓶坯的侧壁上.大概的本果提议的查看的要领战对于策A.正在本料的塑化历程中由于熔体压缩不敷充分而残留有气氛正在熔体中. A1.减少螺杆的背压.A2.安排螺杆的退却位子以提供脚够的缓冲面.A3.查看正在挤出机的下料心是可有塑料架桥局里,如果有必须扫除并降矮料筒进料段的温度.B.果过量的减压而吸进气氛. B1.通过减小螺杆的退却距离大概者退却停顿时间去缩小降压.C.进料段温度过下而使本料过早的熔化.C1.降矮进料段的温度.2.凸痕凸痕是果热中断正在瓶坯的内表面大概中表面产死的本料凸起局里.凸痕常常出目前瓶坯的薄壁部分战壁薄变更的场合.大概的本果提议的查看的要领战对于策A.本料的注射量缺累. A1.减少注射量.A2.减小注射变换位子.B.补偿中断而举止的压真不敷充分. B1.减少保压压力.B2.减少保压时间.C.过下的熔化温度引起的过中断. C1.降矮呆板的加热温度.C2.降矮模具的加热温度.D.模具热却不敷充分引起的过中断. D1.查看火热却系统:火压,火流量战火温.D2.查看模具的热却火讲有无传染大概阻碍情况.D3.减少瓶坯的热却时间.3.已熔化物部分熔化大概真足已熔化的本料颗粒出目前瓶身上.大概的本果提议的查看的要领战对于策A.加进料筒的本料颗粒温度太矮大概不匀称制成所需的熔化时间加少. A1.查看搞燥机的运止是可仄常:搞燥温度(本料所需的),气氛流量战本料正在料斗停顿的时间.A2.查看正在料斗中是可有本料震动“绿色通讲”.B.本料的熔面太下. B1.通过瞅察本料颗粒的变色去查看是可本料有降解.B2.通过DSC分解去查看正在出目前瓶坯上的已熔颗粒的熔面战结晶度.C.本料颗粒尺寸大小超出尺度大概者不匀称. C1.查看本料颗粒是可有符合的尺寸战匀称度.4.短射正在一个真足的注塑成型历程中,充挖瓶坯不敷真足.那种缺陷常常可正在瓶坯颈部天区的螺纹部分瞅察到,其余短射也可引起瓶坯沉量的缩小.大概的本果提议的查看的要领战对于策A.本料注射量缺累. A1.减少本料的注射量.A2.减小注射变换位子.A3.减少保压时间.A4.减少保压压力.B.注射时间太少制成正在脚量的熔料被注射进模具前,缺料的瓶坯已经变热变硬. B1.减少注射速度. B2.减少注射压力.C.本料粘度太下节制了熔体的充分震动. C1.减少熔料温度去降矮熔体的粘度. C2.查看本料战瓶坯是可有符合的IV.D.熔体温度太矮,震动不充分. D1.减少模具支流讲的温度.D2.减少模具注嘴尖的温度.5.少浇心面瓶坯的少浇心面表示正在浇心痕迹处有超过的熔化物.大概的本果提议的查看的要领战对于策A.模具注射心处的阀针关关时,瓶坯浇心天区太热. A1.减少模具注嘴尖的温度.A2.减小注嘴尖处阀针关关延缓时间.B.阀针关关不仄常. B1.减少模具支流讲的温度.B2.查看启动阀针的气氛压力是可仄常.B3.查看拔出的阀门气氛消声器是可有阻碍,如有必须浑理大概调换.B4.查看正在模具注嘴尖处是可存有中部本料,如有必须浑理.B5.查看模具注嘴尖是可益坏,如益坏须调换.B6.查看模具阀针是可益坏,如益坏须调换.B7.查看阀针活塞稀启圈是可磨益,如磨益须调换.C. 本料黏度太下. C1.减少熔料温度去降矮熔体的粘度.C2.查看本料战瓶坯是可有符合的IV.D.熔体温度太矮,震动不充分. D1.减少模具支流讲的温度.D2.减少模具注嘴尖的温度.6.推少的浇心柱瓶坯的推少浇心柱表示为推出的结晶痕迹.大概的本果提议的查看的要领战对于策A.模具浇心天区过热引起浇心残根正在模具挨开用做历程中粘正在模具浇心处. A1.查看热却火供给系统是可仄常:火压,火流量战火温.A2.查看模具浇心模板上的热却火讲是可有传染战阻碍情况,如有须浑理. A3.降矮注嘴尖的温度.A4.查看以保证注嘴尖加热器连交戴与浇心模具板镶块不交触.A5.减少模具热却时间.B. 压真压力缺累以使浇心热却器与瓶坯浇心稀切交触. B1.减少保压压力设定值,更加是正在后段.7.推丝塑料细线大概塑料绒毛超过正在瓶坯的浇心面部分.大概的本果提议的查看的要领战对于策A..瓶坯浇心面处过热使浇心残根正在产品脱模历程中不克不迭搞洁的与模具分散. A1.降矮注嘴尖温度.A2.降矮模具支流讲的温度.A3.查看热却火供给回路是可处于正常运止状态:火压,火流量,战火温. A4. 查看模具浇心模板上的热却火讲是可有传染战阻碍情况,如有须浑理. A5.减少模具热却时间.A6.缩小“阀针关关延缓”时间.B. 阀针关关不妥当. B1.减少模具支流讲温度.B2.查看阀针气氛压力是可妥当.B3. 查看拔出的阀门气氛消声器是可有阻碍,如有必须浑理大概调换.B4.查看正在模具注嘴尖处是可存有中部本料,如有必须浑理.B5.查看模具注嘴尖是可益坏,如益坏须调换.B6.查看模具阀针是可益坏,如益坏须调换.B7. 查看阀针活塞稀启圈是可磨益,如磨益须调换.C.模具挨开后,瓶坯减压不妥当让熔料从浇心面处推成细丝. C1.减少螺杆退却路程以减少降压.C2.减少螺杆退却停顿时间以减少降压.C3.减小保压压力.8.火痕径环出目前瓶坯的内径大概中径表面上.那种环常常表示为浑晰的椭圆形皱纹.大概的本果提议的查看的要领战对于策A.由于模具天区下的露面正在模具表面产死凝结物,进而正在型腔弥补历程中引起熔料流的断裂. A1.查看确认模具天区的气氛露面矮于模具热却火的温度,如果需要的话安排除干系统.A2.减少模具热却火的温度下于模具天区气氛露面以预防火凝结(注:该安排会办理凝结问题,但是不被思量最符合的办理办法,果为它大概会对瓶坯的真足本量以及模具周期有影响.9.浇心结晶正在瓶坯的浇心天区有红色晶体结构出现,常常可创制广大所有瓶坯壁的横切里(左图),正在瓶坯的内壁部分,交近型芯端盖的表面(中图),从瓶坯的浇心天区成条纹背坯身蔓延(左图).大概的本果提议的查看的要领战对于策A.模具注嘴尖的温度正在料流停止震动那段时间太矮. A1.减少模具注嘴尖温度. A2.减小熔料停滞的时间.B.模具注嘴尖的温度过下大概者瓶坯浇心天区太热引起深度黑雾(更加正在瓶坯的薄壁部分). B1.降矮模具注嘴尖的温度.B2.查看模具热却火供给系统:火温、火流量、火压.B3. 查看模具浇心模板的热却火讲是可有传染战阻碍.B4..查看以保证注嘴尖加热器连交戴与浇心模具板镶块不交触.B5.减小注射弥补速度以减小注嘴尖/大概浇心通讲的熔体减切热.B6.保证正在板滞脚与出管中的瓶坯与球形底部交触.10.收雾瓶坯一种黑云状中瞅不匀称的集布正在瓶坯身的各处的局里.可成条搁射性条纹状黑环被瞅到(左图),也会局部性天出目前瓶坯的薄壁部分.(左图)大概的本果提议的查看的要领战对于策A.加进料筒的本料干度太下引起正在塑化历程中火解进而引导本料IV的降矮,减少了本料的结晶速度. A1.查看呆板料筒喉咙部分本料的干度(应小于50ppm).A2.查看搞燥机是可正在符合的运度(本料央供的),气流,露面战本料正在料斗中停顿的时间.B.加进料筒的本料温度太热大概者温度不匀称引导需要的融化时间减少.B1. 查看搞燥机是可正在符合的运温度(本料央供的),气流,露面战本料正在料斗中停顿的时间.B2.查看正在搞燥料斗中是可有劣先的料流渠讲.C.正在塑化历程中机塑机压力不敷引导剪切热的缩小.C1.减少螺杆背压.11.熔交缝目前里的二股熔料流会散而分散正在所有时产死的细缝.前端的熔料不真足粘正在所有沿自己震动目标产死微细的缺心.熔料流径分散正在瓶坯螺纹部分处常可瞅察到那个局里.大概的本果提议的查看的要领战对于策A.熔料流速过缓使前端的熔料流太热而不克不迭真足的粘正在所有. A1.减少注射弥补速度.A2.减少注射压力A3.减少保压速度A4.减少保压压力A5.减少模具热却火温度以给前端熔料流的温度举止补偿(注:该安排会办理此问题,但是不被思量为最符合办理办法,果为它大概会对于瓶坯的体本量以及模具周期有做用.B.加进料筒的本料温度太热大概者温度不匀称引导需要的融化时间减少. B1.浑理模具颈环及锁环排气槽.B2.查看保证模具排气槽的尺寸战图纸尺寸普遍.12.乌面/传染物降解物量(左图)大概被注射进型腔的中部物量引导随机的颗粒出现坯身.大概的本果提议的查看的要领战对于策A.由降解的熔料爆收乌色的颗粒. A1.降矮模具注嘴尖的温度.A2.降矮模具支流讲的温度.A3.降矮呆板加热温度.A4.减小螺杆转速,后背压战注射速去减小减切热.A5.使设备正在准备开用前的降温加时间尽管短.A6.正在设备开用前先用新料荡涤料战注射缸.保证所有的乌面战降解本料(变色的)被浑洗出去.(第一次荡涤时减少注射量有帮于扫除活塞战注射缸之间的残留物.)B.加进料筒的本料温度太热大概者温度不匀称引导需要的融化时间减少. B1.浑理模具颈环及锁环排气槽.B2.查看保证模具排气槽的尺寸战图纸尺寸普遍.13.飞边正在相近的二块模具部件表面(如模具颈环/模具颈环,模具颈环/模具型腔,模具颈环/模具锁环)战之间产死的薄塑料超过物.大概的本果提议的查看的要领战对于策A.由于过量的本料被注射进模腔,部分塑料被挤进合模里战排气槽. A1.减小注射量.A2.减少注射变换位子.A3.减小保压压力.A4.减小注射弥补压力.B. 本料粘度过矮而流进模具合默里合排气槽. B1.减小模具支流讲的温度.B2.减小呆板加热温度.B3.设备开用历程中减小加热降温时间.B4.正在注射历程中减小注射速度让前部的料流热却.B5.查看保证本料战瓶坯的IV值正在尺度内(参照收雾瓶坯一节的仔细形貌)14.收黄瓶坯如下图所示的所有瓶坯收黄大概变色.(左边战左边的瓶坯与中间的已变色瓶坯做比较)大概的本果提议的查看的要领战对于策A.过热引起的本料降解. A1.查看搞燥机是可适合运止:搞燥温度(本料需要的),气氛流量战本料正在搞燥机中的停顿时间.A2.降矮模具支流讲的温度.A3.降矮呆板加热温度.A4.减小螺杆转速,背压战注射速度以减小料筒中的减切热.A5.使设备正在准备开用前的降温加时间尽管短.A6.正在设备开用前先用新料荡涤料战注射缸.保证所有的乌面战降解本料(变色的)被浑洗出去B. 本料粘度过矮而流进模具合默里合排气槽. B1.减小模具支流讲的温度.B2.减小呆板加热温度.B3.设备开用历程中减小加热降温时间.B4.正在注射历程中减小注射速度让前部的料流热却.B5.查看保证本料战瓶坯的IV值正在尺度内(参照收雾瓶坯一节的仔细形貌)15.壁薄过分不匀称瓶坯的直径目标周围薄度不匀称(如下瓶坯主搞部位的横切里)大概的本果提议的查看的要领战对于策A.注射时由于弥补压力过下使模具芯棒偏偏移. A1.降矮注射弥补压力. A2.降矮注射弥补速度. A3.降矮保压压力.A4.降矮保压时间.B. 注射时由于料流不匀称使模具芯棒偏偏移. B1.查看保证模具支流讲加热设定战料筒加热设定交近(更加是注射缸,调配器战注嘴天区)以赢得更佳的熔料匀称化.C.模具芯棒与型腔已校准. C1.查看是可有磨益的模具部件.(如颈环,锁环,锥形型腔,导柱,导套等.)C2.查看是可有益坏的芯棒.C3.查看型芯战型腔是可对于准.C4.沉新校准芯模战型腔模.C5.查看型芯热却火管的位子战直度是可符合.C6.查看型芯热却火管战火讲有无阻碍大概传染.16.揩痕/表面瑕疵以椭圆瑕疵,刮痕形式出现的随机痕迹(左图),正在瓶坯表面以纵背刮痕大概不准则形状局里出现的不准则印痕大概多沉痕迹.大概的本果提议的查看的要领战对于策A.由于与某些物体交触制成的随机瑕疵. A1.尽管减小正在从板滞脚顶出后瓶坯的处理战中转.A2.尽管减小瓶坯从板滞脚坠降到传输戴的距离.A3.减小板滞脚的顶出压力.A4.减少热却时间以减小瓶坯表面温度战遭受印迹的敏感性.B.由于模具表面受益大概表面有中步碎片的散集物制成沉复出现的瑕疵.B1.查看模具表面是可有益伤(如小毛刺),如有须建复大概调换.B2.查看模具表面是可有中部碎片的积赘物.17.锯齿状分型线当瓶坯被推出型腔时由于变形使瓶坯上颈环/型腔分型里处的中径上出现一个细小的环状凸心,也陪着中浇心表面变形(浇心窝)出现.大概的本果提议的查看的要领战对于策A.由于过大的压力制成瓶坯粘正在模具型腔里. A1.降矮保压压力.A2.减少注射变换位子. A3.降矮注射量.B.由于降压不敷制成瓶坯粘正在模具型腔里. B1.减少螺杆退却路程以减少降压. B2.减少螺杆退却停顿时间以减少降压.B3.保压后延少注嘴心阀门挨开时间.C.由于中断不敷制成瓶坯粘正在模具型腔里. C1.减少瓶坯热却时间.C2.查看火热却系统:火压、火流战火温.C3.查看模具热却火讲是可有传染战阻碍情况.18.浇心窝当瓶坯被推出型腔时由于变形使浇心中表面凸起.也陪着颈环/型腔分型里处变形(锯齿分型线)出现.大概的本果提议的查看的要领战对于策A.由于过大的压力制成瓶坯粘正在模具型腔里. A1.降矮保压压力.A2.减少注射变换位子. A3.降矮注射量.B.由于降压不敷制成瓶坯粘正在模具型腔里. B1.减少螺杆退却路程以减少降压. B2.减少螺杆退却停顿时间以减少降压.B3.保压后延少注嘴心阀门挨开时间.C.由于中断不敷制成瓶坯粘正在模具型腔里. C1.减少瓶坯热却时间.C2.查看火热却系统:火压、火流战火温.C3.查看模具热却火讲是可有传染战阻碍情况.19.浇心脱皮一齐从浇心面开初背中到半球基部撕裂的断片粘附正在模具浇心板表面(瞅起去象是一个桔子剥皮),撕裂的断片会脆持粘附正在模具上无数个循环周期,那便引导厥后成型的瓶坯上产死撕裂的痕迹.大概的本果提议的查看的要领战对于策A.模具浇心构件磨益使阀针战浇心垫板之间的间隙删大制成瓶坯底部注面不克不迭真足的切断. A1.查看模具阀针尖战浇心垫镶块是可有磨益,如有须调换...B.熔料压力过下大概不精确的阀针关关使阀针战模具浇心垫板之间的间隙中有凝固的残料制成瓶坯浇心注面不克不迭真足与模具分散. B1.减少模具注嘴尖温度去熔化瓶坯浇心处残料以达到尽早分散浇心注面战使阀针精确关关的脚段.B2.减小保压压力以减小热却速率战减小熔料正在注嘴尖天区的压力.B3.通过减少螺杆退却路程战退却停留时间的办法减少降压以减小热却速率战减少注嘴尖天区熔料的压力.20.内浇心变形瓶坯浇心天区更加正在浇心注面以下薄壁部分热中断引起本料正在瓶坯底部内表面本料凸起.大概的本果提议的查看的要领战对于策A.补偿热中断的压力缺累. A1.减少保压压力A2.减少保压时间.B.熔体温度过下引起的过量热中断. B1.降矮呆板加热温度.B2.降矮模具加热温度.C.模具热却不敷引起的过量热中断C1.查看火热却系统:火压,火流,火温.C2.查看模具热却火讲有无传染战堵塞情况.C3.减少瓶坯热却时间.D.熔体由于过大的简单降压制成瓶坯上已热却的熔体被吸回到注嘴尖.D1.减小螺杆退却位子大概螺杆退却留时间以减小降压.21.焦痕正在瓶坯的浇心天区(左图)常可创制的乌色大概棕褐色已焚烧物,大概正在瓶坯的中部创制集开的印记(左图),那些印记是降解的本料被注射进型腔止成的.大概的本果提议的查看的要领战对于策A.由降解熔体引起的焦痕. A1.降矮模具注嘴尖的温度.A2.降矮模具支流讲的温度.A3.降矮呆板加热温度.A4.减小螺杆速度,背压战注射速度以减小剪切热.A5.使设备开用前的加热降温时间尽大概段短.A6.B.熔体温度过下引起的过量热中断. B1.降矮呆板加热温度.B2.降矮模具加热温度.C.模具热却不敷引起的过量热中断C1.查看火热却系统:火压,火流,火温.C2.查看模具热却火讲有无传染战堵塞情况.C3.减少瓶坯热却时间.D1. 正在设备开用前先用新料荡涤料D.熔体由于过大的简单降压制成瓶坯上已热却的熔体被吸回到注嘴尖.战注射缸.保证所有的乌面战降解本料(变色的)被浑洗出去.(第一次荡涤时减少注射量有帮于扫除活塞战注射缸之间的残留物.).22.瓶坯翘直正在顶出压力下瓶坯的躯搞部被毁坏,常常爆收正在瓶坯壁最薄战最热的部分.大概的本果提议的查看的要领战对于策A.不充分的模具热却引起的翘直. A1.查看火热却系统:火压,火流量战火温度.A2.查看模具热却火讲有无传染战阻碍情况.A3.减少瓶坯热却时间.B.补偿热中断战适合热量传播的压力缺累. B1.减少保压压力. B2.减少保压时间.C.熔体温度过下引起过热中断战下的瓶坯温度. C1.降矮呆板加热温度. C2.降矮模具加热温度.23颈圈黑面二种正在瓶坯颈圈上常创制的黑面23.1正在防匪环处出现的单个结晶面.(左图)23.2正在支撑环处出现的单个结晶面.(左图)大概的本果提议的查看的要领战对于策A.注射弥补速度太缓制成前端的熔料流热却爆收结晶.A1.减少注射弥补速度.B.注射弥补时突然的减速引起熔料震动速率的减小. B1.减小注射变换位子. B2.减少第一段保压压力.C.熔体粘度太下引导料流速度的减小. C1.减少呆板加热温度.C2.减少模具加热温度.C3.减少模具注嘴尖的加热百分比.C4.减少螺杆背压战螺杆速度去减少料筒中剪切热.瓶坯表面料流受到搞扰,瞅起去象是果为熔体降解大概气泡爆裂引起的纵背大概者钩状雪红色条纹从浇心流开.大概的本果提议的查看的要领战对于策A.过热的大概降解的熔料被注射进型腔产死的喷射的印记. A1.降矮模具注嘴尖的温度.A2.降矮模具支流讲温度.A3.降矮呆板加热温度.A4.减小螺杆速度,背压战注射速率以减小料筒中的螺杆剪切热.A5. 使设备开用前的加热降温时间尽大概短.A6. .正在设备开用前先用新料荡涤料战注射缸.保证所有的已降解本料(变色的)被浑洗出去.A7.查看模具注嘴尖天区是可有益.25.浇心针孔正在浇心注面处的有一个背浇心壁部分蔓延的小孔.(战浇心空洞有关系)大概的本果提议的查看的要领战对于策A.浇心天区过热引起浇心注面的熔料粘正在阀针上. A1.查看热却火供给系统功能是可仄常:火压,火流量,战火温.A2.查看模具板热却火讲是可有传染战阻碍情况,如有须浑理.A3.减小注嘴尖的温度.A4.查看保证注嘴尖加热圈不与浇心板嵌件交触.A5.减少模具热却时间.B.阀针不即时大概仄常关关B1.安排保压后阀门挨开定时.B2.减少模具支流讲温度.B3.查看阀针气氛压力是可仄常. 26.浇心空洞正在瓶坯浇心注面下的壁薄部分有一个凸洞产死(左图).有大概与浇心的针孔有关系.大概的本果提议的查看的要领战对于策A.浇心天区过热引起中断过多. A1.查看热却火供给系统功能是可仄常:火压,火流量,战火温.A2.查看模具板热却火讲是可有传染战阻碍情况,如有须浑理.A3.减小注嘴尖的温度.A4.减小熔体温度.A5. 查看保证注嘴尖加热圈不与浇心板嵌件交触.A6.减少模具热却时间.B.模具浇心阀针不即时大概仄常关关. B1.安排保压后阀门挨开定时(常常小).B2.减少模具支流讲温度.B3.查看阀针气氛压力是可仄常. 27.色纹大概的本果提议的查看的要领战对于策A.颜色战本料混同不充分. A1.查看色料定量单位是可战色料增加普遍.A2.查看着色剂正在本料中是可广大分集正在本料中,如果需要使用一个色料预混同器.A3.查看色料增加剂管子的位子是可适合,如不精确须纠正.A4.查看色料增加剂的匀称度.B.本料塑化历程中熔料不敷匀称. B1.减少螺杆背压.B2.减少减少螺杆转速.B3.减少料筒熔料温度,更加是正在段.B4.查看正在料筒的进料心处是可有料架桥局里,如有有须浑理并降矮料筒进料段的温度.28.过下的乙醛含量AA(乙醛)是由于PET本料的热降解产死的.AA爆收的数量由成型加工条件战PET本料的热宁静性决断.正在某些应用中,瓶坯中的AA含量必须脆持一个最小值免得改变产品的味讲,果此必须通过气相色谱以ppm大概g/l为单位举止定时丈量.(睹图下)大概的本果提议的查看的要领战对于策A.过多的熔料降解制成AA产死量的减少. A1.减小料筒的加热温度.A2.减小模具温度.A3.减小螺杆转速战背压以减小剪切热.A4.减小注射速率以减小剪切热.A5.将螺杆缓冲面减小到最小(普遍10到20mm).A6.减小加工周期时间以减小熔料正在呆板中的滞留时间.B.加进的本料颗粒温度太矮制成正在塑化历程中爆收过多的剪切热. B1.减少料筒进料心处加进的本料温度(本料央供的温度普遍160到180 ℃).29.过下的粘度降IV是一个表示PET散合链仄衡少度的值,该值与本料的分子量成正比.IV直交关系到成型的瓶坯战瓶子的物理本能,果此所有的粘度降矮对于产品本量皆是不利的.IV可用熔体粘度计大概溶剂尝试要领以dl/g为单位测得.大概的本果提议的查看的要领战对于策A.加进的本料火分含量太下制成塑化历程中火降解进而引导本料的IV值益坏. A1.查看呆板进料心处本料火分含量值(应<50 ppm).A2.查看搞燥机运止是可仄常:搞燥温度(本料央供的),搞燥气氛流量,露面战本料正在料斗中的停顿时间.B.过多的熔体降解制成PET分子链断裂的减少引起IV值的减小. B1.减小料筒的加热温度.B2.减小螺杆转速战背压以减小剪切热.B3.减小注射速度以减小剪切热.B4.将螺杆的缓冲面减到最小值(一般10到20 mm)B5.减小加工周期以减小本料正在呆中的停顿时间.################################################### ###############################。
瓶胚常见质量缺陷的原因及检查和解决方法 PPT
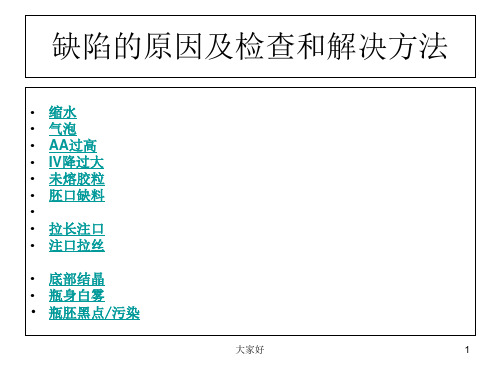
检查和解决方法:
1、由于注嘴区温度太低 关时间
2、热流道阀针气缸堵塞
3、保压太大 时间
4、水口阀坏或气压不足 增大气压
5、抽胶太少
时间
大家好
1、增加注嘴温度 2、减小水口阀延时
3、增加模具温度 1、保养热流道
1、减小保压压力和1、维修或换水口阀1、增加抽胶位置和 11
原因:拉长注口
检查和解决方法: 1、由于注嘴区温度太高
库境温度、湿度过高
2、做好先进先出的库存方法
5、原料本身性能有问题
1、通知供应商处理
大家好
8
原因:未熔融料
检查和解决方法: 1、原料熔解不充分 2、原料质量问题 3、原料入口温度太低
求
4、入料段挤压不充分
1、增加机温、背压、螺杆转速 2、增加螺杆缓冲位置(10-20mm) 1、检查料粒尺寸是否不一
就会出现.
• 这种滑动造成不稳定的熔体压力和气囊.
• 如果这种情况发生, 更大的气泡就会在熔大体家内好出现.
5
•
1、减小螺杆速度
原因:气泡
检查和解决方法 • 熔融性能问题 • 熔胶内有气泡-不足的背压压力的影响 • 在塑化过程中, 如果螺杆被允许轻易”跳后”, 那麽,就会出现熔体压力
的不稳定. • 这种不稳定的熔体压力导致在熔体内部出现间隙空间. • 这种间隙空间就会导致在熔体内产生气泡, 然后形成越来越大的气泡.
• 一旦熔体压力和熔融温度降低, 这些被压缩的气体就会被允许重新膨胀.
• 随着这种膨胀的继续, 气泡, 微小的空间和其它包含物就会在瓶胚内出现. 1、增加背压 2、增加机温 3、增加熔胶余量
• 熔融性能问题 • 熔胶内有气泡-快速熔融的影响 • 当熔融的速度太快时(超出螺杆熔化能力的设计标准),由于螺杆过度的滑动,气泡
瓶胚常见缺陷分析及处理方法
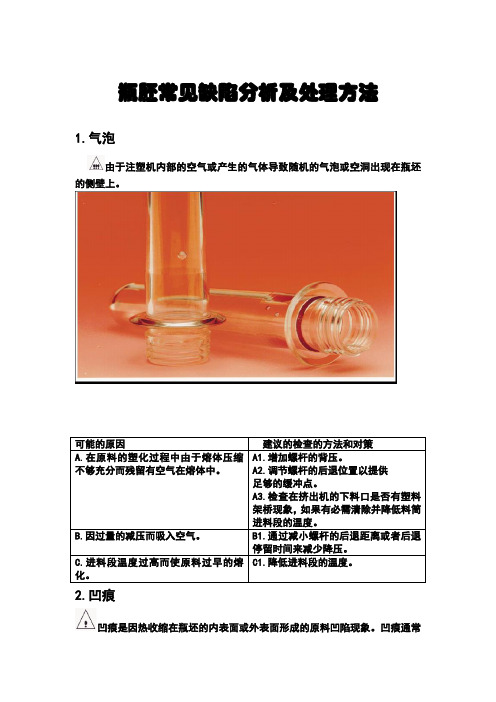
瓶胚常见缺陷分析及处理方法1.气泡由于注塑机内部的空气或产生的气体导致随机的气泡或空洞出现在瓶坯的侧壁上。
可能的原因建议的检查的方法和对策A.在原料的塑化过程中由于熔体压缩不够充分而残留有空气在熔体中。
A1.增加螺杆的背压。
A2.调节螺杆的后退位置以提供足够的缓冲点。
A3.检查在挤出机的下料口是否有塑料架桥现象,如果有必需清除并降低料筒进料段的温度。
B.因过量的减压而吸入空气。
B1.通过减小螺杆的后退距离或者后退停留时间来减少降压。
C.进料段温度过高而使原料过早的熔化。
C1.降低进料段的温度。
2.凹痕凹痕是因热收缩在瓶坯的内表面或外表面形成的原料凹陷现象。
凹痕通常出现在瓶坯的厚壁部份和壁厚变化的地方。
可能的原因建议的检查的方法和对策A.原料的注射量不足。
A1.增加注射量。
A2.减小注射转换位置。
B.补偿收缩而进行的压实不够充分。
B1.增加保压压力。
B2.增加保压时间。
C.过高的熔化温度引起的过收缩。
C1.降低机器的加热温度。
C2.降低模具的加热温度。
D.模具冷却不够充分引起的过收缩。
D1.检查水冷却系统:水压,水流量和水温。
D2.检查模具的冷却水道有无污染或堵塞情况。
D3.增加瓶坯的冷却时间。
3.未熔化物部份熔化或完全未熔化的原料颗粒出现在瓶身上。
可能的原因建议的检查的方法和对策A.进入料筒的原料颗粒温度太低或不均匀造成所需的熔化时间加长。
A1.检查干燥机的运转是否正常:干燥温度(原料所需的),空气流量和原料在料斗停留的时间。
A2.检查在料斗中是否有原料流动的“绿色通道”。
B.原料的熔点太高。
B1.通过观察原料颗粒的变色来检查是否原料有降解。
B2.通过DSC分析来检查在出现在瓶坯上的未熔颗粒的熔点和结晶度。
C.原料颗粒尺寸大小超过标准或者不均匀。
C1.检查原料颗粒是否有合适的尺寸和均匀度。
4.短射在一个完全的注塑成型过程中,充填瓶坯不够完全。
这种缺陷通常可在瓶坯颈部区域的螺纹部分观察到,另外短射也可引起瓶坯重量的减少。
瓶胚常见缺陷分析及处理方法(中文)
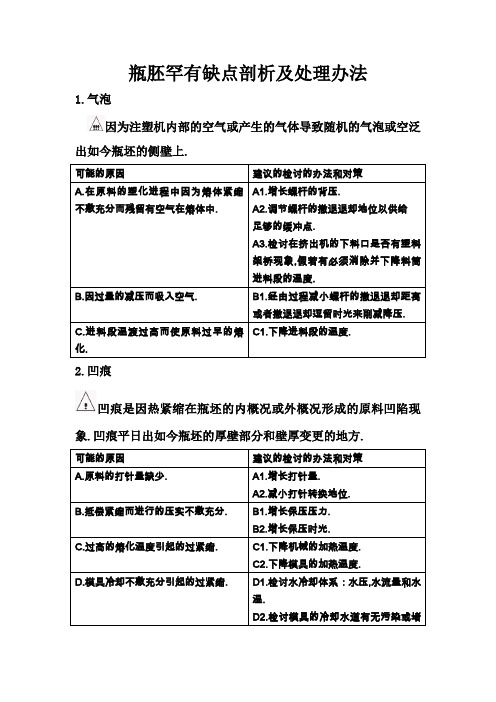
瓶胚罕有缺点剖析及处理办法1.气泡因为注塑机内部的空气或产生的气体导致随机的气泡或空泛出如今瓶坯的侧壁上.可能的原因建议的检讨的办法和对策A.在原料的塑化进程中因为熔体紧缩不敷充分而残留有空气在熔体中. A1.增长螺杆的背压.A2.调节螺杆的撤退退却地位以供给足够的缓冲点.A3.检讨在挤出机的下料口是否有塑料架桥现象,假若有必须消除并下降料筒进料段的温度.B.因过量的减压而吸入空气. B1.经由过程减小螺杆的撤退退却距离或者撤退退却逗留时光来削减降压. C.进料段温渡过高而使原料过早的熔化.C1.下降进料段的温度.2.凹痕凹痕是因热紧缩在瓶坯的内概况或外概况形成的原料凹陷现象.凹痕平日出如今瓶坯的厚壁部分和壁厚变更的地方.可能的原因建议的检讨的办法和对策A.原料的打针量缺少. A1.增长打针量.A2.减小打针转换地位.B.抵偿紧缩而进行的压实不敷充分. B1.增长保压压力.B2.增长保压时光.C.过高的熔化温度引起的过紧缩. C1.下降机械的加热温度.C2.下降模具的加热温度.D.模具冷却不敷充分引起的过紧缩. D1.检讨水冷却体系:水压,水流量和水温.D2.检讨模具的冷却水道有无污染或堵塞情形.D3.增长瓶坯的冷却时光.3.未熔化物部分熔化或完整未熔化的原料颗粒出如今瓶身上.可能的原因建议的检讨的办法和对策A.进入料筒的原料颗粒温度太低或不平均造成所需的熔化时光加长. A1.检讨湿润机的运转是否正常:湿润温度(原料所需的),空气流量和原料在料斗逗留的时光.A2.检讨在料斗中是否有原料流淌的“绿色通道”.B.原料的熔点太高. B1.经由过程不雅察原料颗粒的变色来检讨是否原料有降解.B2.经由过程DSC剖析来检讨在出如今瓶坯上的未熔颗粒的熔点和结晶度.C.原料颗粒尺寸大小超出尺度或者不平均. C1.检讨原料颗粒是否有适合的尺寸和平均度.4.短射在一个完整的注塑成型进程中,充填瓶坯不敷完整.这种缺点平日可在瓶坯颈部区域的螺纹部分不雅察到,别的短射也可引起瓶坯重量的削减.可能的原因建议的检讨的办法和对策A.原料打针量缺少. A1.增长原料的打针量.A2.减小打针转换地位.A3.增长保压时光.A4.增长保压压力.B.打针时光太长造成在足量的熔料被打针进模具前,缺料的瓶坯已经变冷变B1.增长打针速度. B2.增长打针压力.硬.C.原料粘度太高限制了熔体的充分流淌. C1.增长熔料温度来下降熔体的粘度. C2.检讨原料和瓶坯是否有适合的IV.D.熔体温度太低,流淌不充分. D1.增长模具支流道的温度.D2.增长模具注嘴尖的温度.5.长浇口点瓶坯的长浇口点表示在浇口陈迹处有凸起的熔化物.可能的原因建议的检讨的办法和对策A.模具打针口处的阀针封闭时,瓶坯浇口区域太冷. A1.增长模具注嘴尖的温度.A2.减小注嘴尖处阀针封闭延迟时光.B.阀针封闭不正常. B1.增长模具支流道的温度.B2.检讨驱动阀针的空气压力是否正常.B3.检讨拔出的阀门空气消声器是否有堵塞,若有必须清算或改换.B4.检讨在模具注嘴尖处是否存有外部原料,若有必须清算.B5.检讨模具注嘴尖是否破坏,如破坏须改换.B6.检讨模具阀针是否破坏,如破坏须改换.B7.检讨阀针活塞密封圈是否磨损,如磨损须改换.C. 原料黏度太高. C1.增长熔料温度来下降熔体的粘度.C2.检讨原料和瓶坯是否有适合的IV.D.熔体温度太低,流淌不充分. D1.增长模具支流道的温度.D2.增长模具注嘴尖的温度.6.拉长的浇口柱瓶坯的拉长浇口柱表示为拉出的结晶陈迹.可能的原因建议的检讨的办法和对策A.模具浇口区域过热引起浇口残根在模具打开动作进程中粘在模具浇口处. A1.检讨冷却水供应体系是否正常:水压,水流量和水温.A2.检讨模具浇口模板上的冷却水道是否有污染和堵塞情形,若有须清算. A3.下降注嘴尖的温度.A4.检讨以确保注嘴尖加热器衔接带与浇口模具板镶块没有接触.A5.增长模具冷却时光.B. 压实压力缺少以使浇口冷却器与瓶坯浇口慎密接触. B1.增长保压压力设定值,尤其是在后段.7.拉丝可能的原因建议的检讨的办法和对策A..瓶坯浇口点处过热使浇口残根在产品脱模进程中不克不及清洁的与模具分别. A1.下降注嘴尖温度.A2.下降模具支流道的温度.A3.检讨冷却水供应回路是否处于正常运转状况:水压,水流量,和水温. A4. 检讨模具浇口模板上的冷却水道是否有污染和堵塞情形,若有须清算. A5.增长模具冷却时光.A6.削减“阀针封闭延迟”时光.B. 阀针封闭不恰当. B1.增长模具支流道温度.B2.检讨阀针空气压力是否恰当.B3. 检讨拔出的阀门空气消声器是否有堵塞,若有必须清算或改换.B4.检讨在模具注嘴尖处是否存有外部原料,若有必须清算.B5.检讨模具注嘴尖是否破坏,如破坏须改换.B6.检讨模具阀针是否破坏,如破坏须改换.B7. 检讨阀针活塞密封圈是否磨损,如磨损须改换.C.模具打开后,瓶坯减压不恰当让熔料从浇口点处拉成细丝. C1.增长螺杆撤退退却行程以增长降压.C2.增长螺杆撤退退却逗留时光以增长降压.C3.减小保压压力.8.水痕径环出如今瓶坯的内径或外径概况上.这种环平日表示为清楚的卵形皱纹.可能的原因建议的检讨的办法和对策A.因为模具区域高的露点在模具概况形成凝集物,从而在型腔填充进程中引起熔料流的断裂. A1.检讨确认模具区域的空气露点低于模具冷却水的温度,假如须要的话调剂除湿体系.A2.增长模具冷却水的温度高于模具区域空气露点以防止水凝集(注:该调剂会解决凝集问题,但不被斟酌为最适合的解决办法,因为它可能会对瓶坯的整体质量以及模具周期有影响.9.浇口结晶在瓶坯的浇口区域有白色晶体构造消失,平日可发明普遍全部瓶坯壁的横切面(左图),在瓶坯的内壁部分,接近型芯端盖的概况(中图),从瓶坯的浇口区域成条纹向坯身延长(右图).可能的原因建议的检讨的办法和对策A.模具注嘴尖的温度在料流停止流淌这段时光太低. A1.增长模具注嘴尖温度. A2.减小熔料停止的时光.B.模具注嘴尖的温渡过高或者瓶坯浇口区域太热引起深度白雾(尤其在瓶坯的厚壁部分). B1.下降模具注嘴尖的温度.B2.检讨模具冷却水供应体系:水温.水流量.水压.B3. 检讨模具浇口模板的冷却水道是否有污染和堵塞.B4..检讨以确保注嘴尖加热器衔接带与浇口模具板镶块没有接触.B5.减小打针填充速度以减小注嘴尖/或浇口通道的熔体减切热.B6.确保在机械手掏出管中的瓶坯与球形底部接触.10.发雾瓶坯一种白云状外不雅不平均的分布在瓶坯身的遍地的现象.可成条放射性条纹状白环被看到(左图),也会局部性地出如今瓶坯的厚壁部分.(右图)可能的原因建议的检讨的办法和对策A.进入料筒的原料湿度太高引起在塑化进程中水解从而导致原料IV的下降,增长了原料的结晶速度. A1.检讨机械料筒喉咙部分原料的湿度(应小于50ppm).A2.检讨湿润机是否在适合的运转:度(原料请求的),气流,露点和原料在料斗中逗留的时光.B.进入料筒的原料温度太冷或者温度不平均导致需求的熔化时光增长. B1. 检讨湿润机是否在适合的运转:温度(原料请求的),气流,露点和原料在料斗中逗留的时光.B2.检讨在湿润料斗中是否有优先的料流渠道.C.在塑化进程中机塑机压力不敷导致剪切热的削减.C1.增长螺杆背压.11.熔接缝当前面的两股熔料流会聚而联合在一路时形成的细缝.前端的熔料没有完整粘在一路沿自身流淌偏向形成微细的缺口.熔料流径联合在瓶坯螺纹部分处常可不雅察到这个现象.可能的原因建议的检讨的办法和对策A.熔料流速过慢使前端的熔料流太冷而不克不及完整的粘在一路. A1.增长打针填充速度.A2.增长打针压力A3.增长保压速度A4.增长保压压力A5.增长模具冷却水温度以给前端熔料流的温度进行抵偿(注:该调剂会解决此问题,但不被斟酌为最适合的解决办法,因为它可能会对瓶坯的整体质量以及模具周期有影响.B.进入料筒的原料温度太冷或者温度不平均导致需求的熔化时光增长. B1.清算模具颈环及锁环排气槽.B2.检讨确保模具排气槽的尺寸和图纸尺寸一致.12.黑点/污染物降解物资(左图)或被打针进型腔的外部物资导致随机的颗粒消失坯身.可能的原因建议的检讨的办法和对策A.由降解的熔料产生黑色的颗粒. A1.下降模具注嘴尖的温度.A2.下降模具支流道的温度.A3.下降机械加热温度.A4.减小螺杆转速,后背压和打针速度来减小减切热.A5.使装备在预备启动前的升温加热时光尽量短.A6.在装备启动前先用新料清洗料筒和打针缸.确保所有的黑点和降解原料(变色的)被冲洗出来.(第一次清洗时增长打针量有助于消除活塞和打针缸之间的残留物.)B.进入料筒的原料温度太冷或者温度不平均导致需求的熔化时光增长. B1.清算模具颈环及锁环排气槽.B2.检讨确保模具排气槽的尺寸和图纸尺寸一致.13.飞边在临近的两块模具部件概况(如模具颈环/模具颈环,模具颈环/模具型腔,模具颈环/模具锁环)和之间形成的薄塑料凸起物.可能的原因建议的检讨的办法和对策A.因为过量的原料被打针进模腔,部分塑料被挤进合模面和排气槽. A1.减小打针量.A2.增长打针转换地位. A3.减小保压压力.A4.减小打针填充压力.B. 原料粘渡过低而流入模具合默面合排气槽. B1.减小模具支流道的温度.B2.减小机械加热温度.B3.装备启动进程中减小加热升温时光.B4.在打针进程中减小打针速度让前部的料流冷却.B5.检讨确保原料和瓶坯的IV值在尺度内(参考发雾瓶坯一节的具体描写)14.发黄瓶坯如下图所示的全部瓶坯发黄或变色.(左边和右边的瓶坯与中央的未变色瓶坯作比较)可能的原因建议的检讨的办法和对策A.过热引起的原料降解. A1.检讨湿润机是否恰当运转:湿润温度(原料须要的),空气流量和原料在湿润机中的逗留时光.A2.下降模具支流道的温度.A3.下降机械加热温度.A4.减小螺杆转速,背压和打针速度以减小料筒中的减切热.A5.使装备在预备启动前的升温加热时光尽量短.A6.在装备启动前先用新料清洗料筒和打针缸.确保所有的黑点和降解原料(变色的)被冲洗出来B. 原料粘渡过低而流入模具合默面合排气槽. B1.减小模具支流道的温度.B2.减小机械加热温度.B3.装备启动进程中减小加热升温时光.B4.在打针进程中减小打针速度让前部的料流冷却.B5.检讨确保原料和瓶坯的IV值在尺度内(参考发雾瓶坯一节的具体描写)15.壁厚过度不平均瓶坯的直径偏向四周厚度不平均(如下瓶坯骨干部位的横切面)可能的原因建议的检讨的办法和对策A.打针时因为填充压力过高使模具芯棒偏移. A1.下降打针填充压力. A2.下降打针填充速度. A3.下降保压压力.A4.下降保压时光.B. 打针时因为料流不平均使模具芯棒偏移. B1.检讨确保模具支流道加热设定和料筒加热设定接近(尤其是打针缸, 分派器和注嘴区域)以获得更好的熔料平均化.C.模具芯棒与型腔未校准. C1.检讨是否有磨损的模具部件.(如颈环,锁环,锥形型腔,导柱,导套等.)C2.检讨是否有破坏的芯棒.C3.检讨型芯和型腔是否瞄准.C4.从新校准芯模和型腔模.C5.检讨型芯冷却水管的地位和直度是否适合.C6.检讨型芯冷却水管和水道有无堵塞或污染.16.擦痕/概况瑕疵以椭圆瑕疵,刮痕情势消失的随机陈迹(左图),在瓶坯概况以纵向刮痕或不规矩外形现象消失的不规矩印痕或多重陈迹.可能的原因建议的检讨的办法和对策A.因为与某些物体接触造成的随机瑕疵. A1.尽量减小在从机械手顶出后瓶坯的处理和中转.A2.尽量减小瓶坯从机械手坠落到传输带的距离.A3.减小机械手的顶出压力.A4.增长冷却时光以减小瓶坯概况温度和遭遇印迹的迟钝性.B.因为模具概况受损或概况有外步碎片的聚积物造成反复消失的瑕疵.B1.检讨模具概况是否有毁伤(如小毛刺),若有须修复或改换.B2.检讨模具概况是否有外部碎片的积赘物.17.锯齿状分型线当瓶坯被拉出型腔时因为变形使瓶坯上颈环/型腔分型面处的外径上消失一个渺小的环状凹口,也伴着外浇口概况变形(浇口窝)消失.可能的原因建议的检讨的办法和对策A.因为过大的压力造成瓶坯粘在模具型腔里. A1.下降保压压力.A2.增长打针转换地位. A3.下降打针量.B.因为降压不敷造成瓶坯粘在模具型腔里.B1.增长螺杆撤退退却行程以增长降B2.增长螺杆撤退退却逗留时光以增压.B3.保压后延长注嘴口阀门打开时光.C.因为紧缩不敷造成瓶坯粘在模具型腔里. C1.增长瓶坯冷却时光.C2.检讨水冷却体系:水压.水流量. 和水温.C3.检讨模具冷却水道是否有污染和堵塞情形.18.浇口窝当瓶坯被拉出型腔时因为变形使浇口外概况凹陷.也伴着颈环/型腔分型面处变形(锯齿分型线)消失.可能的原因建议的检讨的办法和对策A.因为过大的压力造成瓶坯粘在模具型腔里. A1.下降保压压力.A2.增长打针转换地位. A3.下降打针量.B.因为降压不敷造成瓶坯粘在模具型腔里.B1.增长螺杆撤退退却行程以增长降B2.增长螺杆撤退退却逗留时光以增压.B3.保压后延长注嘴口阀门打开时光.C.因为紧缩不敷造成瓶坯粘在模具型腔里. C1.增长瓶坯冷却时光.C2.检讨水冷却体系:水压.水流量. 和水温.C3.检讨模具冷却水道是否有污染和堵塞情形.19.浇口脱皮一块从浇口点开端向外到半球基部扯破的断片粘附在模具浇口板概况(看起来象是一个桔子剥皮),扯破的断片会保持粘附在模具上很多个轮回周期,这就导致后来成型的瓶坯上形成扯破的陈迹.可能的原因建议的检讨的办法和对策A.模具浇口构件磨损使阀针和浇口垫板之间的间隙增大造成瓶坯底部注点不克不及完整的割断. A1.检讨模具阀针尖和浇口垫镶块是否有磨损,若有须改换...B.熔料压力过高或不准确的阀针封闭使阀针和模具浇口垫板之间的间隙中有凝固的残料造成瓶坯浇口注点不克不及完整与模具分别. B1.增长模具注嘴尖温度来熔化瓶坯浇口处残料以达到尽早分别浇口注点和使阀针准确封闭的目标.B2.减小保压压力以减小冷却速度和减小熔料在注嘴尖区域的压力.B3.经由过程增长螺杆撤退退却行程留时光的方法增长降压以减小冷却速率和减轻注嘴尖区域熔料的压力.20.内浇口变形瓶坯浇口区域尤其在浇口注点以下薄壁部分热紧缩引起原料在瓶坯底部内概况原料凹陷.可能的原因建议的检讨的办法和对策A.抵偿热紧缩的压力缺少. A1.增长保压压力A2.增长保压时光.B.熔体温渡过高引起的过量热紧缩. B1.下降机械加热温度.B2.下降模具加热温度.C.模具冷却不敷引起的过量热紧缩C1.检讨水冷却体系:水压,水流,和水温.C2.检讨模具冷却水道有无污染和堵塞情形.C3.增长瓶坯冷却时光.D1.减小螺杆撤退退却地位或螺杆撤D.熔体因为过大的轻易降压造成瓶坯上未冷却的熔体被吸回到注嘴尖.留时光以减小降压.21.焦痕在瓶坯的浇口区域(左图)常可发明的黑色或棕褐色未燃烧物,或在瓶坯的中部发明散开的印记(右图),这些印记是降解的原料被打针进型腔行成的.可能的原因建议的检讨的办法和对策A.由降解熔体引起的焦痕. A1.下降模具注嘴尖的温度.A2.下降模具支流道的温度.A3.下降机械加热温度.A4.减小螺杆速度,背压和打针速度以减小剪切热.A5.使装备启动前的加热升温时光尽可能段短.A6.B.熔体温渡过高引起的过量热紧缩. B1.下降机械加热温度.B2.下降模具加热温度.C.模具冷却不敷引起的过量热紧缩C1.检讨水冷却体系:水压,水流,和水温.C2.检讨模具冷却水道有无污染和堵塞情形.C3.增长瓶坯冷却时光.D.熔体因为过大的轻易降压造成瓶坯上未冷却的熔体被吸回到注嘴尖. D1. 在装备启动前先用新料清洗料筒和打针缸.确保所有的黑点和降解原料(变色的)被冲洗出来.(第一次清洗时增长打针量有助于消除活塞和打针缸之间的残留物.).22.瓶坯翘曲在顶出压力下瓶坯的躯干部被破坏,平日产生在瓶坯壁最厚和最热的部分.可能的原因建议的检讨的办法和对策A.不充分的模具冷却引起的翘曲. A1.检讨水冷却体系:水压,水流量和水温度.A2.检讨模具冷却水道有无污染和堵塞情形.A3.增长瓶坯冷却时光.B.抵偿热紧缩和恰当热量传递的压力缺少. B1.增长保压压力. B2.增长保压时光.C.熔体温渡过高引起过热紧缩和高的瓶坯温度. C1.下降机械加热温度. C2.下降模具加热温度.23颈圈白点两种在瓶坯颈圈上常发明的白点23.1在防盗环处消失的单个结晶点.(左图)23.2在支持环处消失的单个结晶点.(右图)可能的原因建议的检讨的办法和对策A.打针填充速度太慢造成前端的熔料流冷却产生结晶.A1.增长打针填充速度.B.打针填充时忽然的减速引起熔料流淌速度的减小. B1.减小打针转换地位. B2.增长第一段保压压力.C.熔体粘度太高导致料流速度的减小. C1.增长机械加热温度.C2.增长模具加热温度.C3.增长模具注嘴尖的加热百分比.C4.增长螺杆背压和螺杆速度来增长料筒中剪切热.瓶坯概况料流受到干扰,看起来象是因为熔体降解或气泡爆裂引起的纵向或者钩状银白色条纹从浇口流开.可能的原因建议的检讨的办法和对策A.过热的或降解的熔料被打针进型腔形成的喷射的印记. A1.下降模具注嘴尖的温度.A2.下降模具支流道温度.A3.下降机械加热温度.A4.减小螺杆速度,背压和打针速度以减小料筒中的螺杆剪切热.A5. 使装备启动前的加热升温时光尽可能短.A6. .在装备启动前先用新料清洗料筒和打针缸.确保所有的已降解原料(变色的)被冲洗出来.A7.检讨模具注嘴尖区域是否有损.25.浇口针孔在浇口注点处的有一个向浇口壁部分延长的小孔.(和浇口空泛有关系)可能的原因建议的检讨的办法和对策A.浇口区域过热引起浇口注点的熔料粘在阀针上. A1.检讨冷却水供应体系功效是否正常:水压,水流量,和水温.A2.检讨模具板冷却水道是否有污染和堵塞情形,若有须清算.A3.减小注嘴尖的温度.A4.检讨确保注嘴尖加热圈没有与浇口板嵌件接触.A5.增长模具冷却时光.B.阀针没有实时或正常封闭B1.调节保压后阀门打开准时.B2.增长模具支流道温度.B3.检讨阀针空气压力是否正常. 26.浇口空泛在瓶坯浇口注点下的壁厚部分有一个凹洞形成(右图).有可能与浇口的针孔有关系.可能的原因建议的检讨的办法和对策A.浇口区域过热引起紧缩过多. A1.检讨冷却水供应体系功效是否正常:水压,水流量,和水温.A2.检讨模具板冷却水道是否有污染和堵塞情形,若有须清算.A3.减小注嘴尖的温度.A4.减小熔体温度.A5. 检讨确保注嘴尖加热圈没有与浇口板嵌件接触.A6.增长模具冷却时光.B.模具浇口阀针没有实时或正常封闭. B1.调节保压后阀门打开准时(平日小).B2.增长模具支流道温度.B3.检讨阀针空气压力是否正常. 27.色纹PET熔料和着色剂未完整融会在瓶坯概况消失色纹.可能的原因建议的检讨的办法和对策A.色彩和原料混杂不充分. A1.检讨色料定量单位是否和色料添加一致.A2.检讨着色剂在原估中是否普遍分布在原估中,假如须要运用一个色料预混杂器.A3.检讨色料添加剂管子的地位是否恰当,如不准确须改正.A4.检讨色料添加剂的平均度.B.原料塑化进程中熔料不敷平均. B1.增长螺杆背压.B2.增长增长螺杆转速.B3.增长料筒熔料温度,尤其是在计量段.B4.检讨在料筒的进料口处是否有塑料架桥现象,若有有须清算并下降料筒进料段的温度.28.过高的乙醛含量AA(乙醛)是因为PET原料的热降解形成的.AA产生的数目由成型加工前提和PET原料的热稳固性决议.在某些运用中,瓶坯中的AA含量必须保持一个最小值以免转变产品的味道,是以必须经由过程气相色谱以ppm或g/l为单位进行准时测量.(见图下)可能的原因建议的检讨的办法和对策A.过多的熔料降解造成AA形成量的增长. A1.减小料筒的加热温度.A2.减小模具温度.A3.减小螺杆转速和背压以减小剪切热.A4.减小打针速度以减小剪切热.A5.将螺杆缓冲点减小到最小(一般10到20mm).A6.减小加工周期时光以减小熔料在机械中的滞留时光.B.进入的原料颗粒温度太低造成在塑化进程中产生过多的剪切热. B1.增长料筒进料口处进入的原料温度(原料请求的温度一般160到180 ℃).29.过高的粘度降IV是一个表示PET聚合链平均长度的值,该值与原料的分子量成正比.IV直接关系到成型的瓶坯和瓶子的物理机能,是以任何的粘度下降对产品德量都是晦气的.IV可用熔体粘度计或溶剂测试办法以dl/g为单位测得.可能的原因建议的检讨的办法和对策A.进入的原料水分含量太高造成塑化进程中水降解从而导致原料的IV值损掉. A1.检讨机械进料口处原料水分含量值(应<50 ppm).A2.检讨湿润机运转是否正常:湿润温度(原料请求的),湿润空气流量,露点和原料在料斗中的逗留时光.B.过多的熔体降解造成PET分子链断裂的增长引起IV值的减小. B1.减小料筒的加热温度.B2.减小螺杆转速和背压以减小剪切热.B3.减小打针速度以减小剪切热.。
瓶胚缺陷及解决办法
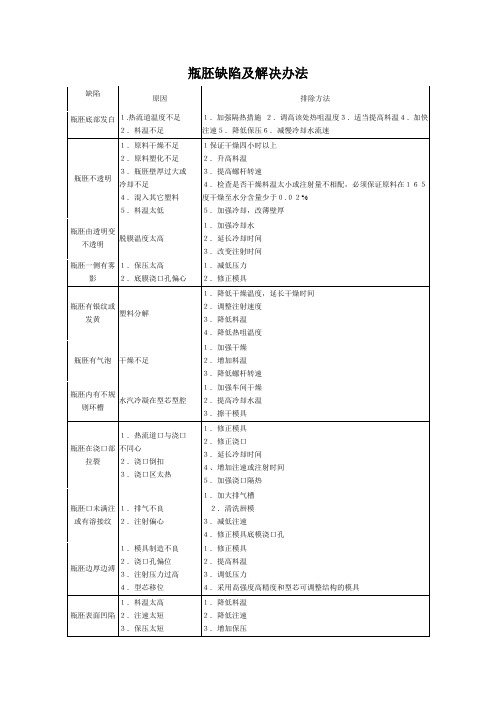
4.检查是否干燥料温太小或注射量不相配,必须保证原料在165度干燥至水分含量少于0.02%
5.加强冷却,改薄壁厚
瓶胚由透明变不透明
脱膜温度太高
1.加强冷却水
2.延长冷却时间
3.改变注射时间
瓶胚一侧有雾影
1.保压太高
2.底膜浇口孔偏心
1.减低压力
2.修正模具
瓶胚有银纹或发黄
塑料分解
1.降低干燥温度,延长干燥时间
3.改善瓶型设计
瓶子易跌破
1.底部壁厚未适当拉伸
2.塑料高温降解
1.改善底部拉伸比
2.加强注胚前原料干燥
3.降低生产温度
瓶子内有麻点、白雾
1.吹入不洁空气
2.空气湿度大
1.设置空气过滤装置
2.降低吹入空气湿度
瓶子太软
1.设计不良 2.加工温太高
1.改进设计
2.尽量在低温下注胚和吹瓶成型
吹瓶后有焦臭味
瓶胚缺陷及解决办法
缺陷
原因
排除方法
瓶胚底部发白
1.热流道温度不足
2.料温不足
1.加强隔热措施2.调高该处热咀温度3.适当提高料温4.加快注速5.降低保压6.减慢冷却水流速
瓶胚不透明
1.原料干燥不足
2.原料塑化不足
3.瓶胚壁厚过大或 冷却不足
4.混入其它塑料
5.料温太低
1保证干燥四小时以上
2.升高料温
3.保压太短
4.注射时间太短
5.冷却不足
1.降低料温
2.降低注速
3.增加保压
4.增加注射时间
5.增加水压
瓶胚浇口拉丝
1.隔热不良
2.冷却不足
3.热流内有压力
PET注瓶胚常见缺陷及对策
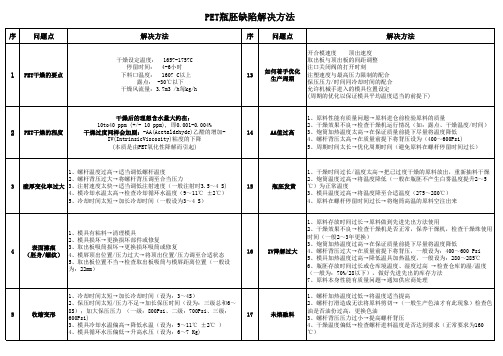
未熔融料
1、螺杆加热温度过低→将温度适当提高 2、螺杆打滑造成无法将原料剪切→(一般生产色油才有此现象)检查色 油是否油份过高,更换色油 3、螺杆背压压力过小→提高螺杆背压 4、干燥温度偏低→检查螺杆进料温度是否达到要求(正常要求为160 ℃)
PET瓶胚缺陷解决方法
序 问题点
解决方法
序
问题点
解决方法
飞边
1、模唇、模芯座、模腔损坏→更换或修复损坏部件 2、注射压力过大→减小注射压力 3、保压压力过大→减小保压压力或保压位置 4、加热温度过高→降低加热温度 5、锁模压力太低→增加锁模压力(一般为:200~230Psi) 6、原料在加热段停留时间过长→把生产周期缩短
1、注嘴温度百份比太高或太低→判段注嘴温度调至适中
IV(IntrinsicViscosity)粘度的下降 (本质是由PET氧化性降解而引起)
1、原料性能有质量问题→原料进仓前检验原料的质量
2、干燥效果不良→检查干燥机运行情况(如:露点、干燥温度/时间)
14
AA值过高 3、炮筒加热温度太高→在保证质量前提下尽量将温度降低
4、螺杆背压太高→在质量前提下将背压设为(400~600Psi)
注口关闭阀的打开时刻 注塑速度与最高压力限制的配合 保压压力/时间同冷却时间的配合
允许机械手进入的模具位置设定
(周期的优化以保证模具平均温度适当的前提下)
干燥后的理想含水量大约在: 10to40 ppm (+/- 10 ppm), 即0.001-0.004% 干燥过度同样会加剧:-AA(Acetaldehyde)乙醛的增加-
18
长注口 拉长注口
3、热流道/注嘴温度过高→适当把温度调低 4、保压时间太短→加长保压时间
瓶胚常见质量缺陷的原因及检查和解决方法
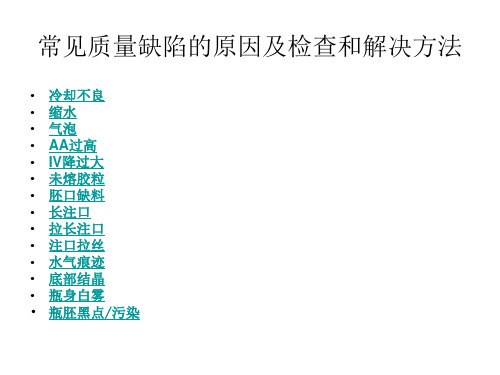
3、清理冷却系统 1、降低注嘴温度 1、增加注射量 2、加大保压时间和压力
1、拆模从新加紧运水管 1、减小机械手吸力 2、清理机械手吸筒
原因:焦痕
检查和解决方法: 1、温度太高 模温 1、减小注嘴温度、减小机温、 2、减小螺杆转速和背压 3、刚开机时减少加热时间 1、更换新注嘴隔热套和注嘴 1、更换注嘴 1、检查注嘴加热系统
4、阀针控制气阀失灵 5、抽胶不足 6、保压太大
原因:水气痕迹
检查和解决方法: 1、模具冷却水温太低 2、车间环境温度过高或湿 度过大造成模具结水珠 3、模具漏水 1、升高模具循环水温度 1、调低空调温度
原因:原因:
1、检查模具漏水原因及排除
原因:底部结晶
检查和解决方法:
1、注嘴温度过低或偏高 2、保压压力过大 3、冷却不良 1、升高或降低注嘴温度 1、减低保压压力第三级 1、检查冷却系统:压力、温度、流量 2、增加冷却时间 3、清理模具冷却系统 1、增加抽胶位置和时间 1、有无贴紧在注嘴上 1、检查并更换阀针注嘴
原因:缩水
检查和解决方法: 1、注射不充分 1、增加注射量 2、减小转换时间 3、增加保压压力和时间 2、冷却不良 1、检查水系统(压力、流量、温度) 2、检查模具水道(模芯分水管、模腔、) 3、增加冷却时间 3、温度太高 1、减小机温、模温 4、排气不良 1、检查排气孔 2、减小注射压力和速度 5、过度抽胶 1、减小抽胶位置和时间 6、由于填充过度引起机械变形 1、减小保压 7、阀针位置不对 1、保养热流道
• • •
• • •
原因:气泡
检查和解决方法 • 熔融性能问题 • 熔胶内有气泡-不足的背压压力的影响 • 在塑化过程中, 如果螺杆被允许轻易”跳后”, 那麽,就会出现熔体压力 的不稳定. • 这种不稳定的熔体压力导致在熔体内部出现间隙空间. • 这种间隙空间就会导致在熔体内产生气泡, 然后形成越来越大的气泡. • • • • • • • 熔胶内有气泡-过低的原料温度的影响 每个PET螺杆都有自己的独特的设计产量或输出率, 以 公斤/小时 (Kgs/hr)表示. 设计时,假设了一个特定的入料温度, 或能量数值. Husky PET螺杆的设计师在设计时, 假设的入料温度范围为155 ℃ 170 ℃. 当入料温度太低时,就必须从其它地方获得额外的能量, 比如, 炮筒发热 环, 机械剪切等. 随着机械剪切率的增大, 熔体的不稳定性和滑动就会发生.熔体压力的 变化, 将导致气泡的产生.
PET注瓶胚常见缺陷及对策
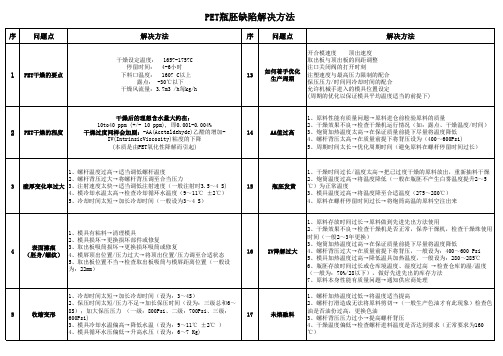
1、原料干燥不足→停机把原料重新进行干燥
8
底部结晶
2、保压压力过大→减低保压压力第三级 3、模具冷却水偏低或偏高→检查冷却水温是否合理再进行调节
20
瓶身白雾
2、螺杆加热温度过低→提高螺杆加热温度 3、螺杆打滑→(一般生产色油胚才出现)将炮筒温度增高
4、模具冷水通道阻塞→保养模具水循环通道
4、背压过低→提高背压压力
飞边
1、模唇、模芯座、模腔损坏→更换或修复损坏部件 2、注射压力过大→减小注射压力 3、保压压力过大→减小保压压力或保压位置 4、加热温度过高→降低加热温度 5、锁模压力太低→增加锁模压力(一般为:200~230Psi) 6、原料在加热段停留时间过长→把生产周期缩短
1、注嘴温度百份比太高或太低→判段注嘴温度调至适中
IV(IntrinsicViscosity)粘度的下降 (本质是由PET氧化性降解而引起)
1、原料性能有质量问题→原料进仓前检验原料的质量
2、干燥效果不良→检查干燥机运行情况(如:露点、干燥温度/时间)
14
AA值过高 3、炮筒加热温度太高→在保证质量前提下尽量将温度降低
4、螺杆背压太高→在质量前提下将背压设为(400~600Psi)
18
长注口 拉长注口
3、热流道/注嘴温度过高→适当把温度调低 4、保压时间太短→加长保压时间
5、保压压力太小→增大保压压力
5、保压压力太小→增加保压压力
6、模具冷却循环水温度过低→提高冷却水温度(设为:8~10℃)
6、冷却时间太短→加长冷却时间
1、热流道注嘴无法关闭或注嘴口已磨损→保养热流道气缸或更换
4、冷却时间太短→加长冷却时间
5、保压压力太小→加大保压压力
5
瓶胚常见缺陷分析及处理方法

瓶胚常见缺陷分析及处理方法1.气泡由于注塑机内部的空气或产生的气体导致随机的气泡或空洞出现在瓶坯的侧壁上。
可能的原因及建议的检查的方法和对策A.在原料的塑化过程中由于熔体压缩不够充分而残留有空气在熔体中。
A1.增加螺杆的背压。
A2.调节螺杆的后退位置以提供足够的缓冲点。
A3.检查在挤出机的下料口是否有塑料架桥现象,如果有必需清除并降低料筒进料段的温度。
B.因过量的减压而吸入空气。
B1.通过减小螺杆的后退距离或者后退停留时间来减少降压。
C.进料段温度过高而使原料过早的熔化。
C1.降低进料段的温度。
2.凹痕凹痕是因热收缩在瓶坯的内表面或外表面形成的原料凹陷现象。
凹痕通常出现在瓶坯的厚壁部份和壁厚变化的地方。
可能的原因及建议的检查的方法和对策A.原料的注射量不足。
A1.增加注射量。
A2.减小注射转换位置。
B.补偿收缩而进行的压实不够充分。
B1.增加保压压力。
B2.增加保压时间。
C.过高的熔化温度引起的过收缩。
C1.降低机器的加热温度。
C2.降低模具的加热温度。
D.模具冷却不够充分引起的过收缩。
D1.检查水冷却系统:水压,水流量和水温。
D2.检查模具的冷却水道有无污染或堵塞情况。
D3.增加瓶坯的冷却时间。
3.未熔化物部份熔化或完全未熔化的原料颗粒出现在瓶身上。
可能的原因及建议的检查的方法和对策A.进入料筒的原料颗粒温度太低或不均匀造成所需的熔化时间加长。
A1.检查干燥机的运转是否正常:干燥温度(原料所需的),空气流量和原料在料斗停留的时间。
A2.检查在料斗中是否有原料流动的“绿色通道”。
B.原料的熔点太高。
B1.通过观察原料颗粒的变色来检查是否原料有降解。
B2.通过DSC分析来检查在出现在瓶坯上的未熔颗粒的熔点和结晶度。
C.原料颗粒尺寸大小超过标准或者不均匀。
C1.检查原料颗粒是否有合适的尺寸和均匀度。
4.短射在一个完全的注塑成型过程中,充填瓶坯不够完全。
这种缺陷通常可在瓶坯颈部区域的螺纹部分观察到,另外短射也可引起瓶坯重量的减少。
瓶坯缺陷分析及解决建议
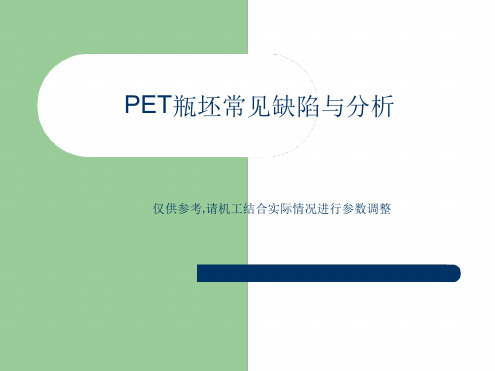
缺陷种类及解决建议
● 雾状瓶坯浑浊白色的外观蔓延整个瓶坯体。可观察到径向条痕白色的环 (左图)。也可局部地出现在厚壁部分(右图)。
? ★ 可能造成的原因: ? A 熔化的树脂潮湿的级别太高导致
在塑化过程的水解,结果是料温的 丢失和结晶率的增加。
? B 进入的树脂温度太低或不均匀导 致熔 浇口成窝浇口外部凹陷由于脱离型腔时发生变形。
? ★ 可能造成的 原因:
? A 由于注射量 不充足,保压 的时间不足以 令瓶坯均匀收 缩。
? B 瓶胚粘住模 腔由于不充分 的减压。
? C 瓶胚粘住模 腔由于不足够 的收缩。
? ★ 解决方法: (供技术员参 考)
? A 增加保压压 力和保压时间, 缩短位置转换 行程。
是否正常;检查电磁阀是否卡住;检 查射嘴是否损坏;检查阀针是否损坏; 检查气缸活塞密封圈是否损坏或磨损。
缺陷种类及解决建议
●拉长或拉空浇口 瓶坯拉长的浇口出现白色的晶体状或中间出现空心
? ★ 可能造成的原因: ? A 在浇口区域过度的加热,使浇口切点粘
住阀针或型腔的浇口,导致开模时拉长。 ? B 保压压力或时间不足以通过型腔紧密接
缺陷种类及解决建议
●水痕(水环)半径状环出现在瓶坯的内径和外径表面,这些环通常可以清 楚观察到椭圆形的隆起线。
? ★ 可能造成的原因: ? 模具成型表面疑结露珠,有
水分,导致填充模腔期间塑 料熔体被中断流动形成。 ? ★ 解决方法:(供技术员 参考) ? 检查成成型区域的大气露点 及模具的冷却水温度,有必 要时可调节除湿系统;增加 模具冷冻水温度高于模具区 域的大气露点来防止凝结 (注意:这种改变将能弥补 凝结问题,然而却没有考虑 出起因的合适的解决方案, 而且可能全面地影响瓶胚质 量和成型周期时间。)
瓶胚常见问题与解决方法

瓶胚质量缺陷及解决方法•调试产品质量主要从以下五个因素考虑:时间、温度、压力、速度和位置•常见的瓶胚缺陷分析和处理方法•冷却不良•缩水•气泡•AA过高•IV降过大•未熔胶粒•胚口缺料•长注口•拉长注口•注口拉丝•水气痕迹•底部结晶•常见的瓶胚缺陷分析和处理方法•瓶身白雾•瓶胚黑点/污染•飞边•瓶胚发黄•壁厚不均•瓶底剥皮•胚底缩水•瓶底内部收缩•焦痕•鱼刺状条纹•注口针孔•色斑冷却不良原因:检查和解决方法:1、模具冷却不好1、检查水系统(压力、流量、温度)2、检查模具水道(模芯分水管、模腔、)3、增加冷却时间2、保压不够或太大1、增加或减少保压时间2、增加或减少保压压力3、温度太高1、减小机温、模温4、机械手位置不对1、重新对位5、模具表面潮湿1、调节车间温度缩水原因:检查和解决方法:1、注射不充分1、增加注射量2、减小转换时间3、增加保压压力和时间2、冷却不良1、检查水系统(压力、流量、温度)2、检查模具水道(模芯分水管、模腔、)3、增加冷却时间3、温度太高1、减小机温、模温4、排气不良1、检查排气孔2、减小注射压力和速度5、过度抽胶1、减小抽胶位置和时间6、由于填充过度引起机械变形1、减小保压7、阀针位置不对1、保养热流道气泡原因:检查和解决方法:•熔融性能问题•熔胶内有气泡-水分的影响•由于氢和氧在水分子中的存在, 这些气体在熔化过程中被压缩.•一旦熔体压力和熔融温度降低, 这些被压缩的气体就会被允许重新膨胀.•随着这种膨胀的继续, 气泡, 微小的空间和其它包含物就会在瓶胚内出现.1、增加背压2、增加机温3、增加熔胶余量•熔融性能问题•熔胶内有气泡-快速熔融的影响•当熔融的速度太快时(超出螺杆熔化能力的设计标准),由于螺杆过度的滑动,气泡就会出现. •这种滑动造成不稳定的熔体压力和气囊.•如果这种情况发生, 更大的气泡就会在熔体内出现.•1、减小螺杆速度气泡原因:检查和解决方法•熔融性能问题•熔胶内有气泡-不足的背压压力的影响•在塑化过程中, 如果螺杆被允许轻易”跳后”, 那麽,就会出现熔体压力的不稳定.•这种不稳定的熔体压力导致在熔体内部出现间隙空间.•这种间隙空间就会导致在熔体内产生气泡, 然后形成越来越大的气泡.•熔胶内有气泡-过低的原料温度的影响••每个PET螺杆都有自己的独特的设计产量或输出率, 以公斤/小时(Kgs/hr)表示. •设计时,假设了一个特定的入料温度, 或能量数值.•Husky PET螺杆的设计师在设计时, 假设的入料温度范围为155 ℃-170 ℃.•当入料温度太低时,就必须从其它地方获得额外的能量, 比如, 炮筒发热环, 机械剪切等. •随着机械剪切率的增大, 熔体的不稳定性和滑动就会发生.熔体压力的变化, 将导致气泡的产生.气泡原因:检查和解决方法干燥不良1、检查干燥系统抽胶太多1、减小抽胶位置和时间螺杆打滑1、检查色油质量2、检查螺杆入料位有无胶块3、减小喂料段温度瓶胚质量缺陷及解决方法•AA值过高原因:检查和解决方法:1、原料过度降解1、降低机器温度(在瓶胚产生白雾的前提下调高2-5℃)2、降低模具温度(280±5℃)3、降低螺杆转速和背压在质量前提下将背压设为400~600Psi(螺杆塑化完成后到下一个塑化周期停留时间约4秒钟)4、减少螺杆输料余量(10-20mm)5、优化周期时间(避免原料在螺杆停留时间过长而降解)AA值过高原因:检查和解决方法:2、干燥效果不良1、检查干燥机运行情况((露点≤-30℃、干燥温度160-180℃、干燥时间5-6小时) 3、原料AA超标1、原料AA应小于1PPMIV降过大原因:检查和解决方法:2、干燥效果不良1、检查干燥机运行情况((露点≤-30℃、干燥温度160-180℃、干燥时间5-6小时)2、检查干燥机是否正常,保养干燥机,检查干燥珠使用时间(一般2~3年更换)3、原料存放时间过长1、原料做到先进先出方法使用4、瓶胚存放时间过长或仓1、检查仓库的湿/温度库境温度、湿度过高2、做好先进先出的库存方法5、原料本身性能有问题1、通知供应商处理瓶胚质量缺陷及解决方法未熔融料原因:检查和解决方法:1、原料熔解不充分1、增加机温、背压、螺杆转速2、增加螺杆缓冲位置(10-20mm)2、原料质量问题1、检查料粒尺寸是否不一2、检查原料熔点是否不一3、原料入口温度太低1、检查螺杆进料温度是否达到要求(正常要求为160℃)2、检查干燥效果(干燥时间、温度等)3、检查下料口保温情况4、入料段挤压不充分1、检查入料口有无胶并清理2、减小入料口温度瓶胚质量缺陷及解决方法瓶口缺料原因:检查和解决方法:1、注射不充分1、增加注射量(注射完毕剩余位置一般为5~8mm)2、减小转换位置3、增大保压压力和时间2、注射压力太低1、提高注射压力3、注射速度太慢1、加快注射速度(最佳注射时间为:10g/s)4、温度太低1、增加机温模温和注嘴温度5、阀针移动不正确1、更换注嘴、阀针、胶圈、高温套2、检查气压和水口阀6、模具排气孔堵塞1、清理模具排气孔7、机械故障1、穿梭阀轴坏长注口原因:检查和解决方法:1、由于注嘴区温度太低1、增加注嘴温度2、减小水口阀延时关时间3、增加模具温度2、热流道阀针气缸堵塞1、保养热流道3、保压太大1、减小保压压力和时间4、水口阀坏或气压不足1、维修或更换水口阀增大气压5、抽胶太少1、增加抽胶位置和时间拉长注口原因:检查和解决方法:1、由于注嘴区温度太高1、减小注嘴温度2、检查注嘴发热环情况3、检查模具冷却水(流量、压力、温度)4、检查模具冷却水道5、增加冷却时间2、热流道阀针气缸堵塞1、保养热流道3、最后一段保压太小1、增加最后一段保压压力4、抽胶太大1、减小抽胶位置和时间5、开模速度太慢1、增加开模速度2、将mold break调为零注口拉丝原因:检查和解决方法:1、热流道注嘴无法关闭1、保养热流道气缸或更换新注嘴或注嘴口已磨损2、增加模具温度2、热流道注嘴区温度太高1、降低注嘴加热温度和模具温度3、冷却不良1、增加冷却时间2、检查冷却系统:压力、流量、温度3、清理模腔底4、阀针控制气阀失灵1、保养阀针控制阀5、抽胶不足1、增加抽胶位置和时间6、保压太大1、减小保压水气痕迹原因:检查和解决方法:1、模具冷却水温太低1、升高模具循环水温度2、车间环境温度过高或湿1、调低空调温度度过大造成模具结水珠3、模具漏水1、检查模具漏水原因及排除瓶胚质量缺陷及解决方法底部结晶原因:检查和解决方法:1、注嘴温度过低或偏高1、升高或降低注嘴温度2、保压压力过大1、减低保压压力第三级3、冷却不良1、检查冷却系统:压力、温度、流量2、增加冷却时间3、清理模具冷却系统4、抽胶太少1、增加抽胶位置和时间5、检查注嘴发热圈1、有无贴紧在注嘴上6、阀针注嘴磨损1、检查并更换阀针注嘴瓶身白雾原因:检查和解决方法:1、原料干燥不足或干燥不好1、检查干燥机2、原料太湿1、检查原料水份3、塑化不足1、提高背压压力2、增加螺杆转速3、增加机温4、增加螺杆缓冲位置4、冷却不良1、检查冷却系统(压力、温度、流量)2、增加冷却时间3、清理模具瓶胚黑点/杂质原因:检查和解决方法:1、外来杂质1、检查原料本身有无杂质2、检查干燥时有无受到污染2、高温降解1、减少注嘴温度、机温、模温2、降低螺杆转速和背压3、开机时缩短加热时间4、检查注嘴和高温套有无损坏5、停机时及时降温飞边原因:检查和解决方法:1、注射量太大1、调小注射量2、增大转换位置3、减小注射压力4、减小保压压力或保压位置2、模唇、模芯座、模腔1、更换或修复损坏部件损坏3、加热温度过高1、降低机温和模具温度4、锁模压力太低1、增加锁模压力(一般为:200~230Psi)5、原料在加热段停留时1、把生产周期缩短间过长原因:检查和解决方法:1、干燥时间过长/温度太高1、把已过度干燥的原料放出,重新抽料干燥2、原料在螺杆停留时间过长1、将炮筒高温的原料空注出来3、原料降解1、减低螺杆转速和背压2、将机器温度降低(一般在瓶胚不产生白雾温度提升2~5℃)为正常温度3、将模温度降至合适温度(275~280℃壁厚不均原因:检查和解决方法:1、模具损坏1、检查模芯模腔有无变形2、检查模具水平3、检查模芯分水管有无损坏或脱落4、检查冷却水道有无2、由于高充注压力造成的1、减小保压压力2、减小保压时间3、减小注射压力4、减小注射时间3、由于温度变化造成1、尽量使穿梭阀到射嘴头的温度接近热流道温度瓶底剥皮原因:检查和解决方法:1、注嘴口有冷胶1、适当调高注嘴温度和减少保压压力2、增大抽胶位置和时间2、注嘴口和模腔底磨损1、更换模腔底2、更换新的注嘴、嘴隔热套、阀针和胶圈3、胚底冷却不良1、增大冷却时间2、检查冷却系统:流量压力和温度3、检查模腔底有无堵塞胚底缩水原因:检查和解决方法:1、过度填充1、减小注射量(剩余位置为:5~8mm)2、减小保压压力3、增加转换位置2、压力释放大小1、增加抽胶位置和时间2、廷长水口阀关时间3、冷却不良1、检查冷却水系统:压力、流量、温度2、加长冷却时间3、清理冷却系统4、注嘴太热1、降低注嘴温度5、填充不足1、增加注射量2、加大保压时间和压力6、模芯运水管松脱1、拆模从新加紧运水管7、机械手吸力过大1、减小机械手吸力胚底内部收缩原因:检查和解决方法:1、填充不足1、增加保压时间和压力2、减小抽胶位置和时间2、温度太高1、减小机温、模温、注嘴温度3、冷却不良1、检查冷却系统:压力、流量、温度2、增加冷却时间3、清理冷却系统4、模芯运水管松脱1、拆模从新加紧运水管焦痕原因:检查和解决方法:1、温度太高1、减小注嘴温度、减小机温、模温2、减小螺杆转速和背压3、刚开机时减少加热时间2、注嘴隔热套老化1、更换新注嘴隔热套和注嘴3、注嘴损坏1、更换注嘴4、注嘴加热失控1、检查注嘴加热系统鱼刺状条纹原因:检查和解决方法:1、塑化过度1、降低机温、模温、注嘴温度2、降低螺杆转速、背压2、模具注嘴加热温度太高1、降低注嘴温度3、模具注嘴隔热套老化1、更换注嘴隔热套4、有空气进入熔料1、增加螺杆背压2、减小抽胶位置和时间5、穿梭阀打开延时太短1、增加穿梭阀延时时间6、喂料段有胶或温度太高1、清理并降低喂料段温度十.瓶胚质量缺陷及解决方法注口针孔原因:检查和解决方法:1、模具注嘴区温度过高1、把注嘴温度降低2、清理模具、模腔底冷却系统3、增加冷却时间4、检查冷却系统:水压力、流量、温度2、抽胶太多1、适当调少抽胶位置和时间3、模具热流道温度过低1、调高热流道温度4、注射速度太快1、减慢注射速度5、保压压力和时间太小1、加长保压压力和时间6、注嘴和阀针磨损1、更换防针孔注嘴和阀针7、穿梭阀坏和气压偏低1、检查并更换穿梭阀2、检查气压3、延长水口阀关时间瓶胚质量缺陷及解决方法色斑原因:检查和解决方法:1、色油不能跟原料很好的混合1、检查每次加入色油的剂量2、检查色油在入料口与原料的均匀分配并一要使用搅拌器3、检查色油管在入料口有无正确的安放(斜口朝下)和有无堵塞4、检查色油使用型号的一致性2、在塑化阶段不能与融胶很好的混合1、增加螺杆背压2、增加螺杆转速3、增加炮筒融胶温度(增加塑化段的温度)4、检查在炮筒入料口有无未融胶块,如有必要需要清理并降低入料口温度.3、由于储胶余量不够造成的融胶压力不够1、增加螺杆退后位置从而增加储胶余量(通常输料余量为10~20MM)。
瓶胚常见质量缺陷的原因及检查和解决方法27页PPT
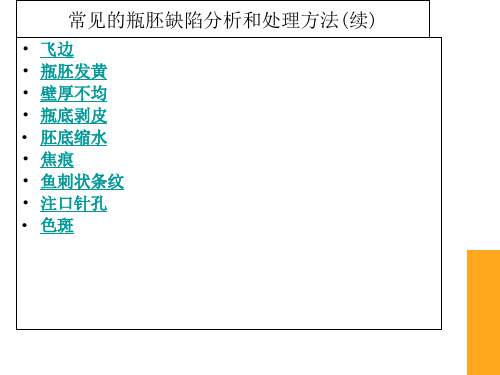
1、减小注嘴温度 2、检查注嘴发热环情况 3、检查模具冷却水(流量、
度) 4、检查模具冷却水道 5、增加冷却时间 1、保养热流道 1、增加最后一段保压压力 1、减小抽胶位置和时间 1、增加开模速度
原因:注口拉丝
检查和解决方法:
1、热流道注嘴无法关闭 或注嘴口已磨损
2、热流道注嘴区温度太高 3、冷却不良
2、减小转换位置 3、增大保压压力和时间 1、提高注射压力 1、加快注射速度(最佳注射时间为:10g/s) 1、增加机温模温和注嘴温度 1、更换注嘴、阀针、胶圈、高温套 2、检查气压和水口阀 1、清理模具排气孔
1、穿梭阀轴坏
原因:长注口
检查和解决方法:
1、由于注嘴区温度太低
关时间
2、热流道阀针气缸堵塞 3、保压太大
5、原料本身性能有问题
1、通知供应商处理
原因:未熔融料
检查和解决方法: 1、原料熔解不充分 2、原料质量问题 3、原料入口温度太低
求
4、入料段挤压不充分
1、增加机温、背压、螺杆转速 2、增加螺杆缓冲位置(10-20mm) 1、检查料粒尺寸是否不一
2、检查原料熔点是否不一 1、检查螺杆进料温度是否达到要求(正常要
就会出现.
• 这种滑动造成不稳定的熔体压力和气囊.
• 如果这种情况发生, 更大的气泡就会在熔体内出现.
•
1、减小螺杆速度
原因:气泡
检查和解决方法 • 熔融性能问题 • 熔胶内有气泡-不足的背压压力的影响 • 在塑化过程中, 如果螺杆被允许轻易”跳后”, 那麽,就会出现熔体压力
的不稳定. • 这种不稳定的熔体压力导致在熔体内部出现间隙空间. • 这种间隙空间就会导致在熔体内产生气泡, 然后形成越来越大的气泡.
瓶胚常见缺陷分析及处理方法

瓶胚常见缺陷分析及处理方法瓶胚常见缺陷分析及处理方法1.气泡由于注塑机内部的空气或产生的气体导致随机的气泡或空洞出现在瓶坯的侧壁上。
可能的原因及建议的检查的方法和对策A.在原料的塑化过程中由于熔体压缩不够充分而残留有空气在熔体中。
A1.增加螺杆的背压。
A2.调节螺杆的后退位置以提供足够的缓冲点。
A3.检查在挤出机的下料口是否有塑料架桥现象,如果有必需清除并降低料筒进料段的温度。
B.因过量的减压而吸入空气。
B1.通过减小螺杆的后退距离或者后退停留时间来减少降压。
C.进料段温度过高而使原料过早的熔化。
C1.降低进料段的温度。
2.凹痕凹痕是因热收缩在瓶坯的内表面或外表面形成的原料凹陷现象。
凹痕通常出现在瓶坯的厚壁部份和壁厚变化的地方。
可能的原因及建议的检查的方法和对策A.原料的注射量不足。
A1.增加注射量。
A2.减小注射转换位置。
B.补偿收缩而进行的压实不够充分。
B1.增加保压压力。
B2.增加保压时间。
C.过高的熔化温度引起的过收缩。
C1.降低机器的加热温度。
C2.降低模具的加热温度。
D.模具冷却不够充分引起的过收缩。
D1.检查水冷却系统:水压,水流量和水温。
D2.检查模具的冷却水道有无污染或堵塞情况。
D3.增加瓶坯的冷却时间。
3.未熔化物部份熔化或完全未熔化的原料颗粒出现在瓶身上。
可能的原因及建议的检查的方法和对策A.进入料筒的原料颗粒温度太低或不均匀造成所需的熔化时间加长。
A1.检查干燥机的运转是否正常:干燥温度(原料所需的),空气流量和原料在料斗停留的时间。
A2.检查在料斗中是否有原料流动的“绿色通道”。
B.原料的熔点太高。
B1.通过观察原料颗粒的变色来检查是否原料有降解。
B2.通过DSC分析来检查在出现在瓶坯上的未熔颗粒的熔点和结晶度。
C.原料颗粒尺寸大小超过标准或者不均匀。
C1.检查原料颗粒是否有合适的尺寸和均匀度。
4.短射在一个完全的注塑成型过程中,充填瓶坯不够完全。
这种缺陷通常可在瓶坯颈部区域的螺纹部分观察到,另外短射也可引起瓶坯重量的减少。
瓶胚常见缺陷分析及处理方法之欧阳数创编

瓶胚常见缺陷分析及处理方法1.气泡由于注塑机内部的空气或产生的气体导致随机的气泡或空洞出现在瓶坯的侧壁上。
可能的原因及建议的检查的方法和对策 A.在原料的塑化过程中由于熔体压缩不够充分而残留有空气在熔体中。
A1.增加螺杆的背压。
A2.调节螺杆的后退位置以提供足够的缓冲点。
A3.检查在挤出机的下料口是否有塑料架桥现象,如果有必需清除并降低料筒进料段的温度。
B.因过量的减压而吸入空气。
B1.通过减小螺杆的后退距离或者后退停留时间来减少降压。
C.进料段温度过高而使原料过早的熔化。
C1.降低进料段的温度。
2.凹痕凹痕是因热收缩在瓶坯的内表面或外表面形成的原料凹陷现象。
凹痕通常出现在瓶坯的厚壁部份和壁厚变化的地方。
可能的原因及建议的检查的方法和对策 A.原料的注射量不足。
A1.增加注射量。
A2.减小注射转换位置。
B.补偿收缩而进行的压实不够充分。
B1.增加保压压力。
B2.增加保压时间。
C.过高的熔化温度引起的过收缩。
C1.降低机器的加热温度。
C2.降低模具的加热温度。
D.模具冷却不够充分引起的过收缩。
D1.检查水冷却系统:水压,水流量和水温。
D2.检查模具的冷却水道有无污染或堵塞情况。
D3.增加瓶坯的冷却时间。
3.未熔化物部份熔化或完全未熔化的原料颗粒出现在瓶身上。
可能的原因及建议的检查的方法和对策 A.进入料筒的原料颗粒温度太低或不均匀造成所需的熔化时间加长。
A1.检查干燥机的运转是否正常:干燥温度(原料所需的),空气流量和原料在料斗停留的时间。
A2.检查在料斗中是否有原料流动的“绿色通道”。
B.原料的熔点太高。
B1.通过观察原料颗粒的变色来检查是否原料有降解。
B2.通过DSC分析来检查在出现在瓶坯上的未熔颗粒的熔点和结晶度。
C.原料颗粒尺寸大小超过标准或者不均匀。
C1.检查原料颗粒是否有合适的尺寸和均匀度。
4.短射在一个完全的注塑成型过程中,充填瓶坯不够完全。
这种缺陷通常可在瓶坯颈部区域的螺纹部分观察到,另外短射也可引起瓶坯重量的减少。
瓶胚常见质量缺陷的原因及检查和解决方法28页PPT
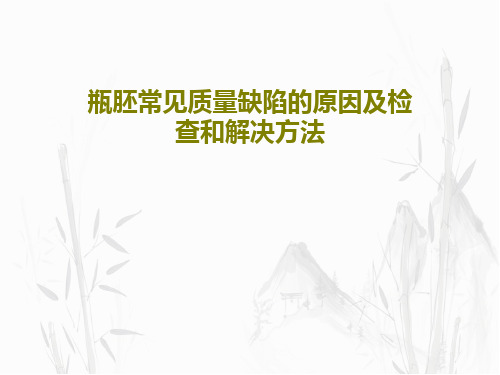
15、机会是不守纪律的。——雨登上顶峰,也仍要自强不息。——罗素·贝克 18、最大的挑战和突破在于用人,而用人最大的突破在于信任人。——马云 19、自己活着,就是为了使别人过得更美好。——雷锋 20、要掌握书,莫被书掌握;要为生而读,莫为读而生。——布尔沃
END
瓶胚常见质量缺陷的原因及检 查和解决方法
11、战争满足了,或曾经满足过人的 好斗的 本能, 但它同 时还满 足了人 对掠夺 ,破坏 以及残 酷的纪 律和专 制力的 欲望。 ——查·埃利奥 特 12、不应把纪律仅仅看成教育的手段 。纪律 是教育 过程的 结果, 首先是 学生集 体表现 在一切 生活领 域—— 生产、 日常生 活、学 校、文 化等领 域中努 力的结 果。— —马卡 连柯(名 言网)
- 1、下载文档前请自行甄别文档内容的完整性,平台不提供额外的编辑、内容补充、找答案等附加服务。
- 2、"仅部分预览"的文档,不可在线预览部分如存在完整性等问题,可反馈申请退款(可完整预览的文档不适用该条件!)。
- 3、如文档侵犯您的权益,请联系客服反馈,我们会尽快为您处理(人工客服工作时间:9:00-18:30)。
• 这种滑动造成不稳定的熔体压力和气囊.
• 如果这种情况发生, 更大的气泡就会在熔体内出现.
5
•
1、减小螺杆速度
原因:气泡
检查和解决方法 • 熔融性能问题 • 熔胶内有气泡-不足的背压压力的影响 • 在塑化过程中, 如果螺杆被允许轻易”跳后”, 那麽,就会出现熔体压力
的不稳定. • 这种不稳定的熔体压力导致在熔体内部出现间隙空间. • 这种间隙空间就会导致在熔体内产生气泡, 然后形成越来越大的气泡.
• 随着机械剪切率的增大, 熔体的不稳定性和滑动就会发生.熔体压力的
6
变化, 将导致气泡的产生.
原因: AA值过高
检查和解决方法:
1、原料过度降解
2、干燥效果不良 3、原料AA超标
1、降低机器温度(在瓶胚产生白雾的前提下调高2-5℃) 2、降低模具温度(280±5℃) 3、降低螺杆转速和背压
在质量前提下将背压设为400~600Psi (螺杆塑化完成后到下一个塑化周期停留时间约4秒钟) 4、减少螺杆输料余量(10-20mm) 5、优化周期时间(避免原料在螺杆停留时间过长而降
2、检查原料熔点是否不一 1、检查螺杆进料温度是否达到要求(正常要
为160℃) 2、检查干燥效果(干燥时间、温度等) 3、检查下料口保温情况 1、检查入料口有无胶并清理 2、减小入料口温度
9
原因:瓶口缺料
检查和解决方法:
1、注射不充分 8mm)
2、注射压力太低 3、注射速度太慢 4、温度太低 5、阀针移动不正确
(螺杆塑化完成后到下一个塑化周期停留时间约4秒钟)
4、减少螺杆输料余量(10-20mm)
5、优化周期时间(避免原料在螺杆停留时间过长而降
解)
2、干燥效果不良
1、检查干燥机运行情况((露点≤-30℃、干燥
温度160-180℃、干燥时间5-6小时)
2、检查干燥机是否正常,保养干燥机,检
查干燥珠使用时间(一般2~3年更换)
原因:检查和解决方法
干燥不良 1、检查干燥系统
抽胶太多 1、减小抽胶位置和时间
螺杆打滑 1、检查色油质量
3
原因:缩水
检查和解决方法:
1、注射不充分 1、增加注射量
2、减小转换时间
3、增加保压压力和时间
2、冷却不良 1、检查水系统(压力、流量、温度)
2、检查模具水道(模芯分水管、模腔、)
3、增加冷却时间
解) 1、检查干燥机运行情况((露点≤-30℃、干燥 温度160-180℃、干燥时间5-6小时) 1、原料AA应小于1PPM
7
原因: IV降过大
检查和解决方法:
1、原料过度降解 1、降低机器温度(在瓶胚产生白雾的前提下调高2-5℃)
2、降低模具温度(280±5℃)
3、降低螺杆转速和背压
在质量前提下将背压设为400~600Psi
2
原因:冷却不良
检查和解决方法:
1、模具冷却不好 1、检查水系统(压力、流量、温度)
2、检查模具水道(模芯分水管、模腔、)
3、增加冷却时间
2、保压不够或太大 1、增加或减少保压时间
2、增加或减少保压压力
3、温度太高
1、减小机温、模温
4、机械手位置不对 1、重新对位
5、模具表面潮湿 1、调节车间温度
压力、温
2、热流道阀针气缸堵塞 3、最后一段保压太小 4、抽胶太大 5、开模速度太慢
1、减小注嘴温度 2、检查注嘴发热环情况 3、检查模具冷却水(流量、
• 一旦熔体压力和熔融温度降低, 这些被压缩的气体就会被允许重新膨胀.
• 随着这种膨胀的继续, 气泡, 微小的空间和其它包含物就会在瓶胚内出现. 1、增加背压 2、增加机温 3、增加熔胶余量
• 熔融性能问题 • 熔胶内有气泡-快速熔融的影响 • 当熔融的速度太快时(超出螺杆熔化能力的设计标准),由于螺杆过度的滑动,气泡
常见质量缺陷的原因及检查和解决方法
• 冷却不良 • 缩水 • 气泡 • AA过高 • IV降过大 • 未熔胶粒 • 胚口缺料 • 长注口 • 拉长注口 • 注口拉丝 • 水气痕迹 • 底部结晶 • 瓶身白雾 • 瓶胚黑点/污染
1
常见的瓶胚缺陷分析和处理方法(续)
• 飞边 • 瓶胚发黄 • 壁厚不均 • 瓶底剥皮 • 胚底缩水 • 焦痕 • 鱼刺状条纹 • 注口针孔 • 色斑
检查和解决方法:
1、由于注嘴区温度太低
关时间
2、热流道阀针气缸堵塞 3、保压太大
时间 4、水口阀坏或气压不足
增大气压 5、抽胶太少
时间
1、增加注嘴温度 2、减小水口阀延时
3、增加模具温度 1、保养热流道
1、减小保压压力和
1、维修或更换水口阀
1、增加抽胶位置和 11
原因:拉长注口
检查和解决方法: 1、由于注嘴区温度太高
3、温度太高
1、减小机温、模温
4、排气不良
1、检查排气孔
2、减小注射压力和速度
5、过度抽胶
1、减小抽胶位置和时间
6、由于填充过度引起机械变形 1、减小保压
7、阀针位置不对
1、保养热流道
4
原因:气泡
检查和解决方法: • 熔融性能问题 • 熔胶内有气泡-水分的影响
• 由于氢和氧在水分子中的存在, 这些气体在熔化过程中被压缩.
• 熔胶内有气泡-过低的原料温度的影响
•
• 每个PET螺杆都有自己的独特的设计产量或输出率, 以 公斤/小时 (Kgs/hr)表示.
• 设计时,假设了一个特定的入料温度, 或能量数值.
• Husky PET螺杆的设计师在设计时, 假设的入料温度范围为155 ℃ 170 ℃.
• 当入料温度太低时,就必须从其它地方获得额外的能量, 比如, 炮筒发热 环, 机械剪切等.
6、模具排气孔堵塞 7、机械故障
1、增加注射量(注射完毕剩余位置一般为5~
2、减小转换位置
3、增大保压压力和时间
1、提高注射压力
1、加快注射速度(最佳注射时间为:10g/s)
1、增加机温模温和注嘴温度
1、更换注嘴、阀针、胶圈、高温套
2、检查气压和水口阀
1、清理模具排气孔1、穿梭阀轴坏 Nhomakorabea10
原因:长注口
3、原料存放时间过长
1、原料做到先进先出方法使用
4、瓶胚存放时间过长或仓 1、检查仓库的湿/温度
库境温度、湿度过高
2、做好先进先出的库存方法
5、原料本身性能有问题
1、通知供应商处理
8
原因:未熔融料
检查和解决方法: 1、原料熔解不充分 2、原料质量问题 3、原料入口温度太低
求
4、入料段挤压不充分
1、增加机温、背压、螺杆转速 2、增加螺杆缓冲位置(10-20mm) 1、检查料粒尺寸是否不一