IE七大手法改善案例
IE七大手法及案例

防呆法之 自动原理
3.自动原理 以各种光学、电学、力学、机构学、化学等原理来限制某些动作的执行或不 执行,以避免错误之发生。目前这些自动开关非常普遍,也是非常简易的 “自动化”之应用。 (1)以“浮力”的方式来控制 例:抽水马桶之水箱内设有浮球,水升至某一高度时,浮球推动拉杆,切断
水源。 (2)以“重量”控制的方式来完成 例:电梯超载时,门关不上,电梯不能上下,警告钟也鸣起。 (3)以“光线”控制的方式来完成 例:自动照相机,光线若不足时,则快门按不下去。 (4)以“时间”控制的方式来完成 例:洗手间内的“烘手机”,按一次只有“一分钟”,时间一到自动停止。
防呆法之 自动原理
(5)以“方向”控制的方式来完成 例:超级市场内进口及出口之单向栏栅,只能进不能出。或只能出不能进。 (6)以“电流”用量的方式来完成 例:家庭的电源开关皆装置保险丝,用电过量时,保险丝就熔断,造成断电。 (7)以“温度”控制的方式来完成 例:家庭内冷气机之温度控制,冷度够时,自动停止,温度上升时,自动开启
双手法 动改法
IE七大手法简介
授人以鱼,不如授人以渔!
名称 动改法 防呆法 五五法 双手法
人机法
流程法 抽查法
目的 改善人体动作的方式,减少疲劳使工作更为舒适、更有效率. 如何避免做错事情,使工作第一次就做好的. 借着质问的技巧来发掘出改善的构想. 研究人体双手在工作时的过程,借以发掘出可改善之地方.
判断以下防呆用的是什么原理?
治具上面贴有 不一样的颜色
相符原理
机器工作时需手同时下 压绿色按扭方可
保险原理
AB C
AB C
相符原理
断根原理
相符原理
断根原理
手机壳生产混穴的防呆改善
IE七大手法及案例

IE七大手法及案例1. 爱情陷阱爱情陷阱是一种常见的IE(影响力操作)手法,经常被用于操纵他人的情感和感情。
这种手法利用人们对爱情的渴望,诱使他们做出意想不到的决策。
案例:在一起工作的同事张三和李四一直以好朋友的关系相处。
某一天,张三觉得自己对李四有了更深的感情,于是开始表达对李四的追求。
李四感到困惑,因为他从未考虑过与张三发展更多的关系。
但是,张三利用他们之间已经建立的友谊和信任,不断向李四表达自己对他的爱慕之情,并强调如果李四拒绝他,他将永远失去对李四的友情。
在不断的情感轰炸下,李四最终同意与张三发展恋爱关系。
2. 损失厌恶损失厌恶是一种IE手法,适用于一种心理现象,即人们更倾向于避免损失,而不是追求收益。
这种手法利用了人们对损失的担忧,来控制他们的行为和决策。
案例:某公司推出一项新的会员计划,为新加入的会员提供一年免费使用的特权。
公司精心设计了会员计划,使会员在第二年续费时可以享受更多的优惠和额外的特权。
通过这种方式,公司让人们感觉到如果不续费,就会失去原本获得的特权,并且可能错过更多的好处。
这种损失厌恶的策略促使大部分会员选择继续使用该服务并续费。
3. 社会认同社会认同是一种IE手法,通过使人们感到自己与某个团体或社交群体相关联,来影响他们的决策。
这种手法利用了人们对社会认同和群体归属感的需求。
案例:某汽车品牌在广告中强调他们的产品是“时尚和先进的城市人”的选择。
他们使用年轻,时尚的模特来展示汽车,并且将汽车置于现代化的城市背景中。
通过这种方式,汽车品牌试图让人们相信拥有该汽车可以让他们成为时尚和先进的一员,与这个群体产生社会认同感。
4. 权威说服权威说服是一种IE手法,通过引用权威人物或专家的意见和观点来影响他人的决策。
这种手法利用了人们对于权威和专业知识的尊重和信任。
案例:在一项新药推广活动中,制药公司邀请了知名医学专家发表演讲并撰写相关文章,介绍该药物的疗效和优势。
这使人们更加信任该药物的有效性,因为他们相信专家的权威意见。
IE改善实战技法ppt课件
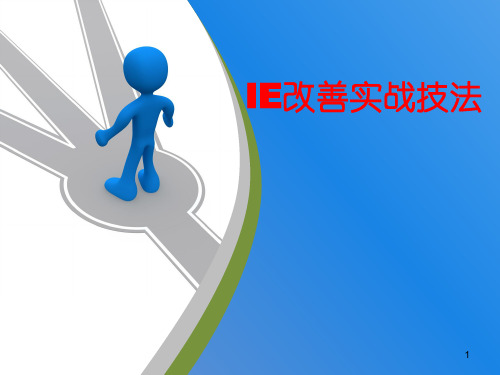
• 能否使用不同的肌肉群?如 手指、腕部、前臂、上臂、 軀幹等?。
• 能否使用較強的肌肉組?如 用大腿肌肉擔負重荷,以 腳操從台鉗。
• 能否消除或縮短用手握緊 的時間。
31
31
查檢表應用示例
能否消除“握緊”?能否使用工具和設備?
• 答:可以在工作台上安裝六角形夾具,以保持六角 螺母的牢固、直立,從而消除用手握緊的動作。
能否改變作業次?能否採用槓桿原原理?
• 答:將拉桿旋到螺栓上,比螺栓旋到桿上容易,因 為前者可利用槓桿的作用,使操作變得容易。
能否降低對視力的要求?
• 答:將小零件放在操作者面前,尋找方便。
32
32
问题讨论
我司现场的作业那些地方可以改善,应如何 改善?
33
IE七大手法之二—— 流程法
意义:
泰勒的第一个案例:沙铲
吉尔布雷斯夫妇 砌墙动作不依赖直觉,而以扎实 的资料作根据;影片分析(MTM);
3
如何降低生產成本
廠
址 選 擇 分 析
工 序 分 析
作 業 分 析
動 素 分 析
效益
使用工業工程手法來進行
4
4
IE概论
定义 1: • 工业工程是对人员、物料、设备、能源和信息所组成的集
成系统,进行设计、改善和设置的一门学科.它综合运用数 学、物理学和社会科学方面的专门知识和技术,以及工程 分析和设计的原理与方法,对该系统所取得的成果进行确 定、预测和评价. • ----美国 工业工程师学会(AIIE) 1995年) 定义 2: • 工业工程是对一个组织中人、物料和设备的使用及其费用 作详细分析研究,这种工作由工业工程师完成,目的是使组 织能够提高生产率、利润率和效率. • ----美国 大百科全书 1982年版
IE七大手法改善案例

五. 防錯法 案例3:SMT空焊降低改善1/3
改善前 1.1 新機種Raptor量產初期,SMT BSide目檢工站發現SD Conn空焊(浮高)與掉件不良,達0.78%,占總不良比重:22%, 居不良首位.
五. 防錯法 案例3:SMT空焊降低改善2/3
改善后 在BSide Reflow前增加一個夾具(如圖),能彈性的支撑SD
改善前
改善后
設計制作測試自動拔插治具,減少誤操作,減少劃傷
五. 防錯法 案例2:SMT上料防混料改善1/3
上料防混料---防錯料台車支架的使用
改善前
改善後
HITACHI台車
軌道 號條
碼
自製防錯料 台車支架
物料
料帶易重疊交叉,且不易發現 掃描軌道號太遠,不易判斷對應軌道
以上缺陷使上料員不能及時發現
上料
2
2
5 爐前目檢
1
1
6
AOI
1
1
7 爐后比對
1
1
8 爐后目檢
2
1
合計
10人 8人
精簡 1
1 2
B side
改善前 改善后
NO 工站
人數
1
線長
1
1
2 全技員
1
0
3
印刷
1
1
4
上料
2
2
5 爐前目檢 1
1
6
AOI
1
1
7 爐后比對 1
1
8 爐后目檢 3
1
合計
11人 9人
精簡 1
2 2
五. 防錯法 案例1:L10測試治具改善1/1
Conn,防止焊點重熔時受重力等影響產生不良.
动作改善法(IE七大手法)
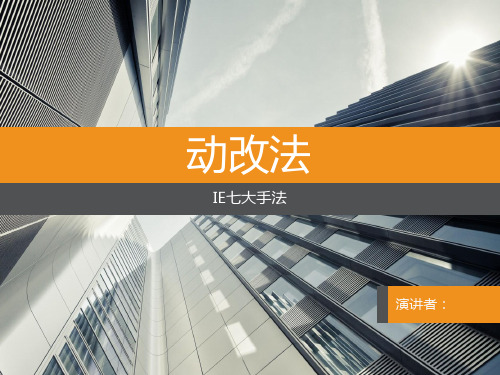
动作改善原则
动作改善原则:有关人体运用的原则 6﹑避免突变原则:连续曲线运动较方向突变直线运动为佳 动作过程中,如果突然改变方向或急剧停止肯定使动作 节奏发生停顿,造成动作效率降低。所以,作业动作设计时 要使动作路线尽量保持直线或圆滑曲线。
28
Hale Waihona Puke 动作改善原则动作改善原则:有关人体运用的原则 6﹑避免突变原则:连续曲线运动较方向突变直线运动为佳
40
动作改善原则
动作改善原则:有关工作场所布置和环境的原则 11﹑重力喂料原则:利用重力喂料,越近越好 零部件、物料等利用重力喂料和各种存放工装送到作业 岗位,越近越好。 应用案例:设备喂料系统。
41
动作改善原则
动作改善原则:有关工作场所布置和环境的原则 11﹑重力喂料原则:利用重力喂料,越近越好 应用案例:标准零部件箱。
1防呆法防错法foolproof防呆法2动作改善法动作经济原则动改法3流程程序法流程法455w1h5x5何法五五法5人机配合法多动作法人机法6双手操作法双手法7工作抽查法抽查法目录1动改法的定义2动改法的涵义3动改法的应用范围4动改法的作用5动作改善原则有关人体运用的原则有关工作场所布置和环境的原则有关于工具设备的原则6动作改善的技巧7思考题目录动改法动改法的定义
30
动作改善原则
动作改善原则:有关人体运用的原则 7﹑弹道式动作较轻快: 例如,挥动高尔夫球杆时,一旦击出后,杆子肯定顺势挥出, 没有办法在在中途(例如在肩部的高度)停顿下来。
31
动作改善原则
动作改善原则:有关人体运用的原则 8﹑节奏轻松原则:动作宜轻松有节奏 动作也必须保持轻松的节奏,让作业者在不太需要判断 的环境下进行作业。容易停下来进行判断的作业,实际上更 容易令人疲乏。顺着动作的顺序,把材料和工具摆放在合适 的位置,是保持动任节奏的关键。
ie七大手法运用案例

ie七大手法运用案例IE七大手法是指项目经理启发式管理的七个方法,可分别用于管理项目进度、质量、成本、风险、资源、沟通和人员等方面。
在项目管理中,运用IE七大手法可以帮助项目团队高效务实地完成项目,提高项目成功率。
以下是IE七大手法运用案例。
1. 甘特图:甘特图是一种项目进度管理工具,高效地呈现项目进度及各项活动的时间安排。
在某家公司的新版手机研发项目中,项目经理运用甘特图进行计划管理。
该项目共分为三个阶段,每个阶段均有若干个子任务,每个子任务分配一个完成时间。
通过甘特图,项目经理可以清晰地把握项目进度,及时调整计划,有效地掌控项目进展。
2. 直方图:直方图是一种定量数据的可视化工具,通过条形图表达数据信息,便于快速了解数据分布特征。
某家公司的品质改革项目中,项目经理使用直方图描述各个工序的不合格品率。
通过直方图,项目团队可以对大量数据进行整理和分析,进而制定对应策略,不断提高产品质量水平。
3. 七步法:七步法是解决问题的一种管理工具,可以帮助项目团队有效梳理问题、制定解决方案及跟进执行情况。
某市政改造项目中,团队发现路灯低空照明度低,使用七步法进行改造。
经过收集、分类、剖析、汉化、归纳、头臆及总结七个步骤,最终制定了合理的解决方案,成功完成改造任务。
4. 余弦定理:余弦定理是一种解决多:多冲突的决策分析工具,可帮助项目团队量化分析取舍风险与利益,制定更加科学的决策。
某家公司的新产品设计项目中,项目团队运用余弦定理处理多个方案并消除夹杂的主观因素,最终选定了最优方案,实现成功推进项目。
5. PERT图:PERT图工具是一种复杂项目管理的工具,通过概率论建立的方法,计算出项目完成时间的可能值及可能的风险概率,对项目进度提出可行建设性计划。
某家公司的扩建项目中,使用PERT图工具实现资源和时间的合理分配,避免了资金浪费和时间延误,成功完成了扩建项目。
6. 帕累托图:帕累托图是一种具有参考价值的图表,可以帮助项目团队识别追求成本或时间效益的重点工作,使团队更好地集中资源以有效完成目标。
IE七大手法及现场改善技巧
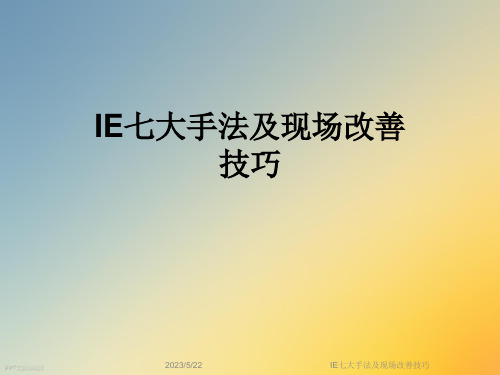
2>. 保險原理: 采用二個以上的動作必需共同或依序執行才能完成工作.
3>. 自動原理: 以各種光學、電學、力學、機構學、化學等原理來限制某些動作的執行
或不執行,以避免錯誤之發生.目前這些自動開關非常普遍,非常簡易的
“自動化”之應用.
4>. 相符原理: 藉用檢核是否相符合的動作,來防止錯誤的發生.
5>. 順序原理: 避免工作之順序或流程前后倒置,可依編號順序排列,可以減少或避免錯
PPT文档演模板
IE七大手法及现场改善技巧
•IE七大手法之二 — 動改法
原則5: 物體之”動量”盡可能利用;但如需用肌力制止時,則應將其減至最小度.
原則6: 連續曲線運動較方向突變直線運動為佳.
原則7: 彈道式運動較輕快.
原則8: 動作宜輕鬆有節奏.
原則9: 眼睛的視點應盡少變動並盡量接近.
* 一個雖沒有多大學識的人,只要他認為工作仍有改善的可能,那麼他就比您更
PPT文档演模板
適合這工作.
IE七大手法及现场改善技巧
•拋棄成見 打
•IE七大手法之四 — 五五法
3.2 何處最需要改善 ※ 您的時間非常富貴,應妥善運用;挑最重要的事情優先做!
瓶頸的地方是最值得改善的,順利的地方留待以后有時間再去研究.
1>. 使作業的動作輕鬆
2>. 使作業不要技能與直覺
3>. 使作業不會有危險
4>. 使作業不依賴感官
EXL: 在連續幾個測試站間加檔板,防止未測品流至下一站.
5.基本原理
1>. 排除化: 剔除會造成錯誤的原因.
2>. 替代化: 利用更確實的方法來代替.
3>. 容易化: 使作業變得更容易、更合適、更獨特,或共同性以減低失敗.適合化、共同化、
动作改善法(IE七大手法)
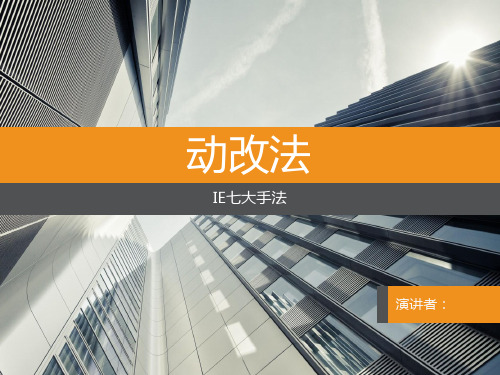
动作改善原则
动作改善原则:有关人体运用的原则 6﹑避免突变原则:连续曲线运动较方向突变直线运动为佳 动作过程中,如果突然改变方向或急剧停止肯定使动作 节奏发生停顿,造成动作效率降低。所以,作业动作设计时 要使动作路线尽量保持直线或圆滑曲线。
28
动作改善原则
动作改善原则:有关人体运用的原则 6﹑避免突变原则:连续曲线运动较方向突变直线运动为佳
4、使动作轻松: 动作轻松,可促使作业顺畅,及有规律并可减少疲劳,
促进作业安全。 例,活用倾斜式料架;
0.005分/次
0.005分/次
增大放入口
作
部
业
件
台
箱
☆ 省掉弯腰姿势
☆ 省掉回头转身
☆ 工具容易存取
13
动作经济原则
动作经济的四个基本原理: 4、使动作轻松: 如,汽车装配时车轮由自动提升设备,自动提升到与车轴高 度,操作人员只需要用开关进行控制就可以了
20
动作改善原则
动作改善原则:有关人体运用的原则 应用案例:
单手作业
双手对称反向作业
21
动作改善原则
动作改善原则:有关人体运用的原则 4﹑降低等级原则:尽量用最低等级动作来工作 人体的手动作可以分为五个等级。等级越低的动作,用 时越短且不易疲劳。为使工作高效,且不易疲劳,就要用低 等级的动作来工作。换句话说:物料与搬运距离越近越好。
物料存放在物料 盒中按加工的顺 序摆放
34
动作改善原则
动作改善原则:有关工作场所布置和环境的原则 9﹑固定位置原则:工具物料要放置在固定的地方
35
动作改善原则
动作改善原则:有关工作场所布置和环境的原则 9﹑固定位置原则:工具物料要放置在固定的地方
IE七大手法案例(组装)ppt课件
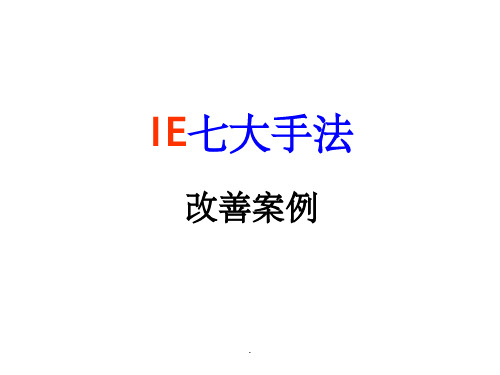
A:“不是。”
Q:“為什么不做?”
A:“改善意識不強。”
.
案例1
狀 改善后
結果﹕ 將線體支撐架向內移動﹐將上檢員工位移至 線頭正對線體﹐雙手同時作業﹐取消伸臂動 作﹐坐著操作. 上檢員工作強度大﹐疲勞 .
案例2
現狀描述
該系列機種自量產以來在DIP線和組裝線 均發生擊發板不充電現象﹐經工程分析确 認原因是MCU板上保險絲熔斷。
保險絲
安全隱患
.
案例2 改善歷程—真因求索
問:為什么數碼相機擊發板電路會不充電? 答:因為連接擊發板電路的保險絲熔斷。
問:為什么連接擊發板電路的保險絲會熔斷? 答:因為保險絲工作時電流超過額定值。
問:為什么保險絲的電流會超過額定值? 答:因為連接擊發板電路的FPC在接口處發生短路。
問:為什么FPC會在接口處發生短路? 答:因為FPC裝入接口后易發生偏位。
左手 4 3 4 11
現行方法
右手 4 4 3 11
根據動作經濟原則﹐考慮增加治工具來減少動作數量﹐縮短cycle time
.
案例2
貼label改善
利用如圖所示自動 貼紙機﹐可以取消 該工站折疊貼紙動 作(其耗時為1.2s)
工作 ﹕ 貼貼紙 開始 ﹕ 雙手空的 ---工具在流水線旁 ﹐ 產品在流水線上 結束 ﹕ 貼好一件產品放至流水線上
拆布套投側板 (1人)
出 L10 組裝 (1人)
裝箱 (1人)
套布套 (1人)
簡化 流程
烤漆廠裝箱
裝配作業
貼1pc腳墊 (1人)
拆布套投側板 (1人)
出L10 組裝 (1人)
改善前: Arches2機種側板腳 墊由L5組裝廠負責 粘貼,造成人力浪費
IE七大手法和现场改善技巧

IE七大手法和现场改善技巧课程背景:IE起源于美国,是在泰勒科学原基础上发展起来的一门应用性工程技术学科,强调综合地提高生产率,降低生产成本,保证产品质量,使系统处于最佳运行状态而获得巨大的整体效益。
IE的知识和方法在美日等发达国家已经成为普遍化的理念,通过取消、合并、重排、简化等优化手法不断改进操作流程,形成一系列非常实用的技术、方法及工程程序,是企业通向世界级制造系统,实现企业竞争的必由之路。
课程结合大量实案例及图片,让学员能够把技术与管理进行有机的结合。
学习后可为企业制定出生产标准、劳动定额工时、工艺流程及现场管理优化等进行实务操作。
并根据现代IE 的发展,重点阐述了精益生产系统中解决多品种少批量生产的快速换型以及零缺陷技术实现的重要手段防错法。
课程内容延展到企业经营活动的全过程,追求企业经营有效投入和经济产出的最大化、价值最大化。
课程收益:掌握常用的IE手法和改善技巧。
协助企业进行系统优化。
减少浪费,降低成本。
提高人、机、物利用率。
提升企业综合竞争力。
实现快速而有效的换型。
如何第一次将事情做对。
效率、效益最大化。
课程大纲:第一部分:工业工程概述一、IE的起源、定义与IE工作范畴1、IE的原理与发展历史2、IE技术的核心内容和追求目标第二部分:传统IE——时间研究与方法研究二、IE操作程序图、流程程序图、线图使用与实战技术1、生产流程分析概述2、生产流程分析的语言及记号3、生产流程分析步骤:(包括:作业分析、搬运分析、检验分析、停滞分析、库存分析)4、流程图--数据收集---流程分析---改善方案---标准化5、工艺流程实战分析案例6、作业流程分析案例7、联合作业流程分析案例8、减少工序数量,缩短总作业时间9、人机联合作业10、停滞与等待的分析与改善11、工程流程图案例分析及实战模拟演练三、搬运及布置(Layout)的效率分析与改善1、搬运及场地布置经济原则2、物流原理与搬运合理化3、单元制生产模式与布局改善4、搬运工程分析程序分析5、搬运路径分析线图6、搬运工具设计与选择7、案例研讨四、MOD动作效率分析与改善技术1、动作分析的目的与改善顺序2、动作分析的要领3、动作分析的目的与改善顺序4、运用动作分析提高效率5、运用动作经济原理提高效率6、动作的经济原则7、预定动作标准时间法(PTS)与预定动作测时法(MTO)8、案例分析与实战模拟演练五、标准时间研究与生产线平衡1、时间研究目的与方法2、秒表,记录表,流程分解原则3、标准工时的实际测定及制定4、实测单元测试方法5、时间值记录法6、评比与宽放的设定原则与影响因素7、标准时间的计算、维护及工时的衡量技术8、如何运用标准工时平衡生产线9、标准工时案例分析及模拟实战演练第三部分:现代IE——精益化策略六、精益生产系统概述1、精益生产的理念思想2、精益生产的发展过程及追求目标3、精益生产的技术体系七、快速换型(SMED)实操训练1、准备阶段2、分析现状3、暴露并消除异常4、形成改善思路5、策划改善方案6、实施快速换型改进7、快速换型改进效果跟踪8、巩固快速换型改善成果八、防错防呆法技术应用1、防错法的目的和意义2、防错法的基本原则3、防错法的进行步骤4、防错法的应用原理5、防错法的一般事例6、防错法行业案例分析。
IE七大手法介绍与实战分析

产生失误的原因基本可归为三大类,即人的原因、方法原因和设备原因,如下表:
失误原因
原因归类
所占比例
忘记
人
77.8%
对过程/作业不熟悉
人
缺乏工作经验
人
故意失误
人
疏忽
人
行动迟缓
人
缺乏适当的作业指导
方法
11.1%
突发事件
设备
11.1%
从表中可以看出,在导致失误的原因中,人占了绝大部分(77.8%),其次为作业方法和设备原因。
考虑下列因素,有无工序、操作可取消、合并、调整、简化 不需要的工序或操作; 改变工作顺序; 改变设备或利用新设备; 改变工厂布置或重新编排设备; 改变操作或贮存的位置; 改变订购材料的规格; 发挥每个工人的技术专长。
2.3 流程改善:有关搬运的改善
IE七大手法2:流程法
考虑下列因素,哪些搬运可以取消、合并、重排、简化 取消某些操作; 改变物品存放的场所或位置; 改变工厂布置; 改变搬运方法; 改变工艺过程或工作顺序; 改变产品设计; 改变原材料或零部件的规格。
A
B
B
A
IE七大手法3:时间分析法
3.4 时间分析之测量方法(秒表测时法):秒表测时法1、归零法:第一单元开始时,母指按下A键开动码表,第一单元结束时即按A 键停表,记下时间后按B键归零.2、连续测时法: 观测的第一单元开始按A键至整 个观测期间只按B键记录每一单元或动素时间,观测结束时方归零3. 累积测试法:用两个秒表, 一表开动,另一表即停止,一表停止则另一表开动,分段记录停止表上的时间后即归零
IE 手 法 的 特 征
客观性----采用IE分析程序方法,不同的人会得到相同的结果;定量性----对现实状态能进行定量分析,容易进行检讨;通用性----是用相同的符号及图表分析,能够信息共享;
IE七大手法及案例
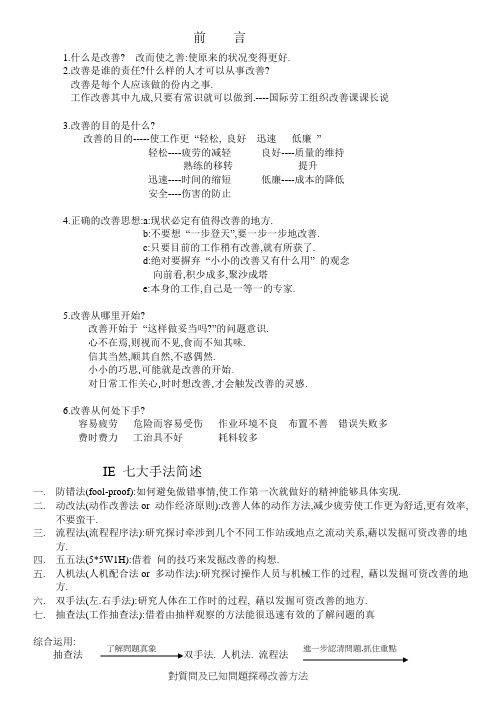
前言1.什么是改善? 改而使之善:使原来的状况变得更好.2.改善是谁的责任?什么样的人才可以从事改善?改善是每个人应该做的份内之事.工作改善其中九成,只要有常识就可以做到.----国际劳工组织改善课课长说3.改善的目的是什么?改善的目的-----使工作更“轻松, 良好迅速低廉”轻松----疲劳的减轻良好----质量的维持熟练的移转提升迅速----时间的缩短低廉----成本的降低安全----伤害的防止4.正确的改善思想:a:现状必定有值得改善的地方.b:不要想“一步登天”,要一步一步地改善.c:只要目前的工作稍有改善,就有所获了.d:绝对要摒弃“小小的改善又有什么用” 的观念向前看,积少成多,聚沙成塔e:本身的工作,自己是一等一的专家.5.改善从哪里开始?改善开始于“这样做妥当吗?”的问题意识.心不在焉,则视而不见,食而不知其味.信其当然,顺其自然,不惑偶然.小小的巧思,可能就是改善的开始.对日常工作关心,时时想改善,才会触发改善的灵感.6.改善从何处下手?容易疲劳危险而容易受伤作业环境不良布置不善错误失败多费时费力工治具不好耗料较多IE 七大手法简述一.防错法(fool-proof):如何避免做错事情,使工作第一次就做好的精神能够具体实现.二.动改法(动作改善法or 动作经济原则):改善人体的动作方法,减少疲劳使工作更为舒适,更有效率,不要蛮干.三.流程法(流程程序法):研究探讨牵涉到几个不同工作站或地点之流动关系,藉以发掘可资改善的地方.四.五五法(5*5W1H):借着问的技巧来发掘改善的构想.五.人机法(人机配合法or 多动作法):研究探讨操作人员与机械工作的过程, 藉以发掘可资改善的地方.六.双手法(左.右手法):研究人体在工作时的过程, 藉以发掘可资改善的地方.七.抽查法(工作抽查法):借着由抽样观察的方法能很迅速有效的了解问题的真_综合运用:抽查法. 人机法. 流程法五五法. 防错法. 动改法 对质问及已知问题探发改善方法 实现改善目标 区别: QC 七大手法:着重在问题的分析.抓重点I E 七大手法:着重在了解问题,应用改善方法解决问题 .第一部分 防呆法(防错法)1.防错法的意义:如何去防止错误发生的方法. 将发生的可能性降至最低/杜绝其发生2.目的:2.1具有即使人为疏忽也不会发生错误的构造 -------- 不需要注意力. 2.2具有外行人来做也不会错的构造 -------- 不需要经验与直觉.2.3具有不管是谁或何时工作都不会出错的构造 -------- 不需要高度的技能或专门的知识.3.功用:积极----绝不会再发生 消极----发生率降至最低4.进行步骤调查发现人为疏忽----> 设定目标,制定实际计划----->调查人为疏忽的原因----->提出防错的改善方案-----> 实施改善方案-----> check 实施效果-----> 维持管制状态排除法: 剔除会造成错误的要因. 替代法: 利用更确实的方法代替.容易化: 使作业变得更容易.更合适,更独特,或共同性以减低失败 适合化,共同化,集中化,特殊/个别化.异常检出 :前站虽有不良,但下站可以挑出,以降低其危害性.缓和影响: 作业失败的影响在其波及过程中,用方法使其缓和或吸收. 观念: 要求捕更多的鱼,首先必须讲求捕鱼技术的传授与使用. (授之以鱼不如授之以渔: 给某人几条鱼不如教给他)引申: 以不教而战,谓杀之.不教其方法,做错是主管之错.防呆法应用原理:•断根原理: 将原因从根本上排除,使绝不会发生错误. •例 : 下水道盖板 / 防护栏加高• 保险原理: 藉用二个以上的动作或依序执行才能完成工作.例 : 冲床双按钮 / 保险丝使用• 自动原理: 以自动化的方式来限制某些动作执行或不执行.例 : 设备积料 / 欠料感应進一步認清問題,抓住重點 對質問及已知問題探尋改善方法•相符原理: 藉用检核是否相符合的动作,来防止错误的发生.例: 自动机转向机构/ PCB的Post孔(极性槽)•顺序原理: 避免工作顺序或流程前后倒置,依编号顺序排列.例: 各类数据编页/ 食品厂自动门•隔离原理: 分隔不同区域的方式,保护某些地区使其不造成危险或错误的现象发生例: 不良品盒的使用/ 重工区域划分•复制原理: 同一工作,如需做二次以上,最好以COPY方式达成.例: 表格、发文的COPY / 治工具复制•层别原理: 线条粗细,不同的颜色.例: 制服不同/ 特别管制线/内外标签颜色•警告原理: 以声光等方式.例: 自动机报警灯/ Open/Short测试报警•缓和原理: 鸡蛋装运,保利龙等方式运用例: 设备流道、缓冲器案例:1.QL系列:改善前:压入机台承座材质为铁的,对产品PIN头有刮伤见铜,塑料打伤现象,且产品不易取出,后段用显微镜检验.改善后:将压入机台承座改为塑料,即避免了这一系列问题,产品轻松取下,且取消显微镜检验.2.DM-JACK半成品改善前:模板定位销是圆的,塑料易反装,导致整板塑料端子报废.改善后:模板定位销改为三角形,产品不易转动,并在模板前装一红色箭头,防止塑料放反.3.喷印机流道改善:改善前:由于产品体积较小,质量较轻.喷印时容易出现喷反,漏喷,重喷等多种品质隐患.改善后:在流道中间加一截挡板,来防止产品放反.消除多种隐患.4.治具合并:改善前:DM-JACK半成品插好1#,2#端子后,分别放入压入机压入,折CARRY机折CARRY,按两次按钮,送入下一工站.改善后:将压入机,折CARRY机合并,插好端子后放入,按一次按钮即可.5,JPD-004压入机台改善前:JPD003N-004在压入时右手十指去按,其它四指张开,一不小心就压到手指.改善后:给压入机台加上防护罩,消除安全隐患.第二部分动改法省力动作原则省时动作原则对”不可能”的人而言,就是”不可能”.动改法动作舒适原则对”可能”的人而言就是”可能”.动作简化原则原因:他动了脑子,想出了可能的点子出来.A.有关人体运用的原则原则1: 两手同时开始及完成动作(例: 试想独臂作业).原则2: 除休息时间外,两手不应同时空闲.原则3: 两臂的动作应反向同时对称.同时动作能使心理及生理上产生平衡的感觉,减少运用身体的应力机会,工作起来较轻松愉快.原则4: 尽可能以最低等级动作工作(动作等级分类: 如下图所示)原则5: 物体的动量尽可能利用之(例: 产品沿流道下滑/打击机).所谓动量,就是冲量=M*V (质量*速度)原则6: 联机曲线运动较方向突变直线运动佳(例:画圆与画正方形).研究表明:方向突变不但浪费时间,而且容易引起疲劳.原则7: 弹道式运动较轻快.弹道式运动只有在下列情形下才会停止下来:1.反向的肌肉制止力量2.碰到阻碍物3.运动的动量消失了原则8: 动作宜轻松有节奏.韵律节奏是指:有定期性的重复动作发生.B.有关工作场所布置与环境之原则原则9: 工具物料应置于固定处所.整理整顿的重要性: 减少寻找时间.例: 物料摆放五定定点、定位、定品、位型、定量1~10杂乱排列时顺序联机较困难,定位排列联机容易.原则10: 工具物料装置应依工作顺序排列并置于近处.使物料在使用过程中的活动范围减至最小.例: 现场物料摆放依工序/ 物品摆放依使用顺序(或先进先出).原则11: 利用重力喂料,愈近愈佳. (以防冲击太大)例:现场物料斗(箱)原则12: 利用重力堕送.例:沿斜面下滑.原则13: 适当之照明.适当的照明指:1. 适合其工作的充足光照度2. 光线颜色必须适当,没有反光3. 正确的投射方向同时考虑物体的”可见度”,可见度由下列因素决定:1.物体本身的明亮度2.物体与背景物的对比度3.物体本身的尺寸大小4.物体与眼睛之距离.5.其中因素如:注意力分散.疲劳.反应时间及反光等.原则14: 工作台椅应适当舒适.肘部能放于工作台上为佳,高椅时必须有垫脚设计.例: 试想若椅子太高或太低会怎么样.一般一个良好的坐椅设计应具有下列特征:1.高低可以调整2.坚固耐用,不会摇摆.3.坐垫应考虑人体工效学之形状成形.4.必须有靠背以支撑脊椎骨.C 有关手工具设备之原则原则15: 尽量以足踏/ 夹具替代手之工作.例: 脚踏开关/ 产品座附夹具功能.足踏设计考虑: 1.踏板面积大小2.踩踏时身体重量负荷之大小.3.设计方式:不要使操作者在操作时产生身体重心不稳的现象原则16: 尽可能将二种工具合并.将工具放下后再拿起比将一头转为另一头费时.例: 铆SHELL & 整形治具/ 预压& 热熔治具.原则17: 工具、物料预放在工作位置(例: 目视工具定位板).预放工具:将物体预先放置在适当的使用位置上,方便抓取,省时.悬挂的起子比放在一边时拿取省时.(下降.上升)原则18: 以手指负荷能力分配工作.原则19: 手柄接触面积尽可能加大例: 汽车方向盘包皮/圆形手柄.原则20: 操作杆尽可能少变更姿势.例: 船舵盘手把的适当数量设置/ 机车方向盘由Y形=> 圆形动作改善的基本方向?动作改善的重点要作动作改善必须从排除以下工作着手:1.需用力气的工作:必须使手.脚或全身用力方能完成的工作,或向膝下方伸手及蹲下拿起物品的动作.因为这些工作会引起肌肉的疲劳.2.不自然的姿势:如蹲下做事,弯腰工作等.3.需要注意力的工作:如必须仔细对准的工作或必须谨慎挑选的工作等都会引起精神上的疲劳.4.厌恶的工作:如噪音大,空气污浊,机器易故障的工作.•改善原则: 剔除合并重排简化动作改善的技巧与要点一.剔除a.剔除所可能的作业步骤或动作(包括身体,足,手臂或眼)b.剔除工作中的不规律性,使动作成为自发性,并使各种物品置放于固定地点.c.剔除以手作为持物工具的工作d.剔除不方便或不自然的动作e.剔除必须使用肌力才能维持的姿势f.剔除必须使用肌力的工作,而以动力工具取代之g.剔除必克服”动量”的工作h.剔除危险的工作i.剔除所有不必要的闲置时间二.合并a.把必须突然改变方向的各个小动作结合成一个连续的曲线动作b.合并各种工具使之成为用途c.合并可能的作业d.合并可能同时进行的动作三.重组a.使工作平均于两手,两手之同时动作最好呈对称性b.小组作业时,应把工作平均分配给各成员c.把工作安排成清的直线顺序四.简化a.使用最低等级的肌肉工作b.减少视觉动作并降低必须注视的次数c.保持在正常动作范围内工作d.缩短动作距离e.使手柄,操作杆,脚踏板,按钮均在手足可及之处f.在需要运用肌力时,应尽量利用工具或工作物的动量g.使用最简单的动素组合来完成工作h.减少每一动作的复杂性第三部分流程法一.流程法的意义:是”制程分析”最基本,最重要的技朮.也是降低”隐藏成本”,分析解决间题的最有力的工具.1.特点:清楚的标示所有的加工.搬运.检验.迟延等事项据以分析研究.设法减低各种事物的次数与所需时间及距离,降低隐藏成本的情况由此可以显示出来.2.运用范围:a.该件工作必须经历一个以上不同地点的动作才能完成.b.该件工作必须经由一个以上人来完成.3.功用:a.用于记载现行工作的过程.b.依5.1之记录,加以质问,寻求改善的地方.c.用以比较改善前及改善后之差异情形.5.符号:1作业------凡是需操作或使物理,化学性变化,准备物料等的总称搬运------由A处移至B处检验------鉴定物体而加以检查,测量等等待------物体或人因情况不允许或不立即采取下一步骤时称等待储存------物体之保存或等待流程图为 a.工作物流程图:以物体为;对象记录其被加工完成的流程图.b.工作人流程图:按工作人之动作来记录的流程图.c.图表介绍:为分析流程方便而特作规定.二.流程分析部分1.作业分析:考虑操作是否受设计方面的影响.加工条件是否可以改变(合并工站.动作等)2.搬运分析:搬运重量,距离,所费时间.其间还涉及到厂房空间及布置,机器排列,运输方法和工具等.3.检验(质量)分析:检验的目的:减少质量的变异性. 通常须考虑制成品的功能要求,精确度要求.检出不良品时,其检验价值如何?4.储存分析:此部分发生往往是因为材料或零件未到货,或者下一步加工之机器不胜重荷,须暂为等待所致.因此应对各种控制作重点考虑.5.等待分析:延迟纯为浪费,理应减至最低限度.此部分涉及人员调配控制及闲余能量分析的问题.应考虑人为或设备改进部分(由人工--- 电梯,拖车等)总之,各工站的分析都应在观察记录的基础上依照”ECRS”的原则予以处理.三.流程查核表“工作物”流程查核表:1.基本原则:a.减少制程数.b.安排最佳顺序. C.使各制程尽可能经济化.d.减少搬运e.如果有利时设法合并制程f.缩短移动距离g.找出最经济的移动方法h.在制品之存货量降低i.在最有利的位置使用最少的控制点.2.考虑下列因素有无制程可以省略?.a.不需要的制程(探讨:为何现在有?)b.使用新设备(探讨:为何目前使用此设备?)c.改变操作或储存位置(探讨:为何目前在此位置?)d.改变工作顺序(探讨:为何使用目前的工作顺序?)e.改变产品设计(探讨:为何现在如此设计?)f.改变入厂材料规格. (探讨:为何目前所定的材料如此?)3.有哪些制程可以合并在一起..1.工作场所.位置2.设备3.制造顺序4.产品设计’5.原材料.物料4.若重新安排制程,是否能使制程更短?5.有哪些制程可以更简化?四.”工作人”流程查核表1.基本原则a.尽可能删除不必要的步骤b.合并步骤c.缩短步骤d.安排最佳的顺序e.尽可能使各步骤经济化2.考虑下列步骤有无操作可以省略.合并.缩短.简短?a.不需要的操作.b.改变工作顺序c.利用新设备或重新编排设备d.改变产品形式e.更深入地认识部分的工人.3.考虑下列因素,有何移动可以被省略.合并.缩短.简短?a.废除某些操作b.改变物品存放场所c.将某些操作移到其他较方便的制程中d.改变工厂布置e.改变工作顺序f.利用输送带(必须是经济的)4. 考虑下列因素,有何延迟可以被省略.合并.缩短.简短?a.改变工作顺序b.改变工厂布置c.使用新设备或不同设备5.有何计数或检验的工作可以被省略.合并.缩短.简短?a.它们真的需要吗?能带来哪些效果或情报?b.有无不必要的重复现象.c.这些工作由别人来做是否更方便?d.在制程中,它们是否在最佳位置?e.能否使用抽样检验或统计控制?6.有无制程变得更加安全?a.改变工作顺序.b.使用新的或不同的设备c.改变工厂布置第四部分:五五法(质疑创意法)•When / Where / Who / What / why/how一.目的:熟悉有系统的质问技巧,以协助吾人发掘问题的真正根源所在以及可能的创造改善途径.5W1H: where:何处,在什么地方,什么空间when:何时what:何者.是什么东西/事/发生对象who:何人,是什么人在做/生产主体why:为何,怎么做的5 * 5 问法:指对问题的质疑不只一次,多问几次.在改善前1.要”打破砂锅问到底”,确实掌握了解问题所在.2.掌握现状的所有事实.怀疑并非只是笼统的抽象思维,应该是有系统的,循序渐进的,而且是有具体的方向. 生产的五大要素与5W1Hwhy二.质问的技巧1.对”目的”(WHAT)的质问a.目的是什么?b.条件是什么c.哪一部分工作要做d.重点是什么? 什么有关系? 规范是什么?功用是什么?等等.2.有关”人”(man)方面的质问a.是谁做的? 为何由他做?是否可由别人做? 谁最适合做这些事?b.为什么不把授权(股长)去决定?谁做最好?效率最高?3.对”工作顺序”(when)的质问:变更时间的顺序a.在何时做的? 为何要在当时做? 改在另外的时间又如何?4.有关”何时”的质问是否可改变时间点来达到既消除瓶颈,又达到预期目的呢?5.对”地点”(where)的质疑:变更场所或对场所内的物品布置重新组合.在何处做的?改善创意的基本观念.△打破传统习惯的束缚. ~~~没有最好、只有更好△工作改善最大的阻碍,并不在于技朮不足,而在于一个人的想法. ~~~ 别轻易说“不行”,起而行之△尝试从另一个角度来思考.~~~ 善于假设、推断,假若我是你该怎么做△发挥直觉力----创造力的源泉.~~~ 觉得不对(不应该),就应试着去改善△蚕食策略. ~~~ 不怕多、只怕不知道多或不去做.五五法实例:JACK永久性open抱怨无作业标准未制作标准未重视无隐患意识懒(有概念) 无训练无概念产生创意的思考法则相反法则:里外调换,上下颠倒,职务互换,作业次序反转,由左向右改为由右向左.例: 主管轮调/工站次序调整拼图法则将每一基本单元分解出来,再尝试重新组合的方式,可能会有意想不到的效果例:如何配色衣服会更美观?大小法则改变尺寸.形状等的大小,看看其影响会如何?改变增大时有加.乘,缩小时有减.除,根据这种原则可以产生很多创意.例:西瓜瓜子无子瓜/产品吹气等多余工站例外法则将经常发生的事物与偶然发生的事物作区别.偶发事件作例外管理(“一般”与“特殊”情况)例: 制造部的例外管理.集合法则将多用途的东西组合,或不同单元的事物结合,效用会如何呢?例:刀.叉,开瓶匙的结合/音乐卡片替代法则考虑用别的方式来替代现有的方式,会有什么样的结果呢?例:呆.废料可再利用吗?/是否有更合适的代用品?饭粒代胶水模仿法则模仿是创意的最佳触媒,借着参考现物触类旁通引发新的创意.蜘蛛网鱼网/蛙眼弧形雷达水平法则发挥联想力.考虑由水平方向支思考.突破传统及习惯上的缚束.例花香味化妆品味坐式椅子形状定数法则将经常发生的事物予以制度化,可以产生许多简化的效果及提高.例:特殊管治方法.第五部分人机法•意义:以图表的方式.,记录操作人员与一部或多部机器的操作关系,并藉此记录来进一步的分析与改善.•作用:---- 人与机器的时间有无空闲.---- 利用这段空闲,操作另一部机器.---- 利用空闲,作清除削屑、量测或其他手工工作.一.作用:学习如何记录人与机器配合工作时的过程.即:主要是分析人工或机器能量(时间)的闲余,以谋求消除浪费增进效率之道.在人机配合法中一般人工作周期往往比机器运行周期短,为谋求利用这些闲余,方法如下:a.利用这些空闲时间操作另一部机器b.利用这些空闲时间作清除余料,量测工作wu或其他手工之操作.2..适用范围a.1人多机或1机b.数人多机或1机c.数人操作共同的工作.3.功用:a.了解在现况下,操作人员之时间或机器之时间是否妥善应用.b.依上述之记录加以质疑,寻求改善的地方.c.用以比较改善前与改善后的差异情形.4.符号说明:三.人机查检表1.基本原则:a.平衡小组之工作量b.增加机器使用之比率c.减轻负担最重的人员之工作d.删除不必要的步骤e.合并各步骤f.使每一步骤容易进行2.附属操作能否删除?a.视同不必要而删除b.以改善工作次序而删除c.使用新的或不同之设备而删除d.以改变布置而删除3.移动能否删除?a.随操作之删除而删除b.合并c.改变设备d.改变布置e.改变工作次序f.使用输送带4.迟延能否删除?a.改变工作次序b.改变布置c.使用新的或不同的设备5.检验能否删除?a.此检真的必须吗?检后资料是否有用?b.是否有必要?c.留给下工站是否更方便?d.在此检验是否为最佳位置?6.操作能否合并a.改变工作之次序b.以新或不同之设备c.改变布置7.移动能否合并?a.—b.---c.改变每次搬运之数量8.迟延能否合并?9.检验能否合并?a.改变工作之次序b.改变布置10.操作能否简易行之?a.使用更好的工具b.改变control的位置c.使用更大的容器d.利用惯性e.减少视觉需求f.采用更舒适的高度g.使用夹具11.移物能否简易行之?c.改变布置,缩短距离d.改变移物之方向e.改变在制程中的位置,以缩短距离12..由于新人员之影响所产生的迟延,能否删除?a.改变参加小组人员b.改变所使用是改变:减少人员迟延时间至最低程度,以减少影响器械工作时间减少机器之空闲时至最低限度.c.小组中各人之工作岗位间的距离重新安排d.改变小组内各人之工作次序第六部分双手法•意义:以图表的方式.,记录操作人员与一部或多部机器的操作关系,并藉此记录来进一步的分析与改善.1.适用范围: a.适用于以人为主的工作,即研究对象为人体的双手或双足b.专注于某一固定工作地点之研究,即该工作固定在此地点上实施/c.该件工作有高度的重复性,即该件工作会再次大量生产2.功用: a.用于记录现行操作者的双手(足)的动作过程.b.对所记录下的内容加以质疑,寻求改善的地方.c.用于比较改善前与改善后的情形,差异.3.正常工作范围:指在坐姿状态双手之正常活动可及的范围,是为正常工作范围(约37-40cm)作用:---- 人与机器的时间有无空闲.---- 利用这段空闲,操作另一部机器.---- 利用空闲,作清除削屑、量测或其他手工工作.一.双手查检表1.基本原则a.将步骤减至最低b.安排最好顺序c.合并可能的步骤d.使每一步骤尽量简单e.平衡双手f.避免用手持住g.工作场所应考虑人体工学2.附属操作能否删除a.因不需要而删除b.因改变工作顺序而删除c.因改变工具或设备而删除d.因改变工作场所的布置而删除e.因材料的些许改变而删除f.因产品的些许改变而删除g.因治具,夹具的使用或改善而删除3.移物能否删除?a.因不需要而删除b.因改变工具,设备或利用自动滑落,工具使用方法改变等而删除4.持住动作能否删除?a.因不必要而删除b.因使用简单的持住装置或挂具需要而删除5.迟延能否删除或缩短?a.因不必要b.改变身体各部位的工作c.平衡身体各部位的工作d.同时做两件事e.修改工作,使两手做相同工作,但相位(phase)不同6.附属操作能否简化?a.使用较好的工具b.改变工具的放置位置c.使用较好的材料容器d.可能的话,利用杠杆原理(leverage)e.可能的话,利用慢性原理f.可能的话,利用重力原理g.减少使用视觉的需要h.改善工作场所的高度(使之在肘部以下)7.移物能否简化?a.改变布置,缩短距离b.改变移动方向c.使移动平顺而连续,避免骤停现象8.持住能否简化?a.缩短持住时间b.使用较有力的身体部位(如腿)或使用足部操作之夹具.第七部分抽查法•利用统计学原理,进行抽样调查的方法.•样本的概念/ 群体.•抽样及工作抽查的好处:---- 时间上不允许/ 成本大/ 不可能/ 不必要---- 观测时间短---- 从事观测记录的人员不需要具备太高深的技术---- 对被观测的对象所产生的干扰次数及时间。
- 1、下载文档前请自行甄别文档内容的完整性,平台不提供额外的编辑、内容补充、找答案等附加服务。
- 2、"仅部分预览"的文档,不可在线预览部分如存在完整性等问题,可反馈申请退款(可完整预览的文档不适用该条件!)。
- 3、如文档侵犯您的权益,请联系客服反馈,我们会尽快为您处理(人工客服工作时间:9:00-18:30)。
作業空間及通 道狹窄
5
一.人機配合法 案例2.DIP制程FCT測試改善2/3
改善歷程
改善后雙邊作業 1.人員作業效率提 高,1人操作9臺 機 2.機臺利用率提升 3.空間利用率高
6
一.人機配合法 案例2.DIP制程FCT測試改善3/3
改善后效果
【改善前】 【改善后】
7
二. 動作改善法 案例1:DIP制程取放治具改善1/3
消除手臂突變
11
三. 流程程序法 案例1:成型制程改善1/3
原作業 動畫演示
成型
印刷
組裝
12
三. 流程程序法 案例1:成型制程改善2/3
改善前流程
1
1
改善后流程
1
1
成型出爐
品質檢驗 貼保護膜
成型出爐 品質檢驗 貼保護膜 運至印刷 印刷 運至組裝 暫存 揭保護膜 組裝
1 2 2 3 4 3
2
運至印刷
1.L10測試治具改善 2.SMT上料防混料改善 3:SMT空焊降低改善
1.烤漆車間物流改善 2.烤漆雜質毛絲分析 1:組裝雙手作業改善
P20 P21-23 P24-26
P27-29 P30 P31-32
五五法(5W1H提問)
雙手操作法
2
一.人機配合法 案例1.完成品無線檢查改善1/2
人機操作分析
改善前 完成品無線檢查 一人兩機﹐人的利用率 只有50.8%﹐造成人力 的巨大浪費。
3
一.人機配合法 案例1.完成品無線檢查改善2/2
人機操作分析
改善后 完成品無線檢查 一人三機﹐人的利用率 提升到75.6%﹐大大提 升人的利用率
4
一.人機配合法 案例2.DIP制程FCT測試改善1/3
現狀分析
1.人的工作效率為50%. 2.機器的利用率為60%.
改善后Drill時間的流程程序圖
減少多次 操作和修 復針測等 無效工時
16
四. 抽查法 案例1:SMT人力精實改善1/3
SMT人力配置現狀(改善前)
A side (10人)
NO 1 工站 線長 人數 1 NO 1
B side (11人)
工站 線長 人數 1
2
3 4 5 6 7 8 合計
全技員
印刷 上料 爐前目檢 AOI 爐后比對 爐后目檢 工站
改善后效果
A side
改善前 NO 工站 改善后 人數 1 0 1 2 1 1 精簡 NO 1 2 3 4 5 工站 線長 全技員 印刷 上料 爐前目檢 1 1 1 2 1
B side
改善前 改善后 人數 1 0 1 2 1 1 精簡
1
2
線長
全技員
1
1
3
4 5
印刷
上料 爐前目檢
1
2 1
6
7 8 合計
檢驗
裝齒輪組 等待 貼排線 插軟板 傳遞半成品
4
1
鎖螺絲
4
4
1.5
貼貼紙
檢驗
時間 操作 (s) ○ 1 4 4.5 4 4 1 2.5 4 5 1.5 31.5 19
檢驗 □
2.5
1
9
改善作業後,平均工時由42.3->31.5S
32
1
1 2 1 1 1 2 10人
2
3 4 5 6 7 8 合計
全技員
印刷 上料 爐前目檢 AOI 爐后比對 爐后目檢 工站
1
1 2 1 1 1 3 11人
17
四. 抽查法 案例1:SMT人力精實改善2/3
改善歷程
選擇線體﹕
選取單側上料和兩側上料兩種線體進行抽樣 利用工作抽樣法評估﹕
18
四. 抽查法 案例1:SMT人力精實改善3/3
物料暫放區
全 檢 帶
全 檢 帶
全 檢 帶 物流交叉點多
鳥籠車暫放區
物料暫放區
物流路線集中 運 輸 帶 運 輸 帶
27
運 輸 帶
六. 五五法 案例1:烤漆車間物流改善2/3
改善過程
項目
Why When
分類分析
為什么要做?
改善對策
車間佈局不合理,人員物料流通交 叉點較多,對產品產生影響.而且也 耗費較多的人力物力. 在生產排配淡季產能爬坡之前 增加一個風淋室,改善上下料區與 立式烤爐布局
AOI
爐后比對 爐后目檢
1
1 2 10人
1
1 1 8人 1 2
6
7 8 合計
AOI
爐后比對 爐后目檢
1
1 3 11人
1
1 1 9人 2 2
19
五. 防錯法 案例1:L10測試治具改善1/1
改善前
改善后
設計制作測試自動拔插治具,減少誤操作,減少劃傷
20
五. 防錯法 案例2:SMT上料防混料改善1/3
揭保護膜 印刷 貼保護膜 運至組裝 暫存 揭保護膜 組裝
1 2 3 3
1
5
6
5 6
13
三. 流程程序法 案例1:成型制程改善3/3
改善后作業 動畫演示
成型
印刷
組裝
改善后節約一次保護膜的使用
14
三. 流程程序法 案例2:鑽孔加工流程改善1/2
改善前Drill時間的流程程序圖
15
三. 流程程序法 案例2:鑽孔加工流程改善2/2
為甚麼要對車間進行佈局整改?
何時做?有無其他更合適的時間? 選擇什么時間去做該項工作? 完成了什么?有無其他更好的工作? 對車間改善做了什么工作? 由誰做?有無更合適的人? 由誰其完成該項工作?
What
Who Where How
IE工程師主導改善專案,生產物流 部門配合執行
只有一個風淋室,上下料區集中,立 式烤爐與全檢區布局不合理 減少交叉點,儘可能的使物料單向 流通.盡可能的縮短流通距離.
上料防混料---防錯料台車支架的使用
改善前
自製防錯料 台車支架
改善後
HITACHI台車
軌道 號條 碼 物料
料帶易重疊交叉,且不易發現 掃描軌道號太遠,不易判斷對應軌道 以上缺陷使上料員不能及時發現 物料交叉接錯
物料擺放整齊,不會形成料帶交叉 對應掃描軌道號就在料帶下方,掃 描時不會掃錯 防錯料台車支架可以有效防止
2 檢
5
10
物流路線簡單 9 運 運 輸 輸 帶
物料暫放區
物料風 鳥籠車暫放區 淋室
6
帶
8 運 運 輸 輸 帶 帶
29
7 運 輸 帶
六. 五五法 案例2:烤漆雜質毛絲分析1/1
對于高光烤漆產品雜質毛絲不良多的原因分析 為什么會產生雜質毛絲的不良? 環境中不可避免的存在一些細微的塵粒,粘在產品 表面就會形成雜質毛絲 為什么這些塵粒會粘在產品表面? 因為產品表面靜電值超過規定,發生靜電吸附 為什么我們已經用了靜電除塵的方法,產品表面靜電 值還會超標?
28
在何處做?有無其他更合適的地方?
不合理的佈局主要表現在那裡? 如何做?有無其它更合适的方法? 怎樣進行有效改善?
六. 五五法 案例1:烤漆車間物流改善3/3
改善后物流圖示
物料風 淋室
貨淋室回流
1
品保區
全 帶 全 3 檢 單向流通減少交叉 帶 全 4 檢 帶 貨淋室回流
鳥籠車暫放區 物 料 暫 放 區
裝齒輪組
取排線 貼排線 等待 插軟板 傳遞半成品
4
2.5
3
4.5
4
2.8 2..5
4
2.5 5
檢驗
19
11 2.8
9.5
左手無效時間7.8S,搬運11S能否降低?
31
七. 雙手法 案例1:組裝雙手作業改善2/2 下蓋組裝雙手作業分析
左手
搬運半成品
1 4
改善後
符號 搬運 等待 D
右手
等待
4.5 2.5 5
,
23
五. 防錯法 案例3:SMT空焊降低改善1/3
改善前 1.1 新機種Raptor量產初期,SMT BSide目檢工站發現SD Conn空焊(浮高)與掉件不良,達0.78%,占總不良比重:22%, 居不良首位.
24
五. 防錯法 案例3:SMT空焊降低改善2/3
改善后 在BSide Reflow前增加一個夾具(如圖),能彈性的支撑SD Conn,防止焊點重熔時受重力等影響產生不良.
夾持PCB 板邊
彈片支撑CN23
25
五. 防錯法 案例3:SMT空焊降低改善3/3
改善效果 統計確認,增加夾具後過BSide Reflow導致的該不良從 0.78%降到0.01%.產品品質得到客戶更好的認可.
26
六. 五五法 案例1:烤漆車間物流改善1/3
現狀物流圖示
貨淋室回流
物料風 淋室
品保區
現狀描述
作業員作業內容:
2 1
1.取放PCB板與載具
2.浮高檢查 作業員1在傳送帶上拿 板,取放產品,并轉身放 治具,持續作業,勞動強 度高。
8
二. 動作改善法 案例1:DIP制程取放治具改善2/3
改善歷程
9
二. 動作改善法 案例1:DIP制程取放治具改善3/3
改善后效果
改善后動畫演示:
波峰焊
新增流水線
因為靜電除塵后的粘塵布擦拭產品表面又產生了 靜電,因此產生靜電吸附,造成雜質毛絲的不良
30
七. 雙手法 案例1:組裝雙手作業改善1/2 下蓋組裝雙手作業分析 改善前
左手
轉身搬運 檢驗
3 4.5
右手
等待 取齒輪組 鎖螺絲 貼貼紙
符號 時間 操作 搬運 等待 檢驗 (s) ○ D □ 3 4.5 3 4 4.5 2.5 4 2.5 2.8 4 5 2.5 42.3