(9)光刻工艺
半导体光刻工艺介绍

半导体光刻工艺介绍
半导体光刻工艺是半导体制造中最为重要的工序之一。
主要作用是将图形信息从掩模版(也称掩膜版)上保真传输、转印到半导体材料衬底上。
以下是光刻工艺的主要步骤:
硅片清洗烘干:湿法清洗+去离子水冲洗+脱水烘焙(热板150~250℃,1~2分钟,氮气保护)。
涂底:气相成底膜的热板涂底。
旋转涂胶:静态涂胶(Static)。
软烘:真空热板,85~120℃,30~60秒。
对准并曝光:光刻机通常采用步进式 (Stepper)或扫描式 (Scanner)等,通过近紫外光 (Near Ultra-Violet,NUV)、中紫外光 (Mid UV,MUV)、深紫外光(Deep UV,DUV)、真空紫外光 (Vacuum UV,VUV)、极短紫外光 (Extreme UV,EUV)、X-光 (X-Ray)等光源对光刻胶进行曝光,使得晶圆内产生电路图案。
后烘:PEB,Post Exposure Baking。
显影:Development。
硬烘:Hard Baking。
光刻工艺的基本原理是利用涂敷在衬底表面的光刻胶的光化学反应作用,记录掩模版上的器件图形,从而实现将集成器件图形从设计转印到衬底的目的。
光刻工艺流程
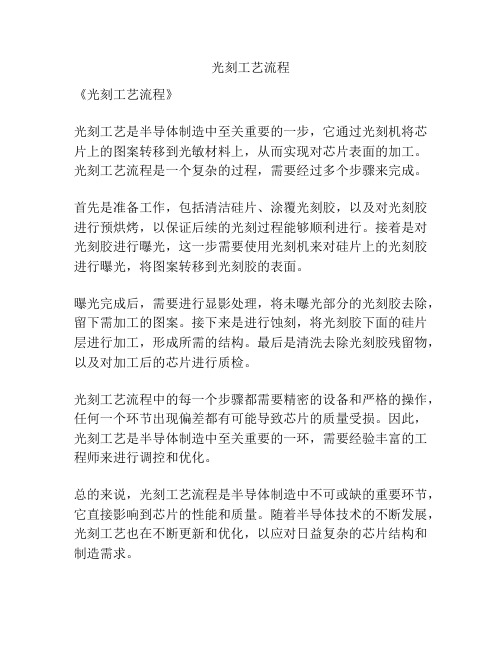
光刻工艺流程
《光刻工艺流程》
光刻工艺是半导体制造中至关重要的一步,它通过光刻机将芯片上的图案转移到光敏材料上,从而实现对芯片表面的加工。
光刻工艺流程是一个复杂的过程,需要经过多个步骤来完成。
首先是准备工作,包括清洁硅片、涂覆光刻胶,以及对光刻胶进行预烘烤,以保证后续的光刻过程能够顺利进行。
接着是对光刻胶进行曝光,这一步需要使用光刻机来对硅片上的光刻胶进行曝光,将图案转移到光刻胶的表面。
曝光完成后,需要进行显影处理,将未曝光部分的光刻胶去除,留下需加工的图案。
接下来是进行蚀刻,将光刻胶下面的硅片层进行加工,形成所需的结构。
最后是清洗去除光刻胶残留物,以及对加工后的芯片进行质检。
光刻工艺流程中的每一个步骤都需要精密的设备和严格的操作,任何一个环节出现偏差都有可能导致芯片的质量受损。
因此,光刻工艺是半导体制造中至关重要的一环,需要经验丰富的工程师来进行调控和优化。
总的来说,光刻工艺流程是半导体制造中不可或缺的重要环节,它直接影响到芯片的性能和质量。
随着半导体技术的不断发展,光刻工艺也在不断更新和优化,以应对日益复杂的芯片结构和制造需求。
基本光刻工艺流程

期望印在硅片上的光刻胶结构
光刻胶岛
Substrate
Chrome铬 Window
Quartz石英 Island
Mask pattern required when using negative photoresist (opposite of intended structure) 当使用负胶时要求掩膜版上 的图形与想要的结构相反
Mask pattern required when using positive photoresist
(same as intended structure) 当使用正胶时要求掩膜版上
的图形与想要的结构相同
13.3 光刻10步法
把图形从掩膜版上转移到晶圆表面 是由多个步骤完成的(见下页图),特 征图形尺寸、对准精度、晶园表面情况 和光刻层数都会影响到特定光刻工艺的 难以程度。虽然许多光刻工艺都不尽相 同,但大部分都是基于光刻10步法的变 异或选项。所以了解和掌握基本的光刻 10步法是非常必要的。
电波
电波
波长 10 ( cm )
10
10
10
10
10
10
• 除了普通光源,经常还根据不同需要选择X射 线或者电子束作为曝光光源。那么光刻胶灵敏 性作为一个参数,使通过能够使基本的反应开 始所需要的能量总和来衡量的,它的单位是mJ/ 平方厘米
• 负性胶通常的曝光时间是5~15秒,而正性胶则 需要用上3~4倍的时间。
Island
Window
pPhhoottoorreessiisstt
OOoxxiiddee SSsiiillliiicccooonnnsssuuubbbssstttrrraaattteee
Resulting pattern after the resist is developed.
光刻工艺的主要步骤
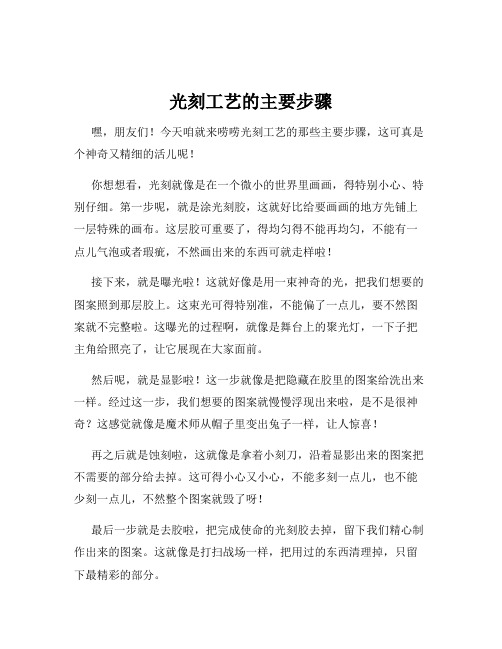
光刻工艺的主要步骤嘿,朋友们!今天咱就来唠唠光刻工艺的那些主要步骤,这可真是个神奇又精细的活儿呢!你想想看,光刻就像是在一个微小的世界里画画,得特别小心、特别仔细。
第一步呢,就是涂光刻胶,这就好比给要画画的地方先铺上一层特殊的画布。
这层胶可重要了,得均匀得不能再均匀,不能有一点儿气泡或者瑕疵,不然画出来的东西可就走样啦!接下来,就是曝光啦!这就好像是用一束神奇的光,把我们想要的图案照到那层胶上。
这束光可得特别准,不能偏了一点儿,要不然图案就不完整啦。
这曝光的过程啊,就像是舞台上的聚光灯,一下子把主角给照亮了,让它展现在大家面前。
然后呢,就是显影啦!这一步就像是把隐藏在胶里的图案给洗出来一样。
经过这一步,我们想要的图案就慢慢浮现出来啦,是不是很神奇?这感觉就像是魔术师从帽子里变出兔子一样,让人惊喜!再之后就是蚀刻啦,这就像是拿着小刻刀,沿着显影出来的图案把不需要的部分给去掉。
这可得小心又小心,不能多刻一点儿,也不能少刻一点儿,不然整个图案就毁了呀!最后一步就是去胶啦,把完成使命的光刻胶去掉,留下我们精心制作出来的图案。
这就像是打扫战场一样,把用过的东西清理掉,只留下最精彩的部分。
你说这光刻工艺神奇不神奇?每一步都得小心翼翼,就像走钢丝一样,稍有偏差就前功尽弃啦!但正是因为有了这么精细的工艺,我们才能有那些厉害的芯片,让我们的电子设备变得越来越强大。
这就好像是搭积木,一块一块小心地堆起来,最后建成一座漂亮的城堡。
所以啊,可别小看了这光刻工艺的主要步骤,它们可都是至关重要的呢!没有它们,哪来我们现在这么方便快捷的科技生活呀!这就像是一场精彩的演出,每一个环节都不能出错,才能给观众带来最棒的体验。
咱得好好感谢那些在背后默默努力的科学家和工程师们,是他们让这一切成为可能啊!怎么样,现在是不是对光刻工艺的主要步骤有了更深刻的认识啦?。
光刻工艺流程

光刻工艺流程
光刻工艺是在半导体制造中至关重要的一个工艺,它是制造芯片必不可少的环节。
本文将介绍光刻工艺流程及其每个步骤的作用和方法。
首先,要准备好硅片和光刻胶。
硅片上会先涂上一层光刻胶,然后通过光刻机对其进行曝光、显影和烘干的操作。
其次,进行光刻胶的涂布。
首先,将准备好的硅片放到光刻机的微小旋转台上,然后,使用光刻胶涂布机器对硅片进行涂布,将光刻胶均匀地涂抹在硅片上。
这个工作是十分重要的,因为如果光刻胶的涂布不均匀,将会影响后续制程的成果。
接着,进行曝光。
将涂好光刻胶的硅片放入光刻机的曝光台中,加入掩模版后,开启光刻机器的曝光光源,使镀有光刻胶的硅片根据掩膜图案将辐射能量吸收。
曝光时间的长短取决于掩膜的复杂程度以及所用的光刻胶类型。
进行显影。
曝光后,将硅片放入显影液中,在显影液中加持一定时间使没有经过曝光的光刻胶部分被清除,从而满足标准掩膜的设计要求。
要注意控制显影液的温度,时间和浓度,否则就会对芯片的制造产生影响。
最后进行烘干。
显影后的光刻胶薄层需要进行烘干,通过烘干将液体显影液中多余的水分挥发掉,光刻胶薄层变得坚硬。
需要注意的是,烘干的温度和时间要正确,不要过度或不足,以确保质量的稳定性。
总之,光刻工艺流程是一个非常精细的制程,非常需要注意每个步骤的细节,更需要操作人员的技术经验和操作规范。
只有这样,我们才能在制造芯片过程中保证产品的一致性和稳定性。
光刻与刻蚀工艺
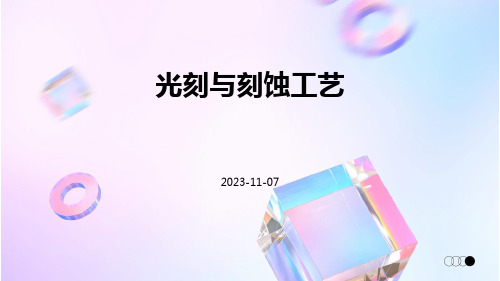
涂胶/显影技术
01
02
03
涂胶
在晶圆表面涂上一层光敏 胶,以保护非曝光区域并 提高图像对比度。
显影
用适当的溶剂去除曝光区 域的光敏胶,以形成所需 的图案。
控制胶厚
保持胶厚均匀,以避免图 像的扭曲和失真。
烘烤与曝光技术
烘烤
通过加热去除晶圆表面的湿气,以提高光敏胶的灵敏度和图像质 量。
曝光
将掩模图像投影到光敏胶上,通过光化学反应将图像转移到晶圆 上。
非接触式光刻
投影式非接触
利用光学系统将掩膜板上的图像投影到光刻胶涂层上,优点是无需直接接触,缺点是难度较高,需要精确的控 制系统。
电子束光刻
利用电子束在光刻胶上直接曝光,优点是分辨率高、无需掩膜板,缺点是生产效率低。
投影式光刻
接触式投影
掩膜板与光刻胶涂层之间保持接触,通过投影系统将图像投影到光刻胶上,优点是操作简单、高效, 缺点是图像质量可能受到掩膜板损伤和光刻胶污染的影响。
要点二
损伤控制
是指在刻蚀过程中避免对材料产生损伤。对于某些特殊 材料,如脆性材料,损伤控制尤为重要。如果刻蚀过程 中产生过多损伤,可能会导致材料性能下降甚至破裂。
感谢您的观看
THANKS
光刻工艺的基本步骤
涂胶
将光刻胶涂敷在硅片表面,以形成 光刻胶层。
烘烤
通过烘烤使光刻胶层干燥并固化。
曝光
将掩膜版上的图形对准硅片上的光 刻胶层,并使用曝光设备将图形转 移到光刻胶上。
显影
使用显影液将曝光后的光刻胶进行 化学处理,使图形更加清晰地展现 出来。
光刻工艺的重要性
光刻工艺是半导体制造中的关键环节,直接影响芯片的制造 质量和性能。
光刻工艺基础知识

光刻工艺基础知识PHOTO光刻工艺基础知识PHOTO (注:引用资料) 光刻工艺基础知识PHOTOPHOTO 流程?答:上光阻→曝光→显影→显影后检查→CD量测→Overlay量测何为光阻?其功能为何?其分为哪两种?搭:Photoresist(光阻).是一种感光的物质,其作用是将Pattern从光罩(Reticle)上传递到Wafer上的一种介质。
其分为正光阻和负光阻。
何为正光阻?答:正光阻,是光阻的一种,这种光阻的特性是将其曝光之后,感光部分的性质会改变,并在之后的显影过程中被曝光的部分被去除。
何为负光阻?答:负光阻也是光阻的一种类型,将其曝光之后,感光部分的性质被改变,但是这种光阻的特性与正光阻的特性刚好相反,其感光部分在将来的显影过程中会被留下,而没有被感光的部分则被显影过程去除。
何谓Photo?答:Photo=Photolithgraphy,光刻,将图形从光罩上成象到光阻上的过程。
Photo主要流程为何?答:Photo的流程分为前处理,上光阻,Soft Bake, 曝光,PEB,显影,Hard Bake 等。
何谓PHOTO区之前处理?答:在Wafer上涂布光阻之前,需要先对Wafer表面进行一系列的处理工作,以使光阻能在后面的涂布过程中能够被更可靠的涂布。
前处理主要包括Bake,HDMS等过程。
其中通过Bake将Wafer表面吸收的水分去除,然后进行HDMS(六甲基乙硅氮烷,以增加光阻与晶体表面附着的能力)工作,以使Wafer表面更容易与光阻结合。
何谓上光阻?答:上光阻是为了在Wafer表面得到厚度均匀的光阻薄膜。
光阻通过喷嘴(Nozzle)被喷涂在高速旋转的Wafer表面,并在离心力的作用下被均匀的涂布在Wafer的表面。
何谓Soft Bake?答:上完光阻之后,要进行Soft Bake,其主要目的是通过Soft Bake将光阻中的溶剂蒸发,并控制光阻的敏感度和将来的线宽,同时也将光阻中的残余内应力释放。
光刻工艺步骤介绍

光刻工艺步骤介绍光刻工艺是一种重要的微电子制造技术,用于将电子芯片的图案转移至硅片上。
下面我将详细介绍光刻工艺的步骤。
第一步:准备硅片在光刻工艺开始之前,首先需要准备好硅片。
这包括清洗硅片表面以去除任何杂质,并在其表面形成一层薄的光刻胶。
光刻胶一般是由聚合物(如光刻胶),溶剂和添加剂组成的混合物。
第二步:涂覆光刻胶准备好的硅片放置在旋涂机上,然后将光刻胶涂覆在硅片表面。
旋涂机会以高速旋转硅片,使光刻胶均匀地覆盖在整个表面上。
涂覆的光刻胶会在硅片上形成一层均匀的薄膜。
第三步:预烘烤涂覆光刻胶后,硅片需要进行预烘烤。
预烘烤的目的是将光刻胶中的溶剂挥发掉,使光刻胶更加稳定。
预烘烤是在较低的温度下进行的,一般在90-100°C之间。
第四步:对准和曝光在对准和曝光步骤中,使用光刻机将芯片的图案转移到光刻胶层上。
首先,在光刻机的对准系统下,将硅片和图案的掩膜进行对准。
对准系统使用电子束或激光进行确切的对准。
一旦对准完成,光刻机会使用紫外线光源照射光刻胶。
光刻胶的激发使其发生化学反应,形成了曝光图案。
第五步:后烘烤曝光完成后,硅片需要进行后烘烤。
后烘烤的目的是将光刻胶中的曝光图案进行固化,并增强其耐久性。
后烘烤的温度和时间会根据光刻胶的类型和用途而有所不同。
第六步:显影显影是将曝光图案从光刻胶中暴露出来的步骤。
使用化学溶液将未曝光的光刻胶部分溶解掉,只留下曝光图案。
这一步骤在洗涤机中进行,确保均匀地清洗掉不需要的光刻胶部分。
第七步:清洗显影完成后,硅片需要通过化学溶液进行清洗,以去除任何剩余的光刻胶和杂质。
清洗过程往往需要使用多种溶液和机械清洗的步骤,以确保硅片表面干净。
第八步:测量和检验最后一步是对光刻结果进行测量和检验。
使用显微镜、扫描电子显微镜(SEM)等设备,检查光刻图案是否与设计要求相符。
测量和检验可以帮助确认制造过程中的任何错误或缺陷,以便及时进行修正。
光刻胶及光刻工艺流程

光刻胶及光刻工艺流程光刻胶是集成电路制造过程中重要的材料之一,它的主要作用是在光刻工艺中作为掩膜保护剂,将紫外光照射过的区域与未经照射的区域进行区分,从而完成器件的精密图案的形成。
本文将介绍光刻胶及其在光刻工艺流程中的应用。
光刻胶(Photoresist)是一种特殊的感光材料,它可以在光的照射下发生化学反应,改变物质的化学和物理性质。
根据其特性,光刻胶可以分为两种类型:负型光刻胶和正型光刻胶。
负型光刻胶是在紫外光照射下,光刻胶会发生聚合反应,形成一层比原来的胶层更为固化的区域。
而未曝光的胶层在显影过程中被去除,形成比曝光区域更深的“坑”。
因此,负型光刻胶可形成器件的凹陷结构。
正型光刻胶则相反,未曝光的胶层会进一步发生聚合反应,在显影过程中保留下来形成比曝光区域更高的区域。
正型光刻胶可形成器件的突起结构。
在光刻工艺流程中,首先需要将光刻胶涂覆在晶圆表面。
这一步骤称为光刻胶的涂布。
涂布的目的是将光刻胶均匀地涂覆在晶圆表面,并形成一定厚度的胶层。
涂布方法包括旋涂法、滚涂法和喷洒法等。
涂布完成后,需要将光刻胶进行预烘烤。
预烘烤的目的是将光刻胶中的溶剂迅速挥发掉,使胶层迅速形成。
预烘烤的温度和时间需根据光刻胶的类型和要求进行调节。
接下来是曝光步骤。
曝光是将掩膜和光刻胶放置在光刻机中,通过紫外光的照射,将掩膜上的图案转移到光刻胶上。
光刻机使用的光源多是紫外光源,如Hg灯或氘灯。
曝光的参数包括曝光时间、曝光强度和曝光模式等。
完成曝光后,需要进行显影。
显影是将晶圆放入显影液中,显影液会溶解或去除光刻胶中未曝光的部分,留下曝光的部分。
显影液的种类和浓度需根据光刻胶的类型和要求进行选择。
显影完成后,还需进行后处理。
后处理通常包括后烘烤和清洗两个步骤。
后烘烤是将晶圆放入恒温烘炉中,将光刻胶中残留的溶剂和显影液彻底除去,使光刻胶更加稳定。
清洗则是将晶圆浸泡在溶剂中,去除掉与已曝光的光刻胶没有反应的部分。
光刻胶及其对应的工艺流程是集成电路制造中至关重要的一部分。
光刻工艺简要流程介绍

光刻工艺简要流程介绍光刻工艺是集成电路制造过程中的一项重要工艺,其主要作用是将电路图案按照一定比例缩小并转移到硅片上,形成集成电路的图案。
下面是光刻工艺的简要流程介绍。
1.硅片准备:首先,需要对硅片进行一系列处理,包括清洗、去除表面氧化层、去除杂质等,以确保硅片的表面光洁度和纯净度。
2.上光胶:将光刻胶涂布在硅片表面。
光刻胶是一种特殊的光敏聚合物,对特定波长的光线敏感。
胶涂布可以通过旋涂法、喷涂法等方式进行,以确保胶涂布均匀。
3.等光干燥:将胶涂布的硅片放入特定设备中进行等光干燥。
等光干燥的目的是将胶涂布的光刻胶暴露于特定的光照条件下,以进行后续的曝光制程。
4.接触曝光:采用光刻机进行接触曝光,将预先准备好的掩膜与胶涂布的硅片接触,并通过曝光源投射光束。
光刻胶能够吸收光束并将光的图案转移到胶涂布的硅片上,形成所需的电路图案。
5.显影:经过曝光后,需要进行显影,以去除未受光束照射的光刻胶。
显影液的成分根据光刻胶的特性来确定,可以通过浸泡、喷淋等方式进行显影。
显影液能够溶解未暴露于光束的部分光刻胶,从而形成所需的电路图案。
6.退胶:为了保护已经形成的电路图案,需要对胶涂布的硅片进行退胶处理。
退胶过程中使用氧等氧化物气体,能够将胶层中的光刻胶蒸发掉,从而完全去除胶层。
7.清洗:清洗是整个光刻工艺中的一个重要环节,目的是去除残留的光刻胶、显影液等杂质,并确保表面的洁净度。
清洗方法包括浸泡、超声波清洗、喷淋等。
8.检测:对最终产生的图案进行检测,确保电路图案的质量和准确性。
检测方法包括显微镜观察、扫描电子显微镜观察等。
以上就是光刻工艺的简要流程介绍。
光刻工艺是集成电路制造中至关重要的一环,通过精确的光刻过程,可以将电路图案转移到硅片上,实现电路的制造。
随着半导体技术的不断发展,光刻工艺也在不断改变和创新,以满足更高性能和更小尺寸的集成电路的需求。
第三章 光刻工艺技术

第三章光刻工艺技术光刻的本质在于将掩膜版上的图形复制到要进行刻蚀和离子注入的硅片上,作为半导体及其相关产业发展和进步的关键技术之一,光刻一方面被认为是半导体制造业发展的瓶颈,另一方面它却作为推动者,支撑着半导体产业的发展。
3.1 光学成像原理光刻的原理起源于印刷技术中的照相制版,是在一个平面上加工形成微图形。
随着器件尺寸的不断缩小,光刻技术也从最初的接触式、接近式曝光发展到目前普遍使用的投影式曝光,图3.1是投影式曝光示意图。
投影式曝光技术中由于硅片和掩膜版没有接触,从而避免了由于接触引入的工艺缺陷,同时掩膜版的利用率得以提高,因此,该曝光技术成为了目前光刻技术的主流。
下面介绍投影式曝光技术中的光学成像原理:图3.1 投影式曝光示意图光是一种电磁波,具有波动性。
根据惠更斯原理,波在传播过程中如遇障碍物,特别是当障碍物的大小与光的波长大小相当时,在障碍物附近衍生的多个点光源发出的球面波相叠加,使光波绕到障碍物的背面进行传播,从而发生衍射现象,如图3.2-3.3所示。
图3.2 光的衍射现象图3.3 光发生衍射时的衍射角由布拉格定律可以得到各级衍射角的大小为sinα=nλ/P,(n=0,±1, ±2, ±3……) (3.1)其中α为衍射角,λ为光源波长,P为光栅周期。
由此可见,P越小,相应衍射角就越大,透镜上产生的各级明暗条纹相隔距离就越大。
光刻系统中有两个重要的指标用以表征光刻成像质量:分辨率和焦深。
首先讨论两个重要参数:数值孔径(NA)和相干系数(σ)。
NA表征物镜收集衍射光的能力,用物镜收集的最大衍射角αm的正弦值表示,即NA=n·sinαm(3.2)其中,n为介质的折射率。
由此可知:NA越大,物镜收集衍射光的级次就越高(αm越大),另外,还可以通过增加介质折射率n的方法来增加数值孔径NA(如后面提到的浸没式光刻)。
光的空间相干系数σ说明了投影物镜表面被光源占据的程度,如图3.4所示,σ= sin δ/sin α = NA C /NA O (3.3)其中NA C 和NA O 分别为聚焦物镜和投影物镜的数值孔径。
光刻和刻蚀工艺流程
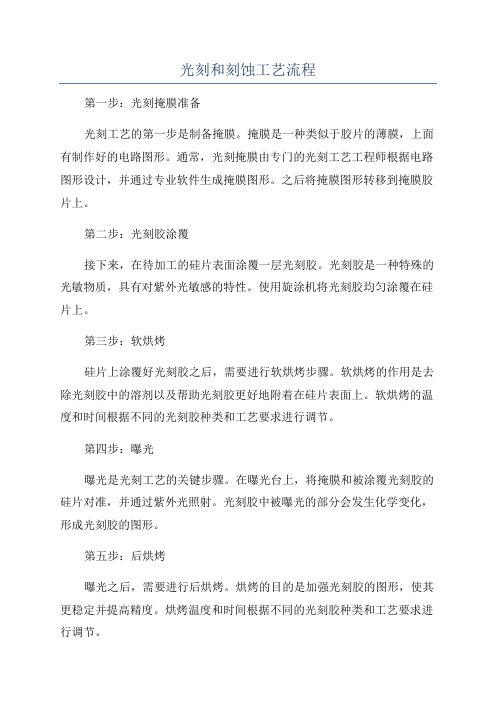
光刻和刻蚀工艺流程第一步:光刻掩膜准备光刻工艺的第一步是制备掩膜。
掩膜是一种类似于胶片的薄膜,上面有制作好的电路图形。
通常,光刻掩膜由专门的光刻工艺工程师根据电路图形设计,并通过专业软件生成掩膜图形。
之后将掩膜图形转移到掩膜胶片上。
第二步:光刻胶涂覆接下来,在待加工的硅片表面涂覆一层光刻胶。
光刻胶是一种特殊的光敏物质,具有对紫外光敏感的特性。
使用旋涂机将光刻胶均匀涂覆在硅片上。
第三步:软烘烤硅片上涂覆好光刻胶之后,需要进行软烘烤步骤。
软烘烤的作用是去除光刻胶中的溶剂以及帮助光刻胶更好地附着在硅片表面上。
软烘烤的温度和时间根据不同的光刻胶种类和工艺要求进行调节。
第四步:曝光曝光是光刻工艺的关键步骤。
在曝光台上,将掩膜和被涂覆光刻胶的硅片对准,并通过紫外光照射。
光刻胶中被曝光的部分会发生化学变化,形成光刻胶的图形。
第五步:后烘烤曝光之后,需要进行后烘烤。
烘烤的目的是加强光刻胶的图形,使其更稳定并提高精度。
烘烤温度和时间根据不同的光刻胶种类和工艺要求进行调节。
第六步:显影显影是将光刻胶中未曝光的部分溶解掉的步骤。
将硅片浸入特定的显影液中,显影液会将光刻胶中溶解掉的部分清除掉,形成具有电路图形的光刻胶。
第七步:刻蚀刻蚀是将未被光刻胶保护的硅片表面精确地去除掉部分的步骤,以形成电路图形。
刻蚀液根据硅片的材料和刻蚀目标而确定。
将硅片浸入刻蚀液中,刻蚀液会剥离掉没有光刻胶保护的硅片表面,形成光刻胶的图形。
第八步:去光刻胶刻蚀完成后,需要将光刻胶从硅片上去除。
通常使用酸性或碱性溶液将光刻胶溶解掉。
去光刻胶后,就得到了具有电路图形的硅片。
以上就是光刻和刻蚀的工艺流程。
光刻和刻蚀工艺对于微电子芯片的制造至关重要,能够提供精确的电路图形,是制造集成电路的基础步骤。
随着技术的不断发展,光刻和刻蚀工艺也在不断改进,以满足高集成度和高性能的微电子芯片的制造需求。
9章 光刻工艺

本章的学习目标: 1.了解光刻主要的特征参数。 2.掌握光刻胶的组成,能够区分正性光刻胶和
负性光刻胶。 3.了解掩膜板的分类及制备工艺流程。 4.掌握光刻工艺流程。 5.了解常用的光刻机的组成及特点。
9.1 光刻概念
图9-1 半导体制造工艺流程
图9-2 光刻的基本原理
1. 光刻的特征参数
Vacuum
微波烘箱
四、对准和曝光
工艺目的: 对准和曝光是将掩膜板上的图形通过镜头由紫外 光传递到涂有光刻胶的硅片上, 形成光敏感物质的 空间精确分布,从而实现精确的图形转移。
对准——同轴和离轴对准系统
曝光
对准标记
对准标记
1. 投影掩膜版的对位标记(RA) :在版的左右两 侧, RA与步进光刻机上的基准标记对准 2. 整场对准标记(GA):第一次曝光时被光刻在硅 片左右两边,用于每个硅片的粗对准 3. 精对准标记(FA):每个场曝光时被光刻的,用 于每个硅片曝光场和投影掩膜版的对准
3)刻画,利用电子束或激光等通过原版对空白版进行曝光, 将图形转移到光刻胶上,即刻画;
4)形成图形,对铬膜、氧化铁膜或明胶等进行刻蚀,形成 图形,最后除去残胶; 5)检测与修补,测量关键尺寸,检测针孔或残余遮光膜等 缺陷并对其进行修补; 6)老化与终检,在200~300℃的温度下烘烤几个小时,对 其进行老化。 (4)掩膜版分类
Developer puddle
Wafer Form puddle Spin spray
Spin rinse and dry
经曝光的正胶逐层溶解,中和反应只在光 刻胶表面进行。
非曝光区的负胶在显影液中首先形成凝胶 体,然后再分解,这就使整个负胶层被显影液 浸透而膨胀变形。
光刻工艺 光刻对准

NIKON工艺一、对位概述对光刻而言,其最重要的工艺控制项有两个,其一是条宽控制,其二是对位控制。
随着产品特征尺寸的越来越小,条宽和对位控制的要求也越来越高。
目前0.5um的产品,条宽的要求一般是不超过中心值的10%,即条宽在0.5±0.05um之间变化;对位则根据不同的层次有不同的要求,一般而言,在多晶和孔光刻时对位的要求最高,特别是在孔光刻时,由于孔分为有源区和多晶上的孔,对位的要求更高,部分产品多晶上孔的对位偏差甚至要求小于0.14um。
在现在的IC电路制造过程中,一个完整的芯片一般都要经过十几到二十几次的光刻,在这么多次光刻中,除了第一次光刻以外,其余层次的光刻在曝光前都要将该层次的图形与以前层次留下的图形对准。
对位的过程存在于上版和圆片曝光的过程中,其目的是将光刻版上的图形最大精度的覆盖到圆片上已存在的图形上。
它包括了以下几部分:光刻版对位系统、圆片对位系统(又包括LSA、FIA等)。
对于NIKON的步进重复曝光机(Step & Repeat)而言,对位其实也就是定位,它实际上不是用圆片上的图形与掩膜版上的图形直接对准来对位的,而是彼此独立的,即,确定掩膜版的位臵是一个独立的过程,确定圆片的位臵又是另一个独立的过程。
它的对位原理是,在曝光台上有一基准标记,可以把它看作是定位用坐标系的原点,所有其它的位臵都相对该点来确定的。
分别将掩膜版和圆片与该基准标记对准就可确定它们的位臵。
在确定了两者的位臵后,掩膜版上的图形转移到圆片上就是对准的。
光刻版对位系统略。
圆片对位系统圆片对位系统中,根据特定的应用或为解决依赖于圆片工艺(如铝层)而产生的对位错误,发展了各种各样对位系统:LSA、LIA、FIA。
这里先作一个比较:这三种方式的最大差异是处理对位过程中遇到问题的侧重点不同,特别是在铝上,高温溅射的铝在填充对位标记的台阶时,由于铝表面构造粗糙和铝对对位标记的填充不对称等原因,对位的精度往往要比其它层次差很多。
光刻工艺参数

光刻工艺参数一、光刻工艺参数概述光刻工艺是半导体制造中的核心环节,其参数的选择直接影响到最终的制程质量和产品性能。
这些参数共同决定了光刻的分辨率、对比度和曝光剂量等关键因素,从而在微观层面上塑造了集成电路的几何形状和结构。
在光刻工艺中,参数主要包括光源波长、曝光剂量、焦距、数值孔径等。
它们相互关联,共同决定了光刻的质量和效果。
二、光刻工艺参数详解1.光源波长:光源波长是光刻工艺中的关键参数,它决定了光的分辨率。
短波长的光源具有较高的分辨率,但同时也需要相应的设备和材料来支持。
目前,深紫外(DUV)和极紫外(EUV)光源是主流的选择。
2.曝光剂量:曝光剂量决定了曝光过程中光能量的多少,它影响着曝光时间和光强。
曝光剂量要适量,太少会导致曝光不足,太多则可能导致过度曝光。
3.焦距:焦距是指光束通过镜头时,主平面与镜头光轴之间的距离。
在光刻工艺中,焦距的准确性对成像质量有着至关重要的影响。
4.数值孔径:数值孔径(NA)描述了镜头聚光的性能,是镜头与光刻胶之间的透镜效应的量度。
数值孔径越大,光线的汇聚能力越强,成像质量越好。
三、光刻工艺参数优化随着半导体技术的不断发展,对光刻工艺的要求也越来越高。
为了提高制程质量和产品性能,必须对光刻工艺参数进行优化。
优化过程需要综合考虑多个因素,如设备条件、材料特性、环境因素等。
此外,为了实现更精细的制程和更高的产能,科研人员还在不断探索新的光源技术、镜头技术和光刻胶技术等。
四、未来展望随着科技的不断发展,未来的光刻工艺将面临更多的挑战和机遇。
一方面,随着摩尔定律的延续,集成电路的制程将会越来越小,对光刻工艺的要求也会越来越高。
另一方面,随着新材料的出现和应用,光刻工艺也将面临新的变革和突破。
例如,极紫外光刻技术(EUV)被认为是下一代光刻技术的重要方向之一,它具有更高的分辨率和更低的制造成本等优势。
此外,随着人工智能和大数据等技术的应用,光刻工艺的数据分析和智能化管理也将成为未来的重要研究方向。
光刻与刻蚀工艺

张道礼 教授 Email: zhang-daoli@ Voice: 87542894
微电子工艺学
6.1 概述
扩散掺杂 掺 杂 离子注入掺杂 物理气相淀积 微电子单项工艺 薄膜制备 化学气相淀积
外 延
光 图形转移 刻 蚀 刻
6.1 概述
在集成电路制造中,主要的光刻设备是利用紫外光(≈0.2~ 0.4m)的光学仪器。 刻蚀:在光刻胶掩蔽下,根据需要形成微图形的膜层不同,采 用不同的刻蚀物质和方法在膜层上进行选择性刻蚀。 这样,去掉光刻胶以后,三维设计图形就转移到了衬底的相关 膜层上。图形转移工艺是如此重要,以至一种微电子工艺技术的水 平通常以光刻和刻蚀的图形线宽(特征尺寸)表示。
8.2 光刻工艺
光刻胶的性能参数
a. 光学性质:如灵敏度、分辨率、对比度、折射率;
b. 力学和化学性质 :如固溶度、黏滞度、抗蚀性、热稳定性、流 动性和对环境气氛的敏感度;
c. 其它性质:如纯度、金属含量、可使用范围、有效期和燃点;
一、分辨率 分辨率是指每毫米宽度内能够光刻出可分辨的最多线对数,它 是对光刻工艺可以达到的最小图形尺寸的一种描述。在线宽 L 与 线条间距相等的情况下,分辨率为:R 1 (mm 1 ) ,光刻分辨率受 2L 光刻系统、光刻胶和光刻等多方面因素影响。
+
_ 显影后的理想光刻胶剖面
_
8.2 光刻工艺
Imin
Imax
另一个可以从对比度中得到的光刻胶性能指标是调制传输函 I max I min MTF 数(MTF),它可以用来描述曝光图形的质量: I max I min 其中Imax 和Imin 分别为曝光图形上最大和最小辐照强度。 D D 光刻胶临界调制传输函数(CMTF)为:CMTF D100 D0 100 0 CMTF的典型值约为0.4。如果一个实际光刻图形的MTF小 于所用光刻胶的CMTF,则光刻图形上的最小尺寸线条不能被分 辨。反之,则可能被分辨。 101/ 1 对比度与CMTF的关系为: CMTF 101/ 1 对于曝光系统,如果该系统对各种线条的MTF均已知,则 根据光刻胶对比度可计算出该系统能够形成的最小图形尺寸。
光刻工艺 空间成像对比度

光刻工艺空间成像对比度光刻工艺是半导体制造过程中的重要环节,用于在硅片上制作微小的图案。
在光刻过程中,空间成像对比度是一个关键指标,它描述了图案在投影光下的清晰度和对比度。
本文将从光刻工艺的基本原理、光刻机的工作原理以及提高空间成像对比度的方法等方面进行阐述。
光刻工艺是通过光刻胶将图案转移到硅片上的一种制造工艺。
在光刻过程中,光刻胶被涂覆在硅片表面,然后通过光刻机上的光源和掩模,将光照射在光刻胶上。
光照射后,光刻胶会发生化学反应,形成可溶解或不可溶解的区域。
通过洗涤和腐蚀等步骤,将不需要的部分去除,最终形成所需的图案。
空间成像对比度是指在光刻过程中,投影光经过掩模后在光刻胶表面形成的图案的清晰度和对比度。
空间成像对比度的高低直接影响到最终图案的质量和精度。
在光刻机的工作原理中,光源是一个重要的因素。
光源的光强度和波长会直接影响到空间成像对比度。
光刻机通常采用高压汞灯或激光器作为光源。
高压汞灯可以提供较高的光强度,但波长较长,容易产生光的散射和衍射,降低了空间成像对比度。
激光器光源具有较小的波长,可以提供较高的空间成像对比度。
除了光源的选择,还有一些方法可以提高空间成像对比度。
首先,选择合适的光刻胶是关键。
光刻胶的分辨率和对比度是影响空间成像对比度的重要因素。
一般来说,分辨率越高,对比度就越好。
其次,掩模的质量和对光刻胶的光透过率也会影响空间成像对比度。
掩模的制作过程需要精确控制,以确保图案的清晰度和对比度。
此外,光刻机的调试和校准也是提高空间成像对比度的关键步骤。
通过调整光源的光强度、光刻胶的厚度和曝光时间等参数,可以优化空间成像对比度。
空间成像对比度是光刻工艺中的一个重要指标,它直接影响到图案的清晰度和对比度。
在光刻过程中,通过选择合适的光源、优化光刻胶和掩模等方法,可以提高空间成像对比度。
这些措施能够提高图案的质量和精度,满足不断提高的微电子制造需求。
- 1、下载文档前请自行甄别文档内容的完整性,平台不提供额外的编辑、内容补充、找答案等附加服务。
- 2、"仅部分预览"的文档,不可在线预览部分如存在完整性等问题,可反馈申请退款(可完整预览的文档不适用该条件!)。
- 3、如文档侵犯您的权益,请联系客服反馈,我们会尽快为您处理(人工客服工作时间:9:00-18:30)。
9.2.7 显影检验
在显影和烘焙之后就要完成光刻掩膜工艺的 第一次质检,通常叫显影检验。
目的是区分那些有很低可能性通过最终掩膜
检验的衬底,提供工艺性能和工艺控制数据,
以及分出需要重做的衬底。
43
检测内容:
掩膜版选用是否正确;
光刻胶层的质量是否满足要求;
图形质量; 套准精度是否满足要求。
44
光刻胶钻蚀 图形尺寸变化
套刻对准不良
光刻胶膜损伤 线条是否齐、陡
钻蚀
针孔、小岛、划伤
针孔、小岛
45
9.2.8 刻蚀
为了制作集成电路元器件,须将光刻胶上的图形进一
步转移到光刻胶下层的材料上。这个任务由刻蚀完成。
刻蚀就是将涂胶前所淀积的薄膜没有被光刻胶覆盖和
保护的那部分除掉,到达将光刻胶上的图形转移到其
193DUV
VUV EUV
90/65…32nm
CaF2 lenses Reflective mirrors
12
光刻分辨率
光刻分辨率是指光刻工艺得到的光刻胶图形能分辨线条的最小 线宽 L ,也可以用单位尺寸的线条数表示。光刻分辨率是决定
芯片最小特征尺寸的最主要因素。
L L
分辨率
R=1/2L (mm-1); 直接用线宽L表示
曝光中要特别注意曝光光源的选择和对准。
29
简单的光学系统曝光图
30
曝光光源的选择:紫外光用于光刻胶的曝光是因为光 刻胶与这个特定波长的光反应。波长很重要,因为较 短波长的可以获得光刻胶上较小尺寸的分辨率。
对准:是指光刻掩膜版与光刻机之间的对准,二者均 刻有对准标记,使标记对准即可达到光刻掩膜版与光 刻机的对准。
9.3.3
针孔
•在氧化层上,除了需要刻蚀的窗口外,在其它区域也
可能产生大小一般在 1~3 微米的细小孔洞。这些孔洞,
由于光刻应用的特征尺寸非常小,且各层都须精确 匹配,所以需要配合紧密。图形套准精度是衡量被 刻印的图形能否匹配前面刻印图形的一种尺度。
18
9.2 基本光刻工艺流程
一般的光刻工艺要经历底膜处理、涂胶、前烘、曝 光、显影、坚膜、刻蚀、去胶、检验工序。
19
20
9.2.1 底膜处理
底膜处理是光刻工艺的第一步,其主要目的 是对硅衬底表面进行处理,以增强衬底与光 刻胶之间的黏附性。
6
第9章 光刻工艺
9.1 概述
9.2 基本光刻工艺流程 9.3 光刻技术中的常见问题
7
9.1 概述
光刻 (photolithography)就是将掩模版(光刻版)
上的几何图形转移到覆盖在半导体衬底表面的
对光辐照敏感薄膜材料(光刻胶)上去的工艺
过程 。
光刻是微电子工艺中最重要的单项工艺之一。
三、图形外没有残留的被腐蚀物质。
同时要求图形套刻准确,无污染等。
但在光刻过程中,常出现浮胶、毛刺、钻蚀、针孔
和小岛等缺陷。
50
9.3.1 浮胶
浮胶就是在显影和腐蚀过程中,由于化学试剂不断
侵入光刻胶膜与SiO2或其它薄膜间的界面,所引起的
光刻胶图形胶膜皱起或剥落的现象。
51
显影时产生浮胶的原因有:
9.1.1
分辨率 R
分辨率是指一个光学系统精确区分目标的能力。 微图形加工的最小分辨率是指光刻系统所能分辨和加 工的最小线条尺寸或机器能充分打印出的区域。
分辨率是决定光刻系统最重要的指标,能分辨的线宽 越小,分辨率越高。其由瑞利定律决定:
R k1 NA
分辨率系数k1=0.6~0.8
下层材料上的目的。
SiO2、Al、poly-Si等薄膜
光刻和刻蚀是两个不同的加工工艺,,,光刻。 46
9.2.9 去胶
光刻胶除了在光刻过程中作为从光刻掩膜版到衬底 的图形转移媒介外,还可以作为刻蚀时不需刻蚀区 的保护膜。
当刻蚀完成后,光刻胶已经不再有用,需要将其去 除,就是去胶。此外刻蚀过程中残留的各种试剂也 要清除。
套准:对准的结果,或者每个连续图形与先前层匹配 的精度,称为套准。
31
对准曝光
曝光,曝光剂量等于光强与曝光时间的乘积。 曝光过度会导致图形侧墙倾斜;
入射光波长越短,可实现的特征尺寸越小,
图形分辨率越高,但能量越小;
首次曝光需要对准晶向,多次曝光之间需要
进行图形对准。
32
33
光的反射、干涉、衍射与驻波
提高分辨率: NA,,k1
11
数值孔径NA=0.16~0.8
使用光源缩小
光源 波长(nm) 术语 技术节点
光源
汞灯
汞灯 KrF(激光)
436
365 248
g线
i线 DUV
>0.5mm
0.5/0.35mm 0.25/0.13mm
ArF (激光)
F2 (激光) 等离子体
193
157 13.5
底膜处理包括以下过程: 1、清洗;2、烘干;3、增粘处理(涂底)。
21
9.2.2
涂胶
在硅片表面涂敷的光刻胶应厚度均匀、附着
性强、没有缺陷。
在涂胶之前,硅片一般需要经过脱水烘焙, 或涂敷能增加光刻胶与硅片表面附着能力的 化合物。六甲基乙硅氮烷 (HMDS)
22
涂胶工艺示意图
3000~6000 rpm,0.5~1 mm
①胶膜与基片表面粘附不牢。 ②胶的光化学反应性能不好,胶膜过厚,或者收缩膨胀 不均。 ③烘焙时间不足或过度。 ④曝光不足。 ⑤显影时间过长,使胶膜软化。
腐蚀时产生浮胶的原因:
①坚膜时胶膜没有烘透,膜不坚固。 ②腐蚀液配方不当。例如,腐蚀SiO2的氟化氢缓冲腐蚀
液中,氟化铵太少,化学活泼性太强。
③腐蚀温度太低或太高。
须适当控制温度。
41
坚膜
坚膜后还需要光学稳定。通过光学稳定,使光刻胶在 干法刻蚀过程中的抗蚀得到增强,而且还可以减少离
子注入过程中从光刻胶中逸出的气体,防止在光刻层
中形成气泡。
光学稳定是通过紫外光辐照和加热来完成的。 光学稳定可以使光刻胶产生均匀的交叉链接,提高光 刻胶的抗刻蚀能力,进而提高刻蚀工艺的选择性。
显影完成之后,需要经过漂洗,之后再旋干。
39
9.2.6 坚膜
坚膜也叫后烘,是为了去除由于显影液的浸泡引起的 胶膜软化、溶胀现象,能使胶膜附着能力增强,抗腐
蚀能力提高。
坚膜温度要高于前烘和曝光后烘烤温度,较高的坚膜
温度可使坚膜后光刻胶中的溶剂含量更少,但增加了
去胶时的困难。且光刻胶内部拉伸应力的增加会使光 刻胶的附着性下降,因此必须适当的控制坚膜温度 。
53
9.3.2 毛刺和钻蚀
产生毛刺和钻蚀的原因有:
①基片表面存在污物,油垢,小颗粒或吸附水汽, 使光刻胶与氧化层粘附不良。 ②氧化层表面存在磷硅玻璃,与光刻胶粘附不好, 耐腐蚀性能差,引起钻蚀。 ③光刻胶中存在颗粒状物质,造成局部粘附不良。 ④对于光硬化型光刻胶,曝光不足,显影时产生 溶钻,腐蚀时造成毛刺或钻蚀。 ⑤显影时间过长,图形边缘发生溶钻,腐蚀时造 成钻蚀。 ⑥掩模图形的黑区边缘有毛刺状缺陷。 54
用光刻图形来确定分立元器件和集成电路中的
各个区域、如注入区、接触窗口和压焊区等。
8
用光刻工艺确定的光刻胶图并不是最后器件的
构成部分,仅是图形的印模,为了制备出实际
器件的结构图形,还必须再一次把光刻胶图形
转移到光刻胶下面组成器件的材料层上。也就
是使用能够对非掩膜部分进行选择性去除的刻
蚀工艺来实现图形的转移。
47
去胶分为:湿法去胶和干法去胶; 湿法去胶中又有有机溶液和无机溶液去胶; 湿法去胶:用溶剂、用浓硫酸 98%H2SO4+H2O2+胶 →CO+CO2+H2O
干法去胶:氧气加热去胶 O2+胶 → CO+CO2+H2O 等离子去胶
48
9.2.10 最终检验
在基本的光刻工艺过程中,最终步骤是检验。
衬底在入射白光或紫外光下首先接受表面目检,
以检查污点和大的微粒污染。之后是显微镜检
验或自动检验来检验缺陷和图案变形。
显微镜目检、线宽控制、对准检查。
49
9.3 光刻技术中的常见问题
半导体器件和集成电路的制造对光刻质量有如下要求:
一、刻蚀的图形完整,尺寸准确,边缘整齐陡直; 二、图形内没有针孔;
玷污灰尘,通过在较高温度下进行烘焙,可
以使溶剂从光刻胶内挥发出来。
前烘方法:热平板传导;红外线辐射;干燥 循环热风。 10~30 min,80~110 C
26
27
28
9.2.4 曝光
曝光是使光刻掩模版与涂上光刻胶的衬底对 准,用光源经过光刻掩模版照射衬底,使接
受到光照的光刻胶的光学特性发生变化。
高分辨率; 高灵敏度的光刻胶; 低缺陷; 精密的套刻精度:误差≤± 10%L; 可对大尺寸硅片进行光刻加工;
5
第9章 光刻工艺
光刻(photolithography)就是将掩膜版(光刻版)上的几何图 形转移到覆盖在半导体衬底表面的对光辐照敏感的薄膜材料 (光刻胶)上去的工艺工程。
23
23
涂胶厚度主要由光刻胶粘度和转速决定
24
涂胶步骤:
将光刻胶溶液喷射到硅片表面上;