铬镍合金配料计算(Cr50Ni50)
镍当量的计算
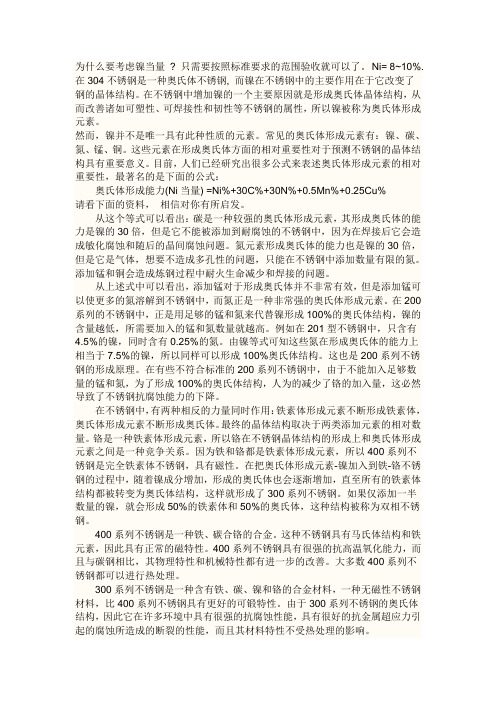
为什么要考虑镍当量? 只需要按照标准要求的范围验收就可以了。
Ni= 8~10%. 在304不锈钢是一种奥氏体不锈钢, 而镍在不锈钢中的主要作用在于它改变了钢的晶体结构。
在不锈钢中增加镍的一个主要原因就是形成奥氏体晶体结构,从而改善诸如可塑性、可焊接性和韧性等不锈钢的属性,所以镍被称为奥氏体形成元素。
然而,镍并不是唯一具有此种性质的元素。
常见的奥氏体形成元素有:镍、碳、氮、锰、铜。
这些元素在形成奥氏体方面的相对重要性对于预测不锈钢的晶体结构具有重要意义。
目前,人们已经研究出很多公式来表述奥氏体形成元素的相对重要性,最著名的是下面的公式:奥氏体形成能力(Ni当量) =Ni%+30C%+30N%+0.5Mn%+0.25Cu%请看下面的资料,相信对你有所启发。
从这个等式可以看出:碳是一种较强的奥氏体形成元素,其形成奥氏体的能力是镍的30倍,但是它不能被添加到耐腐蚀的不锈钢中,因为在焊接后它会造成敏化腐蚀和随后的晶间腐蚀问题。
氮元素形成奥氏体的能力也是镍的30倍,但是它是气体,想要不造成多孔性的问题,只能在不锈钢中添加数量有限的氮。
添加锰和铜会造成炼钢过程中耐火生命减少和焊接的问题。
从上述式中可以看出,添加锰对于形成奥氏体并不非常有效,但是添加锰可以使更多的氮溶解到不锈钢中,而氮正是一种非常强的奥氏体形成元素。
在200系列的不锈钢中,正是用足够的锰和氮来代替镍形成100%的奥氏体结构,镍的含量越低,所需要加入的锰和氮数量就越高。
例如在201型不锈钢中,只含有4.5%的镍,同时含有0.25%的氮。
由镍等式可知这些氮在形成奥氏体的能力上相当于7.5%的镍,所以同样可以形成100%奥氏体结构。
这也是200系列不锈钢的形成原理。
在有些不符合标准的200系列不锈钢中,由于不能加入足够数量的锰和氮,为了形成100%的奥氏体结构,人为的减少了铬的加入量,这必然导致了不锈钢抗腐蚀能力的下降。
在不锈钢中,有两种相反的力量同时作用:铁素体形成元素不断形成铁素体,奥氏体形成元素不断形成奥氏体。
合金元素的pin值
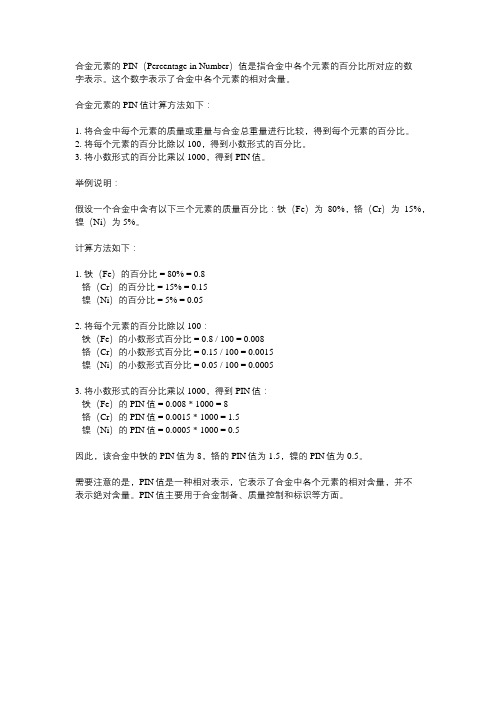
合金元素的PIN(Percentage in Number)值是指合金中各个元素的百分比所对应的数
字表示。
这个数字表示了合金中各个元素的相对含量。
合金元素的PIN值计算方法如下:
1. 将合金中每个元素的质量或重量与合金总重量进行比较,得到每个元素的百分比。
2. 将每个元素的百分比除以100,得到小数形式的百分比。
3. 将小数形式的百分比乘以1000,得到PIN值。
举例说明:
假设一个合金中含有以下三个元素的质量百分比:铁(Fe)为80%,铬(Cr)为15%,镍(Ni)为5%。
计算方法如下:
1. 铁(Fe)的百分比 = 80% = 0.8
铬(Cr)的百分比 = 15% = 0.15
镍(Ni)的百分比 = 5% = 0.05
2. 将每个元素的百分比除以100:
铁(Fe)的小数形式百分比 = 0.8 / 100 = 0.008
铬(Cr)的小数形式百分比 = 0.15 / 100 = 0.0015
镍(Ni)的小数形式百分比 = 0.05 / 100 = 0.0005
3. 将小数形式的百分比乘以1000,得到PIN值:
铁(Fe)的PIN值 = 0.008 * 1000 = 8
铬(Cr)的PIN值 = 0.0015 * 1000 = 1.5
镍(Ni)的PIN值 = 0.0005 * 1000 = 0.5
因此,该合金中铁的PIN值为8,铬的PIN值为1.5,镍的PIN值为0.5。
需要注意的是,PIN值是一种相对表示,它表示了合金中各个元素的相对含量,并不
表示绝对含量。
PIN值主要用于合金制备、质量控制和标识等方面。
合金配料计算程序操作说明书

配料程序帮助文档引言合金配料有很多的计算方法(人工凭经验计算、用计算器、用Excel设置函数表,用配料程序计算)。
手工计算是最原始的方法,可惜很多企业都在用,这要完全靠掌炉工的经验估计,而且只能粗略估算,碰到元素多、材料种类多的时候力不从心,计算速度也不快并容易出错,至于还要考虑结果最优最节省成本那只能是完全靠经验了,有经验的老师傅知道合理搭配废料,而新手估计都是越纯的料越好用,因为计算也简单,投炉熔解也简单(再生铝行业有句话叫只要舍得A00铝锭加入,没有调整不好的成份!)但是拿纯铝做杂铝牌号明显是降级处理了,会大幅提高原材料成本。
Excel函数表有了很大的改进,计算结果精确,有很多精通Excel的配料员都能设计出这种函数表,相比上面的手工计算方便并准确了很多,可惜很多习惯了手工计算的老师傅估计还用不惯Excel;Excel函数表的原理基本类似:设定好牌号的标准范围、原材料的成份+回收率,生产的时候配料员大概估计每种材料需要加入的量,然后慢慢调节到牌号的要求标准,这里还是要依赖配料员的经验,每种材料用多少、用哪些材料都是人怎么想就怎么录入,至于是否最节省成本谁也不知道(有经验的知道搭配利用废料,而新手还是喜欢用纯料)。
配料程序计算能弥补上面几种方法的缺点,目前市面有很多款配料计算的程序,本人不是第一个做这方面研究的,之前就有某名牌大学设计出一款配料计算软件,虽然不清楚某些配料程序里面的计算方法,我测试过几款国内的配料程序,据说是用遗传算法,并且承诺计算出来的结果成本最低,但测试计算之后并不是成本最低(也许跟手工计算的比较是更节省,但是我把相同的数据用本套程序计算做比较发现还有更优化的结果),而对方也只是含糊回答(说是还考虑了其它因素等等),有一款国外引进的配料软件(该公司不止做配料程序,还有其它很多铸造行业的软件),当然这款软件里面还有很多其它的功能,算是一款优秀的程序了(相比国内某些小的配料程序),但也存在同样的问题(计算结果不是最节省成本的,后续给大家演示他们公布的数据及计算结果跟本套程序计算的结果做比较),上述说明不是为了贬低别人而抬高自己,而本人去试用别人的程序跟自己的比较也只是为了完善并优化自己的系统,相信用户的眼睛是雪亮的,也欢迎其它配料程序来跟本套系统做比较,毕竟人类都是互相学习才能进步。
1配料计算

1.炉料成分的配定原则配料过程中,炉料化学成分的配定主要考虑钢种规格成分、冶炼方法、元素特性及工艺的具体要求等。
具体为:(1)碳的配定。
炉料中碳的配定主要考虑钢种规格成分、熔化期碳的烧损及氧化期的脱碳量,还应考虑还原期补加合金和造渣制度对钢液的增碳。
熔化期碳元素的烧损与助熔方式有关,可根据实际生产的具体条件,总结固有规律,一般波动在0.60%左右。
氧化期的脱碳量应根据工艺的具体要求而定,对于新炉时的第一炉,脱碳量应大于0.40%。
不氧化法碳的配定应保证全熔碳位于钢种规格要求的下限附近。
(2)硅的配定。
在一般情况下,氧化法冶炼钢铁料的硅主要是由生铁和废钢带入,全熔后的硅不应大于0.30%,以免延缓熔池的沸腾时间。
返吹法冶炼为了提高合金元素的收得率,根据工艺要求可配入硅废钢或硅铁,但也不宜超过1.0%以上,对于特殊情况也可不配。
(3)锰的配定。
用氧化法冶炼的钢种,如锰的规格含量较高,配料时一般不予以考虑;如锰的规格含量较低,配料时应严格控制,尽量避免炼钢工进行脱锰操作。
对于一些用途重要的钢种,为了使钢中的非金属夹杂物能够充分上浮,熔清后钢液中的锰含量不应低于0.20%,但也不宜过高,以免影响熔池的沸腾及脱磷。
由于不氧化法或返吹法冶炼脱锰操作困难,因此配锰量不得超过钢种规格的中限。
高速钢中锰影响钢的晶粒度,配入量应越低越好。
(4)铬的配定。
用氧化法冶炼的钢种,钢中的铬含量应尽可能的低。
冶炼高铬钢时,配铬量不氧化法按出钢量的中下限控制,返吹法则低于下限。
(5)镍、钼元素的配定。
钢中镍、钼含量较高时,镍、钼含量按钢种规格的中下限配入,并同炉料一起装炉。
冶炼无镍钢时,钢铁料中的镍含量应低于该钢种规定的残余成分。
高速钢中的镍对硬度有害无利,因此要求残余含量越低越好。
(6)钨的配定。
钨是弱还原剂,在钢的冶炼过程中,因用氧方式的不同而有不同的损失。
矿石法冶炼,任何钢种均不人为配钨,且要求残余钨越低越好。
不氧化法和返吹法冶炼时,应按钢种规格含量的中下限配入,并同炉料一起装炉。
合金吸收率及配料技术公式

合金元素的吸收率及配料技术公式1、 中频感应炉熔炼时,加入铁合金中的合金元素收得率是多少?在整个熔炼过程中碳、硅、锰等元素的变化规律是什么?熔炼低合金钢、单元高合金钢、多元高合金钢时,在配料时怎样计算特合金的加入量? 1)中频感应炉熔炼时合金元素的收得率,见表1表1 合金元素的收得率2)中频炉熔炼中,碳、硅、锰等元素的变化规律:①C 在熔炼全过程要烧损,炉料较好时碳烧损0.03%-0.06%。
废钢等熔清,经预脱氧后取炉前钢样到出钢碳烧损约0.02%(碳钢,低合金钢);②废钢熔清后的残硅:碱性炉约0.1%,中性炉约0.15%,酸性炉约0.25%;③废钢熔清后的残Mn :碱性炉、中性炉约0.2%~0.25%,酸性炉约0.1%~0.15%;④铁合金中的碳100%回收,硫、磷100%回收;⑤铁合金中的硅(稀土硅铁合金)100%回收;⑥酸性炉出钢前出现硅还原现象,钢液中增硅0.05%。
3)熔炼低合金钢时,铁合金加入量按下式计算:序号 合金名称 作用及加入时间 合金元素收得率 碱性炉 中性炉 酸性炉 1 FeSi 合金化,出钢前5~8min 85 90 100 2 FeMn 合金化,出钢前5~8min 90~95 85 75~80 3 FeCr 合金化,出钢前5~8min 95 95 95 4 FeNo 熔毕,或出钢前15~30min 98 95 95 5 FeW 熔毕,或出钢前15~30min 98 95 95 6 FeTi 铝终脱氧后加入,或冲包50~70 50~70 50~70 7 FeV 合金化,出钢前5~-8min (质量分数小于0.3%) 80~9080~90 80~90 合金化,出钢前5~8min (质量分数大于1.0%)95 90 90 8 FeNb 合金化,出钢前5~8min90 90 85 9 FeB 冲包40~60 40~60 40~60 10 金属镍 合金化,出钢前15~30min 98 98 95 11 金属铜 合金化,出钢前15~30min 98 98 95 12 石墨电极粉 增碳,出钢前5~8min 90 90 90 13焦炭粉增碳出钢前5~8min808080铁合金加入量 =4)熔炼单元高合金钢时,铁合金加入量按下式计算:铁合金加入量 =5)熔炼多元高合金钢时,各元素加入量都很大,一种铁合金加入,钢液量随之增大,影响其他元素在钢中的含量,故采用“补加系数”法计算(补加系数是指每加入100kg 合金料需补加的量),程序如下:① 各项合金占有量 =② 纯钢液占有量=100%-各项合金占有量之和 ③ 补加系数 =④ 钢液综合收得率=95%~97%。
高碳铬铁配料计算方法(精编文档).doc

【最新整理,下载后即可编辑】高碳铬铁配料计算方法一、基本知识1、元素、分子式、分子量铬Cr —52 铁Fe —56 氧O —16 碳C —12硅Si —28 三氧化二铬Cr 2O 3—152 二氧化硅SiO 2—60氧化镁MgO 三氧化二铝Al 2O 32、基本反应与反应系数Cr 2O 3+3C=2Cr+3CO1公斤Cr 2O 3还原成Cr =)0.6842公斤 Cr 2O 3的还系数是还原1公斤Cr 用 =)0.3462公斤 FeO+C=Fe+CO还原1公斤Fe 用C =)0.2143公斤SiO 2+2C=Si+2CO还原1公斤Si 用C =)0.8571公斤3、Cr/Fe 与M/A(1)Cr/Fe 是矿石中的铬和铁的重量比,Cr/Fe 越高合金中Cr 含量越高。
(2)M/A 是矿石中的MgO 和Al 2O 3的重量比,M/A 表示矿石的难易熔化的程度,一般入炉矿石M/A 为1.2以上较好。
二、计算条件1、焦炭利用率90%2、铬矿中Cr 还原率95%3、铬矿中Fe 还原率98%4、合金中C9%,Si0.5%三、原料成份举例说明:铬矿含水4.5%焦炭固定碳83.7%,灰份14.8%,挥发分1.5%,含水8.2%主要成分表按100公斤干铬矿(104.5公斤铬矿)计算(1)合金重量和成份100公斤干铬矿中含Cr ,100×0.2826=28.26公斤进入合金的Cr 为28.26×0.95=26.85公斤进入合金中的Fe 为100×0.1013×0.98=9.93公斤合金中铬和铁占总重量的百分比是(100-9-0.5)%=90.5%合金重量为(26.85-9.93)÷0.905=40.64公斤合金成分为:还原26.85公斤Cr 用C :26.85 =)0.3462=9.30公斤还原9.93公斤Fe 用C :9.93 =)0.2143=2.13公斤还原0.2公斤Si 用C :0.2 =)0.8571=0.17公斤60合金增C : 3.66公斤 总用C 量是:9.30+2.13+0.17+3.66=15.26公斤入炉C :15.26÷0.9=16.96公斤入炉干焦炭:16.96÷0.837=20.26公斤入炉焦炭:20.26÷(1-0.082)=22.07公斤(3)硅石配入量计算加硅石前的炉渣成分SiO 2:来自矿石:100×0.1145=11.45公斤来自焦炭20.26×0.148×0.458=1.37公斤进入合金:0.2 =0.43公斤SiO 2含量是公斤Al 2O 3:来自矿石:100×0.1218=12.18公斤来自焦炭:20.26×0.148×0.309=0.93公斤Al 2O 3含量是12.18+0.93=13.11公斤MgO :来自矿石:100×0.1932=19.32公斤来自焦炭:20.26×0.148×0.0172=0.05公斤MgO 含量是19.32+0.05=19.37公斤这样,Al 2O 3与MgO 含量的和是13.11+19.37=32.48公斤A-M 二元系中Al 2O 3 =40%MgO =60%在A-M-S 的点自顶点作连线交1700℃温度线,再作平行线与右边相交于SiO 2=34%的点。
铸钢配料计算表

化学成份(%)
C
Si
Mn Cr Ni Mo Cu Ti W
0.1 0.5 6.5 14 4.5
0.8
0.1 0.5
1 17 0.5
0.2 0.3
1
0.05
1.5 17.5 7.5
0 90 0.1105 97 0.107185 0.2 4
0.3
0
0 0 0 0 000Fra bibliotek0 0.615 7.175 3.08 0 0 0 0
0.370055 0.09 2.4973 28.48 19.9 0 0 0 0
0.369685 0.0899 2.4948 28.46 19.9 0 0 0 0
使用方法: 1.在炉料行输入 各种炉料的化学 成份。 2.收得率行输入 各种元素收得率 。如果不清楚, 就用现生产的品 种核算一下。 3.在加入量(%) 输入列中输入各 种炉料加入量。
90 95.5 97.5 100 100 100
0 0.5873 6.996 3.08 0 0 0 0
80 0.4
2.5
50
50
58
99
58
0.271 97
0.1
2 22.04 16.8 0 0 0 0
90 95.5 97.5 100 100 100
0.26287 0.09 1.91 21.49 16.8 0 0 0 0
0.00
0.04
0.04
0.00
41
40.96
0.00
00
0
0
0
0.00
0.04
0.02
0.1
0.10
0 0 0 0 0.00004
0.00002
镍铬合金熔点
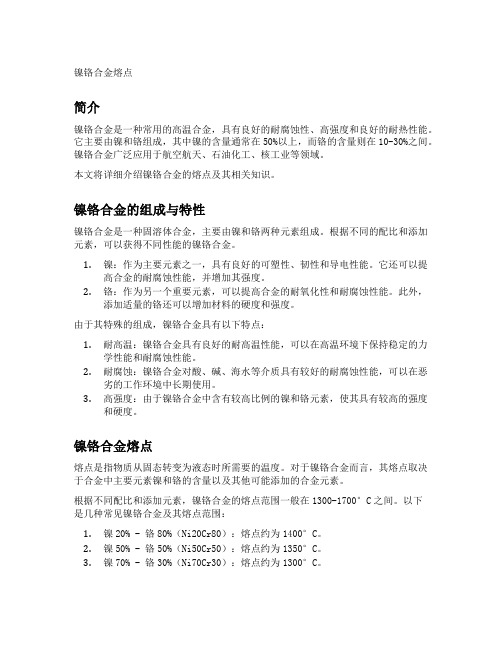
镍铬合金熔点简介镍铬合金是一种常用的高温合金,具有良好的耐腐蚀性、高强度和良好的耐热性能。
它主要由镍和铬组成,其中镍的含量通常在50%以上,而铬的含量则在10-30%之间。
镍铬合金广泛应用于航空航天、石油化工、核工业等领域。
本文将详细介绍镍铬合金的熔点及其相关知识。
镍铬合金的组成与特性镍铬合金是一种固溶体合金,主要由镍和铬两种元素组成。
根据不同的配比和添加元素,可以获得不同性能的镍铬合金。
1.镍:作为主要元素之一,具有良好的可塑性、韧性和导电性能。
它还可以提高合金的耐腐蚀性能,并增加其强度。
2.铬:作为另一个重要元素,可以提高合金的耐氧化性和耐腐蚀性能。
此外,添加适量的铬还可以增加材料的硬度和强度。
由于其特殊的组成,镍铬合金具有以下特点:1.耐高温:镍铬合金具有良好的耐高温性能,可以在高温环境下保持稳定的力学性能和耐腐蚀性能。
2.耐腐蚀:镍铬合金对酸、碱、海水等介质具有较好的耐腐蚀性能,可以在恶劣的工作环境中长期使用。
3.高强度:由于镍铬合金中含有较高比例的镍和铬元素,使其具有较高的强度和硬度。
镍铬合金熔点熔点是指物质从固态转变为液态时所需要的温度。
对于镍铬合金而言,其熔点取决于合金中主要元素镍和铬的含量以及其他可能添加的合金元素。
根据不同配比和添加元素,镍铬合金的熔点范围一般在1300-1700°C之间。
以下是几种常见镍铬合金及其熔点范围:1.镍20% - 铬80%(Ni20Cr80):熔点约为1400°C。
2.镍50% - 铬50%(Ni50Cr50):熔点约为1350°C。
3.镍70% - 铬30%(Ni70Cr30):熔点约为1300°C。
需要注意的是,以上数值仅为近似值,实际的熔点可能会受到合金中其他元素的影响。
影响镍铬合金熔点的因素镍铬合金的熔点受到多种因素的影响,以下是一些常见因素:1.元素含量:镍和铬元素的含量对合金的熔点有直接影响。
一般来说,镍含量越高,熔点越高;而铬含量越高,熔点也会相应提高。
合金配料计算

合金加入量的计算钢水量校核及碳钢、低合金钢的合金加入量计算A 钢水量校核实际生产中,由于计量不准,炉料质量波动大或操作的因素(如吹氧铁损、大沸腾跑钢、加铁矿等),会出现钢液的实际重量与计划重量不符,给化学成分的控制及钢的浇铸造成困难。
因此,校核钢液的实际重量是正确计算合金加入量的基础。
首先找一个在合金钢中收得率比较稳定的元素,根据其分析增量和计算增量来校对钢液量。
计算公式为:PΔM=PoΔMo 或P=Po (9-3)式中:P为钢液的实际重量,Kg;Po为原计划的钢液质量,Kg;ΔM为取样分析校核的元素增量,%;ΔMo为按Po计算校核的元素增量,%。
公式中用镍和钼作为校核元素最为准确,对于不含镍和钼的钢液,也可以用锰元素来校核还原期钢水重量,因为锰受冶炼温度及钢中氧、硫含量的影响较大,所以在氧化过程中或还原初期用锰校核的准确性较差。
氧化期钢液的重量校核主要凭经验。
例如:原计划钢液质量为30t,加钼前钼的含量为0.12%,加钼后计算钼的含量为0.26%,实际分析为0.25%。
求钢液的实际质量?解:P=30000×(0.26-0.12)%/(0.25-0.12)%=32307(Kg)由本例可以看出,钢中钼的含量仅差0.10%,钢液的实际质量就与原计划质量相差2300Kg。
然而化学分析往往出现±(0.01%~0.03%)的偏差,这对准确校核钢液质量带来困难。
因此,式9-3只适用于理论上的计算。
而实际生产中钢液质量的校核一般采用下式计算:P=GC/ΔM (9-4)式中:P为钢液的实际重量,Kg;G为校核元素铁合金补加量,Kg;C为校核元素铁合金成分,%;ΔM为取样分析校核元素的增量,%。
例如:往炉中加入钼铁15Kg,钢液中的钼含量由0.2%增到0.25%。
已知钼铁中钼的成分为60%。
求炉中钢液的实际质量?解:P=(15×60%)/(0.25-0.20)%=18000(Kg)例如:冶炼20CrNiA钢,因电子称临时出故障,装入的钢铁料没有称量,由装料工估算装料。
电炉炼钢的配料计算,装料方法及操作
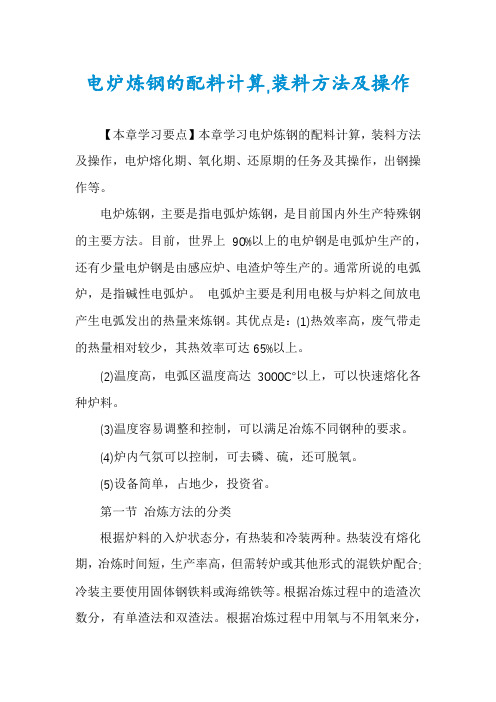
电炉炼钢的配料计算,装料方法及操作【本章学习要点】本章学习电炉炼钢的配料计算,装料方法及操作,电炉熔化期、氧化期、还原期的任务及其操作,出钢操作等。
电炉炼钢,主要是指电弧炉炼钢,是目前国内外生产特殊钢的主要方法。
目前,世界上90%以上的电炉钢是电弧炉生产的,还有少量电炉钢是由感应炉、电渣炉等生产的。
通常所说的电弧炉,是指碱性电弧炉。
电弧炉主要是利用电极与炉料之间放电产生电弧发出的热量来炼钢。
其优点是:(1)热效率高,废气带走的热量相对较少,其热效率可达65%以上。
(2)温度高,电弧区温度高达3000℃以上,可以快速熔化各种炉料。
(3)温度容易调整和控制,可以满足冶炼不同钢种的要求。
(4)炉内气氛可以控制,可去磷、硫,还可脱氧。
(5)设备简单,占地少,投资省。
第一节冶炼方法的分类根据炉料的入炉状态分,有热装和冷装两种。
热装没有熔化期,冶炼时间短,生产率高,但需转炉或其他形式的混铁炉配合;冷装主要使用固体钢铁料或海绵铁等。
根据冶炼过程中的造渣次数分,有单渣法和双渣法。
根据冶炼过程中用氧与不用氧来分,有氧化法和不氧化法。
氧化法多采用双渣冶炼,但也有采用单渣冶炼的,如电炉钢的快速冶炼,而不氧化法均采用单渣冶炼。
此外,还有返回吹氧法。
根据氧化期供氧方式的不同,有矿石氧化法、氧气氧化法和矿、氧综合氧化法及氩氧混吹法。
冶炼方法的确定主要取决于炉料的组成以及对成品钢的质量要求,下面我们扼要介绍几种冶炼方法:(1)氧化法。
氧化法冶炼的特点是有氧化期,在冶炼过程中采用氧化剂用来氧化钢液中的Si、Mn、P等超规格的元素及其他杂质。
因此,该法虽是采用粗料却能冶炼出高级优质钢,所以应用极为广泛。
缺点是冶炼时间长,易氧化元素烧损大。
(2)不氧化法。
不氧化法冶炼的特点是没有氧化期,一般全用精料,如本钢种或类似本钢种返回废钢以及软钢等,要求磷及其他杂质含量越低越好,配入的合金元素含量应进入或接近于成品钢规格的中限或下限。
不氧化法冶炼可回收大量贵重合金元素和缩短冶炼时间。
高铬配料计算
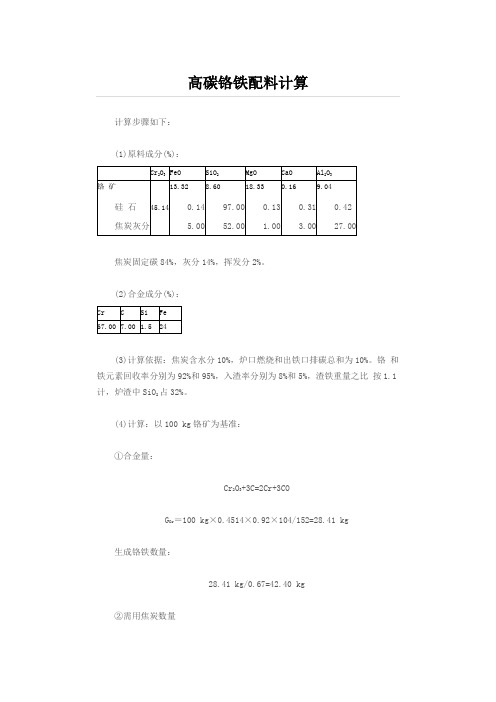
高碳铬铁配料计算计算步骤如下:(1)原料成分(%):焦炭固定碳84%,灰分14%,挥发分2%。
(2)合金成分(%):(3)计算依据:焦炭含水分10%,炉口燃烧和出铁口排碳总和为10%。
铬和铁元素回收率分别为92%和95%,入渣率分别为8%和5%,渣铁重量之比按1.1计,炉渣中SiO2占32%。
(4)计算:以100 kg铬矿为基准:①合金量:Cr2O3+3C=2Cr+3COG Cr=100 kg×0.4514×0.92×104/152=28.41 kg生成铬铁数量:28.41 kg/0.67=42.40 kg②需用焦炭数量还原Cr2O3用碳量:Cr2O3+3C=2Cr+3COG C=100 kg×0.4514×0.92×36/152=9.84 kg 还原FeO用碳量:FeO+C=Fe+COG C=100 kg×0.1332×0.95×12/72=2.109 kg 还原SiO2用碳量:SiO2+2C=Si+2COG C=42.40 kg×0.015×24/28=0.545 kg合金增碳:G C=42.40 kg×0.07=2.97 kg碳总消耗量:G C=(9.84+2.109+0.545+2.97)kg=15.464 kg 折合成原料中焦炭数量:G(焦炭)=15.464 kg/(0.84×0.9×0.9)=22.728 kg ③硅石用量:还原反应消耗:G SiO2=42.40 kg×0.15×60/28=1.36 kg进入炉渣中SiO2数量:G SiO2=42.40 kg×1.1×0.32=14.92 kg焦炭带入SiO2:G SiO2=22.728 kg×0.14×0.52×0.9×0.9=1.34 kg 矿石带入SiO2:G SiO2=100 kg×0.084=8.4 kg应补加SiO2的数量:G SiO2=(1.36+14.92-1.34-8.4) kg=6.54 kg折合成硅石量:G硅石=6.54 kg/0.97=6.74 kg炉料组成:铬矿 100 kg,硅石 6.74 kg,焦炭 22.728 kg。
焊材消耗量计算方法

焊材消耗量计算方法
一、计算公式
W(g)A(cm2) ρ(g/cm3)L(cm) η 1.2
焊接材料所要量截面积密度焊道长熔敷效率余高以20%焊
道计
密度ρ焊接方法1/ηη
碳钢7.8 焊条电弧焊 1.82 55% Cr-Ni不锈钢7.9 氩弧焊 1.10 90% Cr-Ni-Mo不锈钢8.0 CO2药芯 1.15 89% 铜、镍8.9 埋弧自动焊、
CO2实芯
1.05 95%
二、焊剂计算
1、埋弧自动焊焊剂=1.2W
2、带极堆焊焊剂一种焊剂=0.9W
二种焊剂=1.0W
3、机加工复层焊条=4过度层焊材
三、每Kg焊材根数
1、焊条碳钢:Ф3.2 30~31根/Kg 不锈钢31根/Kg
Ф4.0 18根/Kg 不锈钢19根/Kg
Ф5.0 12根/Kg
2、氩弧焊丝:每盒:5 Kg Ф2.4:28根/Kg Ф2.5:26根/Kg
Ф2.0:26根/Kg Ф1.2堆焊每盘:20Kg
3、气保焊焊丝:药芯Ф1.2堆焊每盘:12.5Kg
实芯Ф1.2堆焊每盘:20Kg
4、埋弧焊焊丝每盘:20 Kg
5、带极堆焊:哈焊所每盘:35~40 Kg
大钢每盘:35~40 Kg
进口每盘:35~40 Kg。
合金配料计算公式

合金配料计算公式
合金配料计算公式是根据合金中每种元素的重量百分比来计算的。
以下是计算公式和解释:
1. 求出各元素的原子量。
原子量是元素原子的相对质量。
例如,纯铁的原子量为55.845 g/mol,纯铬的原子量为51.996 g/mol。
2. 计算合金中每种元素的摩尔质量。
摩尔质量是元素一摩尔的质量。
例如,一摩尔的铁的质量为55.845 g,一摩尔的铬的质量为51.996 g。
3. 计算合金中每种元素的摩尔分数。
摩尔分数是每种元素的摩尔质量与合金中所有元素摩尔质量之和的比值。
例如,合金中铁的摩尔分数为铁的摩尔质量除以所有元素的摩尔质量之和。
4. 计算每种元素的重量百分比。
重量百分比是每种元素的质量与合金总质量之比,乘以100%。
例如,如果合金中铁的重量为100 g,总质量为500 g,则铁的重量百分比为(100 g / 500 g) x 100% = 20%。
综上所述,合金配料计算公式可以用以下公式表示:
重量百分比= (元素摩尔分数x 元素原子量) / 合金摩尔质量x 100% 其中,元素原子量和合金摩尔质量需要根据具体情况进行计算。
灰铁配料计算
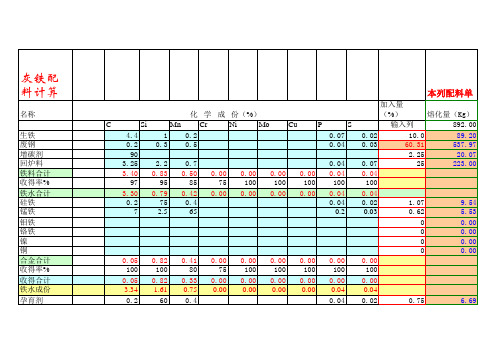
0.00 100 0.00 0.00
0.00 100 0.00 0.00
0.00 0.00
0.00 0.00
Байду номын сангаас
0.00 0.00
孕育剂带进铁液的硅量不大于0.3%,碳量不大于0.1%。 不同壁厚灰铸铁的成份 牌号 壁厚 C Si Mn P S HT100 <10 3.6-3.8 2.3-2.6 0.4-0.6 0.4 0.15 10-30 3.5-3.7 2.2-2.5 >30 3.4-3.6 2.1-2.4 HT150 <20 3.5-3.7 2.2-2.4 0.4-0.6 0.4 0.15 20-30 3.4-3.6 2.0-2.3 >30 3.3-3.5 1.8-2.2 HT200 <20 3.3-3.5 1.9-2.3 0.6-0.8 0.3 0.12 20-40 3.2-3.4 1.8-2.2 >40 3.1-3.3 1.6-1.9 HT250 <20 3.2-3.4 1.7-2.0 0.7-0.9 0.25 0.12 20-40 3.1-3.3 1.6-.18 >40 3.0-3.2 1.4-1.6 HT300 >15 3.0-3.2 1.4-1.7 0.7-0.9 0.2 0.1 高于250通过孕育得到 HT350 >20 2.9-3.1 1.2-1.6 0.8-1.0 0.15 0.1 HT400 >25 2.8-3.0 1.0-1.5 0.8-1.2 0.15 0.1
本列配料单
加入量(%) 熔化量(Kg) Cu P S 输入列 892.00 0.07 0.02 10.0 89.20 0.04 0.03 60.31 537.97 2.25 20.07 0.04 0.07 25 223.00 0.00 0.04 0.04 100 100 100 0.00 0.04 0.04 0.04 0.02 1.07 9.54 0.2 0.03 0.62 5.53 0 0.00 0 0.00 0 0.00 0 0.00 0.00 0.00 0.00 100 100 100 0.00 0.00 0.00 0.00 0.04 0.04 0.04 0.02 0.75 6.69 100 0.00 0.04 0.00 0.00 0.08 0.04
铬当量和镍当量计算公式
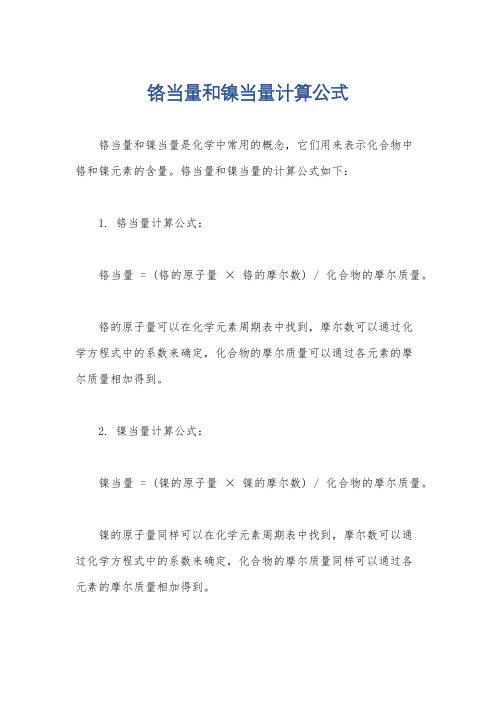
铬当量和镍当量计算公式
铬当量和镍当量是化学中常用的概念,它们用来表示化合物中
铬和镍元素的含量。
铬当量和镍当量的计算公式如下:
1. 铬当量计算公式:
铬当量 = (铬的原子量× 铬的摩尔数) / 化合物的摩尔质量。
铬的原子量可以在化学元素周期表中找到,摩尔数可以通过化
学方程式中的系数来确定,化合物的摩尔质量可以通过各元素的摩
尔质量相加得到。
2. 镍当量计算公式:
镍当量 = (镍的原子量× 镍的摩尔数) / 化合物的摩尔质量。
镍的原子量同样可以在化学元素周期表中找到,摩尔数可以通
过化学方程式中的系数来确定,化合物的摩尔质量同样可以通过各
元素的摩尔质量相加得到。
这些公式可以帮助化学研究人员和工程师确定化合物中铬和镍元素的含量,从而更好地理解和控制化合物的性质和行为。
这些计算公式对于理解化学反应和工业生产过程中的材料配比都具有重要的意义。
co50合金成分
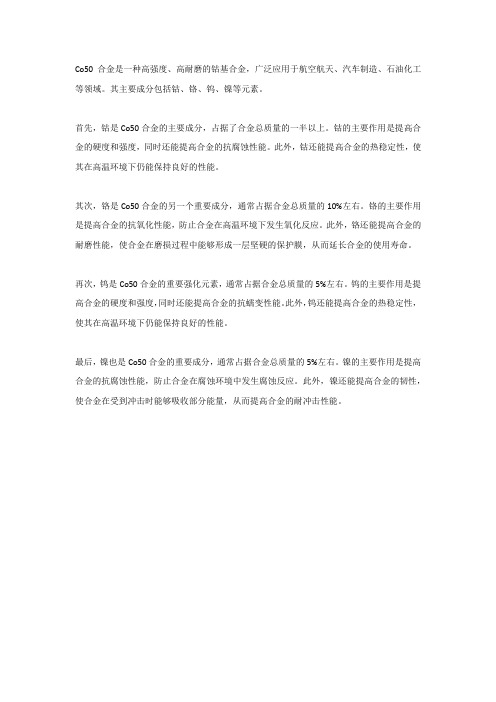
Co50合金是一种高强度、高耐磨的钴基合金,广泛应用于航空航天、汽车制造、石油化工等领域。
其主要成分包括钴、铬、钨、镍等元素。
首先,钴是Co50合金的主要成分,占据了合金总质量的一半以上。
钴的主要作用是提高合金的硬度和强度,同时还能提高合金的抗腐蚀性能。
此外,钴还能提高合金的热稳定性,使其在高温环境下仍能保持良好的性能。
其次,铬是Co50合金的另一个重要成分,通常占据合金总质量的10%左右。
铬的主要作用是提高合金的抗氧化性能,防止合金在高温环境下发生氧化反应。
此外,铬还能提高合金的耐磨性能,使合金在磨损过程中能够形成一层坚硬的保护膜,从而延长合金的使用寿命。
再次,钨是Co50合金的重要强化元素,通常占据合金总质量的5%左右。
钨的主要作用是提高合金的硬度和强度,同时还能提高合金的抗蠕变性能。
此外,钨还能提高合金的热稳定性,使其在高温环境下仍能保持良好的性能。
最后,镍也是Co50合金的重要成分,通常占据合金总质量的5%左右。
镍的主要作用是提高合金的抗腐蚀性能,防止合金在腐蚀环境中发生腐蚀反应。
此外,镍还能提高合金的韧性,使合金在受到冲击时能够吸收部分能量,从而提高合金的耐冲击性能。
镍铁合金上配料流程上传

1号混料桶
↓
2号混料桶加水制团
↓
烧结
↓
破碎
↓↓
<5mm 5mm-100mm
↓↓
返回1号混料桶↓
配料
↓↓
焦炭 石灰
↓
入炉
1、湿镍矿(一般为红土矿块25%、粉75%)+石灰(CaO),料场铲车堆料混拌,石灰吸水脱水;
2、筛分:1)块料20mm-450mm;2)粉料<20mm;
3、块料:破碎<20mm;
4、块料与粉料+Байду номын сангаас粉,进入1号混料桶混料;
5、进入2号混料桶加入适当水混料,制团;
6、送入车间焙烧,矿料中的结晶水在720℃蒸发,混入水焙烧时200-300℃能蒸发掉;
7、破碎:1)<5mm的返回1号混料桶;2)块料5mm-100mm;
8、配料:块料5mm-100mm + 焦炭 +石灰→入炉。
镍铁合金上料配料流程湿镍矿块25粉75石灰cao5mm5mm100mm焦炭石灰湿镍矿一般为红土矿块25粉75石灰cao料场铲车堆料混拌石灰吸水脱水
镍铁合金上料配料流程
湿镍矿(块25%、粉75%)石灰(CaO)
↓混料脱水↓
↓
筛分
↓↓
20mm-450mm块料<20mm粉料 煤粉
↓
破碎<20mm↓↓
↓↓↓