PCB生产流程简介
PCB生产制造全流程介绍

全板镀铜(主要是为加厚保护那层薄薄的化学铜以防其在空气
中氧化,形成孔内无铜或破洞)
pcb的生产流程
磨板(采用去毛刺、清洁、刷光和研磨等手段来调整金属表面
状态)
pcb的生产流程
贴膜(加热加压的条件下将干膜抗蚀剂粘贴在覆铜箔板上
)
pcb的生产流程
图形转移(将照相底版上的电路图像转移到覆铜箔层压板上,
HPGL 及 Post Script. HPGL 及 Post Script.
HPGL 及 Post Script. Gerber (RS-274) Text file文字檔 Excellon Format Text file文字檔 IPC-356 or 其它從CAD輸出之各種 格式 Text file文字檔
钻孔刀径=成品孔径+6mil(在满
足最小刀径和板厚孔径比情况下,又 无特殊需求,via孔不必遵循此条件)
阻焊焊盘直径=焊盘直径+4mil
9 最小成品孔径板厚比 10 最小内层隔离环宽(mil) 11 最小焊环宽(mil) 12 最小芯材板厚 13 最大成品板厚范围(mm) 14 最小焊盘直径(mil) 15 最大成品板尺寸(inch) 16 压板厚度公差(mil) 17 成品层间对位精度(mil) 18 成品孔径精度(mil) 19 最小网格间距(mil) 20 最小绿油桥间距(mil) 21 机械加工精度(mil) 22 最小外型铣刀(mm) 23 最大V-CUT板尺寸(inch) 24 最小金属化槽钻咀(mm) 25 层数
PCB厂典型组织结构图
PCB全流程介绍
1.销售(接单---工程审核单-报价规则 ---报价) 2.工程(出菲林,层压叠板) 3.计划 (Bom) 4.生产(品
pcb板生产流程
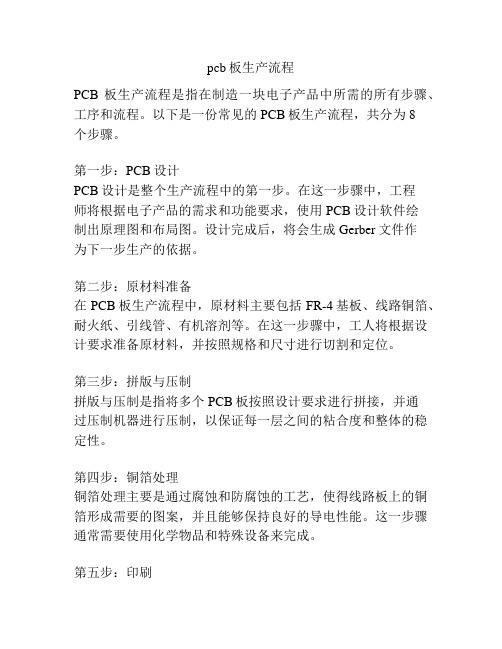
pcb板生产流程PCB板生产流程是指在制造一块电子产品中所需的所有步骤、工序和流程。
以下是一份常见的PCB板生产流程,共分为8个步骤。
第一步:PCB设计PCB设计是整个生产流程中的第一步。
在这一步骤中,工程师将根据电子产品的需求和功能要求,使用PCB设计软件绘制出原理图和布局图。
设计完成后,将会生成Gerber文件作为下一步生产的依据。
第二步:原材料准备在PCB板生产流程中,原材料主要包括FR-4基板、线路铜箔、耐火纸、引线管、有机溶剂等。
在这一步骤中,工人将根据设计要求准备原材料,并按照规格和尺寸进行切割和定位。
第三步:拼版与压制拼版与压制是指将多个PCB板按照设计要求进行拼接,并通过压制机器进行压制,以保证每一层之间的粘合度和整体的稳定性。
第四步:铜箔处理铜箔处理主要是通过腐蚀和防腐蚀的工艺,使得线路板上的铜箔形成需要的图案,并且能够保持良好的导电性能。
这一步骤通常需要使用化学物品和特殊设备来完成。
第五步:印刷印刷是将PCB板上的线路进行印刷,以使它们可见并且能够达到预期的导电效果。
在这一步骤中,工人会使用特殊的印刷设备和油墨材料来完成印刷。
第六步:外层处理外层处理是指对整个PCB板进行表面处理以保护铜箔层和印刷层,通常使用覆盖层来覆盖整个PCB板表面。
这一步骤可以防止铜箔氧化、腐蚀和磨损,从而提高整个PCB板的使用寿命和性能。
第七步:钻孔与插孔钻孔与插孔是将PCB板上的钻孔和插孔进行打孔和定位,以方便后续的元器件安装和连接。
这一步骤通常使用钻床和其他特殊设备来完成。
第八步:元器件安装与焊接元器件安装是将电子产品所需的各个元器件安装到PCB板上的特定位置。
安装完成后,使用焊接设备进行焊接,以保证元器件与PCB板之间的稳固连接。
这一步骤通常需要工程师和技术人员共同完成。
总结起来,PCB板生产流程包括PCB设计、原材料准备、拼版与压制、铜箔处理、印刷、外层处理、钻孔与插孔以及元器件安装与焊接等8个步骤。
pcb主要生产流程

PCB主要生产流程PCB(Printed Circuit Board,印刷电路板)是电子产品中不可或缺的组成部分,它通过连接电子元件,实现电路的功能。
PCB的生产流程主要包括设计、制版、印刷、成型、组装和测试等步骤。
下面将详细介绍PCB主要生产流程的步骤和流程。
1. 设计PCB的设计是整个生产流程的起点,它决定了电路板的布局、连接方式、尺寸等重要参数。
设计师根据电路原理图和功能需求,使用专业的PCB设计软件进行布线、布局,确定电路板上各个元件的位置和连接方式。
2. 制版制版是将设计好的PCB图纸转化为可供生产使用的制版文件。
制版过程主要包括图纸转换、图纸校对和图纸输出等步骤。
首先,设计师将PCB设计文件转化为制版软件可识别的格式,通常是Gerber格式。
然后,进行图纸校对,检查图纸是否与设计要求一致,是否存在错误或问题。
最后,将校对无误的图纸输出为制版文件,通常是光刻胶层、蚀刻层、钻孔层等。
3. 印刷印刷是将制版文件上的电路图案印制到电路板上的过程。
印刷过程主要包括基材准备、蚀刻、镀铜等步骤。
首先,准备好电路板基材,通常是玻璃纤维增强树脂板(FR-4)。
然后,将制版文件上的图案通过光刻技术转移到电路板上的光刻胶层。
接下来,使用蚀刻液将未被光刻胶保护的铜层蚀刻掉,形成电路图案。
最后,在蚀刻后的电路板上进行镀铜,增加电路板的导电性和耐腐蚀性。
4. 成型成型是将印刷好的电路板进行切割和打孔,使其符合设计要求的尺寸和形状。
成型过程主要包括切割、打孔、去毛刺等步骤。
首先,根据设计要求,将印刷好的电路板进行切割,通常使用切割机进行。
然后,使用钻孔机在电路板上打孔,以便安装元件和连接电路。
最后,去除切割和打孔过程中产生的毛刺,保证电路板表面的平整和光滑。
5. 组装组装是将印刷好的电路板上的元件进行安装和焊接,形成完整的电路功能。
组装过程主要包括元件贴装和焊接等步骤。
首先,将需要安装的元件按照设计要求的位置放置在电路板上。
PCB板生产流程

PCB板生产流程PCB板(Printed Circuit Board,印刷电路板)是电子设备的重要组成部分,它作为电子元器件间连接的主要平台,承载着电子设备的信号传输和电源供应等功能。
PCB板的生产流程可以分为设计、制版、堆叠、钻孔、镀膜、曝光、蚀刻、压线、测试和组装等多个步骤。
下面将详细介绍PCB板的生产流程。
1.设计:PCB板生产的第一步是根据电子设备的功能和需求进行设计。
设计师使用电路设计软件将电路连接和布局规划在PCB板上,确定电路板上元器件的位置和信号传输路径。
2.制版:设计师将设计好的PCB板图纸输出成底版,然后通过光刻技术将设计好的电路图案和排线传导图案转移到电路板表面,形成底板。
3.堆叠:堆叠是将多层电路板叠在一起形成复合板。
多层板可以提高电路板的密度,同时也可以提高电路板的抗干扰能力。
堆叠时需要注意各层之间的信号和电源的分布。
4.钻孔:在制作PCB板时,需要在准确的位置上钻出连接跳线和焊盘的孔,以便连接元器件和导线。
通常使用数控钻床或激光钻孔机进行钻孔。
5.镀膜:在PCB板的表面镀上一层金属,一方面可以保护电路和导线不被氧化,另一方面也可以提高焊接接触度。
常用的金属材料包括镍和金。
6.曝光:将底板上覆盖的感光层用光来曝光,以暴露出底板上的图案和线路。
曝光后的感光层会发生物理或化学变化,形成图案和线路。
7.蚀刻:通过化学蚀刻的方式将没有被曝光的感光层经过蚀刻去除,露出底板上的铜层。
经过蚀刻后,就可以形成PCB板上的电路图案和导线。
8.压线:在PCB板的金属层上覆盖一层焊盘,用于连接元器件和电路板。
焊盘会通过一种叫做压铜的工艺来形成。
9.测试:通过对PCB板的电气特性进行测试,确保电路板的质量和性能符合要求。
测试中会检查电路板的连通性、阻抗匹配等参数。
10.组装:将元器件、电阻、电容等进行焊接,完成整个电路板的组装。
组装时需要将元器件与焊盘进行精确定位,在连接之后进行焊接。
以上就是PCB板生产的基本流程。
pcb板生产流程

pcb板生产流程
PCB板生产流程是指将电路图设计完成后,通过一系列的加工工艺,将电路图转化为实际的电路板。
一般而言,PCB板生产流程包含以下几个步骤:
1. 设计电路图:根据电子元器件的尺寸、引脚位置、电气连接关系等,利用电路设计软件绘制出电路图。
2. 制作印刷版:将电路图输出成印刷版,即铜箔板,这个板子是制造PCB的原材料。
3. 板上光绘:将印刷版放置在光刻机上,通过光刻制作出电路图形。
4. 蚀刻:在蚀刻机中将铜箔板上不需要的部分化学蚀去,只留下需要导电的铜箔部分。
5. 钻孔:将需要连接的部分进行钻孔处理。
6. 小孔放电:利用小孔放电机去除电路板上孔洞积聚的金属。
7. 外部加工:将电路板切割成需要的尺寸,并进行表面处理等。
8. 焊接:将电子元器件与电路板焊接在一起。
9. 测试:通过测试仪器对PCB板进行测试,检查制造是否正确。
10. 完成:经过一系列的工艺处理,PCB板最终被制造出来。
- 1 -。
PCB生产流程简介

PCB生產流程簡介目錄﹕1.PCB大致生產流程簡介。
2.各生產制程簡介。
3.各制程相關Coupon 簡介。
一、PCB大致生產流程內層線路→內層檢驗→壓板→鑽孔→電鍍一銅→外層線路→電鍍二銅→防焊綠漆→OSP/IMG/HASL→切型→測試→外層檢驗→包裝出貨二、各制程生產流程簡介1.內層線路制程﹕(1).作業流程﹕(2).流程簡介﹕a.前處理﹕利用電解脫脂方式,產生大量氧氣摩擦銅表面,以機械物理力量清潔表面;產生的氧氣會使液體翻騰,使新鹼液與油脂污垢之接觸增加,使油脂皂化、乳化以達到清潔表面之目的. 陽極主反應﹕M→M n+ +ne-2OH-→H2+O2+2e-陽極副反應﹕2Cu + O2→CuO2陰極主反應﹕Cu2+ + 2e-→Cu 2H+ +2e-→H2b.曝光與蝕刻﹕圖示﹕壓膜前基板壓膜後基板干膜曝光干膜顯影蝕刻後基板去膜後基板曝光原理﹕曝光即在紫外光照射下,光引發劑吸收了光能分解成游離基,游離基再引發聚合單體進行聚合交聯反應後形成不溶于稀鹼溶液的體形大分子結構。
蝕刻原理﹕CuCl2 + Cu→2CuCl2CuCl + 2HCl→H2Cu2Cl4H2Cu2Cl4 + H2O2→2CuCl2 + 2H2O作業環境要求﹕因干膜的主要特性就是遇可見光會發生聚合,故壓膜、曝光作業必須在黃光室內作業,避免干膜遇見可見光發生不必要的聚合而失效。
2.內層檢驗制程﹕(1).制程目的﹕對內層線路課出來的內層板進行檢驗,防止缺點板流失到後制程造成報廢;同時為壓板制程沖出鉚釘孔。
(3).各流程單元功能﹕a. CCD沖孔﹕對內層線路課出來的內層板利用CCD沖孔機在板邊沖出高精准度之孔位,供壓板課上鉚釘後壓合,並作為課內後單元之測試定位孔;b.P/G銅面測試﹕利用P/G測試機對內層板之POWER/GROUND層進行偵測,找出上面的銅渣並去除之,否則壓合後會造成內層斷路報廢;c.AOI光學檢測﹕將線路面的缺點,如短路、斷路、缺口、銅渣等,利用光學系統偵測出來並存儲于電腦,供VRS使用;d. VRS確認﹕對AOI偵測後記憶起來的缺點資料利用VRS確認機逐個放大,人工確認其真假。
线路板的生产流程
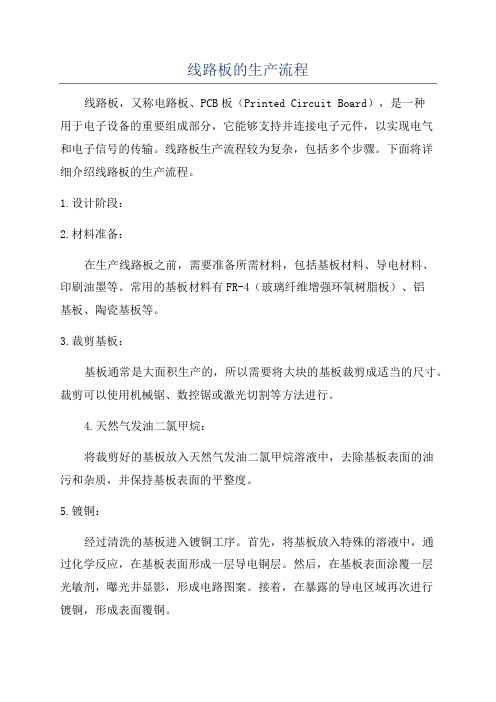
线路板的生产流程线路板,又称电路板、PCB板(Printed Circuit Board),是一种用于电子设备的重要组成部分,它能够支持并连接电子元件,以实现电气和电子信号的传输。
线路板生产流程较为复杂,包括多个步骤。
下面将详细介绍线路板的生产流程。
1.设计阶段:2.材料准备:在生产线路板之前,需要准备所需材料,包括基板材料、导电材料、印刷油墨等。
常用的基板材料有FR-4(玻璃纤维增强环氧树脂板)、铝基板、陶瓷基板等。
3.裁剪基板:基板通常是大面积生产的,所以需要将大块的基板裁剪成适当的尺寸。
裁剪可以使用机械锯、数控锯或激光切割等方法进行。
4.天然气发油二氯甲烷:将裁剪好的基板放入天然气发油二氯甲烷溶液中,去除基板表面的油污和杂质,并保持基板表面的平整度。
5.镀铜:经过清洗的基板进入镀铜工序。
首先,将基板放入特殊的溶液中,通过化学反应,在基板表面形成一层导电铜层。
然后,在基板表面涂覆一层光敏剂,曝光并显影,形成电路图案。
接着,在暴露的导电区域再次进行镀铜,形成表面覆铜。
6.制作印刷油墨层:将基板放入蚀刻装置中,使用化学蚀刻的方法,去除导电图案以外的覆铜层。
然后,涂覆印刷油墨,使其填充在蚀刻后的凹槽中。
蚀刻完成后,印刷油墨形成线路图案。
7.进行钻孔:使用自动钻孔机,根据电路设计要求,在印刷油墨的空白处钻孔,形成电路板上元器件安装的孔位。
8.加热热点:为了提高焊接效果,还应在电路板上加热,使得元件焊接更加牢固。
9.焊接元器件:使用自动贴片机将元件精确地贴附在电路板上。
然后,将元器件与电路板焊接在一起。
10.进行功能测试:完成焊接后,对线路板进行功能测试,以确保产品的性能和质量。
11.过程检验和调试:对生产过程中的每个环节进行检验,以及对生产出的产品进行调试和测试,以确保线路板的质量和可靠性。
12.进行喷锡、包装等工序:对已经完成测试的线路板进行喷锡等镀处理,以确保线路板的稳定性和耐久性。
然后,根据客户需求,进行包装和标识。
pcb生产流程

pcb生产流程
PCB生产流程通常包括以下几个步骤:
1. 原材料准备:准备所需的原材料,包括基板、铜箔、电阻、电容、芯片等。
2. 图纸设计:根据产品需求绘制PCB的布局图和电路图,确定布线规则和元器件位置。
3. 印制电路板制作:通过化学反应将电路图上的线路、焊盘等传输到基板上,形成印刷电路板(PCB)。
4. 光刻制作:利用光刻技术将电路图转移到铜箔上,形成铜箔电路。
5. 电镀:在铜箔上涂上一层保护膜,然后通过电解核实,将金属覆盖在铜箔上,增加导电性。
6. 电路板组装:将元器件按照电路图的布局要求分布在PCB板上,并通过焊接技术将它们固定在板上。
7. 焊接:通过波峰焊或热风烙铁等方式将元器件与PCB板焊接在一起。
8. 焊接检测:检测焊接质量和电气性能,包括引脚连接、电压、电流等。
9. 硅胶封装:保护元器件免受外部环境的干扰和损害,提高产品的稳定性和可靠性。
10. 测试:测试装配好的电路板的功能和性能是否满足设计要求。
11. 包装:将测试合格的电路板进行包装,包括静电包装、箱装等。
12. 质量控制:对成品进行质量检验,确保产品质量符合要求。
以上是一般的PCB生产流程,具体的流程可能根据产品的不同有所差异。
PCB制造流程简介

PCB制造流程简介一.A/W 底片制作这是一个在单张胶片上用激光或绘图或是接触印制形成电路图的过程。
根据应用需要将底片母片或是生产母片,生产母片用来在涂覆了感光材料或贴了感光干膜的Laminate上印制电路。
二.原材料采购/IQC检查Incoming Inspection of Laminates覆铜板的来料检验检验从Vendor处采购的符合采购规范的半固化片,使得只有合格的覆铜板被用于生产。
(覆铜板由半固化片和铜箔经热压而成,laminate必须是FR4级的,四功能环氧树脂或高功能环氧树脂,laminate的玻璃转移温度范围是130~140℃)Incoming Inspection of Prepreg半固化片的来料检验检验从合格的Vendor处采购的符合采购规范的半固化片,使得只有合格的半固化片用于生产。
(Prepreg由玻璃布和涂抹在上面的半固化环氧树脂组成。
)三.Warehouse Shearing切板货仓作为一个辅助性功能的部门,担负着产品需要之物料的收发工作包括(收料&发货)。
平时,货仓需要帮助生产部门,将较大尺寸的板裁剪成所需尺寸,材料准备。
四.Inner Layer内层Pre-clean预清洗预清洗:清洗内层板表面及改进铜面与湿膜的黏附性。
Coating涂膜涂膜:在内层表面涂湿膜(湿膜被用印刷线路或导电图形)。
Stricky Roller粘性滚轮粘性滚轮:在印图前通过滚轮除去已涂膜内层上的灰尘颗粒。
Imaging印刷线路印刷线路:在已涂有光阻剂的内层上使用底边印刷图形并使用紫外光确定图形。
Developing显影此过程是除去或溶解掉软的未曝光的光阻剂,露出不想要的铜并为蚀刻做好准备。
显影后硬化的光阻剂将留在内层表面。
Etching蚀刻蚀刻:从内层表面除去不想要的铜。
Strip去膜去膜:在光阻剂下的铜线路将被去膜,露出所要的铜线路。
AOI自动光学检测自动光学检测:扫描出任何能造成板面故障的缺陷。
PCB制造详介

PCB制造详介PCB(Printed Circuit Board)制造是电子行业中不可避免的一个环节。
PCB是电子元器件之间互相连接的核心组成部分。
它的制造包括从原始材料到最终成品的一系列步骤。
本文将详细介绍PCB制造的过程及其各个环节。
第一步:设计与原材料选择PCB的制造首先需要进行设计,确定电路板上各部件的位置和连接方式。
这需要经验丰富的工程师进行,使用特定的设计软件完成。
完成设计后,需要根据PCB板上电子元器件的要求,选择相应的原材料。
例如,基板材料可以是FR4(玻璃纤维)、铝基板或陶瓷基板,其中FR4是最常用的材料之一。
第二步:印制电路板层压印制电路板层压是PCB制造的核心步骤之一,主要用于制造多层板。
这一步骤是将各层电路板粘合起来,形成一个电路板。
这通常需要使用高温、高压的机器,也需要使用有机化学材料,如粘接剂和助焊剂。
该过程通常有许多次重复,以确保每层都按照设计来排列。
第三步:划线及钻孔在印制电路板层压后,需要划线来定义电路板的轮廓。
这可以通过机械和激光划线完成。
在完成划线后,需要在PCB板上钻出各种连接孔。
这些孔可以是用于走线的通孔或用于安装电子元器件的焊盘圆孔。
第四步:镀金电子元器件通常需要焊接在PCB板上。
为此,需要在焊盘上镀上金属,通常是镀金。
这可以防止氧化和腐蚀,确保焊接的质量和稳定性。
第五步:沉铜沉铜可以在电路板制造的任何阶段进行。
这是PCB制造的另一个核心步骤,用于在电路板上形成导电路径。
当铜被沉积在电路板的表面时,可以使用化学或电化学的方式,沉积在电路板上形成所需的电路路径。
这可以使用电镀或电解铜等方法完成。
第六步:覆铜钻孔在电路板层压完成后,需要进行覆铜钻孔。
这是在PCB上预先钻入连接孔,以便在后期连接不同电子元器件。
该步骤通常需要使用微型化的钻头进行钻孔,并在钻过程中使电路板的层与层之间不受破坏。
第七步:阻焊覆盖为了保护PCB电路板不受外部损害,需要进行覆盖阻焊。
PCB全流程讲解
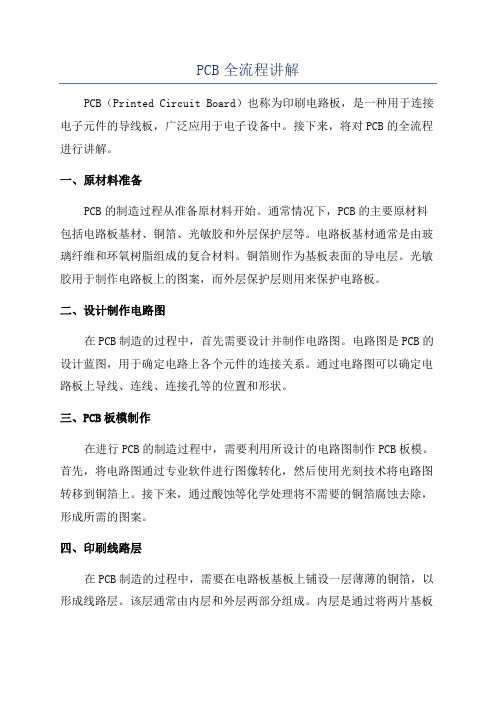
PCB全流程讲解PCB(Printed Circuit Board)也称为印刷电路板,是一种用于连接电子元件的导线板,广泛应用于电子设备中。
接下来,将对PCB的全流程进行讲解。
一、原材料准备PCB的制造过程从准备原材料开始。
通常情况下,PCB的主要原材料包括电路板基材、铜箔、光敏胶和外层保护层等。
电路板基材通常是由玻璃纤维和环氧树脂组成的复合材料。
铜箔则作为基板表面的导电层。
光敏胶用于制作电路板上的图案,而外层保护层则用来保护电路板。
二、设计制作电路图在PCB制造的过程中,首先需要设计并制作电路图。
电路图是PCB的设计蓝图,用于确定电路上各个元件的连接关系。
通过电路图可以确定电路板上导线、连线、连接孔等的位置和形状。
三、PCB板模制作在进行PCB的制造过程中,需要利用所设计的电路图制作PCB板模。
首先,将电路图通过专业软件进行图像转化,然后使用光刻技术将电路图转移到铜箔上。
接下来,通过酸蚀等化学处理将不需要的铜箔腐蚀去除,形成所需的图案。
四、印刷线路层在PCB制造的过程中,需要在电路板基板上铺设一层薄薄的铜箔,以形成线路层。
该层通常由内层和外层两部分组成。
内层是通过将两片基板用铜箔连接在一起,然后通过酸蚀等方法将不需要的铜箔去除,形成所需的线路图案。
外层则通过类似的方法制作。
五、开孔在PCB制造过程中,为了实现电子元件的插入和连接,需要在电路板上开孔。
开孔一般通过机械钻孔或激光钻制作,孔径和孔距需要与电子元件的尺寸和规格相匹配。
六、喷镘制图喷镘制图是将光敏胶喷涂到PCB板上,并利用UV光照射将胶层固化,形成所需的图案。
通过此步骤,可以形成电路板上各个元件的图案,并形成电路板的最终形态。
七、焊接元件和测试在PCB板制造完成后,需要将所需的电子元件焊接到电路板上。
通常情况下,焊接过程包括表面贴装技术(SMT)和插件技术(PTH)。
焊接完成后,还需要进行电路板的测试,以确保元件的正常工作。
八、清洁和包装在所有的制造步骤完成后,还需要对PCB板进行清洁和包装。
pcb生产流程简介

PCB的生产流程主要包括以下步骤:
1. 设计:使用CAD软件进行电路原理图和PCB布局的设计,确定PCB板的尺寸、布线方式、焊盘大小等信息。
2. 图形转换:将电路原理图和PCB布局图转换成Gerber文件,以便进行制版和刻蚀等工艺。
3. 制版:通过将Gerber文件转换成光阻膜,然后通过曝光、显影等工艺将光阻膜图形转移到铜箔上,制作出PCB板的线路和图形。
4. 刻蚀:将不需要的铜箔部分去除,形成PCB板的线路和图形。
5. 钻孔:在PCB板上钻出各种孔位,包括焊盘孔、定位孔、安装孔等。
6. 涂覆:将覆铜板上的光阻膜去除,然后覆盖一层焊膜,以便进行焊接操作。
7. 焊接:将元器件安装到PCB板上,并进行焊接。
8. 检测:对焊接后的PCB板进行质量检测,包括AOI检测、X射线检测、ICT检测等。
9. 清洗:将焊接后的PCB板清洗干净,以便进行后续的封装和组装操作。
此外,还包括一些特定类型的PCB板的生产工艺:
1. 内层线路制作:包括前处理、内层涂布、曝光、显影、蚀刻、去
膜等步骤。
2. 外层线路制作:包括前处理、压干膜、曝光、显影、蚀刻、去膜等步骤。
3. 防焊漆流程:包括前处理、刷漆、曝光、显影等步骤。
4. 表面处理:包括化金(化学镍金)、镀金等步骤。
5. 成型:把板子裁切成客户需要的尺寸。
6. 电测&出货检验:包括飞针测试、专用测试机等检测方法。
以上是PCB生产的主要流程,供您参考,建议咨询专业人士获取更准确的信息。
pcb制程流程

PCB制程流程主要包括以下步骤:
裁板:将PCB基板裁剪成生产尺寸。
前处理:清洁PCB基板表面,去除表面污染物。
压膜:将干膜贴在PCB基板表层,为后续的图像转移做准备。
曝光:使用曝光设备利用紫外光对覆膜基板进行曝光,从而将基板的图像转移至干膜上。
DE:将进行曝光以后的基板经过显影、蚀刻、去膜,进而完成内层板的制作。
内检:检测及维修板子线路。
压合:将多个内层板压合成一张板子。
钻孔:按照客户要求利用钻孔机将板子钻出直径不同,大小不一的孔洞,使板子之间通孔以便后续加工插件,也可以帮助板子散热。
一次铜:为外层板已经钻好的孔镀铜,使板子各层线路导通。
外层:为方便后续工艺做出线路。
二次铜与蚀刻:二次镀铜,进行蚀刻。
以上步骤完成后,PCB制作流程基本完成。
pcb生产流程
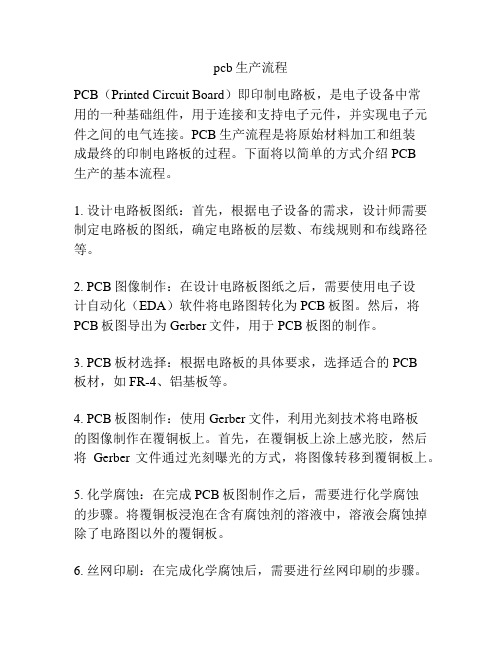
pcb生产流程PCB(Printed Circuit Board)即印制电路板,是电子设备中常用的一种基础组件,用于连接和支持电子元件,并实现电子元件之间的电气连接。
PCB生产流程是将原始材料加工和组装成最终的印制电路板的过程。
下面将以简单的方式介绍PCB生产的基本流程。
1. 设计电路板图纸:首先,根据电子设备的需求,设计师需要制定电路板的图纸,确定电路板的层数、布线规则和布线路径等。
2. PCB图像制作:在设计电路板图纸之后,需要使用电子设计自动化(EDA)软件将电路图转化为PCB板图。
然后,将PCB板图导出为Gerber文件,用于PCB板图的制作。
3. PCB板材选择:根据电路板的具体要求,选择适合的PCB板材,如FR-4、铝基板等。
4. PCB板图制作:使用Gerber文件,利用光刻技术将电路板的图像制作在覆铜板上。
首先,在覆铜板上涂上感光胶,然后将Gerber文件通过光刻曝光的方式,将图像转移到覆铜板上。
5. 化学腐蚀:在完成PCB板图制作之后,需要进行化学腐蚀的步骤。
将覆铜板浸泡在含有腐蚀剂的溶液中,溶液会腐蚀掉除了电路图以外的覆铜板。
6. 丝网印刷:在完成化学腐蚀后,需要进行丝网印刷的步骤。
丝网印刷是将焊膏通过丝网印刷在PCB板上,用于焊接电子元件。
7. 元件贴装:在完成丝网印刷后,将电子元件通过自动贴装机精确地贴装在PCB板上,电子元件与PCB板上的焊膏形成电气连接。
8. 回流焊接:将贴装好的电子元件的焊膏通过回流焊接炉进行加热,使焊膏熔化,同时将电子元件固定在PCB板上。
9. 检验和测试:对焊接后的PCB板进行检验和测试,确保电子元件的焊接质量和电气连接的可靠性。
10. 包装和出货:在通过检验和测试之后,将PCB板进行包装,并准备出货。
当然,上述仅是PCB生产的主要流程,并不是详细的指导。
在实际生产中,还需要考虑到细节和特定的要求,如表面处理、钻孔、装配等。
但总体而言,以上介绍的是PCB生产的基本流程,可以帮助我们了解PCB的生产过程。
PCB生产工艺流程

PCB生产工艺流程PCB(Printed Circuit Board),即印刷电路板,是一种用于连接和支持电子元件的电路板。
在电子制造业中,PCB生产工艺流程是非常重要的,决定了PCB的质量和可靠性。
下面将详细介绍PCB生产工艺流程。
1.原材料准备:2.毛胚制备:毛胚制备是PCB生产的核心步骤,包括蚀刻、覆铜、打孔等工艺。
(1)蚀刻:将覆铜层保护膜部分剥离,然后将空白部分蚀刻掉,形成电路板的形状和线路。
(2)覆铜:将覆铜液均匀涂布在基板表面,使得基板表面形成一层铜箔,用于导电。
(3)打孔:根据设计要求,在基板上打孔,以便进行电子元件的连接。
3.图案制作:图案制作是指将电路设计图案转移到PCB板上,包括图案制作光阻、曝光、显影等步骤。
(1)图案制作光阻:将光敏涂料(光阻剂)涂覆在PCB板上,然后通过加热或暴露于紫外线下,使涂层固化。
(2)曝光:将电路设计图案通过连续曝光到光阻层上,形成与电路板设计图案相同的光刻图案。
(3)显影:用显影剂去除未固化的光刻图案。
4.蚀刻:蚀刻是将未被光刻图案遮蔽的铜箔部分蚀刻掉,形成电路板的导线和连接孔。
5.镀金:镀金是为了提高PCB板的导电性和耐腐蚀性,使得PCB板更加稳定和可靠。
常用的镀金方法有化学镀金、电镀镀金和电镀锡等。
6.排钻:排钻是用机器将电路板上的孔进行排列和钻孔,以便电子元件的安装和焊接。
7.焊盘沉镀:焊盘沉镀是为了提高焊接连接性能,保证电子元件的焊接质量。
通常采用热浸镀锡或喷锡等方法。
8.控制板外层:将两块PCB板层叠在一起,通过压力和温度将其压合在一起。
9.修边:通过机器将PCB板修边成所需的形状和尺寸。
10.印刷标识:11.成品检验:对PCB板进行检验,包括外观检查、尺寸检查、电气性能测试等。
12.包装和出货:将通过检验的PCB板进行包装,并按照要求进行分拣和出货。
以上是PCB生产工艺的主要流程,每个步骤都需要严格控制和操作,以保证PCB板的质量和可靠性。
PCB生产流程介绍
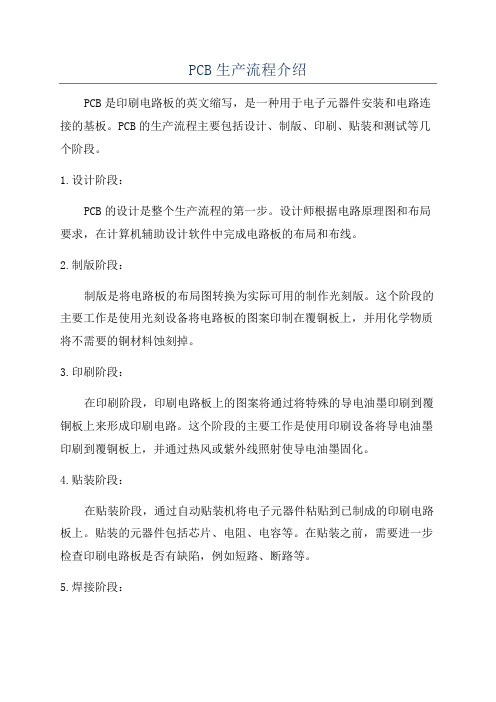
PCB生产流程介绍PCB是印刷电路板的英文缩写,是一种用于电子元器件安装和电路连接的基板。
PCB的生产流程主要包括设计、制版、印刷、贴装和测试等几个阶段。
1.设计阶段:PCB的设计是整个生产流程的第一步。
设计师根据电路原理图和布局要求,在计算机辅助设计软件中完成电路板的布局和布线。
2.制版阶段:制版是将电路板的布局图转换为实际可用的制作光刻版。
这个阶段的主要工作是使用光刻设备将电路板的图案印制在覆铜板上,并用化学物质将不需要的铜材料蚀刻掉。
3.印刷阶段:在印刷阶段,印刷电路板上的图案将通过将特殊的导电油墨印刷到覆铜板上来形成印刷电路。
这个阶段的主要工作是使用印刷设备将导电油墨印刷到覆铜板上,并通过热风或紫外线照射使导电油墨固化。
4.贴装阶段:在贴装阶段,通过自动贴装机将电子元器件粘贴到已制成的印刷电路板上。
贴装的元器件包括芯片、电阻、电容等。
在贴装之前,需要进一步检查印刷电路板是否有缺陷,例如短路、断路等。
5.焊接阶段:在焊接阶段,通过波峰焊接机将贴装完成的电子元器件与印刷电路板焊接在一起。
焊接的方法通常有浸锡法和无铅焊接法两种。
焊接完成后,需要进行视觉检测和电气性能测试,以确保焊接的质量和可靠性。
6.测试阶段:在测试阶段,对已制成的印刷电路板进行电气性能测试,以确保其功能正常。
测试方法包括功能测试、电气测试和可靠性测试等。
7.包装阶段:以上是PCB的主要生产流程介绍。
每个阶段都需要严格的操作和控制,以确保PCB的质量和性能。
同时,随着科技的进步,PCB的生产流程也在不断发展和改进,以满足日益复杂的电子产品需求。
PCB流程简介-全流程
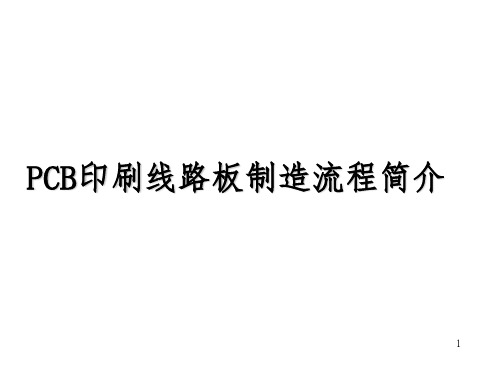
➢溶剂显像型 ➢半水溶液显像型 ➢ 碱水溶液显像型
水溶性干膜主要是由于其组成中含有机酸根,会与 强碱反应使成为有机酸的盐类,可被水溶掉。
35
(外层课)介绍
☺ 曝光(Exposure):
制程目的: 通过 image transfer技术在干膜上曝出客 户所需的线路 重要的原物料:底片
目的:
➢ 把经处理过的基板铜面透过热 压方式贴上抗蚀干膜
主要原物料:干膜(Dry Film)
➢ 溶剂显像型
➢ 半水溶液显像型
➢ 碱水溶液显像型
干膜
➢ 水溶性干膜主要是由于它组成 成分中含有机酸根,会与强碱 反应,使成为有机酸的盐类, 可被水溶掉。
压膜前
压膜后
7
(内层课)介绍
曝光(EXPOSURE): 目的: ➢ 采用UV光,把原始底片上的图像转 移到感光底板上(干膜/湿膜)
PCB印刷线路板制造流程简介
1
PCB制造流程简介
制一部(发料至DESMEAR前)
内层课:裁板;内层前处理;压膜;曝光;DES连线 内层检验课:CCD冲孔;AOI检验;VRS确认 压板课:棕化;铆钉;叠板;压合;后处理 钻孔课:上PIN;钻孔;下PIN
2
流程介绍:
(内层课)介绍
裁板
前处理
压膜
曝光
DES
会存在一些误判的缺点,故需通过人工加以确认
44
(外层检验课)介绍
☺V.R.S:
全称为Verify Repair Station,确认系统 目的:通过与A.O.I连线,将每片板子的测试资料传给V.R.S ,并由人工对A.O.I的测试缺点进行确认。 需注意的事项:V.R.S的确认人员不光要对测试缺点进行确
PCB生产制造全流程介绍

PCB生产制造全流程介绍PCB(Printed Circuit Board)是指印刷电路板,是电子产品中不可缺少的一个核心部件。
PCB的制造流程是一系列复杂而精密的步骤,以下将对PCB的生产制造全流程进行详细介绍。
首先是设计阶段。
在设计阶段,制造商需要根据电子产品的需求和要求,设计电路板的布局和电路连线。
这需要使用CAD软件进行电路板的设计,并进行电路仿真和验证,以确保设计的正确性和可行性。
接下来是原材料的准备。
PCB的制造过程中主要使用到的原材料有:铜箔、玻璃纤维布和树脂。
铜箔用于制作电路板的导线,玻璃纤维布用于增强电路板的强度,树脂则用于粘合铜箔和玻璃纤维布。
这些原材料需要进行精细的处理和准备。
然后是制作电路板的内层。
内层的制作分为以下几个步骤:首先,在玻璃纤维布上涂布树脂,并将铜箔覆盖在其中。
然后,将其放入高温高压的压板中,使得树脂固化,铜箔与玻璃纤维布紧密结合。
最后,对其进行修边和抛光,使得制作好的内层电路板表面光滑平整。
接下来是制作电路板的外层。
外层的制作分为以下几个步骤:首先,将制作好的内层电路板与带有电路图案的透明胶片对位,然后在铜箔上涂布光刻胶。
接着,将电路图案的透明胶片放置在光刻胶上,用紫外线照射,使得光刻胶固化。
之后,将其放入腐蚀液中,使得未被光刻胶保护的铜箔被腐蚀掉,从而形成电路图案。
最后,再次进行修边和抛光,使得制作好的外层电路板表面光滑平整。
然后是通过多孔板的制作。
多孔板是指电路板上的穿孔,用于连接内层电路和外层电路。
多孔板的制作分为以下几个步骤:首先,将内层电路板与带有孔位信息的透明胶片对位,然后通过钻孔机进行钻孔。
接着,将钻孔的位置涂布导电涂料,使得多孔板形成导电通路。
最后,进行清洗和检查,确保多孔板的质量和性能。
最后是电路板的组装和测试。
在组装阶段,制造商需要将电子元件焊接到PCB上,并通过贴片和插件的方式完成。
然后,对焊接好的电路板进行自动化和手工的测试,以确保电路板的功能正常和稳定。
PCB生产流程介绍
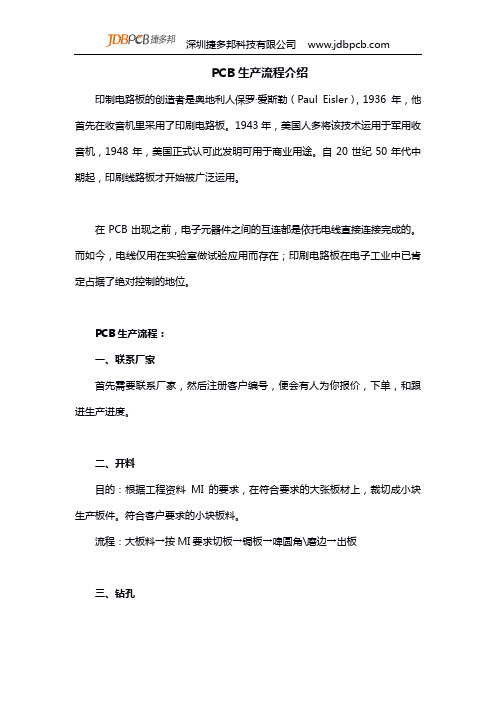
PCB生产流程介绍印制电路板的创造者是奥地利人保罗·爱斯勒(Paul Eisler),1936年,他首先在收音机里采用了印刷电路板。
1943年,美国人多将该技术运用于军用收音机,1948年,美国正式认可此发明可用于商业用途。
自20世纪50年代中期起,印刷线路板才开始被广泛运用。
在PCB出现之前,电子元器件之间的互连都是依托电线直接连接完成的。
而如今,电线仅用在实验室做试验应用而存在;印刷电路板在电子工业中已肯定占据了绝对控制的地位。
PCB生产流程:一、联系厂家首先需要联系厂家,然后注册客户编号,便会有人为你报价,下单,和跟进生产进度。
二、开料目的:根据工程资料MI的要求,在符合要求的大张板材上,裁切成小块生产板件。
符合客户要求的小块板料。
流程:大板料→按MI要求切板→锔板→啤圆角\磨边→出板三、钻孔目的:根据工程资料,在所开符合要求尺寸的板料上,相应的位置钻出所求的孔径。
流程:叠板销钉→上板→钻孔→下板→检查\修理四、沉铜目的:沉铜是利用化学方法在绝缘孔壁上沉积上一层薄铜。
流程:粗磨→挂板→沉铜自动线→下板→浸%稀H2SO4→加厚铜五、图形转移目的:图形转移是生产菲林上的图像转移到板上蓝油流程:磨板→印第一面→烘干→印第二面→烘干→爆光→冲影→检查干膜流程:磨板→压膜→静置→对位→曝光→静置→冲影→检查六、图形电镀目的:图形电镀是在线路图形裸露的铜皮上或孔壁上电镀一层达到要求厚度的铜层与要求厚度的金镍或锡层。
流程:上板→除油→水洗二次→微蚀→水洗→酸洗→镀铜→水洗→浸酸→镀锡→水洗→下板七、退膜目的:用NaOH溶液退去抗电镀覆盖膜层使非线路铜层裸露出来。
流程:水膜:插架→浸碱→冲洗→擦洗→过机;干膜:放板→过机八、蚀刻目的:蚀刻是利用化学反应法将非线路部位的铜层腐蚀去。
九、绿油目的:绿油是将绿油菲林的图形转移到板上,起到保护线路和阻止焊接零件时线路上锡的作用。
流程:磨板→印感光绿油→锔板→曝光→冲影;磨板→印第一面→烘板→印第二面→烘板十、字符目的:字符是提供的一种便于辩认的标记流程:绿油终锔后→冷却静置→调网→印字符→后锔十一、镀金手指目的:在插头手指上镀上一层要求厚度的镍\金层,使之更具有硬度的耐磨性流程:上板→除油→水洗两次→微蚀→水洗两次→酸洗→镀铜→水洗→镀镍→水洗→镀金镀锡板 (并列的一种工艺)目的:喷锡是在未覆盖阻焊油的裸露铜面上喷上一层铅锡,以保护铜面不蚀氧化,以保证具有良好的焊接性能。
pcb全生产流程

pcb全生产流程PCB生产流程1 开料:我们目前用的板料的大料(sheet)主要有下面公称尺寸:48x36 ,48x40, 48x42INCH,一般最大开料为18X24IHCH。
把sheet切割成多个生产panel即开料。
开料分横、直料,因板料的48INCH方向与其垂直方向(36/40/42)的收缩比率不一样,所以对一张大料(sheet)内开出的panel,对panel长边与48inch边平行的定义为直料(Z),对panel 长边与大料48inch边垂直的定义为横料(H)。
一般情况下,六层及以下板可开横直料板料的利用率:客户成品最大边界的面积总和与大料sheet的比。
基材-------又名覆铜板。
将补强材料浸以树脂,一面或两面覆以铜箔,经热压而成的一种板状材料,称为覆铜箔层压板。
它是做PCB的基本材料,常叫基材。
基材主要由P片,铜箔两者组合而成。
TG测量方法:TMA法----热澎胀分析法DSC法----示差扫描量热法。
DMA法----差热分析法。
. Tg -玻璃态转化温度TG:表示板料保持刚性的最高温度。
但近年来由于电子产品各种性能要求愈来愈高,所以对材料的特性也要求日益严苛。
如抗湿性、抗化性、抗溶剂性、抗热性,尺寸稳定性等都要求改进,以适应更广泛的用途, 而这些性质都与树脂的 Tg 有关。
Tg 提高之后上述各种性质也都自然变好,如 Tg 提高后;a.其耐热性增强,使基板在X 及Y 方向的膨胀减少,使得板子在受热后铜线路与基材之间附着力不致减弱太多,使线路有较好的附着力。
b.在Z 方向的膨胀减小后,使得通孔之孔壁受热后不易被底材所拉断。
c. Tg 增高后,其树脂中架桥之密度必定提高很多,使其有更好的抗水性及防溶剂性。
-使板子受热后不易发生白点或织纹显露,而有更好的强度及介电性.-至于尺寸的安定性,由于自动插装或表面装配之严格要求就更为重要了。
因而近年来如何提高环氧树脂之Tg 是基板材所追求的要务。
- 1、下载文档前请自行甄别文档内容的完整性,平台不提供额外的编辑、内容补充、找答案等附加服务。
- 2、"仅部分预览"的文档,不可在线预览部分如存在完整性等问题,可反馈申请退款(可完整预览的文档不适用该条件!)。
- 3、如文档侵犯您的权益,请联系客服反馈,我们会尽快为您处理(人工客服工作时间:9:00-18:30)。
25
压板——棕化线 压板——棕化线 ——
26
压板——铆合 压板——铆合 ——
铆合:(铆合;预叠) 铆合:(铆合;预叠) :(铆合 目的:(四层板不需铆钉) 目的 利用铆钉将多张内层板钉在一起, 以避免后续加工时产生层间滑移 主要原物料: 主要原物料:铆钉;P/P P/P(PREPREG):由树脂和玻璃纤维 布组成,据玻璃布种类可分为 1060;1080;2116;7628等几种 树脂据交联状况可分为: A阶(完全未固化);B阶(半固化);C 阶(完全固化)三类,生产中使用的 全为B阶状态的P/P
底板
護作用之錫剥除 重要原物料:HNO3+H2O2 兩液型剥錫液
二次銅
53
沉银线
54
金手指
☺金手指(G/F) 金手指( 金手指
♣目的:优越的导电性、抗氧化性、耐磨性 ♣原理:氧化还原 ♣主要原物料:金盐
55
Gold Finger
镀金前
Flow Chart
鍍金前
前处理
镀金
镀金后
后处理
56
沉金线
曝光(EXPOSURE): 曝光(EXPOSURE): 目的: 目的: 经光源作用将原始底片上的图像转 移到感光底板上 主要原物料:底片 主要原物料: 内层所用底片为负片,即白色透光部 分发生光聚合反应, 黑色部分则因 不透光,不发生反应,外层所用底片 刚好与内层相反,底片为正片
UV光 光
曝光前
曝光后
目的: 目的: 将铜箔(Copper)、胶片(Prepreg)与氧化处理后的内层 线路板压合成多层板
24
压板——棕化 压板——棕化 —— 棕化: 棕化: 目的: 目的: (1)粗化铜面,增加与树脂接触表面积 (2)增加铜面对流动树脂之湿润性 (3)使铜面钝化,避免发生不良反应 主要物料:棕花药液 主要物料
18
内层——褪膜 内层——褪膜 ——
褪膜(STRIP): 褪膜(STRIP): 目的: 目的: 利用强碱将保护铜面之抗 蚀层剥掉,露出线路图形
去膜前
主要原物料: 主要原物料:NaOH
去膜后
19
内层——褪膜 内层——褪膜 ——
20
内层检验
流程介绍: 流程介绍:
CCD冲孔
AOI检验
VRS确认
目的: 目的: 对内层生产板进行检查,挑出异常板并进行处理
4
PCB制造流程简介(PA0) PCB制造流程简介(PA0) 制造流程简介
5
内层介绍
裁板 前处理
菲林
压膜
曝光
DES
(显影、蚀 刻、褪膜)
6
内层
☺裁板(BOARD CUT): 裁板(BOARD 裁板 ☺目的: 目的: 目的 按照设计要求,将 基板材料裁切成需要 的尺寸。
7
内层
前处理(PRETREAT): 前处理(PRETREAT): 目的: 目的:
43
乾膜 UV光 底片
曝光机
44
显影
显影(Developing): 目的: 洗掉未发生聚合 反应的区域,已感光部分因 已发生聚合反应洗不掉而留 在铜面上成为蚀刻或电镀的 阻剂膜. 重要原物料:弱堿 (Na2CO3)
乾膜 一次銅
45
显影线
46
二次沉铜
☺ 流程介紹: 流程介紹
二次镀铜 镀锡 剥膜 线路蚀刻 剥锡
57
文字印刷
印一面文字
文字
S/M
烘烤
文字
印另一面文字
58
成型
成型
♣
目的:让板子裁切成客户所需规格尺寸 原理:数位机床机械切割 主要原物料:铣刀
♣
♣
59
CNC Flow Chart 成型前
成型
成型后
60
终检
AOI检验
61
最终流程
终检——包装 包装 终检
♣ ♣
目的:确保出货的品质 流程: A 测试 B 检验 C 包装
38
一次銅
一次沉铜线
39
压膜、曝光、 压膜、曝光、显影
☺ 流程介绍: 流程介绍: 介绍
前处理 压膜 曝光 显影
☺ 目的: 目的: 经过钻孔及通孔电镀后,内外层已经连 通,本制程製作外 层线路,以达电性的完整
40
压膜
压膜(Lamination): 压膜(Lamination): 目的: 目的: 通过热压法使干膜紧密附着在铜面上。
PCB制造流程简介 PCB制造流程简介
远东国际租赁有限公司 工业装备事业部 刘海永 2009年12月26日
1
PCB制造流程简介——工厂 PCB制造流程简介——工厂 制造流程简介——
2
PCB制造流程简介——生产车间 PCB制造流程简介——生产车间 制造流程简介——
3
PCB制造流程简介——准备 PCB制造流程简介——准备 制造流程简介——
乾膜 二次銅
50
镀锡
51
褪膜蚀刻
☺褪膜 褪膜
♣ ♣ 目的:将抗电镀用的干膜用 重要物料:剥膜液(KOH)
二次銅 底板 保護錫層
药水溶化;
☺线路蚀刻: 线路蚀刻: 线路蚀刻
♣ 掉 ♣ 重要物料:蚀刻液(氨水) 目的:将非导体部分的铜蚀刻
保護錫層
二次銅
52
褪锡
☺褪锡: 褪锡: 褪锡
♣ ♣ 目的:將導體部分的起保
内层——压膜 内层——压膜 —— 压膜(LAMINATION): 压膜(LAMINATION): 目的: 目的: 将经处理之基板铜面透过 热压方式贴上抗蚀干膜 主要原物料: 主要原物料: 干膜(Dry Film) 干膜 溶剂
压膜前
压膜后
11
内层——压膜机 内层——压膜机 ——
12
内层——曝光 内层——曝光 ——
☺ 目的: 目的:
♣ ♣ 按客户要求镀铜的厚度; 完成线路
47
二次沉铜
☺ 二次沉铜: 二次沉铜:
♣ 目的:将显影后的裸
铜面厚度加厚,已达到客 户要求。 ♣ 重要物料:铜球
乾膜
二次銅
48
二次沉铜线
49
镀锡
☺ 镀锡: 镀锡:
保護錫層
♣
目的:在镀完的二次铜
表面镀上一层保护锡,作为 蚀刻时的保护剂。 ♣ 重要物料:锡球
垫板
34
钻孔
流程介绍: 流程介绍: 目的: 目的:在板面上钻出层与层之间线路连接的导通孔
35
钻孔
36
成型
☺裁剪成各个单元 裁剪成各个单元
37
一次沉铜
一次铜 一次铜 目的: 目的: 镀上200-500 micro inch的厚度的铜 以保护仅有20-40 micro inch厚度的化学 铜不被后制程破坏造成 孔破。 重要原物料: 重要原物料: 铜球
去除铜面上的污染物,增加铜面 粗糙度,以利于后续的压膜制程 铜箔 绝缘层
主要原物料: 主要原物料:
刷轮 前处理后 铜面状况 示意图
8
内层课——前处理 内层课——前处理 ——
9
内层——图形转移 内层——图形转移 ——
目的: 目的: 利用影像转移原理制作内层线路 DES为显影;蚀刻;去膜连线简称
10
铆钉
2L 3L 4L 5L
2L 3L 4L 5L
27
压板
叠板: 叠板: 目的: 目的: 将预叠合好之板叠成待压 多层板形式 主要原物料: 主要原物料:铜皮 电镀铜皮;按厚度可分为 1/3OZ(代号T) 1/2OZ(代号H) 1OZ(代号1) RCC(覆树脂铜皮)等
Layer 1 Layer 2 Layer 3 Layer 4 Layer 5 Layer 6
13
内层——曝光机 内层——曝光机 ——
14
内层——显影 内层——显影 ——
显影(DEVELOPING): 显影(DEVELOPING): 目的: 目的: 用碱液作用将未发生化学反 应之干膜部分冲掉 主要原物料: 主要原物料:Na2CO3 使用将未发生聚合反应之干 膜冲掉,而发生聚合反应之 干膜则保留在板面上作为蚀 刻时之抗蚀保护层
重要物料: 重要物料: 乾膜(Dry 乾膜(Dry film) 溶剂显像型 半水溶液显像型 硷水溶液显像型
41
压膜机
42
曝光
曝光(Exposure): 曝光 目的: 通过 image transfer技术在 干膜上曝出客户所需的线路。 重要物料: 底片 外层所用底片与内层相反,为 负片(白底黑线) 白色的部分紫外光透射过去, 干膜发生聚合反应,不能被显影液 洗掉
显影前
显影后
15
内层——显影 内层——显影 ——
16
内层——蚀刻 内层——蚀刻 ——
蚀刻(ETCHING): 蚀刻(ETCHING): 目的: 目的: 利用药液将显影后露出的 铜蚀掉, 铜蚀掉,形成内层线路图 形 主要原物料: 主要原物料:蚀刻药液 (CuCl2)
蚀刻前
蚀刻后
17
内层——蚀刻线 内层——蚀刻线 ——
28
压板
压合: 压合: 目的: 目的:通过热压方式将叠合板压成多层板 主要原物料: 主要原物料:牛皮纸;钢板
热板
压力 钢板 牛皮纸 承载盘
可叠很多层
29
压板——冷压 压板——冷压 ——
30
压板——热压 压板——热压 ——
31
压板
后处理: 后处理: 目的: 目的: 经割剖;打靶;捞边;磨边等工序,对压合的多层板进行初步 外形处理。 主要原物料:钻头;铣刀 主要原物料
32
钻孔
☺ 流程介绍 流程介绍
钻孔 去毛头 (Deburr) 去胶渣 (Desmear) 化学铜 (PTH) 一次铜 Panel plating
☺ 一次铜目的: 一次铜目的: 目的 使孔璧上的非导体部分的树脂及玻璃纤维进行金属 化,以方便进行后面的电镀铜制程,形成导电及焊接的金 属孔璧