生产过程质量审核记录表
过程质量审核表-全过程
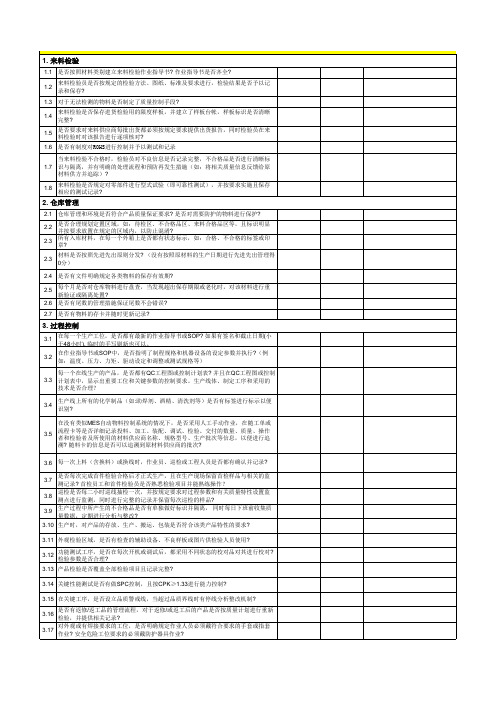
3.20 出货之前,是否通过筛选、老化和抽样加速试验来确保产品可靠性?
3.21
是否有文件规定对成品进行型式试验(或可靠性)管理程序,对产品性能测试计划 、频次、项目、设备等作出规定并实施? 试验项目是否齐全且试验方案合理?
3.22 是否全面模拟产品的使用环境进行破坏性试验或寿命测试,并保留试验记录?
3.23 对模具、夹具、工装是否有变更履历、使用寿命管理台帐等信息?
3.24
对设备是否采取三级保养制度(如:日、月度/季度或年度保养),且对每类设备明 确定义预防保养的项目且保留保养记录?
3.25 订单是否能明确区分不同的生产要求?(如:RoHS和非RoHS、内销和外销等)
3.26 生产线的在线检测工序是否制定了措施可以保证所有产品都检测并不会被重复检测?
材料供方并追踪)?
1.8
来料检验是否规定对零部件进行型式试验(即可靠性测试),并按要求实施且保存 相应的测试记录?
2. 仓库管理
2.1 仓库管理和环境是否符合产品质量保证要求? 是否对需要防护的物料进行保护?
2.2
是否合理规划定置区域,如:待检区、不合格品区、来料合格品区等,且标识明显 并按要求放置在规定的区域内,以防止混淆?
4.3 包装的产品是否统一朝同一方向并排列整齐,如:产品标示码统一向一个方向?
4.4 产品放入包装盒/箱内时,是否有保护措施避免产品变形、破损和产品表面氧化? 4.5 在每一个包装盒上,是否都有贴环保标贴或盖环保标示印章? 4.6 入库产品是否对存放环境(温湿度)、堆放高度有明确规定并满足该要求? 4.7 在每一个包装盒上是否都有合格章? 变更前后的标识是否有明显的区别? 4.8 是否有制度规定出货前对物料进行检验,检验项目和抽样数量是否合理?
过程审核检查表范例
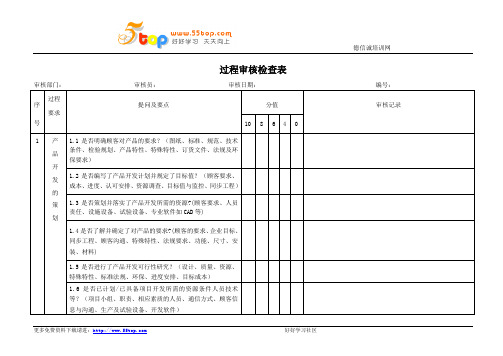
德信诚培训网过程审核检查表审核部门:审核员:审核日期:编号:序号过程要求提问及要点分值审核记录10 8 6 4 01 产品开发的策划1.1是否明确顾客对产品的要求?(图纸、标准、规范、技术条件、检验规划、产品特性、特殊特性、订货文件、法规及环保要求)1.2是否编写了产品开发计划并规定了目标值?(顾客要求、成本、进度、认可安排、资源调查、目标值与监控、同步工程)1.3是否策划并落实了产品开发所需的资源?(顾客要求、人员责任、设施设备、试验设备、专业软件如CAD等)1.4是否了解并确定了对产品的要求?(顾客的要求、企业目标、同步工程、顾客沟通、特殊特性、法规要求、功能、尺寸、安装、材料)1.5是否进行了产品开发可行性研究?(设计、质量、资源、特殊特性、标准法规、环保、进度安排、目标成本)1.6是否已计划/已具备项目开发所需的资源条件人员技术等?(项目小组、职责、相应素质的人员、通信方式、顾客信息与沟通、生产及试验设备、开发软件)德信诚培训网过程审核检查表(IATF16949-2016)审核部门:审核员:审核日期:编号:序号过程要求提问及要点分值审核记录10 8 6 4 02 产品开发落实2.1是否进行了DFMEA的分析,并确定了改进措施?(顾客要求、产品建议书、功能、安全性、可靠性、易维修性、主要特性、环保要求、试验结果、DFMEA及改进的特定设施)2.2项目运作过程中是否对DFMEA进行了补充更新?已确定的措施是否已经落实?(顾客要求、重要参数、特性法规要求、功能尺寸、材料、环保要求、运输、FMEA措施)2.3是否制定了质量控制计划?(标出的重要特性,检验及试验流程、配置的设备、测量技术、验收标准)2.4是否具有各阶段所要求的认可合格证明?(产品试验如整机试验、功能试验、寿命试验、样件状态、小批样件、计量器具)2.5、是否已具备所要求的产品开发能力?(顾客要求、人员素质、设备、样件、模具、试验/检验/实验室)3 过 3.1是否了解并明确对产品的要求?(顾客要求、法规要求、物流方程开发的策划案、技术供货条件、质量协议、重要特性、环保要求)3.2是否编制了过程开发计划并确定了目标值?(顾客要求、目标成本、进度安排、样件/试生产/批量生产、资源调查及配置、更改方案、合格供方、目标监控)3.3是否已策划并落实了批量生产的资源?(顾客要求、原材料清单及供方名录、人员责任、班产能力、设施/设备/工装/模具/试验设备、运输工具、周转箱、仓库)3.4是否了解并考虑到了对生产过程的要求?(顾客要求、法规要求、能力验证、设备及试验设备的适应性、生产布局、搬运包装、贮存、标识)3.5是否已计划/已具备项目开发所需的人员与技术条件?(项目领导小组/职责、人员素质、设备能力、顾客沟通、CP\APQP\FMEA)3.6是否开展了PFMEA并确定了改进措施?(过程风险如工序、供方、顾客要求、功能、重要参数、可追溯性、环保要求、运输)德信诚培训网过程审核检查表审核部门:审核员:审核日期:编号:序号过程要求提问及要点分值审核记录10 8 6 4 04 过程开发的落实4.1项目运作过程是否对PFMEA进行了补充更新?已确定的措施是否落实?(顾客要求、工序/供方、重要特性、法规要求、安装尺寸、材料、可追溯性、PFMEA措施)4.2是否制定了质量计划?(包括:产品组件、部件、零件和材料及生产过程中的检验流程、设备、测量技术、验收标准)4.3是否具有各阶段所要求的认可/合格证明?(产品试验报告、样件、首批样品、产品特性/过程特性证明、设备等)4.4批量生产前是否进行了试生产?(试生产批量、过程能力调查、样品检测、人员素质、指导书、生产布局)4.5生产文件和检验文件是否齐全?(过程参数、检验规范包括:频次、方法、记录、反应计划,现场易于得到)4.6是否已具备所要求的批量生产能力?(合格供方、材料清单、人员素质、设备运行效率、单台产量、设备能力、运输工具、周转箱等)5 生产过程5.1供方/原材料5.1.1是否仅允许已认可的供方供货?(合格供方名录、认证证书、营业执照、实物质量评定)5.1.2能否确保供方所供产品达成协议要求?(供方协议、试验记录、检验方法、频次、缺陷分析、能力验证)5.1.3是否对供方实物质量进行了评价?有偏差时是否采取了纠正措施?(质量会议纪要、改进计划的商定与跟踪,改进后的质量验证、供方的分析评定记录)5.1.4是否与供方新产品与过程的持续改进商定了质量目标并实施?(项目小组、质量目标、减少废品、提高满意度、质量/价格/服务目标)5.1.5批量供货的产品是否得到了批量生产认可?(样件认可、首批报告、可靠性研究、鉴定线路)5.1.6对顾客提供的产品,是否严格按与顾客商定的方法进行管理?(质量文件、控制/验证/贮存/运输/包装要求)5 生产过程5.1.7原材料库存量,库存状态是否适合于生产要求?(看板/准时化生产、贮存成本、应急计划、先进先出)5.1.8对原材料/剩余料的入库和贮存是否进行了适当控制?(包装、标识、先进先出、秩序与清洁、贮存条件如:防损伤/污染/混批/混料)5.1.9员工是否得到相应培训?(产品/规范/顾客要求/。
2016版VDA6.3过程审核检查表
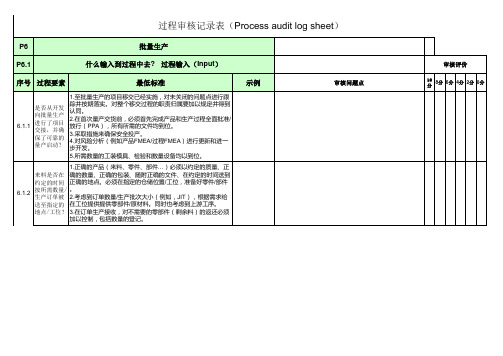
是否对原材 污染。仓储区/加工区/容器必须达到零部件/产品所需的必要的
料进行适当 整洁/清洁要求。要定义清洁周期,并且加以监控。
的仓储,所 3.加工工位/装配线上的零部件/物料的供应必须便与安全操作
6.1.3
使用的运输 。 工具/包装设 4.必须通过合适的方法,监控为特殊材料/零部件规定的仓储时
备是否适合 间以及使用有效期(最长、最短仓储时间,规定的中间临时仓
量要求? 性有影响的测量装置的校准。
4.对于影响到测量结果合试验的附属装置,要采取同样的方式
加以监控。
加工工位和
6.4.4
检验工位是 否满足具体
要求?
1.加工工位及周边布置的条件环境适合于生产操作和产品的要 求,从而可以预防或避免污染、损伤、混料。 2.这也适用于临时的和永久的返工返修、拣选、检验工位。 3.除此以外,还根据具体的工作任务,在人机工程学的基础上 对加工工位设计进行了调整。
P6.2
工作内容/过程流程(所有生产过程是否受控?)
控制计划里 的要求是否 6.2.1* 完整,并且 得到有效实 施?
1.基于控制计划的生产和检验文件完备。其中必须对检验文件 、检验设备、检验方法、检验频度/周期、重新评定等加以规 定。 2.这些文件必须随时可获取。 3.对于影响到产品特性/质量的过程参数必须加以完整地描述。 过程参数和检验特性必须带有公差。 4.在过程控制图上规定控制限,控制限可探测、可追溯。 5.针对过程要求和检验特性,要对发现的不符合项以及启动的 措施加以记录。 6.对过程异常所要采取的措施(反应计划),相关责任人必须 清楚,实施措施并加以记录。 7.如产品对生产工艺有特殊要求,那么相关的机器/工装/辅助 设备的参数数据要在控制计划和/或生产检验文件中加以规定 。 8.详细规定返工条件,并且在过程中加以保障(零部件标识, 重新检验)
制造过程审核检查表
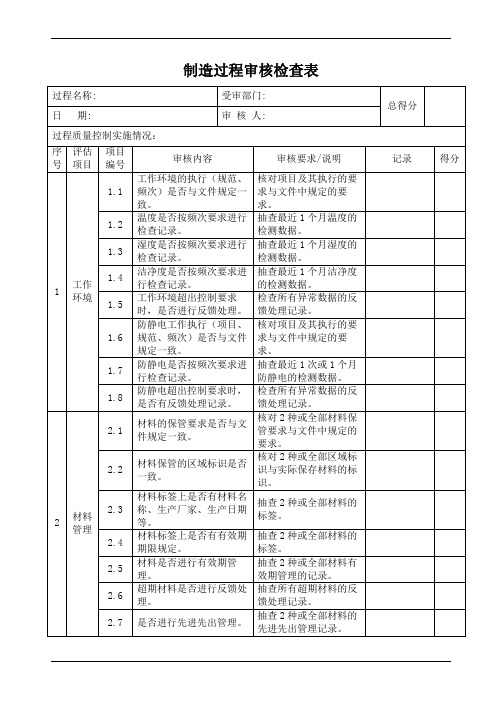
设备状态标识是否正确。
核对3台设备的状态标识。
4.4
是否制定年度PM工作计划。
检查年度PM工作计划。
4.5
是否按照年度PM工作计划实施。
抽查3个项目确认实施情况。
4.6
关键设备的备件是否进行可得性分析。
抽查最近2个月设备可得性分析记录表。
4.7
是否对关键设备的停机原因进行分析并改善。
抽查最近2个月关键设备故障停机原因分析及改善记录表。
4.8
设备故障维修后是否进行记录。
抽查最近2个月设备维修的记录。
4.9
设备维修后是否进行QC验证。
抽查最近2个月设备维修后的QC记录。
5
工装管理
5.1
是否有工装保管台账。
检查工装保管台账。
5.2
是否按工装文件的规定进行管理。
抽查2个工装核对其实施情况与文件规定的要求。
6
量测管理
6.1
是否有量测设备的管理台账。
检查没有达成质量目标的分析改进措施。
7.13
Cpk、Ppk是否满足要求。
检查工序的过程能力分析指数Cpk、Ppk值。
7.14
过程能力(Cpk、Ppk)不满足要求时,是否进行分析改进。
检查过程能力分析改进的相关措施。
7.15
关键参数是否按要求进行SPC管控。
检查要求SPC管控的管控图。
7.16
超出规范限或控制限后是否进行处置。
核对5项CP文件与作业指导书的内容。
7.3
设备中的工艺参数是否与文件中的规定一致。
抽查3台设备核对当前程序的工艺参数与文件规定的要求。
7.4
记录表中监控要求是否与作业指导书要求一致。
过程审核检查表-ok

过程能力/目标
与过程有关的质量目标是否达到?
抽××件产品进行检测,查其合格率是否符合规定要求(如目标要求)?
查看现场的SPC控制图,判断过程是否受控?
与特殊特性有关的过程是否进行了过程能力研究?
收集数据,计算过程能力指数?结果是否符合要求?
FR820203 B/0
控制计划中有无产品和过程特殊特性的控制要求?是否执行?
控制计划中的反应计划是否得到实施?
综合评价控制计划的可行性与正确性?
2/1
过程/人的因素
是否持证上岗?有无经验?技能如何?
上岗前是否接受过上个岗培训?有无过程质量控制的知识?
是否熟悉本岗位的作业文件并能掌握其要求?
是否能认真执行作业文件的规定?
作业效率高低如何?
员工是否熟悉并执行包装规范,是否明确包装要求?
产品包装质量是否符合要求,是否进行了检查?
2
交付
是否确定了与顾客保持联络的顾客代表?
交付时产品是否满足了所有顾客要求?
产品出库是否符合程序或文件规定,手续是否齐全?
交付是否按合同要求进行,是否满足100%准时?
在交付至目的地期间,是否对产品进行了防护?
3
材料在仓库和车间现场是否进行了适当防护?
是否对顾客财产按要求进行了接收、贮存、使用、异常报告?
FR820203 B/0
过程审核检查表
No
品名规格
审核过程
交付/服务
审核员
审核日期
序号
审核
项目
审核内容
审核情况记录(分)
备注
10
7
4
0
nb
1
终检
包装
对最终产品是否进行了验证(检验和试验),是否符合顾客或订单要求?
过程审核检查及记录表
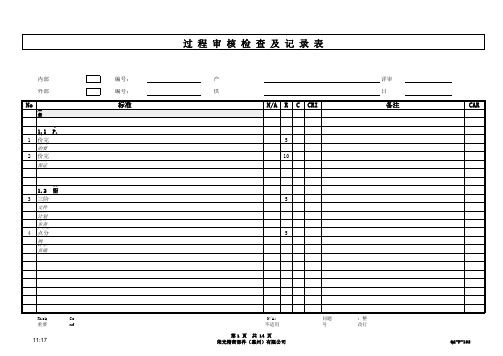
内部评审: 外部评审:
编号: 编号:
产品: 供应商:
评审人: 日期:
No
第一章 QAP.p
评审标准
N/A
R
C
CRI
备注
CAR
1 2
1.1 QAP.p 有一份完整的强制性要求文件提供吗?
有关的要求文件必须提供,并要求随时更新;
5 10
有一份完整的质量保证文件提供吗?
标识:零件号、更改等级、标记、可见性、可读性,等等; 可追踪性:产品由来源到终点存在联系
46 在生产工位和传送过程中无破损风险?
包装和装卸设备,周转库存区,等
5 5
47 生产计划与荣光公司交货要求(每日送货需求量)一致? 紧急批次有标识吗?
R: Risk重要性C: Conformity合格程度 (0 = 好; 4 =通过; 7 =不足; 10 =没有)
评审标准
Chap. 2 sub-total carried over:
N/A
R
C
CRI
备注
CAR
16 对于进货产品有评审程序吗?
对于有关的产品进行PQA评审。有一份评审时间安排吗?
5 5
17 对于每一类零件,是否进行包括更改等级的PQA归档吗 (手工样件,试装零件)? 2.1.4 标识与可追溯性 18 对于物料批次和具有受控特性、关键特性、安全/法规特性的零部件, 有标识和可追溯性吗? 19 分有如下质量状态吗?:待决定、接受、拒收、例外接受、返工等等?
评审标准
N/A
R
C
CRI
备注
CAR
8 9
2.1 采购及进货检验 采购订单上有特定的要求吗?
过程审核记录表模板

研发 生产管理部
产品 对各个项目阶段,已按要求具有了必要的能力证明以及认可批准。详见《项目小组成员名单》。
过程 对各个项目阶段,已按要求具有了必要的能力证明以及认可批准。详见《项目小组成员名单》。
产品
对各个阶段应用了生产控制计划,并在生产控制计划的基础上编制了具体的生产和检验文件。例如试生产 、批产阶段均应用了控制计划。
提问
3.5
是否确保了采购件质量符合要求?已供货的批量产品是 否得到所要求的认可,并落实了所要求的改进措施
被审部门 采购部
适用 过程 模具开发协议、质量协议。
薄弱环节/建议措施及审核发现
得分 2 4 6 8 10
10
是否启动应 急措施?
是否启动应 急措施?
No.
提问
被审部门
适用
薄弱环节/建议措施及审核发现
4.9
为确保正式投产,是否对项目移交至生产开展了控制管 理?
生产管理部 过程 对项目移交进行移交评审接收。
10
是否启动应 急措施?
No.
提问
5.1
是否只和获得批准/放行且具备质量能力的供应商开展 合作?
5.2 在供应链中是否考虑到了客户要求?
5.3
是否与供应商就供货绩效约定了目标,并且加以了落 实?
产品 已落实。详见《APQP进度表》。
过程 已落实。详见《APQP进度表》。
得分 2 4 6 8 10
10 10 10 10
研发
产品 人员已到位并进行培训
10
4.3 人力资源是否到位并且具备资质?
生产管理部 过程 对新进员工已进行岗位技能培训。见培训记录、《生产员工技能矩阵表》
10
研发
产品 基础设施到位并且适用。详见《设备、工装、监视和测量设备清单》。
VDA6.3过程审核检查表(带示例_自动计算符合率)

一些重点工序的质控点没有对不良品运用统计 技术分析(P图或nP图)
X
M6.4.3 Are the causes of product and process nonconformities analyzed and the corrective actions rel checked for their effectiveness? 在与产品要求/过程要求有偏差时,是否分析原因 并检 查纠正措施的有效性?
过程审核检查
NO: 版次: 修订号: 表格编号:
审核报告编号(Audit Report Nbr.)2005-001 审核日期(Audit-Date): 6/1~6/2
Process Step 2
描述(Description): 压铸过程 1 操作工不明白产品质量/过程质量的要求。 2 作业指导书要求对首件产品确认品质 实际没有检查记录(P图)
X
M6.2.2 Can the quality requirements be monitored
effectively during serial production with the rel implemented inspection measuring and test equipment?在批量生产中使 用的检测.试验设备 是否能有效地监控质量要求?
0 4 6 8 10 0 4 6 8 10
负责生产设备/生产环境的职责和权限。 负责生产设备的维修和保养职责。
X
M6.1.3 Are the employees suitable to perform the
required tasks and is their qualification rel maintained? 员工是否适合于完成所交付的任务并保持其素质?
VDA 过程审核检查表及打分表—

日期:发现/背离等级生产 (工序 2 - 10)退火6.1.人员/素质6.1.1.是否对员工委以监控产品质量/过程质量的职责和权限?10查:明确授予了操作人员、车间主任的质量职责及质量管理员的过程监控职责6.1.2.是否对员工委以负责生产设备/生产环境的职责和权限?10查:球化退火炉,设备编号完好,标识牌上明确责任人为卜科平6.1.3.员工是否适合于完成所交付的任务并保持其素质?8查:现场记录与作业指导书相符6.1.4.是否有包括顶岗规定的人员配置计划?8查:有员工技能矩阵图及人员能力评价记录6.1.5.是否有效地使用了提高员工工作积极性的方法?10查:有员工奖罚制度,行政部能提供奖励及处罚记录。
6.2.生产设备/工装6.2.1.生产设备/工装模具是否能保证满足产品特定的质量要求?10查:能提供设备保养规程、保养计划、保养记录、维修记录;查:能提供工装管理规定、保养记录、精度检查记录。
关注易损零件/易损部位的定期更新记录。
查:能提供设备履历、工装履历等。
查:能提供工装验收记录并与工装设计文件比较。
包括易损件/部位的更换/维修周期的规定及实施。
6.2.2.在批量生产中使用的检测,试验设备是否能有效地监控质量要求?10查:提供《2017年检测设备外校检定证书台账》、《2017年计量器具外校检定计划》、《计量器具内校计划》及校准台账查:现场使用是千分尺,编号:45186,合格证上的校准日期为:2017/5/19,有效期为2018/5/18;6.2.3.生产工位,检验工位是否符合要求?8查:根据生产流程制定生产、检验工位,符合要求6.2.4.生产文件与检验文件中是否标出所有的重要技术要求,并坚持执行?10查:09118-08015《控制计划》与《作业指导书》该工序,没有特殊特性要求。
6.2.5.对产品调整/更换是否有必备的辅助器具?8查:配备有相关的辅助器具,如提升机等6.2.6.是否进行批量生产起始认可,并记录调整参数或偏差情况?10查:35K退火工艺记录参数符合《作业指导书》规定6.2.7.是否按时落实要求的纠正措施并检查其有效性?10查:质量目标未达标,每天在QRQC会议通报,并进行原因分析、制定改进措施,在后续会议中汇报实施结果日期:日期:日期:日期:6.1.1.是否对员工委以监控产品质量/过程质量的职责和权限?查:明确授予了操作人员、车间主任的质量职责及质量管理员的过程监控职责6.1.2.是否对员工委以负责生产设备/生产环境的职责和权限?查:设备标识是完好、正确有效,明确了设备责任人6.1.3.员工是否适合于完成所交付的任务并保持其素质?查:员工对本岗位作业指导书能理解和执行(首件记录、设备点检、工装服役档案等),符合。
过程审核检查记录表
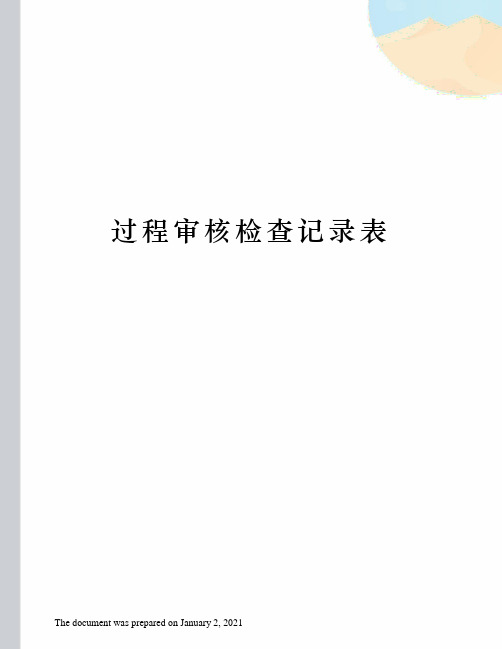
-仓库管理系统
-FIFO 先进先出 / 按照批次投入使用
-有序和清洁
-气候条件
-防损防污防锈
-标识可追溯性/ 检验状态/ 加工工序/ 使用状态
-确保防止混放和混用
-隔离库设置并使用
1.9员工素质是否满足了相应的岗位要求
- 产品/技术规范/特殊的顾客要求
-模块中的零部件的产品特性和加工过程的专业知识
- 工装模具/设备/机器的保养和维修状态包括有计划的维修
2.2.2在批量生产中使用的测量和检验设备能否有效地监控质量要求-可靠性试验、功能试验和耐腐蚀试验
-测量精度/检测设备能力
-数据采集和可评价性
-检测设备的校准证明
2.2.3生产工位和检验工位是否符合要求
-人机工程学
-照明
-有序清洁
-环境保护
-工作环境/零件搬运
-数据采集和可评价性
-检测设备的校准证明
2.2.3生产工位和检验工位是否符合要求
-人机工程学
-照明
-有序清洁
-环境保护
-工作环境/零件搬运
-安全生产
2.2.4在生产文件和检验文件中是否标出全部的重要事项并得到遵守
- 过程参数如压力、温度、时间、速度
-机器/工装模具/辅助器具的数据
-检验规范重要的特性、检验器具、方法、检验频次
-安全生产
2.2.4在生产文件和检验文件中是否标出全部的重要事项并得到遵守
- 过程参数如压力、温度、时间、速度
-机器/工装模具/辅助器具的数据
-检验规范重要的特性、检验器具、方法、检验频次
-过程控制图中的控制限
-机器能力和过程能力的证明
-设备操作指导
-作业指导书
IATF16949--过程审核检查表-(含审核记录)-
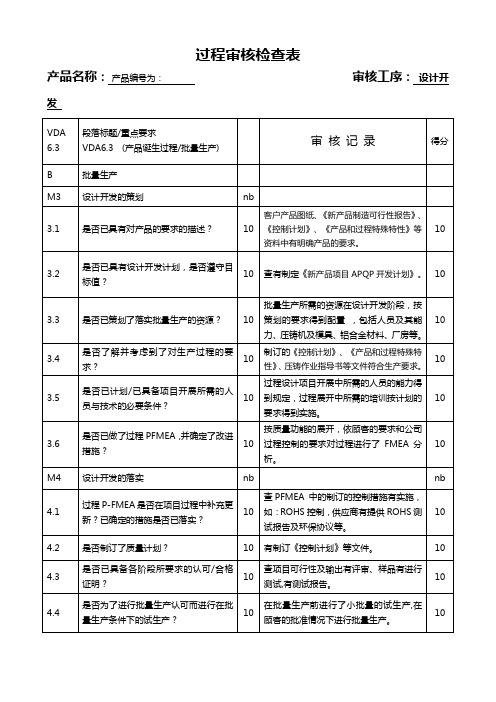
生产数量按下达的生产计划进行,能满足顾客要求,对车间的产品流向策划了流程图,确保产品有序运往下道工序。
10
6.3.2
产品/零件是否按要求贮存?运输器具/包装方法是否按产品/零件的特性而定?
10
产品现场无堆积,摆放整齐。用纸箱包装。
10
6.3.3
废品、返修件和调整件以及车间内的剩余料是否坚持分别贮存与并标识?
10
查岗位说明书中有明确员工、品管人员的职责和权限。询问品管负责人何平生,清楚自己的职责。
10
6.1.2
是否对员工委以负责生产设备/生产环境的职责和权限?
10
询问压铸员工邹、贾,明确生产设备的操作和现场5S工作要求。
10
6.1.3
员工是否适合于完成所交付的任务并保持其素质?
10
查压铸机作业员工邹、贾,明确生产及产品品质要求。
10
有制定了成品合格率、生产计划及时完成率、过程CPK等目标,目标达标。
10
过程审核检查表
产品名称:产品编号为:审核工序:包装入库
VDA
6.3
段落标题/重点要求
VDA6.3 (产品诞生过程/批量生产)
审 核 记 录
得分
M6
生产
6.1
人员/素质
nb
6.1.1
是否对员工委以监控产品质量/过程质量的职责和权限?
10
查员工职务说明书中有明确员工的职责和权限。
10
6.1.2
是否对员工委以负责生产设备/生产环境的职责和权限?
10
询问包装工吴学文清楚相关要求。
10
6.1.3
员工是否适合于完成所交付的任务并保持其素质?
10
询问包装工吴,明确生产要求。
质量管理体系内审检查及记录表(范本)

4.1
质量管理体系总要求
1)质量管理体系的结构和层次是否清楚?
2)过程是否识别并表述?
3)是否存在和明确对产品质量有影响的外包过程?如何控制?
4)过程的顺序及相互关系是否明确?
5)有那些控制准则和方法?
6)如何保证体系运作所需的资源?
7)信息是否充分?
7.5.4
顾客财产是否在合同中明确是否包括知识财产
当顾客财产出现损坏或不适用时是否记录并报告客户
7.5.1
是否按规定向顾客提供了服务包括各种配件服务及执行国家“三包”的规定
8.2.1
对顾客满意与否的信息收集规定了哪些渠道执行情况如何
对客户投诉如何处理了解对顾客投诉处理情况及处理结果是否满意
8.5.2
质量方针的适应性是否规定定期或不定期的评审和修订?
5.4.1
质量目标
1)质量目标是否制定并发布?
2)质量目标是否分解和落实?分解是否适宜并得到评审?
3)质量目标是否量化并可测量?
4)质量目标是否与质量方针保持一致?
5)质量是否满足产品要求所需的内容?
质量目标的实现情况如何是否实现了持续改进?
5.4.2
参与评审的部门是否包括被评审设计/开发阶段有关的职能部门的代表
评审的结果和之后的跟进措施是否有记录
7.5.3
是否进行设计/开发验证确保满足设计/开发输入要求,如何验证
7.3.5
验证的结果及之后的跟进措施是否有记录
7.3.6
是否对设计和开发进行确认是否在产品交付或实施之前完成
确认结果及必要措施的记录是否保持
纠正和预防措施开展情况及有效性
注:合格在评价栏打“√”,不合格在评价栏打“╳”,观察项作“△”。
过程审核检查表-VDA6.3

号
过程
要求
提问及要点
分值
审核记录
10
8
6
4
0
P4
产
品
和
过
程
开
发
的
实
现
P4.4是否获得了针对产品和过程开发所要求的批准和放行?
如:物料数据是否已确认并放行?
FMEA中的风险措施已实施,其有效性得到确认?
量产放行前是否有PPAP?
是否在顾客SOP前落实产品和过程的验证与确认?
P4.5是否已制定并落实产品与过程开发的制造和检验规范?
是否有考虑订单数量/生产批次大小,从而确保提供的零部件/材料能够满足相应工位的需求??
在订单生产完成后,是否有将剩余物料返还?
6.1.3是否对来料进行了适当的存储,所使用的运输工具/包装设备是否适合来料的特殊特性?
如:在各阶段是否执行包装规范的要求?
是否提供合适的运输工具,以免运输过程中的产品受损或被污染?
仓储区/加工工位/周转盘是否规定清洁周期,其清洁度是否满足要求?
审核产品:审核部门:PDT小组(研发/工程主导)审核员:陪审员:审核日期:
序号
过程
要求
提问及要点
分值
审核记录
10
8
6
4
0
P6
过
程
分
析
/
生
产
P6.1
过程
输入
是否有合适的方法,监控特殊材料/零部件规定的仓储时间以及使用有效期?
对于零部件/来料/关键生产资料及辅料,是否采限措施,防止受到环境/气候的影响?
6.1.5是否对量产过程中的产品或者过程变更开展了跟踪和记录?
如:是否建立了变更流程?
过程审核检查表
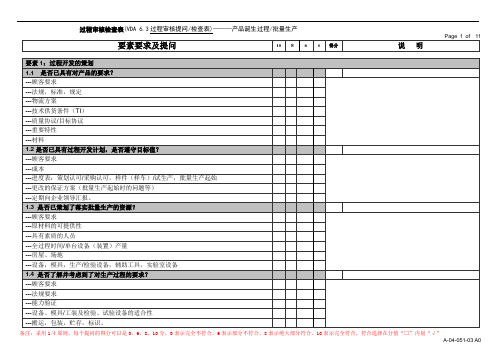
----需考虑要点,如:质量协议、发货审核、耐久试验(调查失效状况)、贮存/下单加工/零件准备/发货、功能检验、检验/测量设备的合格状态、商定的检验、测试方法、产品规范的现时性。
5.2是否保证了对顾客的服务?
----需考虑要点,如:顾客访问的纪要,必要时根据纪要制订相应的措施、产品使用的知识、落实新的要求、关于改进措施的通知、关于产品更改/过程更改/移地生产(包括供方)的通知、首批样品送检/重新送样(试制样品/批产样品)、关于偏离要求的信息。
—成本优化
—减少浪费(例如:废品和返修)
—降低库存量。
4.4.6对产品和过程是否有确定的目标值,并监控是否达到目标?
---需考虑要点,如:人员的出勤率、缺勤率、已生产数量、质量数据(例如:缺陷率,审核结果)、流转时间、缺陷成本(不符合性)、过程特性值(例如:过程能力指数)。
要素5:服务/顾客满意程度
—准时化生产
—先进先出
—仓库管理
—更改状态
—向下道工序只供合格件
—数量记录/统计
—信息流
4.3.2产品/零件是否按要求贮存?运输器具/包装方法是否按产品/零件的特性?
—贮存量
—防损伤
—零件定置
—整齐,清洁,不超装(库存场地,周转箱)
—控制贮存时间
—环境影响
4.3.3废品、返修件和调整件以及车间内的剩余料是否坚持分别贮存并标识?
---需考虑要点,例如:补充的材料检验、功能检验及耐及检验、因果图、FMEA/缺陷分析、过程能力分析、质量小组活动、8D方法。
4.4.4对过程和产品是否定期进行审核?
---审核时机,如:新项目/新过程/新产品、未满足质量要求(内部/外部)、验证是否遵守质量要求、指出改进的潜能。
过程审核检查表_2
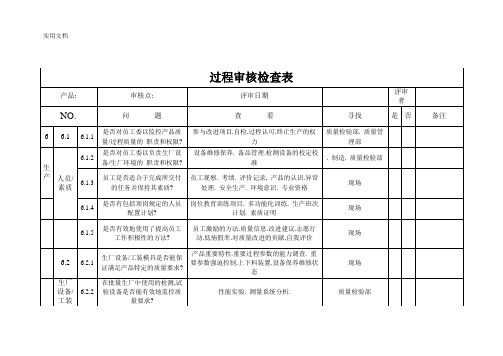
生产部
D2.3
是否根据评定的结果(实物质量问题或质量能力不足)与供方一起制定提高措施并落实?
与问题供方领导的会谈.改进计划的落实.改进的服务过程.审核结果
生产部
D2.4
是否与供方协商确定改进过程和外委服务的目标/措施并加以落实?
持续改进.确定可度量的目标值.成本优化
顾客满意度调查
质量管理部
服务
D3.2.2
是否对纠正措施的落实情况及其有效性进行审查?
顾客.内部抱怨.再发防止措施报告.结果验证.内审,管审
质量检验部
D3.2.3
是否能保证满足对过程的特殊质量要求?
设备维护.照明,人机工程学
生产部.
D3.2.4
是否对服务过程的有效性进行监控?
顾客满意度调查
质量管理部
D3.2.5
原始记录.控制图.数据收集.过程参数的记录装置(时间.温度等).停机.参数更改
项目公司.质量检验部
缺陷分析/纠正措施/持续改进(KVP)
6.4.2
是否用统计技术分析质量数据/过程数据,并由此制定改进措施?
过程能力.缺陷.过程参数.废品.返修件.隔离通知返修.生产节拍.可靠性失效特征(SPC.排列图.因果图)
项目公司.质量检验部.
D3.1.3
在服务过程中使用的员工是否有能力完成所交给的任务?是否对其素质进行定期的监控?
安全环保.质量意识.员工满意度.培训措施
生产部
D3.1.4
是否调查并能保证满足人员需求?是否有足够的顶岗人员?
人员需求调查.费用核算.重要岗位代理制度
生产部
D3.2
D3.2.1
是否对服务进行认可?是否调查并记录其与要求之间的偏差?
过程审核检查表--示例

2.3.5工装模具、设备和检测设备是否合适地存放?
考虑要点:防损伤的存放;有序清洁;定置存放区;有管理的发放;环境影响;标识;明确的认可状态和更改状态;
此工序配置的所有工装、设备及量具要求操作者保持其清洁状态,确保其使用,并执行
考虑要点:足够的、合适的运输器具;定置库位;最小的/无中间库存;看板(KANBAN);JIT;先进先出(FIFO);仓库管理;更改状态;向下道工序只供给合格件;产量记录分析;信息流;
在生产过程中,规定由下工序的作业人员向本工序进行适时领用,一次性领用量不超过XX箱,保证各工序间的物流均衡流动。
2.3.2产品/零件是否按要求存放,运输器具/包装设备是否与产品/零件的特点相适应?
过程审核检查表
审核日期:年月日~年月日审核员:
检查项目
检查要点
客观论据记录
评分
10
8
6
4
0
3顾客关怀/顾客满意度(服务)
3.1是否满足顾客对质量管理体系、产品和过程的要求?
考虑要点:质量管理体系按照ISO/TS16949:2002标准;质量协议;针对零缺陷要求的目标协议;交付审核;耐久试验(调查失效模式);功能检验;
公司建立了相应的程序文件及应急计划程序,对于突出事件能及时做出反映,特殊是当顾客出现抱怨时的及时处理。
8
3.4与质量要求有偏差时,是否进行了缺陷分析并实施了改进措施?
考虑要点:分析的可能性(实验室、检验和试验设施、人员);;实验室符合ISO/IEC17025的要求;针对缺陷特性进行排列图-分析(内部/外部)各有关部门的介入(内部/外部);运用解决问题的方法(如8D-报告);
生产过程质量控制检查记录表1
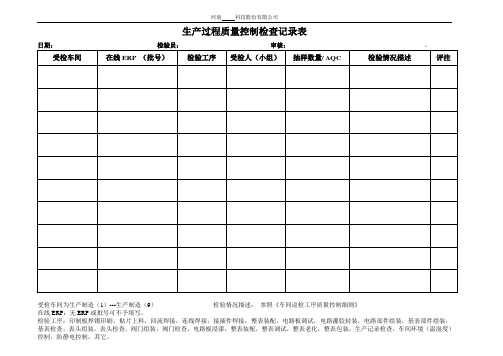
河南科技股份有限公司
生产过程质量控制检查记录表
日期:检验员:审核:。
受检车间为生产制造(1)---生产制造(9)检验情况描述:参照《车间巡检工序质量控制细则》
在线ERP:无ERP或批号可不予填写。
检验工序:印制板焊锡印刷,贴片上料,回流焊接,连线焊接,接插件焊接,整表装配,电路板调试,电路灌胶封装,电路部件组装,基表部件组装,基表检查,表头组装,表头检查,阀门组装,阀门检查,电路板浸漆,整表装配,整表调试,整表老化,整表包装,生产记录检查,车间环境(温湿度)控制。
防静电控制,其它。
- 1、下载文档前请自行甄别文档内容的完整性,平台不提供额外的编辑、内容补充、找答案等附加服务。
- 2、"仅部分预览"的文档,不可在线预览部分如存在完整性等问题,可反馈申请退款(可完整预览的文档不适用该条件!)。
- 3、如文档侵犯您的权益,请联系客服反馈,我们会尽快为您处理(人工客服工作时间:9:00-18:30)。
需考虑要点,例如:
-- 补充的尺寸检验、材料检验、功能检验及耐久检验
-- 因果图
-- FMEA/缺陷分析
-- 过程能力分析
-- 质量小组活动
-- 8D方法。
过程审核提问表
注塑过程□装配□涂装□
审核员:被审核方:
日期:
要素
提问
要求/说明
10
8
6
4
0
异常状况/备注
过程审核记录表
注塑过程□装配□涂装□
审核员:被审核方:
日期:
要素
提问
要求/说明
10
8
6
4
0
异常状况/备注
6.1人员/素
质
6.1.1是否对员工委以监控产品质量/过程质量的职责和权限?
6.1.2是否对员工委以负责生产设备/生产环境的职责和权限?
6.1.3员工是否适合于完成所交付的任务并保持其素质?
需考虑要点,例如:
6.3.5模具/工具,工装,检验、测量和试验设备是否按要求存放?
需考虑要点,例如:
-- 贮存量;防损伤;零件定置
-- 整齐,清洁,不超装(库存场地,周转箱)
-- 控制贮存时间
-- 环境影响,空调。
需考虑要点,例如:
-- 隔离库,隔离区;标识
-- 标识妥当的存放废品、返修件、调整件的容器
-- 缺陷产品和缺陷特性
-- 参与改进项目
-- 自检
-- 过程认可/点检(设备点检/首件检验/末件检验)
-- 过程控制(理解控制图)
-- 终止生产的权利。
需考虑要点,例如:
--环境的整齐和清洁
-- 进行/报请维修与保养
-- 零件准备/贮存
-- 进行/报请对检测,试验设备的检定和校准。
需考虑要点,例如:
-- 过程上岗指导/培训/资格的证明
-- 模具/设备/机器的保养维修状态(包括有计划的维修)。
过程审核提问表
注塑过程□装配□涂装□
审核员:被审核方:
日期:
要素
提问
要求/说明
10
8
6
4
0
异常状况/备注
6.2 生产设备
/生产工装
6.2.2在批量生产中使用的检测,试验设备是否能有效地监控质量要求?
6.2.3生产工位,检验工位是否符合要求?
6.2.4生产文件与检验文件中是否标出所有的重要技术要求,并坚持执行?
-- 产品以及发生缺陷的知识
-- 对安全生产/环境意识的指导
-- 关于如何处理“具有特别备证要求的零件”的指导
-- 资格证明(例如:焊接证书,视力测定,厂内机动车驾驶证)。
过程审核提问表
注塑过程□装配□涂装□
审核员:被审核方:
日期:
要素
提问
要求/说明
10
8
6
4
0
异常状况/备注
6.1人员/素
质
6.2 生产设备
需考虑要点,例如:
-- 原始记录卡;缺陷收集卡
-- 控制图;参数更改;数据收集
-- 过程参数的记录装置(例如:温度,时间,压力)
-- 设备停机;停电
需考虑要点,例如:
-- 过程能力;过程参数
-- 缺陷种类/缺陷频次;缺陷成本(不符合性)
-- 废品/返修件;隔离通知/分选
-- 节拍/流转时间;可靠性/失效特征。
-- 质量信息(目标值/实际值)
-- 改进建议
-- 志愿行动(培训,质量小组)
-- 低病假率
-- 对质量改进的贡献
-- 自我评定。
需考虑要点,例如:
-- 对重要特性/过程特定的参数进行机器能力调查/过程能力调查
-- 重要参数要强迫控制/调整
-- 在偏离额定值时报警(例如:声光报警,自动断闸)
-- 上/下料装置
6.4 缺陷分析
/纠正措施/持
续改进
(KVP)
6.4.4对过程和产品是否定期进行审核?
6.4.5对产品和过程是否进行持续改进?
6.4.6对产品和过程是否有确定的目标值,并监控是否达到目标?
必须有产品及产品过程的审核计划。审核原因有,例如:
-- 新项目/新过程/新产品
-- 未满足质量要求(内部/外部)
6.2.5对产品调整/更换是否有必备的辅助器具?
-- 可靠性试验,功能试验,耐腐蚀试验
-- 测量精度/检具能力调查
-- 数据采集和分析
-- 检具标定的证明
需考虑要点,例如:
-- 人机工程学
-- 照明
-- 整齐和清洁、环境保护
-- 环境和零件搬运
-- 安全生产。
需考虑要点,例如:
-- 过程参数(例如:压力,温度,时间,速度)
过程审核提问表
注塑过程□装配□涂装□
审核员:被审核方:
日期:
要素
提问
要求/说明
10
8
6
4
0
异常状况/备注
6.3运输/搬运
/贮存/包装
6.3.2产品/零件是否按要求贮存?运输方式/包装方法是否按产品/零件的特性而定?
6.3.3废品、返修件和调整件以及车间内混批、不混料并保证可追溯性?
-- 审核后提出的改进计划
--给责任者的信息
-- 内部/外部的接口会谈
-- 内部抱怨
-- 顾客抱怨
-- 顾客调查
需考虑要点,例如:
-- 看板管理;准时化生产
-- 先进先出;仓库管理
-- 更改状态;向下道工序只供合格件
-- 数量记录/统计;信息流
-- 足够、合适的运输器具
-- 定置库位;
-- 最小库存/无中间库存
-- 改进过程受控状态(例如:工艺流程分析)
-- 优化更换装备时间,提高设备利用率
-- 降低流转时间
-- 降低库存量。
需考虑要点,例如:已生产数量; 质量数据(例如:缺陷率,审核结果);流转时间;缺陷成本(不符合性);过程特性值(例如:过程能力指数)。
-- 机器/模具/辅助装置的数据(模具号,机器号)
-- 检验规范(重要特性,检验、测量和试验设备,方法,频次)
-- 过程控制图的控制限
-- 机器能力证明和过程能力证明
-- 操作说明、作业指导书、检验指导书
--发生缺陷时的信息
-- 调整计划
-- 调整辅助装置/比较辅助方法
-- 灵活的模具更换装置
--极限标样
过程审核提问表
注塑过程□装配□涂装□
审核员:被审核方:
日期:
要素
提问
要求/说明
10
8
6
4
0
异常状况/备注
6.2 生产设备
/生产工装
6.3运输/搬运
/贮存/包装
6.2.6是否进行批量生产起始认可,并记录调整参数或偏差情况?
6.2.7是否按时落实要求的纠正措施并检查琪 有效性?
6.3.1产品数量/生产批次的大小是否按需求而定?是否有目的地运往下道工序?
需考虑要点,例如:
-- 新产品,产品更改
-- 停机/过程中断;修理,更换模具
-- 更换材料(例如:换炉/批号)
-- 生产参数更改、参数的现时性
-- 首件检验并记录存档
-- 工作岗位的整齐和清洁;包装
-- 模具与检验、测量和试验设备的认可/更改状态。
-- 风险分析(过程P-FMEA)/缺陷分析/QRQC分析
-- 验证是否遵守质量要求;指出改进的潜能。
必须把偏差报告给责任者,并对改进措施进行跟踪。
需考虑要点,例如:顾客要求;重要特性;功能;过程参数/过程能力指数;标识、包装; 确定的过程工序/工艺流程。
必须根据至今积累的质量/成本和服务方面的知识去调查改进的潜力。需考虑要点,例如:
-- 成本优化
-- 减少浪费(例如:废品和返修)
/生产工装
6.1.4是否有包括顶岗规定的人员配置计划?
6.1.5是否有效地使用了提高员工工作积极性的方法?
6.2.1生产设备/工装模具是否能保证满足产品特定的质量要求?
需考虑要点,例如:
-- 生产班次计划(按任务单)
-- 素质证明(素质列表)
-- 工作分析/时间核算(例如:MTM,REFA)。
需考虑要点,例如:
过程审核提问表
注塑过程□装配□涂装□
审核员:被审核方:
日期:
要素
提问
要求/说明
10
8
6
4
0
异常状况/备注
6.4 缺陷分析
/纠正措施/持
续改进
(KVP)
6.4.1是否完整地记录质量数据/过程数据,并具有可评定性?
6.4.2是否用统计技术分析质量数据/过程数据,并由此制订改进措施?
6.4.3在与产品要求/过程要求有偏差时,是否分析原因并检查纠正措施的有效性?
-- 确定生产过程中不合格品的分离/返修工位。
需考虑要点,例如:
-- 零件标识;炉/批号标识;去除无效标识
-- 工作状态、检验状态和使用状态的标识
-- 有效期;有关零件/生产数据的工作指令。
需考虑要点,例如:
-- 防损存放;整齐和清洁
-- 定置存放;有管理的发放
-- 环境影响
-- 标识;明确的认可状态与更改状态