【涂装人必看】车轮电泳涂装线实际生产注意事项
汽车电泳涂装工艺维护管理及质量控制

汽车电泳涂装工艺维护管理及质量控制随着汽车工业的发展,汽车电泳涂装工艺逐渐成为汽车制造过程中不可或缺的一环。
汽车电泳涂装工艺是一种将电泳涂料均匀地附着在汽车表面的工艺,具有坚固耐用、环保节能等优势。
为了确保汽车电泳涂装的质量,维护管理及质量控制显得尤为重要。
维护管理是汽车电泳涂装工艺的基础。
在使用电泳涂装设备前,必须做好设备的维护保养工作。
定期清洁设备内部,保持设备的正常运转;检查设备的电气线路和涂装喷嘴等部件的连接情况,确保设备的安全可靠;检查电泳涂料的质量,避免使用劣质涂料对设备和涂装效果造成损害。
只有做好维护管理工作,才能保证汽车电泳涂装工艺的稳定性和可靠性。
质量控制是汽车电泳涂装工艺的关键。
在汽车电泳涂装过程中,要严格控制涂料的均匀性和厚度。
通过调整电泳涂装设备的参数,如涂料的浓度、电压、电流等,以及喷嘴的位置和角度,确保涂料均匀附着在汽车表面,避免出现涂料厚度不均或漏涂的情况。
同时,还需要对涂装后的汽车进行质量检测,如涂层的附着力、耐腐蚀性等,以确保涂装质量符合要求。
为了提高汽车电泳涂装工艺的质量,还可以采取一些措施。
例如,定期对涂装设备进行维护保养,及时更换老化或损坏的零件,保证设备的正常运转;加强人员培训和技术指导,提高操作人员的技术水平和工作质量;加强现场管理,严格执行涂装工艺规范,确保每一道工序都符合标准要求;建立健全的质量管理体系,对涂装工艺进行全面监控和控制。
汽车电泳涂装工艺的维护管理及质量控制是确保涂装质量的关键。
通过做好设备的维护保养、严格控制涂料的均匀性和厚度,以及加强人员培训和技术指导等措施,可以提高汽车电泳涂装工艺的质量,保证涂装效果的稳定和可靠。
只有注重维护管理和质量控制,才能使汽车电泳涂装工艺发挥出最佳效果,为汽车制造提供优质的涂装保障。
车轮电泳涂装中几个问题的探讨

() 1 除油 不彻 底
蚀等, 需要对 车轮进行除氧化皮 、 锈处理 。在连续 式生产 线 除 上, 常采 用酸洗处理工艺 。
车 轮 有 夹 缝 , 需 要 酸 洗 , 就 这 类 涂 装 线 上 , 常 出 现 又 现 经
从工艺 上看 , 预脱脂 、 脱脂两道 工序 , 有喷 淋和 浸渍 , 一 对 般工件 是完全可 以除去工件上 油污 的, 但从实 际效 果看 , 却存 在 夹缝 等处除油 不净 现象 。这 与脱脂 剂性 能 不 良有关 , 如果 脱脂剂 除了含有几种常规碱性 成分外 , 还是 以 0 P一1 0乳 化剂 ( 清洗性较差 ) 和十二烷 基苯磺 酸钠 为表 面活性 剂 , 那么这 类 脱脂剂 品种简单 、 组合 效应 不强 , 少高 效强 渗透 剂 , 以难 缺 所 以除尽 夹缝 内油污 , 也就直接影响磷化效果 。
业、 自动化程度 高等 优点 已被 各行 业广 泛采 用 。电泳涂 装 可
以对工 件的 内腔 、 夹缝等部位进行 涂装 , 以大 大提 高这些 区 可 域 的防腐性能 。在 车轮涂 装工 艺上 , 是按 中高档 涂装 要 求 也 施 工 , 主要工 艺为脱脂 、 其 磷化 、 电泳 、 面漆 ( 喷粉 ) 罩 光漆等 。 / 但 车轮主要是 由钢板成 型焊接组合 , 属典 型带有 夹缝 的工件 ,
烤、 下件 ( 转挂面涂线 ) 。
电泳车间安全操作规程

电泳车间安全操作规程一、引言电泳车间是一种常见的涂装工艺,用于给工件表面涂上一层均匀、致密的涂层。
为了保障员工的人身安全和车间设备的正常运行,制定本安全操作规程。
二、车间布局与设备安全1. 车间应保持整洁,通风良好,防止积尘和有害气体积聚。
2. 电泳槽、输送线等设备应定期检查,确保其正常运行,防止漏电和其他安全隐患。
3. 车间应设置明显的安全标识和紧急停机按钮,方便员工在紧急情况下住手设备。
三、员工安全培训与操作要求1. 所有进入电泳车间的员工必须接受安全培训,了解电泳工艺的基本原理和操作规程。
2. 员工在操作电泳设备前,应穿戴好个人防护装备,包括防护服、安全帽、防滑鞋等。
3. 禁止在车间内吸烟、饮食,严禁携带易燃、易爆物品进入车间。
4. 员工应按照操作规程正确使用电泳设备,禁止私自调整设备参数或者进行未经授权的操作。
四、化学品安全管理1. 车间内使用的化学品应符合国家标准,储存于专用柜中,远离火源和高温区域。
2. 使用化学品前,应子细阅读产品安全说明书,了解其危(wei)险性和正确的使用方法。
3. 使用化学品时应佩戴好防护手套、眼镜等个人防护装备,避免直接接触皮肤和眼睛。
4. 废弃的化学品应按照规定进行分类、储存和处理,禁止随意倾倒或者混合处理。
五、紧急情况应急预案1. 建立车间紧急情况应急预案,明确员工的逃生路线和避难点。
2. 定期组织紧急演练,提高员工应急避险能力和自救能力。
3. 车间应配备适量的灭火器材和消防设备,确保在发生火灾等紧急情况时能够及时扑灭和报警。
六、安全检查与事故报告1. 定期进行车间安全检查,发现问题及时整改,确保车间设备和环境的安全性。
2. 发生事故或者安全事件时,应即将上报相关部门,并进行详细的事故报告和调查。
七、员工责任与奖惩制度1. 员工应严格遵守本操作规程,自觉维护车间安全和工作秩序。
2. 对违反操作规程的员工,将依据公司相关制度进行相应的纪律处分。
3. 对积极参预安全工作、提出合理建议的员工,将赋予相应的奖励和表彰。
涂装生产线操作流程及注意事项
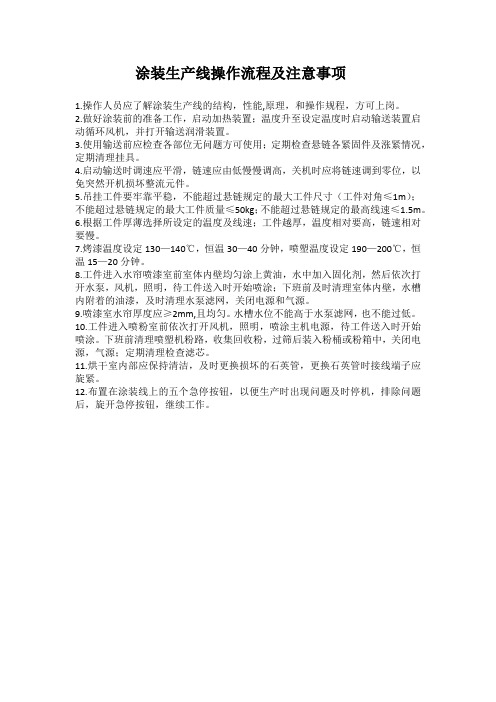
涂装生产线操作流程及注意事项
1.操作人员应了解涂装生产线的结构,性能,原理,和操作规程,方可上岗。
2.做好涂装前的准备工作,启动加热装置;温度升至设定温度时启动输送装置启动循环风机,并打开输送润滑装置。
3.使用输送前应检查各部位无问题方可使用;定期检查悬链各紧固件及涨紧情况,定期清理挂具。
4.启动输送时调速应平滑,链速应由低慢慢调高,关机时应将链速调到零位,以免突然开机损坏整流元件。
5.吊挂工件要牢靠平稳,不能超过悬链规定的最大工件尺寸(工件对角≤1m);不能超过悬链规定的最大工件质量≤50kg;不能超过悬链规定的最高线速≤1.5m。
6.根据工件厚薄选择所设定的温度及线速;工件越厚,温度相对要高,链速相对要慢。
7.烤漆温度设定130—140℃,恒温30—40分钟,喷塑温度设定190—200℃,恒温15—20分钟。
8.工件进入水帘喷漆室前室体内壁均匀涂上黄油,水中加入固化剂,然后依次打开水泵,风机,照明,待工件送入时开始喷涂;下班前及时清理室体内壁,水槽内附着的油漆,及时清理水泵滤网,关闭电源和气源。
9.喷漆室水帘厚度应≥2mm,且均匀。
水槽水位不能高于水泵滤网,也不能过低。
10.工件进入喷粉室前依次打开风机,照明,喷涂主机电源,待工件送入时开始喷涂。
下班前清理喷塑机粉路,收集回收粉,过筛后装入粉桶或粉箱中,关闭电源,气源;定期清理检查滤芯。
11.烘干室内部应保持清洁,及时更换损坏的石英管,更换石英管时接线端子应旋紧。
12.布置在涂装线上的五个急停按钮,以便生产时出现问题及时停机,排除问题后,旋开急停按钮,继续工作。
汽车电泳涂装工艺维护管理及质量控制

汽车电泳涂装工艺维护管理及质量控制随着汽车行业的发展,汽车电泳涂装工艺在汽车制造中扮演着至关重要的角色。
汽车电泳涂装工艺不仅可以提供汽车表面的保护,还能增加汽车的美观度和耐久性。
然而,为了保证汽车电泳涂装的质量,必须进行维护管理和质量控制。
本文将从管理和控制两个方面,探讨汽车电泳涂装工艺的维护和质量控制。
一、维护管理1. 定期设定维护计划:为了保证汽车电泳涂装工艺的正常运行,需要制定一个定期的维护计划。
该计划应包括设备的检查、清洁和维修等内容。
定期的维护工作可以及时发现和解决潜在的问题,从而保证电泳涂装工艺的稳定运行。
2. 培训员工:汽车电泳涂装工艺是一项复杂的技术工作,需要经验丰富的员工进行操作。
因此,为了保证工艺的质量,必须对员工进行培训。
培训内容包括工艺的原理、操作技巧以及常见问题的解决方法等。
通过培训,可以提高员工的技术水平,减少操作失误,提升工艺的稳定性和质量。
3. 设立质量管理体系:为了保证汽车电泳涂装工艺的质量,需要建立一个完善的质量管理体系。
该体系应包括质量目标的设定、质量标准的制定、质量监控的实施等内容。
通过建立质量管理体系,可以对工艺进行全面监控,及时发现和纠正问题,提高工艺的质量稳定性。
二、质量控制1. 原材料的选择和检测:汽车电泳涂装工艺的质量直接关系到原材料的选择和质量。
因此,在进行工艺液的选择时,必须严格按照工艺要求选择合适的原材料。
同时,对原材料进行检测,确保其质量符合要求,避免因原材料问题导致的工艺质量问题。
2. 工艺参数的控制:汽车电泳涂装工艺涉及到众多的参数,如温度、时间、电压等。
这些参数的控制直接影响到工艺的质量。
因此,在进行工艺操作时,必须严格控制这些参数,确保其稳定在规定范围内。
同时,定期检查和校准设备,保证参数的准确性和可靠性。
3. 质量检测和分析:为了保证汽车电泳涂装工艺的质量,需要进行质量检测和分析。
质量检测包括对涂装膜的厚度、附着力、耐腐蚀性等进行测试。
电泳车间安全操作规程

电泳车间安全操作规程一、引言电泳车间是一种常见的涂装车间,主要用于对金属制品进行防腐蚀涂装。
为了确保员工的人身安全和车间设备的正常运行,制定本安全操作规程。
二、车间布局与设备安全1. 车间布局:电泳车间应合理布局,通道宽敞,设备摆放整齐,易于操作和维护。
2. 电泳槽安全:电泳槽应固定在地面上,确保稳定性。
槽内应保持清洁,避免杂物积聚。
3. 电源与电缆安全:电源设备应符合安全标准,并定期检查和维护。
电缆应整齐布置,避免交叉和绊倒风险。
三、个人防护措施1. 穿戴防护服:进入电泳车间的员工必须穿戴防护服,包括工作服、手套、安全鞋等。
防护服应定期更换和清洗。
2. 使用个人防护装备:根据工作需要,员工应佩戴防护眼镜、防尘口罩、耳塞等个人防护装备,确保工作安全。
3. 防护设施:车间应配备紧急洗眼器、淋浴器等防护设施,并定期检查其功能是否正常。
四、化学品管理1. 化学品存储:化学品应分类存放,标识清晰,避免相互混合。
存储区域应通风良好,远离火源和高温物品。
2. 化学品使用:员工在使用化学品时,应佩戴防护手套和口罩,并遵循正确的操作步骤。
避免接触皮肤和吸入有害气体。
五、机械设备操作1. 操作规程:员工在操作机械设备前,应接受相应的培训,并熟悉设备操作规程。
禁止未经培训人员操作设备。
2. 设备维护:定期检查设备的运行状态,如发现异常应及时报修。
禁止私自拆卸设备或进行未经授权的维修。
六、火灾防护措施1. 灭火设备:车间应配备灭火器、消防栓等灭火设备,并定期检查其有效性。
2. 火灾逃生通道:车间内应设有明确的火灾逃生通道,并保持畅通。
员工应定期参加火灾逃生演练。
七、应急预案1. 事故报告:发生事故时,员工应立即向上级报告,并采取相应的紧急措施。
2. 紧急救援:车间应配备急救箱,并指定专人负责急救工作。
员工应定期接受急救培训。
八、员工培训与考核1. 安全培训:新员工入职前应接受电泳车间安全操作培训,并签署安全承诺书。
2. 定期考核:对员工进行定期安全知识考核,确保员工对安全操作规程的理解和掌握。
电泳车间安全操作规程

电泳车间安全操作规程标题:电泳车间安全操作规程引言概述:电泳车间是涂装生产中重要的环节,为了确保生产过程安全稳定,制定了一系列的安全操作规程。
本文将详细介绍电泳车间的安全操作规程,以确保生产过程中的安全性和稳定性。
一、人员安全1.1 人员培训:所有进入电泳车间的人员必须接受相关的安全培训,了解电泳设备的操作规程和安全注意事项。
1.2 穿戴防护装备:进入电泳车间的人员必须穿戴符合要求的防护装备,包括护目镜、手套、防护服等。
1.3 禁止单独作业:在电泳车间作业时,禁止单独作业,必须有其他人员在场并保持联系。
二、设备安全2.1 定期检查:电泳设备必须定期进行检查和维护,确保设备运行正常,避免发生故障。
2.2 操作规程:操作电泳设备时必须按照操作规程进行,严禁擅自更改设备参数和操作方式。
2.3 紧急停车装置:电泳设备必须配备紧急停车装置,以应对突发情况并确保人员安全。
三、化学品安全3.1 储存规范:所有化学品必须按照规定的方式储存,避免混淆和泄漏。
3.2 使用注意:在使用化学品时必须佩戴防护装备,避免直接接触和吸入有害气体。
3.3 废弃处理:废弃的化学品必须按照规定的方式处理,避免对环境造成污染。
四、火灾安全4.1 防火措施:电泳车间必须配备灭火器等防火设备,以应对火灾风险。
4.2 禁止吸烟:电泳车间内严禁吸烟,避免引起火灾事故。
4.3 火灾演练:定期进行火灾演练,提高员工应对火灾的能力和反应速度。
五、紧急救援5.1 应急预案:制定电泳车间的紧急救援预案,明确员工应对突发情况的流程和措施。
5.2 紧急联系:所有员工必须了解紧急联系方式,及时报告事故并寻求匡助。
5.3 急救知识:员工必须接受急救知识培训,提高应对紧急情况的能力。
结论:电泳车间的安全操作规程对于保障生产过程的安全稳定具有重要意义,惟独严格遵守规程要求,才干确保生产过程的顺利进行。
希翼所有员工都能认真遵守规程,共同维护电泳车间的安全环境。
汽车电泳涂装工艺维护管理及质量控制

汽车电泳涂装⼯艺维护管理及质量控制·汽车电泳涂装⼯艺维护管理及质量控制论述汽车车⾝阴极电泳涂装⼯艺的维护、管理及正常⽣产时阴极电泳涂装⽣产现场和电泳槽液的质量控制要点。
电泳涂装;⼯艺维护、管理;质量控制。
前⾔电泳漆膜的质量,对于整车漆膜外观起到⾮常重要的作⽤,好的电泳漆膜外观,即可减少后道⼯序的⼯作强度,⼜可为后道⼯序提供好的漆膜基础。
为确保⽣产的正常进⾏和获得稳定的涂装质量,电泳涂装⽣产现场必须对⼯艺设备、槽液和⽣产环境进⾏严格的科学管理并做好⽇常的维护和运⾏记录,必须定期测定相关参数并做成变化曲线,从中发现规律,及时找出问题并解决。
虽然涂装设备、⼯艺和材料对漆膜质量影响很⼤,但涂装管理也不容忽视。
⼀、电泳涂装的⼯艺管理汽车车⾝阴极电泳涂装⼯艺⼀般由前处理、电泳涂装、电泳后清洗、电泳涂膜烘⼲等四道主要⼯序组成,对这些⼯序进⾏严格、周密和良好的⼯艺管理对磷化、电泳涂层质量以及整车油漆涂层质量产⽣⾮常重⼤的影响。
1.1 前处理⼯艺汽车车⾝⾦属零件涂装前处理主要包括脱脂、除锈、除氧化⽪及化学转化膜处理(磷化、氧化、钝化) 。
⾸先应清洗掉各种污物(如油污、锈、氧化⽪、焊渣、⾦属屑等) ,随后进⾏化学处理(磷化、钝化) ,并进⾏充分⽔洗,以洗掉前处理药品、磷化沉渣等,最后⽤去离⼦⽔洗。
所⽤去离⼦⽔⽔质要好,电导率应不⼤于25µS/ cm,并确保车⾝的滴⽔电导率不⼤于50µS/ cm。
车⾝经前处理后油污未洗净⽽带⼊电泳槽内会影响电泳质量,产⽣缩孔、针孔;锈不除掉,磷化不上,还易产⽣电泳涂膜的异常附着,且在涂膜下能继续扩蚀;氧化⽪不除净,则不导电,泳涂不上;焊渣、⾦属屑、前处理药品、磷化沉渣不除净⽽带⼊电泳槽,则会影响槽液稳定性和涂装质量。
实践证明,车⾝阴极电泳涂装前的磷化膜应具备以下质量标准:外观为结晶细⼩、致密、均匀、⽆锈蚀、⽆沉渣沉积的浅灰⾊膜层;磷化膜质量应在2~3 g/m2 范围内;结晶细度应⼩于10µm;P⽐在85%以上[即膜中Zn2 Fe ( PO4 ) 2·4H2O含量⾼,耐碱性好]。
涂装线安全操作规程

涂装线安全操作规程涂装线是一个涂料施工的生产线,是许多制造企业生产过程中必不可少的环节。
随着现代化制造业的不断发展,涂装线的使用越来越广泛,涂装线的安全操作变得越来越重要。
在涂装线上工作需要遵守一系列的规程和安全操作,以确保工作人员的安全和正常的生产。
涂装线安全操作规程的目的是制定一系列详细、全面的规定,使工作人员在涂装线上工作时,能够清楚明确的了解安全操作要求,避免意外事故的发生,同时,提高工作效率,保证生产质量。
一、涂装线的危险源涂装生产线的危险源主要有以下几点:1. 蒸发的有害气体在微型气体泄漏或卡塞导致,可引起爆炸或中毒。
之前做好防护措施和仔细开展配气操作,尽可能缩小发生这种情况的可能性。
2. 火源在涂装线上使用火源或接近容易起火的物件时,往往容易造成爆炸和火灾。
在涂装生产线工作时,不能吸烟,也不能使用明火,更不能将易燃和易爆的物质放在涂装车间中。
3. 异物飞溅在操作喷涂枪时,往往会泄漏剩余的涂料,喷头也会突然出现故障。
在此真个过程中,操作者应该始终保持警惕,避免异物飞溅,易照成伤害或损坏。
4. 高温与静电在进行烤漆批处理时,一些烤漆生产会出现较高的温度。
同时,由于涂装过程中会产生大量的静电,涂装线工作人员必须严格遵守安全操作要求,尽可能的降低温度,避免因为静电引起火灾或其他伤害事故。
二、涂装线的安全操作规范1. 严格遵守个人防护要求涂装线工作人员在涂装线上工作时,必须按照规定穿戴好防护服、口罩、手套、防护帽等必要的个人防护设备。
2. 充分检查和维护设备在启动涂装生产线前,必须检查生产设备是否操作顺畅,电线电缆是否损坏等情况,从而确保一切顺利。
如果设备出现一些问题,应该尽快通知维修人员进行维护,确保生产线的正常运行。
3. 动作规范和灵活,注重安全在涂装生产线上要严格遵守动作规范,注重安全和灵活性,时刻保持警惕。
在涂装线上操作时不要做出过分激动或肆意猖狂的操作,保持沉着的心态,冷静应对各种意外情况。
汽车电泳涂装工艺维护管理及质量控制

汽车电泳涂装工艺维护管理及质量控制一、汽车电泳涂装工艺维护管理1. 设备维护管理汽车电泳涂装设备是整个生产线的核心,设备的正常运行对于生产效率和产品质量都有着至关重要的影响。
因此,设备的维护管理是非常重要的。
(1)设备保养定期对设备进行保养,清洗设备内部,更换易损件,保证设备的正常运行。
(2)设备检修定期对设备进行检修,发现问题及时处理,避免设备故障对生产造成影响。
2. 涂料管理(1)涂料储存涂料需要储存在干燥、通风、避光的地方,避免受潮、变质。
(2)涂料搅拌涂料需要定期搅拌,保证其均匀性。
(3)涂料筛选涂料需要通过筛网进行筛选,去除其中的杂质,保证涂装质量。
3. 操作规范(1)操作人员需要进行专业培训,掌握涂装工艺的基本知识和操作技能。
(2)操作人员需要遵守操作规范,严格按照操作流程进行操作,避免操作失误。
二、汽车电泳涂装质量控制1. 涂装前处理汽车电泳涂装前需要进行表面处理,包括除油、除锈、除氧化皮等。
表面处理的质量对于涂装后的质量有着至关重要的影响。
2. 涂装参数控制(1)涂料的稀释比例需要控制在合适的范围内,避免过度稀释或过度浓缩。
(2)涂料的喷涂厚度需要控制在合适的范围内,避免涂层过厚或过薄。
(3)涂装温度和湿度需要控制在合适的范围内,避免温度过高或过低,湿度过大或过小。
3. 涂装后处理涂装后需要进行烘干、冷却等后处理,保证涂层的质量。
4. 涂装质量检验(1)外观检验涂装后需要进行外观检验,包括涂层的平整度、光泽度、色泽等。
(2)附着力检验涂装后需要进行附着力检验,保证涂层的附着力符合要求。
(3)耐腐蚀性检验涂装后需要进行耐腐蚀性检验,保证涂层的耐腐蚀性符合要求。
以上是关于汽车电泳涂装工艺维护管理及质量控制的章节划分,希望对您有所帮助。
汽车电泳涂装常见问题及其解决措施

汽车电泳涂装常见问题及其解决措施汽车电泳涂装常见问题及其解决措施摘要:介绍了汽车车身电泳涂装工艺流程,主要包括预清理、脱脂、表调、磷化、沥干、阴极电泳、烘干和冷却。
分析了汽车电泳涂装中常见的一些问题,如缩孔、气泡、漏底。
给出了其解决措施。
关键词:汽车;涂装;电泳;缩孔1 前言电泳涂装是汽车车身涂装的第一道环节,也可以说是整个车身涂装的基础,其质量的好坏直接影响车身的抗腐蚀性能及漆膜的装饰效果。
本文根据生产实际,对电泳涂装中出现的一些问题进行分析,介绍了解决的措施,希望对读者能有所启迪和帮助。
2 汽车车身电泳涂装工艺流程手工预清理─(60 ± 5) °C 洪流冲洗─(60 ± 5) °C 预脱脂─(60 ± 5) °C 脱脂─水洗2 次─表调─(43 ± 2) °C磷化─水洗2 次─去离子水洗─沥干─(28 ± 1) °C 阴极电泳─超滤洗2 次─去离子水洗─沥干─电泳烘干─强冷─电泳后存放。
3 常见问题分析及其解决措施上述电泳涂装工艺流程中,车身冲洗采用全浸式喷浸结合的处理方式,而车身运输系统采用自行葫芦和滑橇地面输送机相结合的方式。
受工艺条件、设备、车身结构的限制,在车身电泳涂装生产过程中出现了一些问题。
以下为常见问题及其解决方法。
3. 1 滑橇底部油泥污染导致电泳缩孔及其解决办法在车身经手工预清理完后,进行洪流冲洗前,需要将车身承载在滑橇上并锁紧,再装挂在自行葫芦系统的吊架上,然后依次通过电泳涂装各工艺槽。
当滑橇第一次通过电泳槽时,滑橇表面会泳涂上一层电泳漆膜,形成绝缘层。
而当滑橇承载车身再一次通过电泳槽时,滑橇表面因有绝缘层的存在而不会泳涂上新的电泳漆膜,但会一次次附上一层新的电泳浮漆。
由于电泳后的水洗工艺主要是针对车身,而位于车身底部的滑橇不可能被冲洗干净。
因此,当附有电泳浮漆的滑橇在电泳后工位(如电泳烤房、电泳烤后存放)的输送链上前行时,滑橇底部的电泳浮漆和已泳涂上的电泳漆膜与输送链上的滚子不断接触、摩擦,就会粘附滚子上的润滑油,形成油泥。
电泳涂漆工安全操作规程

电泳涂漆工安全操作规程为确保电泳涂漆工作的安全和顺利进行,制定以下安全操作规程:一、基本要求1.必须通过电泳涂漆工作安全教育后,方能上岗作业。
2.在操作前要穿戴好防护装备,包括手套、口罩、护目镜和防护服。
3.具体岗位的电泳涂漆工作人员必须熟悉操作程序,并遵守相关规定和标准。
如需要调整,必须检查、确认并经过质量部门的评审批准。
二、电气安全1.必须有专人对电器设备进行检查和维护。
2.必须使用合格电线以及电器设备。
3.使用电气设备时必须关注其工作状态,如有异常立即停机检查。
4.不可随意改变控制器的设置参数。
5.禁止擅自打开控制箱的电器、安装或修理电器或设备。
三、机械安全1.涂料桶和输送设备的清洗必须完全停机后进行。
2.严禁在涂装治具上和在输送线路上使用手抓住或踩住修理线路。
3.进行装置、安装或调整设备时,请勿插手旋转的机械部件。
4.若出现较大的噪声或异响,应立即停止设备并进行检查。
四、涂装安全1.使用涂料时必须使用高质量的涂料,不可混合使用、使用过期涂料,以免对产品质量产生不良影响。
2.在使用过程中,必须注意密闭设备的压力,要随时检查喷漆系统的泄压情况。
3.喷涂操作时,请注意使用高温、高压气体、高速喷射等特殊现象可能引起的安全隐患,务必保持警觉。
4.涂料易燃,无论何时都不允许吸烟。
五、紧急情况处理在发生紧急情况时,必须立即停机,并根据情况实施相应措施,包括但不限于以下内容:1.电气故障:立即停止电源,排除故障。
2.机械故障:立即停止设备,进行检查维修。
3.涂装故障:立即停止喷涂工艺和涂料供应,检查后再开工作。
六、其他注意事项1.不得将任何状况视为常态,始终保持警觉和高度关注。
2.严禁带有松散衣物、首饰、发带等在房间内操作。
3.出现任何违反规定的情况,应立即向质量部门报告。
4.具体岗位的电泳涂漆工作人员必须不断学习、提高技能,以提高整体的工作水平和质量。
结语以上就是电泳涂漆工安全操作规程。
作为承担涂装工作的一名电泳涂漆工作人员,我们必须严格遵守这些规定和要求,增强自身安全意识,不断提高工作质量和技能水平,确保电泳涂漆工作的顺利进行。
电泳车间安全操作规程

电泳车间安全操作规程一、引言电泳车间是进行电泳涂装工艺的关键环节,为确保生产过程的安全和质量,制定本安全操作规程。
本规程旨在规范电泳车间的操作流程,保障员工和设备的安全,减少事故发生的风险。
二、作业人员安全要求1. 所有作业人员必须经过相关培训并持有相应的操作证书,了解电泳车间的操作规程和安全注意事项。
2. 作业人员必须穿戴符合要求的工作服、防护服和个人防护装备,包括安全帽、防护眼镜、防护口罩、耳塞等。
3. 作业人员在进入车间前必须进行身体检查,确保身体健康,不得患有感染性疾病或者其他危害作业安全的疾病。
4. 作业人员必须严格遵守车间的安全操作规程,不得擅自更改设备参数或者操作流程。
三、设备安全要求1. 电泳设备必须经过定期维护和检修,确保其正常运行和安全性能。
2. 设备的电源和电气路线必须符合国家标准,并定期进行检查和维护。
3. 设备周围必须保持通道畅通,不得堆放杂物或者阻挡安全出口。
4. 设备的操作面板必须清晰标识,操作按钮必须正常工作,如发现异常应及时报修。
四、化学品安全管理1. 车间内使用的化学品必须具备相应的安全数据表,并储存在指定的储存区域内。
2. 作业人员必须佩戴适当的防护手套和眼镜,避免直接接触化学品。
3. 使用化学品时必须确保通风良好,避免有害气体积聚。
4. 废弃的化学品必须按照像关规定进行分类、储存和处理,不得随意倾倒或者混合处理。
五、紧急情况应急预案1. 车间内必须配备相应的消防器材,并定期进行检查和维护。
2. 作业人员必须熟悉紧急情况的应急预案,包括火灾、泄漏等情况的处理方法。
3. 发生紧急情况时,作业人员必须即将向车间负责人报告,并按照预案进行应急处理,确保人员安全和设备无损。
六、安全巡查和记录1. 车间负责人必须定期进行安全巡查,发现问题及时整改,并记录巡查情况。
2. 巡查记录必须包括巡查时间、巡查人员、巡查内容、存在的问题和整改情况等。
3. 巡查记录必须保存一年以上,以备安全检查和事故调查使用。
涂装生产线需要注意什么

涂装生产线需要注意什么涂装生产线需要注意以下几个方面:设备选择、原料准备、色彩管理、人员培训、环保措施、质量控制等。
首先,设备选择是涂装生产线的重要步骤。
选择适合自家产品的喷涂设备,需要考虑产品的尺寸、材质、涂装方式等因素。
不同尺寸的产品可能需要不同规格的设备,同时,不同材质的产品也需要不同类型的设备来保证涂层的附着力和均匀性。
此外,涂装方式也可以选择手工涂装或自动化涂装,根据企业自身的需求和经济实力,选择适合的涂装设备。
其次,原料准备也是涂装生产线需要注意的一个重要环节。
涂料是保证涂装质量的关键,选用优质的涂料对于涂装效果的稳定性和产品的持久度非常重要。
所以,企业应该选择正规的供应商,购买符合质量标准的涂料。
在储存和使用涂料的过程中,需要严格按照指定的温度、湿度等环境条件进行保存,以防止涂料变质或造成涂层质量问题。
色彩管理也是涂装生产线需要重点关注的方面。
在涂装生产中,颜色的一致性是非常重要的,特别是对于同款产品的颜色要求更为苛刻。
为了保证颜色的一致性,企业应该建立完善的色彩管理系统,包括对涂料的颜色进行标准化管理,制定并执行涂装工艺控制标准,严格控制涂料的搅拌和配比等环节,确保每次生产的涂料颜色能够稳定地达到要求。
人员培训也不可忽视。
涂装生产线涉及到很多技术操作,需要操作人员具备一定的专业知识和技能。
企业应该对操作人员进行全面的培训,使他们熟悉涂装工艺流程、设备操作规程、颜色管理等方面的知识,掌握正确的操作方法和质量控制技术。
通过定期的培训和考核,提高操作人员的技术水平和素质,确保涂装生产线的正常运行和产品质量的稳定性。
环保措施也是涂装生产线需要重视的方面。
涂装过程中会产生废气、废水和废固体等污染物,对环境造成一定的影响。
为了减少对环境的污染,企业应该安装和使用有效的排污设备,对废气、废水进行处理和净化。
另外,企业还应该定期进行环境检测,确保涂装生产过程中的污染物排放符合国家和地方的相关标准,积极履行企业的环境保护责任。
电泳涂漆工安全操作规程(三篇)

电泳涂漆工安全操作规程第一章总则第一条为了保障电泳涂漆工操作人员的生命安全和身体健康,维护生产设备的正常运行,避免事故的发生,制定本安全操作规程。
第二条本规程适用于所有从事电泳涂漆工作的人员。
所有操作人员必须严格遵守本规程,并参加相应的安全培训。
第三条进入涂装车间的人员,必须佩戴个人防护装备,并经过相应的卫生消毒处理。
第四条对于未经培训的人员,禁止进入涂装车间进行操作。
第五条涂装车间内禁止吸烟、使用明火和携带易燃易爆物品。
第二章个人防护第六条涂装工作人员必须佩戴以下个人防护装备:(一)呼吸防护:佩戴防尘口罩或防毒面具,根据实际作业情况选择适当的防护设备。
(二)眼面防护:佩戴防护眼镜或防风镜,防止化学物质或颗粒物进入眼睛。
(三)耳朵防护:在产生较大噪音的环境中,佩戴耳塞或耳罩。
(四)手部防护:佩戴化学防护手套,防止与涂料或溶剂接触。
(五)身体防护:穿戴适当的工作服,避免直接暴露在涂料和溶剂中。
第七条涂装工作人员在工作期间,应该随时检查个人防护装备的状态,如发现破损或失效,应及时更换。
第八条涂装工作人员应按照规定的程序进行个人卫生消毒处理,避免带入有害物质。
第三章操作安全第九条操作人员应具备相关的技术知识和操作经验,并接受必要的安全培训。
第十条涂装工作应在专用的喷涂室内进行,禁止在开放空间或无通风条件下进行操作。
第十一条涂装过程中应严禁将喷枪对准人员,确保周围人员的安全。
第十二条涂装工作应佩戴静电带电器,并按要求进行接地,以防止静电引起的火灾。
第十三条涂装过程中应保持良好的通风条件,确保室内空气质量良好,避免涂料和溶剂的积聚。
第四章火灾防范第十四条涂装车间应配备灭火器和自动火灾报警设备,并定期进行检查和维护。
第十五条涂装车间应设置明确的火灾疏散通道和安全出口,并保持通畅。
第十六条涂装车间应定期进行消防演练,提高员工的火灾应急处理能力。
第十七条涂装车间内禁止存放易燃易爆物品,如有需要,应存放在专用的防火柜中。
车轮电泳涂装中几个问题的探讨

车轮电泳、自泳涂装中几个问题的探讨当前汽车、农用车、家电、轻工产品的种类与生产厂家繁多,各生产厂在车身、零部件的制造工艺过程中,为提高涂装质量、降低成本,大多采用了阴极电泳漆作为涂装与防腐处理的底层涂料,可以说电泳涂装因其涂料利用率高、易于连续作业、自动化程度高等优点已被各行业广泛采用。
电泳涂装可以对工件的内腔、夹缝等部位进行涂装,可以大大提高这些区域的防腐性能。
在车轮涂装工艺上,也是按中高档涂装要求施工,其主要工艺为脱脂、磷化、电泳(自泳)、面漆(喷粉)/罩光漆等。
但车轮主要是由钢板成型焊接组合,属典型带有夹缝的工件,而板材又主要是热轧板,带有较多的氧化皮,或存在较多的锈蚀等,需要对车轮进行除氧化皮、除锈处理。
在连续式生产线上,常采用酸洗处理工艺。
车轮有夹缝,又需要酸洗,现就这类涂装线上,经常出现的问题给予分析,并提出改进措施,以提高涂装质量,减少涂装弊病。
1车轮涂装工艺国内某大型车轮生产线上,车轮的涂装工艺为:上件、预脱脂(喷淋)、脱脂、水洗、水洗、酸洗(盐酸)、水洗、水洗、水洗、中和、水洗、表调、磷化、水洗、水洗、水洗、纯水洗、纯水洗、阴极电泳、0次UF 水洗、UF1水洗、UF2水洗、纯水洗、纯水洗、烘烤、下件(转挂面涂线)。
全线采用连续式流水线生产,浸槽为船形槽,前处理、电泳、烘道成循环输送系统,即共用一条输送链。
2涂装中常见问题2.1车轮夹缝的起泡返锈问题在生产线上,常有车轮夹缝、焊缝等处磷化膜出现返锈,磷化膜不完整现象。
电泳后车轮夹缝里出现漆膜起泡或者有类似漆渣状的物质存在。
另外,电泳后的车轮长时间放在室外后,有时会从车轮夹缝处流出黄色锈水。
在生产中,车轮夹缝越小,越易出现此类问题。
2.1.1原因分析(1)除油不彻底从工艺上看,预脱脂、脱脂两道工序,有喷淋和浸渍,对一般工件是完全可以除去工件上油污的,但从实际效果看,却存在夹缝等处除油不净现象。
这与脱脂剂性能不良有关,如果脱脂剂除了含有几种常规碱性成分外,还是以0P-10乳化剂(清洗性较差)和十二烷基苯磺酸钠为表面活性剂,那么这类脱脂剂品种简单、组合效应不强,缺少高效强渗透剂,所以难以除尽夹缝内油污,也就直接影响磷化效果。
电泳涂装安全生产管理制度

一、总则为保障电泳涂装生产过程中的安全,防止事故发生,保障员工生命财产安全,根据国家有关安全生产法律法规和行业标准,结合本企业实际情况,特制定本制度。
二、安全生产责任1. 企业法定代表人对本企业的安全生产工作全面负责,是企业安全生产的第一责任人。
2. 各部门负责人对本部门的安全生产工作负直接责任。
3. 各岗位操作人员对本岗位的安全生产工作负直接责任。
4. 安全生产管理人员负责本企业安全生产的监督、检查和管理工作。
三、安全生产措施1. 安全教育培训(1)新员工上岗前必须进行安全教育培训,培训合格后方可上岗。
(2)定期对员工进行安全生产知识、技能培训,提高员工的安全意识和自我保护能力。
2. 安全生产设备设施(1)电泳涂装设备设施必须符合国家安全生产标准,定期进行检测、维修和保养。
(2)配备必要的安全防护设施,如防护罩、防护网、防护栏等。
3. 安全操作规程(1)严格执行电泳涂装操作规程,确保操作人员正确使用设备设施。
(2)操作人员必须佩戴必要的防护用品,如防护眼镜、防护手套、防护服等。
4. 用电安全(1)禁止私拉乱接电线,非专业人员不得擅自改动电气线路。
(2)电气设备发生故障时,立即切断电源,通知专业人员进行维修。
5. 防火防爆(1)严禁在电泳涂装区域内吸烟、使用明火。
(2)配备消防器材,定期检查、维护,确保消防设施完好有效。
6. 环境保护(1)严格执行废水、废气排放标准,确保污染物达标排放。
(2)加强环保设施运行管理,定期检测、维护,确保设施正常运行。
四、安全生产检查1. 定期开展安全生产检查,及时发现和消除安全隐患。
2. 对检查中发现的安全隐患,及时采取措施予以整改,确保整改到位。
3. 对安全生产检查中发现的问题,对相关责任人进行责任追究。
五、事故报告与处理1. 事故发生后,立即向企业负责人报告,并启动应急预案。
2. 依法依规进行事故调查处理,查明事故原因,追究相关责任。
3. 事故处理后,总结经验教训,制定防范措施,防止类似事故再次发生。
电泳车间安全操作规程

电泳车间安全操作规程引言概述:电泳车间是一种常见的工业车间,用于进行电泳涂装工艺。
在电泳车间进行作业时,必须严格遵守安全操作规程,以确保工作人员的人身安全和车间设备的正常运行。
本文将详细阐述电泳车间安全操作规程的五个大点,包括个人防护、设备操作、材料使用、紧急情况处理和车间清洁。
正文内容:1. 个人防护1.1 穿戴防护服:工作人员应穿戴符合安全要求的防护服,包括工作服、手套、鞋子等,以保护身体免受化学物质的侵害。
1.2 戴防护眼镜和口罩:在操作过程中,工作人员应戴上防护眼镜和口罩,以防止涂料飞溅或吸入有害气体。
1.3 使用防护手套:工作人员应选择适合的防护手套,并定期更换,以防止皮肤接触到有害物质。
1.4 保持车间通风:保持车间通风良好,以确保有害气体及时排除,减少对工作人员的危害。
2. 设备操作2.1 熟悉设备操作规程:工作人员在操作电泳设备之前,应仔细阅读并熟悉设备操作规程,确保正确操作。
2.2 检查设备状态:在操作设备之前,工作人员应检查设备的运行状态,如电源、涂料供应、喷涂枪等,确保设备正常运行。
2.3 使用正确的工具和设备:工作人员应使用符合要求的工具和设备进行操作,避免因使用不当的工具导致事故发生。
2.4 定期维护设备:定期对电泳设备进行维护和保养,确保设备的正常运行和安全使用。
3. 材料使用3.1 使用符合要求的涂料:工作人员应使用符合标准的涂料,避免使用过期或质量不合格的涂料,以确保涂装效果和人身安全。
3.2 储存和处理涂料:涂料应储存在专用的储存区域内,避免与其他化学品混存,同时在处理涂料时要注意防火防爆措施。
3.3 控制涂料用量:合理控制涂料用量,避免浪费和过度喷涂,以提高资源利用率和减少环境污染。
4. 紧急情况处理4.1 灭火器和应急装置:车间内应配备足够数量的灭火器和应急装置,并定期检查和维护,以应对突发火灾和其他紧急情况。
4.2 疏散路线和逃生通道:车间内应设置清晰明确的疏散路线和逃生通道,并定期演练,确保工作人员能够迅速疏散。
涂装生产线在生产过程中应当注意的安全事项

涂装生产线在生产过程中应当注意的安全事项。
一、涂装生产线上应注意被涂物件的装挂。
预先通过试浸来设计挂具及物件在涂装生产线上的装挂方式,保证工件在浸涂时处于最佳位置。
被涂物的最大平面应接近垂直,其他平面与水平呈10°-40°角,使余漆的涂装面上能够较流畅地流尽。
二、在涂装生产线上涂装时为防止溶剂在车间内的扩散和尘埃落入漆槽内,浸漆槽应保护起来。
三、大型物件在涂装生产线上浸涂后,应待溶剂基本挥发后再送入烘房。
四、涂装时要不断注意涂料粘度的测定,每班应测定1-2次粘度,若粘度增高超过原粘度的10%,就应及时补加溶剂。
添加溶剂时,应停止浸涂作业。
搅拌均匀后,测定粘度,然后再继续作业。
五、漆膜的厚度主要决定于涂装生产线上物体提升的速率以及漆液的粘度。
在按上述要求控制了漆液的粘度后,涂装生产线应按照漆膜30um左右的最大限速度,根据不同的设备,实验确定合适的提升速率。
按此速率均匀地提升被涂物件。
提升速率快,漆膜薄;提升速率慢,漆膜厚且不均匀。
六、在涂装生产线上进行浸涂操作时,有时造成被涂上、下部的漆膜具有厚度差异,尤其是在被涂物的下边缘出现肥厚积存。
为提高涂层的装饰性,在小批量浸涂时用刷子手工除掉多余积存的漆滴,也可用离心力或静电引力设备除掉这些漆滴。
七、在涂装生产线上浸涂木制件时,注意时间不能太长,以免木材吸入过量的涂料,造成慢干和浪费。
八、加强通风设备,防止溶剂蒸气的危害;注意防火措置的安排和定期检查涂装生产线。
本文由涂装生产线http://www.整理。
电 泳 涂 装 线 作 业 指 导 书
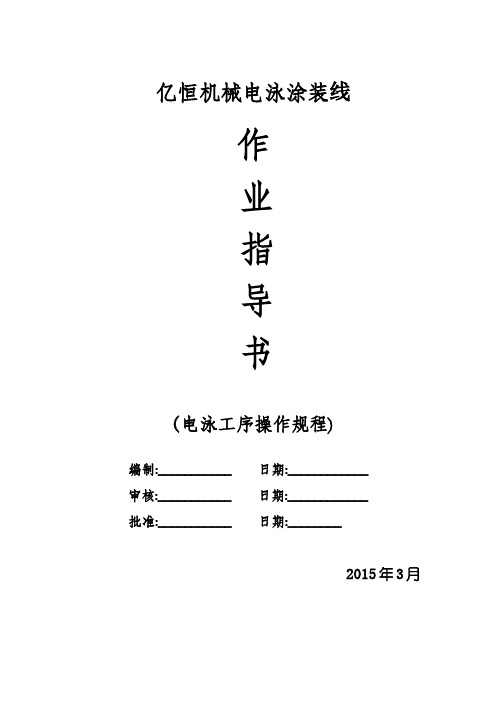
亿恒机械电泳涂装线作业指导书(电泳工序操作规程)编制:___________ 日期:____________审核:___________ 日期:____________批准:___________ 日期:________2015年3月电泳工序操作规程一.总则本工序为阴极电泳涂装生产线,包括预处理、前处理、电沉积、后水洗和烘干下件四个单元,目的为金属件表面做上一层耐腐蚀性耐抗击性装饰性的电泳漆涂层,为了实现正常生产特制定该作业指导书。
二.各单元作业内容、质量要求和注意事项:(一)预处理作业内容:1、检查工件是否存在钣金缺陷及磕碰拉伤,工艺孔或周边有无毛刺。
2、对工件有轻微锈蚀的部位进行打磨去锈处理,油污较重的部位进行擦洗处理;锈蚀、氧化皮较重的工件上酸洗线处理。
3、清除工件内腔与表面的一切杂物。
质量要求:工件内外表面应无锈迹、焊渣、金属屑及其它杂物,无较重的油污。
注意事项:1、工作时按要求使用打磨器具,及时检查打磨器具的使用状态,按规定进行维护和保养;佩戴护目镜或护罩、戴手套,穿长袖工作服,确保作业时的设备安全和人身安全。
2、禁止野蛮作业,防止造成磕碰拉伤。
3、现场工件按品种和生产计划合理放置,保证人流与物流通畅。
(二)前处理1.上件:作业内容:(1)将预清理完毕的工件拉到上件工位。
(2)检查挂具或挂钩挂工件的接触点是否打磨,确保导电性能良好。
(3)检查预清理作业质量(符合工艺手册要求),确认合格后,选择合适的挂具或挂钩挂工件。
(4)做好上件品种及数量记录。
注意事项:(1)挂件时必须检查挂具或挂钩情况和工件挂的部位,保证挂的牢固可靠。
(2)及时清理去除挂具或挂钩上的附漆,确保导电良好。
(3)按要求佩戴安全帽、手套等防护用品;未采取足够防护措施时,不的作业。
2.预脱脂:工作原理:钢铁件表面为了防锈涂上一层油,油的存在,会影响工件涂装的质量。
采用喷淋的方式将药剂喷洒在工件上,附着在工件上的油污被药剂乳化、溶解和分散,而将油污去除。
- 1、下载文档前请自行甄别文档内容的完整性,平台不提供额外的编辑、内容补充、找答案等附加服务。
- 2、"仅部分预览"的文档,不可在线预览部分如存在完整性等问题,可反馈申请退款(可完整预览的文档不适用该条件!)。
- 3、如文档侵犯您的权益,请联系客服反馈,我们会尽快为您处理(人工客服工作时间:9:00-18:30)。
【涂装人必看】车轮电泳涂装线实际生产注意事项
摘要:根据车轮电泳涂装线实际生产中出现的问题,分析了出现问题的可能原因,并根据实际情况提出改进措施,有效解决或控制了所出现的问题,提高了涂装质量。
引言:当前汽车、农用车、家电、轻工产品的种类与生产厂家繁多,各生产厂在车身、零部件的制造工艺过程中,为提高涂装质量、降低成本,大多采用了阴极电泳漆作为涂装与防腐处理的底层涂料,可以说电泳涂装因其涂料利用率高、易于连续作业、自动化程度高等优点已被各行业广泛采用。
电泳涂装可以对工件的内腔、夹缝等部位进行涂装,可以大大提高这些区域的防腐性能。
在车轮涂装工艺上,也是按中高档涂装要求施工,其主要工艺为脱脂、磷化、电泳、面漆(喷粉)/罩光漆等。
但车轮主要是由钢板成型焊接组合,属典型带有夹缝的工件,而板材又主要是热轧板,带有较多的氧化皮,或存在较多的锈蚀等,需要对车轮进行除氧化皮、除锈处理。
在连续式生产线上,常采用酸洗处理工艺。
车轮有夹缝,又需要酸洗,现就这类涂装线上,经常出现的问题给予分析,并提出改进措施,以提高涂装质量,减少涂装弊病。
1 车轮涂装工艺国内某大型车轮生产线上,车轮的涂装工艺为:上件、预脱脂(喷淋)、脱脂、水洗、水洗、酸洗(盐酸)、水洗、水洗、水洗、中和、水洗、表调、磷化、水洗、水洗、
水洗、纯水洗、纯水洗、阴极电泳、0次UF水洗、UF1水洗、UF2水洗、纯水洗、纯水洗、烘烤、下件(转挂面涂线)。
全线采用连续式流水线生产,浸槽为船形槽,前处理、电泳、烘道成循环输送系统,即共用一条输送链。
2涂装中常见问题2.1 车轮夹缝的起泡返锈问题在生产线上,常有车轮夹缝、焊缝等处磷化膜出现返锈,磷化膜不完整现象。
电泳后车轮夹缝里出现漆膜起泡或者有类似漆渣状的物质存在。
另外,电泳后的车轮长时间放在室外后,有时会从车轮夹缝处流出黄色锈水。
在生产中,车轮夹缝越小,越易出现此类问题。
2.1.1原因分析(1)除油不彻底从工艺上看,预脱脂、脱脂两道工序,有喷淋和浸渍,对一般工件是完全可以除去工件上油污的,但从实际效果看,却存在夹缝等处除油不净现象。
这与脱脂剂性能不良有关,如果脱脂剂除了含有几种常规碱性成分外,还是以0P-10乳化剂(清洗性较差)和十二烷基苯磺酸钠为表面活性剂,那么这类脱脂剂品种简单、组合效应不强,缺少高效强渗透剂,所以难以除尽夹缝内油污,也就直接影响磷化效果。
(2)残留酸根离子的影响车轮在酸洗时,由于C1-、SO2-4等无机酸根离子半径很小,极容易渗到车轮夹缝内部,在后道水洗时也较难以清洗干净,这些酸根离子就成为腐蚀的隐患。
碱中和时夹缝内的铁盐残余物就会发生酸碱中和,迅速生成难溶的Fe(OH)2及Fe(OH)3,这些絮状沉淀物把铁盐封闭在夹缝内,加速夹缝腐蚀,同时还会干扰磷化反应进
行,使磷化膜不完整。
最终导致磷化膜多孔、易锈的现象产生。
夹缝内残存的酸根离子还导致工件与阴极电泳漆液界面处,
局部电导率升高,造成局部电解反应加剧并产生大量气体,影响漆膜的附着,使湿漆膜起泡、脱落。
甚至,夹缝处由于电极反应过于剧烈,导致漆膜击穿,漆液凝聚形成类似漆渣状的物质。
(3)磷化方面车轮夹缝里若pH偏高,工件、溶液界面发生酸碱中和反应,一方面阻碍甚至停止磷化初始反应,不易或不能形成磷化膜;另一方面由于金属表面H+的消耗,导致磷酸根各级离解平衡向右移动,磷酸盐沉淀的过饱和度太大,不利于磷化反应进行,导致磷化膜粗大,无结合力,也会造成磷化液稳定性变差。
夹缝里若pH值偏低,引起金属腐蚀的加速、加剧,产生大量的铁离子,导致磷化渣较多,磷化质量变差。
磷化膜与阴极电泳配套性差。
原来生产线上磷化选择是普锌磷化膜,耐碱腐蚀性差,溶解量大(阴极电泳涂装时工件与漆液的界面pH短时内可上升到12~13),加之夹缝内磷化膜结合力差,溶解量就更大,溶解脱落的金属离子存在于漆膜与阴极界面之间,进一步加剧了电解反应,更易引起漆膜起泡甚至击穿。
2.1.2改进措施(1)提高脱脂效果提高脱脂效果,可以从以下几个方面来考虑:(a)工艺方面,可以在最前面增加一道热水喷淋清洗工序,可有效去除工件表面90%以上的机械杂质,减轻脱脂工序的负荷。
另外,这对于车轮夹缝夹带残酸问题也会有一定程度的改善;(b)选择优化脱脂剂品种。
根据脱脂剂各
组分的不同作用,适当调整配比,并适当减少偏硅酸钠含量(它的清洗性差,遇酸形成难以洗掉的硅胶,危害极大)。
充分发挥表面活性剂的组合效应,增添JFC渗透剂(渗透性好)、TX—15乳化剂(亲水性强),可最大限度地除尽夹缝内油污;(c)加强对脱脂槽液的管理。
脱脂液有效浓度以游离碱度来控制,但不能单凭游离碱来判断脱脂液的效果,因为尽管碱度不降低,但表面活性剂的有效浓度也会损失或失效,所以有时会出现碱度
正常而除油效果不好的现象。
因此除需要每天补加脱脂剂外,还需定期换槽。
换槽时将二次脱脂液继续作为预脱脂液用,
重新配二次脱脂液,这样既提高脱脂液的利用率,又能使脱脂液始终保持最佳状态。
同时生产中,严格按工艺要求对脱脂温度、时间等参数进行控制。
(2)加强对工件脱脂后的水洗加强脱脂后的水洗,经常更新水洗用水,防止水洗槽内的污物对工件造成二次污染,同时也要防止工件在工序间出现返锈现象。
(3)酸洗液的选择常用的酸洗液有盐酸、磷酸、硫酸等。
经过现场实验验证,采用硫酸除锈时,漆膜起泡率高;盐酸除锈起泡轻微;磷酸除锈最有利。
当然,还应从成本及适应自动化生产线节奏上来综合考虑选用何种酸洗液,但考虑夹缝问题,建议不选择硫酸。
(4)控制中和工序的中和剂浓度在保证能完全中和车轮表面、夹缝等处残留酸液的前提下,尽可能地降低中和剂的浓度,防止碱液残留在车轮夹缝内。
(5)提高表调效果工件的表调效果也要重视,应选择一种优异的表调剂,
可对提高磷化的质量起到良好的辅助作用。
(6)磷化剂的选择与控制提高磷化的质量,提高其防锈性能,控制各项参数,防止磷化膜发花、粗糙、挂灰等问题。
尤其是工件在磷化前出现返锈情况时,更应注意对磷化液游离酸度、酸比、温度等参数的控制。
改善磷化与阴极电泳的配套性。
选择低锌的锌、镍、锰三元系的,且与阴极电泳配套性良好的磷化液品种,可以提高磷化质量及电泳后涂层的整体性能。
(7)加强对夹缝、焊缝等处的人工清洗及清洁为减少工件夹缝、焊缝等处的化学液的残留,工件在进入电泳槽前,可以安排人工用高压干净纯水对夹缝、焊缝等处进行清洗。
同时,建议人工用压缩空气对工件夹缝、焊缝、兜液部位进行吹水,一方面可以减少工件带液对电泳槽液的污染,另一方面也可以减少工件夹缝、焊缝等处涂装弊病的产生。
2.2车轮内局部漆膜不完整问题2.2.1原因分析(1)车轮弧顶处漆膜不完整,主要原因是工件在入槽时弧顶处存在气泡,致使漆液无法电泳上工件。
(2)车轮内侧底部漆膜不完整,主要原因是底部兜液,在进入电泳烘道前没有沥液干净,较多的积水在短时内急剧升温,水液沸腾致使漆膜破损。
另外,在电泳槽入口处,可以在液面下,增加对入槽后工件的增润喷管,以赶走工件弧顶处的气泡。
(2)在车轮进入烘道前,增加人工用压缩空气对工件内的积水进行吹干,一方面可以避免积水造成漆膜弊病,另一方面也可以节约烘道保
温的能耗。
2.3漆膜外观有颗粒、锈渣等异物问题漆膜外观
存在较多的颗粒、锈渣等异物,在进行喷漆(粉)前,不得不用大量的人力对工件进行打磨、清理,提高了生产成本。
2.3.1原因分析由于本线是前处理、电泳同烘道共用一条输送链,而且酸洗用的是盐酸有较强的挥发性,对输送悬链、挂具等产生了较强的腐蚀。
悬链、挂具的锈层脱落,尤其是在烘道内的高温更易造成锈层爆裂,锈层、颗粒就直接影响了漆膜的外观质量。
2.2.2改进措施(1)调整工件上挂的角度,一方面可以设计、改进挂具,另一方面可以充分利用车轮本身的多孔结构,让车轮自身的孔成为工件入槽后的排气孔,这样可以使工件在进槽时不压泡,使工件每个部位都能得到处理。