染整加工降低缩水率的11大方法
面料后整理的20种方法

面料后整理的20种方法导语:面料后整理是面料出厂前的最后工序,也是必不可少的重要流程。
近几年来,面料后整理技术不断从其他技术领域引进借鉴各种新技术(如低温等离子体处理、生物工程、超声波技术、电子束辐射处理、喷墨印花技术、微胶囊技术、纳米技术等),以提高加工深度,获得良好的整理产品。
预缩预缩是用物理方法减少面料浸水后的收缩以降低缩水率的工艺过程。
机械预缩是将织物先经喷汽或喷雾给湿,再施以经向机械挤压,使屈曲波高增大,然后经松式干燥。
拉幅拉幅是利用纤维素、蚕丝、羊毛等纤维在潮湿条件下所具有的可塑性,将面料幅宽逐渐拉阔至规定尺寸进行烘干,使面料形态得以稳定的工艺过程,也称定幅整理。
上浆上浆是指面料浸涂浆液并烘干以获得手感厚实和硬挺效果的整理过程。
热定型热定型是使热塑性纤维及混纺或交织物形态相对稳定的工艺过程,主要用于受热后易收缩变形的锦纶或涤纶等合成纤维及其混纺物的加工。
经热定型的面料,能提高尺寸稳定性,手感较为硬挺。
增白增白是利用光的补色原理增加纺织品的白度的工艺过程,又称加白。
增白方法有上蓝和荧光增白两种。
轧光、电光和轧纹轧光是利用纤维在湿热条件下的可塑性将面料表面轧平或轧出平行的细密斜纹,以增进织物光泽的工艺过程。
平轧光是由硬辊和软辊组成硬轧点,面料经轧压后,纱线被压扁,表面光滑,光泽增强、手感硬挺。
软轧光是由两只软辊组成软轧点,面料经轧压后,纱线稍扁平,光泽柔和、手感柔软。
电光是使用通电加热的轧辊对面料轧光。
轧纹是由刻有阳纹花纹的钢辊和软辊组成轧点,在热轧条件下,面料可获得呈现光泽的花纹。
磨绒、磨毛用砂磨辊(或带)将面料表面磨出一层短而密的绒毛的工艺过程称为磨绒,又称磨毛,磨毛整理能使经纬纱同时产生绒毛,且绒毛短而密。
起毛起毛是用密集的针或刺将织物表层的纤维剔起,形成一层绒毛的工艺过程,又称拉绒整理,起毛主要用于粗纺毛织物、腈纶织物和棉织物等。
绒毛层可以提高面料的保暖性,改善外观并使手感柔软。
最常见的纺织面料缩水率及影响因素

书山有路勤为径;学海无涯苦作舟最常见的纺织面料缩水率及影响因素缩水是纺织品在一定状态经过洗涤、脱水、干燥等过程发生长度或宽度变化的一种现象。
缩水程度涉及不同种类的纤维、织物的结构、织物加工时所受之不同外力作用等等。
织物的缩水率是指织物在洗涤或浸水后织物收缩的百分数。
缩水率最小的是合成纤维及混纺织品,其次是毛织品、麻织品、棉织品居中,丝织品缩水较大,而最大的是粘胶纤维、人造棉、人造毛类织物。
客观的讲,全棉面料多少都存在着缩水褪色的问题,关键是后面的整理。
所以一般家纺的面料都是经过预缩处理。
值得注意的是经过预缩处理不等于不缩水,而是指缩水率控制在国标3%~4%以,内衣料尤其是天然纤维的衣料会缩水。
因此,在选购衣料时,除了对织物的质量、色泽、花型进行挑选外,对织物的缩水率也应当有所了解。
纤维及织缩的影响纤维本身吸水后,会产生一定程度的溶胀。
通常纤维的溶胀都是各向异性的(锦纶除外),即长度缩短,直径增大。
通常把织物下水前后的长度差与其原长的百分比称为缩水率。
吸水能力越强,溶胀越剧烈,缩水率越高,织物的尺寸稳定性越差。
织物本身的长度与所使用的纱(丝)线长度是不同的,通常用织缩率来表示两者的差异。
织缩率(%)= [纱(丝)线长度-织物长度] / 织物长度织物在下水后,由于纤维本身的溶胀,使织物长度进一步缩短,产生缩水率。
织物的织缩率不同,其缩水率的大小就不同。
织物本身的组织结构及织造张力不同,其织缩率就不同。
织造张力小,织物紧密厚实,织缩率大,织物的缩水率就小;织造张力大,织物就疏松轻薄,织缩率小,织物专注下一代成长,为了孩子。
棉针织物的防缩

针织物整理的目的是发挥针织物或给予针织物以新的性能,以满足人们的需要。
根据加工的性质,可将整理工艺分为二大类:一类为物理机械整理、防缩、起绒、热定型。
另一类为化学整理如树脂整理,特殊整理。
一、棉织物的防缩整理1、棉针织物缩水:在染整加工中,织物受到拉伸积累形变。
如果用这种积累形变的针织坯布缝制成衣,则一经水洗,织物积累的形变,就要回缩,就会发生不合比例的尺寸改变。
1.1 为了避免棉针织物缩水,可设想有两个途径a、理想流程:理布→缝头→常温溢流机染色→松式烘干机(无张力)→长规程(十节)开幅定型→无张力打卷机(或落布折叠包装)b、强迫回缩:润湿的织物受到振荡,施加相反的力,强迫织物回缩,才能使织物线圈恢复到理想的空间结构。
达到稳定产状态,然后维持这一状态进行烘干使之固定下来。
实验得知:回潮4% 细罗纹针织物在室温振动25分钟。
其收缩率仅为可回缩量的8%,而100%浸湿后在热空气中,振动20分钟,再室温振动5分钟,则回缩率可达67%。
2、防缩工艺及设备2.1 防缩工艺1:热定型防缩法,棉针织物不能采用。
2.2 防缩工艺2:棉纤维浓碱液和张力下可进行重整排列,以稳定其尺寸即所谓丝光处理。
2.3 机械防缩法:利用专门设备强迫织物预先回缩的方法。
a、机械防缩设备:按纵向强迫回缩的预缩机;按横向伸展预缩机b、超喂工艺:超喂湿扩幅,超喂烘干超喂预缩,超喂定型二、棉针织物的缩水率问题1、缩水率的测定1.1 掌握织物缩水率的测试方法及了解织物收缩原因。
1.2 仪器:水箱 M988型织物缩机,针织物2±R,量尺、缝线、铅笔。
1.3 实验程序(晾干缩水率)a、仪器与工具:M988型织物缩水机,转速500±20r/min 容量为40L,量尺。
b、试验条件:试液为清水,温度为45±2℃,浴比1:50。
试验时间:棉和合纤织物为30分钟。
+ + ++ + ++ + +c、试样准备:取样,需经热定型后24h,距布端2-5米处,数量不得少于2块。
怎样降低缩率

降低针织面料缩水率的方法(1)在针织物炼漂过程中尽量减小张力。
( 2)在针织物染整加工过程中,凡是湿布烘干都是尽量施松张力 降低伸长避免门幅过度窄缩 如果是开幅连烘的机台在开幅后要加装小的容布箱再穿进布架以避免开幅与轧水间张力过大。
(3)在针织物丝光过程中,要掌握扩幅张力要保持坯布的幅宽注意控制纬向张力。
(4)各道工序的平洗机导布棍,轧棍、烘筒应加强维修保证平整光洁。
避免张力放松时起皱水槽中的导辊要运转自如 同一机台前后轧辊烘筒的线速度相差不应太大 经向张力掌握布不拖地为准在长台的分段过程中应有松紧调节开降架装置或分段传动调节装置以控制张力的大小。
( 5)丝光后的产品应严格控制后道加工过程中的张力因为丝光后再伸长经向缩水率在实际生产操作中可以在各道工序中制定半制品幅宽指标在各机台的去布处于以测量考核 后序要对前工序进行验收保证半制品应有的幅宽。
( 6)对于一些机械运动张力需要人工控制张力。
严格工艺操作 加强工艺操作 加强机械清洁减小运转张力有效的降低织物的缩水率。
(7)加强对丝光加工工艺条件的检查 有条件的的染厂可以用直辊和布铗结合丝光。
(8)经向缩水率较大的品种:如卡其、华达呢府绸织物要进行预缩处理、降低缩水率。
在这些品种在紧式加工中。
仅依机械上放松张力 则最好的缩水率也高达4%左右 这一缩率宜采用预缩的办法来进一步降低 产品经过预缩处理后不但缩水率降低了。
同时还可以获得较好的手感 纹路清晰光泽柔和。
(9)对于纬向缩水率较大品种 有的由于坯布幅宽不合理 即使合理的加工条件也仍有较大的纬向缩水率加工条件差的缩水率更大 必须采取进一步改进措施丝光品种要保证落布幅宽达到要求。
此外还需要在坯布规格上加以改进 在不增加成本或少增加成本条件下 将坯布幅宽放宽 以保证纬向缩水率降到要求范围内。
(10)对于涤棉合纤混纺织物要抓好定性丝光工序工艺及操作可较好控制缩水率关于测缩率的方法先取1米长的面料,然后分别在面料的经向纬向上做好标记,一个角做2组标记,这样一共是4组标记一共是8个标记点,然后用尺分别量出经向标记点之间的距离和纬向标记点的距离,然后将布放入30±3°的温水中浸泡10分钟,取出布把布烘干然后在测量经纬向之间的距离,然后进行计算,计算的公式是(洗涤前距离-洗涤后距离)/洗涤前距离×100%,就能得到缩率。
布料为什么会缩水?如何减少缩水幅度?

布料为什么会缩水?如何减少缩水幅度?收缩水率和面料还有织物组织结构有关系:天然纤维如棉、毛、丝、麻的吸湿性相对较大,故缩水率也大;而丙纶、涤纶等化学纤维的吸湿性小,故缩水率也小。
织物结构的紧密、稀松也会影响其缩水程度,稀松结构的衣料,一般较紧密结构的缩水率大所以想买不缩水的衣服是不可能的而且尽量不要因为缩水率的原因买纯化纤的衣服,现在还是全棉的跟全羊毛的舒服。
但是注意点就可以减少缩水啦:1洗衣是尽量少加洗衣粉或洗衣液,适当用些金纺等柔软剂,会缩的少些。
2洗之前用淡盐水泡半个小时,然后再用凉水清洗,即可;对于已经缩水的衣服,可以将衣服套在大纸板上撑开,然后再用熨斗一熨,衣服可恢复原状。
(不建议用纸板撑哦,容易让衣服损坏或者变形)3干洗4缩水厉害的,看面料可以用蒸汽熨烫。
织物缩水机理织物的缩水问题,通常是经向缩水较为严重。
这主要与它们在染整加工过程中,经向经常处于紧张状态有关。
棉织物在加工过程中,由于纤维和纱(线)受到拉伸,特别在潮湿条件下,更易发生伸长,如果维持这种拉伸状态进行干燥,该状态就会被暂时定型,导致“干燥定型”形变,而存在着内应力。
当这种织物再度润湿时,由于内应力松弛,使纤维和纱(线)的长度缩短,而构成织物缩水。
但是根据对棉织物的伸长率和缩水率的测定,发现它们之间并无一一对应的关系,同时发现织物中具有正常捻度纱的缩水率很少超过2%,而棉布的缩水率有时却可高达10%。
显然,仅从纤维和纱的内应力松弛并不能说明棉布的缩水现象。
为了进一步弄清楚棉布的缩水机理,就有必要分析纤维、纱和织物在水中尺寸变化的情况。
棉纤维吸湿以后的溶胀异向性,已为大家所熟知,如果纤维中无内应力,即不具有“干燥定型”形变时,长度非但不会缩短,相反还要增长一些。
那么,如果纤维中存在着“干燥定型"形变,润湿后,长度将发生怎样的变化?表2—2列举了具有不同“干燥定型”形变的棉纤维,在再度润湿和干燥后的长度收缩情况。
可以看出“干燥定型”形变大的纤维,在再度润湿后的长度收缩也较多,但形变并不能全部消失。
防缩处理

防缩整理第一节引言经过染整加工后已干燥的织物,如果在松弛状态下再被水润湿时,往往会发生比较明显的收缩,这种现象称为缩水。
通常以织物按规定方法洗涤前后的经向或纬向的长度差,占洗涤前长度的百分率,来表示该织物的经向或纬向缩水率。
若用尺寸尚未稳定(也称为具有潜在收缩)的织物做成服装,经过洗涤,由于发生一定程度的收缩,会导致服装变形和走样,给使用者带来不少的困难和损失。
因此,织物的缩水现象早已受到人们的注意。
有些织物,除了有一般的缩水现象外,在一定的条件下洗涤时,由于机械作用,纤维会产生特殊的蠕动而相互纠缠,并使织物缩成紧密状态,这种收缩称为毡缩,通常可以面积变化的百分率来表示。
不同纤维制成的织物,它们的收缩情况不完全相同。
例如,某些毛织物不但在初次洗涤中,具有较大的收缩(称为初次收缩),而且,经过多次洗涤后,还会继续发生很大的收缩(称为后续收缩)。
棉和麻纤维织物的初次收缩虽然有时较大,但它们的后续收缩都不很高。
这些现象反映了不同纤维织物的收缩机理是不完全相同的。
有的可能是由于缩水和毡缩这两方面的因素所造成,也有的可能是其中之一。
羊毛织物除了具有一般的缩水现象外,还容易生毡缩,粘胶纤维织物也发现有类似的现象,纤维素纤维与合成纤维的混纺织物,经过热定型后,其缩水问题远不如纯纤维素纤维织物严重,这是由于大部分合成纤维的吸湿性较低的缘故。
此外,即使是由相同的纤维制成的织物,它们的收缩情况还与纱和织物的结构以及织物经过的加工过程有关。
本章主要讨论纤维素纤维织物缩水的机理和防缩整理方法以及毛织物的防毡缩整理。
第二节织物缩水机理织物的缩水问题,通常是经向缩水较为严重。
这主要与它们在染整加工过程中,经向经常处于紧张状态有关。
棉织物在加工过程中,由于纤维和纱(线)受到拉伸,特别在潮湿条件下,更易发生伸长,如果维持这种拉伸状态进行干燥,该状态就会被暂时定型,导致“干燥定型”形变,而存在着内应力。
当这种织物再度润湿时,由于内应力松弛,使纤维和纱(线)的长度缩短,而构成织物缩水。
染厂后整理技术(定型)
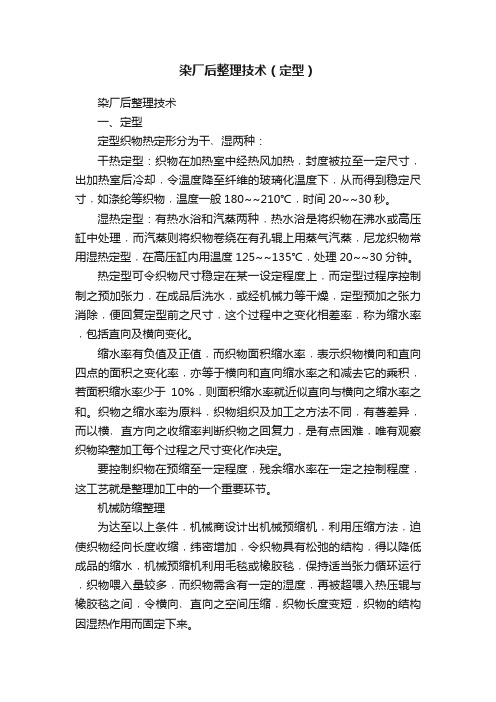
染厂后整理技术(定型)染厂后整理技术一、定型定型织物热定形分为干﹑湿两种:干热定型:织物在加热室中经热风加热﹐封度被拉至一定尺寸﹐出加热室后冷却﹐令温度降至纤维的玻璃化温度下﹐从而得到稳定尺寸﹐如涤纶等织物﹐温度一般180~~210℃﹐时间20~~30秒。
湿热定型:有热水浴和汽蒸两种﹐热水浴是将织物在沸水或高压缸中处理﹐而汽蒸则将织物卷绕在有孔辊上用蒸气汽蒸﹐尼龙织物常用湿热定型﹐在高压缸内用温度125~~135℃﹐处理20~~30分钟。
热定型可令织物尺寸稳定在某一设定程度上﹐而定型过程序控制制之预加张力﹐在成品后洗水﹐或经机械力等干燥﹐定型预加之张力消除﹐便回复定型前之尺寸﹐这个过程中之变化相差率﹐称为缩水率﹐包括直向及横向变化。
缩水率有负值及正值﹐而织物面积缩水率﹐表示织物横向和直向四点的面积之变化率﹐亦等于横向和直向缩水率之和减去它的乘积﹐若面积缩水率少于10%﹐则面积缩水率就近似直向与横向之缩水率之和。
织物之缩水率为原料﹐织物组织及加工之方法不同﹐有著差异﹐而以横﹑直方向之收缩率判断织物之回复力﹐是有点困难﹐唯有观察织物染整加工每个过程之尺寸变化作决定。
要控制织物在预缩至一定程度﹐残余缩水率在一定之控制程度﹐这工艺就是整理加工中的一个重要环节。
机械防缩整理为达至以上条件﹐机械商设计出机械预缩机﹐利用压缩方法﹐迫使织物经向长度收缩﹐纬密增加﹐令织物具有松弛的结构﹐得以降低成品的缩水﹐机械预缩机利用毛毯或橡胶毯﹐保持适当张力循环运行﹐织物喂入量较多﹐而织物需含有一定的湿度﹐再被超喂入热压辊与橡胶毯之间﹐令横向﹑直向之空间压缩﹐织物长度变短﹐织物的结构因湿热作用而固定下来。
进行预缩前﹐织物需给湿令纤维柔性增大﹐压缩控制于胶毯厚度和曲率变化大小﹐经此工序织物再洗水的缩率可降低至1%﹐手感亦较好。
控制缩水率的方法要多方面进行才能获得预期效果。
(1) 织物设定之规格是否符合基本之要求。
(2) 纱线之种类及缩率之变化。
染整问题总结

染整问题总结引言染整是纺织行业中重要的一个环节,主要负责将纱线、面料等进行染色、整理和处理,使其达到预期的色彩、质地和外观效果。
然而,在染整过程中经常会出现一些问题,影响产品质量和生产效率。
本文将对染整问题进行总结和分析,希望能够帮助相关从业人员尽快解决问题。
问题一:色差问题在染整过程中,色差是一个常见的问题。
染色后的纱线或面料与预期色彩存在一定的偏差,造成产品的色彩不稳定或不一致。
产生色差的原因可以归结为以下几点:1.配方不准确:染色配方中的染料浓度、PH值、时间等参数可能存在误差,导致染色结果与预期不符。
2.染色条件不合适:温度、湿度、搅拌速度等条件对染色结果有重要影响,不合适的条件可能导致色差问题。
3.染料质量问题:染料的质量差异也会导致染色结果不稳定,有些染料可能存在色牢度不高的问题,容易褪色或变色。
4.染色工艺控制不当:染色过程中搅拌、上浆、漂洗等环节的控制不当也会产生色差。
解决色差问题的方法包括加强配方管理,严格控制染色条件,选择高质量的染料和改进染色工艺等。
问题二:退色问题退色是指染色后的纱线或面料出现褪色现象,使得产品的颜色失去原有的鲜艳度。
退色的原因主要有以下几点:1.染料固定不牢:染料在染色后未完全固定在纤维上,容易在后续的使用或洗涤过程中褪色。
2.染色不均匀:染色过程中染料的分散均匀程度不够,导致染色结果不稳定,在使用或洗涤后容易出现部分褪色的情况。
3.织物质量问题:如果面料质地不均匀或存在质量问题,染色后容易出现褪色。
解决退色问题的方法包括加强染料固定性能的测试和控制,改进染色工艺,选择质地均匀的面料等。
问题三:尺寸变化问题在染整过程中,纱线和面料的尺寸变化是一个常见的问题。
尺寸变化指的是纱线或面料在染整过程中发生的收缩或伸展现象,导致最终产品的尺寸与预期不符。
尺寸变化的原因主要有以下几点:1.温度影响:纱线或面料在高温下会发生收缩,而在低温下会发生伸展,染色过程中的温度变化可能导致尺寸变化。
亚麻防缩整理
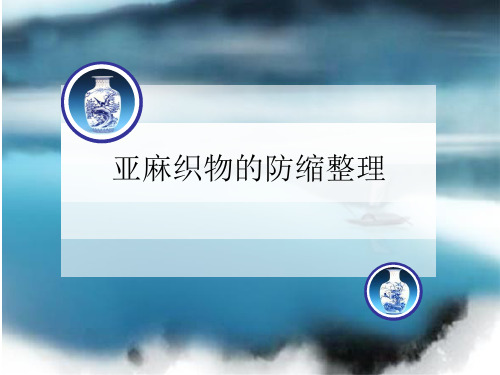
2 防, 经过洗涤,由于发生一定程度的收缩, 会导致服装变形走样,因此织物的防缩 整理在稳定织物的尺寸稳定性方面尤为 突出。
亚麻织物的缩水机理
织物是由经纱和纬纱交织而成的,经纱 纬纱起伏较大,表明它们的织缩较大。当 亚麻织物润湿后,其结构发生变化,这是 导致织物缩水的主要原因。 注意与缩水率比较 织缩=(L1-L2)/L2 LI为纱线长度L2为织 成织物后长度
当纱线处于自由状态时,纤维吸湿导致纤维 直径变大,纤维必然要调整其在纱线中的位置 和姿态来适应变化。 在没有外力作用的情况下,经纱不可能 自动增加长度,也不可能通过解捻来增加 长度,同时纬纱之间由于交织助力,也不 能有较大的滑移运动,只能通过经纱间距 离的缩短,来满足纬纱绕经纱的行程不变, 从而导致织物宏观上长度的减小
防缩方法及原理
亚麻织物防缩处理的基本原理是在织物 成为成品前,采用一定的机械处理,减小 织物的内应力,增加织物的织缩,使织物 具有更为松弛的结构,消除织物潜在收缩 的趋向。 经过这种机械整理后的织物,不但干燥 定形的形变减小,而且织物在润湿后发生 溶胀时,由于经纱与纬纱之间留有足够的 余地或空隙,便不会引起织物径向长度的 缩短和纬向方向的收缩。
亚麻织物的防缩整理
亚麻织物的防缩整理
概况 亚麻织物的缩水机理 防缩方法及原理 防缩整理设备
概况
衡量缩水 1 定义 程度 缩水:经过染整加工并干燥的织物,如 的指标
果在松弛的状态下再度被水润湿的时,会 发生明显的收缩。 织物的缩水率通常以织物按照规定方法 洗涤前后径向(纬向)的长度差,占洗涤 前长度的百分率表示。径向缩水率,纬向 缩水率。
防缩整理设备
亚麻厂目前采用的防缩机主要有橡皮式压 缩式防缩机和毛毯式压缩式防缩机。
[转载]织物缩水、起皱的原因和处理方法
![[转载]织物缩水、起皱的原因和处理方法](https://img.taocdn.com/s3/m/62185e16a7c30c22590102020740be1e650ecc4a.png)
[转载]织物缩水、起皱的原因和处理方法织物缩水、起皱的原因和处理方法作者:冷姿态_1、织物缩水的原因织物被水浸湿或洗涤干燥后,经纬线出现收缩现象,织物的尺寸发生变化,这就叫缩水。
通常造成织物缩水的主要原因有:⑴纤维因素各种纤维织物在纺纱、织造、染色和整理过程中,都要受到不同程度的拉伸力的作用,从而使经纬纱线产生伸长变形,其中一部分变形即使很长时间仍不能恢复,这样织物内部残留的部分内应力变形成隐性的收缩力。
当织物在被水浸湿后,水分子进入纤维内部和纤维之间,使纤维处于自然状态,促使弹性变形恢复,织物就出现了缩水现象。
不同纺织纤维其缩水程度也不相同,一般吸湿性比较大的纤维,由于吸水纤维膨胀,直径增大,长度缩短,便发生织物面积变形收缩。
特别是羊毛织品,由于羊毛纤维表面存在鳞片结构,在热水中受到不规则机械力作用,引起毛纤维间相互滑运,由于顺、逆鳞片方向运动摩擦因数间的差异,导致毛纤维发生向纤维尖端方向单向运动由此引起纤维缠结,使纤维密度提高,织物延伸性和表面积减少,最后达到纤维间不能发生相对运动的程度,这种情况成为羊毛的毡缩。
而且这种变化是不可逆的。
因此羊毛织物不宜用水洗。
⑵密度因素在许多面料中,纱线密度不同,缩水性能也不一样。
密度高的织物如华达呢、卡其等经纱排列的密而紧,在受湿热时,经纱没有多大膨胀的余地,这样纬纱的收缩率增加不大,缩水率就小;纬密度较稀的织物,在受湿热时因其排列稀松而可以充分膨胀,使经纱迅速增加曲折度,其缩水情况就会较重。
⑶燃料的因素衣物面料在整理过程中投入的浆料多,面料的缩水率就高。
经上浆工艺处理的衣物面料,其曲折度降低而挺括性增强,但经水洗后,上面的浆料洗掉,纤维空隙增大,其吸水量和曲折度也随之变大,从而使缩水率也增大。
⑷工艺因素织物面料在染整加工过程中,包括织物整烫后,都会不同程度地受到一定的张力作用,引起织物伸长。
但这种伸长是暂时的,一旦织物再次下水,就会在水的溶涨作用下,失去外力造成的紧张状态,伴随着这种变化,纤维也会出现相应的回缩,引起织物的缩水。
染整工艺中染后整理问题及助剂的选用
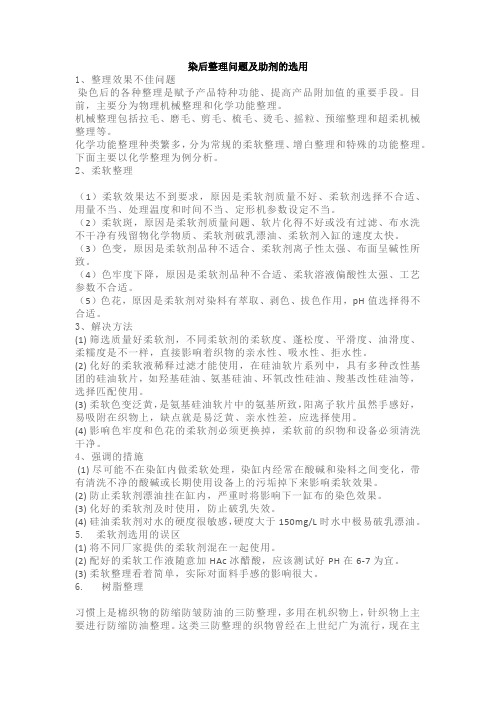
染后整理问题及助剂的选用1、整理效果不佳问题染色后的各种整理是赋予产品特种功能、提高产品附加值的重要手段。
目前,主要分为物理机械整理和化学功能整理。
机械整理包括拉毛、磨毛、剪毛、梳毛、烫毛、摇粒、预缩整理和超柔机械整理等。
化学功能整理种类繁多,分为常规的柔软整理、增白整理和特殊的功能整理。
下面主要以化学整理为例分析。
2、柔软整理(1)柔软效果达不到要求,原因是柔软剂质量不好、柔软剂选择不合适、用量不当、处理温度和时间不当、定形机参数设定不当。
(2)柔软斑,原因是柔软剂质量问题、软片化得不好或没有过滤、布水洗不干净有残留物化学物质、柔软剂破乳漂油、柔软剂入缸的速度太快。
(3)色变,原因是柔软剂品种不适合、柔软剂离子性太强、布面呈碱性所致。
(4)色牢度下降,原因是柔软剂品种不合适、柔软溶液偏酸性太强、工艺参数不合适。
(5)色花,原因是柔软剂对染料有萃取、剥色、拔色作用,pH值选择得不合适。
3、解决方法(1) 筛选质量好柔软剂,不同柔软剂的柔软度、蓬松度、平滑度、油滑度、柔糯度是不一样,直接影响着织物的亲水性、吸水性、拒水性。
(2) 化好的柔软液稀释过滤才能使用,在硅油软片系列中,具有多种改性基团的硅油软片,如羟基硅油、氨基硅油、环氧改性硅油、羧基改性硅油等,选择匹配使用。
(3) 柔软色变泛黄,是氨基硅油软片中的氨基所致,阳离子软片虽然手感好,易吸附在织物上,缺点就是易泛黄、亲水性差,应选择使用。
(4) 影响色牢度和色花的柔软剂必须更换掉,柔软前的织物和设备必须清洗干净。
4、强调的措施(1) 尽可能不在染缸内做柔软处理,染缸内经常在酸碱和染料之间变化,带有清洗不净的酸碱或长期使用设备上的污垢掉下来影响柔软效果。
(2) 防止柔软剂漂油挂在缸内,严重时将影响下一缸布的染色效果。
(3) 化好的柔软剂及时使用,防止破乳失效。
(4) 硅油柔软剂对水的硬度很敏感,硬度大于150mg/L时水中极易破乳漂油。
5. 柔软剂选用的误区(1) 将不同厂家提供的柔软剂混在一起使用。
染整工艺大全
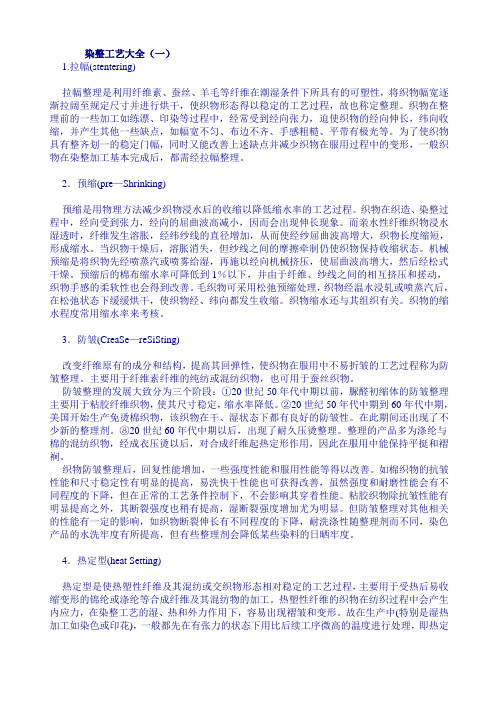
染整工艺大全(一)1.拉幅(stentering)拉幅整理是利用纤维素、蚕丝、羊毛等纤维在潮湿条件下所具有的可塑性,将织物幅宽逐渐拉阔至规定尺寸并进行烘干,使织物形态得以稳定的工艺过程,故也称定整理。
织物在整理前的一些加工如练漂、印染等过程中,经常受到经向张力,迫使织物的经向伸长,纬向收缩,并产生其他一些缺点,如幅宽不匀、布边不齐、手感粗糙、平带有极光等。
为了使织物具有整齐划一的稳定门幅,同时又能改善上述缺点并减少织物在服用过程中的变形,一般织物在染整加工基本完成后,都需经拉幅整理。
2.预缩(pre—Shrinking)预缩是用物理方法减少织物浸水后的收缩以降低缩水率的工艺过程。
织物在织造、染整过程中,经向受到张力,经向的屈曲波高减小,因而会出现伸长现象。
而亲水性纤维织物浸水湿透时,纤维发生溶胀,经纬纱线的直径增加,从而使经纱屈曲波高增大,织物长度缩短,形成缩水。
当织物干燥后,溶胀消失,但纱线之间的摩擦牵制仍使织物保持收缩状态。
机械预缩是将织物先经喷蒸汽或喷雾给湿,再施以经向机械挤压,使屈曲波高增大,然后经松式干燥。
预缩后的棉布缩水率可降低到1%以下,并由于纤维、纱线之间的相互挤压和搓动,织物手感的柔软性也会得到改善。
毛织物可采用松弛预缩处理,织物经温水浸轧或喷蒸汽后,在松弛状态下缓缓烘干,使织物经、纬向都发生收缩。
织物缩水还与其组织有关。
织物的缩水程度常用缩水率来考核。
3.防皱(CreaSe—reSiSting)改变纤维原有的成分和结构,提高其回弹性,使织物在服用中不易折皱的工艺过程称为防皱整理。
主要用于纤维素纤维的纯纺或混纺织物,也可用于蚕丝织物。
防皱整理的发展大致分为三个阶段:①20世纪50年代中期以前,脲醛初缩体的防皱整理主要用于粘胶纤维织物,使其尺寸稳定,缩水率降低。
②20世纪50年代中期到60年代中期,美国开始生产免烫棉织物,该织物在干、湿状态下都有良好的防皱性。
在此期间还出现了不少新的整理剂。
纺织加工中的面料缩水和变形控制

纺织加工中的面料缩水和变形控制随着人们对服装品质的要求越来越高,纺织加工中的面料缩水和变形控制也变得越来越重要。
面料缩水和变形是影响服装质量和舒适度的主要因素之一,因此这两个问题必须得到充分的控制。
本文将详细介绍面料缩水和变形的原因、影响、控制方法等方面的内容。
一、面料缩水的原因及影响面料缩水是指面料在水洗或湿润状态下发生尺寸变化的现象。
主要原因包括纤维收缩、松弛、损伤和纱线扭曲等。
其中,纤维和纱线的收缩率是面料缩水的主要因素。
纤维收缩率和纱线收缩率不同,根据织物的组织结构、纱线的织法、纤维的形状和长度等不同因素,得到的织物面料缩水率也不同。
一般来说,天然纤维(如棉、羊毛)的缩水率较高,而合成纤维(如尼龙、涤纶)的缩水率较低。
当面料缩水率高于设计缩水率时,会导致服装尺寸不合适、形变等问题。
面料缩水的影响还包括色牢度、手感和外观。
过高的温度和挤压力会导致面料表面出现白色线条等痕迹,严重的情况会破坏面料的整体外观。
此外,面料的缩水也会影响服装的色牢度和手感。
综上所述,控制面料缩水是保证服装品质和舒适度的关键。
下面我们将介绍如何控制面料缩水。
二、控制面料缩水的方法1. 选用合适的面料在选择面料时,应该考虑面料的组织结构、纤维织法和纤维的长度等因素。
对于要求面料缩水率较低的产品,应该选择合成纤维或纤维长度较短的天然纤维。
2. 控制面料的处理温度面料处理温度是影响面料缩水率的关键因素。
面料在处理过程中的温度过高会导致纤维和纱线的过度收缩,从而增加面料的缩水率。
因此,在面料处理过程中应该控制温度,避免过高的温度。
3. 增加面料的拉伸度增加面料的拉伸度可以减少其缩水率。
在面料处理过程中,适当增加面料的拉伸度有助于纤维和纱线的松弛,从而减少面料的缩水率。
当面料被拉伸时,纤维和纱线之间的间隙增大,使得水分能够更加容易地进入到面料内部,从而增加了面料的水分吸收率。
4. 使用缩水率测试仪在面料加工过程中,使用缩水率测试仪可以有效地测量面料的缩水率。
解决产品缩水的参考方案

解决产品缩水的参考方案
在生产中经常会遇到产品收缩变形大,表面有凹陷,内部有气泡,缩孔等现象。
我们生产的耳勾系列产品中,像APHRODITE EARHOOK 经常出现表面凹陷(表面缩水明显),ARAGORN EARHOOK 的铁线位有气泡等。
产品出现上述问题涉及多方面原因。
就产品本身而言,产品的材料不同,产品各部分厚度不同,产品的成型质量要求导致产品的浇口位置设置局限性大都可能导致上述问题的发生。
从注塑工艺来分析,主要涉及到成型时的原料的成型温度,注射时间,注射压力和注射速度。
在成型温度保证达到,注射时间足够的前提下,产品缩水可能是注射压力和保压压力不够,可以尝试用加大注射压力和保压压力的方法来解决。
注射速度太快容易产生气泡,注射速度太慢又影响产品的充填质量。
针对我们的情况,生产时塑料的成型温度都能保证达到,但往往经过对产品成型参数多次更改调试,却依然会出现上述不良成型现象。
从模具方面入手,我们常用的方法是加大浇口入水位置的尺寸,希望通过这样延迟浇口冷却,使产品的保压效果更
好。
但是这样的做法往往令到产品的浇口入水位置发白,而且效果不是十分理想。
根据国外的一些先进经验,结合我们自己遇到的生产问题,可用下述方法尝试解决,如图1,在设计三板,点浇口模具时,在保证水口出模顺利的前提下,可以适当减小浇口的夹角,从常用的3○-4○改到2○。
在设计浇口时,应注意如图1中所示位置①的尺寸与产品壁厚尺寸相近。
图1 三板模点浇口设计。
学习对于缩水率!你要明白这些…

学习对于缩水率!你要明白这些…无论国际还是国内市场,消费者对服装的尺寸稳定性要求越来越高。
特别是国际市场,对面料不断提出防缩、优级防缩、超级防缩的特殊要求,对印染企业生产,缩水率是一个困扰。
01机械预缩整理用物理方法减少织物浸水后的收缩以降低缩水的整理过程,又称机械预缩整理。
织物在染整过程中经向受到张力,经向的屈曲波高减小,因而会出现伸长现象。
亲水性纤维织物浸水湿透时,纤维发生溶胀,经、纬纱的直径增加,从而使经纱屈曲波高增大,织物长度缩短,形成缩水。
长度缩短与原来长度的百分比称为缩水率。
机械预缩是把织物先经喷蒸汽或喷雾给湿,再施以经向机械挤压,使屈曲波高增大,然后经松式干燥。
预缩后的棉布缩水率可以降低到1%以下,并由于纤维、纱线之间的相互挤压和搓动,织物手感的柔软性也会得到改善。
毛织物可采用松弛预缩处理,织物经温水浸轧或喷蒸汽后,在松弛状态下缓缓烘干,使织物经、纬向都发生收缩。
02设备分类橡胶毯预缩机常用的是三辊式,主要由一定厚度并富有弹性的环状无接缝橡胶毯、喂布辊和表面光滑并可加热的承压辊组成(图1)。
橡胶毯保持适当的张力循环运行,经过喂布辊和承压辊之间,两辊对橡胶毯有一轧点P(图2),织物自轧点P进入承压辊和橡胶毯之间,并随之运行。
橡胶毯包在喂布辊上时其外弧受到延伸(图2中之A),当橡胶毯经过轧点包于承压辊时,原来延伸的外弧即转变为内弧而收缩(图2中之A');此外,橡胶毯进入轧点P时被压薄而伸长,出轧点后在PS段内自行收缩并逐渐恢复到原来厚度,使织物在橡胶毯和承压辊的紧压下,随着橡胶毯一起收缩而取得预缩效果。
三辊预缩机配有给湿、松式烘干装置,可用于棉织物及棉与化纤的混纺织物。
两辊阻滞预缩机主要由喂布辊、阻滞辊和压板刀组成(图3)。
喂布辊表面光滑,运行速度较快。
阻滞辊的橡胶表面硬度较低,运行速度较喂布辊稍慢。
压板的前端安装在进入两辊轧点的附近处。
在预缩过程中,由喂布辊以较快速度将织物喂入,进入轧点时,由于阻滞辊速度较慢以及压板前端的阻力,织物受到挤压而收缩。
如何处理面料的缩水和变形问题
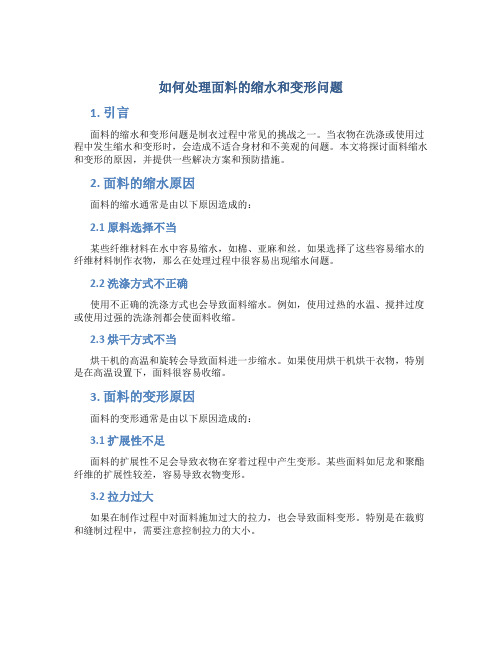
如何处理面料的缩水和变形问题1. 引言面料的缩水和变形问题是制衣过程中常见的挑战之一。
当衣物在洗涤或使用过程中发生缩水和变形时,会造成不适合身材和不美观的问题。
本文将探讨面料缩水和变形的原因,并提供一些解决方案和预防措施。
2. 面料的缩水原因面料的缩水通常是由以下原因造成的:2.1 原料选择不当某些纤维材料在水中容易缩水,如棉、亚麻和丝。
如果选择了这些容易缩水的纤维材料制作衣物,那么在处理过程中很容易出现缩水问题。
2.2 洗涤方式不正确使用不正确的洗涤方式也会导致面料缩水。
例如,使用过热的水温、搅拌过度或使用过强的洗涤剂都会使面料收缩。
2.3 烘干方式不当烘干机的高温和旋转会导致面料进一步缩水。
如果使用烘干机烘干衣物,特别是在高温设置下,面料很容易收缩。
3. 面料的变形原因面料的变形通常是由以下原因造成的:3.1 扩展性不足面料的扩展性不足会导致衣物在穿着过程中产生变形。
某些面料如尼龙和聚酯纤维的扩展性较差,容易导致衣物变形。
3.2 拉力过大如果在制作过程中对面料施加过大的拉力,也会导致面料变形。
特别是在裁剪和缝制过程中,需要注意控制拉力的大小。
3.3 不合适的工艺处理工艺处理不当也是面料变形的原因之一。
例如,使用过热的熨烫温度、不适当的压力和时间等都可能导致面料变形。
4. 处理面料的缩水和变形问题的解决方案4.1 选择合适的面料在制作衣物之前,应根据需求选择合适的面料,避免选择容易缩水和变形的面料。
4.2 遵循正确的洗涤方式在洗涤衣物时,应遵循正确的洗涤方式。
根据面料的特性,选择适当的水温、洗涤剂和洗涤时间,避免面料受到损害和缩水。
4.3 避免过度搅拌在洗衣机中洗涤衣物时,应控制搅拌的力度。
避免过度搅拌导致面料缩水。
4.4 空气干燥或晾晒避免使用高温烘干机,可以选择将衣物晾晒或自然风干。
空气干燥对于避免面料收缩非常重要。
4.5 控制裁剪和缝制过程中的拉力在裁剪和缝制过程中,要注意控制拉力的大小。
染整加工降低缩水率的11大方法【实践经验总结】

染整加工降低缩水率的11大方法【实践经验总结】上期回顾史上最全针织面料常见疵点及原因分析正文每天充电5分钟,可抵学习2小时!染整加工降低缩水率的11大方法1.在炼漂过程中尽量减小张力。
2.在染整加工过程中凡是湿布烘干都是尽量施松张力,降低伸长避免门幅过度窄缩,如果是开幅连烘的机台在开幅后要加装小的容布箱再穿进布架以避免开幅与轧水之间的张力过大。
3.在丝光过程中要掌握扩幅张力要保持坯布的幅宽注意控制纬向张力。
4.各道工序的平洗机导布棍.轧棍,烘筒,应加强维修保证平整光洁.避免张力放松时起皱水槽中的导辊要运转自如,同一机台前后轧辊烘筒的线速度相差不应太大,经向张力掌握布不拖地为准在长台的分段过程中应有松紧调节开降架装置或分段传动调节装置以控制张力的大小。
5.丝光后的产品应严格控制后道加工过程中的张力因为丝光后再伸长经向缩水率在实际生产操作中可以在各道工序中制定半制品幅宽指标在各机台的去布处于以测量考核,后序要对前工序进行验收保证半制品应有的幅宽。
6.对于一些机械运动张力需要人工控制张力.严格工艺操作,加强工艺操作,加强机械清洁减小运转张力有效的降低织物的缩水率。
7.加强对丝光加工工艺条件的检查,有条件的的染厂可以用直辊和布铗结合丝光。
8经向缩水率较大的品种:如卡其,华达呢府绸织物要进行预缩处理.降低缩水率.在这些品种在紧式加工中.仅依靠机械上放松张力,则最好的缩水率也高达4%左右,这一缩率宜采用预缩的办法来进一步降低,产品经过预缩处理后不但缩水率降低了.同时还可以获得较好的手感,纹路清晰光泽柔和。
9.对于纬向缩水率较大的品种,有的由于坯布幅宽不合理,即使合理的加工条件,也仍有较大的纬向缩水率加工条件差的缩水率更大,必须采取进一步的改进措施,丝光品种要保证落布幅宽达到要求.此外还要需要在坯布规格上加以改进,在不增加成本或少增加成本的条件下,将坯布的幅宽放宽,以保证纬向缩水率降到要求范围内。
10.进行树脂整理可降低缩水率并提高弹性(需注意手感)另涂层也可以降低缩水率。
纺织加工中的防缩和防皱工艺
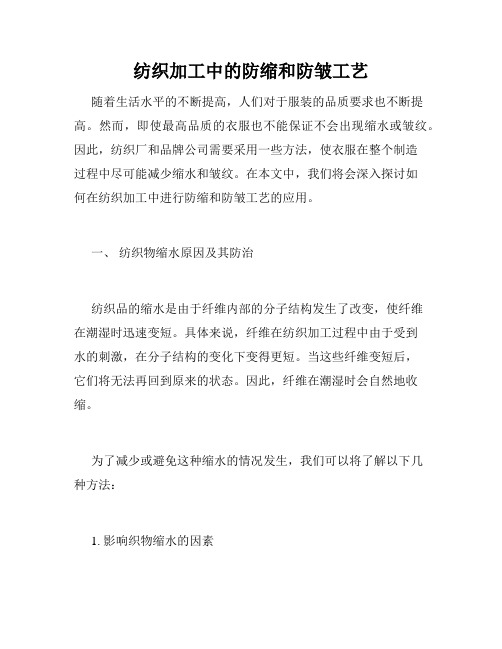
纺织加工中的防缩和防皱工艺随着生活水平的不断提高,人们对于服装的品质要求也不断提高。
然而,即使最高品质的衣服也不能保证不会出现缩水或皱纹。
因此,纺织厂和品牌公司需要采用一些方法,使衣服在整个制造过程中尽可能减少缩水和皱纹。
在本文中,我们将会深入探讨如何在纺织加工中进行防缩和防皱工艺的应用。
一、纺织物缩水原因及其防治纺织品的缩水是由于纤维内部的分子结构发生了改变,使纤维在潮湿时迅速变短。
具体来说,纤维在纺织加工过程中由于受到水的刺激,在分子结构的变化下变得更短。
当这些纤维变短后,它们将无法再回到原来的状态。
因此,纤维在潮湿时会自然地收缩。
为了减少或避免这种缩水的情况发生,我们可以将了解以下几种方法:1. 影响织物缩水的因素在了解如何预防织物缩水之前,我们需要知道织物缩水的因素。
除了接触水以外,织物缩水还有以下因素:1) 热力:当织物在热水中浸泡或经过高温时,纤维会因为受到能量而变短,织物受到收缩的影响。
2) 机械作用:包括洗涤机洗涤、干燥机烘干和高速转动热气套管等。
3) 织物重量:一些太细的面料会因其轻质而易受到影响。
4) 洗涤方式:先洗涤再浸泡,先浸泡再洗涤或分批次洗涤,会对织物缩水产生不同的影响。
2. 使用纤维防缩剂或预缩处理在纺织品制造中,预缩是实现产品尺寸稳定的重要方法。
例如,经过预缩处理的花呢面料在用水洗涤或干洗时不容易缩水。
此外,早期的纤维防缩处理主要使用化学方法,后来多采用高温干燥预缩和微波预缩,一定程度上能够减轻缩水的情况,但是,需要根据实际生产需求进行选择。
3. 加入缩水性小的纤维细纤维材料具有较大的表面较积,更容易被水分子吸附,从而引起缩水。
相反,粗纤维材料因表面较积小,所以不容易受到水分子的影响。
因此,通过加入缩水性小的纤维并控制纤维混合比例可以降低织物缩水的程度。
4. 控制低温和水的使用洗涤织物时,水温要控制在30度以下,因为相对低的水温不会使织物缩水。
此外,在干衣机中,使用中等温度进行干燥也可以减少织物缩水情况的发生。
最常见的纺织面料的缩水知识!

客观的讲,全棉面料多少都存在着缩水褪色的问题,关键是后面的整理。所以一般家纺的面料都是经过预缩处理。
值得注意的是经过预缩处理不等于不缩水,而是指缩水率控制在国标3%-4%以内衣料尤其是天然纤维的衣料会缩水。因此,在选购衣料时,除了对织物的质量、色泽、花型进行挑选外,对织物的缩水率也应当有所了解。
一. 纤维及织缩的影响
纤维本身吸水后,会产生一定程度的溶胀。通常纤维的溶胀都是各向异性的(锦纶除外),即长度缩短,直径增大。通常把织物下水前后的长度差与其原长的百分比称为缩水率。吸水能力越强,溶胀越剧烈,缩水率越高,织物的尺寸稳定性越差。
织物本身的长度与所使用的纱(丝)线长度是不同的,通常用织缩率来表示两者的差异。
织缩率(%)=[纱(丝)线长度-织物长度]/织物长度
织物在下水后,由于纤维本身的溶胀,使织物长度进一步缩短,产生缩水率。织物的织缩率不同,其缩水率的大小就不同。织物本身的组织结构及织造张力不同,其织缩率就不同。织造张力小,织物紧密厚实,织缩率大,织物的缩水率就小;织造张力大,织物就疏松轻薄,织缩率小,织物的缩水率就大。在染整加工中,为了降低织物的缩水率,常采用预缩整理的方式来加大纬密,预先提高织缩率,从而降低织物的缩水率。
三. 一般面料的缩水率为:
棉4%--10%;
化纤4%--8%;
棉涤3.5%--5 5%;
本色白布为3%;
毛蓝布为3-4%;
府绸为3-4.5%;
花布为3-3.5%;
斜纹布为4%;
劳动布为10%;
人造棉为10%。
四. 影响缩水率原因:
1、原材料
织物防缩整理

第十章防缩整理第一节概述经过染整加工的干燥织物,如果在松驰状态下再被水润湿时,往往会发生明显的收缩,这种现象称为缩水。
其缩水程度通常用缩水率来表示:1、缩水率指织物按规定方法洗涤前后的径向或纬向的长度差,占洗涤前长度的百分率。
2、毡缩对于羊毛织物,除了具有一般的缩水现象外,在一定条件下洗涤时,由于机械作用纤维会产生特殊的蠕动而相互纠缠,并使织物缩成紧密状态,这种现象称为毡缩。
此时,通常用面积收缩百分率来表示。
由于纤维性能上的差异,因此不同纤维的织物其缩水情况也是不一样的如:①毛织物:在洗涤时除了具有较大的初次收缩外,而且经多次洗涤后,还会继续发生很大的后续收缩;②棉、麻织物:一般初次收缩较大,但其后续收缩较低;③合成纤维及其混纺织物:由于经过热定型加工,外加其吸湿性能较低,缩水问题不如棉、麻织物那样严重;④粘胶织物:除了具有一般的缩水现象外,有时还易发生毡缩现象;关于织物的收缩,除了纤维本身发生收缩外,还与纱和织物的组织结构及加工过程有关。
第二节织物收水机理织物的缩水,主要是径向缩水较为严重,这与织物在染整加工中径向常处于紧张状态,干燥后织物中的纤维存在内应力有关。
棉布的缩水率有时可高达10%。
为了弄清棉布的缩水机理,必须分析纤维、纱线和织物在水中的尺寸的变化情况。
一、纤维在水中的尺寸变化对纺织纤维而言,吸湿后溶胀,并呈现各向异性即长度和直径的变化率相差较大。
无“干燥定型”形变纤维润湿后的尺寸变化情况如下:由实验结果可知:润湿后纤维的长度和直径都是增长的。
二、纱在水中的尺寸变化情况纱线润湿时,主要表现为纱线的溶胀和长度的收缩,同时也伴有应力松弛。
当纱线处于自由状态时,纤维吸湿导致纤维直径的增大,纤维必然要调整其在纱线中的位置和姿态来适应变化。
由实验结果可知:对于中等捻系数的棉纱,在水中的收缩率一般为1-2%左右。
因此,对于缩水率较大的棉织物的收缩,必然与织物的组织结构有关。
三、织物在水中的尺寸变化织物是由径、纬纱交织而成,当织物润湿后,由于其结构的变化而导致织物收缩:其示意图如右所示:当织物润湿后,纱的直径变大,如果纬纱仍要保持润湿前的间距,那径纱势必要发生一定伸长才能满足。
- 1、下载文档前请自行甄别文档内容的完整性,平台不提供额外的编辑、内容补充、找答案等附加服务。
- 2、"仅部分预览"的文档,不可在线预览部分如存在完整性等问题,可反馈申请退款(可完整预览的文档不适用该条件!)。
- 3、如文档侵犯您的权益,请联系客服反馈,我们会尽快为您处理(人工客服工作时间:9:00-18:30)。
1.在炼漂过程中尽量减小张力。
2.在染整加工过程中凡是湿布烘干都是尽量施松张力,降低伸长避免门幅过度窄缩,如果是开幅连烘的机台在开幅后要加装小的容布箱再穿进布架以避免开幅与轧水之间的张力过大。
3.在丝光过程中要掌握扩幅张力要保持坯布的幅宽注意控制纬向张力。
4.各道工序的平洗机导布棍.轧棍,烘筒,应加强维修保证平整光洁.避免张力放松时起皱水槽中的导辊要运转自如,同一机台前后轧辊烘筒的线速度相差不应太大,经向张力掌握布不拖地为准在长台的分段过程中应有松紧调节开降架装置或分段传动调节装置以控制张力的大小。
5.丝光后的产品应严格控制后道加工过程中的张力因为丝光后再伸长经向缩水率在实际生
产操作中可以在各道工序中制定半制品幅宽指标在各机台的去布处于以测量考核,后序要对前工序进行验收保证半制品应有的幅宽。
6.对于一些机械运动张力需要人工控制张力.严格工艺操作,加强工艺操作,加强机械清洁减小运转张力有效的降低织物的缩水率。
7.加强对丝光加工工艺条件的检查,有条件的的染厂可以用直辊和布铗结合丝光。
8经向缩水率较大的品种:如卡其,华达呢府绸织物要进行预缩处理.降低缩水率.在这些品种
在紧式加工中.仅依靠机械上放松张力,则最好的缩水率也高达4%左右,这一缩率宜采用预缩的办法来进一步降低,产品经过预缩处理后不但缩水率降低了.同时还可以获得较好的手感,
纹路清晰光泽柔和。
9.对于纬向缩水率较大的品种,有的由于坯布幅宽不合理,即使合理的加工条件,也仍有较大的纬向缩水率加工条件差的缩水率更大,必须采取进一步的改进措施,丝光品种要保证落布幅宽达到要求.此外还要需要在坯布规格上加以改进,在不增加成本或少增加成本的条件下,将坯布的幅宽放宽,以保证纬向缩水率降到要求范围内。
10.进行树脂整理可降低缩水率并提高弹性(需注意手感)另涂层也可以降低缩水率。
11.对于T/C合纤混纺织物要抓好定性丝光工序工艺及操作可较好控制缩水率。