铝合金砂型铸造-壳体
ZL系列铸造铝合金的应用
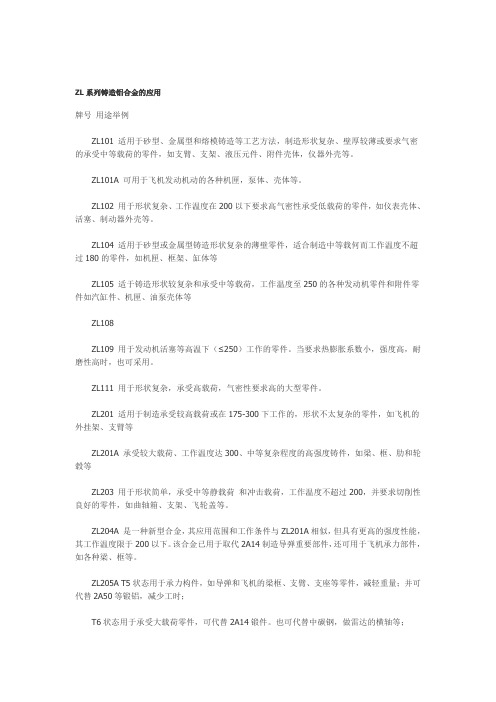
ZL系列铸造铝合金的应用牌号用途举例ZL101 适用于砂型、金属型和熔模铸造等工艺方法,制造形状复杂、壁厚较薄或要求气密的承受中等载荷的零件,如支臂、支架、液压元件、附件壳体,仪器外壳等。
ZL101A 可用于飞机发动机动的各种机匣,泵体、壳体等。
ZL102 用于形状复杂、工作温度在200以下要求高气密性承受低载荷的零件,如仪表壳体、活塞、制动器外壳等。
ZL104 适用于砂型或金属型铸造形状复杂的薄壁零件,适合制造中等载何而工作温度不超过180的零件,如机匣、框架、缸体等ZL105 适于铸造形状较复杂和承受中等载荷,工作温度至250的各种发动机零件和附件零件如汽缸件、机匣、油泵壳体等ZL108ZL109 用于发动机活塞等高温下(≤250)工作的零件。
当要求热膨胀系数小,强度高,耐磨性高时,也可采用。
ZL111 用于形状复杂,承受高载荷,气密性要求高的大型零件。
ZL201 适用于制造承受较高载荷或在175-300下工作的,形状不太复杂的零件,如飞机的外挂架、支臂等ZL201A 承受较大载荷、工作温度达300、中等复杂程度的高强度铸件,如梁、框、肋和轮毂等ZL203 用于形状简单,承受中等静载荷和冲击载荷,工作温度不超过200,并要求切削性良好的零件,如曲轴箱、支架、飞轮盖等。
ZL204A 是一种新型合金,其应用范围和工作条件与ZL201A相似,但具有更高的强度性能,其工作温度限于200以下。
该合金已用于取代2A14制造导弹重要部件,还可用于飞机承力部件,如各种梁、框等。
ZL205A T5状态用于承力构件,如导弹和飞机的梁框、支臂、支座等零件,减轻重量;并可代替2A50等锻铝,减少工时;T6状态用于承受大载荷零件,可代替2A14锻件。
也可代替中碳钢,做雷达的横轴等;T7状态合金用于在腐蚀气氛中工作的承力构件,如代替45号钢制作超高压线路架线中轮。
ZL207 用于制造工作温度达400并要求气密的零件,如飞机空气分配器和电动活门壳体等,可取代铜或钛合金,显著减轻重量,降低成本。
铝合金电机壳低压砂型铸造工艺设计

铝合金电机壳低压砂型铸造工艺设计摘要:近年来,在节能减排和环保的需求下,汽车制造企业的研发重点正在由传统燃料汽车向新能源汽车转移。
铝合金电机壳作为新能源汽车的动力总成核心铸件,结构比较复杂,铸造难度大。
水冷电机壳体的侧壁环绕冷却水套的密封性是产品的重要技术要求,也是产品最大的铸造。
同时,电机壳体上、下端面以及侧壁的缩松也是工艺开发中需要避免的铸造缺陷。
随着计算机技术在铸造领域的迅速发展,通过铸造过程模拟仿真分析模拟可以预测铸造缺陷,评估工艺可行性。
关键词:铝合金电机壳;低压砂型铸造;工艺设计;前言:由于大型薄壁壳体类铸件壁的空间分布无明显规律,有必要在低压铸造设备完备的前提下针对树脂砂或石墨型低压铸造方法进行工艺试验研究,从而铸造成组织致密、尺寸精确的优质铸件这类铸件在核电装备中亦具有重要地位。
一、对象目前,型号弹上产品的壳体类铸件可以分为两大类:①四面体结构;②五面体结构。
四面体壳体铸件长一般为260~280 mm,宽140~150 mm,高120~150 mm,最小壁厚3 mm,最大壁厚10 mm。
在每个侧面的两端都有突出的台肩;要求铸件满足规定的各项技术要求;其材质选用ZL 104或ZL 114A,铸件毛坯重约20 kg;要求铸件不能有裂纹、气孔、缩松、夹杂等铸造缺陷;铸件针孔度要求为三级,局部允许四级。
以往所采用的砂型重力铸造方法不能满足技术要求。
二、铝合金电机壳低压砂型铸造工艺设计1.铸件的浇注位置。
铸件的浇注位置是指浇注时铸件在铸型中的位置。
浇注位置是根据零件的结构特点、尺寸、重量、技术要求、铸造合金特性、铸造方法以及生产车间的条件决定的。
正确的浇注位置应能保证获得健全的铸件,并使造型、造芯和清理方便。
铸件的加工面、主要工作面应尽量放在底部或侧面,以防止这些表面上产生沙眼、气孔、夹渣等铸造缺陷。
因此,根据上述要求和有利于铸件的凝固顺序,以及有利于砂心的定位和稳固支撑、使排气顺畅等的分析,砂箱中铸件数量的确定砂箱中铸件的数量一般要根据工艺要求和生产条件(生产批量及设备的相互要求和配合等)来确定。
各种铸造铝合金牌号的主要特点及应用
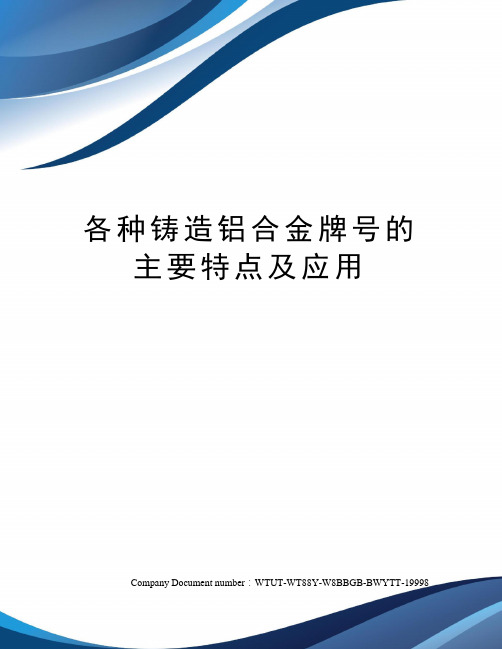
各种铸造铝合金牌号的主要特点及应用Company Document number:WTUT-WT88Y-W8BBGB-BWYTT-19998各种铸造铝合金牌号的主要特点及用途ZL101的特点是成分简单,容易熔炼和铸造,铸造性能好,气密性好、焊接和切削加工性能也比较好,但力学性能不高。
适合铸造薄壁、大面积和形状复杂的、强度要求不高的各种零件,如泵的壳体、齿轮箱、仪表壳(框架)及家电产品上的零件等。
主要采用砂型铸造和金属型铸造。
Zl101A由于是在ZL101的基础上加了微量Ti,细化了晶粒,强化了合金的组织,其综合性能高于Zl101、ZL102,并有较好的抗蚀性能,可用作一般载荷的工程结构件和摩托车、汽车及家电、仪表产品上的各种结构件的优质铸件。
其使用量目前仅次于ZL102。
多采用砂型和金属型铸造。
(ZL101A合金是以ZL101合金为基础严格控制杂质含量,改进铸造技术可以获得更高的力学性能。
铸造性能,耐腐蚀性能和焊接性良好。
用于铸造各种壳体零件,飞机的泵体、汽车变速箱、燃油箱的弯管等)Zl102这种合金的最大特点是流动性好,其它性能与ZL101差不多,但气密性比ZL101要好,可用来铸造各种形状复杂、薄壁的压铸件和强度要求不高的薄壁、大面积、形状复杂的金属或砂型铸件。
不论是压铸件还是金属型、砂型铸件,都是民用产品上用得最多的一个铸造铝合金品种。
Zl104因其工晶体量多,又加入了Mn,抵消了材料中混入的Fe有害作用,有较好的铸造性能和优良的气密性、耐蚀性,焊接和切削加工性能也比较好,但耐热性能较差,适合制作形状复杂、尺寸较大的有较大负荷的动力结构件,如增压器壳体、气缸盖,气缸套等零件,主要用压铸,也多采用砂型和金属型铸造。
Zl105、ZL105A由于加入了Cu,降低了Si的含量,其铸造性能和焊接性能都比ZL104差,但室温和高温强度、切削加工性能都比ZL104要好,塑性稍低,抗蚀性能较差。
适合用作形状复杂、尺寸较大、有重大负荷的动力结构件。
各种牌号铸铝的主要特点及用途
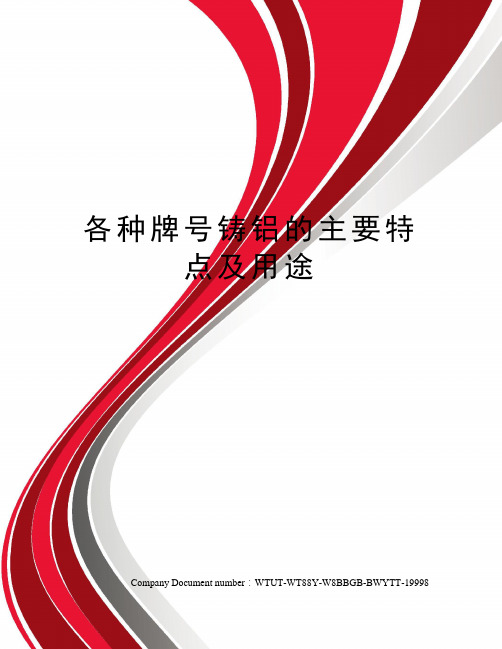
各种牌号铸铝的主要特点及用途Company Document number:WTUT-WT88Y-W8BBGB-BWYTT-19998各种牌号铝合金的主要特点及用途ZL101的特点是成分简单,容易熔炼和铸造,铸造性能好,气密性好、焊接和切削加工性能也比较好,但力学性能不高。
适合铸造薄壁、大面积和形状复杂的、强度要求不高的各种零件,如泵的壳体、齿轮箱、仪表壳(框架)及家电产品上的零件等。
主要采用砂型铸造和金属型铸造。
Zl101A由于是在ZL101的基础上加了微量Ti,细化了晶粒,强化了合金的组织,其综合性能高于Zl101、ZL102,并有较好的抗蚀性能,可用作一般载荷的工程结构件和摩托车、汽车及家电、仪表产品上的各种结构件的优质铸件。
其使用量目前仅次于ZL102。
多采用砂型和金属型铸造。
Zl102这种合金的最大特点是流动性好,其它性能与ZL101差不多,但气密性比ZL101要好,可用来铸造各种形状复杂、薄壁的压铸件和强度要求不高的薄壁、大面积、形状复杂的金属或砂型铸件。
不论是压铸件还是金属型、砂型铸件,都是民用产品上用得最多的一个铸造铝合金品种。
Zl104因其工晶体量多,又加入了Mn,抵消了材料中混入的Fe有害作用,有较好的铸造性能和优良的气密性、耐蚀性,焊接和切削加工性能也比较好,但耐热性能较差,适合制作形状复杂、尺寸较大的有较大负荷的动力结构件,如增压器壳体、气缸盖,气缸套等零件,主要用压铸,也多采用砂型和金属型铸造。
Zl105、ZL105A由于加入了Cu,降低了Si的含量,其铸造性能和焊接性能都比ZL104差,但室温和高温强度、切削加工性能都比ZL104要好,塑性稍低,抗蚀性能较差。
适合用作形状复杂、尺寸较大、有重大负荷的动力结构件。
如增压器壳体、气缸盖、气缸套等零件。
Zl105A是降低了ZL105的杂质元素Fe的含量,提高了合金的强度,具有比ZL105更好的力学性能,多采用铸造优质铸件。
ZL106由于提高了Si的含量,又加入了微量的Ti、Mn,使合金的铸造性能和高温性能优于ZL105气密性、耐蚀性也较好,可用作一般负荷的结构件及要求气密性较好和在较高温度下工作的零件,主要采用砂型和金属型铸造。
常见铸造工艺

常见铸造工艺一、铸造工艺概述铸造是通过将熔化的金属或合金倒入模具中,经过冷却凝固后得到所需形状的工艺。
铸造工艺广泛应用于各个领域,如汽车、航空、船舶、机械、建筑等。
二、常见铸造工艺分类1. 砂型铸造:以石英砂为主要原料制作模具,常用于生产大型和中小型零件。
2. 金属型铸造:采用金属模具进行浇注,可生产高精度和高质量的零件。
3. 压力铸造:利用高压力将液态金属注入模具中,适用于生产复杂形状的零件。
4. 熔蜡模铸造:先制作出蜡模具,然后在蜡模上涂覆陶瓷浆料,并进行干燥和硬化。
最后将蜡模加热蒸发掉,留下空心的陶瓷壳体,再进行浇注。
5. 精密铸造:采用特殊工艺和设备进行生产,可生产高精度和高质量的零件。
三、详细介绍常见铸造工艺1. 砂型铸造(1)模具制作:先根据零件的形状和尺寸制作出模板,然后将模板放入砂箱中,用湿砂将其覆盖。
待湿砂干燥后,将模板取出,留下模具。
(2)浇注:将铝合金或其他金属加热至液态状态,然后倒入模具中。
待金属冷却凝固后,取出零件。
(3)处理:对零件进行去毛刺、打磨等处理。
2. 金属型铸造(1)模具制作:根据零件的形状和尺寸制作出金属模具。
(2)浇注:将液态金属倒入金属模具中。
待金属冷却凝固后,取出零件。
(3)处理:对零件进行去毛刺、打磨等处理。
3. 压力铸造(1)模具制作:根据零件的形状和尺寸制作出压力铸造机所需的模具。
(2)浇注:将液态金属通过高压力喷射到模具中。
待金属冷却凝固后,取出零件。
(3)处理:对零件进行去毛刺、打磨等处理。
4. 熔蜡模铸造(1)蜡模制作:根据零件的形状和尺寸制作出蜡模具。
(2)陶瓷壳体制作:将蜡模浸入陶瓷浆料中,待干燥后再重复涂覆几层。
最后将其加热硬化。
(3)浇注:将液态金属倒入陶瓷壳体中。
待金属冷却凝固后,取出零件。
(4)处理:对零件进行去毛刺、打磨等处理,并将陶瓷壳体清理干净。
5. 精密铸造(1)模具制作:根据零件的形状和尺寸制作出精密模具。
(2)浇注:采用真空或低压浇注技术,将液态金属倒入模具中。
铸造零部件举例

铸造零部件举例
铸造是一种通过将熔融金属或合金浇注进模具中制造三维形状
的工艺。
在制造中,常常需要使用各种形状和尺寸的零部件。
下面以几种常见的零部件为例,介绍铸造技术的应用。
1. 铸造轮毂:轮毂是车辆的重要零部件之一,它连接轮胎和车轴,负责承受车辆的重量和提供牵引力。
铸造轮毂需要高强度和耐磨性能。
传统的铸造方法是采用砂型铸造,但现在越来越多的轮毂采用低压铸造或重力铸造来提高质量和生产效率。
2. 铸造引擎缸体:引擎缸体是发动机中最重要的部件之一,它固定汽缸和配气机构。
引擎缸体需要高强度、高耐用性和高耐热性。
常用的材料包括铝合金、铸铁和镁合金。
铸造引擎缸体通常采用压铸或重力铸造。
3. 铸造水泵壳体:水泵壳体是水泵的主体部分,它用于将水从低处吸入并向高处泵送。
水泵壳体需要具有高强度、高耐用性和耐蚀性。
通常采用砂型铸造或压铸工艺制造。
铸造技术在不同领域中得到广泛应用,可以生产出各种形状和尺寸的零部件。
通过不断改进工艺和材料,铸造技术在制造中的地位不断提高。
- 1 -。
壳型铸造工艺

壳型铸造工艺壳型铸造工艺壳型铸造工艺是一种常见的金属铸造工艺,广泛应用于各个领域的制造业中。
它以其高精度和良好的表面质量而受到重视。
在本文中,我将深入探讨壳型铸造工艺的原理、应用和发展前景,并分享我对该工艺的观点和理解。
作为一种近几十年来发展迅猛的铸造工艺,壳型铸造工艺通过制作具有空腔的模具来实现金属制品的生产。
其基本原理是在充填模腔的过程中,通过模具表面上的壳层材料固化形成壳体。
待模具内的金属液体冷却凝固后,壳体即可被拆除,从而得到所需的金属制品。
值得一提的是,壳型铸造工艺在铸造精度方面有着较大的优势。
相比传统的砂型铸造工艺,壳型铸造能够制造出更为精细的铸件。
这得益于壳型铸造工艺中所使用的耐高温的耐火材料,它们能够承受高温条件下的熔融金属,并保持壳体的稳定性。
另外,由于模具外壳较为坚硬,不易变形,壳型铸造还能够生产出具有较高表面质量和复杂结构的零件。
相较于其他几种常见的铸造工艺,壳型铸造工艺在这些方面具有明显的优势。
壳型铸造工艺在各个行业有着广泛的应用。
例如在航空航天领域,壳型铸造工艺常被用来生产高温合金零件、涡轮叶片等。
由于这些零件通常需要具备高强度和耐腐蚀性能,而壳型铸造工艺能够提供高精度和高质量的铸造件,因此成为了最佳选择。
在汽车制造领域,壳型铸造工艺可以用于生产发动机零部件、变速箱外壳等。
壳型铸造工艺还被广泛应用于船舶、军事装备、工程机械等领域。
随着科技的不断进步,壳型铸造工艺也在不断改善和创新。
近年来,随着数控(Computer Numerical Control, CNC)技术的发展,壳型铸造工艺与CNC技术的结合越来越紧密。
通过CNC技术,可以实现对铸型的精确加工和控制,进一步提高铸件的精度和质量。
3D打印技术的快速发展也为壳型铸造工艺提供了新的可能性。
通过3D打印技术,可以快速制作出复杂形状的铸型,减少模具制作的时间和成本。
壳型铸造工艺在金属制品制造领域具有广泛的应用前景和发展潜力。
铝合金铸造工艺流程
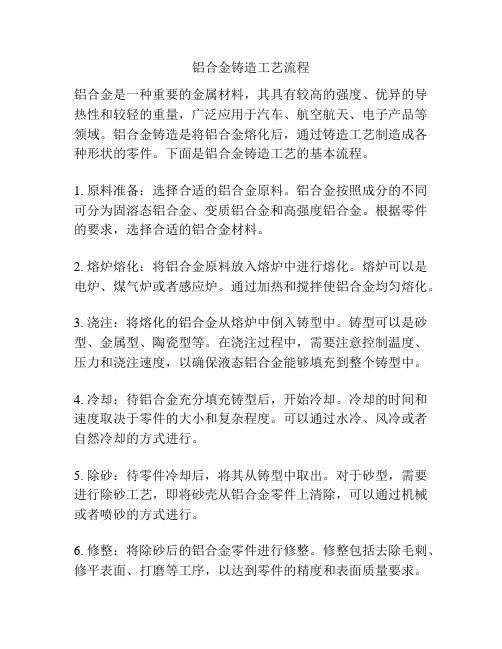
铝合金铸造工艺流程铝合金是一种重要的金属材料,其具有较高的强度、优异的导热性和较轻的重量,广泛应用于汽车、航空航天、电子产品等领域。
铝合金铸造是将铝合金熔化后,通过铸造工艺制造成各种形状的零件。
下面是铝合金铸造工艺的基本流程。
1. 原料准备:选择合适的铝合金原料。
铝合金按照成分的不同可分为固溶态铝合金、变质铝合金和高强度铝合金。
根据零件的要求,选择合适的铝合金材料。
2. 熔炉熔化:将铝合金原料放入熔炉中进行熔化。
熔炉可以是电炉、煤气炉或者感应炉。
通过加热和搅拌使铝合金均匀熔化。
3. 浇注:将熔化的铝合金从熔炉中倒入铸型中。
铸型可以是砂型、金属型、陶瓷型等。
在浇注过程中,需要注意控制温度、压力和浇注速度,以确保液态铝合金能够填充到整个铸型中。
4. 冷却:待铝合金充分填充铸型后,开始冷却。
冷却的时间和速度取决于零件的大小和复杂程度。
可以通过水冷、风冷或者自然冷却的方式进行。
5. 除砂:待零件冷却后,将其从铸型中取出。
对于砂型,需要进行除砂工艺,即将砂壳从铝合金零件上清除,可以通过机械或者喷砂的方式进行。
6. 修整:将除砂后的铝合金零件进行修整。
修整包括去除毛刺、修平表面、打磨等工序,以达到零件的精度和表面质量要求。
7. 热处理:对于一些需要强度或者耐腐蚀性能提升的铝合金零件,需要进行热处理工艺。
热处理包括固溶处理和时效处理,能够改善铝合金的力学性能和耐腐蚀性能。
8. 表面处理:根据需要对铝合金零件进行表面处理。
常见的表面处理包括阳极氧化、电泳涂装、喷涂等,以提高零件的耐腐蚀性、装饰性和表面硬度。
9. 检测:对铝合金零件进行质量检测。
常见的检测方法包括外观检查、尺寸检查、材料成分分析等,确保零件的质量达到要求。
10. 包装出厂:经过检测合格的铝合金零件进行包装,包括防潮、防震和标识等。
最后,将零件出厂,交付给客户使用。
以上是铝合金铸造工艺的基本流程。
不同的零件和要求可能会有所不同,但整体流程相似。
铝合金铸造工艺的发展,不仅提高了铝合金零件的生产效率和质量,也推动了铝合金在各个领域的广泛应用。
基于ProCAST的铝合金吸阀壳体铸造模拟

表2 ZL114A合金的化学成分6.250.180.070.150.550.08余铝合金铸件容易产生气孔、针孔等缺陷,且本次铸件平均壁厚为12.2mm ,容易导致铸造问题,因此型砂还需考虑发气量是否足够、流动性是否好、是否易紧实等一系列问题。
所以为了能获得高精度、表面光洁、强度高的铸件,经过全面的对比和分析后,最终选择了碱性酚醛树脂自硬砂。
2 铸造工艺设计浇注位置是指浇注时铸件在铸型中的空间位置,对铸件的凝固有着重要影响,主要考虑铸件的重要部位、重要加工面应朝下或者呈直立状态;使铸件的大平面朝下;保证铸件充型正常;有利于铸件补缩等。
铝合金凝固实际过程比较复杂,且很有可能发生氧化反应,由此产生氧化膜,在充型过程中在某处聚集,导致铸件出现缺陷。
综合考虑,为使金属液能够平稳充型,减少氧化,决定选择底注式浇注系统进行水平倾注。
由于吸阀壳体结构相对复杂,所以选用一箱一件方案。
按照铸件的技术要求,其尺寸公差应该达到GB/T 6414—1999的CT11-12级,根据铸件毛坯尺寸,对照国标,确定铸件尺寸公差为3.6mm 。
机械加工余量等级取F-H 级,所以法兰盘取5mm 。
材料为铝硅合金,且收缩时受到一定阻力,所以铸造收缩率取1%。
造型时使用木模,型砂为自硬树脂砂,起模斜度取0°35′。
吸阀壳体上的螺栓孔直径小于20mm ,所以选择不铸出。
砂芯较大,采用芯骨作为支撑。
浇注时间对充型过程及铸件质量有着重要影响,可以通过下式进行确定:31s G τδ= (1)式中:τ为浇注时间;G 为包括冒口在内的铸件总重量;δ为铸件壁厚;s 1为浇注金属的系数。
带入吸阀壳体数据,计算出浇注时间约为15s 。
本次模拟将采用两个方案进行浇注,方案一为立做平浇,浇注系统采用开放式,各单元截面比为∑F 直:∑F 横:∑F 内=1:2:3,如图2。
浇注系统设置在砂芯中,底注反雨淋式,采用埋管造型。
浇注时对砂型冲击较小,充型均匀平稳,可减少金属液氧化和飞溅。
砂铸铝铸件标准

砂铸铝铸件标准
砂铸铝铸件标准号是「GJB 862A-2009 砂铸铝件外观相关技术条件」。
这个标准对砂铸铝铸件的外观给出了基本要求,并明确了一些具体的技术、外观和尺寸的检查、疵点和瑕疵检查以及检验要求。
首先,要求砂铸铝铸件的外观应具有均匀的外观,消除和混杂物的合金表面不应具有毛坯及毛刺、划痕、流块及锻后流块、块分离、垢、渗漏、锈蚀等缺陷,外观质量应符合技术要求。
其次,在考虑外观的同时,还需要考虑砂铸铝铸件的热处理情况,以及后续的表面处理方式等,以确保砂铸铝铸件的外观质量满足设计要求。
热处理及相关表面处理方式及质量检验标准应遵循相关的具体标准。
以上信息仅供参考,如有需要,建议您查阅相关网站。
大型薄壁高强度铝合金异型舱壳精密砂型铸造成型关键技术应用研究

大型薄壁高强度铝合金异型舱壳精密砂型铸造成型关键技术应用研究**本文由“高档数控机床与基础制造装备”国家科技 重大专项(课题编号:2017ZX04009001)支持。
王华侨',王永凤「,郭玉',张权',付忠奎,,冯四伟I,罗海涛',赵华萍 ',李玉胜2,翟虎2,赵连君2,赵偲宇'1.湖北三江航天红阳机电有限公司(湖北孝感432000)2.沈阳明腾科技有限公司(辽宁沈阳110101)3.湖北大学知行学院(湖北武汉430011)【摘要】对某大型薄壁高强度铝合金网格筋异形舱壳整体精密铸造成型的关键技术进行了系统介绍,从铸件的结构特点、工艺方案选型、铸造模拟仿真、铸件加工质量等进行了深入 的分析和优化。
该大型薄壁网格筋异形舱壳整体精密铸造成型所采用的系列工艺及设计 技术,克服了传统制造方案无法实现或实现起来成本高、周期长、管理难等缺点,对于同类结构铸件的整体精密铸造成型成功实现具有重要的技术创新意义,同时对于提升国内大 型高强度铝合金复杂构件的精密铸造成型具有重要的指导和借鉴价值。
关键词:高强度铝合金;薄壁网格筋;异形舱壳;精密铸造;模拟仿真中图分类号:TG249 文献标识码:BDOklO.l 2147/ki. 1671-3508.2019.03.017Research on Critical Technology of Precision Casting for Large ThinWall High-Strength Aluminum Alloy Special-Shaped Cabin Shell[Abstract] In this paper, the key technology of a large thin wall high strength aluminum alloymesh bar for the whole precision casting is introduced, and the structure features, the selection ofthe process scheme, the simulation of the casting, the quality of the product and so on are deeplyanalyzed and optimized. The series of process and design techniques used in the whole precisioncasting of the large thin wall mesh reinforcement can overcome the shortcomings of thetraditional manufacturing scheme which can not be realized or realized, such as high cost, longperiod and difficult management. It has important technical innovation significance for the complete precision casting of similar structure products. At the same time, it has important guiding and reference value for improving the precision casting forming of large domestichigh-strength aluminum alloy components.Key words : high strength aluminum alloy ; thin-walled grid bar; special-shaped cabin shell ;precision casting; simulation1铸件结构特点1.1铸件结构特点某异形舱壳总体结构设计采用网格筋骨架+蒙皮整体铸造结构,如图1所示。
铝合金铸造技术

铝合金铸造技术一、铝合金铸造技术是啥呢?嘿,宝子们!今天咱来唠唠铝合金铸造技术。
这铝合金铸造啊,就像是给铝合金变魔术一样。
铝合金这东西可不得了,又轻又结实,在好多地方都能用得上。
铝合金铸造技术呢,就是把铝合金变成各种各样形状的方法。
这可不是随随便便就能做到的哦。
它就像是一个超级复杂又超级有趣的大工程。
你想啊,铝合金本来是一块一块或者一坨一坨的原材料,通过铸造技术,就能变成汽车零件、飞机零件,还有那些超酷的电子产品的外壳呢。
这过程就像是把一块面团捏成各种形状的小饼干一样,只不过这个“面团”是铝合金,而且这个“捏”的过程可讲究了。
二、铝合金铸造技术的种类1. 砂型铸造这是一种比较传统的方法啦。
就像是用沙子做一个模子,然后把铝合金熔化成液态,倒进这个沙子做的模子里。
等铝合金冷却凝固了,把沙子去掉,就得到了想要的形状。
这听起来简单,其实里面的学问可大了。
沙子的选择就很重要,要那种能承受高温,又不会和铝合金发生奇怪反应的沙子。
而且在做模子的时候,要保证模子的形状非常精准,不然做出来的铝合金零件就不合格啦。
2. 压铸压铸就比较高大上了。
它是用很大的压力把铝合金液注射到模具里。
这种方法做出来的零件精度很高,表面还很光滑。
不过呢,压铸的设备可老贵了,而且对模具的要求也特别高。
就像是给铝合金做了一个超级豪华的定制套房,从进去到成型都得按照严格的标准来。
3. 熔模铸造这个也很有趣哦。
先做一个蜡模,然后在蜡模外面裹上一层陶瓷之类的材料,做成一个壳。
再把蜡模融化掉,这样就得到了一个空心的模具。
最后把铝合金液倒进去,冷却后就得到了零件。
这个方法做出来的零件形状可以很复杂,就像那些精美的工艺品一样。
三、铝合金铸造技术的难点1. 温度控制铝合金在铸造的时候,温度可重要了。
温度太高,铝合金液可能会和模具发生反应,或者产生一些气孔之类的缺陷。
温度太低呢,铝合金液就不容易流动,可能就填不满模具,那做出来的零件就缺胳膊少腿的啦。
就像烤蛋糕一样,温度不对,蛋糕就烤不好。
铸造工艺与方法
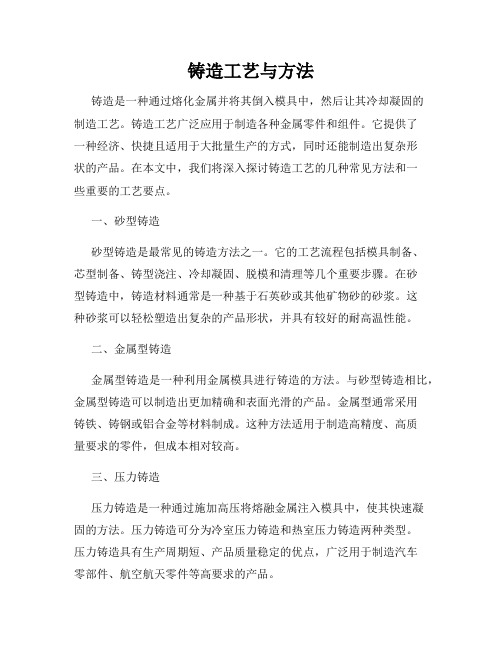
铸造工艺与方法铸造是一种通过熔化金属并将其倒入模具中,然后让其冷却凝固的制造工艺。
铸造工艺广泛应用于制造各种金属零件和组件。
它提供了一种经济、快捷且适用于大批量生产的方式,同时还能制造出复杂形状的产品。
在本文中,我们将深入探讨铸造工艺的几种常见方法和一些重要的工艺要点。
一、砂型铸造砂型铸造是最常见的铸造方法之一。
它的工艺流程包括模具制备、芯型制备、铸型浇注、冷却凝固、脱模和清理等几个重要步骤。
在砂型铸造中,铸造材料通常是一种基于石英砂或其他矿物砂的砂浆。
这种砂浆可以轻松塑造出复杂的产品形状,并具有较好的耐高温性能。
二、金属型铸造金属型铸造是一种利用金属模具进行铸造的方法。
与砂型铸造相比,金属型铸造可以制造出更加精确和表面光滑的产品。
金属型通常采用铸铁、铸钢或铝合金等材料制成。
这种方法适用于制造高精度、高质量要求的零件,但成本相对较高。
三、压力铸造压力铸造是一种通过施加高压将熔融金属注入模具中,使其快速凝固的方法。
压力铸造可分为冷室压力铸造和热室压力铸造两种类型。
压力铸造具有生产周期短、产品质量稳定的优点,广泛用于制造汽车零部件、航空航天零件等高要求的产品。
四、蜡型铸造蜡型铸造是一种精密铸造方法,通常用于制造复杂形状的零件。
在蜡型铸造中,首先制作出与最终产品形状相同的蜡模。
然后将蜡模浸入石膏混合物中,形成石膏壳体。
当石膏干燥后,将其放入高温烘箱中,使蜡模燃尽,留下空腔。
最后,将熔融金属倒入石膏壳体,待其冷却凝固后,获得成品。
蜡型铸造可以制造出高精度和精细表面处理的产品。
五、连铸连铸是一种用于生产连续坯料(铜、铁、铝等)的铸造工艺。
它是通过将熔融金属倒入长型模具中,然后通过冷却凝固使其形成坯料。
连铸工艺具有高效性和高质量的优点,被广泛应用于钢铁和有色金属工业中。
在选择合适的铸造工艺时,需要考虑到产品的设计要求、成本、生产周期以及所需材料等因素。
此外,铸造过程中还应注意控制合金的化学成分、铸型的温度和湿度,以及铸造过程中的冷却速度,以确保产品质量。
中国常用的铸造铝合金牌号特点及用途
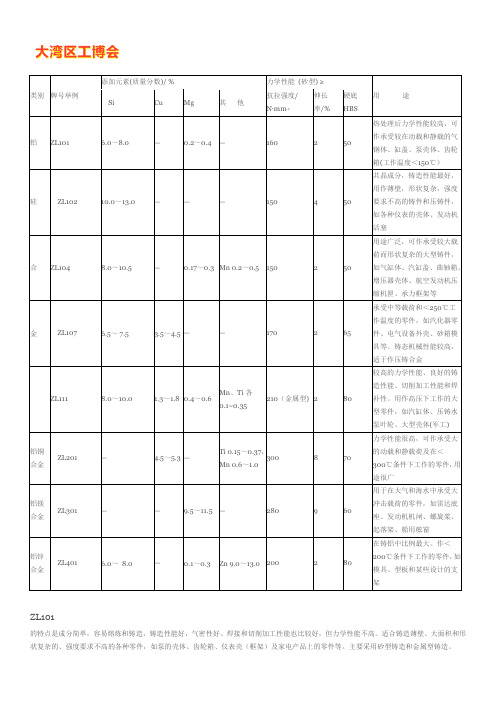
Si Cu ZL10210.0ZL1048.0ZL107 6.5ZL1118.0ZL201—ZL301—ZL401 6.0Zl101A由于是在ZL101的基础上加了微量Ti,细化了晶粒,强化了合金的组织,其综合性能高于Zl101、ZL102,并有较好的抗蚀性能,可用作一般载荷的工程结构件和摩托车、汽车及家电、仪表产品上的各种结构件的优质铸件。
其使用量目前仅次于ZL102。
多采用砂型和金属型铸造。
(ZL101A合金是以ZL101合金为基础严格控制杂质含量,改进铸造技术可以获得更高的力学性能。
铸造性能,耐腐蚀性能和焊接性良好。
用于铸造各种壳体零件,飞机的泵体、汽车变速箱、燃油箱的弯管等)Zl102这种合金的最大特点是流动性好,其它性能与ZL101差不多,但气密性比ZL101要好,可用来铸造各种形状复杂、薄壁的压铸件和强度要求不高的薄壁、大面积、形状复杂的金属或砂型铸件。
不论是压铸件还是金属型、砂型铸件,都是民用产品上用得最多的一个铸造铝合金品种。
Zl104因其工晶体量多,又加入了Mn,抵消了材料中混入的Fe有害作用,有较好的铸造性能和优良的气密性、耐蚀性,焊接和切削加工性能也比较好,但耐热性能较差,适合制作形状复杂、尺寸较大的有较大负荷的动力结构件,如增压器壳体、气缸盖,气缸套等零件,主要用压铸,也多采用砂型和金属型铸造。
Zl105、ZL105A由于加入了Cu,降低了Si的含量,其铸造性能和焊接性能都比ZL104差,但室温和高温强度、切削加工性能都比ZL104要好,塑性稍低,抗蚀性能较差。
适合用作形状复杂、尺寸较大、有重大负荷的动力结构件。
如增压器壳体、气缸盖、气缸套等零件。
Zl105A是降低了ZL105的杂质元素Fe的含量,提高了合金的强度,具有比ZL105更好的力学性能,多采用铸造优质铸件。
ZL106由于提高了Si的含量,又加入了微量的Ti、Mn,使合金的铸造性能和高温性能优于ZL105气密性、耐蚀性也较好,可用作一般负荷的结构件及要求气密性较好和在较高温度下工作的零件,主要采用砂型和金属型铸造。
铝合金高压开关壳体铸造针孔形成原因及解决措施

FOUNDRY工艺技术Vol.68No.52019铝合金咼压开关壳体铸造针孔形成原因及解决措施赵丽娟(常州工业职业技术学院,江苏常州213164)摘要:铝合金高压开关壳体形状复杂,采用低压砂型铸造时,端面处有针孔缺陷。
分析认为,针孔缺陷形成的原因是铸件内浇口设计在端面处,凝固时冷却缓慢,导致氢气析出,阻碍铝滋补缩,形成气缩孔。
通过对铸造工艺优化,加快壳体端面部位冷却速率,解决了铸件针孔缺陷。
关键词:高压开关壳体;针孔;铸造工艺;气缩孔随着输变电设备需求的增长,大型耐压铝合金壳体类铸件用量日益增多。
外壳铝合金化是适于输变电等级向500-800kV发展的重要趋势,也是高压输变电装备关键部件制造技术的一次重大变革。
铝合金壳体形状复杂,且多为承压,有较高的内部品质、力学性能和气密性要求,对材料性能和成形技术要求较高,生产难度较大W 低压铸造以充型平稳、速度可按铸件结构控制、铸件致密和力学性能高等优点受到重视⑴。
本研究中的高压开关壳体采用低压砂型铸造工艺,原工艺加工后端面处目视可见大面积1〜2mm针孔(见图1),壳体在进行氮气检漏时不合格。
铸件经X-ray检测,其余位置均无缺陷,端面针孔缺陷是漏气的主要原因。
1检验分析1.1化学成分分析壳体材料为A356铸造铝合金,采用Al-10Sr合金变质。
将壳体本体取样,按照GB/T20975.25—2008《铝及铝合金化学分析方法》要求,分析其化学成分如表1。
表中化学成分符合ASTM B26/B26M中A356的规定,可以排除成分偏差的原因。
作者简介:赵丽娟(1979-),女,满族,讲师,硕士,主要研究方向为材料成型技术oE-mail; 44779432@中图分类号:TG292文献标识码:B文章编号:1001-4977(2019)05-0516-03收稿日期:2019-01-07收到初稿, 2019—02—01收到修订稿。
1.2金相组织分析对壳体端面针孔部位缺陷处进行显微组织观察,结果见图2。
铸造铝合金定义分类用途

铸造铝合金一、概念可用金属铸造成形工艺直接获得零件的铝合金。
二、特性铸造铝合金必须具备以下特性,其中最关键是流动性和可填充型。
(1)有填充狭槽窄缝部分的良好流动性。
(2)有适应其他许多金属所要求的低熔点。
(3)导热性能好,熔融铝的热量能快速向铸模,铸造周期较短。
(4)熔体中的氢气和其它有害气体可通过处理得到有效的控制。
(5)铝合金铸造时,没有热脆开裂和撕裂的倾向。
(6)化学稳定性好,有高的抗蚀性能。
(7)不易产生表面缺陷,铸件表面有良好的光泽和低的表面粗糙度,而且易于进行表面处理。
(8)铸造铝合金的加工性能好,可用压模.硬(永久)模.生砂和干砂模.熔模.石膏型铸造模进行铸造生产,也可用真空铸造.低压和高压铸造.挤压铸造.半固体铸造.离心铸造等方法形成,生产不同用途.不同品种规格.不同性能的各种铸件。
三、分类据主要合金元素差异有四类铸造铝合金。
(1)铝硅系合金,也叫“硅铝明”或“矽铝明”。
有良好铸造性能和耐磨性能,热胀系数小,在铸造铝合金中品种最多,用量最大的合金,含硅量在10%~25%。
有时添加0.2%~0.6%镁的硅铝合金,广泛用于结构件,如壳体、缸体、箱体和框架等。
有时添加适量的铜和镁,能提高合金的力学性能和耐热性。
此类合金广泛用于制造活塞等部件。
(2)铝铜合金,含铜4.5%~5.3%合金强化效果最佳,适当加入锰和钛能显著提高室温、高温强度和铸造性能。
主要用于制作承受大的动、静载荷和形状不复杂的砂型铸件。
(3)铝镁合金,密度最小(2.55g/cm3),强度最高(355MPa左右)的铸造铝合金,含镁12%,强化效果最佳。
合金在大气和海水中的抗腐蚀性能好,室温下有良好的综合力学性能和可切削性,可用于作雷达底座、飞机的发动机机匣、螺旋桨、起落架等零件,也可作装饰材料。
(4)铝锌系合金,为改善性能常加入硅、镁元素,常称为“锌硅铝明”。
在铸造条件下,该合金有淬火作用,即“自行淬火”。
不经热处理就可使用,以变质热处理后,铸件有较高的强度。
各种牌号铸铝的主要特点及用途

各种牌号铸铝的主要特点及用途Prepared on 24 November 2020各种牌号铝合金的主要特点及用途ZL101的特点是成分简单,容易熔炼和铸造,铸造性能好,气密性好、焊接和切削加工性能也比较好,但力学性能不高。
适合铸造薄壁、大面积和形状复杂的、强度要求不高的各种零件,如泵的壳体、齿轮箱、仪表壳(框架)及家电产品上的零件等。
主要采用砂型铸造和金属型铸造。
Zl101A由于是在ZL101的基础上加了微量Ti,细化了晶粒,强化了合金的组织,其综合性能高于Zl101、ZL102,并有较好的抗蚀性能,可用作一般载荷的工程结构件和摩托车、汽车及家电、仪表产品上的各种结构件的优质铸件。
其使用量目前仅次于ZL102。
多采用砂型和金属型铸造。
Zl102这种合金的最大特点是流动性好,其它性能与ZL101差不多,但气密性比ZL101要好,可用来铸造各种形状复杂、薄壁的压铸件和强度要求不高的薄壁、大面积、形状复杂的金属或砂型铸件。
不论是压铸件还是金属型、砂型铸件,都是民用产品上用得最多的一个铸造铝合金品种。
Zl104因其工晶体量多,又加入了Mn,抵消了材料中混入的Fe有害作用,有较好的铸造性能和优良的气密性、耐蚀性,焊接和切削加工性能也比较好,但耐热性能较差,适合制作形状复杂、尺寸较大的有较大负荷的动力结构件,如增压器壳体、气缸盖,气缸套等零件,主要用压铸,也多采用砂型和金属型铸造。
Zl105、ZL105A由于加入了Cu,降低了Si的含量,其铸造性能和焊接性能都比ZL104差,但室温和高温强度、切削加工性能都比ZL104要好,塑性稍低,抗蚀性能较差。
适合用作形状复杂、尺寸较大、有重大负荷的动力结构件。
如增压器壳体、气缸盖、气缸套等零件。
Zl105A是降低了ZL105的杂质元素Fe的含量,提高了合金的强度,具有比ZL105更好的力学性能,多采用铸造优质铸件。
ZL106由于提高了Si的含量,又加入了微量的Ti、Mn,使合金的铸造性能和高温性能优于ZL105气密性、耐蚀性也较好,可用作一般负荷的结构件及要求气密性较好和在较高温度下工作的零件,主要采用砂型和金属型铸造。
大型铝合金耐压壳体的低压铸造工艺

大型铝合金耐压壳体的低压铸造工艺摘要:针对大型铝合金耐压壳体的铸造工艺充分利用了低压铸造法进行了实验研究。
通过实验可以发现,在实际进行大型铝合金耐压壳体铸造过程中充分利用双升液管铸造工艺,并对相关的工艺参数进行合理设置,就能够有效提升铝合金耐压壳体批量铸造生产中的产品质量。
关键词:铝合金;耐压壳体;低压铸造;工艺参数引言某工程在施工过程中需要大量使用耐压壳体来作为全封闭组合电器的组装材料,针对耐压壳体铸件必须要求其水压破裂性实验强度超过3.75MPa,其属于一种大型的铝合金耐压壳体铸件,该设备在生产作业出去的时候主要使用的是树脂砂型动力铸造工艺,在该工艺流程下铸件产品的合格率仅仅能够达到50%,而且在针孔度、圆跳度以及平面度等几个指标方面,铸件都存在严重的超标现象,而且针对其气密性进行检查的过程中发现,一次性合格的成功率非常低。
1 铸造工艺设计该工程实际使用的铸件整体重量达到40kg,而是一种回转体形态,筒壁的厚度能够达到15mm,由于该铸件内腔部分本身存在一定的斜度,主要采取的分型方式如下图1所示,这样就能够铁芯的抽出提供方便。
图1 铸造工艺方案上述这种分型方式在实际进行工艺设计的过程中必须要对以下几点进行充分考虑。
首先,由于在该铸件中法兰面比较厚,这个铸件密封面的上顶面,因此在实际进行工艺设计过程中必须要对该位置产生缩孔或者针孔等缺陷给与高度重视;其次,由于该铸件两侧分布的凸台属于一种局部热节,要想实现补缩非常困难;再次,由于该铸件整体结构尺寸相对较大,而且其浇注的重量也比较大,在实际进行内浇道施工时可以通过多个引入口的方法来有效避免出现局部过热现象;最后,在整个铸造过程中法兰密封槽以及下焊接坡口是整个铸造过程中最主要的质量控制点[1]。
根据上图1所示的工艺设计方案进行知道,该方案主要的特点是充分利用了双升液管阶梯充型方式,这样不仅能够进一步提升整个铸件的致密度,也能够有效避免在铸件的入口位置发生局部过热现象,这样就能够实现铸造过程中铸件气孔以及缩松等缺陷。
铝合金薄壁铸件砂型无模铸造工艺

铝合金薄壁铸件砂型无模铸造工艺摘要:介绍铝合金薄壁铝合金铸件采用砂型无模铸造的工艺流程及特点,并通过零件结构分析产生冷隔、缩松等缺陷风险,设计了双浇口开放式顶注式浇注系统及内浇口上方设置多处异性冒口。
结果表明,双浇口开放顶注重力式浇注可以解决薄壁件砂型浇注产生的冷隔、缩松等缺陷,取得显著的经济效益。
关键词:砂型无模;无模精密成型;凝固收缩中图分类号:Sand mold less casting process for thin wall aluminum alloycastingsOU Hong-rong ZHOU Liang-jian FAN Jin-qianGuangxi Yuchai Machinery Co. Ltd.Yulin,Guangxi Province,China,537000Abstract: The technological process and characteristics of sand mold less casting for thin-walled aluminum alloy castings are introduced. Through the structural analysis of the parts, the risk of defects such as cold shut and shrinkage porosity is caused. The double gate open top injection gating system is designed, and a number of heterogeneous risers are set above the inner gate. The results show that the double gate open top pouring gravity pouring can solve the defects of cold shut and shrinkage caused by sand mold pouring ofthin-walled parts, and obtain significant economic benefits.Key words: Sand mould without mould;Dieless precision forming;Solidification shrinkage1引言节能减排和轻量化是目前发动机制造行业不断追求的目标,目前大多数柴油发动机的零部件都是由铸铁材料铸造而成。
- 1、下载文档前请自行甄别文档内容的完整性,平台不提供额外的编辑、内容补充、找答案等附加服务。
- 2、"仅部分预览"的文档,不可在线预览部分如存在完整性等问题,可反馈申请退款(可完整预览的文档不适用该条件!)。
- 3、如文档侵犯您的权益,请联系客服反馈,我们会尽快为您处理(人工客服工作时间:9:00-18:30)。
冒口2 尺寸:直 径 2” x 高4” (普通砂冒口)
使用保温冒口套, 则尺寸减小为: 直径1” x高 2”
冒口 3尺寸:直 径 2” x 高4”
冒口4尺寸:直 径 2” x高 4”
通过分析冒口的放置位置,现铸件应该旋 转180度,以便于补缩。添加冒口后的铸件 工艺如下图所示:
根据铸件和冒口特点,顶冒口1、2 采用保温冒口套,3、4采用普通侧 冒口。
问题解答
问: 为什么冒口尺寸会过大?
答: 计算冒口大小的模数法是一种近似算法,同 样补缩体积也是根据假设的冒口补缩率确定 的。不同的合金-铸型材料会影响实际的冒口 效率,所以需要根据经验调整相应的补缩效 率。
问题解答
问: 下一步该如何做呢?
答: 接下来,调整冒口尺寸,在凸台位置增加冒 口或冷铁,再次进行模拟,分析结果。
联系方式 天津富宇创想科技有限公司
公司网站:
2. 最大冒口高度改为 3” 3. 在凸缘位置采用三角形冒口。 4. 在凸台位置放置铝合金冷铁。 5. 增大了内浇口尺寸。
改进的浇冒口系统
铝合金冷铁
模拟结果分析
凝固过程图
凝固过程显示,在顶部存在一个 小的孤立热节。
热节
缩孔预测分析
缩孔是由于缺少补缩形成的。如果连接冒口的补 缩通道过早凝固,则孤立液相区得不到补缩, 就会产生缩孔。SOLIDCast通过计算铸件收 缩及凝固过程液态金属补缩流动,预测可能 产生的缩孔。
问题解答
问: 有没有自动优化冒口的方法?
答: SOLIDCast 中有优化模块 OPTICast ,采 用多变量-响应面优化算法,自动找到铸件质 量和工艺出品率最高时的最小冒口尺寸。
铝合金砂型铸造工艺分析 模拟 #2
对于模拟#2, 对模型进行了一下调整:
1. 增加了冒口锥度,并延伸到铸型顶面。
接下来,设计浇铸系统。一般来说, 浇注系统有利于形成正的温度梯度, 也就是说尽量由冒口进入,从而使 冒口成为最热的部分。
工艺设计完成后,使用SOLIDCast进行初次 模拟,以验证浇冒口系统设计是否合理,是 否需要进一步的改进。
模拟结果如下图所示…
铸件完全凝固时的温度分布图。
铸件和冒口的凝固顺序。(颜色越 深的地方凝固越早)
X射线显示铸件上的缩孔分布。
热节位置产生的小缩孔。
缩松预测
缩松,即微观尺度弥散型的小孔。可能是在凝固 比较慢的特殊情况下(凝固前沿的波动超过 某一临界值)形成的。 SOLIDCast 通过局 部凝固时间和凝固速度来预测铸件上可能产 生的缩松。
X射线显示铸件上的缩松分布
非常小的局部热节
结论
改进后的工艺,基本上能得到良好的铸件。顶部 缩孔级别很小,如果有必要可以加一个小的 顶冒口(或减小冷铁)进行消除。 缩松很小,且水平很低,通过实际的X射线很可 能都无法检测到。实际很可能不会出问题, 但如果必要,可在该处增加小冷铁。
根据铸件类型,首先选 择“敏感性” 系数.
“向导”自动分析铸件,确定补缩区域,本例中存在4个独 立地补缩区,则需要放置4个冒口.
冒口设计向导 能够显示铸件上的各个补缩区, 如下图所示:
补缩区 1
补缩区 2
补缩区 3
补缩区 4
要想获得合格铸件,每个补缩区都需要放置冒 口. The Riser Design冒口设计向导 Wizard can 通过显示每个补缩区中模数最大的点,能够 确定放置冒口的最佳位置。 如下图所示:
冒口放置点 1
冒口放置点 2
冒口放置点 3
冒口放置点 4
接下来确定冒口尺寸。
根据模数和补缩体积,冒口设计向导能够自 动计算出相应的冒口大小。
计算得到的冒口1 的尺寸:直径 3” x 高 6” (假设为普 通砂冒口)
如果假设冒口1 采用保温冒口套, 则冒口尺寸减小 为:直径 2.5” x 高 4”
通过X射线透视图分析铸件和冒口中 的缩孔。除了下部小凸台,铸件其 他位置未发现缺陷。
小缩孔
小结
1. 凸台中的缩孔可以通过增加小冒口或冷铁 来消除。 2. 冒口(特别是顶部大冒口)尺寸看起来还 可以减小,而不会影响铸件质量。
问题解答 问: 为什么“冒口设计向导”未提示在小凸台缩 孔位置放置冒口? 答: 在“冒口设计向导”中,需要设置“敏感 度”。敏感度越高,能够识别的补缩区越小。 本例中,需要设置更高的敏感度。而如何设 置正确的敏感度也需要一定的学习积累过程。
初始模拟结果:等轴测视图
暗的区域先凝固,亮的区域后凝固.
XY 视图
初始模拟完成后,就可以使用SOLIDCast中的 冒口设计向导开始冒口设计. 冒口设计向导 将模拟结果转换为“模数”和“体积”数据,根据 冒口模数大于铸件,冒口补缩体积大于铸件凝 固收缩量,计算出冒口的最小尺寸.
冒口设计向导使用模数和补缩体积来计算冒 口大小. 从下图开始:
铝合金砂型铸件分析 -壳体
在本例中,通过图示说明使用SOLIDCast™ 中的工具建立铸件工艺的过程。
以铸件的三维模型为起点。首先导入铸件 STL文件,如下图所示。
导入的铸件三维几何(XZ 视图)
导入的铸件三维几何(等轴测试图)
下一步,对不带浇冒口系统的铸件进行模拟, 确定铸件的“自然”凝固顺序,以便于得到浇口 和冒口的正确放置位置. 铸件材料类型设为:C355 铝合金, 铸型为方形, 材料为橄榄石砂. 计算时间: 1 GHz PC, 约50分钟