液体动压润滑向心滑动轴承实验
液体动压润滑径向轴承油膜压力和特性曲线
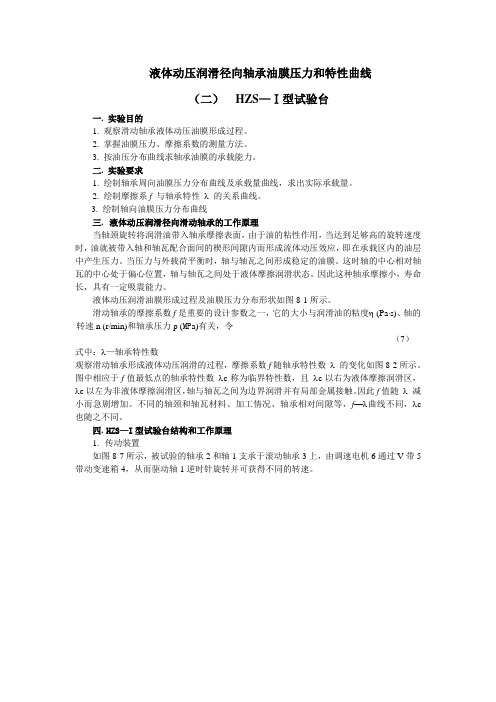
液体动压润滑径向轴承油膜压力和特性曲线(二)HZS—Ⅰ型试验台一. 实验目的1. 观察滑动轴承液体动压油膜形成过程。
2. 掌握油膜压力、摩擦系数的测量方法。
3. 按油压分布曲线求轴承油膜的承载能力。
二. 实验要求1. 绘制轴承周向油膜压力分布曲线及承载量曲线,求出实际承载量。
2. 绘制摩擦系f 与轴承特性λ的关系曲线。
3. 绘制轴向油膜压力分布曲线三.液体动压润滑径向滑动轴承的工作原理当轴颈旋转将润滑油带入轴承摩擦表面,由于油的粘性作用,当达到足够高的旋转速度时,油就被带入轴和轴瓦配合面间的楔形间隙内而形成流体动压效应,即在承载区内的油层中产生压力。
当压力与外载荷平衡时,轴与轴瓦之间形成稳定的油膜。
这时轴的中心相对轴瓦的中心处于偏心位置,轴与轴瓦之间处于液体摩擦润滑状态。
因此这种轴承摩擦小,寿命长,具有一定吸震能力。
液体动压润滑油膜形成过程及油膜压力分布形状如图8-1所示。
滑动轴承的摩擦系数f是重要的设计参数之一,它的大小与润滑油的粘度η (Pa⋅s)、轴的转速n (r/min)和轴承压力p (MP a)有关,令(7)式中:λ—轴承特性数观察滑动轴承形成液体动压润滑的过程,摩擦系数f随轴承特性数λ的变化如图8-2所示。
图中相应于f值最低点的轴承特性数λc称为临界特性数,且λc以右为液体摩擦润滑区,λc以左为非液体摩擦润滑区,轴与轴瓦之间为边界润滑并有局部金属接触。
因此f值随λ减小而急剧增加。
不同的轴颈和轴瓦材料、加工情况、轴承相对间隙等,f—λ曲线不同,λc 也随之不同。
四.HZS—I型试验台结构和工作原理1.传动装置如图8-7所示,被试验的轴承2和轴1支承于滚动轴承3上,由调速电机6通过V带5带动变速箱4,从而驱动轴1逆时针旋转并可获得不同的转速。
1—轴2—试验轴承3—滚动轴承4—变速箱5—V带传动6—调速电机图8-7 传动装置示意图2.加载装置该试验台采用静压加载装置,如图图8-8所示。
图中4为静压加载板,它位于被试轴承上部,并固定于箱座上,当输入压力油至加载板的油腔时,载荷即施加在轴承上,轴承载荷为:F = 9.18 (p o A+Go) N(8)式中:p o—油腔供油压力,p o = 3 kg/cm2;A —油腔在水平面上投影面积,2Go —初始载荷(包括压力表、平衡重及轴瓦的自重)Go = 8 kgf 。
液体动压润滑轴承实验指导书

《液体动压润滑轴承》实验指导书一、实验目的1、观察径向滑动轴承液体动压润滑油膜的形成过程和现象。
2、测定和绘制径向滑动轴承径向油膜压力曲线,求轴承的承载能力。
3、观察载荷和转速改变时油膜压力的变化的情况。
4、观察径向滑动轴承油膜的轴向压力分布情况,绘制轴向油膜压力曲线。
5、了解径向滑动轴承的摩檫系数f的测量方法,绘制摩擦特性曲线。
二、实验台结构与技术参数1、实验台的主要结构如图所示1、三角带2、直流电机3、主轴箱4、主轴5、主轴瓦6、油压表(8只)、7、螺旋加载器8、测力弹簧片9、测力计(百分表)2、结构特点实验台主轴4、由两个高精度的单列向心球轴承支承。
直流电机2通过三角带1传动给主轴4,主轴顺时针旋转,主轴上装有精密加工制造的主轴瓦5,由无机调速器来实现主轴的无机变速,轴的转速由装在面板上的左数码管显示。
主轴瓦外圆上方被加载装置压住,通过螺旋加载器的加载杆即可实现对轴瓦加载,加载大小由载荷传感器传出,由装在面板上的右数码管显示。
主轴瓦上装有测力杆,通过百分表9可测出测力弹簧片变形Δ值。
主轴瓦前端装有7只油压表,测量在轴瓦全长1/2处(即中间位置)的径向压力,在轴瓦全长1/4处(距后端)装有1只油压表(即第8只),测量该处的径向压力,第8只油压表与前端装有的第4只油压表都安装在主轴瓦的同一条母线上。
3、主要技术参数实验主轴瓦内直径(即主轴直径)d=70mm、有效长度(宽度)B=125mm、材料 ZQSn6-6-3加载范围0~1000 N 调速范围n=3~500 rpm百分表精度 0.01mm 量程0~10mm 油压表精度 2.5级量程0~0.6MPa 测力杆上测力点与轴承中心距离L=120mm测力弹簧片特性系数k=0.098N/格(百分表每格)2、控制面板(如图)1、转速显示2、压力显示3、油膜指示4、电源开关5、压力调零6、转速调节7、测量键8、存储键9查看键10复位键在单片机的程序控制下,可完成“复位”“测量”“查看”“存储”4种测试功能,通电后,该电路自动开始工作,个位右下方的小数点亮,即表示电路正在检测并计算转速。
流体动压润滑径向滑动轴承计算举例

流体动压润滑径向滑动轴承计算举例
试设计一流体动压润滑径向滑动轴承。
其径向外载荷为 5000N ,轴颈转速为960r/min ,轴颈所允 许的最小直
径为20mm 。
解:
工作载荷HN 〕 ^000~
轴馬宽径叱引d
卷考值 [―TT ----- 1 轴颈直径贞mm]
歹且1 00 ▼ r 自定义'
轴转速
960
开赠i 计算
混合润滑计算
rt 十算结果显示
釉承压强(MPaJ 12.5000 釉頑速度〔“旳]1 0053 r 使用参考间隍计算
3)估算轴承间隙
卩间隙计算结果显示
直径间003
相对间隙
0.0015
计算间隙
4)选择材料
包角选择n iso
ZCuSn10P1
J
许用摄大压强〔忖pa] 许用摄丈速度丽畑 许用 pv®(Mpa x m/s ) 材料属性 15
10
15 踢音洞
材料适用场合
用于中速、重戟及受变载荷的轴承.用于中速、
承°
中载的轴 参考值
轴承平均压强12.500MPa 轴承平均速度
1. OOSm/s pv® 1
2.566M Pa.m/s
5)流体动压润滑计算结果
1) 选择轴承的内径
二
101
12.5663
0.00110
席自定文相对间隙
输入自定义相对间隙值: |0.0015
匚吝输入已知裁量
轴承相
(从
略)
6)根据计算结果需要重新设计,按“返回”按钮,即可以得到可行方案。
液体动力润滑径向滑动轴承设计计算

液体动力润滑径向滑动轴承设计计算流体动力润滑的楔效应承载机理已在第四章作过简要说明,本章将讨论流体动力润滑理论的基本方程(即雷诺方程)及其在液体动力润滑径向滑动轴承设计计算中的应用。
(一)流体动力润滑的基本方程流体动力润滑理论的基本方程是流体膜压力分布的微分方程。
它是从粘性流体动力学的基本方程出发,作了一些假设条件后得出的。
假设条件:流体为牛顿流体;流体膜中流体的流动是层流;忽略压力对流体粘度的影响;略去惯性力及重力的影响;认为流体不可压缩;流体膜中的压力沿膜厚方向不变。
图12-12中,两平板被润滑油隔开,设板A 沿x 轴方向以速度v 移动;另一板B 为静止。
再假定油在两平板间沿 z 轴方向没有流动(可视此运动副在z 轴方向的尺寸为无限大)。
现从层流运动的油膜中取一微单元体进行分析。
作用在此微单元体右面和左面的压力分别为p 及p p dx x ∂⎛⎞+⎜∂⎝⎠⎟,作用在单元体上、下两面的切应力分别为τ及dy y ττ⎛⎞∂+⎜⎟∂⎝⎠。
根据x 方向的平衡条件,得:整理后得根据牛顿流体摩擦定律,得,代入上式得 该式表示了压力沿x 轴方向的变化与速度沿y 轴方向的变化关系。
下面进一步介绍流体动力润滑理论的基本方程。
1.油层的速度分布将上式改写成(a)对y 积分后得(c)根据边界条件决定积分常数C1及C2:当y=0时,v= V;y=h(h为相应于所取单元体处的油膜厚度)时,v=0,则得:代入(c)式后,即得 (d)由上可见,v由两部分组成:式中前一项表示速度呈线性分布,这是直接由剪切流引起的;后一项表示速度呈抛物线分布,这是由油流沿x方向的变化所产生的压力流所引起的。
2、润滑油流量当无侧漏时,润滑油在单位时间内流经任意截面上单位宽度面积的流量为:将式(d)代入式(e)并积分后,得(f)设在 p=p max处的油膜厚度为h0(即时当润滑油连续流动时,各截面的流量相等,由此得 :整理后得该式为一维雷诺方程。
液体动压轴承实验2

液体动压轴承实验一、实验目的了解轴承油膜承载现象及其参数对轴承性能的影响,掌握油压及摩擦系数测试方法,加深对液体动压润滑原理的认识。
二、实验要求1、测定并绘出轴承油膜压力周向分布曲线及轴向分布曲线,并求出轴承的承载量。
2、计算实测端泄对轴承压力分布的影响系数k 值。
看其是否符合油膜压力沿抛物线分布规律。
3、测定轴承单位压力、滑动速度、润滑油粘度与摩擦系数之间的关系,绘制出轴承摩擦特性曲线。
三、试验台简介液体动压轴承试验台可用来进行油膜压力分布及轴承摩擦特性曲线的测定。
加载方法采用静压油垫。
调速方式采用 JZT 型调速电机,并配以变速箱,可实现 20~580r/min 无级变速,主轴转速可根据控制器表盘转速读数直接得出。
1、试验台主要技术参数(1)试验轴承参数轴颈直径d = 60mm。
轴颈有效长度l = 120mm直径间隙 0.07表面粗糙度1.6 ∇轴承材料ZQSn6-6-3(铸锡青铜)轴承自重G=80N(包括压力表及平衡锤等)(2)加载范围 3000N(3)加载油腔水平投影面积 188.5cm2(4)测力杆上测力点与轴承中心偏移距离 17mm(5)转速范围20~5800r/min(6)主电机功率0.375KW2、试验台总体布置图1 为试验台总体布置,图中 1 为试验轴承箱,由联轴器与变速箱 7 相联,6为液压箱,装于底座 9 内部,12 为调速电机,8 为调速电机控制器,5 为加载油腔压力表,2 为轴承供油压力表。
油泵电机开关为 10,主电机开关为 11,总开关位于试验台正面。
图 1 试验台总体布置图1-实验轴承箱 2-轴承供油压力表 3-减压阀 4-溢流阀 5-加载油腔压力表 6-液压箱7-变速箱8-调速电机控制器9-底座10-油泵电机开关11-主电机开关12-调速电机13-三角带传动装置3、试验轴承箱图 2 为试验轴承箱,图中 2 为主轴,由两只 P5 级滚动轴承支承。
6 为试验轴承,空套在主轴上,轴承内径d = 60mm,有效长度l= 120mm,在中间横断面,即有效长度 1/2 处的断面上沿周向开有七个测压孔,在 120º范围内均匀分布,距中间断面 1/4 处,即距周向测压孔15mm 处在铅直方向还开有另一个测压孔(即轴向测压孔),图中 1 表示七只压力表分别与七个周向测压孔相联,8 为一只与轴向测压孔相联的压力表,3 为加载盖板,固定在箱体上,加载油腔在水平面上的投影面积为188.5cm2.轴承外圆左侧装有测杆4、环5装在测杆端部,其与轴承中心距离为 78 mm。
液体动力润滑径向滑动轴承承载能力测试实验
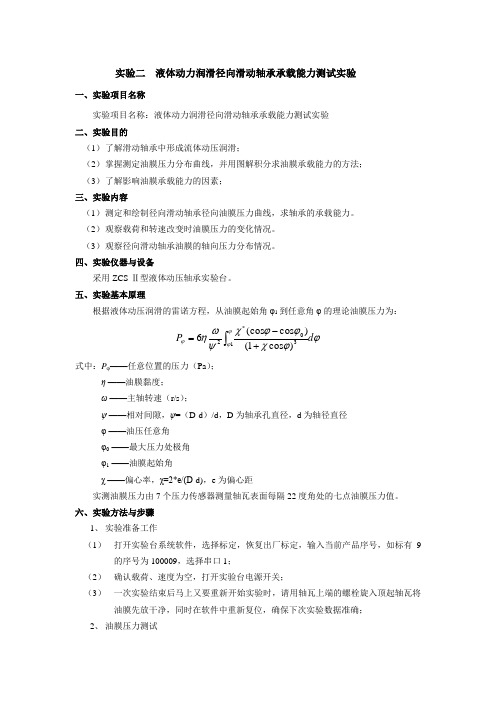
实验二 液体动力润滑径向滑动轴承承载能力测试实验一、实验项目名称实验项目名称:液体动力润滑径向滑动轴承承载能力测试实验二、实验目的(1) 了解滑动轴承中形成流体动压润滑;(2) 掌握测定油膜压力分布曲线,并用图解积分求油膜承载能力的方法;(3) 了解影响油膜承载能力的因素;三、实验内容(1) 测定和绘制径向滑动轴承径向油膜压力曲线,求轴承的承载能力。
(2) 观察载荷和转速改变时油膜压力的变化情况。
(3) 观察径向滑动轴承油膜的轴向压力分布情况。
四、实验仪器与设备采用ZCS-Ⅱ型液体动压轴承实验台。
五、实验基本原理根据液体动压润滑的雷诺方程,从油膜起始角φ1到任意角φ的理论油膜压力为:ϕϕχϕϕχψωηϕϕϕd P ⎰+-=130*2)cos 1()cos (cos 6 式中:P φ——任意位置的压力(Pa );η ——油膜黏度;ω ——主轴转速(r/s ); ψ ——相对间隙,ψ=(D-d )/d ,D 为轴承孔直径,d 为轴径直径φ ——油压任意角φ0 ——最大压力处极角φ1 ——油膜起始角χ ——偏心率,χ=2*e/(D -d),e 为偏心距实测油膜压力由7个压力传感器测量轴瓦表面每隔22度角处的七点油膜压力值。
六、实验方法与步骤1、 实验准备工作(1) 打开实验台系统软件,选择标定,恢复出厂标定,输入当前产品序号,如标有9的序号为100009,选择串口1;(2) 确认载荷、速度为空,打开实验台电源开关;(3) 一次实验结束后马上又要重新开始实验时,请用轴瓦上端的螺栓旋入顶起轴瓦将油膜先放干净,同时在软件中重新复位,确保下次实验数据准确;2、 油膜压力测试(1)击“自动采集”,将电机速度旋转到200r/min左右,然后慢慢加载到1800N,观察油膜压力采集七点参数值,点击“提取数据”;(2)点击“实测曲线”作出测得的7个压力值之曲线,点击“理论曲线”作出理论压力曲线,对两者进行比较;(3)点击“结果显示”,显示轴承平均压力、轴承pv值、油膜最小厚度;(4)点击“打印”,将油膜压力实验结果打印出来。
流体动压润滑条件下滑动轴承的优化分析.

本科毕业设计题目流体动压润滑条件下滑动轴承的优化分析专业汽车服务工程作者姓名李洋洋学号2011206004单位机械与汽车工程学院指导教师杜娟2015年5月教务处编原创性声明本人郑重声明:所提交的学位论文是本人在导师指导下,独立进行研究取得的成果。
除文中已经引用的内容外,论文中不包含其他人已经发表或撰写过的研究成果,也不包含为获得聊城大学或其他教育机构的学位证书而使用过的材料。
对本文的研究作出重要贡献的个人和集体,均在文中以明确的方式表明。
本人承担本声明的相应责任。
学位论文作者签名:日期:指导教师签名:日期:摘要就当今的汽车而言,大约有80%的机械部件的损坏来自于磨损。
机械系统中摩擦能够得到相关的优化,更能够提高机械性能,延长其使用寿命。
然而传统发动机滑动轴承用非定常流体设计,对于发动机滑动轴承耐磨性能并没有真正的进行定性分析,缺乏一定的说服力。
本文首先介绍了滑动轴承的相关知识,然后对流体动压润滑进行详细说明并建立了流体动压润滑的计算模型,然后以发动机主轴承为例,分析轴承在不同转速下的最小油膜厚度、润滑油温升,发现转速过高时,油膜厚度过小且温升过高,导致滑动轴承不能处于良好的润滑状态,分析该现象的原因并提出相关改进方案:增粗轴颈、加宽轴承。
然后分别根据两种改进方案在不同转速下的最小油膜厚度、润滑油温升两个角度分析改进措施的优劣性。
关键词:流体动力润滑;转速;最小油膜厚度;温升AbstractIn terms of today's cars, and about 80% of the damage of the mechanical components from wear and tear. Mechanical friction in the system can get related optimization, more can improve the mechanical properties, extend its service life. However, the traditional engine bearing design with unsteady flow for engine bearing wear resistance and no real qualitative analysis, the lack of certain powers of persuasion.This paper first introduces the sliding bearing of the related knowledge, and elaborate on the hydrodynamic pressure lubrication and the calculation of hydrodynamic pressure lubrication model is established, and then to launch a main bearing as an example, analysis of the bearing under different rotational speed, the minimum oil film thickness, oil temperature rise, found at high speed, the temperature rise of the oil film thickness is too small and too high, lead to sliding bearing can't in good lubrication condition, analyses the reason of this phenomenon and put forward relevant improvement plan: enlargement of journal, widen the bearing. Then respectively according to the two kinds of improved scheme under different rotational speed, the minimum oil film thickness, oil temperature rise two Angle analysis of superiority and inferiority of some improvement measures.Keywords:hydrodynamic lubrication; Speed; Minimum oil film thickness; Temperature rise目录前言................................................................................................I I 1.轴承设计计算所涉及到的基础知识 .. (1)1.1 滑动轴承 (1)1.2牛顿粘性定律 (2)1.3.表面粗糙度 (3)1.3.1表面粗糙度定义 (3)1.3.2 表面粗糙度对零件的影响 (3)2.流体动压润滑 (4)2.1流体动压润滑基本理论 (4)2.2流体动力润滑的基本方程 (5)2.2.1油层速度的分布 (5)2.2.2润滑油流量 (6)3.发动机滑动轴承的流体润滑设计 (8)3.1建立弹性流体动压润滑的计算模型 (8)3.1.1建立动压润滑模型 (8)3.1.2相关参数选择 (8)3.2动压润滑设计 (9)3.2.1油膜承载能力的计算 (9)3.2.2最小油膜厚度的计算 (10)3.2.3轴承热平衡计算 (11)4.发动机主轴承流体润滑计算与结果分析 (12)4.1流体润滑计算 (12)4.2流体润滑计算结果分析 (15)5.发动机主轴承耐磨性改进方案 (16)5.1增大轴颈直径 (16)5.1.1最小油膜厚度分析改进方案 (16)5.1.2润滑油温升分析改进方案 (17)5.2增大轴承宽度 (17)5.2.1最小油膜厚度分析改进方案 (17)5.2.2润滑油温升分析改进方案 (18)结论 (19)参考文献 (20)致谢 (21)流体动压润滑条件下滑动轴承的耐磨性优化分析前言滑动轴承是机械系统中常见的装置之一,也是生产过程中不可或缺的原件。
滑动轴承实验指导书(更新并附实验报告)

滑动轴承实验一、概述滑动轴承用于支承转动零件,是一种在机械中被广泛应用的重要零部件。
根据轴承的工作原理,滑动轴承属于滑动摩擦类型。
滑动轴承中的润滑油若能形成一定的油膜厚度而将作相对转动的轴承与轴颈表面分开,则运动副表面就不发生接触,从而降低摩擦、减少磨损,延长轴承的使用寿命。
根据流体润滑形成原理的不同,润滑油膜分为流体静压润滑(外部供压式)及流体动压润滑(内部自生式),本章讨论流体动压轴承实验。
流体动压润滑轴承其工作原理是通过韧颈旋转,借助流体粘性将润滑油带人轴颈与轴瓦配合表面的收敛楔形间隙内,由于润滑油由大端人口至小端出口的流动过程中必须满足流体流动连续性条件,从而润滑油在间隙内就自然形成周向油膜压力(见图1),在油膜压力作用下,轴颈由图l(a)所示的位置被推向图1(b)所示的位置。
图1 动压油膜的形成当动压油膜的压力p 在载荷F 方向分力的合力与载荷F 平衡时,轴颈中心处于某一相应稳定的平衡位置O 1,O 1位置的坐标为O 1(e ,Φ)。
其中e =OO 1,称为偏心距;Φ为偏位角(轴承中心O 与轴颈中心O 1连线与外载荷F 作用线间的夹角)。
随着轴承载荷、转速、润滑油种类等参数的变化以及轴承几何参数(如宽径比、相对间隙)的不同.轴颈中心的位置也随之发生变化。
对处于工况参数随时间变化下工作的非稳态滑动轴承,轴心的轨迹将形成一条轴心轨迹图。
为了保证形成完全的液体摩擦状态,对于实际的工程表面,最小油膜厚度必须满足下列条件:()21min Z z R R S h += (1)式中,S 为安全系数,通常取S ≥2;R z1,R Z2分别为轴颈和铀瓦孔表面粗糙度的十点高度。
滑动轴承实验是分析滑动轴承承载机理的基本实验,它是分析与研究轴承的润滑特性以及进行滑动轴承创新性设计的重要实践基础。
根据要求不同,滑动轴承实验分为基本型、综合设计型和研究创新型三种类型。
(1)掌握实验装置的结构原理,了解滑动轴承的润滑方式、轴承实验台的加载方法以及轴承实验台主轴的驱动方式及调速的原理。
液体摩擦动压向心滑动轴承的设计
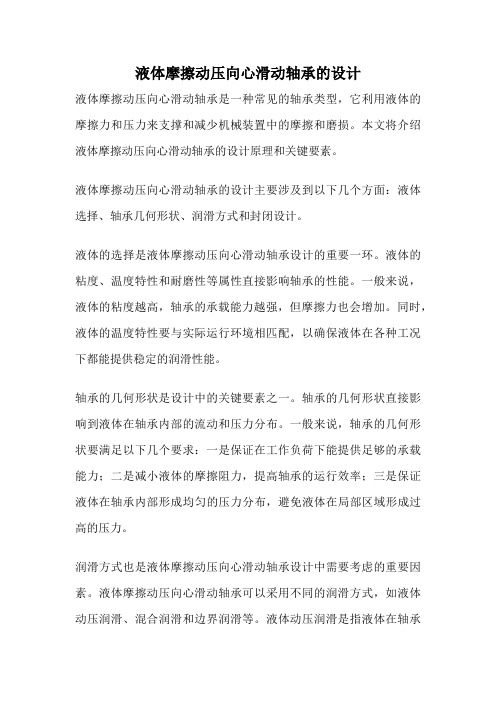
液体摩擦动压向心滑动轴承的设计液体摩擦动压向心滑动轴承是一种常见的轴承类型,它利用液体的摩擦力和压力来支撑和减少机械装置中的摩擦和磨损。
本文将介绍液体摩擦动压向心滑动轴承的设计原理和关键要素。
液体摩擦动压向心滑动轴承的设计主要涉及到以下几个方面:液体选择、轴承几何形状、润滑方式和封闭设计。
液体的选择是液体摩擦动压向心滑动轴承设计的重要一环。
液体的粘度、温度特性和耐磨性等属性直接影响轴承的性能。
一般来说,液体的粘度越高,轴承的承载能力越强,但摩擦力也会增加。
同时,液体的温度特性要与实际运行环境相匹配,以确保液体在各种工况下都能提供稳定的润滑性能。
轴承的几何形状是设计中的关键要素之一。
轴承的几何形状直接影响到液体在轴承内部的流动和压力分布。
一般来说,轴承的几何形状要满足以下几个要求:一是保证在工作负荷下能提供足够的承载能力;二是减小液体的摩擦阻力,提高轴承的运行效率;三是保证液体在轴承内部形成均匀的压力分布,避免液体在局部区域形成过高的压力。
润滑方式也是液体摩擦动压向心滑动轴承设计中需要考虑的重要因素。
液体摩擦动压向心滑动轴承可以采用不同的润滑方式,如液体动压润滑、混合润滑和边界润滑等。
液体动压润滑是指液体在轴承内形成动压膜,减小摩擦力和磨损;混合润滑是指液体和固体之间形成混合膜,提供更好的润滑效果;边界润滑是指液体无法形成润滑膜,但可以在摩擦表面上形成一层保护膜,减小摩擦和磨损。
封闭设计是液体摩擦动压向心滑动轴承设计中需要考虑的另一个重要因素。
封闭设计可以防止外界杂质进入轴承内部,同时防止液体的泄漏。
封闭设计通常包括密封圈和密封垫等部件,可以有效地提高轴承的使用寿命和可靠性。
液体摩擦动压向心滑动轴承的设计需要考虑液体选择、轴承几何形状、润滑方式和封闭设计等因素。
合理的设计可以提高轴承的承载能力、降低摩擦和磨损,并确保轴承的可靠性和使用寿命。
对于特定的应用场景,设计人员需要根据实际需求和工作环境选择适当的设计参数,以实现最佳的轴承性能。
液体动压滑动轴承实验指导书

实验四 液体动压滑动轴承实验指导书一、实验目的1、了解实验台的构造和工作原理,通过实验进一步了解动压润滑的形成,加深对动压原理的认识。
2、学习动压轴承油膜压力分布的测定方法,绘制油膜压力径向和轴向分布图,验证理论分布曲线。
3、掌握动压轴承摩擦特征曲线的测定方法,绘制f —n 曲线,加深对润滑状态与各参数间关系的理解。
二、实验原理及装置1.概述此项实验是径向加载的液体动压滑动轴承实验。
其目的是测量轴承与转轴间隙中的油膜在圆周方向的压力分布值(见图1),并验证径向油膜压力最大值批P MAX 不在外载荷F R 的垂线位置,而是在最小油膜厚度附近,即0=∂∂XP 处。
该实验还可以测试下列几项内容。
(1)测量轴承与转轴间隙中的油膜在轴线方向的压力分布值,并验证轴向压力分布曲线呈抛物线分布,即轴向油膜最大压力值在轴承宽度的中间位置(见图2)。
图1 周向油膜压力分布曲线 图2轴向油膜压力分布曲线(2)测量径向液体动压滑动轴承在不同转速、不同载荷、不同粘度润滑油情况下的摩擦系数f 值,根据取得的一系列f 值,可以做出滑动轴承的摩擦特性曲线,进而分析液体动压的形成过程,并找出非液体摩擦到液体摩擦的临界点,以便确定一定载荷、一定粘度润滑油情况下形成液体动压的最低转速,或一定转速、一定粘度润滑油情况下保证液体动压状态的最大载荷(见图3)。
图3 轴承摩擦特性曲线2.实验装置及原理本实验使用湖南长庆科教仪器有限公司生产的HS-B型液体动压轴承实验台如图4所示,它由传动装置、加载装置、摩擦系数测量装置、油膜压力测量装置和被试验轴承等组成。
图4 滑动轴承试验台1.操纵面板2.电机3.三角带4.轴向油压传感器接头5.外加载荷传感器6.螺旋加载杆7.摩擦力传感器测力装置8.径向油压传感器(7只)9.传感器支撑板10.主轴11.主轴瓦12.主轴箱1)传动装置由直流电机2通过三角带3带动主轴顺时针旋转,由无级调速器实现无级调速。
本实验台主轴的转速范围为3~375rpm,主轴的转速由装在面板1上的数码管直接读出。
液压传动轴承实验
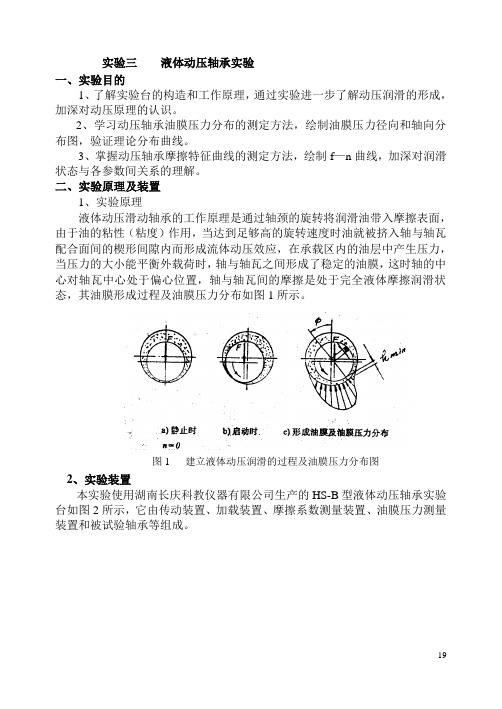
实验三液体动压轴承实验一、实验目的1、了解实验台的构造和工作原理,通过实验进一步了解动压润滑的形成,加深对动压原理的认识。
2、学习动压轴承油膜压力分布的测定方法,绘制油膜压力径向和轴向分布图,验证理论分布曲线。
3、掌握动压轴承摩擦特征曲线的测定方法,绘制f—n曲线,加深对润滑状态与各参数间关系的理解。
二、实验原理及装置1、实验原理液体动压滑动轴承的工作原理是通过轴颈的旋转将润滑油带入摩擦表面,由于油的粘性(粘度)作用,当达到足够高的旋转速度时油就被挤入轴与轴瓦配合面间的楔形间隙内而形成流体动压效应,在承载区内的油层中产生压力,当压力的大小能平衡外载荷时,轴与轴瓦之间形成了稳定的油膜,这时轴的中心对轴瓦中心处于偏心位置,轴与轴瓦间的摩擦是处于完全液体摩擦润滑状态,其油膜形成过程及油膜压力分布如图1所示。
图1 建立液体动压润滑的过程及油膜压力分布图2、实验装置本实验使用湖南长庆科教仪器有限公司生产的HS-B型液体动压轴承实验台如图2所示,它由传动装置、加载装置、摩擦系数测量装置、油膜压力测量装置和被试验轴承等组成。
图2 滑动轴承试验台1.操纵面板2.电机3.三角带4.轴向油压传感器接头5.外加载荷传感器6.螺旋加载杆7.摩擦力传感器测力装置8.径向油压传感器(7只)9.传感器支撑板10.主轴11.主轴瓦12.主轴箱1)传动装置由直流电机2通过三角带3带动主轴顺时针旋转,由无级调速器实现无级调速。
本实验台主轴的转速范围为3~375rpm,主轴的转速由装在面板1上的数码管直接读出。
2)加载装置油膜的径向压力分布曲线是在一定的载荷和一定的转速下绘制的。
当载荷改变或轴的转速改变时所测出的压力值是不同的,所绘出的压力分布曲线也是不同的。
转速的改变方法如前所述。
本实验台采用螺旋加载,转动螺杆即可改变载荷的大小,所以载荷之值通过传感器数字显示,直接在实验台的操纵板上读出。
3)摩擦系数测量装置径向滑动轴承的摩擦系数f随轴承的特性系数λ=μn/p值的改变而改变(μ—油的动力粘度,n—轴的转速,P—压力,P=W/Bd,W—轴上的载荷,W=轴瓦自重+外加载荷。
实验三 滑动轴承实验

实验17 滑动轴承实验之二滑动轴承的工作原理是通过轴颈将润滑油带入轴承摩擦表面,由于油的粘性(粘度)作用,当达到足够高的旋转速度时,油就被带入轴与轴瓦配合面间的楔形间隙内形成流体动压效应,即在承载区内的油层中产生压力。
当压力能平衡外载荷时,轴与轴瓦之间形成了稳定的油膜。
这时轴的中心对轴瓦中心处于偏心位置,轴与轴瓦之间处于完全液体摩擦润滑状态。
因此这种轴承摩擦小,轴承寿命长,具有一定吸振能力。
本实验就是让学生直观地了解滑动轴承的动压油膜形成过程与现象,通过绘制出滑动轴承径向油膜压力分布曲线与承载量曲线,深刻理解滑动轴承的工作原理。
一、实验目的1.观察滑动轴承的液体摩擦现象。
2.了解摩擦系数与压力及滑动速度之间的关系。
3.按油压分布曲线求轴承油膜的承载能力。
图17-1 试验机结构简图二、设备和工具试验机结构简图如图17-1所示,它包括以下几部分:1.轴与轴瓦轴8材料为45钢,轴颈径表面淬火,磨光,通过滚动轴承安装在支座上。
轴瓦7材料为锡青铜。
在轴瓦的中间截面处,沿半圆周均布七个小孔,分别与压力表相连。
2.加载系统由砝码16,通过由杆件11,12,13,14,15组成的杠杆系统及由杠件3,9,10组成的平行四边形机构,将载荷加到轴瓦上。
3.传动系统由直流电动机,通过三角带传动,驱动轴逆时针转动。
直流电动机用硅整流电源实现无级调速。
4. 供油方法轴转动时,由浸入油池中的轴,将润滑油均匀的带如轴与瓦之间的楔形间隙中,形成压力油膜。
5. 测摩擦力装置轴转动时,对轴瓦产生轴向摩擦力F ,其摩擦力矩F.d/2使构件3翻转。
由固定在构件3上的百分表2测出弹簧片在百分表处的变形量。
作用在支点1处反力Q 与弹簧片的变形成正比。
可根据变形测出反力Q ,进而可推算出摩擦力F 。
6. 摩擦状态指示装置图17-2 摩擦状态指示电路图17-2摩擦状态指示电路。
将轴与轴瓦串联在指示灯电路中,当轴与轴瓦之间被润滑油完全分开;及处于液体摩擦状态时,指示灯熄灭,当轴与瓦之间力非液体摩擦状态时指示灯亮或闪动。
液体动压径向滑动轴承实验

液体动压径向滑动轴承实验一、实验内容与目的:1.观察径向滑动轴承的摩擦现象,加深对概念的理解;2.测绘径向滑动轴承的摩擦特性曲线,掌握测绘方法;3.测绘径向滑动轴承油膜压力曲线,求油膜承载能力。
了解复杂问题的简化处理方法。
二、实验设备的结构与工作原理:本实验有二类(二种型号)设备,它们的结构示意图如图1和图2所示:它们包括以下几个部分:类型项目HS-A型试验台HZ型试验台轴与轴瓦轴材料为45号钢,轴径经表面淬火、磨光,表面粗糙度达到Ra=1.6用滚动轴承支承在机架上,轴瓦材料为ZCuSn5Pb5Zn5(旧国标为锡青铜6-6-3),轴瓦内孔精镗后与轴研配以保证与轴配合精度。
在轴瓦的中间径向截面处,沿半圆周布置七个与轴和轴瓦间油膜相通的小孔,这些小孔又分别与压力表相连。
七个小孔位置为沿半圆周的圆周角分别为300、500、700······1500。
七个小孔位置为沿半圆周的圆周角分别为22.50、450、67.50······157.50。
瓦外面与测力弹簧相接。
轴的转速调节装置轴的转动是由直流电动机通过“V”型带来带动的。
由无级调速器实现轴的无级调速。
本实验台轴沿顺时针(面对实验台面板)方向转动。
轴的转速范围为0~500转/分。
轴的转速由调速旋钮控制,实现无级调速。
转速值由数码管直接读出。
本实验台轴沿逆时针(面对实验台面板)方向转动。
轴的转速范围为0~500转/分。
轴的转速由调速旋钮控制,实现无级调速。
转速值由数码管直接读出。
轴与轴瓦间油膜压力测量轴与轴瓦间油膜压力是通过安装在轴瓦上的压力表测量的。
当轴在一定转速下承受一定载荷时,可以从分布在轴瓦上的七块压力表上读出此时油膜的压力值(压力分布情况前面已介绍)加载系统采用螺旋加载方式。
转动螺旋即可改变载荷的大小。
所加载荷之值通过传感器和数字电路由数码器显示。
二、滑动轴承实验指导及实验报告

滑动轴承实验报告一、实验目的及要求1、液体动力润滑滑动轴承油膜压力周向分布的测试分析;2、液体动力润滑滑动轴承油膜压力周向分布的仿真分析;3、液体动力润滑滑动轴承摩擦特征曲线的测定;4、液体动力润滑滑动轴承实验的其他重要参数测定:如轴承平均压力值、轴承PV值、偏心率、最小油膜厚度等。
二、实验基本原理实验台的构造如图3-1所示。
1、实验台的传动装置由直流电动机通过V带传动驱动轴沿顺时针(面对实验台面板)方向转动,由无级调速器实现轴的无级调速,由软件界面内的读数窗口读出。
2、轴与轴瓦间的油膜压力测量装置轴的材料为45号钢,经表面游淬火、磨光,由滚动轴承支承在箱体上,轴的下半部浸泡在润滑油中,本实验台采用的润滑油的牌号为0.34PaS。
轴瓦的材料为铸锡铅青铜,牌号为ZCuSn5Pb5Zn5(即旧牌号和ZQSn6-6-3)。
在轴瓦的一个径向平面内沿圆周钻有7个小孔,每个小孔沿圆周相隔20º,每个小孔连接一个压力表,用来测量该径向平面内相应点的油膜压力,由此可绘制出径向油膜压力分布曲线。
沿轴瓦的一个轴向剖面装有两个压力表,用来观察有限长滑动轴承沿轴向的油膜压力情况。
3、加载装置油膜的径向压力分布曲线是在一定的载荷和一定的转速下绘制的。
当载荷改变或轴的转速改变时抽测出的压力值是不同的,所绘出的压力分布曲线的形状也是不同的。
转速的改变方法于前所述。
本实验台采用螺旋加载,转动螺旋即可改变载荷的大小,所加载荷之值通过传感器数字显示,直接在测控箱面板右显示窗口上读出(取中间值)。
这种加载方式的主要优点是结构简单、可靠,使用方便,载荷的大小可任意调节。
4、摩擦系数f测量装置径向滑动轴承的摩擦系数f随轴承的特性系数值λ =ηn /p的改变而改变( ―油的动力粘度,n―轴的转速,p―压力,p= W/Bd,W―轴上的载荷,B―轴瓦的宽度,d―轴的直径)。
在边界摩擦时,f随λ的增大而变化很小(由于n值很小,建议用手慢慢转动轴),进入混合摩擦后,λ的改变引起f的急剧变化,在刚形成液体摩擦时f达到最小值,此后,随λ的增大油膜厚度亦随之增大,因而f 亦有所增大。
滑动轴承实验报告

液体动压滑动轴承实验报告一、实验目的1、测量轴承的径向和轴向油膜压力分布曲线。
2、观察径向滑动轴承液体动压润滑油膜的形成过程和现象。
3、观察载荷和转速改变时的油膜压力的变化情况。
4、观察径向滑动轴承油膜的轴向压力分布情况。
5、测定和绘制径向滑动轴承径向油膜压力曲线,求轴承的承载能力。
6、了解径向滑动轴承的摩擦系数f的测量方法和摩擦特性曲线λ的绘制方法。
二、实验设备及工具滑动轴承实验台三、实验原理1、油膜压力的测量轴承实验台结构如图1所示,它主要包括:调速电动机、传动系统、液压系统和实验轴承箱等部分组成。
图1 轴承实验台结构图1、操纵面板2、电机3、三角带4、轴向油压传感器接头5、外加载荷传感器6、螺旋加载杆7、摩擦力传感器测力装置8、径向油压传感器(8只)9、传感器支撑板10、主轴11、主轴瓦12、主轴箱在轴承承载区的中央平面上,沿径向钻有8个直径为1m m的小孔。
各孔间隔为22.50,每个小孔分别联接一个压力表。
在承载区内的径向压力可通过相应的压力表直接读出。
将轴径直径(d=60mm)按比例绘在纸上,将1~8个压力表读数按比例相应标出。
(建议压力以1c m代表5kgf/cm2)将压力向量连成一条光滑曲线,即得到轴承中央剖面油膜压力分布曲线)。
同理,读出第4和第8个压力表示数,由于轴向两端端泄影响,两端压力为零。
光滑连结0‘,8’,4‘,8’和0‘各点,即得到轴向油膜压力分布曲线。
2、摩擦系数的测量径向滑动轴承的摩擦系数f 随轴承的特性系数λ(λ=ηn/p )值的改变而改变。
在边界摩擦时,f 随λ值的增大而变化很小,进入混合摩擦后,λ值的改变引起f 急剧变化,在刚形成液体摩擦时f 达到最小值,此后,随λ值的增大油膜厚度亦随之增大,因而f 亦有所增大。
- 1、下载文档前请自行甄别文档内容的完整性,平台不提供额外的编辑、内容补充、找答案等附加服务。
- 2、"仅部分预览"的文档,不可在线预览部分如存在完整性等问题,可反馈申请退款(可完整预览的文档不适用该条件!)。
- 3、如文档侵犯您的权益,请联系客服反馈,我们会尽快为您处理(人工客服工作时间:9:00-18:30)。
3’
4’
5’
2’
F
3
45
6’
6
2 1’
1
7 7’
端泄影响系数
Pm
2’ 1’
3’ 4’
5’ 6’ 7’
12 3
4 5 67
七、实验报告要求
数据记录
压力表号 p1
p2
p3
p4
p5
p6
p7
p8 (轴向)
压力
江苏大学工业中心
七、实验报告要求
绘制油膜的轴向和周向压力分布曲线
3’
µl
=
0.001 m mm
5’
江苏大学工业中心
四、实验设备
动力装置 油压测试装置
加载装置
1-直流电动机 2-三角带 3-传感器 4-螺旋加载杆 5-弹簧片 6-测力计(百分表) 7-压力表(径向7只,轴向一只) 8-主轴瓦 9-主轴 10-主轴箱
江苏大学工业中心
五、实验步骤
实验条件:W=70kgf,n=500r/min。 1、打开电源。 2、将转速调至500r/min左右。 3、加载,外载荷为70Kg.f。 4、等待油压表稳定后读出P1-P8的数据,记录在表格中。
稳定后再进行数据记录。
江苏大学工业中心
分组实验
2’
F
3
4 5
6’
µP
MPa
= 0.01
mm
4’
8’
8’
2
1’ 1 20o
6 7’ 7
30o
30o
0
0
B/4
d
B/2
B
n
周向压力分布曲线
轴向压力分布曲线
江苏大学工业中心
七、实验报告要求
计算轴承3’ 的端泄4’影响系数
5’
2’
F
3
45
6’
6
2 1’
1
7 7’
2’ 1’
3’ 4’
5’ 6’ 7’
12 3
二、实验目的
观察向心滑动轴承动压油膜形成过程, 测绘出向心滑动轴承的轴向及周向油 膜压力分布曲线。
计算轴承的端泄影响系数
江苏大学工业中心
三、实验原理
剖分式向心滑动轴承
江苏大学工业中心
三、实验原理
形成液体动压润滑的条件
楔形间隙
连续充满的 润滑油
相对滑动 使得润滑油
大口进, 小口出。
江苏大学工业中心
B
周向压力分布曲线
轴向压分布曲线
江苏大学工业中心
六、数据处理
3’
4’ 5’
µl
=
0.001
m mm
2’
F
3 45 2
6’
µP
MPa
= 0.01
mm
8’
4’ 8’
1’ 1 20o
6 7’ 7
30o
30o
0
0
B/4
d
B/2
B
n
周向压力分布曲线 曲线分布于上半周内。
轴向压力分布曲线
江苏大学工业中心
六、数据处理
压力表号 p1
p2
p3
p4
p5
p6
p7
p8 (轴向)
压力 0.1 0.2 0.35 0.3 0.25 0.2 0.1 0.2
5、卸载(先卸载荷再卸转速),关机,断电。
江苏大学工业中心
六、数据处理
做油膜压力周向和轴向分布曲线
3’
4’
5’
2’
F
3 2
1’ 1
4
6’
5
6 7’
7
4’
8’
8’
0
0
B/4
B/2
三、实验原理
液体动压油膜的建立过程
初始状态 不稳定润滑阶段 稳定工作状态
楔形间隙
润滑油
大口进小口出
配合公差 楔形间隙
轴转动
泵油
动压油膜
承载
江苏大学工业中心
三、实验原理
江苏大学工业中心
四、实验设备
CTHD滑动轴承实验台
1-操纵面板 2-电机 3-三角带 4-轴向油压表接头 5-螺旋加载杆 6-百分表测力计装置 7-径向油压表(7只) 8-传感器支承板 9-主轴 10-主轴瓦 11-主轴箱
4 5 67
Pm
=? =?
江苏大学工业中心
七、实验报告要求
完成实验思考题 转速发生改变,油压分布曲线会不会发生改变? 为什么?
江苏大学工业中心
八、注意事项
在启动电机转动之前请确认载荷为空, 1 即要求先启动电机再加载。
2
外加载荷传感器所加负载不允许超过 100kg,以免损坏传感器元件。
由于油膜形成需要一小段时间,所以在 3 开机实验或在变化载荷或转速后请待其
《机械原理及设计》课程实验
液体动压润滑 向心滑动轴承实验
江苏大学工业中心
一、引言
实验对象:向心滑动轴承
轴承上 承受的 载荷方 向与轴 中心线 垂直。
滚动轴承
滑动轴承
江苏大学工业中心
一、引言
实验条件:液体动压润滑 利用轴本身回转时的泵油作用,把油带入 摩擦面间,建立压力油膜而把摩擦面分开。
江苏大学工业中心