改善作业现场的方法
ie工程现场改善方案

ie工程现场改善方案一、引言:随着工程行业的发展,越来越多的企业开始关注工程现场的改善问题。
IE工程作为一种管理和优化工程现场生产的方法,不仅可以提高生产效率,降低成本,还可以改善工作环境,提升员工工作满意度。
本文将以某工程现场为例,提出IE工程现场改善方案,以期为类似的工程现场提供参考。
二、现状分析:某工程现场是一家制造企业的生产基地,主要生产零部件和组件。
然而,该工程现场存在一些问题,例如生产效率低,物料管理混乱,工艺流程不够合理,员工工作负荷过重,工作环境较差等。
这些问题不仅影响了企业的生产和经营,也影响了员工的工作体验和生活质量。
因此,为了解决这些问题,需要对工程现场进行改善。
三、IE工程现场改善方案:1. 进行价值流分析:通过价值流分析,了解生产流程的瓶颈和浪费,找到生产效率低下的原因。
针对分析结果,制定相应的改善计划,优化生产流程。
2. 实施5S管理:建立起规范的物料管理和生产环境,包括整理、整顿、清扫、清洁、素养。
通过5S管理,提高现场的整体效率和安全性。
3. 设计并实施标准化作业程序:为每个工序制定标准化的作业程序,规范生产操作。
通过标准化作业程序,提高生产质量和效率。
4. 应用作业分析技术:通过作业分析,评估员工的工作强度和负荷,合理安排员工的工作任务,避免过重的工作负荷。
5. 实施人机工程学改善:对工作环境进行改善,包括工作高度、工作台面、照明等,提高员工的舒适度和安全性。
6. 建立绩效评价体系:建立合理的绩效评价体系,鼓励员工参与工程现场改善工作,激发员工的工作动力和创造力。
7. 进行员工培训:针对工程现场的改善方案,对员工进行相关的培训,提高员工的技能和素质,增强员工的工程现场管理意识。
8. 建立改善持续改进机制:建立持续改进的机制,定期对工程现场进行检查和评估,及时发现和解决问题,保持工程现场的良好状态。
四、改善效果评估:通过实施上述的IE工程现场改善方案,预计可以取得以下改善效果:1. 生产效率提高:通过价值流分析和优化生产流程,提高生产效率,减少浪费。
现场改善及ie手法

THANK YOU
感谢聆听
时间研究
通过观察和测量作业人员完成某项任务所需的时间,制定合理的时 间标准。
作业标准化
将最优的作业方法和流程标准化,确保所有作业人员都能按照统一 的标准进行操作,提高生产效率和产品质量。
标准作业程序(SOP)制定
编写详细的标准作业程序,明确每一步骤的操作规范和要求,为作 业人员提供明确的指导。
生产线平衡与布局优化
运用各种计划和控制手段,确 保生产系统按照预定目标高效 运行。
IE手法在现场改善中的应用
流程优化
通过分析和改进工作流程,消除浪费、提高效率 。例如,减少不必要的操作步骤、简化工作流程 等。
设备改善
对生产设备进行改进和优化,提高设备效率和可 靠性。例如,采用自动化设备、改进设备维护计 划等。
物料管理
意义
现场改善是企业提高竞争力、实现可持续发展的重要手段之一。 通过现场改善,企业可以不断提高产品质量、降低生产成本、提 高生产效率、增强员工士气,从而赢得更多的市场份额和客户信 任。
现场改善的目标与原则
目标
现场改善的主要目标是提高生产效率、降低生 产成本、提高产品质量、增强员工士气等,以
实现企业的整体经营目标。
现场改善及IE手法
目
CONTENCT
录Hale Waihona Puke • 现场改善概述 • IE手法简介 • 现场改善的步骤与方法 • IE手法在现场改善中的具体应用 • 现场改善的实践案例 • 现场改善的挑战与对策
01
现场改善概述
现场改善的定义与意义
定义
现场改善是一种通过优化工作流程、提高工作效率和质量、降低 成本等方法,对生产现场进行持续改进的管理方法。
现场改善计划和行动计划

现场改善计划和行动计划
目的:
通过分析工厂现场的风险点和不足,制定改善计划和具体行动,以提高工厂整体安全管理水平。
一、现场识别和评估
1. 通过工厂现场视察,识别存在的风险点,包括:
- 機器操作区域无安全障壁
- 操作人员无个人防护装备
- 操作程序缺少详细說明
2. 使用风险评估表对每個风险点进行风险等級分析
二、改善目标和措施
根据风险分析结果,制定以下改善目标和措施:
1. 目标:消除存在高风险可能的地方
措施:为所有机器设置安全罩及隔离区
2. 目标:降低中风险可能性
措施:为所有操作人员提供安全装备,并制定详细操作规程
3. 目标:杜絕低风险事件的發生
措施:开展安全培训及作业管制
三、实施计划
1. 责任单位:安全管理部门
2. 实施日期:2021年6月1日-2021年8月31日
3. 具体任务安排:参照附件
4. 资源保障:根据实施计划安排所需人力、物力支持
四、效果评估
实施完工后使用相同的评估表对现场进行再评估,调查员工意见,检查达成情况,并写出评估报告。
以上为一份简单的"现场改善计划和行动计划"样本,实际应根据企业的实际情况进行修改完善。
精益现场改善提案表范文

精益现场改善提案表范文
内容:
尊敬的领导:
我代表部门,就现场改善提出以下提案。
一、存在问题
1. 物料堆放无序,查找不便
我们部门的物料堆放没有固定位置,员工需要花费时间去不同地方找料,降低了工作效率。
2. 器具使用无序,不易查找
部门共用器具放置混乱,使用后没有放回原位,导致频繁搜索器具的时间。
3. 作业区划分不清晰,容易发生混乱
作业区没有明确的标示与划分,不同作业区域混杂,导致人员频繁走动和工具搜索。
二、改善措施
1. 设立物料固定堆放区,贴标示,定期清点。
在部门空地处划定物料专区,分类堆放物料,并贴上标示,定期核查物料。
2. 设置公共器具存放处,使用后放回原位。
在显眼位置设置公共器具架,要求使用后放回原位。
3. 对作业区进行标示划分,人员就地作业。
用标示标出不同作业区域,人员就近当前区域作业,减少走动。
三、预期效果
1. 查找物料效率提高30%
2. 查找器具效率提高20%
3. 每人无效走动减少50%
改善这些问题,可以提高部门作业效率,创建更好的工作环境。
感谢领导的支持!
此致
礼!
部门全体员工
年月日。
生产现场改善方案

生产现场改善方案生产现场改善是指通过不断优化和改进生产现场的各种因素,以提高生产效率、降低生产成本、提升产品质量和保障员工安全等目标的一系列措施。
在生产现场改善中,我们可以采取以下方案来提升生产效率和质量。
一、标准化工作流程标准化工作流程是生产现场改善的基础,它可以确保每一项工作都按照固定的程序进行,并且能够无差错地完成。
通过标准化工作流程,可以减少工作中的浪费和瑕疵,提高生产效率和质量。
标准化工作流程的实施需要进行详细的工作流程分析和标准操作程序的制定,包括设备设置、原材料准备、工艺操作、质量检验等各个环节。
同时,还需要进行相关员工培训,确保每一位员工都能够准确地遵循标准操作程序进行工作,并且能够熟练地应对各种工作场景。
二、自动化设备的应用在现代生产中,自动化设备的应用可以大大提高生产效率和质量。
自动化设备能够取代人工操作,减少人为的误差和疲劳,提高生产效率,减少生产时间。
同时,自动化设备能够提供更高的精确度和稳定性,减少产品瑕疵率,提高产品质量。
在引入自动化设备时,需要评估投资回报率,并进行详细的设备选型和安装调试。
同时,还需要进行相关员工培训,让员工熟练掌握自动化设备的操作和维护,确保设备的正常运转。
三、现场布局的优化现场布局是生产现场改善的重要内容之一,它能够影响到生产效率和安全性。
通过优化现场布局,可以减少物料和人员的移动距离,缩短物料和信息的传递时间,提高生产效率。
同时,优化现场布局还能够提高生产现场的安全性,减少事故发生的概率。
在优化现场布局时,需要进行详细的现场调研和分析,了解现场的工作流程和各个设备之间的关系。
同时,还需要考虑人员的工作条件和安全要求,合理分配工作空间和通道。
最后,需要进行现场布局的调整和改进,确保布局的合理性和可行性。
四、供应链管理的优化供应链管理是生产现场改善的重要组成部分,它关系到物料的准时供应、库存的控制和质量的保障。
通过优化供应链管理,可以提高物料的及时性和准确性,减少物料的浪费和停工现象。
精益生产中现场改善有何方法

精益生产中现场改善有何方法在当今竞争激烈的市场环境下,企业要想生存和发展,就必须不断提高生产效率、降低成本、提升产品质量。
精益生产作为一种先进的生产管理理念和方法,已经被越来越多的企业所采用。
而现场改善则是精益生产的核心环节之一,通过对生产现场进行持续的改进和优化,可以有效地消除浪费、提高生产效率和产品质量。
那么,精益生产中的现场改善到底有哪些方法呢?一、5S 管理5S 管理是精益生产中现场改善的基础,包括整理(Seiri)、整顿(Seiton)、清扫(Seiso)、清洁(Seiketsu)和素养(Shitsuke)五个方面。
整理就是区分要与不要的物品,将不要的物品清除出工作现场,只保留必要的物品。
这样可以减少现场的混乱,提高工作效率。
整顿是将整理后留下的必要物品进行分类、定位、标识,使其易于寻找和使用。
通过整顿,可以缩短寻找物品的时间,提高工作效率。
清扫是指清除工作现场的灰尘、油污、垃圾等,保持现场的清洁。
清扫不仅可以创造一个良好的工作环境,还可以发现设备的潜在问题。
清洁是将整理、整顿、清扫的做法制度化、规范化,保持现场的良好状态。
素养是指培养员工养成良好的工作习惯和遵守规章制度的意识,使5S 管理能够长期有效地实施下去。
通过实施 5S 管理,可以使工作现场变得整洁、有序,提高工作效率,减少浪费,为现场改善打下坚实的基础。
二、标准化作业标准化作业是指对生产过程中的每一个操作步骤、动作、时间、质量标准等进行明确规定,使员工能够按照标准进行操作。
标准化作业可以消除操作过程中的变异,提高生产效率和产品质量。
制定标准化作业的过程中,需要对生产过程进行详细的观察和分析,找出最佳的操作方法和流程,并将其形成标准文件。
同时,要对员工进行培训,确保员工能够理解和掌握标准化作业的要求。
在实施标准化作业的过程中,要不断地对标准进行检查和修订,以适应生产条件的变化和改进的需要。
三、目视管理目视管理是通过各种视觉信号,如颜色、标识、图表等,将生产现场的信息直观地展示给员工,使员工能够快速地了解生产状况和问题。
作业存在的问题及改进措施
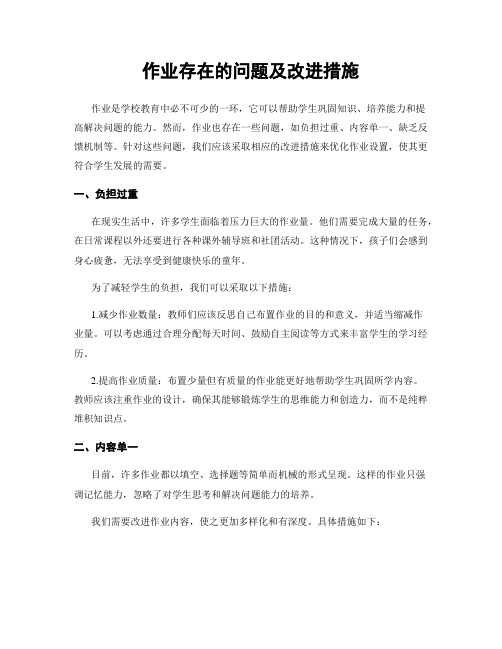
作业存在的问题及改进措施作业是学校教育中必不可少的一环,它可以帮助学生巩固知识、培养能力和提高解决问题的能力。
然而,作业也存在一些问题,如负担过重、内容单一、缺乏反馈机制等。
针对这些问题,我们应该采取相应的改进措施来优化作业设置,使其更符合学生发展的需要。
一、负担过重在现实生活中,许多学生面临着压力巨大的作业量。
他们需要完成大量的任务,在日常课程以外还要进行各种课外辅导班和社团活动。
这种情况下,孩子们会感到身心疲惫,无法享受到健康快乐的童年。
为了减轻学生的负担,我们可以采取以下措施:1.减少作业数量:教师们应该反思自己布置作业的目的和意义,并适当缩减作业量。
可以考虑通过合理分配每天时间、鼓励自主阅读等方式来丰富学生的学习经历。
2.提高作业质量:布置少量但有质量的作业能更好地帮助学生巩固所学内容。
教师应该注重作业的设计,确保其能够锻炼学生的思维能力和创造力,而不是纯粹堆积知识点。
二、内容单一目前,许多作业都以填空、选择题等简单而机械的形式呈现。
这样的作业只强调记忆能力,忽略了对学生思考和解决问题能力的培养。
我们需要改进作业内容,使之更加多样化和有深度。
具体措施如下:1.鼓励开放性思考:为了激发学生的创造力和批判性思维,可以设置一些开放性问题,让学生通过分析和解释来回答。
这样的作业可以促使学生主动思考,并培养他们在未来面对新问题时独立思考和解决问题的能力。
2.增加实践性任务:将理论与实际结合,给予学生一些实践任务。
这样的任务既可以涉及到课堂内部分情境模拟,也可以涉及到社会实践活动。
通过实际操作,学生能够更好地理解所学知识,并将其应用于实际场景中。
三、缺乏反馈机制许多作业评价仅仅停留在字数是否达标、是否按照要求完成等方面,缺乏个性化的反馈。
这种做法无法真正帮助学生发现自身的问题,从而提高他们的学习能力。
为了更好地评价作业、给予学生个性化的反馈,我们可以进行以下改进:1.注重思维过程:在评价过程中,教师应该关注学生解题的思维过程,并给予针对性的指导和建议。
生产车间现场改善方案
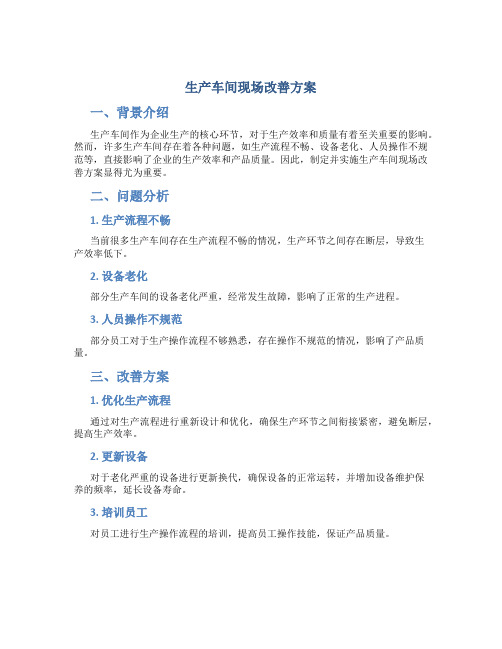
生产车间现场改善方案一、背景介绍生产车间作为企业生产的核心环节,对于生产效率和质量有着至关重要的影响。
然而,许多生产车间存在着各种问题,如生产流程不畅、设备老化、人员操作不规范等,直接影响了企业的生产效率和产品质量。
因此,制定并实施生产车间现场改善方案显得尤为重要。
二、问题分析1. 生产流程不畅当前很多生产车间存在生产流程不畅的情况,生产环节之间存在断层,导致生产效率低下。
2. 设备老化部分生产车间的设备老化严重,经常发生故障,影响了正常的生产进程。
3. 人员操作不规范部分员工对于生产操作流程不够熟悉,存在操作不规范的情况,影响了产品质量。
三、改善方案1. 优化生产流程通过对生产流程进行重新设计和优化,确保生产环节之间衔接紧密,避免断层,提高生产效率。
2. 更新设备对于老化严重的设备进行更新换代,确保设备的正常运转,并增加设备维护保养的频率,延长设备寿命。
3. 培训员工对员工进行生产操作流程的培训,提高员工操作技能,保证产品质量。
四、实施步骤1. 制定改善计划根据问题分析,制定具体的改善方案和实施计划。
2. 落实责任人明确改善方案的责任人,确保改善工作有序进行。
3. 实施改善方案按照制定的改善方案,逐步实施生产车间现场改善工作。
4. 监督检查定期对改善工作进行监督检查,及时发现问题并采取措施纠正。
五、改善效果评估1. 生产效率提升优化生产流程和更新设备,生产效率得到提升,产能得到增加。
2. 产品质量提高员工操作水平提升和设备更新,产品质量得到提高,消除了质量问题带来的损失。
3. 员工满意度提升通过培训员工,提高了员工的工作技能和工作积极性,增加了员工的满意度。
六、结语生产车间现场改善是企业提高生产效率和产品质量的一个重要举措,通过优化生产流程、更新设备和培训员工,可以实现生产车间的现场改善,对于企业的发展具有重要意义。
希望以上改善方案能够为企业的生产车间改善工作提供一定的参考和指导。
精益现场改善8个方法

IE现场改善8个方法:视与视ECRS动作分析软件1、工艺流程查一查即向工艺流程要效益。
分析现有生产、工作的全过程,哪些工艺流程不合理,哪些地方出现了倒流,哪些地方出现了停放,包括储藏保管、停放状态、保管手段(如储存容器配备、货架配备、设施条件)、有无积压状态?哪些工艺路线和环节可以取消、合并、简化?寻找最佳停放条件,确定经济合理的工艺路线。
请用视与视ECRS工时分析软件2、平面图上找一找即向平面布置要效益。
仔细检查和分析工厂平面布置图、车间平面布置图和设备平面布置图,分析作业方式和设备、设施的配置,按生产流程的流动方向,有无重复路线和倒流情况,找出不合理的部分,调整和设计一种新的布局,使生产流程在新的布置图上路线最短,配置最合理。
请用视与视ECRS工时分析软件3、流水线上算一算即向流水线要效益。
研究流水线的节拍、每个工序的作业时间是否平衡,如果发现不平衡,就要通过裁并、简化、分解等等手法,平衡流水线。
消除因个别工序缓慢而导致的窝工和堆积。
请用视与视ECRS工时分析软件4、动作分析测一测即向动作分析要效益°研究工作者的动作,分析人与物的结合状态,消除多余的动作、无效动作或缓慢动作,如弯腰作业、站在凳子上作业、蹲着作业、作业场所不畅、没有适合的工位器具、人与物处于寻找状态等,通过对人的动作和环境状态的分析和测定,确定合理的操作或工作方法;探讨减少人的无效劳动,消除浪费,解决现场杂乱,实现人和物紧密结合,提高作业效率。
请用视与视ECRS工时分析软件5、搬运时空压一压即向搬运时间和空间要效益。
据统计,在产品生产中搬运和停顿时间约占70・80%,搬运的费用约占加工费的25・40%,要通过对搬运次数、搬运方法、搬运手段、搬运条件、搬运时间和搬运距离等综合分析,尽量减少搬运时间和空间,寻找最佳方法、手段和条件。
请用视与视ECRS工时分析软件6、人机工程挤一挤即向人机联合作业要效益。
人和设备构成了人机工程,在分析时要分析作业者和机器在同一时间内的工作情况,有无窝工、等待、无效时间,通过调整工作顺序改进人机配合,寻求合理的方法,使人的操作和机器的运转协调配合,将等待时间减少到最大限度,充分发挥人和机器的效率。
现场改善方案及几点建议
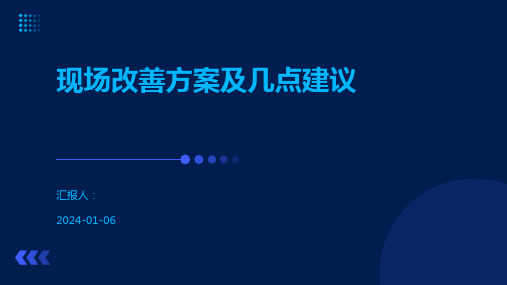
持续改进
根据评估结果和生产实际情况,对标准作业 指导书进行持续改进。
目视化管理
标识管理
对现场物品、区域、设备等进 行明确标识,方便识别。
颜色管理
利用不同颜色区分物品、区域 或状态,提高视觉效果。
图形管理
利用图表、图示等形式展示数 据、流程等信息,便于理解。
看板管理
设置看板,展示关键指标、目 标、计划等信息,提高管理效
03
设备与工装管理
设备维护保养
定期检查
制定设备检查计划,定期对设备进行全面检查,确保 设备处于良好状态。
预防性维护
实施预防性维护,定期更换易损件,清洗和润滑关键 部位,预防设备故障。
应急维修
建立应急维修机制,对突发故障进行快速响应和处理 ,尽快恢复生产。
工装夹具优化
分析和改进
对现有工装夹具进行分析,找出 存在的问题和改进点,进行优化
率。
02
人员培训与激励
培训计划
01
定期培训
制定定期培训计划,确保员工不 断更新知识和技能,提高工作效 率。
针对性培训
02
03
培训效果评估
根据员工的岗位和职责,提供针 对性的培训课程,以满足工作需 求。
对培训计划进行定期评估,了解 员工的学习成果,以便调整培训 内容和方式。
激励机制
薪酬激励
提供具有竞争力的薪酬福利,激发员工的工作积极性和创造力。
建立应急预案,组织应急演练,提高应对突发事 件的能力。
环境因素控制
识别现场环境因素,评估其对 环境的影响,制定相应的控制
措施。
加强废弃物分类、回收和处 理工作,减少对环境的污染
。
合理利用资源,降低能源消耗 ,提高能源利用效率。
现场七大基础改善手法

现场七大基础改善手法一、定置管理企业做“6S”要进行定置、定位,有的企业做的是五定管理,即定置、定位、定点、定容、定量。
1.定置概念定置是把物品放在合理的位置。
所谓定置管理,又称为定容管理,是根据物料特点制作专门的放置容器或设制专门的放置方法,确保员工取放方便,提高效率。
“置”是放置容器或放置方法的意思,不是位置的“置”。
2.定置方法改善案例具体操作见视频,在此不再赘述。
定置的方法在现场运用比较广泛,企业要善于利用此硬件上的保证,避免因员工的不同而造成不同效果,保证现场的质量和效率。
二、定位管理定位管理又称定点管理,是将物品存放在最合理的位置,在生产过程中方便取放。
这个点是某一具体位置,“位”是位置的意思。
不同的东西摆放在不同地方,带来的劳动强度和作业效率是不同的。
根据工业工程中的动作经济原则,企业要进行作业配置,即要让员工在工序作业时,伸手就能够取到需要的东西,左右手要用的东西分别放在左右两边,最好在两个小臂范围之内,也即最适合区域,如果两个空间不够,可以将手伸出去的空间区域也叫适合区。
日本专家认为,员工在工序上作业,手的移动距离在30厘米以内是可以接受的,超过30厘米就需要进行改善。
【案例】气动扳手的改善某企业的一个车间进行家电组装,需用气动扳手。
改善前,气动扳手是利用低压空气打螺栓,当工序作业产品流出来后,扳手放在右边的作业台上,拿过扳手连打若干螺栓以后,需要好几分钟才会过来,但如果把气动扳手放回去,位置稍微不恰当,气动扳手控制阀门的叶片就会突出来,一转扳手,容易滚到地下,造成很多麻烦。
定位改善后,把扳手挂起来,调节好相应的位置高度,作业时手一伸(不要超过30厘米),一抓一打,打完后手一松,扳手自然弹回去,给员工减少很多麻烦。
可见,对物品进行合理定位,可以解决员工动作强度的问题。
三、定量管理定量管理就是在定置管理的基础上,规定一个容器中存放物品的数量,便于材料供应和数量管理。
现代工业生产讲究精细化,现场生产主要靠最精细化的配送,而生产的产品根据不同的形状有不同的包装,这就需要进行定量管理。
现场改善方案及几点建议

Luzhou Detian Ceramics Co., Ltd
何志 2016.6.27
尊敬的刘总、李总并各位领导:
本人加入得天陶瓷已一个多月的时间。期间耗时半个月对公司所有车间的生产流
程有了一个初步的熟悉,对于公司的工艺流程及生产管理现状已经有了一个初步的认识。后 定职于整个公司最重要也是最关键的成型车间,在此期间发现了一系列急需改善的问题点。 根据本人以前的工作经验,拟定了部分的改善思路与几点建议。由于本人以前未接触过陶瓷 行业,肯定存在诸多认识不到位之处,还望各位领导指教。 以上 何志 2016.6.27
排拉方式:
通过现场实测数据分析,此排拉的瓶颈岗位在于精坯外观全检。 瓶颈岗位时间:N/T=6.46S 标准工时:3600S/6.5S=553个; 若每日上班8H,其中,作业时间7.5H,则全天产能为7.5H*553个=4153个; 若按现阶段产能,共需6组人完成每日25000的产能; 目前仅有4人,实行抽检的方式,若导入全检,则总人力需求为6组*2人=12人,需求8人; 增加的人力成本: 全检人员采用计时的方式,若每人每月2000元工资,则月增加人力成本2000*8=16000元; 若采取全检的方式,其他不看,仅瓶底泥渣一项就提升大约2%的成瓷良率水平。减 少报废的件数:25000*0.02=500件;每月节省500件*30天=15000件; 假设成瓷的报废成本为2元/个,则减少报废15000件*2元=30000元,相比人力成本支出可节约 公司成本30000元-16000元=14000元。 故根据以上数据得出结论,必须在精坯检导入全检的方式,以提升成瓷的良率水平。 若成型的制程改善比较明显,能大大提升直通率,才可考虑由全检变更为抽检。这样才 能最大限度的为公司节省成本。若导入流水线,则可将全检集成在流水线,这样成型车间的 精坯可直接到达烧成车间,进入窑炉烧制,提高坯架车周转效率。
改善现场作业环境,消除潜在安全隐患的文章
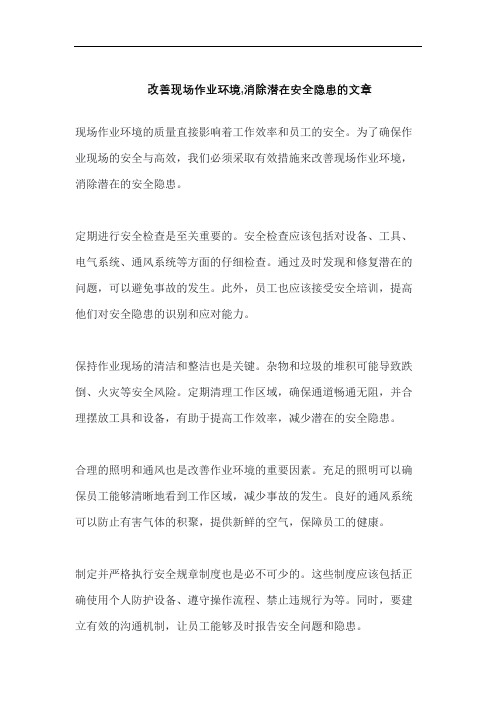
改善现场作业环境,消除潜在安全隐患的文章
现场作业环境的质量直接影响着工作效率和员工的安全。
为了确保作业现场的安全与高效,我们必须采取有效措施来改善现场作业环境,消除潜在的安全隐患。
定期进行安全检查是至关重要的。
安全检查应该包括对设备、工具、电气系统、通风系统等方面的仔细检查。
通过及时发现和修复潜在的问题,可以避免事故的发生。
此外,员工也应该接受安全培训,提高他们对安全隐患的识别和应对能力。
保持作业现场的清洁和整洁也是关键。
杂物和垃圾的堆积可能导致跌倒、火灾等安全风险。
定期清理工作区域,确保通道畅通无阻,并合理摆放工具和设备,有助于提高工作效率,减少潜在的安全隐患。
合理的照明和通风也是改善作业环境的重要因素。
充足的照明可以确保员工能够清晰地看到工作区域,减少事故的发生。
良好的通风系统可以防止有害气体的积聚,提供新鲜的空气,保障员工的健康。
制定并严格执行安全规章制度也是必不可少的。
这些制度应该包括正确使用个人防护设备、遵守操作流程、禁止违规行为等。
同时,要建立有效的沟通机制,让员工能够及时报告安全问题和隐患。
持续的培训和教育是提高员工安全意识的关键。
通过定期的安全培训,员工可以了解最新的安全知识和操作技巧,增强他们的安全意识和责任感。
改善现场作业环境和消除潜在安全隐患是一项综合性的工作。
只有通过定期检查、清洁整理、良好的照明通风、严格的规章制度和持续的培训教育,我们才能创造一个安全、高效的工作环境,保障员工的生命安全和企业的稳定发展。
现场作业的改善
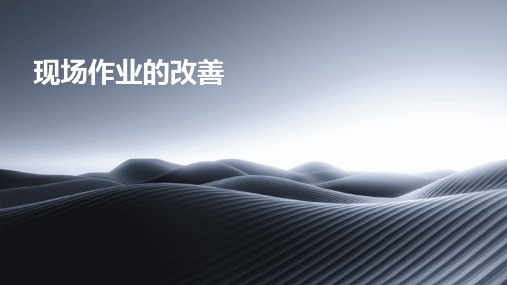
根据现场情况,制定详细的改 善计划,包括改善目标、改善 措施、实施步骤、资源需求等 ,以确保改善工作的顺利进行 。
现场作业改善需要各部门的紧 密协作,包括生产、技术、质 量、安全等方面的人员,应建 立高效的团队协作机制,确保 改善工作的顺利推进。
在现场作业改善过程中,应注 重数据收集和分析,及时发现 问题并采取相应措施,持续改 进和优化现场作业流程。
提高作业质量
通过标准化作业和质量控制, 提高产品质量和客户满意度。
促进企业持续发展
通过不断改善现场作业,提高 企业竞争力和市场地位。
汇报范围
改善方案制定
根据现状分析,制定相应的改善方案,包 括优化作业流程、提高资源配置效率、引
入新的技术和设备等方面。
A 现场作业现状分析
对当前的现场作业情况进行详细分 析,包括作业流程、资源配置、作
改善措施中包括减少资源浪费、提高设备利用率等,有效降低 了现场作业的成本。
通过引入先进的作业技术和方法,本次改善提升了现场作业的 质量水平,减少了错误和缺陷的发生。
改善措施着重加强了现场作业的安全管理,提高了员工的安全 意识和操作技能,确保了作业过程的安全性。
对未来现场作业改善的展望和期待
智能化发展
制定具体的改进计划,包括改进目标、时间表、资源需求等,以确保持续改进的 顺利进行。
05
现场作业改善的经验与教训
改善过程中的经验和教训总结
充分了解现场情况
制定详细的改善计划
加强团队协作
注重数据分析和持续改进
在进行现场作业改善前,必须 充分了解现场的实际情况,包 括设备、人员、环境等方面, 以便制定切实可行的改善方案 。
质量问题
现场作业质量不稳定,存在产品缺陷和不良品,影响客户满意度 和企到位
施工现场作业环境改善与舒适度提升的方法与实践

施工现场作业环境改善与舒适度提升的方法与实践一、现状及问题分析施工现场作为一个高强度、高风险的工作环境,人们常常对其产生不满和不适应。
尘土飞扬、噪声刺耳,使得工人们长时间暴露在恶劣环境中,身心压力倍增。
同时,作业环境较差也会影响到工作效率和质量,给施工单位带来一定的经济损失。
二、物理环境改善改善施工现场物理环境,是提升施工舒适度的重要方法。
例如,加强施工现场的噪音防护,可以采用隔音墙、隔音隔热窗等技术手段,将噪音减至最小限度。
另外,施工现场的通风和空气质量也需要关注,可以增设通风设备,确保室内空气流通,减少粉尘和有害气体的积聚。
三、安全管理与培训施工现场的安全管理是工人们工作舒适度的保障。
施工单位应完善安全管理制度,定期检查施工现场的安全设施,保证设备的安全可靠性。
此外,组织专业人员对工人进行安全培训,提高他们的安全意识和应急处理能力,从而降低事故发生的概率,保护工人的生命安全。
四、人性化的管理措施为提升施工现场的舒适度,施工单位可以采取一系列人性化管理措施。
比如,设置休息区域,为工人提供舒适的休息设施,在工作间隙给予工人必要的休息和放松时间。
同时,可以建立员工关怀机制,关注员工的生活需求和心理健康,为工人提供良好的工作氛围。
五、施工现场文化建设文化建设是提升施工现场舒适度的重要环节。
通过开展各类文化活动,如工人技能大赛、文艺演出等,增强工人的凝聚力和归属感。
同时,可以悬挂一些正能量的标语、画面等,在施工现场营造积极向上的氛围。
六、人力资源管理优化合理管理施工现场的人力资源,对环境改善和舒适度提升起着至关重要的作用。
施工单位可以通过多元化的用工形式,提高工人的待遇和福利,增强他们的工作积极性和创造力。
此外,可以加强对工人的激励和奖励,鼓励他们在工作中发挥个人特长,提高整体效能。
七、技术手段与创新借助科技的力量,通过技术手段的创新,可以进一步改善施工现场的作业环境。
采用先进的设备和工艺,能够有效降低噪音、粉尘和有害气体的产生。
强化现场作业标准

强化现场作业标准
强化现场作业标准是提高生产效率和保障生产安全的重要手段。
通过制定明确的作业标准,并确保员工严格遵守这些标准,可以确保生产过程的稳定性和一致性,同时减少错误和事故的发生。
以下是一些关于如何强化现场作业标准的建议:
1.制定明确的作业标准:与现场作业人员共同制定明确的作业标准,包括操作规程、安全规程和质量控制标准等。
确保这些标准具体、可操作性强,能够在实践中得到有效执行。
2.提供培训和指导:为现场员工提供充分的培训和指导,确保他们了解并掌握作业标准。
通过培训和指导,帮助员工提高技能水平,增强对标准的理解和执行力。
3.建立监督和激励机制:建立有效的监督和激励机制,对遵守作业标准的员工给予奖励和表彰,对违规行为进行惩罚和纠正。
通过正负激励相结合的方式,激发员工遵守标准的积极性。
4.定期审查和更新标准:定期审查作业标准,根据实际情况进行必要的更新和改进。
确保标准始终能反映当前的最佳实践和技术水平,以保证现场作业的持续优化。
5.促进跨部门合作与交流:加强跨部门之间的合作与交流,共同分享经验和最佳实践。
通过跨部门的合作,可以发现现有标准的不足之处,并相互学习和借鉴,提高标准的完善性和实用性。
6.运用科技手段提升管理效率:运用科技手段,如智能化监控、数据分
析等,提升现场管理的效率和精度。
通过科技手段对现场作业数据进行实时采集、分析和反馈,及时发现和解决问题,促进标准的更好执行。
总之,强化现场作业标准是一个持续的过程,需要领导层的支持和员工的积极参与。
通过不断完善和优化标准,提高员工的技能和意识,加强监督和激励,可以有效地提高现场作业的效率和安全性。
- 1、下载文档前请自行甄别文档内容的完整性,平台不提供额外的编辑、内容补充、找答案等附加服务。
- 2、"仅部分预览"的文档,不可在线预览部分如存在完整性等问题,可反馈申请退款(可完整预览的文档不适用该条件!)。
- 3、如文档侵犯您的权益,请联系客服反馈,我们会尽快为您处理(人工客服工作时间:9:00-18:30)。
1 多种少量的生产管理要领 2 生产效率实战案例分析演练
3 综合效率损失分析
4 改善作业现场的方法
5 提升效率的管理技巧
6 生产进度的有效控制手段
一、多种少量的生产管理要项
NO 1 多 种 品种多 2 少量 特 性 管理方式(例)
换线多
批量小 样品多 订货生产
3. 换线时间、次数降低 1. 标准化 2. 群组技术(GT)运用 1. 小组生产 2. 多能工 3. 专线生产 4. 个人生产 1. 开发进度之掌握 2. 主力产品的推出 1. 生产周程管制 2. 混线生产 3. 产销工作及程序调整 4. 制程时间缩短 5. 短线生产
● ● ● ● ●
此项作业(动作)可否剔除
此项作业经努力可否消除掉 可否减少工作环节或时间 是否可以不必搬运 是否可以减少作业人数
四、改善作业现场的方法
工作简化法(三) 2、
● ● ● ● ●
几个作业可否同时进行 几项作业可否合并进行 工程分割是否恰当 工程之间负荷平衡度如何
检验工作能否合并
四、改善作业现场的方法
四、改善作业现场的方法
工程分析法(二)
有关检验方面的改善
● ● ● ● ● ●
可否不要检验
可否由全检变为抽检
定点检验可否改变为巡回检验 检验的量可否减少 检验基准、方法、数量是否恰当
批量计数可否自动化 /
四、改善作业现场的方法
工程分析法(三)
三、综合效率损失分析
某企业周异常工时统计表
No.
1
异常原因
计划异常 材料异常 设备异常 品质异常 产品异常
异常工时 责任单位 责任工时
396 采购 业务 生管 采购 仓库 生技 制造 品管 采购 制造 开发 198 124 74 792 198 148 50 618 124 99 50
2 3
990 198
生产日报表
部门:
Ⅰ 、 应 有 时 间 =( 1+2+3) 项次 1 2 3 合 项 目 时 间 项次 1 2 3 合 Ⅲ、除外时间 项次 1 2 3 4 5 6 合 实勤时间 项次 1 2 3 4 5 合 综合效率 说明事项: = 计 作业能率 × 稼动率 = 产品名称 项 早 开 教 盘 清 公 计 损失时间 生产数 良品数 目 会 会 育 点 扫 出 时 间 项次 1 2 3 4 5 6 合 实际时间 标准工时 标准时间 实用时间 项 目 项 缺 目 勤 应出勤数 加班时间 借入时间 计
1、实施目标管理 2、善用时间管理
3、推动颜色管理
4、活用数字管理
5、贯彻源头管理
6、使生产线平衡
工作简化法(四) 3、
● ●
作业顺序可否重排
工作流程可否重排
●
●
工厂布置可否调整
物流线路可否改变
四、改善作业现场的方法
工作简化法(五) 4、 ● 有无更简单的替代方法 ● 工具可否改善 ● 可否机械化、自动化 ● 全检可否改成抽检 ● 检验的量可否减少 ● 可否缩短搬运距离或次数 ● 可否减少库存
有关搬运方面的改善
● ● ● ● ●
是否可以不必搬运 是否可以减少搬运次数 是否可以缩短搬运距离 可否变更搬运路线 搬运工具是否恰当
●
是否作安全上的防备
四、改善作业现场的方法
工程分析法(四)
有关存储方面的改善
●
是否可消除或减少存储
●
● ●
呆滞品或废品是否定期清理
存储场所及规划是否合理 存储的物品可否简化 http://www.q345jiaogang.co
日期:
Ⅱ 、 不 就 业 时 间 =1+2+3 时 间
迟到早退 借出时间 计 Ⅳ、异常时间 时 间
计划异常 材料异常 设备异常 制程异常 机种异常 水电异常 计 稼动率 作业能率 备 注
填表:
审核:
二、生产效率实战案例分析演练
案例:
某生产单位有员工21人,正常上班时间每天8小时,某日有 一员工因事请假,另一员工因病请假,为此主管向另一生产单 位借用一名员工。当日生产A产品,标准工时为1分/件,生产到 10:00,因断料停线30分钟,下午14:00,生管又临时要求生产B 产品,并立即停止A产品生产,备料至15:00开始生产B产品,为 了赶货,当晚有15人继续加班,加班两个小时后下班,不过 18:20出现品质异常,为此,停工处理至18:52恢复生产,已知 B产品标准工时为1.5分/件,下班时统计当日生产状况,A产品 生产量为4500件,其中不良品有57件,B产品生产2300件,其中 不良品94件。/
●
分割作业,分配到其他耗时也较短的
工程,而省略原工程
●
从耗时长的工程,接过一部分作业
●
●
把耗时较短的工程结合起来
把需要两个人的工程,改成一个人就
能应付的工程
五、提升效率的管理技巧
思考题:
如何激励员工工作热情,提升生
产效率?对计件工资制与计时工资制
的企业分别有哪些有效的方法。
六、生产进度的有效控制手段
动作经济原则(一)
1、 2、 3、
四、改善作业现场的方法
动作经济原则(二)
1、
●
脚或左手能操作的事,不使 用右手 尽量使双手同时作业,也同 时结束 不要使双手同时静止,手空 闲时,须动脑想另一工作
●
●
四、改善作业现场的方法
动作经济原则(三)
2、
● ●
尽量使用小运动来操作工作 材料及器具应放置于伸手能及的范围 内,并尽量放在靠手处 小单元的动作次数应尽量减少 工具应予简化、易用 材料及零件应使用易拿取之容器 工作物较长或较重、或体积较大时, 应利用保持器具
效率的定义
●
生产力(效率)=
产出量 投入量
● 综合生产效率 = 作业能率 * 稼动率 ● 作业能率=
实际生产量
标准生产量
=
标准时间
实用时间
● 标准生产量 = 实用时间 / 标准工时
● 稼动率=
实勤时间 – 损失时间
实勤时间 ● 实勤时间 = 投入时间
● 投入时间=(出勤人数*出勤时间)+加班+借入-借出时间 ● 损失时间 = 无作业时间 = 非生产时间之和
● ● ● ●
四、改善作业现场的方法
动作经济原则(四)
3、
●
●
●
●
动作能予规律化 双手可反向运动,而不可同向运动 利用惯性、重力、自然力等,尤其 尽量利用动力装置 为了减少疲劳,作业椅及作业台的 高度应适合
四、改善作业现场的方法
工作简化法(一)
1
2
3 4
四、改善作业现场的方法
工作简化法(二)
1、
4 5
841 50
四、改善作业现场的方法
IE手法
●工程分析法
●现场布置法 ●搬运布置法
●动作分析法
●动作经济原则 ●稼动分析法
●工作简化法
●生产平衡法 ●时间研究 ●标准时间
四、改善作业现场的方法
工程分析法(一)
有关作业方面的改善 ● 此项作业经努力可否消除掉 ● 工程分割是否恰当 ● 可否减少工程数或时间 ● 工程之间负荷平衡度如何 ● 可否重排工序 ● 工具可否改善 ● 可否机械化、自动化
四、改善作业现场的方法
生产线平衡法(一)
1、使耗时比较长的工程,能够 ● 分割作业,把部分作业分配到耗时较短 的工程; ● 改善作业,缩短作业时间; ● 使作业机械化; ● 提高机械效能; ● 增加作业人员 ● 更换技术水准更高的作业人员
四、改善作业现场的方法
生产线平衡法(二)
2、改善耗时较短的工程
试求该生产单位之作业能率,稼动率及综合效率。
三、综合效率损失分析
1.方法损失
● ● ● ●
作业者不熟练 作业者不积极 作业者未按照标准作业 无效作业、不合理浪费的作业 生产线设计不平衡 不平衡未加调整
2.平衡损失
● ●
3.稼动损失
● 无作业时间多
例:换线、换模、换料、机器故障、 模具故障、停工待料、品质异常、 开 会 、 教 育 、 停 电……/
13、思考(PN) 14、放在前面(PP)
四、改善作业现场的方法
动作分析法(三) 15、保持(H)∩
16、不可避免的延迟(UD)
17、可避免的延迟(AD) 18、休息(R)
四、改善作业现场的方法
动作分析法(四)
1、 第三类动素 着眼点: 2、 第二类动素 着眼点: 3、 第三类动素 着眼点:
四、改善作业现场的方法
四、改善作业现场的方法
动作分析法(一)
⌒
⌒
⌒
1、空手移动(TE) 2、抓起(G)∩ 3、载重移动(TL) 4、决定位置(P) 5、组合(A) 6、分解(DA) 7、使用(U)∪ 8、放下(RL) ⌒ 9、调查(IS)
四、改善作业现场的方法
动作分析法(二) 10、寻找(SH) 11、发现(E)
12、选择(ST)→
标准工时的运用
标准工时:在标准作业条件下,中等熟练作业人员 以正常之努力完成一件工作的时间。
标准工时=实测工时×评核系数×(1+宽放率)
实测工时=实测时间/测试周期 宽放率=管理宽放率+疲劳宽放率+生理宽放率 管理宽放率:3% - 10% 生理宽放率:2% - 5% 疲劳宽放率:5% - 20%
工种 疲劳宽放率 特轻作业 0.5 轻作业 5~10 中作业 10~20 重作业 20~30 特重作业 30~60