福特_8D工作法
8D基础知识

8D基础知识8D是起源于福特公司处理质量问题的一种方法。
凡是福特公司的供应商遇到问题必须强制用这种方法。
后来这方法好,其他的非福特公司的供应商也引进这方法处理问题。
就这样家喻户晓,各行业通吃。
而且不仅仅解决工作问题,解决家庭生活问题也很有效。
一、8D报告八步骤D1-第一步骤: 建立解决问题小组----由品质部召集相关人员若问题无法独立解决,通知你认为有关的人员组成团队。
团队的成员必须有能力执行,例如调整机器或懂得改变制程条件,或能指挥作筛选等。
备注:执行者不列入。
D2-第二步骤: 描述问题----由品质部收集,并向小组人员传达向团队说明何时、何地、发生了什么事、严重程度、目前状态、如何紧急处理、以及展示照片和收集到的证物。
想象你是FBI的办案人员,将证物、细节描述越清楚,团队解决问题将越快。
D3-第三步骤: 执行暂时对策---由小组人员负责执行若真正原因还未找到,暂时用什么方法可以最快地防止问题?如全检、筛选、将自动改为手动、库存清查等。
暂时对策决定后,即立刻交由团队成员带回执行。
备注:为了防止遗漏,纠正措施五要→客户仓库、在途、客户生产线、工厂生产线 & 工厂仓库D4-第四步骤: 找出问题真正原因----由小组人员讨论后确定找问题真正原因时,最好不要盲目地动手改变目前的生产状态,先动动脑。
第一件事是要先观察、分析、比较。
列出所知道的所有生产条件(即鱼骨图),逐一观察,看看是否有些条件走样,还是最近有些什么异动?换了夹具吗?换了作业员?换了供应商?换了运输商?修过电源供应器?流程改过?或比较良品与不良品的检查结果,看看哪个数据有很大的差异?尺寸?重量?电压值?CPK?耐电压?等等不良的发生,总是有原因,资料分析常常可以看出蛛丝马迹。
这样的分析,可以帮助您缩小范围,越来越接近问题核心。
当分析完成,列出您认为最有可能的几项,再逐一动手作些调整改变,并且观察哪些改变可使品质回复正常及影响变异的程度,进而找到问题真正的原因。
2020年整理福特-8D工作法.pdf

8D报告百科名片8D又称团队导向问题解决方法、8D问题求解法(8D Problem Solving)是福特公司处理问题的一种方法,亦适用于制程能力指数低於其应有值时有关问题的解决,它提供了一套符合逻辑的解决问题的方法,同时对於统计制程管制与实际的品质提升架起了一座桥梁。
简介8D最早是美国福特公司使用的经典质量问题分析手法。
二战期间,美国政府率先采用一种类似8D的流程——“军事标准1520”,又称之为“不合格品的修正行动及部署系统”。
1987年,福特汽车公司首次用书面记录下8D法,在其一份课程手册中这一方法被命名为“团队导向的问题解决法”(Team Oriented Problem Solving)。
当时,福特的动力系统部门正被一些经年累月、反复出现的生产问题搞得焦头烂额,因此其管理层提请福特集团提供指导课程,帮助解决难题。
问题解决8步法8D(8 Disciplines)问题解决8步法8D的原名叫做8 Disciplines,意思是8个人人皆知解决问题的固定步骤。
原始是由Ford公司,全球化品质管制及改善的特殊必备方法,之后已成为QS9000/ISO TS16949、福特公司的特殊要求。
凡是做FORD 的零件,必须采用8D 作为品质改善的工具,目前有些企业并非 FORD 的供应商或汽车业的合作伙伴,也很喜欢用这个方便而有效的方法解决品质问题,成为一个固定而有共识的标准化问题解决步骤。
Discipline 1. 成立改善小组(Form the Team):由议题之相关人员组成,通常是跨功能性的,说明团队成员间的彼此分工方式或担任的责任与角色。
Discipline 2. 描述问题(Describe the Problem):将问题尽可能量化而清楚地表达,并能解决中长期的问题而不是只有眼前的问题。
Discipline 3. 实施及确认暂时性的对策(Contain the Problem):对于解决 D2 之立即而短期行动,避免问题扩大或持续恶化,包含清库存、缩短PM时间、加派人力等。
福特-8D工作法

8D报告百科名片8D又称团队导向问题解决方法、8D问题求解法(8D Problem Solving)是福特公司处理问题的一种方法,亦适用于制程能力指数低於其应有值时有关问题的解决,它提供了一套符合逻辑的解决问题的方法,同时对於统计制程管制与实际的品质提升架起了一座桥梁。
简介8D最早是美国福特公司使用的经典质量问题分析手法。
二战期间,美国政府率先采用一种类似8D的流程——“军事标准1520”,又称之为“不合格品的修正行动及部署系统”。
1987年,福特汽车公司首次用书面记录下8D法,在其一份课程手册中这一方法被命名为“团队导向的问题解决法”(Team Oriented Problem Solving)。
当时,福特的动力系统部门正被一些经年累月、反复出现的生产问题搞得焦头烂额,因此其管理层提请福特集团提供指导课程,帮助解决难题。
问题解决8步法8D(8 Disciplines)问题解决8步法8D的原名叫做8 Disciplines,意思是8个人人皆知解决问题的固定步骤。
原始是由Ford公司,全球化品质管制及改善的特殊必备方法,之后已成为QS9000/ISO TS16949、福特公司的特殊要求。
凡是做FORD 的零件,必须采用8D 作为品质改善的工具,目前有些企业并非FORD的供应商或汽车业的合作伙伴,也很喜欢用这个方便而有效的方法解决品质问题,成为一个固定而有共识的标准化问题解决步骤。
Discipline 1. 成立改善小组(Form the Team):由议题之相关人员组成,通常是跨功能性的,说明团队成员间的彼此分工方式或担任的责任与角色。
Discipline 2. 描述问题(Describe the Problem):将问题尽可能量化而清楚地表达,并能解决中长期的问题而不是只有眼前的问题。
Discipline 3. 实施及确认暂时性的对策(Contain the Problem):对于解决D2 之立即而短期行动,避免问题扩大或持续恶化,包含清库存、缩短PM时间、加派人力等。
福特问题解决之8D报告

福特问题解决之8D流程8D又称团队导向问题解决方法,8D问题求解法(Eight Disciplines Problem Solving)是福特公司处理问题的一种方法,亦适用于制程能力指数低於其应有值时有关问题的解决。
它提供了一套符合逻辑的解决问题的方法,同时对於统计制程管制与实际的品质提升架起了一座桥梁。
二战期间,美国政府率先采用一种类似8D的流程——“军事标准1520”,又称之为“不合格品的修正行动及部署系统”。
1987年,福特汽车公司首次用书面记录下8D法,在其一份课程手册中这一方法被命名为“团队导向的问题解决法”(Team Oriented Problem Solving)。
当时,福特的动力系统部门正被一些经年累月、反复出现的生产问题搞得焦头烂额,因此其管理层提请福特集团提供指导课程,帮助解决难题。
8D主要用于汽车及类似加工行业的问题解决方法。
原始是由Ford公司,全球化品质管制及改善的特殊必备方法,之后已成为QS9000/ TS16949、福特公司的特殊要求。
该方法适用于解决各类可能遇到的简单或复杂的问题;8D方法就是要建立一个体系,让整个团队共享信息,努力达成目标。
8D本身不提供成功解决问题的方法或途径,但它是解决问题的一个很有用的工具;亦适用于过程能力指数低于其应有值时有关问题的解决;面对顾客投诉及重大不良时,提供解决问题的方法。
8D法是美国福特公司解决产品质量问题的一种方法,曾在供应商中广泛推行,现已成为国际汽车行业(特别是汽车零部件产家)广泛采用来解决产品质量问题最好的、有效的方法。
D0:征兆紧急反应措施目的:主要是为了看此类问题是否需要用8D来解决,如果问题太小,或是不适合用8D来解决的问题,例如价格,经费等等,这一步是针对问题发生时候的紧急反应。
关键要点:判断问题的类型、大小、范畴等等。
与D3不同,D0是针对问题发生的反应,而D3是针对产品或服务问题本身的暂时应对措施。
D1:小组成立目的:成立一个小组,小组成员具备工艺/产品的知识,有配给的时间并授予了权限,同时应具有所要求的能解决问题和实施纠正措施的技术素质。
质量管理之8D改善

质量管理之8D改善在进行企业质量改善辅导过程中,针对一般性的质量问题,我们会推荐8D改善方法。
8D 问题解决法的处理方式是先找到根本原因、采取行动消除根本原因,并实施永久对策,此作法是有效的,而且也可以找出系统会允许此错误出现的原因。
漏失点(escapepoints)的研究就是为了提升系统侦测错误的能力,即使错误再度发生,也有能力可以检测出来。
一、什么是8D8D是福特公司以及福特供应商必须要用的解决质量问题的工具,现已成为全球化品质管理及其它领域改善的必备方法。
8D(Eight-Disciplines),意思是8个解决问题的固定步骤;也可以称为TOPS (TeamOrientedproblemsolving)即团队导向问题解决方法。
由一个准备过程和8个标准步骤组成,这些步骤用来客观地确定、定义和解决问题并防止相似问题的再次发生。
8个步骤分别为:D1:成立小组D2:问题的描述D3:实施并验证临时措施D4:确定和验证根本原因D5:选择并验证永久纠正措施D6:实施永久纠正措施D7:防止再发生D8:承认小组及个人的贡献二、为何需要8D①对于企业:当标准与实际产生差距时,由以前的责备转化成由8D的方法来解决问题通过建立小组,采用团队合作的模式进行解决问题,以助于消除部门间壁垒,提高团队合作精神小组成员来源于不同的部门,有助于提供问题有效的解决方法。
通过8D的标准步骤,可以防止相同或类似的问题重复发生。
通过建立小组训练内部合作的技巧推进有效的问题解决和预防技术改进供方整体质量、生产率、成本等防止相同或类似问题的再发生,提高顾客满意度③对于顾客增强对供方的产品和过程的信心促进供应链能力的提升使过程运营更加稳定与供方互利的关系④对于个人形成逻辑的思维能力:问题发现—问题分析—问题解决—预防再发生熟知8D的相关工具(5WHY、FMEA、控制计划、七大质量工具、SPC等)学习其他部门的相关知识培养团队意识。
三、何时使用8D针对过程中偶然发生的问题重复发生,一直没有解决的问题问题出现后,异常原因未知比较重大的问题,个人无法解决客户要求回复的质量投诉问题存在一定的改进空间四、8D的实施步骤如何制作?以一个生活中的案例来进行解答,将一步步带你进入8D改善的殿堂。
福特-8D工作法PDF.pdf

8D报告百科名片8D又称团队导向问题解决方法、8D问题求解法(8D Problem Solving)是福特公司处理问题的一种方法,亦适用于制程能力指数低於其应有值时有关问题的解决,它提供了一套符合逻辑的解决问题的方法,同时对於统计制程管制与实际的品质提升架起了一座桥梁。
简介8D最早是美国福特公司使用的经典质量问题分析手法。
二战期间,美国政府率先采用一种类似8D的流程——“军事标准1520”,又称之为“不合格品的修正行动及部署系统”。
1987年,福特汽车公司首次用书面记录下8D法,在其一份课程手册中这一方法被命名为“团队导向的问题解决法”(Team Oriented Problem Solving)。
当时,福特的动力系统部门正被一些经年累月、反复出现的生产问题搞得焦头烂额,因此其管理层提请福特集团提供指导课程,帮助解决难题。
问题解决8步法8D(8 Disciplines)问题解决8步法8D的原名叫做8 Disciplines,意思是8个人人皆知解决问题的固定步骤。
原始是由Ford公司,全球化品质管制及改善的特殊必备方法,之后已成为QS9000/ISO TS16949、福特公司的特殊要求。
凡是做FORD 的零件,必须采用8D 作为品质改善的工具,目前有些企业并非 FORD 的供应商或汽车业的合作伙伴,也很喜欢用这个方便而有效的方法解决品质问题,成为一个固定而有共识的标准化问题解决步骤。
Discipline 1. 成立改善小组(Form the Team):由议题之相关人员组成,通常是跨功能性的,说明团队成员间的彼此分工方式或担任的责任与角色。
Discipline 2. 描述问题(Describe the Problem):将问题尽可能量化而清楚地表达,并能解决中长期的问题而不是只有眼前的问题。
Discipline 3. 实施及确认暂时性的对策(Contain the Problem):对于解决 D2 之立即而短期行动,避免问题扩大或持续恶化,包含清库存、缩短PM时间、加派人力等。
1_福特8D简介(教材)

FOURACE INDUSTRIES LTD 科利实业有限公司原因分析问题解决( 8D法)培训教材编制: ISO办公室日期: 2003年12月25日福特8D简介8D就是英文(8 Disciplines) 的缩写,在生产的过程中,面对异常问题发生时,按照8个标题指示的步骤,提出治标及治本的改善方法,8D方法,又称团队导向问题解决方法,是福特公司处理问题的一种方法,亦适用于制程能力指数低于其应有值时有关问题的解决,它提供了一套符合逻辑的解决问题的方法,同时对于统计制程管制与问题的把握与改善1.问题只有已经倒闭的企业才没有问题,一个班组也是一样。
身为管理人员,其实最大的任务,就是解决问题。
管理的技巧也可以说是解决问题的技巧。
所谓问题,是指“应有状态”与“实际状态”的差异。
其中“应有状态”幷非理想状态,而是“应该如此”,是作为某种工作的结果所能预测的状态,与此相比较的实际状态出现差异时,就认为有问题。
包括:(1)本来应该的状态与实际的差距;(2)不能放任需要马上解决的事情;(3)给其它的人员或下一工序添加异常,留下不良影响;(4)必须致力解决的部分;(5)想使之实现,使之成功的事情。
下图为问题的形成示意图(详见附图1)。
附图1 问题的形成示意图2.问题意识2.1 问题意识的定义把现在开始可能会发生的或已经成为问题的作为问题来认识;这种对待问题的心理活动就是问题意识。
2.2 问题意识产生的因素问题意识一般从以下几个因素中产生:(1)否定现状的精神(意识到不能维持现状)使自己陷入困境,为之烦恼的,觉得有疑问的事情有浪费、勉强和不合理故障、投诉、索赔事件(2)更高的追求(想做得更好)理想、展望、憧憬使命感、责任感成就感、正义感3.问题的种类3.1 人员的问题/ 工作的问题如果是人员的意识不到位,就要进行思想意识教育;如果是技能不足,则要强化某方面的技能;如果是工作方法不合适,我们就要调整相应的工作方法。
3.2 组织的问题/ 目标的问题如果我们的组织团队战斗力不够,那幺团队的重塑过程是必要的;如果因为目标不切合实际造成业绩偏离,我们就应该进行目标的调整。
福特-8D工作法
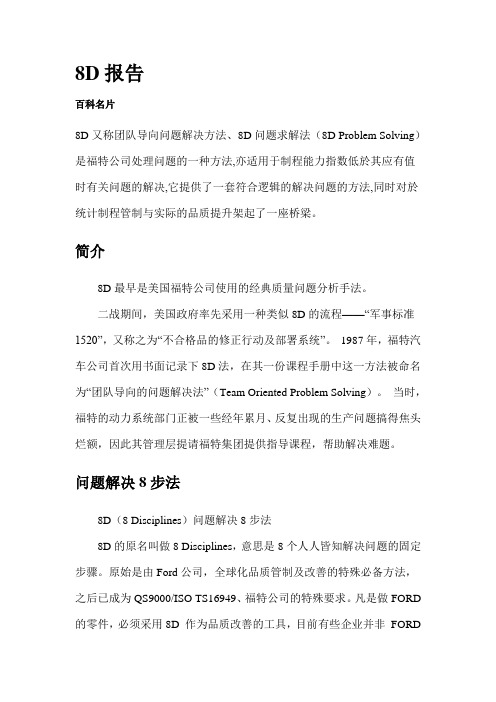
8D报告百科名片8D又称团队导向问题解决方法、8D问题求解法(8D Problem Solving)是福特公司处理问题的一种方法,亦适用于制程能力指数低於其应有值时有关问题的解决,它提供了一套符合逻辑的解决问题的方法,同时对於统计制程管制与实际的品质提升架起了一座桥梁。
简介8D最早是美国福特公司使用的经典质量问题分析手法。
二战期间,美国政府率先采用一种类似8D的流程——“军事标准1520”,又称之为“不合格品的修正行动及部署系统”。
1987年,福特汽车公司首次用书面记录下8D法,在其一份课程手册中这一方法被命名为“团队导向的问题解决法”(Team Oriented Problem Solving)。
当时,福特的动力系统部门正被一些经年累月、反复出现的生产问题搞得焦头烂额,因此其管理层提请福特集团提供指导课程,帮助解决难题。
问题解决8步法8D(8 Disciplines)问题解决8步法8D的原名叫做8 Disciplines,意思是8个人人皆知解决问题的固定步骤。
原始是由Ford公司,全球化品质管制及改善的特殊必备方法,之后已成为QS9000/ISO TS16949、福特公司的特殊要求。
凡是做FORD 的零件,必须采用8D 作为品质改善的工具,目前有些企业并非FORD的供应商或汽车业的合作伙伴,也很喜欢用这个方便而有效的方法解决品质问题,成为一个固定而有共识的标准化问题解决步骤。
Discipline 1. 成立改善小组(Form the Team):由议题之相关人员组成,通常是跨功能性的,说明团队成员间的彼此分工方式或担任的责任与角色。
Discipline 2. 描述问题(Describe the Problem):将问题尽可能量化而清楚地表达,并能解决中长期的问题而不是只有眼前的问题。
Discipline 3. 实施及确认暂时性的对策(Contain the Problem):对于解决D2 之立即而短期行动,避免问题扩大或持续恶化,包含清库存、缩短PM时间、加派人力等。
福特(Ford)8D培训教材

也不要写工作报告
Page 10 of 47
成员包括:
❖ 指导员(CHAMPION) 一般为主管阶层,对小组的进度有 监督, 支持及决策决定 权力.
❖ 组长(LEADER)-负责协调,活动进行的引导,汇总小组的意 见及决策并呈报,尽量不要深入某部份细节,以免迷失方向.
❖ 问5次为什么的做法:
➢对于某个问题,为何会引起?其原因①先搞明白。 ➢为何会引起原因①的发生?将原因②也搞清楚。 ➢为何会引起原因②的发生?将原因③弄明白。 ➢为何会引起原因③的发生?将原因④弄明白。 ➢为何会引起原因④的发生?将原因⑤弄明白。
Page 20 of 47
❖ 用这种方式持续地去做,根本的原因就能显現出来。 ❖ 分析出来的根本的原因必须是能导出具有効果、
且有効率的再发防止对策才行。 ❖ 要注意的是问题发生的原因不一定只有一个。
❖ 通常第一个答案不会是真正的答案 ❖ 5 Why 可以找出真正的原因 ❖ 简单的案子可能4Why,3Why或2Why即找出根本原
因,但复杂的或许要5 Why, 6 Why, 7 Why…
Page 21 of 47
做5 Why 分析时应注意事项
因会影响结果时,不能说有因果关系)。
Page 23 of 47
5 Why 范例: 为何停机
❖ 问1:为什么机器停了? 答1:因为机器超载, 保险丝烧断了
❖ 问2:为什么机器会超载? 答2: 因为轴承的润滑不足
❖ 问3:为什么轴承会润滑不足? 答3: 因为润滑系统失灵了
❖ 问4: 为什么润滑系统会失灵? 答4: 因为润滑系统的轮轴耗损了
福特8D

福特8D﹝Disciplines﹞─2001.038 - Ds就是8个DISCIPLINES。
最早系由美国福特汽车公司遇到不知道『真正肇因﹝ROOT CAUSE﹞』的问题时,用来解决问题的方法。
因为功效卓著,广为美国企业接受,随着美国COMPAQ计算机公司对外采购的增加,COMPAQ公司会要求其协力厂商运用此一方法来解决所遭遇到的各种问题,而快速地在计算机业界被广泛应用。
在台湾的IC制造龙头台积电也广泛地应用此一方法解决甚多的问题。
8 - Ds通常比较适合用在团队以事实为导向来解决问题。
原文是TEAM ORIENTED PROBLEM SOLVING,简称为TOPS。
其概略架构如下:注意到问题1.采取团队处理模式→将具专业知识的人员编组成小组,按其分派的时间、权限,运用技术性方法来解决问题,及进行矫正措施。
需有指挥官。
2.叙述问题→藉由可量化的术语,运用5W1H,详细叙述内部/外部顾客的问题并记录之。
3.实施及确认暂时﹝围堵﹞行动→在尚未确定永久对策之前,先界定并实施围堵行动,使内部/外部顾客不再受到该问题的困扰。
并确认围堵行动的有效性。
4.界定及确认真正肇因→指出所有可解释会造成该问题的『可能原因』,然后与D2的问题叙述及试验数据比对测试,找出原因。
提出能消除真正肇因的方案。
5.确认矫正行动→透过暂时性的预先生产方式的测试计划,确定所选定的矫正措施确实能为顾客解决问题,同时不会演伸不良影响。
6.实施永久性矫正计划→界定并执行最好的永久性矫正措施,确定该真正肇因已被消除。
一旦正式生产后,监视长期的影响。
若有必要,实施紧急处理措施。
7.防止再发→修订管理系统,操作程序的常规、惯例及程序,防止该问题或类似问题再发。
8.恭喜你的团队→肯定团队的集体努力。
8 - Ds通常只用掉一张A4的纸浆这8项纪律置于其上,它不但是解决问题的方法,亦是解决问题的程序,同时又是一个标准,更是一种进度及结果的报告表。
虽然8 - Ds是TOPS解决问题时的一种程序、步骤,一种结论的报告。
8D报告方法
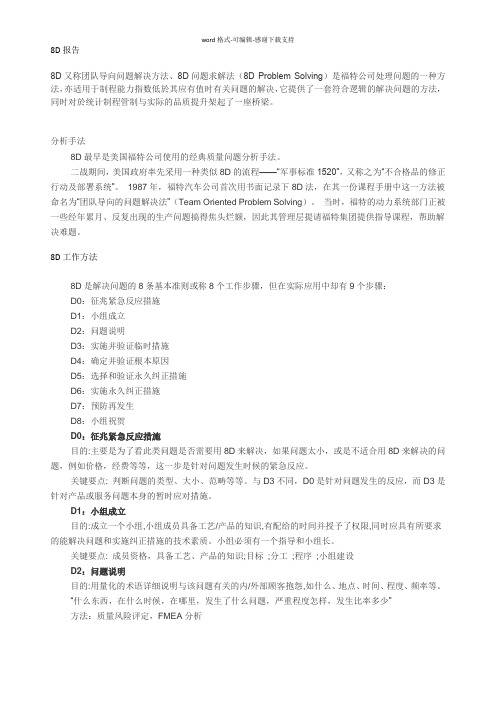
8D报告8D又称团队导向问题解决方法、8D问题求解法(8D Problem Solving)是福特公司处理问题的一种方法,亦适用于制程能力指数低於其应有值时有关问题的解决,它提供了一套符合逻辑的解决问题的方法,同时对於统计制程管制与实际的品质提升架起了一座桥梁。
分析手法8D最早是美国福特公司使用的经典质量问题分析手法。
二战期间,美国政府率先采用一种类似8D的流程——“军事标准1520”,又称之为“不合格品的修正行动及部署系统”。
1987年,福特汽车公司首次用书面记录下8D法,在其一份课程手册中这一方法被命名为“团队导向的问题解决法”(Team Oriented Problem Solving)。
当时,福特的动力系统部门正被一些经年累月、反复出现的生产问题搞得焦头烂额,因此其管理层提请福特集团提供指导课程,帮助解决难题。
8D工作方法8D是解决问题的8条基本准则或称8个工作步骤,但在实际应用中却有9个步骤:D0:征兆紧急反应措施D1:小组成立D2:问题说明D3:实施并验证临时措施D4:确定并验证根本原因D5:选择和验证永久纠正措施D6:实施永久纠正措施D7:预防再发生D8:小组祝贺D0:征兆紧急反应措施目的:主要是为了看此类问题是否需要用8D来解决,如果问题太小,或是不适合用8D来解决的问题,例如价格,经费等等,这一步是针对问题发生时候的紧急反应。
关键要点: 判断问题的类型、大小、范畴等等。
与D3不同,D0是针对问题发生的反应,而D3是针对产品或服务问题本身的暂时应对措施。
D1:小组成立目的:成立一个小组,小组成员具备工艺/产品的知识,有配给的时间并授予了权限,同时应具有所要求的能解决问题和实施纠正措施的技术素质。
小组必须有一个指导和小组长。
关键要点: 成员资格,具备工艺、产品的知识;目标;分工;程序;小组建设D2:问题说明目的:用量化的术语详细说明与该问题有关的内/外部顾客抱怨,如什么、地点、时间、程度、频率等。
8D的工作方法及运用
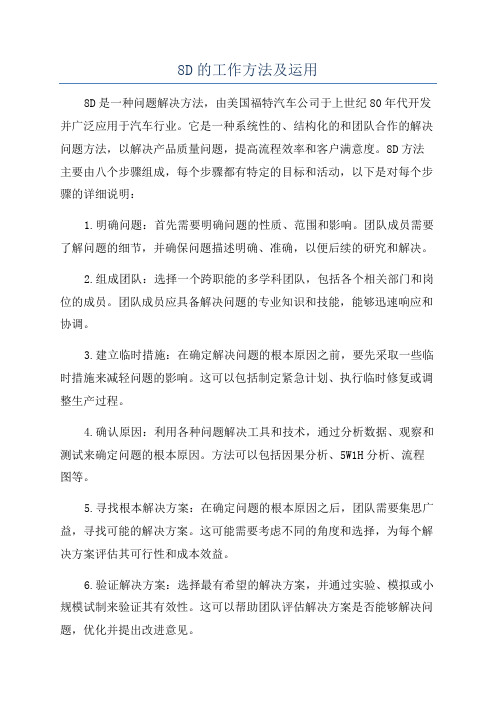
8D的工作方法及运用8D是一种问题解决方法,由美国福特汽车公司于上世纪80年代开发并广泛应用于汽车行业。
它是一种系统性的、结构化的和团队合作的解决问题方法,以解决产品质量问题,提高流程效率和客户满意度。
8D方法主要由八个步骤组成,每个步骤都有特定的目标和活动,以下是对每个步骤的详细说明:1.明确问题:首先需要明确问题的性质、范围和影响。
团队成员需要了解问题的细节,并确保问题描述明确、准确,以便后续的研究和解决。
2.组成团队:选择一个跨职能的多学科团队,包括各个相关部门和岗位的成员。
团队成员应具备解决问题的专业知识和技能,能够迅速响应和协调。
3.建立临时措施:在确定解决问题的根本原因之前,要先采取一些临时措施来减轻问题的影响。
这可以包括制定紧急计划、执行临时修复或调整生产过程。
4.确认原因:利用各种问题解决工具和技术,通过分析数据、观察和测试来确定问题的根本原因。
方法可以包括因果分析、5W1H分析、流程图等。
5.寻找根本解决方案:在确定问题的根本原因之后,团队需要集思广益,寻找可能的解决方案。
这可能需要考虑不同的角度和选择,为每个解决方案评估其可行性和成本效益。
6.验证解决方案:选择最有希望的解决方案,并通过实验、模拟或小规模试制来验证其有效性。
这可以帮助团队评估解决方案是否能够解决问题,优化并提出改进意见。
7.预防再次发生:一旦解决方案被证实有效,团队需要开发和实施预防措施,以防止类似问题再次发生。
这可以包括更新和修改流程、改善工艺和培训工作人员。
8.确认效果并提出奖励:在解决方案实施一段时间后,团队应评估解决效果,并将结果与原始问题相比较。
如果解决方案能够实现预期的效果,可以对团队成员进行表彰和奖励。
8D方法强调团队协作和持续改进,能够帮助组织有效地解决各种问题。
它具有结构化的步骤和工具,使团队能够系统地分析问题、找到根本原因并提出解决方案。
此外,8D还强调持续的改进和预防,为组织提供了一种改善流程和产品质量的方法。
图解8D分析法
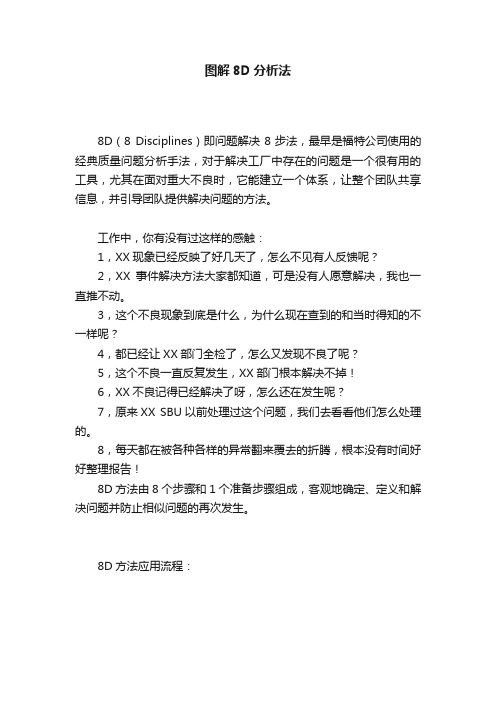
图解8D分析法8D(8 Disciplines)即问题解决8步法,最早是福特公司使用的经典质量问题分析手法,对于解决工厂中存在的问题是一个很有用的工具,尤其在面对重大不良时,它能建立一个体系,让整个团队共享信息,并引导团队提供解决问题的方法。
工作中,你有没有过这样的感触:1,XX现象已经反映了好几天了,怎么不见有人反馈呢?2,XX事件解决方法大家都知道,可是没有人愿意解决,我也一直推不动。
3,这个不良现象到底是什么,为什么现在查到的和当时得知的不一样呢?4,都已经让XX部门全检了,怎么又发现不良了呢?5,这个不良一直反复发生,XX部门根本解决不掉!6,XX不良记得已经解决了呀,怎么还在发生呢?7,原来XX SBU以前处理过这个问题,我们去看看他们怎么处理的。
8,每天都在被各种各样的异常翻来覆去的折腾,根本没有时间好好整理报告!8D方法由8个步骤和1个准备步骤组成,客观地确定、定义和解决问题并防止相似问题的再次发生。
8D方法应用流程:01 D1组建问题解决团队8D原名就是叫团队导向问题解决步骤,8D小组需要由具备产品及制程知识,能支配时间且拥有职权及技能的人士组成,必须指定一名8D团队组长。
不具备以上条件的8D是失败的8D,它没法在你需要资源解决问题时提供帮助。
若一个体系出现了质量异常,绝非单一部门职能失效,否则整个体系需要重新进行完善。
8D团队的角色构成:8D负责人:作为8D项目支持者的身份参与8D项目。
没有负责人的签字8D报告不能进行关闭审批。
8D组长:负责8D全过程的进行直至问题解决、8D项目关闭8D 组员:在组长的协调下利用自身知识与技能参与8D问题的解决确定团队成员应注意的问题:团队人数:4~10人组长的选择:部门经理指定本部门人员或亲自担任组员的选择原则:与问题相关且具备相关的资源、能力D1的常见性错误:选择的8D团队成员对涉及问题没有相关知识或认识;只有一两个人实施8D过程。
02D2描述问题以客户的角度和观点详细描述其所感受到的问题现象,将所遭遇的问题,以量化的方式,明确出所涉及的人、事、时、地、为何、如何、多少。
8D工作方法课稿

•D2——小组成员
• D3——临时对策
•D4——确定和验证根本缘由
• H406111由FQC员工XXX进展标识,06/16/2023生 产。
• 产品标识过程是:在FQC检验前手工进展产品标 识,然后进展产品检验,合格后包装入库。由于 是手工标识,作标识员工有可能标识错误。以前 曾在外观检验中觉察标识错误,导致返工重新标 识。另外FQC外观检验时,可能由于检验员专注 于产品缺陷的检验,而无视标识错误。所以标识 错误的缘由应是标识员工人为失误,而FQC检验 中未觉察标识错误。
转换开关。10/18/2023上午9点电工觉察电 源自动转换开关过热发红。
• D2——小组成员
• D3——临时对策
•D4——确定和验证根本缘由
可能缘由:电源自动转换开关触点老化,接触电阻 过大,导致过热发红。
根本缘由的验证:很明显可看到开关触点过热发红 并冒烟。
• D5——订正措施
• D6——执行和验证订正措施
2、包括哪些内容?
• D1——问题描述 • 什么时间、什么地点、发生什么事、用数
据说明问题的严峻程度
• D2——小组成员 • 选择有力量解决该问题的人,团队力气大
于个人
• D3——临时对策 • 实行应急措施,防止问题扩大
• D4——确定和验证根本缘由 • 从人、机、料、法、环五个方面考虑,排
• D7——预防措施
• D8——庆贺
4、小结
8D实际上就是一套分析问题解决问题的程序
共有8个步骤 强调团队的力气 可以说就是PDCA的具体化 与寻常用的CAR、特别单等并无本质区分 8D更程序化、标准化
8D
• D1——问题描述 • D2——小组成员 • D3——临时对策 • D4——确定和验证根本缘由 • D5——订正措施 • D6——执行和验证订正措施 • D7——预防措施 • D8——庆贺
- 1、下载文档前请自行甄别文档内容的完整性,平台不提供额外的编辑、内容补充、找答案等附加服务。
- 2、"仅部分预览"的文档,不可在线预览部分如存在完整性等问题,可反馈申请退款(可完整预览的文档不适用该条件!)。
- 3、如文档侵犯您的权益,请联系客服反馈,我们会尽快为您处理(人工客服工作时间:9:00-18:30)。
8D报告百科名片8D又称团队导向问题解决方法、8D问题求解法(8D Problem Solving)是福特公司处理问题的一种方法,亦适用于制程能力指数低於其应有值时有关问题的解决,它提供了一套符合逻辑的解决问题的方法,同时对於统计制程管制与实际的品质提升架起了一座桥梁。
简介8D最早是美国福特公司使用的经典质量问题分析手法。
二战期间,美国政府率先采用一种类似8D的流程——“军事标准1520”,又称之为“不合格品的修正行动及部署系统”。
1987年,福特汽车公司首次用书面记录下8D法,在其一份课程手册中这一方法被命名为“团队导向的问题解决法”(Team Oriented Problem Solving)。
当时,福特的动力系统部门正被一些经年累月、反复出现的生产问题搞得焦头烂额,因此其管理层提请福特集团提供指导课程,帮助解决难题。
问题解决8步法8D(8 Disciplines)问题解决8步法8D的原名叫做8 Disciplines,意思是8个人人皆知解决问题的固定步骤。
原始是由Ford公司,全球化品质管制及改善的特殊必备方法,之后已成为QS9000/ISO TS16949、福特公司的特殊要求。
凡是做FORD 的零件,必须采用8D 作为品质改善的工具,目前有些企业并非FORD的供应商或汽车业的合作伙伴,也很喜欢用这个方便而有效的方法解决品质问题,成为一个固定而有共识的标准化问题解决步骤。
Discipline 1. 成立改善小组(Form the Team):由议题之相关人员组成,通常是跨功能性的,说明团队成员间的彼此分工方式或担任的责任与角色。
Discipline 2. 描述问题(Describe the Problem):将问题尽可能量化而清楚地表达,并能解决中长期的问题而不是只有眼前的问题。
Discipline 3. 实施及确认暂时性的对策(Contain the Problem):对于解决D2 之立即而短期行动,避免问题扩大或持续恶化,包含清库存、缩短PM时间、加派人力等。
Discipline 4. 原因分析及验证真因(Identify the Root Cause):发生D2 问题的真正原因、说明分析方法、使用工具(品质工具)的应用。
Discipline 5. 选定及确认长期改善行动效果(Formulate and Verify Corrective Actions):拟订改善计划、列出可能解决方案、选定与执行长期对策、验证改善措施,清除D4 发生的真正原因,通常以一个步骤一个步骤的方式说明长期改善对策,可以应用专案计划甘特图(Gantt Chart),并说明品质手法的应用。
Discipline 6. 改善问题并确认最终效果(Correct the Problem and Confirm the Effects):执行D5 后的结果与成效验证。
Discipline 7. 预防再发生及标准化(Prevent the Problem):确保D4 问题不会再次发生的后续行动方案,如人员教育训练、改善案例分享(Fan out) 、作业标准化、产出BKM、执行FCN 、分享知识和经验等。
Discipline 8. 恭喜小组及规划未来方向(Congratulate the Team):若上述步骤完成后问题已改善,肯定改善小组的努力,并规划未来改善方向。
8D适用围该方法适用于解决各类可能遇到的简单或复杂的问题;8D方法就是要建立一个体系,让整个团队共享信息,努力达成目标。
8D本身不提供成功解决问题的方法或途径,但它是解决问题的一个很有用的工具;亦适用于过程能力指数低于其应有值时有关问题的解决;面对顾客投诉及重大不良时,提供解决问题的方法。
8D法是美国福特公司解决产品质量问题的一种方法,曾在供应商中广泛推行,现已成为国际汽车行业(特别是汽车零部件产家)广泛采用来解决产品质量问题最好的、有效的方法。
8D工作方法的8个步骤8D是解决问题的8条基本准则或称8个工作步骤,但在实际应用中却有9个步骤:D0:征兆紧急反应措施D1:小组成立D2:问题说明D3:实施并验证临时措施D4:确定并验证根本原因D5:选择和验证永久纠正措施D6:实施永久纠正措施D7:预防再发生D8:小组祝贺D0:征兆紧急反应措施目的:主要是为了看此类问题是否需要用8D来解决,如果问题太小,或是不适合用8D来解决的问题,例如价格,经费等等,这一步是针对问题发生时候的紧急反应。
关键要点: 判断问题的类型、大小、畴等等。
与D3不同,D0是针对问题发生的反应,而D3是针对产品或服务问题本身的暂时应对措施。
D1:小组成立目的:成立一个小组,小组成员具备工艺/产品的知识,有配给的时间并授予了权限,同时应具有所要求的能解决问题和实施纠正措施的技术素质。
小组必须有一个指导和小组长。
关键要点: 成员资格,具备工艺、产品的知识;目标;分工;程序;小组建设D2:问题说明目的:用量化的术语详细说明与该问题有关的/外部顾客抱怨,如什么、地点、时间、程度、频率等。
“什么东西出了什么问题”方法:质量风险评定,FMEA分析关键要点:收集和组织所有有关数据以说明问题;问题说明是所描述问题的特别有用的数据的总结;审核现有数据,识别问题、确定围;细分问题,将复杂问题细分为单个问题;问题定义,找到和顾客所确认问题一致的说明,“什么东西出了什么问题”,而原因又未知风险等级。
D3:实施并验证临时措施目的:保证在永久纠正措施实施前,将问题与外部顾客隔离。
(原为唯一可选步骤,但发展至今都需采用)方法:FMEA、DOE、PPM关键要点: 评价紧急响应措施;找出和选择最佳“临时抑制措施”;决策;实施,并作好记录;验证(DOE、PPM分析、控制图等)D4:确定并验证根本原因目的:用统计工具列出可以用来解释问题起因的所有潜在原因,将问题说明中提到的造成偏差的一系列事件或环境或原因相互隔离测试并确定产生问题的根本原因。
方法:FMEA、PPM、DOE、控制图、5why法关键要点: 评估可能原因列表中的每一个原因;原因可否使问题排除;验证;控制计划D5:选择并验证永久纠正措施目的:在生产前测试方案,并对方案进行评审以确定所选的校正措施能够解决客户问题,同时对其它过程不会有不良影响。
方法:FMEA关键要点: 重新审视小组成员资格;决策,选择最佳措施;重新评估临时措施,如必要重新选择;验证;管理层承诺执行永久纠正措施;控制计划D6:实施永久纠正措施目的:制定一个实施永久措施的计划,确定过程控制方法并纳入文件,以确保根本原因的消除。
在生产中应用该措施时应监督其长期效果。
方法:防错、统计控制关键要点: 重新审视小组成员;执行永久纠正措施,废除临时措施;利用故障的可测量性确认故障已经排除;控制计划、工艺文件修改D7:预防再发生目的:修改现有的管理系统、操作系统、工作惯例、设计与规程以防止这一问题与所有类似问题重复发生。
关键要点:选择预防措施;验证有效性;决策;组织、人员、设备、环境、材料、文件重新确定D8:小组祝贺目的:承认小组的集体努力,对小组工作进行总结并祝贺。
关键要点: 有选择的保留重要文档;流览小组工作,将心得形成文件;了解小组对解决问题的集体力量,及对解决问题作出的贡献;必要的物质、精神奖励。
对8D工作方法的评价1.优点发现真正肇因的有效方法,并能够采取针对性措施消除真正肇因,执行永久性矫正措施。
能够帮助探索允许问题逃逸的控制系统。
逃逸点的研究有助于提高控制系统在问题再次出现时的监测能力。
预防机制的研究有助于帮助系统将问题控制在初级阶段。
2.缺点8D培训费时,且本身具有难度。
除了对8D问题解决流程进行培训外,还需要数据挖掘的培训,以及对所需用到的分析工具(如帕累托图、鱼骨图和流程图,等等)进行培训。
[1]参考资料8D报告百科名片8D又称团队导向问题解决方法、8D问题求解法(8D Problem Solving)是福特公司处理问题的一种方法,亦适用于制程能力指数低於其应有值时有关问题的解决,它提供了一套符合逻辑的解决问题的方法,同时对於统计制程管制与实际的品质提升架起了一座桥梁。
目录简介问题解决8步法8D适用围8D工作方法的8个步骤1.对8D工作方法的评价简介8D最早是美国福特公司使用的经典质量问题分析手法。
二战期间,美国政府率先采用一种类似8D的流程——“军事标准1520”,又称之为“不合格品的修正行动及部署系统”。
1987年,福特汽车公司首次用书面记录下8D法,在其一份课程手册中这一方法被命名为“团队导向的问题解决法”(Team Oriented Problem Solving)。
当时,福特的动力系统部门正被一些经年累月、反复出现的生产问题搞得焦头烂额,因此其管理层提请福特集团提供指导课程,帮助解决难题。
问题解决8步法8D(8 Disciplines)问题解决8步法8D的原名叫做8 Disciplines,意思是8个人人皆知解决问题的固定步骤。
原始是由Ford公司,全球化品质管制及改善的特殊必备方法,之后已成为QS9000/ISO TS16949、福特公司的特殊要求。
凡是做FORD 的零件,必须采用8D 作为品质改善的工具,目前有些企业并非FORD 的供应商或汽车业的合作伙伴,也很喜欢用这个方便而有效的方法解决品质问题,成为一个固定而有共识的标准化问题解决步骤。
Discipline 1. 成立改善小组(Form the Team):由议题之相关人员组成,通常是跨功能性的,说明团队成员间的彼此分工方式或担任的责任与角色。
Discipline 2. 描述问题(Describe the Problem):将问题尽可能量化而清楚地表达,并能解决中长期的问题而不是只有眼前的问题。
Discipline 3. 实施及确认暂时性的对策(Contain the Problem):对于解决D2 之立即而短期行动,避免问题扩大或持续恶化,包含清库存、缩短PM时间、加派人力等。
Discipline 4. 原因分析及验证真因(Identify the Root Cause):发生D2 问题的真正原因、说明分析方法、使用工具(品质工具)的应用。
Discipline 5. 选定及确认长期改善行动效果(Formulate and Verify Corrective Actions):拟订改善计划、列出可能解决方案、选定与执行长期对策、验证改善措施,清除D4 发生的真正原因,通常以一个步骤一个步骤的方式说明长期改善对策,可以应用专案计划甘特图(Gantt Chart),并说明品质手法的应用。
Discipline 6. 改善问题并确认最终效果(Correct the Problem and Confirm the Effects):执行D5 后的结果与成效验证。