锻造热处理
锻件热处理

锻件热处理锻件是一种金属成形加工方法,在完成锻造后需要经过热处理。
锻件热处理是指将锻件加热到一定的温度,使之发生一系列物理或化学变化,达到改变其组织结构和性能的目的。
本文将针对锻件热处理的流程、方法和机理进行阐述。
锻件热处理的流程锻件热处理流程通常包括三个步骤:加热、保温和冷却。
其中,加热和冷却的过程都非常关键,因为这两个步骤会直接影响到锻件的微观组织和力学性能。
1.加热加热是指将锻件加热到一定的温度,使之发生晶粒长大、变形、晶格缺陷消失、相变等变化,从而获得一定的机械性能。
加热温度和时间是通过锻件的成分、形状和尺寸等因素来决定的。
一般来说,锻件加热到一定温度后,其冷却速度直接影响到锻件的性能。
常见的加热方式包括电阻加热、燃气加热、电弧加热、激光加热等。
2.保温保温是指将已经加热到一定温度的锻件保持在一个固定的温度下一定时间,以使锻件内部保持均匀温度,从而达到热处理的效果。
保温时间和温度取决于锻件的材质和尺寸。
优化中间温度和时间会对晶粒尺寸和锻件性能有着直接的影响。
相较于加热和冷却,保温过程是一个相对简单的步骤。
3.冷却冷却是指将经过加热和保温过程的锻件缓慢冷却至室温,使之形成相应的组织结构和力学性能。
冷却方式和速度对锻件的性能有着直接的影响。
常用的冷却方式包括空气冷却、水冷却等。
锻件热处理的方法和机理1.灭火热处理灭火热处理是指将经过加热处理的锻件,迅速放入冷却介质中,使其迅速冷却达到强化锻件的目的。
灭火热处理可以分为水淬火、油淬火、高温淬火和空气冷却等多种方式,其中以水淬火的强度最大,油淬火次之,在高温淬火和空气冷却中最低。
灭火热处理的机理是利用快速冷却的方式,使锻件内部的物理性能和化学性能发生变化,形成更加细小的晶粒和组织结构。
从而达到提高锻件材质的强度和硬度的目的。
2.回火热处理回火热处理是指在灭火热处理完成后,对锻件进行再次加热并显著降低冷却速度,从而提高锻件的韧性和塑性。
对于某些硬度较高的锻件,为了兼顾强度与韧性的要求,通常需要进行回火处理。
锻造工艺过程及模具设计第3章锻造的加热

3.6.2 锻件的冷却规范
1.空冷 :在空气中冷却,速度较快 。
2.坑(箱)冷:锻件锻后放到地坑 或铁箱中封闭冷却,或埋入坑中砂 子、石灰或炉渣内冷却。
3.炉冷:锻件锻后直接装入炉中按 一定的冷却规范缓慢冷却。
3.7 中小钢锻件的热处理
3.7.1 退火 退火是将钢加热到一定的温度,保温
1)反应是可逆反应,向右:氧化反应,向左:
还原反应。 2)加热时,与空气消耗系数有关。
空气消耗系数:又称空气过剩系数,是燃料燃 烧实际供给的空气量与理论计算空气量之比。 3)空气充足时,炉气呈氧化性,空气不足时, 炉 气呈还原性。 4)控制反应前后的生成物与反应物的浓度比。
炉气和被加热钢材的平衡图如下:
• 电热体材料:铁铬铝合金 镍铬合金 碳化硅元件 二硅化钼
图3.1 电阻炉原理图 1-电热体 2-坯料 3-变压器
●盐浴炉加热原理: 电流通过炉内电极产生
的热量把导电介质——盐熔 融,通过高温介质的对流与 传导将埋入介质中的金属加 热。 ●盐浴炉的分类:按照热源的 位置分外热式和内热式。 ●盐浴炉加热的优点:
、
辐射加热坯料。
燃料来源方便、加热炉修造容易、
加热费低、适应性强。
缺点::劳动条件差,加热速度慢, 质量低、热效率低。
应用范围:大、中、小型坯料。
2 电加热 利用电能转换热能来加热坯料。
1)电阻加热 电阻加热与火焰加热原理相同,根据
发热元件的不同分为: 电阻炉加热、 盐浴炉加热、接触电
加热
• 电阻炉加热原理:利用电 流通过炉内的电热体产生 的能量,加热炉内的金属 坯料。原理如图3.1。
升温快、加热均匀,可 以实现 金属坯料整体或局 部的无氧化加热。 ●盐浴炉加热的缺点:
铸造、热处理、锻造工艺基础

5.2锻造比 • 锻造比是锻造时金属变形程度的一种表示方法。 锻造比以金属变形前后的横 断面积的比值来表示。不同的锻造工序,锻造比的计算方法各不相同。 • 1、拔长时,锻造比为y=F0/F1或y=L1/L0 • 式中F0,L0—拔长前钢锭或钢坯的横断面积和长度; • F1 ,L1—拔长后钢锭或钢坯的横截面积和长度。 • 2、镦粗时的锻造比,也称镦粗比或压缩比,其值为 • y=F1/F0或y=H0/H1 • F0, H0—镦粗前钢锭或钢坯的横截面积和高度; • F1, H1—镦粗后钢锭或钢坯的横截面积和高度。
三箱造型浇注位置和分型面
5/
2.3浇注位置选择原则
(1)铸件的重要加工面应朝下或侧立。因铸件的上表面容易产生砂眼、气孔、 夹渣等缺陷,组织也不如下表面致密; (2)铸件的大平面应朝下。大平面朝上容易产生夹砂缺陷 (3)为防止铸件薄壁部分产生浇不足或冷隔缺陷,应将面积较大的薄壁部分 置于铸型下部或使其处于垂直或倾斜的位置; (4)对于容易产生缩孔的铸件,应使厚的部分放在铸型的上部或侧面,以便 在铸件厚壁处直接安置冒口,使之实现自下而上的定向凝固。
两组数 铸铁选用
13/
4.1 PROCAST仿真简介 • Procast是为评价和优化铸造工艺与铸造产品而开发的专业CAE软件 • Procast是所有铸造模拟软件中集成化程度最高的 • 配备了功能强大的数据接口和自动网格划分工具 • 全部模块化设计,适合任何铸造过程的模拟 • 采用有限元技术,是目前唯一能对铸造凝固过程进行热——流动——应力完
24/
5.4锻造术语 • 锻件重量:锻件毛坯的实际重量 • 飞边重量:锻造过程中外轮廓分模面处多余的材料 • 料芯重量:锻造过程中内孔多余的材料 • 火耗重量: 锻件在锻打过程中的热损耗 • 下料重量(切料重量):锻打一件锻件所需要的钢坯重量 • 材料消耗定额:锻打一件锻件所需要的钢材消耗总重量
锻造及锻后热处理工艺规范

目录1.钢质自由锻件加热工艺规范2.钢锭(坯)加热规范若干概念3.加热操作守则4.锻造操作守则5.锻件锻后冷却规范6.锻件锻后炉冷工艺曲线7.锻件锻后热装炉工艺曲线8.冷锻件校直前加热、校直后(补焊后)回火工艺曲线9.锻件各钢种正火(或退火)及高温回火温度表10.锻件有效截面计算方法钢质自由锻件加热工艺规范一.范围:本规范规定了钢质自由锻件的通用加热技术条件。
本规范适用于碳素钢、合金钢、高合金钢、高温合金钢(铁基、镍基)的冷、热、半热钢锭(坯)的锻造前加热二.常用钢号分组和始、终锻加热温度范围:注1:始锻温度为锻前加热允许最高炉温,由于钢锭的铸态初生晶粒加热时过热倾向比同钢号钢坯小,故两者的锻前加热温度相差20℃~30℃;注2:根据产品的特性、锻件技术条件、变形量等因素,始锻温度可以适当调整;注3:本规范未列入的钢种,可按化学成分相近的钢号确定;注4:重要的、关键产品的、特殊材质的钢号,其加热工艺曲线由技术部编制;注5:几种不同的钢种,不同尺寸的钢锭(或坯料),在同一加热炉加热时,要以合金成分高的,尺寸大的钢锭(或坯料)为依据编制加热工艺曲线。
三.冷钢坯。
钢锭加热规范:钢锭(坯)加热规范若干概念1.钢锭(坯)入炉前的表面温度≥550℃的称为热钢锭,400~550℃的称为半热钢锭(坯),≤400℃的称为冷钢锭。
2.锻件半成品坯料的加热平均直径计算原则:δ -壁厚H- 高度或长度D- 外径1)实心圆类:当D>H时,按H计算;当D<H时,按D计算。
2)筒类锻坯:H>D 当H>δ时,按1.3δ计算。
3)空心盘(环)类:H<D当H>δ时,按δ计算;当H<δ时,按H计算。
3.为了避免锻件粗晶组织,最后一火的始锻温度可按其剩余锻造比(Y)确定:Y=1.3~1.6 最高加热温度1050℃Y<1.3 最高加热温度950℃4.不同钢种不同规格的坯料同炉加热时,装炉温度和升温速度均按较低的选用,保温时间按较长的选用。
大型锻件锻后热处理的研究及注意事项

河北汇 工机械设备有 限公 司 ( 巨鹿 0 5 5 2 5 0 ) 杨钟胜
大 型 锻 件 的 白点 和氢 脆 缺 陷 的危 害性 很 大 ,所
以 大 型锻 件 锻 后 热 处 理 要 求 防 止 白点 和 氢 脆 ,同
瞬 间 形成 ,而 是 逐 渐 形成 的 。从 停 锻到 出现 白 点 , 需 要 经 历一 段时 间 ,这 段时 间称 之 为 白 点形 成 的孕 育 期 或潜 伏 期 。孕 育 期 的长 短取 决 于钢 的含 氢量 , 同时 也取 决 于锻 件 的厚 度 。
力 ,重结 晶细 化 晶粒 ,同时 去 氢 。
1 . 有关钢 中白点 的基本概念
( 1 )白点的危害性 白点是过 高 时 ,钢 显著 变
脆 ,从 本 质来 看 , 白点也 属 于脆 性 破 坏 。 白点 的存 在 使 钢 的 力学 性 能 特 别 是 横 向 塑 性 和 韧 性 急 剧 降 低 ,成 为最 危 险 的断 裂源 ,严 重影 响 零件 的 使 用性 能 和 寿 命 。 因此 ,锻 件 中一 旦 发现 白点 ,则 该 锻件 必须 报 废 。 ( 2 ) 白点 的 形 貌 在 锻 件 的 纵 向断 裂 面 上 呈
中含有足够数量的氢是形成白点的必要条件,内应
力 的存 在具 有 促进 白点形 成 的作 用 。 ( 5 )白 点 的 三大 特 点 ① 白点 从 来 不 在 锻 件 的 表面 形 成 。根 据 有 关资 料表 明 ,其形 成 总是 在 锻 件 内部 ,含有 白点 的 区域 离锻 件 表 面有 相 当一 段 距 离 ,约 5 0 mm。② 白点是 在 锻 后 ,当 锻件 冷 却 到 比
即进 行 锻后 去 氢 退火 。
锻造及锻后热处理工艺规范
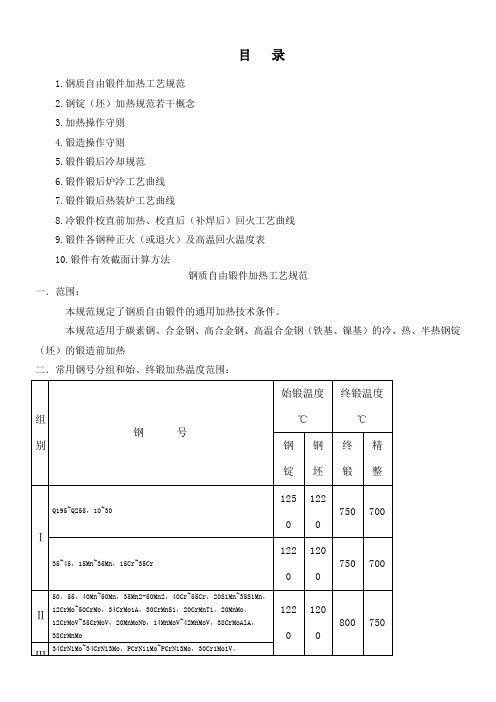
目录1.钢质自由锻件加热工艺规范2.钢锭(坯)加热规范若干概念3.加热操作守则4.锻造操作守则5.锻件锻后冷却规范6.锻件锻后炉冷工艺曲线7.锻件锻后热装炉工艺曲线8.冷锻件校直前加热、校直后(补焊后)回火工艺曲线9.锻件各钢种正火(或退火)及高温回火温度表10.锻件有效截面计算方法钢质自由锻件加热工艺规范一.范围:本规范规定了钢质自由锻件的通用加热技术条件。
本规范适用于碳素钢、合金钢、高合金钢、高温合金钢(铁基、镍基)的冷、热、半热钢锭(坯)的锻造前加热二.常用钢号分组和始、终锻加热温度范围:注1:始锻温度为锻前加热允许最高炉温,由于钢锭的铸态初生晶粒加热时过热倾向比同钢号钢坯小,故两者的锻前加热温度相差20℃~30℃;注2:根据产品的特性、锻件技术条件、变形量等因素,始锻温度可以适当调整;注3:本规范未列入的钢种,可按化学成分相近的钢号确定;注4:重要的、关键产品的、特殊材质的钢号,其加热工艺曲线由技术部编制;注5:几种不同的钢种,不同尺寸的钢锭(或坯料),在同一加热炉加热时,要以合金成分高的,尺寸大的钢锭(或坯料)为依据编制加热工艺曲线。
三.冷钢坯。
钢锭加热规范:钢锭(坯)加热规范若干概念1.钢锭(坯)入炉前的表面温度≥550℃的称为热钢锭,400~550℃的称为半热钢锭(坯),≤400℃的称为冷钢锭。
2.锻件半成品坯料的加热平均直径计算原则:δ -壁厚 H- 高度或长度 D- 外径1)实心圆类:当D>H时,按H计算;当D<H时,按D计算。
2)筒类锻坯:H>D 当H>δ时,按1.3δ计算。
3)空心盘(环)类:H<D当H>δ时,按δ计算;当H<δ时,按H计算。
3.为了避免锻件粗晶组织,最后一火的始锻温度可按其剩余锻造比(Y)确定:Y=1.3~1.6 最高加热温度1050℃Y<1.3 最高加热温度950℃4.不同钢种不同规格的坯料同炉加热时,装炉温度和升温速度均按较低的选用,保温时间按较长的选用。
锻造_热处理实验报告

一、实验目的1. 理解锻造与热处理的基本原理及其在金属材料加工中的应用。
2. 掌握锻造工艺参数对材料组织与性能的影响。
3. 学习使用锻造设备和热处理设备,了解其操作流程。
4. 通过实验,分析锻造热处理对材料微观组织、力学性能的影响。
二、实验仪器与材料1. 仪器:锻造设备(锤、钳、模具等)、加热炉、冷却设备、金相显微镜、洛氏硬度计、抛光机、腐蚀剂等。
2. 材料:碳钢、合金钢等金属材料。
三、实验原理1. 锻造:通过高温加热使金属塑性增加,在外力作用下改变其形状和尺寸的加工方法。
2. 热处理:通过加热、保温和冷却,使金属内部组织发生变化,从而改变其性能。
四、实验步骤1. 锻造工艺(1)将金属加热至适宜温度(通常为金属熔点的70%左右)。
(2)将加热后的金属放入模具中,进行锻造操作。
(3)根据需要,对锻造后的工件进行热处理。
2. 热处理工艺(1)将锻造后的工件加热至适宜温度(通常为Ac3以上30~50℃)。
(2)保温一段时间,使工件内部组织达到均匀状态。
(3)以适当的冷却速度冷却工件,使其组织发生转变。
五、实验结果与分析1. 金相组织观察通过金相显微镜观察锻造热处理后的工件组织,分析其微观结构变化。
2. 力学性能测试使用洛氏硬度计测试工件的硬度,分析热处理对硬度的影响。
3. 性能分析根据实验结果,分析锻造热处理对工件组织、性能的影响。
六、实验结论1. 锻造热处理可以显著改善金属材料的组织结构和性能。
2. 锻造工艺参数(如加热温度、保温时间、冷却速度等)对工件组织、性能有显著影响。
3. 通过合理的锻造热处理工艺,可以提高金属材料的强度、硬度、韧性等性能。
七、实验注意事项1. 锻造过程中,应严格控制加热温度、保温时间和冷却速度,以获得理想的组织结构。
2. 热处理过程中,应选择合适的加热炉和冷却设备,确保工件温度均匀。
3. 在实验过程中,应注意安全,防止烫伤、火灾等事故发生。
八、实验总结本次实验使我们对锻造热处理工艺有了更深入的了解,掌握了锻造工艺参数对材料组织、性能的影响。
T10刚的热处理

T10刚的热处理1、预备热处理(球化退火)锻造后为了给后序的加工、最终热处理工序作好准备, 应消除锻件内的应力, 改善组织, 并使其具有合适的硬度和稳定细小的组织, 以利于机械加工。
因此锻件要在毛坏状态下进行预先热处理。
T10A 碳素工具钢, 一般采取球化退火, 使渗碳体成球状均匀分布, 若锻件沿晶界出现网状碳化物时, 则先进行正火处理, 消除网状碳化物, 然后进行球化退火。
通常采用球化退火, 以获得铁素体机体上分布的细小均匀的粒状碳化物组织。
表1 球化退火工艺参数钢号加热等温温度/℃时间/ h温度/℃时间/ h 空冷硬度T10A 750~ 780 2~ 3 680~ 700 3~ 5 炉冷至500℃空冷 HB197 2、最终热处理(淬火+低温回火)2.1、淬火( 1) 淬火温度T10淬透性低。
需要用水冷却, 容易产生变形和淬裂, 另外碳素工具钢对过热敏感, 晶粒容易长大, 其淬火温度一般是在碳化物与奥氏体共存的两相区内, 这是由于碳化物的存在不仅可以阻止奥氏体的长大, 使碳素工具钢保持较小晶粒,从而能在高硬度条件下保证具有一定的韧性; 而且剩余碳化物的存在也有利于模具耐磨性的提高。
为防止过热, 选取最低的淬火加热温度( 760~ 780℃ ) , 是获得最好机械性能的关键,为防止淬火开裂, 必须在淬火方法上实现均匀冷却。
( 2) 加热、保温时间的确定由于加热时间与模具的材质、工件大小有关。
升温时间因工件大小而异, 保温时间依材质而不同, 加热时间不可取一定值, 加热时间的长短直接影响模具的组织性能。
为保证T10A 冷作模具基体奥氏体化, 碳化物溶解, 必须有一定保温时间, 保温时间采用40~ 60 min。
2.2、回火模具在淬火或电火花加工后应及时进行回火处理, 回火温度应根据模具的硬度性能要求选择不同的回火温度, 以获得不同强度、韧性及硬度要求, T10 碳素工具钢在不同回火温度下的硬度如表表2T10 碳素工具钢在不同回火温度下的硬度钢号达到下列硬度(HRC)范围的回火温度/℃T10A 45~ 50 50~ 54 54~ 58 58~ 62360~ 380 300~ 320 250~ 270 160~ 180。
铸造-锻造-热处理

【铸造】
1.熔融的液态金属填满型腔冷却。制件中间易产生气孔。
2.把金属加热熔化后倒入砂型或模子里,冷却后凝固成为器物。
3.铸造对被加工才料有要求,一般铸铁、铝等的铸造性能较好。铸造不具备锻造的诸多优点,但它能制造形状复杂的零,因此常用于力学性能要求不高的支称件的毛丕制造。例如机床外壳等。
目的:提高钢件表面硬度、耐磨性及疲劳强度,心部仍保持韧性状态。
应用要点:
1.多用于中碳钢制件,一般淬透层深度为2~6mm;
2.适用于单件或小批量生产的大型工件和需要局部淬火的工件。
9.感应加热表面淬火
操作方法:将钢件放入感应器中,使钢件表层产生感应电流,在极短的时间内加热到淬火温度,然后喷水冷却。
2. 不仅可以作为各种较为重要结构的最后热处理,而且还可以作为某些紧密零件,如丝杠等的预先热处理,以减小变形。
6.时效
操作方法:将钢件加热到80~200度,保温5~20小时或更长时间,然后随炉取出在空气中冷却。
目的:
1. 稳定钢件淬火后的组织,减小存放或使用期间的变形;
2.减轻淬火以及磨削加工后的内应力,稳定形状和尺寸。
【锻造】
1.主要是在高温下用挤压的方法成型。可以细化制件中的晶粒。
2.用锤击等方法,使在可塑状态下的金属材料成为具有一定形状和尺寸的工件,并改变它的物理性质。
3.锻造时,金属经过塑性变形,有细化晶粒的做用,切纤维连续,因此常用于重要零件的毛丕制造,例如轴、齿论等。
【热处理】
热处理是将工件在介质中加热到一定温度并保温一定时间,然后用一定速度冷却,以改变金属的组织结构,从而改变其性能(包括物理、化学和力学性能)的工艺。改善钢的力学性能或加工性能。
锻造裂纹与热处理裂纹原理形态

一:锻造裂纹与热处理裂纹形态一:锻造裂纹一般在高温时形成,锻造变形时由于裂纹扩大并接触空气,故在100X或500X 的显微镜下观察,可见到裂纹内充有氧化皮,且两侧是脱碳的,组织为铁素体,其特征是裂纹比较粗壮且一般经多条形式存在,无明细尖端,比较圆纯,无明细的方向性,除以上典型外,有时会出现有些锻造裂纹比较细。
裂纹周围不是全脱碳而是半脱碳。
淬火加热过程中产生的裂纹与锻造加热过程形成的裂纹在性质和上有明显的差别。
对结构钢而言,热处理温度一般较锻造温度要低得多,即使是高速钢、高合金钢其加热保温时间则远远小于锻造温度。
由于热处理加热温度偏高,保温时间过长或快速加热,均会在加热过程中产生早期开裂。
产生沿着较粗大晶粒边界分布的裂纹;裂纹两侧略有脱碳组织,零件加热速度过快,也会产生早期开裂,这种裂纹两侧无明显脱碳,但裂纹内及其尾部充有氧化皮。
有时因高温仪器失灵,温度非常高,致使零件的组织极粗大,其裂纹沿粗大晶粒边界分布。
结构钢常见的缺陷:1 锻造缺陷(1)过热、过烧:主要特征是晶粒粗大,有明显的魏氏组织。
出现过烧说明加热温度高、断口晶粒粗大,凹凸不平,无金属光泽,晶界周围有氧化脱碳现象。
(2)锻造裂纹:常产生于组织粗大,应力集中处或合金元素偏析处,裂纹内部常充满氧化皮。
锻造温度高,或者终端温度低,都容易产生裂纹。
还有一种裂纹是锻造后喷水冷却后形成的。
(3)折叠:冲孔、切料、刀板磨损、锻造粗糙等原因造成了表面缺陷,在后续锻造时,将表面氧化皮等缺陷卷入锻件本体内而形成折缝。
在显微镜上观察时,可发现折叠周围有明显脱碳。
2 热处理缺陷(1)淬裂:其特点是刚健挺直,呈穿晶分布,起始点较宽,尾部细长曲折。
此种裂纹多产生于马氏体转变之后,故裂纹周围的显微组织与其它区域无明显区别,也无脱碳现象。
(2)过热:显微组织粗大,如果是轻度过热,可采用二次淬火来挽救。
(3)过烧:除晶粒粗大外,部分晶粒已趋于熔化,晶界极粗。
(4)软点:显微组织有块状或网状屈氏体和未溶铁素体等。
锻造及锻后热处理工艺规范DOC.doc
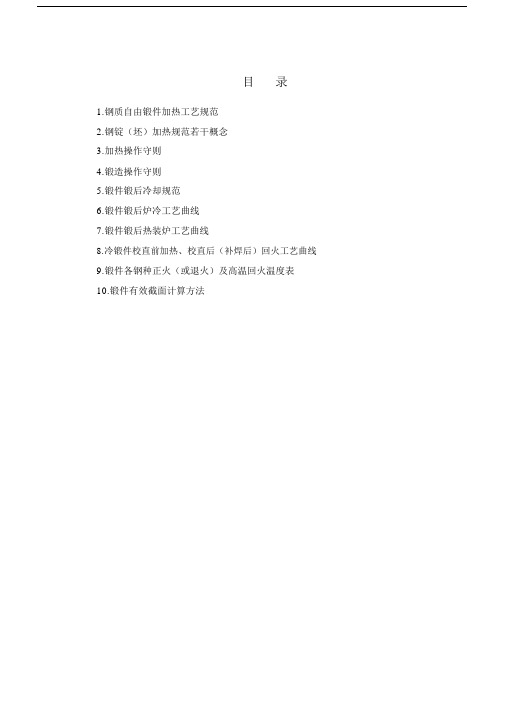
目录1.钢质自由锻件加热工艺规范2.钢锭(坯)加热规范若干概念3.加热操作守则4.锻造操作守则5.锻件锻后冷却规范6.锻件锻后炉冷工艺曲线7.锻件锻后热装炉工艺曲线8.冷锻件校直前加热、校直后(补焊后)回火工艺曲线9.锻件各钢种正火(或退火)及高温回火温度表10.锻件有效截面计算方法钢质自由锻件加热工艺规范一.范围:本规范规定了钢质自由锻件的通用加热技术条件。
本规范适用于碳素钢、合金钢、高合金钢、高温合金钢(铁基、镍基)的冷、热、半热钢锭(坯)的锻造前加热二.常用钢号分组和始、终锻加热温度范围:组号钢别Q195~Q255, 10~30Ⅰ35~45,15Mn~35Mn ,15Cr~35Cr50,55,40Mn~50Mn ,35Mn2-50Mn2 ,40Cr~55Cr ,20SiMn~35SiMn ,12CrMo~50CrMo ,34CrMo1A ,30CrMnSi , 20CrMnTi ,20MnMo ,Ⅱ12CrMoV~35CrMoV , 20MnMoNb , 14MnMoV~42MnMoV,38CrMoAlA ,38CrMnMo34CrNiMo~34CrNi3Mo,PCrNi1Mo~PCrNi3Mo,30Cr1Mo1V,25Cr2Ni4MoV ,22Cr2Ni4MoV ,5CrNiMo ,5CrMnMo ,37SiMn2MoV 30Cr2MoV ,40CrNiMo ,18CrNiW ,50Si2~60Si2 ,65Mn ,50CrNiW ,50CrMnMo ,60CrMnMo ,60CrMnVT7~T10 , 9Cr,9Cr2, 9Cr2Mo , 9Cr2V ,9CrSi ,70Cr3Mo ,Ⅲ1Cr13~4Cr13 ,86Cr2MoV ,Cr5Mo , 17-4PH0Cr18Ni9~2Cr18Ni9 ,0Cr18Ni9Ti , Cr17Ni2 , F316LN50Mn18Cr4 , 50Mn18Cr4N , 50Mn18Cr4WN , 18Cr18Mn18NGCr15,GCr15SiMn , 3Cr2W8V ,CrWMo , 4CrW2Si~6CrW2SiCr12MoV1 , 4Cr5MoVSi(H11) , W18Cr4VGH80, GH901, GH904 ,GH4145 ,WR26 ,ⅣNiCr20TiAl , incone1600, incone1800始锻温度终锻温度℃℃钢锭钢坯终锻精整12501220750700 1220120075070012201200800750 12001180850800 120011808508001200 1180 850 800 1180 1160 950 900 1130 1100 930 930注 1:始锻温度为锻前加热允许最高炉温,由于钢锭的铸态初生晶粒加热时过热倾向比同钢号钢坯小,故两者的锻前加热温度相差 20℃~30℃;注 2:根据产品的特性、锻件技术条件、变形量等因素,始锻温度可以适当调整;注 3:本规范未列入的钢种,可按化学成分相近的钢号确定;注 4:重要的、关键产品的、特殊材质的钢号,其加热工艺曲线由技术部编制;注 5:几种不同的钢种,不同尺寸的钢锭(或坯料),在同一加热炉加热时,要以合金成分高的,尺寸大的钢锭(或坯料)为依据编制加热工艺曲线。
锻件的热处理种类及应用
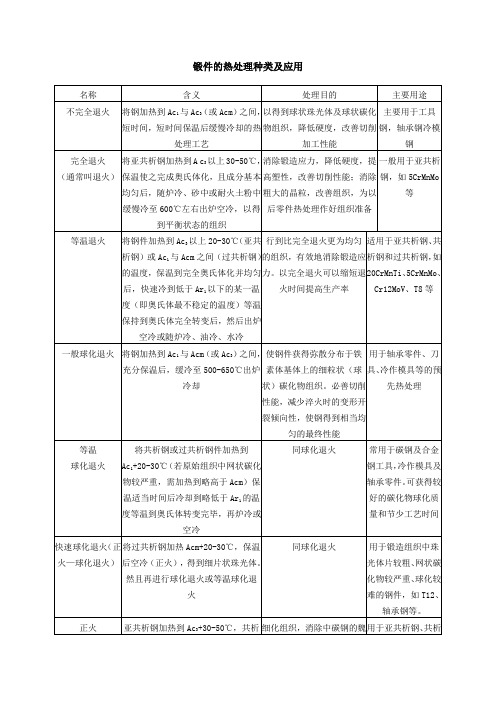
“蛤蟆皮” 铝合金、铜合金的坯料,在镦粗时表
由于坯料过热,晶粒粗大而引起
表面 面形成“蛤蟆皮”,或者出现类似秸 有粗晶环的铝合金毛坏,在镦粗时也会出现这种现象
皮的粗糙表面,严重时还要开裂
魏氏 α 相或 (α+β)钛合金坏料过热后,其显微由于加热温度超过了(α+β)钛合金的 β 转变温度而
(普通正火) 钢和过共析钢加热到 Acm+30-50℃, 氏组织或过共析钢的网状 钢和过共析钢的热
保温一定时间后空冷,得到珠光体型碳化物,减小应力,改善切
处理
组织的热处理
削加工性能
二段正火 按普通正火加热保温后,先把工件快 减少变形和消除非正常组 用于形状复杂或断
冷到 Ar1 以下 550℃左右,然后再放入
白点在合金结构钢中常见,在普通碳
钢中也有发现
缩孔残余 在锻件低倍检查时,出现不规则的皱 由于钢锭冒口部分产生的集中缩孔未切除干净,开坯
折状缝隙,形似裂纹,呈现深褐色或
和轧制时残留在钢坯内部而产生的
灰白色;高倍检查缩孔残余附近有大
量非金属夹杂物,质脆易剥落
铝合金挤压 经热处理后供应的铝合金挤压棒材, 主要是由于铝合金中 Mn、Cr 等元素以及挤压时金属
热处理工艺
将时效强化合金或不锈钢、耐热钢加 改善锻态时的强化相不均匀分 用于不锈钢、耐
热到一定高温(不锈钢、耐热钢为 布,降低硬度、提高塑性、抗 热钢和时效强化
1000-1150℃)使强化相全部或大部 蚀性及导电性或为以后的时效
合金
分溶入固溶体,并调整晶粒尺寸,然
处理进行准备
后以较快速度(水、空气等)冷却
棒材上的粗 在其横断面外层环形内出现粗大晶 与挤压筒壁之间的摩擦,使棒材表面层变形剧烈所致
热处理工艺对锻造材料的组织和力学性能的优化
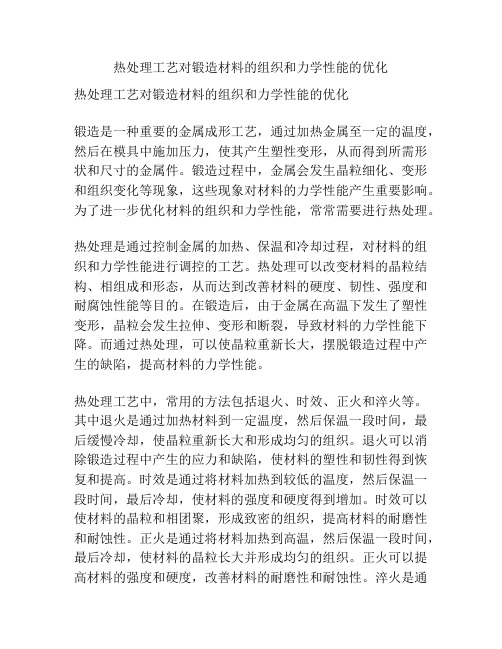
热处理工艺对锻造材料的组织和力学性能的优化热处理工艺对锻造材料的组织和力学性能的优化锻造是一种重要的金属成形工艺,通过加热金属至一定的温度,然后在模具中施加压力,使其产生塑性变形,从而得到所需形状和尺寸的金属件。
锻造过程中,金属会发生晶粒细化、变形和组织变化等现象,这些现象对材料的力学性能产生重要影响。
为了进一步优化材料的组织和力学性能,常常需要进行热处理。
热处理是通过控制金属的加热、保温和冷却过程,对材料的组织和力学性能进行调控的工艺。
热处理可以改变材料的晶粒结构、相组成和形态,从而达到改善材料的硬度、韧性、强度和耐腐蚀性能等目的。
在锻造后,由于金属在高温下发生了塑性变形,晶粒会发生拉伸、变形和断裂,导致材料的力学性能下降。
而通过热处理,可以使晶粒重新长大,摆脱锻造过程中产生的缺陷,提高材料的力学性能。
热处理工艺中,常用的方法包括退火、时效、正火和淬火等。
其中退火是通过加热材料到一定温度,然后保温一段时间,最后缓慢冷却,使晶粒重新长大和形成均匀的组织。
退火可以消除锻造过程中产生的应力和缺陷,使材料的塑性和韧性得到恢复和提高。
时效是通过将材料加热到较低的温度,然后保温一段时间,最后冷却,使材料的强度和硬度得到增加。
时效可以使材料的晶粒和相团聚,形成致密的组织,提高材料的耐磨性和耐蚀性。
正火是通过将材料加热到高温,然后保温一段时间,最后冷却,使材料的晶粒长大并形成均匀的组织。
正火可以提高材料的强度和硬度,改善材料的耐磨性和耐蚀性。
淬火是通过将材料迅速冷却,使其形成马氏体组织,从而提高材料的强度、硬度和耐磨性。
淬火可以使材料的晶粒细化,并形成致密的组织。
通过合理选择和控制热处理工艺参数,可以对锻造材料的组织和力学性能进行优化。
首先,应根据不同的材料和需求,选择适当的热处理方法。
比如,对于需要提高材料的硬度和强度的情况,可以采用淬火工艺;对于需要提高材料的韧性和韧度的情况,可以采用退火工艺。
其次,应控制热处理过程中的温度、时间和冷却速度等参数。
锻造与热处理(张)
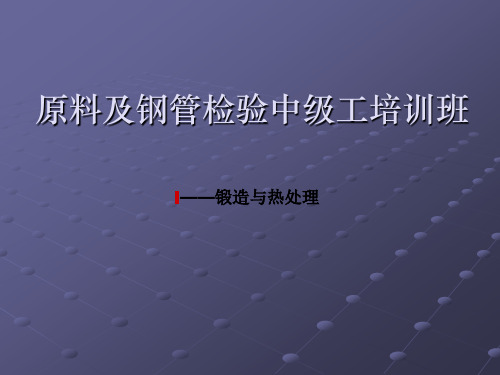
2:压力容器热处理名词解析
8. 固溶处理
将合金加热至高温单相区,并经过充分的保温,使 过剩相充分溶解到固溶体中后快速冷却,以得到过 饱和固溶体的工艺,称为固溶处理。固溶处理的目 的,是为了改善金属的塑性和韧性,并为进一步进 行沉淀硬化处理准备条件。
2:压力容器热处理名词解析
9. 退火 把钢加热到临界点(Ac1或Ac3)或再结晶温度以上, 保温适当时间,然后缓慢冷却,使组织达到接近平衡状 态的热处理工艺。可分为: 完全退火,又称重结晶退火,一般简称退火,是加热至 Ac3以上20~40℃保温后缓冷的一种热处理操作。退火 可以细化晶粒,消除内应力,改善钢的性能,主要用于 亚共析成分的各种钢材和热轧型材。 消除应力退火是将钢加热到500~600℃(Ac1以下), 然后保温、缓冷的热处理操作。
1、热处理一般过程
压力容器使用的低合金钢和合金钢中加有锰、铬、 钼、镍、钒等各种合金元素,合金元素的加入会 使TTT曲线图发生变化。概括地说TTT曲线图的 变化有两个方面:一是绝大多数合金元素能使C 曲线的位置右移,其后果是使淬火临界冷却速度 减小,有利于提高零件的淬透性;但对于不希望 发生淬硬现象的工件来说则是不利的,例如低碳 钢焊缝焊后自然冷却一般不会淬硬,但某些低合 金钢焊缝焊后自然冷却往往会淬硬。二是合金元 素的加入能改变TTT曲线的形状。
1、热处理一般过程
锅炉压力容器使用的低碳属 亚共析钢 ,左图就是亚共析 钢的TTT图,与共析钢的TTT 曲线相比,在曲线鼻尖上部 区域多出一条线。这表明奥 氏体在转变为珠光体类组织 之前,亚共析钢比共析钢多 一个先析出铁素体的过程 。
1、热处理一般过程
此外,亚共析钢C曲线的位 置相对于共析钢的C曲线位 置左移,这意味着前者等温 转变所需时间较短,也意味 着在连续冷却的条件下,如 果冷却速度相同,亚共析钢 的组织的塑性和韧性相对较 好,硬度相对较低 。
锻造及锻后热处理工艺规范

目录1.钢质自由锻件加热工艺规范2.钢锭(坯)加热规范若干看法3.加热操作守则4.锻造操作守则5.锻件锻后冷却规范6.锻件锻后炉冷工艺曲线7.锻件锻后热装炉工艺曲线8.冷锻件校直前加热、校直后(补焊后)回火工艺曲线9.锻件各钢种正火(或退火)及高温回火温度表10.锻件有效截面计算方法钢质自由锻件加热工艺规范一.范围:本规范规定了钢质自由锻件的通用加热技术条件。
本规范适用于碳素钢、合金钢、高合金钢、高温合金钢(铁基、镍基)的冷、热、半热钢锭(坯)的锻造前加热二.常用钢号分组和始、终锻加热温度范围:组号钢别Q195~Q255, 10~30Ⅰ35~45,15Mn~35Mn ,15Cr~35Cr50,55,40Mn~50Mn ,35Mn2-50Mn2 ,40Cr~55Cr ,20SiMn~35SiMn ,12CrMo~50CrMo ,34CrMo1A ,30CrMnSi , 20CrMnTi ,20MnMo ,Ⅱ12CrMoV~35CrMoV , 20MnMoNb , 14MnMoV~42MnMoV,38CrMoAlA ,38CrMnMo34CrNiMo~34CrNi3Mo,PCrNi1Mo~PCrNi3Mo,30Cr1Mo1V,25Cr2Ni4MoV ,22Cr2Ni4MoV ,5CrNiMo ,5CrMnMo ,37SiMn2MoV 30Cr2MoV ,40CrNiMo ,18CrNiW ,50Si2~60Si2 ,65Mn ,50CrNiW ,50CrMnMo ,60CrMnMo ,60CrMnVT7~T10 , 9Cr,9Cr2, 9Cr2Mo , 9Cr2V ,9CrSi ,70Cr3Mo ,Ⅲ1Cr13~4Cr13 ,86Cr2MoV ,Cr5Mo , 17-4PH0Cr18Ni9~2Cr18Ni9 ,0Cr18Ni9Ti , Cr17Ni2 , F316LN50Mn18Cr4 , 50Mn18Cr4N , 50Mn18Cr4WN , 18Cr18Mn18NGCr15,GCr15SiMn , 3Cr2W8V ,CrWMo , 4CrW2Si~6CrW2SiCr12MoV1 , 4Cr5MoVSi(H11) , W18Cr4VGH80, GH901, GH904 ,GH4145 ,WR26 ,ⅣNiCr20TiAl , incone1600, incone1800始锻温度终锻温度℃℃钢锭钢坯终锻精整12501220750700 1220120075070012201200800750 12001180850800 1200118085080012001180850800 11801160950900 11301100930930注1:始锻温度为锻前加热赞成最高炉温,由于钢锭的铸态初生晶粒加热时过热倾向比同钢号钢坯小,故两者的锻前加热温度相差 20℃~30℃;注2:依照产品的特点、锻件技术条件、变形量等因素,始锻温度能够合适调整;注3:本规范未列入的钢种,可按化学成分周边的钢号确定;注4:重要的、要点产品的、特别材质的钢号,其加热工艺曲线由技术部编制;注5:几种不同样的钢种,不同样尺寸的钢锭(或坯料),在同一加热炉加热时,要以合金成分高的,尺寸大的钢锭(或坯料)为依照编制加热工艺曲线。
锻后热处理

锻后热处理一、锻后热处理的目的:锻后热处理又称第一热处理或预备热处理。
主要目的是防止白点与氢脆,消除内应力,降低硬度,改善锻件的切削性能,改善零件内部组织,细化晶粒,为最终热处理做好组织准备。
对不再进行最终热处理的零件,通过本道热处理工序后,达到零件技术条件规定的各项要求。
钢的正火和退火选择一般原则:正火和退火在某种程序上有相似之处,它们在实际生产中,有时可以相互代替的。
退火和正火的选用原则主要从如下三方面考虑:1、从使用性能上考虑:如果钢件的性能要求不太高,随后不再进行淬火和回火的话,则往往可以用正火来提高力学性能;但如果零件的形状比较复杂,正火的冷却速度有形成裂纹危险的话,则采用退火。
另外从减少最终热处理(淬火)的变形开裂倾向来看,退火比正火好。
2、从切削性能上考虑:一般来说,金属的硬度在160-240HBS范围内的切削加工性能比较良好,过高的硬度不但难以加工且会造成刀具很快磨损,而过低的硬度则形成很长的切削缠绕刀具,造成刀具发热和磨损,加工后零件表面粗糙度较大。
低中碳结构钢以正火作为预先热处理比较合适,高碳结构钢和工具钢则以退火较好。
3、从经济上考虑:正火比退火的生产周期短,能耗少且操作简单,故在可能的条件下应优先考虑以正火代替退火。
装炉时应注意什么?解释一下台车炉均温、保温、封炉冷、炉冷概念:装炉时应全面考虑工艺要求、加热均匀性、便于目测、出炉方便、冷却均匀等,并力求做到台车负荷均匀。
台车炉均温指炉顶偶达到规定之温度,保温指炉温、件温、偶温三温一致,工件温度及其均匀性以大表读数和目测工件表面颜色为准。
封炉冷为停火并关闭闸板、点火孔炉冷,在冷却过程中不得打开炉门和炉盖。
炉冷台车炉400度,井式炉300度以上停火关闭闸板炉内冷却,在上述温度下为打开闸板冷却。
退火、正火缺陷,返修方法:过烧形成原因:加热温度过高使晶界氧化或局部熔化。
返修方法:报废。
黑斑形成原因:高碳钢加热温度过高保温时间过长使渗碳体石墨化,断口呈灰黑色。
锻造及锻后热处理工艺规范
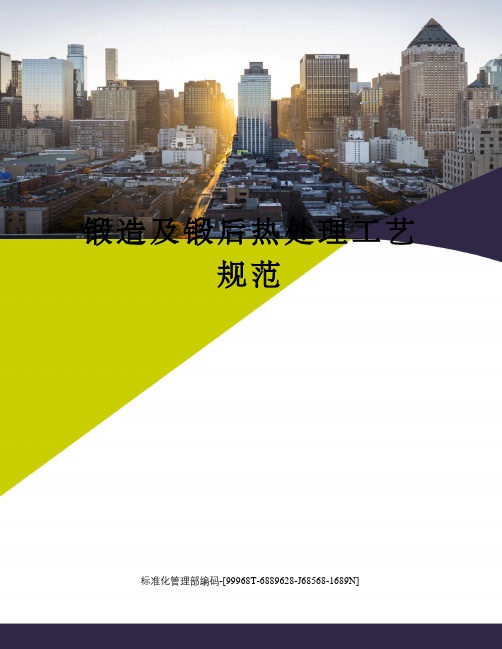
锻造及锻后热处理工艺规范标准化管理部编码-[99968T-6889628-J68568-1689N]目录1.钢质自由锻件加热工艺规范2.钢锭(坯)加热规范若干概念3.加热操作守则4.锻造操作守则5.锻件锻后冷却规范6.锻件锻后炉冷工艺曲线7.锻件锻后热装炉工艺曲线8.冷锻件校直前加热、校直后(补焊后)回火工艺曲线9.锻件各钢种正火(或退火)及高温回火温度表10.锻件有效截面计算方法钢质自由锻件加热工艺规范一.范围:本规范规定了钢质自由锻件的通用加热技术条件。
本规范适用于碳素钢、合金钢、高合金钢、高温合金钢(铁基、镍基)的冷、热、半热钢锭(坯)的锻造前加热二.常用钢号分组和始、终锻加热温度范围:注1:始锻温度为锻前加热允许最高炉温,由于钢锭的铸态初生晶粒加热时过热倾向比同钢号钢坯小,故两者的锻前加热温度相差20℃~30℃;注2:根据产品的特性、锻件技术条件、变形量等因素,始锻温度可以适当调整;注3:本规范未列入的钢种,可按化学成分相近的钢号确定;注4:重要的、关键产品的、特殊材质的钢号,其加热工艺曲线由技术部编制;注5:几种不同的钢种,不同尺寸的钢锭(或坯料),在同一加热炉加热时,要以合金成分高的,尺寸大的钢锭(或坯料)为依据编制加热工艺曲线。
三.冷钢坯。
钢锭加热规范:钢锭(坯)加热规范若干概念1.钢锭(坯)入炉前的表面温度≥550℃的称为热钢锭,400~550℃的称为半热钢锭(坯),≤400℃的称为冷钢锭。
2.锻件半成品坯料的加热平均直径计算原则:δ -壁厚 H- 高度或长度 D- 外径1)实心圆类:当D>H时,按H计算;当D<H时,按D计算。
2)筒类锻坯:H>D 当H>δ时,按δ计算。
3)空心盘(环)类:H<D当H>δ时,按δ计算;当H<δ时,按H计算。
3.为了避免锻件粗晶组织,最后一火的始锻温度可按其剩余锻造比(Y)确定:Y=~ 最高加热温度1050℃Y< 最高加热温度950℃4.不同钢种不同规格的坯料同炉加热时,装炉温度和升温速度均按较低的选用,保温时间按较长的选用。
锻造前的准备和锻后热处理
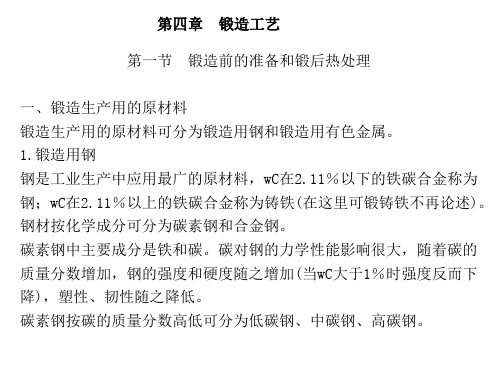
6.精密剪切下料 由于无飞边锻模、精密锻造、冷挤压以及精密辗压等新工艺的出现 和日益广泛的应用,对棒料剪切下料工艺的要求也越来越高。要求 采用精密下料方法,以提高断面质量,减少切断变形,严格控制下 料公差和提高劳动生产率。 采用的方法有在现有剪切设备上改进剪切模具;采用新的精密剪切 下料设备;采用综合措施,由计算机控制下料等。其中有套筒模剪 切、径向加紧剪切和精密剪床进行剪切。 除上述切割方法外,还有等离子切割法、电子束切割法、阳极切割 法等。
1.锯切 锯切常在圆盘锯、弓形锯和带锯上进行。圆盘锯是由电动机带动带 齿的锯盘慢速旋转并移动,而将棒料切断。圆盘锯通用性强,锯盘
的最大直径可达2m,能够锯切的棒料直径在750mm以下。 弓形锯是由电动机带动带齿的锯条作往复移动,而把棒料切断。弓 形锯投资少,使用方便,适用于小批生产,可以锯切的棒料直径在1
割的金属,如高温合金GH33等。缺点是砂轮损耗较大;工人劳动条 件较差,需要有良好的通风设备;切割低熔点金属棒料时(如铝合 金等),对切割端面稍有影响。
5.气割
气割是利用氧气和可燃气体的气割器(称割炬),产生温度很高的火焰, 使割缝上的金属熔化而烧断金属材料。 气割主要用于大型钢坯和锻件的大断面切割,也可以用于小批生产的 大型模锻件的切边。气割下料的费用较低,设备简单轻便。但气割下 料的断面质量差,金属损耗较多,精度低,生产率低,劳动条件差, 且影响金属的性能。
锻造用钢锭前热处理工艺流程

锻造用钢锭前热处理工艺流程下载温馨提示:该文档是我店铺精心编制而成,希望大家下载以后,能够帮助大家解决实际的问题。
文档下载后可定制随意修改,请根据实际需要进行相应的调整和使用,谢谢!并且,本店铺为大家提供各种各样类型的实用资料,如教育随笔、日记赏析、句子摘抄、古诗大全、经典美文、话题作文、工作总结、词语解析、文案摘录、其他资料等等,如想了解不同资料格式和写法,敬请关注!Download tips: This document is carefully compiled by the editor. I hope that after you download them, they can help yousolve practical problems. The document can be customized and modified after downloading, please adjust and use it according to actual needs, thank you!In addition, our shop provides you with various types of practical materials, such as educational essays, diary appreciation, sentence excerpts, ancient poems, classic articles, topic composition, work summary, word parsing, copy excerpts,other materials and so on, want to know different data formats and writing methods, please pay attention!热处理是制备工业用钢锭的重要工艺环节,通过在一定温度范围内加热和冷却,使金属材料的内部结构和性能发生改变,以提高其机械性能、耐磨性和耐久性。
- 1、下载文档前请自行甄别文档内容的完整性,平台不提供额外的编辑、内容补充、找答案等附加服务。
- 2、"仅部分预览"的文档,不可在线预览部分如存在完整性等问题,可反馈申请退款(可完整预览的文档不适用该条件!)。
- 3、如文档侵犯您的权益,请联系客服反馈,我们会尽快为您处理(人工客服工作时间:9:00-18:30)。
(4) 超声波检验
• 超声波检验是检验材料是否有内部缺陷的主要手 段之一。因为在检验中经常需要调整灵敏度,而 且是使用底波反射进行比较或调整,因此零件完 全加工成形后会影响正常的超声波检验。比如螺 纹、油孔、键槽、台阶等加工后会影响检验的进 行,还会影响结果的判断,因此超声波检验应在 制造的适当阶段进行。所谓适当阶段一般是指材 料最终热处理后(因为热处理有形成内部缺陷的 可能)。最终热处理之前的超声波检验只能算作 预先探伤,内部控制,不能作为最终检验结果。
目的主要是使钢件得到马氏体(或贝氏体)组织,提高钢的硬度 和强度 。
淬 火 温 度 范 围
冷却介质
冷却速度: 盐水 > 水 > 盐浴 > 油
淬火方法
单介质淬火:水、油冷
双介质淬火:水冷 + 油冷
分级淬火: >Ms盐浴中均温+空冷
等温淬火( 在盐、碱浴中) → 下B
淬火缺陷
过热与过烧 硬度不足和软点
某锻件扩氢时间
2.4主要锻造缺陷监督要点
• 温度控制不当引起的缺陷
• 过热、过烧、终锻温度偏低引起的裂纹(龟裂)等
• 锻造不当引起的缺陷
• 折叠、芯部未锻透、内部裂纹(包括饼类锻件镦锻时的刚 性撕裂)等
• 切头尾量不足使钢锭两端缺陷残留在锻件上 • 锻造比过大引起各向异性 • 扩氢时间不够造成白点 • 不锈钢锻造时易发生表面龟裂或裂纹
氧化与脱碳 变形和开裂
回火
淬火后,加热到Ac1以下,保温,冷却。 目的:消除淬火应力,调整性能。
低温回火(150~250℃) → 回火M ( 过饱和F +薄片状Fe2.4C ) + A‘ 。 淬火应力↓ ,韧性↑ ,保持淬火后的高硬度。
用于高C工具钢等。 中温回火(350~500℃)→ 回火T (F +细粒状Cm ) 。弹性极限和屈 服强度↑,韧性和硬度中等。 用于弹簧等。 高温回火(500~650℃)→ 回火S (等轴状F +粒状Cm ) 。综合机械 性能最好, 即强度、塑性和韧性都较好。 用于重要零件。调质处理 —— 淬火 + 高温回火
目的是细化晶粒,消除网状渗碳体,并为淬火、切削加工等后续工 序作组织准备。
钢的种类
低碳 低合金钢
中碳钢
过共析钢
正火主要目的
消除过热组织、细化晶粒、改善切削性
消除组织缺陷、保持硬度、为调质做准备 消除网状二次渗碳体、为球化退火和 淬火做准备
高合金钢 淬火作用(空淬)
淬火
淬火是指将工件加热奥氏体化后,以适当方式冷却获得马氏体或 (和)贝氏体组织的热处理工艺。
• 时效硬化是新相从过饱和固溶体中析出而得到强 化。有时需要加入固溶强化元素W、Mo等。
• 抗腐蚀试验时的敏化处理
AP1000主管道固溶热处里
2.5.4锻件试样的模拟焊后热处理
• 由于锻件部件在今后的组装中要经历焊接 、焊后热处理及焊接返修、焊接返修后的 焊后热处理等数次热循环的作用。锻件试 样的模拟焊后热处理的目的是通过模拟热 循环的过程并在模拟焊后热处理结束后进 行的机械性能试验结果中得出符合性能要 求的结论,确保锻件材料在今后所经历的 数次热循环后材料的力学性能和晶体结构 等不会发生很大的影响和变化。
2.5.1钢在淬火时的组织转变
2.5.2合金元素的影响
热处理设备
分类
退火分类
完全退火 球化退火 等温退火 扩散退火 去应力退火
加热温度
A3线以上 30-50°C
A1线以上 20-40°C
冷却方式 主要目的
缓慢冷却
消除粗晶和 不均匀组织
缓冷至
将片状P变为
600°C空冷 球状P
适用范围
亚共析钢
过共析钢
• • 各种检验方法均有优缺点,有时需要用
多种方法检验互相作为补充。
第2讲
• 第2讲
• 锻造和热处理
• 锻造有锤锻、 • 水压机自由锻造、 • 模锻等领域。 • 大型锻件均采用水压机
自由锻造,其它从略。
水压机
2.1 锻造的目的
• 锻造有两个主要目的: • 一是成形 • 二是改善内部质量
2.2 锻造中的主要注意事项
• 2.2.1 钢锭的加热 • 2.2.2 温度与锻造阻力之间的关系 • 2.2.3 温度与保温时间对奥氏体晶粒度的影
对面进行远区探测。特殊情况下可以采取一些措施减小盲 区(如使用小晶片探头)或水浸探伤等。
•
厚壁管道的横波检验中要注意避免产生近内表面的
探伤盲区。比如使用K1探头,在与切线呈45°的包络线
内部是探伤盲区,其中有缺陷会遗漏。因此需要计算,或
使用相同尺寸的对比试块。发现有盲区时应调整入射角度
或采用其它措施。
• 由于核电主设备所用的锻件重量大,进行热处理时材料表 面和心部在淬火过程中冷却速度不一样,造成内外质量的 不一致。
• 力学性能取样位置的要求
承受强辐照的反应堆压力容器 筒节用的Mn-Ni-Mo合金钢锻件
不锈钢的固溶热处理和时效硬化
• 不锈钢的固溶热处理仅针对奥氏体不锈钢。因在 固态加热和冷却的过程中,不发生基体组织转变, 为了将平衡组织中的碳化物等影响韧性和耐蚀性 的第2相消除,将材料加热到1000℃以上,保持 一段时间,让碳化物等充分溶解到奥氏体晶粒中 去,然后,在水中快速冷却,形成室温下的单相 过饱和固溶体。此时材料最软。
探伤盲区示意图
2) 使用6dB方法测量缺陷的大小
• 使用6dB方法测量缺陷的大小是基于将缺陷当成是平底孔 来进行的。一般是假设缺陷较大,晶片发射的所有射线被 缺陷反射回来,这时反射波最高。然后移动晶片,当一部 分发射波脱离缺陷时反射波降低,当晶片中心移动到缺陷 边缘时,晶片发射波的一半反射回来,反射波幅度为原来 的一半,正好是6dB。由此确定缺陷的边缘和尺寸。使用 该方法确定的缺陷尺寸小于或等于晶片尺寸时,测量的结 果是错误的,必须使用其它方法确定缺陷的大小。或说明 缺陷较小,只使用平底孔当量而不计其尺寸。
(5) 射线照相检验
• 射线照相检验中X射线检验和γ射线检验等, 主要用于铸件内部质量检验和焊缝焊接质 量检验。射线照相检验对于体积性的缺陷 (缩孔,夹杂类)比较敏感,对于非体积 性的缺陷敏感性较差 。
(6) 涡流和漏磁通检验
• 管道的内部质量检验中有时使用涡流或漏 磁通检验。涡流或漏磁通检验能检测出重 大缺陷,特别是尖短型缺陷。
响 • 2.2.4 低温锻造的缺陷 • 2.2.5 高温造成的过热和过烧
2.3 锻造中锻件的锻造比
• 锻造中材料的表面流动现象 • 最终锻造的临界变形量 • 终锻温度和锻件晶粒度 • 锻造精度与内在质量 • 锻造中锻件的锻后冷却 • 预备热处理的目的 • 扩氢和过冷
压机与材料的表面流动现象
锻后热处理
钢的淬透性
• 钢的化学成分决定该钢种的淬透性 • 圆柱端部喷水试验可以确定材料的淬透性 • 尺寸对淬透性的影响
2.5.3尺寸对性能的影响
• 材料的尺寸越大,相同冷却条件下因材料的热容量的影响, 冷却速度越慢,要达到规定的冷却速度就困难,而且相应 产生的热应力也变大。淬火过程中除了热应力还有组织转 变的应力。晶粒由奥氏体的面心立方转变为马氏体的体心 立方时,是一种晶格的弹性切变,体积膨胀。
1) 超声波检验中的盲区
• 通常使用的直探头纵波检验是使用机油耦合的表面接触法 检验,晶片发射的超声波在进入零件时,在表面有一个与
晶片大小成比例的盲区(见下图)。在近表面的一段范围 内,由于杂波较高,即使没有缺陷也有较高的反射波,有 缺陷时也难以判断。不过,一般情况下从前面说明的钢锭 结构来看,零件表面以及近表面处于钢锭的柱状晶带,其 内部质量是比较好的,缺陷比较少。而且还可以在零件的
• 以下图中纵坐标改为纤维断口率
持久强度和蠕变强度
落锤试验
3.2 金相检验
• 金相检验有夹杂物检验,ASME规范材料的 夹杂物检验一般取消。现在均按照ISO国际 标准进行,夹杂物分为粗系和细系两类分 别有标准图谱进行对照比较确定。
• 组织的检验和晶粒度的测定 组织判定由高倍显微照片确定 晶粒度测定可以与标准图谱进行比较,也 有进行测量的。
试块就是长横孔,判断计算一定要经过公式计算,不能按
经验估计。
超声波检验的优缺点
• 超声波检验很灵敏,特别是对于裂纹,可 以用多种方法进行确认。试验方法和设备 也相对简单,但对于缺陷的定性有一定的 难度。细小夹杂物、晶粒粗大、疏松等缺 陷的草状波有时难以分辨。再加之超声波 检验人为因素太强,结果又不容易记录和 再现,因此经常引发争论。超声波检验对 于方向与入射声束方向呈平行的缺陷不容 易发现而造成漏检。
•
另外对于平底孔,6dB方法可以用来比较缺陷的大
小,增加6dB缺陷的当量面积就扩大到原来的2倍,当量
直径就增加到原来的根号2倍。这种评价方法绝对不能用
于其它场合。在以长横孔为基准时,以上所有内容均不正
确,6dB可以使缺陷的当量直径扩大达16倍。这些在缺陷
的计算和评价时应特别注意。焊缝的超声波检验所用对比
具体要求
• 模拟消除应力热处理的保温时间应该不小 于焊接后(包括补焊)消除应力热处理中 保温时间总量的80%。
第3讲 试验和检验
• 简单介绍一下与核电设备机械设备有关的 常用试验和检验。主要有:
• 力学性能试验 • 金相试验 • 宏观缺陷检验
3.1 机械性能
屈服强度
冲击试验
脆性转变温度 FATT50
3.3 宏观缺陷的检验手段
• 宏观缺陷检验一般采用无损检验的方法。 无损检验有表面检验和内部体积检验。表 面缺陷的发现和评定一般有目视检验、液 体渗透检验、磁粉检验和涡流检验。材料 内部缺陷的发现和评定主要有超声波检验, 涡流检验和射线照相检验等。现简单介绍 如下:
(1) 表面目视检验
• 表面目视检验是很重要但也很容易被忽视。表面 目视检验除专门的人员进行成品检验外,还包括 在整个加工过程中注意切削过程中金属断屑是否 正常,若金属切屑总在一个地方断,就应注意是 否有表面缺陷的存在。成品检验时应注意零件的 照明和检查时视线的角度等。仔细的目视检验应 该能够发现尺寸为0.5mm以上的表面缺陷。目视 检验中对于开口很小的裂纹容易漏检,而这类缺 陷又是绝对不允许存在的,因此,重要零件的表 面检验还应进行液体渗透检验或磁粉检验。