材料成形加工复习提纲.pptx
广工材料成形工艺基础复习提纲(机电专业及近机专业 )

材料成形工艺基础复习提纲(机电专业及近机专业)第一章1.铸造是一种将液态金属(一般为合金)浇入铸型型腔、冷却凝固后获得毛坯或零件(通称为铸件)的成形工艺。
2.铸造成形工艺的特点:①适合制造形状复杂、特别是内腔形状复杂的铸件;②铸件的大小几乎不受限制;③使用的材料范围广,凡能熔化成液态的金属材料几乎均可用于铸造。
3.铸造成形工艺的分类:①砂型铸造;砂型铸造适用于金属材料、大小、形状和批量不同的各种铸件,成本低廉。
②特种铸造;特种铸造是指砂型铸造以外的铸造工艺。
4.合金的铸造性能:主要包括合金的流动性、收缩性、吸气性以及成分偏析倾向性等性能。
5.液态合金填充铸型的过程简称为充型。
6、合金的流动性越好,充填铸型的能力就越强。
合金的流动性越差,铸件就越容易产生浇不到、冷隔等缺陷。
而且,流动性差也是引起铸件气孔、夹渣和缩孔缺陷的间接原因。
6.灰铸铁、硅黄铜的流动性较好,铸钢较差,铝合金居中。
7.不同化学成分的合金,因结晶特性、粘度不同,其流动性亦不同。
共晶成分合金的流动性最好。
8.浇注温度较高的金属液粘度较低,过热度较高,蓄热多,保持液态的时间较长,故流动性较好。
但浇注温度过高,会导致金属的收缩增大,吸气增多,氧化严重,使铸件产生缩孔、缩松、气孔和粘砂等缺陷。
9.增大浇注压力显然可改善金属的流动性,常采用增加直浇道高度的方法或采用压力铸造、离心铸造工艺来增大浇注压力,提高金属的流动性。
10.合金在浇注、凝固直到冷却到室温的过程中体积或尺寸缩减的现象,称为收缩。
11.合金的收缩过程有三个阶段:①液态收缩;②凝固收缩;③固态收缩。
合金的总收缩为上述三种收缩的和。
12.在常用铸造合金中,铸钢收缩率较大,而灰铸铁较小。
12.液态金属在铸型中的凝固过程中,由液态收缩和凝固收缩所引起的体积缩减如得不到金属液的补充,就会在铸件最后凝固的部分形成孔洞。
由此造成的集中孔洞称为缩孔,细小分散的孔洞称为缩松。
13.纯金属和共晶成分的合金易形成集中缩孔。
《材料成型与工艺》PPT课件

产品造型材料及工艺
第七章 涂装工艺
复习:金属涂装技术 在制品表面形成以有机物为主体的涂层,并干燥成膜的工艺,称为涂装技术,简称为
涂装。涂装所用的材料是各种涂料。涂装工艺一般包括制件表面涂装前处理、涂敷涂料及 涂层干燥三大步骤。 涂装的目的有三方面:
①保护作用。防止制品表面受腐蚀、被划伤、脏污,提高制品的耐久性。 ②装饰作用。将制品表面装饰成涂层所具有的色彩、光泽和肌理,使制品外观在视觉 感受上成为美观悦目的制品。 ③特殊作用。使制品具有隔热、绝缘、耐水、耐辐射、阻尼、杀菌、吸收雷达波、 隔音、导电等特殊功能。特别是通过涂装与其它表面处理技术相更加的多重处理,可获得 能适应相当苛刻条件和使用环境的防护装饰涂层。
效
围
强单
果
广
好
7.3.2 涂料的性质与装饰效果
1.色彩
2.光泽 3.粘度 4. 附着性
第七章 涂装工艺
@ 2008 Fujian University of Technology. Department of Machine electrical. Industrial design specialty.
2.通用醇酸树脂漆
常用于不能进行烘干作业的 大型机床、农机、工程机械、
大型车辆等机械产品的涂装
3.底漆和防锈漆
醇酸树脂特点之一是对铁及 一些有色金属、木材等表面 有良好的附着力。因此,它 们被广泛用于各种设备的底
漆
7.2.3 氨基树脂涂料
①清漆色浅、不易泛黄
②漆膜坚硬、附着性好、机械强度高、耐 候性、装饰性好
@ 2008 Fujian University of Technology. Department of Machine electrical. Industrial design specialty.
材料成形复习提纲
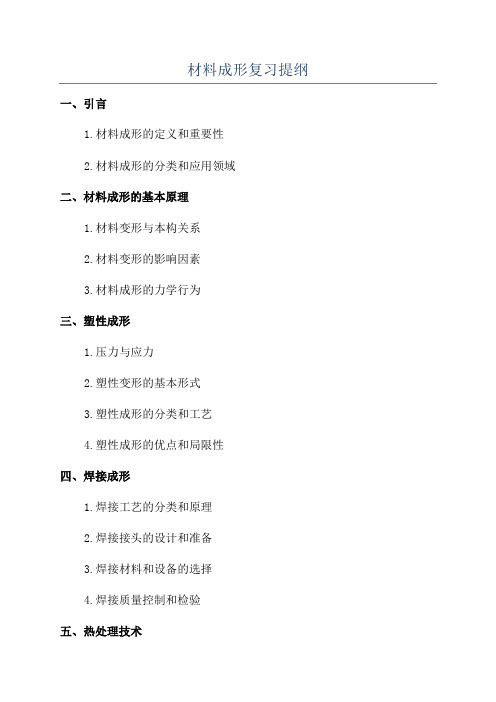
材料成形复习提纲
一、引言
1.材料成形的定义和重要性
2.材料成形的分类和应用领域
二、材料成形的基本原理
1.材料变形与本构关系
2.材料变形的影响因素
3.材料成形的力学行为
三、塑性成形
1.压力与应力
2.塑性变形的基本形式
3.塑性成形的分类和工艺
4.塑性成形的优点和局限性
四、焊接成形
1.焊接工艺的分类和原理
2.焊接接头的设计和准备
3.焊接材料和设备的选择
4.焊接质量控制和检验
五、热处理技术
1.热处理的目的和作用
2.热处理的分类和工艺
3.热处理对材料性能的影响
4.热处理过程控制和参数选择
六、表面处理技术
1.表面处理的目的和作用
2.表面处理的分类和工艺
3.表面处理对材料性能的影响
4.表面处理过程控制和参数选择
七、材料成形的质量控制与检验
1.质量控制的重要性和原则
2.常用的成形质量检验方法
3.质量缺陷的分析和处理
八、新型材料成形技术
1.新型材料与成形技术的关系
2.新型材料成形技术的研究进展
3.新型材料成形技术的应用前景
九、结语
1.材料成形的发展趋势和挑战
2.对材料成形的思考和展望。
材料成型复习提纲(完整版)
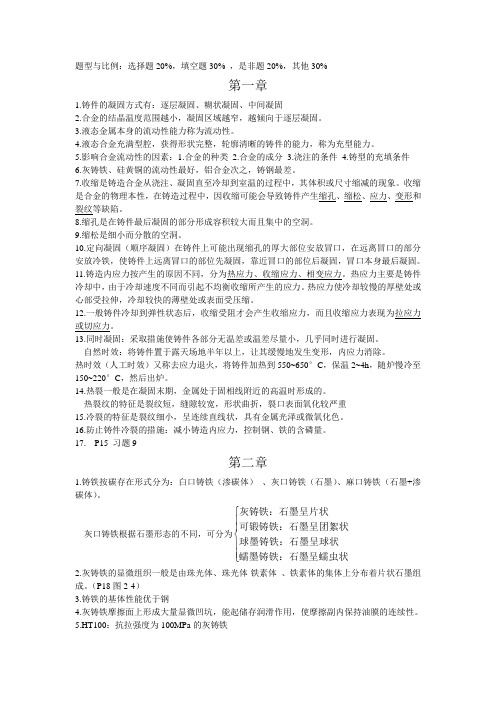
题型与比例:选择题20%,填空题30% ,是非题20%,其他30%第一章1.铸件的凝固方式有:逐层凝固、糊状凝固、中间凝固2.合金的结晶温度范围越小,凝固区域越窄,越倾向于逐层凝固。
3.液态金属本身的流动性能力称为流动性。
4.液态合金充满型腔,获得形状完整,轮廓清晰的铸件的能力,称为充型能力。
5.影响合金流动性的因素:1.合金的种类2.合金的成分3.浇注的条件4.铸型的充填条件6.灰铸铁、硅黄铜的流动性最好,铝合金次之,铸钢最差。
7.收缩是铸造合金从浇注、凝固直至冷却到室温的过程中,其体积或尺寸缩减的现象。
收缩是合金的物理本性,在铸造过程中,因收缩可能会导致铸件产生缩孔、缩松、应力、变形和裂纹等缺陷。
8.缩孔是在铸件最后凝固的部分形成容积较大而且集中的空洞。
9.缩松是细小而分散的空洞。
10.定向凝固(顺序凝固)在铸件上可能出现缩孔的厚大部位安放冒口,在远离冒口的部分安放冷铁,使铸件上远离冒口的部位先凝固,靠近冒口的部位后凝固,冒口本身最后凝固。
11.铸造内应力按产生的原因不同,分为热应力、收缩应力、相变应力。
热应力主要是铸件冷却中,由于冷却速度不同而引起不均衡收缩所产生的应力。
热应力使冷却较慢的厚壁处或心部受拉伸,冷却较快的薄壁处或表面受压缩。
12.一般铸件冷却到弹性状态后,收缩受阻才会产生收缩应力,而且收缩应力表现为拉应力或切应力。
13.同时凝固:采取措施使铸件各部分无温差或温差尽量小,几乎同时进行凝固。
自然时效:将铸件置于露天场地半年以上,让其缓慢地发生变形,内应力消除。
热时效(人工时效)又称去应力退火,将铸件加热到550~650°C,保温2~4h,随炉慢冷至150~220°C,然后出炉。
14.热裂一般是在凝固末期,金属处于固相线附近的高温时形成的。
热裂纹的特征是裂纹短,缝隙较宽,形状曲折,裂口表面氧化较严重15.冷裂的特征是裂纹细小,呈连续直线状,具有金属光泽或微氧化色。
金属材料成型基础资料.pptx

电阻热:Q=I2Rt
焊条
-
焊接电弧
工件
d
+
d离
焊接电弧的稳定燃烧 — 就是带电粒子产生、 运动、复合、产生的动态平衡过程。
第5页/共60页
2 . 电弧的构造及热量分布 阴极区:2400k 36% 阳极区:2600k 42% 弧柱区:5000~8000k 21%
3 . 电弧的极性
1 . 设备简单、应用灵活方便。
2 . 劳动条件差、生产率低、质量不稳定。
二、手工电弧焊焊接过程
①引弧 ② 形成熔池
三、焊接电弧
③形成焊缝
1 . 焊接电弧的概念
第4页/共60页
在焊条末端和工件两极之间的气体介 质中,产生强烈而持久的放电现象。
使气体电离 具备两个条件
阴极发射电子
接触电阻:R 短路电流:I
适用于易氧化的有色金属及合金钢材料的焊接。 如:铝、镁、钛及其合金和耐热钢、不锈钢等。
第29页/共60页
三、 CO2气体保护焊
以CO2气体作为保护性介质的电弧焊方法。
焊接热源:电弧热
保护介质:CO2
① 与金属发生化学反应—产生夹渣缺陷
CO2 ② 溶解于液体金属中—产生 CO 气孔缺陷
③ 比重大于空气(25%)
第26页/共60页
非熔化极亚弧焊
熔化极亚弧焊
第27页/共60页
第28页/共60页
3)氩弧焊的特点及应用 ① 机械保护效果好,焊缝金属纯净,焊缝成形美观,
焊接质量优良。 ② 电弧燃烧稳定,飞溅小。 ③ 焊接热影响区和变形小。 ④ 可进行全位置焊接。 ⑤ 氩气昂贵,设备造价高。
应用: 适用所有金属材料的焊接。
镍及镍合金焊条—Ni ; 铜及铜合金焊条—T;
材料成型加工复习资料
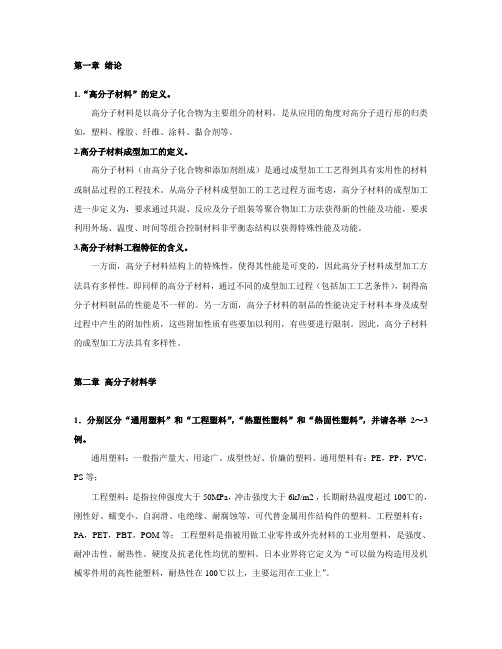
第一章绪论1.“高分子材料”的定义。
高分子材料是以高分子化合物为主要组分的材料,是从应用的角度对高分子进行形的归类如,塑料、橡胶、纤维、涂料、黏合剂等。
2.高分子材料成型加工的定义。
高分子材料(由高分子化合物和添加剂组成)是通过成型加工工艺得到具有实用性的材料或制品过程的工程技术。
从高分子材料成型加工的工艺过程方面考虑,高分子材料的成型加工进一步定义为,要求通过共混、反应及分子组装等聚合物加工方法获得新的性能及功能,要求利用外场、温度、时间等组合控制材料非平衡态结构以获得特殊性能及功能。
3.高分子材料工程特征的含义。
一方面,高分子材料结构上的特殊性,使得其性能是可变的,因此高分子材料成型加工方法具有多样性。
即同样的高分子材料,通过不同的成型加工过程(包括加工工艺条件),制得高分子材料制品的性能是不一样的。
另一方面,高分子材料的制品的性能决定于材料本身及成型过程中产生的附加性质,这些附加性质有些要加以利用,有些要进行限制。
因此,高分子材料的成型加工方法具有多样性。
第二章高分子材料学1.分别区分“通用塑料”和“工程塑料”,“热塑性塑料”和“热固性塑料”,并请各举2~3例。
通用塑料:一般指产量大、用途广、成型性好、价廉的塑料。
通用塑料有:PE,PP,PVC,PS等;工程塑料:是指拉伸强度大于50MPa,冲击强度大于6kJ/m2 ,长期耐热温度超过100℃的,刚性好、蠕变小、自润滑、电绝缘、耐腐蚀等,可代替金属用作结构件的塑料。
工程塑料有:PA,PET,PBT,POM等;工程塑料是指被用做工业零件或外壳材料的工业用塑料,是强度、耐冲击性、耐热性、硬度及抗老化性均优的塑料。
日本业界将它定义为“可以做为构造用及机械零件用的高性能塑料,耐热性在100℃以上,主要运用在工业上”。
热塑性塑料:加热时变软以至流动,冷却变硬,这种过程是可逆的,可以反复进行。
聚乙烯、聚丙烯、聚氯乙烯、聚苯乙烯、聚甲醛、聚砜、聚苯醚,氯化聚醚等都是热塑性塑料。
高分子材料成型加工基础复习提纲 高分子材料成型加工基础复习

高分子材料成型加工基础复习提纲绪论及第一章:混合与混炼1、聚合物加工:高聚物的成型加工,通常是在一定的温度下使弹性固体、固体粉状或粒状、糊状或溶液状态的高分子化合物变性或熔融,经过模具或口型流道的压塑,形成所需的形状,在形状形成的过程中有的材料会发生化学变化(如交联,最终得到能保持所取得形状的制品的工艺过程。
P52、聚合物的加工工艺过程一般可以分为混炼、成型、后加工等三大部分。
P53、混合混炼的目的:为获得综合性能优异的聚合物材料,除继续研制合成新型聚合物外,通过混合、混炼方法对聚合物的共混改性已成为发展聚合物材料的一种卓有成效的途径。
P74、共混的方法:a 机械共混法 b 液体共混法 c 共聚—共混法 d 互穿网络聚合物IPN 制备技术P75、共聚物的均匀性是指被分散的物在共混体中浓度分布的均一性,或者说分散相浓度分布的变化大小。
6、共聚物的分散程度是指被分散的物质(如橡胶中掺混部分塑料)破碎程度如何,或者说分散相在共混体中的破碎程度。
P117、常见的共混体系有:a固体 / 固体混合、b液体 / 液体混合、c固体 / 液体混合。
P208、混炼三要素及其作用:a压缩;物料在承受剪切前先经受压缩,使物料的密度增加,这样剪切时,剪切力作用大,可提高剪切效率,同时当物料被压缩时,物料内部会发生流动,产生由于压缩引起的流动剪切 b剪切剪切的作用是把高粘度分散相的粒子或凝聚体分散于其它的分散介质中 c分配置换分布由置换来完成。
P229、混合与混炼设备根据操作方式分为间歇式和连续式两大类。
P2510、常见初混合设备概念及类型:初混合设备是指物料在非熔融状态下(粉料、粒料、液体添加剂)进行混合所用的设备。
常用的典型初混合设备有 a 转鼓式混合机 b 螺带混合机 c Z 型捏合机 d 高速混合机p25-2811、混炼和塑化的概念及它们的区别:将各种配合剂混入并均匀分散在橡胶中的过程叫混炼;将各种配合剂混入并均匀分散在塑料熔体中的过程叫塑化。
ok 高分子材料成型加工原理 复习课提纲

高分子材料成型加工原理复习课提纲1 在工业上获得成功应用的“高分子材料”在概念上要具有哪些方面的特点或要求?有一定的力学性能兼或同时具有一定的功能特性具有一定的可加工性市场价值经济价值环保、节能、安全特征社会价值。
要求:可满足生产或生活中的某种需要,并能够参与社会经济发展的循环过程3 如何理解“流动”?流动:运动单元在外力场作用下运动并损耗能量聚合物流体的流动现象:聚合物流体某尺寸水平上的运动单元在外力场作用下产生相对运动而损失能量的现象。
5为满足成型和加工的需要,通常如何获得或调控某些特定的高分子材料的流动性?调整温度压力等外部工艺条件,影响包括范氏力,氢键,分子间配合键等等对分子结构进行改性,如纤维素,或将化学结构与工艺条件相结合,如针对一些天然高分子材料优选,引入低分子增塑剂和超临界流体等介质,如对淀粉,PVC改性等6 聚合物材料的可加工性通常包含哪些方面?可挤压性,可模塑性,可延展性,可纺性7 熔融指数?熔融指数在实际的成型加工过程中有什么样的应用?其局限性?熔融指数定义为:在一定的温度和压力下,10min内从特定毛细管中流出的聚合物熔体的克数,单位为g/10min。
熔体流动速率可表征热塑性塑料在熔融状态下的粘流特性,对保证热塑性塑料及其制品的质量,对调整生产工艺,都有重要的指导意义。
但该方法也有局限性,不同品种的高聚物之间不能用其熔融指数值比较其测定结果,不能直接用于实际加工过程中的高切变速率下的计算,只能作为参考数据。
此种仪器测得的流动性能指标,是在低剪切速率下测得的,不存在广泛的应力应变速率关系,因而不能用来研究熔体粘度和温度、粘度与剪切速率的依赖关系,仅能比较相同结构聚合物分子量或熔体粘度的相对数值。
11什么是静态流变学?什么是动态流变学?各侧重于哪些应用?.静态流变学:又称稳态流变学,研究单一方向稳态剪切作用下聚合物流体的流动和形变动态流变学:研究周期动态作用下聚合物流体的流动和形变。
材料成形复提纲

材料成形技术基础复习提纲第一章绪论第二章液态材料铸造成形技术过程Ⅰ.复习提纲一、名词解释•1、缩孔、缩松•铸件在冷却和凝固过程中,由于合金的液态收缩和凝固收缩,往往在铸件最后凝固的地方出现孔洞。
容积大而比较集中的孔洞称为缩孔;细小而分散的孔洞称为缩松•2、顺序凝固和同时凝固•顺序凝固:采用各种措施保证在铸件上远离冒口或浇道的部分到冒口或浇道件之间建立一个递增的温度梯度,按照远离冒口的部分最先凝固,然后是靠近冒口部分,最后才是冒口本身凝固的次序进行。
•同时凝固:采取工艺措施保证铸件各没有温差或温差很小,使各部分同时凝固。
•3、宏观偏析、微观偏析•微观偏析:微小(晶粒)尺寸范围内各部分的化学成分不均匀现象。
•宏观偏析:较大尺寸范围内化学成分不均匀的现象。
•4、流动性、充型能力•充型能力:液态合金充满铸型型腔,获得形状完整,轮廓清晰铸件的能力。
衡量充型能力可用所能形成的铸件最小壁厚•流动性:液态铸造合金本身的流动能力,衡量流动性一般采用螺旋试样长度•5、自由收缩、受阻收缩•铸件在铸型中的收缩仅受到金属表面与助兴表面之间的摩擦阻力时,为自由收缩•如果铸件在铸型中的收缩还受到其他阻碍,则为受阻收缩。
二、填空•1、现代制造过程分类一般分为质量不变过程,质量减少过程,质量增加过程。
•2、一般用最小壁厚来表征液态金属的充型能力,用螺旋线试样长度来表征液态金属的流动性。
•3、影响液态金属充型能力的因素有金属的流动性、铸型性质、浇注条件、铸件结构四个方面。
•4、影响铸造合金收缩的因素有缩松、缩孔、铸造应力、铸件的变形和裂纹。
•5、铸造缩孔形成的基本条件是金属在恒温或者很窄的温度范围内结晶,铸件由表及里逐层凝固,缩松形成的基本条件是金属的结晶温度范围较宽,呈体积凝固方式。
•6、铸件实际收缩过程中受到的阻力分为铸型表面的摩擦力、热阻力、机械阻力三种。
•7、铸造应力按形成原因不同分为热应力,相变应力,机械阻碍应力三种应力。
材料成型复习(2)
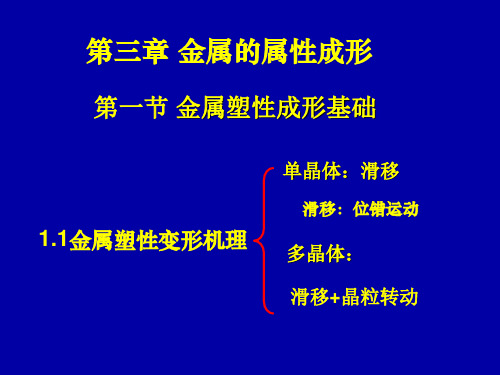
1. 冲裁工艺设计 2. 弯曲工艺设计 3. 拉深工艺设计 4. 冲压工序选择 5. 冲压模具选择及区别 6. 零件结构的冲压工艺性
第四章 连接成形
第一节 焊接理论基础
熔焊液相冶金
1.1熔焊冶金过程 熔池结晶
焊接接头的组织 转变
1.2焊接应力与变形
产生原 因 焊接残余应力的调节
焊接残余应力的消除方 法
考试题型举例-问答题
1、铸铁中石墨存在形式有哪几种?试对 影响铸铁石墨化的因素进行分析。
2.3 轧制
纵轧 斜轧 横轧
2.4 挤压
第三节 金属塑性成形工艺设计
1.绘制锻件图
3.1 自由锻工艺设计
2. 确定变形工序 3. 计算毛坯重量尺寸
4. 零件结构的自由锻 工艺性
3.2 模锻工艺设计
敷料即余块 1.绘制模锻件图 2. 确定模锻工步 3. 修整及热处理 4. 零件结构的模锻工艺性
3.3 冲压工艺设计
3.2 常用金属 材料的焊接
碳钢的焊接 低合金结构钢的焊接 不绣钢的焊接 耐热钢的焊接 铸铁的焊接 非铁金属的焊接
第四节 焊接结构设计和工艺设计简介
结构材料的选择
4 焊接结构设计
焊缝布置
焊接方法选择
焊接接头设计
作为期末复习提纲,具体内容围绕书本或课 件进行。
考试题型举例-填空题
1、下列材料中,焊接性最好的是( )。 A. HT200 B. 65 C. T10A D. 30
第三章 金属的属性成形
第一节 金属塑性成形基础
1.1金属塑性变形机理
单晶体:滑移
滑移:位错运动
多晶体: 滑移+晶粒转动
第二节 金属塑性成形方法
2.1 锻造
材料成型复习课件
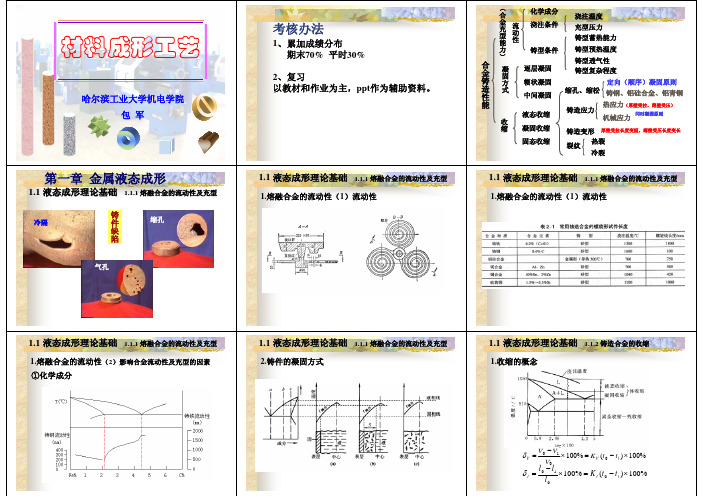
1.1.2 铸造合金的收缩
1.1 液态成形理论基础
1.1.2 铸造合金的收缩
1.1 液态成形理论基础
1.1.2 铸造合金的收缩
缩孔及缩松的形成
缩孔及缩松的形成
缩孔、缩松与相图及合金成分关系
1.1 液态成形理论基础
1.1.2 铸造合金的收缩
1.1 液态成形理论基础
1.1.2 铸造合金的收缩
1.1 液态成形理论基础
3.工艺参数的确定 (2)起模斜度
1.3 液态成形件工艺及结构设计 1.3.1 砂型铸造工艺设计
3.工艺参数的确定 (3)收缩率
生产批量 大量生产 成批生产 单件、小批量生 产
最小铸出孔的直径d 灰铸铁件 12~15 15~30 30~50 铸钢件 — 30~50 50 影响因素:侧壁高度;造型方法;模型材料; 影响因素 外壁斜度0.5°~3 °,内壁3 °~10 °; 零件有结构斜度、无起模困难的模样,可不加起模斜度。 铸造收缩率灰铸铁为0.7%~1.0%, 铸造碳钢为1.3%~2.0%, 铸造锡青铜为1.2%~1.4%
机 器 造 型
震击紧实 压实紧实 射砂紧实 气流紧实 气冲紧实
芯盒 制芯 造型 模样
芯砂 熔化金属
} 合型
浇注
型砂
1.2 液态成形工艺
熔模铸造
1.2.2 特 种 铸 造
1.2 液态成形工艺
熔模铸造 蜡模制造 压型 蜡模压制 蜡模组装 结壳 浸涂料 撒砂 化学硬化 硬化 工艺过程 脱蜡
1.2.2 特 种 铸 造
1.1 液态成形理论基础
4.铸件变形
1.1.2 铸造合金的收缩
1.1 液态成形理论基础
4.铸件变形
1.1.2 铸造合金的收缩
材料成型PPT课件
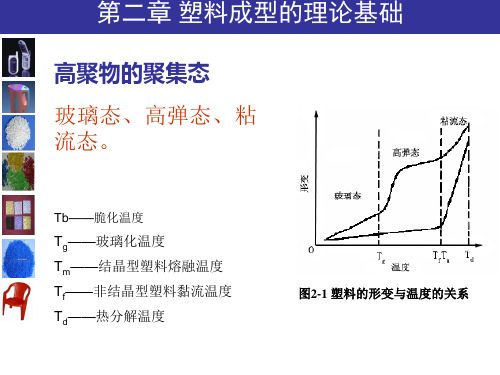
22.3.2聚聚合合物物在的模流内变的行流为动
入口效应、离模膨胀
Unstable flow
挤出胀大现象
B
A
C
胀大比 die
B D max D0
在工程实践中考虑入口效应的目的有两个:
➢1 保证制品的成型质量,在必要时避免或减 小入口效应。
➢2 在确定注射压力时,在考虑所有流道(包 括浇口)总长引起的压力损耗的同时,还要 考虑入口效应引起的压力损失
•鲨鱼皮形 •波浪形 •竹节形 •螺旋形 •不规则破裂
2.3 聚合物的加热与冷却
• 热源:
– 外热:电阻丝(经济、简单、方便、温度波动 较大);微波(适合较厚发泡成型);红外线;
热油(温度控制精确,设备复杂,成本高); 热水、蒸气。
– 内热:摩擦热
Q
1 J
a
2
• 冷却:水(注射模、挤出定型模、中空模
低分子多为此类
宾汉 流体
假塑 性流 体
膨胀
(τy 和η为常数)
n<1
凝胶糊、良溶 在剪切力增大到一 剂的浓溶液 定值后才能流动。
大多数聚合物 剪切增加,粘度下
熔体、溶液、 降。原因为分子
糊
“解缠”
2.2 聚合物的流变行为
拉伸粘度
如果引起聚合物熔体的流动不是剪切应力
而是拉伸应力时,仿照式(2—2)即有拉
聚合物的结晶
有结晶倾向
两类聚合物
无结晶倾向
结晶过程是聚合物由非晶态转变为晶态的过程,发生 在Tg和Tm温度之间。
结晶度:聚合物是不可能完全结晶的,仅有 有限的结晶度,而且结晶度依聚合物结晶的历史 不同而不同。
材料成型工艺基础复习提纲
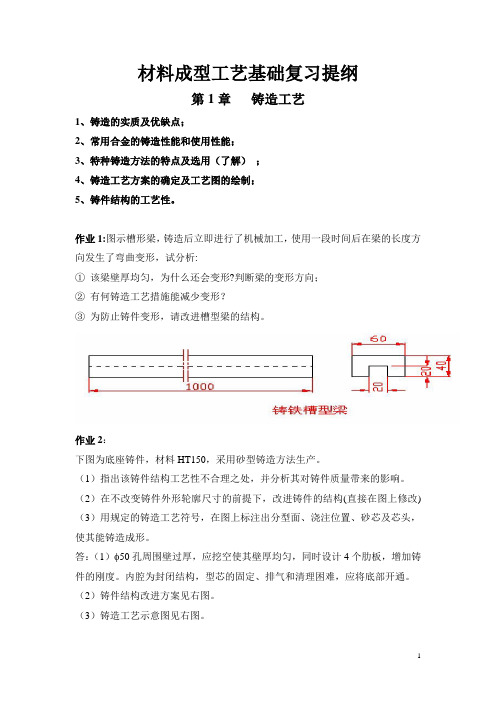
材料成型工艺基础复习提纲第1章铸造工艺1、铸造的实质及优缺点;2、常用合金的铸造性能和使用性能;3、特种铸造方法的特点及选用(了解);4、铸造工艺方案的确定及工艺图的绘制;5、铸件结构的工艺性。
作业1:图示槽形梁,铸造后立即进行了机械加工,使用一段时间后在梁的长度方向发生了弯曲变形,试分析:①该梁壁厚均匀,为什么还会变形?判断梁的变形方向;②有何铸造工艺措施能减少变形?③为防止铸件变形,请改进槽型梁的结构。
作业2:下图为底座铸件,材料HT150,采用砂型铸造方法生产。
(1)指出该铸件结构工艺性不合理之处,并分析其对铸件质量带来的影响。
(2)在不改变铸件外形轮廓尺寸的前提下,改进铸件的结构(直接在图上修改) (3)用规定的铸造工艺符号,在图上标注出分型面、浇注位置、砂芯及芯头,使其能铸造成形。
答:(1) 50孔周围壁过厚,应挖空使其壁厚均匀,同时设计4个肋板,增加铸件的刚度。
内腔为封闭结构,型芯的固定、排气和清理困难,应将底部开通。
(2)铸件结构改进方案见右图。
(3)铸造工艺示意图见右图。
修改后:作业3:确定图4-27所示铸件的铸造工艺方案,要求如下:(1)按单件、小批生产和大量生产两种条件分析最佳方案;(2)按所选方案绘制铸造工艺图(包括浇注位置、分型面、分模面、型芯及芯头)。
第2章锻压工艺1、锻造的实质及优缺点;2、各种模锻方法的特点、模锻工步的选择、锻件图的绘制;3、冲压工艺方案的确定、拉深系数的计算。
4、其它塑性成形方法的特点及选用(了解);图示零件采用锤上模锻方法制坯,结构上有哪些不合理的地方?拟定模锻工步,定性地绘出锻件图。
作业:用低碳钢板大批量生产右图所示冲压件,(1)试拟订其生产基本工序,并画出工序简图;(2)生产冲孔模具时,应先制造凹模还是凸模? 为什么?(3)若模具间隙过大,对冲压件切断面的质量有何影响?答: (1)该冲压件的生产基本工序为: 1.落料-冲孔 2.弯曲 3.冲两侧孔(2)生产冲孔模具时,应先制造凸模。
(2020年整理)材料成形加工复习提纲.pptx

保压压力越高,保压时间越长,则凝封压力越高,脱模时(实际脱模温度一般比模温略高)模腔残余应力越高,因而制品内应力 越大且脱模越困难
制品脱模和抽芯的最佳条件:成形物温度下降到玻璃化温度 (或热变形温度)以下且模腔压力下降到与大气压平衡(即模腔 残余压力=0)
制品冷却过程中模腔残余压力为零若出现在冷却初期,制品表面将出现凹陷 若零压力在冷却过程中期出现,则内部未凝熔体凝固时会在足够厚的外壳拉应力作用下而产生缩孔或裂纹 只有残余应力为零出现在冷却过程后期时,制品内外都已凝固才不致发生缺陷
与螺杆挤出机内熔融塑化过程类似(主要不同点是:螺杆挤出机的熔融塑化过程是稳态连续过程,而移动螺杆式注射机的熔融是 非稳态间歇式过程) 为提高塑化速率和塑化质量,柱塞式注射机机筒前端通常都设置分流梭,柱塞式注射机必须采用分流梭,移动螺杆式塑化效果好,不 采用分流梭
•锁模力:比注射压力(40~200MPa)小,但应大于模腔内实际压力
料性能和模具结构而定,如果采用热流道模具一般不退回。 1.充模方式
熔体充模两种极端方式:扩展流和喷射流 扩展流:模腔内空气能顺利排出,所得制品质量(包括强度和外观等)较好
学海无涯 ➢ 过低速度会延长充模时间,同时熔体过度冷却可能引起充模不全,出现熔接痕甚至出现分层,影响制品强度 喷射流:模内原有空气和被湍流熔体卷入的空气无法排出,而且被压缩形成高温高压气体而引起熔体局部烧伤及分解,同时易
热塑性塑料可以采用压延成形,压延产品可以是薄膜、片材、人造革和各种涂层制品等。压延机按辊筒数目分为双辊、三辊、四 辊、五辊甚至六辊。压延机以三辊和四辊最多,橡胶一般使用三辊压延机,塑料压延多使用四辊压延机。辊筒的排列方式有三角型、 直线型、逆 L 型、斜 Z 型、L 型、正 Z 型等,目前应用最普遍的是斜 Z 型和逆L 型。
- 1、下载文档前请自行甄别文档内容的完整性,平台不提供额外的编辑、内容补充、找答案等附加服务。
- 2、"仅部分预览"的文档,不可在线预览部分如存在完整性等问题,可反馈申请退款(可完整预览的文档不适用该条件!)。
- 3、如文档侵犯您的权益,请联系客服反馈,我们会尽快为您处理(人工客服工作时间:9:00-18:30)。
与螺杆挤出机内熔融塑化过程类似(主要不同点是:螺杆挤出机的熔融塑化过程是稳态连续过程,而移动螺杆式注射机的熔融是 非稳态间歇式过程) 为提高塑化速率和塑化质量,柱塞式注射机机筒前端通常都设置分流梭,柱塞式注射机必须采用分流梭,移动螺杆式塑化效果好,不 采用分流梭
•锁模力:比注射压力(40~200MPa)小,但应大于模腔内实际压力
单螺杆挤出机一般由加料系统、挤出系统、加热冷却系统、传动系统和控制系统等部分构成。挤出系统是单螺杆挤出机的主体, 包括机筒、螺杆、机头和口模等,而螺杆是最核心部件。螺杆的几何结构参数有螺杆直径、长径比、压缩比、螺距、螺槽深度、螺旋 角、螺杆与机筒间间隙、螺头形状等。除三段式普通螺杆外,还有分离型螺杆、屏障型螺杆、分流型螺杆、分配混合型螺杆、排气型 螺杆等多种高效型螺杆。
分等因素影响高分子成形的降解难易和降解程度。 热固性高分子成形必然涉及交联,而有时热塑性高分子成形时会有意引入适当的交联。逐步交联反应有加成聚合交联反应和缩
合 聚合交联反应两种类型。
第五章 挤出成形 挤出成形生产线的核心设备是挤出机。挤出机主要有螺杆挤出机和柱塞式挤出机两大类,挤出成形普遍使用的挤出机是螺杆挤出 机。
高弹形变的危害。高弹态成形时,可以采用较大的外力和/或较长的作用时间获得成形所需要的不可逆形变。 高分子成形的固化方式有冷却固化、传质固化和反应固化三种。不稳定温度场和不稳定传热是冷却固化过程的重要特征。 高分子成形的取向。根据驱动力情况,高分子成形的取向通常有剪切流动取向和拉伸流动取向两种类型。按取向的方式,取向可
分为单轴取向和双轴取向(或称平面取向)两种。高分子和填料在剪切流动过程均可以发生取向。 拉伸流动取向有粘流拉伸和塑性拉伸两种,塑性拉伸流动时发生的取向包括链段程度高。温差诱导取向是拉伸流动取向的特殊情况。 按降解过程化学反应的特征,高分子的降解有自由基链式降解和逐步降解两种机理。高分子结构、成形温度、成形应力、氧、水
学 海 无涯
按照用途,高分子材料分为塑料、化学纤维、橡胶、胶黏剂和涂料五类。 高分子材料的成形有黏流态成形、塑性成形和玻璃态成形三种形式。 高分子材料的可成形性包括可挤出性、可纺性、可模塑性和可延性。 可纺性是作为成纤聚合物的必要条件。胀大型是正常的纺丝细流类型,液滴型、漫流型和破裂型是纺丝过程必须避免出现的挤出 细流情形。 实际纺丝生产中通常采用最大稳定纺丝速度或断头次数来判定聚合物的可纺性。 可延性取决于聚合物自身性质和塑性形变条件。 线型聚合物是典型黏弹性材料,总形变由普弹形变、高弹形变和粘性形变三部分所组成。成形形式和条件不同,可逆形变和不可 逆形变两种成分相对比例不同。粘流态(或熔融态)成形易于获得较大的形状改变,成形制品的使用因次稳定性好,但是应充分重 视
料性能和模具结构而定,如果采用热流道模具一般不退回。 1.充模方式
2
学海无涯 熔体充模两种极端方式:扩展流和喷射流 扩展流:模腔内空气能顺利排出,所得制品质量(包括强度和外观等)较好 ➢ 过低速度会延长充模时间,同时熔体过度冷却可能引起充模不全,出现熔接痕甚至出现分层,影响制品强度 喷射流:模内原有空气和被湍流熔体卷入的空气无法排出,而且被压缩形成高温高压气体而引起熔体局部烧伤及分解,同时易
出现熔体破裂等缺陷,因而制品质量不均匀,内应力较大,表面常有裂纹 扩展流充模方式是最理想的充模方式,而喷射流充模方式应极力避免 保压压力越高,保压时间越长,凝封时模腔压力越高,模腔内成形物平均温度越低,所得制品的密实度越高
保压压力越高,保压时间越长,则凝封压力越高,脱模时(实际脱模温度一般比模温略高)模腔残余应力越高,因而制品内应力 越大且脱模越困难
•喷嘴温度通常略低于机筒温度:因为喷嘴处产生较大摩擦热使物料出现较大温升,如果喷嘴温度过高则在直通式喷嘴处会发生
“流涎现象”
•注射成形周期:完成一次注射成形所需的全部时间,包括注射时间、保压时间、冷却时间及其它辅助时间(如开模、脱模、嵌件
安放、闭模等),注射成形周期中不另含加料塑化时间
•热固性塑料注射成形,热固性树脂充模结束后不必保压补料
学海无涯
法主要用于生产高强度的薄膜。平膜法双向拉伸工艺有平膜逐次双向拉伸和平膜纵横同步双向拉伸两种拉伸实施方法,其中平膜逐次 双向拉伸工艺应用最广。平膜逐次双向拉伸方法有先纵拉后横拉和先横拉后纵拉两种方式,生产上用得最多的是先纵拉后横拉方式 。 先纵拉后横拉方式的平膜法逐次双向拉伸薄膜成形工艺过程包括厚片急冷、纵向拉伸、横向拉伸、热定形、冷却、切边和卷取。 管膜 双向拉伸薄膜的生产工艺按照薄膜引出的走向可以分为上吹法、平吹法和下吹法,成形工艺流程包括管坯挤出、吹胀与牵引、 冷却和 卷绕。
(2)湿法纺丝原理 湿纺纺程上存在径向应力分布,导致湿纺凝固丝往往存在皮芯层结构,皮层取向度比芯层高。传质扩散过程是湿法纺丝时实现固 化的原因。溶剂和沉淀剂两者之间的相对扩散速率是相分离的驱动力。溶剂和沉淀剂的扩散系数受到凝固浴浓度、种类和温度等许多 因素的影响。相分离是湿法纺丝的成形机理。湿纺初生纤维的取向度一般很低,基本没有结晶或者存在少量结晶或准晶序态。
第十一章 聚酯纤维熔纺成形 1.聚酯原料及纤维 涤纶、锦纶和丙纶产品都采用熔体纺丝方法成形。聚酯纤维通常是指聚对苯二甲酸乙二酯纤维,商品名为涤纶。PET 生产有酯交 换法和直接酯化法两条路线。纤维用 PET 树脂的分子量通常为 15000~22000。纯 PET 的熔点为 267℃。聚酯纤维为部分结晶纤维,具有 优异的综合性能。聚酯纤维的改性方法分为化学改性和物理改性两类。 聚酯预取向丝(POY)是在纺速 3000~4000m/min 条件下获得的卷绕丝,具有高取向、低结晶的结构特点。影响 POY 结构和性能的 工艺参数有纺丝条件、冷却吹风条件、卷绕速度、上油集束位置、纺丝机上有无导丝盘等。POY 纺丝常采用高压纺丝或中压纺丝,对 切片的特性粘数和含水率要求较严格。POY 的纺速应尽量选择在防止发生取向诱导结晶作用的范围内。 聚酯全拉伸丝(FDY)生产工艺是在 POY 高速纺丝过程中引入有效拉伸,卷绕速度达到 5000m·min-1 以上。FDY 生产工艺是纺丝-
聚合物物料在螺杆挤出机中的挤出过程,可分为固体输送区、熔融区和熔体输送区三个区域。熔体在螺杆均化段的实际流动是正 流、逆流、环流和漏流四种流动的组合流动,在螺槽内熔体呈螺旋形流动轨迹沿螺槽逐渐流向机头方向。螺杆挤出机稳定挤出的条件 是固体输送速率≥熔化速率≥熔体输送速率。
根据螺杆特性曲线和口模特性曲线,可确定螺杆挤出机配合特定口模的工作点,即挤出生产率和机头压力。螺杆挤出机生产率受 1
热塑性塑料的注射过程包括加料、塑化、注射充模、冷却固化和脱模等几个主要步骤。塑化、注射充模和冷却固化是决定成形周 期和制品质量的关键过程。移动螺杆式注射机对物料的塑化能力和塑化质量都比柱塞式注射机好。注射充模过程可分为引料入模、 流 动充模和压实与增密三个阶段。冷却固化可分为保压、熔体倒流与模腔凝封、浇口凝封后的继冷期三个阶段。
4
学海无 涯
拉伸-卷绕一步法连续工艺。 聚酯全取向丝(FOY)生产工艺是采用 6000m/min 以上的超高纺速以获得具有高度取向结构的长丝的纺丝工艺。FOY 具有微原纤结
•注射机工作过程:合模及锁紧、注射装置前移、注射、保压、制品冷却及预塑化、注射装置后退和开模顶出制品
(1)合模及锁紧
•合模时模具首先以低压力快速闭合,动定模快要接触时低压低速以免模具强力碰撞或模具内嵌件松动,合模后高压锁紧模具 •注射装置退回:避免使喷嘴与冷模长时间接触导致喷嘴处温度过低以致喷嘴处熔体凝固而无法进行下一次注射;是否退回根据物
塑料塑性成形主要有热成形、中空吹塑成形和双向拉伸薄膜成形等。 按型坯制造方法的不同,中空吹塑工艺可分为挤出-吹塑法和注射-吹塑法两种。中空吹塑的重要工艺因素有型坯温度、吹塑模 具温度、充气压力与充气速率、吹胀比和冷却时间等。
拉伸薄膜成形有单轴拉伸和双轴拉伸两种方式。双向拉伸薄膜的成形工艺有平膜法和管膜法两种,其中平膜法采用较广泛,平膜 3
学海无涯
机头压力、螺杆转速、螺杆几何尺寸等因素的影响。 热塑性塑料管材的机头大体上可分为直通式、直角式和偏移式三种,其中用得最多的是直通式机头。挤出管材的定径方法有定径
套、定径环和定径板等。
第六章 注射成形 注射成形是间歇生产过程。 注射成形设备包括注射机、注射模具和辅助设备。注射机是注射成形的核心设备。 根据外形特征,注射机分为立式、卧式和角式三类。根据结构特点,注射机分为移动螺杆式注射机和柱塞式注射机两大类。移动 螺杆式注射机是目前注射成形最常采用的注射机。
高分子泡沫制品成形的发泡方法有机械发泡法、物理发泡法和化学发泡法三种。高分子泡沫制品的成形过程一般可分为泡核形成、 泡孔增长和泡体固化三个阶段。塑料普通制品的成形工艺都可用于成形泡沫塑料,比如挤出成形、注射成形、模压成形、浇注成形和 压延成形等。
第十章 化学纤维成形原理 化学纤维的主要成形原料是成纤聚合物。成纤聚合物有天然高分子聚合物和合成高分子聚合物两大类,前者生产的是人造纤维, 后者生产的是合成纤维。 化学纤维成形通常采用熔体或浓溶液进行纺丝,前者称为熔体纺丝,后者称为溶液纺丝,普通溶液纺丝包括湿法纺丝和干法纺丝 两种。后加工随化纤品种、纺丝方法和产品要求而异,主要后加工工序是拉伸和热定形。 熔体纺丝中纤维结构的形成和发展主要是指纺丝线上聚合物的取向和结晶。纺丝过程中的取向有两种机理,一种是处于熔体状态 下的黏流流动取向机理,另一种是丝条固化后的塑性拉伸流动(或称塑性形变)取向机理。结晶能力强的成纤聚合物容易冻结黏流拉 伸流动取向,但是往往难以启动塑性形变取向机理。结晶能力弱的成纤聚合物通过黏流拉伸流动取向机理获得的有效取向较小,常规 纺时在纺程上的取向机理主要是黏流拉伸流动取向,卷绕丝取向度通常很小;但是纺速增加到 5000m/min 左右,容易启动塑性形变取 向机理,因此取向程度可以较高,高速纺卷绕丝通常比常规纺存在更明显的皮芯结构。