齿轮常用材料的选择及其热处理工艺分析
齿轮常用材料及热处理

齿轮常用材料及热处理
为了保证齿轮工作的可靠性,提高其使用寿命,齿轮的材料及其热处理应根据工作条件和材料的特点来选取。
对齿轮材料的基本要求是:应使齿面具有足够的硬度和耐磨性,齿心具有足够的韧性,以防止齿面的各种失效,同时应具有良好的冷、热加工的工艺性,以达到齿轮的各种技术要求。
常用的齿轮材料为各种牌号的优质碳素结构钢、合金结构钢、铸钢、铸铁和非金属材料等。
一般多采用锻件或轧制钢材。
当齿轮结构尺寸较大,轮坯不易锻造时,可采用铸钢;开式低速传动时,可采用灰铸铁或球墨铸铁、低速重载的齿轮易产生齿面塑性变形,轮齿也易折断,宜选用综合性能较好的钢材;高速齿轮易产生齿面点蚀,宜选用齿面硬度高的材料;受冲击载荷的齿轮,宜选用韧性好的材料。
对高速、轻载而又要求低噪声的齿轮传动,也可采用非金属材料、如夹布胶木、尼龙等。
常用的齿轮材料及其力学性能列于下表。
根据热处理后齿面硬度的不同,齿轮可分为软齿面齿轮(≤350HBS)和硬齿面齿轮(>350HBS)。
一般要求的齿轮传动可采用软齿面齿轮。
为了减小胶合的可能性,并使配对的大小齿轮寿命相当,通常使小齿轮齿面硬度比大齿轮齿面硬度高出30~
50HBS。
对于高速、重载或重要的齿轮传动,可采用硬齿面齿轮组合,齿面硬度可大致相同。
常用齿轮材料及其力学性能。
齿轮材料的选择原则是什么

齿轮材料的选择原则齿轮的材料及其选择原则由轮齿的失效形式可知,设计齿轮传动时,应使齿面具有较高的抗磨损、抗点蚀、抗胶合及抗塑性变形的能力,而齿根要有较高的抗折断能力。
因此,对齿轮材料性能的基本要求为齿面要硬、齿芯要韧。
(一)常用的齿轮材料1(钢钢材的韧性好,耐冲击,还可通过热处理或化学热处理改善其力学性能及提高齿面的硬度,故最适于用来制造齿轮。
(1)锻钢除尺寸过大或者是结构形状复杂只宜铸造者外,一般都用锻钢制造齿轮,常用的是含碳量在0. 15%~0.6%的碳钢或合金钢。
制造齿轮的锻钢可分为:1)经热处理后切齿的齿轮所用的锻钢。
、对于强度、速度及精度都要求不高的齿轮,应采用软齿面(硬度?350 HBS)以便于切齿,并使刀具不致迅速磨损变钝。
因此,应将齿轮毛坯经过常化(正火)或调质处理后切齿。
切制后即为成品。
其精度一般为8级,精切时可达7级。
这类齿轮制造简便、经济、生产率高。
2)需进行精加工的齿轮所用的锻钢。
高速、重载及精密机器(如精密机床、航空发动机)所用的主要齿轮传动,除要求材料性能优良,轮齿具有高强度及齿面具有高硬度(如58~ 65 HRC)外,还应进行磨齿等精加工。
需精加工的齿轮目前多是先切齿,再做表面硬化处理,最后进行精加工,精度可达5级或4级。
这类齿轮精度高,价格较贵,所用热处理方法有表面淬火、渗碳、氮化、软氮化及氰化等。
所用材料视具体要求及热处理方法而定。
合金钢材根据所含金属的成分及性能,可分别使材料的韧性、耐冲击、耐磨及抗胶合的性能等获得提高,也可通过热处理或化学热处理改善材料的力学性能及提高齿面的硬度。
所以对于既是高速、重载,又要求尺寸小、质量小的航空用齿轮,就都用性能优良的合金钢(如20CrMnTi、20Cr2Ni4A等)来制造。
由于硬齿面齿轮具有力学性能高、结构尺寸小等优点,因而一些工业发达的国家在一般机械中也普遍采用了中、硬齿面的齿轮传动。
(2)铸钢铸钢的耐磨性及强度均较好,但应经退火及常化处理,必要时也可进行调质。
常用齿轮材料的选择及其热处理工艺

面淬火 、 调质和正火等 , 在齿轮制造 中都被应用 , 因此 , 齿轮 的 大渗碳表层 的压应力 , 提高疲劳强度 , 并可清除氧化皮 。 选材和热处理方法的选用较其它零件复杂。这就 需要 设计人 2 航空发动机齿轮承受高速 和重载 , ) 比汽车 、 拖拉机齿轮 员根据齿轮承载能力 的不同 , 理选择 材料和 毛坯及 热处理 的工作 条件更为恶劣 , 合 除要求 高的耐疲 劳性外 , 还要求齿轮 的 工艺 , 制定 相应 的工艺路线 , 并 用最经济的办法最 大限度地发 心部具有高 的强度 和韧性 , 一般 多采用 1C N3 1 C2 iA 2 riA、2 rN4 挥 材 料 的潜 能 , 到 “ 尽 其用 ” 做 物 。 或 1C2 iWA 等 高 级 渗 碳 钢 制 造 , 了 节 约 镍 , 用 8 rN4 为 可 2 常 用 齿 轮 材 料 及 热 处理 工艺 的选 择 1C MnSM A代替 1C2 iWA。这两种钢 的切削加工性能 5 r 2 io 8 rN4
材料 等 的 选择 及 热 处理 工 艺进 行 了分 析 。
关键词 : 齿轮材料 ; 热处理 ; 锻钢 ; 铸钢 ; 铸铁 ; 色金属 ; 有 非金 属材料
中 图分 类 号 : G 6 .3 文 献 标 识 码 : T 127 A 文章 编 号 :0 8—66 (0 6 0 0 0 0 10 75 20 )5— 15— 2
● 李 玉 平
( 新余 高等专科学校 工 程系 , 江西 新余 3 80 ) 3 00
摘
要: 齿轮 是机械传动 中应用最广泛的零件之一 , 它在 工作 中的受力情况 比较复杂 。在齿轮 的制造过程 中, 合理选择
材料 与热处理 工艺 , 是提 高承栽能力和延长使用寿命的必要保证 就常用齿轮 材料锻钢、 铸钢 、 铸铁 、 色金属 、 有 非金属
齿轮材料选择及其热处理
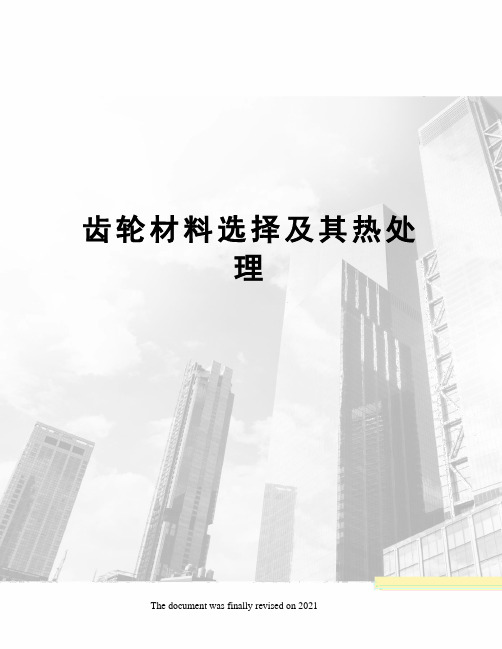
齿轮材料选择及其热处理The document was finally revised on 2021齿轮材料选择及其热处理摘要:齿轮是轮缘上有齿能连续啮合传递运动和动力的机械元件,是能互相啮合的有齿的机械零件,是机械传动中应用最广泛的零件之一。
在齿轮的制造过程中,合理选择材料与热处理工艺,是提高承载能力和延长使用寿命的必要保证。
常用齿轮材料锻钢、铸钢、铸铁、有色金属、非金属材料等的选择及热处理工艺进行了分析。
关键词:齿轮材料热处理工艺一、齿轮结构:二、齿轮的分类:按其外形分为:圆柱齿轮、锥齿轮、非圆齿轮、、蜗杆蜗轮按齿线形状分为:直齿轮、斜齿轮、人字齿轮、曲线齿轮按轮齿所在的表面分为:外齿轮、内齿轮按制造方法可分为:铸造齿轮、切制齿轮、轧制齿轮、烧结齿轮三、常用齿轮材料及热处理工艺的选择:1)高承载能力的重要齿轮,如汽车、拖拉机、矿山机械及航空发动机等齿轮汽车、拖拉机等齿轮主要分装在变速箱和差速器中,推动汽车、拖拉机运行,所以传递功率、冲击力及摩擦压力都很大, 工作条件比较差。
因此在耐磨性、疲劳强度、心部强度和冲击韧性等方面的要求均比较高,因此选用渗碳钢经渗碳、淬火及低温回火后使用最为合适。
小模数齿轮一般采用20Cr和20CrMnTi,而较大模数齿轮采用30CrMnTi 钢。
工艺路线一般为:备料——锻造——正火——机械粗加工、半精加工——渗碳+ 淬火+ 低温回火——喷丸——校正——精加工2)中等承载能力的齿轮,主要用于切削机床齿轮机床齿轮大多用于齿轮箱,传递动力,改变运动速度和方向,工作条件相对较好,载荷不大,工作平稳无强烈冲击,转速也不高,属工作条件较好的齿轮。
因此,要求综合力学性能好,一般选用调质钢制造, 如40 钢、45 钢、40Cr、40SiMn 等。
工艺路线一般为:备料——锻造——正火——机械粗加工——调质——机械半精加工——高频感应淬火+ 低温回火——磨削3)较低承载能力的齿轮较低承载能力的齿轮一般选用中碳钢(40、45)或低合金中碳钢(40Cr、40Mn、40MnB等)制造,进行调质处理,调质后硬度约为200~300HB。
机械结构中大型齿轮的成分材质以及生产制造工艺

当涉及到机械结构中的大型齿轮时,其成分材质和生产制造工艺是至关重要的。
大型齿轮通常用于重型机械设备和工程机械中,其质量和可靠性直接影响着设备的性能和安全。
本文将深入探讨大型齿轮的成分材质以及生产制造工艺,从而对相关领域的专业人士和广大读者提供有益的参考和指导。
一、大型齿轮的成分材质大型齿轮通常由金属材料制成,常见的成分材质包括但不限于以下几种:1.高强度合金钢:具有良好的硬度和耐磨性,适用于高负荷、高速度、长工作时间的齿轮传动系统;2.碳素钢:具有较高的韧性和耐磨性,适用于一般负载和速度条件下的齿轮传动系统;3.不锈钢:具有耐腐蚀性和耐热性,适用于工作环境要求高的齿轮传动系统;4.铝合金:轻质、高强度,适用于一些轻型机械设备的齿轮传动系统。
以上材料的选择应根据具体的工作条件和要求来确定,需要考虑到负载、速度、温度、工作时间等因素。
合适的成分材质能够保证齿轮的稳定性和寿命,同时降低维护和更换成本。
二、大型齿轮的生产制造工艺大型齿轮的生产制造工艺是保证其精密度和可靠性的关键。
通常情况下,大型齿轮的生产制造工艺包括以下几个主要步骤:1.材料准备:选择合适的金属材料,并按照设计要求进行材料切割和预加工,以便后续的成形和加工工艺;2.成形加工:使用锻造或铸造工艺对齿轮进行整体成形,保证齿轮的整体性和强度;3.精密加工:通过车削、磨削等精密加工工艺对齿轮的外形和齿面进行加工,保证其精度和匹配性;4.热处理:对齿轮进行热处理,以提高其硬度和耐磨性;5.装配和调试:将齿轮与轴承、轴等部件进行装配,同时进行调试和检测,确保齿轮传动系统的正常运转。
不同的工艺步骤相互配合,共同保证了大型齿轮的质量和性能。
在生产制造过程中,需要严格按照相关标准和要求进行操作,同时注重工艺流程的控制和管理,以确保齿轮的质量和稳定性。
在实际生产制造中,还可以根据具体的要求和条件选择合适的生产设备和工艺流程,利用先进的数控加工技术和自动化设备,提高生产效率和产品质量。
齿轮常用材料及热处理

齿轮常用材料及热处理
为了保证齿轮工作的可靠性,提高其使用寿命,齿轮的材料及其热处理应根据工作条件和材料的特点来选取。
对齿轮材料的基本要求是:应使齿面具有足够的硬度和耐磨性,齿心具有足够的韧性,以防止齿面的各种失效,同时应具有良好的冷、热加工的工艺性,以达到齿轮的各种技术要求。
常用的齿轮材料为各种牌号的优质碳素结构钢、合金结构钢、铸钢、铸铁和非金属材料等。
一般多采用锻件或轧制钢材。
当齿轮结构尺寸较大,轮坯不易锻造时,可采用铸钢;开式低速传动时,可采用灰铸铁或球墨铸铁、低速重载的齿轮易产生齿面塑性变形,轮齿也易折断,宜选用综合性能较好的钢材;高速齿轮易产生齿面点蚀,宜选用齿面硬度高的材料;受冲击载荷的齿轮,宜选用韧性好的材料。
对高速、轻载而又要求低噪声的齿轮传动,也可采用非金属材料、如夹布胶木、尼龙等。
常用的齿轮材料及其力学性能列于下表。
根据热处理后齿面硬度的不同,齿轮可分为软齿面齿轮(≤350HBS)和硬齿面齿轮(>350HBS)。
一般要求的齿轮传动可采用软齿面齿轮。
为了减小胶合的可能性,并使配对的大小齿轮寿命相当,通常使小齿轮齿面硬度比大齿轮齿面硬度高出30~
50HBS。
对于高速、重载或重要的齿轮传动,可采用硬齿面齿轮组合,齿面硬度可大致相同。
常用齿轮材料及其力学性能。
齿轮材料及热处理
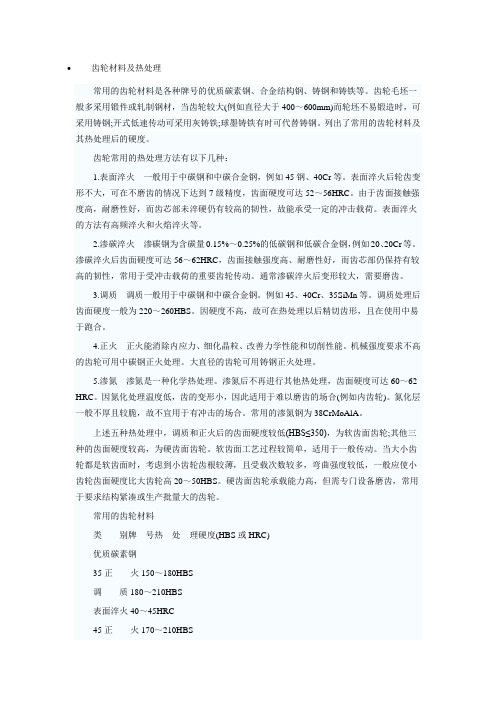
齿轮材料及热处理常用的齿轮材料是各种牌号的优质碳素钢、合金结构钢、铸钢和铸铁等。
齿轮毛坯一般多采用锻件或轧制钢材,当齿轮较大(例如直径大于400~600mm)而轮坯不易锻造时,可采用铸钢;开式低速传动可采用灰铸铁;球墨铸铁有时可代替铸钢。
列出了常用的齿轮材料及其热处理后的硬度。
齿轮常用的热处理方法有以下几种:1.表面淬火一般用于中碳钢和中碳合金钢,例如45钢、40Cr等。
表面淬火后轮齿变形不大,可在不磨齿的情况下达到7级精度,齿面硬度可达52~56HRC。
由于齿面接触强度高,耐磨性好,而齿芯部未淬硬仍有较高的韧性,故能承受一定的冲击载荷。
表面淬火的方法有高频淬火和火焰淬火等。
2.渗碳淬火渗碳钢为含碳量0.15%~0.25%的低碳钢和低碳合金钢,例如20、20Cr等。
渗碳淬火后齿面硬度可达56~62HRC,齿面接触强度高、耐磨性好,而齿芯部仍保持有较高的韧性,常用于受冲击载荷的重要齿轮传动。
通常渗碳淬火后变形较大,需要磨齿。
3.调质调质一般用于中碳钢和中碳合金钢。
例如45、40Cr、35SiMn等。
调质处理后齿面硬度一般为220~260HBS。
因硬度不高,故可在热处理以后精切齿形,且在使用中易于跑合。
4.正火正火能消除内应力、细化晶粒、改善力学性能和切削性能。
机械强度要求不高的齿轮可用中碳钢正火处理。
大直径的齿轮可用铸钢正火处理。
5.渗氮渗氮是一种化学热处理。
渗氮后不再进行其他热处理,齿面硬度可达60~62 HRC。
因氮化处理温度低,齿的变形小,因此适用于难以磨齿的场合(例如内齿轮)。
氮化层一般不厚且较脆,故不宜用于有冲击的场合。
常用的渗氮钢为38CrMoAlA。
上述五种热处理中,调质和正火后的齿面硬度较低(HBS≤350),为软齿面齿轮;其他三种的齿面硬度较高,为硬齿面齿轮。
软齿面工艺过程较简单,适用于一般传动。
当大小齿轮都是软齿面时,考虑到小齿轮齿根较薄,且受载次数较多,弯曲强度较低,一般应使小齿轮齿面硬度比大齿轮高20~50HBS。
常用齿轮材料的选择及其热处理工艺总结
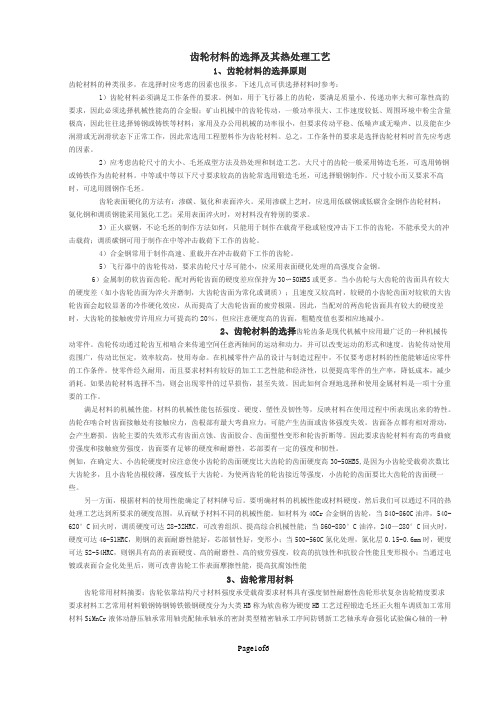
齿轮材料的选择及其热处理工艺1、齿轮材料的选择原则齿轮材料的种类很多,在选择时应考虑的因素也很多,下述几点可供选择材料时参考:1)齿轮材料必须满足工作条件的要求。
例如,用于飞行器上的齿轮,要满足质量小、传递功率大和可靠性高的要求,因此必须选择机械性能高的合金银;矿山机械中的齿轮传动,一般功率很大、工作速度较低、周围环境中粉尘含量极高,因此往往选择铸钢或铸铁等材料;家用及办公用机械的功率很小,但要求传动平稳、低噪声或无噪声、以及能在少润滑或无润滑状态下正常工作,因此常选用工程塑料作为齿轮材料。
总之,工作条件的要求是选择齿轮材料时首先应考虑的因素。
2)应考虑齿轮尺寸的大小、毛坯成型方法及热处理和制造工艺。
大尺寸的齿轮一般采用铸造毛坯,可选用铸钢或铸铁作为齿轮材料。
中等或中等以下尺寸要求较高的齿轮常选用锻造毛坯,可选择锻钢制作。
尺寸较小而又要求不高时,可选用圆钢作毛坯。
齿轮表面硬化的方法有:渗碳、氨化和表面淬火。
采用渗碳上艺时,应选用低碳钢或低碳含金钢作齿轮材料;氨化钢和调质钢能采用氮化工艺;采用表面淬火时,对材料没有特别的要求。
3)正火碳钢,不论毛坯的制作方法如何,只能用于制作在载荷平稳或轻度冲击下工作的齿轮,不能承受大的冲击载荷;调质碳钢可用于制作在中等冲击载荷下工作的齿轮。
4)合金钢常用于制作高速、重载并在冲击载荷下工作的齿轮。
5)飞行器中的齿轮传动,要求齿轮尺寸尽可能小,应采用表面硬化处理的高强度合金钢。
6)金属制的软齿面齿轮,配对两轮齿面的硬度差应保持为30〜50HBS或更多。
当小齿轮与大齿轮的齿面具有较大的硬度差(如小齿轮齿面为淬火并磨制,大齿轮齿面为常化或调质);且速度又较高时,较硬的小齿轮齿面对较软的大齿轮齿面会起较显著的冷作硬化效应,从而提高了大齿轮齿面的疲劳极限。
因此,当配对的两齿轮齿面具有较大的硬度差时,大齿轮的接触疲劳许用应力可提高约20%,但应注意硬度高的齿面,粗糙度值也要相应地减小。
常用齿轮材料选择及其热处理工艺
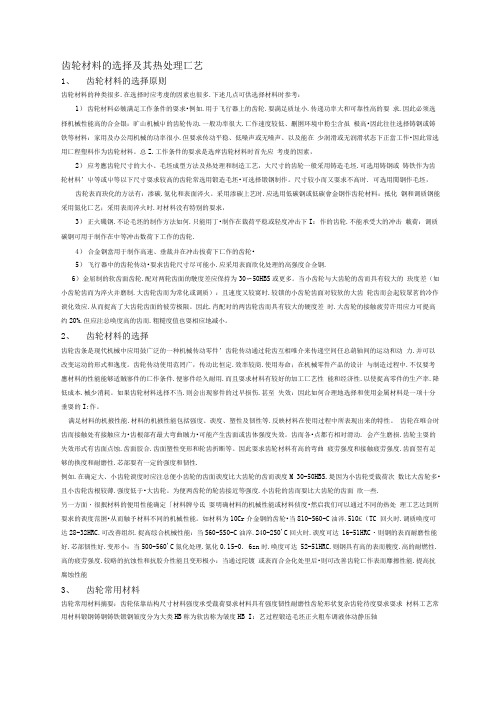
齿轮材料的选择及其热处理匸艺1、齿轮材料的选择原则齿轮材料的种类很多.在选择时应考虔的因素也很多.下述几点可供选择材料时参考:1)齿轮材料必皴满足工作条件的耍求•例如.用于飞行器上的齿轮.耍满足质址小.传递功率大和可靠性高的耍求.因此必须选择机械性能高的合佥银:旷山机械屮的齿轮传动.一般功率很大.匸作速度较低、删圉环境中粉尘含虽极高•因此往往选择铸钢或铸铁等材料:家用及办公用机械的功率很小.但要求传动平稳、低噪声或无噪声、以及能在少润滑或无润滑状态下正當工作•因此常选用匸程塑料作为齿轮材料。
总Z.工作条件的耍求是选痒齿轮材料时首先应考虔的因素,2)应考應齿轮尺寸的大小、毛坯成型方法及热处理和制造工艺,大尺寸的齿轮一般采用铸造毛坯.可选用铸钢或铸铁作为齿轮材料’屮等或屮等以下尺寸耍求较高的齿轮常选用锻造毛坯•可选择锻钢制作。
尺寸较小而又耍求不高时. 可选用閲钢作毛坯,齿轮表而玦化的方法有:渗碳.氨化和表面淬火。
采用渗碳上艺时.应选用低碳钢或低碳會金钢作齿轮材料:抵化钢和调质钢能采用氮化匸艺;采用表而淬火时.对材料没有特别的耍求,3)正火磯钢.不论毛坯的制作方法如何.只能用丁•制作在裁荷平稳或轻度冲击下I:作的齿轮.不能承受大的冲击載荷:调质碳钢可用于制作在中等冲击数荷下工作的齿轮.4)合金钢當用于制作高速、垂裁并在冲击拔荷下匸作的齿轮•5)飞行器中的齿轮传动•耍求齿轮尺寸尽可能小.应采用表面欣化处理的高强度合佥钢.6)金屈制的软齿面齿轮.配对两轮齿面的駛度差应保持为30〜50HBS或更多。
当小齿轮与大齿轮的齿而具有较大的玦度差(如小齿轮齿而为淬火并磨制.大齿轮齿而为常化或调质):且速度又较窩时.较锁的小齿轮齿面对较软的大齿轮齿而会起较眾茗的冷作谀化效应.从而捉高了大齿轮齿面的彼劳极限。
因此.肖配对的两齿轮齿而具有较大的硬度差时.大齿轮的接触疲劳许用应力可提高约20%.但应注总唤度高的齿而.粗糙度值也耍相应地减小。
齿轮常用材料和热处理
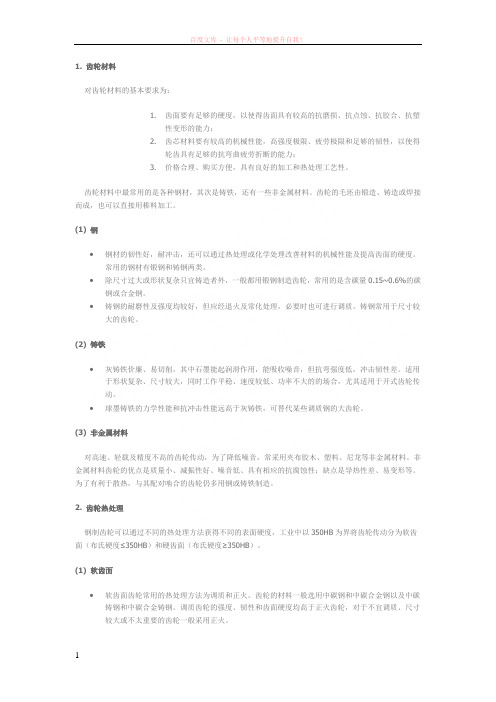
1. 齿轮材料对齿轮材料的基本要求为:1.齿面要有足够的硬度,以使得齿面具有较高的抗磨损、抗点蚀、抗胶合、抗塑性变形的能力;2.齿芯材料要有较高的机械性能,高强度极限、疲劳极限和足够的韧性,以使得轮齿具有足够的抗弯曲疲劳折断的能力;3.价格合理、购买方便,具有良好的加工和热处理工艺性。
齿轮材料中最常用的是各种钢材,其次是铸铁,还有一些非金属材料。
齿轮的毛坯由锻造、铸造或焊接而成,也可以直接用棒料加工。
(1) 钢•钢材的韧性好,耐冲击,还可以通过热处理或化学处理改善材料的机械性能及提高齿面的硬度。
常用的钢材有锻钢和铸钢两类。
•除尺寸过大或形状复杂只宜铸造者外,一般都用锻钢制造齿轮,常用的是含碳量0.15~0.6%的碳钢或合金钢。
•铸钢的耐磨性及强度均较好,但应经退火及常化处理,必要时也可进行调质。
铸钢常用于尺寸较大的齿轮。
(2) 铸铁•灰铸铁价廉、易切削,其中石墨能起润滑作用,能吸收噪音,但抗弯强度低,冲击韧性差。
适用于形状复杂、尺寸较大,同时工作平稳、速度较低、功率不大的的场合,尤其适用于开式齿轮传动。
•球墨铸铁的力学性能和抗冲击性能远高于灰铸铁,可替代某些调质钢的大齿轮。
(3) 非金属材料对高速、轻载及精度不高的齿轮传动,为了降低噪音,常采用夹布胶木、塑料、尼龙等非金属材料。
非金属材料齿轮的优点是质量小、减振性好、噪音低、具有相应的抗腐蚀性;缺点是导热性差、易变形等。
为了有利于散热,与其配对啮合的齿轮仍多用钢或铸铁制造。
2. 齿轮热处理钢制齿轮可以通过不同的热处理方法获得不同的表面硬度,工业中以350HB为界将齿轮传动分为软齿面(布氏硬度≤350HB)和硬齿面(布氏硬度≥350HB)。
(1) 软齿面•软齿面齿轮常用的热处理方法为调质和正火。
齿轮的材料一般选用中碳钢和中碳合金钢以及中碳铸钢和中碳合金铸钢。
调质齿轮的强度、韧性和齿面硬度均高于正火齿轮,对于不宜调质、尺寸较大或不太重要的齿轮一般采用正火。
常用齿轮材料的选择及其热处理工艺总结
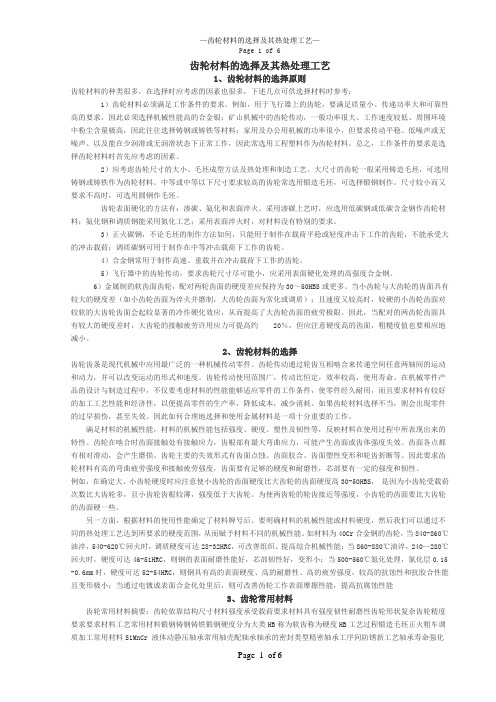
齿轮材料的选择及其热处理工艺1、齿轮材料的选择原则齿轮材料的种类很多,在选择时应考虑的因素也很多,下述几点可供选择材料时参考:1)齿轮材料必须满足工作条件的要求。
例如,用于飞行器上的齿轮,要满足质量小、传递功率大和可靠性高的要求,因此必须选择机械性能高的合金银;矿山机械中的齿轮传动,一般功率很大、工作速度较低、周围环境中粉尘含量极高,因此往往选择铸钢或铸铁等材料;家用及办公用机械的功率很小,但要求传动平稳、低噪声或无噪声、以及能在少润滑或无润滑状态下正常工作,因此常选用工程塑料作为齿轮材料。
总之,工作条件的要求是选择齿轮材料时首先应考虑的因素。
2)应考虑齿轮尺寸的大小、毛坯成型方法及热处理和制造工艺。
大尺寸的齿轮一般采用铸造毛坯,可选用铸钢或铸铁作为齿轮材料。
中等或中等以下尺寸要求较高的齿轮常选用锻造毛坯,可选择锻钢制作。
尺寸较小而又要求不高时,可选用圆钢作毛坯。
齿轮表面硬化的方法有:渗碳、氨化和表面淬火。
采用渗碳上艺时,应选用低碳钢或低碳含金钢作齿轮材料;氨化钢和调质钢能采用氮化工艺;采用表面淬火时,对材料没有特别的要求。
3)正火碳钢,不论毛坯的制作方法如何,只能用于制作在载荷平稳或轻度冲击下工作的齿轮,不能承受大的冲击载荷;调质碳钢可用于制作在中等冲击载荷下工作的齿轮。
4)合金钢常用于制作高速、重载并在冲击载荷下工作的齿轮。
5)飞行器中的齿轮传动,要求齿轮尺寸尽可能小,应采用表面硬化处理的高强度合金钢。
6)金属制的软齿面齿轮,配对两轮齿面的硬度差应保持为30~50HBS或更多。
当小齿轮与大齿轮的齿面具有较大的硬度差(如小齿轮齿面为淬火并磨制,大齿轮齿面为常化或调质);且速度又较高时,较硬的小齿轮齿面对较软的大齿轮齿面会起较显著的冷作硬化效应,从而提高了大齿轮齿面的疲劳极限。
因此,当配对的两齿轮齿面具有较大的硬度差时,大齿轮的接触疲劳许用应力可提高约20%,但应注意硬度高的齿面,粗糙度值也要相应地减小。
汽车齿轮材料的选择及其热处理工艺
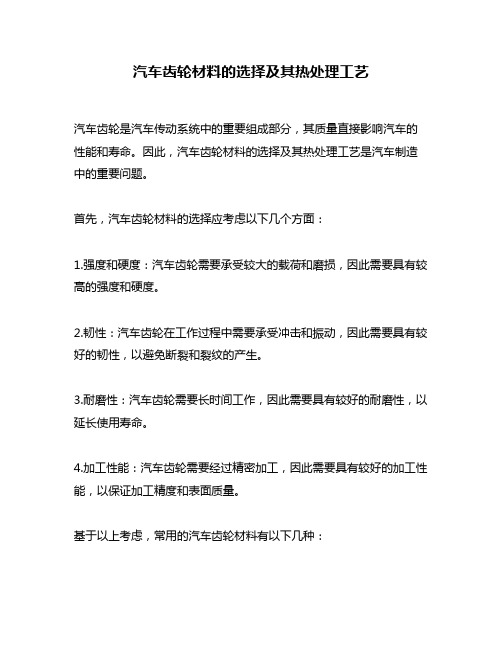
汽车齿轮材料的选择及其热处理工艺汽车齿轮是汽车传动系统中的重要组成部分,其质量直接影响汽车的性能和寿命。
因此,汽车齿轮材料的选择及其热处理工艺是汽车制造中的重要问题。
首先,汽车齿轮材料的选择应考虑以下几个方面:1.强度和硬度:汽车齿轮需要承受较大的载荷和磨损,因此需要具有较高的强度和硬度。
2.韧性:汽车齿轮在工作过程中需要承受冲击和振动,因此需要具有较好的韧性,以避免断裂和裂纹的产生。
3.耐磨性:汽车齿轮需要长时间工作,因此需要具有较好的耐磨性,以延长使用寿命。
4.加工性能:汽车齿轮需要经过精密加工,因此需要具有较好的加工性能,以保证加工精度和表面质量。
基于以上考虑,常用的汽车齿轮材料有以下几种:1.碳素钢:碳素钢具有较高的强度和硬度,但韧性较差,容易产生裂纹和断裂。
2.合金钢:合金钢具有较高的强度、硬度和韧性,但加工性能较差,需要采用先进的加工工艺。
3.铸铁:铸铁具有较好的耐磨性和韧性,但强度和硬度较低,适用于低速和中速齿轮。
4.不锈钢:不锈钢具有较好的耐腐蚀性和韧性,但强度和硬度较低,适用于低速和中速齿轮。
其次,汽车齿轮材料的热处理工艺也是影响其性能的重要因素。
常用的热处理工艺有以下几种:1.淬火:淬火可以提高齿轮的硬度和强度,但会降低韧性,容易产生裂纹和断裂。
2.回火:回火可以提高齿轮的韧性和耐磨性,但会降低硬度和强度。
3.正火:正火可以提高齿轮的强度和硬度,同时保持一定的韧性和耐磨性。
4.表面强化:表面强化可以提高齿轮的耐磨性和疲劳寿命,常用的方法有渗碳、氮化和喷涂等。
综上所述,汽车齿轮材料的选择及其热处理工艺是汽车制造中的重要问题,需要综合考虑材料的强度、硬度、韧性、耐磨性和加工性能等因素,选择合适的材料和热处理工艺,以保证汽车齿轮的性能和寿命。
齿轮材料及其热处理
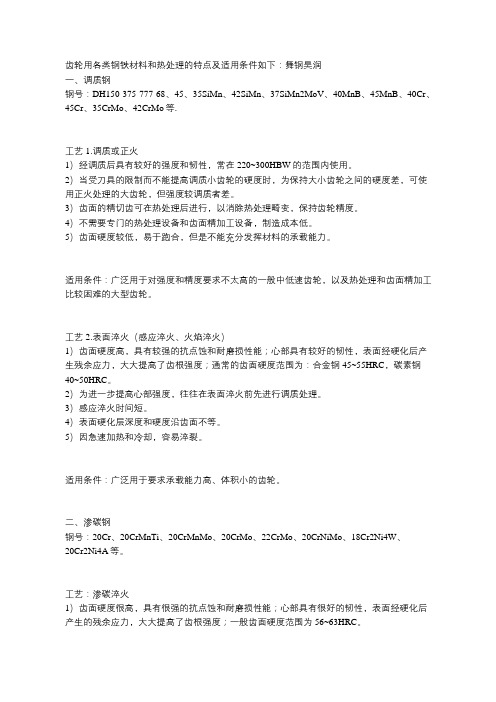
齿轮用各类钢铁材料和热处理的特点及适用条件如下:舞钢昊润一、调质钢钢号:DH150-375-777-68、45、35SiMn、42SiMn、37SiMn2MoV、40MnB、45MnB、40Cr、45Cr、35CrMo、42CrMo等.工艺1.调质或正火1)经调质后具有较好的强度和韧性,常在220~300HBW的范围内使用。
2)当受刀具的限制而不能提高调质小齿轮的硬度时,为保持大小齿轮之间的硬度差,可使用正火处理的大齿轮,但强度较调质者差。
3)齿面的精切齿可在热处理后进行,以消除热处理畸变,保持齿轮精度。
4)不需要专门的热处理设备和齿面精加工设备,制造成本低。
5)齿面硬度较低,易于跑合,但是不能充分发挥材料的承载能力。
适用条件:广泛用于对强度和精度要求不太高的一般中低速齿轮,以及热处理和齿面精加工比较困难的大型齿轮。
工艺2.表面淬火(感应淬火、火焰淬火)1)齿面硬度高,具有较强的抗点蚀和耐磨损性能;心部具有较好的韧性,表面经硬化后产生残余应力,大大提高了齿根强度;通常的齿面硬度范围为:合金钢45~55HRC,碳素钢40~50HRC。
2)为进一步提高心部强度,往往在表面淬火前先进行调质处理。
3)感应淬火时间短。
4)表面硬化层深度和硬度沿齿面不等。
5)因急速加热和冷却,容易淬裂。
适用条件:广泛用于要求承载能力高、体积小的齿轮。
二、渗碳钢钢号:20Cr、20CrMnTi、20CrMnMo、20CrMo、22CrMo、20CrNiMo、18Cr2Ni4W、20Cr2Ni4A等。
工艺:渗碳淬火1)齿面硬度很高,具有很强的抗点蚀和耐磨损性能;心部具有很好的韧性,表面经硬化后产生的残余应力,大大提高了齿根强度;一般齿面硬度范围为56~63HRC。
2)切削性能较好。
3)热处理畸变较大,热处理后应磨齿,增加了加工时间和成本,但是可以获得高的精度。
适用条件:广泛用于要求承载能力高、耐冲击性能好、精度高、体积小的中型以下齿轮。
常用铸造齿轮材料及其热处理工艺方法
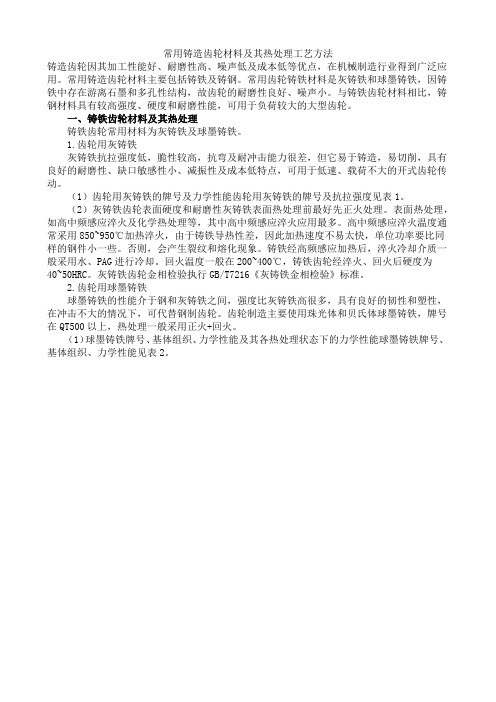
常用铸造齿轮材料及其热处理工艺方法铸造齿轮因其加工性能好、耐磨性高、噪声低及成本低等优点,在机械制造行业得到广泛应用。
常用铸造齿轮材料主要包括铸铁及铸钢。
常用齿轮铸铁材料是灰铸铁和球墨铸铁,因铸铁中存在游离石墨和多孔性结构,故齿轮的耐磨性良好、噪声小。
与铸铁齿轮材料相比,铸钢材料具有较高强度、硬度和耐磨性能,可用于负荷较大的大型齿轮。
一、铸铁齿轮材料及其热处理铸铁齿轮常用材料为灰铸铁及球墨铸铁。
1.齿轮用灰铸铁灰铸铁抗拉强度低,脆性较高,抗弯及耐冲击能力很差,但它易于铸造,易切削,具有良好的耐磨性、缺口敏感性小、减振性及成本低特点,可用于低速、载荷不大的开式齿轮传动。
(1)齿轮用灰铸铁的牌号及力学性能齿轮用灰铸铁的牌号及抗拉强度见表1。
(2)灰铸铁齿轮表面硬度和耐磨性灰铸铁表面热处理前最好先正火处理。
表面热处理,如高中频感应淬火及化学热处理等,其中高中频感应淬火应用最多。
高中频感应淬火温度通常采用850~950℃加热淬火,由于铸铁导热性差,因此加热速度不易太快,单位功率要比同样的钢件小一些。
否则,会产生裂纹和熔化现象。
铸铁经高频感应加热后,淬火冷却介质一般采用水、PAG进行冷却。
回火温度一般在200~400℃,铸铁齿轮经淬火、回火后硬度为40~50HRC。
灰铸铁齿轮金相检验执行GB/T7216《灰铸铁金相检验》标准。
2.齿轮用球墨铸铁球墨铸铁的性能介于钢和灰铸铁之间,强度比灰铸铁高很多,具有良好的韧性和塑性,在冲击不大的情况下,可代替钢制齿轮。
齿轮制造主要使用珠光体和贝氏体球墨铸铁,牌号在QT500以上,热处理一般采用正火+回火。
(1)球墨铸铁牌号、基体组织、力学性能及其各热处理状态下的力学性能球墨铸铁牌号、基体组织、力学性能见表2。
(2)球墨铸铁热处理铸造齿轮毛坯的预处理一般采用退火、正火,也可进行正火+回火,或调质处理。
球墨铸铁齿轮的常用热处理工艺见表3。
(3)球墨铸铁金相检验执行GB/T9441《球墨铸铁金相检验》标准。
汽车齿轮材料的选择及其热处理工艺
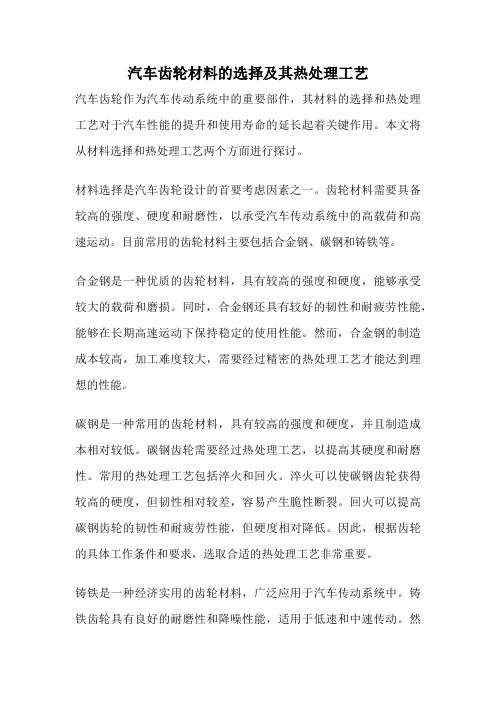
汽车齿轮材料的选择及其热处理工艺汽车齿轮作为汽车传动系统中的重要部件,其材料的选择和热处理工艺对于汽车性能的提升和使用寿命的延长起着关键作用。
本文将从材料选择和热处理工艺两个方面进行探讨。
材料选择是汽车齿轮设计的首要考虑因素之一。
齿轮材料需要具备较高的强度、硬度和耐磨性,以承受汽车传动系统中的高载荷和高速运动。
目前常用的齿轮材料主要包括合金钢、碳钢和铸铁等。
合金钢是一种优质的齿轮材料,具有较高的强度和硬度,能够承受较大的载荷和磨损。
同时,合金钢还具有较好的韧性和耐疲劳性能,能够在长期高速运动下保持稳定的使用性能。
然而,合金钢的制造成本较高,加工难度较大,需要经过精密的热处理工艺才能达到理想的性能。
碳钢是一种常用的齿轮材料,具有较高的强度和硬度,并且制造成本相对较低。
碳钢齿轮需要经过热处理工艺,以提高其硬度和耐磨性。
常用的热处理工艺包括淬火和回火。
淬火可以使碳钢齿轮获得较高的硬度,但韧性相对较差,容易产生脆性断裂。
回火可以提高碳钢齿轮的韧性和耐疲劳性能,但硬度相对降低。
因此,根据齿轮的具体工作条件和要求,选取合适的热处理工艺非常重要。
铸铁是一种经济实用的齿轮材料,广泛应用于汽车传动系统中。
铸铁齿轮具有良好的耐磨性和降噪性能,适用于低速和中速传动。
然而,铸铁齿轮的强度和韧性相对较低,容易产生断裂和疲劳损伤。
因此,在设计铸铁齿轮时,需要考虑到其工作条件和要求,合理选择材料和热处理工艺。
热处理工艺对齿轮材料的性能提升至关重要。
在热处理过程中,通过控制加热温度、保温时间和冷却速率等参数,使材料的组织结构发生变化,从而改善其机械性能和耐磨性。
常用的热处理工艺包括淬火、回火、表面渗碳和氮化等。
淬火是一种常用的热处理工艺,通过快速冷却使材料达到高硬度和高强度。
淬火后的材料具有较高的耐磨性和抗断裂能力,适用于高速传动。
然而,淬火过程中容易产生应力集中和变形问题,需要进行适当的回火处理以提高韧性。
回火是一种常用的热处理工艺,通过加热材料至适当温度并保温一段时间后,再进行适当冷却。
汽车齿轮材料的选择及其热处理工艺

汽车齿轮材料的选择及其热处理工艺一、引言汽车齿轮作为传动系统的核心部件之一,其性能对整个汽车的运行质量和寿命有着重要的影响。
齿轮的材料选择和热处理工艺对于其强度、硬度、耐磨性以及齿面质量等方面都有着关键作用。
本文将从材料的选择和热处理工艺两个方面,对汽车齿轮进行深入探讨。
二、汽车齿轮材料的选择2.1 材料要求汽车齿轮材料在选择时需要考虑以下要求: - 高强度:齿轮需要承受较大的载荷和冲击,因此材料需要具备较高的强度; - 耐磨性:齿轮在长时间摩擦中容易受到磨损,材料需要具备一定的耐磨性; - 高硬度:齿轮表面需要有足够的硬度,以提高齿面的使用寿命; - 良好的韧性:齿轮在受到冲击时需要具备良好的韧性,以避免断裂; - 低摩擦系数:材料需要具备较低的摩擦系数,以减少能量损失。
2.2 常用材料根据以上要求,目前常用的汽车齿轮材料主要包括以下几种:2.2.1 碳素钢碳素钢是最常见的齿轮材料之一,其具有良好的强度和耐磨性。
由于其制造成本较低,被广泛应用于中低档汽车的齿轮制造中。
2.2.2 低合金钢低合金钢相对于碳素钢来说,具有更好的强度和韧性,适用于中高档汽车的齿轮制造。
通过适当的热处理工艺,可以进一步提高其性能。
2.2.3 铸造钢铸造钢可以根据具体应用的要求,选择不同的成分和硬化方式。
其制造成本较高,但可以获得较高的硬度和强度,适用于高档车型。
2.2.4 渗碳钢渗碳钢是通过在碳含量较低的钢表面渗入碳元素,从而提高齿轮表面的硬度和耐磨性。
它在制造成本和性能之间取得了很好的平衡,适用于中档车型的齿轮制造。
三、汽车齿轮的热处理工艺3.1 热处理的目的热处理是通过对材料进行加热和冷却,改变其内部组织和性能的工艺。
对于汽车齿轮而言,热处理的目的主要包括以下几个方面: - 提高材料的硬度和强度; - 改善材料的韧性和抗疲劳性能; - 调整材料的组织结构,提高齿面的质量。
3.2 常用热处理工艺根据齿轮的材料和要求,常见的热处理工艺包括以下几种:3.2.1 淬火和回火淬火是将齿轮材料加热至临界温度后迅速冷却,使其获得高硬度和较好的强度。
- 1、下载文档前请自行甄别文档内容的完整性,平台不提供额外的编辑、内容补充、找答案等附加服务。
- 2、"仅部分预览"的文档,不可在线预览部分如存在完整性等问题,可反馈申请退款(可完整预览的文档不适用该条件!)。
- 3、如文档侵犯您的权益,请联系客服反馈,我们会尽快为您处理(人工客服工作时间:9:00-18:30)。
齿轮常用材料的选择及其热处理工艺分析
介绍了齿轮常用材料及典型齿轮的热处理工艺,结合常用齿轮材料的性能特点,总结了齿轮材料选用原则及热处理工艺与提高其承载能力以及延长使用寿命之间的关系,旨在通过理论来指导实践。
标签:齿轮材料;热处理;性能;承载能力
引言
齿轮作为传动系统中应用非常广泛的零件,在工作时,所受应力往往是非常复杂的,一是需要承受齿轮齿根部的循环往复的弯曲应力,二还要考虑接触应力以及齿面之间的相互接触所带来的不良影响,同时具有较强的摩擦齿面,齿轮啮合时,它会吸收一定量的冲击载荷。
齿轮使用过程应避免齿面磨损太多,甚至以断齿、疲劳点蚀形式失效。
合适的热处理工艺能提高齿轮的耐磨性、承载能力和使用寿命,热处理后的齿轮具有高的弯曲疲劳强度和接触疲劳强度(抗疲劳点蚀),齿面具有较高的硬度和耐磨性,齿轮心部具有足够的强度和韧性[1]。
齿轮材料的选择以及相关的热处理工艺无论是对于齿轮的质量,又或者是齿轮的使用性能都会产生很大的影响。
比较常用的热处理工艺包括:表面淬火、碳氮共渗、渗碳、渗氮、回火、正火等。
而对于齿轮材料的选择,锻钢、铸钢、铸铁、有色金属、非金属材料等都是非常理想的选择。
1 齿轮材料及热处理工艺
1.1 锻钢
根据齿面的软硬程度,钢制齿轮包括软齿面齿轮和硬齿面齿轮,它们之间的分界线是布氏硬度为350HBS的时候,大于350HBS为硬齿面,反之则是软齿面。
1.1.1 软齿面齿轮
软尺面齿轮,工艺路线:锻造毛坯→正火→粗车→调质、精加工。
常用材料;45#、35SiMn、40Cr、40CrNi、40MnB等。
软齿面齿轮的特点:性能优良,齿面本身的硬度、强度都理想,齿心的韧性好;热处理后切齿精度可达8级;制造简单、经济、生产率高,对精度要求不高。
1.1.2 硬齿面齿轮
(1)采用中碳钢时的加工工艺过程为:锻造毛坯→常化→粗切→调质→精切→高、中频淬火→低温回火→珩齿或研磨剂跑合、电火花跑合。
常用材料:45、40Cr、40CrNi。
硬齿面齿轮的特点有以下几点:a.齿面硬度高HRC=48-55,接触强度高,耐磨性好。
b.齿芯保持调质后的韧性高,耐冲击能力好,承载能力较高。
c.精度下降半数,可达7级精度。
d.适合批量化生产,如:汽车、机床等中速中载变速箱齿轮。
(2)采用低碳钢时的加工工艺过程为:锻造毛坯→常化→粗切→调质→精切→渗碳淬火→低温回火→磨齿。
常用材料;20Cr、20CrMnTi、20MnB、20CrMnTo。
硬齿面齿轮的特点有以下几点:a.齿面硬度高,承载能力强。
b.芯部韧性好,耐冲击。
c.适合于高速、重载、过载传动或结构设计排列密集的情况,包括一般用到的机车主传动齿轮以及航空用齿轮。
1.2 铸铁
开式传动齿轮一般是用灰铸铁材料制造,由于灰铸铁组织中的石墨起润滑作用,摩擦系数较小,成本低,切削加工性能好等优点。
但是缺点也是非常明显的,比方说抗弯强度不高、材料较脆、抗冲击性能较差。
灰铸铁HT200、HT250、HT300等材料常用来制造一些低承载能力、低传动速度,抗冲击能力差,精度要求不高并且结构设计紧凑的齿轮。
灰铸铁制造的齿轮更多的用于开式齿轮的传动。
对于闭式传动情况,球墨铸铁QT600-3、QT500-7越来越受到市场的欢迎,使用越来越广泛。
考虑到铸铁齿轮需要具备较高的耐磨特性,因此铸铁齿轮一般都需要经过铸造应力退火、正常化、加工表面淬火处理,可以改善铸铁齿轮的综合性能,有时候还会用到表面淬火[2]。
1.3 铸钢
铸钢的应用场合多见于外观轮廓尺寸比较大的场合,并且一般的轮廓比较复杂,还需要具备一定的承载能力。
如果使用锻造没法顺利进行的时候,那么铸钢就是非常理想的一种选择,而且铸钢齿轮的强度相比锻钢齿轮而言,要低百分之十。
一般用于农机方面的铸造齿轮,其精度要求会相对偏低一点。
但是如果是用于作为传动件的齿轮,尤其是需要实现精确传动的机械,则对铸造齿轮提出了更高的要求。
想要提高铸钢齿轮的精度,可以从加工工艺的过程中着手,进行正火或退火的机械处理,消除应力和硬度不均匀的铸件,提高金属的切削加工性能,以改善零件的综合性能,对于要求较低以及低速工作的铸钢齿轮而言,可用退火或正火处理,如果考虑到齿轮需要有较高的耐磨性,那么表面淬火也是一种选择(如火焰淬火)。
ZG270-500、ZG310-570等铸钢齿轮,铸造之后正火,粗加工后表面淬火+低温回火,可满足性能要求。
1.4 有色金属
黄铜、铝青铜、硅青铜、锡青铜制造的齿轮比较常见。
对于抗腐蚀,耐磨性要求较高的齒轮或者是承载能力不大的齿轮而言,这些材料都是非常理想的选择。
而对于要求质量比较小的齿轮而言,硬铝和超硬铝则是首选。
此外,对于蜗轮蜗杆传动,由于传动比一般都很大,而且需要承载较大的力,所以对于蜗轮蜗杆传动件而言,一般选择锡青铜材料,优点就是可以减少咬合黏着情况的发生。
1.5 非金属材料
在齿轮材料上应用比较广泛的非金属一般有布质、木质、塑料、尼龙等,特别是针对高速轻载的齿轮而言,这些材料的应用较多。
工作条件不同,破坏形式的多样化,在选择材料的时候需要进行强度计算,合理的选择。
1.6 齿轮材料的选用原则
(1)齿轮轮齿的冲击载荷和刚度不足应选择良好韧性的
材料,可选用低碳钢,经渗碳淬火处理,以提高刚度。
(2)对于高速闭式变速器和齿轮齿面容易点蚀,应选择齿面硬度好,材质好,可用于表面硬化处理中碳钢。
(3)对低速中载且轮齿容易折断、点蚀、磨损等情况时的齿轮,应选取机械强度高,齿面硬度高等综合机械性较好的材料,可选中碳钢进行调质精切处理[3]。
(4)力求所选材料总类少,方便管理,应该考虑资源和供应情况等方面。
(5)当齿轮的结构尺寸精度要求高,耐磨性好时,要采用合金钢。
2 典型齿轮选材及热处理工艺
2.1 机床齿轮
机床齿轮的作用是传递动力、改变运动速度和方向,相对于汽车、拖拉机的齿轮而言,机床齿轮所承载的工作负荷小很多,并且一般都处于中等工作速度(6~10m/s)运转比较平稳,因此常选用钢或40Cr钢制造,工艺路线为:下料-锻造-正火-粗加工-调质-粗加工-高频淬火及低温回火-精磨。
锻造以使同一批毛坯具有相同的硬度,便于加工,使组织均匀,减少锻件的应力。
普通齿轮,正火处理也可作预先热处理工序。
通过调质处理可以提高齿轮综合力学性能,其齿面强度和齿轮心部的韧性都得到了显著的改善,并能承受较大的弯曲应力和冲击应力,通过回火索氏体组织后调质的齿轮,可以使得齿轮在进行淬火处理的时候,具有较小的变形。
高频淬火,增加了齿轮表面的硬度以及耐磨性能,使齿轮表面具有压应力,使齿轮的疲劳损伤降低,在通过高频淬火后应进行相应低温回火,促使淬火的应力得到消除。
2.2 汽车齿轮
汽车齿轮的工作条件比机床齿轮的工作条件差很多,在主传动系统中,齿轮的应力较大,对齿轮的影响很大,所以对齿轮材料的要求很高。
由于汽车齿轮的弯曲应力和接触应力较大,对于如此重要的齿轮,需要进行渗碳处理和淬火热处理,使齿轮的耐磨性和耐疲劳性增强。
齿轮芯应具有足够的强度和韧性,需要淬透性要求较高的材料,心部硬度应为35到45HRC之间。
此外,在批量生产时,必须注意材料的力学性能和工艺性能[4]。
选用20CrMnTi钢具有较高的机械性能,经过淬火和低温回火的热处理后,其表面硬度可达到58~62 HRC,心部硬度可以达到30~45HRC。
如果想增加表面应力也应采用喷丸处理,使表面压应力增大。
因此渗碳齿轮的工艺路线为:下料-锻造-正火-切削加工-渗碳、淬火及低温回火-喷丸-磨削加工。
锻造能够是工件齿轮成形,改善组织,使韧性增大;正火能够让组织变得均匀、提高硬度、改善切削加工;“渗碳、淬火+低温回火”能夠使齿端面获得耐磨性增强,抗疲劳较大的硬化层,同时使心部获得强韧的低碳回火马氏体、细珠光体或铁素体层;然后在通过喷丸处理使齿面硬度增大到1-3HRC,使表面残余压应力增大,从而提高接触疲劳强度[5]。
3 结束语
在选择齿轮材料时,如果能够根据齿轮的性能来选择合理的材料,将有助于提高齿轮的使用寿命和承载能力,需要相关技术人员掌握各种材料的相关理论,在选择材料的时候做出合理的选择,根据相关齿轮的基本要求进行相应的热处理,使齿轮达到所需要的精度,并且提高它的承载能力和使用寿命。
参考文献:
[1]赵越超,付莹.齿轮材料的选择及热处理[J].煤矿机械,2007.
[2]李玉平.常用齿轮材料的选择及其热工艺处理分析[J].新余高专学报,2006.
[3]石勇.浅析材料的选择及热处理对齿轮传动的影响[J].机械管理开发,2011.
[4]林江.机械制造基础[M].北京:机械工业出版社,2014.
[5]杨瑞成,胡勇.机械工程材料[M].重庆:重庆大学出版社,2012.。