叶轮动平衡
叶轮动平衡问题及解决办法
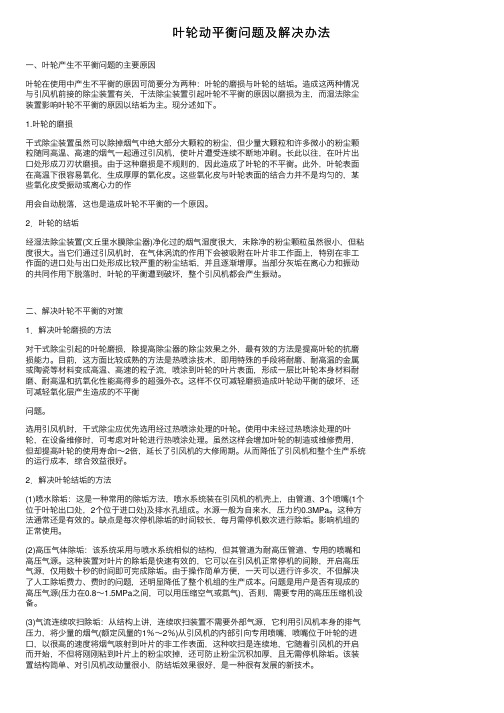
叶轮动平衡问题及解决办法⼀、叶轮产⽣不平衡问题的主要原因叶轮在使⽤中产⽣不平衡的原因可简要分为两种:叶轮的磨损与叶轮的结垢。
造成这两种情况与引风机前接的除尘装置有关,⼲法除尘装置引起叶轮不平衡的原因以磨损为主,⽽湿法除尘装置影响叶轮不平衡的原因以结垢为主。
现分述如下。
1.叶轮的磨损⼲式除尘装置虽然可以除掉烟⽓中绝⼤部分⼤颗粒的粉尘,但少量⼤颗粒和许多微⼩的粉尘颗粒随同⾼温、⾼速的烟⽓⼀起通过引风机,使叶⽚遭受连续不断地冲刷。
长此以往,在叶⽚出⼝处形成⼑刃状磨损。
由于这种磨损是不规则的,因此造成了叶轮的不平衡。
此外,叶轮表⾯在⾼温下很容易氧化,⽣成厚厚的氧化⽪。
这些氧化⽪与叶轮表⾯的结合⼒并不是均匀的,某些氧化⽪受振动或离⼼⼒的作⽤会⾃动脱落,这也是造成叶轮不平衡的⼀个原因。
2.叶轮的结垢经湿法除尘装置(⽂丘⾥⽔膜除尘器)净化过的烟⽓湿度很⼤,未除净的粉尘颗粒虽然很⼩,但粘度很⼤。
当它们通过引风机时,在⽓体涡流的作⽤下会被吸附在叶⽚⾮⼯作⾯上,特别在⾮⼯作⾯的进⼝处与出⼝处形成⽐较严重的粉尘结垢,并且逐渐增厚。
当部分灰垢在离⼼⼒和振动的共同作⽤下脱落时,叶轮的平衡遭到破坏,整个引风机都会产⽣振动。
⼆、解决叶轮不平衡的对策1.解决叶轮磨损的⽅法对⼲式除尘引起的叶轮磨损,除提⾼除尘器的除尘效果之外,最有效的⽅法是提⾼叶轮的抗磨损能⼒。
⽬前,这⽅⾯⽐较成熟的⽅法是热喷涂技术,即⽤特殊的⼿段将耐磨、耐⾼温的⾦属或陶瓷等材料变成⾼温、⾼速的粒⼦流,喷涂到叶轮的叶⽚表⾯,形成⼀层⽐叶轮本⾝材料耐磨、耐⾼温和抗氧化性能⾼得多的超强外⾐。
这样不仅可减轻磨损造成叶轮动平衡的破坏,还可减轻氧化层产⽣造成的不平衡问题。
选⽤引风机时,⼲式除尘应优先选⽤经过热喷涂处理的叶轮。
使⽤中未经过热喷涂处理的叶轮,在设备维修时,可考虑对叶轮进⾏热喷涂处理。
虽然这样会增加叶轮的制造或维修费⽤,但却提⾼叶轮的使⽤寿命l~2倍,延长了引风机的⼤修周期。
风机叶轮动平衡问题及解决办法

风机叶轮动均衡问题及解决方法一、叶轮产生不均衡问题的主要原由叶轮在使用中产生不均衡的原由可简要分为两种:叶轮的磨损与叶轮的结垢。
造成这两种状况与引风机前接的除尘装置相关,干法除尘装置惹起叶轮不均衡的原由以磨损为主,而湿法除尘装置影响叶轮不均衡的原由以结垢为主。
现分述以下。
1.叶轮的磨损干式除尘装置固然能够除去烟气中绝大多数大颗粒的粉尘,但少许大颗粒和很多细小的粉尘颗粒伴同高温、高速的烟气一同经过引风机,使叶片遭到连续不停地冲洗。
长此过去,在叶片出口处形成刀刃状磨损。
因为这类磨损是不规则的,所以造成了叶轮的不均衡。
别的,叶轮表面在高温下很简单氧化,生成厚厚的氧化皮。
这些氧化皮与叶轮表面的结协力其实不是平均的,某些氧化皮受振动或离心力的作用会自动零落,这也是造成叶轮不均衡的一个原由。
2.叶轮的结垢经湿法除尘装置 (文丘里水膜除尘器 )净化过的烟气湿度很大,未除净的粉尘颗粒固然很小,但粘度很大。
当它们经过引风机时,在气体涡流的作用下会被吸附在叶片非工作面上,特别在非工作面的入口处与出口处形成比较严重的粉尘结垢,而且渐渐增厚。
当部分灰垢在离心力和振动的共同作用下零落时,叶轮的均衡受到损坏,整个引风机都会产生振动。
二、解决叶轮不均衡的对策1.解决叶轮磨损的方法对干式除尘惹起的叶轮磨损,除提升除尘器的除尘成效以外,最有效的方法是提升叶轮的抗磨损能力。
当前,这方面比较成熟的方法是热喷涂技术,即用特别的手段将耐磨、耐高温的金属或陶瓷等资料变为高温、高速的粒子流,喷涂到叶轮的叶片表面,形成一层比叶轮自己资料耐磨、耐高平和抗氧化性能高得多的超强外套。
这样不单可减少磨损造成叶轮动均衡的损坏,还可减少氧化层产生造成的不均衡问题。
采纳引风机时,干式除尘应优先采纳经过热喷涂办理的叶轮。
使用中未经过热喷涂办理的叶轮,在设施维修时,可考虑对叶轮进行热喷涂办理。
固然这样会增添叶轮的制造或维修花费,但却提升叶轮的使用寿命 l~2 倍,延伸了引风机的大修周期。
叶轮的静平衡和动平衡完整版
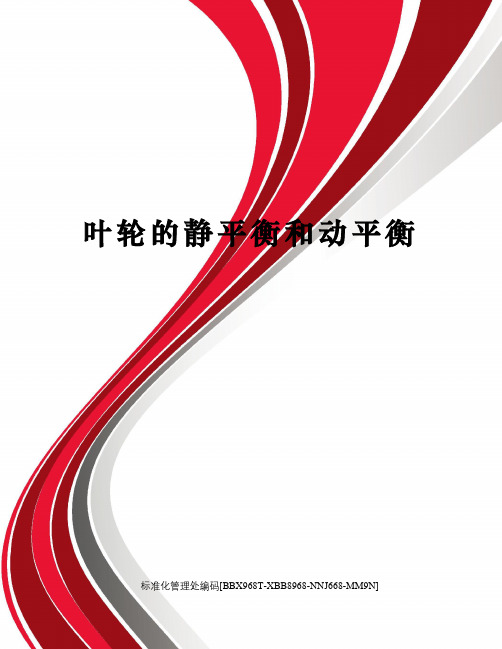
叶轮的静平衡和动平衡标准化管理处编码[BBX968T-XBB8968-NNJ668-MM9N]转子(泵叶轮)的静平衡和动平衡1、动静平衡的定义1)静平衡在转子一个校正面上进行校正平衡,校正后的剩余不平衡量,以保证转子在静态时是在许用不平衡量的规定范围内,为静平衡又称单面平衡。
2)动平衡在转子两个校正面上同时进行校正平衡,校正后的剩余不平衡量,以保证转子在动态时是在许用不平衡量的规定范围内,为动平衡又称双面平衡。
2、转子平衡的选择与确定如何选择转子的平衡方式,是一个关键问题。
其选择有这样一个原则:只要满足于转子平衡后用途需要的前提下,能做静平衡的,则不要做动平衡,能做动平衡的,则不要做静动平衡。
原因很简单,静平衡要比动平衡容易做,动平衡要比静动平衡容易做,省功、省力、省费用。
如何进行转子平衡型式的确定则需要从以下几个因素和依据来确定:1)转子的几何形状、结构尺寸,特别是转子的直径D与转子的两校正面间的距离尺寸b之比值,以及转子的支撑间距等。
2)转子的工作转速。
3)有关转子平衡技术要求的技术标准,如GB3215、API610第八版、GB9239和ISO1940等。
3、转子做静平衡的条件在GB9239-88平衡标准中,对刚性转子做静平衡的条件定义为:"如果盘状转子的支撑间距足够大并且旋转时盘状部位的轴向跳动很小,从而可忽略偶不平衡(动平衡),这时可用一个校正面校正不平衡即单面(静)平衡,对具体转子必须验证这些条件是否满足。
在对大量的某种类型的转子在一个平面上平衡后,就可求得最大的剩余偶不平衡量,并除以支撑距离。
如果在最不利的情况下这个值不大于许用剩余不平衡量的一半,则采用单面(静)平衡就足够了。
从这个定义中不难看出转子只做单面(静)平衡的条件主要有三个方面:一个是转子几何形状为盘状;一个是转子在平衡机上做平衡时的支撑间距要大;再一个是转子旋转时其校正面的端面跳动要很小。
对以上三个条件作如下说明:1)何谓盘状转子主要用转子的直径D与转子的两校正面间的距离尺寸b之比值来确定。
叶轮的静平衡和动平衡
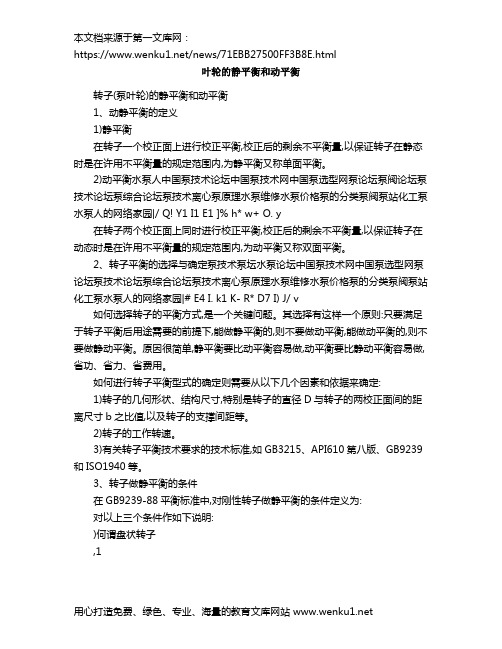
叶轮的静平衡和动平衡转子(泵叶轮)的静平衡和动平衡1、动静平衡的定义1)静平衡在转子一个校正面上进行校正平衡,校正后的剩余不平衡量,以保证转子在静态时是在许用不平衡量的规定范围内,为静平衡又称单面平衡。
2)动平衡水泵人中国泵技术论坛中国泵技术网中国泵选型网泵论坛泵阀论坛泵技术论坛泵综合论坛泵技术离心泵原理水泵维修水泵价格泵的分类泵阀泵站化工泵水泵人的网络家园|/ Q! Y1 I1 E1 ]% h* w+ O. y在转子两个校正面上同时进行校正平衡,校正后的剩余不平衡量,以保证转子在动态时是在许用不平衡量的规定范围内,为动平衡又称双面平衡。
2、转子平衡的选择与确定泵技术泵坛水泵论坛中国泵技术网中国泵选型网泵论坛泵技术论坛泵综合论坛泵技术离心泵原理水泵维修水泵价格泵的分类泵阀泵站化工泵水泵人的网络家园|# E4 I. k1 K- R* D7 I) J/ v如何选择转子的平衡方式,是一个关键问题。
其选择有这样一个原则:只要满足于转子平衡后用途需要的前提下,能做静平衡的,则不要做动平衡,能做动平衡的,则不要做静动平衡。
原因很简单,静平衡要比动平衡容易做,动平衡要比静动平衡容易做,省功、省力、省费用。
如何进行转子平衡型式的确定则需要从以下几个因素和依据来确定:1)转子的几何形状、结构尺寸,特别是转子的直径D与转子的两校正面间的距离尺寸b之比值,以及转子的支撑间距等。
2)转子的工作转速。
3)有关转子平衡技术要求的技术标准,如GB3215、API610第八版、GB9239和ISO1940等。
3、转子做静平衡的条件在GB9239-88平衡标准中,对刚性转子做静平衡的条件定义为:对以上三个条件作如下说明:)何谓盘状转子,1主要用转子的直径D与转子的两校正面间的距离尺寸b之比值来确定。
在API610第八版标准中规定D/b<6时,转子只做单面平衡就可以了;D/b≥6时可以作为转子是否为盘状转子的条件规定,但不能绝对化,因为转子做何种平衡还要考虑转子的工作转速。
风机叶轮动平衡方法
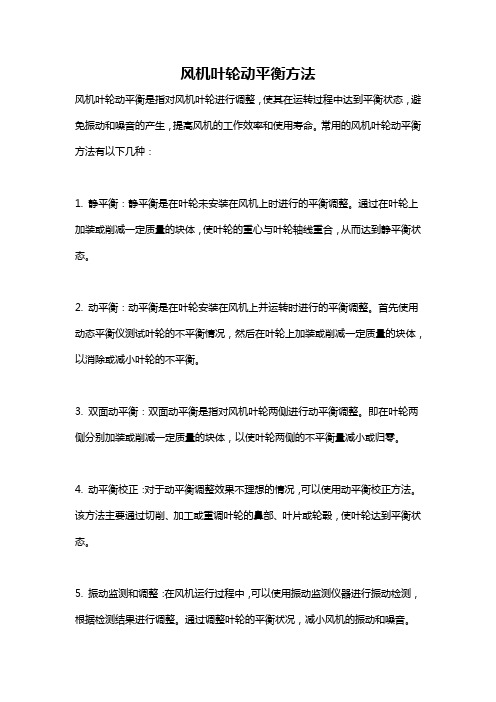
风机叶轮动平衡方法
风机叶轮动平衡是指对风机叶轮进行调整,使其在运转过程中达到平衡状态,避免振动和噪音的产生,提高风机的工作效率和使用寿命。
常用的风机叶轮动平衡方法有以下几种:
1. 静平衡:静平衡是在叶轮未安装在风机上时进行的平衡调整。
通过在叶轮上加装或削减一定质量的块体,使叶轮的重心与叶轮轴线重合,从而达到静平衡状态。
2. 动平衡:动平衡是在叶轮安装在风机上并运转时进行的平衡调整。
首先使用动态平衡仪测试叶轮的不平衡情况,然后在叶轮上加装或削减一定质量的块体,以消除或减小叶轮的不平衡。
3. 双面动平衡:双面动平衡是指对风机叶轮两侧进行动平衡调整。
即在叶轮两侧分别加装或削减一定质量的块体,以使叶轮两侧的不平衡量减小或归零。
4. 动平衡校正:对于动平衡调整效果不理想的情况,可以使用动平衡校正方法。
该方法主要通过切削、加工或重调叶轮的鼻部、叶片或轮毂,使叶轮达到平衡状态。
5. 振动监测和调整:在风机运行过程中,可以使用振动监测仪器进行振动检测,根据检测结果进行调整。
通过调整叶轮的平衡状况,减小风机的振动和噪音。
需要注意的是,风机叶轮动平衡的方法选择要根据具体情况和要求,有时可能需要结合不同的方法进行调整。
同时,在进行叶轮动平衡调整时,要保证操作安全,并严格按照相关标准和规范进行操作。
风机叶轮动平衡标准

风机叶轮动平衡标准风机叶轮动平衡是指在风机运行过程中,为了保证风机叶轮的正常运转,需要对其进行动平衡处理。
风机叶轮的动平衡是风机正常运行的基础,也是确保风机性能稳定和延长使用寿命的重要措施。
风机叶轮动平衡的标准通常要求在风机设计和制造过程中,叶轮的几何形状、质量分布和转动精度等方面都要符合一定的要求。
这些要求主要包括以下几个方面:1. 静平衡:在风机叶轮安装之前,需要进行静平衡处理。
静平衡是指在叶轮停止转动的情况下,通过调整叶轮上的质量分布,使叶轮在任何位置都能保持平衡。
静平衡的目的是消除叶轮的静不平衡力矩,确保叶轮在运行时不会出现振动和共振现象。
2. 动平衡:在风机叶轮安装之后,还需要进行动平衡处理。
动平衡是指在叶轮运转的情况下,通过调整叶轮上的质量分布,使叶轮在高速旋转时能够保持平衡。
动平衡的目的是消除叶轮的动不平衡力矩,减小叶轮的振动和噪声,提高风机的运行稳定性和可靠性。
3. 平衡质量标准:风机叶轮动平衡的质量标准通常采用国际标准ISO1940《旋转机械-平衡品质的规定》。
该标准规定了不同类型旋转机械的动平衡质量等级和振动速度限值。
根据风机的使用环境和要求,可以选择不同的动平衡质量等级和振动速度限值。
4. 动平衡方法:风机叶轮的动平衡通常采用静态平衡法、半静平衡法和动平衡法。
静态平衡法是通过在叶轮上加上固定的校正质量来达到平衡;半静平衡法是在叶轮上加上可调校的校正质量来达到平衡;动平衡法是通过在叶轮上加上可调校的校正质量和转动校正质量来达到平衡。
根据不同的叶轮结构和平衡要求,可以选择不同的动平衡方法。
5. 动平衡设备:风机叶轮的动平衡通常需要使用专用的动平衡设备。
动平衡设备主要包括平衡机、加速度传感器、转速传感器等。
平衡机可以测量和分析叶轮的动平衡状态,根据平衡结果进行校正调整。
风机叶轮的动平衡是保证风机正常运行的重要环节,符合动平衡标准可以提高风机的运行稳定性和可靠性,减小振动和噪声,延长使用寿命。
水泵叶轮动平衡标准

水泵叶轮动平衡标准
水泵叶轮的平衡是确保水泵正常运行和减少振动噪音的重要方面。
水泵叶轮的平衡通常遵循一些标准和规范,这些标准规定了叶轮的平衡质量要求、测试方法和接受标准。
以下是一些关于水泵叶轮平衡标准的信息:
1.ISO 1940-1:ISO 1940-1 是国际标准化组织(ISO)发布的标
准,规定了机械旋转部件的平衡质量要求。
这包括水泵叶轮。
ISO 1940-1 标准将平衡质量划分为不同的等级,根据叶轮的用
途和要求,可以选择适当的平衡等级。
2.API标准:美国石油学会(API)发布了一些与石油和天然气行
业相关的标准,其中包括与泵设备和叶轮平衡相关的标准。
这
些标准可能会针对特定的应用和行业需求。
3.ANSI/HI标准:美国泵制造商协会(Hydraulic Institute,HI)
发布了一些与泵和叶轮的设计和平衡相关的标准,这些标准通
常被用于工业泵和相关设备的制造。
4.国家和地区标准:不同国家和地区可能有自己的标准和规范,
用于规定水泵叶轮的平衡要求。
这些标准通常根据当地产业和
法规的需要而制定。
水泵叶轮平衡的具体要求和标准可能因应用、行业和地区而有所不同。
在设计、制造和安装水泵叶轮时,通常需要参考适用的标准和规范,以确保叶轮的平衡质量达到要求。
这可以减少振动、延长水泵的使用寿命,提高运行效率,并减少维护成本。
做叶轮动平衡的操作方法
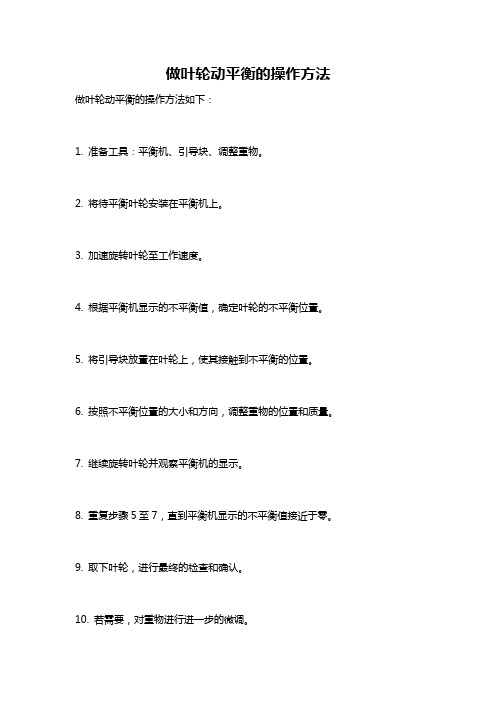
做叶轮动平衡的操作方法做叶轮动平衡的操作方法如下:
1. 准备工具:平衡机、引导块、调整重物。
2. 将待平衡叶轮安装在平衡机上。
3. 加速旋转叶轮至工作速度。
4. 根据平衡机显示的不平衡值,确定叶轮的不平衡位置。
5. 将引导块放置在叶轮上,使其接触到不平衡的位置。
6. 按照不平衡位置的大小和方向,调整重物的位置和质量。
7. 继续旋转叶轮并观察平衡机的显示。
8. 重复步骤5至7,直到平衡机显示的不平衡值接近于零。
9. 取下叶轮,进行最终的检查和确认。
10. 若需要,对重物进行进一步的微调。
11. 将平衡好的叶轮安装回原始设备中。
风机叶轮动平衡问题及解决办法

风机叶轮动平衡问题及解决办法(总4页)-CAL-FENGHAI.-(YICAI)-Company One1-CAL-本页仅作为文档封面,使用请直接删除风机叶轮动平衡问题及解决办法一、叶轮产生不平衡问题的主要原因叶轮在使用中产生不平衡的原因可简要分为两种:叶轮的磨损与叶轮的结垢。
造成这两种情况与引风机前接的除尘装置有关,干法除尘装置引起叶轮不平衡的原因以磨损为主,而湿法除尘装置影响叶轮不平衡的原因以结垢为主。
现分述如下。
1.叶轮的磨损干式除尘装置虽然可以除掉烟气中绝大部分大颗粒的粉尘,但少量大颗粒和许多微小的粉尘颗粒随同高温、高速的烟气一起通过引风机,使叶片遭受连续不断地冲刷。
长此以往,在叶片出口处形成刀刃状磨损。
由于这种磨损是不规则的,因此造成了叶轮的不平衡。
此外,叶轮表面在高温下很容易氧化,生成厚厚的氧化皮。
这些氧化皮与叶轮表面的结合力并不是均匀的,某些氧化皮受振动或离心力的作用会自动脱落,这也是造成叶轮不平衡的一个原因。
2.叶轮的结垢经湿法除尘装置(文丘里水膜除尘器)净化过的烟气湿度很大,未除净的粉尘颗粒虽然很小,但粘度很大。
当它们通过引风机时,在气体涡流的作用下会被吸附在叶片非工作面上,特别在非工作面的进口处与出口处形成比较严重的粉尘结垢,并且逐渐增厚。
当部分灰垢在离心力和振动的共同作用下脱落时,叶轮的平衡遭到破坏,整个引风机都会产生振动。
二、解决叶轮不平衡的对策1.解决叶轮磨损的方法对干式除尘引起的叶轮磨损,除提高除尘器的除尘效果之外,最有效的方法是提高叶轮的抗磨损能力。
目前,这方面比较成熟的方法是热喷涂技术,即用特殊的手段将耐磨、耐高温的金属或陶瓷等材料变成高温、高速的粒子流,喷涂到叶轮的叶片表面,形成一层比叶轮本身材料耐磨、耐高温和抗氧化性能高得多的超强外衣。
这样不仅可减轻磨损造成叶轮动平衡的破坏,还可减轻氧化层产生造成的不平衡问题。
选用引风机时,干式除尘应优先选用经过热喷涂处理的叶轮。
叶轮动平衡报告
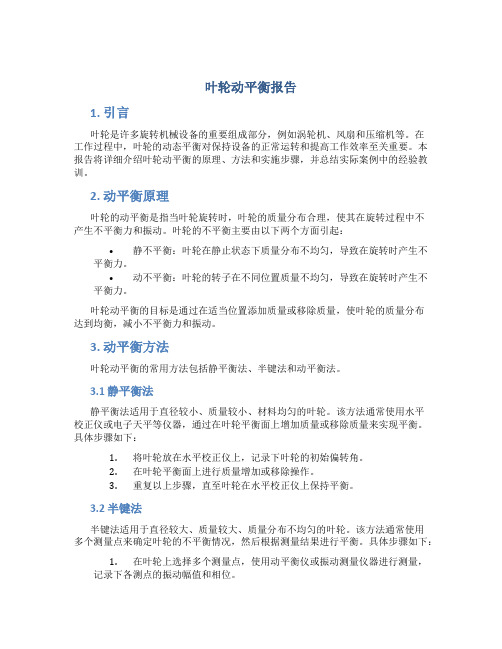
叶轮动平衡报告1. 引言叶轮是许多旋转机械设备的重要组成部分,例如涡轮机、风扇和压缩机等。
在工作过程中,叶轮的动态平衡对保持设备的正常运转和提高工作效率至关重要。
本报告将详细介绍叶轮动平衡的原理、方法和实施步骤,并总结实际案例中的经验教训。
2. 动平衡原理叶轮的动平衡是指当叶轮旋转时,叶轮的质量分布合理,使其在旋转过程中不产生不平衡力和振动。
叶轮的不平衡主要由以下两个方面引起:•静不平衡:叶轮在静止状态下质量分布不均匀,导致在旋转时产生不平衡力。
•动不平衡:叶轮的转子在不同位置质量不均匀,导致在旋转时产生不平衡力。
叶轮动平衡的目标是通过在适当位置添加质量或移除质量,使叶轮的质量分布达到均衡,减小不平衡力和振动。
3. 动平衡方法叶轮动平衡的常用方法包括静平衡法、半键法和动平衡法。
3.1 静平衡法静平衡法适用于直径较小、质量较小、材料均匀的叶轮。
该方法通常使用水平校正仪或电子天平等仪器,通过在叶轮平衡面上增加质量或移除质量来实现平衡。
具体步骤如下:1.将叶轮放在水平校正仪上,记录下叶轮的初始偏转角。
2.在叶轮平衡面上进行质量增加或移除操作。
3.重复以上步骤,直至叶轮在水平校正仪上保持平衡。
3.2 半键法半键法适用于直径较大、质量较大、质量分布不均匀的叶轮。
该方法通常使用多个测量点来确定叶轮的不平衡情况,然后根据测量结果进行平衡。
具体步骤如下:1.在叶轮上选择多个测量点,使用动平衡仪或振动测量仪器进行测量,记录下各测点的振动幅值和相位。
2.根据测量结果计算叶轮的不平衡量和位置。
3.在不平衡位置处增加质量或移除质量,重复以上步骤,直至叶轮的振动幅值和相位达到要求范围内。
3.3 动平衡法动平衡法适用于直径较大、质量较大、质量分布不均匀的叶轮。
该方法通过将叶轮放置在动平衡装置上,在旋转时利用离心力将不平衡体移至特定位置,达到平衡的目的。
具体步骤如下:1.将叶轮安装在动平衡装置上,启动叶轮旋转。
2.根据动平衡装置测量的振动幅值和相位,调整叶轮的不平衡量和位置。
风机叶轮动平衡问题及解决办法

风机叶轮动平衡问题及解决办法一、叶轮产生不平衡问题得主要原因叶轮在使用中产生不平衡得原因可简要分为两种:叶轮得磨损与叶轮得结垢。
造成这两种情况与引风机前接得除尘装置有关,干法除尘装置引起叶轮不平衡得原因以磨损为主,而湿法除尘装置影响叶轮不平衡得原因以结垢为主。
现分述如下、1.叶轮得磨损干式除尘装置虽然可以除掉烟气中绝大部分大颗粒得粉尘,但少量大颗粒与许多微小得粉尘颗粒随同高温、高速得烟气一起通过引风机,使叶片遭受连续不断地冲刷、长此以往,在叶片出口处形成刀刃状磨损。
由于这种磨损就是不规则得,因此造成了叶轮得不平衡、此外,叶轮表面在高温下很容易氧化,生成厚厚得氧化皮。
这些氧化皮与叶轮表面得结合力并不就是均匀得,某些氧化皮受振动或离心力得作用会自动脱落,这也就是造成叶轮不平衡得一个原因。
2、叶轮得结垢经湿法除尘装置(文丘里水膜除尘器)净化过得烟气湿度很大,未除净得粉尘颗粒虽然很小,但粘度很大。
当它们通过引风机时,在气体涡流得作用下会被吸附在叶片非工作面上,特别在非工作面得进口处与出口处形成比较严重得粉尘结垢,并且逐渐增厚。
当部分灰垢在离心力与振动得共同作用下脱落时,叶轮得平衡遭到破坏,整个引风机都会产生振动。
二、解决叶轮不平衡得对策1.解决叶轮磨损得方法对干式除尘引起得叶轮磨损,除提高除尘器得除尘效果之外,最有效得方法就是提高叶轮得抗磨损能力。
目前,这方面比较成熟得方法就是热喷涂技术,即用特殊得手段将耐磨、耐高温得金属或陶瓷等材料变成高温、高速得粒子流,喷涂到叶轮得叶片表面,形成一层比叶轮本身材料耐磨、耐高温与抗氧化性能高得多得超强外衣。
这样不仅可减轻磨损造成叶轮动平衡得破坏,还可减轻氧化层产生造成得不平衡问题。
选用引风机时,干式除尘应优先选用经过热喷涂处理得叶轮。
使用中未经过热喷涂处理得叶轮,在设备维修时,可考虑对叶轮进行热喷涂处理。
虽然这样会增加叶轮得制造或维修费用,但却提高叶轮得使用寿命l~2倍,延长了引风机得大修周期。
风机叶轮动平衡问题及解决办法
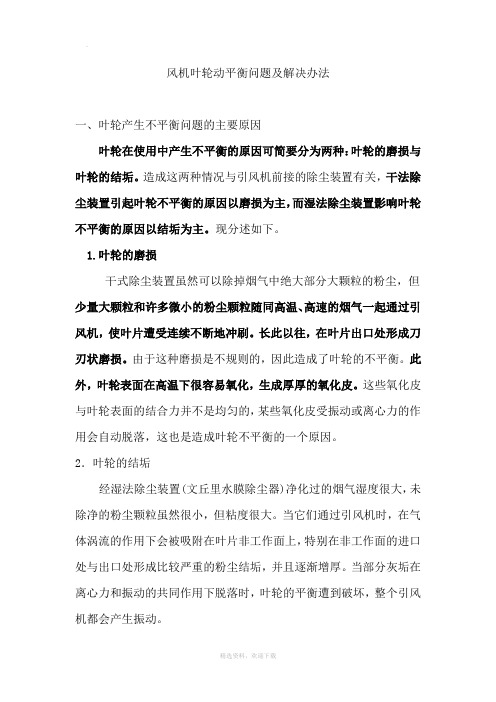
风机叶轮动平衡问题及解决办法一、叶轮产生不平衡问题的主要原因叶轮在使用中产生不平衡的原因可简要分为两种:叶轮的磨损与叶轮的结垢。
造成这两种情况与引风机前接的除尘装置有关,干法除尘装置引起叶轮不平衡的原因以磨损为主,而湿法除尘装置影响叶轮不平衡的原因以结垢为主。
现分述如下。
1.叶轮的磨损干式除尘装置虽然可以除掉烟气中绝大部分大颗粒的粉尘,但少量大颗粒和许多微小的粉尘颗粒随同高温、高速的烟气一起通过引风机,使叶片遭受连续不断地冲刷。
长此以往,在叶片出口处形成刀刃状磨损。
由于这种磨损是不规则的,因此造成了叶轮的不平衡。
此外,叶轮表面在高温下很容易氧化,生成厚厚的氧化皮。
这些氧化皮与叶轮表面的结合力并不是均匀的,某些氧化皮受振动或离心力的作用会自动脱落,这也是造成叶轮不平衡的一个原因。
2.叶轮的结垢经湿法除尘装置(文丘里水膜除尘器)净化过的烟气湿度很大,未除净的粉尘颗粒虽然很小,但粘度很大。
当它们通过引风机时,在气体涡流的作用下会被吸附在叶片非工作面上,特别在非工作面的进口处与出口处形成比较严重的粉尘结垢,并且逐渐增厚。
当部分灰垢在离心力和振动的共同作用下脱落时,叶轮的平衡遭到破坏,整个引风机都会产生振动。
二、解决叶轮不平衡的对策1.解决叶轮磨损的方法对干式除尘引起的叶轮磨损,除提高除尘器的除尘效果之外,最有效的方法是提高叶轮的抗磨损能力。
目前,这方面比较成熟的方法是热喷涂技术,即用特殊的手段将耐磨、耐高温的金属或陶瓷等材料变成高温、高速的粒子流,喷涂到叶轮的叶片表面,形成一层比叶轮本身材料耐磨、耐高温和抗氧化性能高得多的超强外衣。
这样不仅可减轻磨损造成叶轮动平衡的破坏,还可减轻氧化层产生造成的不平衡问题。
选用引风机时,干式除尘应优先选用经过热喷涂处理的叶轮。
使用中未经过热喷涂处理的叶轮,在设备维修时,可考虑对叶轮进行热喷涂处理。
虽然这样会增加叶轮的制造或维修费用,但却提高叶轮的使用寿命l~2倍,延长了引风机的大修周期。
离心泵叶轮动平衡测试操作规程
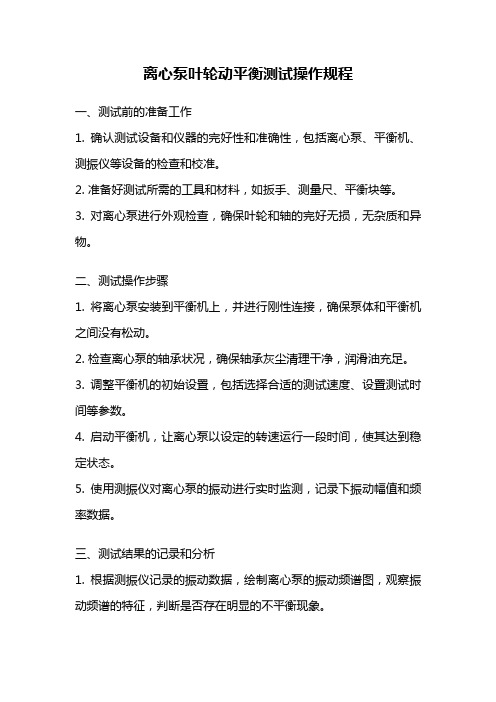
离心泵叶轮动平衡测试操作规程一、测试前的准备工作1. 确认测试设备和仪器的完好性和准确性,包括离心泵、平衡机、测振仪等设备的检查和校准。
2. 准备好测试所需的工具和材料,如扳手、测量尺、平衡块等。
3. 对离心泵进行外观检查,确保叶轮和轴的完好无损,无杂质和异物。
二、测试操作步骤1. 将离心泵安装到平衡机上,并进行刚性连接,确保泵体和平衡机之间没有松动。
2. 检查离心泵的轴承状况,确保轴承灰尘清理干净,润滑油充足。
3. 调整平衡机的初始设置,包括选择合适的测试速度、设置测试时间等参数。
4. 启动平衡机,让离心泵以设定的转速运行一段时间,使其达到稳定状态。
5. 使用测振仪对离心泵的振动进行实时监测,记录下振动幅值和频率数据。
三、测试结果的记录和分析1. 根据测振仪记录的振动数据,绘制离心泵的振动频谱图,观察振动频谱的特征,判断是否存在明显的不平衡现象。
2. 如果存在不平衡现象,根据振动频谱图确定不平衡的位置,并计算出不平衡的大小。
3. 根据不平衡的位置,在相应位置加上适量的平衡块,以提高离心泵的动平衡性能。
4. 重新进行测试,记录下调整后的振动幅值和频率数据,以验证调整效果。
四、测试后的处理和报告1. 拆卸离心泵和平衡机之间的连接,对离心泵进行外观检查,确保无损坏和杂质。
2. 对测试结果进行整理和分析,包括不平衡的位置、大小和调整效果等,编制测试报告。
3. 根据测试报告中的结果,对离心泵进行必要的调整和维修,以提高其动平衡性能。
4. 将测试报告存档,作为离心泵维护和质量控制的参考文件。
通过以上的操作规程,可以确保对离心泵叶轮的动平衡性能进行准确的测试和调整。
合理的测试操作和详细的记录可以帮助操作人员及时发现和解决离心泵叶轮的不平衡问题,提高离心泵的工作效率和安全性。
同时,定期进行离心泵叶轮的动平衡测试也是保证设备长期稳定运行的重要措施之一。
单级叶轮动平衡

单级叶轮动平衡
下面是单级叶轮动平衡的一般步骤:
1.准备工作:首先,确定叶轮的设计参数和规格,并检查叶轮的外
观和材料是否完好。
同时,确保相关设备和工具的准备就绪。
2.检测:将叶轮安装到动平衡机上,并通过传感器检测叶轮在旋转
时的振动情况。
传感器可以测量叶轮的径向振动、轴向振动和切向振动等。
3.分析:根据检测结果,利用动平衡机的软件或仪表对振动数据进
行分析和处理。
通过分析,确定叶轮的不平衡量和位置。
4.添加补偿质量:根据分析结果,在叶轮上添加相应的补偿质量来
平衡叶轮。
补偿质量可以是附加质量块或去除材料。
5.重新检测:在添加补偿质量后,重新进行振动检测,以确认叶轮
是否已经达到平衡状态。
如果仍存在不平衡,需要进行进一步的调整和重复检测的过程。
6.完成和记录:一旦叶轮达到平衡状态,将其从动平衡机上取下,
并记录平衡前后的振动数据、调整量和位置等信息。
这些记录对于以后的维护和调试非常重要。
大型引风机叶轮的动平衡问题及对策

大型引风机叶轮的动平衡问题及对策大型引风机叶轮的动平衡问题及对策一、叶轮产生不平衡问题的主要原因叶轮在使用中产生不平衡的原因可简要分为两种:叶轮的磨损与叶轮的结垢。
造成这两种情况与引风机前接的除尘装置有关,干法除尘装置引起叶轮不平衡的原因以磨损为主,而湿法除尘装置影响叶轮不平衡的原因以结垢为主。
现分述如下。
1.叶轮的磨损干式除尘装置虽然可以除掉烟气中绝大部分大颗粒的粉尘,但少量大颗粒和许多微小的粉尘颗粒随同高温、高速的烟气一起通过引风机,使叶片遭受连续不断地冲刷。
长此以往,在叶片出口处形成刀刃状磨损。
由于这种磨损是不规则的,因此造成了叶轮的不平衡。
此外,叶轮表面在高温下很容易氧化,生成厚厚的氧化皮。
这些氧化皮与叶轮表面的结合力并不是均匀的,某些氧化皮受振动或离心力的作用会自动脱落,这也是造成叶轮不平衡的一个原因。
2.叶轮的结垢经湿法除尘装置(文丘里水膜除尘器)净化过的烟气湿度很大,未除净的粉尘颗粒虽然很小,但粘度很大。
当它们通过引风机时,在气体涡流的作用下会被吸附在叶片非工作面上,特别在非工作面的进口处与出口处形成比较严重的粉尘结垢,并且逐渐增厚。
当部分灰垢在离心力和振动的共同作用下脱落时,叶轮的平衡遭到破坏,整个引风机都会产生振动。
二、解决叶轮不平衡的对策1.解决叶轮磨损的方法对干式除尘引起的叶轮磨损,除提高除尘器的除尘效果之外,最有效的方法是提高叶轮的抗磨损能力。
目前,这方面比较成熟的方法是热喷涂技术,即用特殊的手段将耐磨、耐高温的金属或陶瓷等材料变成高温、高速的粒子流,喷涂到叶轮的叶片表面,形成一层比叶轮本身材料耐磨、耐高温和抗氧化性能高得多的超强外衣。
这样不仅可减轻磨损造成叶轮动平衡的破坏,还可减轻氧化层产生造成的不平衡问题。
选用引风机时,干式除尘应优先选用经过热喷涂处理的叶轮。
使用中未经过热喷涂处理的叶轮,在设备维修时,可考虑对叶轮进行热喷涂处理。
虽然这样会增加叶轮的制造或维修费用,但却提高叶轮的使用寿命l~2倍,延长了引风机的大修周期。
烟机叶轮动平衡

烟机叶轮动平衡
烟机叶轮动平衡是指对烟机的叶轮进行动态平衡调整以达到更好的运转效果。
在使用烟机的过程中,叶轮存在不平衡现象,这会导致烟机运转时产生振动和噪音,甚至损坏机器。
为了避免这些问题的发生,需要对烟机叶轮进行动平衡调整。
烟机叶轮动平衡的过程包括测量叶轮的不平衡量,确定不平衡量的位置和大小,并在相应位置加上平衡重块,最终验证是否达到平衡状态。
动平衡的目的是使叶
轮在运转时达到最佳的运转效果,减少能耗和噪音,同时也保护烟机主体的安全和稳定运转。
对于烟机生产厂家和用户而言,烟机叶轮动平衡是一项十分重要的技术活动,它直接关系到烟机的运转效率和使用寿命。
只有在保证烟机叶轮动平衡的情况下,才能达到更好的使用效果和安全保障。
叶轮动平衡 测试原理
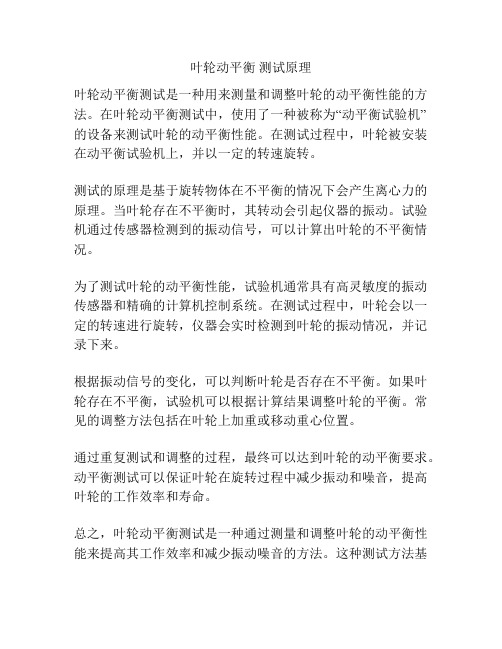
叶轮动平衡测试原理
叶轮动平衡测试是一种用来测量和调整叶轮的动平衡性能的方法。
在叶轮动平衡测试中,使用了一种被称为“动平衡试验机”的设备来测试叶轮的动平衡性能。
在测试过程中,叶轮被安装在动平衡试验机上,并以一定的转速旋转。
测试的原理是基于旋转物体在不平衡的情况下会产生离心力的原理。
当叶轮存在不平衡时,其转动会引起仪器的振动。
试验机通过传感器检测到的振动信号,可以计算出叶轮的不平衡情况。
为了测试叶轮的动平衡性能,试验机通常具有高灵敏度的振动传感器和精确的计算机控制系统。
在测试过程中,叶轮会以一定的转速进行旋转,仪器会实时检测到叶轮的振动情况,并记录下来。
根据振动信号的变化,可以判断叶轮是否存在不平衡。
如果叶轮存在不平衡,试验机可以根据计算结果调整叶轮的平衡。
常见的调整方法包括在叶轮上加重或移动重心位置。
通过重复测试和调整的过程,最终可以达到叶轮的动平衡要求。
动平衡测试可以保证叶轮在旋转过程中减少振动和噪音,提高叶轮的工作效率和寿命。
总之,叶轮动平衡测试是一种通过测量和调整叶轮的动平衡性能来提高其工作效率和减少振动噪音的方法。
这种测试方法基
于旋转物体在不平衡的情况下会产生离心力的原理,通过振动传感器和计算机控制系统来实现。
- 1、下载文档前请自行甄别文档内容的完整性,平台不提供额外的编辑、内容补充、找答案等附加服务。
- 2、"仅部分预览"的文档,不可在线预览部分如存在完整性等问题,可反馈申请退款(可完整预览的文档不适用该条件!)。
- 3、如文档侵犯您的权益,请联系客服反馈,我们会尽快为您处理(人工客服工作时间:9:00-18:30)。
叶轮动平衡
如何解决风机叶轮动平衡问题
企业要实现设备管理现代化,应当积极推行先进的设备管理方法和采取以设备状态监测为基础的设备维修技术。
设备状态监测及故障诊断技术是设备预防性维修的前提。
特别是重工企业,工作连续性强及安全可靠性要求高,通过状态监测的推广,可以逐步掌握水泵、风机等大、中型设备的工作状态,以杜绝事故停机损失。
如何解决风机叶轮动平衡问题,就要亚泰光电告诉你。
一、叶轮产生不平衡问题的主要原因叶轮在使用中产生不平衡的原因可简要分为两种:叶轮的磨损与叶轮的结垢。
造成这两种情况与引风机前接的除尘装置有关,干法除尘装置引起叶轮不平衡的原因以磨损为主,而湿法除尘装置影响叶轮不平衡的原因以结垢为主。
现分述如下。
1.叶轮的磨损干式除尘装置虽然可以除掉烟气中绝大部分大颗粒的粉尘,但少量大颗粒和许多微小的粉尘颗粒随同高温、高速的烟气一起通过引风机,使叶片遭受连续不断地冲刷。
长此以往,在叶片出口处形成刀刃状磨损。
由于这种磨损是不规则的,因此造成了叶轮的不平衡。
此外,叶轮表面在高温下很容易氧化,生成厚厚的氧化皮。
这些氧化皮与叶轮表面的结合力并不是均匀的,某些氧化皮受振动或离心力的作用会自动脱落,这也是造成叶轮不平衡的一个原因。
2.叶轮的结垢经湿法除尘装置(文丘里水膜除尘器)净化过的烟气湿度很大,未除净的粉尘颗粒虽然很小,但粘度很大。
当它们通过引风机时,在气体涡流的作用下会被吸附在叶片非工作面上,特别在非工作面的进口处与出口处形成比较严重的粉尘结垢,并且逐渐增厚。
当部分灰垢在离心力和振动的共同作用下脱落时,叶轮的平衡遭到破坏,整个引风机都会产生振动。
二、解决叶轮不平衡的对策 1.解决叶轮磨损的方法对干式除尘引起的叶轮磨损,除提高除尘器的除尘效果之外,最有效的方法是提高叶轮的抗磨损能力。
目前,这方面比较成熟的方法是热喷涂技术,即用特殊的手段将耐磨、耐高温的金属或陶瓷等材料变成高温、高速的粒子流,喷涂到叶轮的叶片表面,形成一层比叶轮本身材料耐磨、耐高温和抗氧化性能高得多的超强外衣。
这样不仅可减轻磨损造成叶轮动平衡的破坏,还可减轻氧化层产生造成的不平衡问题。
选用引风机时,干式除尘应优先选用经过热喷涂处理的叶轮。
使用中未经过热喷涂处理的叶轮,在设备维修时,可考虑对叶轮进行热喷涂处理。
虽然这样会增加叶轮的制造或维修费用,但却提高叶轮的使用寿命l~2倍,延长了引风机的大修周期。
从而降低了引风机和整个生产系统的运行成本,综合效益很好。
2.解决叶轮结垢的方法 (1)喷水除垢:这是一种常用的除垢方法,喷水系统装在引风机的机壳上,由管道、3个喷嘴(1个位于叶轮出口处,2个位于进口处)及排水孔组成。
水源一般为自来水,压力约0.3MPa。
这种方法通常还是有效的。
缺点是每次停机除垢的时间较长,每月需停机数次进行除垢。
影响机组的正常使用。
(2)高压气体除垢:该系统采用与喷水系统相似的结构,但其管道为耐高压管道、专用的喷嘴和高压气源。
这种装置对叶片的除垢是快速有效的,它可以在引风机正常停机的间隙,开启高压气源,仅用数十秒的时间即可完成除垢。
由于操作简单方便,一天可以进行许多次,不但解决了人工除垢费力、费时的问题,还明显降低了整个机组的生产成本。
问题是用户是否有现成的高压气源(压力在0.8~1.5MPa之间,可以用压缩空气或氮气),否则,需要专用的高压压缩机设备。
(3)气流连续吹扫除垢:从结构上讲,连续吹扫装置不需要外部气源,它利用引风机本身的排气压力,将少量的烟气(额定风量的1%~2%)从引风机的内部引向专用喷嘴,喷嘴位于叶轮的进口,以很高的速度将烟气咳射到叶片的非工作表面,这种吹扫是连续地,它随着引风机的开启而开始,不但将刚刚粘到叶片上的粉尘吹掉,还可防止粉尘沉积加厚,且无需停机除垢。
该装置结构简单、对引风机改动量很小,防结垢效果很好,是一种很有发展的新技术。
3.叶轮动平衡的校正无论是采用热喷涂处理的叶轮,还是采用各种方法除垢的叶轮,其效果都不会一劳永逸。
引风机在长期使用后,仍会出现振动超过允许上限值阶情况。
此时,叶轮的不平衡问题只能通过动平衡校正来解决。