铸造、热处理、锻造工艺基础
铸造工艺基础知识及理论

铸造工艺基础知识及理论目录一、基础概念 (2)1.1 铸造的定义与意义 (3)1.2 铸造工艺的种类与应用 (4)二、铸造材料 (6)三、铸造设备 (7)3.1 熔炼设备 (9)3.2 锻造设备 (10)3.3 后处理设备 (11)四、铸造工艺过程 (12)五、铸造工艺设计 (13)5.1 工艺方案的确定 (15)5.2 工艺参数的选择 (16)5.3 工艺文件的编制 (18)六、铸造质量与控制 (20)6.1 铸造缺陷的产生原因及防止措施 (22)6.2 铸造质量检测方法与标准 (23)七、铸造生产与环境 (24)7.1 铸造生产的环保要求 (26)7.2 环保设备的应用与管理 (27)八、现代铸造技术的发展趋势 (28)8.1 快速凝固与近净形铸造技术 (30)8.2 数字化与智能化铸造技术 (31)8.3 生物铸造与绿色铸造技术 (33)一、基础概念铸造工艺是指将熔炼好的液态金属浇入铸型,待其凝固后获得所需形状和性能的金属制品的过程。
它是制造业中非常重要的工艺之一,广泛应用于汽车、航空、建筑、电子等领域。
铸造工艺的基础知识主要包括液态金属的性质、铸型(即模具)的设计与制造、浇注系统、凝固过程以及后处理等。
这些知识是理解和掌握铸造工艺的基本前提。
液态金属的性质:液态金属在铸造过程中的流动性、填充能力、冷却速度等对其最终的产品质量有着决定性的影响。
了解液态金属的成分、温度、粘度等基本性质对于铸造工艺的设计和实践都是非常重要的。
铸型的设计与制造:铸型是形成金属制品形状和内部结构的重要工具。
铸型的设计需要考虑到金属液的流动性和凝固特性,以及制品的精度和表面质量要求。
铸型的制造也需要选用合适的材料,并经过精密加工才能达到设计要求。
浇注系统:浇注系统是连接铸型和液态金属的通道,包括浇口杯、直浇道、横浇道和内浇道等部分。
合理的浇注系统设计可以确保金属液均匀地注入铸型,并有利于热量和气体的排出,从而提高制品的质量和生产效率。
金属材料的工艺性能

金属材料的工艺性能金属材料的工艺性能是指制造工艺过程中材料适应加工的性能,即指其铸造性能、锻造性能、焊接性能、切削加工性能和热处理工艺性能。
1、铸造性能金属材料铸造成形获得优良铸件的能力称为铸造性能,用流动性、收缩性和偏析来衡量。
1)流动性熔融金属的流动能力称为流动性。
流动性好的金属容易充满铸型,从而获得外形完整和尺寸精确、轮廓清晰的铸件;2)收缩性铸件在凝固和冷却的过程中,其体积和尺寸减少的现象称为收缩性。
铸件用金属材料的收视率越小越好;3)偏析铸锭或铸件化学成分和组织的不均匀现象称为偏析,偏析大会使铸件各部分的力学性能有很大的差异,降低铸件的质量。
被铸物质多为原为固态,但加热至液态的金属,如铜、铁、锡等,铸模的材料可以是沙,金属甚至陶瓷。
南关菜市场东头前两年有两个人把大量的铝易拉罐盒熔化后倒进模子里铸成大大小小的铝锅、铝盆等2、锻造性工业革命前锻造是普遍的金属加工工艺,马蹄铁、冷兵器、铠甲均由各国的铁匠手锻造(俗称打铁),金银首饰加工、金属包装材料是锻造与冲压的总和。
什么是锻造性能?锻造性能:金属材料用锻压加工方法成形的适应能力称锻造性。
锻造性主要取决于金属材料的塑性和变形抗力。
塑性越好,变形抗力越小,金属的锻造性能越好。
高碳钢不易锻造,高速钢更难。
(塑性:断裂前材料产生永久变形的能力。
)3、焊接性金属材料对焊接加工的适应性成为焊接性。
也就是在一定的焊接工艺条件下,获得优质焊接接头的难易程度。
钢材的含碳量高低是焊接性能好坏的主要因素,含碳量和合金元素含量越高,焊接性能越差。
4、切削加工性能切削加工性能一般用切削后的表面质量(用表面粗糙程度高低衡量)和道具寿命来表示。
金属材料具有适当的硬度和足够的脆性时切削性良好。
改变钢的化学成分(如加入少量铅、磷等元素)和进行适当的热处理(如低碳钢进行正火,高碳钢进行球化退火)可以提高刚的切削加工性能。
(热处理的四把火:正火、退火、淬火、回火等,后面我们将进一步学习。
机械零件的加工工艺与热处理方法

机械零件的加工工艺与热处理方法一、机械零件加工工艺机械零件加工工艺是指将原始材料通过一系列的加工工艺,如锻造、铸造、车削、铣削、磨削等方法,制造成符合要求的零件的过程。
下面将介绍几种常见的机械零件加工工艺。
1. 锻造锻造是指通过对金属材料进行冲击或压缩,改变其形状和尺寸的工艺。
常见的锻造方法有冲击锻造、自由锻造和模锻造等。
锻造工艺可以提高金属材料的强度和硬度,改善其内部组织结构,使零件具有良好的力学性能。
2. 铸造铸造是指将熔化的金属注入到铸型中,经过冷却凝固后得到所需形状的零件的工艺。
铸造工艺可以制造出形状复杂的零件,并且可以利用铸造工艺制造大型零件。
常见的铸造方法有砂型铸造、金属型铸造和压力铸造等。
3. 车削车削是指通过旋转工件,利用切削刀具对工件进行加工的工艺。
车削可以加工各种形状的零件,如轴、孔、齿轮等。
车削工艺可以提高零件的精度和表面质量。
4. 铣削铣削是指通过旋转刀具,将工件表面的材料切削下来,得到所需形状的工艺。
铣削可以加工平面、曲面和复杂形状的零件。
铣削工艺可以提高零件的精度和表面质量。
5. 磨削磨削是指通过磨粒对工件表面进行切削,得到所需精度和表面质量的工艺。
磨削可以加工高硬度材料和精密零件。
磨削工艺可以提高零件的尺寸精度和表面质量。
二、机械零件的热处理方法热处理是指通过加热、保温和冷却等工艺,改变材料的组织结构和性能的方法。
下面将介绍几种常见的机械零件热处理方法。
1. 淬火淬火是指将工件加热到临界温度以上,然后迅速冷却到室温的工艺。
淬火可以使金属材料快速冷却,从而改善其硬度和强度。
淬火后的零件具有较高的硬度和耐磨性,但也较脆。
2. 回火回火是指将已经淬火的零件加热到一定温度,然后保温一段时间,最后冷却到室温的工艺。
回火可以消除淬火过程中产生的内部应力,提高零件的韧性和韧度。
3. 等温淬火等温淬火是指将工件加热到临界温度以上,保温一段时间,然后迅速冷却到室温的工艺。
等温淬火可以使零件具有较高的硬度和强度,并且能够保持较好的韧性。
铸造工艺和锻造工艺

1、铸造:就是将金属熔炼成符合一定要求液体并浇进铸型里,经冷却凝固、清整处理后得到有预定形状、尺寸和性能铸件(零件或毛坯)工艺过程。
现代机械制造工业基础工艺。
铸造生产毛坯成本低廉,对于形状复杂、尤其是含有复杂内腔零件,更能显示出它经济性;同时它适应性较广,且含有很好综合机械性能。
但铸造生产所需材料(如金属、木材、燃料、造型材料等)和设备(如冶金炉、混砂机、造型机、造芯机、落砂机、抛丸机、铸铁平板等)较多,且会产生粉尘、有害气体和噪声而污染环境。
铸造是人类掌握较早一个金属热加工工艺,已经有约6000年历史。
公元前3200年,美索不达米亚出现铜青蛙铸件。
公元前13~前10世纪之间,中国已进入青铜铸件全盛时期,工艺上已达成相当高水平,如商代重875千克司母戊方鼎、战国曾侯乙尊盘和西汉透光镜等全部是古代铸造代表产品。
早期铸造受陶器影响较大,铸件大多为农业生产、宗教、生活等方面工具或用具,艺术色彩较浓。
公元前513年,中国铸出了世界上最早见于文字记载铸铁件——晋国铸鼎(约270千克重)。
公元8世纪前后,欧洲开始生产铸铁件。
18世纪工业**后,铸件进入为大工业服务新时期。
进入20世纪,铸造发展速度很快,前后开发出球墨铸铁,可锻铸铁,超低碳不锈钢和铝铜、铝硅、铝镁合金,钛基、镍基合金等铸造金属材料,并发明了对灰铸铁进行孕育处理新工艺。
50年代以后,出现了湿砂高压造型,化学硬化砂造型和造芯、负压造型和其它特种铸造、抛丸清理等新工艺。
铸造种类很多,按造型方法习惯上分为:①一般砂型铸造,包含湿砂型、干砂型和化学硬化砂型3类。
②特种铸造,按造型材料又可分为以天然矿产砂石为关键造型材料特种铸造(如熔模铸造、泥型铸造、铸造车间壳型铸造、负压铸造、实型铸造、陶瓷型铸造等)和以金属为关键铸型材料特种铸造(如金属型铸造、压力铸造、连续铸造、低压铸造、离心铸造等)两类。
铸造工艺通常包含:①铸型(使液态金属成为固态铸件容器)准备,铸型按所用材料可分为砂型、金属型、陶瓷型、泥型、石墨型等,按使用次数可分为一次性型、半永久型和永久型,铸型准备优劣是影响铸件质量关键原因;②铸造金属熔化和浇注,铸造金属(铸造合金)关键有铸铁、铸钢和铸造有色合金;③铸件处理和检验,铸件处理包含清除型芯和铸件表面异物、切除浇冒口、铲磨毛刺和披缝等凸出物和热处理、整形、防锈处理和粗加工等。
铸造教案(一)

铸造教案(一)【教学组织】1.提问10分钟2.讲解70分钟3.小结5分钟4.布置作业5分钟5.两课时【教学内容】第四章金属热加工基础●热加工是在较高温度(高于再结晶温度)下对金属材料进行加工的方法。
热加工通常包括热处理、铸造、热轧、锻造、焊接、热切割、热喷涂等工艺。
第一节铸造成形●铸造是指熔炼金属,制造铸型,并将熔融金属浇入与零件形状相适应的铸型中,待液态金属凝固后获得一定形状、尺寸和性能的金属零件或毛坯的成形方法。
●用铸造成形方法得到的毛坯称为铸件。
一、铸造基础知识1.铸造方法分类铸造方法主要分为砂型铸造和特种铸造两类。
●砂型铸造是指在砂型中生产铸件的铸造方法。
●特种铸造是指与砂型铸造不同的其他铸造方法。
特种铸造包括金属型铸造、压力铸造、离心铸造、熔模铸造、低压铸造、陶瓷型铸造、连续铸造和挤压铸造等。
2.铸造特点(1)铸造适应性广。
(2)铸造具有较好的经济性。
(3)铸件力学性能较低。
二、砂型铸造1.造型材料、造型工具及砂型组成(1)造型材料。
●制造铸型用的材料称为造型材料。
造型材料主要包括型砂和芯砂。
型砂和芯砂主要由原砂(SiO2)、粘结剂(如粘土、膨润土、水玻璃、植物油、树脂等)、附加物(如煤粉或木屑等)、旧砂和水组成。
造型材料应具备一定的强度、可塑性、耐火性、透气性、退让性和溃散性等性能。
(2)造型工具。
●制造铸型用的工具称为造型工具。
造型工具有:砂箱、底板、舂砂锤、通气针、起模针、皮老虎、镘刀、秋叶、提钩、半圆等。
(3)砂型组成。
●从砂型中取出模样后形成的空腔称为型腔。
●上砂型与下砂型的分界面称为分型面。
●型芯上的延伸部分称为芯头,用于安放和固定型芯。
图4-5 砂型组成示意图2.造型方法●用型砂及模样等工艺装备制造砂型的方法和过程,称为造型。
造型方法通常分为手工造型和机器造型两大类。
(1)手工造型。
●全部用手或手动工具完成的造型工序称为手工造型。
①整体模造型。
●整体模造型是将模样做成与零件形状相应的整体结构进行造型的方法。
导轨的生产工艺

导轨是一种重要的机械基础件,广泛应用于机床、自动化设备、航空航天等领域。
导轨的生产工艺一般包括以下几个步骤:
1.材料选择:导轨的材料一般为钢材或不锈钢等金属材料,要求材料具有高强度、高硬度和高耐磨性等特点。
2.铸造或锻造:导轨的制造一般采用铸造或锻造工艺,将金属材料熔化后浇注或锻造成所需的形状和尺寸。
3.热处理:为了提高导轨的硬度和耐磨性,需要进行热处理。
一般采用淬火、回火等工艺,使导轨具有所需的机械性能。
4.加工:导轨的加工包括车削、磨削、铣削等工艺,以使导轨表面平整、光滑,尺寸精度高,并符合所需的几何形状和尺寸。
5.表面处理:导轨的表面处理一般包括电镀、喷涂等工艺,以提高导轨的耐腐蚀性和美观性。
6.检验和质量控制:导轨的生产过程中需要进行严格的检验和质量控制,以确保导轨符合所需的规格和标准,并具有良好的机械性能和使用寿命。
以上是导轨的主要生产工艺流程,具体的生产工艺还需要根据不同的应用场合和要求进行调整和优化。
铸造教案(一)
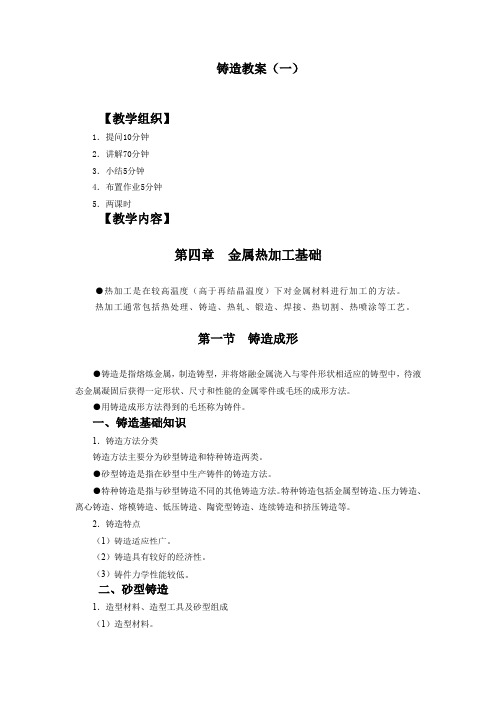
铸造教案(一)【教学组织】1.提问10分钟2.讲解70分钟3.小结5分钟4.布置作业5分钟5.两课时【教学内容】第四章金属热加工基础●热加工是在较高温度(高于再结晶温度)下对金属材料进行加工的方法。
热加工通常包括热处理、铸造、热轧、锻造、焊接、热切割、热喷涂等工艺。
第一节铸造成形●铸造是指熔炼金属,制造铸型,并将熔融金属浇入与零件形状相适应的铸型中,待液态金属凝固后获得一定形状、尺寸和性能的金属零件或毛坯的成形方法。
●用铸造成形方法得到的毛坯称为铸件。
一、铸造基础知识1.铸造方法分类铸造方法主要分为砂型铸造和特种铸造两类。
●砂型铸造是指在砂型中生产铸件的铸造方法。
●特种铸造是指与砂型铸造不同的其他铸造方法。
特种铸造包括金属型铸造、压力铸造、离心铸造、熔模铸造、低压铸造、陶瓷型铸造、连续铸造和挤压铸造等。
2.铸造特点(1)(2)铸造具有较好的经济性。
(3)二、砂型铸造1.造型材料、造型工具及砂型组成(1)造型材料。
●制造铸型用的材料称为造型材料。
造型材料主要包括型砂和芯砂。
型砂和芯砂主要由原砂(SiO2)、粘结剂(如粘土、膨润土、水玻璃、植物油、树脂等)、附加物(如煤粉或木屑等)、旧砂和水组成。
造型材料应具备一定的强度、可塑性、耐火性、透气性、退让性和溃散性等性能。
(2)造型工具。
●制造铸型用的工具称为造型工具。
造型工具有:砂箱、底板、舂砂锤、通气针、起模针、皮老虎、镘刀、秋叶、提钩、半圆等。
(3)砂型组成。
●从砂型中取出模样后形成的空腔称为型腔。
●上砂型与下砂型的分界面称为分型面。
●型芯上的延伸部分称为芯头,用于安放和固定型芯。
图4-5 砂型组成示意图2.造型方法●用型砂及模样等工艺装备制造砂型的方法和过程,称为造型。
造型方法通常分为手工造型和机器造型两大类。
(1)手工造型。
●全部用手或手动工具完成的造型工序称为手工造型。
①整体模造型。
●整体模造型是将模样做成与零件形状相应的整体结构进行造型的方法。
锻造工艺知识点总结

锻造工艺知识点总结1. 材料准备在锻造工艺中,材料的选择对成品的质量和性能有着直接的影响。
常见的锻造材料包括碳钢、合金钢、不锈钢、铝合金、铜合金等。
在选择材料时,需要考虑其机械性能、化学成分、热处理性能等因素。
同时,还需要根据锻造零件的形状、尺寸和用途来确定材料的种类和规格。
在准备材料时,需要注意保持材料的表面清洁,并严格控制材料的质量。
2. 设备操作锻造设备是进行锻造工艺的关键设备,其操作技术和安全生产是非常重要的。
常见的锻造设备包括锻造机、冷镦机、液压机等。
在设备操作过程中,需要严格遵守操作规程,正确使用设备,保持设备的良好状态。
同时,还需要对设备进行定期检查和维护,及时发现和排除设备故障,确保设备的安全和稳定运行。
3. 工艺参数在进行锻造工艺时,需要控制一定的工艺参数,以确保锻造件的质量和形状。
常见的工艺参数包括温度、压力、锻造速度、模具形状等。
在锻造过程中,需要根据不同的材料和锻造件的形状和尺寸来确定合适的工艺参数。
通过合理控制工艺参数,可以有效地提高锻造件的性能和表面质量。
4. 质量控制质量控制是锻造工艺的重要环节,对于保证锻造件的质量和性能至关重要。
在进行锻造过程中,需要对每一道工序进行质量检验和控制,确保每一个工艺环节的质量达标。
在锻造件成形后,还需要对其进行尺寸测量、力学性能测试、表面质量检查等多项质量检验,以验证其质量和性能是否满足要求。
总之,锻造工艺是一项复杂而又重要的金属加工工艺,需要掌握一定的知识和技能。
在实际生产中,需要严格按照工艺流程和操作规程进行操作,确保锻造件的质量和性能。
希望通过本文的总结,能够对锻造工艺有更深入的了解和认识,为相关从业人员提供一定的参考和指导。
汽车生产制造工艺过程中的七大制造工艺

汽车生产制造工艺过程中的七大制造工艺摘要:汽车模具生产中采用了多种制造工艺。
生产中常用的制造工艺有七种:铸造、锻造、冷冲压、焊接、金属切削、热处理和装配。
这七种制造工艺各有其特点和用途。
关键词:汽车;模具;制造;汽车生产在汽车模具生产中,需要大量的加工工艺,在生产过程中,我们最熟悉的是七种生产工艺,它们有着悠久的历史,随着高效率和高技术的发展,一些传统的制造工艺得到了改进。
一、汽车生产制造工艺铸造铸造是将熔化的金属倒入铸模的型腔中,冷却并凝固,从而生产产品的一种方法。
在汽车制造过程中,有许多铸铁零件,占汽车总重量的10%左右,如气缸体、变速箱、转向器壳、后桥壳、制动鼓、各种支架等,通常用砂型模具来制造。
砂型主要由砂制成,掺有粘结剂和水。
砂模材料必须有一定的粘结强度,使之能被塑成所需的形状,并能在不倒塌的情况下抵抗铁水的冲刷。
为了在砂型中形成符合铸件形状的型腔,模型必须由木材制成,称为木模。
热金属的体积在冷却后会收缩。
因此,在铸件原有尺寸的基础上,根据收缩率增大木模尺寸,加工表面相应变厚。
空心铸件需要制成砂芯和相应的芯木模具(芯盒)。
用木模,空心砂模可以转动(铸件也被称为“翻砂”)。
二、汽车生产制造工艺锻造汽车齿轮、车轴毛坯采用自由锻造加工。
模锻是将金属坯放入锻模腔中,承受冲击或压力而成形的一种方法。
模型锻造有点像面团在模具中被压成饼干形状的过程。
与自由锻造相比,模锻生产的工件形状和尺寸更为复杂和精确。
汽车模锻的典型例子有:发动机连杆和曲轴、汽车前轴、转向节等。
三、汽车生产制造工艺冷冲压冷冲压或板料冲压是使金属板料在冲模中承受压力而被切离或成形的加工方法。
日常生活用品,女口铝锅、饭盒、脸盆等就是采用冷冲压的加工方法制成。
例如制造饭盒,首先需要切出长方形并带有4个圆角的坯料(行家称为“落料”),然后用凸模将这块坯料压入凹模而成形(行家称为“拉深”)。
在拉深工序,平面的板料变为盒状,其4边向上垂直弯曲,4个拐角的材料产生堆聚并可看到皱褶。
铸造锻造工艺流程
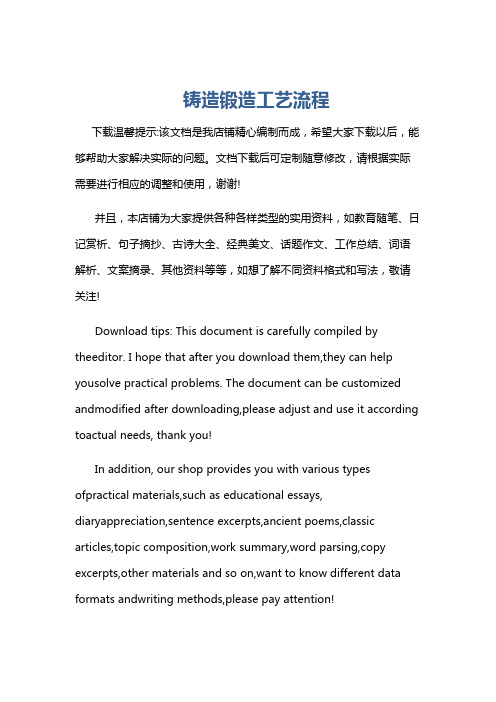
铸造锻造工艺流程下载温馨提示:该文档是我店铺精心编制而成,希望大家下载以后,能够帮助大家解决实际的问题。
文档下载后可定制随意修改,请根据实际需要进行相应的调整和使用,谢谢!并且,本店铺为大家提供各种各样类型的实用资料,如教育随笔、日记赏析、句子摘抄、古诗大全、经典美文、话题作文、工作总结、词语解析、文案摘录、其他资料等等,如想了解不同资料格式和写法,敬请关注!Download tips: This document is carefully compiled by theeditor. I hope that after you download them,they can help yousolve practical problems. The document can be customized andmodified after downloading,please adjust and use it according toactual needs, thank you!In addition, our shop provides you with various types ofpractical materials,such as educational essays, diaryappreciation,sentence excerpts,ancient poems,classic articles,topic composition,work summary,word parsing,copy excerpts,other materials and so on,want to know different data formats andwriting methods,please pay attention!铸造锻造工艺流程一、准备工作阶段在开始铸造锻造工艺之前,需要进行全面细致的准备。
锻造基础知识大汇集

锻造基础知识大汇集 Document number:WTWYT-WYWY-BTGTT-YTTYU-2018GTforming1950专注锻造、冲压、钣金成形行业,汇聚作者与读者、用户与装配商、行业与市场最新动态,通过行业市场类、技术交互类、技术文章类题材为锻压行业打造一流的交流学习、技术传播、信息服务平台。
锻造工艺(Forging Process)是一种利用锻压机械对金属坯料施加压力,使其产生塑性变形以获得具有一定机械性能、一定形状和尺寸锻件的加工方法,锻压(锻造与冲压)的两大组成部分之一。
变形温度钢的开始再结晶温度约为727℃,但普遍采用800℃作为划分线,高于800℃的是热锻;在300~800℃之间称为温锻或半热锻。
坯料根据坯料的移动方式,锻造可分为自由锻、镦粗、挤压、模锻、闭式模锻、闭式镦锻。
1、自由锻。
利用冲击力或压力使金属在上下两个抵铁(砧块)间产生变形以获得所需锻件,主要有手工锻造和机械锻造两种。
2、模锻。
模锻又分为开式模锻和闭式模锻.金属坯料在具有一定形状的锻模膛内受压变形而获得锻件,又可分为冷镦、辊锻、径向锻造和挤压等等。
3、闭式模锻和闭式镦锻由于没有飞边,材料的利用率就高。
用一道工序或几道工序就可能完成复杂锻件的精加工。
由于没有飞边,锻件的受力面积就减少,所需要的荷载也减少。
但是,应注意不能使坯料完全受到限制,为此要严格控制坯料的体积,控制锻模的相对位置和对锻件进行测量,努力减少锻模的磨损。
锻模根据锻模的运动方式,锻造又可分为摆辗、摆旋锻、辊锻、楔横轧、辗环和斜轧等方式。
摆辗、摆旋锻和辗环也可用精锻加工。
为了提高材料的利用率,辊锻和横轧可用作细长材料的前道工序加工。
与自由锻一样的旋转锻造也是局部成形的,它的优点是与锻件尺寸相比,锻造力较小情况下也可实现形成。
包括自由锻在内的这种锻造方式,加工时材料从模具面附近向自由表面扩展,因此,很难保证精度,所以,将锻模的运动方向和旋锻工序用计算机控制,就可用较低的锻造力获得形状复杂、精度高的产品,例如生产品种多、尺寸大的汽轮机叶片等锻件。
机械制造基础(金属工艺学) 第二章 铸造
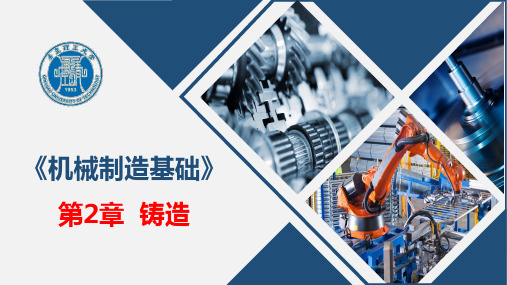
第2章 铸造
01 铸造工艺基础 02 合金铸件的生产工艺 03 砂型铸造 04 特种铸造 05 铸件结构设计
第2章 铸造
铸造工艺特点 1)适合制造形状复杂的毛坯
第2章 铸造
铸造工艺特点 2)毛坯大小不受限制
第2章 铸造
铸造工艺特点 3)材料不受限制(能熔化的金属) 4)生产成本低(原材料来源广泛) 5)应用广泛(历史最久的金属成型方法,40%~80%)
2.3.2 浇注位置和分型面的选择—浇注位置 1)铸件的重要加工面应朝下或位于侧面
2.3 砂型铸造
2.3.2 浇注位置和分型面的选择—浇注位置 2)铸件宽大平面应朝下
2.3 砂型铸造
2.3.2 浇注位置和分型面的选择—浇注位置 3)面积较大的薄壁部分应置于铸型下部
2.3 砂型铸造
2.3.2 浇注位置和分型面的选择—分型面 分型面:铸型组元之间的结合面或分界面。 分型面影响: 1)铸件质量; 2)生产工序的难易; 3)切削加工的工作量。
2.2.1 铸铁件生产 2)球墨铸铁 由于石墨成球状,它对基体的缩减和割裂作用减至最低限度,球墨
铸铁具有比灰铸铁高的多的力学性能,塑韧性大大提高。
2.2 合金铸件的生产工艺
2.2.1 铸铁件生产 2)球墨铸铁
球墨铸铁的牌号、 性能及用途 QTXXX-X
2.2 合金铸件的生产工艺
2.2.1 铸铁件生产 3)可锻铸铁 将白口铸铁件经长时间的高温石墨化退火,使白口铸铁中的渗碳体
04 特种铸造 05 铸件结构设计
2.3 砂型铸造
铸造工艺
砂型铸造
特种铸造
手工造型 机器造型 金属型铸造 熔模铸造
压力铸造 低压铸造
陶瓷型铸造 离心铸造
2.3 砂型铸造
《机械制造基础》课程标准

《机械制造基础》课程标准一、课程简介《机械制造基础》是一门重要的机械类专业基础课程,旨在培养学生掌握机械制造的基本理论、基本知识和基本技能。
本课程涵盖了机械制造的工艺、材料、加工方法、质量控制等方面的知识,为学生今后从事机械制造领域的工作打下坚实的基础。
二、课程目标1. 知识目标:学生能够掌握机械制造的基本理论,包括金属材料、热处理、铸造、锻造、焊接、切削加工等方面的知识;2. 能力目标:学生能够运用所学知识解决实际生产中的问题,具备一定的机械制造工艺设计、材料选择、加工方法确定等方面的能力;3. 素质目标:学生能够树立安全意识、环保意识、质量意识,具备团队合作精神和沟通协调能力。
三、教学内容与要求1. 金属材料与热处理:了解金属材料的性能特点及分类,掌握常见金属材料的牌号、性能及应用,熟悉热处理的方法及工艺;2. 铸造与锻造:了解铸造和锻造的基本原理和方法,熟悉铸造和锻造模具的结构和设计,能够根据实际生产需要选择合适的铸造和锻造方法;3. 焊接与连接:了解焊接和连接的基本原理和方法,熟悉常用焊接和连接材料的性能及选用,能够根据实际生产需要选择合适的焊接和连接方法;4. 切削加工:了解切削加工的基本原理和方法,熟悉常用刀具、夹具的结构和设计,能够根据实际生产需要选择合适的切削加工方法;5. 机械加工工艺:了解机械加工的基本原理和方法,熟悉机械加工工艺流程的设计和实施,能够根据实际生产需要制定合理的机械加工工艺流程。
四、教学方法与手段1. 采用多媒体教学,通过图片、视频等形式展示机械制造过程,提高学生的学习兴趣;2. 结合实际案例进行教学,使学生更好地理解机械制造的实际应用;3. 组织学生参观实习基地,让学生亲身感受机械制造的实际情况;4. 定期组织学生进行讨论和交流,鼓励学生提出自己的见解和想法。
五、教学评估与考核1. 平时成绩:包括出勤率、作业完成情况、课堂表现等,占总评成绩的30%;2. 期中考试:检验学生对本课程知识的掌握程度,占总评成绩的30%;3. 实验成绩:根据实验报告、实验操作等综合评定,占总评成绩的20%;4. 课程论文:要求学生结合所学知识,撰写一篇与机械制造相关的论文,占总评成绩的20%。
热加工实训报告心得体会
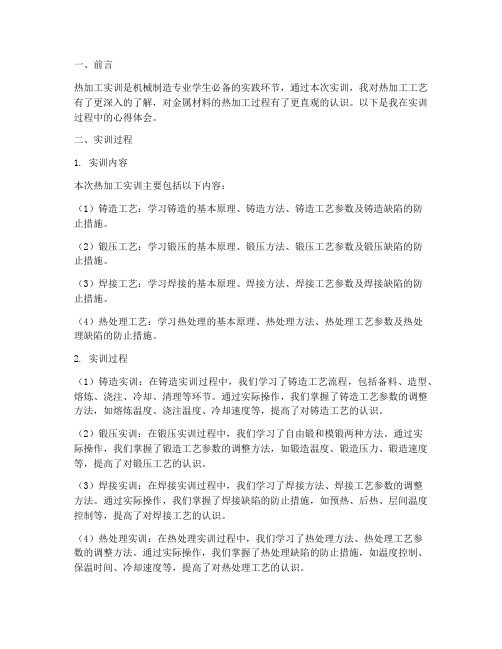
一、前言热加工实训是机械制造专业学生必备的实践环节,通过本次实训,我对热加工工艺有了更深入的了解,对金属材料的热加工过程有了更直观的认识。
以下是我在实训过程中的心得体会。
二、实训过程1. 实训内容本次热加工实训主要包括以下内容:(1)铸造工艺:学习铸造的基本原理、铸造方法、铸造工艺参数及铸造缺陷的防止措施。
(2)锻压工艺:学习锻压的基本原理、锻压方法、锻压工艺参数及锻压缺陷的防止措施。
(3)焊接工艺:学习焊接的基本原理、焊接方法、焊接工艺参数及焊接缺陷的防止措施。
(4)热处理工艺:学习热处理的基本原理、热处理方法、热处理工艺参数及热处理缺陷的防止措施。
2. 实训过程(1)铸造实训:在铸造实训过程中,我们学习了铸造工艺流程,包括备料、造型、熔炼、浇注、冷却、清理等环节。
通过实际操作,我们掌握了铸造工艺参数的调整方法,如熔炼温度、浇注温度、冷却速度等,提高了对铸造工艺的认识。
(2)锻压实训:在锻压实训过程中,我们学习了自由锻和模锻两种方法。
通过实际操作,我们掌握了锻造工艺参数的调整方法,如锻造温度、锻造压力、锻造速度等,提高了对锻压工艺的认识。
(3)焊接实训:在焊接实训过程中,我们学习了焊接方法、焊接工艺参数的调整方法。
通过实际操作,我们掌握了焊接缺陷的防止措施,如预热、后热、层间温度控制等,提高了对焊接工艺的认识。
(4)热处理实训:在热处理实训过程中,我们学习了热处理方法、热处理工艺参数的调整方法。
通过实际操作,我们掌握了热处理缺陷的防止措施,如温度控制、保温时间、冷却速度等,提高了对热处理工艺的认识。
三、实训心得体会1. 理论与实践相结合通过本次热加工实训,我深刻体会到理论与实践相结合的重要性。
在课堂上学习到的理论知识,只有通过实际操作才能真正掌握。
在实训过程中,我不仅巩固了课堂所学知识,还学会了如何将理论知识应用于实际生产中。
2. 操作技能的提高在实训过程中,我学会了各种热加工工艺的操作方法,如铸造、锻压、焊接、热处理等。
《 金属材料与热处理》(4学时和12学时)总复习题

基础课程《金属材料与热处理》应掌握知识重庆市机械高级技工学校培训中心备注:1、未标注“▲”符号的内容是培训4学时的班级必须掌握。
2、已标注“▲”符号的内容是培训12学时的班级在完成4学时培训的基础上增加的必须掌握内容,也就是说,培训12学时的班级对给出的内容应全部掌握。
复习要求第二章金属材料的性能一、了解金属的性能概述二、理解金属的力学性能定义及其应用▲三、理解金属的工艺性能定义及其应用第三章铁碳合金▲一、了解金属的实际晶体结构二、了解合金的基本组织▲三、熟悉铁碳合金的基本组织四、二元Fe3C相图的运用1、了解二元Fe3C相图的运用▲2、理解二元Fe3C相图,并会运用相图分析钢铁热处理组织转变过程4、基本会用二元Fe3C相图铸造、锻造、热处理工艺制定依据五、掌握碳素钢的分类、牌号表示方法及性能第四章钢的热处理一、理解钢的热处理原理,并掌握热处理分类方法二、基本熟悉常见钢的整体热处理工艺方法▲三、基本熟悉钢表面热处理工艺方法▲四、了解钢在加热和冷却时的组织转变五、基本能对典型零件的热处理后给予质量评价和分析第五章合金钢▲一、了解合金元素在钢中的作用二、掌握合金钢分类和牌号表示方法▲三、基本熟悉合金结构钢和合金工具钢常用牌号、性能和用途第六章铸铁▲一、了解铸铁的基本组织,熟知铸铁的分类二、常用铸铁(灰铸铁、可锻铸铁、球墨铸铁)的牌价、性能、用途第七章有色金属及硬质合金▲一、了解纯铝的牌号、性能和用途二、基本熟悉铝合金分类、牌号、性能和用途附基本复习题于后第二章金属材料的性能—.填空题(将正确答案填写在横线上)2. 强度的常用衡量指标有.屈服强度、和抗拉强度,分别用符号ReL、和Rm表示。
二.判断题(正确的打“√”,错误的打“×”)▲3. 做布氏硬度试验时,在相同实验条件下,压痕直径越小说明材料的硬度越低。
(×)7. 一般用洛氏硬度机而不用布氏硬度机来检测淬火钢成品工件的硬度。
(√)▲9. 一般来说,硬度高的材料其强度也较高。
金属材料的加工工艺

金属材料的加工工艺金属材料的加工工艺是指通过一系列的制造过程,将金属原料加工成所需要的最终产品的技术和方法。
金属材料是工业生产中最常用的材料之一,广泛应用于机械制造、建筑、汽车、电子等领域。
下面将介绍几种常见的金属材料加工工艺。
1. 锻造工艺:锻造是将金属材料置于模具中,通过力的作用使其产生塑性变形,得到所需形状的一种加工方法。
锻造可以分为自由锻造、模锻和挤压锻造等几种方式,适用于加工各种金属制品。
锻造工艺可提高材料的力学性能,改善金属的内部组织结构,提高产品的强度和硬度。
2. 铸造工艺:铸造是利用熔化的金属材料,借助模具的形状和负压力将金属液注入模具中,通过冷却和凝固得到所需形状和尺寸的工艺。
铸造是最早的金属加工方式之一,具有制造成本低、适应性广和生产效率高的特点。
3. 切削工艺:切削工艺是将金属材料放置在车床、铣床、钻床等机械设备上,通过旋转或振动的刀具来削除金属材料的一种加工方法。
切削工艺适用于制造各种形状的金属产品,并可以提高产品的精度和表面质量。
4. 焊接工艺:焊接是将金属材料通过高温或化学反应等方法进行连接的加工方式。
焊接工艺可以将金属材料连接成复杂的结构,常用于制造机械设备、船舶、桥梁等工程项目。
以上是几种常见的金属材料加工工艺,每种工艺都有自身的特点和适用范围。
随着科技的不断进步,金属材料加工工艺也在不断创新和完善,以满足不同领域对于金属制品的需求。
继续写相关内容,1500字5. 轧制工艺:轧制是将金属坯料经过一系列辊道的压制和塑性变形,从而得到所需的形状和尺寸的加工方法。
轧制工艺常用于生产金属板材、棒材、型材等产品。
通过轧制,可以改变金属的厚度、宽度以及截面形状,同时还能提高金属的硬度和强度。
6. 冷冲压工艺:冷冲压是将金属板材放置于冲床上,通过冲击力和冲压模具对金属板材进行塑性变形的一种加工方法。
冷冲压工艺常用于生产金属件、金属组件和金属外壳等产品。
冷冲压具有成本低、生产效率高、批量生产等优点,并可实现复杂形状和精度要求较高的产品制造。
机械制造基础复习题完整版

1.工艺的组成:工序、安装、工位、工步、走刀。
2.工艺过程分为:铸造、锻造、冲压、焊接、机械加工、热处理、装配。
3.生产类型:单件生产、成批生产、大量生产。
4.设计基准:工序基准、定位基准、测量基准、装配基准。
5.工件装夹由找正装夹(直接找正装夹、画线找正装夹)和夹具装夹。
6.工件定位有欠定位、过定位。
7.切削用量三要素:切削速度、进给量、背吃刀量。
8.切削层参数:切削层公称厚度、切削层公称宽度、切削层公称横截面积。
9.车刀切削部分六要素:前刀面、主后刀面、副后刀面、主切削刃、副切削刃、刀尖。
10.刀具标注角度的参考系:几面、切削平面、正交平面。
11.刀具的标注角度:前角、后角、主偏角、副偏角、刃倾角。
12.刀具材料的性能要求:较高的硬度和耐磨性、足够的强度和韧性、较高的耐磨性、良好的导热性和耐磨冲击性能、良好的工艺性。
13.常用的刀具材料:高速钢、硬质合金、工具钢、陶瓷、立方氮化硼、金刚石。
14.切削变形区的划分:第一变形区(从OA线到OM线的区域)、第二变形区、第三变形区。
15.切削变形程度的三种表示方法:变形系数(变形系数与剪切角有关,剪切角增大,变形系数减小,切削变形减小)、相对滑移、剪切角(前角增大,剪切角增大,变形减小。
摩擦角增大,剪切角减小,变形增大)。
16.积屑瘤的形成:连续流动的切削从粘在前刀面上的金属层上流过时,如果温度与压力适当,切削底部材料也会被阻滞在已经“冷焊”在前刀面上的金属层上,粘成一体,使粘结层逐步长大,形成积屑瘤。
17.积屑瘤对切削过程的影响:使刀具前角变大、使切削厚度变化、使加工表面粗糙度增大、对刀具寿命的影响。
18.防止积屑瘤的措施:正确选用切削速度、使用润滑性能好的切削液、增大刀具前角、适当提高工件材料硬度。
19.影响切削变形的因素:工件材料、刀具前角、切削速度、切削层公称厚度。
20.切削的形状类型:带状切削、节状切削、粒状切削、崩碎切削。
21.对切削的控制措施:采用断屑槽、改变刀具角度、调整切削用量。
- 1、下载文档前请自行甄别文档内容的完整性,平台不提供额外的编辑、内容补充、找答案等附加服务。
- 2、"仅部分预览"的文档,不可在线预览部分如存在完整性等问题,可反馈申请退款(可完整预览的文档不适用该条件!)。
- 3、如文档侵犯您的权益,请联系客服反馈,我们会尽快为您处理(人工客服工作时间:9:00-18:30)。
5.2锻造比 • 锻造比是锻造时金属变形程度的一种表示方法。 锻造比以金属变形前后的横 断面积的比值来表示。不同的锻造工序,锻造比的计算方法各不相同。 • 1、拔长时,锻造比为y=F0/F1或y=L1/L0 • 式中F0,L0—拔长前钢锭或钢坯的横断面积和长度; • F1 ,L1—拔长后钢锭或钢坯的横截面积和长度。 • 2、镦粗时的锻造比,也称镦粗比或压缩比,其值为 • y=F1/F0或y=H0/H1 • F0, H0—镦粗前钢锭或钢坯的横截面积和高度; • F1, H1—镦粗后钢锭或钢坯的横截面积和高度。
三箱造型浇注位置和分型面
5/
2.3浇注位置选择原则
(1)铸件的重要加工面应朝下或侧立。因铸件的上表面容易产生砂眼、气孔、 夹渣等缺陷,组织也不如下表面致密; (2)铸件的大平面应朝下。大平面朝上容易产生夹砂缺陷 (3)为防止铸件薄壁部分产生浇不足或冷隔缺陷,应将面积较大的薄壁部分 置于铸型下部或使其处于垂直或倾斜的位置; (4)对于容易产生缩孔的铸件,应使厚的部分放在铸型的上部或侧面,以便 在铸件厚壁处直接安置冒口,使之实现自下而上的定向凝固。
两组数 铸铁选用
13/
4.1 PROCAST仿真简介 • Procast是为评价和优化铸造工艺与铸造产品而开发的专业CAE软件 • Procast是所有铸造模拟软件中集成化程度最高的 • 配备了功能强大的数据接口和自动网格划分工具 • 全部模块化设计,适合任何铸造过程的模拟 • 采用有限元技术,是目前唯一能对铸造凝固过程进行热——流动——应力完
24/
5.4锻造术语 • 锻件重量:锻件毛坯的实际重量 • 飞边重量:锻造过程中外轮廓分模面处多余的材料 • 料芯重量:锻造过程中内孔多余的材料 • 火耗重量: 锻件在锻打过程中的热损耗 • 下料重量(切料重量):锻打一件锻件所需要的钢坯重量 • 材料消耗定额:锻打一件锻件所需要的钢材消耗总重量
25/
工程与结构用低合金铸钢件共包含八种牌号: ZGD270-480;ZGD290-510;ZGD345-570;ZGD410-620; ZGD535-720;ZGD650-830;ZGD730-910;ZGD840-1030。
3.2铸钢牌号的性能与用途
10/
3.3常存元素对钢性能的影响
11/
3.4.铸铁牌号
使凝固更倾向于顺序凝固。
6/
2.4铸型分型面的选择原则
铸造工艺合理性的关键之一。铸型分型面的选择应能在保证铸件质量的 前提下,尽量简化工艺,节省人力物力。
应尽量使分型面是一个平直的面;
应尽量减少分型面的数量;
选择原则
应尽量使型芯和活块的数量减少; 应使铸件的全部或大部分置入同一砂箱;应使铸件的全部 或大部分置入下箱;
1/
• 一.铸造的定义与分类 • 二.浇注位置与分型面的选择 • 三.铸钢铸铁的牌号 • 四.铸造仿真研究(PROCAST仿真简介) • 五.锻造工艺基础 • 六.热处理工艺流程
2/
1.1铸造的定义:
将液态合金浇注到与零件形状、尺寸相适应的铸型空腔中,待其冷却凝固,以获 得毛坯或零件的生产方法称为铸造。
应保证模样能顺利的从铸型中取出。
7/
8/
3.1铸钢牌号
铸钢牌号由铸钢的拼音简写ZG和屈服强度、抗拉强度数值表示。 如ZG230-450。一般工程用铸造碳钢件按GB 5613的规定分为: ZG200-400;ZG230-450;ZG270-500;ZG310-570;ZG340-640五种铸钢牌号。
20/
4.5缺陷的预测
21/
5.1锻造的工艺流程
不同的锻造方法有不同的流程,其中以热模锻的工艺流程最长,一般顺序为:锻坯下 料;锻坯加热;辊锻备坯;模锻成形;切边;冲孔;矫正;中间检验,检验锻件的尺寸和 表面缺陷;锻件热处理,用以消除锻造应力,改善金属切削性能;清理,主要是去除表面 氧化皮;矫正;检查,一般锻件要经过外观和硬度检查,重要锻件还要经过化学成分分析、 机械性能、残余应力等检验和无损探伤。
总高度;A为法兰锻件毛坯焊端外径;N为法兰锻件毛坯颈部外径。φ为冲孔用冲头外 径;1.6φ2 H为芯料重量。
28/
• 3 、G烧损计算方法为: G烧损=K G锻件 • K为烧损系数,锻件锻一次完成K=0.05; 锻件锻二次完成K=0.06;锻件锻三次完成
K=0.07;锻件锻四次完成K=0.08. 一般地当重量≤30Kg的矩形锻件和圆饼形锻件 K=0.05;不冲孔的法兰锻件及重量≤100Kg的矩形锻件和圆饼形锻件K=0.06;重量 ≤100Kg环形锻件和重量≤100Kg冲孔的法兰锻件及重量≤500Kg的矩形锻件和圆饼形≤ 锻件K=0.07;重量>100Kg环形锻件和重量>100Kg冲孔的法兰锻件及重量>500Kg 的矩形锻件和圆饼形锻件K=0.08. • 4、锻件余量:当工件最大尺寸≤150mm时,锻件余量取12mm;当工件最大尺寸> 150mm且≤350mm时,锻件余量取20mm;当工件最大尺寸>350mm时,一般 都是机械手操作,锻件余量相对手工操作要大些,当工件最大尺寸>350mm且≤60 0mm时,锻件余量取30mm;当工件最大尺寸>600mm且≤1000mm时,锻 件余量取40mm;当工件最大尺寸>1000mm且≤2000mm时,锻件余量取5 0mm;当工件最大尺寸>2000mm,锻件余量取60mm. • 5、关于1.6φ2 H为芯料重量说明:φ为冲孔用冲头外径,一般取冲孔内径的 • 2/5,φ最大外径为500mm. • 6、其他说明:当工件内径≤150mm时不冲孔;当工件内径>150mm时冲孔。 • Ⅲ级和Ⅳ级法兰锻成圆饼状或圆环状;当法兰外径≤350mm时,法兰锻成法兰状;当 法兰外径>350mm时,法兰锻成圆饼状或圆环状。
15/
4.3 汽车轮毂的充型过程
充型15%
充型25%
16/
4.3 汽车轮毂的充型过程
充型35%
充型55%
17/
4.3 汽车轮毂的充型过程
充型70%
充型90%
18/
4.4凝固过程模拟分析
改善工艺前的温度场分布
19/
对于改善工艺前,在开始凝固阶段,轮辋部分的凝固不是同步进 行的,由于在型腔的变截面处热熔较小,所以冷却速度较快。这与实 际是相符的。对应各轮辐中部的凝固先于对应轮辐与轮辋连接处。因 镁合金的容积热容量比较小所以冷却速度较快 ,对应各轮辐中部的凝 固先于对应轮辐与轮辋连接处。在轮辋、轮辐和它们之间的连接处的 厚度差别比较大,因此在轮辐中部区域会产生早期凝固现象,而在轮 辐与轮辋的连接处易产生热节 。由于热节部分在凝固过程中得不到很 好的补缩,于是对应于各个连接区域存在潜在的缩孔缺陷并且很可能 产生热裂 。在轮辐与轮辐相交处的外沿,出现热集中区的红斑,此区 域周围的合金液的凝固比率都大于该处,阻断了轮毂浇道的补缩作用 ,使得此处无法得到中央浇道的补充,因此此处很有可能是缺陷产生 的部位 。
全耦合的铸造模拟软件
14/
4.2 汽车轮毂的铸造仿真 • 运用三维造型软件对汽车轮毂进行三维实体造型并对浇注系统进行设计,实体模型如 图1所示。将铸件模型保存为X-T扩展名的文件,导入Procast软件中进行网格划分。对 网格单位进行设定,网格单位设为6mm。首先在Procast的meshcast模块中进行面网格 的划分。经过修改之后自动生成体网格模型,共有节点66703个,单元309209个。
• 铸铁名称,代号及牌号表示方法 • 铸铁名称...............代号牌号.....................实例 • 灰铸铁......................HT.........................HT100 • 蠕墨铸铁..................RuT........................RuT400 • 球墨铸铁..................QT.........................QT400-17 • 黑心可锻铸铁...........KHT........................KHT300-06 • 白心可锻铸铁...........KBT........................KBT350-04 • 珠光体可锻铸铁.......KZT........................KZT450-06 • 耐磨铸铁..................MT.........................MT Cu1PTi-150 • 抗磨白口铸铁...........KmBT....................KmBTMn5Mo2Cu • 抗磨球墨铸铁...........KmQT....................KmQTMn6 • 冷硬铸铁..................LT...........................LTCrMoR • 耐蚀铸铁..................ST..........................STSi15R • 耐蚀球墨铸铁...........SQT.......................SQTAl15Si5 • 耐热铸铁..................RT..........................RTCr2 • 耐热球墨铸铁..........RQT........................RQTA16 • 奥氏体铸铁..............AT.........................---• ...牌号中代号后面的一组数字,表示抗拉强度值;有两组数字时,第一组表示抗拉强度值,第二组表示延伸率值。
27/
(5):对于冲孔法兰形锻件: G锻件= 6.17×D2×C + 6.17×(N/2+A/2)2×(H-C) -6.17×d2×H +1.6φ2 H (碳钢和低合金钢
) G锻件= 6.23×D2×C + 6.23×(N/2+A/2)2×(H-C) -6.23×d2×H +1.6φ2 H (不锈钢) D为法兰锻件毛坯外径;d为法兰锻件毛坯内径; C为法兰锻件毛坯厚度;H为法兰锻件毛坯