机床热变形误差实时补偿技术(精)
机床热误差产生原因分析及常用补偿办法

机床热误差产生原因分析及常用补偿办法一、引言在数控机床加工中,机床的稳定性和精度是直接影响加工质量的重要因素。
而机床的热误差是影响机床加工精度的主要因素之一。
本文将分析机床热误差产生的原因,并探讨常用的补偿办法,旨在帮助读者理解和解决机床热误差问题。
二、机床热误差产生原因分析(一)热误差的基本原理机床在加工过程中会受到各种外部环境因素的影响,以及自身零部件因摩擦、压力等衍生出的内部热效应。
这些因素都会导致机床的温度发生变化,从而影响机床的几何尺寸和传动精度,从而产生热误差。
(二)原因一:外部环境的影响机床所处的环境温度、湿度等都会对机床产生影响。
冬季室内温度相对较低,会导致机床传动件温度下降,从而引起机床的几何尺寸发生变化;夏季室内温度相对较高,机床零件温度会上升,进而影响机床的加工精度。
(三)原因二:机床自身结构及零部件的影响机床自身的结构、传动件、润滑系统等都会引起机床的温度变化,从而产生热误差。
机床各部件的热膨胀率不同,使得机床温度的变化导致机床的尺寸和传动精度发生变化;机床的润滑系统也会因温度变化而影响机床的加工精度。
(四)原因三:加工过程本身的热效应三、常用的补偿办法(一)采用温度控制系统采用温度控制系统能够控制机床的温度,从而减小温度对机床的影响。
在机床上安装温度传感器,实时监控机床的温度,并通过控制冷却系统或者加热系统,使机床的温度始终保持在一个稳定的范围内,从而减小机床的热误差。
(二)采用热误差补偿技术热误差补偿技术是一种通过软件或者硬件手段来对机床热误差进行补偿的技术。
通过对机床的温度进行监测,并根据温度变化对机床的坐标进行实时补偿,从而减小热误差对机床加工精度的影响。
(三)改进机床结构及材料改进机床的结构和材料也是减小热误差的重要途径。
采用低热膨胀率的材料来制造机床零部件,或者改进机床的结构,减小零部件的膨胀率,从而减小热误差的产生。
(四)优化加工工艺在加工过程中,通过优化工艺参数,减小加工零部件的摩擦和热效应,也可以减小热误差的产生。
机床热变形误差实时补偿技术.
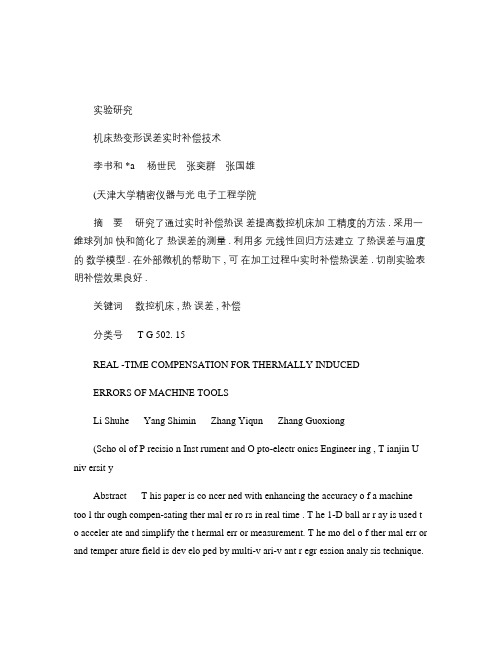
实验研究机床热变形误差实时补偿技术李书和 *a 杨世民张奕群张国雄(天津大学精密仪器与光电子工程学院摘要研究了通过实时补偿热误差提高数控机床加工精度的方法 . 采用一维球列加快和简化了热误差的测量 . 利用多元线性回归方法建立了热误差与温度的数学模型 . 在外部微机的帮助下 , 可在加工过程中实时补偿热误差 . 切削实验表明补偿效果良好 .关键词数控机床 , 热误差 , 补偿分类号 T G 502. 15REAL -TIME COMPENSATION FOR THERMALLY INDUCEDERRORS OF MACHINE TOOLSLi Shuhe Yang Shimin Zhang Yiqun Zhang Guoxiong(Scho ol of P recisio n Inst rument and O pto-electr onics Engineer ing , T ianjin U niv ersit yAbstract T his paper is co ncer ned with enhancing the accuracy o f a machine too l thr ough compen-sating ther mal er ro rs in real time . T he 1-D ball ar r ay is used t o acceler ate and simplify the t hermal err or measurement. T he mo del o f ther mal err or and temper ature field is dev elo ped by multi-v ari-v ant r egr ession analy sis technique.W ith the aid o f an ex ternal PC, t he er ro r can be compensat ed in real tim e. T he cutting test show s that the effect of co mpensatio n is satisfacto ry.Keywords N C machine t oo l , thermal er ro r , err or compensatio n科学技术的发展对数控机床的精度和可靠性提出了越来越高的要求 . 大量研究表明 , 热误差是数控机床最大的误差源 , 占总误差的 40%~70%[1]. 减小热误差可通过三种方法 , 即改进设计、温度控制和误差补偿 . 其中误差补偿是一种方便、经济而有效的方法 [2]. 本文以 JCS-018A 立式型加工中心为对象进行了研究 . 首先通过实验建立热误差与机床上若干点的温升之间的数学模型 , 在加工过程中借助外部微机监测温度 , 根据模型计算热误差 , 利用微机与机床数控系统的通讯技术及机床运动的可控性 , 修改进给量 , 从而实现实时补偿 . 1998年 11月No v. 1998天津大学学报 JOURNAL OF TIANJIN UNIVERSITY 第 31卷第 6期 V o l. 31N o. 6a 本文 1997年 1月 8日收到 . 1997年 5月 7日收到修改稿 .*, ,1测量方法1. 1热误差的测量机床热误差是由于内外热源作用下 , 刀具相对工件产生热位移造成的 . 由于丝杠的热膨胀和立柱的热弯曲 , 热误差不仅取决于温度而且随各轴的位置而变化 . 为了全面快速地测量热误差 , 本文采用了一种一维球列检具 . 一维球列即在一刚度足够的基座上等间隔镗一系列尺寸相同的锥孔 , 在锥孔上粘一系列尺寸相同、球度误差很小的钢球 . 使用在 xy z 三个方向同时瞄准球心的三维测头 , 测量球心的坐标 . 以 z 轴为例说明测量原理 , 如图 1a 所示 , 将一维球列装卡在工作台上 , 调整使其与 z 轴平行 . 将测头固定在主轴箱上 , 在机床未升温状态对各球心坐标进行测量 , 测值作为参考值 . 然后 , 机床以一定方式运转 , 每隔一定时间对各球心坐标测量一次 , 在新状态下的测量值相对参考值的变化反映了机床的热漂移 . 从所测热漂移值可以得到各项热误差.(a 工作台 (b 双测头图 1热误差的测量Fig . 1 Thermal error measurement1 机床坐标系零点的漂移$d (t 1, x 0, y 0, z 0 =[x 0(t i -x 0(0 , y 0(t i -y 0(0 , z 0(t i -z 0(0 ](1 式中 :[x 0(0 , y 0(0 , z 0(0 ]为各球心坐标的参考值 ; [x o (t i , y 0(t i , z 0(t i ]为第 t i 时刻各球心坐标的测量值 .2 机床各轴单位长度的热膨胀k lx (t i =[x 2(t i -x 1(t i -x 2(0 +x 1(0 ]/lk ly (t i =[y 2(t i -y 1(t i -y 2(0 +y 1(0 ]/lk lz (t i =[z 2(t i -z 1(t i -z 2(0 +z 1(0 ]/l(2 3 立柱的倾斜立柱倾斜通过测量两个 Z 平面上坐标值 [x 1(t i , y 1(t i ]和 [x 2(t i , y 2(t i ]来确定 . 立柱在 x 方向的热倾斜 :A x (t i =[x 2(t i -x 1(t i -x 2(0 +x 1(0 ]/l (3・ 811・第 31卷第 6期李书和等 :机床热变形误差实时补偿技术A y (t i =[y 2(t i -y 1(t i -y 2(0 +y 1(0 ]/l4 刀轴的热倾斜刀轴倾斜的测量需要使用双测头 , 如图 1b 所示 . 两个测头之间的距离与一维球列的各球心距相等 , 通过测头 a 、 b 的测量值来确定 .刀轴在 x 方向的热倾斜 :B x (t i =[x b (t i -x a (t i -x b (0 +x a (0 ]/l(4刀轴在 y 方向的热倾斜 :B y (t i =[y b (t i -y a (t i -y b (0 +y a (0 ]/l对上述各误差最大的几项进行补偿就可大幅度提高精度 .1. 2温度的测量根据对热源分布、热量传播、敏感部分等的理论分析和初步实验 , 在床身上比较重要的位置分布 12个热敏电阻 , 测量温度 . 热敏电阻的位置和作用如表 1所示 .表 1热敏电阻的位置和作用Tab . 1 The positions and functions of temperature sensors 热敏电阻T 1T 2, T 11, T 12, T 9T 3, T 7, T 8T 5, T 10T 4T 6位置工作台主轴轴套、主轴箱立柱的上下端 Z 轴滚珠丝杠一维球列检具前后轴承、电机轴承作用参考温度主轴的热变形立柱的热膨胀丝杠的热膨胀检具的热膨胀 1. 3测量策略为辨识机床热特性 , 让机床运行方式接近加工状态 , 在不同的坐标下 , 实验方式有三种 :1 主轴以不同的固定转速转动 ;2 主轴按转速谱转动 ;3 主轴转速模拟实际加工过程 . 2热特性的分析在一典型实验中 (主轴转速 n =800r /min, t =0~210m in; n =0r/m in, t=210~300min 发现 , 主轴前后轴承的磨擦热是机床的最大热源 , 温度变化最为剧烈 , 幅值达 4~5℃ . 而立柱的热容量较大 , 温升比较缓慢 , 在主轴停转后立柱温度仍继续上升 . z 轴滚珠丝杠轴承的温度变化很大 . 主轴箱箱体左右的温度变化不太剧烈 . 床身温度和室温变化缓慢 .在热误差方面 , z 轴零点热漂移最大 , 可达 30L m, x 轴和 y 轴热漂移值较小 , 仅为 5L m . 同时 z 轴热膨胀也最大 , 相对零点 100mm 距离的热膨胀达 3~4L m .分析表明 , 该机床 z 轴热误差最大 . 实际上 z 轴热误差是主轴热膨胀、主轴箱热变形、 z 轴滚珠丝杠热膨胀和立柱热变形等几部分造成的 . 其中丝杠膨胀和立柱的弯曲与 z 轴位置有关 , 如图 2示 .图 3为不同 z 坐标下 (z 1=-50, z 2=-150, z 3=-250, z 4=-350 z 轴热漂移的情况 . 开始阶段几条曲线比较相似 , 随时间的推移而逐渐分离 . 这是由于开始阶段热漂移主要是由与位置无关的主轴热位移造成的 , 变化速度比较快 , 很快达到热平衡 . 此后 , 与位置有关的热・ 812・天津大学学报1998年 11月热漂移的不同.图 2 z 轴热误差的分量图 3不同 z 坐标下的热误差Fig . 2 The components of z -axis Fig . 3 Thermal errors at diff erentthermal error z coordinates3热误差的建模由于 z 轴的热误差最大 , 这里只研究 z 轴热误差的建模 . 图 4和图 5为模型拟合热误差和预测新工作状态下热误差的情况.图 4对一新工作条件下 (800r /m in 图 5对一新工作条件下 (DIN 8602转速谱热误差的拟合情况热误差的预测情况Fig . 4 Fitting result of the thermal error at Fig . 5 Prediction result of the thermal error a new cutting condition (800r /min at a new cutting condition (D IN 8602spectr um3. 1误差合成公式z 轴任一坐标处 z 1的热误差为$z (z 1 =$z (z 0 +k (z 1-z 0 (5 式中 :$z (z 0 为 z 轴零点处的热漂移 ; k 为 z 轴单位长度的热膨胀 . 这里只考虑了这两项最显著的误差 .3. 2多元线性回归模型采用线性回归分析分别建立 z 轴零点热漂移和 z 轴热膨胀与温度的模型 . 模型的形式为 [3]・ 813・第 31卷第 6期李书和等 :机床热变形误差实时补偿技术y d =B 0+B 1x 1+B 2x 2+…… +B m x m +E 式中 :yd 为所要估计的热误差; x 1, … , x m 为机床各测温点的温升值 ; B 0, B 1, … , B m 为模型中的未知参数 ; E 为残余误差 . 模型中的参数用最小二乘法估计 .3. 3热敏感点的选择在建立模型时 , 自变量的选择是一个关键问题 . 如果遗漏了重要的变量 , 回归效果一定不会好 . 自变量过多 , 把对因变量影响不显著的也引入 , 会影响方程的稳定性 , 效果也不会好 . 同时 , 实时监测、计算等的任务量也加大了 . 为从 12个候选温度测点中挑选“ 热敏感点” , 从而建立最优模型 , 采用了逐步线性回归方法 . 回归方程每次选入一个变量 , 每选入一个新的自变量后都重新对构成该方程的每个自变量进行一轮新的偏 F 检验 . 如果发现某个自变量的上述边际贡献不显著 , 不论是前期选入的还是现期选入的 , 都要剔除出回归方程 , 并用剩下的自变量重新拟合回归方程 . 这一过程按上述原则一直进行 , 直到待筛选的全部自变量中根据给定的显著水平没有一个再能被选入或排除出刚构成的回归方程为止 . 这些工作都用大型数学工具软件包 SPSS 来实现 . 最终 , 选出 4个“ 热敏感点” , 即工作台、主轴箱箱体、立柱和主轴轴承 . 由图 4和图 5可见模型拟合热误差和预测一种新工作状态下热误差 , 结果比较准确 .4热误差补偿的执行大多数数控系统不具备热误差实时补偿功能 , 所以要借助于外部微机 . 监测机床上 4个点的温度 , 通过接口板采集机床的坐标位置 , 利用存储在微机中热误差模型计算热误差 . 利用微机与数控 CNC 系统的直接通讯技术 , 将补偿值传送到机床控制器 , 通过改变机床零点的位置来实现实时补偿 .为了验证热误差的补偿效果 , 进行了铣削实验 , 以所铣槽深的变化反映热误差 . JCS -018A 的定位精度为 1L m , 加工的工艺条件为 :主轴转速 1000r /m in , 切削量 0. 1m m , 不使用冷却液 . 在相同的条件下进行了多次实验 . 槽深误差由 7L m 减小到 2L m , 补偿效果达到 70%左右 .5结论研究了 JCS-018A 型加工中心热误差的补偿 . 用一维球列测量机床加工空间内的热误差 , 在机床结构的关键位置上布置热敏电阻测量温度 , 制订了测量策略 , 对机床的热特性进行了分析并利用回归分析确定热误差与 4个敏感点的温度之间的关系 . 通过切削实验 , 验证热误差补偿效果非常明显 .参考文献1 Bryan J. International status of th ermal er ror research. Annals of th e CIRP, 1990; 39(2 :645~6562 Chen J S, Yuan J, Ni J e t al . Real-time com pens ation for time-variant volumetric error on a machining center. ASM E Jour nal of Engineering for Ind ustry ,1993; 114:472~4793, ・ 814・天津大学学报1998年 11月。
机床热误差产生原因分析及常用补偿办法
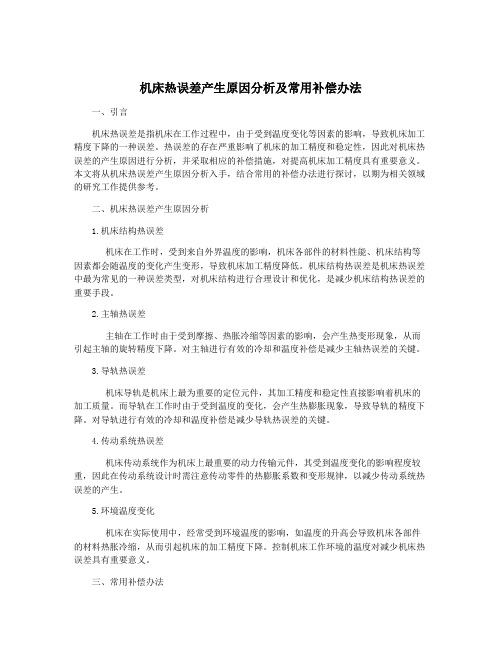
机床热误差产生原因分析及常用补偿办法一、引言机床热误差是指机床在工作过程中,由于受到温度变化等因素的影响,导致机床加工精度下降的一种误差。
热误差的存在严重影响了机床的加工精度和稳定性,因此对机床热误差的产生原因进行分析,并采取相应的补偿措施,对提高机床加工精度具有重要意义。
本文将从机床热误差产生原因分析入手,结合常用的补偿办法进行探讨,以期为相关领域的研究工作提供参考。
二、机床热误差产生原因分析1.机床结构热误差机床在工作时,受到来自外界温度的影响,机床各部件的材料性能、机床结构等因素都会随温度的变化产生变形,导致机床加工精度降低。
机床结构热误差是机床热误差中最为常见的一种误差类型,对机床结构进行合理设计和优化,是减少机床结构热误差的重要手段。
2.主轴热误差主轴在工作时由于受到摩擦、热胀冷缩等因素的影响,会产生热变形现象,从而引起主轴的旋转精度下降。
对主轴进行有效的冷却和温度补偿是减少主轴热误差的关键。
3.导轨热误差机床导轨是机床上最为重要的定位元件,其加工精度和稳定性直接影响着机床的加工质量。
而导轨在工作时由于受到温度的变化,会产生热膨胀现象,导致导轨的精度下降。
对导轨进行有效的冷却和温度补偿是减少导轨热误差的关键。
4.传动系统热误差机床传动系统作为机床上最重要的动力传输元件,其受到温度变化的影响程度较重,因此在传动系统设计时需注意传动零件的热膨胀系数和变形规律,以减少传动系统热误差的产生。
5.环境温度变化机床在实际使用中,经常受到环境温度的影响,如温度的升高会导致机床各部件的材料热胀冷缩,从而引起机床的加工精度下降。
控制机床工作环境的温度对减少机床热误差具有重要意义。
三、常用补偿办法1.热环境调节通过对机床工作环境进行温度调节,以降低环境温度的变化对机床产生的影响,减少热误差的产生。
对机床工作间进行隔热处理,也是一种有效的热环境调节手段。
2.温度补偿技术温度补偿技术是利用传感器实时监测机床各部件的温度变化,并通过控制系统对机床进行温度补偿,以减少热误差的产生。
数控机床误差补偿技术及应用热误差补偿技术

作者: 赵宏林 , 北京密云水库北京机床研究所, 西 安理工大学博士生 , 邮编: 101512 ( 编辑 徐鸿根 )
( 收稿日期 : 1998— 11— 12)
实测结果。
图 2 五点法测量时电涡流传感器布置简图
图 3 滑枕系统热变形误差测量和补偿原理图
图 4 X HFA 4220 加工中心滑枕系统热变形误差 图 1 X 、 Y、 Z 轴丝杠热变形
4 结论
热变形误差是影响机床定位精度的重要 因素之 一。文章将热变形误差与机床空间几何运动误差和载 荷误差分量结合在一起 , 提出机床综合误差的计算模 型。用 5 点法获得机床的热变 形误差参数。对 XHFA2420 加工中心的实验可见 , 滑枕系统的热 空间误 差 X 向从 9. 6Lm 减小到 3. 4L m , Y 向从 66. 7Lm 减小 到 10. 4 L m , Z 向从 182. 0Lm 减小到 35. 1 L m , 误差补 偿量达 65% 以上。 参 考 文 献
2 薄壁盲孔加工新工艺
2. 1 电火花加工 电火花加工不存在机械力作用, 因此不会出现薄 壁盲孔的加工变形问题 , 也容易保证两孔及薄壁的尺 寸精度和形状精度。薄壁盲孔的电火花加工是对已加 工出 Á 1. 8m m × 8m m 成型预孔的工件进行数控电火 花摇动加工, 加工中工具电极旋转, 工件随工作台按给 定半径做圆摇动 , 通过二者之间的火花放电修光薄壁 盲孔的侧面。 由于采取了一系列工艺措施, 例如电极反 拷、 电极内孔中心冲油等, 所以能够保证薄壁厚度的一 致性。 电火花加工中的高温和工作液的快速冷却作用 , 使薄壁的表面产生变质层和应力层。由于电火花加工 后的表面应力表现为拉应力 , 因而存在微裂纹, 使弹性 元件的疲劳强度下降, 因此对于高质量的弹性元件必
机床热误差产生原因分析及常用补偿办法

对降低热误差带来了更高的难度。 2.2误差补偿技术 误差补偿技术在实际使用中有十分明显的效果,得到了人
们的广泛认可,对降低热误差具有重要的意义。误差补偿技术 主要分为直接补偿和间接补偿这两类。
直接补偿一般通过间接测量以及补偿位移大小进行补偿, 技术人员如果想要知道道具的位置,仅需要通过工件上的传感 器进行测量,虽然直接补偿的使用并不困难,但是会停止切削 过程,降低工作 效 率。不 同 于 直 接 补 偿,简 介 补 偿 需 要 知 道 设 计热误差模型以及传感器反馈数值来明确实时状态,进而进行 误差补偿。
关键词:热误差;数控机床;建模
机床是一种重要的工业设备,在机械生产中具有举足轻重 的作用。现阶段,我 国 工 业 生 产 逐 渐 趋 于 自 动 化 形 态,精 密 制 造技术也在不断发展,这就对机床提出了新的要求,不能够仅 仅满足于高精度以及高速度这类传统工作需要,还要具备精密 化以及智能化的生产特征。机床精度是机床的重要参数,决定 了加工质量的高低,而对于机床精度而言,相关的影响因素一 般有许多部分,主要是热变形误差、机床制造装配几何误差、切 削加工引起的切削力变形误差以及磨损误差等。
2.3优化设计及其他控制方法 有限元分析技术是一种先进的技术,对各方面的发展都有 有效的参考和帮助。通过这种技术,设计人员在机床设计中越 来越 注 重 机 床 的 绿 色 设 计、系 统 动 态 设 计 以 及 优 化 设 计 等 方面。 近些年来新型材料不断产生,对其他行业的发展也带来了 推动作用。譬如可 以 将 花 岗 岩 用 于 机 床 床 身,而 陶 瓷 轴 承、磁 力轴承及气体静压轴承等可改善接触条件,降低接触热产生, 提高转动精度。通过对机床使用过程和加工过程的相互作用 研究,温差对其使用精度影响较大,可以采用优化加工顺序和 加工参数来减少热变形的产生。 3热误差补偿技术存在的问题 近些年来,由于 科 技 的 进 步 和 创 新,热 误 差 补 偿 技 术 相 对 于过去已经有了较大的提升,解决了部分机床的热误差问题。 但是在实际生产过程中,一部分生产问题仍然没有得到改善, 在应用中还存在诸多不便。对于一些高质量的加工场合,对国 外高端机床有很大的依赖,我国机床的热误差补偿技术仍然无 法机型批量生产使用。 一些热误差产生的特征是重要的参考内容,但是对其进行 测量和辨识会耗费大量资源,机床在工作中周围环境的变化是 热误差的一方面因素,同时,加工工况、切削参数以及工作时长 也是热误差的影响因素。 机床在工作过程中的环境温度一般都在不断变化,如果要 建立热误差补偿模型,就只能建立某个温度范围的模型,在其 他温度状态下,相应的数学模型就不再适用。 4结语 综上所述,机床 是 工 业 生 产 的 重 要 部 分,对 工 业 生 产 具 有 重要的意义。为了有效降低机床的热误差,提升机床的加工精 度,就必须要充分了解机床热误差产生的因素,从这些因素入 手,采用误差避免技术、误差补偿技术研究优化设计其他控制 方法,进而改善机床的质量,保证机床工作效率,为工业生产提 供根本保证。 参考文献: [1]LiY,ZhaoW,LanS,etal.A reviewonspindlethermal errorcompensationinmachinetools[J].InternationalJournalof MachineToolsandManufacture,2015,(95):2038. [2]罗文.数控机 床 热 误 差 检 测 与 补 偿 技 术 [D].南 京:南 京航空航天大学,2010.
CNC机床加工中的热变形控制与补偿

CNC机床加工中的热变形控制与补偿引言CNC(Computer Numerical Control)机床是现代制造业中的重要装备,其高精度和高效率使其在各行各业中得到了广泛应用。
然而,由于材料在加工中受到热力影响导致的热变形对加工质量和精度产生了不可忽视的影响。
因此,在CNC机床加工中,热变形的控制与补偿显得尤为重要。
一、热变形的原因CNC机床加工中的热变形主要源于以下几个方面:1. 主轴驱动引起的热变形:主轴的高速旋转产生摩擦热,使主轴温度升高,进而引起机床各部位的热膨胀,导致热变形;2. 切削加工引起的热变形:切削过程中,刀具与工件之间的摩擦产生的热量会使工件局部温度升高,导致热膨胀和变形;3. 内部应力引起的热变形:材料加工后内部应力的释放也会导致热变形。
二、热变形的影响热变形对CNC机床加工的影响主要表现在以下几个方面:1. 加工精度下降:由于机械结构的热膨胀导致零件定位的改变,使加工精度降低;2. 加工质量下降:热变形使得工件表面产生热裂纹、残余应力等缺陷,影响工件的材料性能和使用寿命;3. 加工效率降低:热变形会导致加工过程中频繁调整机床参数,增加生产时间和成本;4. 刀具磨损加剧:由于热变形使刀具与工件接触面积增大,导致刀具磨损加剧,降低切削效率。
三、热变形的控制为了控制CNC机床加工中的热变形,可以采取以下措施:1. 机床结构设计优化:通过对机床结构进行合理的分析和设计,减少热变形的程度;2. 冷却系统改进:加强冷却系统,通过冷却液对主轴和切削区域进行冷却,有效降低温度;3. 热稳定性材料应用:选择具有较低热膨胀系数和较高热导率的材料,减少热变形的可能性;4. 温度监测与控制:通过安装温度传感器,对机床的温度进行监测,及时进行温度调整;5. 热补偿技术应用:通过在机床控制系统中引入热补偿算法,对机床进行实时的热补偿,减小热变形对加工质量的影响。
四、热变形的补偿热变形的补偿是通过对加工过程中发生的热变形进行修正,以保证加工精度和质量。
机床热误差产生原因分析及常用补偿办法

机床热误差产生原因分析及常用补偿办法一、引言现代制造业对产品精度的要求越来越高,但是机床在加工过程中会受到温度影响,导致热误差的产生。
如果不对热误差进行有效的补偿,将会直接影响产品的加工质量,甚至导致生产事故。
研究机床热误差的产生原因以及常用的补偿办法对于保障产品加工精度具有重要意义。
二、机床热误差的产生原因分析1.机床结构热变形机床在工作过程中会受到外部环境温度变化的影响,导致机床结构材料的热膨胀或收缩,从而引起机床的尺寸变化。
特别是大型数控机床,在长时间的加工过程中,由于机床结构的温升会导致机床的各个部分产生不同程度的热变形,从而引起热误差的产生。
2.主轴热变形机床的主轴在高速加工过程中会受到较大的摩擦力和热量的影响,导致主轴温升,从而引起主轴的热变形。
主轴的热变形会直接影响到工件的加工精度,甚至导致产品质量不合格。
3.润滑油温度机床在工作过程中需要进行润滑,而润滑油的温度会直接影响到机床各个零部件的温度。
当润滑油温度升高时,会导致机床各个部件的温度升高,从而引起热误差的产生。
4.外部环境温度5.加工热量6.其他因素除了上述因素之外,机床的热误差还受到机床结构设计、机床材料特性、润滑方式、切削参数等多方面的影响。
以上这些因素的综合作用,导致了机床热误差的产生,因此在实际生产中,需要采取相应的措施对热误差进行有效的补偿。
三、机床热误差的常用补偿办法1.温度补偿温度补偿是对机床热误差进行校正的有效方法之一。
通过在机床的各个部件上设置温度传感器,实时监测机床的温度变化,并且通过控制系统对温度进行实时补偿,从而减小了机床的热误差。
2.结构优化通过对机床的结构进行优化设计,例如采用热稳定性好的材料、合理设置机床的冷却系统、优化机床的传热结构等,可以有效减小机床热误差的产生。
3.控制系统补偿控制系统补偿是通过对机床数控系统的程序进行调整,以达到对热误差的补偿效果。
例如在机床数控系统中设置热误差的补偿参数,通过对加工程序进行调整,从而达到对热误差进行有效补偿的目的。
机床加工过程中误差成因及补偿方法分析

机床加工过程中误差成因及补偿方法分析摘要:在数控机床加工过程中,通常会由于加工过程中产生的热、施加力、尺寸测量、控制系统及定位不精准等因素导致零件的加工尺寸产生出入。
在目前的数控机床中,通常会采用补偿控制技术以抵消或减弱上述误差,在数控机床产生以来,补偿控制就随之出现,如何提高加工过程中的精度始终是该领域中的重要课题。
关键词:机床加工;误差类型;补偿方法1数控机床的概述及加工误差优化的重要性1.1数控机床的概述数控机床(Numerical Control MachineTool)是一种采用数字化控制技术的机床。
通过编程,将加工工艺的各项参数转化为数控指令,输入到数控系统中。
数控系统按照预设的程序,通过伺服驱动系统驱动机床各运动部件实现刀具与工件的相对运动,完成零件的加工。
数控机床具有加工精度高、自动化程度高、生产效率高、加工范围广等特点,被广泛应用于航空、航天、汽车、模具等领域的零件加工。
1.2加工误差优化的重要性加工误差优化在数控机床加工过程中具有极高的重要性。
优化加工误差不仅有利于提高零件的加工精度,确保产品质量,还可以提高生产效率,降低制造成本,从而增强企业的市场竞争力。
2数控机床加工误差的类型及成因2.1机床导轨误差机床导轨误差是指在机床的制造、装配和使用过程中,由于导轨表面的磨损、凹凸不平、制造加工误差、装配调整误差、污染、温度变化等因素引起的位置误差。
导轨误差对机床的加工精度和稳定性产生严重影响,可能导致加工件精度下降、表面质量劣化、加工速度减慢、工具寿命缩短等问题。
制造过程中的加工误差是导致导轨误差的重要原因,包括材料变形、工艺偏差、加工质量不佳等因素。
2.2丝杠与滚珠丝杠副误差丝杠副误差是指在制造、装配和使用过程中因加工误差、装配误差、磨损、变形等因素引起的丝杠副位置误差。
丝杠误差会影响数控机床定位精度和运动精度,降低机床加工精度和稳定性。
在制造过程中,丝杠的加工误差是导致丝杠误差的主要原因之一。
机床的热误差产生及补偿方法

1 ) B P神经网络 ;
‘
原始 误差 的特 点和规律 , 建立 误差数 学模 型 , 尽量使 人为造 成 的 误差 和原始误差两 者的数值 相等 、 方 向相反 , 从 而减少加工误差 ,
2 ) 人体免疫 系统 R B F ( A I R B F ) 网络; 3 ) 贝叶斯网络 ; 4 ) 最优线性组合神经 网络 ; 5 ) 模糊神经网络 ;
补 偿相关 的技 术有 检测技 术 、 传感 技术 、 信 号处理 技术 、 光 电技 机 床的热误差 主要是 由于机床 工作 时复杂 的温度场 造成机 术 、 材料 技术 、 计算机技 术 以及控 制技术等 。作 为一 门新 技术分 床各部件 变形 即机 床的热动态过程而引起 的。机床运转过程 中 , 支, 误差补偿技术具有 自己的独立 内容 和特色。进一步研究误差 运动部件 在内部和外部热源作用下 , 产生热量并传 给机床各部位 补偿技术 , 使其理论化 、 系统化 , 将 具有非常重要的科 学意义 。 产生温差 , 使各零部件产生热变形 , 造成加工精度下降。 工程性误差补偿技术 的工程意义是非常显著 的 , 它包含 3层 一是采用误差补偿技术可 以较容易地 达到“ 硬技术 ” 要花费 机床热误差产生机理如图 1 所示 。机床各种内部热源 的发热 含 义 :
现将各种建模方法集 中如下 : 3 . 1 最小 二 乘 相 关 图 1 机床 热误 差产 生机 理 1 ) 多元线性 回归模型( MR A) ; 工 件 热 误 差 主 要 是 由 于 工 件 在 加 工 过 程 中产 生 大 量 的 切 削 2 ) 最小二乘支持向量机( L S .S VM) : 热, 其 中一部分 切削热传 人工件 , 使工件 产生热膨胀 变形 。 因此 , 3 ) 动态 自适应加权最小二乘支持矢量机( WL S .S V M) ; 工 件是在热 膨胀 的状 态下进行 加工 , 而工件加 工完成后 , 在常 温 4 ) 在线最小二乘支持 向量机 ( 0 L S .S V M) :
数控机床误差测量与实时智能补偿关键技术及应用

数控机床误差测量与实时智能补偿关键技术
及应用
随着工程制造业的发展,数控机床逐渐取代了传统的机床,成为
了高效精密加工的主力军。
然而,由于数控机床存在着系统误差、尺
寸误差等问题,导致加工精度不尽如人意。
为了解决这些问题,数控
机床误差测量与实时智能补偿技术应运而生。
数控机床误差测量是指通过对数控机床加工过程中存在的误差进
行精确测量和分析,找出误差的来源及其大小,并将其量化,以便进
一步进行补偿。
通常,数控机床误差可以分为几种类型,如基础误差、运动误差、非线性误差等。
针对不同的误差类型,可以采用不同的测
量方法,如激光干涉、摆角测量、位移传感器等。
数控机床实时智能补偿是指在加工过程中实时检测误差,并通过
计算机智能算法进行补偿,以提高加工精度和加工效率。
实时智能补
偿主要包括两种方法:一种是反馈补偿,即将误差进行反馈并进行补偿;另一种是前馈补偿,即预测误差并在中途进行补偿,以减小实际
误差。
数控机床误差测量与实时智能补偿技术已经得到了广泛的应用,
其主要作用有以下几点:首先,可以提高数控机床的加工精度和加工
效率,从而提高产品的质量;其次,可以减少废品率,降低生产成本;第三,可以提高数控机床的稳定性和可靠性,从而延长设备的使用寿命。
总之,数控机床误差测量与实时智能补偿技术是数控机床加工领
域中的关键技术之一,其应用前景十分广阔。
随着技术的不断发展和
完善,相信它将为工程制造业的发展做出更大的贡献。
数控机床误差实时补偿技术及应用

数控机床误差实时补偿技术及应用数控机床误差实时补偿技术是一种通过测量和监控机床的误差,然后通过算法和控制系统来实时修正这些误差的技术。
它可以显著提高机床的加工精度和稳定性,使得加工的零件更加精确和一致。
下面将介绍数控机床误差实时补偿技术的原理、方法和应用。
数控机床误差实时补偿技术的原理是基于机床的误差源和误差特点进行建模,并通过控制系统实时调整机床的运动轨迹来补偿这些误差。
机床的误差主要包括几何误差、动态误差和热误差等。
几何误差是由机床结构、加工刀具和工件等因素引起的,例如导轨的尺寸偏差、传动装置的误差等。
动态误差是由机床运动过程中的惯性力、弹性变形等因素引起的,例如加工过程中的振动和共振等。
热误差是由于机床在工作过程中产生的热源,例如主轴的热膨胀和冷却液的温度变化等。
数控机床误差实时补偿技术的方法一般包括两个步骤:误差测量和误差补偿。
误差测量是通过传感器或测量仪器实时检测机床的误差,并将其反馈给控制系统。
常用的测量方法包括激光干涉法、电容法和光栅尺等。
误差补偿是在控制系统中根据误差测量结果进行数学建模和分析,并根据补偿算法调整控制指令,使得机床的运动轨迹达到期望的精度。
数控机床误差实时补偿技术在实际应用中具有广泛的应用领域。
首先,它可以应用于航空航天领域的高精度零件加工。
航空航天零件对精度和质量要求非常高,数控机床误差实时补偿技术可以有效提高加工精度,降低零件的尺寸偏差和表面光洁度,从而提高航空航天产品的性能和可靠性。
其次,它可以应用于汽车制造领域的模具加工。
模具制造对精度和一致性要求较高,数控机床误差实时补偿技术可以有效减少模具的尺寸和形状偏差,提高模具的加工质量和寿命。
此外,它还可以应用于医疗器械制造、光学仪器加工等领域。
总之,数控机床误差实时补偿技术是一种通过测量和监控机床的误差,并通过控制系统实时调整机床运动轨迹的技术。
它可以显著提高机床的加工精度和稳定性,广泛应用于航空航天、汽车制造、医疗器械等领域,为实现高精度和高质量的零件加工提供了重要的技术手段。
机床热误差产生原因分析及常用补偿办法

机床热误差产生原因分析及常用补偿办法机床热误差是指机床在加工过程中由于温度变化引起的尺寸误差。
机床加工过程中会产生大量的热量,而这些热量会导致机床各个部件的温度发生变化,从而引起机床的尺寸变化。
机床热误差主要由以下几个方面的原因引起:1. 机床结构材料的热膨胀:机床主要由铸铁、钢材等金属材料构成,这些材料在加热后会发生热膨胀。
不同材料的热膨胀系数不同,会导致机床各个部件的尺寸发生变化。
2. 加工过程中的摩擦产热:机床在加工过程中,工件与刀具之间会产生摩擦。
摩擦会产生大量的热量,导致机床各个部件的温度升高。
3. 外界环境温度的变化:机床在使用过程中,周围环境的温度会发生变化。
由于机床与环境之间存在热传导,环境温度的变化会影响机床的温度,从而引起尺寸误差。
为了减小机床热误差对加工精度的影响,常用的补偿办法有以下几种:1. 温度补偿:通过测量机床各个部件的温度,对加工程序进行补偿。
可以根据机床的温度曲线,预测机床的热变形,并根据这些变形信息对加工程序进行修正,使加工结果能够达到设计要求。
2. 热稳定化技术:通过采用一定的散热装置,控制机床的温度升高速度,减小机床的热变形。
常用的方法有:增加散热面积、改善散热条件、利用冷却介质对机床进行冷却等。
3. 工艺调整:根据机床加工过程中的热变形规律,调整工艺参数,以减小热误差对加工精度的影响。
通过减小切削刀片与工件之间的摩擦力,降低机床温度升高速度。
4. 采用合适的材料:选择热稳定性好的材料,降低材料的热膨胀系数,减小机床热误差的产生。
机床热误差的产生原因主要是由材料的热膨胀、摩擦产热和外界环境温度的变化等因素引起的。
为了减小机床热误差对加工精度的影响,可以采取温度补偿、热稳定化技术、工艺调整和选择合适的材料等补偿办法。
这些措施可以有效减小机床热误差,提高加工精度。
机床热误差产生原因分析及常用补偿办法

机床热误差产生原因分析及常用补偿办法一、引言随着科学技术的不断发展,机床在工业生产中发挥着越来越重要的作用。
由于各种因素的影响,机床在工作过程中会产生热误差,影响加工精度和稳定性。
研究机床热误差的产生原因,寻求有效的补偿办法,对提高机床加工精度具有重要的意义。
本文将对机床热误差产生原因进行分析,并介绍常用的补偿办法。
二、机床热误差产生原因分析1. 机床结构变形机床在工作过程中,由于受到切削力和惯性力的作用,会导致机床结构的变形。
特别是高速加工时,机床的结构变形更加显著。
这些结构变形会导致机床的位置精度和直线度产生偏差,从而影响加工精度。
2. 主轴热变形在机床工作过程中,主轴由于长时间高速运转,会产生较大的热量。
热量的积聚会引起主轴材料的热膨胀,导致主轴的几何形状发生变化,从而影响主轴的旋转精度。
3. 传动系统的热误差机床的传动系统是由各种机械零部件组成,这些零部件在工作过程中会受到热的影响而发生膨胀或收缩。
尤其是在高速、高精度加工时,由于传动系统的热膨胀影响,会引起工件的位置偏差和形状误差。
4. 环境温度变化周围环境的温度变化也会对机床的热误差产生影响。
特别是在季节转换的时候,温度的变化会导致机床零部件的温度梯度不均匀,进而产生热误差。
5. 冷却液系统的稳定性机床的冷却液系统在工作中起着降温和润滑的作用,稳定性对于机床的热误差具有很大的影响。
如果冷却液系统的供给不均匀或温度波动较大,就会导致机床温度分布不均匀,从而引起热误差。
三、机床热误差补偿办法1. 热补偿热补偿是指通过传感器实时监测机床各部位的温度变化,然后根据监测到的温度数据,通过数学模型计算出热误差的补偿值,再加以修正,以实现对机床热误差的补偿。
通过热补偿的方法可以实现对机床热误差的准确修正,提高了机床的加工精度。
2. 结构改进通过优化设计机床结构,采用高强度、高刚性的材料,改进大梁、床身等部位的结构形式,减少机床在工作过程中的结构变形,以减小热误差的产生。
机床热变形及温度补偿
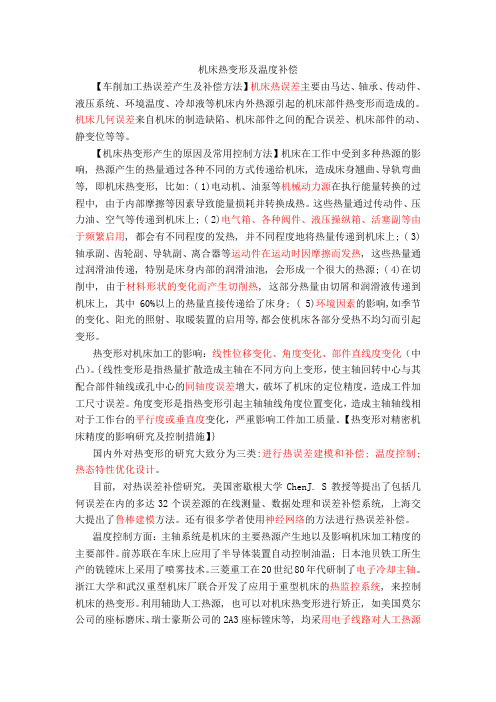
机床热变形及温度补偿【车削加工热误差产生及补偿方法】机床热误差主要由马达、轴承、传动件、液压系统、环境温度、冷却液等机床内外热源引起的机床部件热变形而造成的。
机床几何误差来自机床的制造缺陷、机床部件之间的配合误差、机床部件的动、静变位等等。
【机床热变形产生的原因及常用控制方法】机床在工作中受到多种热源的影响, 热源产生的热量通过各种不同的方式传递给机床, 造成床身翘曲、导轨弯曲等, 即机床热变形, 比如: ( 1)电动机、油泵等机械动力源在执行能量转换的过程中, 由于内部摩擦等因素导致能量损耗并转换成热。
这些热量通过传动件、压力油、空气等传递到机床上; ( 2)电气箱、各种阀件、液压操纵箱、活塞副等由于频繁启用, 都会有不同程度的发热, 并不同程度地将热量传递到机床上; ( 3)轴承副、齿轮副、导轨副、离合器等运动件在运动时因摩擦而发热, 这些热量通过润滑油传递, 特别是床身内部的润滑油池, 会形成一个很大的热源; ( 4)在切削中, 由于材料形状的变化而产生切削热, 这部分热量由切屑和润滑液传递到机床上, 其中60%以上的热量直接传递给了床身; ( 5)环境因素的影响,如季节的变化、阳光的照射、取暖装置的启用等,都会使机床各部分受热不均匀而引起变形。
热变形对机床加工的影响:线性位移变化、角度变化、部件直线度变化(中凸)。
{线性变形是指热量扩散造成主轴在不同方向上变形,使主轴回转中心与其配合部件轴线或孔中心的同轴度误差增大,破坏了机床的定位精度,造成工件加工尺寸误差。
角度变形是指热变形引起主轴轴线角度位置变化,造成主轴轴线相对于工作台的平行度或垂直度变化,严重影响工件加工质量。
【热变形对精密机床精度的影响研究及控制措施】}国内外对热变形的研究大致分为三类:进行热误差建模和补偿; 温度控制; 热态特性优化设计。
目前, 对热误差补偿研究, 美国密歇根大学ChenJ. S教授等提出了包括几何误差在内的多达32个误差源的在线测量、数据处理和误差补偿系统, 上海交大提出了鲁棒建模方法。
数控机床的热稳定性与热误差补偿技术

数控机床的热稳定性与热误差补偿技术随着工业自动化的发展,数控机床在制造业中扮演着重要的角色。
然而,数控机床的热稳定性和热误差一直是制约其精度和稳定性的重要因素。
本文将探讨数控机床的热稳定性问题以及热误差补偿技术的应用。
首先,数控机床的热稳定性是指机床在工作过程中受到热变形和热膨胀等因素的影响,导致工件加工精度下降。
这是因为数控机床在加工过程中会产生大量的热量,而机床的各个部件又具有不同的热膨胀系数。
当机床受热后,不同部件的热膨胀程度不同,从而导致机床的几何形状发生变化,进而影响工件的加工精度。
为了解决数控机床的热稳定性问题,热误差补偿技术应运而生。
热误差补偿技术是通过测量机床在工作过程中的温度分布,然后根据测量结果对机床进行热误差补偿,以提高机床的加工精度和稳定性。
热误差补偿技术主要包括温度传感器的选择和安装、温度测量与分析、热误差模型的建立和热误差补偿算法的设计等方面。
在选择和安装温度传感器时,需要考虑传感器的精度、响应速度、稳定性等因素。
常用的温度传感器有热电偶和热敏电阻等。
热电偶具有响应速度快、测量范围广等优点,但其精度受到环境温度和电磁干扰的影响较大;而热敏电阻则具有精度高、稳定性好等优点,但其响应速度相对较慢。
因此,在选择温度传感器时需要根据具体的应用场景进行综合考虑。
温度测量与分析是热误差补偿技术的重要环节。
通过合理的温度测量与分析,可以获取机床在工作过程中的温度分布情况,为后续的热误差补偿提供准确的数据支持。
在温度测量方面,可以采用红外测温仪、热像仪等非接触式测温设备,以避免对机床结构的影响。
在温度分析方面,可以借助计算机仿真软件对机床的温度分布进行模拟和分析,以揭示机床的热稳定性问题。
热误差模型的建立是热误差补偿技术的核心内容。
热误差模型是通过对机床的温度分布数据进行处理和分析,建立机床的热变形和热膨胀等热误差的数学模型。
热误差模型的建立需要考虑机床的结构特点、材料特性以及温度变化等因素。
一种新的数控机床热误差实时补偿方法

机 械 设 计 与 制 造
24 4
文 章 编 号 :0 13 9 (0 0 0 2 4 0 10 ~ 9 7 2 1 ) 卜0 4 — 2
一
M a h n r De i n c iey sg
&
M a u1月
种新 的数控机床热误差实 时补偿 方法 : } :
别 曾黄麟 、勇
( 四川理工 学院 自动化 与 电子信 息工程 学院 , 成都 630 ) 40 0
A e a p o c f h mal ro o p n a in o n w p r a h o er r r m e s t n NC c ie t o s t e c o ma hn o l
★来稿 只期 :0 9 0 —1 ★基金项 目: 20— 3 8 四川省教 育厅基础应用研究课题基金的部分资助(0 8 4 ) 2 0 A10
第1 期
孙 勇等 : 种新 的数控机 床 热误差 实时补偿 方法 一
25 4
试 验 , 度 分 别 由 (7 ~ 1 ~ 59。 温 2 . 4 . 3 -)变化 , 升 最 大为 1.。和 由 6 3 温 3 , 7
1 引言
精密加工技术 已经成为现代机械制造业 中最重要的组成部 分和发腱方向 , 冈此提高数控加工精度变的尤为重要 , 而数控加
机床热误差产生原因分析及常用补偿办法

机床热误差产生原因分析及常用补偿办法机床热误差是指机床在工作过程中由于热力的影响而产生的误差。
机床在工作过程中会受到加工过程中的大量热源的影响,如主轴传动系统的磨削和加工过程中的摩擦热、电主轴传动系统的电机发热、主轴及导轨系列受到的外部环境温度的影响等。
机床热误差的产生原因主要有以下几个方面:1. 机床结构本身的热膨胀。
机床材料在受热后会发生热膨胀现象,导致机床的尺寸发生变化,进而影响机床的定位精度。
2. 机床工作环境的温度变化。
机床工作环境的温度变化会直接影响机床的工作精度,特别是需要高精度的加工过程中,如果机床工作环境温度变化较大,将会导致机床的加工精度下降。
3. 导轨系列的变形。
导轨系列是机床的重要组成部分,其在机床加工过程中发生的变形会直接影响机床的加工精度。
当导轨系列受到温度的影响时,会发生热变形,导致机床的加工精度下降。
1. 滚动补偿。
机床滚动补偿主要是通过在控制系统中对机床的各个轴进行实时补偿,通过调整机床的位置来补偿热误差的影响。
2. 温度传感器补偿。
在机床的关键位置安装温度传感器,通过测量温度变化来实时监测机床的热变形情况,并通过控制系统对机床进行补偿。
3. 冷却系统。
通过在机床中设置冷却系统,可以有效控制机床工作环境的温度变化,从而减小机床的热误差。
4. 结构改进。
针对机床结构本身的热膨胀问题,可以通过改进结构设计,选用合适的材料,以及采用降低热膨胀系数的方法来减小热误差的影响。
机床热误差的产生对机床的加工精度有着重要的影响,因此需要采取相应的补偿办法来减小热误差的影响。
在使用机床时,需要根据具体情况选择合适的补偿办法,以提高机床的加工精度。
机床热误差产生原因分析及常用补偿办法

机床热误差产生原因分析及常用补偿办法【摘要】本文围绕着机床热误差的产生原因和常用补偿办法展开讨论。
首先介绍了研究背景、研究意义和研究目的,引出了对机床热误差的分析。
在详细分析了机床热误差的产生原因,包括环境温度变化、机床结构刚度和材料特性等方面。
介绍了常用的补偿办法,如温度补偿、结构设计和工艺改进等方法。
最后通过总结和展望,强调了对机床热误差的重视与解决的重要性,为提高加工精度和效率提供了参考。
本文对于了解和应对机床热误差具有一定的指导意义。
【关键词】1. 机床2. 热误差3. 产生原因分析4. 常用补偿办法5. 研究背景6. 研究意义7. 研究目的8. 总结9. 展望1. 引言1.1 研究背景机床热误差是制约数控机床加工精度的重要因素之一,随着机床精度要求的不断提高,对机床热误差的研究也越来越受到重视。
机床在工作过程中,受到外界环境温度的影响以及机械传动元件自身运动和内部热源等因素的影响,都会导致机床温度的变化,进而引起机床热误差的产生。
研究机床热误差的产生原因及补偿办法,有助于提高机床加工精度,保证加工质量,提高生产效率。
在实际生产中,采取有效的补偿措施可以减小机床热误差对加工精度的影响,提高机床的加工稳定性和可靠性。
深入研究机床热误差的产生原因及常用补偿办法具有重要的理论和实践意义,可以为数控加工领域的发展提供技术支撑和参考依据。
1.2 研究意义机床热误差是影响机床加工精度的重要因素之一,研究机床热误差的产生原因及补偿办法具有重要的理论和实际意义。
了解机床热误差产生的原因可以帮助我们更深入地理解机床加工过程中出现的误差,为准确控制机床精度提供理论基础。
通过采取有效的补偿办法来消除或减小机床热误差,可以提高机床加工精度,降低生产成本,提高生产效率,提高产品质量,从而增强企业在市场竞争中的优势。
深入研究机床热误差产生原因和补偿办法具有重要的理论意义和实际应用价值,有助于推动我国机床制造业技术水平的提升,促进制造业的发展和经济的繁荣。
CNC机床加工中的刀具热变形与补偿技术

CNC机床加工中的刀具热变形与补偿技术随着制造业的发展和技术的进步,CNC(Computer Numerical Control,计算机数控)机床在加工领域中得到了广泛应用。
与传统机床相比,CNC机床具有高精度、高效率、高稳定性等优势。
然而,在CNC机床的加工过程中,刀具热变形成为了制约加工质量和精度的因素之一。
为了解决刀具热变形对加工的影响,研究人员开发了各种刀具补偿技术,以实现更精确的加工。
1. 刀具热变形的原因在CNC机床加工过程中,刀具受到的高速转动和切削热的作用,会使刀具产生热量,进而导致刀具自身温度升高。
刀具热变形主要由以下几个方面原因引起:1.1 切削热引起的热膨胀在刀具与工件接触切削时,由于工件材料的高温和切削力的作用,刀具表面会受到切削热的影响,导致刀具表面温度升高,从而产生热膨胀。
热膨胀会导致刀具尺寸变化,进而影响加工精度。
1.2 高速旋转引起的离心力CNC机床刀具在高速旋转时,会产生离心力。
这种离心力对刀具的形状和刚度产生不利影响,进而引起刀具热变形。
1.3 刀具材料的热导率不同刀具材料的热导率不同,会导致刀具不同部位的温度分布不均匀,形成局部热变形。
这不仅影响了刀具的形状,也对加工的精度产生了负面影响。
2. 刀具热变形的影响刀具热变形会对加工过程和加工质量造成多方面的影响。
2.1 加工精度降低刀具热变形导致刀具的实际形状和理论形状不一致,使得加工件的尺寸精度下降,影响加工质量。
2.2 表面质量下降由于刀具热变形导致切削震动增加,会使刀具与工件之间的摩擦增加,最终导致工件表面粗糙度提高,表面质量下降。
2.3 刀具寿命减少刀具热变形会对刀具材料产生一定的热应力,从而对刀具寿命产生不利影响。
长时间的刀具热变形会加速刀具的磨损和损坏,降低刀具寿命。
3. 刀具热变形的补偿技术为了克服刀具热变形对加工质量和精度的影响,研究人员提出了多种刀具热变形的补偿技术。
3.1 刀具预热补偿通过在刀具加工前对刀具进行预热处理,使刀具达到与加工相同的温度,减小加工过程中刀具的热变形。
机床热误差产生原因分析及常用补偿办法
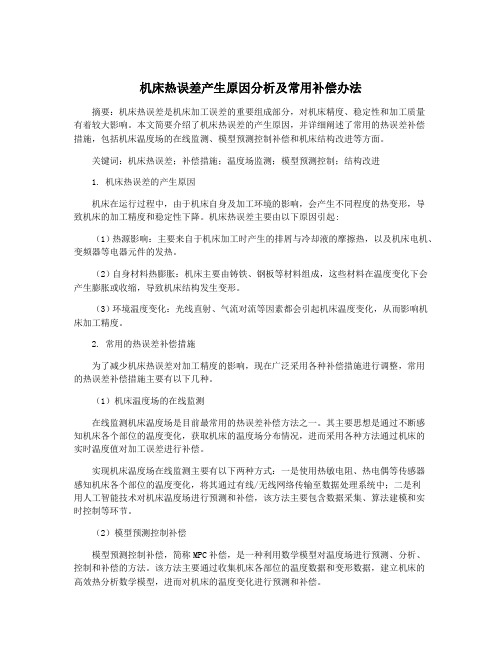
机床热误差产生原因分析及常用补偿办法摘要:机床热误差是机床加工误差的重要组成部分,对机床精度、稳定性和加工质量有着较大影响。
本文简要介绍了机床热误差的产生原因,并详细阐述了常用的热误差补偿措施,包括机床温度场的在线监测、模型预测控制补偿和机床结构改进等方面。
关键词:机床热误差;补偿措施;温度场监测;模型预测控制;结构改进1. 机床热误差的产生原因机床在运行过程中,由于机床自身及加工环境的影响,会产生不同程度的热变形,导致机床的加工精度和稳定性下降。
机床热误差主要由以下原因引起:(1)热源影响:主要来自于机床加工时产生的排屑与冷却液的摩擦热,以及机床电机、变频器等电器元件的发热。
(2)自身材料热膨胀:机床主要由铸铁、钢板等材料组成,这些材料在温度变化下会产生膨胀或收缩,导致机床结构发生变形。
(3)环境温度变化:光线直射、气流对流等因素都会引起机床温度变化,从而影响机床加工精度。
2. 常用的热误差补偿措施为了减少机床热误差对加工精度的影响,现在广泛采用各种补偿措施进行调整,常用的热误差补偿措施主要有以下几种。
(1)机床温度场的在线监测在线监测机床温度场是目前最常用的热误差补偿方法之一。
其主要思想是通过不断感知机床各个部位的温度变化,获取机床的温度场分布情况,进而采用各种方法通过机床的实时温度值对加工误差进行补偿。
实现机床温度场在线监测主要有以下两种方式:一是使用热敏电阻、热电偶等传感器感知机床各个部位的温度变化,将其通过有线/无线网络传输至数据处理系统中;二是利用人工智能技术对机床温度场进行预测和补偿,该方法主要包含数据采集、算法建模和实时控制等环节。
(2)模型预测控制补偿模型预测控制补偿,简称MPC补偿,是一种利用数学模型对温度场进行预测、分析、控制和补偿的方法。
该方法主要通过收集机床各部位的温度数据和变形数据,建立机床的高效热分析数学模型,进而对机床的温度变化进行预测和补偿。
MPC补偿方法能够快速适应机床工作环境的变化,且可以根据用户的需求对模型参数进行调整和优化。
- 1、下载文档前请自行甄别文档内容的完整性,平台不提供额外的编辑、内容补充、找答案等附加服务。
- 2、"仅部分预览"的文档,不可在线预览部分如存在完整性等问题,可反馈申请退款(可完整预览的文档不适用该条件!)。
- 3、如文档侵犯您的权益,请联系客服反馈,我们会尽快为您处理(人工客服工作时间:9:00-18:30)。
实验研究机床热变形误差实时补偿技术李书和 *a 杨世民张奕群张国雄(天津大学精密仪器与光电子工程学院摘要研究了通过实时补偿热误差提高数控机床加工精度的方法 . 采用一维球列加快和简化了热误差的测量 . 利用多元线性回归方法建立了热误差与温度的数学模型 . 在外部微机的帮助下 , 可在加工过程中实时补偿热误差 . 切削实验表明补偿效果良好 .关键词数控机床 , 热误差 , 补偿分类号 T G 502. 15REAL -TIME COMPENSATION FOR THERMALLY INDUCEDERRORS OF MACHINE TOOLSLi Shuhe Yang Shimin Zhang Yiqun Zhang Guoxiong(Scho ol of P recisio n Inst rument and O pto-electr onics Engineer ing , T ianjin U niv ersit yAbstract T his paper is co ncer ned with enhancing the accuracy o f a machine too l thr ough compen-sating ther mal er ro rs in real time . T he 1-D ball ar r ay is used t o acceler ate and simplify the t hermal err or measurement. T he mo del o f ther mal err or and temper ature field is dev elo ped by multi-v ari-v ant r egr ession analy sis technique.W ith the aid o f an ex ternal PC, t he er ro r can be compensat ed in real tim e. T he cutting test show s that the effect of co mpensatio n is satisfacto ry.Keywords N C machine t oo l , thermal er ro r , err or compensatio n科学技术的发展对数控机床的精度和可靠性提出了越来越高的要求 . 大量研究表明 , 热误差是数控机床最大的误差源 , 占总误差的 40%~70%[1]. 减小热误差可通过三种方法 , 即改进设计、温度控制和误差补偿 . 其中误差补偿是一种方便、经济而有效的方法 [2]. 本文以 JCS-018A 立式型加工中心为对象进行了研究 . 首先通过实验建立热误差与机床上若干点的温升之间的数学模型 , 在加工过程中借助外部微机监测温度 , 根据模型计算热误差 , 利用微机与机床数控系统的通讯技术及机床运动的可控性 , 修改进给量 , 从而实现实时补偿 . 1998年 11月No v. 1998天津大学学报 JOURNAL OF TIANJIN UNIVERSITY 第 31卷第 6期 V o l. 31N o. 6a 本文 1997年 1月 8日收到 . 1997年 5月 7日收到修改稿 .*, ,1测量方法1. 1热误差的测量机床热误差是由于内外热源作用下 , 刀具相对工件产生热位移造成的 . 由于丝杠的热膨胀和立柱的热弯曲 , 热误差不仅取决于温度而且随各轴的位置而变化 . 为了全面快速地测量热误差 , 本文采用了一种一维球列检具 . 一维球列即在一刚度足够的基座上等间隔镗一系列尺寸相同的锥孔 , 在锥孔上粘一系列尺寸相同、球度误差很小的钢球 . 使用在 xy z 三个方向同时瞄准球心的三维测头 , 测量球心的坐标 . 以 z 轴为例说明测量原理 , 如图 1a 所示 , 将一维球列装卡在工作台上 , 调整使其与 z 轴平行 . 将测头固定在主轴箱上 , 在机床未升温状态对各球心坐标进行测量 , 测值作为参考值 . 然后 , 机床以一定方式运转 , 每隔一定时间对各球心坐标测量一次 , 在新状态下的测量值相对参考值的变化反映了机床的热漂移 . 从所测热漂移值可以得到各项热误差.(a 工作台 (b 双测头图 1热误差的测量Fig . 1 Thermal error measurement1 机床坐标系零点的漂移$d (t 1, x 0, y 0, z 0 =[x 0(t i -x 0(0 , y 0(t i -y 0(0 , z 0(t i -z 0(0 ](1 式中 :[x 0(0 , y 0(0 , z 0(0 ]为各球心坐标的参考值 ; [x o (t i , y 0(t i , z 0(t i ]为第 t i 时刻各球心坐标的测量值 .2 机床各轴单位长度的热膨胀k lx (t i =[x 2(t i -x 1(t i -x 2(0 +x 1(0 ]/lk ly (t i =[y 2(t i -y 1(t i -y 2(0 +y 1(0 ]/lk lz (t i =[z 2(t i -z 1(t i -z 2(0 +z 1(0 ]/l(2 3 立柱的倾斜立柱倾斜通过测量两个 Z 平面上坐标值 [x 1(t i , y 1(t i ]和 [x 2(t i , y 2(t i ]来确定 . 立柱在 x 方向的热倾斜 :A x (t i =[x 2(t i -x 1(t i -x 2(0 +x 1(0 ]/l (3・ 811・第 31卷第 6期李书和等 :机床热变形误差实时补偿技术A y (t i =[y 2(t i -y 1(t i -y 2(0 +y 1(0 ]/l4 刀轴的热倾斜刀轴倾斜的测量需要使用双测头 , 如图 1b 所示 . 两个测头之间的距离与一维球列的各球心距相等 , 通过测头 a 、 b 的测量值来确定 .刀轴在 x 方向的热倾斜 :B x (t i =[x b (t i -x a (t i -x b (0 +x a (0 ]/l(4刀轴在 y 方向的热倾斜 :B y (t i =[y b (t i -y a (t i -y b (0 +y a (0 ]/l对上述各误差最大的几项进行补偿就可大幅度提高精度 .1. 2温度的测量根据对热源分布、热量传播、敏感部分等的理论分析和初步实验 , 在床身上比较重要的位置分布 12个热敏电阻 , 测量温度 . 热敏电阻的位置和作用如表 1所示 .表 1热敏电阻的位置和作用Tab . 1 The positions and functions of temperature sensors 热敏电阻T 1T 2, T 11, T 12, T 9T 3, T 7, T 8T 5, T 10T 4T 6位置工作台主轴轴套、主轴箱立柱的上下端 Z 轴滚珠丝杠一维球列检具前后轴承、电机轴承作用参考温度主轴的热变形立柱的热膨胀丝杠的热膨胀检具的热膨胀 1. 3测量策略为辨识机床热特性 , 让机床运行方式接近加工状态 , 在不同的坐标下 , 实验方式有三种 :1 主轴以不同的固定转速转动 ;2 主轴按转速谱转动 ;3 主轴转速模拟实际加工过程 . 2热特性的分析在一典型实验中 (主轴转速 n =800r /min, t =0~210m in; n =0r/m in, t=210~300min 发现 , 主轴前后轴承的磨擦热是机床的最大热源 , 温度变化最为剧烈 , 幅值达 4~5℃ . 而立柱的热容量较大 , 温升比较缓慢 , 在主轴停转后立柱温度仍继续上升 . z 轴滚珠丝杠轴承的温度变化很大 . 主轴箱箱体左右的温度变化不太剧烈 . 床身温度和室温变化缓慢 .在热误差方面 , z 轴零点热漂移最大 , 可达 30L m, x 轴和 y 轴热漂移值较小 , 仅为 5L m . 同时 z 轴热膨胀也最大 , 相对零点 100mm 距离的热膨胀达 3~4L m .分析表明 , 该机床 z 轴热误差最大 . 实际上 z 轴热误差是主轴热膨胀、主轴箱热变形、 z 轴滚珠丝杠热膨胀和立柱热变形等几部分造成的 . 其中丝杠膨胀和立柱的弯曲与 z 轴位置有关 , 如图 2示 .图 3为不同 z 坐标下 (z 1=-50, z 2=-150, z 3=-250, z 4=-350 z 轴热漂移的情况 . 开始阶段几条曲线比较相似 , 随时间的推移而逐渐分离 . 这是由于开始阶段热漂移主要是由与位置无关的主轴热位移造成的 , 变化速度比较快 , 很快达到热平衡 . 此后 , 与位置有关的热・ 812・天津大学学报1998年 11月热漂移的不同.图 2 z 轴热误差的分量图 3不同 z 坐标下的热误差Fig . 2 The components of z -axis Fig . 3 Thermal errors at diff erentthermal error z coordinates3热误差的建模由于 z 轴的热误差最大 , 这里只研究 z 轴热误差的建模 . 图 4和图 5为模型拟合热误差和预测新工作状态下热误差的情况.图 4对一新工作条件下 (800r /m in 图 5对一新工作条件下 (DIN 8602转速谱热误差的拟合情况热误差的预测情况Fig . 4 Fitting result of the thermal error at Fig . 5 Prediction result of the thermal error a new cutting condition (800r /min at a new cutting condition (D IN 8602spectr um3. 1误差合成公式z 轴任一坐标处 z 1的热误差为$z (z 1 =$z (z 0 +k (z 1-z 0 (5 式中 :$z (z 0 为 z 轴零点处的热漂移 ; k 为 z 轴单位长度的热膨胀 . 这里只考虑了这两项最显著的误差 .3. 2多元线性回归模型采用线性回归分析分别建立 z 轴零点热漂移和 z 轴热膨胀与温度的模型 . 模型的形式为 [3]・ 813・第 31卷第 6期李书和等 :机床热变形误差实时补偿技术y d =B 0+B 1x 1+B 2x 2+…… +B m x m +E 式中 :yd 为所要估计的热误差; x 1, … , x m 为机床各测温点的温升值 ; B 0, B 1, … , B m 为模型中的未知参数 ; E 为残余误差 . 模型中的参数用最小二乘法估计 .3. 3热敏感点的选择在建立模型时 , 自变量的选择是一个关键问题 . 如果遗漏了重要的变量 , 回归效果一定不会好 . 自变量过多 , 把对因变量影响不显著的也引入 , 会影响方程的稳定性 , 效果也不会好 . 同时 , 实时监测、计算等的任务量也加大了 . 为从 12个候选温度测点中挑选“ 热敏感点” , 从而建立最优模型 , 采用了逐步线性回归方法 . 回归方程每次选入一个变量 , 每选入一个新的自变量后都重新对构成该方程的每个自变量进行一轮新的偏 F 检验 . 如果发现某个自变量的上述边际贡献不显著 , 不论是前期选入的还是现期选入的 , 都要剔除出回归方程 , 并用剩下的自变量重新拟合回归方程 . 这一过程按上述原则一直进行 , 直到待筛选的全部自变量中根据给定的显著水平没有一个再能被选入或排除出刚构成的回归方程为止 . 这些工作都用大型数学工具软件包 SPSS 来实现 . 最终 , 选出 4个“ 热敏感点” , 即工作台、主轴箱箱体、立柱和主轴轴承 . 由图 4和图 5可见模型拟合热误差和预测一种新工作状态下热误差 , 结果比较准确 .4热误差补偿的执行大多数数控系统不具备热误差实时补偿功能 , 所以要借助于外部微机 . 监测机床上 4个点的温度 , 通过接口板采集机床的坐标位置 , 利用存储在微机中热误差模型计算热误差 . 利用微机与数控 CNC 系统的直接通讯技术 , 将补偿值传送到机床控制器 , 通过改变机床零点的位置来实现实时补偿 .为了验证热误差的补偿效果 , 进行了铣削实验 , 以所铣槽深的变化反映热误差 . JCS -018A 的定位精度为 1L m , 加工的工艺条件为 :主轴转速 1000r /m in , 切削量 0. 1m m , 不使用冷却液 . 在相同的条件下进行了多次实验 . 槽深误差由 7L m 减小到 2L m , 补偿效果达到 70%左右 .5结论研究了 JCS-018A 型加工中心热误差的补偿 . 用一维球列测量机床加工空间内的热误差 , 在机床结构的关键位置上布置热敏电阻测量温度 , 制订了测量策略 , 对机床的热特性进行了分析并利用回归分析确定热误差与 4个敏感点的温度之间的关系 . 通过切削实验 , 验证热误差补偿效果非常明显 .参考文献1 Bryan J. International status of th ermal er ror research. Annals of th e CIRP, 1990; 39(2 :645~6562 Chen J S, Yuan J, Ni J e t al . Real-time com pens ation for time-variant volumetric error on a machining center. ASM E Jour nal of Engineering for Ind ustry ,1993; 114:472~4793, ・ 814・天津大学学报1998年 11月。