EQY_3_86电镀层与化学处理层标准
电镀检验标准
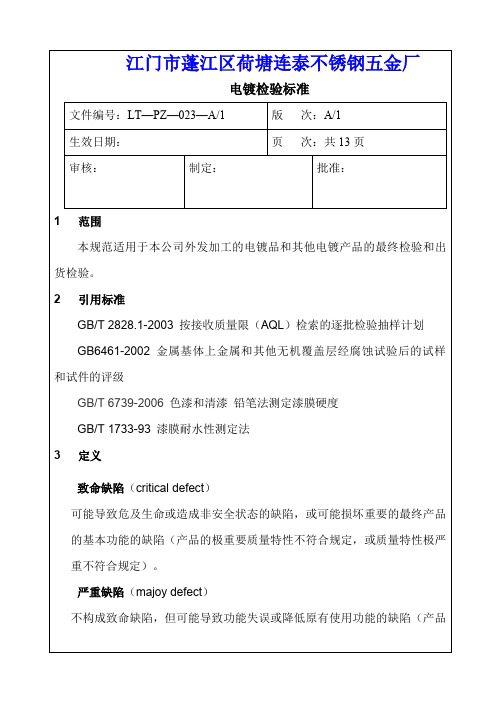
内、外包装箱损坏
√
(√)
内包装纸、袋破损,产品直接与包装盒或箱接触
√
标记或标识模糊
√
6抽样方案
外观检验的抽样
除非客户另有规定,否则按抽样计划表GB/T2828.1—2003
尺寸与配合检验的抽样有配合要求的产品,应对其配合尺寸进行检测。
除非客户另有规定,否则按抽样计划表GB/T2828.1—2003
CR
MA
MI
尺寸
各控制尺寸符合产品标准规定
控制尺寸稍超出公差,但不影响装配
√
控制尺寸超出公差,现场无法装配
√
膜厚
镀层厚度符合产品标准规定
镀层厚度严重低于客户给定的下限值
√
镀层厚度稍低于下限值,且盐雾测试合格
√
耐腐蚀
镀层/漆膜的防腐能力达到规定要求
盐雾测试不通过,不可接受
√
微孔数
大于8000孔/cm2
可靠性试验的抽样
除非客户另有规定,否则,所有可靠性试验(如膜厚、附着力、耐蚀性等)按抽样表执行。
注:可能时,可靠性试验的样本应从上、中、下挂位等量抽取。
替代的抽样方案
如果合同或订单或产品标准中规定了替代的抽样方案,可用其替代表中的方案。
转移规则
所有产品的检验由正常检验开始,批的接收或拒收应符合相应的抽样方案。发现某些批不符合接收准则而拒收时,应在剔除所有不合格品或修正缺陷后,作为连续批再取样和检验。
转移规则:
a)在连续系列批中,如果连续5批中有2批被拒收,则抽样方案由正常检验转入加严检验。
b)若在加严检验中,连续5批被接收,则可以重新恢复正常检验程序。
c)若连续10批停留在加严检验,未能达到符合恢复正常检验要求,则在改进产品质量以前,应停止本规范所规定的抽样检验。
EQY-3-2008电镀层及化学处理层_修改后_
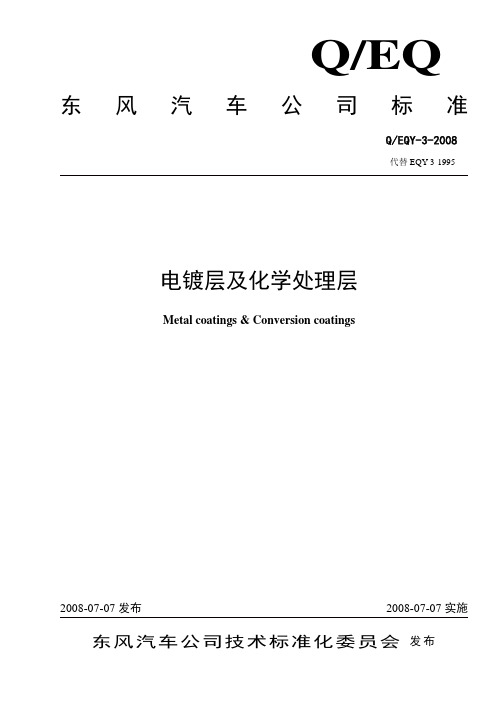
Z8H 镀锌六价铬钝化
Z8G
EP·Zn8 EP·Zn8B EP·Zn8H EP·Zn8G
Z9 驾驶室外部零件
Z9B (保安件及严酷腐蚀件)
Z9H 镀锌六价铬钝化
Z9G
EP·Zn13 EP·Zn13B EP·Zn13H EP·Zn13G
T7
EP·Zn5TC
驾驶室内部零件
T7B
EP·Zn5TB
4 各种镀覆层的表示方法(复合标记)
4.1 通用的表示方法 基体材料/镀覆方法·镀覆名称·镀覆层厚度(或镀覆层等级、镀层单位面积质量)·后处理 其中“·”的标记只出现在“镀覆方法”和“镀覆名称”之间,其它几处省略。
4.2 基体材料的表示符号 金属材料基体用其化学元素符号表示,合金材料基体用其主要成分的化学元素符号表示。常用的基
无铬锌铝涂层
G6
Ct·ZA3、Ct·ZA5
无铬锌铝涂层(黑色)
G7
Ct·ZA3H、Ct·ZA5H
镀铅
P1
Pb3、Pb5、Pb7
镀铜
D1
Cu3、Cu5、Cu7
氧化
Y
CO
锌盐磷化
H1
ZnPh10
锰盐磷化
H2
MnPh5
注 1:一个代号可以对应数个标记(镀层厚度不同),实际镀层厚度是按螺距确定,见 Q/DFLY1017。
镀覆工艺
表面处理代号
相应的复合标记 (注1)
镀锌六价铬白色钝化
Z1
Zn3B、Zn5B、Zn7B
镀锌六价铬彩色强化钝化(注2)
Z2
Zn3EL、Zn5EL、Zn7EL
镀锌六价铬彩色钝化
Z3
Zn3、Zn5、Zn7
镀锌六价铬绿色钝化
电镀国家标准.

中华人民共和国国家标准金属覆盖层钢铁制品热镀锌层技术要求Metallic coatings——Hot dip galvanized coatingson fabricated ferrous products—SpecificationGB/T 13912-92本标准参照采用国际标准 ISO 1459——1973(E)《金属覆盖层——热铰锌防腐蚀层——指导原则》和 ISO 1461——1973(E)《金属覆盖层——钢铁制品热镀锌层——技术条件》。
1 主题内容与适用范围本标准规定了钢铁制品上热镀锌层的技术要求。
本标准适用于钢铁制品防腐蚀的热镀锌层。
本标准不适用于未加工成形的钢铁线材、管材和板材上的热镀锌层。
本标准对热镀锌前基体材料的性质、表面状态不作规定。
影响热镀锌效果的基体材料状况参见附录A(参考件)。
本标准对热镀锌产品的后处理未作规定。
2 引用标准GB 2828 逐批检查计数抽样程序及抽样表(适用于连续批的检查)GB 4956 磁性金属基体上非磁性覆盖层厚度测量磁性方法GB 12334 金属和其他无机覆盖层关于厚度测量的定义和一般规则GB/T 13825 金属覆盖层黑色金属材料热镀锌层的质量测定称量法3 术语3.1热镀锌将钢件或铸件浸入熔融的锌液中在其表面形成锌—铁合金或锌和锌—铁合金覆盖层的工艺过程和方法。
3.2热镀锌层(简称:镀层)采用热镀锌方法所获得的锌—铁合金或锌和锌—铁合金覆盖层。
3.3主要表面指制件上热镀锌前和热镀锌后的某些表面。
该表面上的镀层对于制件的外观和(或)使用性能是起主要作用的。
3.4 检查批(简称:批)为实施抽样检查汇集起来的热镀锌件。
在热镀锌厂检验时,指一个生产班内同一镀槽中生产的相同类型和大小的热镀锌件。
交货后由需方检验时,指一次订货或一次交货量。
3.5 样本从批中随机抽取的镀件或镀件组。
3.6基本测量面在主要表面上进行规定次数测量的区域。
3.7局部厚度在基本测量面内进行规定次数厚度测量的算术平均值。
电镀层和化学处理层技术条件

电镀层和化学处理层技术条件目录1 围 (2)2 规性引用文件 (2)3 技术要求 (2)3.1 使用条件 (2)3.2 选择原则 (2)3.3 锌电镀层 (3)3.4 铜电镀层 (3)3.5 镍镀层 (3)3.6 铬镀层 (4)3.7 锡镀层 (4)3.8 银镀层 (4)4 覆盖层厚度标识方法 (4)4.1 覆盖层组成部分 (4)4.2 紧固件镀层厚度 (7)5 表面质量及镀层检验 (7)5.1 表面质量 (7)5.2 湿热试验 (7)5.3 盐雾试验 (8)5.4 覆层 (8)6 运输及贮存 (8)6.1 运输 (8)6.2 贮存 (8)电镀层和化学处理层技术条件1 围本标准规定了产品零(部)件金属电镀层和化学处理层(以下简称覆盖层)的使用条件分类、选用原则、厚度及标识方法、表面质量和镀层检验、运输及贮存。
本标准适用于产品零(部)件(金属和非金属制件)的电镀和化学处理。
本标准在图样、技术文件中引用时,其标注方法为:电镀层和化学处理按Q/JC J129。
2 规性引用文件下列文件对于本文件的应用是必不可少的。
凡是注日期的引用文件,仅所注日期的版本适用于本文件。
凡是不注日期的引用文件,其最新版本(包括所有的修改单)适用于本文件。
GB/T 131—2006 产品几何技术规(GPS)技术产品文件中表面结构的表示法GB/T 2423.4—2008 电工电子产品环境试验第2部分:试验方法试验Db:交变湿热(12h+12h循环)GB/T 2423.17—2008 电工电子产品环境试验第2部分:试验方法试验Ka:盐雾GB/T 2828.1—2012 计数抽样检验程序第1部分:按接收质量限(AQL)检索的逐批检验抽样计划GB/T 5267.1—2002 紧固件电镀层GB/T 9797—2005 金属覆盖层镍+铬和铜+镍+铬电镀层GB/T 9798—2005 金属覆盖层镍电沉积层GB/T 9799—2011 金属及其他无机覆盖层钢铁上经过处理的锌电镀层GB/T 11379—2008 金属覆盖层工程用铬电镀层GB/T 12599—2002 金属覆盖层锡电镀层技术规和试验方法GB/T 12600—2005 金属覆盖层塑料上镍+铬电镀层GB/T 13346—2012 金属及其它无机覆盖层钢铁上经过处理的镉电镀GB/T 13911—2008 金属镀覆和化学处理标识方法GB/T 17461—1998 金属覆盖层锡-铅合金电镀层GB/T 17462—1998 金属覆盖层锡-镍合金电镀层ISO 4521 金属覆盖层工程用银和银合金电镀层3 技术要求3.1 使用条件覆盖层使用条件,按气候环境变化的程度分为三类。
电镀锌层技术条件

电镀锌层技术条件前言本标准根据GB/T1.1-2000《标准化工作导则第1部分:标准的结构和编写规则》首次制定了《电镀锌层技术条件》。
本标准自实施之日起,EQY-3-95《电镀层及化学处理层》第8.1节"镀锌层"停止执行。
本标准由东风汽车公司标准化委员会工艺材料标准化分委会提出。
本标准由东风汽车公司工艺研究所技术归口。
本标准起草单位:东风汽车公司工艺研究所。
1 范围本标准规定了在铁基体材料上,在水溶性电解液中,用电解的方法获得的锌层。
本标准适用于东风汽车公司产品开发部门设计的、东风汽车公司生产的各类汽车所使用的零部件及总成电镀锌层的质量控制和验收。
2 规范性引用文件下列文件中的条款通过本标准的引用而成为本标准的条款。
凡是注日期的引用文件,其随后所有的修改单(不包括勘误的内容)或修订版均不适用于本标准,然而,鼓励根据本标准达成协议的各方研究是否可使用这些文件的最新版本。
凡是不注日期的引用文件,其最新版本适用于本标准。
GB 4956-85磁性金属基体上非磁性覆盖层厚度测量磁性方法GB 5267-85螺纹紧固件电镀层GB 5270-85金属基体上金属覆盖层附着强度试验方法GB 6462-86金属和氧化物覆盖层横断面厚度显微镜测量方法GB 6463-86金属和其它无机覆盖层厚度测量方法评述GB/T 10125-1997人造气氛腐蚀试验盐雾试验3 术语3.1 主要表面在工件的某些表面上,其镀层对制件的外观和(或)使用性能起着重要作用。
3.2 厚度镀层厚度是指在工件的主要表面上,凡是能与直径为20mm的球体相接触的部位上的镀层厚度的最小值。
4 镀覆层的表示方法4.1 通用镀覆表示方法基体材料/镀覆方法²镀覆名称²镀覆层厚度²镀覆层特征²后处理对于电镀锌可以是:基体材料/镀覆方法²镀覆名称²镀覆层厚度²钝化膜类型²其它后处理4.2 铁基体上电镀锌表示方法4.2.1 完整的表示方法例如EP²Zn6CEQ其中EP表示电镀;Zn表示锌;6表示镀层厚度为6μm;C表示彩色钝化;E表示强化钝化;Q表示除氢处理(各种后处理标记见6.2节和6.3节)。
公司标准电镀层及化学处理层标准
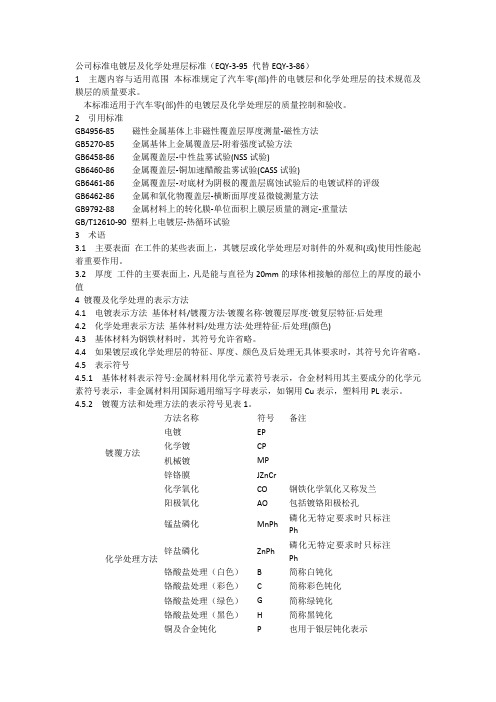
公司标准电镀层及化学处理层标准(EQY-3-95 代替EQY-3-86)1主题内容与适用范围本标准规定了汽车零(部)件的电镀层和化学处理层的技术规范及膜层的质量要求。
本标准适用于汽车零(部)件的电镀层及化学处理层的质量控制和验收。
2引用标准GB4956-85磁性金属基体上非磁性覆盖层厚度测量-磁性方法GB5270-85金属基体上金属覆盖层-附着强度试验方法GB6458-86金属覆盖层-中性盐雾试验(NSS试验)GB6460-86金属覆盖层-铜加速醋酸盐雾试验(CASS试验)GB6461-86金属覆盖层-对底材为阴极的覆盖层腐蚀试验后的电镀试样的评级GB6462-86金属和氧化物覆盖层-横断面厚度显微镜测量方法GB9792-88金属材料上的转化膜-单位面积上膜层质量的测定-重量法GB/T12610-90 塑料上电镀层-热循环试验3术语3.1主要表面在工件的某些表面上,其镀层或化学处理层对制件的外观和(或)使用性能起着重要作用。
3.2厚度工件的主要表面上,凡是能与直径为20mm的球体相接触的部位上的厚度的最小值4 镀覆及化学处理的表示方法4.1电镀表示方法基体材料/镀覆方法·镀覆名称·镀覆层厚度·镀复层特征·后处理4.2化学处理表示方法基体材料/处理方法·处理特征·后处理(颜色)4.3基体材料为钢铁材料时,其符号允许省略。
4.4如果镀层或化学处理层的特征、厚度、颜色及后处理无具体要求时,其符号允许省略。
4.5表示符号4.5.1基体材料表示符号:金属材料用化学元素符号表示,合金材料用其主要成分的化学元素符号表示,非金属材料用国际通用缩写字母表示,如铜用Cu表示,塑料用PL表示。
4.5.2镀覆方法和处理方法的表示符号见表1。
方法名称符号备注镀覆方法电镀EP化学镀CP机械镀MP 锌铬膜JZnCr化学处理方法化学氧化CO 钢铁化学氧化又称发兰阳极氧化AO 包括镀铬阳极松孔锰盐磷化MnPh磷化无特定要求时只标注Ph锌盐磷化ZnPh磷化无特定要求时只标注Ph铬酸盐处理(白色) B 简称白钝化铬酸盐处理(彩色) C 简称彩色钝化铬酸盐处理(绿色)G 简称绿钝化铬酸盐处理(黑色)H 简称黑钝化铜及合金钝化P 也用于银层钝化表示4.5.3镀层厚度用阿拉伯数字表示,单位为μm。
电镀层及化学处理层厚度标准

鎳層的保護
• 镍层表面保护剂 型号: NI605 成 分:日本进口稀释剂及各种添加剂 用 途:用于镍镀层的表面防护 功 能:防止镍镀层表面的腐蚀变色,减小摩擦,增大耐磨性,也适 用于锌、铝、铬等金属。 状 态:无色透明低粘度液体 密 度:15℃ 1.32 g/cm3 粘 度:20℃ 1.30 cst 流 动 点:-30℃以下 引 火 点:无 接触电阻:2m欧姆 以下(涂敷试片时) 体电阻系:1010欧姆 ·cm 以上 工作温度:-60℃~+100℃ 涂敷温度:室温 涂敷用量:约28g/m2 使用方法:将工件浸涂(或刷涂)1分钟,常温下自然干燥3分钟即可 包 装:5kg铁桶装 贮 存:阴凉避光处保存
電鍍
• 電鍍5要素: • 1.陰極:被鍍物,指各種接插件 • 2.陽極:若是可溶性陽極,則為欲鍍金屬;
若是不可溶性陽極,大部份是貴金屬(如 白金)
• 3.電鍍藥水:含有要鍍金屬離子的電鍍藥 水
• 4.電鍍槽:儲存電鍍藥水 • 5.整流器:提供直流電源的設備 • 簡單流程:
氧化層的去除
1.用稀盐酸溶解(镍单质与非氧化性稀酸的作 用十分缓慢)。 2.以镍为阴极电解氢氧化钠溶液(导电性较 好),氧化镍就会被还原为镍。 3.氨水去除
鍍鉛層
備註: 铅的外观呈灰黑色,有毒性,光泽性镀铅也呈灰色,所以由于外观和环境维 护的缘由而在运用下遭到限制,但是铅的共同功用使许多产品依然对镀铅有 需求。铅有较好的抗硫性,抗稀盐酸及稀硫酸功用也很好,但无机酸(如草 酸、醋酸、果酸等)对它有肯定的浸蚀作用,所以镀铅不能用于饮食盛皿的 镀层。
鍍錫層
電鍍鎳層
備註: 1 镀镍层建议采用双层镍,但光亮镍的厚度应不大于镍层总厚度的25%。 2.美觀抗腐蝕 3.銀色偏黃
電鍍鉻(gè)層
一汽富维高新电镀零件检验标准

Q/FAGX长春一汽富维高新汽车饰件有限公司企业标准Q/FAGXES11-B-001-2010-1 汽车用塑料电镀零件检验标准2010-10-29发布2010-11-01实施编制:滕国岩审核:批准:批准:2010-11-29长春一汽富维高新汽车饰件有限公司发布目录1.目的032.范围033.术语03-044.检验规范04 4.1.检验区域划分04 4.1.1.划分区域04-05 4.1.1.1.直视面05 4.1.1.1.1.A区05 4.1.1.1.2.B区06 4.1.1.2.侧视面06 4.1.1.3.俯视面06-07 4.1.1.4.装配隐藏面07 4.1.1.5.装车隐藏面07-08 4..2.缺陷等级定义09 4.2.1.A类缺陷09 4.2.2.B类缺陷09 4.2.3.C类缺陷09 4.3.缺陷定义09-11 4.4.检验方式规定12 4.5.各区域检验标准12-14 4.6分区检验原则15 4.7所有周边类检测面及区域划分15-281. 目的:以顾客为导向,加强对相应缺陷的控制以检验标准为依据,客观进行评价防止不必要的竞争,优化电镀零件制造展望适应新规则以顾客要求和改进能力为基础,进行竞争形势分析引入奥迪特短时间评审2. 范围:适用于汽车塑料电镀零件外观检验客户:一汽大众,一汽轿车,墨西哥大众。
3. 术语:3.1 电镀:电镀就是利用电解的方式使金属或金属合金沉积在工件表面,以形成均匀、致密、结合力良好的金属层的过程;3.2 检验:为确定某一物质的性质、特征、组成等而进行的试验,或根据一定的要求和标准来检查试验对象品质的优良程度。
3.2.1通常把对物理特性的检验称为物理检验;3.2.2对化学性质或组成的检验称为化学检验或简称化验。
3.2.3检验一般有破坏性检验和非破坏性检验,前者只能从整体中取样进行抽查,然后用数理统计方法推定整体的情况;后者可对整体进行逐个检查。
3.2.4 从被检对象的类别考虑,人们又常将它分为半成品检验、成品检验或商品检验等。
电镀标准要求

一:塑胶产品电镀工艺(水电镀与真空电镀)简介塑胶产品电镀工艺简介:常见的塑胶产品电镀工艺有两种:水电镀和真空离子镀。
1、水电镀:一般适用于ABS料、ABS+PC料的产品。
主要工艺是将需电镀的产品放入化学电镀液中进行电镀。
根据客户的不同需要,可镀成不同的颜色,与高光银色、亚银色、灰银色。
因为电镀后的产品其导电性显著增强,对于某些需绝缘的部件怎么办?办法有两种:其一,在需绝缘的部位涂上绝缘油,该部位在电镀时就不会被电镀到,从而达到绝缘效果!当然,涂了绝缘油的部位会变黑,就不适宜作为外观面了。
其二,在需电镀的部位用特殊的胶纸贴住,保护起来,同样达到绝缘的效果。
2、真空离子镀,又称真空镀膜:一般适用范围较广,如ABS料、ABS+PC料、PC料的产品。
同时因其工艺流程复杂、环境、设备要求高,单价比水电镀昂贵。
现对其工艺流程作简要介绍:产品表面清洁、去静电--〉喷底漆--〉烘烤底漆--〉真空镀膜--〉喷面漆--〉烘烤面漆--〉包装。
真空电镀可分为一般真空电镀、UV真空电镀、真空电镀特殊;工艺有蒸镀、溅镀、枪色等。
3、两种工艺的区别:水电镀因工艺较简单,从设备到环境得要求均没有真空离子镀苛刻,从而被广泛应用。
在东莞很容易找到此类的供应商。
而真空电镀优秀供应商在东莞、深圳两地不是很多,至少俺目前没有太多此类供应商信息。
但,水电镀有个弱点,只能镀ABS料和ABS+PC料(此料镀的效果也不是很理想)。
而ABS料耐温只有80℃,这使得它的应用范围被限制了。
而,真空电镀可达200℃左右,这对使用在高温的部件就可以进行电镀处理了。
像风嘴、风嘴环使用PC料,这些部件均要求耐130℃的高温。
另,一般要求耐高温的部件,做真空电镀都要在最后喷一层UV 油,这样使得产品表面即有光泽、有耐高温、同时又保证附着力。
4、两种工艺的优缺点:A、简单来说,如真空电镀不过UV油,其附着力很差,无法过百格TEST,而水电镀的明显好于真空电镀!因此,为保证真空电镀的附着力,均需后续进行特殊的喷涂处理,成本当然高些。
电镀层的选择及标记对电镀层的要求

电镀层的选择及标记对电镀层的要求第一節镀层使用条件的分类 1 第二節电镀层的选择 1 第三節金属镀层的表示方式(GB-1238-76) 5 第四節金属镀层的表示方式(JIS H 0404) 5第一节对电镀层的要求电镀层的主要目的用于﹕1.保护金属零件表面﹐防止腐蚀2.装饰零件外表﹐使外表美观3.提高零件的工作性能电镀层种类和厚度的选择﹐主要取决于下列因素﹕1.零件的工作环境2.被镀零件的种类﹑材料和性质3.电镀层的性质和用途4.零件的结构﹑形状和尺寸的公差5.镀层与其互相接触金属的材料﹑性质对电镀层的要求﹕1.镀层与基体金属﹑镀层与镀层之间﹐应有良好的结合力2.镀层应结晶细致﹑平整﹑厚度均匀3.镀层应具有规定的厚定和尽可能少的孔隙4.镀层应具有规定的各项指针﹐如光亮度﹑硬度﹑导电性等第二节镀层使用条件的分类镀层的使用条件﹐按照气候环境程度分为以下三类。
第一类腐蚀性比较严重的工作环境第二类腐蚀性中等的工作境第三类腐蚀性轻微的工作环境从保护基体金属免腐蚀的要求来看﹐一般可考虑﹕A.贵金属﹑含铬18%以上的不锈钢﹑轧制的磁性合金材料﹑以及镍铜合金等﹐一般不需再加保护层B.碳钢﹑低合金钢和铸铁制造的零件﹐大气中容易腐蚀﹐应加保护层。
C.铜和铜合金制造的零件﹐根据不同的使用条件﹐采用光亮酸洗﹑钝化﹑电镀或涂漆保护等。
用磷青铜或铍青铜制造的精密零件可以不进行表面处理。
D.铝和铝合金制造的零件﹐可以采用阳极氧化和封闭处理。
E.锌合金制造的可以零件﹐可以采用磷化﹑钝化﹑电镀或涂漆防护第三节电镀层的选择镀层按其用途可分为下列三类﹕1.防护性镀层2.防护-装饰性镀层3.工作保护镀层各类电镀层的特性及作用见电镀层的推荐厚度(JB/288-75)防护-装饰性镀层的推荐厚度见表(1-10)1-11镀覆方法﹑处理方法的符号D.颜色表示方法﹕E.合金镀层的表示方法示例﹕电镀含锡60%的锡铅合金15~~20μmD ‧60SnPb15电镀镍钴磷合金3~~5μm D ‧80Ni20CoP3~5F. 多层镀层的表示方法﹕镀层名称应按镀覆顺序标出每层的名称与厚度﹐层间用斜线“/”隔开。
表面处理作业指导书

篇一:表面处理作业指导书发黑表面处理作业指导书1.目的、范围为保证本公司生产需发黑处理的产品符合技术标准要求而编制的作业指导书,适用于本公司生产的管接头、法兰等附件的发黑处理。
2.准备工作2.1每天上班后开动电源将槽液加热至沸点,扒去槽中的氧化铁(沉淀物);2.2扒去沉淀物后加入0.5kg左右的黄血盐(亚铁氰化钾); 2.3按发黑工艺技术要求加入一定量亚硝酸钠(符合5~8:1); 2.4用温度计测量发黑槽液湿度,确保槽液温度140~144℃,若温度过高要加水,并控制好加热电源;3.发黑工艺去油———(去铜)→酸洗→清洗→氧化(或二次氧化)→清洗→热水清洗→皂化→浸水膜装置换油→入库。
3.1去油3.1.1化学去油naoh100~150克/升+na2co320-27克/升加热至沸点滚桶内加入少量废酸和铁悄; 3.1.2.用汽油或柴油洗洗油; 3.1.3.用喷砂或喷丸去除油及锈;3.1.4.淬火回火的工件可用滚桶去油及锈。
3.2去铜用铬酸250~300克/升+硫酸铵80~100克/升(无铜时可省去此道工序)加水浸1~2分钟,然后再在清水中清洗。
3.3 酸洗用30%工业盐酸浸1~2分钟去除油污及锈酸洗时间不能太长。
3.4 清洗清洗后在弱碱槽内中和,防止酸带入氧化槽中。
3.5 氧化氢氧化钠650~700克/升+亚硝酸钠100~150克/升加热到140~ 144℃,保温30~60分钟naoh: nano2=5~8:1。
3.6 清洗氧化后在流动的清水中冲洗。
3.7 热水清洗热水90~100℃,清洗1~2分钟。
3.8 皂化10%~20%工业皂片或三乙油酸皂加热50~60℃1~2分钟温度不能太高。
3.9 上油浸ms-1水膜置换防锈油.3.10入库4.发黑过程4.1发黑前,工件必须经充分的酸洗和清洗,拉力工件必须垂直装框,便于清洗;4.2发黑时必须严格执行工艺技术要求,液面的油渣要及时捞掉,槽液要及时补充;4.3发黑后须经高压水度分喷洗,经沸水清洗,皂化温度控制在50~60℃; 4.4工件经沥掉过量油后装框、入库。
【汽车行业类】汽车用电镀层和化学处理层

(汽车行业)汽车用电镀层和化学处理层中华人民共和国第壹机械工业部部标准JB2864—81汽车用电镀层和化学处理层本标准适用于汽车及其附件等产品的电镀层和化学处理层。
1本标准包括电镀层和化学处理层的厚度、硬度和耐蚀性等。
电镀层厚度和化学处理层厚度是指零件的主要表面上的最小值。
主要表面是指装配后零件在产品中使用时容易受到腐蚀的、磨损的或其他工作表面。
对通常条件下不容易达到规定厚度的表面,如深孔内部、深凹处等,壹般不作为主要表面。
如有特殊厚度要求时,应在技术文件上注明。
壹、镀锌层2镀锌层的厚度及耐蚀性要求应符合表1规定。
3镀锌层镀后均应经彩虹色钝化处理。
二、镀镉层4镀镉层的厚度及耐蚀性要求应符合表2规定。
注:除特殊需要外,原则上不采用镀镉层。
5镀镜层镀后均应经彩虹色钝化处理。
三、镀锡层6镀锡层的厚度及耐蚀性要求应符合表3规定。
7稳定接触电阻钢件镀锡时,必须镀以5微米铜层为底层。
8接触镀锡(H·Sn)不规定镀层厚度。
9熟浸镀锡(J·Sn)不规定镀层厚度。
四、镀银层10镀银层的厚度及耐蚀性要求应符合表4规定。
11镀后必须进行抗暗处理。
五、镀铅层12镀铅层的厚度及耐蚀性要求应符合表5规定。
13钢件镀铅时,必须镀铜作为底层。
六、镀铜层14镀铜层的厚度要求应符合表6规定。
15防止渗碳镀铜部位的表面光洁度不低于△6,如其光洁度低于▽6时,则应适当增加镀层厚度,以保证防止渗碳的质量。
16接触镀铜(H·Cu)不规定镀层厚度。
七、镀镍层17镀镍层的厚度及耐蚀性要求应符合表7规定。
八、镀硬铬层18镀硬铬层的厚度和硬度要求应符合表8规定。
九、镀松孔铬层19镀松孔铬层的厚度。
松孔层深度及硬度要求应符合表9规定。
注:镀层厚度和松孔层深度不包括磨削量。
20镀后必须去氢。
十、防护装饰性镀铬层21防护装饰性镀铬层的镀层等级应符合表10规定。
22防护装饰性镀铬层的厚度及耐蚀性要求应符合表11规定。
23允许选用不同镀层组合和厚度,但耐蚀性能必须符合该等级规定的指标。
镀层和化学覆盖层技术规范——锌电镀层

(检验和试验方法技术标准)镀层和化学覆盖层技术规范—锌电镀层目次前言 (II)1范围 (1)2规范性引用文件 (1)3术语和定义 (1)4工艺质量要求 (2)5镀层表面质量和性能的检验方法 (6)6镀件验收规则 (7)前言为了提高金属电镀和化学处理件生产制造质量,加强对电镀和化学处理制品生产流程相关环节的监督检验和质量控制,并为电镀层和化学处理层的质量验收和试验方法提供标准,同时为结构设计人员提供参考,特编写本系列标准。
《镀层和化学覆盖层技术规范》为系列标准:a)Q/ZX 12.206.1《镀层和化学覆盖层技术规范-锌电镀层》;b)Q/ZX 12.206.2《镀层和化学覆盖层技术规范-铝合金化学导电氧化》;c)Q/ZX 12.206.3《镀层和化学覆盖层技术规范-镍电镀层》;d)Q/ZX 12.206.4《镀层和化学覆盖层技术规范-铝合金阳极氧化》;e)Q/ZX 12.206.5《镀层和化学覆盖层技术规范-铜+镍+铬电镀层》;f)Q/ZX 12.206.6《镀层和化学覆盖层技术规范-钢铁和铜合金化学转化膜》;g)Q/ZX 12.206.7《镀层和化学覆盖层技术规范-达克罗涂覆层》;h)Q/ZX 12.206.8《镀层和化学覆盖层技术规范-铬电镀层》;i)Q/ZX 12.206.9《镀层和化学覆盖层技术规范-锡电镀层》;j)Q/ZX 12.206.10《镀层和化学覆盖层技术规范-热镀锌和连续电镀锌板材》;……镀层和化学覆盖层技术规范——锌电镀层1范围本标准规定了中兴通讯股份有限公司对金属锌电镀层的工艺质量要求、检验方法和验收规则。
本标准适用于中兴通讯股份有限公司外协加工表面电镀锌(包括彩色钝化、白色钝化、黑色钝化、军绿色钝化)零件的设计、加工和检验。
本标准同时也适用于电镀锌工艺的鉴定和批量生产的质量检验依据。
2规范性引用文件下列文件中的条款通过本标准的引用而成为本标准的条款。
凡是注日期的引用文件,其随后所有的修改单(不包括勘误的内容)或修改版均不适用于本标准,然而,鼓励根据本标准达成协议的各方研究是否使用这些文件的最新版本。
电镀国家标准.

中华人民共和国国家标准金属覆盖层钢铁制品热镀锌层技术要求Metallic coatings——Hot dip galvanized coatingson fabricated ferrous products—SpecificationGB/T 13912-92本标准参照采用国际标准 ISO 1459——1973(E)《金属覆盖层——热铰锌防腐蚀层——指导原则》和 ISO 1461——1973(E)《金属覆盖层——钢铁制品热镀锌层——技术条件》。
1 主题内容与适用范围本标准规定了钢铁制品上热镀锌层的技术要求。
本标准适用于钢铁制品防腐蚀的热镀锌层。
本标准不适用于未加工成形的钢铁线材、管材和板材上的热镀锌层。
本标准对热镀锌前基体材料的性质、表面状态不作规定。
影响热镀锌效果的基体材料状况参见附录A(参考件)。
本标准对热镀锌产品的后处理未作规定。
2 引用标准GB 2828 逐批检查计数抽样程序及抽样表(适用于连续批的检查)GB 4956 磁性金属基体上非磁性覆盖层厚度测量磁性方法GB 12334 金属和其他无机覆盖层关于厚度测量的定义和一般规则GB/T 13825 金属覆盖层黑色金属材料热镀锌层的质量测定称量法3 术语3.1热镀锌将钢件或铸件浸入熔融的锌液中在其表面形成锌—铁合金或锌和锌—铁合金覆盖层的工艺过程和方法。
3.2热镀锌层(简称:镀层)采用热镀锌方法所获得的锌—铁合金或锌和锌—铁合金覆盖层。
3.3主要表面指制件上热镀锌前和热镀锌后的某些表面。
该表面上的镀层对于制件的外观和(或)使用性能是起主要作用的。
3.4 检查批(简称:批)为实施抽样检查汇集起来的热镀锌件。
在热镀锌厂检验时,指一个生产班内同一镀槽中生产的相同类型和大小的热镀锌件。
交货后由需方检验时,指一次订货或一次交货量。
3.5 样本从批中随机抽取的镀件或镀件组。
3.6基本测量面在主要表面上进行规定次数测量的区域。
3.7局部厚度在基本测量面内进行规定次数厚度测量的算术平均值。
电镀检验规范及方法
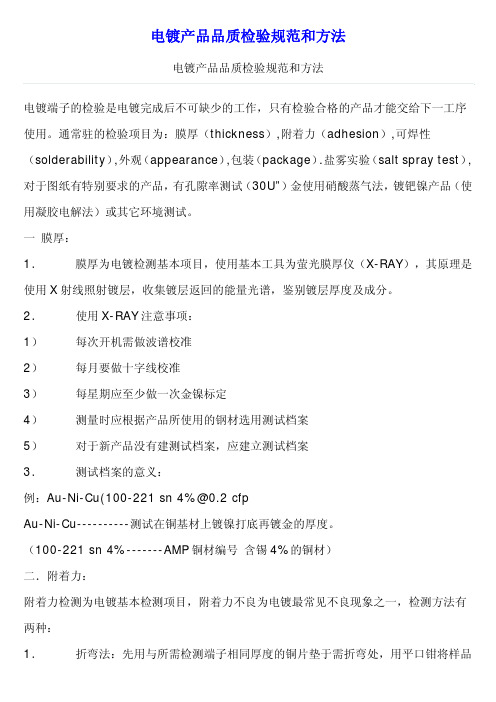
电镀产品品质检验规范和方法电镀产品品质检验规范和方法电镀端子的检验是电镀完成后不可缺少的工作,只有检验合格的产品才能交给下一工序使用。
通常驻的检验项目为:膜厚(thickness),附着力(adhesion),可焊性(solderability),外观(appearance),包装(package).盐雾实验(salt spray test),对于图纸有特别要求的产品,有孔隙率测试(30U”)金使用硝酸蒸气法,镀钯镍产品(使用凝胶电解法)或其它环境测试。
一膜厚:1.膜厚为电镀检测基本项目,使用基本工具为萤光膜厚仪(X-RAY),其原理是使用X射线照射镀层,收集镀层返回的能量光谱,鉴别镀层厚度及成分。
2.使用X-RAY注意事项:1)每次开机需做波谱校准2)每月要做十字线校准3)每星期应至少做一次金镍标定4)测量时应根据产品所使用的钢材选用测试档案5)对于新产品没有建测试档案,应建立测试档案3.测试档案的意义:例:Au-Ni-Cu(100-221 sn 4%@0.2 cfpAu-Ni-Cu----------测试在铜基材上镀镍打底再镀金的厚度。
(100-221 sn 4%-------AMP铜材编号含锡4%的铜材)二.附着力:附着力检测为电镀基本检测项目,附着力不良为电镀最常见不良现象之一,检测方法有两种:1.折弯法:先用与所需检测端子相同厚度的铜片垫于需折弯处,用平口钳将样品弯曲至180度,用显微镜观察弯曲面是否有镀层起皮,剥落等现象。
2.胶带法:用3M胶带紧牢地粘贴在欲试验样品表面,垂直90度,迅速撕开胶带,观察胶带上有载剥落金属皮膜。
如目视无法观察清楚,可使用10倍显微镜观察。
3.结果判定:a) 不可有掉落金属粉末及补胶带粘起之现象。
b) 不可有金属镀层剥落之现象。
c) 在底材未被折断下,折弯后不可有严重龟裂及起皮之现象。
d) 不可有起泡之现象e) 在底材未被折断下,不可有裸露出下层金属之现象。
EQY-3-86电镀层及化学处理层标准

电镀层及化学处理层标准(EQY-3-95 代替EQY-3-86)1 主题内容与适用范围本标准规定了汽车零(部)件的电镀层和化学处理层的技术规范及膜层的质量要求。
本标准适用于汽车零(部)件的电镀层及化学处理层的质量控制和验收。
2 引用标准GB4956-85 磁性金属基体上非磁性覆盖层厚度测量-磁性方法GB5270-85 金属基体上金属覆盖层-附着强度试验方法GB6458-86 金属覆盖层-中性盐雾试验(NSS试验)GB6460-86 金属覆盖层-铜加速醋酸盐雾试验(CASS试验)GB6461-86 金属覆盖层-对底材为阴极的覆盖层腐蚀试验后的电镀试样的评级GB6462-86 金属和氧化物覆盖层-横断面厚度显微镜测量方法GB9792-88 金属材料上的转化膜-单位面积上膜层质量的测定-重量法GB/T12610-90 塑料上电镀层-热循环试验3 术语3.1 主要表面在工件的某些表面上,其镀层或化学处理层对制件的外观和(或)使用性能起着重要作用。
3.2 厚度工件的主要表面上,凡是能与直径为20mm的球体相接触的部位上的厚度的最小值。
电镀层及化学处理层标准(EQY-3-95 代替EQY-3-86)4 镀覆及化学处理的表示方法4.1 电镀表示方法基体材料/镀覆方法·镀覆名称·镀覆层厚度·镀复层特征·后处理4.2 化学处理表示方法基体材料/处理方法·处理特征·后处理(颜色)4.3 基体材料为钢铁材料时,其符号允许省略。
4.4 如果镀层或化学处理层的特征、厚度、颜色及后处理无具体要求时,其符号允许省略。
4.5 表示符号4.5.1 基体材料表示符号:金属材料用化学元素符号表示,合金材料用其主要成分的化学元素符号表示,非金属材料用国际通用缩写字母表示,如铜用Cu表示,塑料用PL表示。
4.5.2 镀覆方法和处理方法的表示符号见表1。
表1方法名称符号备注镀覆方法电镀化学镀机械镀锌铬膜EPCPMPJZnCr化学处理方法化学氧化阳极氧化锰盐磷化锌盐磷化铬酸盐处理(白色)铬酸盐处理(彩色)铬酸盐处理(绿色)铬酸盐处理(黑色)铜及合金钝化COAOMnPhZnPhBCGHP钢铁化学氧化又称发兰包括镀铬阳极松孔磷化无特定要求时只标注Ph磷化无特定要求时只标注Ph简称白钝化简称彩色钝化简称绿钝化简称黑钝化也用于银层钝化表示4.5.3 镀层厚度用阿拉伯数字表示,单位为μm。
D.Zn等表面处理代码含义
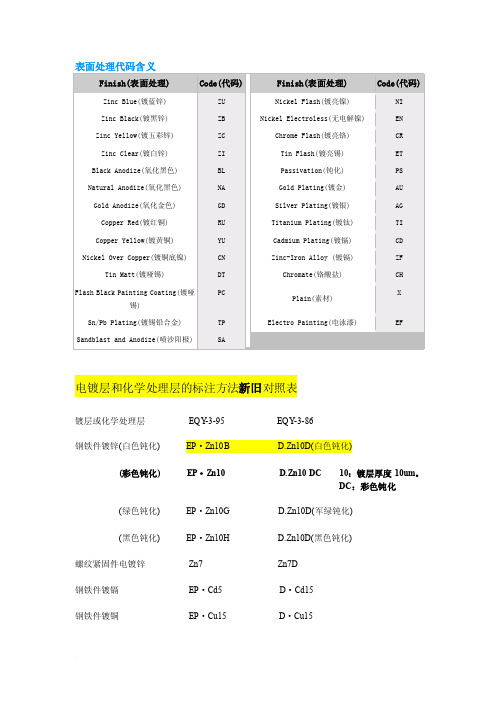
表面处理代码含义Finish(表面处理)Code(代码)Finish(表面处理)Code(代码) Zinc Blue(镀蓝锌) ZU Nickel Flash(镀亮镍) NIZinc Black(镀黑锌) ZB Nickel Electroless(无电解镍) ENZinc Yellow(镀五彩锌) ZC Chrome Flash(镀亮铬) CRZinc Clear(镀白锌) ZI Tin Flash(镀亮锡) ET Black Anodize(氧化黑色) BL Passivation(钝化) PS Natural Anodize(氧化黑色) NA Gold Plating(镀金) AU Gold Anodize(氧化金色) GD Silver Plating(镀银) AG Copper Red(镀红铜) RU Titanium Plating(镀钛) TICopper Yellow(镀黄铜) YU Cadmium Plating(镀镉) CD Nickel Over Copper(镀铜底镍) CN Zinc-Iron Alloy (镀镉) ZF Tin Matt(镀哑锡) DT Chromate(铬酸盐) CHFlash Black Painting Coating(镀哑锡) PCPlain(素材)XSn/Pb Plating(镀锡铅合金) TP Electro Painting(电泳漆) EF Sandblast and Anodize(喷沙阳极) SA电镀层和化学处理层的标注方法新旧对照表镀层或化学处理层EQY-3-95EQY-3-86钢铁件镀锌(白色钝化)EP·Zn10B D.Zn10D(白色钝化)(彩色钝化)EP·Zn10 D.Zn10 DC 10:镀层厚度10um。
DC:彩色钝化(绿色钝化)EP·Zn10G D.Zn10D(军绿钝化)(黑色钝化)EP·Zn10H D.Zn10D(黑色钝化)螺纹紧固件电镀锌Zn7Zn7D钢铁件镀镉EP·Cd5D·Cd15钢铁件镀铜EP·Cu15D·Cu15钢铁件镀铅EP·Pb15D·Pb15铜件镀铅Cu/EP·Pb15D·Pb15螺纹紧固件镀铅Pb7Pb7D钢铁件镀锡EP·Sn15D·Sn15铜件镀镍Cu/EP·Ni6-钢铁件镀硬铬EP·Cr13D·YCr13钢铁件镀松孔铬EP·Cr150AO D·KCr150钢铁件防护装饰性镀铬EP·Cu20Ni30Cr-锌铸件防护装饰性镀铬Zn/EP·Cu20Ni30Cr-钢铁件镀银EP·Ag15P D·Ag15铜件镀银Cu/EP·Ag6P D·Ag6塑料件镀铜镍铬PL/EP·Cu25Ni12Cr-钢铁件化学镀镍CP·Ni25-钢铁件氧化CO H·Y钢铁件锰盐磷化MnPh5H·ML钢铁件锌盐磷化ZnPh10H·FL铝合金阳极氧化Al/AO D·Y·Al铝合金化学氧化Al/CO H·Y·Al锌合金钝化Zn/C H·D铜合金钝化Cu/P H·D转载请注明出自( 六西格玛品质网 ),本贴地址:/thread-23463-1-1.html东风汽车公司标准电镀层及化学处理层标准(EQY-3-95 代替EQY-3-86)1主题内容与适用范围本标准规定了汽车零(部)件的电镀层和化学处理层的技术规范及膜层的质量要求。
电镀层技术条件
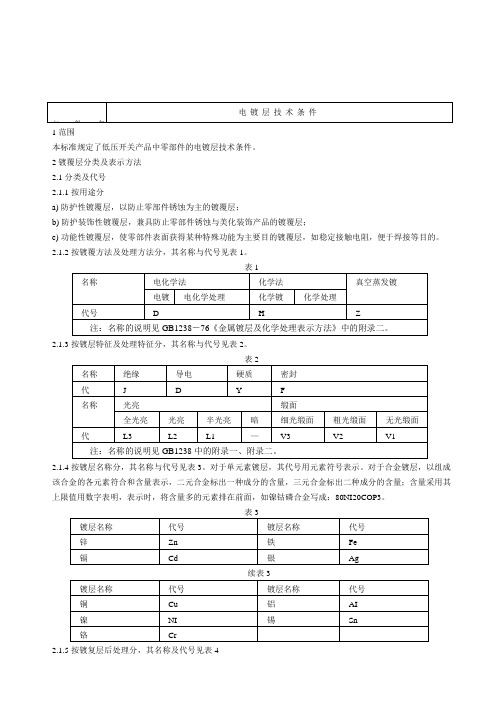
1范围本标准规定了低压开关产品中零部件的电镀层技术条件。
2镀覆层分类及表示方法2.1分类及代号2.1.1按用途分a)防护性镀覆层,以防止零部件锈蚀为主的镀覆层;b)防护装饰性镀覆层,兼具防止零部件锈蚀与美化装饰产品的镀覆层;c)功能性镀覆层,使零部件表面获得某种特殊功能为主要目的镀覆层,如稳定接触电阻,便于焊接等目的。
2.1.2按镀覆方法及处理方法分,其名称与代号见表1。
2.1.3按镀层特征及处理特征分,其名称与代号见表2。
表22.1.4按镀层名称分,其名称与代号见表3。
对于单元素镀层,其代号用元素符号表示。
对于合金镀层,以组成该合金的各元素符合和含量表示,二元合金标出一种成分的含量,三元合金标出二种成分的含量;含量采用其上限值用数字表明,表示时,将含量多的元素排在前面,如镍钴磷合金写成:80NI20COP3。
2.1.5按镀复层后处理分,其名称及代号见表42.2表示方法2.2.1完整表示方法a)表示方法的基本组成及含义见下示:b)对于多层镀层,在表示镀覆层名称与厚度时,应按镀覆顺序标出每层名称与厚度,层间用斜“/”隔开,对于处理层则不表示出厚度。
c)对于需要表示后处理层的颜色时,应在后处理代号后加颜色名称或代号。
常用颜色代号见表5。
后处理,按表4、表5规定的代号表示镀层厚度下限,用数字表示,单位为um(仅电镀层才表示)镀层名称(处理名称)按2.1.4表示镀层特征(处理特征)当需要表示时,按表2规定的代号表示镀覆方法,采用表1规定的代号表示d)当需要表示出镀覆前的表面准备工序时,应在镀覆方法前指出准备工序代号(见表6),并在准备工序代号与镀覆代号之间用—斜线“∕”隔开。
2.2.2标注的简化a)镀覆前的表面准备工序,除非为了保持工件的质量特性或为了获得某种特征之外,一般不以予表示。
b)当镀层厚度不便表示时,可不标注。
c)对于紧固件的镀覆层,当采用电镀电化学处理获得镀覆层时可省略去镀覆方法代号,采用彩虹钝化时允许省略去颜色代号。
- 1、下载文档前请自行甄别文档内容的完整性,平台不提供额外的编辑、内容补充、找答案等附加服务。
- 2、"仅部分预览"的文档,不可在线预览部分如存在完整性等问题,可反馈申请退款(可完整预览的文档不适用该条件!)。
- 3、如文档侵犯您的权益,请联系客服反馈,我们会尽快为您处理(人工客服工作时间:9:00-18:30)。
电镀层及化学处理层标准(EQY-3-95 代替EQY-3-86)1 主题内容与适用范围本标准规定了汽车零(部)件的电镀层和化学处理层的技术规范及膜层的质量要求。
本标准适用于汽车零(部)件的电镀层及化学处理层的质量控制和验收。
2 引用标准GB4956-85 磁性金属基体上非磁性覆盖层厚度测量-磁性方法GB5270-85 金属基体上金属覆盖层-附着强度试验方法GB6458-86 金属覆盖层-中性盐雾试验(NSS试验)GB6460-86 金属覆盖层-铜加速醋酸盐雾试验(CASS试验)GB6461-86 金属覆盖层-对底材为阴极的覆盖层腐蚀试验后的电镀试样的评级GB6462-86 金属和氧化物覆盖层-横断面厚度显微镜测量方法GB9792-88 金属材料上的转化膜-单位面积上膜层质量的测定-重量法GB/T12610-90 塑料上电镀层-热循环试验3 术语3.1 主要表面在工件的某些表面上,其镀层或化学处理层对制件的外观和(或)使用性能起着重要作用。
3.2 厚度工件的主要表面上,凡是能与直径为20mm的球体相接触的部位上的厚度的最小值。
电镀层及化学处理层标准(EQY-3-95 代替EQY-3-86)4 镀覆及化学处理的表示方法4.1 电镀表示方法基体材料/镀覆方法·镀覆名称·镀覆层厚度·镀复层特征·后处理4.2 化学处理表示方法基体材料/处理方法·处理特征·后处理(颜色)4.3 基体材料为钢铁材料时,其符号允许省略。
4.4 如果镀层或化学处理层的特征、厚度、颜色及后处理无具体要求时,其符号允许省略。
4.5 表示符号4.5.1 基体材料表示符号:金属材料用化学元素符号表示,合金材料用其主要成分的化学元素符号表示,非金属材料用国际通用缩写字母表示,如铜用Cu表示,塑料用PL表示。
4.5.2 镀覆方法和处理方法的表示符号见表1。
表1方法名称符号备注镀覆方法电镀化学镀机械镀锌铬膜EPCPMPJZnCr化学处理方法化学氧化阳极氧化锰盐磷化锌盐磷化铬酸盐处理(白色)铬酸盐处理(彩色)铬酸盐处理(绿色)铬酸盐处理(黑色)铜及合金钝化COAOMnPhZnPhBCGHP钢铁化学氧化又称发兰包括镀铬阳极松孔磷化无特定要求时只标注Ph磷化无特定要求时只标注Ph简称白钝化简称彩色钝化简称绿钝化简称黑钝化也用于银层钝化表示4.5.3 镀层厚度用阿拉伯数字表示,单位为μm。
4.6 如有特殊要求,应在镀层或化学处理层后面注明,如: EP·Zn15除氢处理5 电镀和化学处理层在产品图纸上的标注5.1 零(部)件所需的电镀层和化学处理层应作为"技术要求"在产品图纸上或有关技术文件中注明。
5.2 产品图中电镀层和化学处理层的标注方法一般是标注电镀层或化学处理层的标记及其标准号,如:钢铁件镀锌:EP·Zn10B EQY-3-95钢铁件锰盐磷化:MnPh EQY-3-95铝和铝合金阳极氧化:Al/AO EQY-3-955.3 产品图上所标的零件尺寸,除螺纹外,均指镀前加工尺寸,如指包括镀层或化学处理层在内,必须注明;螺纹尺寸均指镀后(成品)尺寸。
5.4 产品图上所标的粗糙度均指镀前的机械加工粗糙度,如指镀后的粗糙度,必须注明。
6 电镀层和化学处理层使用条件分类电镀层和化学处理层的分类根据零部件在汽车上的位置和作用来确定,见表2电镀层及化学处理层标准(EQY-3-95 代替EQY-3-86)7 电镀和化学处理前零件质量的规定7.1 待镀零件应无油污,油漆,金属屑,锈蚀和氧化皮。
7.2 待镀零件应无毛刺,裂纹,磕碰伤,机械变形或其它机械损伤。
7.3 热处理的零件,不允许严重脱碳,不允许带有高温烧结的污垢和锈蚀。
但允许有轻微的氧化色。
7.4 焊接件应无多余的焊料和焊渣,焊缝应经喷砂或其它方法清理。
7.5 带有复杂内腔的焊接件,铸件或液压成形件,应在不影响使用的部位留有便于液,气排出的工艺孔。
7.6 不经机加工的铸件,锻件,其表面应进行喷丸或喷砂处理。
喷后不应有残留的砂粒或未除尽的氧化皮和涂料烧结物。
7.7 经磨削加工的或探伤检查的零件应无剩磁,磁粉及荧光粉等。
7.8 凡设计规定有配合要求的零部件,应留有镀覆层厚度的工艺尺寸。
7.9 凡是金属和橡胶,金属和塑料,冷轧钢和未经清理的热轧钢,精加工件和毛坯件,铆焊件及其他特殊组件需要镀覆时,应先与工艺部门商定,并制定双方同意的技术验收规范。
7.10 表面粗糙度小于Ra1.6的零件,不允许有锈迹。
8 电镀层及化学处理层的技术要求8.1 镀锌层8.1.1 镀锌层的使用条件及厚度见表3。
注:1.紧固件的标记允许省略表示电镀的EP2.厚的电镀锌层有一定的脆性,慎用EP·Zn258.1.2 普通螺纹紧固件,镀层的厚度按表4规定。
注:1、上表的镀层厚度及检验方法也适用于其他镀层,以求量规统一。
2、带螺纹件的平板件,其厚度以螺纹为主,如有特殊要求需另注明。
3、对某些基体酸洗易过腐蚀的零件,镀后通端止端都要检验。
8.1.3 电镀锌后,通常用铬酸盐进行钝化处理,形成铬酸盐转化膜。
铬酸盐转化膜的分类、典型外观、耐蚀性要求、使用条件见表5。
注:1、彩虹色钝化允许省略标记。
2、中性盐雾试验按GB6458的规定进行,出现白色腐蚀产物的时间不能低于表5所列数值。
3、盐雾试验前,铬酸盐转化膜需经室温下至少24h老化。
8.1.4 零件需要保证无氢脆时,应在图纸上注明"除氢处理"。
8.1.5 除氢处理应在镀后4h以内并在铬酸盐转化处理之前进行,其方法按附录A1方法进行。
8.1.6 镀锌层附着强度检验按GB5270进行,也允许将零件置于200°C 烘箱中保温30min , 镀层应不起泡,不脱落。
代8.2.2 防渗碳镀铜部位不允许有毛刺、翻边,基体表面粗糙度不大于Ra1.6,如粗糙度大于Ra1.6时,应适当增加厚度。
8.2.3 防渗碳和防碳氮共渗,镀铜层应无孔隙,检验方法按附录A.2方法进行。
8.3 镀镍层8.3.1 镀镍层的厚度及使用条件见表7。
8.4 镀铬层8.4.1 镀铬层的厚度和硬度要求见表8。
注:表中的镀层厚度不包括磨削量。
8.4.2 活塞环镀铬层结合强度的测定方法按附录A.3方法进行,镀层与基体不应产生分离。
8.5 镀松孔铬层8.5.1 镀松孔铬层的厚度、松孔深度及硬度要求见表9。
8.6 防护装饰性镀铬层8.6.1 防护装饰性镀铬层的厚度及耐蚀性(CASS试验)要求见表10。
注1 镀镍层建议采用双层镍,但光亮镍的厚度应不大于镍层总厚度的25%。
2 建议采用微裂纹铬或微孔铬代替普通铬。
8.6.2 允许采用不同镀层组合和厚度,但耐蚀性能必须符合该等级规定的指标。
8 电镀层及化学处理层的技术要求8.7 镀银层8.7.1 镀银层厚度及耐蚀性要求见表11。
8.7.2 镀银后必须进行电解钝化,抗暗处理。
8.7.3 在钢铁上镀银时,必须先预镀铜层。
8.8 镀铅层8.8.1 镀铅层的厚度及耐蚀性要求见表12。
8.8.2 具有普通螺纹的零件,镀层的厚度及有关检验方法按8.1.2规定。
8.8.3 镀铅层孔隙率应按附录A.2方法进行检查。
8.9 镀锡层8.9.1 镀锡层的厚度及耐蚀性要求见表13。
注: 对于电气产品,允许EP·Sn3用于钎焊。
8.9.2 稳定接触电阻钢件镀锡时,必须镀以5μm 厚的铜底层。
8.10 镀镉层8.10.1 镀镉层的厚度及耐蚀性要求见表14。
8.10.2 除特殊要求外,原则上不采用镀镉层。
8.10.3 镀镉层镀后均应经彩虹色钝化处理,有特殊要求者需在产品图上注明。
8.10.4 镀镉层的弹性零件必须进行除氢处理,其方法按附录A.1方法进行。
电镀层及化学处理层标准(EQY-3-95 代替EQY-3-86)8 电镀层及化学处理层的技术要求8.11 塑料上铜+镍+铬电镀层8.11.1 塑料上铜镍铬电镀层的厚度和耐蚀性能要求见表15。
8.11.2 允许采用不同镀层组合和不同厚度,但耐蚀性能必须符合该等级规定的指标。
8.11.3 结合强度试验,根据使用条件按GB/T12610规定的方法进行。
试验周期为四个热循环,试验后镀层不应出现目视可见的缺陷,如起泡、裂纹或脱落。
8.12 化学镀镍层8.12.1 化学镀镍层的厚度、硬度要求见表16。
注:CP·Ni25Ht表示化学镀镍后需经热处理(一般400℃1h),其硬度值为热处理后的硬度值。
8.12.2 附着强度按GB5270的规定的方法进行。
8.13 钢铁化学氧化、磷化处理8.13.1 钢铁化学氧化、磷化处理的标记,膜层质量及使用条件见表17。
8.13.2 化学氧化膜和磷化膜的孔隙试验采用点滴法,其溶液配制及其试验方法见表18。
8.13.3 化学氧化及防蚀磷化后应随即浸防锈油或乳化液,如特殊要求,须另注明。
8.13.4 膜层应均匀完整,致密,不允许有红色、绿色、白色挂灰。
8.13.5 钢铁件因材质不同,氧化后允许色泽不同。
a、碳钢、低合金钢氧化后为黑色。
b、合金钢因成份或含量不同,氧化膜允许为红褐色、兰黑色或浅黑色。
c、铸铁、铸钢的氧化膜为暗褐色。
8.13.6 单位面积上磷化膜层质量的测定按GB9792规定的方法进行。
8 电镀层及化学处理层的技术要求8.14 铝及铝合金阳极氧化和化学氧化8.14.1 铝和铝合金阳极氧化及化学氧化的氧化膜厚度及耐蚀性要求见表19。
注:因材料不同,工艺不同,膜层色泽不作规定。
8.15 锌合金铬酸盐钝化处理8.15.1 锌合金钝化处理的标记,耐蚀性和使用条件要求见表20。
8.15.2 钝化膜一般为金黄色或带彩虹色。
8.16 铜及铜合金钝化处理铜及铜合金钝化处理的标记,外观要求及使用条件见表21。
8.17 锌铬膜锌铬膜的标记、膜层质量、耐蚀性及使用条件见表22。
注:1、适用于高强度零件,不适用于在280℃以上工作的零件。
2、前处理不允许酸洗。
8.18 机械镀锌机械镀锌的标记、镀层厚度、耐蚀性及使用条件见表23。
注:1、具有普通螺纹的零件、镀层的厚度及有关检验方法按8.1.2规定进行2、前处理不允许酸洗。
3、镀后进行彩色钝化。
4、有润滑要求的需特殊注明。
电镀层及化学处理层标准(EQY-3-95 代替EQY-3-86)9 检验方法与验收规则9.1 镀层厚度的测定按GB4956或GB6462规定的方法进行。
9.2 中性盐雾试验(NSS试验)按GB6458规定的方法进行。
9.3 铜加速醋酸盐雾试验(CASS试验)按GB6460规定的方法进行。
9.4 腐蚀试验结果的检验与评级按GB6461规定的方法进行。
10 电镀层和化学处理层的质量检查10.1 电镀层和化学处理层的厚度等级应符合产品图纸的要求。