齿轮硬度要求
联轴器齿轮硬度标准

联轴器齿轮硬度标准
联轴器齿轮硬度标准一般要求达到HRC48~53,最低硬度值不低于HRC30。
这个标准主要依据齿轮材质和实际使用情况而定,不同的材料和工艺处理的硬度范围不同。
同时,硬度也是衡量齿轮质量的重要指标之一,对于联轴器齿轮的承载能力和使用寿命都有一定影响。
在工业应用中,对于大型重载的齿轮,其硬度通常会比较高,以保证其具有足够的耐磨性和抗冲击能力。
而对于一些精密或轻载的齿轮,则会选择较低的硬度以保证其具有良好的切削加工性和抗疲劳性能。
联轴器齿轮硬度的标准主要取决于齿轮的材料和制造工艺。
对于中碳或低碳钢制造的齿轮,常用的牌号有45、45Cr、40Mn、40MnVB、38CrMoA1A等。
其中,38CrMoA1A是氮化钢,氮化处理后表面硬度可相当于HRC-65\~70。
其他各种牌号通常进行高频加热表面蘸火,其硬度为HRC48\~53。
40Cr也可氮化处理,表面硬度相当于HRC54\~57。
对于受较大冲击载荷的齿轮,可以采用低碳钢和低碳合金制造,常用的牌号有20、20Cr、20CrMoTi、20Mn2B等。
对于硬度标准,金属硬度是衡量金属材料软硬程度的一项重要指标,通常以邵氏硬度或洛氏硬度为标准。
具体来说,联轴器齿轮的硬度标
准应满足36\~49HRC,最低硬度值不低于30HRC。
以上内容仅供参考,具体的技术要求和参数可能因不同的制造工艺和使用场景而有所差异,可以咨询相关机械制造专家或查阅专业机械制造书籍获取更全面和准确的信息。
齿轮的技术要求

齿轮的技术要求
1. 齿轮的精度可太重要了啊!你想想看,要是齿轮精度不够,那机器不就像喝醉了似的,能好好工作吗?就好比手表里的齿轮,要是精度差了那么一点点,那手表还能准确走时吗?
2. 齿轮的硬度也不容忽视呀!不硬的话,那不是很快就会磨损吗?就像人的骨头一样,要是软乎乎的,怎么能支撑起身体呢?
3. 齿轮的表面粗糙度得有要求吧!要是粗糙得很,那不是摩擦超级大,能顺畅运转吗?这就好像粗糙的路面,车子开上去能舒服吗?
4. 齿轮的齿数比例也很关键好不好!要是乱来,那整个系统不就乱套啦?就好像跑步的步伐不协调,能跑得快吗?
5. 齿轮的材料得选好哇!要是质量差的材料,能扛得住长时间使用吗?就跟穿了双劣质鞋子去跑步,能跑多远呢?
6. 齿轮的安装精度也不能马虎哇!装不好的话,那不是会晃来晃去,能正常工作吗?就像搭积木没搭稳,会倒下来一样。
7. 齿轮的润滑也很必要呀!没润滑,那不是干磨,多伤齿轮呀!这就好像没喝水的嗓子,能好受吗?
8. 齿轮的噪音控制也很重要啊!要是嗡嗡响个不停,那多烦人呐!就像一直有只蚊子在耳边叫,能不烦吗?
9. 齿轮的稳定性那可是必须保证的哟!不稳定的话,随时可能出问题呀!就像在风浪中摇摆的小船,多危险啊!总之,齿轮的这些技术要求真是一个都不能忽视啊,它们关系到整个机器的性能和寿命呢!。
汽车齿轮有哪些质量要求

汽车齿轮有哪些质量要求汽车齿轮是汽车传动系统中至关重要的组件之一,负责将发动机产生的动力传递给车轮,使汽车能够运行。
因此,汽车齿轮的质量要求至关重要。
本文将从齿轮材料、齿轮精度、齿轮硬度以及齿轮的耐磨性等方面,详细介绍汽车齿轮的质量要求。
齿轮材料是决定汽车齿轮质量的重要因素之一。
一般而言,汽车齿轮常用的材料包括钢、铸铁和铜合金等。
钢材具有高强度和耐磨性的优点,适合用于高负荷和高速运行的汽车齿轮。
铸铁材料则具有良好的减震性能,适用于需要减少噪音和振动的齿轮传动系统。
铜合金材料则在高温和高速环境下具有较好的耐磨性和耐蚀性,适用于特殊工况下的齿轮传动。
齿轮的精度对于汽车齿轮的质量要求也非常重要。
齿轮精度包括齿轮的模数、齿数、齿廓曲线和齿轮的配合间隙等。
精度高的齿轮能够保证齿轮传动的精确性和稳定性,减少能量损失和噪音。
因此,汽车齿轮的制造过程需要精确的加工和检测设备,确保齿轮的精度符合要求。
齿轮的硬度也是齿轮质量要求的重要方面之一。
齿轮的硬度决定了齿轮的强度和耐磨性。
通常情况下,汽车齿轮的硬度要求在45-55HRC之间,以保证齿轮在长时间高速运行时不会发生变形或磨损。
因此,在齿轮制造过程中,需要进行适当的热处理和淬火工艺,以获得符合要求的硬度。
汽车齿轮的耐磨性也是其质量要求的重要考虑因素之一。
汽车齿轮在长时间高速运行中,会受到较大的摩擦和磨损,因此需要具备良好的耐磨性能。
一般来说,齿轮的耐磨性取决于材料的硬度、表面润滑和齿轮的精度等因素。
为了提高齿轮的耐磨性,可以采用表面渗碳、渗氮等表面处理技术,形成硬度高、耐磨层。
汽车齿轮的质量要求包括齿轮材料的选择、齿轮精度的控制、齿轮硬度的保证以及齿轮的耐磨性等方面。
只有符合这些要求的齿轮才能确保汽车传动系统的正常运行和长久使用。
因此,在汽车齿轮的生产和使用过程中,必须严格遵守这些质量要求,以保证汽车的性能和安全。
球磨机小齿轮(含轴)技术要求03.21
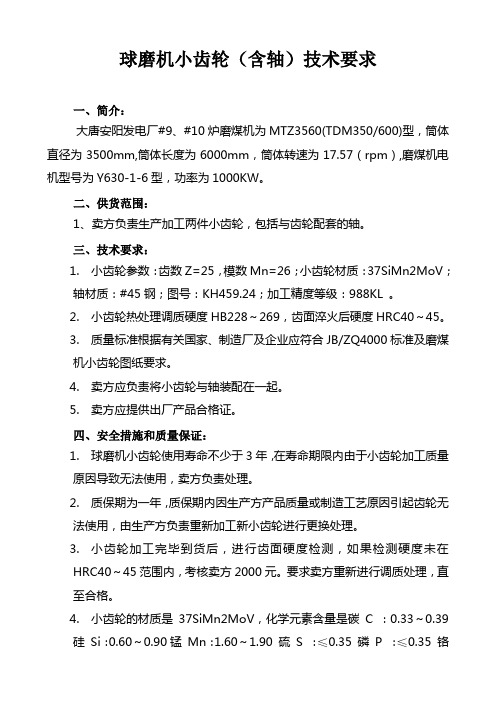
球磨机小齿轮(含轴)技术要求一、简介:大唐安阳发电厂#9、#10炉磨煤机为MTZ3560(TDM350/600)型,筒体直径为3500mm,筒体长度为6000mm,筒体转速为17.57(rpm),磨煤机电机型号为Y630-1-6型,功率为1000KW。
二、供货范围:1、卖方负责生产加工两件小齿轮,包括与齿轮配套的轴。
三、技术要求:1.小齿轮参数:齿数Z=25,模数Mn=26;小齿轮材质:37SiMn2MoV;轴材质:#45钢;图号:KH459.24;加工精度等级:988KL 。
2.小齿轮热处理调质硬度HB228~269,齿面淬火后硬度HRC40~45。
3.质量标准根据有关国家、制造厂及企业应符合JB/ZQ4000标准及磨煤机小齿轮图纸要求。
4.卖方应负责将小齿轮与轴装配在一起。
5.卖方应提供出厂产品合格证。
四、安全措施和质量保证:1.球磨机小齿轮使用寿命不少于3年,在寿命期限内由于小齿轮加工质量原因导致无法使用,卖方负责处理。
2.质保期为一年,质保期内因生产方产品质量或制造工艺原因引起齿轮无法使用,由生产方负责重新加工新小齿轮进行更换处理。
3.小齿轮加工完毕到货后,进行齿面硬度检测,如果检测硬度未在HRC40~45范围内,考核卖方2000元。
要求卖方重新进行调质处理,直至合格。
4.小齿轮的材质是37SiMn2MoV,化学元素含量是碳 C :0.33~0.39 硅Si:0.60~0.90锰 Mn:1.60~1.90 硫 S :≤0.35 磷 P :≤0.35 铬 Cr:≤0.30镍 Ni:≤0.30铜 Cu:≤0.30钒 V :0.60~0.90钼 Mo:0.60~1.50 加工好齿轮后到厂买方对小齿轮材质进行验收,验收不合格考核卖方3000元,并要求卖方重新加工制造。
五、供货周期:1、签订合同后,一个月内供货。
超出供货周期每推迟一天考核1000元。
齿轮的硬度检测方法
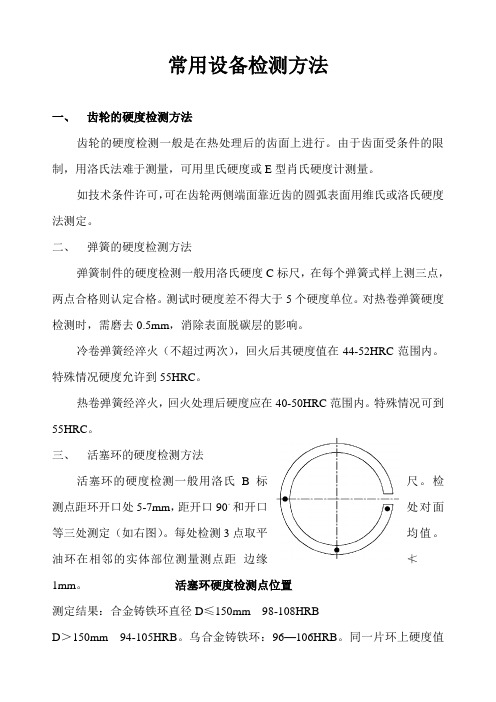
常用设备检测方法一、齿轮的硬度检测方法齿轮的硬度检测一般是在热处理后的齿面上进行。
由于齿面受条件的限制,用洛氏法难于测量,可用里氏硬度或E型肖氏硬度计测量。
如技术条件许可,可在齿轮两侧端面靠近齿的圆弧表面用维氏或洛氏硬度法测定。
二、弹簧的硬度检测方法弹簧制件的硬度检测一般用洛氏硬度C标尺,在每个弹簧式样上测三点,两点合格则认定合格。
测试时硬度差不得大于5个硬度单位。
对热卷弹簧硬度检测时,需磨去0.5mm,消除表面脱碳层的影响。
冷卷弹簧经淬火(不超过两次),回火后其硬度值在44-52HRC范围内。
特殊情况硬度允许到55HRC。
热卷弹簧经淬火,回火处理后硬度应在40-50HRC范围内。
特殊情况可到55HRC。
三、活塞环的硬度检测方法活塞环的硬度检测一般用洛氏B标尺。
检测点距环开口处5-7mm,距开口90。
和开口处对面等三处测定(如右图)。
每处检测3点取平均值。
油环在相邻的实体部位测量测点距边缘≮1mm。
活塞环硬度检测点位置测定结果:合金铸铁环直径D≤150mm 98-108HRBD>150mm 94-105HRB。
乌合金铸铁环:96—106HRB。
同一片环上硬度值差≯3 HRB。
四、焊接接头的硬度检测方法焊接接头及堆焊金属的硬度实验GB2654-89规定:焊接件硬度可用布氏、洛氏、维氏硬度试验方法检测。
试样检测面与支承面应经加工磨平。
厚度小于3mm的焊接接头允许在其表面测定硬度。
测定位置按下图焊接件硬度的测定位置标线进行。
测试时应注意避开焊接缺陷处。
焊接件硬度的测定位置标线五、金属覆盖层检测方法金属覆盖层主要有电沉积层,自催化气度层、喷涂层(包括爆炸喷涂和等离子喷涂层)以及铝材阳极氧化腹膜层等。
1、检测方法覆盖层硬度检测通常是应用显微和小负荷维氏硬度检测方法。
压头除维氏压头外,有时还应选用努普氏压头。
2、检测技术要求检测力大小应慎重选用,因为覆盖层一般都比较薄,如果检测力过大硬度值会受基体材料硬度的影响;如果检测力选用过小,容易引入较大误差,都会影响检测的准确性。
常用的齿轮材料

一、常用的齿轮材料是钢、铸铁和非金属材料。
1、锻钢钢材的韧性好,耐冲击,还可以通过热处理或化学热处理改善其力学性能及提高齿面硬度,故最适应于用来制造齿轮。
除尺寸过大(da>400~600mm)或者是结构形状复杂只宜铸造者外,一般都用锻钢制造齿轮,常用的是含碳量在(0.15~0.6)%的碳钢或合金钢。
制造齿轮的锻钢可分为:软齿面(硬度≤350HBS):经热处理后切齿的齿轮所用的锻钢对于强度、速度及精度都要求不高的齿轮,应采用以便于切齿,并使刀具不致迅速磨损变钝。
因此,应将齿轮毛坯经过正火(正火)或调质处理后切齿。
切制后即为成品。
其精度一般为8级,精切时可达7级。
这类齿轮制造简便、经济、生产效率高。
硬齿面(硬度>350HBS):需进行精加工的齿轮所用的锻钢高速、重载及精密机器(如精密机床、航空发动机)所用的主要齿轮传动,除要求材料性能优良,轮齿具有高强度及齿面具有高硬度(如58~65HRC)外,还应进行磨齿等精加工。
需精加工的齿轮目前多是先切齿,再做表面硬化处理,最后进行精加工,精度可达5级或4级。
这类齿轮精度高,价格较贵,所以热处理方法有表面淬火、滲碳、氮化、软氮化及氰化等。
所以材料视具体要求及热处理方法而定。
合金钢根据所含金属的成分及性能,可分别使材料的韧性、耐冲击、耐磨及抗胶合的性能等获得提高,也可通过热处理或化学热处理改善材料的力学性能及提高齿面的硬度。
所以对于既是高速、重载又要求尺寸小、质量小的航空用齿轮,就都用性能优良的合金钢(如20CrMnTi,20Cr2Ni4A等)来制造。
2、铸钢铸钢的耐磨性及强度均较好,但应经退火及正火处理,必要时也可进行调质。
铸钢常用于尺寸较大的齿轮。
3.铸铁灰铸铁性质较脆,抗冲击及耐磨性都较差,但抗胶合及抗点蚀的能力较好。
灰铸铁齿轮常用于工作平稳、速度较低、功率不大的场合。
4.非金属材料对高速轻载及精度不高的齿轮传动,为了降低噪声,常用非金属材料(如夹布胶木、尼龙等)做小齿轮,大齿轮仍用钢或铸铁制造。
软齿面和硬齿面的界限

软齿面和硬齿面的界限
软齿面和硬齿面是齿轮传动中常用的两种齿面类型,它们的界限主要是根据齿面硬度来划分的。
一般来说,软齿面的硬度通常在 HRC35 以下,而硬齿面的硬度则在 HRC35 及以上。
这个硬度界限并不是绝对的,实际应用中会根据具体情况进行调整。
软齿面通常用于低负载、低速度的传动应用,例如手动工具、家用电器等。
软齿面的加工成本相对较低,因为它们可以通过常规的加工方法(如铣削、磨削等)进行制造。
软齿面的齿轮具有较好的耐磨性和抗胶合性能,但在高负载或高速情况下容易磨损或失效。
硬齿面则适用于高负载、高速度的传动应用,例如工业机械、汽车传动等。
硬齿面的齿轮通常需要采用特殊的加工工艺(如磨削、电火花加工等)来制造,因此加工成本相对较高。
硬齿面的齿轮具有更高的耐磨性、强度和抗疲劳性能,能够承受更高的负载和速度。
需要注意的是,软齿面和硬齿面的选择不仅取决于齿面硬度,还受到传动功率、速度、工作环境等因素的影响。
在实际应用中,需要综合考虑这些因素来选择合适的齿面类型,以确保齿轮传动的可靠性和效率。
总的来说,软齿面和硬齿面的界限是根据齿面硬度来划分的,但具体的选择应根据传动要求和工作条件进行综合考虑。
粉末冶金齿轮强度

粉末冶金齿轮强度粉末冶金齿轮在汽车和摩托车中所占的比例远大于其他领域的粉末冶金零件,那么,粉末冶金齿轮的硬度会是多少?1、普通粉末冶金齿轮(密度6.8-7.0)在扭矩下,可达14NM。
2、粉末冶金齿轮的精度取决于材料的膨胀系数和模具精度。
一般直径50的内齿轮国产模具约为8-9级,模具为7-8级。
锥齿轮还有一个等级高。
粉末冶金齿轮可批量生产,一致性好。
3、用粉末冶金毛坯加工齿轮,强度可提高10%左右。
如何提高粉末冶金齿轮的硬度、强度和精度?硬度:粉末冶金齿轮的硬度密度等级与细后处理密切相关。
粉末冶金齿轮烧结后添加表面水蒸气和渗碳处理等处理方法,提高齿轮硬度,提高处理中的耐磨性,使用寿命长,安全。
强度:齿轮原料中含有廉价木炭,抑制渗碳层,用少量细铁粉提高气体材料的强度,或添加活化烧结的辅助材料,可以有效提高齿轮的强度。
精度:粉末冶金的齿轮精度要控制材料的膨胀系数和模具的精度,国外进口的齿轮模具约为7-8级。
粉末冶金齿轮一般用什么材料?1、也称为粉末冶金摩擦材料、烧结摩擦材料由气体金属(铜、铁或其他合金)、润滑组(铅、石墨、二硫化钼等)、摩擦组(二氧化硅、石棉等)三部分组成。
摩擦系数高,能快速吸收动能,制动、传动速度快,磨损小。
强度高,耐高温,导热系数好。
耐胶合成,抗腐蚀,受油和湿气影响小。
主要用于离合器和制动器的制造。
2、粉末冶金模具材料包括硬质合金、粉末冶金高速钢等。
后者组织均匀、颗粒小、无偏析,比高速钢铸造韧性和耐磨性好,热处理变形少,寿命长。
可用于制造切削工具、模具、零件的原材料。
3、粉末冶金高温材料包括粉末冶金高温合金、高熔点金属和合金、金属陶瓷、分散强化、纤维强化材料等。
用于制造高温下使用的涡轮盘、喷嘴、叶片和其他高温部件。
4、摩擦材料:由基体金属(铜、铁或其他合金)、润滑组元(铅、石墨、二硫化钼等)、摩擦组元(二氧化硅、石棉等)3部分组成。
其摩擦系数高,能很快吸收动能,制动、传动速度快、磨损小,强度高,耐高温,导热性好;抗咬合性好,耐腐蚀,受油脂、潮湿影响小,主要用于制造离合器和制动器。
齿轮材料的基本要求
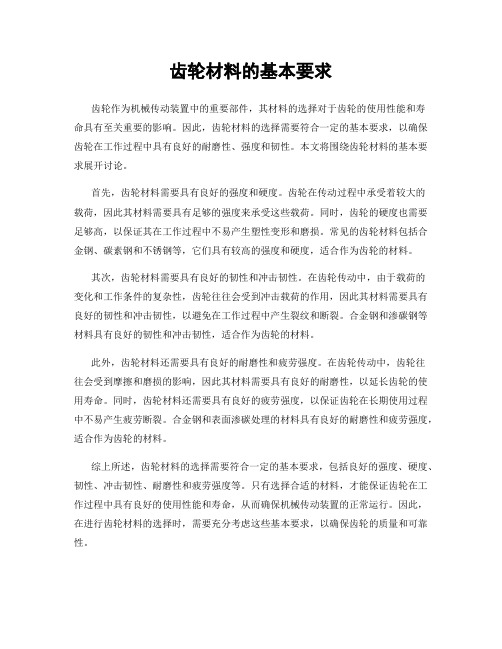
齿轮材料的基本要求齿轮作为机械传动装置中的重要部件,其材料的选择对于齿轮的使用性能和寿命具有至关重要的影响。
因此,齿轮材料的选择需要符合一定的基本要求,以确保齿轮在工作过程中具有良好的耐磨性、强度和韧性。
本文将围绕齿轮材料的基本要求展开讨论。
首先,齿轮材料需要具有良好的强度和硬度。
齿轮在传动过程中承受着较大的载荷,因此其材料需要具有足够的强度来承受这些载荷。
同时,齿轮的硬度也需要足够高,以保证其在工作过程中不易产生塑性变形和磨损。
常见的齿轮材料包括合金钢、碳素钢和不锈钢等,它们具有较高的强度和硬度,适合作为齿轮的材料。
其次,齿轮材料需要具有良好的韧性和冲击韧性。
在齿轮传动中,由于载荷的变化和工作条件的复杂性,齿轮往往会受到冲击载荷的作用,因此其材料需要具有良好的韧性和冲击韧性,以避免在工作过程中产生裂纹和断裂。
合金钢和渗碳钢等材料具有良好的韧性和冲击韧性,适合作为齿轮的材料。
此外,齿轮材料还需要具有良好的耐磨性和疲劳强度。
在齿轮传动中,齿轮往往会受到摩擦和磨损的影响,因此其材料需要具有良好的耐磨性,以延长齿轮的使用寿命。
同时,齿轮材料还需要具有良好的疲劳强度,以保证齿轮在长期使用过程中不易产生疲劳断裂。
合金钢和表面渗碳处理的材料具有良好的耐磨性和疲劳强度,适合作为齿轮的材料。
综上所述,齿轮材料的选择需要符合一定的基本要求,包括良好的强度、硬度、韧性、冲击韧性、耐磨性和疲劳强度等。
只有选择合适的材料,才能保证齿轮在工作过程中具有良好的使用性能和寿命,从而确保机械传动装置的正常运行。
因此,在进行齿轮材料的选择时,需要充分考虑这些基本要求,以确保齿轮的质量和可靠性。
减速机齿轮常用材料

一、锻钢钢的强度高,耐冲击,用热处理方法能显著改善机械性能,所有它是制造齿轮的主要材料。
由于锻造毛坯的纤维方向有利于提高轮齿的弯曲强度,所以大部分齿轮如采用锻造毛坯,只有受力小和不重要的齿轮才直接采用轧制钢材。
按照齿坯处理方法和切齿工艺,制造齿轮的钢材及热处理方法分为两大类:*类:齿面硬度HB≤350,用中碳钢45号钢、50号钢或中碳合金钢40Gr、40MnB、35SiMn等近行调质或正火处理,终切齿可在热处理后进行。
调质后,硬度不高(HB=220~250),材料的综合性能(机械强度和冲右韧性等)比较好,适用于低速、中速和中等平稳载荷下工作。
工控设备机械中的减速机齿轮多用此类。
45号钢价格低,供应充足,应用最普遍。
正火后,综合性能有所改善,但不如调质,多用于直径很大不便调质和不重要的齿轮。
选用第—类材料时,小齿轮硬度要比大齿轮硬度高出20~40HB,以使两个齿轮寿命接近相等。
第二类:齿面硬度HB≥350,用中碳钢和中碳合金钢进行表面淬火(齿面硬度HRG=50一55),或者用低碳钢和低碳合金钢进行表面掺碳淬火处理(齿面硬度HRG=58—63)。
处理后齿面硬度高;齿芯韧性好。
所以承载能力强,耐冲击,但加工困难,成本较高,减速机中应用较少。
二、铸钢当齿轮直径较大(D>400—600毫米)时,齿坯不易锻造,因而常采用铸钢齿坯并进行正火处理。
常用的牌号有ZG45及ZH50等。
三、铸铁铸铁价格低廉,能铸造出复杂的结构形状,但灰铸铁的抗弯强度及耐冲击能力较差,故只用于低速轻载的开式齿轮传动中,常用的牌号有HT15-33、HT20—40、HTr30—54等,球墨铸铁的机械性能比灰铸铁高,可部分代替碳素钢,常用的牌号有QT60-2等。
四、非金属材料高速轻载的齿轮传功,常用非金属齿轮与另一金属齿轮配合工作,以减少齿轮传动的噪音。
常用的非金属材料有酚醛层压板(夹布胶木)、尼龙等。
这种齿轮的承载能力低、寿命短,其许用载荷只有钢齿轮的25—30%。
齿轮锻钢件技术要求

齿轮锻钢件技术要求
齿轮锻钢件的技术要求包括以下几个方面:
1. 余量尺寸:齿轮锻件余量尺寸应符合国家标准。
2. 锻造比:齿轮锻件在锻造中要保证合适的锻造比,不得使用尺寸近似的圆钢锻打。
3. 材质:齿轮锻件的材质应与零件的材质一致,化学成分应符合国家标准,并出具材质单。
4. 温度:要保证正常的锻打温度,不能低温锻打或过烧。
5. 外形:锻件外形要整齐、均匀,不允许有叠皮、断裂等锻造缺陷。
6. 精度:齿轮的精度对齿轮传动性能和使用寿命有着重要影响。
根据齿轮使用场合的不同,需要选择不同精度等级的齿轮。
7. 齿面硬度:齿轮齿面硬度是根据工作载荷和转速等因素来确定的,不同硬度的齿轮适用于不同的工作条件。
8. 润滑油:齿轮传动需要润滑油,以减少齿面磨损和摩擦阻力,提高齿轮使用寿命。
9. 热处理:齿轮需要进行热处理,以改变其内部组织结构,提高其力学性能和耐久性。
10. 清洁度:齿轮应保持清洁,以防止杂质和污物对齿轮传动造成不良影响。
11. 防锈处理:齿轮应进行防锈处理,以防止其生锈和腐蚀。
以上是齿轮锻钢件的一些主要技术要求,这些要求需要根据具体的工作条件和使用要求来制定。
同时,还需要根据具体情况进行相应的实验和测试,以确保齿轮锻钢件的质量和可靠性。
齿 轮 热 处 理 技 术 要 求

齿轮热处理技术要求编制:校对:审核:批准:南京华实齿轮传动设备有限公司二零一三年十月1.齿轮件热处理技术要求1.1渗碳件热处理质量要求1.1.1 热处理1.1.1.1 预备热处理1.1.1.1.1 对于18Cr2NiWA、20Cr2Ni4A,采用正火+高温回火作为预备热处理。
1.1.1.1.2 预备热处理后,要求按照GB/T 231-2009 《金属布氏硬度试验》进行硬度检查,要求硬度170-210HBW。
热处理后硬度应均匀,单件硬度差值≤20HBW(三点),同批硬度差值≤30HBW,组织允许为均匀分布的珠光体+铁素体+粒状贝氏体。
1.1.1.2 渗碳准备1.1.1.2.1 热处理前要求:所有零件及吊装夹具在入炉前应彻底清洗、去油。
经清洗后的工件,表面不应有锈迹、油污、斑点等影响渗碳质量的表面缺陷。
1.1.1.2.2 工件清洗后应自然干燥或风干、烘干。
进入渗碳炉的工件应完全干燥。
1.1.1.2.3 防渗:应根据工件外形及机械加工要求对工件的非渗碳部位进行有效的防渗保护。
1.1.1.3 渗碳+淬火+低温回火+喷丸1.1.1.3.1 渗碳应采用可控气氛渗碳炉进行处理,能精确控制炉内气氛的碳势及各项工艺参数,确保渗碳质量的稳定性与一致性。
1.1.1.3.2 渗碳:应根据工件热处理要求,选择适当的强渗、扩散的碳势、保温时间、渗碳后处理方式(中冷、高回等)等工艺参数,以使工件达到相应的组织和性能。
1.1.1.3.3 淬火:根据工件所需的冷却特性选择合适的淬火介质及淬火温度,淬后清洗。
1.1.1.3.4 低温回火:工件必须在淬火出油后2小时之内回火,回火温度及时间、次数等视工件大小及有效硬化层深、金相组织而定。
1.1.1.3.5 喷抛丸:经热处理完毕的齿轮,应进行抛丸处理,喷丸表面覆盖率≥200%,喷丸强度≥0.35A,喷丸后要求齿根部为残余压应力。
抛丸后,所有表面不允许存在裂纹。
1.1.2 热处理质量检验1.1.2.1 标准试样1.1.2.1.1 试样要求:材料从锻件本体切取、同预备热处理制作。
齿轮硬度要求
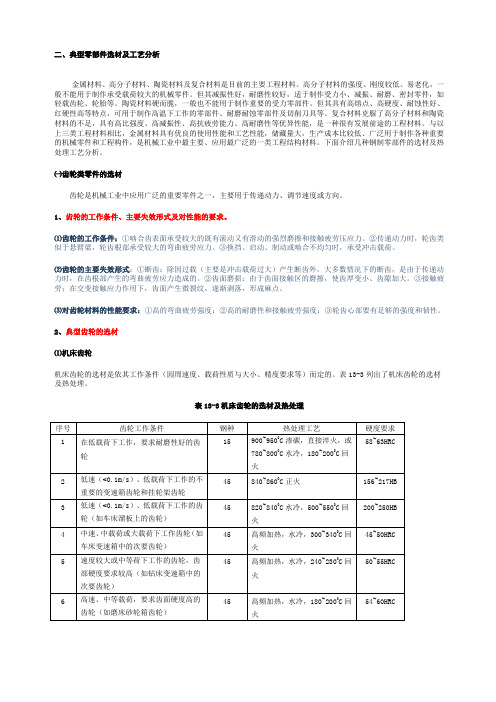
二、典型零部件选材及工艺分析金属材料、高分子材料、陶瓷材料及复合材料是目前的主要工程材料。
高分子材料的强度、刚度较低、易老化,一般不能用于制作承受载荷较大的机械零件。
但其减振性好,耐磨性较好,适于制作受力小、减振、耐磨、密封零件,如轻载齿轮、轮胎等。
陶瓷材料硬而脆,一般也不能用于制作重要的受力零部件。
但其具有高熔点、高硬度、耐蚀性好、红硬性高等特点,可用于制作高温下工作的零部件、耐磨耐蚀零部件及切削刀具等。
复合材料克服了高分子材料和陶瓷材料的不足,具有高比强度、高减振性、高抗疲劳能力、高耐磨性等优异性能,是一种很有发展前途的工程材料。
与以上三类工程材料相比,金属材料具有优良的使用性能和工艺性能,储藏量大,生产成本比较低、广泛用于制作各种重要的机械零件和工程构件,是机械工业中最主要、应用最广泛的一类工程结构材料。
下面介绍几种钢制零部件的选材及热处理工艺分析。
㈠齿轮类零件的选材齿轮是机械工业中应用广泛的重要零件之一,主要用于传递动力、调节速度或方向。
1、齿轮的工作条件、主要失效形式及对性能的要求。
⑴齿轮的工作条件:①啮合齿表面承受较大的既有滚动又有滑动的强烈磨擦和接触疲劳压应力。
②传递动力时,轮齿类似于悬臂梁,轮齿根部承受较大的弯曲疲劳应力。
③换挡、启动、制动或啮合不均匀时,承受冲击载荷。
⑵齿轮的主要失效形式:①断齿:除因过载(主要是冲击载荷过大)产生断齿外,大多数情况下的断齿,是由于传递动力时,在齿根部产生的弯曲疲劳应力造成的。
②齿面磨损:由于齿面接触区的磨擦,使齿厚变小、齿隙加大。
③接触疲劳;在交变接触应力作用下,齿面产生微裂纹,遂渐剥落,形成麻点。
⑶对齿轮材料的性能要求:①高的弯曲疲劳强度;②高的耐磨性和接触疲劳强度;③轮齿心部要有足够的强度和韧性。
2、典型齿轮的选材⑴机床齿轮机床齿轮的选材是依其工作条件(园周速度、载荷性质与大小、精度要求等)而定的。
表13-3列出了机床齿轮的选材及热处理。
表13-3机床齿轮的选材及热处理传动齿轮工作时受力不大,工作较平稳,没有强烈冲击,对强度和韧性的要求都不太高,一般用中碳钢(例如45钢)经正火或调质后,再经高频感应加热表面淬火强化,提高耐磨性,表面硬度可达52~58HRC。
齿轮硬度要求

二、典型零部件选材及工艺分析金属材料、高分子材料、陶瓷材料及复合材料是目前的主要工程材料。
高分子材料的强度、刚度较低、易老化,一般不能用于制作承受载荷较大的机械零件。
但其减振性好,耐磨性较好,适于制作受力小、减振、耐磨、密封零件,如轻载齿轮、轮胎等。
陶瓷材料硬而脆,一般也不能用于制作重要的受力零部件。
但其具有高熔点、高硬度、耐蚀性好、红硬性高等特点,可用于制作高温下工作的零部件、耐磨耐蚀零部件及切削刀具等。
复合材料克服了高分子材料和陶瓷材料的不足,具有高比强度、高减振性、高抗疲劳能力、高耐磨性等优异性能,是一种很有发展前途的工程材料。
与以上三类工程材料相比,金属材料具有优良的使用性能和工艺性能,储藏量大,生产成本比较低、广泛用于制作各种重要的机械零件和工程构件,是机械工业中最主要、应用最广泛的一类工程结构材料。
下面介绍几种钢制零部件的选材及热处理工艺分析。
㈠齿轮类零件的选材齿轮是机械工业中应用广泛的重要零件之一,主要用于传递动力、调节速度或方向。
1、齿轮的工作条件、主要失效形式及对性能的要求。
⑴齿轮的工作条件:①啮合齿表面承受较大的既有滚动又有滑动的强烈磨擦和接触疲劳压应力。
②传递动力时,轮齿类似于悬臂梁,轮齿根部承受较大的弯曲疲劳应力。
③换挡、启动、制动或啮合不均匀时,承受冲击载荷。
⑵齿轮的主要失效形式:①断齿:除因过载(主要是冲击载荷过大)产生断齿外,大多数情况下的断齿,是由于传递动力时,在齿根部产生的弯曲疲劳应力造成的。
②齿面磨损:由于齿面接触区的磨擦,使齿厚变小、齿隙加大。
③接触疲劳;在交变接触应力作用下,齿面产生微裂纹,遂渐剥落,形成麻点。
⑶对齿轮材料的性能要求:①高的弯曲疲劳强度;②高的耐磨性和接触疲劳强度;③轮齿心部要有足够的强度和韧性。
2、典型齿轮的选材⑴机床齿轮机床齿轮的选材是依其工作条件(园周速度、载荷性质与大小、精度要求等)而定的。
表13-3列出了机床齿轮的选材及热处理。
表13-3 机床齿轮的选材及热处理床传动齿轮工作时受力不大,工作较平稳,没有强烈冲击,对强度和韧性的要求都不太高,一般用中碳钢(例如45钢)经正火或调质后,再经高频感应加热表面淬火强化,提高耐磨性,表面硬度可达52~58HRC。
齿轮感应淬火要求

齿轮感应淬火要求材料:42CrMo4模数:7外径:524mm高度:70mm重量:50kg1、技术要求:硬化层深度:(界限硬度435HV1,根据AGMA 923《Metallurgical Specifications for Steel Gearing》标准)部位节圆齿顶齿根硬化层深度要求2.2-2.8mm 4.5-5.5mm ≥1.45mm 同一齿上硬度测量不得小于三点,硬度差不得大于2HRC,同一齿轮上硬度测量不得小于四个齿,并且测量的齿必须均匀分布,硬度差不得大于3HRC。
金相组织:感应层组织应主要为回火马氏体组织,不允许存在未溶珠光体组织(放大100×)以及贝氏体(放大400×);节圆感应层组织主要为细晶回火马氏体组织,以及不大于5%的非马氏体组织;齿底感应层组织主要为细晶回火马氏体组织,以及不大于10%的非马氏体组织。
(根据AGMA 923《Metallurgical Specifications for Steel Gearing》标准检验)表面缺陷:齿轮不允许过烧或者过热。
磁粉探伤:不允许存在淬火裂纹。
齿面硬度:55-60 HRC工件工作时间:≤5min2、试验方法使用SDF同步双频感应淬火技术减少工件热处理变形量,通过对工件表面施加高功率密度的能量,热量梯度很大,热传导比较快,加热时间很短,通常只有几百毫秒。
加热时间的缩短,导致渗入心部的热量比较少,这就很大程度上减少了工件的变形量。
因此,加热时间的缩短,能有效地减少工件的变形量。
同时,如果工件在加热过程中进行高速旋转,转速则需要360RPM左右,这样就大大提高了工件表面的受热均匀性。
此外,SDF同步双频感应技术能够把能量分散在所需加热表面,获得理想的轮廓硬化层。
将实验齿轮进行线切割,根据AGMA 923《Metallurgical Specifications for Steel Gearing》标准检测齿顶硬化层深度、节圆硬化层深度、齿根硬化层深度,齿面硬度,根据AGMA 923 检测节圆、齿根感应层组织;根据磁探表面不允许有淬火裂纹。
齿轮的材料及其选择原则
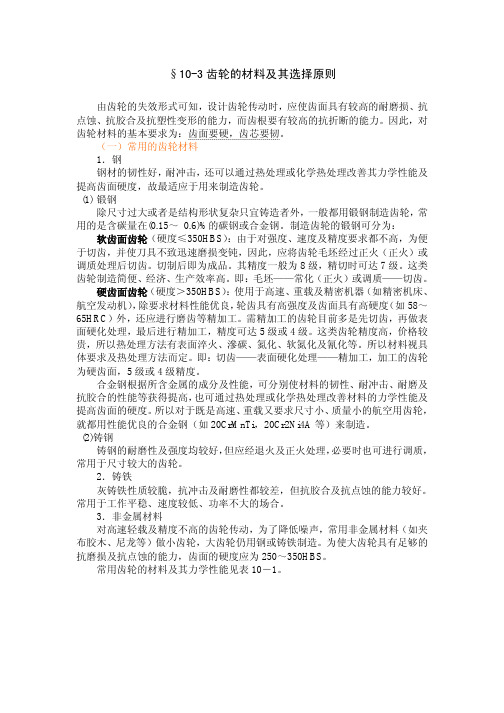
§10-3齿轮的材料及其选择原则由齿轮的失效形式可知,设计齿轮传动时,应使齿面具有较高的耐磨损、抗点蚀、抗胶合及抗塑性变形的能力,而齿根要有较高的抗折断的能力。
因此,对齿轮材料的基本要求为:齿面要硬,齿芯要韧。
(一)常用的齿轮材料1.钢钢材的韧性好,耐冲击,还可以通过热处理或化学热处理改善其力学性能及提高齿面硬度,故最适应于用来制造齿轮。
(1)锻钢除尺寸过大或者是结构形状复杂只宜铸造者外,一般都用锻钢制造齿轮,常用的是含碳量在(0.15~0.6)%的碳钢或合金钢。
制造齿轮的锻钢可分为:软齿面齿轮(硬度≤350HBS):由于对强度、速度及精度要求都不高,为便于切齿,并使刀具不致迅速磨损变钝,因此,应将齿轮毛坯经过正火(正火)或调质处理后切齿。
切制后即为成品。
其精度一般为8级,精切时可达7级。
这类齿轮制造简便、经济、生产效率高。
即:毛坯——常化(正火)或调质——切齿。
硬齿面齿轮(硬度>350HBS):使用于高速、重载及精密机器(如精密机床、航空发动机),除要求材料性能优良,轮齿具有高强度及齿面具有高硬度(如58~65HRC)外,还应进行磨齿等精加工。
需精加工的齿轮目前多是先切齿,再做表面硬化处理,最后进行精加工,精度可达5级或4级。
这类齿轮精度高,价格较贵,所以热处理方法有表面淬火、滲碳、氮化、软氮化及氰化等。
所以材料视具体要求及热处理方法而定。
即:切齿——表面硬化处理——精加工,加工的齿轮为硬齿面,5级或4级精度。
合金钢根据所含金属的成分及性能,可分别使材料的韧性、耐冲击、耐磨及抗胶合的性能等获得提高,也可通过热处理或化学热处理改善材料的力学性能及提高齿面的硬度。
所以对于既是高速、重载又要求尺寸小、质量小的航空用齿轮,就都用性能优良的合金钢(如20CrMnTi,20Cr2Ni4A等)来制造。
(2)铸钢铸钢的耐磨性及强度均较好,但应经退火及正火处理,必要时也可进行调质,常用于尺寸较大的齿轮。
常用的齿轮材料是各种牌号的优质碳素钢
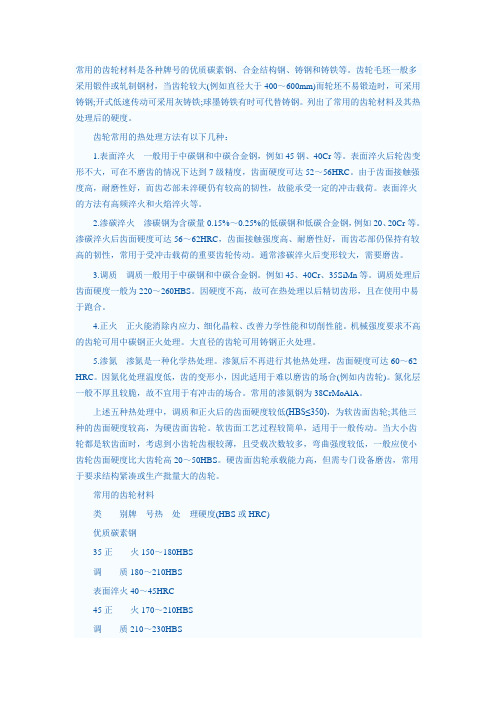
常用的齿轮材料是各种牌号的优质碳素钢、合金结构钢、铸钢和铸铁等。
齿轮毛坯一般多采用锻件或轧制钢材,当齿轮较大(例如直径大于400~600mm)而轮坯不易锻造时,可采用铸钢;开式低速传动可采用灰铸铁;球墨铸铁有时可代替铸钢。
列出了常用的齿轮材料及其热处理后的硬度。
齿轮常用的热处理方法有以下几种:1.表面淬火一般用于中碳钢和中碳合金钢,例如45钢、40Cr等。
表面淬火后轮齿变形不大,可在不磨齿的情况下达到7级精度,齿面硬度可达52~56HRC。
由于齿面接触强度高,耐磨性好,而齿芯部未淬硬仍有较高的韧性,故能承受一定的冲击载荷。
表面淬火的方法有高频淬火和火焰淬火等。
2.渗碳淬火渗碳钢为含碳量0.15%~0.25%的低碳钢和低碳合金钢,例如20、20Cr等。
渗碳淬火后齿面硬度可达56~62HRC,齿面接触强度高、耐磨性好,而齿芯部仍保持有较高的韧性,常用于受冲击载荷的重要齿轮传动。
通常渗碳淬火后变形较大,需要磨齿。
3.调质调质一般用于中碳钢和中碳合金钢。
例如45、40Cr、35SiMn等。
调质处理后齿面硬度一般为220~260HBS。
因硬度不高,故可在热处理以后精切齿形,且在使用中易于跑合。
4.正火正火能消除内应力、细化晶粒、改善力学性能和切削性能。
机械强度要求不高的齿轮可用中碳钢正火处理。
大直径的齿轮可用铸钢正火处理。
5.渗氮渗氮是一种化学热处理。
渗氮后不再进行其他热处理,齿面硬度可达60~62 HRC。
因氮化处理温度低,齿的变形小,因此适用于难以磨齿的场合(例如内齿轮)。
氮化层一般不厚且较脆,故不宜用于有冲击的场合。
常用的渗氮钢为38CrMoAlA。
上述五种热处理中,调质和正火后的齿面硬度较低(HBS≤350),为软齿面齿轮;其他三种的齿面硬度较高,为硬齿面齿轮。
软齿面工艺过程较简单,适用于一般传动。
当大小齿轮都是软齿面时,考虑到小齿轮齿根较薄,且受载次数较多,弯曲强度较低,一般应使小齿轮齿面硬度比大齿轮高20~50HBS。
齿轮检验标准
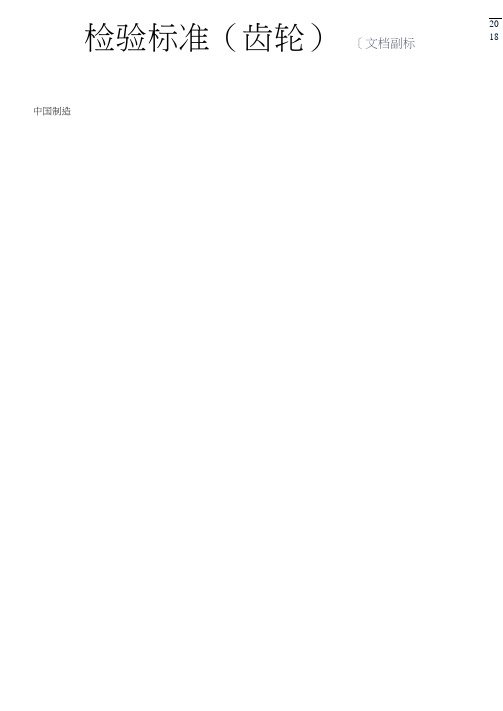
检验标准(齿轮)[文档副标中国制造20 18书适用范 围适用于齿轮产品检验。
齿轮箱产品检验按照单机检验规范和要求检验,检验项11和内容如下: 外观及附带资料检验铸件不允许有明显的披缝、凹陷、飞边、胀箱等缺陷;焊缝符合图纸要求,表面光滑平整,无裂纹、焊瘤、焊渣、飞溅:经过喷砂(丸)处理,表面质量等级应达到Sd2级,经过手工或机械打磨,表面质量 应达到St2级:外露结合面边缘整齐、均匀,不应有明显的错位;表面漆膜厚度,遵从技术文件要求,油漆无流挂、漏涂、污物、剥落现象:装入沉孔的螺钉不应高于零件表面,其头部与沉孔之间不得有明显偏心;固定销、螺 栓尾端应略高于零件表面;外露轴端略高于包容件的端面,内孔表面与壳体凸缘间的壁厚应 均匀对称; 外露件表面不应有磕碰、锈蚀、锐角、飞边、毛刺、残漆、油污、型砂,外露的螺钉、 螺母、定位销等紧固件应完整,不得有扭伤锤伤划痕,安装牢固,不应有松动现象: 电机等配套件型号、规格与要求一致,外观无损伤、碰伤、掉漆; 外型尺寸及安装孔位符合图纸要求;附带资料齐全(关键件及部件出厂检验记录、热处理或振动时效报告、特殊材质证明、 技术图纸、配套的未装零件和外购件明细)。
空运转试验试验前,检查油位,加注润滑油。
试验在无负荷状态下进行,试验条件与齿轮箱产品工 况一致,试验不少于4小时,正反各2小时。
用以检验齿轮箱的运转状态、温度变化、功率 消耗,以及运转动作的灵活性、平稳性、可靠性、安全性。
检验项目和内容如下: 轴承温度检测:进料检验标齿轮箱产品检验指导 准(齿轮)运转开始和结束时,用红外测温仪在轴承端盖处检测轴承温度。
轴承温度及温升,应符合技术协议及相关技术文件要求,如无明确规定,可参考以下指标:室温下,滚动轴承温度不高于80°C,温升不超过40°Co传动噪声检测用声级计进行检测,测点位置的确定按下列原则:先估算设备尺寸,根据尺寸确定测点的位置。
设备最大尺寸D<lm,测试点离设备表面30cm:设备最大尺寸D二lm,测试点离设备表面100cm;设备最大尺寸D>lm,测试点离设备表面300cm。
- 1、下载文档前请自行甄别文档内容的完整性,平台不提供额外的编辑、内容补充、找答案等附加服务。
- 2、"仅部分预览"的文档,不可在线预览部分如存在完整性等问题,可反馈申请退款(可完整预览的文档不适用该条件!)。
- 3、如文档侵犯您的权益,请联系客服反馈,我们会尽快为您处理(人工客服工作时间:9:00-18:30)。
齿轮硬度要求 IMB standardization office【IMB 5AB- IMBK 08- IMB 2C】二、典型零部件选材及工艺分析金属材料、高分子材料、陶瓷材料及复合材料是目前的主要工程材料。
高分子材料的强度、刚度较低、易老化,一般不能用于制作承受载荷较大的机械零件。
但其减振性好,耐磨性较好,适于制作受力小、减振、耐磨、密封零件,如轻载齿轮、轮胎等。
陶瓷材料硬而脆,一般也不能用于制作重要的受力零部件。
但其具有高熔点、高硬度、耐蚀性好、红硬性高等特点,可用于制作高温下工作的零部件、耐磨耐蚀零部件及切削刀具等。
复合材料克服了高分子材料和陶瓷材料的不足,具有高比强度、高减振性、高抗疲劳能力、高耐磨性等优异性能,是一种很有发展前途的工程材料。
与以上三类工程材料相比,金属材料具有优良的使用性能和工艺性能,储藏量大,生产成本比较低、广泛用于制作各种重要的机械零件和工程构件,是机械工业中最主要、应用最广泛的一类工程结构材料。
下面介绍几种钢制零部件的选材及热处理工艺分析。
㈠齿轮类零件的选材齿轮是机械工业中应用广泛的重要零件之一,主要用于传递动力、调节速度或方向。
1、齿轮的工作条件、主要失效形式及对性能的要求。
⑴齿轮的工作条件:①啮合齿表面承受较大的既有滚动又有滑动的强烈磨擦和接触疲劳压应力。
②传递动力时,轮齿类似于悬臂梁,轮齿根部承受较大的弯曲疲劳应力。
③换挡、启动、制动或啮合不均匀时,承受冲击载荷。
⑵齿轮的主要失效形式:①断齿:除因过载(主要是冲击载荷过大)产生断齿外,大多数情况下的断齿,是由于传递动力时,在齿根部产生的弯曲疲劳应力造成的。
②齿面磨损:由于齿面接触区的磨擦,使齿厚变小、齿隙加大。
③接触疲劳;在交变接触应力作用下,齿面产生微裂纹,遂渐剥落,形成麻点。
⑶对齿轮材料的性能要求:①高的弯曲疲劳强度;②高的耐磨性和接触疲劳强度;③轮齿心部要有足够的强度和韧性。
2、典型齿轮的选材⑴机床齿轮机床齿轮的选材是依其工作条件(园周速度、载荷性质与大小、精度要求等)而定的。
表13-3列出了机床齿轮的选材及热处理。
表13-3 机床齿轮的选材及热处理床传动齿轮工作时受力不大,工作较平稳,没有强烈冲击,对强度和韧性的要求都不太高,一般用中碳钢(例如45钢)经正火或调质后,再经高频感应加热表面淬火强化,提高耐磨性,表面硬度可达52~58HRC。
对于性能要求较高的齿轮,可选用中碳合金钢(例如40Cr等)。
其工艺路线为:备料→锻造→正火→粗机械加工→调质→精机械加工→高频淬火+低温回火→装配。
正火工序作为预备热处理,可改善组织,消除锻造应力,调整硬度便于机械加工,并为后续的调质工序做好组织准备。
正火后硬度一般为180~207HB,其切削加工性能好。
经调质处理后可获得较高的综合力学性能,提高齿轮心部的强度和韧性,以承受较大的弯曲应力和冲击载荷。
调质后的硬度为33~48HRC。
高频淬火+低温回火可提高齿轮表面的硬度和耐磨性,提高齿轮表面接触疲劳强度。
高频加热表面淬火加热速度快,淬火后脱碳倾向和淬火变形小,同时齿面硬度比普通淬火高约2HRC,表面形成压应力层,从而提高齿轮的疲劳强度。
齿轮使用状态下的显微组织为:表面是回火马氏体+残余奥氏体,心部是回火索氏体。
⑵汽车、拖拉机齿轮汽车、拖拉机齿轮的选材及热处理详见表13-4。
表13-4 汽车、拖拉机齿轮常用钢种及热处理①m n—法向模数;② m s—端面模数与机床齿轮比较,汽车、拖拉机齿轮工作时受力较大,受冲击频繁,因而对性能的要求较高。
这类齿轮通常使用合金渗碳钢(例如:20CrMnTi、20MnVB)制造。
其工艺路线为:备料→锻造→正火→机械加工→渗碳→淬火+低温回大→喷丸→磨削→装配。
正火处理的作用与机床齿轮相同。
经渗碳、淬火+低温回火后,齿面硬度可达58~62HRC,心部硬度为35~45HRC。
齿轮的耐冲击能力、弯曲疲劳强度和接触疲劳强度均相应提高。
喷丸处理能使齿面硬度提高约2~3HRC,并提高齿面的压应力,进一步提高接触疲劳强度。
齿轮在使用状态下的显微组织为:表面是回火马氏体+残余奥氏体+碳化物颗粒,心部淬透时是低碳回火马氏体(+铁素体),未淬透时,是索氏体+铁素体。
㈡轴类零部件的选材轴是机械工业中最基础的零部件之一,主要用以支承传动零部件并传递运动和动力。
1、轴的工作条件,主要失效形式及对性能的要求。
⑴轴的工作条件:①传递扭矩,承受交变扭转载荷作用。
同时也往往承受交变弯曲载荷或拉、压载荷的作用。
②轴颈承受较大的磨擦。
③承受一定的过载或冲击载荷。
⑵轴的主要失效形式:①疲劳断裂由于受交变的扭转载荷和弯曲疲劳载荷的长期作用,造成轴的疲劳断裂,这是最主要的失效形式。
②断裂失效由于受过载或冲击载荷的作用,造成轴折断或扭断。
③磨损失效轴颈或花键处的过度磨损使形状、尺寸发生变化。
⑶对轴用材料的性能要求:①高的疲劳强度,以防止疲劳断裂。
②良好的综合力学性能,以防止冲击或过载断裂。
③良好的耐磨性,以防止轴颈磨损。
2、典型轴的选材对轴类零部件进行选材时,应根据工作条件和技术要求来决定。
承受中等载荷,转速又不高的轴,大多选用中碳钢(例如45钢),进行调质或正火处理。
对于要求高一些的轴,可选用合金调质钢(例如40Cr)并进行调质处理。
对要求耐磨的轴颈和锥孔部位,在调质处理后需进行表面淬火。
当轴承受重载荷、高转速、大冲击时,应选用合金渗碳钢(例如20CrMnTi)进行渗碳淬火处理。
⑴机床主轴图13-8为C620车床主轴简图。
该主轴承受交变扭转和弯曲载荷。
但载荷和转速不高,冲击载荷也不大。
轴颈和锥孔处有磨擦。
按以上分析,C620车床主轴可选用45钢,经调质处理后,硬度为220~250HB,轴颈和锥孔需进行表面淬火,硬度为46~54HRC。
其工艺路图13-8 C620车床主轴简图线为:备料→锻造→正火→粗机械加工→调质→精机械加工→表面淬火+低温回火→磨削→装配。
正火可改善组织、消除锻造缺陷,调整硬度便于机械加工,并为调质做好组织准备。
调质可获得回火索氏体,具有较高的综合力学性能,提高疲劳强度和抗冲击能力。
表面淬火+低温回火可获得高硬度和高耐磨性。
表13-5给出了机床主轴的选材和热处理。
表13-5 根据工作条件推荐选用的机床主轴材料及其热处理工艺资料来源:合金刚手册下册第三分册,治金工业出版,1979年版。
⑵汽轮机主轴汽轮机主轴尺寸大、工作负荷大,承受弯曲、扭转载荷及离心力和温度的联合作用。
汽轮机主轴的主要失效方式是蠕变变形和由白点、夹杂、焊接裂纹等缺陷引起的低应力脆断、疲劳断裂或应力腐蚀开裂。
因此对汽轮机主轴材料除要求其在性能上具有高的强度和足够的塑韧性外,还要求其锻件中不出现较大的夹杂、白点、焊接裂纹等缺陷。
对于在500℃以上工作的主轴还要求其材料具有一定的高温强度。
根据汽轮机的功率和主轴工作温度的不同,所选用的材料也不同。
对于工作在450℃以下的材料,可不必考虑高温强度,如果汽轮机功率较小(<12000kW),且主轴尺寸较小,可选用45钢,如果汽轮机功率较大(>12000kW),且主轴尺寸较大,则须选用35CrMo钢,以提高淬透性。
对于工作在500℃以上的主轴,由于汽轮机功率大(>125000kW),要求高温强度高,需选用珠光体耐热钢,通常高中压主轴选用25CrMoVA或27Cr2MoVA钢,低压主轴选用15CrMo或17CrMoV钢。
对于工作温度更高,要求更高高温强度的主轴,可选用珠光体耐热钢20Cr3MoWV(<540℃)或铁基耐热合金Cr14Ni26MoTi(<650℃)、Cr14Ni35MoWTiAl(<680℃)制造。
气轮机主轴的工艺路线为:备料→锻造→第一次正火→去氢处理→第二次正火→高温回火→机械加工→成品。
第一次正火可消除锻造内应力;去氢处理的目的是使氢从锻件中扩散出去,防止产生白点;第二次正火是为了细化组织,提高高温强度;高温回火是为了消除正火产生的内应力,使合金元素分布更趋合理(V、Ti充分进入碳化物,Mo充分溶入铁素体),从而进一步提高高温强度。
⑶内燃机曲轴曲轴是内燃机的脊梁骨,工作时受交变的扭转、弯曲载荷以及振动和冲击力的作用。
按内燃机的转速不同可选用不同的材料。
通常低速内燃机曲轴选用正火态的45钢或球黑铸铁;中速的内燃机曲轴选用调质态的45钢、调质态的中碳合金钢(例如40Cr)或球墨铸铁。
高速内燃机曲轴选用强度级别再高一些的合金钢(例如42CrMo 等)。
内燃机曲轴的工艺路线为:备料→锻造→正火→粗机械加工→调质→精机械加工→轴颈表面淬火+低温回火→磨削→装配。
各热处理工序的作用与机床主轴的相同。
近年来常采用球墨铸铁代替45钢制作曲轴,其工艺路线为:备料→熔炼→铸造→正火→高温回火→机械加工→轴颈表面淬火+低温回火→装配。
铸造质量是球墨铸铁的关键,首先要保证铸铁的球化良好、无铸造缺陷,然后再经风冷正火,以增加组织中的珠光体含量并细化珠光体,提高其强度,硬度和耐磨性,高温回火的目的是消除正火所造成的内应力。
㈢汽轮机叶片的选材叶片是汽轮机的关键部件,它直接起着将蒸汽或燃气的热能转变为机械能的作用。
1、叶片的工作条件、失效方式及性能要求⑴叶片的工作条件:①受蒸汽或燃气弯矩的作用;②承受中、高压过热蒸汽的冲刷或湿蒸汽的电化学腐蚀或高温燃气的氧化和腐蚀;③受湿蒸汽中的水滴或燃气中的杂质磨损;④气流作用的频率与叶片自振频率相等时产生的共振力的作用。
⑵叶片的失效方式:叶片的失效方式为蠕变变形、断裂(包括振动疲劳断裂、应力腐蚀开裂、蠕变疲劳断裂及热疲劳开裂)和表面损伤(包括氧化、电化学腐蚀和磨损)。
⑶对叶片的性能要求:①高的室温和高温强度、塑性及韧性,以防止蠕变变形和疲劳断裂;②高的化学稳定性,以防止氧化、腐蚀及应力腐蚀开裂;③导热性好,热膨胀系数小,以防止热疲劳破坏;④耐磨性好,以防止冲刷磨损和机械磨损;⑤减振性好,以防止共振疲劳破坏;⑥良好的冷、热加工性能,以利于叶片成型、提高生产效率。
2、叶片的选材及热处理叶片材料的选择主要取决于工作温度。
对于中、低压汽轮机,叶片工作温度不高(<500℃),其失效的主要方式不是蠕变,而是共振疲劳和应力腐蚀开裂,因此,除在结构设计上避免共振外,应选用减振性能好的1Cr13和2Cr13马氏体不锈钢。
对于工作于过热蒸汽中的前级叶片,虽温度较高(450~475℃),但腐蚀不明显,可采用低合金钢20CrMo进行氮化、镀硬铬或堆焊硬质合金。
汽轮机后级叶片的工艺路线为:备料→模锻→退火→机械加工→调质→热整形→去应力退火→机械加工叶片根→镀硬铬→抛光→磁粉探伤→成品。
退火是为了消除锻造应力,细化组织,改善切削加工性能,为调质作组织准备;调质是为了使叶片获得良好的综合力学性能和高温强度;热整形可提高叶片精度,校正热处理变形;去应力退火是为了消除热整形内应力;镀硬铬是为了提高抗氧化和耐蚀性。