表面粗糙度的测量方法1
表面粗糙度的测量

表面粗糙度的测量目录一、表面粗糙度的检测 (2)二、表面粗糙度的测量 (3)三、参考标准 (4)四、参考文献 (5)一、表面粗糙度的检测表面粗糙度是指加工表面具有的较小间距和微小峰谷不平度。
其两波峰或两波谷之间的距离(波距)很小(在1mm以下),用肉眼是难以区别的,因此它属于微观几何形状误差。
表面粗糙度越小,则表面越光滑。
表面粗糙度的大小,对机械零件的使用性能有很大的影响,主要表现在以下几个方面:1)表面粗糙度影响零件的耐磨性。
表面越粗糙,配合表面间的有效接触面积越小,压强越大,磨损就越快。
2)表面粗糙度影响配合性质的稳定性。
对间隙配合来说,表面越粗糙,就越易磨损,使工作过程中间隙逐渐增大;对过盈配合来说,由于装配时将微观凸峰挤平,减小了实际有效过盈,降低了联结强度。
3)表面粗糙度影响零件的疲劳强度。
粗糙零件的表面存在较大的波谷,它们像尖角缺口和裂纹一样,对应力集中很敏感,从而影响零件的疲劳强度。
4)表面粗糙度影响零件的抗腐蚀性。
粗糙的表面,易使腐蚀性气体或液体通过表面的微观凹谷渗入到金属内层,造成表面腐蚀。
5)表面粗糙度影响零件的密封性。
粗糙的表面之间无法严密地贴合,气体或液体通过接触面间的缝隙渗漏。
6)表面粗糙度影响零件的接触刚度。
接触刚度是零件结合面在外力作用下,抵抗接触变形的能力。
机器的刚度在很大程度上取决于各零件之间的接触刚度。
7)影响零件的测量精度。
零件被测表面和测量工具测量面的表面粗糙度都会直接影响测量的精度,尤其是在精密测量时。
此外,表面粗糙度对零件的镀涂层、导热性和接触电阻、反射能力和辐射性能、液体和气体流动的阻力、导体表面电流的流通等都会有不同程度的影响。
表面粗糙度基本术语:取样长度:评定表面粗糙度所规定的一段基准线长度。
应与表面粗糙度的大小相适应。
规定取样长度是为了限制和减弱表面波纹度对表面粗糙测量结果的影响,一般在一个取样长度内应包含5个以上的波峰和波谷。
评定长度:为了全面、充分地反映被测表面的特性,在评定或测量表面轮廓时所必需的一段长度。
粗糙度测量标准
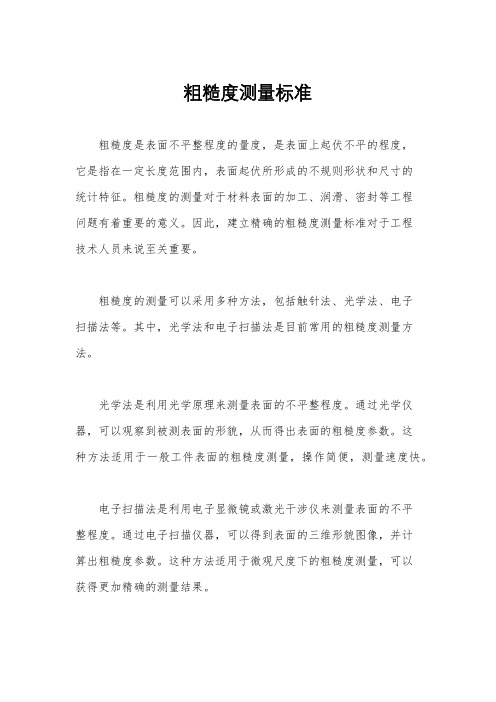
粗糙度测量标准粗糙度是表面不平整程度的量度,是表面上起伏不平的程度,它是指在一定长度范围内,表面起伏所形成的不规则形状和尺寸的统计特征。
粗糙度的测量对于材料表面的加工、润滑、密封等工程问题有着重要的意义。
因此,建立精确的粗糙度测量标准对于工程技术人员来说至关重要。
粗糙度的测量可以采用多种方法,包括触针法、光学法、电子扫描法等。
其中,光学法和电子扫描法是目前常用的粗糙度测量方法。
光学法是利用光学原理来测量表面的不平整程度。
通过光学仪器,可以观察到被测表面的形貌,从而得出表面的粗糙度参数。
这种方法适用于一般工件表面的粗糙度测量,操作简便,测量速度快。
电子扫描法是利用电子显微镜或激光干涉仪来测量表面的不平整程度。
通过电子扫描仪器,可以得到表面的三维形貌图像,并计算出粗糙度参数。
这种方法适用于微观尺度下的粗糙度测量,可以获得更加精确的测量结果。
在进行粗糙度测量时,需要注意以下几点:1. 样品的准备,在进行粗糙度测量之前,需要对样品进行适当的处理,确保表面清洁、平整,以便获得准确的测量结果。
2. 仪器的校准,在使用光学仪器或电子扫描仪进行粗糙度测量之前,需要对仪器进行校准,以确保测量的准确性和可靠性。
3. 测量参数的选择,在进行粗糙度测量时,需要选择合适的测量参数,如 Ra、Rz、Rq等,以便全面地描述表面的粗糙度特征。
4. 数据的分析,在获得粗糙度测量数据之后,需要对数据进行分析,得出合理的结论,并根据需要进行进一步的加工或处理。
总之,粗糙度测量是工程技术中非常重要的一项工作。
建立准确的粗糙度测量标准,选择合适的测量方法和仪器,严格控制测量过程,对于提高产品质量、改善加工工艺、保证工程安全具有重要意义。
希望工程技术人员能够重视粗糙度测量工作,不断提高测量技术水平,为工程技术的发展贡献自己的力量。
混凝土表面粗糙度标准及其测量方法

混凝土表面粗糙度标准及其测量方法一、前言混凝土表面粗糙度是混凝土结构的一个重要参数。
它不仅影响混凝土结构的力学性能,还直接影响着混凝土表面的美观度和耐久性。
因此,确定混凝土表面粗糙度标准及其测量方法对于混凝土结构的设计、施工和维护具有非常重要的意义。
二、混凝土表面粗糙度标准及其分类混凝土表面粗糙度标准通常指的是混凝土表面的水平面粗糙度。
目前,国内外常用的混凝土表面粗糙度标准有以下几种:1.美国ACI318-14《混凝土结构规范》中规定的混凝土表面粗糙度标准根据ACI318-14规范,混凝土表面粗糙度分为以下几个等级:(1) A级:表面光滑,无可见的凸起和凹陷。
(2) B级:表面较光滑,有少量的凸起和凹陷,但凸起和凹陷的高度不超过1/8英寸(3.2mm)。
(3) C级:表面粗糙,有可见的凸起和凹陷,但凸起和凹陷的高度不超过1/4英寸(6.4mm)。
(4) D级:表面非常粗糙,有很多的凸起和凹陷,凸起和凹陷的高度可以超过1/4英寸(6.4mm)。
2.欧洲EN 13670《预应力混凝土结构》中规定的混凝土表面粗糙度标准根据EN 13670规范,混凝土表面粗糙度分为以下几个等级:(1) A级:表面光滑,无可见的凸起和凹陷。
(2) B级:表面较光滑,有少量的凸起和凹陷,但凸起和凹陷的高度不超过1.5mm。
(3) C级:表面粗糙,有可见的凸起和凹陷,但凸起和凹陷的高度不超过3mm。
(4) D级:表面非常粗糙,有很多的凸起和凹陷,凸起和凹陷的高度可以超过3mm。
3.国内JGJ/T 152-2008《混凝土结构工程验收规范》中规定的混凝土表面粗糙度标准根据JGJ/T 152-2008规范,混凝土表面粗糙度分为以下几个等级:(1) A级:表面光滑,无可见的凸起和凹陷。
(2) B级:表面较光滑,有少量的凸起和凹陷,但凸起和凹陷的高度不超过2mm。
(3) C级:表面粗糙,有可见的凸起和凹陷,但凸起和凹陷的高度不超过4mm。
表面粗糙度对光学性能的影响及其测量方法

表面粗糙度对光学性能的影响及其测量方法光学元件的表面粗糙度是一个重要参数,对光的反射、折射以及透射都有影响。
粗糙的表面会导致光线的扩散、反射、散射和吸收,从而影响光学元件的性能。
因此,对表面粗糙度的测量和控制非常重要,特别是在高精度光学器件设计和制造过程中。
影响光学性能的表面粗糙度光学元件的表面粗糙度主要影响反射、折射和透射几个方面。
首先,表面粗糙度会导致光线的散射和吸收,特别是在高频段。
其次,表面粗糙度会导致光的反射、折射和透射的方向和程度不同,从而影响光学元件的性能。
特别是在高精度应用中,如激光成像、干涉测量、光学传感器、照明和光学通信等领域,表面粗糙度的控制非常关键。
测量表面粗糙度的方法为了控制光学元件的表面粗糙度,需要对其进行测量。
目前常用的表面粗糙度测量方法有接触式和非接触式两种方法。
接触式表面粗糙度测量方法包括拉伸法、微观测量方法和机械针头等方法。
非接触式表面粗糙度测量方法包括光学方法、电学方法和力学方法等。
下面让我们就其中一些常用的方法进行介绍。
1. 拉伸法拉伸法是一种接触式测量方法,它是通过钢丝或橡胶刮子等测量仪器刮过样品的表面,然后通过测量刮痕的深度来确定表面粗糙度的大小。
这种方法适用于较大的表面、强度较高的材料以及较贵的样品。
但是,它的缺点就是不能测量较小的表面粗糙度。
2. 微观测量法微观测量法是一种比较准确的接触式表面粗糙度测量方法,常用的方法包括扫描探针显微镜和电子显微镜等。
这种方法可以测量很小的表面比如纳米级别的表面,但是需要专业的设备和技能。
3. 光学方法光学方法是一种非接触式表面粗糙度测量方法,包括干涉法、反射法和透射法等。
其中,干涉法是一种测量表面形貌的方法,反射法和透射法是测量表面粗糙度的方法。
干涉法是通过双波长干涉仪和相位移方法来测量表面高度差的方法,适用于比较平坦的表面。
反射法是通过测量光在表面反射时的角度差以及光线的强度来确定表面粗糙度的大小。
透射法是通过测量光在样品上透过和反射的光强的变化来确定表面粗糙度的大小。
表面粗糙度的测量

表面粗糙度的测量表面粗糙度的测量方法有光切法,光波干涉法及触针法(又称针描法)等,工厂常用的还有粗糙度样板直接和被测工件对照的比较法,以及利用塑性和可铸性材料将被测工件加工表面的加工痕迹复印下来,然后再测量复印的印模的印模法。
一、实验目的1.建立对表面粗糙度的感性认识;2.了解用双管显微镜测量表面粗糙度的原理及方法。
二、实验内容用双管显微镜测量表面粗糙度的Rz值。
三、测量原理及仪器说明双管显微镜又撑光切显微镜,它是利用被测表面能反射光的特性,根据“光切法原理”制成的光学仪器,其测量范围取决于选用的物镜的放大倍数,一般用于测量0.8-80微米的表面粗糙度Rz值。
仪器外型如图1所示,它由底座6,支柱5,横臂2,测微目镜13,可换物镜8及工作台7等部分组成。
仪器备有四种不同倍数(7X,14X,30X,60X)物镜组,被测表面粗糙度大小(估测)来选择相应倍数的物镜组(见表1)。
表1 双管显微镜测量参数物镜放大倍数N 总放大倍数目镜视场直径(mm)物镜与工件距离(mm)测量范围Rz(µm)换算系数E(微米/格)7X 60X 2.5 9.5 30~30 1.2514X 120X 1.3 2.5 6.3~20 0.6330X 260X 0.6 0.2 1.6~6.3 0.29460X 510X 0.3 0.04 0.8~1.6 0.147测量原理如图2所示,被测表面为P1-P2阶梯表面,当一平行光束从45度方向投射到阶梯表面时,即被折成S1和S2两段,从垂直于光束的方向上就可以在显微镜内看到S1和S2两段光带的放大像S1'S2',同时距离h也被放大为h1'。
通过测量和计算,可求得被测表面的不平度高度h。
这种方法类似在零件表面斜切一刀,然后观察其剖面的轮廓形状,因此称为光切法。
图3为双管显微镜的光学系统图,由光源1发出的光,经聚光镜2,狭缝3,物镜4以45度方向投射到北测表面上,调整仪器使反射光束经物镜5成像在目镜分划板6上,光束被测上表面的S1点反射,在下表面S2点反射,它们各成像于分划板6的S1'和S2',距离h1被放大为h1',通过目镜可观察到凹凸不平的光带(图4(b)),光带边缘即工件表面上被照亮了的h1的放大轮廓像h1',测量h1'即可求出被测表面的不平高度h2。
表面粗糙度概念及测量方法
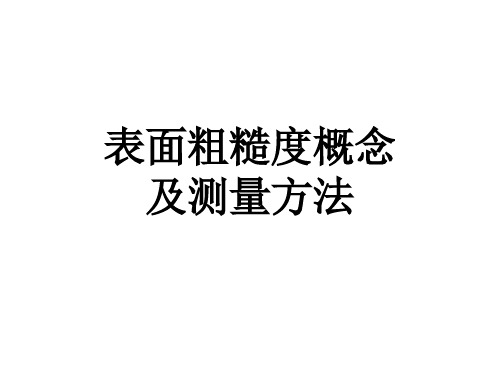
表面粗糙度
一、表面粗糙度的基本概念
表示零件表面具有较小间距和峰谷所组成的微观几何形 状特性,称为表面粗糙度。
表面粗糙度对零件的配合性质、耐磨性、强度、抗腐性 密封性、外观要求等影响很大,因此,零件表面的粗糙度的 要求也有不同。一般说来,凡零件上有配合要求或有相对运 动的表面,表面粗糙度参数值要小。
四、表面粗糙度代号在图样上的标注
★ 在同一图样上每一表面只注一次粗糙度代号,且应注 在可见轮廓线、尺寸界线、引出线或它们的延长线上,并 尽可能靠近有关尺寸线。
★ 当零件的大部分表面具有相同的粗糙度要求时,对其
中使用最多的一种,代(符)号,可统一注在图纸的右上
角。加注 “其余”二字。 例如:
C×45ο
其余 25
φ φ M φ
★ 在不同方向的
表面上标注时,代
3.2
号中的数字及符号
的方向必须按图中
的规定标注。
★ 代号中的数字
方向应与 尺寸数 字的方向 一致。
3.2
★ 符号的尖端必 须从材料 外指向 表面。
30° 3.2
3.2 3.2
30° 3.2
★ 当零件所有表面都有 相同表面粗糙度要求时, 可在图样右上角统一标注 代号。
同一零件上,工作表面比非工作表面粗糙度值 小;摩擦表面比非摩擦表面要小;受循环载荷的表 面要小;配合要求高、联接要求可靠、受重载的表 面粗糙度值都应小;同一精度,小尺寸比大尺寸、 轴比孔的表面粗糙度值要小。
2.参数的选用:首选主要评定参数1—2个,在常用 尺寸段内,选用Ra。附加评定参数必须与主要评定 参数连用。常用数值范围内,Ra=0.025—6.3, Rz=0.1—25μm,优先选用Ra.
表面粗糙度的测量
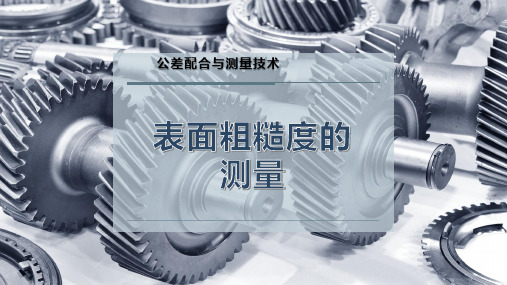
光切法测量原理为从光源发出的光线经聚光镜和狭缝形成一束扁 平光带,通过物镜组以45°方向投射在被测表面上。由于被测表面上 存在微观不平的峰谷,被具有平直边缘的狭缝像的亮带照亮后,表面 的波峰在S点产生反射,波谷在S′点产生反射,在与被测表面成另一 个45°方向经物镜放大后反射到目镜分划板上。从目镜中可以看到被 测表面实际轮廓的影像各自成像在分划板的a和a′处,若两点之间的 距离为N,用目镜上的测微百分表测出轮廓影像的高度N,根据物镜组 的放大倍数K,即可算出被测轮廓的实际高度h。
公差配合与要进行尺寸和形位误差的 测量,还要进行表面粗糙度的测量。其测量方法很多,下面 仅介绍几种常见的测量方法。 一、比较法
比较法是将被测表面与表面粗糙度样块相比较来判断工 件表面粗糙度是否合格的检验方法。
表面粗糙度样块的材料、加工方法和加工纹理方向最好 与被测工件相同,这样有利于比较,提高判断的准确性。另 外,也可以从生产的零件中选择样品,经精密仪器检定后, 作为标准样板使用。
公差配合与测量技术
用样板比较时,可以用肉眼判断,也可以用手触摸感觉, 为了提高比较的准确性,还可以借助放大镜和比较显微镜。 这种测量方法简便易行,适于在车间现场使用,常用于评定 中等或较粗糙的表面。 二、光切法
光切法就是利用“光切原理”来测量零件表面的粗糙度; 工厂中常用的光切显微镜(又称为双管显微镜),就是根 据光切原理制成的测量粗糙度仪器。
光切显微镜
三、针描法 针描法的工作原理是利用金刚石触针在被测表面上等速
缓慢移动,由于实际轮廓的微观起伏,迫使触针上下移动, 该微量移动通过传感器转换成电信号,并经过放大和处理得 到被测参数的相关数值。按照针描法原理测量表面粗糙度的 常用量仪有电动轮廓仪。
第四章 表面粗糙度测量
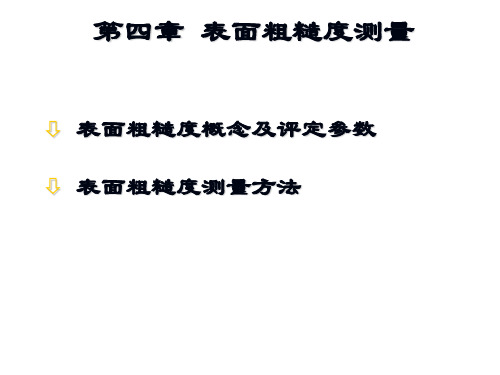
第四章表面粗糙度测量⇩表面粗糙度概念及评定参数⇩表面粗糙度测量方法4.1 表面粗糙度概念及评定参数一、表面粗糙度概念表面粗糙度是指由加工表面上具有的较小间距和峰谷组成的微观几何形状特性,亦称微观不平度。
它是由于在加工过程中刀具和零件的摩擦、切削分离时的塑性变形和金属撕裂,以及加工系统的振动等原因形成的。
零件的横截面形状是复杂的,一般按波距(间距)分成三类:表面粗糙度:波距小于1mm表面波度:波距在1~10mm形状误差:波距大于等于10mm表面粗糙度对零件使用性能的影响:1、对摩擦磨损的影响2、对配合性质的影响3、对抗腐蚀性的影响4、对抗疲劳强度的影响5、对结合密封性的影响(一)基本术语1、取样长度(l)在测量和评定表面粗糙度时所规定的具有表面轮廓特征的一段基准线长度。
一般至少包含5个以上轮廓峰谷。
2、评定长度(l n)在测量和评定表面粗糙度时所规定的一段最小长度。
一般情况下为5个取样长度。
(一)基本术语3、轮廓中线(m )2) 轮廓的算术平均中线:具有几何轮廓形状,在取样长度内与轮廓走向一致的基准线,该线划分轮廓并使上下两部分的面积相等.1) 轮廓的最小二乘中线: 具有几何轮廓形状并划分轮廓的基准线,在取样长度内使轮廓线上各点的轮廓偏距的平方和最小.[]20()min l y x dx =⎰1212n n F F F F F F'''++⋅⋅⋅+=++⋅⋅⋅+(二) 表面粗糙度评定参数1、轮廓算术平均偏差(R a)2、轮廓微观不平度十点高度(R z )3、轮廓最大高度(R y)1、轮廓算术平均偏差(R a )在取样长度内,轮廓偏距绝对值的算术平均值。
0111()()a nl i i R y x dx y x l n ==∑⎰2、轮廓微观不平度十点高度(R z )在取样长度内,5个最大轮廓的峰高y pi 和5个最大轮廓的谷深y vi和的平均值之和。
55111()5z pi vi i i R y y ===+∑∑3、轮廓最大高度(R y )在取样长度内轮廓最高点与轮廓最低点之间的距离.max max y p v R y y =+国标规定采用中线制来评定表面粗糙度,粗糙度的评定参数一般从轮廓算术平均偏差、微观不平度十点高度、轮廓最大高度中选取,推荐优先选用轮廓算(一)测量方向的选取原则1.当图样上未规定测量方向时,对于一般切削加工表面,应在垂直于加工痕迹的方向上测量;2.当图样上明确规定测量方向的特定要求时,则应按要求测量;3.当无法确定表面加工纹理方向时(如经研磨的加工表面),应通过选定的几个不同方向测量,然后取其中的最大值作为被测表面的粗糙度参数值。
表面粗糙度测量技术方法与设备介绍

表面粗糙度测量技术方法与设备介绍表面粗糙度是指物体表面的不均匀性或不平整程度。
在许多工业领域中,表面粗糙度的测量非常重要,因为它直接影响到物体的功能和性能。
本文将介绍一些常用的表面粗糙度测量技术方法与设备。
一、光学方法光学方法是一种非接触式测量表面粗糙度的技术。
例如,白光干涉法和激光扫描仪是其中常用的两种方法。
1. 白光干涉法白光干涉法是通过观察物体表面反射光的干涉图案来测量表面粗糙度的方法。
它利用白光经过物体表面反射时,不同高度的表面会产生不同的光程差,从而形成干涉条纹。
通过分析干涉条纹的特征,可以计算出表面的粗糙度参数。
2. 激光扫描仪激光扫描仪是一种使用激光束来扫描物体表面的设备。
它通过激光从不同角度照射物体表面,并通过接收器接收反射回来的激光信号,根据信号的强度和相位变化来计算表面的粗糙度参数。
激光扫描仪具有高精度和高分辨率的优点,适用于复杂曲面的粗糙度测量。
二、机械方法机械方法是一种通过机械设备对物体表面进行接触式测量的技术。
它常用于工业生产线上的实时检测。
1. 探针测量法探针测量法是一种常见的机械测量方法。
它使用一根装有传感器的探针,通过垂直移动探针并记录表面高度的变化,从而测量表面的粗糙度。
探针测量法可以适用于不同形状和材质的表面,但是由于是接触式测量,可能会对物体造成轻微的损伤。
2. 高斯仪测量法高斯仪是一种利用一个平面平行于被测表面的高斯孔隙板的装置进行测量的方法。
通过将高斯孔隙板压在物体表面上,并测量孔隙板下的气压变化,可以计算出表面的粗糙度参数。
高斯仪具有简单、准确的特点,被广泛应用于工业生产中。
三、电子方法电子方法是利用电子设备对物体表面的电信号进行测量和分析的技术。
1. 扫描电子显微镜(SEM)扫描电子显微镜是一种利用电子束扫描表面,并通过接收被扫描物体表面反射的电子信号来观察和测量物体表面形貌的设备。
SEM具有非常高的分辨率和放大倍率,可以用于微观尺度下的表面粗糙度测量。
测试金属表面粗糙度的方法
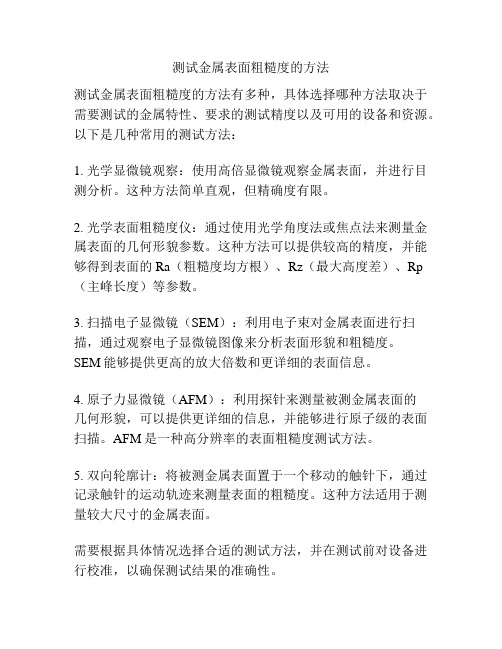
测试金属表面粗糙度的方法
测试金属表面粗糙度的方法有多种,具体选择哪种方法取决于需要测试的金属特性、要求的测试精度以及可用的设备和资源。
以下是几种常用的测试方法:
1. 光学显微镜观察:使用高倍显微镜观察金属表面,并进行目测分析。
这种方法简单直观,但精确度有限。
2. 光学表面粗糙度仪:通过使用光学角度法或焦点法来测量金属表面的几何形貌参数。
这种方法可以提供较高的精度,并能够得到表面的Ra(粗糙度均方根)、Rz(最大高度差)、Rp (主峰长度)等参数。
3. 扫描电子显微镜(SEM):利用电子束对金属表面进行扫描,通过观察电子显微镜图像来分析表面形貌和粗糙度。
SEM能够提供更高的放大倍数和更详细的表面信息。
4. 原子力显微镜(AFM):利用探针来测量被测金属表面的
几何形貌,可以提供更详细的信息,并能够进行原子级的表面扫描。
AFM是一种高分辨率的表面粗糙度测试方法。
5. 双向轮廓计:将被测金属表面置于一个移动的触针下,通过记录触针的运动轨迹来测量表面的粗糙度。
这种方法适用于测量较大尺寸的金属表面。
需要根据具体情况选择合适的测试方法,并在测试前对设备进行校准,以确保测试结果的准确性。
表面 粗糙度及测量
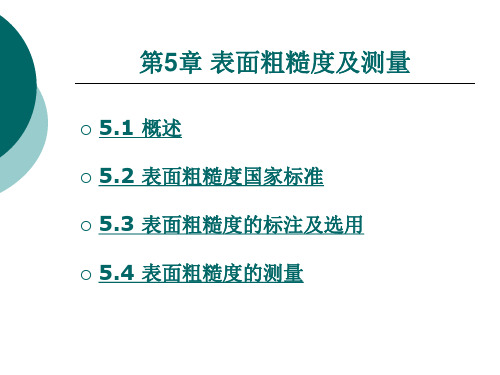
5.2 表面粗糙度国家标准
4.基准线(中线m)
基准线是用以评定表面粗糙度参数大小所规定的一条参考线, 作为评定表面粗糙度参数大小的基准。该线具有几何轮廓形 状并划分实际轮廓,在整个取样长度内与实际轮廓走向一致。 基准线有如下两种:
(1)轮廓的最小二乘中线:在取样长度内,使轮廓上各点
第5章 表面粗糙度及测量
5.1 概述 5.2 表面粗糙度国家标准 5.3 表面粗糙度的标注及选用 5.4 表面粗糙度的测量
5.1 概述
5.1.1 表面粗糙度的概念
经机械加工或其他方法获得的零件表面,总是要出现宏观和 微观的几何误差,其中微观的几何误差即零件表面上存在较 小间距的峰谷痕迹,如图5-1所示。表面粗糙度就是表述这 些峰谷高低程度和间距状况的微观几何形状特性的指标。
上一页 下一页 返回
5.1 概述
3.疲劳强度方面 表面越粗糙,一般表面微观不平的凹痕就越深,交变应力作
用下的应力集中就会越严重,越易造成零件疲劳强度的降低 而导致失效。 4.耐腐蚀方面 表面越粗糙,腐蚀性的气体或液体越易在谷底处聚集,并通 过表面微观凹谷,渗入到金属内层,造成表面腐蚀。 5.接触刚度方面 表面越粗糙,表面间接触面积就越小,致使单位面积受力就 增大,造成峰顶处的局部塑性变形加剧,接触刚度下降,影 响机器工作精度和平稳性。 此外,表面粗糙度还影响结合面的密封性,影响产品外观和 表面涂层的质量等。
当零件所有表面具有相同的表面粗糙度要求时,其标注如图 5-12所示。
上一页 下一页 返回
5.3 表面粗糙度的标注及选用
当齿轮、蜗轮、渐开线花键等工作表面没有画出齿形时,其 表面粗糙度代号可标注在节圆上。如图5-13所示。
螺纹工作表面没有画出牙形时,可按图5-14的方式标注。 中心孔的工作表面,键槽工作表面、圆角、倒角的表面粗糙
公差配合与测量技术 测量表面粗糙度的方法

测量表面粗糙度的方法表面粗糙度的检测,我们常用的有以下几中方法1.显微镜比较法,Ra0.32;将被测表面与表面粗糙度比较样块靠近在一起,用比较显微镜观察两者被放大的表面,以样块工作面上的粗糙度为标准,观察比较被测表面是否达到相应样块的表面粗糙度;从而判定被测表面粗糙度是否符合规定。
此方法不能测出粗糙度参数值2.光切显微镜测量法,Rz:0.8~100;光切显微镜(双管显微镜)是利用光切原理测量表面粗糙度的方法。
从目镜观察表面粗糙度轮廓图像,用测微装置测量Rz值和Ry值。
也可通过测量描绘出轮廓图像,再计算Ra值,因其方法较繁而不常用。
必要时可将粗糙度轮廓图像拍照下来评定。
光切显微镜适用于计量室3.样块比较法,直接目测:Ra2.5;用放大镜:Ra0.32~0.5;以表面粗糙度比较样块工作面上的粗糙度为标准,用视觉法或触觉法与被测表面进行比较,以判定被测表面是否符合规定用样块进行比较检验时,样块和被测表面的材质、加工方法应尽可能一致;样块比较法简单易行,适合在生产现场使用4.电动轮廓仪比较法,Ra:0.025~6.3;Rz:0.1~25;电动轮廓仪系触针式仪器。
测量时仪器触针尖端在被测表面上垂直于加工纹理方向的截面上,做水平移动测量,从指示仪表直接得出一个测量行程Ra值。
这是Ra值测量常用的方法。
或者用仪器的记录装置,描绘粗糙度轮廓曲线的放大图,再计算Ra或Rz值。
此类仪器适用在计量室。
但便携式电动轮廓仪可在生产现场使用5干涉显微镜测量法,Rz:.032~0.8;涉显微镜是利用光波干涉原理,以光波波长为基准来测量表面粗糙度的。
被测表面有一定的粗糙度就呈现出凸凹不平的峰谷状干涉条纹,通过目镜观察、利用测微装置测量这些干涉条纹的数目和峰谷的弯曲程度,即可计算出表面粗糙度的Ra值。
必要时还可将干涉条纹的峰谷拍照下来评定。
干涉法适用于精密加工的表面粗糙度测量。
适合在计量室使用而在现场工作中,我们用的多的是:样块比较法和电动轮廓检测法,样块比较法要求对粗糙度的敏感要求比较高,有些老师傅还是可以做到的,毕竟是凭经验和感觉去比较的,而电动轮廓检测法是靠仪器测量,这样测量出来的准确度就大大提高了,所以说,我们建议用电动轮廓检测法.用什么方法去检测1.比较法:将被测表面和表面粗糙度样板直接进行比较,多用于车间,评定表面粗糙度值较大的工件。
浅谈触针式表面粗糙度测量技术与方法(1)

浅谈触针式表面粗糙度测量技术与方法摘要:表面粗糙度对精密加工工件的性能有着很大的影响。
机械、电子及光学工业的飞速发展,对精密机械加工工件表面的质量及结构小型化的要求日益提高,使得表面粗糙度测量显现出越来越重要的地位。
通过对度表面粗糙测量技术的发展历史、现状与发展趋势,文中阐述一种表面粗糙度测量仪的工作原理和性能,并对其相关问题做了讨论。
关键词:表面;粗糙度;测量技术;触针式粗糙度仪Discussion on the technique and method for measuring the surfaceroughness of stylusAbstract: S urface roughness has great influence on the performance of precision machining. With the rapid development of mechanical, electronic and optical industries, the requirement of the quality and the size of the surface of the precision machined parts is increasing, and the surface roughness measurement is becoming more and more important. This paper describes the working principle and performance of a surface roughness measuring instrument by the development history, present situation and development trend of the degree surface roughness measuring technology, and discusses the related problems.Key words:surface roughness; measuring technique; stylus type roughness tester1 引言1.1触针式粗糙度轮廓仪粗糙度测量仪通常分为接触式和非接触式。
喷砂后表面粗糙度的测定方法
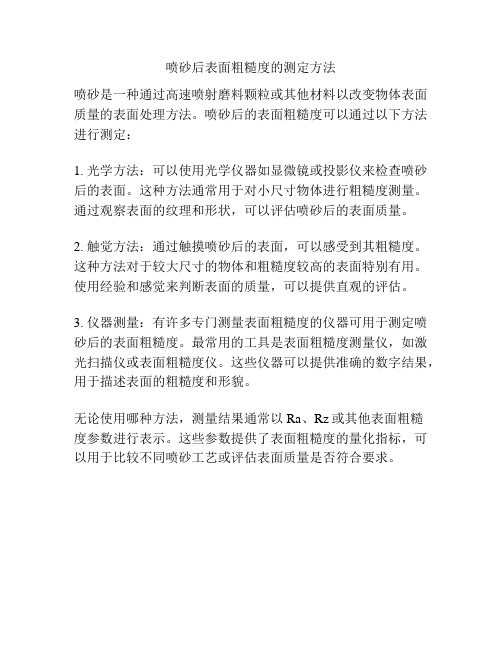
喷砂后表面粗糙度的测定方法
喷砂是一种通过高速喷射磨料颗粒或其他材料以改变物体表面质量的表面处理方法。
喷砂后的表面粗糙度可以通过以下方法进行测定:
1. 光学方法:可以使用光学仪器如显微镜或投影仪来检查喷砂后的表面。
这种方法通常用于对小尺寸物体进行粗糙度测量。
通过观察表面的纹理和形状,可以评估喷砂后的表面质量。
2. 触觉方法:通过触摸喷砂后的表面,可以感受到其粗糙度。
这种方法对于较大尺寸的物体和粗糙度较高的表面特别有用。
使用经验和感觉来判断表面的质量,可以提供直观的评估。
3. 仪器测量:有许多专门测量表面粗糙度的仪器可用于测定喷砂后的表面粗糙度。
最常用的工具是表面粗糙度测量仪,如激光扫描仪或表面粗糙度仪。
这些仪器可以提供准确的数字结果,用于描述表面的粗糙度和形貌。
无论使用哪种方法,测量结果通常以Ra、Rz或其他表面粗糙
度参数进行表示。
这些参数提供了表面粗糙度的量化指标,可以用于比较不同喷砂工艺或评估表面质量是否符合要求。
几种表面粗糙度测量方法介绍
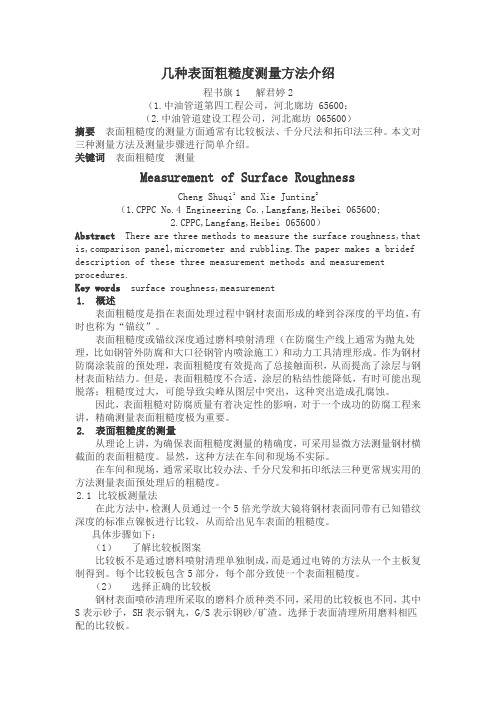
几种表面粗糙度测量方法介绍程书旗1 解君婷2(1.中油管道第四工程公司,河北廊坊 65600;(2.中油管道建设工程公司,河北廊坊 065600)摘要表面粗糙度的测量方面通常有比较板法、千分尺法和拓印法三种。
本文对三种测量方法及测量步骤进行简单介绍。
关键词表面粗糙度测量Measurement of Surface RoughnessCheng Shuqi1 and Xie Junting2(1.CPPC No.4 Engineering Co.,Langfang,Heibei 065600;2.CPPC,Langfang,Heibei 065600)Abstract There are three methods to measure the surface roughness,that is,comparison panel,micrometer and rubbling.The paper makes a bridef description of these three measurement methods and measurement procedures.Key words surface roughness,measurement1.概述表面粗糙度是指在表面处理过程中钢材表面形成的峰到谷深度的平均值,有时也称为“锚纹”。
表面粗糙度或锚纹深度通过磨料喷射清理(在防腐生产线上通常为抛丸处理,比如钢管外防腐和大口径钢管内喷涂施工)和动力工具清理形成。
作为钢材防腐涂装前的预处理,表面粗糙度有效提高了总接触面积,从而提高了涂层与钢材表面粘结力。
但是,表面粗糙度不合适,涂层的粘结性能降低,有时可能出现脱落;粗糙度过大,可能导致尖峰从图层中突出,这种突出造成孔腐蚀。
因此,表面粗糙对防腐质量有着决定性的影响,对于一个成功的防腐工程来讲,精确测量表面粗糙度极为重要。
2.表面粗糙度的测量从理论上讲,为确保表面粗糙度测量的精确度,可采用显微方法测量钢材横截面的表面粗糙度。
第四章 表面粗糙度及表面微观形貌测量

1 m RC = ∑ Z ti m i =1
RC =
(h2 + h4 ......h10 ) − (h1 + h3 .......h9 ) 5
第
轮廓最大高度 Ry
新标准: 新标准: Rz
11 页
为在取样长度l内 轮廓的峰顶线与谷底线之间距离。 为在取样长度 内,轮廓的峰顶线与谷底线之间距离。 峰顶线与谷底线分别指在取样长度内,平行于中线且通过轮廓 峰顶线与谷底线分别指在取样长度内,平行于中线且通过轮廓 中线 的最高点和最低点的线。 的最高点和最低点的线。
第
2、电动轮廓仪
27 页
显示
触针法电信号处理工作原理
第
台式电动轮廓仪的结构
28 页
基座: 基座:1+7 驱动箱: 驱动箱:6 传感器:9 传感器: 电器箱: 电器箱:3 记录器: 记录器:10
12-V形块 形块
第 29 页
典型电动轮廓仪介绍 P99
第
五、印 模 法
大型零件的内表面
30 页
印模法的原理: 印模法的原理: 利用某些塑性材料作块状印模,贴合在被测表面上, 利用某些塑性材料作块状印模,贴合在被测表面上,取下 在印模上存有被测表面的轮廓形状, 后,在印模上存有被测表面的轮廓形状,然后对印模的表面进 行测量,得出原来零件的表面粗糙度。 行测量,得出原来零件的表面粗糙度。 常用的印模材料有: 常用的印模材料有: 川蜡、石蜡、赛璐珞和低熔点合金等。 川蜡、石蜡、赛璐珞和低熔点合金等。
第
表面微观形貌测量的意义 表面微观形貌测量的意义 (P93) 微观形貌 1、影响零件的使用性能 、 2、监测工艺过程状态 、 3、改善表面质量 、 4、与纳米技术、生物技术等学科相互影响 、与纳米技术、
表面粗糙度 测量方法
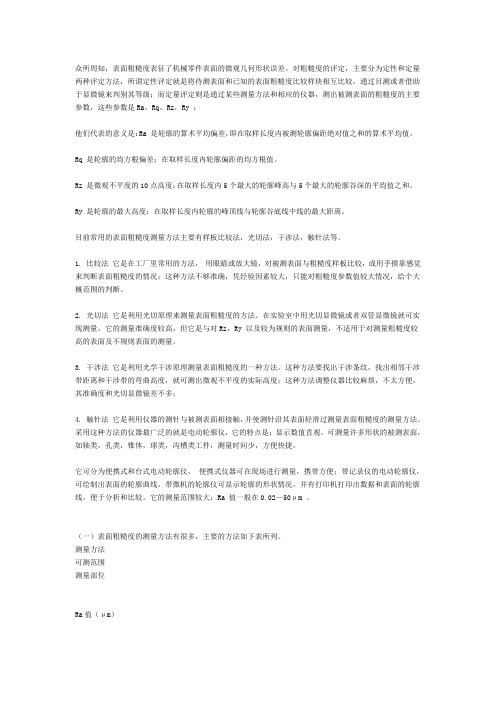
众所周知,表面粗糙度表征了机械零件表面的微观几何形状误差。
对粗糙度的评定,主要分为定性和定量两种评定方法,所谓定性评定就是将待测表面和已知的表面粗糙度比较样块相互比较,通过目测或者借助于显微镜来判别其等级;而定量评定则是通过某些测量方法和相应的仪器,测出被测表面的粗糙度的主要参数,这些参数是Ra,Rq,Rz,Ry ;他们代表的意义是:Ra 是轮廓的算术平均偏差,即在取样长度内被测轮廓偏距绝对值之和的算术平均值。
Rq 是轮廓的均方根偏差:在取样长度内轮廓偏距的均方根值。
Rz 是微观不平度的10点高度:在取样长度内5个最大的轮廓峰高与5个最大的轮廓谷深的平均值之和。
Ry 是轮廓的最大高度:在取样长度内轮廓的峰顶线与轮廓谷底线中线的最大距离。
目前常用的表面粗糙度测量方法主要有样板比较法,光切法,干涉法,触针法等。
1. 比较法它是在工厂里常用的方法,用眼睛或放大镜,对被测表面与粗糙度样板比较,或用手摸靠感觉来判断表面粗糙度的情况;这种方法不够准确,凭经验因素较大,只能对粗糙度参数值较大情况,给个大概范围的判断。
2. 光切法它是利用光切原理来测量表面粗糙度的方法。
在实验室中用光切显微镜或者双管显微镜就可实现测量,它的测量准确度较高,但它是与对Rz,Ry 以及较为规则的表面测量,不适用于对测量粗糙度较高的表面及不规则表面的测量。
3. 干涉法它是利用光学干涉原理测量表面粗糙度的一种方法。
这种方法要找出干涉条纹,找出相邻干涉带距离和干涉带的弯曲高度,就可测出微观不平度的实际高度;这种方法调整仪器比较麻烦,不太方便,其准确度和光切显微镜差不多;4. 触针法它是利用仪器的测针与被测表面相接触,并使测针沿其表面轻滑过测量表面粗糙度的测量方法。
采用这种方法的仪器最广泛的就是电动轮廓仪,它的特点是:显示数值直观,可测量许多形状的被测表面,如轴类,孔类,锥体,球类,沟槽类工件,测量时间少,方便快捷。
它可分为便携式和台式电动轮廓仪,便携式仪器可在现场进行测量,携带方便;带记录仪的电动轮廓仪,可绘制出表面的轮廓曲线,带微机的轮廓仪可显示轮廓的形状情况,并有打印机打印出数据和表面的轮廓线,便于分析和比较。
混凝土表面粗糙度标准及其测量方法

混凝土表面粗糙度标准及其测量方法混凝土表面粗糙度是衡量混凝土表面平滑程度的重要参数,对于许多建筑工程来说,它是关乎施工质量和使用安全的关键因素。
本文将深入探讨混凝土表面粗糙度标准及其测量方法,旨在为读者提供全面且深入的理解。
一、混凝土表面粗糙度的意义混凝土表面粗糙度直接影响着混凝土结构的外观和性能。
适当的粗糙度可以提高混凝土的抗滑性能,使其在湿滑环境下具有更好的防滑效果,防止人员或车辆发生滑倒事故。
粗糙度还会影响混凝土的抗渗性、粘结力以及涂层或涂料的附着力,因此粗糙度的控制对于工程质量和使用寿命也具有重要影响。
二、混凝土表面粗糙度标准对于混凝土表面的粗糙度标准,主要有以下几种常用的指标:1. Rz值:采用国际通用的指标,表示混凝土表面上一定长度范围内的最大凹凸高度差。
2. Ra值:表示单位长度内的平均表面粗糙度值,用于比较不同混凝土表面粗糙度的大小。
3. Rq值:表示混凝土表面上一定长度范围内的平均凹凸高度差的平方平均根值,用于更加全面地评估表面粗糙度。
4. Rt值:表示混凝土表面上一定长度范围内的最大凹/凸高度差。
除了这些指标外,不同行业和使用领域还会有一些特定的标准和指标,例如在卫生间或厨房地面等需要防滑的场所,还会使用更为具体的摩擦系数来描述混凝土表面的粗糙度。
三、测量混凝土表面粗糙度的方法测量混凝土表面粗糙度可以采用多种方法,下面介绍两种常用的方法:1. 微触探法:通过用特定力量的探针在混凝土表面划过并记录下表面凹凸的情况,再通过相应的公式计算出表面粗糙度指标。
该方法具有操作简单、快速、准确等优点,且适用于不同形状和尺寸的混凝土表面。
2. 光学测量法:通过使用激光或投射特定光源的仪器,获取混凝土表面的图像或影像,再通过图像处理技术分析表面的凹凸情况并计算出相应的粗糙度指标。
该方法适用于大面积表面的测量和精密测量,但对于光照和尺寸限制较为敏感,需要在实际应用中进行适当的校正和调整。
四、对混凝土表面粗糙度标准的理解和观点混凝土表面粗糙度标准的制定是基于安全、施工质量和使用需求等多方面的考虑。
粗糙度检测方法及评定

粗糙度检测方法及评定
一、粗糙度检测方法 1、用视觉来检测粗糙度:通过肉眼观察,直接观察工件表面的形貌,来判断其粗糙度。
这是一种简单、实用的方法。
2、用比较法检测粗糙度:将试件与一般平整的参考物体做比较,根据不同类型和尺寸的参考物体,来判断试件表面的粗糙度。
3、用量化法检测粗糙度:将表面粗糙度量化,以规定的尺寸和形状的金刚石弹头或砂轮装置,来测量试件表面的粗糙度。
4、用激光扫描技术检测粗糙度:用激光扫描仪来检测工件表面的粗糙度,它能够快速、准确的测量工件表面的精细尺寸。
二、粗糙度评定 1、粗糙度评定要根据粗糙度的标准来进行,主要有三种:粗糙度数值、粗糙度等级和粗糙度范围。
2、粗糙度数值:根据工件表面的粗糙度,用数字表示,来判断工件表面的粗糙程度。
3、粗糙度等级:将粗糙度分为几个等级,来判断工件表面的粗糙度。
4、粗糙度范围:将粗糙度的标准规定在一定的范围内,来判断工件表面的粗糙度。
5、粗糙度评价:根据粗糙度的标准,对工件表面的粗糙度进行评价,从而得出结论。
6、粗糙度分析:根据粗糙度的标准,分析工件表面的粗糙度,从而得出最优的粗糙度设定。
总之,粗糙度检测方法及评定,是一种对工件表面粗糙度进行检测和评定的方法,主要使用视觉比较法、量化
法和激光扫描技术,以及根据粗糙度的标准,来进行粗糙度评定、评价和分析。
这种方法可以检测出试件表面的粗糙度,从而得出准确的结论,提高产品质量,满足生产要求。
表面粗糙度测量
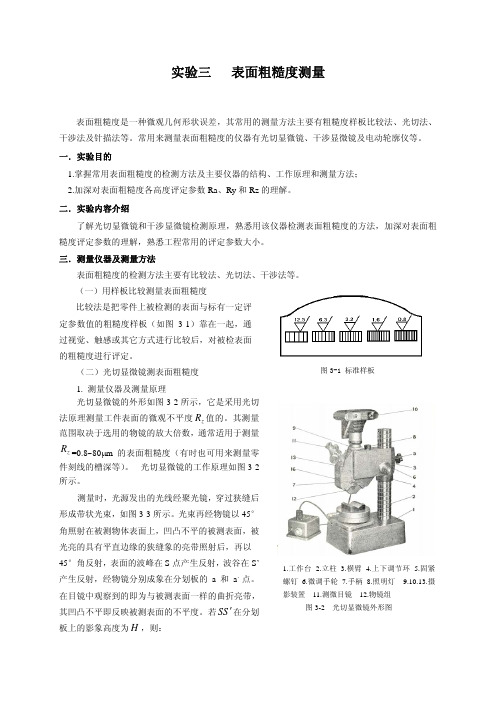
干涉条纹的弯曲。相应部位峰、谷的高度差 h 与干涉条纹弯曲量 a 和干涉条纹间距 b 有关(如图 3-10b
所示),其关系式为:
h= a×λ b2
式中:λ 为测量中的光波波长。本实验就利用测量干涉条纹弯曲量 a 和干涉条纹间距 b 来确定 R z 值
3
和 R y 值。
2. 测量步骤 (1)调整仪器 a 开亮灯泡,转动手柄 10 和 6(见图 3-6),使图 3-6 中的遮光
目镜的固紧螺钉,转动测微目镜,使其中的十字线的水平线与光带轮廓中线(估计方向)平行,锁 紧螺钉,然后转动测微目镜测微器上的刻度套筒,使十字线的水平线在光带最清晰的一边。在取样
长度 l 范围内,,找出 5 个最高峰点和 5 个
最低谷点,并分别用十字线的水平线与之
相切,如图 3-4 所示。读出十个读数 a 1、a 2、 a 3…… a 12,填入表 3-3,并按下式计算出 10
1~0.03 um 表面粗糙度的 R z 值和 R y 值。
a)
b)
图 3-6 6JA 型干涉显微镜的外形图
6JA 型干涉显微镜的外形图如图 3-6 所示。该仪器的
光学系统图如图 3-7 所示,由光源 1 发出的光束,通过聚
光镜 2、4、8(3 是滤色片),经分光镜 9 分成两束。其中
一束经补偿板 10、物镜 11 至被测表面 18 再经 原光路
h 松开图 2-10 中螺母 1b,转动测微目镜 1,使视场中十字线之一与干涉条纹平行,然后拧紧螺
母,此时即可进行具体的测量工作。
(2)测量方法。
在此仪器上,表面粗糙度可以用两种方法测量。
第一种用测微目镜测量:
a 转动测微目镜中与干涉条纹平
行的十字线中的一条线,对准一条干涉
- 1、下载文档前请自行甄别文档内容的完整性,平台不提供额外的编辑、内容补充、找答案等附加服务。
- 2、"仅部分预览"的文档,不可在线预览部分如存在完整性等问题,可反馈申请退款(可完整预览的文档不适用该条件!)。
- 3、如文档侵犯您的权益,请联系客服反馈,我们会尽快为您处理(人工客服工作时间:9:00-18:30)。
y
i 1
5
pi
y vi
i 1
5
5
在取样长度内,也可从平行于轮廓中线m的任意一根线算起, 计算被测轮廓的五个最高点(峰)到五个最低点(谷)之间 的平均距离
Rz
(h2 h4 ...h10 ) (h1 h3 ...h9 ) = 5
3.轮廓最大高度
在取样长度内,轮廓峰顶线和轮廓谷底线之间的距离 (图4-3)。
实际工作中,对加工表面粗糙度的评 定可归纳为如下四种方式。
1.与表面粗糙度标准样板比较的方法
表面粗糙度样板:按各种加工方法做成的不同几何形状的 一套标准表面样块,用来与被测的表面 相比较。
表面粗糙度样板
测量方法:
目测法:Ra值2.5-80m的表面;
用5~10倍放大镜比较:Ra值0.32-2.5m的表面;
(2)算术平均中线: 在取样长度范围内,划分实际轮廓为上、下两部分, 且使上下两部分面积相等的线。
轮廓的算术平均中线
二、评定参数及数值:
对评定参数的基本要求:
(1)正确、充分反映表面微观几何形状特征;
(2)具有定量的结果; (3)测量方便。
国标从水平和高度两方向各规定了三个评定参数:三个基本 参数(水平),三个附加的评定参数(高度)
图4-5 光切原理
2.测量仪器原理及定度
(1)原理 光切显微镜的光路原理如图4-6所示。用测微目镜量出a、 a’的距离N,即可求出峰谷间的高度。
图4-6 光切显微镜光路
由于物镜分辨率及景深的限制,光切法测量范围一般为:
Rz= (80~0.8)m(旧国标3~9)。
式h=N/(Vcos45°)中有无理数,计算、使用不便,在仪
目的: 为充分合理地反映某一表面的粗糙度特征。
(加工表面有着不同程度的不均匀性)。 选择原则:一般按五个取样长度来确定。
4.轮廓中线m:是评定表面粗糙度数值的基准线。具有几 何轮廓形状与被测表面几何形状一致,并将被测轮廓加 以划分的线。类型有:
(1)最小二乘中线: 使轮廓上各点的轮廓偏转距y(在测量方向上轮廓上 的点至基准线的距离)的平方和为最小的基准线。
问题1:工件特点? (大小、轻重、材料) 问题2:测哪里的粗糙度? (内、外表面;平面、柱面、球面、齿面、牙型面) 问题3:测量有什么特点? 问题4:与长度、角度测量有何不同?
测量单位和标准量
测量方法
测量精度
长度单位-um 表面粗糙度样板 光波波长 电压、电流标准
测量方案设计
1、轮廓算术平均偏差Ra 在取样长度L内,轮廓偏距绝对值的算术0
1 n Ra yi n i 1
Rz
图4-3 表面粗糙度的高度参数
2.微观不平度十点高度
在取样长度内五个最大的轮廓峰高的平均值与五个最大的轮 廓谷深的平均值之和,如图4-3所示。用公式表示为:
结构模式如图9—7所示。
粗糙度测量方法主要是以不同类型的传感器所反映的测量原理来分类 的。表9—l 4列出了各类转换形式的传感器。运算装置包括信号放大器、 滤波器和各种型式的计算处理(如信号变换、模数转换、时控、数字计 算等)装置。输出设备包括指针式电量表、记录器、光电输出器、电传 打字机、磁带输出器、Tv显示屏、绘图仪等。其中,传感器是基本组成 部分,在取得表面测量信号以后,亦可用人工进行计算处理给出结果。
其他方法:激光散射法、激光散班法、激光全息法等。
二、光切法测量表面粗糙度
1.光切法原理:
所谓光切法就是用一狭窄的扁平光 束以一定的倾斜角照射到被测表面上, 光束在被测表面上发生反射,将表面微 观不平度用显微镜放大成象进行观测的 方法。图4-5是光切法的测量原理图。
若倾斜角取45°,则得: h’=h/cos45° 若观测显微物镜的倍数V,则: N=Vh’ 用显微镜测出象的大小N,即 可求出h值: h=N/(Vcos45°) 测量表面粗糙度峰谷距离的 原理与上述相同。
2.在选定截面上直接测量表面微观不平度数值的方法
普遍采用、定量测量、严格按照定义测、本节重点。
常用的有光切法、干涉法、触针法等各种测量原理的光学或 电学仪器。
3.印模法测量表面粗糙度
对于大型零件或零件内表面等不易直接测量的情况下可用此 法。
印模表面的峰谷值总要比被测表面的峰谷值要小些,因而对 此结果需加以修正。其修正系数值与所用材料等有关,应由 实验来确定。
V=
a 2 a1 Z
令C=5/V,则:h=cn (um) 式中,n为测量峰谷高度时两次读数的差值(格数)。 显然,上式使用简便。
C值的物理意义就是测微鼓轮一小格所对应的峰谷方向
的高度值。
3.测量方法 测量前,选择相应的物镜(表4-2)并已知定度值C。然后 调节显微镜使视场呈现清晰的狭缝象及表面象,且至狭缝 象的一个边缘最清晰为止。 (1)测量Rz值 其测量方法应符合定义。 Rz值可按下式计算:
垂直分辨率优于1nm,水平分辨力0.4μm
6JA干涉显微镜 测量光路见图4-12。
图4-12 干涉显微镜光路
四、触针法测量表面粗糙度
1.触针法的测量原理
触针法又称针描法,它是一种接触式测量方法,是利用仪器 的测针与被测表面相接触,并使测针沿其表面轻轻划过以测 量表面粗糙度的一种测量法。 将一个很尖的触针(半径可以做到微米量级的金钢石针尖) 垂直安臵在被测表面上作横向移动,由于工作表面粗糙不平, 因而触针将随着被测表面轮廓形状作垂直起伏运动。将这种 微小位移通过电路转换成电信号并加以放大和运算处理,即 可得到工件表面粗糙度参数值;也可通过记录器描绘出表面 轮廓图形,再进行数据处理,进而得出表面粗糙度参数值。 这类仪器垂直方向的分辨率最高可达到几纳米。 适宜测量值为5—0.02m范围内的表面粗糙度。
5 5 Rz=1/2C hi ' hi / 5 i 1 i 1 (2)测量Ry值:
Ry=1/2C
hmax hmix
三、干涉显微镜测量表面粗糙度
干涉显微镜测量原理:
联合运用干涉原理和显微放大原理。对测量 面垂直高度方向的微观不平度通过光波干涉法进 行放大测量,对表面粗糙度的水平参数通过显微 放大系统测量。
性情况,此时最好将各部位的测量结果分别注出,或给出平均值结
果并附加说明
第二节表面粗糙度的测 量方法
主要内容:
1、光切法量表面粗糙度 2、干涉显微镜测量表面粗糙度 3、触针法测量表面粗糙度 电感轮廓仪
激光干涉式轮廓仪
压电式轮廓仪 重点:光切显微镜的原理和定度
任务:表面粗糙度的测量
测量对象和被测量
表面粗糙度的测量
第一节表面粗糙度的评定参数
主要内容:
1、主要术语及定义 取样长度L
n
评定长度L 轮廓中线m 2、6个评定参数
3个基本、3个附加
3、一般规定
重点: 3个基本评定参数
一.主要术语及定义
1.实际轮廓:平面与实际表面相交所得的轮廓线。 按照相截方向的不同,它又可分为横向实际轮廓和纵向实 际轮廓。在评定或测量表面粗糙度时,除非特别指明,通 常均指横向实际轮廓,即与加工纹理方向垂直的截面上的 轮廓。
15.2 表面粗糙度测量的基本原则
(1)测量方向 按现行标准所定义的各种粗糙度评定参数,是基于轮廓法确定数值,
是在被测表面的法向截面上的实际轮廓上进行测量的结果。由于垂直于
被测表面的法向截面存在各种不同的测量方向.试验表明,大多数的切 削加工表面,在横向轮廓上测得的粗糙度数值比较大,只是有的该铣加
实际轮廓图
横向实际轮廓图
2.取样长度l:用于判别和测量表面粗糙度时所规定的一段基 准线长度。 量取方向:它在轮廓总的走向上。 目的:限制和削弱表面波度对表面粗糙度测量结果的影响。 (几何滤波) 选择原则: 5≤ l p /3 常用的取样长度见表4-1。
3.评定长度L : 评定轮廓所必须的一段长度,它包括一个或数个取样长 度。
n
轮廓支承长度与取样长度之比,就是轮廓支承长度率。
tp = (p /L) ×100%
轮廓支承长度率
1.5 表而粗糙度测量方法综述及测量的基本原则
15.1
测量方法综述
对加工表面质量的评定,除了用视觉和触觉进行定性地比较检验的
方法以外,并逐步实现了用数值确定表面粗糙度参数值的定量测量。从
本世纪30年代陆续提出了测量粗糙度的方法原理和仪器以来,已发展了 一系列利用光学、机械、电气原理的表面粗糙度专用测量仪器,其基本
器设计时采用机械方法加以有理化 ,其方法如图4-7所 示。此时:
h= a/2V
式中: a—用仪器测微目镜瞄准峰谷象高度N(图4-7 中十字线位臵I与II)时两次读数差值; h—表面粗糙度的某一峰谷高度; V —所选用物镜的放大倍数。 双管显微镜
双管显微镜视场图
双管显微镜
光切显微镜读数
(2)定度: 在光切显微镜上,把确定测微目镜的鼓轮上每小格所对 应的被测峰谷高度值的过程叫作“定度”。(h= a/2V) 定度首先是求物镜的放大倍率。求物镜放大倍率的方法 是用一个标准刻线尺(通常为专用附件,刻度间隔为 0.01mm,共101条刻线)来测定各个物镜的实际放大率。 如图4-8所示,物镜放大率为:
用比较显微镜:Ra值0.08-10m的表面。 触觉比较法:被加工表面Ra值0.63-10m。
注意点:样板与被测件的加工方法、材料、形状都相同。 适用范围:工厂比较常用,尤其是车间检验中常用。一般