预制构件质量通病
预制小型混凝土构件质量通病防治措施
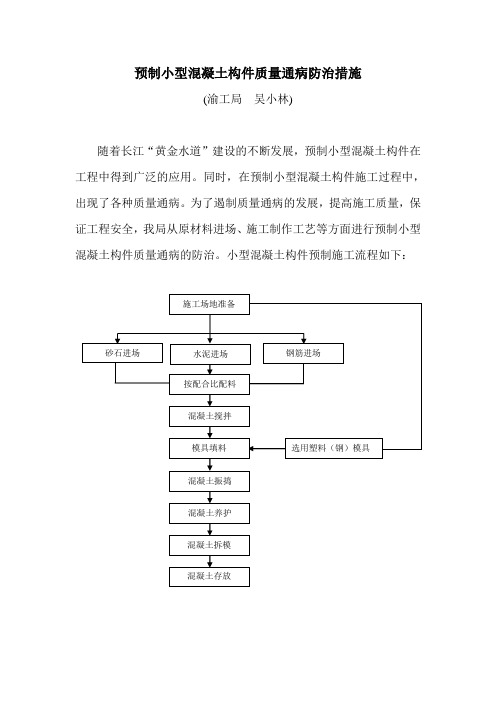
预制小型混凝土构件质量通病防治措施(渝工局吴小林)随着长江“黄金水道”建设的不断发展,预制小型混凝土构件在工程中得到广泛的应用。
同时,在预制小型混凝土构件施工过程中,出现了各种质量通病。
为了遏制质量通病的发展,提高施工质量,保证工程安全,我局从原材料进场、施工制作工艺等方面进行预制小型混凝土构件质量通病的防治。
小型混凝土构件预制施工流程如下:一、原材料进场方面质量通病1、钢筋进场控制表现特征:钢筋大小不一,参差不齐,钢筋抗拉强度、弯曲强度、重量等指标小于设计要求,钢筋直接堆放在地面上。
成因:以次充好,供货商选用小厂钢筋,钢筋堆放不规范。
危害:钢筋易氧化生锈,缩短小型混凝土构件使用寿命。
防治措施:a、检查出厂合格证,钢筋进场时进行供货商、施工方、监理方和业主方等多方验收,并进行现场见证取样送检。
检测结果合格后,才能进场使用;b、分规格、品种、批次、生产厂家分别堆放,防止混用,便于万一需要复试或退场不会搞乱;c、有标识,除了标注规格、品种、批次、生产厂家等材质的基本数据外,还应标注“合格”、“已送试”、“不合格”等内容,防止误用;d、钢筋堆放应离地,不发生泥土污染,不浸在水中,有条件的应做架子,钢筋分层上架。
关键技术:检查合格证、见证取样送检、堆放规范相关图片或示意图:钢筋参差不齐见证取样送检钢筋标识钢筋堆放相关数据:序号项目名称钢筋规格进场数量送检数量检测结果送检频率1 XX项目φ10mm 943t 16组全部合格每60t一组2 XX项目φ10mm 1582t 27组不合格1组,退场60t,其余全部合格每60t一组3 XX项目φ10mm 1569t 27组不合格2组,退场120t,其余全部合格每60t一组2、砂石进场控制表现特征:砂石颜色呈现泥黄色,颗粒直径偏小,大小不均,黄砂和碎石混合堆放。
成因:砂石含泥量较大,粒径级配不连续,砂石堆放不规范。
危害:导致小型混凝土构件易出现孔洞,降低混凝土强度,按配合比配料不准确。
预制梁场质量通病及防治措施

3
模板施工
木模板变形大
(1)对进场的模板材质、尺寸、厚度进行检查。
(2)拆模过程中要避免强拉硬拽、用力过猛。拆下的模板要及时运到存储场地,严禁在拆模现场乱堆乱放模板。
(3)周转次数多、变形大的模板不予使用。
4
预埋件施工
预埋件位置偏差大或漏埋
(1)设计图纸中明确应该预埋的预埋件数量、预埋位置和使用要求等。
质量通病及防治措施
序号
工序
质量通病
防范措施
1
基坑开挖
基坑超挖
扰动
(1)加强测量复核,要设高程控制桩,指派专人负责经常复测高程。
(2)机械开挖基槽时要由专人指挥,当机械挖至还剩20cm时,应由人工开挖修整。当开挖较浅沟槽时则采用人工开挖。
(3)当出现超挖或扰动时,应挖出扰动土并回填砂、石或其他建筑材料,分层夯实到设计标高。
2
钢筋施工
搭接焊焊缝不良
(1)严格选择焊接参数,并对焊工进行标准化操作培训,提高焊工操作水平。
(2)控制单面焊焊缝长度不小于10d,双面焊焊接长度不小于5d。
咬边或夹渣
(1)咬边的防治措施:选择合适的电流,避免电流过大;操作时电弧不能拉得过长,并控制好焊条的角度和运弧的方法;
(2)夹渣的防治措施:正确选择焊接电流,焊接时必须将焊接区域内的脏物清除干净。
(2)采用可靠的连接方式,如焊接等。
5
混凝土施工
台座、轨道基础上表面平整度超标
(1)加密台座、轨道梁施工平面内控制测量点。
(2)混凝土浇筑至顶面时要及时清浆、并带线抹面。
抹面。
台座侧面缺棱掉角
(1)混凝土浇筑完成后要封闭养护,强度低于2.5MPa时,禁止拆除模板。
PC构件质量通病及预防

精心整理PC混凝土预制构件常见的质量通病
蜂窝
麻面
孔洞
气泡
(6
烂根
露筋
指混凝土内部钢筋裸露在构件表面
缺棱掉角
指结构或构件边角处混凝土局部掉落,不规则,棱角有缺陷
处理方法:
裂缝
裂纹从混凝土表面延伸至混凝土内部,按照深度不同可分为表面裂纹,深层裂纹,贯穿裂纹。
贯穿性裂缝或深层的结构裂缝对构件的强度,耐久性,防水等造成不良影响,对钢筋的保护尤其不利。
处理方法:
色差
水纹
(1
(2
(1)优先选用保水性好的水泥,保证拌合时间。
(2)连续浇筑,生产中表层砼若有明显泌水要及时清除,采取铲掉更新新料的办法处理。
飞边
指构件拆模后由漏砂或多于砂浆形成的毛边,飞刺等。
某码头实例工程预制构件质量通病的分析、处理措施

某码头实例工程预制构件质量通病的分析、处理措施摘要:本文通过对阳江港吉树作业区#J9~#J10 泊位码头工程的监理实例,对引桥预制构件生产过程中出现的混凝土质量通病,从监理的角度,分析混凝土预制构件质量通病产生的主要原因,找出技术或者管理方面的问题,提出预制混凝土构件质量通病的处理方法和措施,积极预防预制混凝土构件质量通病反复发生,提高预制构件成品质量。
关键词:预制构件质量通病分析处理方法引言高桩码头预制构件作为码头工程中主要构件,其质量是整个码头工程质量的关键,直接影响到码头的安全和使用功能。
在许多预制构件生产中,受环境、材料、施工工艺和施工人员的工作态度等因素影响,加上管理不到位和技术上的疏忽,我们常常可以发现拆模后的预制构件混凝土存在裂缝、蜂窝、麻面、气泡和漏浆等质量通病发生。
这些都不同程度地影响着结构的质量和外观,有的甚至会造成意想不到的工程质量事故。
因此加强预制构件现场生产质量控制,避免质量通病的发生,是生产过程中质量控制的重点,只有通过对生产过程中发现的质量通病及时进行分析处理,才能避免混凝土质量通病在预制构件生产过程中多次发生,确保预制构件的安全性、耐久性,并使外观和内在质量满足建设单位的要求。
1 工程概况阳江港海陵湾港区吉树作业区#9~#10泊位,位于九姜河口南岸,为建设2个3000吨级多用途泊位,利用规划岸线长度为222m,水工结构按照5000吨级设计船型设计。
该工程设计年吞吐量为150万吨/年,其中杂货件40万吨/年、钢铁90万吨/年、集装箱2万TEU/年。
包括码头1座,平台长 222m,宽 45m,为高桩梁板式结构。
共分为 8 个结构段。
上部结构为预制梁板结构,由现浇桩帽、现浇横梁、预制横梁、预制次梁、预制面板、预制轨道梁、预制管沟梁、预制靠船构件、现浇面层及磨耗层等组成;引桥共两座,宽12m。
引桥为高桩梁板式结构,上部结构为预制梁板结构,由现浇帽梁、现浇次梁、预制次梁、预制面板、现浇面板及磨耗层组成。
预制构件质量通病

前言装配式混凝土建筑以预制构件为主要构件,常见的预制构件种类有外墙板(“三明治”结构),内墙板,叠合板,阳台板,空调板,楼梯,隔墙板,预制梁,预制柱等。
构件自身的质量是整个工程质量的关键,但因预制构件行业发展速度快、专业人员和产业技术工人匮乏、产业配套不成熟等因素,在预制构件生产过程中,预制构件质量通病时有发生,影响预制构件的外观质量和使用安全。
1. 编制目的降低预制构件在生产、检验等环节质量通病问题发生频次,提升产品质量,保证工程质量。
2、常见的预制构件质量通病介绍预制构件生产中,由于各方面的原因,如混凝土配合比、水泥质量、砂石料规格、施工工艺、蒸养工序、过程控制、运输方式等因素造成预制构件质量可控性较差,会产生各种质量通病:如蜂窝、麻面、气泡、缺棱掉角等,这类质量通病对结构、建筑通常都没有太大影响,属于次要质量缺陷,但在外观要求较高的项目(如清水混凝土项目)中,这类问题就会成为主要问题;如平整度超差、构件几何尺寸偏差等质量问题不一定会造成结构缺陷,但可能影响建筑功能和施工效率;如裂纹、强度不足、钢筋保护层问题等这类质量通病可能影响到结构安全,属于重要质量缺陷。
3、常见的预制构件质量通病、原因分析及预控措施3.1 蜂窝指混凝土结构局部出现酥松,砂浆少,石子多,气泡或石子之间形成空隙类似蜂窝状的窟窿(见图1)。
图1 预制构件蜂窝缺陷其产生原因是:(1)混凝土配合比不当或砂、石、水泥、水计量不准,造成砂浆少,石子多。
砂石级配不好,砂子少,石子多。
(2)混凝土搅拌时间不够,搅拌不均匀,和易性差。
(3)模具缝隙未堵严,造成浇筑振捣时缝隙漏浆。
(4)一次性浇筑混凝土或分层不清。
(5)混凝土振捣时间短,混凝土不密实。
预控措施:(1)严格控制混凝土配合比,做到计量准确,混凝土拌合均匀,坍落度适合。
(2)控制混凝土搅拌时间,最短不得少于规范规定。
(3)模具拼缝严密。
(4)混凝土浇筑应分层下料(预制构件端面高度大于300mm时,应分层浇筑,每层混凝土浇筑高度不得超过300mm),分层振捣,直至气泡排除为止。
装配式(PC)构件质量通病防治

装配式(PC)构件质量通病防治一、混凝土质量缺陷预制构件混凝土结构表面质量缺陷大致可以分为7个方面:麻面、蜂窝、露筋、孔洞、表面破损、不平整、表观微裂纹。
1、混凝土的麻面麻面是结构构件表面上呈现无数的小凹点,而无钢筋暴露的现象。
①.成因分析:1)钢平台、模具等表面未清理干净,附有水泥浆渣等杂物;(2)拼缝漏浆,靠近拼缝的构件表面浆少,拆模后出现麻面;(3)混凝土没有分层浇筑,造成混凝土离析,出现麻面;(4)混凝土入仓后振捣不到位,气泡未能完全排出,拆模后出现麻面;5)振捣过迟,振捣时已有部分凝固。
②.预防措施:1)钢平台、模具表面清理干净,脱模剂应涂刷均匀;(2)混凝土搅拌时间要适宜,一般应为1-2分钟;3)浇筑前检查拼缝,对可能漏浆的缝,设法封堵;4)振捣遵循快插慢拔原则,振动棒插入到拔出时间控制在20s为佳,插入下层5-10cm,振捣至混凝土表面平坦泛浆、不冒气泡、不显著下沉为止;5)新拌制混凝土必须按水泥或外加剂的性质,在初凝前振捣。
③.处置惩罚方法:1)用稀草酸溶液将该处脱模剂油点或污点用毛刷洗净,在修补前先用水湿透;2)修补用的水泥品种必须与原混凝土一致,砂子为细砂,粒径最大不宜超过1mm,按照漆工刮腻子的方法,将砂浆用刮刀大力压入麻点,随即刮平;3)水泥砂浆的配比为1:2或1:2.5,由于数量较多,可用人工在小桶内搅匀,随搅随用,必要时掺拌白水泥调色;4)修补完成后,用麻袋举行保湿养护。
2、混凝土的蜂窝蜂窝是混凝土外表呈现蜂窝似的窟窿。
①.成因分析:1)主要原因是混凝土入仓后振捣不到位,气泡未能完全排出,拆模后出现蜂窝;2)振捣过迟,振捣时已有部分凝固。
3)模板表面有较大的杂物未清理干净。
②.预防措施:1)浇捣混凝土时振捣一定要到位,不要漏振。
振捣时混凝土气泡要全部排出。
2)振捣时不能间隔时间过长,不能超过2小时(混凝土初凝),具体根据当时气温。
3)模具安装前必须清算干净,刷好模板油,避免因模板未清算干净形成蜂窝。
渡槽预制构件工程质量通病及防治措施

渡槽预制构件工程质量通病及防治措施谈到渡槽预制构件工程,哎呀,很多人脑袋一片空白,啥也不懂。
可这东西,可真跟咱们生活息息相关啊。
你想,水泥桥啊,水泥管啊,通水通电全靠它们,别看这些工程看起来挺简单,实际中可大有学问。
尤其是质量问题,哎呀,真是让人头疼。
啥问题都有,漏水、开裂、甚至掉下来,搞不好还得一身泥,麻烦事接二连三。
今天就跟大家唠唠这些渡槽预制构件工程常见的质量通病,顺便说说咋防治。
首先说到的就是“裂缝”问题,哎,简直是渡槽预制构件中的老大难。
看似一块板子,实际就跟脆皮一样,随时可能开裂。
那裂缝能不麻烦吗?水一进,马上渗透,接着土壤一沉,水就漫上来了。
小裂缝不当回事,结果大水漫灌,整个桥面都成了“湿地”。
你说能不气人?那裂缝咋来的呢?有时候是因为混凝土配比不对,有时候是因为天气太热,水分蒸发快,导致表面干裂。
咋办呢?你得先从源头控制,混凝土搅拌时,水泥、砂石比例要合适,水可不能放多了。
浇筑时,最好是选择不太热的天气,天气一热容易“快干”,混凝土就容易裂。
接下来就是“沉降”问题,说实话,这也很常见。
尤其是那些土质不稳的地方,一不小心,桥梁就出现了不平,甚至下沉。
大家一看,心里都得嘀咕:“这玩意儿能用吗?沉得比我腰上的肉还多!”这种情况,得看看基础是不是打得稳当,设计时是不是考虑到了地基的承载力。
可不是随便找个地儿就建的,像是沙子堆上修房子,指不定哪天就“沉沉沉”地往下掉。
防治这个问题的办法也不难,确保打桩时的质量,选个靠谱的施工队,别想着“节约成本”去偷工减料,地基这一块,得“稳稳的”,要是连地基都不稳,后面的一切都成了空谈。
再有一个问题,就是“漏水”问题。
哎,这个问题说起来,大家心里都不痛快。
尤其是那种天上大雨滂沱,地下水管爆了,整个渡槽就成了“大泳池”。
水怎么不漏呢?就是因为构件接缝处做得不细致!水泥块一合拢,缝隙留得大了,哪有不漏水的道理?这个问题也不复杂,关键在于接缝处的密封处理。
你做得好,水就能留在里面,做得不好,水就溜走。
桥梁施工中预制构件质量通病及防治

桥梁施工中预制构件质量通病及防治摘要:随着近年来国家到地方,针对桥梁工业化生产、装配式施工的相关政策扶持力度越来越大。
桥梁工程施工中预制构件得到了非常广泛的应用,但在这其中也存在着一些质量问题影响着桥梁的使用寿命,为了提升全国桥梁工程预制构件建设的技术和管理工作,加强对桥梁工程预制构件质量相关问题的研究具有十分重要的意义。
关键词:桥梁施工;预制构建;质量通病;防治措施1.桥梁施工预制构件的优点桥梁按结构组成分为数个部件,构件是部件的下一级分类。
如对于简支T型梁桥,所有的T梁组成一个部件,每一片单独T梁是一个构件。
公路桥梁、铁路桥梁、城市立交,在城市化进程中,桥梁预制构件随处可见,构件质量问题直接关乎工程的安全性。
预制构件在桥梁工程中的应用具有如下优点:1.智能化施工。
预制构件工厂生产线主要由以下设备组成:模台、混凝土输送机、混凝土布料机、振动台及控制系统、模台存取机及控制系统、预养护系统及温控系统、立体养护窑及蒸养温控系统、翻转脱模机、运板平车、刮平机、抹光机、模具清扫机、数控划线机、摆渡车、行吊等组成。
在构件生产中建立了集数据采集、流程传递、综合管理的智能工厂管理平台,采用了高效混凝土搅拌设备、钢筋自动化加工设备、智能原材仓储设备、智能传感与控制设备等自动化智能化生产设备,经过合理布置及工序的合理安排,实现了多种智能化、自动化设备协同联动,提升了预制构件生产效率和构件质量,相比于传统生产模式,生产效率可提高约30%。
2.提高施工效率及质量。
通过对目前已建和在建的装配式桥梁总结,预制拼装技术可有效缩短现场施工工期。
其中预制立柱每台班可安装3-4根,预制盖梁每台班可安装2-3个,预制小箱梁每台班可安装6-8片。
混凝土保护层合格率更高,采用卧式支模,钢筋笼及模板整体翻转工艺;混凝土外观质量更高,采用优化设计的模板;混凝土运输更有保障,厂内自建拌合站。
3.降低对交通影响,具有绿色环保的特点。
可夜间吊装施工、支架现浇,白天实现车辆正常通行。
预制装配工程质量通病与防治

部已经反打的保温板切割凿除(宽度按节点图纸 要求)。一是用作施工防火隔离带,二是便于进 行防水施工。
• ②上层预制墙板安装前,墙根底部必须将垃圾清 理干净,内外进行座浆后,安装墙板就位、校正、 临时固定,灌浆前在灌浆孔内洒水湿润,确保灌 浆料的流动性和灌浆密实度。
• ③在水平缝上下各200mm宽范围内做两道JS水泥 基防水涂料。
• ④进行喷淋试验,试验方法同外墙铝合金窗。不 出现渗漏判定为合格,该部位进行外保温施工。
预制装配工程质量通病与防治
装配式建筑常见通病案例分析
1、外墙部分构件墙板未设计上翻600、未留设 止水企口等导致外墙渗漏
1.1构件水平缝设计20mm,保温板缝间直接用水泥砂浆填补, 在没有设置止水措施情况下成为外墙层间接水槽,直接导致 渗漏
防治措施:
• 1、设计部在构件转化时严格按照《预制装配整体 式剪力墙结构体系技术规程》 DGJ32/TJ1252011进行,海门世纪城96#楼6层以上及沈阳世纪 城5、8#楼加设企口止水;见下图
PC构件项目质量通病防治方案
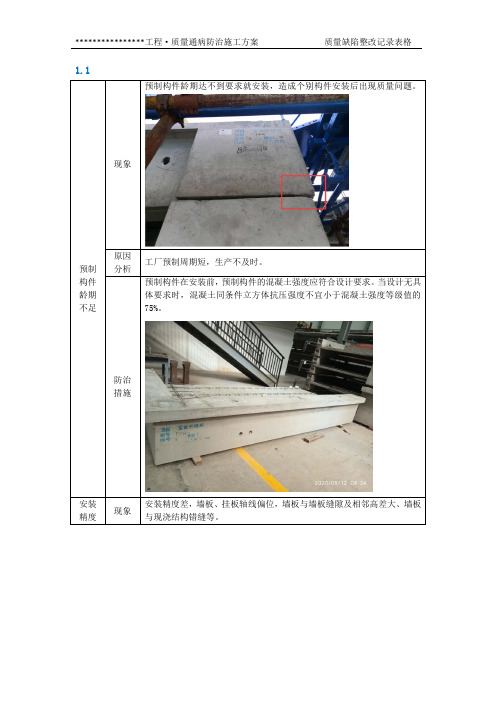
1.1
预制构件龄期达不到要求就安装,造成个别构件安装后出现质量问题。
预制构件在安装前,预制构件的混凝土强度应符合设计要求。
当设计无具
体要求时,混凝土同条件立方体抗压强度不宜小于混凝土强度等级值的
75%。
安装精度差,墙板、挂板轴线偏位,墙板与墙板缝隙及相邻高差大、墙板
1、施工人员操作水平不行,大面积施工前未进行试安装、未组织样板验
预制构件钢筋深入现浇结构尺寸不符合要求;构件与现浇结构之间缝处理不好,造成后期开裂;PC构件安装后楼产生小裂缝。
图1.1
图1.2
5、模板支撑、起拱以及拆模进行严格控制,以防安装后楼板产生裂缝。
钢筋套筒灌浆连接或钢筋约束浆锚搭接连接的连接钢筋偏位,安装困难,影响连接质量。
有效措施处理。
墙板找平垫块不规范,灌浆不规范。
2、模板或连接处缝隙封堵应加强质量控制与验收,保证现浇结构质量。
预制墙板连接的现浇短肢墙模板安装不规范,影响现浇结构质量。
叠合楼板、叠合墙板开裂,叠合楼板之问连接缝开裂,外挂板裂缝,外挂板与外挂板缝、内隔墙与周边裂缝。
1、预制构件进场未严格组织进场验收、把关不严;
4、加强成品保护,严禁在预制构件时开槽打洞。
外墙渗漏。
1、未做好关键部位防水;。
预制装配式建筑PC构件结构质量通病及预防措施
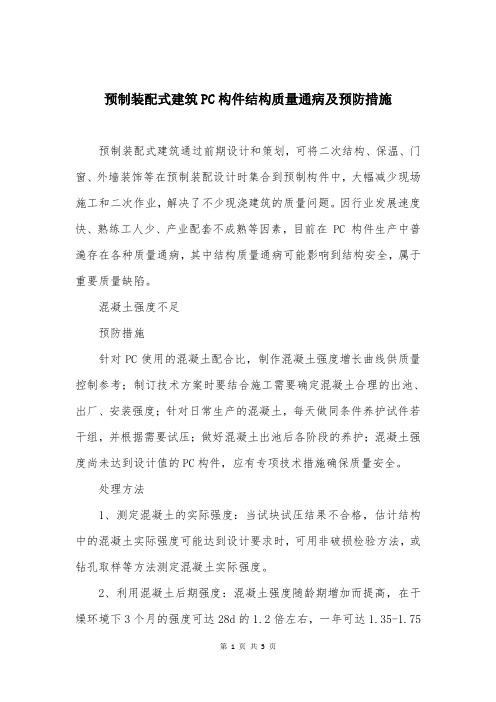
预制装配式建筑PC构件结构质量通病及预防措施预制装配式建筑通过前期设计和策划,可将二次结构、保温、门窗、外墙装饰等在预制装配设计时集合到预制构件中,大幅减少现场施工和二次作业,解决了不少现浇建筑的质量问题。
因行业发展速度快、熟练工人少、产业配套不成熟等因素,目前在 PC 构件生产中普遍存在各种质量通病,其中结构质量通病可能影响到结构安全,属于重要质量缺陷。
混凝土强度不足预防措施针对PC使用的混凝土配合比,制作混凝土强度增长曲线供质量控制参考;制订技术方案时要结合施工需要确定混凝土合理的出池、出厂、安装强度;针对日常生产的混凝土,每天做同条件养护试件若干组,并根据需要试压;做好混凝土出池后各阶段的养护;混凝土强度尚未达到设计值的PC构件,应有专项技术措施确保质量安全。
处理方法1、测定混凝土的实际强度:当试块试压结果不合格,估计结构中的混凝土实际强度可能达到设计要求时,可用非破损检验方法,或钻孔取样等方法测定混凝土实际强度。
2、利用混凝土后期强度:混凝土强度随龄期增加而提高,在干燥环境下3个月的强度可达28d的1.2倍左右,一年可达1.35-1.75倍。
如果混凝土实际强度比设计要求低的不多,可以采用加强养护。
3、减少结构荷载:由于混凝土强度不足造成结构承载能力明显下降,又不便采用加固补强方法处理时,通畅采用减少结构荷载的方法处理。
例如,采用高效轻质的保温材料代替白灰炉渣或水泥炉渣等措施,减轻建筑物自重,又降低建筑物的总高度等。
4、结构加固:柱混凝土强度不足时,可采用外包钢筋混凝土或外包钢加固,也可采用螺旋筋约束柱法加固。
梁混凝土强度低导致抗剪能力不足时,可采用外包钢筋混凝土及粘帖钢板方法加固。
当梁混凝土强度严重不足,导致正截面强度达不到规范要求时,可采用钢筋混凝土加高梁,也可采用预应力拉杆补强体系加固等。
钢筋或结构预埋件尺寸偏差过大预防措施深化设计阶段应用bim技术进行构件钢筋之间、钢筋与预埋件预留孔洞之间的碰撞检查;采用高精度机械进行钢筋半成品加工;结合安装工艺,考虑预留钢筋与现浇段的钢筋的位置关系;钢筋绑扎或焊接必须牢固,固定钢筋骨架和预埋件的措施可靠有效;浇筑混凝土之后要专门安排工人对预埋件和钢筋进行复位;严格执行检验程序。
预制排架结构中混凝土预制构件的质量通病及预防措施
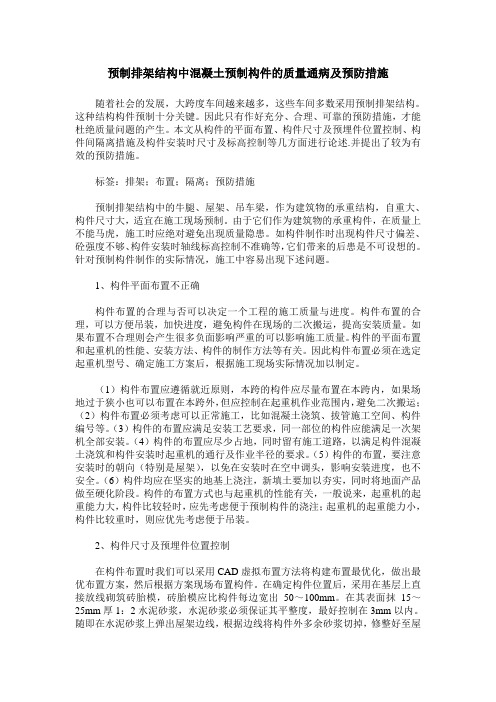
预制排架结构中混凝土预制构件的质量通病及预防措施随着社会的发展,大跨度车间越来越多,这些车间多数采用预制排架结构。
这种结构构件预制十分关键。
因此只有作好充分、合理、可靠的预防措施,才能杜绝质量问题的产生。
本文从构件的平面布置、构件尺寸及预埋件位置控制、构件间隔离措施及构件安装时尺寸及标高控制等几方面进行论述.并提出了较为有效的预防措施。
标签:排架;布置;隔离;预防措施预制排架结构中的牛腿、屋架、吊车梁,作为建筑物的承重结构,自重大、构件尺寸大,适宜在施工现场预制。
由于它们作为建筑物的承重构件,在质量上不能马虎,施工时应绝对避免出现质量隐患。
如构件制作时出现构件尺寸偏差、砼强度不够、构件安装时轴线标高控制不准确等,它们带来的后患是不可设想的。
针对预制构件制作的实际情况,施工中容易出现下述问题。
1、构件平面布置不正确构件布置的合理与否可以决定一个工程的施工质量与进度。
构件布置的合理,可以方便吊装,加快进度,避免构件在现场的二次搬运,提高安装质量。
如果布置不合理则会产生很多负面影响严重的可以影响施工质量。
构件的平面布置和起重机的性能、安装方法、构件的制作方法等有关。
因此构件布置必须在选定起重机型号、确定施工方案后,根据施工现场实际情况加以制定。
(1)构件布置应遵循就近原则,本跨的构件应尽量布置在本跨内,如果场地过于狭小也可以布置在本跨外,但应控制在起重机作业范围内,避免二次搬运;(2)构件布置必须考虑可以正常施工,比如混凝土浇筑、拔管施工空间、构件编号等。
(3)构件的布置应满足安装工艺要求,同一部位的构件应能满足一次架机全部安装。
(4)构件的布置应尽少占地,同时留有施工道路,以满足构件混凝土浇筑和构件安装时起重机的通行及作业半径的要求。
(5)构件的布置,要注意安装时的朝向(特别是屋架),以免在安装时在空中调头,影响安装进度,也不安全。
(6)构件均应在坚实的地基上浇注,新填土要加以夯实,同时将地面产品做至硬化阶段。
混凝土预制构件常见质量通病与防治

混凝土预制构件常见质量通病与防治装配整体式混凝土结构是以预制混凝土构件为主要构件,经装配、连接,结合部分现浇而形成的混凝土结构。
预制构件自身质量是整个工程质量的关键,但由于我国建筑工业化起步相对较晚,标准体系不够健全,专业人员和产业技术工人匮乏,预制构件质量通病时有发生。
1质量通病与防治措施以下是笔者从国内几种体系,十几个项目建设实践梳理总结出来的装配整体式混凝土结构预制构件常见质量通病及其防治措施。
1.1质量问题一预制构件存在裂缝、麻面、缺棱掉角等外表缺陷、外形缺陷。
防治措施:①构件制作前,模具表面必须清理干净,做到光滑、平整、不生锈;模具和混凝土接触面应刷(喷)涂隔离剂,涂刷隔离剂要均匀,不得漏刷或积存。
②钢筋制作安装控制好钢筋间距、保护层厚度,当钢筋保护层过后时,要采取有效的防裂构造措施。
对管道预埋、洞口、边角等薄弱部位应有相应的构造措施。
③优化混凝土配合比,改善混凝土生产工艺。
混凝土配合比应经认真设计和试配,使符合设计强度和性能要求,水泥砂石质量、骨料级配、杂质含量要控制好,外加剂应先试验,严格控制掺用量。
④根据混凝土的品种、工作性等制定合理的搅拌操作规程搅拌均匀。
混凝土浇注宜采用振动台、机械振捣方式成型,并应根据混凝土的品种、工作性、预制构件的规格形状等因素,制定合理的振捣成型操作规程。
⑤预制构件采用自然养护时,应符合现行国家标准《混凝土结构工程施工规范》(GB50666)、现行国家标准《混凝土结构工程施工质量验收规范》(GB50204)的要求。
预制构件采用加热养护时,应按养护制度要求控制静停、升温、恒温和降温时间,并应控制升降温速度不超过20℃/h,最高养护温度不宜超过60℃。
⑥预制构件侧模拆除时的混凝土强度应能保证其表面及棱角不受损伤。
预制构件脱模起吊时,应根据设计要求或具体生产条件确定同条件混凝土抗压强度,且混凝土强度应不小于15MPa。
预制构件在脱模、翻转、运输、安装等各工况的验算,应将构件自重标准值乘以脱模吸附系数或动力系数后作为等效静荷载标准值。
装配式建筑培训之预制构件质量通病、原因分析及预控措施(构件强度不足、混凝土强度离散性大)

装配式建筑培训之预制构件质量通病、原因分析及预控措施(构件强度不足、混凝土强度离散性大)预制构件强度不足问题指同批混凝土试块的抗压强度按《混凝土强度检验评定标准》的规定评定不合格。
产生原因1.原材料质量差1)水泥质量不良。
主要反映在两个方面:一是水泥实际活性(强度)低,主要原因是水泥出厂质量差、保管条件差或贮存时间过长,水泥结块,活性降低。
二是水泥安定性不合格,导致混凝土强度不够。
2)骨料(砂、石)质量不合格,石子本身强度不够,砂子含泥量超标。
3)拌合水质量不合格。
4)外加剂质量差。
2.配合比不合适混凝土配合比是决定强度的重要因素之一,其中水灰比大小直接影响混凝土强度,施工过程中材料计量不准确,外加剂使用方法错误或质量差。
3.施工工艺存在问题1)混凝土拌制时间短且不均匀,影响强度。
2)运输条件和运输设备差,运输距离较远,在运输中使混凝土产生离析。
3)浇筑方法不当,成型振捣不密实。
4)养护条件不良,湿度不够,早期缺水干燥或早期受冻,造成混凝土强度偏低。
5)试件制作不规范。
试件强度试验方法不规范。
4.混凝土养护时间短,措施不到位,缺乏过程混凝土强度监控措施。
预制构件出模强度偏低,后期养护措施不到位。
1.加强试验检查,确保原材料质量,严格控制不合格材料进场。
2.水泥进场必须有出厂合格证,未经检验或检验不合格的严禁使用,加强对水泥贮存和使用的管理。
3.严格控制砂石级配及含泥量等指标,砂石料须经试验合格后方可使用。
4.严格控制混凝土的配合比,保证计量准确。
5.应按顺序拌制混凝土,要合理拌制,保证搅拌时间和均匀性。
6.如在生产过程中发现不合格混凝土时禁止使用,生产车间及时通知试验室调整混凝土质量。
7.按规定认真制作试块,加强对试块的管理和养护。
规范试验程序,严格按操作规程进行试件强度试验。
8.浇筑完的构件,要严格按技术交底的要求蒸汽养护,做好养护记录,并出模的构件洒水养护。
加强落实并执行蒸养养护制度,设置专职养护人员。
- 1、下载文档前请自行甄别文档内容的完整性,平台不提供额外的编辑、内容补充、找答案等附加服务。
- 2、"仅部分预览"的文档,不可在线预览部分如存在完整性等问题,可反馈申请退款(可完整预览的文档不适用该条件!)。
- 3、如文档侵犯您的权益,请联系客服反馈,我们会尽快为您处理(人工客服工作时间:9:00-18:30)。
前言装配式混凝土建筑以预制构件为主要构件,常见的预制构件种类有外墙板(“三明治”结构),内墙板,叠合板,阳台板,空调板,楼梯,隔墙板,预制梁,预制柱等。
构件自身的质量是整个工程质量的关键,但因预制构件行业发展速度快、专业人员和产业技术工人匮乏、产业配套不成熟等因素,在预制构件生产过程中,预制构件质量通病时有发生,影响预制构件的外观质量和使用安全。
1. 编制目的降低预制构件在生产、检验等环节质量通病问题发生频次,提升产品质量,保证工程质量。
2、常见的预制构件质量通病介绍预制构件生产中,由于各方面的原因,如混凝土配合比、水泥质量、砂石料规格、施工工艺、蒸养工序、过程控制、运输方式等因素造成预制构件质量可控性较差,会产生各种质量通病:如蜂窝、麻面、气泡、缺棱掉角等,这类质量通病对结构、建筑通常都没有太大影响,属于次要质量缺陷,但在外观要求较高的项目(如清水混凝土项目)中,这类问题就会成为主要问题;如平整度超差、构件几何尺寸偏差等质量问题不一定会造成结构缺陷,但可能影响建筑功能和施工效率;如裂纹、强度不足、钢筋保护层问题等这类质量通病可能影响到结构安全,属于重要质量缺陷。
3、常见的预制构件质量通病、原因分析及预控措施3.1 蜂窝指混凝土结构局部出现酥松,砂浆少,石子多,气泡或石子之间形成空隙类似蜂窝状的窟窿(见图1)。
图1 预制构件蜂窝缺陷其产生原因是:(1)混凝土配合比不当或砂、石、水泥、水计量不准,造成砂浆少,石子多。
砂石级配不好,砂子少,石子多。
(2)混凝土搅拌时间不够,搅拌不均匀,和易性差。
(3)模具缝隙未堵严,造成浇筑振捣时缝隙漏浆。
(4)一次性浇筑混凝土或分层不清。
(5)混凝土振捣时间短,混凝土不密实。
预控措施:(1)严格控制混凝土配合比,做到计量准确,混凝土拌合均匀,坍落度适合。
(2)控制混凝土搅拌时间,最短不得少于规范规定。
(3)模具拼缝严密。
(4)混凝土浇筑应分层下料(预制构件端面高度大于300mm时,应分层浇筑,每层混凝土浇筑高度不得超过300mm),分层振捣,直至气泡排除为止。
(5)混凝土浇筑过程中应随时检查模具有无漏浆、变形,若有漏浆、变形时,应及时采取补救措施。
(6)振捣设备应根据不同的混凝土品种、工作性能和预制构件的规格形状等因素确定,振捣前应制定合理的振捣成型操作规程。
3.2麻面指构件表面局部出现缺浆粗糙或形成许多小坑、麻点等,形成一个粗糙面(图2)。
图2 预制构件麻面缺陷其产生原因是:(1)模具表面粗糙或粘附水泥浆渣等杂物未清理于净,拆模时混凝土表面被粘坏。
(2)模具清理及脱模剂涂刷工艺不当,致使混凝土中水分被模具吸去,使混凝土失水过多出现麻面。
(3)摸具拼缝不严,局部漏浆。
(4)模具隔离剂涂刷不匀,或局部漏刷或失效,混凝土表面与模板粘结造成麻面。
(5)混凝土振捣不实,气泡未排出,停在模板表面形成麻点。
预控措施:(1)在构件生产前,需要将模具表面清理干净,做到表面平整光滑,保证不出现生锈现象。
(2)模具和混凝土的接触面应涂抹隔离剂,在进行隔离剂的涂刷过程中一定要均匀,不能出现漏刷或者是积存。
(3)混凝土应分层均匀振捣密实,至排除气泡为止。
(4)浇筑混凝土前认真检查模具的牢固性及缝隙是否堵好。
(5)露天生产时,应有相应的质量保证措施。
3.3孔洞指混凝土中孔穴深度和长度均超过保护层厚度(图3)。
图3 预制构件孔洞缺陷其产生的原因是:(1) 在钢筋较密的部位或预留孔洞和埋件处,混凝土下料被搁住,未振捣就继续浇筑上层混凝土。
(2) 混凝上离析,砂浆分离,石子成堆,严重跑浆,又未进行振捣。
(3) 混凝土一次下料过多、过厚,振捣器振动不到,形成松散孔洞。
(4) 混凝土内掉入泥块等杂物,混凝土被卡住。
预控措施:(1) 在钢筋密集处及复杂部位,采用细石混凝土浇灌。
(2) 认真分层振捣密实,严防漏振。
(3) 砂石中混有粘土块、模具工具等杂物掉入混凝土内,应及时清除干净。
3.4气泡指预制构件脱模后,构件表面存在除个别大气泡外,细小气泡多,呈片状密集(图4)。
图4 预制构件气泡缺陷其产生的原因是:(1)砂石级配不合理,粗集料过多,细集料偏少。
(2)骨料大小不当,针片状颗粒含量过多。
(3)用水量较大,水灰比较高的混凝土。
(4)脱模剂质量效果差或选择的脱模剂不合适。
(5)与混凝土浇筑中振捣不充分、不均匀有关。
往往浇筑厚度超过技术规范要求,由于气泡行程过长,即使振捣的时间达到要求,气泡也不能完全排出。
预控措施:(1)严格把好材料关,控制骨料大小和针片状颗粒含量,备料时要认真筛选,剔除不合格材料。
(2)优化混凝土配合比。
(3)模板应清理干净,选择效果较好的脱模剂,脱模剂要涂抹均匀。
(4)分层浇筑,一次放料高度不宜超过300mm。
对于较长构件预制梁要指挥天车来回移动,均匀布料。
(5)要选择适宜的振捣设备,最佳的振捣时间,振捣过程中要按照“快插慢抽、上下抽拔”的方法,操作振动棒要直上直下,快插慢拔,不得漏振,振动时要上下抽动,每一振点的延续时间以表面呈现浮浆为度,以便将气泡排出。
振捣棒插到上一层的浇筑面下100mm为宜,使上下层混凝土结合成整体。
严防出现混凝土欠振、漏振和超振现象。
3.5烂根指预制构件浇筑时,混凝土浆顺模具缝隙从模具底部流出或模具边角位置脱模剂堆积等原因,导致底部混凝土面出现“烂根”(图5)。
图5 预制构件烂根缺陷其产生的原因是:(1)模具拼接缝隙较大,或模具固定螺栓或拉杆未拧牢固。
(2)模具底部封堵材料的材质不理想及封堵不到位造成密封不严,引起混凝土漏浆。
(3)混凝土离析。
(4)脱模剂涂刷不均匀。
预控措施:(1)模具拼缝严密。
(2)模具侧模与侧模间、侧模与底模间应张贴密封条,保证缝隙不漏浆;密封条材质质量应满足生产要求。
(3)优化混凝土配合比。
浇筑过程中注意振捣方法、振捣时间,避免过度振捣。
(4)脱模剂应涂刷均匀,无漏刷、无堆积现象。
3.6露筋指混凝土内部钢筋裸露在构件表面(图6)。
图6 预制构件露筋缺陷其产生的原因是:(1)在灌筑混凝土时,钢筋保护层垫块位移垫块太少或漏放,致使钢筋紧贴模具外露。
(2)结构构件截面小,钢筋过密,石子卡在钢筋上,使水泥砂浆不能充满钢筋周围,造成露筋。
(3)混凝土配合比不当,产生离折,靠模具部位缺浆或模具漏浆。
(4)混凝土保护层太小或保护层处混凝土漏振或振捣不实,或振捣棒撞击钢筋或踩踏钢筋,使钢筋位移,造成露筋。
(5)脱模过早,拆模时缺棱、掉角,导致露筋。
预控措施:(1)钢筋保护层垫块厚度、位置应准确,垫足垫块,并固定好,加强检查。
(2)钢筋稠密区域,按规定选择适当的石子粒径,最大粒径不得超过结构界面最小尺寸的1/3。
(3)保证混凝土配合比准确和良好的和易性。
(4)模板应认真堵好缝隙。
(5)混凝土振捣严禁撞击钢筋,操作时,避免踩踏钢筋,如有踩弯或脱扣等及时调整。
(6)正确掌握脱模时间,防止过早拆模,碰坏棱角。
3.7缺棱掉角指结构或构件边角处混凝土局部掉落,不规则,棱角有缺陷(图7)。
图7 预制构件缺棱掉角缺陷其产生的原因是:(1)脱模过早,造成混凝土边角随模具拆除破损。
(2)拆模操作过猛,边角受外力或重物撞击保护不好棱角被碰掉。
(3)模具边角灰浆等杂物未清理干净,未涂刷隔离剂或涂刷不均匀。
(4)构件成品在脱模起吊、存放、运输等过程受外力或重物撞击保护不好棱角被碰掉。
预控措施:(1)控制构件脱模强度。
脱模时,构件强度应满足设计强度等级时要求方可脱模。
(2)拆模时注意保护棱角,避免用力过猛。
(3)模具边角位置要清理干净,不得粘有灰浆等杂物。
(4)涂刷隔离剂要均匀,不得漏刷或积存。
(5)加强预制构件成品成品的保护。
3.8裂缝裂纹从混凝土表面延伸至混凝土内部,按照深度不同可分为表面裂纹、深层裂纹、贯穿裂纹。
贯穿性裂缝或深层的结构裂缝对构件的强度、耐久性、防水等造成不良影响,对钢筋的保护尤其不利(图8)。
图8 预制构件裂缝缺陷产生的原因是:(1)混凝土失水干缩引起的裂缝:成型后养护不当,受到风吹日晒,表面水分散失快。
(2)采用含泥量大的粉砂配制混凝土,收缩大,抗拉强度低。
(3)不当荷载作用引起的结构裂缝,构件上部放置其他荷载物。
(4)蒸汽养护过程中升温降温太快。
(5)预制构件吊装、码放不当引起的裂缝。
(6)预制构件在运输及库区堆放过程中支垫位置不对产生裂缝。
(7)预制构件较薄、跨度大易引起的裂缝。
(8)构件拆模过早,混凝土强度不足,使得构件在自重或施工荷载下产生裂缝。
(9)钢筋保护层过大或过小。
预控措施:(1)成型后及时覆盖养护,保湿保温。
(2)优化混凝土配合比,控制混凝土自身收缩。
(3)控制混凝土水泥用量,水灰比和砂率不要过大。
严格控制砂、石含泥量,避免使用过量粉砂。
(4)制定详细的构件脱模吊装、码放、倒运、安装方案并严格执行。
构件堆放时支点位置不应引起混凝土发生过大拉应力。
堆放场地应平整夯实,有排水措施。
堆放时垫木要规整,水平方向要位于同一水平线上,竖向要位于同一垂直线上。
堆放高度视构件强度、地面耐压力、垫木强度和堆垛稳定性而定等。
禁止在构件上部放置其他荷载及人员踩踏。
(5)根据实际生产情况制定各类型构件养护方式,设置专人进行养护。
拆模吊装前必须委托试验室做试块抗压报告,在接到实验室强度报告合格单后再对构件实施脱模作业,从而保证构件的质量。
要保证预制构件在规定时间内达到脱模要求值,要求劳务班组优化支模、绑扎等工序作业时间,加强落实蒸养制度,加强对劳务班组(蒸养人员)的管理等。
(6)构件生产过程严格按照图纸及变更施工,保证钢筋保护层厚度符合要求。
在进行钢筋制作中,需要严格控制钢筋间距和保护层的厚度。
如果钢筋保护层出现过厚的现象,需要对其进行防裂措施。
同时需要对管道预埋部位以及洞口和边角部位采取一定的构造加强措施。
(7)减少构件制作跨度,尤其是叠合板构件。
叠合板在吊装过程中经常会因为跨度过大而断裂。
为了解决这一问题,可以事先与设计单位沟通,建议设计单位在进行构件设计时充分考虑这一问题,尽量将叠合板跨度控制在板的挠度范围内,以减少现场吊装过程中叠合板的损坏。
3.9色差指混凝土在施工及养护过程中存在不足,造成构件表面色差过大,影响构件外观质量。
尤其是清水构件直接采用混凝土的自然色作为饰面,因而混凝土表面质量直接影响构件的整体外观质量。
所以混凝土表面应平整、色泽均匀、无碰损和污染现象(图9)。
图9 预制构件色差缺陷其产生的原因是:(1)原材料变化及配料偏差。
(2)搅拌时间不足,水泥与砂石料拌合不均匀,造成色差影响。
(3)混凝土在施工中,由于使用工具不当,如振动棒接触模板振捣,将会在混凝土构件表面形成振动棒印,而影响构件外观效果。
(4)由于混凝土的过振造成混凝土离析出现水线状,形成类似裂缝状影响外观,同时经常引起不必要的麻烦与怀疑。