德州炼油厂火灾爆炸事故案例
BP美国德州炼油厂火灾爆炸事故

BP美国德州炼油厂火灾爆炸事故2005年3月23日中午1∶20左右,BP(英国石油公司)美国德克萨斯州炼油厂的碳氢化合物车间发生了火灾和一系列爆炸事故,15名工人被当场炸死,170余人受伤,在周围工作和居住的许多人成为爆炸产生的浓烟的受害者。
同时,这起事故还导致了严重的经济损失。
这是过去20年间美国作业场所最严重的灾难之一(注:BP德克萨斯州炼油厂隶属于BP北美产品公司,是BP公司最大的综合性炼油厂,每天可处理46万桶原油,日产1 100万加仑汽油)。
爆炸发生后,CSB(美国化工安全与危害调查局)随即于3月26日成立了专门调查小组,并于4月1日正式进驻BP 在德克萨斯州的炼油厂。
CSB于2005年8月17日发布了新闻公报,公布了对BP 公司德州炼油厂系列爆炸事故的初步调查结果。
BP美国德克萨斯州炼油厂火灾爆炸事故现场事故原因分析直接原因异构化装置主管的失职和值班工人没有遵循书面程序的规定操作是事故发生的直接原因。
具体表现在:误操作操作工在异构化装置ISOM开车前误操作,造成烃分馏液面高出控制温度3.9℃。
粗心大意操作工对阀门和液面检查粗心大意,没有及时发现液面超标,结果液面过高导致分馏塔超压,大量物料进入放空罐,气相组分从放空烟囱溢出后发生爆炸。
监管不力异构化装置的主管没有通过检查确保操作人员正确的操作程序。
应急反应主管在事故发生的关键时刻离岗,设备操作人员没有及时拉响疏散警报。
间接原因缺乏文化氛围历经多年的工作环境已被侵蚀到排斥变化的地步,而且缺乏信任、动力和目标。
监督和管理行为不清晰。
对条例的执行不彻底。
员工个人感觉没有提建议和进行改进的权利。
管理不利管理者没有建立或强制实行流程安全、操作执行程序、系统的降低风险优先权等。
没有从BP其他事故中吸取教训。
职责与责任不清复杂组织内的众多变化,包括组织结构和人员的调整,导致了责任不明和沟通不畅。
结果造成员工对角色、职责和优先顺序迷惑不清。
缺乏危害辨识要归咎于对危险辨识不足,对站点流程安全的理解知之甚少,这些导致了人们承受了更大的风险。
德州合力科润化工有限公司“1.1”爆炸事故
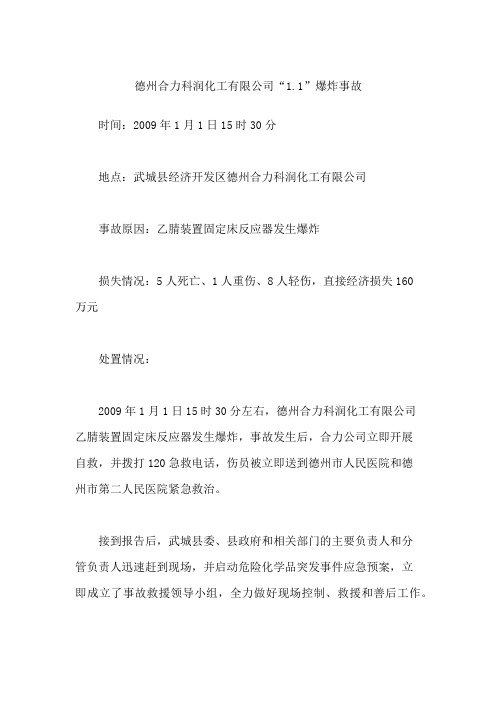
德州合力科润化工有限公司“1.1”爆炸事故时间:2009年1月1日15时30分地点:武城县经济开发区德州合力科润化工有限公司事故原因:乙腈装置固定床反应器发生爆炸损失情况:5人死亡、1人重伤、8人轻伤,直接经济损失160万元处置情况:2009年1月1日15时30分左右,德州合力科润化工有限公司乙腈装置固定床反应器发生爆炸,事故发生后,合力公司立即开展自救,并拨打120急救电话,伤员被立即送到德州市人民医院和德州市第二人民医院紧急救治。
接到报告后,武城县委、县政府和相关部门的主要负责人和分管负责人迅速赶到现场,并启动危险化学品突发事件应急预案,立即成立了事故救援领导小组,全力做好现场控制、救援和善后工作。
(一)迅速抢救伤亡人员。
按照“生命重于泰山、时间就是生命”的原则,武城县委、县政府立即组织公安、消防、卫生等部门迅速开展救助,并将受伤人员转送医院进行紧急救治。
同时,组织公安干警现场值勤,确保事故现场秩序稳定。
(二)迅速成立事故处理领导小组。
立即成立了由县委、县政府主要领导同志任组长,有关领导和相关部门主要负责人为成员的事故处理领导小组,下设综合协调、医疗救治、现场处置、事故调查、善后处理、新闻接待六个工作小组,集中做好事故处置工作。
(三)积极做好伤员救治和伤亡家属的安抚工作。
建立了一个伤亡人员一套工作班子的工作机制,稳定伤亡者家属的情绪,有关领导及卫生局、民政局、劳动局、县医院等单位负责同志靠上工作,积极做好救治和安抚工作。
对于死亡人员,有关部门主要负责人、有关乡镇书记、派出所长和村支部书记,积极做好死者家属的安抚工作,并在最短时间内做好理赔等各项善后工作。
(四)认真搞好事故调查。
组织事故调查小组,积极配合省市调查组的工作,对事故原因展开深入调查,全面调查事故发生的原因。
重点了解这次试车过程中有关物品、设备的质量问题,了解操作规程是否符合规定,为事故处理奠定基础。
(五)加强现场处置。
立即责令德州合力化工公司全面停产整顿,不经验收不得开工、试车。
山东德齐龙化工集团有限公司“7.11”爆炸事故_1

2007年7月11日23时50分,山东省德州市平原县德齐龙化工集团有限公司一分厂16万吨/年氨醇、25万吨/年尿素改扩建项目试车过程中发生爆炸事故,造成9人死亡、1人受伤。
事故发生后,国家安全监管总局局长李毅中、副局长王德学、孙华山,山东省代省长姜大明、副省长王军民对事故救援和处理作出批示。
山东省省长助理张传林赶赴事故现场,组织指导救援工作。
国家安全监管总局派员赴事故现场,协助、指导事故调查处理等工作。
事故单位基本情况德齐龙化工集团有限公司成立于2004年,系原地方国有的平原县化肥厂改制后成立的民营股份制企业。
该公司现有总资产约20亿元,职工约2800人,有2个生产分厂。
主要产品年生产能力为:合成氨75万吨,尿素100万吨,甲醇30万吨,碳酸氢铵24万吨,三聚氰胺3万吨。
事故发生在一分厂16万吨/年氨醇改扩建生产线试车过程中,该生产线由造气、脱硫、脱碳、净化、压缩、合成等工艺单元组成,发生爆炸的是压缩工序2号压缩机七段出口管线。
事故简要经过该公司一分厂16万吨/年氨醇、25万吨/年尿素生产线,于2007年6月开始单机试车,7月5日单机调试完毕,由企业内部组织项目验收。
7月10日2号压缩机单机调试、空气试压(试压至18MPa)、二氧化碳置换完毕。
7月11日15时30分,开始正式投料试车,先开2号压缩机组,引入工艺气体(N2、H2混合气体),逐级向2号压缩机七段(工作压力24MPa)送气试车。
23时50分,2号压缩机七段出口管线突然发生爆炸,气体泄漏引发大火,造成8人当场死亡,一人因大面积烧伤抢救无效于14日凌晨0时10分死亡,一人轻伤。
事故还造成部分厂房顶棚坍塌和仪表盘烧毁。
事故发生的直接原因事故发生后,山东省德州市人民政府组成事故调查组对事故有关情况进行调查,经初步分析判断,排除了化学爆炸和压缩机出口超压的可能,爆炸为物理爆炸。
事故发生的直接原因是2号压缩机七段出口管线存在强度不够、焊接质量差、管线使用前没有试压等严重问题,导致事故的发生。
最新BP德克萨斯炼油厂爆炸事故案例学习(教学版)解析ppt课件
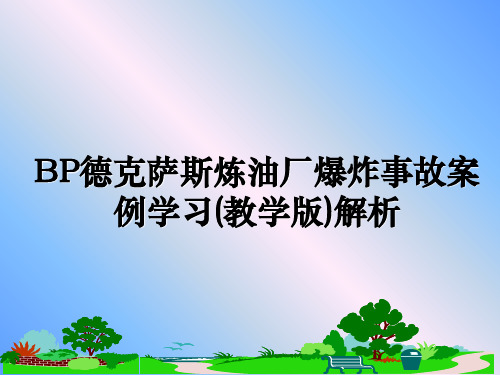
第二章 事故经过
爆炸后放空罐继续喷出烃类物质,装置持续燃烧。
第二章 事故经过
距离异构化装置数百 米远距离上拍摄的图 像-浓烟滚滚
第二章 事故经过
事故后的现场:异构化装置成为了废墟。
第二章 事故经过
2.4 学员观看事故录像 放映该事故的录像,该录像真实的还原了事故发生的
整个过程以及所造成的惨痛后果。 时间:35mintues
12 时40 分左右,发出了高压警报,加热炉的两个 火嘴被关闭以降低物料温度。
由于操作流程所规定的流量控制阀不能正常工作, 因此操作人员使用应急泄压阀将气体排到放空罐中,然 后排至大气。13 时左右,操作人员打开阀门将液体从 塔底送往储罐。
第二章 事故经过
13时左右,换热器出现异常,并且导致进入塔的原 料温度突然上升至150℃以上。
第二章 事故经过
2.5 事故细节的补充叙述
2005年3月23日,生产操作工约翰准时来到得克萨斯炼油厂异构化 装置上班。这是他连续工作的第29天。由于每天只能睡5到6个小时, 他的脑子稍微有点发木。自从BP公司施行人力资源管理的低成本战略 后,操作工人数被减少了,因此操作工常常加班,疲倦成为了普遍的 现象。在装置开车的过程中,约翰没有注意到液位的异常。3个小时后 由于液面超标导致分馏塔超压,大量物料进入放空烟囱,与空气混合 后发生了剧烈爆炸。更糟糕的是,装满回料的拖车也违章停在附近, 引起了连环爆炸,约翰和他的14位工友当场丧生,180多人不同程度地 被烧伤。“得克萨斯炼厂爆炸”事件是十年来,美国工业最为严重的 一次事故。
13 时5 分,进入塔中的液体开始膨胀并沸腾,导致 塔内的液位进一步上升;
13 时10 分左右,塔开始出现溢流,液体被排到塔 顶的排放管中;
BP美国德州炼油厂火灾爆炸事故(2005年3月23日)

BP美国德州炼油厂火灾爆炸事故(2005年3月23日)2005年3月23日13点20分左右,英国石油公司(BP)在美国德克萨斯州(Texas)炼油厂的异构化装置发生爆炸事故,15名工人被当场炸死,170余人受伤,直接经济损失超过15亿美元。
这是近20年来,美国发生的最严重的工业事故。
1 事故经过2005年3月23日早上,英国石油公司(BP)美国德克萨斯州(Texas)炼油厂的一套异构化装置(工艺流程见图1)的抽余油塔在经过2周的短暂维修后,重新开车。
开车过程中,操作人员将可燃的液态烃原料不断泵入抽余油塔。
抽余油塔是一个垂直的蒸馏塔,内径3.8m,高51.8m,容积约586100升,塔内有70块塔板,用于将抽余油分离成轻组分和重组分。
在3个多小时的进料过程中,因塔底馏出物管线上的液位控制阀未开,而报警器和控制系统又发出了错误的指令,使操作者对塔内液位过高毫不知情。
液体原料装满抽余油塔后,进入塔顶馏出管线。
塔顶的管线通往距塔顶以下45.1m的安全阀。
管线中充满液体后,压力迅速从144.8kPa上升到441.3kPa,迫使3个安全阀打开了6分钟,将大量可燃液体泄放到放空罐里。
液体很快充满了34.4m高的放空罐,并沿着罐顶的放空管,像喷泉一样洒落到地面上。
泄漏出来的可燃液体蒸发后,形成可燃气体蒸气云。
在距离放空罐7.6m的地方,停着一辆没有熄火的小型敞蓬载货卡车,发动机引擎的火花点燃了可燃蒸气云,引发了大爆炸,导致正在离放空罐7码远处工作的15名承包商雇员死亡。
2 事故原因美国化学安全局(CSB)通过广泛细致的调查,对事故原因从技术和管理两方面进行了分析。
2.1 技术原因1)抽余油塔上的液位控制阀能够将液体从塔内转移到储罐中。
但是,装置开车时,液位控制阀被一名工人关闭,塔里不断加入物料,却没有产品出来。
2)尽管早先已报告该塔的液位计、液位观察孔和压力控制阀出现故障,但装置仍按原计划开车。
3)放空罐设计不合理,排放气没有连接到火炬系统。
2005年BP德克萨斯州炼油厂爆炸事故
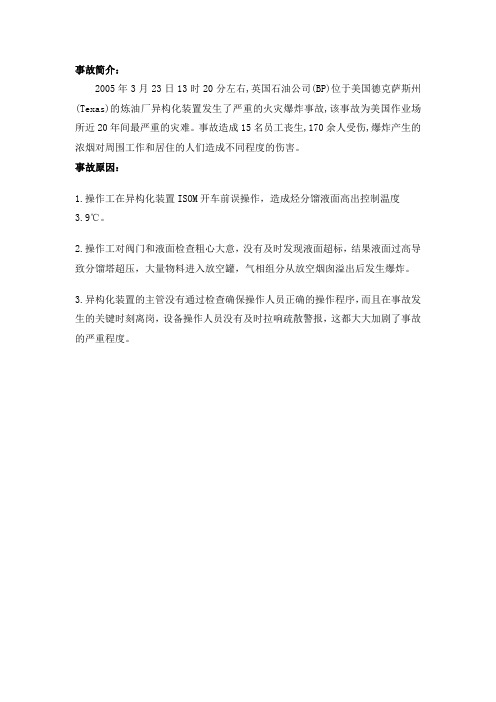
事故简介:
2005年3月23日13时20分左右,英国石油公司(BP)位于美国德克萨斯州(Texas)的炼油厂异构化装置发生了严重的火灾爆炸事故,该事故为美国作业场所近20年间最严重的灾难。
事故造成15名员工丧生,170余人受伤,爆炸产生的浓烟对周围工作和居住的人们造成不同程度的伤害。
事故原因:
1.操作工在异构化装置ISOM开车前误操作,造成烃分馏液面高出控制温度
3.9℃。
2.操作工对阀门和液面检查粗心大意,没有及时发现液面超标,结果液面过高导致分馏塔超压,大量物料进入放空罐,气相组分从放空烟囱溢出后发生爆炸。
3.异构化装置的主管没有通过检查确保操作人员正确的操作程序,而且在事故发生的关键时刻离岗,设备操作人员没有及时拉响疏散警报,这都大大加剧了事故的严重程度。
BP德克萨斯炼油厂爆炸事故案例学习(教学版)分析
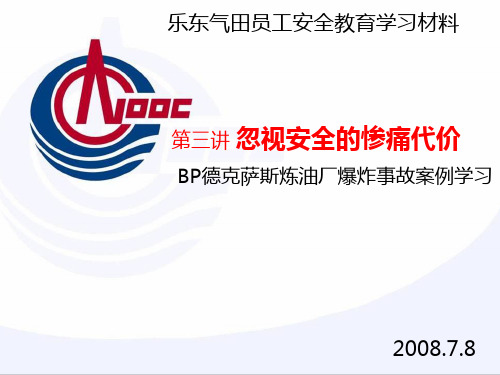
后果:由于削减成本,得克萨斯州炼厂很多设备年久失修, 无法更新;员工雇佣成本和设备更新维护方面的预算被大 量削减。这些削减对生产安全产生了负面影响。
第一章
概述
2005 年3 月23 日13 时20 分左右,英国石油公 司(BP)位于美国德克萨斯州(Texas)的炼油厂 异构化装置发生了严重的火灾爆炸事故,该事故为 美国作业场所近20年间最严重的灾难。事故造成15 名员工丧生,170 余人受伤,爆炸产生的浓烟对周围 工作和居住的人们造成不同程度的伤害。
第一章
概述
1999年之前,得克萨斯城炼油厂属于阿莫科石油公司。在 属于阿莫科石油公司管理期间的1994年,管理层决定减 少得克萨斯炼厂的人数以不断削减人力成本。
第一章
概述
根据当时被各大公司竞相追捧的一个用人原则,减少 18%的员工,就能节省2200万到3300万美元的人力成 本投资。如果减少31%的员工,就能节约4200万到 6100万美元的花销。 1999年,BP收购阿莫科石油公司 在得克萨斯城炼油厂的人员管理和设备投资方面,低 成本的战略得以维持并被BP公司继续维持下去。
第一章
概述
低成本的战略在得克萨斯城炼油厂人员管理方面所产 生的影响:
人手不足 相关机构的研究发现,在过去的四年里,得克萨斯 炼厂的操作工和维护人员加班时间占总工作时间的 27%,有些员工甚至高达68%。这么高的加班比率 远远超出正常水平,这是得克萨斯炼厂员工人数不 足的一种表现。
第一章
概述
BP低成本的战略在设备投资方面的表现: 1999年,BP收购阿莫科后削减了得克萨斯炼厂25%的固定 资产投资,两年后固定资产投资又削减了25%。
2.2 事故过程描述
2005 年3 月23 日凌晨2 时左右,异构化装置的操作人员将 液态烃原料导入分馏塔中。 凌晨3 时30 分,开始进料,当时液位计指示塔内液位在距离 塔底3.0 m 处。 9 时50 分左右,操作员开始将液态原料进行循环,并将更 多的液体打入液位已经过高的塔中,
BP公司得克萨斯州炼油厂火灾爆炸事故原因分析及教训

BP公司得克萨斯州炼油厂火灾爆炸事故原因分析及教训1、BP得州炼油厂火灾爆炸事故概述2005年3月23日中午一点二十分左右,英国石油公司(BP)美国得克萨斯州炼油厂的碳氢化合物车间发生了火灾和一系列爆炸事故,15名工人被当场炸死,170余人受伤,在周围工作和居住的许多人成为爆炸产生的浓烟的受害者,同时,这起事故还导致了严重的经济损失,这是过去20年间美国作业场所最严重的灾难之一(注:BP得克萨斯炼油厂隶属于BP北美产品公司,是BP公司最大的综合性炼油厂,每天可处理46万桶原油,日产1100万加仑汽油)。
爆炸发生后,美国化工安全与危害调查局(CSB)随即于3月26日成立了专门调查小组,并于4月1日正式进驻BP在德州的炼油厂。
CSB于2005年8月17日发布了新闻公报,公布了对BP公司得州炼油厂系列爆炸事故的初步调查结果。
公报认为英国石油公司存在“系统性疏漏”,并呼吁对BP公司旗下5家美国工厂的安全状况进行独立审查。
CSB主席卡罗琳.梅里特表示:“总的来看,调查结果表明英国石油公司在组织决策、安全监督和企业安全文化中存在系统性疏漏,如果不加以改正,这种疏漏可能会导致更多严重事故。
”当天,CSB还对英国石油美国公司、英国石油北美公司和英国石油的全球董事会提出了相关的安全建议,建议要求英国石油更新相关的装置和设备,并可能支持数百名员工就爆炸事故对BP公司提出的诉讼。
CSB要求英国石油在30天内做出答复,并在6至12个月内完成所有工作。
尽管建议让英国石油公司颇为难堪,并将使该公司付出经济上的代价,但是BP首席执行官布朗勋爵仍然表示:“得克萨斯州爆炸时间是英国石油近年来最糟糕的一起悲剧,我们将竭尽所能,确保不再发生此类事件。
美国化工安全与危害调查局的建议是非常受欢迎的,取得了很大的进展,我们将认真对待。
”2005年9月,BP公司因为该爆炸事故被CSB处以2130万美元罚款,BP承认自己对这起事故负责并接受罚款,同时还调拨了7亿美元的专项资金以赔偿受害者并解决针对该公司的指控。
山东化工厂爆炸起火致5人死亡初步原因查明

山东化工厂爆炸起火致5人死亡初步原因查明首先,化工厂生产过程中存在的违规操作是导致爆炸起火的主要原因之一、可能存在工人对设备操作不当,未按照规定的程序进行操作。
在生产过程中,一些有毒有害物质可能未得到适当处理,导致了事故的发生。
其次,化工厂的安全管理不严格也是这起事故的原因之一、化工厂作为危险品生产和储存场所,应该有相应的安全操作规程和应急预案,并对工人进行充分的培训和指导。
然而,事故发生的化工厂可能没有能够提供充分的安全培训,导致工人缺乏必要的应急处理能力,也无法做好事故现场的处置工作。
第三,缺乏有效的安全设施也是这起事故的原因之一、化工厂应该配备防爆设备、高温报警器、喷淋系统等必要的安全设备,以便在事故发生时能够起到及时的报警和控制作用。
然而,事故的化工厂可能在这方面存在不足,导致火灾无法及时控制,甚至发展为爆炸。
此外,由于中国化工行业的发展非常迅速,一些化工企业为了追求经济效益,可能在安全方面投入不足。
特别是一些小型化工厂,由于经济条件限制,安全保障设施和投资不到位,给事故的发生创造了条件。
针对这起事故,应该采取以下措施以防止类似事故再次发生。
首先,相关政府部门应该加强对化工企业的监管,建立更加严格的安全生产制度,确保企业按照规定操作。
其次,化工企业自身应该加强安全管理,加强对员工的安全教育培训,提高员工的安全意识。
同时,化工企业也应该加大对安全设施的投入,确保设备的完好性和有效性。
最后,从长远来看,应该加大对研发和应用安全生产技术的投入,推动化工行业的安全生产技术创新,提升整个行业的安全水平。
总之,山东化工厂爆炸起火事故的初步原因主要包括违规操作、安全管理不严格、缺乏有效的安全设施和企业投入不足等。
为了防止类似事故再次发生,需要政府、企业和整个行业共同努力,加强安全管理和投入,提高安全意识和技术水平。
只有这样,才能最大程度地保护生命财产安全,推动化工行业的可持续发展。
德州化工产业安全生产事故
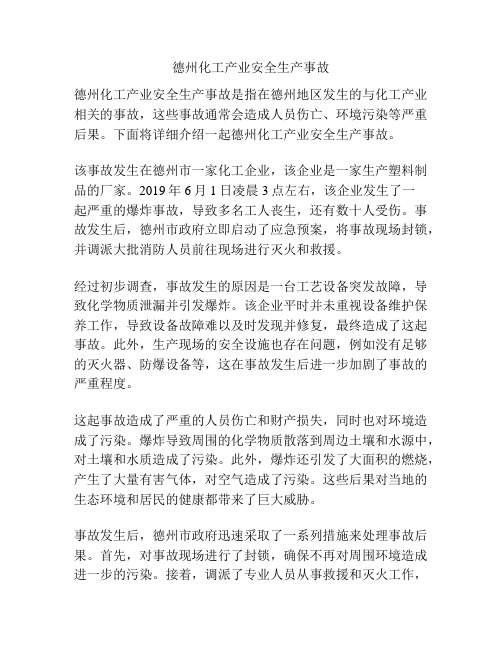
德州化工产业安全生产事故德州化工产业安全生产事故是指在德州地区发生的与化工产业相关的事故,这些事故通常会造成人员伤亡、环境污染等严重后果。
下面将详细介绍一起德州化工产业安全生产事故。
该事故发生在德州市一家化工企业,该企业是一家生产塑料制品的厂家。
2019年6月1日凌晨3点左右,该企业发生了一起严重的爆炸事故,导致多名工人丧生,还有数十人受伤。
事故发生后,德州市政府立即启动了应急预案,将事故现场封锁,并调派大批消防人员前往现场进行灭火和救援。
经过初步调查,事故发生的原因是一台工艺设备突发故障,导致化学物质泄漏并引发爆炸。
该企业平时并未重视设备维护保养工作,导致设备故障难以及时发现并修复,最终造成了这起事故。
此外,生产现场的安全设施也存在问题,例如没有足够的灭火器、防爆设备等,这在事故发生后进一步加剧了事故的严重程度。
这起事故造成了严重的人员伤亡和财产损失,同时也对环境造成了污染。
爆炸导致周围的化学物质散落到周边土壤和水源中,对土壤和水质造成了污染。
此外,爆炸还引发了大面积的燃烧,产生了大量有害气体,对空气造成了污染。
这些后果对当地的生态环境和居民的健康都带来了巨大威胁。
事故发生后,德州市政府迅速采取了一系列措施来处理事故后果。
首先,对事故现场进行了封锁,确保不再对周围环境造成进一步的污染。
接着,调派了专业人员从事救援和灭火工作,尽力减少事故造成的损失。
与此同时,组织专家对土壤、水源和空气进行了监测,及时采取了相应的治理措施。
此外,对事故的责任人进行了严肃的问责,追究了其相应的法律责任。
这起德州化工产业安全生产事故给每个人敲响了警钟,它揭示了化工企业在安全生产方面的薄弱环节。
为了避免类似事故的再次发生,化工企业以及相关部门应该重视安全生产,做好设备维护保养工作,加强员工的安全意识和技能培训,完善应急预案,并定期进行演练。
此外还应加强对外部环境的监测,及时发现和处理安全隐患。
总之,德州化工产业安全生产事故给我们上了一堂生动的安全课,它提醒我们安全生产工作任重道远,化工企业和相关部门要高度重视,加强安全管理,确保化工产业发展能够与人民群众的生命财产安全保持一致,为社会和谐稳定作出贡献。
炼油厂自燃火灾事故原因

炼油厂自燃火灾事故原因概述炼油厂是能源行业中的重要环节,其作用是将原油加工成各种石油产品,如汽油、柴油、润滑油等。
然而,由于炼油过程中涉及许多高温、高压、易燃易爆的化工物质,炼油厂自燃火灾事故是比较普遍的。
自燃火灾事故不仅会造成财产损失,还可能导致严重的人员伤亡和环境污染,因此必须引起高度重视。
本文将分析炼油厂自燃火灾事故的原因,探讨如何通过科学的管理和技术手段预防和控制自燃火灾事故的发生。
一、炼油厂自燃火灾事故的典型案例为了更好地了解炼油厂自燃火灾事故的原因,我们先看一下一些典型的事故案例。
1. 美国德州炼油厂自燃火灾事故2005年3月,美国德州一家炼油厂发生了一起严重的自燃火灾事故,导致15人死亡,数十人受伤。
据调查,事故发生时,炼油厂的一座储油罐发生了自燃,引发了爆炸和大火。
事后调查发现,该储油罐原本对硫化氢等有害气体进行处理,但由于设备老化,未能有效控制有害气体的排放,导致了事故的发生。
2. 俄罗斯炼油厂自燃火灾事故2010年,俄罗斯一家炼油厂发生了一起严重的自燃火灾事故,造成了严重的人员伤亡和环境污染。
据调查,事故发生时,炼油厂的一台精馏塔发生了自燃,引发了大火。
事后调查发现,该精馏塔因长期使用而出现了严重的老化和腐蚀,加上操作人员对设备运行状态的监测不力,导致了事故的发生。
以上两起炼油厂自燃火灾事故,都与设备老化、操作不当等因素有关。
下面我们将详细分析炼油厂自燃火灾事故的原因。
二、炼油厂自燃火灾事故的原因分析1. 设备老化、腐蚀炼油厂里的许多设备都需要长期承受高温、高压、腐蚀和磨损,这使得设备的老化和腐蚀问题十分严重。
一旦设备发生老化、腐蚀,就会导致其失去了原有的安全性能,容易发生自燃火灾事故。
2. 储油罐泄露炼油厂的储油罐是存放原油和石油产品的重要设施,然而由于储油罐的使用年限长和环境因素等原因,储油罐很容易发生泄露,一旦油品泄漏,很容易与空气中的氧气发生化学反应,导致自燃。
3. 作业疏忽炼油厂的作业条件复杂,需要操作人员严格按照操作规程和安全程序进行作业。
山东德州石油化工厂液氯钢瓶爆炸

山东德州石油化工厂液氯钢瓶爆炸(1985年5月9日下午压力容器爆炸)一、事故概况及经过1985年5月9日下午,山东德州石油化工厂,电解车间液氯工段的工人正在进行液氯充装作业,已充装7只0.5吨的液氯钢瓶。
当第7只钢瓶将充装完时,钢瓶突然发生爆炸。
爆炸时产生巨大响声,每瓶被炸成近20块碎块,最大的一块重60kg,飞离现场200多米远。
钢瓶爆炸共造成3人死亡,2人重伤。
二、事故原因分析爆炸的气瓶是德州石油化工厂1984年从天津购入的160只旧气瓶中的一只,化工厂没有按照劳动部颁发的《气瓶安全监察规程》的规定对购进的气瓶作检验,就交给三氯化铝车间。
三氯化铝车间仅检查了钢瓶的外部,更换了瓶阀和易熔合金塞,就将该批气瓶作为合格品报给厂安全科。
厂安全科也没有对这些气瓶进行检查,就将这些气瓶交给销售科,由销售科作为液氯的包装容器投入使用,向社会销售液氯。
在一次充装液氯前,操作工曾发现有几只气瓶曾由瓶内向外流出无色透明的粘稠液体,就向厂安全科作了报告,安全科也向厂部做了报告,但安全科和厂部均未作任何处理,只是让车问将这几只气瓶一起推到液氯充装平台上放置。
于是,这几只内部混有芳香烃(事故后查明无色透明的粘稠液体为芳香烃)的钢瓶被充入液氯。
由于瓶内残存的芳香烃与液氯发生剧烈化学反应,产生高温高压,造成气瓶爆炸。
气瓶内介质混装是这起爆炸事故的直接原因。
三、防止同类事故的措施1.切实加强对液氯钢瓶的管理工作,制定相应的管理制度和安全操作规程。
对液氯钢瓶的使用、充装等人员要进行安全教育,使他们了解和掌握有关安全使用、充装液氯的基本知识并严格按有关要求操作。
2.液氯钢瓶的使用单位必须在液氯钢瓶与用氯设备的联接管线上配置逆止阀、缓冲罐等,以防止设备内物料倒灌钢瓶内。
3.液氯钢瓶充装单位,必须在充装液氯前,由专人对每只液氯钢瓶进行认真检查,确认瓶内没有倒灌除液氯之外的其他介质后方可进行充装。
对有怀疑的钢瓶,必须认真进行清洗,合格后再进行充装。
山东德齐龙化工公司“7.”爆炸事故
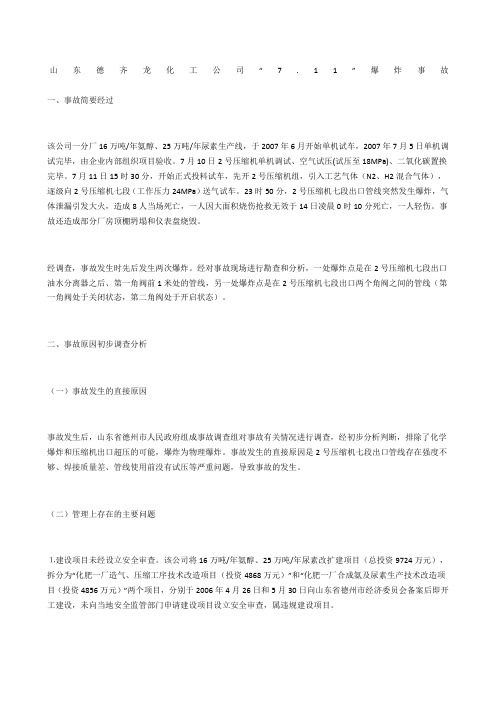
山东德齐龙化工公司“7.11”爆炸事故一、事故简要经过该公司一分厂16万吨/年氨醇、25万吨/年尿素生产线,于2007年6月开始单机试车,2007年7月5日单机调试完毕,由企业内部组织项目验收。
7月10日2号压缩机单机调试、空气试压(试压至18MPa)、二氧化碳置换完毕。
7月11日15时30分,开始正式投料试车,先开2号压缩机组,引入工艺气体(N2、H2混合气体),逐级向2号压缩机七段(工作压力24MPa)送气试车。
23时50分,2号压缩机七段出口管线突然发生爆炸,气体泄漏引发大火,造成8人当场死亡,一人因大面积烧伤抢救无效于14日凌晨0时10分死亡,一人轻伤。
事故还造成部分厂房顶棚坍塌和仪表盘烧毁。
经调查,事故发生时先后发生两次爆炸。
经对事故现场进行勘查和分析,一处爆炸点是在2号压缩机七段出口油水分离器之后、第一角阀前1米处的管线,另一处爆炸点是在2号压缩机七段出口两个角阀之间的管线(第一角阀处于关闭状态,第二角阀处于开启状态)。
二、事故原因初步调查分析(一)事故发生的直接原因事故发生后,山东省德州市人民政府组成事故调查组对事故有关情况进行调查,经初步分析判断,排除了化学爆炸和压缩机出口超压的可能,爆炸为物理爆炸。
事故发生的直接原因是2号压缩机七段出口管线存在强度不够、焊接质量差、管线使用前没有试压等严重问题,导致事故的发生。
(二)管理上存在的主要问题⒈建设项目未经设立安全审查。
该公司将16万吨/年氨醇、25万吨/年尿素改扩建项目(总投资9724万元),拆分为“化肥一厂造气、压缩工序技术改造项目(投资4868万元)”和“化肥一厂合成氨及尿素生产技术改造项目(投资4856万元)”两个项目,分别于2006年4月26日和5月30日向山东省德州市经济委员会备案后即开工建设,未向当地安全监管部门申请建设项目设立安全审查,属违规建设项目。
⒉建设项目工程管理混乱。
该项目无统一设计,仅根据可行性研究报告就组织项目建设,有的单元采取设计、制造、安装整体招标,有的单元采取企业自行设计、市场采购、委托施工方式,有的直接按旧图纸组织施工。
BP美国炼油厂爆炸事故

BP美国德克萨斯(Texas)炼油厂爆炸事故高前进赵建民1、事故简介2005年3月23日下午1点20分,一系列猛烈的爆炸发生在BP美国德克萨斯(Texas)炼油厂的一个正在开工的异构化装置。
爆炸造成15人死亡,180人受伤,在爆炸现场的工艺泄放烟囱旁边当时放置了一些检修用的可移动拖车,这些死伤人员中的大多数当时都是在拖车的里面或外面。
爆炸冲击波摧毁了附近的50个大型化学品储罐,震碎了3/4英里外的居民窗户玻璃,滚滚黑烟从工厂翻腾而出,当局指示约4万4千德克萨斯(Texas)市的居民呆在室内不要外出。
异构化装置被迫停工超过两年,BP公司为此爆炸损失数十亿美元。
图1:事故后的异构化装置的现场3月23日早上,炼油厂的异构化装置的萃取油分馏塔在检修后重新开工进料,操作员用泵连续向分馏塔内送可燃物料超过三个小时,在这三个小时的过程中没有将物料从塔内送出,这和操作开工指导是相矛盾的。
关键的报警和控制仪表显示假值,没能提醒操作员分馏塔内物料的液位已经很高。
结果,在操作员不清楚的的情况下,高170英尺(52米)的分馏塔进料过多,液体进料溢流到了塔顶部的管道中。
分馏塔顶部管道向下走,在约148英尺(45米)高的位置安装有三个安全阀。
当塔顶部的管道充满液体时,塔底部的压力迅速地从21psi升高到64psi,三个安全阀起跳打开持续了6分钟,排放了大量的可燃液体到下游的排放收集罐,这个排放收集罐通过一个泄放烟囱和大气相连通。
排放收集罐和泄放烟囱都相继溢流,大量的可燃液体从113英尺(34米)高的泄放烟囱顶部象喷泉一样地喷涌而出。
排放收集系统是一种陈旧的且不安全的设计,它是在19世纪50年代安装的,这个系统从来也没有和火炬系统相连通,不能安全地收集从工艺装置泄放的液体和可燃易燃的气体。
这些喷涌出的易挥发的液体,流到地面后形成了可燃蒸汽云。
在离排放收集罐约25英尺(7.6m)的地方停了一辆没有熄火发动机空转的皮卡车,扩散的可燃蒸汽随即被点燃,火焰迅速扩散,可燃蒸汽云被点燃,接下来在装置区发生了一系列的爆炸。
BP德克萨斯炼油厂爆炸事故案例学习(学生预习版)
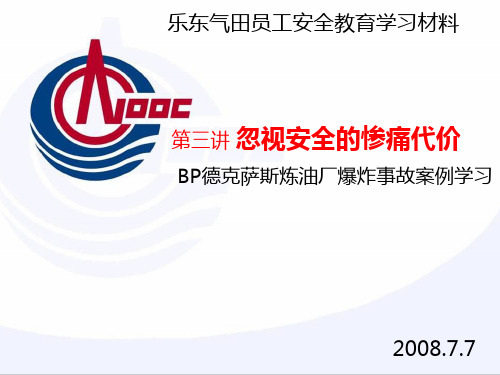
2.2 事故过程描述
2005 年3 月23 日凌晨2 时左右,异构化装置的操作人员将 液态烃原料导入分馏塔中。 凌晨3 时30 分,开始进料,当时液位计指示塔内液位在距离 塔底3.0 m 处。 9 时50 分左右,操作员开始将液态原料进行循环,并将更 多的液体打入液位已经过高的塔中,
第二章
事故经过
事故经过
个人记录区
4.从危险源辨识与风险分析来看
第二章
事故经过
个人记录区
5.你个人认为还需要改进的其他方面?
第三章
事故处理
事故发生后,BP 公司迅速做出反应,BP 首席执行官布 朗勋爵、BP 北美公司总裁罗斯- 费拉里等立即赶往德克萨斯 州,BP 网站也报道了关于事故的最新进展以及公司所采取 的应急措施。BP 公司成立了独立的事故调查小组对事故开 展调查,事故调查小组于2005 年5 月17 日公布了德州炼油 厂爆炸事故的初步调查报告。12 月又提出了最终报告,并通 过BP 公司全球网站向全世界发布。
第二章
事故经过
2.1 事故所处环境
炼油厂异构化装置
2.2 事故环境的工艺设施
1.异构化装置分馏塔 附属设施:来料流量控制阀,液位计,液位高高位报警系统,应急泄压阀BDV,溢流排放 管线,压力安全阀, 2.加热炉 3.换热器 4.放空罐,顶部有烟囱
第二章
2.3 事故背景
事故经过
操作工启动异构化装置
第五章
结束语
像这样一个有着良好安全业绩的世界级的大企业, 通过事故调查仍能发现在企业文化、领导层的个人行 为以及标准的准确度等诸多方面存在的问题。这也应 引起我们的思考,这起事故暴露的问题是不是我们的 企业也存在?
第二章
事故经过
观美国德州炼油厂爆炸事故有感
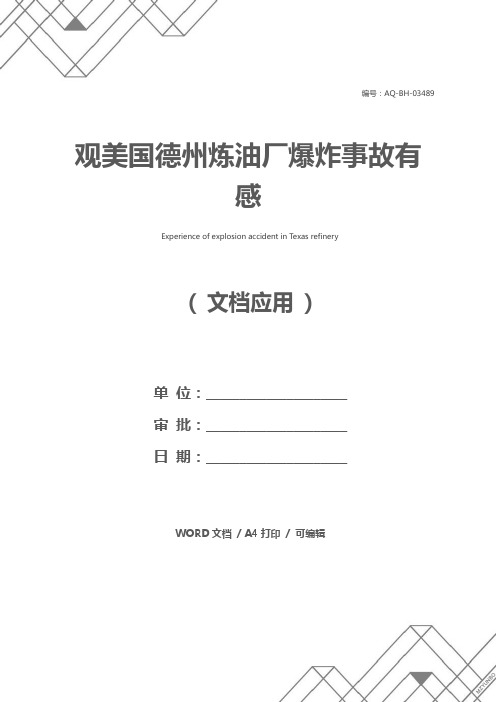
编号:AQ-BH-03489( 文档应用)单位:_____________________审批:_____________________日期:_____________________WORD文档/ A4打印/ 可编辑观美国德州炼油厂爆炸事故有感Experience of explosion accident in Texas refinery观美国德州炼油厂爆炸事故有感备注:每次经过学习之后总想着把自己学习到的经验记录下来,这会在潜移默化中濡染到生活中的其他事情,做事更加具有目的性,做事更加具有连贯性,不再是一股脑去做,步步摸棋。
2014年6月是安全生产月,11日部门进行安全生产事故警示教育活动,组织部门员工及外委运行人员观看美国德州炼油厂爆炸事故视频,并讨论分享观后感。
2005年3月23日13∶20左右,BP(英国石油公司)美国德克萨斯州炼油厂的一套异构化装置的抽余油裂解塔在经过短暂的维修后,重新开车。
启动过程中,操作人员将液态烃原料不断泵入裂解塔,但在3个多小时的加料过程中,没有任何产物馏出,而报警器和控制系统又提供了错误的指令,使操作者对塔内液位过高毫不知情。
液体原料装满裂解塔后,压力迅速上升,迫使塔顶3个安全阀打开,将大量可燃液体泄放并充满放空罐,并沿着罐顶的烟道,像喷泉一样洒落到地面上。
泄漏出来的可燃液体蒸发后,形成可燃气体蒸气云,更不幸的是,在距离放空罐不远的地方,停着一辆没有熄火的载货卡车,发动机引擎的火花点燃了可燃蒸气云,引发了大爆炸。
爆炸事故导致15名工人被当场炸死,170余人受伤,在周围工作和居住的许多人成为爆炸产生的浓烟的受害者。
同时,这起事故还导致了严重的经济损失。
这是过去20年间美国作业场所最严重的灾难之一。
著名的过程安全专家TrevorKletz说,把事故原因简单地归咎于人员误操作,就像不小心跌倒了责怪地心引力一样,无法帮助我们阻止事故再次发生。
为了避免类似事故重演,事故调查组认真分析了事故发生的深层次原因。
山东德齐龙化工集团公司“”爆炸事故
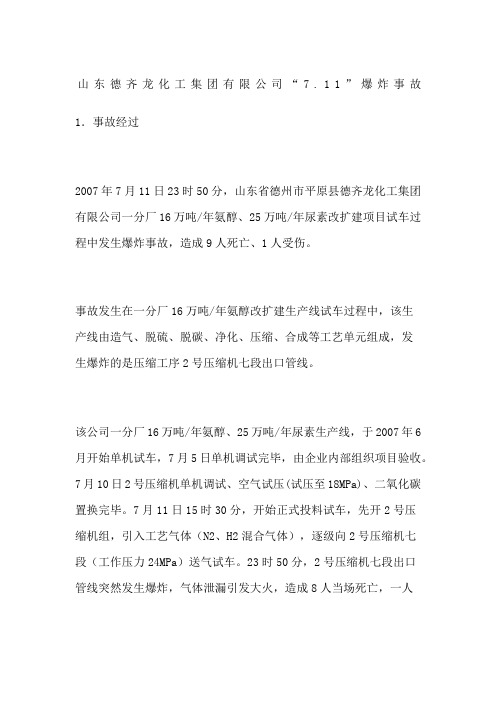
山东德齐龙化工集团有限公司“7.11”爆炸事故1.事故经过2007年7月11日23时50分,山东省德州市平原县德齐龙化工集团有限公司一分厂16万吨/年氨醇、25万吨/年尿素改扩建项目试车过程中发生爆炸事故,造成9人死亡、1人受伤。
事故发生在一分厂16万吨/年氨醇改扩建生产线试车过程中,该生产线由造气、脱硫、脱碳、净化、压缩、合成等工艺单元组成,发生爆炸的是压缩工序2号压缩机七段出口管线。
该公司一分厂16万吨/年氨醇、25万吨/年尿素生产线,于2007年6月开始单机试车,7月5日单机调试完毕,由企业内部组织项目验收。
7月10日2号压缩机单机调试、空气试压(试压至18MPa)、二氧化碳置换完毕。
7月11日15时30分,开始正式投料试车,先开2号压缩机组,引入工艺气体(N2、H2混合气体),逐级向2号压缩机七段(工作压力24MPa)送气试车。
23时50分,2号压缩机七段出口管线突然发生爆炸,气体泄漏引发大火,造成8人当场死亡,一人因大面积烧伤抢救无效于14日凌晨0时10分死亡,一人轻伤。
事故还造成部分厂房顶棚坍塌和仪表盘烧毁。
经调查,事故发生时先后发生两次爆炸。
经对事故现场进行勘查和分析,一处爆炸点是在2号压缩机七段出口油水分离器之后、第一角阀前1米处的管线,另一处爆炸点是在2号压缩机七段出口两个角阀之间的管线(第一角阀处于关闭状态,第二角阀处于开启状态)。
2.事故原因(1)事故发生的直接原因事故发生后,山东省德州市人民政府组成事故调查组对事故有关情况进行调查,经初步分析判断,排除了化学爆炸和压缩机出口超压的可能,爆炸为物理爆炸。
事故发生的直接原因是2号压缩机七段出口管线存在强度不够、焊接质量差、管线使用前没有试压等严重问题,导致事故的发生。
(2)管理上存在的主要问题①建设项目未经设立安全审查。
该公司将16万吨/年氨醇、25万吨/年尿素改扩建项目(总投资9724万元),拆分为“化肥一厂造气、压缩工序技术改造项目(投资4868万元)”和“化肥一厂合成氨及尿素生产技术改造项目(投资4856万元)”两个项目,分别于2006年4月26日和5月30日向山东省德州市经济委员会备案后即开工建设,未向当地安全监管部门申请建设项目设立安全审查,属违规建设项目。
BP美国德州炼油厂火灾事故
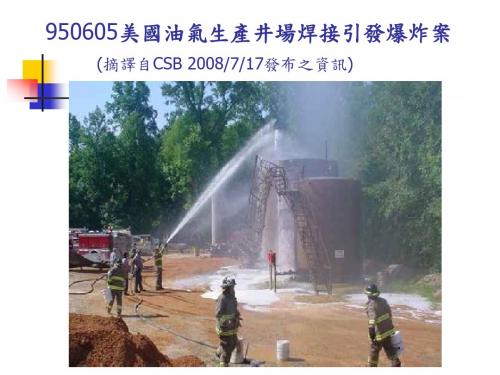
1.焊接前及作業中,未使用氣體偵測儀量測可燃性氣體濃 度。 2.動火作業前未將距離4英尺旁之鄰槽開口管線加帽蓋或 進行盲封隔離等。 3.四座儲槽內部連通,有些槽內仍有可燃性氣體及原油, 卻未先移除與清理,工作環境不安全。 4.將梯子橫置二儲槽作為焊接者的臨時工作平台,並由 維修人員站在槽頂協助穩定橫梯,不符高處作業之安全 程序。
事故原因分析
基本原因: 1.承商缺乏熱作之標準作業程序 承攬商未備製API規範之熱作SOP,以致
-在焊接前未先隔離含有可燃性蒸氣之#2與
#3槽。
-未移除#2號槽之原油。
-未將#3號槽之開口管線加帽蓋致油氣溢散。
-未偵測作業環境油氣濃度等。
事故原因分析
基本原因:
2.承商忽視高處作業之工作安全 未建造儲槽高處焊接之工作平台,僅以梯子橫放 #3及#4槽間以代替工作平台,致需有2名維修人 員在#3槽頂穩固梯子,而被爆炸波及死亡。
Partridge-Raleigh公司及其承攬商應 依API、NFPA提供之指引,並遵循OSHA 的規定執行熱作業,例如建立生產井場 熱作之SOP、工作手冊及製訂工作安全 計畫等,並落實執行。
Байду номын сангаас
3.Partridge-Raleigh及其承商均未建立工作許可 制度以管理動火作業
4.Partridge-Raleigh未建置井場員工之安全計 畫,亦未要求承商施工前應提出安全計畫並執行
改善措施
焊接區應與含可燃性液體(原油)、蒸氣之 儲槽及管線隔離,例如開口管線應設置管 帽或盲封或採取其他隔離措施。
950605美國油氣生產井場焊接引發爆炸案
(摘譯自CSB 2008/7/17發布之資訊)
事故摘要
2006年06月05日,位於美國密西西比州 Raleigh城的Partridge-Raleigh公司之生 產井場,有承攬商進行儲槽新設管線焊接 工作,欲將2個儲槽與第3個儲槽相接。當 天上午8時30分許,焊接火花引燃自鄰槽 未盲封管線溢散出的可燃性蒸氣(相對位 置參見圖示),導致兩個儲槽發生爆炸, 造成承攬商領班及維修人員3人死亡、焊 接工1人重傷的重大事故。
BP德克萨斯州炼油厂火灾爆炸事故资料汇编
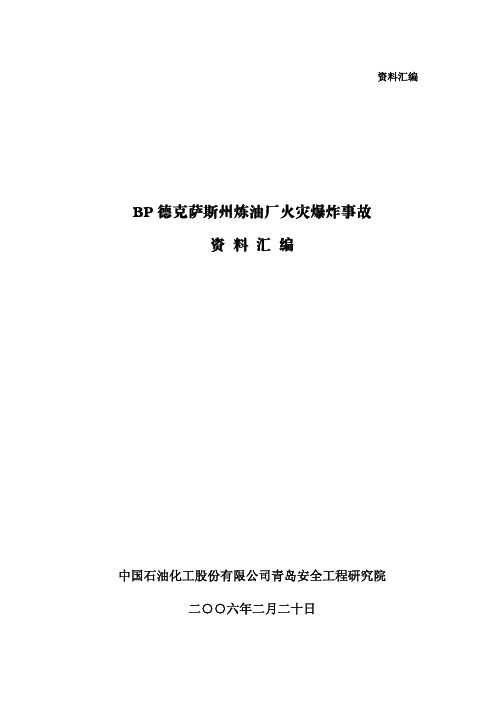
资料汇编BP德克萨斯州炼油厂火灾爆炸事故资 料 汇 编中国石油化工股份有限公司青岛安全工程研究院二○○六年二月二十日目 录1、BP德州炼油厂火灾爆炸事故概述2、BP公司关于爆炸事故的初步调查报告3、美国化工安全与危害调查局(CSB)的初步调查报告1、BP德州炼油厂火灾爆炸事故概述2005年3月23日中午一点二十分左右,英国石油公司(BP)美国德克萨斯州炼油厂的碳氢化合物车间发生了火灾和一系列爆炸事故,15名工人被当场炸死,170余人受伤,在周围工作和居住的许多人成为爆炸产生的浓烟的受害者,同时,这起事故还导致了严重的经济损失,这是过去20年间美国作业场所最严重的灾难之一(注:BP德克萨斯炼油厂隶属于BP北美产品公司,是BP公司最大的综合性炼油厂,每天可处理46万桶原油,日产1100万加仑汽油)。
爆炸发生后,美国化工安全与危害调查局(CSB)随即于3月26日成立了专门调查小组,并于4月1日正式进驻BP在德州的炼油厂。
CSB于2005年8月17日发布了新闻公报,公布了对BP公司德州炼油厂系列爆炸事故的初步调查结果。
公报认为英国石油公司存在“系统性疏漏”,并呼吁对BP公司旗下5家美国工厂的安全状况进行独立审查。
CSB主席卡罗琳·梅里特表示:“总的来看,调查结果表明英国石油公司在组织决策、安全监督和企业安全文化中存在系统性疏漏,如果不加以改正,这种疏漏可能会导致更多严重事故。
”当天,CSB还对英国石油美国公司、英国石油北美公司和英国石油的全球董事会提出了相关的安全建议,建议要求英国石油更新相关的装置和设备,并可能支持数百名员工就爆炸事故对BP公司提出的诉讼。
CSB要求英国石油在30天内做出答复,并在6至12个月内完成所有工作。
尽管建议让英国石油公司颇为难堪,并将使该公司付出经济上的代价,但是BP首席执行官布朗勋爵仍然表示:“得克萨斯州爆炸时间是英国石油近年来最糟糕的一起悲剧,我们将竭尽所能,确保不再发生此类事件。
德州汽运公司石化运销分公司加油站火灾事故案例
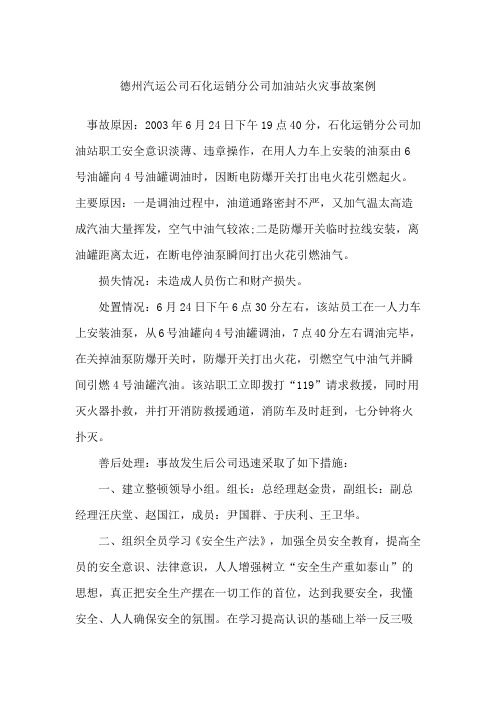
德州汽运公司石化运销分公司加油站火灾事故案例事故原因:2003年6月24日下午19点40分,石化运销分公司加油站职工安全意识淡薄、违章操作,在用人力车上安装的油泵由6号油罐向4号油罐调油时,因断电防爆开关打出电火花引燃起火。
主要原因:一是调油过程中,油道通路密封不严,又加气温太高造成汽油大量挥发,空气中油气较浓;二是防爆开关临时拉线安装,离油罐距离太近,在断电停油泵瞬间打出火花引燃油气。
损失情况:未造成人员伤亡和财产损失。
处置情况:6月24日下午6点30分左右,该站员工在一人力车上安装油泵,从6号油罐向4号油罐调油,7点40分左右调油完毕,在关掉油泵防爆开关时,防爆开关打出火花,引燃空气中油气并瞬间引燃4号油罐汽油。
该站职工立即拨打“119”请求救援,同时用灭火器扑救,并打开消防救援通道,消防车及时赶到,七分钟将火扑灭。
善后处理:事故发生后公司迅速采取了如下措施:一、建立整顿领导小组。
组长:总经理赵金贵,副组长:副总经理汪庆堂、赵国江,成员:尹国群、于庆利、王卫华。
二、组织全员学习《安全生产法》,加强全员安全教育,提高全员的安全意识、法律意识,人人增强树立“安全生产重如泰山”的思想,真正把安全生产摆在一切工作的首位,达到我要安全,我懂安全、人人确保安全的氛围。
在学习提高认识的基础上举一反三吸取教训。
三、加强制度建设,落实好各项规章制度,特别是安全操作规程,在工作中坚决杜绝“三违”现象,严格按照规章制度和安全操作规程办事。
四、严格员工的技术业务培训,经培训考核合格后方能上岗。
五、对站内的电源、电缆线及所有的电器设施进行彻底检查和维护,有专人管理;对站内的所有设备、管线进行一次彻底检查,杜绝一切泄漏现象的发生。
六、卸油、倒油操作时,严格按照规程,必须确保密闭操作,并且各好消防器材,并设专人监护。
七、取消库区内的所有电源开关,彻底清理呼气阀。
八、消防设施迸一步完善加强,配备充足、齐全,摆放整齐。
九、库区安全警示标志要明显,库区内整理清洁完整,严禁停放车辆和存放一切杂物。
- 1、下载文档前请自行甄别文档内容的完整性,平台不提供额外的编辑、内容补充、找答案等附加服务。
- 2、"仅部分预览"的文档,不可在线预览部分如存在完整性等问题,可反馈申请退款(可完整预览的文档不适用该条件!)。
- 3、如文档侵犯您的权益,请联系客服反馈,我们会尽快为您处理(人工客服工作时间:9:00-18:30)。
BP德州炼油厂火灾爆炸事故
1.事故经过简述
2005年3月23日中午一点二十分左右,英国石油公司(BP)美国德克萨斯州炼油厂的碳氢化合物车间发生了火灾和一系列爆炸事故,15名工人被当场炸死,170余人受伤,在周围工作和居住的许多人成为爆炸产生的浓烟的受害者,同时,这起事故还导致了严重的经济损失,这是过去20年间美国作业场所最严重的灾难之一(注:BP德克萨斯炼油厂隶属于BP北美产品公司,是BP公司最大的综合性炼油厂,每天可处理46万桶原油,日产1100万加仑汽油)。
爆炸发生后,美国化工安全与危害调查局(CSB)随即于3月26日成立了专门调查小组,并于4月1日正式进驻BP在德州的炼油厂。
CSB于2005年8月17日发布了新闻公报,公布了对BP公司德州炼油厂系列爆炸事故的初步调查结果。
2.事故原因分析
该爆炸着火事故的直接原因是操作工在异构化装置ISOM开车前误操作,造成烃分馏液面高出控制温度25华氏度。
操作工对阀门和液面检查粗心大意,没有及时发现液面超标,结果液面过高导致分馏塔超压,大量物料进入放空罐,气相组分从放空烟囱溢出后发生爆炸。
异构化装置的主管没有通过检查确保操作人员正确的操作程序,而且在事故发生的关键时刻离岗,设备操作人员没有及时拉响疏散警报,这都大大加剧了事故的严重程度。
总之,异构化装置主管的失职和值班工人没有遵循书面程序的规定是事故发生的根本原因。
德克萨斯城炼油厂的爆炸,还具有五个主要的间接原因:首先,历经多年的工作环境已被侵蚀到排斥变化的地步,而且缺乏信任、动力和目标。
监督和管理行为不清晰。
对条例的执行不彻底。
员工个人感觉没有提建议和进行改进的权力。
第二,管理者没有建立或强制实行流程安全、操作执行程序、系统的降低风险优先权等。
没有从BP其他事故中吸取教训。
第三,复杂组织内的众多变化,包括组织结构和人员的调整,导致了责任不明和沟通不畅。
结果造成员工对角色、职责和优先顺序迷惑不清。
第四,要归咎于对危险辨识不足,对站点流程安全的理解知之甚少——这些导致了人们承受了更大的风险。
最后,低水平的操作管理和炼油厂内由上至下缺乏沟通,意味着对于问题没有及时的早期警报系统。
而且缺乏独立的渠道,无法通过组织彻底的核查来了解这个工厂的水准下滑。
3.事故预防措施
(1)组建了一个新的管理团队进入德克萨斯城炼油厂,精简机构,促进沟通。
明晰岗位角色和职责,并采取措施验证了遵守操作规程。
(2)创建了项目组,以协调并跟踪最终事故调查报告中的建议以及BP公司与OSHA协商相关措施的执行。
(3)在公司层面建立新的安全运行机构,这个机构的主要职能之一就是促进交流与协作,共享相关经验教训。
(4)强化了独立的检查程序,当前的重点是确定系统与程序都被安排在适当的位置,并有效地工作。
我们已建立新的标准,以促进更严格、更有连续性地掌握BP集团的工作和完整性管理。
(5)在未来的5年投入10亿美元,对德克萨斯城炼油厂进行升级维修。
此外,我们将在关键装置上安装先进的过程控制系统,取消在轻度维修中使用放空烟囱,同时加强员工培训,说实话,这方面是有所欠缺的。
(6)推行了新的工程技术实务规范,以管理炼厂和其他加工厂内临时建筑物的使用。