甲醇乙醇的精馏
甲醇乙醇的精馏
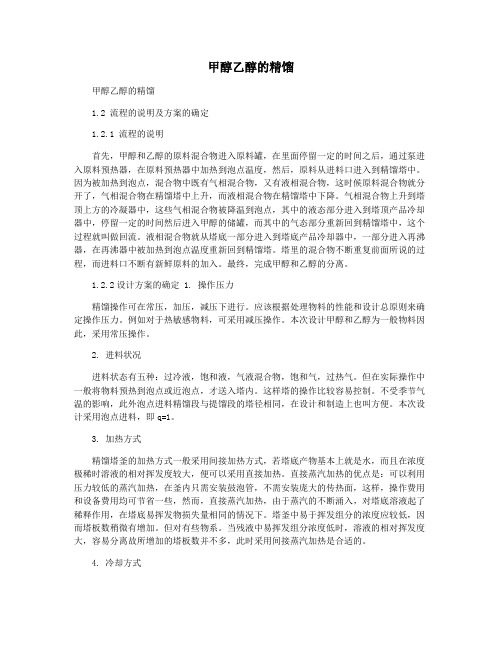
甲醇乙醇的精馏甲醇乙醇的精馏1.2 流程的说明及方案的确定1.2.1 流程的说明首先,甲醇和乙醇的原料混合物进入原料罐,在里面停留一定的时间之后,通过泵进入原料预热器,在原料预热器中加热到泡点温度,然后,原料从进料口进入到精馏塔中。
因为被加热到泡点,混合物中既有气相混合物,又有液相混合物,这时候原料混合物就分开了,气相混合物在精馏塔中上升,而液相混合物在精馏塔中下降。
气相混合物上升到塔顶上方的冷凝器中,这些气相混合物被降温到泡点,其中的液态部分进入到塔顶产品冷却器中,停留一定的时间然后进入甲醇的储罐,而其中的气态部分重新回到精馏塔中,这个过程就叫做回流。
液相混合物就从塔底一部分进入到塔底产品冷却器中,一部分进入再沸器,在再沸器中被加热到泡点温度重新回到精馏塔。
塔里的混合物不断重复前面所说的过程,而进料口不断有新鲜原料的加入。
最终,完成甲醇和乙醇的分离。
1.2.2设计方案的确定 1. 操作压力精馏操作可在常压,加压,减压下进行。
应该根据处理物料的性能和设计总原则来确定操作压力。
例如对于热敏感物料,可采用减压操作。
本次设计甲醇和乙醇为一般物料因此,采用常压操作。
2. 进料状况进料状态有五种:过冷液,饱和液,气液混合物,饱和气,过热气。
但在实际操作中一般将物料预热到泡点或近泡点,才送入塔内。
这样塔的操作比较容易控制。
不受季节气温的影响,此外泡点进料精馏段与提馏段的塔径相同,在设计和制造上也叫方便。
本次设计采用泡点进料,即q=1。
3. 加热方式精馏塔釜的加热方式一般采用间接加热方式,若塔底产物基本上就是水,而且在浓度极稀时溶液的相对挥发度较大,便可以采用直接加热。
直接蒸汽加热的优点是:可以利用压力较低的蒸汽加热,在釜内只需安装鼓泡管,不需安装庞大的传热面,这样,操作费用和设备费用均可节省一些,然而,直接蒸汽加热,由于蒸汽的不断涌入,对塔底溶液起了稀释作用,在塔底易挥发物损失量相同的情况下。
塔釜中易于挥发组分的浓度应较低,因而塔板数稍微有增加。
甲醇精馏技术
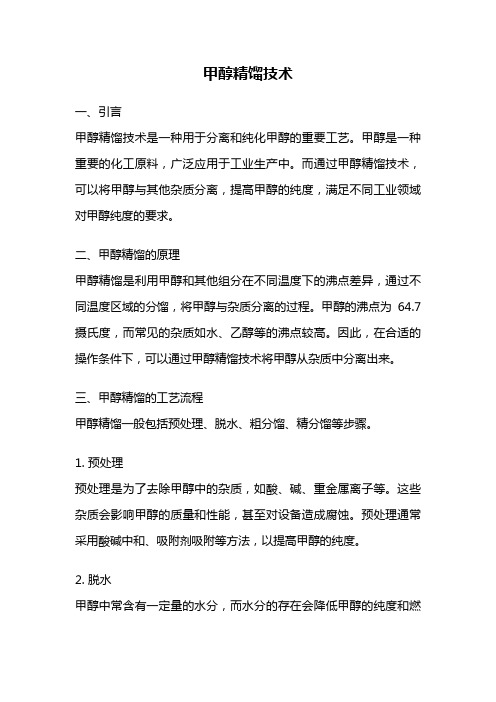
甲醇精馏技术一、引言甲醇精馏技术是一种用于分离和纯化甲醇的重要工艺。
甲醇是一种重要的化工原料,广泛应用于工业生产中。
而通过甲醇精馏技术,可以将甲醇与其他杂质分离,提高甲醇的纯度,满足不同工业领域对甲醇纯度的要求。
二、甲醇精馏的原理甲醇精馏是利用甲醇和其他组分在不同温度下的沸点差异,通过不同温度区域的分馏,将甲醇与杂质分离的过程。
甲醇的沸点为64.7摄氏度,而常见的杂质如水、乙醇等的沸点较高。
因此,在合适的操作条件下,可以通过甲醇精馏技术将甲醇从杂质中分离出来。
三、甲醇精馏的工艺流程甲醇精馏一般包括预处理、脱水、粗分馏、精分馏等步骤。
1. 预处理预处理是为了去除甲醇中的杂质,如酸、碱、重金属离子等。
这些杂质会影响甲醇的质量和性能,甚至对设备造成腐蚀。
预处理通常采用酸碱中和、吸附剂吸附等方法,以提高甲醇的纯度。
2. 脱水甲醇中常含有一定量的水分,而水分的存在会降低甲醇的纯度和燃烧性能。
因此,在甲醇精馏过程中,需要进行脱水处理。
常用的脱水方法有吸附剂吸附、分子筛吸附、低温凝结等。
3. 粗分馏粗分馏是将预处理和脱水后的甲醇进行初步分离。
在粗分馏过程中,通过控制温度和压力,使甲醇和水、乙醇等杂质分别沸腾,然后通过塔板或填料层的作用,将甲醇从上部分离出来,而杂质则从下部排出。
4. 精分馏精分馏是在粗分馏的基础上,进一步提高甲醇的纯度。
精分馏一般采用多级精馏塔进行,通过不同温度区域的分馏,将甲醇与其他杂质进一步分离。
在精分馏过程中,需要根据甲醇和杂质的沸点差异和塔内的温度梯度,精确控制操作条件,以获得所需的甲醇纯度。
四、甲醇精馏的应用甲醇精馏技术广泛应用于化工、医药、食品、能源等领域。
在化工领域,甲醇是制造甲醛、甲酸、乙酸等化工产品的重要原料;在医药领域,甲醇可以用于合成药物原料;在食品领域,甲醇可以用于制造食品添加剂等;在能源领域,甲醇可以作为燃料和替代剂使用。
五、甲醇精馏技术的发展随着化工工艺的不断发展和改进,甲醇精馏技术也在不断进步。
甲醇精馏工艺流程图

甲醇精馏工艺流程图甲醇精馏工艺流程图甲醇精馏是一种常见的用于分离甲醇的工艺。
下面是一种甲醇精馏工艺的流程图简化示意:甲醇粗产品经过预处理后,进入一号蒸馏塔。
在一号蒸馏塔中,甲醇与其他杂质根据沸点的差异进行分离。
在蒸馏过程中,高沸点组分逐渐富集在塔底,而低沸点组分则逐渐富集在塔顶。
经过冷凝后,低沸点组分成为甲醇乙醇混合物,高沸点组分成为甲醇残留液。
甲醇乙醇混合物进入乙醇精馏塔,经过二次精馏可以得到高纯度的甲醇产品。
整个甲醇精馏工艺包括以下主要步骤:1. 前处理:甲醇粗产品经过脱水和醇醚化处理以去除水分和其他杂质。
2. 一号蒸馏塔:粗产品进入一号蒸馏塔,通过加热使其部分汽化。
在塔内,高沸点组分逐渐富集在塔底,低沸点组分富集在塔顶。
塔底产物是甲醇残留液,经过冷凝后回流到塔顶进行再蒸馏。
塔顶产物是甲醇乙醇混合物。
3. 乙醇精馏塔:甲醇乙醇混合物进入乙醇精馏塔进行二次精馏。
在塔内,乙醇和甲醇根据沸点的差异进行分离。
低沸点的乙醇逐渐富集在塔顶,高沸点的甲醇富集在塔底。
塔底产物是甲醇产品,经过冷凝后得到高纯度的甲醇。
4. 产物处理:甲醇产品经过冷却、储存、包装等步骤后可以出厂销售或用于下游生产。
整个甲醇精馏工艺需要考虑的主要因素有塔内温度、压力、进料速率、回收率等。
通过优化这些因素,可以提高甲醇产品的纯度和产率,同时减少能耗和废物排放。
此外,也需要注意控制工艺中的安全风险,保证操作人员和设备的安全。
以上是一种甲醇精馏工艺的简化流程图示意,实际工业生产中可能还有其他步骤和设备。
具体的工艺流程应根据具体情况进行设计和调整。
甲醇精馏工艺流程

经济日报/2003年/02月/26日/格力空调专一化经营的魅力何在?0(3)专一化战略的坚定性和多元化的诱惑王汝林实施专一化的经营战略需要一种战略上的坚定性。
如果说格力在经营上取得了骄人的成绩,首先是格力在发展战略上取得了成绩。
这种成绩突出的表现在他们对专一化战略认识上的深刻,贯彻中的坚定和实践中的准确把握。
因为专一化和多元化之间并没有隔着一道万里长城,所以在实施专一化的过程中,时时面对着多元化的诱惑,很容易走向多元化。
特别是实施专一化经营的企业,一旦企业获得了发展,就会面对新的市场机会和利润诱惑,很容易逐渐背离它所选择的专一化战略,轻易地陷入多元化的误区里。
这主要有三种情况:有很多人对专一化的理解,从战略上是清晰的,但在战术上却是混乱的,以至在具体实践中往往又陷入了多元化的泥坑。
这种说起来清楚,做起来糊涂的问题是非常致命的。
尽管很多创业企业已经认识到,搞大而全的多元化经营是困难的,但到了实践中,就又回到了多元化的思维里。
伸着巴掌到处乱抓,总以为会/东方不亮西方亮0,其结果是,/东方没亮,西方也黑0,这样的教训是很多的。
直到1993年12月,乔治#弗雪就任柯达公司的总裁,采取了四项措施/反璞归真0,出售了三大副业公司,甩掉了经营包袱,重新回到了专一化经营上来。
通过专心研究同一产品的深度开发和衍生开发,才使柯达公司走出了多元化的怪圈,重振了雄风。
在实施专一化战略中另一个十分容易出现的问题是:专一化后形成经营大目标的专一,但市场或产品细分以后往往造成抓不住重点的情况。
多数企业会形成一种专一化后的力量分散和资源分散。
这种在专一化经营中抓不住重点的情况,其实是偏离了专一化战略。
专一化战略是重点战略,战略思想和战术设计都应该抓住重点。
有重点才能有分量,有分量,才能有特色。
有特色才能有人气,才能有商机。
这一点在国内市场开拓中显示出来,在国际市场开拓中同样显示出来。
走国际化道路要按国际牌理出牌,使格力在进军国际市场征程中找到了重点。
化工原理课程设计分离甲醇—乙醇混合液及浮阀精馏塔
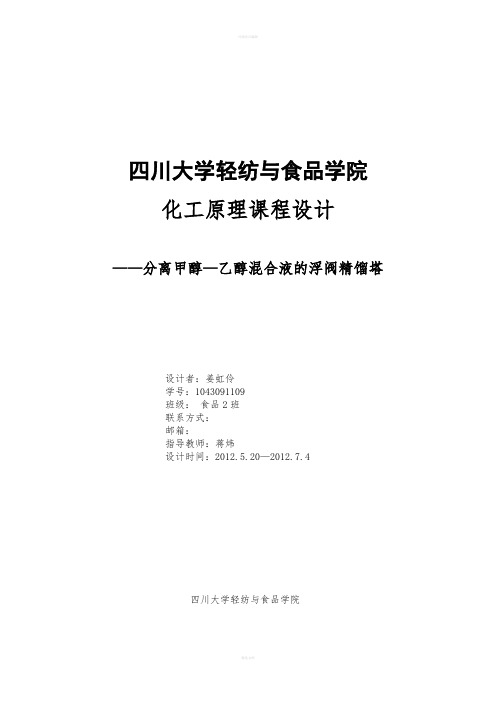
四川大学轻纺与食品学院化工原理课程设计——分离甲醇—乙醇混合液的浮阀精馏塔设计者:姜虹伶学号:1043091109班级:食品2班联系方式:邮箱:指导教师:蒋炜设计时间:2012.5.20—2012.7.4四川大学轻纺与食品学院目录一、设计任务.............................................................................................................................. - 4 -二、背景介绍.............................................................................................................................. - 4 -1 . 精馏原理........................................................................................................................ - 4 -2 . 板式塔作用原理............................................................................................................ - 4 -3 . 浮阀塔............................................................................................................................ - 5 -三、设计流程图.......................................................................................................................... - 5 -四、浮阀塔的设计...................................................................................................................... - 7 -1 . 全塔物料衡算................................................................................................................ - 7 -(1)原料液、馏出液及残液的摩尔分数和均摩尔质量的计算 ............................ - 7 -(2) 原料液、馏出液及残液的摩尔流率计算......................................................... - 8 -2 . 加料热状态参数q值的确定........................................................................................ - 8 -(1)进料液、馏出液、残液的温度确定................................................................ - 8 -(2)q值的计算......................................................................................................... - 9 -(3)q线方程式....................................................................................................... - 10 -3 . 最小回流比的计算...................................................................................................... - 10 -(1)相对挥发度的计算.......................................................................................... - 10 -(2)平衡方程式...................................................................................................... - 11 -(3)最小回流比的计算.......................................................................................... - 11 -(4)实际回流比的计算.......................................................................................... - 11 -4 . 精馏段和提馏段的气、液流量.................................................................................. - 12 -(1) 精馏段内气、液流量 ....................................................................................... - 12 -(2)提馏段内气、液流量...................................................................................... - 13 -5 . 塔板数的计算.............................................................................................................. - 13 -(1)逐板计算法...................................................................................................... - 13 -(2)塔效率.............................................................................................................. - 15 -(3)实际塔板数的计算.......................................................................................... - 16 -6 . 塔径的计算.................................................................................................................. - 16 -(1) 精馏段塔径的计算 ........................................................................................... - 16 -(2)提馏段塔径的计算.......................................................................................... - 20 -(3)塔径的实际值.................................................................................................. - 23 -7. 塔高的确定................................................................................................................. - 23 -五、精馏段塔板结构设计及力学校核 - 24 -1.溢流装置......................................................................................................................... - 24 -(1) 降液管的宽度和截面面积的确定................................................................... - 24 -(2) 出口溢流堰与进口溢流堰的确定................................................................... - 24 -(3) 降液管底隙高度与受液盘的确定................................................................... - 25 -2.板面布置及主要尺寸..................................................................................................... - 25 -(1) 板面布置 .......................................................................................................... - 25 -(2) 浮阀的数目与排列 .......................................................................................... - 26 -3.浮阀塔板的流体力学校核............................................................................................. - 29 -(1) 塔板压降的校核 .............................................................................................. - 29 -(2) 液沫夹带的校核 .............................................................................................. - 29 -(3) 溢流液泛的校核 .............................................................................................. - 30 -(4) 负荷性能图及操作弹性 .................................................................................. - 30 -六、提馏段塔板结构设计及力学校核.................................................................................... - 34 -1 . 溢流装置...................................................................................................................... - 34 -(1) 降液管的宽度和截面面积的确定................................................................... - 34 -(2) 出口溢流堰与进口溢流堰的确定................................................................... - 34 -(3) 降液管底隙高度与受液盘的确定................................................................... - 35 -2 . 板面布置及主要尺寸.................................................................................................. - 35 -(1) 塔板布置 .......................................................................................................... - 35 -(2) 浮阀的数目与排列 ............................................................................................ - 36 -(3) 校核: .............................................................................................................. - 38 -(4) 校核塔板开孔率 .............................................................................................. - 38 -3 . 浮阀塔板的流体力学校核.......................................................................................... - 39 -(1) 塔板压降的校核 .............................................................................................. - 39 -(2) 液沫夹带的校核 .............................................................................................. - 40 -(3) 溢流液泛的校核 .............................................................................................. - 40 -(4) 负荷性能图及操作弹性 .................................................................................. - 41 -七、塔顶冷凝器的选用............................................................................................................ - 44 -1.物料衡算......................................................................................................................... - 44 -2.换热器选用..................................................................................................................... - 45 -3.验算压降......................................................................................................................... - 46 -(1)验算管程压降.................................................................................................. - 46 -(2) 验算管程压降 .................................................................................................. - 46 -4. 核算总传热系数........................................................................................................... - 47 -(1) 管程给热系数 .................................................................................................. - 48 -(2) 壳程给热系数 .................................................................................................. - 48 -(3) 导热系数和传热面积 ...................................................................................... - 48 -八、塔接管设计........................................................................................................................ - 49 -1.塔顶出料管直径............................................................................................................. - 49 -2.回流管直径..................................................................................................................... - 49 -3.进料管直径..................................................................................................................... - 50 -4.馏出液管直径................................................................................................................. - 50 -九、设计总结............................................................................................................................ - 51 -十、参考文献............................................................................................................................ - 51 -一、设计任务设计题目:分离甲醇—乙醇混合液的浮阀精馏塔原料液:组成甲醇0.6 乙醇0.4处理量:8800温度:28℃馏出液:组成苯0.96残液:组成苯0.02(均为摩尔分率)操作压力:常压连续操作二、背景介绍1 . 精馏原理精馏过程的基础依然是混合液组分间挥发度的差异,而塔内的气、液“回流”则是沿塔高不断进行气、液传质实现精馏的必要条件。
甲醇精馏毕业设计
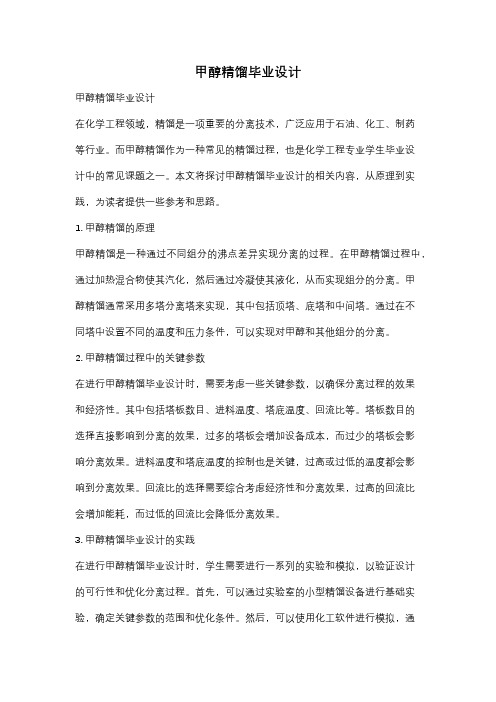
甲醇精馏毕业设计甲醇精馏毕业设计在化学工程领域,精馏是一项重要的分离技术,广泛应用于石油、化工、制药等行业。
而甲醇精馏作为一种常见的精馏过程,也是化学工程专业学生毕业设计中的常见课题之一。
本文将探讨甲醇精馏毕业设计的相关内容,从原理到实践,为读者提供一些参考和思路。
1. 甲醇精馏的原理甲醇精馏是一种通过不同组分的沸点差异实现分离的过程。
在甲醇精馏过程中,通过加热混合物使其汽化,然后通过冷凝使其液化,从而实现组分的分离。
甲醇精馏通常采用多塔分离塔来实现,其中包括顶塔、底塔和中间塔。
通过在不同塔中设置不同的温度和压力条件,可以实现对甲醇和其他组分的分离。
2. 甲醇精馏过程中的关键参数在进行甲醇精馏毕业设计时,需要考虑一些关键参数,以确保分离过程的效果和经济性。
其中包括塔板数目、进料温度、塔底温度、回流比等。
塔板数目的选择直接影响到分离的效果,过多的塔板会增加设备成本,而过少的塔板会影响分离效果。
进料温度和塔底温度的控制也是关键,过高或过低的温度都会影响到分离效果。
回流比的选择需要综合考虑经济性和分离效果,过高的回流比会增加能耗,而过低的回流比会降低分离效果。
3. 甲醇精馏毕业设计的实践在进行甲醇精馏毕业设计时,学生需要进行一系列的实验和模拟,以验证设计的可行性和优化分离过程。
首先,可以通过实验室的小型精馏设备进行基础实验,确定关键参数的范围和优化条件。
然后,可以使用化工软件进行模拟,通过调整参数和优化设计,得到更加合理的分离方案。
最后,可以进行中试实验,验证设计的可行性和稳定性。
4. 甲醇精馏的应用甲醇精馏在工业生产中有广泛的应用。
甲醇作为一种重要的化工原料,广泛用于合成甲醛、甲乙醇、甲苯等化工产品。
通过甲醇精馏,可以实现对甲醇和其他组分的高效分离,提高产品纯度和质量。
甲醇精馏还可以用于废水处理、石油提炼等领域,具有重要的经济和环保意义。
5. 甲醇精馏毕业设计的挑战和展望甲醇精馏毕业设计虽然是一个常见的课题,但也面临一些挑战。
甲醇精馏五塔精馏流程描述

甲醇精馏五塔精馏流程描述下载温馨提示:该文档是我店铺精心编制而成,希望大家下载以后,能够帮助大家解决实际的问题。
文档下载后可定制随意修改,请根据实际需要进行相应的调整和使用,谢谢!并且,本店铺为大家提供各种各样类型的实用资料,如教育随笔、日记赏析、句子摘抄、古诗大全、经典美文、话题作文、工作总结、词语解析、文案摘录、其他资料等等,如想了解不同资料格式和写法,敬请关注!Download tips: This document is carefully compiled by theeditor. I hope that after you download them,they can help yousolve practical problems. The document can be customized andmodified after downloading,please adjust and use it according toactual needs, thank you!In addition, our shop provides you with various types ofpractical materials,such as educational essays, diaryappreciation,sentence excerpts,ancient poems,classic articles,topic composition,work summary,word parsing,copy excerpts,other materials and so on,want to know different data formats andwriting methods,please pay attention!甲醇精馏五塔精馏流程是一种常用的甲醇提纯工艺,主要包括以下五个步骤:1. 预精馏塔:原料甲醇首先进入预精馏塔,在塔内与上升的蒸汽进行逆流接触。
粗甲醇精制工艺—甲醇精制双塔精馏工艺
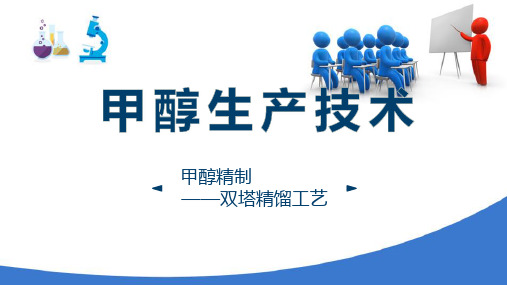
甲醇精制——双塔精馏工艺
✓ 在粗甲醇储槽的出口管上,加入含量为8%~10%NaOH溶液,使粗甲醇呈弱 碱性(PH=8-9),其目的是为了促进胺类及羰基化合物的分解,防止粗甲 醇中有机酸对设备的腐蚀。
✓ 加碱后的粗甲醇,经过热交换器用热水加热到60~70℃后进入预精馏塔。为 了便于脱除粗甲醇中杂质,又考虑到甲醇溶于水,根据萃取原理,在预精馏 塔上部或者进塔回流管上加入一种萃取剂,采用较多的是以蒸汽冷凝水作为 萃取剂,其一般加入量为粗甲醇进料量的20%。
甲醇精制——双塔精馏工艺
✓ 为了提高预精馏后甲醇的稳定性及精制二甲醚,可在预精馏塔塔顶采用二级 或多级冷凝。
✓ 第一级冷凝温度比较高,较轻组分在此难以冷凝,从而减少了返回塔内的轻 组分,也提高了预精馏后甲醇的稳定性。
✓ 第二级冷凝温度为常温,常温下甲醇也可以被冷凝下来,尽可能回收甲醇, 而二甲醚等的轻组分冷凝温度很低,仍以气相形式存在;第三级要以冷冻剂 冷至更低的温度,这样不但可以净化了二甲醚,同时又进一步回收了甲醇。
甲醇精制 ——双塔精馏工艺
甲醇精制——双塔精馏工艺
粗甲醇双塔精馏流程。第一塔为预精馏塔,第Байду номын сангаас塔为主精馏塔, 两塔再沸器热源均为低压蒸汽。
预精馏塔 • 作用:脱除二甲醚;加水萃取,脱除与甲醇沸点 相近
甲醇精馏系统的简介及优化
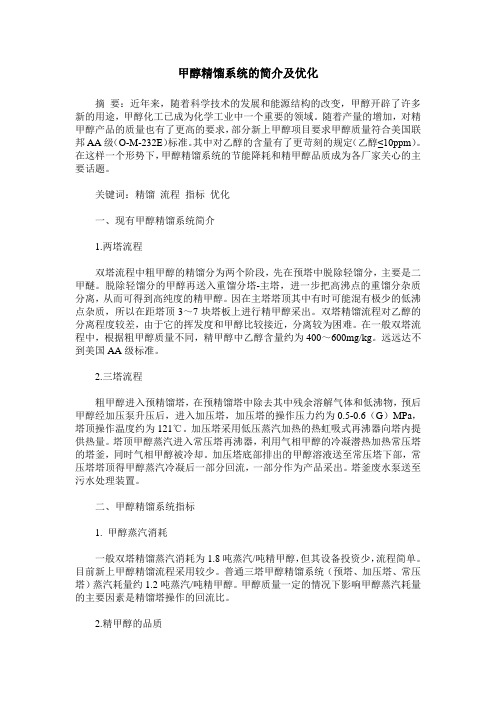
甲醇精馏系统的简介及优化摘要:近年来,随着科学技术的发展和能源结构的改变,甲醇开辟了许多新的用途,甲醇化工已成为化学工业中一个重要的领域。
随着产量的增加,对精甲醇产品的质量也有了更高的要求,部分新上甲醇项目要求甲醇质量符合美国联邦AA级(O-M-232E)标准。
其中对乙醇的含量有了更苛刻的规定(乙醇≤10ppm)。
在这样一个形势下,甲醇精馏系统的节能降耗和精甲醇品质成为各厂家关心的主要话题。
关键词:精馏流程指标优化一、现有甲醇精馏系统简介1.两塔流程双塔流程中粗甲醇的精馏分为两个阶段,先在预塔中脱除轻馏分,主要是二甲醚。
脱除轻馏分的甲醇再送入重馏分塔-主塔,进一步把高沸点的重馏分杂质分离,从而可得到高纯度的精甲醇。
因在主塔塔顶其中有时可能混有极少的低沸点杂质,所以在距塔顶3~7块塔板上进行精甲醇采出。
双塔精馏流程对乙醇的分离程度较差,由于它的挥发度和甲醇比较接近,分离较为困难。
在一般双塔流程中,根据粗甲醇质量不同,精甲醇中乙醇含量约为400~600mg/kg。
远远达不到美国AA级标准。
2.三塔流程粗甲醇进入预精馏塔,在预精馏塔中除去其中残余溶解气体和低沸物,预后甲醇经加压泵升压后,进入加压塔,加压塔的操作压力约为0.5-0.6(G)MPa,塔顶操作温度约为121℃。
加压塔采用低压蒸汽加热的热虹吸式再沸器向塔内提供热量。
塔顶甲醇蒸汽进入常压塔再沸器,利用气相甲醇的冷凝潜热加热常压塔的塔釜,同时气相甲醇被冷却。
加压塔底部排出的甲醇溶液送至常压塔下部,常压塔塔顶得甲醇蒸汽冷凝后一部分回流,一部分作为产品采出。
塔釜废水泵送至污水处理装置。
二、甲醇精馏系统指标1. 甲醇蒸汽消耗一般双塔精馏蒸汽消耗为1.8吨蒸汽/吨精甲醇,但其设备投资少,流程简单。
目前新上甲醇精馏流程采用较少。
普通三塔甲醇精馏系统(预塔、加压塔、常压塔)蒸汽耗量约1.2吨蒸汽/吨精甲醇。
甲醇质量一定的情况下影响甲醇蒸汽耗量的主要因素是精馏塔操作的回流比。
甲醇精馏的方法

甲醇精馏的方法文件排版存档编号:[UYTR-OUPT28-KBNTL98-UYNN208]甲醇精馏的典型工艺流程甲醇精馏产生工艺有多种,分为单塔精馏,双塔精馏,三塔精馏与四塔精馏(即三塔加回收塔)(1) 单塔流程描述采用铜系催化剂低压法合成甲醇,由于粗甲醇中不仅还原性杂质的含量大大减少,而且二甲醚的含量几十倍地降低,因此在取消化学净化的同时,可将预精馏及甲醇-水-重组分的分离在一台主精馏塔内同时进行,即单塔流程,就能获得一般工业上所需要的精甲醇。
单塔流程更适用于合成甲基燃料的分离,很容易获得燃料级甲醇。
单塔流程(见图为粗甲醇产品经过一个塔就可以采出产品。
粗甲醇塔中部加料口送入,轻组分由塔顶排出,高沸点的重组分在进料板以下若塔板处引出,水从塔底排出,产品甲醇在塔顶以下若干块塔板引出。
(2) 双塔流程描述双塔工艺是由脱醚塔,甲醇精馏塔或者主塔组成。
主塔在工厂中产量在100万吨/年以下,仅仅能提供简单的过程,所以设备和投资较低。
传统的工艺流程,是最早用于30MPa压力下以锌铬催化剂合成粗甲醇的精制。
主要步骤有:中和、脱醚、预精馏脱轻组分杂质、氧化净化、主精馏脱水和重组分,最终得到精甲醇产品。
在传统工艺流程上,取消脱醚塔和高锰酸钾的化学净化,只剩下双塔精馏(预精馏塔和主精馏塔)。
其高压法锌铬催化剂合成甲醇和中、低压法铜系催化剂合成甲醇都可适用。
从合成工序来的粗甲醇入预精馏塔,此塔为常压操作。
为了提高预精馏塔后甲醇的稳定性,并尽可能回收甲醇,塔顶采用两级冷凝。
塔顶经部分冷凝后的大部分甲醇、水及少量杂质留在液相作为回流返回塔,二甲醚等轻组分(初馏分)及少量的甲醇、水由塔顶逸出,塔底含水甲醇则由泵送至主精馏塔。
主精馏塔操作压力稍高于预精馏塔,但也可以认为是常压操作,塔顶得到精甲醇产品,塔底含微量甲醇及其它重组分的水送往水处理系统(见图)。
(3) 三塔流程描述三塔工艺是由脱醚塔,加压精馏塔和常压精馏塔组成,形成二效精馏与二甲醇精馏塔甲醇产品的镏出物的混合物。
【doc】甲醇—乙醇—水三元系精馏分离流程研究

甲醇—乙醇—水三元系精馏分离流程研究化学工程2001年第29卷第3期甲醇一乙醇一水三元系精馏分离流程研究白润生杨慧文胡熙恩王学军邓劲光(清华大学核能技术设计研究院,北京1132201)提出了甲醇一乙醇一水三元系的分离问题.计算结果表明,足够量甲醇的存在可破坏乙醇和水之间的共沸现象,使采用普通精馏制取高浓度乙醇成为可能.当甲醇浓度大于0.615摩尔分率时,乙醇和水之间的共沸点完全消失.可通过循环甲醇调整进料中甲醇的含量,一定量甲醇的循环可显着降低精馏塔的投资费用.在示例中,有甲醇循环时的最小塔费用仅相当于无甲醇循环时的40%.实验结果证实了流程的可行性,相近的耕e程已应用于工业生产中.关键词:甲醇乙醇水分离精馏流程TMP(学名甲氧苄啶,一种抗菌药)生产中所用溶剂废液经化学处理后形成甲醇一乙醇-水三元体系,这样,溶剂的回收就成为三元系的分离问题.对乙醇一水体系,普通精馏只能得到95%(质量)乙醇.制取高浓度乙醇的常用方法有乙二醇作为萃取剂的萃取精馏法和苯作为夹带剂的共沸精馏法.这些方法都需要向体系中加入第三组分.对甲醇一乙醇一水三元体系分离,如再加人萃取剂或夹带剂,则变为四元系精馏,流程复杂,投资也大.事实上,因甲醇与水和乙醇无共沸现象,甲醇的存在有可能破坏乙醇和水之间的共沸现象,使采用普通精馏制取高浓度乙醇成为可能.因此,如体系自身含有的甲醇可作为夹带剂使用,并在经济上可行,则分离流程可大大简化.[aroche等人基于一种无限回流比下剩余曲线(ResidueCurve)的技术,提出以甲醇为夹带剂制取无水乙醇的流程.该流程由两个精馏塔组成, 甲醇被加人到95%乙醇进料中.第一个塔用于除去混合物中的水分;第二个塔用于甲醇,乙醇分离.分离出的甲醇循环使用.因甲醇是从外部加入到体系作为夹带剂使用,因此,这一方法属特殊精馏.此外,该流程有一重要缺点,甲醇的循环量太大,为进料量的六倍.其流程综合的目标为体系的可分离性,未考虑费用优化.本文对甲醇-乙醇-水三元体系中甲醇对体系分离的作用进行研究,并结合实际情况,对精馏塔投资费用进行了优化.所得流程通过实验得到检验, 为工业化应用提供设计依据1理论计算1,1理论分析Laroche等人依据甲醇一乙醇一水三元体系的剩余曲线,表明以甲醇为夹带剂制取高浓度乙醇是可行的.本文以乙醇和水的相对挥发度在不同甲醇含量下随/(+)的变化情况来定量表示甲醇含量对乙醇和水相对挥发度的影响.图1为常压相平衡计算结果.可以看出,甲醇的含量对体系的分离效果有重要影响.当/(+)小于0,7时,随甲醇浓度增加,乙醇和水的相对挥发度降低;但当/(+)大于0,8时,随甲醇浓度增加,乙醇和水的相对挥发度则增加.当甲醇含量大于0.615摩尔分率时,乙醇和水的相对挥发度在全组成范围内大于1.由于对甲醇含量的要求可通过循环甲醇来实现,所以,采用普通精馏分离甲醇.乙醇.水三元体系是可行的.白润生,男,I963年生,1992年清华大学化工系1甄士研兜生毕业. ./【+z)图1不同甲醇台■下乙醇对水的相对挥发度白润生等甲醇一乙醇一水三元系精馏分离流程研究1.2分离要求以TMP生产为例,回收的甲醇用于制取甲醇钠,对水分的含量要求严格.回收的乙醇用作溶剂,对水分也有较严格的限制.回收甲醇和乙醇的含量(摩尔分率)要求为:甲醇:大于0.99,水分小于0.005;乙醇:大于0.97,水分小于0.02.n呈\匠粗妊辎甲醇循环量/kmol/h圉2塔投资费用随甲醇循环量变化曲线1.3模拟系统系统为常压操作,汽一液平衡关系采用下式yPT=',P(1)活度系数由WiUson方程计算.参数和物性数据分别选自Gmehiling和Onkon的数据集及Perry~手册.对精馏过程计算,郭天民有详细介绍.设备费用计算采用Rose推荐的方法J对CY型的金属丝网波纹填料,气相动能因子取1.8[7】.1.4优化目标在精馏中,当取高塔板数时,设备投资高;但所需回流比小,能耗低,运行费用低.反之,则投资少而运行费用高.在本体系中,优化目标选为脱水塔和甲醇,乙醇分离塔的设备投资费用.均相共沸精馏的现象之一就是在某些情况下存在一最佳回流比.回流比太大,分离效果反而降低.对甲醇一乙醇-水体系,最佳回流比值约等于6.对塔投资费用进行优化后,回流比约在3~4之间,且随塔高变化不大因此,精馏能耗随回流比变化不大.另一方面,体系沸点低,能耗在总费用中所占比例较低.此外,工厂现有的辅助设备,如换热器,泵和贮罐等,可充分利用,这使得精馏塔的投资费用更显突出.因此,这样处理有其合理性和实用性.在流程优化的过程中,每个塔的进料位置,塔板数和回流比依模拟结果取费用优化值.1.5流程综合甲醇的循环使脱水易于进行.这不仅减少了脱水塔所需的塔板数,而且降低了回流比.这样,虽然进料量增加,但塔负荷并投有明显增加.因此,脱水塔的费用将减少.另一方面,甲醇循环对甲醇,乙醇分离无显着影响,但增加甲醇,乙醇分离塔的负荷因此,甲醇,乙醇分离塔的费用将增加.作为结果,两塔总费用随甲醇循环量的变化不会是一单调函数,必存在一最小点.取不同的甲醇循环量,分别计算两个精馏塔的费用和两塔的总费用,结果见图3.起始,塔总费用曲线随甲醇循环量的增加而迅速下降,达到一最低点后又缓慢上升.这一最低点对应的甲醇循环量为24kmol/h(基于100kmol/h进料量).此时,精馏塔总费用仅为无甲醇回流时的40%最终的流程见图3,各物流组成列于表1.甲醇26.9km0l/h0醇,38Okmol/h圈3费用优化后精馏流程表1圈3中各物流组成(摩尔分率2实验部分2.1精馏装置实验精馏塔为内径25mm的玻璃管,管内填充4,3×3不锈钢e形金属丝网环;管外包覆双层保温石棉布.经甲醇一乙醇体系标定,等板高度约为lO?化学工程2001年第29卷第3期0.04m.塔高:对脱水塔,精馏段长1.3m,提馏段长0.4m;对分离塔,精馏段长0.8m,提馏段长0.6rn.回流比由仪表自动控制.脱水塔,R=3;分离塔,R=4.加热装置为500W电热套,连接电压调节器.2.2分析方法和试样分析仪器为DPS一34o0气相色谱仪,采用热导池检测器.除脱水塔进料和塔底产品外,其余物流的水分含量由卡尔?费休法测定.进料由市售分析纯甲醇,乙醇和无离子水配制.2.3实验结果配制表1中的进塔原料,进行精馏脱水.结果表明,塔顶产品水分含量偏高,达不到脱水要求.为得到合格的乙醇产品,要求提高进塔原料中的甲醇浓度,即需要较大的甲醇循环量.实验结果列于表2,表中进塔原料组成相当于甲醇循环量为86kmol/h的结果.在该进塔原料组成下,经脱水和分离后所得甲醇和乙醇产品组成均达到指定要求.表2物流组成实验结果包含循环甲醇甲醇循环量计算值和实验值之间的差异,可能是由于Wilson参数的选择引起.如有该体系低水分含量下汽_液两相平衡的高精度实验数据,并进行可靠回归,计算结果可望得到改进.2.4工业应用类似图3的流程,在工业中已得到成功应用,稳定运行两年以上.为确保成功,在设计方案及施工中保留乙二醇脱水塔和乙二醇再生塔.但无需运行该两塔即可达到或超过设计指标.3结论本文讨论了甲醇的存在对甲醇一乙醇一水三元体系精馏分离的影响.计算结果表明,一定量甲醇的存在可破坏乙醇和水之间的共沸现象.当甲醇含量大于0.615摩尔分率时,乙醇和水的共沸点消失. 这样,应用普通精馏即可分离该体系,得到高浓度的甲醇和乙醇.进料组成可通过循环甲醇来调整. 循环甲醇虽增加了进料量,但使脱水易于进行,可大大减少脱水塔所需的塔板数和设备费用.在本例的进料组成下,精馏塔总费用对甲醇循环量曲线存在一最低点.适量的甲醇循环能显着地降低设备投资费用.实验结果也表明,虽然为达到分离要求所需的甲醇循环量要大于理论计算值,但利用甲醇循环以增加进塔原料中甲醇的含量,进而脱去体系中的水分,这一方案是可行的.类似的流程,在工业中已得到成功应用,并取得可观的经济效益.符号说明P压力,P且回流比空塔气速,m/s液相组成,摩尔分率Y汽相组成,摩尔分率相对挥发度,,液相活度系数p密度,kg/m3下角标e乙醇i组分m甲醇s饱和蒸汽压T总压v气相W水参考文献lLar~heL,BekiarisN,AndersenHW,eta1.TheCurl-0l|sBehavior0fHomogeneousAzeotropieDistil]afion-lmpli- cationsforEntrainerSelection.AlalEJ.1992.38(9):1309.2LarocheL.BekiarisN,Ar?derBenHW,et日l,Homogene- 01,1.5AzeotropicDisfinaffon:Separsbili~andlqowsheetSyn- thesis.IndEIIgChemRes,1992,31(9):2190.3C,mehilingJ,OnkonUV apor-LiquidEquilibriumData6∞,Aqueous-0I.icSystemW.Germany:DECHEMA,1997,l,Part1.4PeqRH,GrecwDW,MaloreyJD.Perry'sCheanica]EI1gineersHandbook,6thEd.NewY0rk:McGraw.1984.5郭天民等多元汽-液平衡和精馏.北京:化学工业出版杜,1983.6RoseLM.DistJilionDesi~inPractice.Elsevier.1985.7比利特R.蒸馏工程,黄宇梁等译.1985.。
化工原理课程设计——甲醇与乙醇的精馏
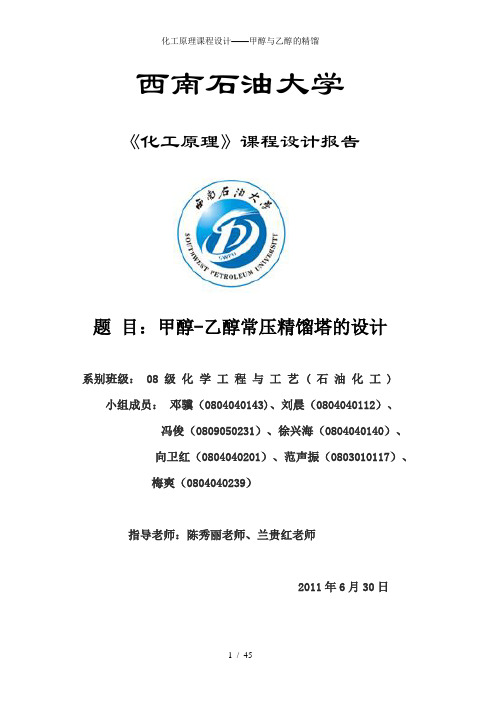
化工原理课程设计——甲醇与乙醇的精馏
西南石油大学
《化工原理》课程设计报告
题 目:甲醇-乙醇常压精馏塔的设计
系别班级: 08 级 化 学 工 程 与 工 艺 ( 石 油 化 工 ) 小组成员: 邓骥(0804040143)、刘晨(0804040112)、 冯俊(0809050231)、徐兴海(0804040140)、 向卫红(0804040201)、范声振(0803010117)、 梅爽(0804040239) 指导老师:陈秀丽老师、兰贵红老师 2011 年 6 月 30 日
甲醇精馏的方法
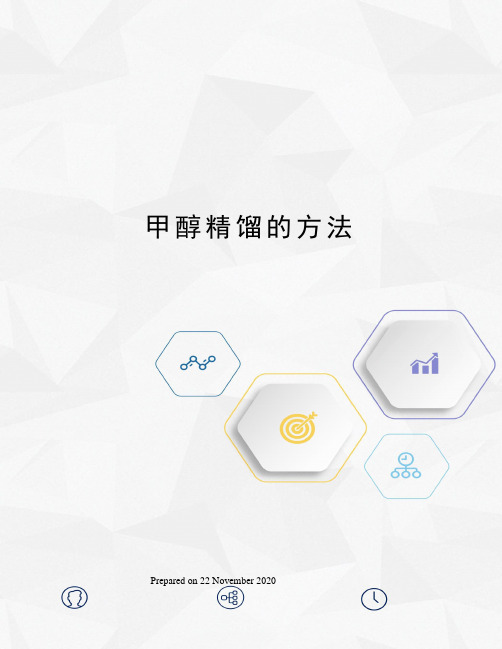
甲醇精馏的方法 Prepared on 22 November 2020甲醇精馏的典型工艺流程甲醇精馏产生工艺有多种,分为单塔精馏,双塔精馏,三塔精馏与四塔精馏(即三塔加回收塔)(1) 单塔流程描述采用铜系催化剂低压法合成甲醇,由于粗甲醇中不仅还原性杂质的含量大大减少,而且二甲醚的含量几十倍地降低,因此在取消化学净化的同时,可将预精馏及甲醇-水-重组分的分离在一台主精馏塔内同时进行,即单塔流程,就能获得一般工业上所需要的精甲醇。
单塔流程更适用于合成甲基燃料的分离,很容易获得燃料级甲醇。
单塔流程(见图为粗甲醇产品经过一个塔就可以采出产品。
粗甲醇塔中部加料口送入,轻组分由塔顶排出,高沸点的重组分在进料板以下若塔板处引出,水从塔底排出,产品甲醇在塔顶以下若干块塔板引出。
(2) 双塔流程描述双塔工艺是由脱醚塔,甲醇精馏塔或者主塔组成。
主塔在工厂中产量在100万吨/年以下,仅仅能提供简单的过程,所以设备和投资较低。
传统的工艺流程,是最早用于30MPa压力下以锌铬催化剂合成粗甲醇的精制。
主要步骤有:中和、脱醚、预精馏脱轻组分杂质、氧化净化、主精馏脱水和重组分,最终得到精甲醇产品。
在传统工艺流程上,取消脱醚塔和高锰酸钾的化学净化,只剩下双塔精馏(预精馏塔和主精馏塔)。
其高压法锌铬催化剂合成甲醇和中、低压法铜系催化剂合成甲醇都可适用。
从合成工序来的粗甲醇入预精馏塔,此塔为常压操作。
为了提高预精馏塔后甲醇的稳定性,并尽可能回收甲醇,塔顶采用两级冷凝。
塔顶经部分冷凝后的大部分甲醇、水及少量杂质留在液相作为回流返回塔,二甲醚等轻组分(初馏分)及少量的甲醇、水由塔顶逸出,塔底含水甲醇则由泵送至主精馏塔。
主精馏塔操作压力稍高于预精馏塔,但也可以认为是常压操作,塔顶得到精甲醇产品,塔底含微量甲醇及其它重组分的水送往水处理系统(见图)。
(3) 三塔流程描述三塔工艺是由脱醚塔,加压精馏塔和常压精馏塔组成,形成二效精馏与二甲醇精馏塔甲醇产品的镏出物的混合物。
甲醇精馏设计总结

甲醇精馏设计总结介绍本文档总结了甲醇精馏设计的相关内容。
甲醇精馏是一种常用的分离技术,可用于提纯甲醇以满足特定的质量要求。
本文将对甲醇精馏的工艺流程、设备设计和操作参数进行详细讨论。
工艺流程甲醇精馏的工艺流程通常包括以下几个步骤:1.进料预处理:原料甲醇通过事先的脱色、脱水等处理,以提高进料的纯度和质量。
2.加热:将进料甲醇加热至适当的温度,以使其蒸发。
3.精馏塔:在精馏塔中,甲醇将与其他组分(如水、杂质等)进行分离。
在塔中,通过利用不同组分的沸点差异,通过冷凝和回流等操作,实现组分的分离。
4.冷凝:将蒸汽冷凝成液体,以回收高纯度的甲醇。
5.分离和回收:将分离后的甲醇和其他组分进行进一步的处理,以回收可再利用的物质,同时满足环保要求。
设备设计甲醇精馏的设备设计需要考虑以下几个方面:1.精馏塔设计:精馏塔是甲醇精馏的核心设备。
在塔内,应设置适当的塔板或填料来增大表面积,以便更好地实现液相和气相的接触。
应根据进料的性质和要求,选择合适的塔板和填料材料。
2.加热设备:加热设备通常采用蒸汽加热方式。
应计算加热器的尺寸和传热面积,以确保能够提供足够的热量,并保持适宜的升温速率。
3.冷凝器设计:冷凝器用于将蒸汽冷凝成液体。
应根据进料流量和温度要求选择适当的冷凝器类型,并设计合适的冷凝面积。
4.控制系统:精馏过程需要精确的温度和压力控制。
应设计一个可靠的控制系统,以确保操作参数的稳定性和精度。
操作参数甲醇精馏的操作参数对分离效果至关重要。
以下是一些常见的操作参数:1.温度:温度是影响馏分的重要参数。
应控制好精馏塔内的温度梯度,以确保在不同的塔板上可以实现合适的汽液平衡。
2.压力:压力对甲醇和其他组分的相平衡有直接影响。
应根据进料的性质和要求,调整适当的操作压力。
3.进料流量和回流比:进料流量和回流比是实现有效甲醇分离的关键参数。
应根据进料的纯度和要求,控制好进料流量和回流比,以确保最佳的分离效果。
4.塔板间液位差:塔板间液位差的控制对精馏效果有很大影响。
含有甲醇的乙醇脱水共沸精馏研究

含有甲醇的乙醇脱水共沸精馏研究Study on Ethanol Dehydration with Methanol by Azeotropic Distillation领域:化学工程研究生:刘彤指导教师:韩振为副研究员企业导师:张志恒高工天津大学化工学院二零一三年六月独创性声明本人声明所呈交的学位论文是本人在导师指导下进行的研究工作和取得的研究成果,除了文中特别加以标注和致谢之处外,论文中不包含其他人已经发表或撰写过的研究成果,也不包含为获得天津大学或其他教育机构的学位或证书而使用过的材料。
与我一同工作的同志对本研究所做的任何贡献均已在论文中作了明确的说明并表示了谢意。
学位论文作者签名:签字日期:年月日学位论文版权使用授权书本学位论文作者完全了解天津大学有关保留、使用学位论文的规定。
特授权天津大学可以将学位论文的全部或部分内容编入有关数据库进行检索,并采用影印、缩印或扫描等复制手段保存、汇编以供查阅和借阅。
同意学校向国家有关部门或机构送交论文的复印件和磁盘。
(保密的学位论文在解密后适用本授权说明)学位论文作者签名:导师签名:签字日期:年月日签字日期:年月日中文摘要乙醇作为一种性能优良的有机溶剂,广泛应用于化工、制药等领域。
共沸精馏是乙醇脱水的有效方法之一,具有流程简单、自动化程度高、产品质量好等优点。
本文以制药企业生产过程中产生的乙醇、甲醇和水的溶剂脱水过程为研究背景,对含有甲醇的乙醇脱水共沸精馏过程进行了研究。
结合共沸剂选取的一般原则,选择环己烷为共沸剂,提出该体系共沸精馏脱水的两塔流程和四塔流程。
利用流程模拟软件Aspen Plus对两塔流程和四塔流程进行了模拟计算,用NRTL模型校正液相的非理想性,所得结果满足分离要求。
在不同甲醇浓度进料条件下,对两塔流程进行了模拟,结果表明,两塔流程可以实现含有甲醇的乙醇脱水。
进料中含有甲醇时,脱水塔和回收塔的能耗均比进料中无甲醇时高。
随着进料中甲醇浓度的增加,两塔流程的乙醇收率降低,脱水塔和回收塔的能耗增加。
分离甲醇和乙醇的方法

分离甲醇和乙醇的方法
甲醇和乙醇是常见的醇类有机物,它们在工业和生活中有着广泛的应用。
但是,由于它们具有相似的物理和化学性质,因此在混合物中很难进行分离。
下面介绍几种分离甲醇和乙醇的方法:
1. 蒸馏法:甲醇和乙醇在不同温度下的沸点不同,可通过蒸馏
将其分离。
通常先进行精馏分离,然后再进行简单蒸馏,以达到更高纯度的分离效果。
2. 萃取法:将甲醇和乙醇混合物与适当的萃取剂(如水)接触,通过分配系数不同将其分离。
萃取后,可以通过蒸馏等方法将获得的物质纯化。
3. 结晶法:在适当的温度和条件下,甲醇和乙醇可以结晶分离。
利用它们在溶剂中的溶解度不同,通过结晶分离可以得到不同纯度的甲醇和乙醇。
4. 活性炭吸附法:利用甲醇和乙醇在活性炭上的吸附能力不同,可以将它们分离。
通过将混合物通过一定压力和温度下的活性炭床层,甲醇和乙醇会被吸附在不同的位置上,从而达到分离的目的。
总之,对于甲醇和乙醇的分离,可以根据其物理和化学性质选择不同的方法,以达到高效、经济、环保的分离效果。
- 1 -。
甲醇精制的三种流程

甲醇精制的三种流程(双塔、高质量三塔精馏、节能型三塔精馏)一、普通双塔流程:精甲醇中的乙醇含量多少,与粗甲醇中的乙醇含量有关;粗甲醇中乙醇的含量又与合成条件有关,如压力、温度、[wiki]催化剂[/wiki]使用前后期、合成气组份和原料结构等等。
低压法(包括轻油为原料用铜系催化剂的高压法)制得的粗甲醇中含乙醇100~ 1000ppm ,而以煤为原料的中压法(联醇)和高压法(亦用铜催化剂)制得的粗甲醇中含乙醇的量可高达400~2000ppm。
所以精甲醇中的乙醇含量差距也较大,一般为100~600ppm ,有时可能高达1000ppm。
这是因为双塔精馏系统,在采出产品的主蒸馏塔塔釜几乎全部为水,乙醇的挥发度又与甲醇比较接近,因而乙醇不可能在塔釜中浓缩,从而有部份乙醇随着甲醇升向塔顶,粗甲醇中相当数量的乙醇转移至精甲醇中。
据国内甲醇生产经验,利用双塔常压精馏方法,也可将精甲醇中乙醇的含量降至<100ppm,满足了甲醇特殊用途的需要。
但根据蒸馏原理和流程特点,在操作中应采取如下措施。
(1)在预蒸馏塔中脱除轻组份时,结合流程特点,严格控制塔顶回流系统的冷凝温度,尽可能脱除部份乙醇。
(2)提高主蒸馏塔[wiki]回流比[/wiki],将[wiki]沸点[/wiki]高于甲醇的乙醇组份大部份压至塔的下部,使其浓集于入料口附近或接近塔釜的提馏段内,以提高塔顶精甲醇的纯度。
(3)据乙醇浓集的部位,一般为入料口上下,乙醇可达数千ppm,适当采出部份液体,以排除乙醇,否则,当塔内组份达到平衡以后,乙醇仍然逐板上升进入塔顶产品中去。
显然,以上通过增大回流比和采出乙醇(其中大部份为甲醇,需再蒸馏予以回收)的办法,是以增加粗甲醇精馏的能耗来换取低乙醇含量的精甲醇产品的。
当粗甲醇中乙醇含量较低时,提高回流比的同时,只需少量采出乙醇,即可使精甲醇中乙醇含量降至50ppm左右,且一次蒸馏甲醇收率在95%以上,这样的工况,每吨精甲醇精馏的能耗约为6MkJ。
- 1、下载文档前请自行甄别文档内容的完整性,平台不提供额外的编辑、内容补充、找答案等附加服务。
- 2、"仅部分预览"的文档,不可在线预览部分如存在完整性等问题,可反馈申请退款(可完整预览的文档不适用该条件!)。
- 3、如文档侵犯您的权益,请联系客服反馈,我们会尽快为您处理(人工客服工作时间:9:00-18:30)。
1.2 流程的说明及方案的确定1.2.1 流程的说明首先,甲醇和乙醇的原料混合物进入原料罐,在里面停留一定的时间之后,通过泵进入原料预热器,在原料预热器中加热到泡点温度,然后,原料从进料口进入到精馏塔中。
因为被加热到泡点,混合物中既有气相混合物,又有液相混合物,这时候原料混合物就分开了,气相混合物在精馏塔中上升,而液相混合物在精馏塔中下降。
气相混合物上升到塔顶上方的冷凝器中,这些气相混合物被降温到泡点,其中的液态部分进入到塔顶产品冷却器中,停留一定的时间然后进入甲醇的储罐,而其中的气态部分重新回到精馏塔中,这个过程就叫做回流。
液相混合物就从塔底一部分进入到塔底产品冷却器中,一部分进入再沸器,在再沸器中被加热到泡点温度重新回到精馏塔。
塔里的混合物不断重复前面所说的过程,而进料口不断有新鲜原料的加入。
最终,完成甲醇和乙醇的分离。
1.2.2设计方案的确定1.操作压力精馏操作可在常压,加压,减压下进行。
应该根据处理物料的性能和设计总原则来确定操作压力。
例如对于热敏感物料,可采用减压操作。
本次设计甲醇和乙醇为一般物料因此,采用常压操作。
2.进料状况进料状态有五种:过冷液,饱和液,气液混合物,饱和气,过热气。
但在实际操作中一般将物料预热到泡点或近泡点,才送入塔内。
这样塔的操作比较容易控制。
不受季节气温的影响,此外泡点进料精馏段与提馏段的塔径相同,在设计和制造上也叫方便。
本次设计采用泡点进料,即q=1。
3.加热方式精馏塔釜的加热方式一般采用间接加热方式,若塔底产物基本上就是水,而且在浓度极稀时溶液的相对挥发度较大,便可以采用直接加热。
直接蒸汽加热的优点是:可以利用压力较低的蒸汽加热,在釜内只需安装鼓泡管,不需安装庞大的传热面,这样,操作费用和设备费用均可节省一些,然而,直接蒸汽加热,由于蒸汽的不断涌入,对塔底溶液起了稀释作用,在塔底易挥发物损失量相同的情况下。
塔釜中易于挥发组分的浓度应较低,因而塔板数稍微有增加。
但对有些物系。
当残液中易挥发组分浓度低时,溶液的相对挥发度大,容易分离故所增加的塔板数并不多,此时采用间接蒸汽加热是合适的。
4.冷却方式塔顶的冷却方式通常水冷却,应尽量使用循环水。
如果要求的冷却温度较低。
可考虑使用冷却盐水来冷却。
5.热能利用精馏过程的特性是重复进行气化和冷凝。
因此,热效率很低,可采用一些改进措施来提高热效率。
因此,根据上述设计方案的讨论及设计任务书的要求,本设计采用常压操作,泡点进料,间接蒸汽加热以及水冷的冷却方式,适当考虑热能利用。
二·塔的工艺设计精馏所进行的是气、液两相之间的传质,而作为气、液两相传质用的塔设备首先必须要能使气、液两相得到充分接触,以达到较高的传质效率。
塔设备设计要具备下列各种基本要求:1、气、液处理量大,即当生产能力大时,仍不致发生大量的雾沫夹带,拦液或液泛等破坏操作的现象。
2、操作稳定,弹性大,即当塔设备的气、液负荷有较大范围的变动,仍能在较高的传质效率下进行稳定操作,并应保证长期连续操作所必须具有的可靠性。
3、流体流动的阻力少,可降低操作费用。
4、结构简单,材料耗用量小,制造和安装容易。
5、耐腐蚀和不易堵塞,方便操作,调节和检修。
6、塔内的滞留量要小。
3.2物料衡算3.2.1原始数据表3—1原始液:甲醇和乙醇的混合物3.2.2查阅文献,整理有关物性数据表3—2 甲醇和乙醇的物理性质1. 料液及塔顶、塔底产品的摩尔分数 原料组成: X F (A )=46/32.0446/32.04+54/46.07= 0.5505X F(B)= 1−0.5505=0.4495馏出液组成:X D (A )=9632.049632.04+446.07= 0.9719X D(B)= 1− 0.9719=0.0281釜出液组成X W (A )= 0.532.040.532.04+99.546.07= 0.0072X W(B)= 1−0.0072=0.99283.2.3物料衡算已知D=D m ∙ω1t∙M 1+D m ∙ω2t∙M 2=28000×1000×96%280×24×32.04+28000×1000×4%280×24×46.07=128.6177 kmol/h总物料衡算 F=D+W=128.6177+W易挥发组分物料衡算 0.9719128.6177+0.0072W= 0.5505 F 联立以上二式得:F=228.3768kmol/h W=99.7591kmol/h表3—3 物料衡算数据记录3.2.4塔温确定由于各操作阶段的甲醇和乙醇的质量百分含量已确定,所以根据甲醇和乙醇的质量百分含量,利用表中数据用内插值法求得各组分的温度。
表3—4塔温温度 相对挥发度 塔顶甲醇的摩尔分数:x D = 0.9719t D =65.3℃α=1.74985 进料甲醇的摩尔分数:x F = 0.5505 t F =66.9℃(泡点温度) α=1.7379 塔底甲醇的摩尔分数:x W = 0.0072t W =77.2℃α=1.66723.2.5 q 值的计算假设为泡点进料,则q = 1。
3.1 塔的结构设计3.1.1精馏塔塔径的计算1.查得有关甲醇与乙醇的安托因方程:甲醇: 得: 0.2301.1473879.7lg +-=T P A乙醇: 得: 65.2223.1554045.8lg +-=T P B将 A P , B P 代入P x P x P B B A A =+进行试差,求塔顶、进料板、及塔釜的压力和温度:1)塔顶:P 1 = 101.3 + 0.7 = 102kPa, x A = D x = 0.9789, 试差得 D t = 62.1 2)进料板位置:11精馏段实际板层数:N 精 = 10/ 55.07% 18每层塔板压降:∆P = 0.7kPa进料板压力:P F = 101.3+0.718=113.9kPa ,x A =x F =0.6080, 试差得 t F = 67.43提馏段实际板层数:N 提 = 38-18=20 塔釜压力:P W = 101.3+0.737 = 127.2kPa 塔釜:x A =x W = 0.0426, 试差得t W = 79.5 求得精馏段及提馏段的平均压力及温度:精馏段: t m =75.642=+FD t t ℃ P m =1082=+FD P P kPa 提馏段:t m ,=5.732=+FW t t ℃ P m ,=5.1202=+FW P P kPa 2.平均摩尔质量的计算:塔顶:M VDm = 0.978932.04+(10.9789) ×46.07=32.34kg/kmol M LDm = 0.964532.04+(10.9645) ×46.07= 32.54kg/kmol 进料板:M VFm = 0.727232.04+(10.7272) ×46.07=35.88 kg/kmol M LFm =0.609532.04+(10.6095) ×46.07=37.52 kg/kmol 塔釜:M VWm = 0.046832.04+(10.0468) ×46.07=45.41 kg/kmol M LWm = 0.027932.04+(10.0279) ×46.07=45.69 kg/kmol 精馏段平均摩尔质量:M Vm =M VDm +M VFm2 = 34.11kg/kmolM Lm =M LDm +M LFm2=35.03kg/kmol提馏段平均摩尔质量:M Vm ,=M VFm +M VWm2= 40.65 kg/kmolM Lm ,=M LFm +M LWm2=41.60 kg/kmol3.平均密度的计算:1)汽相平均密度计算:ρVm =PM RT精馏段汽相平均密度:ρVm =P m ×M VmRT=)75.6415.273(314.811.34108+⨯⨯= 1.311kg/m 3提馏段汽相平均密度:ρVm ,=P m ,×M Vm ,RT ,=)5.7315.273(314.865.405.120+⨯⨯= 1.700kg/m 32)液相平均密度计算:1ρL= ∑w i ρi塔顶:ρA = 749.25 kg/m 3,ρB = 750.11 kg/m 3 得 :ρLDm = 1w AρA +w B ρB=11.75003.025.74997.01+ = 749.29 kg/m 3进料板:ρA = 746.4kg/m 3,ρB = 747.4 kg/m 3得:ρLFm = 1w AρA +w B ρB=4.74746.04.74654.01+= 746.88 kg/m 3塔釜:ρA = 733.5kg/m 3,ρB = 735.04 kg/m 3 得:ρLWm = 1w AρA+w B ρB= 04.73597.05.73303.01+ = 734.97 kg/m 3精馏段液相平均密度:ρLm = 288.74629.749+ = 748.085 kg/m 3提馏段液相平均密度:ρLm ,= 288.74697.734+ = 740.925 kg/m 34.液体平均表面张力计算 液体平均表面张力按下式计算:塔顶:t 1= 62.1,由《化工原理》(第三版,化学工业出版社,陈敏恒)附录σA = 18.35mN/m , σB = 18.40mN/m得:σLDm = x 1σA +(1-x 1) σB =0.964518.35+(1-0.9645) ×18.40 = 18.35 进料板:t F = 67.4,查手册:σA = 17.86mN/m ,σB = 18.00mN/m得:σLFm = x F σA +(1-x F ) σB =0.62817.86+(1-0.628) ×18.00= 17.91 mN/m 塔釜:t W =79.5,查附录:σA =16.80 mN/m ,σB = 17.18mN/m得:σLWm = x F σA +(1-x F ) σB =0.042616.80+(1-0.0426) ×17.18= 17.16 mN/m 精馏段液体表面平均张力:σLm =σLDm +σLFm2 = 18.13mN/m 提馏段液体表面平均张力:σLm ,=σLWm +σLFm2=17.55 mN/m5.液体平均黏度计算:Lm i ix σσ=∑液体平均黏度按下式计算:lgμLm = ∑x i lgμi 塔顶:t 1= 62.1℃查由《化工原理》(第三版,化学工业出版社,陈敏恒)附录 μA = 0.315 mPa ∙s , μB = 0.520 mPa ∙s 得:μLDm = 10∑x i lgμi = 0.32mPa ∙s进料板:t F = 67.4℃,查附录:μA = 0.305 mPa ∙s , μB = 0.485 mPa ∙s 得:μLFm = 10∑x i lgμi = 0.34mPa ∙s塔釜:t W = 79.5℃,查附录:μA = 0.256 mPa ∙s , μB = 0.394 mPa ∙s 得:μLWm = 10∑x i lgμi = 0.38mPa ∙s 精馏段液体平均黏度:μLm = 0.33 mPa ∙s提馏段液体平均黏度:μLm , = 0.36 mPa ∙s6.气液相体积流率计算 精馏段汽相体积流率:V s = VM Vm 3600ρVm= 1.566m 3/s液相体积流率:L s =LM Lm 3600ρLm= 0.00216m 3/s提馏段汽相体积流率:V s ,= '''3600VmVm M V ρ = 1.439m 3/s 液相体积流率:L s , = '''3600LmLmM L ρ = 0.00385m 3/s 7.塔径的确定塔径的确定,需求μmax = C √ρLm −ρVmρVm,C 由下式计算: 由Smith 图查取。