Moldflow与结构分析软件的数值传递方法
MOLDFLOW模流分析

交叉边数量。
非折叠边是指由两个以上的三角 形或3D单元共用一条边。 Fusion网格此项必须是“0”。
共用边数量。 折叠边是指两个三角形或3D单元 共用一条边。 Fusion网格中只能存在折叠边。
STEP 8-创建浇注系统和冷却系统
利用冷却回路向导构建冷却回路
网格的划分和处 理
STEP9-成型窗口分析
网格的划分和处 理
根据产品的几何形状、材料、进浇位置经过一系列的快速计算,预估产 品最佳成型参数,指导后续的工艺参数指定和实际生产中工艺参数的调整
➢ 选择“分析”→“设置分析顺序”→“成型窗口” ➢ 选择“分析”→“工艺设置向导”,按下图设置工艺参数,执行计算
网格的划分和处 理
STEP 8-创建浇注系统和冷却系统
建立浇注系统分流道中心线,赋予冷流道属性
STEP 8-创建浇注系统和冷却系统
➢ 建立浇注系统主流道中心线,赋予冷主流道属性
网格的划分和处 理
➢ 执行划分网格指令
STEP 8-创建浇注系统和冷却系统
检查各区域的连通性
网格的划分和处 理
设置主流道顶部中心节 点作为进胶点,完成浇 注系统设置;
注塑机型号(可以安装注塑机型号库),设置模具温度和熔体温度
STEP 8-创建浇注系统和冷却系统
浇注系统
网格的划分和处 理
STEP 8-创建浇注系统和冷却系统
网格的划分和处 理
直接浇口
点浇口
侧浇口
潜伏浇口
扇形浇口
牛角浇口
STEP 8-创建浇注系统和冷却系统 冷却系统
52
Moldflow基本操作培训CADdoctor操作
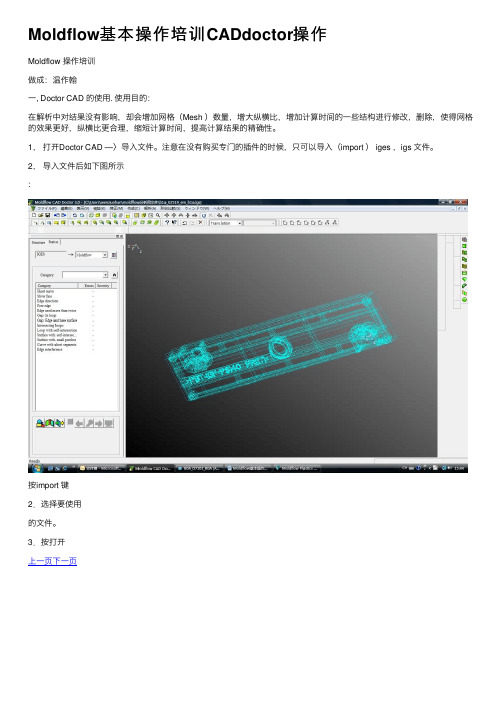
Moldflow基本操作培训 CADdoctor操作
Moldflow 操作培训 做成:温作翰 一, Doctor CAD 的使用. 使用目的: 在解析中对结果没有影响,却会增加网格(Mesh )数量,增大纵横比,增加计算时间的一些结构进行修改,删除,使得网格 的效果更好,纵横比更合理,缩短计算时间,提高计算结果的精确性。 1, 打开Doctor CAD —〉导入文件。注意在没有购买专门的插件的时候,只可以导入(import ) iges ,igs 文件。 2, 导入文件后如下图所示 :
按import 键 2.选择要使用 的文件。 3.按打开 上一页下一页
MoldFlow使用经验教材教学课件
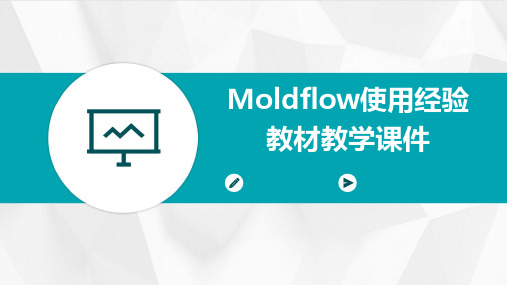
冷却效果评估
介绍如何评估冷却系统的 冷却效果,如通过冷却时 间、温度均匀性等指标进 行评估。
成型工艺优化
注射速度与压力
阐述注射速度和压力对成型工艺的影 响,如对填充效果、产品收缩率等的 影响。
成型参数优化
介绍如何通过调整注射速度、压力、 模具温度等参数优化成型工艺,提高 产品质量和生产效率。
模具温度控制
流道设计
阐述流道设计的要点,如流道截面 形状、流道长度、流道宽度等,以 及如何通过流道设计平衡压力和减 小温差。
冷却系统设计
01
02
03
冷却系统的重要性
强调冷却系统在注塑成型 过程中的重要性,如减小 成型周期、提高产品质量 等。
冷却水路设计
讲解冷却水路的基本类型, 如直通式、环绕式、多通 道式等,以及各自适用的 场景。
Moldflow使用经验 教材教学课件
目录
• Moldflow软件介绍 • Moldflow基础操作教程 • Moldflow进阶操作教程 • Moldflow实战案例分析 • Moldflow常见问题与解决方案 • Moldflow软件更新与未来发展
01
Moldflow软件介绍
软件特点与优势
详细描述
网格划分失败的原因可能包括模型导入错误、网格类型 选择不当、网格参数设置不合理等。解决此问题的方法 包括检查模型文件是否正确、选择合适的网格类型、调 整网格参数等。
材料参数设置问题
总结词
材料参数是影响Moldflow模拟结果的重要因素,如果参数设 置不准确或不完整,将导致模拟结果失真。
详细描述
热交换结构设计
介绍热交换结构在模具设 计中的应用,如水路、气 道等,以提高模具的冷却 效果和减小成型周期。
MOLDFLOW详细操作手册
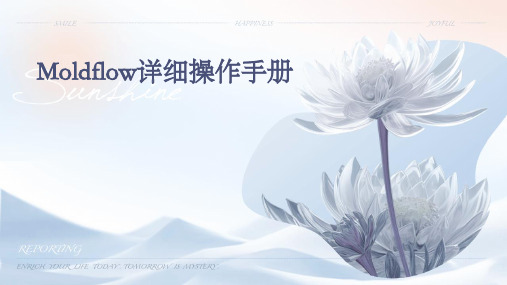
VS
4. 在必要情况下,采用多级注射工艺 来改善填充效果。
05
Moldflow案例分析
案例一:手机壳模具设计优化
总结词
通过Moldflow对手机壳模具进行模拟分析, 优化模具设计,提高生产效率和产品质量。
1. 导入3D模型
将手机壳的3D模型导入Moldflow软件中,并 进行适当的单位和网格划分设置。
冷却介质
根据模具结构和生产条件,选择合适的冷却介质,如水、油等, 以提高冷却效果和减小冷却时间。
模具热平衡分析
温度场分布
通过热平衡分析,了解模具温度场分布情况,为优化模具设计和减 小热误差提供依据。
热传导与对流
分析模具材料、冷却介质和塑料之间的热传导与对流情况,以提高 冷却效果和减小成型周期。
热膨胀与收缩
多模腔模拟
模腔耦合分析
通过多模腔模拟,分析各模腔之间的耦合效应, 以优化模具设计和减小成型误差。
充型平衡
通过多模腔模拟,分析各模腔的充型情况,以实 现各模腔的充型平衡和减小缺陷。
冷却平衡
通过多模腔模拟,分析各模腔的冷却情况,以实 现各模腔的冷却平衡和减小成型周期。
04
Moldflow常见问题与解决 方案
浇注材料等。
03
4. 设计调整
根据模拟分析结果,对模具设计方案进行调 整,如优化浇注系统、改进模具结构等。
05
04
3. 模拟分析
对模具进行充填、流动、保压和冷却 等模拟分析,观察分析结果,评估模 具设计方案的有效性和可行性。
06
5. 验证调整效果
通过再次模拟分析验证调整后的模具设计方案 效果,确保方案的有效性和可行性得到提高。
4. 尝试增加模拟迭代次数或采用更高级的求解算法以提高模 拟精度。
7材料成型过程的计算机模拟——MOLDFLOW
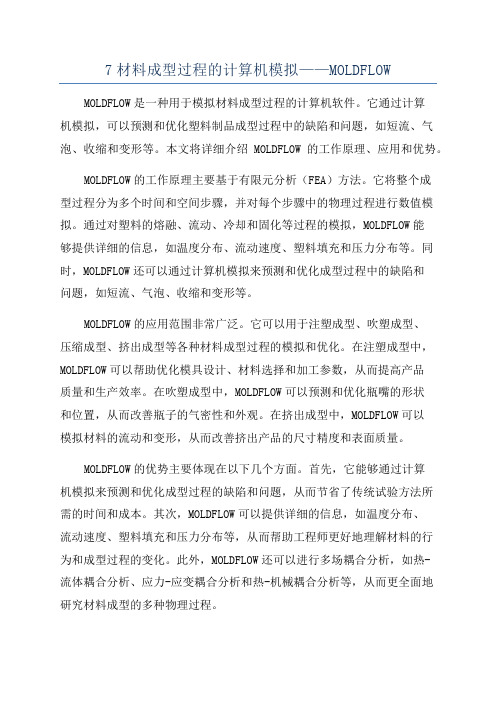
7材料成型过程的计算机模拟——MOLDFLOW MOLDFLOW是一种用于模拟材料成型过程的计算机软件。
它通过计算机模拟,可以预测和优化塑料制品成型过程中的缺陷和问题,如短流、气泡、收缩和变形等。
本文将详细介绍MOLDFLOW的工作原理、应用和优势。
MOLDFLOW的工作原理主要基于有限元分析(FEA)方法。
它将整个成型过程分为多个时间和空间步骤,并对每个步骤中的物理过程进行数值模拟。
通过对塑料的熔融、流动、冷却和固化等过程的模拟,MOLDFLOW能够提供详细的信息,如温度分布、流动速度、塑料填充和压力分布等。
同时,MOLDFLOW还可以通过计算机模拟来预测和优化成型过程中的缺陷和问题,如短流、气泡、收缩和变形等。
MOLDFLOW的应用范围非常广泛。
它可以用于注塑成型、吹塑成型、压缩成型、挤出成型等各种材料成型过程的模拟和优化。
在注塑成型中,MOLDFLOW可以帮助优化模具设计、材料选择和加工参数,从而提高产品质量和生产效率。
在吹塑成型中,MOLDFLOW可以预测和优化瓶嘴的形状和位置,从而改善瓶子的气密性和外观。
在挤出成型中,MOLDFLOW可以模拟材料的流动和变形,从而改善挤出产品的尺寸精度和表面质量。
MOLDFLOW的优势主要体现在以下几个方面。
首先,它能够通过计算机模拟来预测和优化成型过程的缺陷和问题,从而节省了传统试验方法所需的时间和成本。
其次,MOLDFLOW可以提供详细的信息,如温度分布、流动速度、塑料填充和压力分布等,从而帮助工程师更好地理解材料的行为和成型过程的变化。
此外,MOLDFLOW还可以进行多场耦合分析,如热-流体耦合分析、应力-应变耦合分析和热-机械耦合分析等,从而更全面地研究材料成型的多种物理过程。
总之,MOLDFLOW是一种用于模拟材料成型过程的计算机软件。
它通过计算机模拟,可以预测和优化塑料制品成型过程中的缺陷和问题,如短流、气泡、收缩和变形等。
MOLDFLOW的工作原理基于有限元分析方法,它能够模拟塑料的熔融、流动、冷却和固化等过程,并提供详细的信息。
MOLDFLOW模流分析结果解释
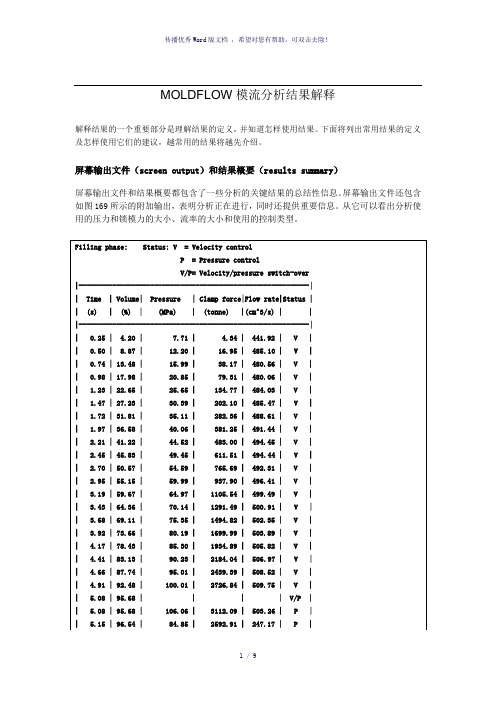
MOLDFLOW模流分析结果解释解释结果的一个重要部分是理解结果的定义,并知道怎样使用结果。
下面将列出常用结果的定义及怎样使用它们的建议,越常用的结果将越先介绍。
屏幕输出文件(screen output)和结果概要(results summary)屏幕输出文件和结果概要都包含了一些分析的关键结果的总结性信息。
屏幕输出文件还包含如图169所示的附加输出,表明分析正在进行,同时还提供重要信息。
从它可以看出分析使用的压力和锁模力的大小、流率的大小和使用的控制类型。
图169. 充模分析的屏幕输出文件屏幕输出文件和结果概要都有与图170相似的部分。
它同时包含了分析过程中(第一部分)和分析结束时的关键信息。
使用这些信息可以快速查看这些变量,从而判断是否需要详细分析某一结果,以发现问题。
图170. 结果概要输出充模时间(Fill Time)充模时间显示的是熔体流动前沿的扩展情况,其默认绘制方式是阴影图,但使用云纹图可更容易解释结果。
云纹线的间距应该相同,这表明熔体流动前沿的速度相等。
制件的填充应该平衡。
当制件平衡充模时,制件的各个远端在同一时刻充满。
对大多数分析,充模时间是一个非常重要的关键结果。
压力(Pressures)有几种不同的压力图,每种以不同的方式显示制件的压力分布。
所有压力图显示的都是制件某个位置(一个节点)、或某一时刻的压力。
使用的最大压力应低于注射机的压力极限,很多注射机的压力极限为140 MPa (~20,000 psi)。
模具的设计压力极限最好为100 MPa (~14,500 psi)左右。
如果所用注塑机的压力极限高于140MPa,则设计极限可相应增大。
模具的设计压力极限应大约为注射机极限的70%。
假如分析没有包括浇注系统,设计压力极限应为注射机极限的50%。
象充模时间一样,压力分布也应该平衡。
压力图和充模时间图看起来应该十分相似,如果相似,则充模时制件内就只有很少或没有潜流。
具体的压力结果定义如下:•压力(Pressure)压力是一个中间结果,每一个节点在分析时间内的每一时刻的压力值都记录了下来。
Moldflow分析结果解释大全要点
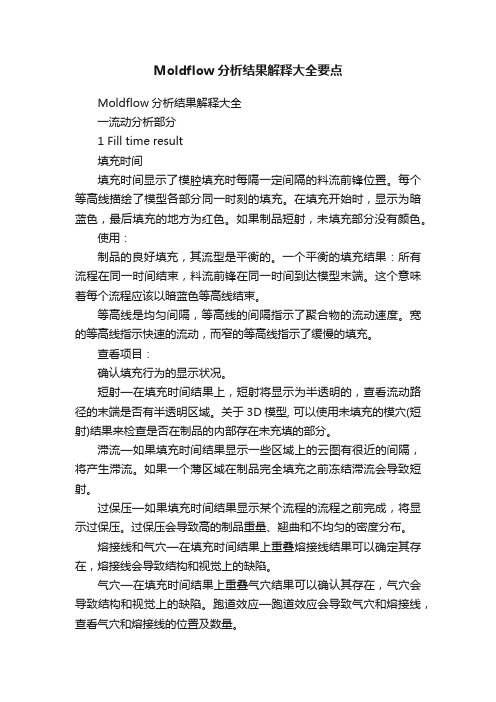
Moldflow分析结果解释大全要点Moldflow分析结果解释大全一流动分析部分1 Fill time result填充时间填充时间显示了模腔填充时每隔一定间隔的料流前锋位置。
每个等高线描绘了模型各部分同一时刻的填充。
在填充开始时,显示为暗蓝色,最后填充的地方为红色。
如果制品短射,未填充部分没有颜色。
使用:制品的良好填充,其流型是平衡的。
一个平衡的填充结果:所有流程在同一时间结束,料流前锋在同一时间到达模型末端。
这个意味着每个流程应该以暗蓝色等高线结束。
等高线是均匀间隔,等高线的间隔指示了聚合物的流动速度。
宽的等高线指示快速的流动,而窄的等高线指示了缓慢的填充。
查看项目:确认填充行为的显示状况。
短射—在填充时间结果上,短射将显示为半透明的,查看流动路径的末端是否有半透明区域。
关于3D模型, 可以使用未填充的模穴(短射)结果来检查是否在制品的内部存在未充填的部分。
滞流—如果填充时间结果显示一些区域上的云图有很近的间隔,将产生滞流。
如果一个薄区域在制品完全填充之前冻结滞流会导致短射。
过保压—如果填充时间结果显示某个流程的流程之前完成,将显示过保压。
过保压会导致高的制品重量、翘曲和不均匀的密度分布。
熔接线和气穴—在填充时间结果上重叠熔接线结果可以确定其存在,熔接线会导致结构和视觉上的缺陷。
气穴—在填充时间结果上重叠气穴结果可以确认其存在,气穴会导致结构和视觉上的缺陷。
跑道效应—跑道效应会导致气穴和熔接线,查看气穴和熔接线的位置及数量。
2 Pressure at velocity/pressure switchover resultV/P切换时刻的压力该结果从流动分析产生,显示了通过模型内的流程在从速度到压力控制切换点的压力分布。
使用:在填充开始前,模腔内各处的压力为零(或者为大气压,绝对压力)。
熔料前沿到达的位置压力才会增加,当熔料前沿向前移动填充后面的区域时压力继续增加,此取决于该位置与熔料前沿的长度。
Moldflow软件操作标准指导书
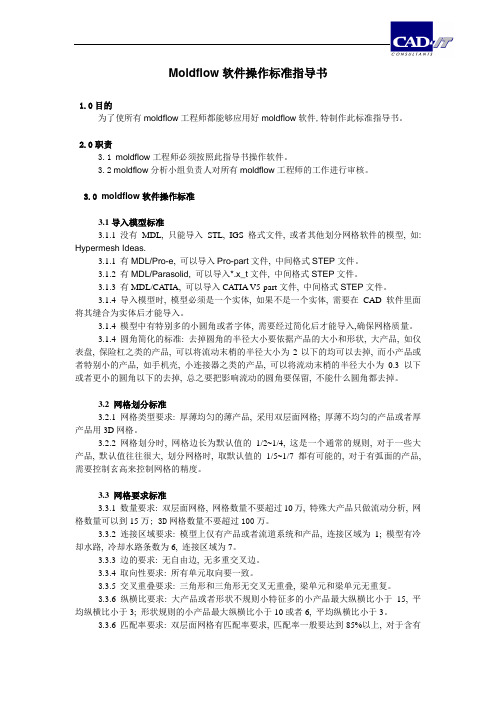
Moldflow软件操作标准指导书1.0目的为了使所有moldflow工程师都能够应用好moldflow软件,特制作此标准指导书。
2.0职责3.1 moldflow工程师必须按照此指导书操作软件。
3.2 moldflow分析小组负责人对所有moldflow工程师的工作进行审核。
3.0 moldflow软件操作标准3.1导入模型标准3.1.1 没有MDL, 只能导入STL, IGS格式文件, 或者其他划分网格软件的模型, 如: Hypermesh Ideas.3.1.1 有MDL/Pro-e, 可以导入Pro-part文件, 中间格式STEP文件。
3.1.2 有MDL/Parasolid, 可以导入*.x_t文件, 中间格式STEP文件。
3.1.3 有MDL/CATIA, 可以导入CATIA V5-part文件, 中间格式STEP文件。
3.1.4 导入模型时, 模型必须是一个实体, 如果不是一个实体, 需要在CAD软件里面将其缝合为实体后才能导入。
3.1.4 模型中有特别多的小圆角或者字体, 需要经过简化后才能导入,确保网格质量。
3.1.4 圆角简化的标准: 去掉圆角的半径大小要依据产品的大小和形状, 大产品, 如仪表盘, 保险杠之类的产品, 可以将流动末梢的半径大小为2以下的均可以去掉, 而小产品或者特别小的产品, 如手机壳, 小连接器之类的产品, 可以将流动末梢的半径大小为0.3以下或者更小的圆角以下的去掉, 总之要把影响流动的圆角要保留, 不能什么圆角都去掉。
3.2 网格划分标准3.2.1 网格类型要求: 厚薄均匀的薄产品, 采用双层面网格; 厚薄不均匀的产品或者厚产品用3D网格。
3.2.2 网格划分时, 网格边长为默认值的1/2~1/4, 这是一个通常的规则, 对于一些大产品, 默认值往往很大, 划分网格时, 取默认值的1/5~1/7都有可能的, 对于有弧面的产品, 需要控制玄高来控制网格的精度。
Moldflow各种功能介绍
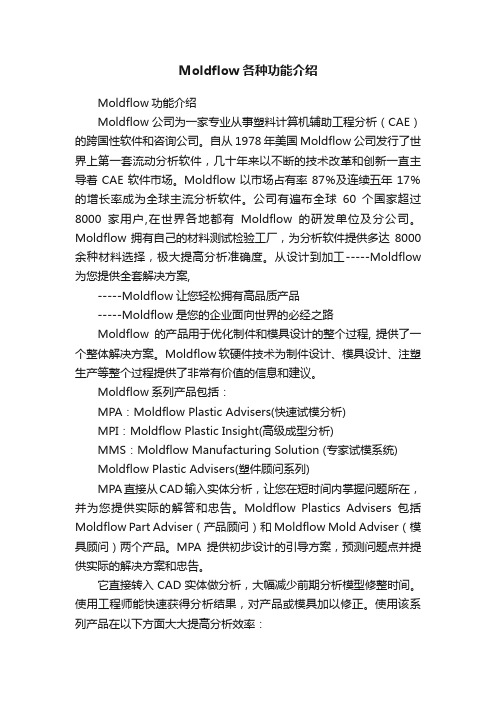
Moldflow各种功能介绍Moldflow功能介绍Moldflow 公司为一家专业从事塑料计算机辅助工程分析(CAE)的跨国性软件和咨询公司。
自从1978年美国Moldflow公司发行了世界上第一套流动分析软件,几十年来以不断的技术改革和创新一直主导着CAE软件市场。
Moldflow以市场占有率87%及连续五年17%的增长率成为全球主流分析软件。
公司有遍布全球60个国家超过8000家用户,在世界各地都有Moldflow的研发单位及分公司。
Moldflow拥有自己的材料测试检验工厂,为分析软件提供多达8000余种材料选择,极大提高分析准确度。
从设计到加工-----Moldflow 为您提供全套解决方案,-----Moldflow让您轻松拥有高品质产品-----Moldflow是您的企业面向世界的必经之路Moldflow的产品用于优化制件和模具设计的整个过程, 提供了一个整体解决方案。
Moldflow软硬件技术为制件设计、模具设计、注塑生产等整个过程提供了非常有价值的信息和建议。
Moldflow系列产品包括:MPA:Moldflow Plastic Advisers(快速试模分析)MPI:Moldflow Plastic Insight(高级成型分析)MMS:Moldflow Manufacturing Solution (专家试模系统)Moldflow Plastic Advisers(塑件顾问系列)MPA直接从CAD输入实体分析,让您在短时间内掌握问题所在,并为您提供实际的解答和忠告。
Moldflow Plastics Advisers包括Moldflow Part Adviser(产品顾问)和Moldflow Mold Adviser(模具顾问)两个产品。
MPA提供初步设计的引导方案,预测问题点并提供实际的解决方案和忠告。
它直接转入CAD实体做分析,大幅减少前期分析模型修整时间。
使用工程师能快速获得分析结果,对产品或模具加以修正。
注塑模模流分析技术-MOLDFLOW
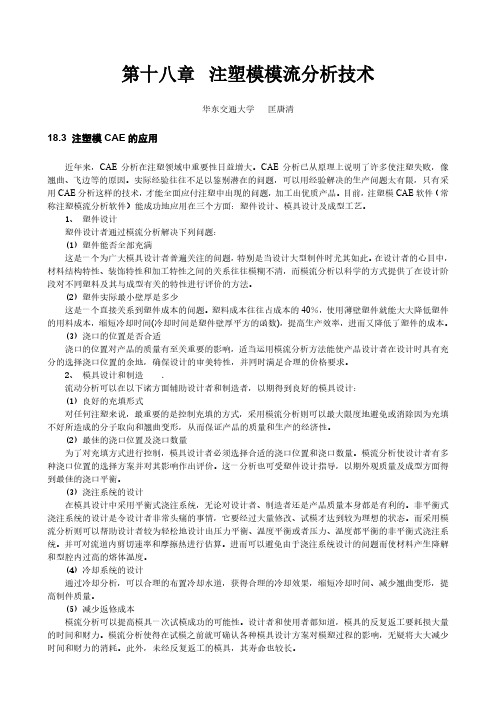
第十八章注塑模模流分析技术华东交通大学匡唐清18.3 注塑模CAE的应用近年来,CAE分析在注塑领域中重要性日益增大。
CAE分析已从原理上说明了许多使注塑失败,像翘曲、飞边等的原因。
实际经验往往不足以鉴别潜在的问题,可以用经验解决的生产问题太有限,只有采用CAE分析这样的技术,才能全面应付注塑中出现的问题,加工出优质产品。
目前,注塑模CAE软件(常称注塑模流分析软件)能成功地应用在三个方面:塑件设计、模具设计及成型工艺。
1、塑件设计塑件设计者通过模流分析解决下列问题:(1)塑件能否全部充满这是一个为广大模具设计者普遍关注的问题,特别是当设计大型制件时尤其如此。
在设计者的心目中,材料结构特性、装饰特性和加工特性之间的关系往往模糊不清,而模流分析以科学的方式提供了在设计阶段对不同塑料及其与成型有关的特性进行评价的方法。
(2)塑件实际最小壁厚是多少这是一个直接关系到塑件成本的问题。
塑料成本往往占成本的40%,使用薄壁塑件就能大大降低塑件的用料成本,缩短冷却时间(冷却时间是塑件壁厚平方的函数),提高生产效率,进而又降低了塑件的成本。
(3)浇口的位置是否合适浇口的位置对产品的质量有至关重要的影响,适当运用模流分析方法能使产品设计者在设计时具有充分的选择浇口位置的余地,确保设计的审美特性,并同时满足合理的价格要求。
2、模具设计和制造.流动分析可以在以下诸方面辅助设计者和制造者,以期得到良好的模具设计:(1)良好的充填形式对任何注塑来说,最重要的是控制充填的方式,采用模流分析则可以最大限度地避免或消除因为充填不好所造成的分子取向和翘曲变形,从而保证产品的质量和生产的经济性。
(2)最佳的浇口位置及浇口数量为了对充填方式进行控制,模具设计者必须选择合适的浇口位置和浇口数量。
模流分析使设计者有多种浇口位置的选择方案并对其影响作出评价。
这一分析也可受塑件设计指导,以期外观质量及成型方面得到最佳的浇口平衡。
(3)浇注系统的设计在模具设计中采用平衡式浇注系统,无论对设计者、制造者还是产品质量本身都是有利的。
MoldFlow软件流动分析及应用

MoldFlow软件流动分析及应用Analysis and Application of Flow with MoldFlow Software麻向军文劲松华南理工大学聚合物新型成型技术国家工程中心华南理工大学—美国MoldFlow高级应用技术中心一、引言对于任何注塑成型来说,最重要的是控制塑料在模具中的流动方式。
制品的许多缺陷,如气穴、熔接痕、短射乃至制品的变形、冷却时间等,都与树脂在模具中的流动方式有关。
MPI/Flow 通过对熔体在模具中的流动行为进行模拟,可以预测和显示熔体流动前沿的推进方式、填充过程中的压力和温度变化、气穴和熔接痕的位置等,帮助工艺人员在试模前对可能出现的缺陷进行预测,找出缺陷产生的原因并加以改进,提高一次试模的成功率。
二、MPI/Flow的作用MPI/Flow能够对注塑成型从制品设计、模具设计到成型工艺提供全面和并行的解决方案。
1、制品设计制品设计者能用MPI/Flow解决以下问题。
(1) 制品能否充满。
这一古老的问题一直为许多设计人员所关注,特别是对于大型制品。
(2) 制品最小壁厚。
在满足制品使用性能和工艺性能的前提下,减小制品壁厚能够大大降低制件的循环时间,从而提高生产效率,降低制件成本。
(3) 制品工艺性能。
在产品设计阶段具有充分的选择浇口位置的余地,确保制品的审美特性。
2、模具设计MPI/Flow能在以下方面辅助模具设计人员,以得到良好的模具设计。
(1) 确保良好的填充形式。
(2) 最佳的浇口位置与数量、类型以及正确地确定阀浇口的开启与闭合时间,有效地发挥阀浇口的作用。
特别是对于有纤维增强的树脂的填充过程,通过分析纤维在流动过程中的取向来判断其对制品强度的影响,并据此判断浇口位置设置的正确与否。
(3) 流道系统的优化设计。
通过流动分析,帮助模具设计人员设计出压力平衡、温度平衡或者压力、温度均平衡的流道系统,并最大程度地减少流道部分的体积。
同时,对流道内熔体的剪切速率和摩擦热进行评估,避免材料的降解和型腔内过高的熔体温度。
moldflow模流分析实例教程pdf

Moldflow模流分析实例教程摘要Moldflow是一种用于注塑成型过程模拟和分析的软件,可以帮助工程师优化产品设计和生产过程。
本文档将介绍Moldflow模流分析的基本概念和使用方法,并通过一个实例来演示其应用。
引言注塑成型是一种广泛应用于制造业的工艺,但在实际生产中常常面临一些问题,例如产品变形、气泡等。
Moldflow是一款强大的模流分析软件,通过数值模拟可以预测和优化注塑过程,从而提高产品质量和生产效率。
本文档将指导读者如何使用Moldflow进行模流分析。
Moldflow模流分析的基本概念Moldflow模流分析基于有限元方法,将注塑模型划分为离散的网格单元,通过求解物理方程来模拟塑料在注塑过程中的流动、冷却和固化等行为。
主要包含以下几个方面的内容:1.前处理:在进行模流分析之前,需要准备注塑模型的几何形状和材料属性等信息,并进行网格划分。
Moldflow提供了丰富的前处理工具,如CAD导入、模型修复和网格生成等。
2.边界条件:边界条件是模流分析中必不可少的一部分,用于描述注塑模型与外部环境之间的交互。
例如,注塑机的注射速度和压力、模具的冷却方式等都是需要指定的边界条件。
3.计算设置:在Moldflow中,用户需要设置一些参数来控制模拟的精度和计算速度。
例如,时间步长、网格密度和求解器选项等。
4.求解过程:一旦完成前处理工作,就可以启动模拟计算。
Moldflow使用数值方法求解注塑模型的流动、温度和应力等物理场,并输出相关结果。
5.后处理:模拟计算完成后,用户可以查看各种模拟结果,如流动通量、温度分布、气泡产生和残余应力等。
Moldflow提供了丰富的后处理功能,可以帮助用户深入分析模拟结果。
Moldflow模流分析实例演示本节将通过一个实例来演示如何使用Moldflow进行模流分析。
假设我们要对一个注塑成型的产品进行优化,以确保其尺寸和形状满足设计要求。
步骤1:在Moldflow中导入产品的CAD模型,并进行模型修复和网格生成。
moldflow模流分析实例教程pdf

Moldflow模流分析实例教程PDF介绍本文档旨在为读者提供关于Moldflow模流分析的实例教程,并提供相关知识和步骤。
Moldflow是一种用于模具设计和注塑成型的数值模拟软件,这个软件可以帮助工程师预测塑料制品的成型过程,并优化模具的设计,从而提高产品质量和生产效率。
目录1.准备工作2.模型导入与准备3.模流分析设置4.结果分析与优化5.生成报告与导出PDF1. 准备工作在进行Moldflow模流分析之前,需要准备以下工作和材料:•3D CAD模型•目标塑料材料的物理特性参数•模具和注塑机的几何参数和运行条件2. 模型导入与准备首先,将CAD模型导入Moldflow软件中。
可以使用多种文件格式来导入CAD模型,如STL、STEP、IGES等。
导入后,需要对模型进行清理和修复,确保模型的几何形状完整和连续。
接下来,需要为模型设置注塑模具。
这一步骤包括确定模具的材料、几何参数、喷嘴位置等。
同时,还需要为注塑机设置运行条件,如温度、压力等。
3. 模流分析设置在进行模流分析之前,需要对分析进行设置。
这包括选择合适的计算网格尺寸、设置计算时间步长、指定材料属性等。
为了更好地模拟实际注塑过程,还需要设置模具和注塑机的运行周期。
可以通过定义开模时间、充模时间、冷却时间等来模拟真实的注塑流程。
4. 结果分析与优化在模流分析完成后,可以对结果进行分析和优化。
Moldflow软件提供了丰富的分析工具,如温度分布、注塑压力、填充时间等。
根据这些分析结果,可以对模具设计和注塑工艺进行优化,提高产品质量和生产效率。
5. 生成报告与导出PDF最后,可以生成模流分析报告并导出为PDF格式。
报告中包括模型几何信息、注塑工艺参数、分析结果等。
这些信息可以帮助工程师和决策者了解模具设计和注塑工艺的影响,并根据分析结果做出相应的调整和决策。
结论本文档提供了关于Moldflow模流分析的实例教程,从准备工作到结果分析与优化,逐步介绍了Moldflow的基本流程和操作步骤。
chap7 Moldflow流动分析步骤

华东交大材料成型 匡唐清 模流分析教程
第7章 流动分析步骤 章
使用Moldflow的工程设计过程 的工程设计过程 使用
确定工程分析目的
清楚分析所能得到的结果 需解决或避免的问题 为何要作此分析 分析没有清晰的目的, 分析没有清晰的目的,将浪费时间
与相关部门人员讨论
包括材料、产品设计、模具设计 制造 生产/工艺 制造、 包括材料、产品设计、模具设计/制造、生产 工艺 应认清各部门的要求、关心的问题、 应认清各部门的要求、关心的问题、限制等 应考虑合适开始进行分析
网格生成 网格评估
查看网格质量是否可以接受 若网格太密或太疏, 若网格太密或太疏,应更改全局边长重划网格 华东交大材料成型 匡唐清 模流分析教程
第7章 流动分析步骤 章
充填优化
准备FEM模型 模型 准备
网格修复
网格统计总体查看 网格诊断分项查看 网格修复工具(自动、手动) 网格修复工具(自动、手动)
华东交大材料成型 匡唐清 模流分析教程
第7章 流动分析步骤 章
优化流动
优化保压
浇口和流道的凝固时间 对保压有很大影响。 对保压有很大影响。没 有流道和浇口将大大降 低保压分析的准确性。 低保压分析的准确性。 保压分析前应进行冷却 分析, 分析,冷却分析确定模 壁温度使得保压分析更 为准确( 为准确(充填分析假定 模具恒温) 模具恒温) 保压优化后, 保压优化后,最后一步 优化翘曲
第7章 流动分析步骤 章
充填优化 确定成型条件
成型工艺可通过成型窗口分析和在填充分析中慢 慢调整来决定,成型窗口分析可用来作为材料和 慢调整来决定,成型窗口分析可用来作为材料和 浇口位置对比的快速分析, 浇口位置对比的快速分析,还可用来优化成型工 如能在填充分析前选择好最佳工艺条件的话, 艺。如能在填充分析前选择好最佳工艺条件的话, 将会节约很多的分析时间。 将会节约很多的分析时间。
Moldflow注塑机参数的输入
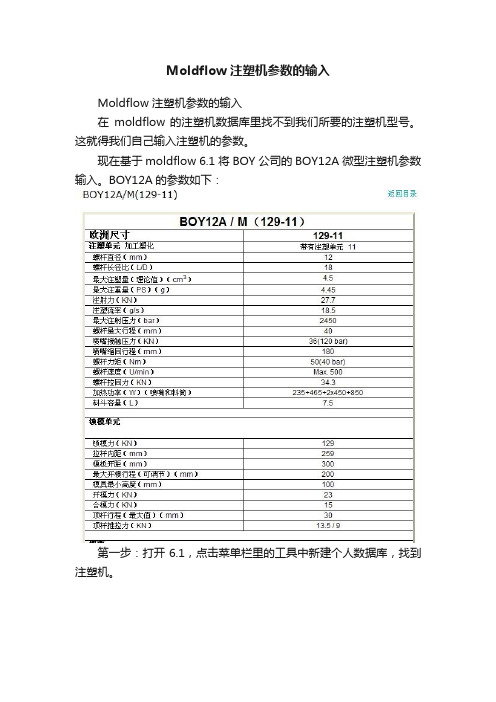
Moldflow注塑机参数的输入
Moldflow 注塑机参数的输入
在moldflow 的注塑机数据库里找不到我们所要的注塑机型号。
这就得我们自己输入注塑机的参数。
现在基于moldflow 6.1 将BOY 公司的BOY12A 微型注塑机参数输入。
BOY12A的参数如下:
第一步:打开6.1,点击菜单栏里的工具中新建个人数据库,找到注塑机。
点击确定,新建
第二步:输入第一栏。
第一栏里都是注塑机的基本信息,如型号、生产厂家等:
第三步:输入第二栏。
第二栏是注塑机注射单元的信息:
第四步:输入第三栏。
第五步:输入第四栏。
完成,点击确定保存。
第六步:调用我们所保存的注塑机参数文档。
点击打开按键选择我们所保存的文件即可。
Moldflow与结构分析软件的数值传递方法

图 2:表层(上图)、剪切层(中图)和核心(下图)位置上有关长纤维取向和长 度分布的 CT 扫描三视图。侧视图中的红线代表仰视图像所处的位置。
在半结晶材料中也可以看到相似的形态特征,图 3(2002 年 Ré gnier)显 示了一种半结晶材料的截面 CT 扫描图像。核心区的晶相通常表现为球状 晶体,其片层(inter-lamellae)结构表示各向异性很低。相反,剪切导致 的结晶却在高剪切区起着重要作用,所以高切区的晶相中包含了取向的 纤维状和串晶状的结构。这些晶体结构是导致非纤维填充的半结晶材料 具有各向异性的主要原因。
析获得各向异性分布的属性和残余应力的结构分析软件。虽然这些均为 基于有限元方法的分析软件,但网格关注点却完全不同。因此,需要在 不同的网格模型之间建立一种准确的映射机制,并且需要高效、无缝地 传输海量的数据。 2: 材性与残余应力的计算 注塑成型产生的残余应力的计算涉及到注塑成型阶段中的压力与温度历 程。残余应力就是模具型腔内冻结在固化的聚合物内的应力,随着温度 的继续下降,其导致的热应力逐渐在模具内的残余应力中占主导地位。 在纤维填充的聚合物复合材料中,为了计算残余应力,需要将局部的热 膨胀系数和刚度属性计算出来。计算出纤维取向张量后这些材性便可以 计算了。由于正交各向异性假设,在每个计算点上采用了以下 9 参数的 取向平均模型(2004 年 Lin 和 Jin 等人提出):
图 6:需要低纵横比的典型结构分析单元类型。
4: 连接的映射策略 传递数据至所有这些结构分析软件所面临的难题是在保留这些单元类型 的同时不违反其为保证精度而设置的基本纵横比要求。将数值分布从一 种类型的网格映射到另一种类型的网格是一种十分合理的策略。然而, 适合大部分单元类型的通用方法是什么呢? 查看这些单元类型时,我们发现大部分单元在其单元域中都有积分点, 如下图所示。这些高斯积分点用来捕捉单元域中的分布情况以提高准确 性的。为了在无需深入分析每种单元类型的情况下找到一种适合大部分 结构分析软件的通用方法,向目标网格的积分点映射所需数值是最好的 方法。
Moldflow Synergy 操作步骤简介

33
15. 指定工艺设置
Moldflow Synergy 2015 操作步骤
MOLDFLOW SYNERGY 2015 流动分析工艺设置 34
16. 运行分析
Moldflow Synergy 2015 操作步骤
点击此处 “作业管理器” “开始分析” 可查看分析进
如不满意网格质量,则重复“步骤7”对网格做进 一步优化.
将已OK的双层面网格复制,以便进行下一步划 分3D几何网格. (任务栏中将其选定点击鼠标 右键选择重复)
17
9. 划分3D几何网格
Moldflow Synergy 2015 操作步骤
“网格” 命令下右上角
将“双层面” “3D”.
OR
右侧任务栏右击 “双 层面网格” “设置网格 类型” “3D”.
Moldflow Synergy 2015 操作步骤简介
操作步骤:
1. 程序启动 2. 新建工程 3. 导入模型文件 4. 划分双层面几何网格 5. 网格统计 6. 诊断网格质量 7. 修复网格 8. 验证网格质量 9. 划分3D几何网格 10. 定义浇口位置
Moldflow Synergy 2015 操作步骤
度
或双击此处 “开始分析”
35
17. 查看结果&创建报告
Moldflow Synergy 2015 操作步骤
点击选择查 看具体结果
双击此处查 看分析结果
36
17. 查看结果&创建报告
Moldflow Synergy 2015 操作步骤
MOLDFLOW SYNERGY 2015 创建 37
38
点击 “立即划分网格”
- 1、下载文档前请自行甄别文档内容的完整性,平台不提供额外的编辑、内容补充、找答案等附加服务。
- 2、"仅部分预览"的文档,不可在线预览部分如存在完整性等问题,可反馈申请退款(可完整预览的文档不适用该条件!)。
- 3、如文档侵犯您的权益,请联系客服反馈,我们会尽快为您处理(人工客服工作时间:9:00-18:30)。
图 3:1 毫米 PP 板的 CT 截面扫描图像
注塑成型塑料零件中由于纤维或晶体取向不光是产生的跨厚度的三明治 结构形态,在空间的不均匀分布也是无法避免的,如图 4 所示的最近通 过 Autodesk Moldflow Insight(AMI)预测的不均匀分布结果。这些预测
工具基于针对短纤维取向、长纤维取向和纤维断裂的复杂计算模型和针 对机械属性和热膨胀系数的微力学模型。只有通过这些模型才能计算注 塑成型导致的残余应力。
图 6:需要低纵横比的典型结构分析单元类型。
4: 连接的映射策略 传递数据至所有这些结构分析软件所面临的难题是在保留这些单元类型 的同时不违反其为保证精度而设置的基本纵横比要求。将数值分布从一 种类型的网格映射到另一种类型的网格是一种十分合理的策略。然而, 适合大部分单元类型的通用方法是什么呢? 查看这些单元类型时,我们发现大部分单元在其单元域中都有积分点, 如下图所示。这些高斯积分点用来捕捉单元域中的分布情况以提高准确 性的。为了在无需深入分析每种单元类型的情况下找到一种适合大部分 结构分析软件的通用方法,向目标网格的积分点映射所需数值是最好的 方法。
1 1 2 2 1 1 e Sklrs Srsij ij ij kl kl S klrs S rsij 1
(2)
1 2 1 2 其中 kl 和 kl 是基体和被包裹体的热膨胀系数张量, S klrs 和 S klrs 是相应的
e 刚度张量, S klrs 是从 (1)计算得到的相应张量。经证明,这个模型符合刚 度张量计算中所用的 Mori-Tanaka 原理(1973 年 Mori 和 Tanaka 提出), 因此被选定为默认模型。
图 4:短纤维材料注塑成型的离合器产品中拉伸模量 E1 的分布。
产生残余应力的原因在于注塑成型过程中跨厚度方向的凝固时间差异, 所形成的压力和温度分布以及模具对固化的聚合物的变形的约束。这些 在注塑件顶出前所形成的残余应力,是注塑件翘曲的驱动因素,因为注 塑件一旦从模具中顶出,注塑导致的残余应力便会开始寻找新的平衡状 态。与平衡的残余应力状态相对应的注塑件变形就是翘曲后的形状,这 就是结构分析中所需要计算的。 计算残余应力需要热膨胀系数和刚度张量在注塑件中的变化分布。由于 聚合物复合材料具有两相的性质,纤维或晶体视为一相,聚合物基体视 为包裹纤维或晶体的另一相,并在 Autodesk Moldflow Insight 软件中使用 了各种针对这些热-机械属性的微力学模型,来计算聚合物基体中纤维或 晶体完全取向一致或取向随机两种特殊形态。然而,纤维或晶体的取向 在整个注塑件中是用张量计算出来的,因此必须在所有计算点上使用一 种取向张量平均算法( Advani&Tucker 1984 ),来计算复合物材性的分 布。只有将这些各向异性属性和通过这些属性计算出的残余应力相结 合,结构分析才有意义。 Abaqus、ANSYS、Nastran 和 LS-DYNA 等主流的结构分析软件都支持使 用各向异性分布的热 -机械属性进行分析,并提供了间接的数据传输方法 以支持该功能的使用。对于注塑成型塑料零件而言, Autodesk Moldflow Insight 能够对整个过程进行仿真,即从注塑成型的填充阶段到脱模后的 翘曲预测。Autodesk Simulation Mechanical 是唯一能够直接从注塑成型分
Moldflow 与结构分析软件的数值传递方法
Autodesk Moldflow 首席研发专家 金小石 Autodesk Moldflow 中国区技术经理 李建 摘要 本文介绍了一种全新的注塑成型引起的残余应力和相应热-机械属性 的映射方法,由于塑料零件在注塑过程中会出现纤维取向和结晶,因此 通常表现为各向异性和非均质属性。这种映射方法能够让大量数据在相 同零件的不同网格模型之间更准确地传递而无需通过接口文件,并且在 注塑成型仿真中所使用的不同材料和应力模型所计算的结果都可以直接 应用到结构分析中。 这种准确性通过一种从适合流动分析的网格到适合结构分析的网格 的点映射机制来实现的,利用了结构分析中的许多单元类型内具有积分 点这一特点。用于注塑成型的塑料零件的重要数据大多数均为张量数 据,如刚度和应力张量。由于纤维取向、热及剪切导致的结晶形态的不 同,每个积分点上的这些数据也不一样。除了刚度张量数据以外,许多 用户都对注塑成型导致的残余应力和热膨胀系数尤为重视。这些数据可 用来在结构分析软件中进行成型后的翘曲的预测,甚至用于后续的再加 工或某种工况载荷下的变形和应力分析。注塑成型分析中用于聚合物复 合材料的微力学模型在数据传输前已经被准确应用,因此这种映射使得 注塑成型分析和结构分析能共享这些特定的微力学模型。 本文所介绍的案例包括了将残余应力传递到结构分析进行翘曲预测的准 确性验证以及注塑成型导致的材料各向异性和刚度张量分布数据的应 用。 1: 介绍 不均匀分布的各向异性材料属性是注塑成型塑料零件的主要特征之一, 尤其是纤维增强材料的塑料零件。在注塑件“冻结”之前,聚合物熔体 中的短纤维会跟随流动方向来确定在自身模具型腔中的取向,从而在高 剪切区形成一个与流动模式相似的取向模式(其中绝大部分纤维的取向 均与流动方向一致),并在厚度中间的核心区域形成一个完全不同的取 向(纤维取向方向通常为随机的或与流动方向垂直)。如图 1 所示,流 体前沿中的泉涌流动将核心区域的纤维方向变为由内向外到模具表面 上,并随着熔体在模具壁上快速冻结,形成一层独特的薄表层。
图 7:一个六边形单元的高斯积分点。
确定这个映射策略后,剩余的工作就是计算这些高斯积分点上的数据分 布,其中大部分为张量数据。然而,大多数结构分析软件无法在高斯积 分点上输入数据,即便可以通过特别的方法从输入文件中提取这些数 据,但输入的数据量会非常庞大。因此,需要将这种映射策略与应用程 序接口(API)结合起来使用,以实现无缝、平滑的数据传输。我们将这
B8 ij akm aml kl aim amj B9 lj akm ami ki alm amj jk aim aml il a jm amk
(1)
其中 aij 和 aijkl 分别是二阶和四阶的纤维取向张量, ij 是克罗内克单位张 量。左边的 C
C
ijkl
B1 aijkl B2 aij kl akl ij B3 aik jl a jl ik ail jk a jk il
B4 ij kl B5 ik jl il jk B6 aij akl B7 aik a jl ail a jk
ijkl
代表平均刚度张量。可使用 Tandon-Weng 单向模型
(1984 年 Tandon 和 Weng 提出)和二维随机模型 (1986 年 Tandon 和 Weng 提出)来计算参数 B1 ~ B9 的值。 热膨胀系数张量是根据 Rosen-Hashin 模型(1970 年 Rosen 和 Hashin 提 出)的张量等价形式(1989 年 Benveniste 和 Dvorak 提出)计算得到的。
图 1 沿注塑成型塑料零件厚度方向的夹层结构形态:其中 S1 代表泉涌流动效应所产 生的表层,S2 代表高剪切导致的高取向对齐区,S3 代表核心区。
即便在塑料行业最近关注的长纤维增强复合材料中,也可以通过纤维取 向分布( FOD )和纤维长度分布( FLD )观察到跨厚度的三明治结构形 态。纤维长度是复合材料最终属性分布的另一个主要因素,如图 2 中 Ticona 所提供的 CT 扫描图像(2010 年 VanAst)所示。
种映射策略部署为一个动态链接库,这是一种称作 Autodesk Moldflow Structural Alliance ( AMSA )的功能,可与任何结构分析软件相集成。 ABAQUS 用户定义子程序(UDS)和 ANSYS 用户可编程特性(UPF)最 先与 AMSA 的功能进行整合。Autodesk Simulation Mechanical 是第一款 将这一功能与包含数千个(热-机械属性的)塑料数据的数据库直接集成 的软件。 5: 示例 如下所示,我们用了一个相机盖模型来评估不同结构分析软件之间翘曲 预测的一致性。我们在 ABAQUS 中使用了一个粗糙的网格模型,但纤维 取向的结果基于 Autodesk Moldflow Insight 中精细网格。如图 8 所示。
图 2:表层(上图)、剪切层(中图)和核心(下图)位置上有关长纤维取向和长 度分布的 CT 扫描三视图。侧视图中的红线代表仰视图像所处的位置。
在半结晶材料中也可以看到相似的形态特征,图 3(2002 年 Ré gnier)显 示了一种半结晶材料的截面 CT 扫描图像。核心区的晶相通常表现为球状 晶体,其片层(inter-lamellae)结构表示各向异性很低。相反,剪切导致 的结晶却在高剪切区起着重要作用,所以高切区的晶相中包含了取向的 纤维状和串晶状的结构。这些晶体结构是导致非纤维填充的半结晶材料 具有各向异性的主要原因。
析获得各向异性分布的属性和残余应力的结构分析软件。虽然这些均为 基于有限元方法的分析软件,但网格关注点却完全不同。因此,需要在 不同的网格模型之间建立一种准确的映射机制,并且需要高效、无缝地 传输海量的数据。 2: 材性与残余应力的计算 注塑成型产生的残余应力的计算涉及到注塑成型阶段中的压力与温度历 程。残余应力就是模具型腔内冻结在固化的聚合物内的应力,随着温度 的继续下降,其导致的热应力逐渐在模具内的残余应力中占主导地位。 在纤维填充的聚合物复合材料中,为了计算残余应力,需要将局部的热 膨胀系数和刚度属性计算出来。计算出纤维取向张量后这些材性便可以 计算了。由于正交各向异性假设,在每个计算点上采用了以下 9 参数的 取向平均模型(2004 年 Lin 和 Jin 等人提出):
这些属性会在下面用于计算残余应力 ( ij )的一般线性-热粘弹性模型中使 用:
T kl kl t t ' dt ' t ' t '