模切浅谈之常见问题分享
模切加工中存在的不良分析
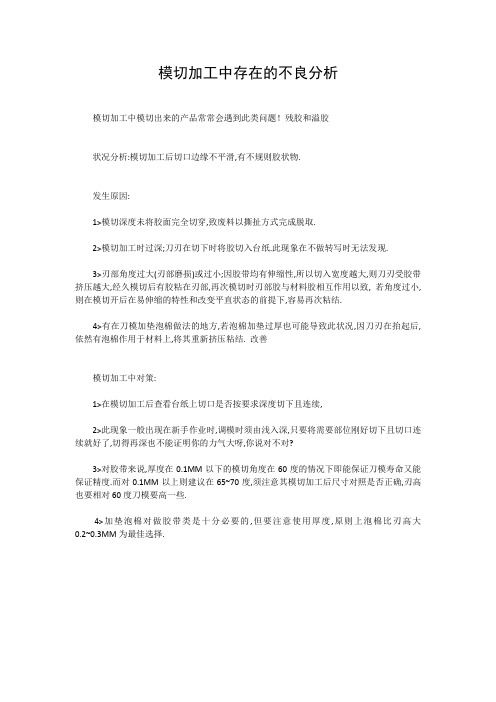
模切加工中存在的不良分析
模切加工中模切出来的产品常常会遇到此类问题!残胶和溢胶
状况分析:模切加工后切口边缘不平滑,有不规则胶状物.
发生原因:
1>模切深度未将胶面完全切穿,致废料以撕扯方式完成脱取.
2>模切加工时过深;刀刃在切下时将胶切入台纸.此现象在不做转写时无法发现.
3>刃部角度过大(刃部磨损)或过小;因胶带均有伸缩性,所以切入宽度越大,则刀刃受胶带挤压越大,经久模切后有胶粘在刃部,再次模切时刃部胶与材料胶相互作用以致, 若角度过小,则在模切开后在易伸缩的特性和改变平直状态的前提下,容易再次粘结.
4>有在刀模加垫泡棉做法的地方,若泡棉加垫过厚也可能导致此状况,因刀刃在抬起后,依然有泡棉作用于材料上,将其重新挤压粘结. 改善
模切加工中对策:
1>在模切加工后查看台纸上切口是否按要求深度切下且连续,
2>此现象一般出现在新手作业时,调模时须由浅入深,只要将需要部位刚好切下且切口连续就好了,切得再深也不能证明你的力气大呀,你说对不对?
3>对胶带来说,厚度在0.1MM以下的模切角度在60度的情况下即能保证刀模寿命又能保证精度.而对0.1MM以上则建议在65~70度,须注意其模切加工后尺寸对照是否正确,刃高也要相对60度刀模要高一些.
4>加垫泡棉对做胶带类是十分必要的,但要注意使用厚度,原则上泡棉比刃高大0.2~0.3MM为最佳选择.。
六种常见模切故障讲解
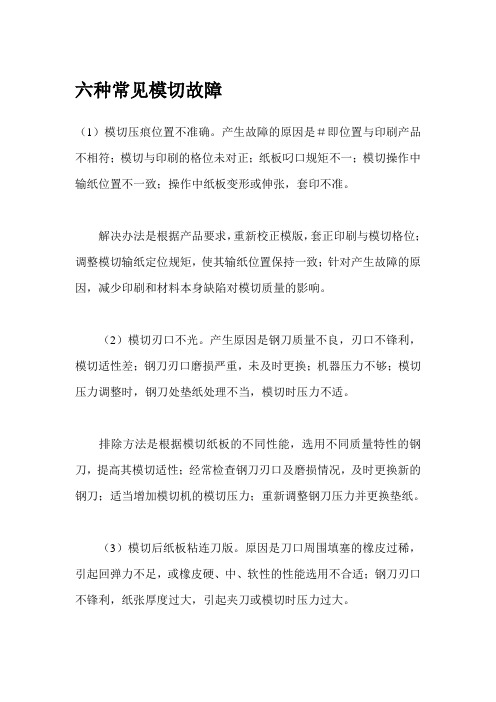
六种常见模切故障(1)模切压痕位置不准确。
产生故障的原因是#即位置与印刷产品不相符;模切与印刷的格位未对正;纸板叼口规矩不一;模切操作中输纸位置不一致;操作中纸板变形或伸张,套印不准。
解决办法是根据产品要求,重新校正模版,套正印刷与模切格位;调整模切输纸定位规矩,使其输纸位置保持一致;针对产生故障的原因,减少印刷和材料本身缺陷对模切质量的影响。
(2)模切刃口不光。
产生原因是钢刀质量不良,刃口不锋利,模切适性差;钢刀刃口磨损严重,未及时更换;机器压力不够;模切压力调整时,钢刀处垫纸处理不当,模切时压力不适。
排除方法是根据模切纸板的不同性能,选用不同质量特性的钢刀,提高其模切适性;经常检查钢刀刃口及磨损情况,及时更换新的钢刀;适当增加模切机的模切压力;重新调整钢刀压力并更换垫纸。
(3)模切后纸板粘连刀版。
原因是刀口周围填塞的橡皮过稀,引起回弹力不足,或橡皮硬、中、软性的性能选用不合适;钢刀刃口不锋利,纸张厚度过大,引起夹刀或模切时压力过大。
可根据模版钢刀分布情况,合理选用不同硬度的橡皮,注意粘塞时要疏密分布适度;适当调整模切压力,必要时更换钢刀。
(4)压痕不清晰有暗线、炸线。
暗线是指不应有的压痕,炸线是指由于压痕压力过重、纸板断裂。
引起故障的原因是:铜线垫纸厚度计算不准确,垫纸过低或过高;铜线选择不合适;模压机压力调整不当,过大或过小;纸质太差,纸张含水量过低,使其脆性增大,韧性降低。
应重新计算并调整钢线剪纸厚度;检查铜线选择是否合适;适当调整模切机的压力大小;根据模压纸板状况,调整模切压痕工艺条件,使两者尽量适应。
(5)折叠成型时,纸板折痕处开裂。
折叠时,如纸板压痕外侧开裂,其原因是压痕过深或压痕宽度不够;若是纸板内侧开裂,则为模压压痕力过大,折叠太深。
可适当减少钢线剪纸厚度;根据纸板厚度将压痕线加宽;适当减小楼切机的压力;或改用高度稍低一些的铜线。
(6)压痕线木规则。
原因是铜线垫纸上的压痕槽留得太宽,纸板压痕时位置不定;铜线垫纸厚度不足,槽形角度不规范,出现多余的圆角,排刀、固刀紧度不合适,铜钱太紧,底部不能同压板平面实现理想接故,压痕时易出现扭动;铜线太松,压痕时易左右窜动。
模切过程中存在六大质量问题及解决办法

模切过程中存在六大质量问题及解决办法1. 模切精度不高精度不高的原因有模切版本身的问题,也有来自印刷品的问题。
手工制作的模切版,误差较大;模切压痕与印刷的作业环境不同会造成纸张变形,导致模切压痕位置不准,尤其是经过上光、覆膜的纸张变形更严重,影响模切精度。
解决办法:选择先进的制版方式,提高模切版的精度:尽量保证模切压痕与印刷在同一作业环境下进行或保证作业环境的同一性(即有相同的温度、湿度等);对上光和覆膜的印张要进行模切预处理,尽量减少纸张变形对模切精度的影响。
2. 模切压痕产生爆线和暗线“爆线”是指由于模切压痕压力过大,超过了纸板纤维的承受极限,使纸板纤维断裂或部分断裂;“暗线”是指不应有的压痕线。
一般是由模切版和压痕钢线选择不合适,模切压力调节不当,纸张质量差,纸张的纤维方向与模切版排刀方向不一致或纸张的含水量低导致纸张柔韧性下降所引起的。
解决方法:选择合适的模切版;适当调节模切机的压力;在模切之前先把要模切的纸张放置在车间里一段时间;加大车间环境的湿度。
另外还有一种特殊情况,就是在模切硬盒烟包小盒时,由于很多位置的压痕线之间距离很近,如果按正常情况配置压痕钢线的高度,模压时对纸张的拉力过大,也会造成爆线。
因此,应设法把对纸张产生的拉力降到最小。
方法有两个:一是降低压痕钢线的高度;二是减少压痕底模条的厚度,两者不能同时使用,否则起不到很好的压痕效果。
较好的方法是降低压痕钢线的高度,降低的高度通常为0.1~0.2mm。
根据纸张厚度确定具体降低多少,定量在350g/m2以上的纸张需降低0.2mm,350g/m2以下的纸张降低0.1mm为宜。
3. 压痕线跑位.不饱满压痕钢线在模切压力的作用下出现扭动会导致压痕线跑位;模切压力不足会导致压痕不饱满。
分别采用更换模切版和加大模切压力的方法可改善此问题。
4. 模切起毛,起尘在模切时,经常会出现模切产品切边不光洁、起毛的现象,特别是一些离压痕线较近的切边处更是严重。
模切常见的问题及处理方法

模切常见的问题及处理方法
模切是一种常见的生产工艺,用于将原材料按照设计要求切割成特定的形状和尺寸。
以下是一些常见的模切问题及处理方法:
1. 尺寸偏差:尺寸偏差是模切过程中常见的问题之一。
处理方法包括调整模切刀具的位置、更换刀具或修改模切设计。
2. 毛刺:毛刺是模切过程中常见的问题之一,通常是由于刀具磨损或刀具不够锋利导致的。
处理方法包括更换刀具或研磨刀具。
3. 压痕:压痕是模切过程中常见的问题之一,通常是由于刀具压力过大或原材料质量不佳导致的。
处理方法包括调整刀具压力、更换原材料或修改模切设计。
4. 切割不彻底:切割不彻底是模切过程中常见的问题之一,通常是由于刀具不够锋利或刀具压力不足导致的。
处理方法包括更换刀具或调整刀具压力。
5. 刀具损坏:刀具损坏是模切过程中常见的问题之一,通常是由于刀具使用时间过长或刀具质量不佳导致的。
处理方法包括更换刀具或研磨刀具。
6. 原材料浪费:原材料浪费是模切过程中常见的问题之一,通常是由于模切设计不合理或原材料质量不佳导致的。
处理方法包括修改模切设计或更换原材料。
总之,模切过程中可能会出现各种问题,需要根据具体情况采取相应的处理方法。
同时,为了避免问题的发生,需要对
模切工艺进行合理的设计和控制,确保原材料质量和刀具的正
常使用。
模切常见质量问题分析及处理 - 副本 - 副本

改用质量好的模切刀
可将纸板进行抽湿处理再进行模切
按纸板厚度合理选择压痕线型号
按纸板厚度和压痕线宽度合理选择痕模切压力大小,纸板含水量过低, 纸板干燥使其脆性变大;纸面纤维抗张强度 差,爆纸情况发生,可在产生爆纸的刀或线 两侧贴8-10mm宽的硬度较大的海绵,用于局 部压扁纸板,减小模切中的纸面拉伸,此外 可在纸板爆裂处泼水加湿处理,便会降低纸 板物理性能,不宜大量、经常使用
模切生产中的质量控制
质量问题
产生原因
解决办法
1)模切刀刃口不锋利,模切钢刀质量差,模切钢刀规格选择 排除方法是根据模切纸板的不 不合理 不同规格的优质模切刀,提高
2)模切刀刃口磨损严重或模切刀变形,
经常检查模切刀的使用情况, 要及时更换模切刀
1、模切刃口纸毛和纸尘
3)模切刀与海绵的选择或安装不规范,
因为海绵胶条应有足够的硬度 张,让模切刀顺利地将纸张切 的纸板选用不财硬度的海绵胶 的安装位置离模切刀身1-2mm 距离太小,如果距离太小,模 绵胶条的受压后,只能向背离 胀,此时纸张还未完全被模切 海绵拉断,这样会产生起毛及 整个模切版上,海绵胶的数量 度,应在各个位置进行均衡的
1)模切刀不够锋利,
3)模切压力过小
适当增大模切压力
4、纸板局部压线爆线
爆线是指模切后的纸板表面纸层开裂,产生的原因:压痕线 型号选择不正确,压痕底模选择不正确,模切压力过大,
适当调整模切压力大小,纸板 纸板干燥使其脆性变大;纸面 差,爆纸情况发生,可在产生 两侧贴8-10mm宽的硬度较大的 部压扁纸板,减小模切中的纸 可在纸板爆裂处泼水加湿处理 板物理性能,不宜大量、经常
可根据模切刀分布选择硬度适中的海绵,密 适度的分布黏贴
改用质量好的模切刀
浅谈模切暗线爆裂原因分析与故障排除

浅谈模切暗线爆裂原因分析与故障排除在纸品包装的印后加工中,模切、压痕是一道重要的工序,它是通过用钢刀和钢线排成的模切版,在模切机上把承印物切成一定的形状、压出痕迹或用于弯折的槽痕,用于弯折的槽痕俗称为暗线。
对暗线的质量要求是宽窄合适,清晰饱满、不爆裂、成型好。
爆裂是一个比较常见的质量问题,其原因多种多样,有的比较直观,有的比较隐蔽,本文试从以下几方面进行分析。
压力不当1.底版暗线里有异物,导致暗线压力剧增是爆裂的常见原因,也是最具破坏性的原因,它往往使暗线整体断裂,导致产品报废,但也较直观,容易判断和解决,只要及时清理干净异物即可排除故障。
对此,在模切过程中要保证底版的清洁,避免异物进入模切机,确保压合部工作顺畅。
2.跑版,即模切版或底版走位。
使得钢线往往压在暗线槽边上,引起较大面积暗线爆裂,并主要集中在同一方向的暗线上。
发现这种情况时应立即重新上版,并锁定模切版和底版。
3. 根据模切工艺的要求,对于不同的纸张应选用不同的钢线,以及不同厚度的底版和不同的暗线槽宽,如果不匹配,也容易引起暗线爆裂。
下面是一种常用的计算方法,供大家参考。
(1)模切卡纸设A:底纸厚度,B:暗线槽宽,C:卡纸厚度,D:钢线厚度,则应有:D≥C;A≤C;B=(C×1.5)+D(2)模切瓦楞纸板设A:底纸厚度,B:暗线槽宽,C:瓦楞纸板(卡裱瓦)厚度,D:钢线厚度,E:压平后瓦楞纸板厚度,则应有:D≥E;A≤E;B=(E × 2)+D一般来讲,在保证暗线不爆裂的情况下,暗线槽要尽量窄,这样暗线饱满、容易弯折,产品成型好,尤其是PET类的纸张,暗线槽要比一般的产品窄一些,但是暗线槽太窄,易引起暗线爆裂。
印品表面处理不当1.压纹的影响压纹工艺是近年来新兴的表面整饰工艺,它通过一个带花纹的钢辊和一个硬质羊毛辊对纸张进行挤压,在纸张表面压出所需的纹路。
压纹工艺开始时仅限于贺卡,台历和书籍的扉页上,而后逐步被纸质包装产品广泛采用。
模切中存在的质量问题及其解决方法

解决 方 法 :首先 要根 据纸 张选 用不 同类 型 的模切 刀 。模 切 刀包括 直 纹 刀和 横 纹 刀 两 种 纹路 的 刀锋 又有高 矮 之分 刀锋 形成 的纹 路和 高 矮不 同 直 接 关系 到 模切 质 量和模 切 刀 的使 用寿 命 。在避 免模 切 起毛 方 面 直纹 刀 比横纹 刀好 在使 用寿 命方 面 矮 锋 刀 比高 锋 刀好 。在 模切 覆 膜 卡 纸 时 应 选 用直 纹 高 锋 刀 要求 刀锋 是 磨 制 的 .最好 不要 采 用压 凹凸一 次
. 一 . .
时 间 :提高 车 间环境 的相 对 湿度 。
另外 还 有 一 种 特 殊 的 情 况 ,就 是 在 模 切 硬 盒 烟 包 小 盒 时 , 由于 很 多 位 置 的压 痕 线 之 间 距 离 很 近 ,如 果 按 正 常 情 况 配 置 压 痕 钢 线 的高 度 模 压 时 对 纸 张 的拉
切 版和 压 痕 钢线 选择 不 合适 模 切 压 力调 节 不 当 纸 张
线 不 饱满 。
3 28 2 0 0
j; t0
目 警 - :l 0 蛹 _
印技 包 装 印 刷 术・ 装 潢 刷
维普资讯
技术看台
专 题报道
解决方法 :分别采用更换模切版和加大模切压力的方法可改善此问题。
压 痕 钢 线 对 纸 张 产 生 的 拉 力 。如 模 切 定 量 为 3 0 / 的纸张 时通 常选 用0 4 m ×1 r m 0 g m r a 3 a
版 的精 度 。尽 量保 证 模切 压 痕 与印 刷过 程在 同一 作 业 环 境 下 进 行 或保 证 作 业 环境 的 同一 性 ( 即相 同 的温 度 相 对 湿 度等 ) ;对 上 光 和 覆膜 后 的纸 张要 进行 模 切 预处 理 .尽 量减 少纸 张 变形对 模切 精度 的影 响 。
浅谈模切生产工艺中存在的问题及其解决方案

浅谈模切生产工艺中存在的问题及其解决方案模切技术在印刷、标签等行业中技术已较成熟,但是在其工艺生产中还是存在一定的问题。
如在产品的检验中,常常发现许多模切制造的产品爆线或者切边起毛等质量问题,这些问题常常都是因为模切制造过程中的一些环节未能准确把握的原因。
针对模切生产过程中存在的一些问题,本文进行了总结并分析。
爆线现象及其对策模切工艺生产中,爆线问题是最常见的问题之一,也是非常值得引人关注的问题。
引发爆线问题的因素也非常多,主要有工作较长时间后有可能模切版上的压痕钢线发生松动、有异物与压槽中、模切压力太大和压痕钢线太高等原因。
详细分析爆线问题的原因后,我们得出以下几种解决方案:1.1.调节模切压力、底模、压痕钢线模切工艺生产中,模切压力、底模、压痕钢线能够较大的影响印品的质量,在使用过程中需调节准确,否则很容易引起爆线。
1.1.1.调节压痕钢线高度时需充分考虑纸张定量因素。
如果纸张定量较低,相应的压痕钢线高度也设置的高一点;也就是说,如果纸张定量较高则相应的压痕钢线高度也降低一些。
在实际模切工艺生产中,如果在同一批的模切原件中含有不同的纸张定量原件,则最好进行分开操作并根据不同的纸张定量原件调节压痕高度,否则十分容易导致爆线问题。
1.1.2.底模痕槽与压痕钢线这两者的高度应该相匹配,这样可以很大程度的降低爆线发生概率,从而得到良好的压痕效果。
1.1.3.长时间工作后,模切版上的压痕钢线常常会有松动现象,容易引起套准偏差、压痕槽和底模错位、压痕线发生偏斜等质量问题。
这样会引发大量的爆线现象,且爆线现象大多数都位于压痕线边缘。
一旦出现此类问题,就需要底模换新或者重新安装模切版上的压痕钢线。
1.1.4.在产品模切工艺生产过程中,为有效防止爆线的产生,需明确并有效协调模切的局部和全局压力。
调节局部压力可通过增加垫纸的方法来实现,全局压力则直接调节模切设备有关参数即可。
1.2.根据产品工艺的不同进行调节模切工艺实施之前,因不同的产品具有特有的性能需求,有时候需要添加一些印后工序,比如UV上光、覆膜等等,这些印后工序对最终的产品模切质量影响较大。
彩盒模切常见11大问题

彩盒模切常见11大问题模切是彩盒加工中的关键步骤,如何保证模切质量是印刷厂非常关注的问题。
目前彩盒印刷厂面临的主要难题是换版时间长、印到切的精度差、模切质量不佳、纸毛多、连接点太多太大、痕线不规则、生产速度慢、废品率高等。
下面介绍几种较为常见的质量问题及其解决方法,希望能对各位同仁有所帮助。
1、模切精度不高问题原因:模切精度不高的原因有模切版本身的问题,也有印刷品的问题。
手工制作的模切版误差较大;模切压痕与印刷过程的作业环境不同会造成纸张变形,导致模切压痕位置不准,尤其是经过上光、覆膜后,纸张的变形更为严重,影响模切精度。
解决办法:选择先进的模切版制版工艺,提高模切版的精度。
尽量保证模切压痕与印刷过程在同一作业环境下进行,或保证作业环境的同一性(即相同的温度、相对湿度等);对上光和覆膜后的纸张要进行模切预处理,尽量减少纸张变形对模切精度的影响。
2、模切压痕产生“爆线”和“暗线”问题原因:“爆线”是指由于模切压痕的压力过大,超过了纸张纤维的承受极限,使纸张纤维断裂或部分断裂;“暗线”是指不应有的压痕线,一般是由于模切版和压痕钢线选择不合适、模切压力调节不当、纸张质量差、纸张纤维方向与模切版排刀方向不一致、纸张含水量低导致柔韧性下降等原因所引起的。
解决方法:选择合适的模切版;适当调节模切压力;在模切之前先把待模切的印刷品在车间里放置一段时间;提高车间环境的相对湿度。
天津长荣印刷设备股份有限公司另外还有一种特殊的情况,就是在模切硬盒烟包小盒时,由于很多位置的压痕线之间距离很近,如果按正常情况配置压痕钢线的高度,模压时对纸张的拉力过大,也会造成“爆线“。
因此,应设法把对纸张产生的拉力降到最小,方法有两个:一是降低压痕钢线的高度;二是减少压痕底模条的厚度,但两者不能同时使用,否则起不到很好的压痕效果。
较好的方法是降低压痕钢线的高度,降低的高度通常为0.1~0.2mm,具体要根据纸张定量确定,定量在350g/m2以上的纸张需降低的压痕钢线的高度为0.2mm,定量在350g/m2以下的纸张宜降低0.1mm。
模切压痕常见的质量问题

模切压痕常见的质量问题
模切压痕是一种常见的加工工艺,用于在材料表面产生所需形状的切割或压痕。
在进行模切压痕时,可能会出现一些常见的质量问题,下面我将从多个角度分别介绍这些问题。
首先,模切压痕的常见质量问题之一是切割或压痕不清晰。
这可能是由于模切刀具磨损、材料质地不均匀或者模切参数设置不当所致。
为了解决这一问题,可以定期更换模切刀具、选择适当的材料或者调整模切参数。
其次,模切压痕时可能会出现材料边缘起毛、毛刺或者裂纹。
这些问题通常是由于模切刀具不锋利、模切速度过快或者材料本身质地脆弱所导致的。
解决这些问题的方法包括定期维护模切刀具、降低模切速度或者选择更适合的材料。
另外,模切压痕过程中可能会出现尺寸不准确的问题。
这可能是由于模切设备的精度不够、材料在模切过程中发生变形或者模切参数设置不当所致。
解决这一问题的方法包括定期校准模切设备、优化模切工艺以及选择合适的材料。
此外,模切压痕过程中还可能出现模切位置偏移、模切深度不一致等问题。
这些问题可能是由于模切设备的稳定性不够、操作人员技术不熟练或者模切刀具磨损严重所致。
为了解决这些问题,可以加强对模切设备的维护保养、培训操作人员技术以及定期更换模切刀具。
总的来说,模切压痕的常见质量问题包括切割或压痕不清晰、材料边缘起毛、毛刺或者裂纹、尺寸不准确以及模切位置偏移、模切深度不一致等。
解决这些问题需要综合考虑模切设备、刀具、材料和工艺参数等多个因素,以确保模切压痕的质量达到要求。
希望以上回答能够满足你的要求。
模切浅谈之常见问题分享

在模切过程当中,每天都会遇到很多小问题,有的甚至让人搞得焦头烂额、头疼不已。
在这里我们就把工作当中的一些问题列出来跟大家分享一下,本人接触的是平刀和辅料类的模切,所以也就跟大家讨论一下普通常见的问题,没关注到或有更好的方法大家多多探讨。
问题1、产品底纸冲穿或不断。
这个分两个方面来看:一是全部冲穿、一是局部冲穿。
从原因上来分析,首先了解你的模具刀锋是否损坏不够锋利。
产品整个冲穿检查你的模切机是否压力不稳定,或是你的模切速度快慢不均,还有的是停机后再开机出现压力不稳,反复检测证实原因后检修你的模切机。
产品局部冲穿检查你下模板是否局部垫得太多,一般调模要求只垫一层胶带最多2层,下模板不能冲切太深。
垫模板选择硬质板,会增加你模切的稳定性,比如:电木板、PET板、亚克力板有的甚至会用铁皮。
问题2 、产品变形。
检查模具没有问题当冲切出来的产品尺寸有出入。
检查你的垫刀棉使用是否恰当(高度、厚度、硬度、弹力等)?这里就不说用什么材料,不一样的产品不一样的要求选材要求都不同,这种我们叫做挤压变形。
再者就是检查你的模切材料是否有贴合是张力控制不均,导致冲出来后产品收缩。
这种体现最明显的就是PE保护膜类或海绵胶类,遇到这样的产品就要在复合的环节控制好材料的张力,减少在模切后产品收缩。
如果张力方面没办法控制到一点都不收缩,记录好你的贴合张力,不同的产品先模切实验,收缩多少将模具相应的放大或缩小多少,下次生产相同产品按照之前参数作业。
还有一个产品变形就是原材料的因素,比如橡胶或海绵类。
这种材料在冲切的时候注意模具角度,一般选择单锋刀,垫刀棉根据实际情况选择高度和硬度。
问题3、细小边类产品模切变形。
为什么把这个分开来说,是因为两个问题性质不一样。
要求不高的产品一般边距太小(0.8mm)以内我们会选择做跳步模,内外框套为冲切。
这种做法在模具成本和调模上面会轻松很多,弊端就是产品尺寸多靠模切机性能和模切师傅控制,容易出现尺寸不良(主要是套位不准、偏位)。
模切使用PET离型膜常见问题及原因排查
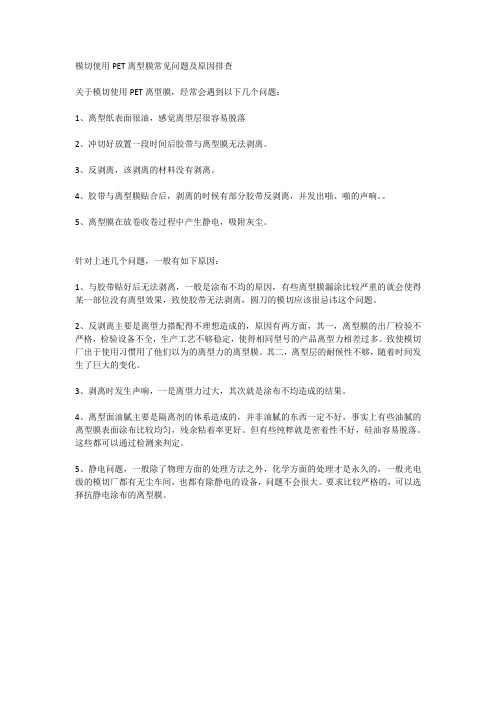
模切使用PET离型膜常见问题及原因排查
关于模切使用PET离型膜,经常会遇到以下几个问题:
1、离型纸表面很油,感觉离型层很容易脱落
2、冲切好放置一段时间后胶带与离型膜无法剥离。
3、反剥离,该剥离的材料没有剥离。
4、胶带与离型膜贴合后,剥离的时候有部分胶带反剥离,并发出啪、啪的声响。
5、离型膜在放卷收卷过程中产生静电,吸附灰尘。
针对上述几个问题,一般有如下原因:
1、与胶带贴好后无法剥离,一般是涂布不均的原因,有些离型膜漏涂比较严重的就会使得某一部位没有离型效果,致使胶带无法剥离,圆刀的模切应该很忌讳这个问题。
2、反剥离主要是离型力搭配得不理想造成的,原因有两方面,其一,离型膜的出厂检验不严格,检验设备不全,生产工艺不够稳定,使得相同型号的产品离型力相差过多。
致使模切厂出于使用习惯用了他们以为的离型力的离型膜。
其二,离型层的耐候性不够,随着时间发生了巨大的变化。
3、剥离时发生声响,一是离型力过大,其次就是涂布不均造成的结果。
4、离型面油腻主要是隔离剂的体系造成的,并非油腻的东西一定不好,事实上有些油腻的离型膜表面涂布比较均匀,残余粘着率更好。
但有些纯粹就是密着性不好,硅油容易脱落。
这些都可以通过检测来判定。
5、静电问题,一般除了物理方面的处理方法之外,化学方面的处理才是永久的,一般光电级的模切厂都有无尘车间,也都有除静电的设备,问题不会很大。
要求比较严格的,可以选择抗静电涂布的离型膜。
模切问题点全解-共16页

一、模切机常见问题与解决方案输纸部分1. 走纸不稳,需经常调节该故障主要是针对国产模切机而言的,由于国产模切机多数没有采用带吸气的传送带,容易导致走纸不稳,纸张定位精度不高,输纸导轮、输纸带、压纸毛轮、前规挡块.侧规挡块等容易磨损。
在走纸之前对纸张进行敲纸、打边并在走纸过程中加以调节可有效解决此问题。
2. 输纸不顺畅引起输纸不顺畅的原因有多种,主要为纸张变形、印刷品表面过于光滑或由其他机械故障引起。
(1) 由纸张变形引起的输纸不顺畅由于模切加工是整个印刷加工最末端的一道工序,纸张经过若干工序加工后容易产生变形,特别是经过高温、高压的上光.覆膜后的纸张变形更加严重,这时飞达往往不能 J 顷利地送纸。
(2) 由印刷品表面过于光滑引起的输纸不顺畅上光覆膜后的产品由于其表面过于光滑,也会给输纸造成一定的困难。
对于以上两种情况,有经验的操作人员会在上纸之前做好前期准备工作,比如:装纸时,在纸张中加入一些木楔子或纸卷使纸张保持平整,在上纸时预先进行打边、敲纸工作或把模切机的速度适当降低,一般可以避免此问题的发生。
(3) 机械故障引起的输纸困难飞达吸嘴吸力不够、距离纸堆上平面的位置不合适、规矩的定位不准确等机械原因会造成输纸过程中出现斜张,双张、空张等故障。
只要平时做好模切机保养工作和机械部位的调节就会避免由于机械故障产生的输纸困难二、模切机模切部分常见问题与解决方案。
A.压力不均匀模切压痕过程中压力不均匀,一般有两种情况:1. 如果压力有轻微的不均匀,可能是由于模切刀、线(钢刀、钢线)分布不均,造成动平台在模切时受力歪斜所致,此时应在模切版上加装平衡刀线,使平台受力均匀。
2. 如果平台前后成四角处出现比较严重的压力不均匀现象,则主要是支撑动平台的四个连杆摆杆高度不一致造成的,此时应打开模切底座的护罩,检查摆杆是否磨损,如磨损严重则需更换,否则需要调整四个压力调整斜铁,直到压力一致为止。
B.模切精度不高模切的精度是衡量模切质量最为重要的标准之一,是生产出合格产品的重要保证,在实际生产过程中,常常出现模切精度达不到设计要求的情况。
模切压痕常见的质量问题

模切压痕常见的质量问题全文共四篇示例,供读者参考第一篇示例:模切和压痕作为印刷后加工的重要环节,常常会出现一些质量问题,影响整个产品的质量和美观度。
下面就来详细介绍一些模切压痕常见的质量问题,以及如何避免和解决这些问题。
1. 边缘不整齐:在模切或压痕过程中,如果刀具或模具使用不当,会导致产品边缘不整齐,甚至出现错位或切断现象。
这种问题会给产品的外观带来很大影响,降低整体质量。
解决方法是选择质量好的刀具或模具,确保模切和压痕的精准度。
2. 压痕深浅不一:在压痕过程中,如果压力不均匀或调节不当,容易导致压痕深浅不一的情况出现。
这会导致产品表面不平整,影响整体美观度。
解决方法是严格控制压力和调节参数,保证压痕的一致性。
3. 模切残留:有时模切或压痕后会出现一些残留物,如纸屑或碎片,这不仅会影响产品的整洁度,还会在后续加工过程中产生不良影响。
避免这种问题的方法是及时清理模切或压痕后的残留物,保持产品表面干净。
5. 模切位置不准确:模切或压痕的位置不准确会导致产品尺寸不匹配或错位,影响产品的使用效果。
避免这种问题的方法是在设计模切或压痕位置时,慎重考虑并确保准确性。
模切和压痕是印刷后加工中非常重要的步骤,质量问题会直接影响整体产品的质量和美观度。
为了避免这些问题的发生,印刷厂家和加工厂家需要定期检查设备和工具的状况,加强员工培训,规范操作流程,确保产品质量。
只有这样,才能生产出高质量的产品,满足客户需求。
第二篇示例:模切压痕是一种常见的加工方法,广泛应用于各种行业的生产中,如印刷包装、电子产品制造、纸品制作等。
模切压痕的质量直接影响到产品的成型质量和使用效果,因此需要对常见的质量问题及其解决方法有所了解。
下面将就模切压痕常见的质量问题进行详细介绍。
一、模切压痕常见的质量问题1. 压痕不清晰压痕不清晰是模切过程中比较常见的质量问题,主要表现为压痕不规整、边缘生毛等。
造成该问题的原因可能有以下几点:(1)模刀磨损严重,刀口不锋利;(2)模刀与底板的间隙设置不合理;(3)受压力不均匀,导致部分区域的压痕不清晰。
模切压痕工艺常见问题及对策

1.模切压痕线位置不准(1)模切刀版制作时有误差;应选择先进的制版方式。
(2)纸板叼口规矩不一;应选择高精度模切机RFID,并增大后定位距离。
(3)模切版与印品未对正;应重新校正模切版或前规、侧规来调整印品的位置。
RIP境不同,造成纸板纤维变形也会使模切压痕线位置不准;应尽量保证模切压痕与印刷在同一环境下进行。
2.压痕线不清晰,有“暗线”或“炸线”(1)压痕钢线和压痕模的选择不合适,应按照以下公式选择。
①若待模切材料为白板纸,压痕模和压痕钢线应满足:压痕模槽深=纸厚;压痕模槽宽=纸厚×1.5+压痕钢线厚度;压痕钢线高度=模切刀高度-纸厚±0.05mm。
②若待模切材料为瓦楞纸输纸,压痕模和压痕钢线应满足:压痕模槽深=瓦楞纸压实时的纸厚;压痕模槽宽=瓦楞纸厚×2+压痕钢线厚度;压痕钢线高度=模切刀高度-瓦楞纸压实时的纸厚。
(2)模切压力调整不当;应通过调压机构调整压力大小。
(3)固定垫板粘贴的厚度不准确;调整方法是重新垫纸。
发展史脆性增大,韧性降低,从而产生“炸线”;可以通过增大环境湿度来解决。
3.压痕线不规则(1)压痕模的槽宽不合适;应按上述方法重新选择。
(2)模切刀版上的线缝太宽,压痕钢线在压力作用下出现扭动;应更换使用合格的模切刀版。
4.折叠糊盒时,纸板折痕处开裂分切原因是压痕线过深或压痕模宽度不够数码印刷印后加工,若内侧开裂,则多为模切压痕压力过大使纸纤维断裂所致;应适当减小模切压力,改用高度稍低一些的压痕钢线,或根据纸板厚度将压痕钢线加宽,并使用槽深小、槽宽大的压痕模。
5.模切时纸板与刀版黏连(1)模切刀周围粘贴的胶条过少或胶条硬度太小设备维护与保养,引起回弹力不足;可根据模切刀分布情况合理选用不同硬度的胶条。
(2)模切刀不锋利,或纸张厚度过大;须更换模切刀。
6.模切散版(1)模切连点小且数量少;应适当增加连点数量,制版时尽量使印品长度方向同纸张传输方向保持一致。
印刷模切中常见问题
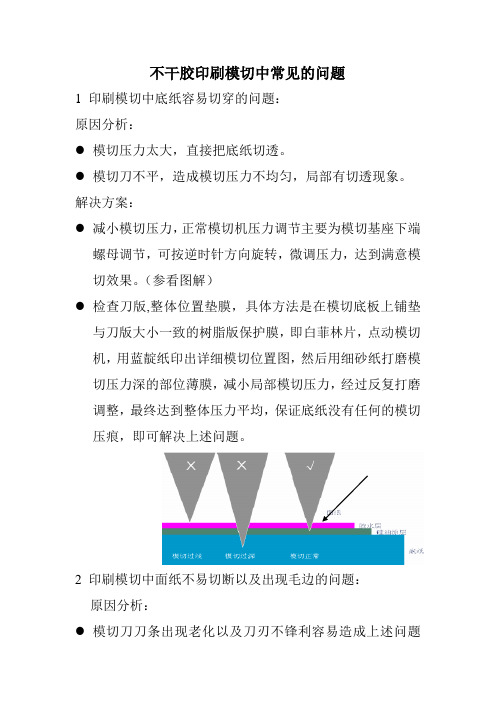
不干胶印刷模切中常见的问题1 印刷模切中底纸容易切穿的问题:原因分析:●模切压力太大,直接把底纸切透。
●模切刀不平,造成模切压力不均匀,局部有切透现象。
解决方案:●减小模切压力,正常模切机压力调节主要为模切基座下端螺母调节,可按逆时针方向旋转,微调压力,达到满意模切效果。
(参看图解)●检查刀版,整体位置垫膜,具体方法是在模切底板上铺垫与刀版大小一致的树脂版保护膜,即白菲林片,点动模切机,用蓝靛纸印出详细模切位置图,然后用细砂纸打磨模切压力深的部位薄膜,减小局部模切压力,经过反复打磨调整,最终达到整体压力平均,保证底纸没有任何的模切压痕,即可解决上述问题。
2 印刷模切中面纸不易切断以及出现毛边的问题:原因分析:●模切刀刀条出现老化以及刀刃不锋利容易造成上述问题发生。
●模切压力不足也容易导致上述问题发生。
解决方案:●检查并更换刀版的模切刀条,区分模切纸类和膜类材料的区别。
参看图解,刀条刀刃角度较宽的适合模切纸类材料,刀条刀刃较窄的适合模切膜类材料。
主要应用在圆刀模切上。
●增加模切刀版压力,顺时针旋转模切机压力螺母,调到合适压力。
3印刷模切中出现的溢胶问题:原因分析:•模切刀条老化以及刀刃不锋利,参看图解2,刀刃磨损钝化后,模切纸张时,胶水被挤向两边,面纸虽被切断,但是胶水没有完全被切断,造成排废时胶水拉丝及胶水回流,形成溢胶。
•模切刀胶丝未完全切断,参看图解1,造成排废拉丝。
•模切压力太深硅油层及底纸被切穿,造成胶水被挤入底纸中,导致排完费边后,标签周围有胶水残留,形成溢胶现象。
•收卷过程中,因为收卷张力过大,造成标签缠绕过紧形成溢胶及标签移位,,主要体现在卫星轮转机和有张力收卷的间歇机上。
解决方案:•更换刀条保持刀刃锋利,并在刀刃上喷涂少量硅油脱模剂,杜绝模切后标签与排废边再次重新复合,影响排废效果。
•调整模切压力与模切刀的平整。
•减小收卷张力,避免张力过大造成标签移位及胶水溢出,具体张力数值依据轮转机机器型号不同,而有所区别,主要张力数值控制在8-16之间,具体数值可咨询机器制造厂家,张力数值大小调节主要体现在纸类收卷和膜类收卷上,膜类收卷张力普遍要小于纸类收卷张力。
不干胶标签模切技术经验谈(四)

不干胶标签模切技术经验谈(四)模切排废带标问题解析1.模切深度不够如果模切刀未将面材完全切断,排废边易将标签带走而出现“飞标”现象。
未将胶黏剂层完全切断亦会引起排废带标,由于排废边下面的胶黏剂与标签下面的胶黏剂发生粘连,标签会被断断续续地带起,并会出现拉丝现象。
2.模切后胶黏剂回流环境温度较高时,胶黏剂的流动性增强,如果模切工位与排废工位相隔较远,易使原先切断的胶黏剂层回流粘连,此时排废边带标的位置不固定,且带标的个数时多时少。
将标签与排废边分开时,可以看到明显的拉丝现象。
这与胶黏剂层未切断而引起的拉丝现象相似(如图1所示),可通过染色法对两者进行区分:胶黏剂回流的标签,模切深度比较深,在底纸硅油层表面能看到模切刀痕;若是胶黏剂层没有完全切断,模切深度比较浅,在底纸硅油层表面的刀痕印迹也很浅,或根本看不到刀痕印迹。
缩短模切工位和排废工位的间距,可使胶黏剂回流的概率大为下降。
而增大排废角度能够减少拉丝现象的出现。
小尺寸排废辊和大排废角度都能在一定程度上迅速剥离排废边,减轻其与标签胶黏剂层的粘连程度,帮助标签与排废边分离。
3.模切刀有瑕疵当排废边带起的标签总位于同一个位置时,可小心地将标签从排废边上揭下,使用放大镜仔细观察标签从排废边揭下时粘连的位置,如果发现存在被拉断的纸纤维,通常不是模切刀有缺口就是刀已经钝了,或是此处的承压位置下陷。
这是由于模切刀问题导致面材未充分切断、标签被排废边带走的常况,与模切刀头尾部位有缝隙出现的情形和似。
4.排废边面积过大对于圆形、鼓形或一些特殊外形的标签,排废边面积与标签面积的比值越大,排废时废边对标签的拉扯力就越大,也越容易带走标签。
在模切刀版的排废边处增加刀片,可使排废时作用力分散,就不容易产生带标问题。
如图2所示。
5,不干胶剥离力偏低不下胶的剥离力偏低会使模切收纸过程中产生“飞标”。
不干胶剥离力偏低的原因主要有两个:①不干胶材料的剥离力本来就设置得偏低,或者不干胶材料储存时间过长,使胶黏剂和硅油发生变异。
常见不干胶模切质量问题释疑
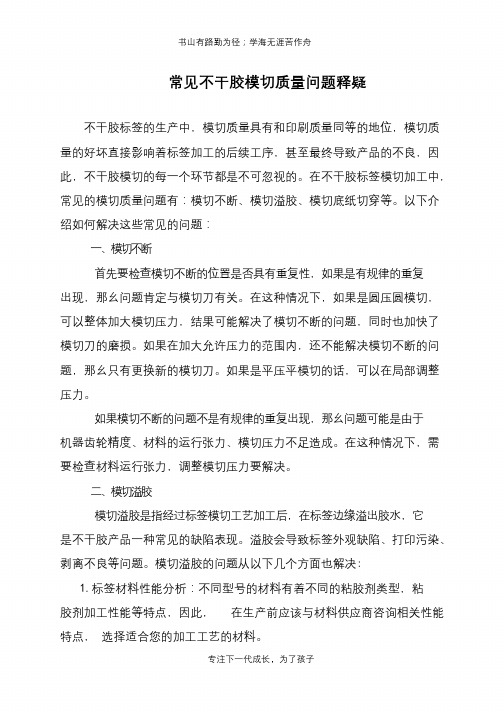
书山有路勤为径;学海无涯苦作舟
常见不干胶模切质量问题释疑
不干胶标签的生产中,模切质量具有和印刷质量同等的地位,模切质量的好坏直接影响着标签加工的后续工序,甚至最终导致产品的不良,因此,不干胶模切的每一个环节都是不可忽视的。
在不干胶标签模切加工中,常见的模切质量问题有:模切不断、模切溢胶、模切底纸切穿等。
以下介绍如何解决这些常见的问题:
一、模切不断
首先要检查模切不断的位置是否具有重复性,如果是有规律的重复
出现,那幺问题肯定与模切刀有关。
在这种情况下,如果是圆压圆模切,可以整体加大模切压力,结果可能解决了模切不断的问题,同时也加快了模切刀的磨损。
如果在加大允许压力的范围内,还不能解决模切不断的问题,那幺只有更换新的模切刀。
如果是平压平模切的话,可以在局部调整压力。
如果模切不断的问题不是有规律的重复出现,那幺问题可能是由于
机器齿轮精度、材料的运行张力、模切压力不足造成。
在这种情况下,需要检查材料运行张力,调整模切压力要解决。
二、模切溢胶
模切溢胶是指经过标签模切工艺加工后,在标签边缘溢出胶水,它
是不干胶产品一种常见的缺陷表现。
溢胶会导致标签外观缺陷、打印污染、剥离不良等问题。
模切溢胶的问题从以下几个方面也解决:
1.标签材料性能分析:不同型号的材料有着不同的粘胶剂类型,粘
胶剂加工性能等特点,因此,在生产前应该与材料供应商咨询相关性能特点,选择适合您的加工工艺的材料。
专注下一代成长,为了孩子。
【管理】模切工厂管理中常见的16大问题点,条条致命!
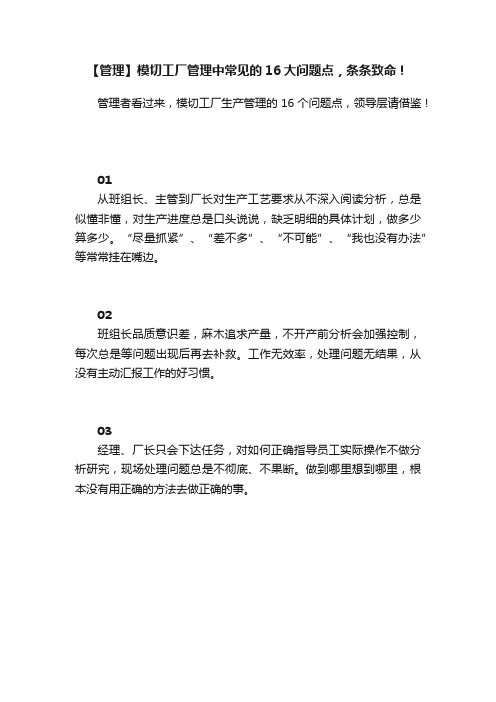
【管理】模切工厂管理中常见的16大问题点,条条致命!管理者看过来,模切工厂生产管理的16个问题点,领导层请借鉴!01从班组长、主管到厂长对生产工艺要求从不深入阅读分析,总是似懂非懂,对生产进度总是口头说说,缺乏明细的具体计划,做多少算多少。
“尽量抓紧”、“差不多”、“不可能”、“我也没有办法”等常常挂在嘴边。
02班组长品质意识差,麻木追求产量,不开产前分析会加强控制,每次总是等问题出现后再去补救。
工作无效率,处理问题无结果,从没有主动汇报工作的好习惯。
03经理、厂长只会下达任务,对如何正确指导员工实际操作不做分析研究,现场处理问题总是不彻底、不果断。
做到哪里想到哪里,根本没有用正确的方法去做正确的事。
04关键时刻厂长、车间主管缺乏主动性及现场统筹、组织指挥能力,每次出货总是忙、乱、差、错。
05品质出了问题不是先解决为快,而是在办公室追究对证、扯皮、责怪、骂人、逃避和推御责任。
06部门之间团结协作意识差,总是以自我为中心,不顾大局,从不主动与他人沟通协作,心胸狭窄者甚至给工作设置阻力。
07大多数车间主管、组长通常喜欢说:“我跟他说过了”、“真麻烦”、“差不多就行了”等不负责任的话。
品质第一的意识十分淡薄。
08厂长、主管、组长缺乏成本核算、数字和表格规范管理的概念,从不做规范的现场记录,对流量从不知如何控制,积压大量半成品出不了成品,交到最后一道工序需大量回修。
09部门之间工作不协调,岗位职责不清,每天工作无计划、行动无目标、作业人员缺乏责任感。
业务员、采购员、技术员之间、部门之间缺乏沟通和讨论。
10现场生产流程管理不规范,程序混乱无先后,组长不会写工序、测工时,计件工价不合理,造成员工情绪化,每到月终发工资总有员工闹到办公室或找老板投诉。
11生产工艺资料编写格式既不标准化又不规范化发放,什么资料该发给谁?谁审核?转交给谁?如何存档编号装订等等,看上去总是乱糟糟,要寻一份资料更是难上难。
客人验货时甚至连样板都找不到。
- 1、下载文档前请自行甄别文档内容的完整性,平台不提供额外的编辑、内容补充、找答案等附加服务。
- 2、"仅部分预览"的文档,不可在线预览部分如存在完整性等问题,可反馈申请退款(可完整预览的文档不适用该条件!)。
- 3、如文档侵犯您的权益,请联系客服反馈,我们会尽快为您处理(人工客服工作时间:9:00-18:30)。
模切浅谈之常见问题分
享
Document number【AA80KGB-AA98YT-AAT8CB-2A6UT-A18GG】
在模切过程当中,每天都会遇到很多小问题,有的甚至让人搞得焦头烂额、头疼不已。
在这里我们就把工作当中的一些问题列出来跟大家分享一下,本人接触的是平刀和辅料类的模切,所以也就跟大家讨论一下普通常见的问题,没关注到或有更好的方法大家多多探讨。
问题1、产品底纸冲穿或不断。
这个分两个方面来看:一是全部冲穿、一是局部冲穿。
从原因上来分析,首先了解你的模具刀锋是否损坏不够锋利。
产品整个冲穿检查你的模切机是否压力不稳定,或是你的模切速度快慢不均,还有的是停机后再开机出现压力不稳,反复检测证实原因后检修你的模切机。
产品局部冲穿检查你下模板是否局部垫得太多,一般调模要求只垫一层胶带最多2层,下模板不能冲切太深。
垫模板选择硬质板,会增加你模切的稳定性,比如:电木板、P E T板、亚克力板有的甚至会用铁皮。
问题2 、产品变形。
检查模具没有问题当冲切出来的产品尺寸有出入。
检查你的垫刀棉使用是否恰当(高度、厚度、硬度、弹力等)?这里就不说用什么材料,不一样的产品不一样的要求选材要求都不同,这种我们叫做挤压变形。
再者就是检查你的模切材料是否有贴合是张力控制不均,导致冲出来后产品收缩。
这种体现最明显的就是PE保护膜类或海绵胶类,遇到这样的产品就要在复合的环节控制好材料的张力,减少在模切后产品收缩。
如果张力方面没办法控制到一点都不收缩,记录好你的贴合张力,不同的产品先模切实验,收缩多少将模具相应的放大或缩小多少,下次生产相同产品按照之前参数作业。
还有一个产品变形就是原材料的因素,比如橡胶或海绵类。
这种材料在冲切的时候注意模具角度,一般选择单锋刀,垫刀棉根据实际情况选择高度和硬度。
问题3、细小边类产品模切变形。
为什么把这个分开来说,是因为两个问题性质不一样。
要求不高的产品一般边距太小(0.8mm)以内我们会选择做跳步模,
内外框套为冲切。
这种做法在模具成本和调模上面会轻松很多,弊端就是产品尺寸多靠模切机性能和模切师傅控制,容易出现尺寸不良(主要是套位不准、偏位)。
还有就是一些不规则产品,在选择激光模一次性冲切的时候可以将模具刀高度降低,以防止在冲切的过程中模具受力后变形。
还有就是小孔或小边距处不能直接用普通的垫刀棉,可以用玻璃胶或硅胶裁成需要形状和尺寸人工塞入模具内。
激光刀模达不到效果的话就要考虑用精密的模具了(腐蚀模、雕刻模等),有些比较难做的产品,一次成型很难达到的,可设计2次成型或更多次套冲成型,以达到产品要求。
问题4、重刀或跳刀不直。
此两种现象主要就跟拉料和卡位有关了。
重刀最主要的原因是拉料拉力不均造成,可将前面放料用吸风或压板带上拉力,注意每卷料的接头可能都会导致拉料间距不同,特别是较厚的材料如泡棉类。
跳刀不直首先确定模具是否调直,原材料是否分直。
调模时多跑一段,将走料拉直后再收回来,前后限位卡死。
问题5、模切产品排废。
关于排废的问题有很多种:1全断产品排废,我们可用保护膜做底,产品半切在保护膜上,然后去了保护膜的成本,有的人在用排废针顶废的时候可能会出现排不净的现象,这多半是你技术的原因,目前我做的产品都能用它排掉(特殊要求的除外)。
2排废时底膜拉断,首先看你的底膜是否太薄,比如有些双层保护膜底膜只有0.03mm厚度,这个在模切来说是比较考技术的,可能你调模和冲切都没问题了,排废就出现拉断底膜的情况。
换上厚的保护膜还是有拉断的情况,那就看看你冲切的时候是否有冲切过深的地方,切坏了底膜导致拉废时底膜从切口处拉断。
另外就是你的底离型膜离型力是否不够,与废料粘合太紧,排废拉力过大拉烂底膜。
问题6、小尺寸产品排废时不能机器排废或部分产品与废料一起排出。
1像摄像
头泡棉这类产品在模切的时候,模具上的垫刀棉需要将外围的废料撕掉,以避免垫刀棉挤压材料造成产品与废料的胶粘合在一起不能排废。
2某些在冲切的时候可以适当的加一些防粘剂(比如脱模剂、洗洁精等),一是防止粘模,也可以防止产品回粘。
2排废的时候机器上的压块松紧度调节好,拉废料的角度掌握。
3、底膜的离型度是否合适,离型度太轻或太重也会影响产品排废以及后续的客户使用。
这些办法试了都不行那就拿出终极法宝,用PET或其他硬质材料剪个治具,在排废时压住你的产品,这样如果还不行,那你就哭吧。
我说上面这几点的前提是你要确定你的产品是全部切透了,不要有的地方你胶都没切断过来跟我说排不了废。
对不起,我是斯文人,我不想骂人。
O K
问题7、产品偏位,这里主要讲套位偏位。
像摄像头泡棉此类小产品,不能做成型模而选用跳步套位。
1在做这样的产品首先你的材料要求一定要直,歪歪扭扭的材料神仙也走不好,就不要怪模切师傅技术不好。
2在走料的时候可以先走一段定好位后再把材料拉回来进行模切,定好的位置前后一定要卡死,不能让材料在模切过程中有上下摆动的情况,必要时下模座上也需要卡位。
3冲切过程中材料拉力一定要稳,不能在拉料时出现时松时紧的情况。
这些环节都检查了没问题但产品还是偏的话,看看你的产品是否偏的有规律,适当的调节一下拉料间距,激光刀模也是有误差的。
问题8、二次套位产品套位不准。
辅料模切二次套位做得最多的应该属防尘网类了,当然也有些公司做的产品类别不同。
需要二次套位的最常见的工艺就是冲定位孔用小孔定位,这就要求选择的底纸稳定性较好,最好是选用离型膜,这样在二次定位冲切的时候才有一个稳定的支撑。
在冲定位孔时最好是一次冲全断去掉废料,有的人想偷懒,故意把定位孔留一点不冲,就省去了清孔废这道工序,也不会搞得整个机台全是孔废。
这个方法对于要求不高的产品来说确实可以说是一个好办法,但要求高的产品就会影响套位精度。
第一次冲切时材
料要压紧,不能时松时紧,一定要走直,不能偏位,模具与材料要垂直,这直接影响着第二次的套位。
第二次套位时前面放料,不能有拉料张力产生,后面排废时也不可拉动机器上的走料。
多个模头有一个偏位考虑是模具的问题,可将模具进行修正,单边偏位可调模切机上模座角度,整体有规律偏位在其他都没有问题的情况下试着按情况改变拉料间距。
问题9、压痕。
这个问题我想每个公司都遇到过,只是轻与重的问题,可能有的产品要求不是那么严就放过了。
这里可能很多人都想得到很好的解决方案,但是我要说这个没有标准的答案,要根据不同的产品而定。
主要可以从几个方面入手:刀锋角度,不同的材料不同的角度;垫刀棉的选择,不同的模具选择合适的垫刀棉;调模,模板上不能有压槽;再有就是下模板,不能太软,冲久了会有压槽产生。
问题10、带手柄类产品二次冲切时机器上边换纸边冲切,容易出现偏位情况。
这类加工方法主要是以走料定位,所以对换纸走料这部分要求比较高,在换纸的时候可以将材料多穿几个轴,用卡位卡死定位,将材料的偏位修正过来,这样模切效果就好很多了。
在模具设计方面很多人喜欢把手柄对排,以方便第一道工序排废,或者有的为了省材料将手柄错开。
这种做法理论上是省材料省事,但对于第二次冲切来说是个麻烦事。
个人觉得最理想的排版是将手柄一字排,这样就算你定位有偏差也可以尽量往里偏,不让胶多出来在手柄上。
人工也不会多,都是机器一次排废,而且对于成本来说这个小东西本来材料成本就几厘钱,可以忽略,相对于你的效率和品质来说,就不要去捡芝麻丢西瓜了。
问题11、防尘网毛丝。
主要原因有2个:一是模具接头不到位,2是防尘网质量差。
有的公司为了节约成本,将胶和网都换成最便宜的,就导致材料很软不易冲切。
这个时候就有很多人将底纸换成离型膜,想以这样来减少加工的难
度。
确实这样对于冲切来说方便很多,但这个毛丝问题依然没解决。
那怎么办呢?换防尘网,这样能够减少产品的毛丝问题,但不能完全杜绝,因为还有个问题出在模具上。
那再换将模具换成腐蚀模,OK,一切解决。
反过来想想,这样的话我的成本增加了多少?有的做个山寨机总共产品价格还没模具费高,这个怎么办?找客户涨价或收模具费——你这客户还要不要了?找老板谈这事——你这工作还要不要了?好吧,那就只有想办法。
既然问题出在模具上,就从模具入手。
激光刀模接口不好这是通病,问题在接口上那我把接口处加一把刀再冲一次呢?结果证明效果很明显,问题迎刃而解。
好了,在这里想到的就以上这些问题,其他还有很多一时也很难去整理出来,只能以后慢慢完善,大家有什么好的东西也可以拿出来一起分享,同行交流就应该不保留。
写得不好大家也别丢砖头,毕竟也耗费了我这么多精力,鼓励一下吧。
我觉得任何事情只要用心,都会去发现问题然后解决问题,对于做技术的人来说这无疑也是人生一大乐趣哉。
有时候你面临的所谓疑难杂症,可能就一个小小的毫不起眼的一个动作就解决了。
所以总结的方法就是:多动脑、多交流。