ie工作改善提案运作流程图
IE工作改善方法ppt课件

第二章、防错法應用原理介绍
2保險原理
籍用二個以上的動作必需共同或依序執行才能完成工作。
(一)籍“共同”動作必須同時執行來完成
例:開銀行保險箱時,須以顧客之鑰匙與銀行之鑰匙,同時插 入鑰匙孔,才能將保險箱打開。
例:操作衝床之工作,爲預防操作人員不小心被手夾傷,所以 設計一雙手必須同時按操作鈕下去,才能執行工作。
13
第二章、防错法應用原理介绍
1斷根原理 將會造成錯誤的原因從根本上排除掉,使絕不
發生錯誤。 (一)籍“排除”的方法來達成 例:錄音帶上若錄有重要的資料想永久保存時,則
可將側邊防再錄孔之一小塊塑膠片取下,便能防 止再錄音。 (二)藉“制止源头”來達成 例:国家为了控制人口增长,实行计划生育结扎手 续。
六、基本原則
在進行“防錯法”時,有以下4原則可供參考:
(一)使作業的動作輕鬆
難於觀察、難拿、難動等作業即變得難做,變得易疲勞而發生
失識。區分顔色使得容易看,或放大標示,或加上把手使得
容易拿,或使用搬運器具使動作輕鬆。
10
第一章、 防錯法
(二)使作業不要技能與直覺 需要高度技能與直覺的作業,容易發生失误。考慮治具及工具,
第二章、防错法應用原理介绍
8層別原理 爲避免將不同之工作做錯,而設法加以區別出來。
(一)以線條之粗細或形狀加以區別 例:所得稅之申報單 將申報人必需填寫之資料範圍記載在粗線框內。 例:回函條請沿虛線之位置撕下。
24
第二章、防错法應用原理介绍
(二)以不同之顔色來代表不同之意義或工作之內容 例:在生產線上 將不良品挂上“紅色”之標貼 將重修品挂上“黃色”之標貼 將良品挂上“綠色”之標貼 人類對顔色的共通認識是以: 綠色:表示“安全”或“良好” 黃色:表示“警示,注意”或“重修品” 紅色:表示“危險”或“不良品”
IE工作开展流程图

没有问题才是最大的问题;
备注 等相关流程;
1、工时管理:围绕已有的标准工时,制定相关的工时管理制度;(在制品定额) 2、生产分析:生产异常、生产瓶颈分析; 3、管理制度:制定生产管理制度、车间文化、5S、激励制度; 4、平衡率:线体平衡率的影响因素分析;
制度成型、异常处理、管理实施;
在基本条件稳定的情况下,针对线体平衡率进行有效的提升及稳固;
阶段 基础
流程图 建标 定流 评审、试行、优化、新产品 试行、推 标准工
改善
工时管
生产分
管理制
平衡
生产优化、提 平衡率提
升级
成本分
布局分
精益生
持续改善,改善无止
阶段目的
工艺 工序 分析
建数据库 提平衡率 (长期、
主要)
维护 优化 (精益生 产)
流程说明 1、形成基础的标准工艺、参数、作业流程、布局等文件;
1、制定生产流程、业务流程、SOP推行流程、问题处理流程、紧急处理流程等相关流程;
1、原产品:评审SOP、工艺优化、实施试行、发现问题、优化SOP、定稿; 2、新产品:生产前相关的工艺文件、SOP、测试规范应全部成型;
1、标准SOP的实施推行;
1、线上人员熟悉作业后,满足了标准工时观测的前提条件,开展标准工时测定工作;
IE工作流程图

(A+B+C+D)+100 公式: Total Allowance Factor= 100
Jabil Circuit HK Ltd.
捷普電子香港有限公司
M’s与人力的计算
生产一部机的正常时间 N.T(秒) N.T x T.A.F =M’s/set 60 总宽放系数 T.A.F Total allowance factor
C: Partlist与BOM的一致性.输入SAP的正ቤተ መጻሕፍቲ ባይዱ性
建议: 为了提高工作效率,可适当的利用VBA编写一些对 B.O.M的程序,可大大简 化繁琐的对B.O.M工作,同时减少人为对B.O.M的错误.
Jabil Circuit HK Ltd.
捷普電子香港有限公司
产品流程的编写与生产工位布置图
在试产过程中,产品流程的编写关系到产品的生产成本与效率 ,产品流程的编写与工 夹具的合理设计应用将尽可能的减少不必要的浪费与无效动素.大大提高生产效率, 降低生产成本.编写产品流程应注意以下几个方面: A: 结合公司布局,设定最佳产品流程,尽可能减少不必要的运输及人力浪费 B: 设定产品合理流程,产品组装顺序的正确性可避免不必要的浪费,如果产品 流程不合理,可能造成装配困难甚至影响品质的稳定性. C: 产品流程应准确的填上标准时间,方便人力及生产工位布置的安排. 生产工位布置图的制作应结合生产线的实际情况,配制包括工位名称,物料车摆放生 产工具,工夹具及组件投放等等.力求将有用的信息传达给相关部门.
下载第二级Partlist 编写最近所有工程 准备预组装清单 变更并载入BOM M’s和组件12NC SAP 下载第三级Partlist 编写最近所有工程 变更并载入BOM 提供预组件样板 SAP 给供应商参考
IE工业工程改善案例

生产实习目的1.通过实习了解工业工程领域的知识的应用背景。
2.深入了解企业中工业工程各种基本知识和原理的实际应用情况,巩固和加深对知识的理解,并加以整合,提高综合分析问题和解决问题的能力。
3.了解实习企业的生产管理的基本情况,发现存在的问题并提出解决方案。
4.掌握提案改善的一般流程及具体做法,在团队中(或个人)如何完成一个提案从提出到发表的全流程,为毕业后的实操奠定坚实基础。
5.学习企业管理人员,工程技术人员对企业的高度责任感,对工作尽职尽责,勇于改革,不断进取创新的奉献精神。
实习任务从数据统计得出的各类产品装配各工件装配 SPT ,及拉平衡状况分析表,及原因分析与改善建议。
装配部部门简介装配部,作为车模生产的最后一道工序,肩负着车模成品的组装和包装的全部生产过程。
装配部现有六条生产线和一条样办组装线。
常用的设备有:钻床,电批,手啤机,风批,烙铁,高周波,封口机等。
为了更好的完成各种的生产任务,装配部引入了精益生产工艺流程。
精益生产是目前工业界公认最佳的一种生产组织体系和方式。
通过合理的排拉,达到合理生产,提高效率和质量的目的。
例子一:DCP1/25 货车,按流程标准可分成:车身半品( 10人),车身组合(16人),内座组合(4人),车底组合(11人),成品组装(7人)和包装(9人)共六个小组(57人)来完成。
每个小组会有一次或以上的自检。
例子二:YTB002 1/42莱茵之星单层客车按流程标准可分成:内座组装(12人),车底组装(9人),车身组装(20人),成品包装(6人)共四个小组(47人)来完成,在其中也加入了多少的自检。
装配车间平面分布图装配生产线平衡改善过程 了解产品组装工艺 对U 型拉进行工时测定,得到统计数据 从统计数据分析U 型拉平衡状况 识别瓶颈工位,找出不平衡的原因 运用平衡改善法则(ECRS 法则)、动作经济原则等方法制定改善方案 将改善方案告知组长或装配主任,实施现场改善 改善效果分析总结平衡改善法则-ECRS 法则简介 符号 名称说明E 取消Eliminate 对于不合理、多余的动作或工位给予取消 C 合并Comebine 对于无法取消又是必要的,看是否可以合并以达到省时、简化的目的 R重排Rearrange 经过取消、合并后,可再根据“何人”“何时”“何处”三个提问后进行重排S简化Simplify 经过取消、合并、重排后的必要工位,应考虑能否采用最简单的方法或设备替代,以节省人力和时间以上ECRS法则,具体可通过下列图片来说明生产中如何运用改善:装配线平衡典型案例数据统计时间:2012/8/2-2012/8/3 U拉序号:U24、U25产品编号:53072(太空车)组装部分:成品和包装改善方案提出时间:2012/8/2改善方案实施时间:2012/8/3改善前各工位组装工艺工位序号 组装工艺SPT(秒)人数设备1 双花轴装进轮子*2,再用啤机压紧 9.5 1 手啤机2 再装入太同车下壳,再用压紧轮子*2 11 1 手啤机3 太空车上壳+太空车下壳组件 6 14 太空车身打螺丝13 1 电动批5 太空车上壳表面粘贴蓝色标签1 8 16 太空车上壳表面粘贴蓝色标签2 8 17 太空车上壳表面粘贴蓝色标签3 8 18 太空车半品装太空车雷达 6 1 抹布9 清洁位,车身抹洗面水 9 1 抹布10 检查位,擦拭车身 10 111 太空车成品装进胶袋 6 112 胶袋粘透明胶纸,并最终装进外箱8 1此款产品的装配线由U25、U24两个U型拉组成,工位分布如下图所示:平衡率=各工序的作业时间/(瓶颈工位时间*人数)=(9.5+11+6+13+8+8+8+6+9+10+6+8)/(13*12)=65.71%平衡损失率=1-平衡率=34.29%改善前装配线工位平衡图改善措施从统计数据分析这条装配线,可以发现瓶颈工位是工位4。
IE简介 提案改善
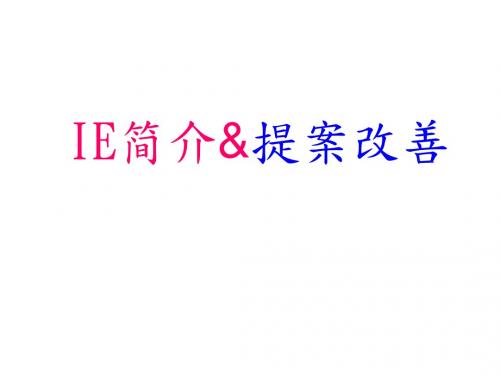
系统管理阶段 1945~1980
行为科学、组织理论、管理理论丛林 运筹学、系统工程、计算机应用
生产领域形成三种典型生产形式
–大量流水
–成批生产
–单件小批
科学管理 + 行为科学 + 系统管理
IE的基本意识
成本和效率意识 问题和改善意识 工作简化和标准化意识 全局和整体化意识 以人为中心的意识
评审基准及其说明
● 凡经单位主管认可实施后之改善提
案,其审查基准按以下项目及比分综合评
定,并依最终得分给予相应奖励。
效果 項目 A B 創意性 10% 思考性 10% 100% 思考能力 合 計
(經濟的) (無形的) 比分 40% 40%
改善建议书和改善报告
如何写好﹕
主题明确 语言精练 具备内容﹕
主 委 会
常务 主任 委员
群级 主管
1.制定本群提案改善总体 目标; 2.总理提案推动委员会会 务; 3.提案改善推动指导性政 策制订;
副主委
各产品处 最高主管
一﹑组织架构
组织 担当 主任 委员 描述 事业群 最高主管 职掌
主 委 会
常务 主任 委员
群级 主管
副主委
各产品处 最高主管
1.指导PCEBG事业群提案改 善推动和政策的落实执 行及监督; 2.制订PCEBG年度提案改善 推动计划及执行; 3.对优良提案的核定和对 群内提案明细汇总表和 月报表及排名核准;
一﹑组织架构
组织 担当 主任 委员 描述 事业群 最高主管 职掌
主 委 会
常务 主任 委员
群级 主管
副主委
各产品处 最高主管
1.协助主任委员制订提案 改善推动指导性政策; 2.建立本产品处提案改善 推动组织并制订提案改 善目标; 3.指导产品处提案改善的 展开; 4.审核产品处员工的提案;
IE六大模块及现场改善流程

A:标准工时制定,标准工时用于生产排配,效率统计,产能分析,成本核算等方面; B:人机操作分析及改善,制定合理的人机比,减少怠机及人员的浪费; C:设备综合效率(OEE)分析及主导改善,提升OEE及产能; D:参与车间平面布局(Layout),合理规划人流.物流.减少搬运的浪费; E:协助工程合理设计制程中的工装夹治具; F:掌握IE工作研究(WS)中的方法研究(MS)及时间研究(TS)
问题点的发现现状分析真正问题点的提出主题设定改善方向限制条件的调查问题点的发现改善案的作成效果预测评价实行计划实施标准化管理数据过去的data现场的七大任务pqcdsme生产的四要素作业者
IE六大模块
现场IE(Field IE) 成本IE(ABC IE) 流程IE(BPR IE) 运营IE(SCM IE) 组织IE(OEE IE) 绩效IE(KPI IE) IE五大意识
A:与工程合作规范产品BOM,精进BOM中物料的单位用量及产品的工艺流程; B:每月工单结案材料成本的核算及分析,掌控实际材料成本的损耗状况; C:作业成本库的建立;根据资源动因计算作业成本; D:确定产品成本驱动因素,根据作业变动计算产品成本; E:每月制造成本(直接材料+直接人工+间接制造成本)报表统计分析; F:ABC作业成本法推行及作业成本管理; G:Cost Down的主导
IE工作流程

�
试产前生产线领 班及组长培训 1.制作样品(会同PM, R&D,ME,QE) 2.生产教导 3.试产问题点(有关 影响组装的方面)
1.更新ORCEL系统 bom routing中 新产品机器工时 2.更新ORCEL生产日报系统 中新产品的标准产量及人力
新增物料及减少物料需 发ECR修改BOM并发 MN控制制程中产品
1.更新ORCEL系统 bom routing中新产品机器工时 2.更新ORCEL生产日报 系统中新产品的标准产 量及人力
模具修改设变需 发MN控制
依据资料核对 BOM
新产品 导入
试模
试产DVT
试产PVT
量产
制作新产品 试用 MPI(45天)
1.生产中异常问题之解决 2.方法改善,降低工时,提高效率
产品导入IE的工作流程
序 新产品导入时,IE需要做哪些工作呢?对于一个新进IE 来说,确实有点摸不著头脑,对于一个已经接过一个机种 的IE来说,流程也不是理的很顺,所以为了各位IE在接新产 品时知道在什么阶段需要做哪些事,哪些事应该在何时完 成,现在就将新产品导入时IE所需做的哪些工作用流程的 方式表现出来. 下图为IE的工作流程.
制作:ANN.XU 审核:
制作产品生产 流程图 制作PMP
发给相关单位QE, PM作3B承认 发给工具室作购买工具的依据 发给相关单位PC作人力的预估 发给产线及相关单位作为产品 控制的依据
日期:06/19/01'
制作工具表 制作人力表 制作版本清单
组装 喷漆 IE 工作流程图
1.核算(预估)新产品成本工时及机器工时;并将 其维护於ORCEL系统bom routing中 2.新产品基本资料录入ORCEL生产生产日 报系统(机种料号) 3.新产品标准产量及人力录入ORCEL生产 日报系统(机种P.P值)
IE改善提案培训课程(PPT 31页)

26
博一家具有限公司
八.公司改善提案制度介绍
成果统计依据: a.材料单价:依财务所提供资料为准。 b.工资率:以RMB 7元/时计算。 c.不良数:依品保提供资料为准。 d.工 时:依生产所提供资料为准。 e.生产数:依PMC所提供审查时候,前12个月实际出货量 之平均数为准。
博一家具有限公司
八.公司改善提案制度介绍
6.3.7奖金方法方式: 6.3.7.1提案奖:以周为单位,执行组长制作统计表交总经理核准,由稽核 办负责以现金发放。 6.3.7.2贡献奖:以月为单位,生产PE制作统计分析表交稽核办查核,查核 情况属实后交总经理核准,由稽核办负责以现金发放。 无形成果:指无法用金额表达之成果,举例如下:
七.改善提案发展阶段
• 第一阶段:发现问题,觉察已经出现的问题 • 第二阶段:发掘问题,预测未来可能发生的问题 • 第三阶段:创造问题,设定更高水准,创造出问题
如何解决“提案写完了” 的问题
பைடு நூலகம்
无意识的提案 活动
问题来找我 被动
有意识的 提案活动
我去找问题 主动
博一家具有限公司
八.公司改善提案制度介绍
之事项。
工厂安全整理、 整顿及机器工
其他有利于本 公司之变革事
具保养事项。
项。
18
无具体内容且 其可操作性差
的项目。
博一家具有限公司
八.公司改善提案制度介绍
不受理之提案
涉及个人生活 或属于个人诉 苦事项。
涉及薪资、人 事异动任免问 题。
(精益改善)精益IE事务流程图

配送物流
Rev. 封箱物流
a.根据当天物料状况打溢领单
溢领手工单
每天8:20~10:00
溢领捡料表
20:20~22:00
b.领溢领料(流程同2.领料)
6.包装及入库
a.领用包材
两小时1次b.成Leabharlann ,半成品封箱,入库两小时1次
7.退料
物料盘点日报表 每天18:00~21:00
a.清点物料,分类整理
6:00~9:00
b.退料:
b-1.良品退scm良品仓
系统名称(SYSTEM):
呆
物流课作业流程
流程说明
Process Description
窗体
1.准备作业
生产排配表
a.生管开工令
b.账务打印捡料表
捡料表
2.领料
a.工令盘点登记,送单至各制程通知对方备工料令发料登记表
b.领料 b-1.查看物料是否短装
3.配送物料
a.按频率送料至各线
短装补料单 物料配送表
良品退料登记表
b-2.不良品退scm不良品仓
来料不良退料登记表
制程不良退料登记表
b-3.
报废明细表
8.工令结案
未结工令报表 每天9:00~10:00
超时结案工令报表 21:00~22:00
9.异常处理
a.工令结案异常
b.短装少料异常
c.退料异常
d.过账异常
联系人/电话
生管
账务
相关部门 SCM/成型/涂装 领料物流
时间
每天15:00~16:00
每天16:00~18:00
每天9:00~10:00 21:00~22:00
每天10:00~18:00 22:00~6:00
(精编)IE现场改善流程

I E 现差 场异 改分 善析 流 程
真正问题点的提出 主题设定
改善方向 限制条件的调查 问题点的发现
改善案的作成
效果预测 评价
实行计划 实施
标准化
管理数据(过去的DATA),现场的七大任务(P.Q.C.D.M.S.E) 生产的四要素(作业者.机械设备.原材料.方法 5W2H/QC手法 适合提高生产力的IE手法 工程分析/搬运分析/稼动分析 工作抽查法 生产线作业编成分析/动作分析 动作经济原则/工厂布置的基本原则 检查表(Check List)
构想的定律:排除.反对.仅处理参数.扩大.缩小.变换顺序 改善的ECRS原则(删除.合并.重排.简化) 3S(简单化Simplification.标准化Standardization.专业化Specialization)
脑力激荡法(Brain Storming) P:Production 产量
Q:Quality 品质
C:Cost
成本
D:Delivery 交期
S:Safety
安全
M:Mora5W2H
Who
何人
人.机器设备
What
何事
对象物.范围
When
何时
时刻.时期.时间
Where
何处
位置.方向
Why
为什么 目的.成果.理由
How
如何做 顺序.方法
How much 多少成本
IE七大手法案例(组装)ppt课件
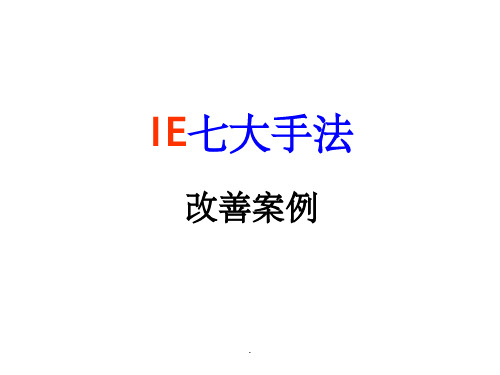
A:“不是。”
Q:“為什么不做?”
A:“改善意識不強。”
.
案例1
狀 改善后
結果﹕ 將線體支撐架向內移動﹐將上檢員工位移至 線頭正對線體﹐雙手同時作業﹐取消伸臂動 作﹐坐著操作. 上檢員工作強度大﹐疲勞 .
案例2
現狀描述
該系列機種自量產以來在DIP線和組裝線 均發生擊發板不充電現象﹐經工程分析确 認原因是MCU板上保險絲熔斷。
保險絲
安全隱患
.
案例2 改善歷程—真因求索
問:為什么數碼相機擊發板電路會不充電? 答:因為連接擊發板電路的保險絲熔斷。
問:為什么連接擊發板電路的保險絲會熔斷? 答:因為保險絲工作時電流超過額定值。
問:為什么保險絲的電流會超過額定值? 答:因為連接擊發板電路的FPC在接口處發生短路。
問:為什么FPC會在接口處發生短路? 答:因為FPC裝入接口后易發生偏位。
左手 4 3 4 11
現行方法
右手 4 4 3 11
根據動作經濟原則﹐考慮增加治工具來減少動作數量﹐縮短cycle time
.
案例2
貼label改善
利用如圖所示自動 貼紙機﹐可以取消 該工站折疊貼紙動 作(其耗時為1.2s)
工作 ﹕ 貼貼紙 開始 ﹕ 雙手空的 ---工具在流水線旁 ﹐ 產品在流水線上 結束 ﹕ 貼好一件產品放至流水線上
拆布套投側板 (1人)
出 L10 組裝 (1人)
裝箱 (1人)
套布套 (1人)
簡化 流程
烤漆廠裝箱
裝配作業
貼1pc腳墊 (1人)
拆布套投側板 (1人)
出L10 組裝 (1人)
改善前: Arches2機種側板腳 墊由L5組裝廠負責 粘貼,造成人力浪費
IE与提案改善.pptx
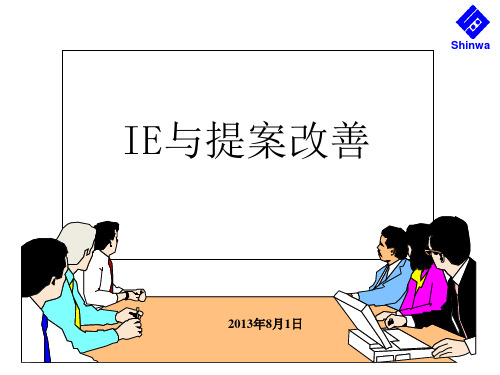
2.8 小时
我们的人力成本是美国的30分之一,生产成本
是美国的3倍
开源
靠策略,靠技术
节流
靠持续改善
改善的基本知识
• 对“改善量变与质变”的正确理解小步阶梯式Sh改inwa
常识性的工具, 进,逐次累积 技巧,不花钱或 而发生质变
全员参与, 少花钱
轻松工作
超越目 前水平
质变
量变
改善的基本知识
改善的目标及改善的主要指针
Shinwa
其实提案活动等类似的由下往上的管理运动,是为了能让这中间的 六成人,也能加入其中。在近年来,企业文化受到重视,这是由于这些 能左右这六成人的行动形式。企业的实力,也是受到这些占有六成的人 之水平来决定的。
这些二成的优秀而积极的人,不管在任何组织或公司之中,他们都 会表现出其个人的意愿开发能力,而显露出其头角。但是,中间的这六 成人,却不是如此。要开发其能力、发挥其能力,即需要有一套策动的 办法或系统。其中之一就是 改善提案制度。
Shinwa
Safer (更安全)
Accurate (更准确)
Better/Best (更好/最好)
Faster (交期更短)
Continuously Consistently (持续,稳定)
Cheaper (成本更低)
Easier
Delightful
(作业更容易) (工作更愉快)
• Productivity ✓ 制造更多的产品 • Quality ✓ 制造更受欢迎的品质 • Cost ✓ 更低廉的成本 • Delivery ✓ 更短的周期 • Safety ✓ 安全的工作环境 • Morale ✓ 高昂的士气
将大多数的员工加以策动,使改善固定化,这是塑造出改善成为企 业文化的一种方法。因此,改善提案活动并不是只有一部分有意愿的人 做就可以了。最理想的就是100% 的全部都来参与。最少也要有二成的人, 加上六成的人,合计八成的人来参加。