大型电渣重熔值得注意的几个问题
电渣压力焊安全技术交底

电渣压力焊安全技术交底在进行电渣压力焊作业时,必须严格遵守安全操作规程,采取相应的安全措施,以防止发生危险事故,保障人身和设备安全。
本文将介绍电渣压力焊作业中需要注意的安全问题和应注意事项。
一、电渣压力焊作业的安全问题1.灼伤电渣压力焊时需要使用高温设备,因此需要特别注意防止灼伤。
工作人员应佩戴符合保护标准的防护器具,如手套、护腿、头盔等,特别是接触高温部分的工人,要穿戴符合标准的隔热服。
2.触电电渣压力焊时需要使用大功率电源,因此容易发生触电事故。
为了避免触电事故的发生,应该建立和遵守符合标准的电气安全控制措施,如绝缘、接地、避雷等。
另外还要注意不要用湿手和带导电物体接触高电压设备。
3.眼睛受伤电渣压力焊时使用的弧光和火花可能会导致火花、碎片等物质飞溅,造成眼睛受伤。
为了防止这种事故的发生,应该佩戴符合安全标准的防护眼镜或面罩,特别是焊接时需要朝向电弧这一方向的工作人员。
4.化学灼伤电渣压力焊作业过程中还需要使用液态焊剂,这种液体会剧烈腐蚀皮肤和呼吸道,造成化学灼伤。
为了防止这种危险事故的发生,应当佩戴符合标准的化学安全防护服、防护手套、口罩等。
二、电渣压力焊作业应注意事项1.焊接场所焊接场所的准备和安排是焊接作业的关键。
一般来说,需要注意以下几个方面:•焊接场地必须符合场地安全要求。
•焊接场地应具备良好的采光和通风条件,避免因为氧气不足或者二氧化碳过量而影响焊接效果和工人健康。
•焊接场地应清理干净,避免易燃、易爆等危险物品杂乱放置。
•在焊接过程中,要注意周围的安全情况,切勿向周围洒弧光,避免影响其他工作人员的安全。
2.设备和材料电渣压力焊需要使用多种设备和材料,因此需要注意合理选材以及维护保养。
在这个方面要注意以下几个方面:•要定期检查和维护设备,确保设备安全可靠。
•所选用的焊接材料必须符合相关技术标准,并且显式的标识在元器件上,以确保其品质。
•焊接材料一定要干燥,不然会影响焊接质量和安全性。
电渣重熔技术
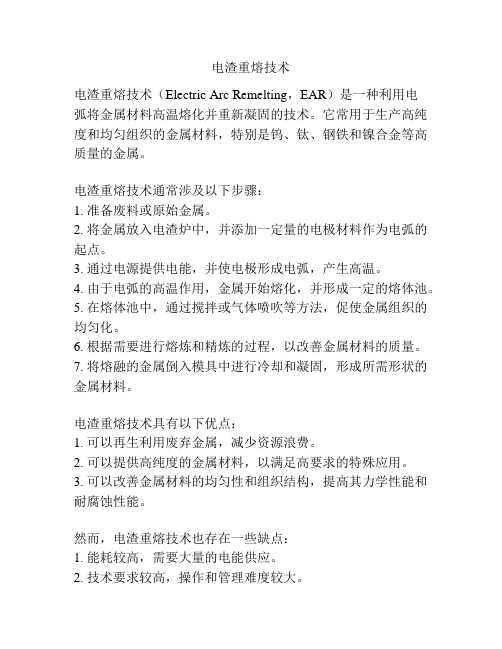
电渣重熔技术
电渣重熔技术(Electric Arc Remelting,EAR)是一种利用电
弧将金属材料高温熔化并重新凝固的技术。
它常用于生产高纯度和均匀组织的金属材料,特别是钨、钛、钢铁和镍合金等高质量的金属。
电渣重熔技术通常涉及以下步骤:
1. 准备废料或原始金属。
2. 将金属放入电渣炉中,并添加一定量的电极材料作为电弧的起点。
3. 通过电源提供电能,并使电极形成电弧,产生高温。
4. 由于电弧的高温作用,金属开始熔化,并形成一定的熔体池。
5. 在熔体池中,通过搅拌或气体喷吹等方法,促使金属组织的均匀化。
6. 根据需要进行熔炼和精炼的过程,以改善金属材料的质量。
7. 将熔融的金属倒入模具中进行冷却和凝固,形成所需形状的金属材料。
电渣重熔技术具有以下优点:
1. 可以再生利用废弃金属,减少资源浪费。
2. 可以提供高纯度的金属材料,以满足高要求的特殊应用。
3. 可以改善金属材料的均匀性和组织结构,提高其力学性能和耐腐蚀性能。
然而,电渣重熔技术也存在一些缺点:
1. 能耗较高,需要大量的电能供应。
2. 技术要求较高,操作和管理难度较大。
3. 一次熔炼的批量较小,生产效率相对较低。
总体而言,电渣重熔技术是一种重要的金属加工技术,可以产生高质量的金属材料,但其应用仍受到能耗和生产效率的限制。
电渣重熔工艺
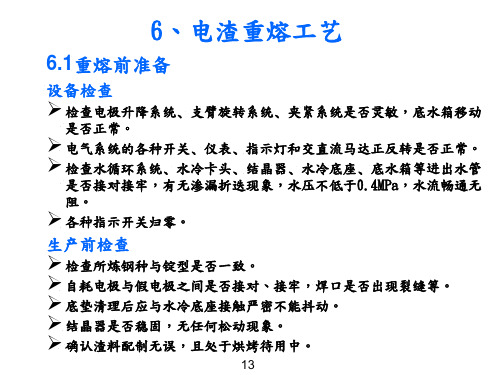
生产前检查
检查所炼钢种与锭型是否一致。 自耗电极与假电极之间是否接对、接牢,焊口是否出现裂缝等。 底垫清理后应与水冷底座接触严密不能抖动。 结晶器是否稳固,无任何松动现象。 确认渣料配制无误,且处于烘烤待用中。
后,垂直入炉,调整中心,使端头距引弧剂(40~50%TiO2、
就越少,电压变化为5V一级为好;电流稳定,不然会在重熔锭的表面出现波纹;电极 升降速率(弧长控制)平稳。
如果是多根电极熔炼一炉料,在自耗电极熔化至焊口还有大概100~150mm时调整电流
旋钮,使电流稍大于冶炼电流约500~1000A,保持1~3分钟后,开始更换另外一金属自 耗电极。更换电极的速度要快,以免在先前的钢锭面形成渣沟,造成断裂。
50~60%的CaF2)50-100mm处。待一切就绪后,配电员将操作台上高压电钮合上, 调整好电流﹑电压,给上自动,待指示仪表盘上电流开始波动后即可加渣。 注意: 加渣时一定要四周均匀加入,一次加入量不要过多,避免冷渣过多造成溶渣凝固,透 气性不好,导致喷渣﹑钻渣。
14
6.3、正常熔炼
待溶渣升温时间达到后,立即将电极离开渣面,切断高压,抬起电极,移动台车换
③假电极被熔化。
④突然停水或冷却水出水温度高于70℃。 ⑤断电超过换电极规定时间1min。
电流在20min之内逐渐调至正常,到后期电极被融化掉只剩100mm左右时电流逐渐递
减至充填电流,进行充填补缩。
15
6.4、电渣重熔基本工作过程
在铜制水冷结晶器内盛有熔融的电渣,自耗电极一端插入熔渣内。 自耗电极、渣池、金属熔池、钢锭、底水箱通过短网导线和变压器形成回路。 在通电过程中,渣池放出焦耳热,将自耗电极端头逐渐熔化,熔融金属汇聚成金属
液滴,穿过渣池,落入结晶器,形成金属熔池,受水冷作用,迅速凝固形成钢锭。
大型电渣重熔值得注意的几个问题
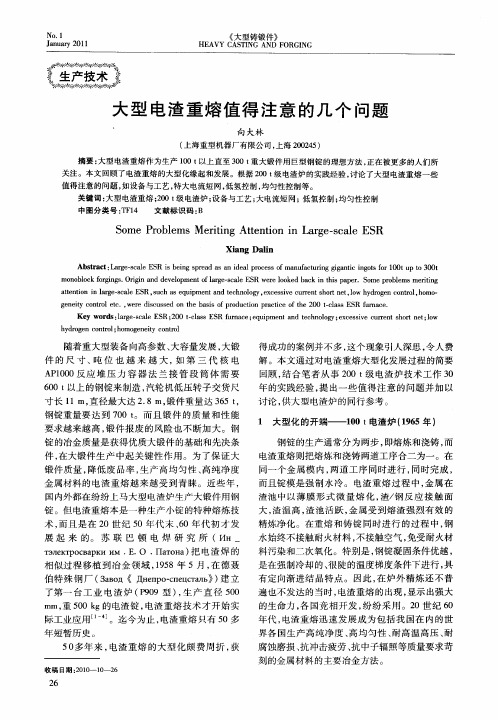
年 的实 践经验 , 出一 些 值 得 注 意 的 问题 并加 以 提
讨论 , 大 型电渣 炉 的同行参 考 。 供
1 大型 化 的开端生 产通 常分 为两 步 , 即熔炼 和浇铸 , 而 电渣 重熔 则把 熔炼 和浇 铸两 道工 序合 二为一 。在 同一 个 金 属模 内 , 两道 工 序 同 时进 行 , 同时完 成 , 而且 锭模 是 强 制 水冷 。电渣 重 熔 过 程 中 , 金属 在
渣池 中以 薄 膜 形 式 微 量 熔 化 , 钢 反应 接 触 面 渣/
锭 。但 电渣 重熔 本是 一种 生产小 锭 的特种 熔炼 技
大 , 温 高 , 池 活 跃 , 属受 到 熔 渣强 烈 有效 的 渣 渣 金
术 , 且是在 2 而 0世 纪 5 0年 代 末 、0年 代 初 才 发 6
No. 1
J n ay2 1 a u r 0 1
《 大型铸锻件》
HEAVY CAS NG TI AND ORGI F NG
大 型 电渣 重 熔 值 得 注 意 的 几 个 问题
向 大 林
( 上海重型机器厂有限公司 , 上海 20 4 ) 0 2 5 摘要 : 型电渣重熔作 为生产 10 t 大 0 以上直 至 3 0t 大锻件用 巨型钢锭 的理想方 法 , 0 重 正在被更多的人们所 关注。本 文回顾 了电渣 重熔 的大型化缘起 和发 展。根据 20 t 0 级电渣 炉的实践 经验 , 讨论 了大型 电渣重熔一些 值得 注意的问题 , 如设备与工艺 , 特大电流短网 , 低氢控制 , 均匀性控制 等。 关键 词 : 大型 电渣重熔 ;0 级 电渣 炉 ; 20t 设备与工艺 ; 电流短 网 ; 大 低氢控制 ; 均匀性控制
MC3电渣重熔过程中的残余应力分析及电渣工艺优化
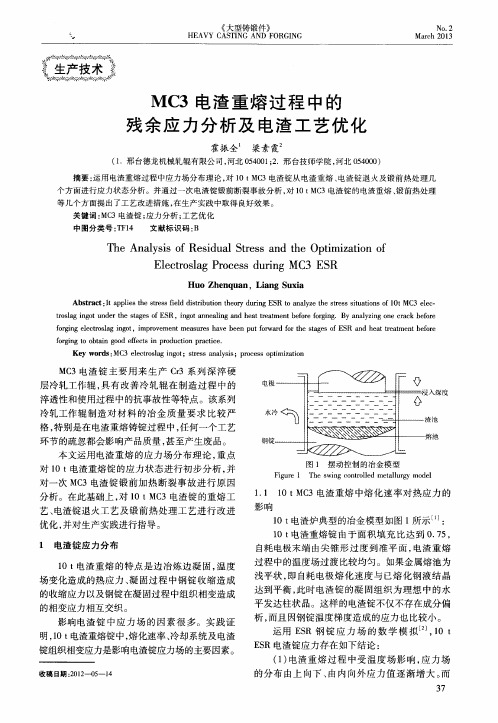
《 大型铸锻件》
H EAVY CAS TI NG AND F0RGI NG
No. 2 Ma r c h 2 0l 3
MC 3电渣 重 熔 过 程 中的 残 余 应 力分 析 及 电渣 工 艺 优 化
霍振 全 梁素 霞
( 1 .邢台德龙机械轧辊有 限公 司 , 河北 0 5 4 0 0 1 ; 2 .邢 台技师学 院 , 河北 0 5 4 0 0 0 ) 摘要 : 运用 电渣重熔过程 中应力场 分布理论 , 对 1 0 t MC 3电渣锭从 电渣重熔 、 电渣锭退火 及锻前 热处理几 个方 面进行应 力状 态分析。并通过一次 电渣锭锻前 断裂 事故分析 , 对 1 0 t MC 3电渣锭 的电渣重熔 、 锻前热处理 等几个方 面提 出了工艺改进措施 , 在生 产实践中取得 良好效果 。 关键 词 : MC 3电渣锭 ; 应 力分析 ; 工艺优 化
1 0 t电渣 重熔 的特 点 是 边 冶 炼 边凝 固 , 温 度 场 变 化造成 的热 应力 、 凝 固 过程 中钢 锭 收 缩 造 成
的收缩 应力 以及钢锭 在凝 固过程 中组 织相 变造 成
过程 的温度 场过 渡 比较 均匀 。如 果金 属熔 池 为 浅平状 , 即 自耗 电极 熔 化 速 度 与 已熔 化 钢 液结 晶
本 文运用 电渣 重熔 的应 力 场 分 布 理 论 , 重 点
对1 0 t 电渣重 熔锭 的应力 状 态 进 行初 步 分 析 , 并
一
7 / /
.
图 1 摆 动 控 制 的冶 金模 型
F i g u r e 1 T h e s w i n g c o n t r o l l e d me t a l l u r g y mo d e l
电渣重熔大型板坯的质量控制

sg e ai n e rg t .Th i r b e o r c u l fl g l n o y E R sr p e ,d u l s i rb e d a d d n o e man p o lm f u f e q a t o r e s b i g tb S i i ls o b e k n o le n e t s a i y a a p
第1 0卷 增 刊
21 0 1年 3月
材
料
与 冶
金
学
报
Vo.1 I 0 S1 M a c 011 rh 2
J u n l fMae il a d Me al r y o r a tras n tl g o u
电渣 重 熔 大 型 板 坯 的质 量控 制
耿 鑫 ,姜周华
所示 .
0
表 面
14 ,
巾 心
表 面
14 /
厚 板 中 的位 置
图 1 氢含 量对 白点 缺 陷 的 影 响
Fi .1 Efe fhy o n c nt n ake dee t [ g f cto dr ge o e ton f l fcs。
入 到渣 池上方 来 控 制 铸锭 中 的氢 含 量 . 过 上 述 经 措施 后 , 铸锭 的探 伤合格 率 明显 得 到改善 .
( 北 大 学 材料 与 冶 金学 院 , 阳 100 ) 东 沈 10 4
摘
要 :电渣重熔大型板坯的 内部质量 问题主要是氢含量 的控制 和偏析 的控制 ;电渣重熔 大型板坯 的表面质
量问题主要为波纹 、重皮或漏渣 以及 凹陷或铸锭 不饱满等 表面缺陷.本 文 旨在总结前 人工作的基础上 ,结合
电渣熔铸工艺
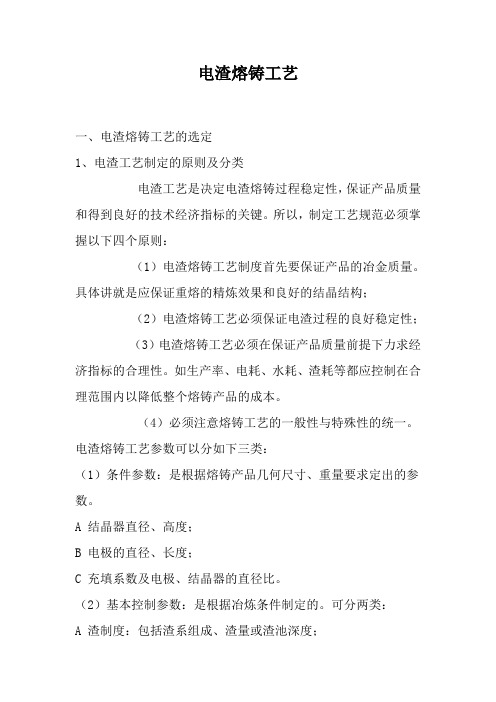
电渣熔铸工艺一、电渣熔铸工艺的选定1、电渣工艺制定的原则及分类电渣工艺是决定电渣熔铸过程稳定性,保证产品质量和得到良好的技术经济指标的关键。
所以,制定工艺规范必须掌握以下四个原则:(1)电渣熔铸工艺制度首先要保证产品的冶金质量。
具体讲就是应保证重熔的精炼效果和良好的结晶结构;(2)电渣熔铸工艺必须保证电渣过程的良好稳定性;(3)电渣熔铸工艺必须在保证产品质量前提下力求经济指标的合理性。
如生产率、电耗、水耗、渣耗等都应控制在合理范围内以降低整个熔铸产品的成本。
(4)必须注意熔铸工艺的一般性与特殊性的统一。
电渣熔铸工艺参数可以分如下三类:(1)条件参数:是根据熔铸产品几何尺寸、重量要求定出的参数。
A 结晶器直径、高度;B 电极的直径、长度;C 充填系数及电极、结晶器的直径比。
(2)基本控制参数:是根据冶炼条件制定的。
可分两类:A 渣制度:包括渣系组成、渣量或渣池深度;B 电制度:包括工作电流或电流密度、工作电压、有效供电功率、比功率等。
(3)目标参数:是基本控制参数综合影响的因变量。
主要包括:A 金属熔池深度;B 极间距离与电极埋入深度;C 熔化率D 渣池温度、渣皮厚度、电耗等。
二、电渣熔铸条件参数的选择1、结晶器尺寸的确定:直径和高度(1)直径的确定:D结=(D产品+A)/(1-δ%)式中:D结—结晶器直径(毫米);D产品—产品的规定尺寸(毫米);A—毛坯加工余量,一般按20~40毫米计算;δ%—熔炼毛坯的减缩率,一般为3±0.5%。
(2)高度的确定:①固定式:H结≈(3~6)D结当D结>300毫米,按下限考虑②抽锭式:2、电极尺寸的确定:直径和长度(1)直径的确定:d极=K•D结式中:d极—电极直径(毫米)D结—结晶器直径(毫米)K—经验系数,可选(0.5~0.6)±0.1(2)长度的确定:①单臂固定式电渣炉:圆柱形产品电极长度的确定: L极= h锭/C•η+Δl式中: L极—单支电极长度(米);h锭—钢锭高度(米);C—充填系数(电极与结晶器截面积之比);Δl—余头(电极剩余长度0.05~0.1米);η—电极致密度,轧、锻电极η=1,铸造电极η=0.95②双臂交替式电渣炉:这种电渣炉对电极长度要求不严格要求,只要电极不长度不小于夹持器有效行程即可。
纯铁电渣重熔的碳和硫控制
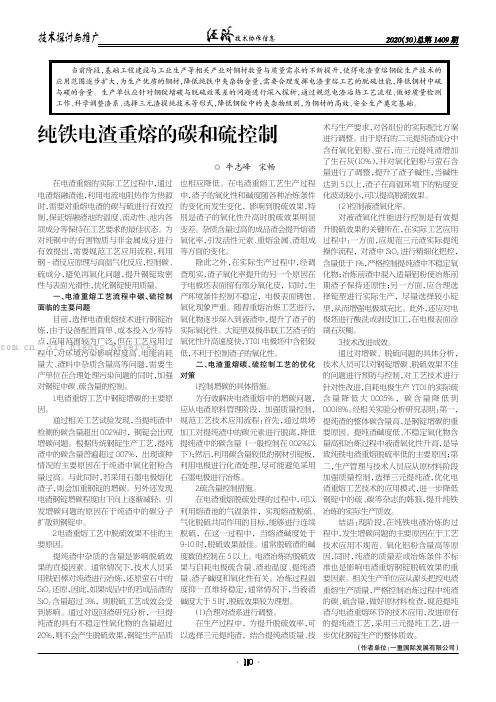
在电渣重熔的实际工艺过程中,通过电渣熔融渣池,利用电流电阻热作为热源时,需要对重熔电渣的碳与硫进行有效控制,保证熔融渣池的温度、流动性、池内各项成分等保持在工艺要求的最佳状态。
为对纯钢中的有害物质与非金属成分进行有效提出,需要规范工艺应用流程,利用钢-渣反应原理与高温气化反应,控制碳、硫成分,避免再氧化问题,提升钢锭致密性与表面光滑性,优化钢锭使用质量。
一、电渣重熔工艺流程中碳、硫控制面临的主要问题目前,选择电渣重熔技术进行钢锭冶炼,由于设备配置简单、成本投入少等特点,应用范围较为广泛,但在工艺应用过程中,对环境污染影响程度高、电能消耗量大、渣料中杂质含量高等问题,需要生产单位在合理处理污染问题的同时,加强对钢锭中碳、硫含量的控制。
1.电渣重熔工艺中钢锭增碳的主要原因。
通过相关工艺试验发现,当提纯渣中检测的碳含量超出0.02%时,钢锭会出现增碳问题。
根据传统钢锭生产工艺,提纯渣中的碳含量普遍超过0.07%,出现该种情况的主要原因在于纯渣中氧化铝粉含量过高。
与此同时,若采用石墨电极熔化渣子,则会加重钢锭的增碳。
另外还发现电渣钢锭增碳程度由下向上逐渐减轻。
引发增碳问题的原因在于纯渣中的碳分子扩散到钢锭中。
2.电渣重熔工艺中脱硫效果不佳的主要原因。
提纯渣中杂质的含量是影响脱硫效果的直接因素。
通常情况下,技术人员采用铁铝棒对纯渣进行冶炼,还原萤石中的SiO 2还原,因此,如果成品中的若成品渣的SiO 2含量超过3%,则脱硫工艺成效会受到影响。
通过对返回渣研究分析,一旦提纯渣的具有不稳定性氧化物的含量超过20%,则不会产生脱硫效果,钢锭生产品质也相应降低。
在电渣重熔工艺生产过程中,渣子的氧化性和碱度随各种冶炼条件的变化而发生变化,影响到脱硫效果,特别是渣子的氧化性升高时脱硫效果明显变差。
杂质含量过高的成品渣会提升熔渣氧化率,引发活性元素、重熔金属、渣组成等方面的变化。
除此之外,在实际生产过程中,经调查现实,渣子氧化率提升的另一个原因在于电极坯表面留有部分氧化皮,同时,生产环境条件控制不稳定,电极表面锈蚀、氧化现象严重。
电渣重熔工艺和理论知识

电渣重熔工艺和理论知识ESR techniques and theoretical knowledge* 一、电渣重熔基础理论知识1、概述电渣冶金起源于美国,一九四〇年霍普金斯取得了发明专利。
一九五八年,苏联德聂泊尔特钢厂工业电渣炉建成,现代电渣冶金开始进入工业化进程。
六十年代中期,由于航空、航天、电子、原子能等工业的发展,电渣重熔在苏联、西欧、美国获得较快的发展,生产的品种包括:优质合金钢、高温合金、精密合金、耐蚀合金以及铝、铜、钛、银等有色金属合金。
我国是世界上电渣冶金起步较早的国家之一,一九六〇年,重庆特殊钢厂、大冶特殊钢厂,大连钢厂及上钢五厂的电渣炉先后建成投产。
紧随其后齐齐哈尔钢厂、抚顺钢厂等工业电渣炉相继建成投产。
五十多年来,我国电渣冶金始终保持着旺盛的发展趋势。
随着我国科学技术突飞猛进的发展,航天航海、汽车制造、石油化工、电站建设、核设施、机械制造等诸多行业,以及军工事业的发展、列车提速等许多领域越来越发挥着电渣钢的作用。
目前最大的一座是原上海重型机器厂电渣炉,重熔钢锭重达200t,现在又筹建450t大型电渣炉。
2009年,我国电渣重熔钢生产能力已超过170万t。
50多年来国内外电渣冶金取得了突飞猛进的发展,新工艺、新技术层出不穷,形成了一个跨专业、跨行业的新学科。
2、现代炼钢方法转炉,电弧炉,电渣重熔炉,真空感应炉,真空自耗炉(电弧重熔炉),电子束重熔炉(EBR)等。
电渣重熔是一种炼钢方法,而不是炉外精炼。
炉外精炼方法有LF,VD,VOD,VAD,RH 等。
3、电渣重熔炉类型3.1按工艺特点分:普通电渣重熔炉,电渣熔铸炉,加压电渣炉,保护气氛(可控气氛)电渣炉,连铸式电渣炉,电渣离心浇注炉,电渣热封顶等。
可控气氛电渣重熔技术。
电渣重熔通常在大气下进行,重熔合金中的氧含量,取决于主要脱氧元素的浓度和该脱氧元素的氧化物在渣中的活度。
此外,渣池上的氧分压或多或少也会产生一定的影响。
过去通常采用往渣池中加入脱氧剂的方法对熔渣连续脱氧,但是这会导致熔渣成分的改变。
电渣重熔过程中氧的控制
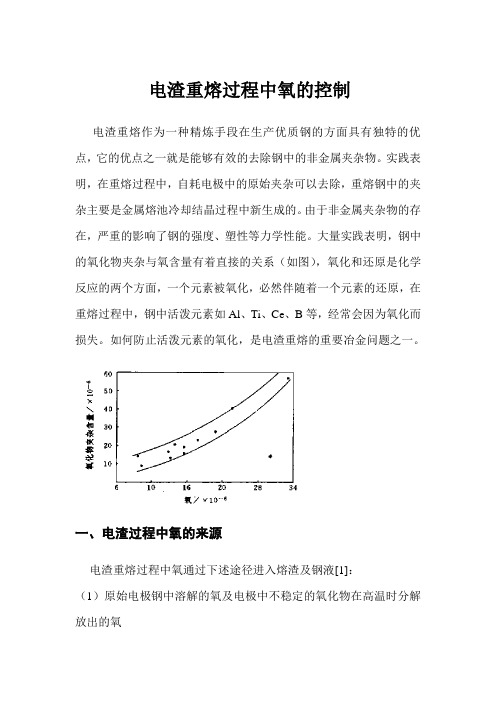
电渣重熔过程中氧的控制电渣重熔作为一种精炼手段在生产优质钢的方面具有独特的优点,它的优点之一就是能够有效的去除钢中的非金属夹杂物。
实践表明,在重熔过程中,自耗电极中的原始夹杂可以去除,重熔钢中的夹杂主要是金属熔池冷却结晶过程中新生成的。
由于非金属夹杂物的存在,严重的影响了钢的强度、塑性等力学性能。
大量实践表明,钢中的氧化物夹杂与氧含量有着直接的关系(如图),氧化和还原是化学反应的两个方面,一个元素被氧化,必然伴随着一个元素的还原,在重熔过程中,钢中活泼元素如Al、Ti、Ce、B等,经常会因为氧化而损失。
如何防止活泼元素的氧化,是电渣重熔的重要冶金问题之一。
一、电渣过程中氧的来源电渣重熔过程中氧通过下述途径进入熔渣及钢液[1]:(1)原始电极钢中溶解的氧及电极中不稳定的氧化物在高温时分解放出的氧(2)电极表面生成的氧化铁皮随电极的重熔带入渣中的氧(3)氧直接从大气中通过渣池转移到金属熔池(4)渣中不稳定氧化物带入金属熔池中的氧二、熔渣的传氧实践表明,当原始电极中的氧含量较低时,电渣冶金实际是一个增氧过程,增氧的程度与渣系的选择密切相关。
W.W.Holzgruber等人通过对惰性气体保护下用不同氧分压及不同渣系分别重熔304不锈钢的含氧对比试验的结果进行分析后得出结论,大气中的氧能透过渣层进入金属中,其氧含量随大气中氧分压的增加而增加,另外不同的渣对氧有不同的透气性,并且其透气性与渣的稳定性相一致,即在惰性气氛下重熔时,钢中氧含量高的渣,其透气性也高。
许多实验已证明,由稳定性低的氧化物所组成的渣重熔的钢含氧量高;而由稳定性高的氧化物所组成的渣重熔的钢含氧量低。
熔渣的传氧方式主要由渣中不稳定的变价氧化物传递,如Fe、Ti、Mn 、Cr 等低价氧化物,在渣池表面吸收大气中的氧,形成高价氧化物。
这些元素的高价氧化物在渣池和金属熔池界面放出氧,变成低价氧化物,氧从而进入钢中,这一反应是一个循环过程。
以Fe的氧化物为例,其全部化学反应如下:2(FeO)+1/2 O2→(Fe2O3)(Fe2O3)+[Fe]→3(FeO)(FeO)→[Fe]+[O]这些元素的低价氧化物都是传氧物质,不断地将空气中的氧送入金属熔池,起到了“气筒”的作用为了准确理解熔渣在电渣过程与氧含量的关系,排除空气在实验过程中的影响,有人在保护气氛下做了如下电渣重熔实验1(如图1)[2]。
为保证安全,熔炼工在熔炼过程中必须要注意些什么?

为保证安全,熔炼工在熔炼过程中必须要注意些什么?湿型砂李群营一、熔炼过程中为保证安全应注意什么?1、常规安全要求(1)现场人员严格按照公司的规定要求,穿戴好劳动保护用品,并在观察高温金属时应使用专用滤光镜。
(2)炉内衬应按一定时间间隔经常检查,以防止“耗尽”。
冷却后检查炉内衬:炉衬厚度(不包括石棉板)经烧损小于65mm~80mm时,必须修炉。
加料应小心细致,以免出现料的“跨桥”、“结盖”。
“桥、盖”下边金属的超高温会造成炉衬腐蚀加快。
(3)炉料应干燥、不含易燃物、密闭容器,不过度生锈。
炉料中液体或易燃物的剧烈沸腾会导致金属液溢出甚至爆炸。
(4)炉前安全坑内不得有积水,以免铁水溅入、倾入后发生爆炸。
2、加料注意事项(1)不管炉料如何,都要在前次的炉料没有熔化完前慢速投入下次熔料。
如果错误地使用铁锈和粘砂多的炉料,炉料块度和形状不良,造成炉料装填不紧密和搭绷严重,或一次加的冷料过多,则容易发生“搭桥”。
必须经常检查液面,一出现搭桥现象,马上处理,捅掉“搭桥”避免“搭桥”形成。
否则下部的铁液就会过热,引起下部炉衬的侵蚀,甚至渗漏铁液或爆炸。
(2)搭桥处理方法:降低熔化电流至500A以下;用铁棒捅掉、穿;若未处理掉,则适当倾转电炉,保持小功率熔化,直至铁水冲破搭桥或结盖层。
(3)在炉料全部熔化后,应立即扒渣,防止结成“渣盖”。
如结成“渣盖”,应立即停电,将“渣盖”打碎扒出炉外,否则下部的铁液就会过热,引起下部炉衬的侵蚀,甚至渗漏铁液或爆炸。
二、熔炼的应急处理1、停电时的应急处理(1)冷却水的应急处理1)电炉控制室的配电总柜中双电源开关应保持在自切换档位,当主电源停电时,安保电源会自动切入,然后马上再次启动炉体水泵。
2)当主电源与安保电源同时停电,则马上通知值班电工,并且准备启动应急发电机,保证炉体的小水泵有电后运行炉体冷却水。
因而柴油发电机必须保证具备一定储量的柴油,而且与设备共同每月运行一次。
3)当柴油发电机也无法启动,则马上对炉体切入自来水。
电渣压力焊注意项
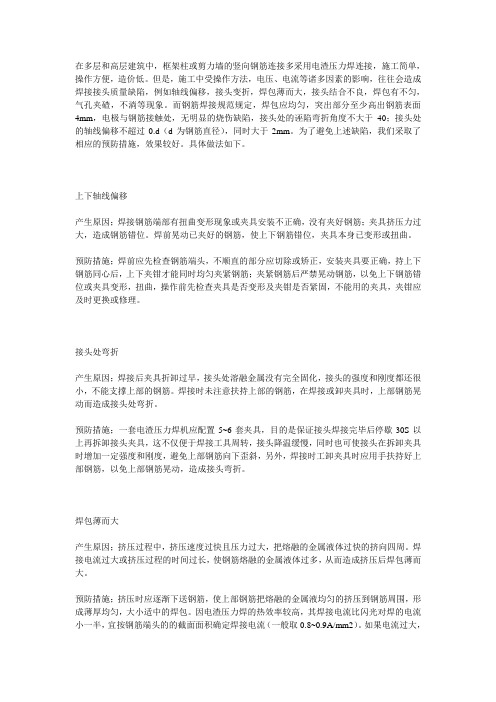
在多层和高层建筑中,框架柱或剪力墙的竖向钢筋连接多采用电渣压力焊连接,施工简单,操作方便,造价低。
但是,施工中受操作方法,电压、电流等诸多因素的影响,往往会造成焊接接头质量缺陷,例如轴线偏移,接头变折,焊包薄而大,接头结合不良,焊包有不匀,气孔夹碴,不淌等现象。
而钢筋焊接规范规定,焊包应均匀,突出部分至少高出钢筋表面4mm,电极与钢筋接触处,无明显的烧伤缺陷,接头处的诬陷弯折角度不大于40;接头处的轴线偏移不超过0.d(d为钢筋直径),同时大于2mm。
为了避免上述缺陷,我们采取了相应的预防措施,效果较好。
具体做法如下。
上下轴线偏移产生原因;焊接钢筋端部有扭曲变形现象或夹具安装不正确,没有夹好钢筋;夹具挤压力过大,造成钢筋错位。
焊前晃动已夹好的钢筋,使上下钢筋错位,夹具本身已变形或扭曲。
预防措施;焊前应先检查钢筋端头,不顺直的部分应切除或矫正,安装夹具要正确,持上下钢筋同心后,上下夹钳才能同时均匀夹紧钢筋;夹紧钢筋后严禁晃动钢筋,以免上下钢筋错位或夹具变形,扭曲,操作前先检查夹具是否变形及夹钳是否紧固,不能用的夹具,夹钳应及时更换或修理。
接头处弯折产生原因;焊接后夹具折卸过早,接头处溶融金属没有完全固化,接头的强度和刚度都还很小,不能支撑上部的钢筋。
焊接时未注意扶持上部的钢筋,在焊接或卸夹具时,上部钢筋晃动而造成接头处弯折。
预防措施;一套电渣压力焊机应配置5~6套夹具,目的是保证接头焊接完毕后停歇30S以上再拆卸接头夹具,这不仅便于焊接工具周转,接头降温缓慢,同时也可使接头在拆卸夹具时增加一定强度和刚度,避免上部钢筋向下歪斜,另外,焊接时工卸夹具时应用手扶持好上部钢筋,以免上部钢筋晃动,造成接头弯折。
焊包薄而大产生原因;挤压过程中,挤压速度过快且压力过大,把熔融的金属液体过快的挤向四周。
焊接电流过大或挤压过程的时间过长,使钢筋熔融的金属液体过多,从而造成挤压后焊包薄而大。
预防措施;挤压时应逐渐下送钢筋,使上部钢筋把熔融的金属液均匀的挤压到钢筋周围,形成薄厚均匀,大小适中的焊包。
高温合金电渣重熔锭表面缺陷的分析
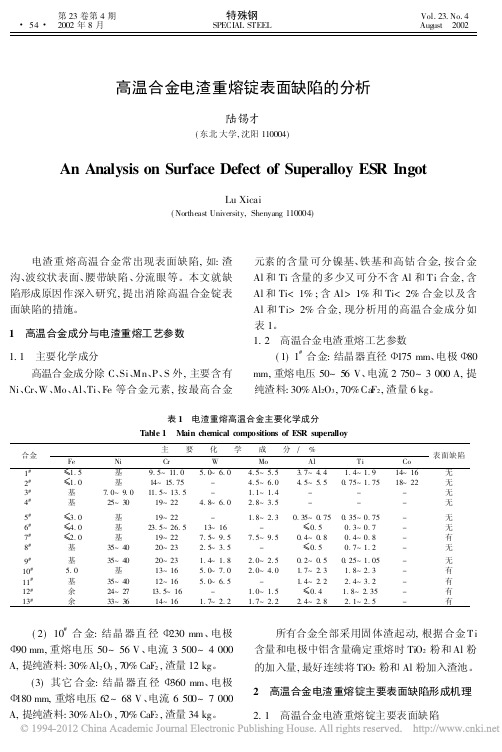
高温合金电渣重熔锭表面缺陷的分析陆锡才(东北大学,沈阳110004)An Analysis on Surface Defect of Superalloy ESR IngotLu Xicai(Northeast University,Shenyang 110004)电渣重熔高温合金常出现表面缺陷,如:渣沟、波纹状表面、腰带缺陷、分流眼等。
本文就缺陷形成原因作深入研究,提出消除高温合金锭表面缺陷的措施。
1 高温合金成分与电渣重熔工艺参数1.1 主要化学成分高温合金成分除C 、Si 、Mn 、P 、S 外,主要含有Ni 、Cr 、W 、Mo 、Al 、Ti 、Fe 等合金元素,按最高合金元素的含量可分镍基、铁基和高钴合金,按合金Al 和Ti 含量的多少又可分不含Al 和Ti 合金,含Al 和Ti<1%;含Al>1%和Ti<2%合金以及含Al 和Ti>2%合金,现分析用的高温合金成分如表1。
1.2 高温合金电渣重熔工艺参数(1)1#合金:结晶器直径5175mm 、电极580mm,重熔电压50~56V 、电流2750~3000A,提纯渣料:30%Al 2O 3,70%Ca F 2,渣量6kg 。
表1 电渣重熔高温合金主要化学成分Table 1 M ain chemical compositions of ESR superalloy合金主 要 化 学 成 分 P %Fe Ni Cr W Mo Al Ti Co 表面缺陷1#[1.5基9.5~11.0 5.0~6.0 4.5~5.5 3.7~4.4 1.4~1.914~16无2#[1.0基14~15.75- 4.5~6.0 4.5~5.50.75~1.7518~22无3#基7.0~9.011.5~13.5- 1.1~1.4---无4#基25~3019~22 4.8~6.0 2.8~3.5---无5#[3.0基19~22- 1.8~2.30.35~0.750.35~0.75-无6#[4.0基23.5~26.513~16-[0.50.3~0.7-无7#[2.0基19~227.5~9.57.5~9.50.4~0.80.4~0.8-有8#基35~4020~232.5~3.5-[0.50.7~1.2-无9#基35~4020~23 1.4~1.8 2.0~2.50.2~0.50.25~1.05-无10# 5.0基13~16 5.0~7.0 2.0~4.0 1.7~2.3 1.8~2.3-有11#基35~4012~16 5.0~6.5- 1.4~2.2 2.4~3.2-有12#余24~2713.5~16- 1.0~1.5[0.4 1.8~2.35-有13#余33~3614~16 1.7~2.21.7~2.22.4~2.82.1~2.5-有(2)10#合金:结晶器直径5230mm 、电极590mm,重熔电压50~56V 、电流3500~4000A,提纯渣料:30%Al 2O 3,70%CaF 2,渣量12kg 。
电渣压力焊质量通病及防治措施

电渣压力焊质量通病及防治措施工程质量保证措施1、质量目标本工程质量目标为合格。
为确保工程质量,从质量管理体系的各工序质量程度网络控制两大方面严格控制,并制定出相应的质量保证措施以确保工程的质量。
质量保证体系的管理组织,从公司到项目部,配套管理,形成严格的统一管理体系,定员定岗责任到人。
2、质量保证体系(1)建立健全质量保证体系,配备足够的专业质量检查人员,确保工程质量。
(2)加强技术管理,认真贯彻国家规范、操作规程及各项管理制度,确确岗位责任制,组织学习图纸、施工组织设计和工艺卡,做好技术交底工作,并建立技术考核制度。
(3)施工过程中,按部位检查操作方法和施工效果、及时纠正差错。
按部位及时填写应检查项目的隐、预检记录单,接受建设单位和质量检查人员检查。
督促班组执行自检、互检制和岗位责任制。
工程变更应提前办理。
如发生涉及结构的质量问题必须及时上报、不准擅自处理。
(4)测量、定位、放线必须准确,严格按施工测量定位方案进行。
定位控制桩要保护好,不得扰动。
(5)绑扎钢筋前要熟悉图纸,近配料检查加工的钢筋品种、规格、数量和形状,是否符合要求。
焊接接头经施焊人员自检后,抽样送到试验室进行机械性能试验。
(6)所有材料和半成品进场应有出厂合格证或检验报告,钢材应双控(合格证和检验报告)。
砼配合比示经试验室和技术经理同意,不得擅自变动。
原材料计量要准确,坍落度要严格控制,不得随意加水,搅拌机后台挂牌,标明配合比和每盘砼用料,砂、石、水泥要做原材料试验。
砼要振捣密实,防止漏振。
拆模后加强浇水养护,进行湿润养护并养护。
(7)严格工序交接制度。
要及时做好隐蔽工程验收记录,认真填写施工日记,确保技术资料完整。
(8)坚持预先定标准、定样板、定材料、定做法。
进场材料、半成品和加工品应执行验收手续,不符合要求的材料不得进场。
(9)土建和水电、安装由现场统一指挥,及时做好预埋件,认真做好各分项工程施工情况及检查记录和隐蔽工程验收记录,及时签证。
大型电渣重熔值得注意的几个问题
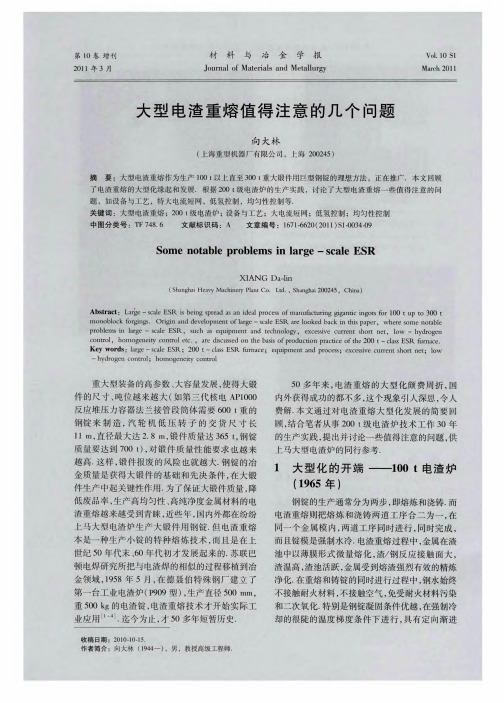
产品的制造过程 , 都必须利用一定 的设备通
过一 定 的工艺 才能 实现 . 设备 是产 品之母 , 工艺 是 产 品之父 . 即使 炉 子好用 , 还有 个会 不会 用 的问 也 题. 因此 , 须全 面掌握 熔炼 软技 术 和一 系列检 测 必 技 术 , 电制 度 、 制 度 、 如 渣 温度 制 度 、 度 制 度 、 速 启 动技 术 、 电极 技 术 、 锭技 术 、 换 抽 高均 匀性 控制 技 术 、 氢控 制技 术 、 氧控 制技 术 、 铝控 制技 术 、 低 低 低 脱氧 技术 、 补缩 技术 、 脱锭 技术 、 气分 析技 术 、 炉 炉
补缩 , 的 2 电渣 锭补 缩需 要好 几个 小时 , 有 0t 结果 钢锭 顶部 不是 包 了 一包 渣 就 是 存 在 暗缩 孔 . 于 至
A FB rqH O博士 都 曾 向笔 者证 实 , 一 再 称 . . oaeK 并
赞 中国 2 0t 0 电渣重熔 技 术 的先 进性 . 美 国康 萨 克公 司 ( o sr op ) 不掌 握大 C nacC r. 也
型 电渣重熔 工 艺 技术 , 管康 萨克 电渣 炉设 备 特 尽 别是供 电部分 做 得 还不 错 , 康 萨 克 大 型 电渣 炉 但 注定 是不 好用 的 . 萨 克公 司总裁 R JR br 博 康 .. oet s 士 曾称赞 中 国的 20t 电渣 炉 “ 一 个 很 好 的 0 级 是
材 料 与 冶 金 学 报
第1 0卷
产权 , 有 独 占性 , 密 程 度很 高 . 掌 握 大 型 电 具 保 不
电渣重熔冷轧辊坯的质量控制

( .S NOSe l n t c ie 1 I te Xiga Ma hn r i y&Mi l Co ,Ld l Rol . t ,Xig i 5 0 5,C ia l nt 42 a0 hn ;
关键词 :电渣重熔 ; 酸性渣 ; 预熔渣 ;夹杂物 ;质量 控制
中 图 分 类 号 :T 4 F 12 文 献 标 识 码 :A 文 章 编 号 :17 — 2 (0 1 S —0 1 4 6 16 0 2 1 ) 109 - 6 0
Qu lyc nr l fc l ol te r d cd b lcr s grme igp o es an r cs t o p a t
贾建平 ,张英杰 ,董艳伍 ,姜 周华
( .中钢 集团 邢 台机械轧辊有 限公司 ,邢 台 0 4 2 ;2 1 5 0 5 .东北大学 材料 与冶金学院 ,沈 阳 i00 ) 10 4 摘 要 :针 对本厂电渣重熔生产锻钢 冷轧辊 坯 的生产实 践进行 了冷 轧辊坯 质量控 制 的研究 工作.对 渣系 选
第1 0卷 增 刊
21 0 1年 3月
材
料
与 台 金
学
报
Vo. 0 S 1 1 1 Ma c O1 rh2 1
J u n lo t r l a d Me al r y o r a fMae i s n tl g a u
电渣 重 熔 冷 轧辊 坯 的质 量 控 制
近 年来 , 随着 工业 的发展 , 电渣 冶金 在 我 国特 种钢 材 的生 产 中发 挥 着 越 来 越 重要 的作 用. 机 邢 是专 业 的轧 辊生 产 企 业 , 生 产 的轧 辊 包 括 铸 钢 所
钢筋电渣压力焊注意事项
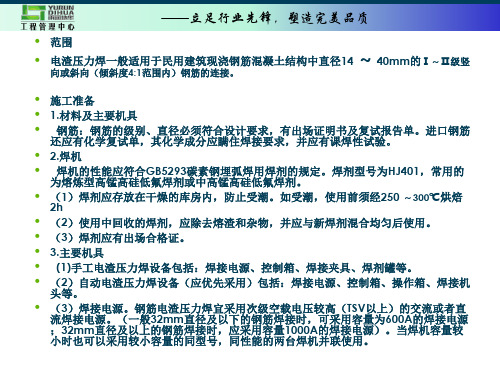
• (3)焊接电源。钢筋电渣压力焊宜采用次级空载电压较高(TSV以上)的交流或者直
流焊接电源。(一般32mm直径及以下的钢筋焊接时,可采用容量为600A的焊接电源 ;32mm直径及以上的钢筋焊接时,应采用容量1000A的焊接电源)。当焊机容量较 小时也可以采用较小容量的同型号,同性能的两台焊机并联使用。
•2.焊机 • 焊机的性能应符合GB5293碳素钢埋弧焊用焊剂的规定。焊剂型号为HJ401,常用的
为熔炼型高锰高硅低氟焊剂或中高锰高硅低氟焊剂。
• (1)焊剂应存放在干燥的库房内,防止受潮。如受潮,使用前须经250 ~300℃烘焙
2h
• (2)使用中回收的焊剂,应除去熔渣和杂物,并应与新焊剂混合均匀后使用。 • (3)焊剂应有出场合格证。 • 3.主要机具 • (1)手工电渣压力焊设备包括:焊接电源、控制箱、焊接夹具、焊剂罐等。 • (2)自动电渣压力焊设备(应优先采用)包括:焊接电源、控制箱、操作箱、焊接机
(2)电弧过程;引燃电弧后,应控制电压值。借助操纵杆 使上下钢筋端面之间保持一定的间距,进行电弧过程的延 时,是焊剂不断融化而形成必要深度的渣池。
(3)电渣过程;随后逐渐下送钢筋,使上钢筋端部都插入 渣池,电弧熄灭,进入电渣过程的延时,使钢筋全断面加 速融化。
(4)挤压断电;电渣过程结束,迅速下送钢筋,使其端面 与下钢筋端面相互接触,趁热排除熔渣和熔化金属。同事 切断电源。
程 t1 电渣过程t2 (表2-23)
• 16 200 ~250 40 ~ 45 22 ~27 14 4 • 18 250 ~ 300 40 ~ 45 22 ~ 27 15 5 • 20 300 ~ 350 40 ~ 45 22 ~ 27 17 5 • 22 350 ~ 400 40 ~ 45 22 ~ 27 18 6 • 25 400 ~ 450 40 ~ 45 22 ~ 27 21 6 • 28 500 ~ 550 40 ~ 45 22 ~ 27 24 6 • 32 600 ~ 650 40 ~ 45 22 ~ 27 27 7 • 36 700 ~ 750 40 ~ 45 22 ~ 27 30 8 • 40 850 ~ 900 40 ~ 45 22 ~ 27 33 9 • 方可夹紧钢筋。 • 钢筋一经夹紧,严防晃动,以免上下钢筋错位和夹具变形。
大锭电渣重熔
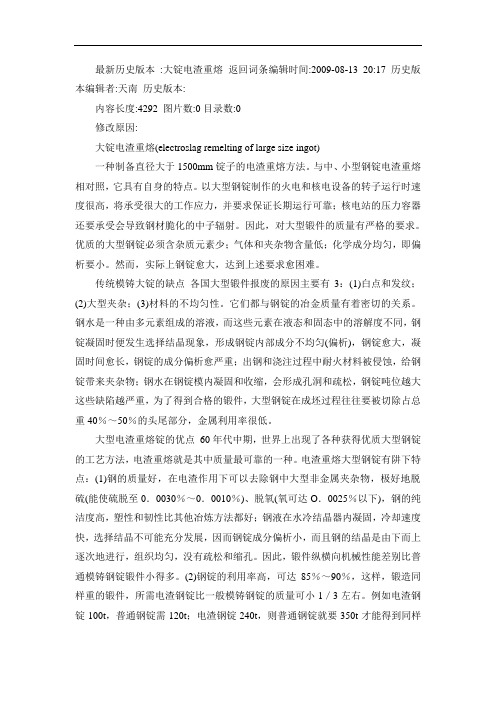
最新历史版本:大锭电渣重熔返回词条编辑时间:2009-08-13 20:17 历史版本编辑者:天南历史版本:内容长度:4292 图片数:0目录数:0修改原因:大锭电渣重熔(electroslag remelting of large size ingot)一种制备直径大于1500mm锭子的电渣重熔方法。
与中、小型钢锭电渣重熔相对照,它具有自身的特点。
以大型钢锭制作的火电和核电设备的转子运行时速度很高,将承受很大的工作应力,并要求保证长期运行可靠;核电站的压力容器还要承受会导致钢材脆化的中子辐射。
因此,对大型锻件的质量有严格的要求。
优质的大型钢锭必须含杂质元素少;气体和夹杂物含量低;化学成分均匀,即偏析要小。
然而,实际上钢锭愈大,达到上述要求愈困难。
传统模铸大锭的缺点各国大型锻件报废的原因主要有3:(1)白点和发纹;(2)大型夹杂;(3)材料的不均匀性。
它们都与钢锭的冶金质量有着密切的关系。
钢水是一种由多元素组成的溶液,而这些元素在液态和固态中的溶解度不同,钢锭凝固时便发生选择结晶现象,形成钢锭内部成分不均匀(偏析),钢锭愈大,凝固时间愈长,钢锭的成分偏析愈严重;出钢和浇注过程中耐火材料被侵蚀,给钢锭带来夹杂物;钢水在钢锭模内凝固和收缩,会形成孔洞和疏松,钢锭吨位越大这些缺陷越严重,为了得到合格的锻件,大型钢锭在成坯过程往往要被切除占总重40%~50%的头尾部分,金属利用率很低。
大型电渣重熔锭的优点60年代中期,世界上出现了各种获得优质大型钢锭的工艺方法,电渣重熔就是其中质量最可靠的一种。
电渣重熔大型钢锭有阱下特点:(1)钢的质量好,在电渣作用下可以去除钢中大型非金属夹杂物,极好地脱硫(能使硫脱至0.0030%~0.0010%)、脱氧(氧可达O.0025%以下),钢的纯洁度高,塑性和韧性比其他冶炼方法都好;钢液在水冷结晶器内凝固,冷却速度快,选择结晶不可能充分发展,因而钢锭成分偏析小,而且钢的结晶是由下而上逐次地进行,组织均匀,没有疏松和缩孔。
电渣压力焊的一些要求
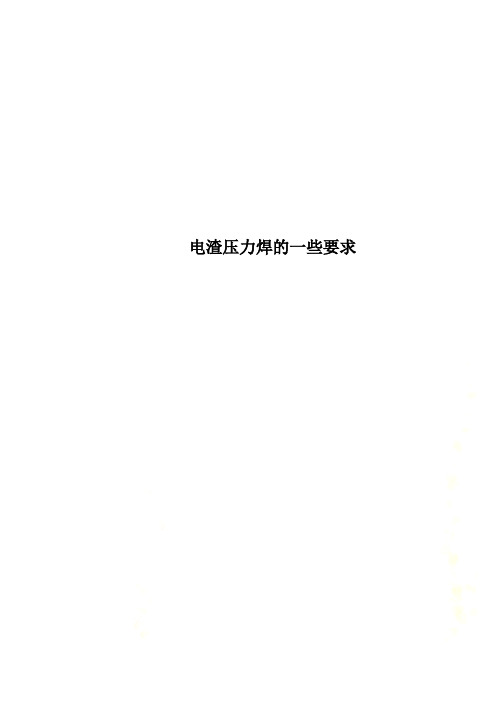
电渣压力焊的一些要求电渣压力焊的一些要求1、质量检查:在钢筋电渣压力焊的焊接生产中,焊工应认真进行自检,若发现偏心、弯折、烧伤、焊包不饱满等焊接缺陷,应切除接头重焊,并查找原因,及时消除。
切除接头时,应切除热影响区的钢筋,即离焊缝中心约为1.1倍钢筋直径的长度范围内的部分应切除。
2、电渣压力焊接头的力学性能检验必须合格。
力学性能检验时,从每批接头中随机切取3个接头作拉伸试验。
在一般构筑物中,以300个同钢筋级别接头作为一批。
在现浇钢筋混凝土多层结构中,以每一楼层或施工区段的同级别钢筋接头作为一批,不足300个接头仍作为一批。
3、焊接质量要求:1、焊包较均匀,突出部分最少高出钢筋表面4mm.2、电极与钢筋接触处,无明显的烧伤缺陷。
3、接头处的弯折角不大于4度。
4、接头处的轴线位移应不超过0.1倍钢筋直径,同时不大于2mm。
外观检查不合格的接头应切除重焊、或采取补救措施。
检验方法:目测或量测。
5 成品保护接头焊毕,应停歇20—30s后才能卸下夹具,以免接头弯折。
6 应注意的质量问题6.1 在钢筋电渣压力焊生产中,应重视焊接全过程中的任何一个环节。
接头部位应清理干净;钢筋安装应上下同心;夹具紧固,严防晃动;引弧过程,力求可靠;电弧过程,延时充分;电渣过程,短而稳定;挤压过程,压力适当。
若出现异常现象,应参照表4—24查找原因,及时清除。
钢筋电渣压力焊接头焊接缺陷与防止措施表4—246.2 电渣压力焊可在负温条件下进行,但当环境温度低于—20℃时,则不宜进行施焊。
雨天、雪天不宜进行施焊,必须施焊时,应采取有效的遮蔽措施。
焊后未冷却的接头,应避免碰到冰雪。
7 质量记录本工艺标准应具备以下质量记录:7.1 钢筋出厂质量证明书或试验报告单。
7.2 焊剂合格证。
7.3 钢筋机械性能复试报告。
7.4 进口钢筋应有化学成分检验报告和可焊性试验报告。
国产钢筋在加工过程中发生脆断、焊接性能不良和机械性能明显不正常的,应有化学成分检验报告。
大型电渣重熔值得注意的几个问题

大型电渣重熔值得注意的几个问题No.1January2011《大型铸锻件》HEA VYCASTINGANDFORGING大型电渣重熔值得注意的几个问题向大林(上海重型机器厂有限公司,上海200245)摘要:大型电渣重熔作为生产100t以上直至300t重大锻件用巨型钢锭的理想方法,正在被更多的人们所关注.本文回顾了电渣重熔的大型化缘起和发展.根据200t级电渣炉的实践经验,讨论了大型电渣重熔一些值得注意的问题,如设备与工艺,特大电流短网,低氢控制,均匀性控制等.关键词:大型电渣重熔;200t级电渣炉;设备与工艺;大电流短网;低氢控制;均匀性控制中图分类号:TFI4文献标识码:B SomeProblemsMeritingAttentioninLarge—scaleESRXiangDalinAbstract:Large—scaleESRisbeingspreadasanidealprocessofmanufacturinggiganticingotsfor100tupto3O Otmonoblockforgings.Originanddevelopmentoflarge—scaleESRwerelookedbackinthispaper.Someproblemsmeritingattentioninlarge—scaleESR,suchasequipmentandtechnology,excessivecurrentshoanet,lowhydrogencontr ol,homo-geneitycontroletc.,werediscussedonthebasisofproductionpracticeofthe200t-classESRfurnace.Keywords:large—scaleESR;200t-classESRfurnace;equipmentandtechnology;excessivecurrentshortnet;lo whydrogencontrol;homogeneitycontrol随着重大型装备向高参数,大容量发展,大锻件的尺寸,吨位也越来越大,如第三代核电AP1000反应堆压力容器法兰接管段筒体需要600t以上的钢锭来制造,汽轮机低压转子交货尺寸长11in,直径最大达2.8Ill,锻件重量达365t,钢锭重量要达到700t.而且锻件的质量和性能要求越来越高,锻件报废的风险也不断加大.钢锭的冶金质量是获得优质大锻件的基础和先决条件,在大锻件生产中起关键性作用.为了保证大锻件质量,降低废品率,生产高均匀性,高纯净度金属材料的电渣重熔越来越受到青睐.近些年,国内外都在纷纷上马大型电渣炉生产大锻件用钢锭.但电渣重熔本是一种生产小锭的特种熔炼技术,而且是在20世纪50年代末,60年代初才发展起来的.苏联巴顿电焊研究所(MH—TaneKTpOCBapKHHM.E.O.HaTOHa)把电渣焊的相似过程移植到冶金领域,1958年5月,在德聂伯特殊钢厂(3aBO~《)Inerapo—cnei~cTanb>>)建立了第一台工业电渣炉(P909型),生产直径500mm,重500kg的电渣锭,电渣重熔技术才开始实际工业应用叫.迄今为止,电渣重熔只有5O多年短暂历史.50多年来,电渣重熔的大型化颇费周折,获收稿日期:2O10—1O—2626得成功的案例并不多,这个现象引人深思,令人费解.本文通过对电渣重熔大型化发展过程的简要回顾,结合笔者从事200t级电渣炉技术工作30 年的实践经验,提出一些值得注意的问题并加以讨论,供大型电渣炉的同行参考.1大型化的开端——10Ot电渣炉(1965年)钢锭的生产通常分为两步,即熔炼和浇铸,而电渣重熔则把熔炼和浇铸两道工序合二为一.在同一个金属模内,两道工序同时进行,同时完成, 而且锭模是强制水冷.电渣重熔过程中,金属在渣池中以薄膜形式微量熔化,渣/钢反应接触面大,渣温高,渣池活跃,金属受到熔渣强烈有效的精炼净化.在重熔和铸锭同时进行的过程中,钢水始终不接触耐火材料,不接触空气,免受耐火材料污染和二次氧化.特别是,钢锭凝固条件优越, 是在强制冷却的,很陡的温度梯度条件下进行,具有定向渐进结晶特点.因此,在炉外精炼还不普遍也不发达的当时,电渣重熔的出现,显示出强大的生命力,各国竞相开发,纷纷采用.20世纪60 年代,电渣重熔迅速发展成为包括我国在内的世界各国生产高纯净度,高均匀性,耐高温高压,耐腐蚀磨损,抗冲击疲劳,抗中子辐照等质量要求苛刻的金属材料的主要冶金方法.《大型铸锻件》HEA VYCASTINGANDFORGINGNo.1January2011中国科技人员睿智卓识,对这一新生事物表现出极大的敏感性.电渣重熔既从内部创造了精炼净化金属的良好条件,又从外部杜绝了夹杂物的来源,尤其具有对于结晶至关重要的优越的冷却条件,而且它把熔炼和铸锭两道工序合二为一, 为解决当今世界上大钢锭的"纯净度"和"均匀性"两大冶金质量难题提供了将两者紧密结合的最佳条件.同时,电渣重熔设备简单,投资很少,工艺灵活,适应性,可控性强,操作易于掌握,质量可靠性高,经济合理有效.这些都是其他冶金方法无可比拟的.因此,电渣重熔问世不久,他们就迅速将这种本来是生产小钢锭的技术创造性地引人大型铸锻件行业,用以生产大锻件用优质大型钢锭. 1965年,很多国家包括一些工业发达国家刚刚开始起步研究电渣重熔技术,世界电渣炉的容量还仅仅在几吨的范围,在沈鸿及林宗棠的倡导和组织下,上海重型机器厂就已建成了100t的3相大型电渣炉(图1).这是世界上最早的大型电渣炉,也是当时世界上最大的电渣炉.其结晶器直径为1500mm和2100mln两种,内胆为钢质,是由3 节叠合而成的固定式长结晶器(1650mm×3).图1100t电渣炉Figure1100tESRfurnace重熔启动用自耗电极炉内化渣.渣料中常常有30%~50%的一次返回渣,渣化清即用A1块对炉渣进行预脱氧,渣池深度(350~380)mm.重熔过程中控制熔化速度,并用Al粉或/和ca.si 粉对炉渣进行脱氧.同时每隔(2~3)h取渣样和钢样分析,根据分析结果随时调整脱氧制度.自耗电极由原有1t小电弧炉生产,以小拼大,用50多炉乃至100多炉电极重熔成一根大型电渣锭. 3根自耗电极夹持在同一个升降机构上,由一台3 相炉用变压器(7500kV A)向3根电极供电同时重熔.所夹持的3根自耗电极同时上升或同时下降.自耗电极经车削加工而成,带螺纹接头.电极与电极通过电极头螺纹连接,和电弧炉石墨电极的连接方法相仿(图2).接电极时无需停电,边连接边送进,熔炼过程照样进行,可生产50t至100t大型电渣锭.设备于1965年初安装,1965年4月开始热调试,用1500mm结晶器于1965年6月29日熔炼出55t电渣锭.同年9月27 日,用2100mm结晶器熔炼出第一根100t电渣锭(60CrMnMo,Q2025mm×4050mm,图3). 1965年共生产了4根100t重的电渣锭.截止1972年11月,共熔炼生产了46根大型电渣锭, 钢种有60CrMnMo,35MnMoV,34CrMnMo,34CrNiMo,34CrNi3Mo,30CrMnMoNb,9Cr2Mo, 37SiMn2MoV,34CrMolA,34CrNi3MoV等. Figure2Consumptiveelectrodes100t电渣炉把当时世界上的电渣锭重量提高了两个数量级,并且解决了上海重型机器厂120MN水压机缺乏大钢锭的无米之炊问题,为制造我国当时最大的轧机2300mln冷轧机支撑辊做出了积极贡献.由于自耗电极需要机械加工,工序太繁杂,金属损耗大,生产成本高,特别是后来发现重熔至螺丝接头处时有小块电极金属脱落掉入金属熔池, 使锻件超声波探伤通不过而报废.这和20世纪30年代美国霍普金斯(R.K.Hopkins)用管状自耗电极熔炼时,重熔金属中不时发现有未熔化的管子电极碎片的情况相类似].此外,二次回路的压降和电感损失都较大,变压器容量的利用率和电效率都较低,钢内胆结晶器在叠合处常常发生局部熔化粘锭,使用寿命短,也不安全.因此,该炉于1972年底停止生产.27No.1January2011《大型铸锻件》HEA VYCASTINGANDFORGINGFigure3A100tESRingot100t电渣炉在世界上首开了电渣重熔大型化的先河,对大型电渣重熔的设备和工艺进行了开创性的尝试和探索,积累了极其宝贵的实践经验.2大型化的典型——160t电渣炉(1971年)和200t级电渣炉(1981年)2.1萨尔钢厂160t电渣炉1971年,西德萨尔钢厂(Saarstah1)建成结晶器直径2300mm的160t电渣炉,1980年l0月生产出第一根160t电渣锭.厂方称,用普通方法制造大锻件,技术上遇到的困难和经济上遭受的损失,使得在已经具备大型熔炼和浇铸手段的情况下被迫上了电渣炉.这座电渣炉(图4)设四个机架,四组彼此独立的供电系统分别对各机架供电.每组供电系统有一台变压器经可控硅变频装置输出(0~10)Hz的低频电供重熔用,以降低大电流二次回路的感抗,提高功率因数.自耗电极由130t电弧炉熔炼,经DH提升脱气处理之后浇铸而成.当使用f2j2300mm,【2j1700mm结晶器时,4根电极同时重熔.当改换成1300mm,(2j1000mm结晶器时,则采用单电极重熔,通过更换电极和抽锭操作,能生产长达(5—6)m的电渣锭,相应的锭重为160t,90t和50t,30t.2.2上海重型机器厂200t电渣炉20世纪70年代,我国第一座核电站秦山核电站开始筹建,秦山核电大锻件需要360t重的电炉钢锭.为了经济而可靠地向核电站提供核电大锻件,在深入研究了大锻件生产的主要质量问题28Figure4160tESRfumaceatremehing和特殊性,认真总结了上海重型机器厂20世纪60年代100t电渣炉的生产实践经验的基础上, 在朱觉教授的精心指导下,上海重型机器厂于1981年创建了世界上最大的200t级电渣炉(图5,图6,图7),并于1983年10月31日生产出第一根205t电渣锭.炉子设3个机架,呈等边三角形布置,每个机架的电极支臂上夹持呈串联形式的两根自耗电极.3个机架各由一台单相变压器供电,6根电极构成3相双极串联回路.自耗电极由40t电弧炉熔炼,经RH循环脱气处理之后浇铸而成.炉子装备了干燥空气保护,除尘和烟气净化设施.重熔过程中交错更换电极,根据锻件需要,可通过抽锭生产240t((2j2730mm×5200mm)以内的任意重量的电渣锭.若更换成直径3300mm的结晶器,则可生产300t重的电渣锭.就重量上说,240t电渣锭相当于400t电炉锭,可生产200t重的锻件;300t电渣锭相当于500t电炉锭,可生产250t重的锻件.该电渣炉还可用于单相重熔,生产不同直径,各种吨位的中小型电渣锭.炉子建成后,针对重熔工艺的关键技术展开了全方位,多层面的深入系统的研究,攻克了一系列重大技术难题,主要有:(1)均匀性控制技术解决了用成分有差异的若干炉号,数十根电极,通过几个昼夜重熔成一根200t电渣锭的成分均匀性问题.(2)大功率,快熔速,高冷却和强脱氧工艺为获得高质量巨型电渣锭提供了重要保证.大功率供电,渣温高,冶金反应的动力学条件好,精炼净化效果强.虽然熔速高达5t/h以上,但由于有《大型铸锻件》HEA VYCASTINGANDFORGINGNo.1January2011Figure5200t—classESRfurnaceatremelting图6核电用207t电渣锭Figure6A207tESRingotfornuclearpower图7核电用205t电渣锭Figure7A205tESRingotfornuclearpower高速强制冷却,使得熔池浅,成分均匀,组织致密. 强制脱氧使渣池始终保持低氧位(FeO≤0.3%), 高冶金性能.因此,200t级电渣炉生产的电渣锭热塑性良好,锻压时一次压下量达1000mm也不开裂.电渣锭中心的密度与锭边缘密度一致.锭中心的二次枝晶间距仅为2mm.氧化物0.5级,硫化物找不到.直径为2113的锻件,超声波探伤起始灵敏度1.1mm也能通过J.(3)低氢控制技术解决了高湿度气候条件下长时间重熔获得低氢巨型电渣锭的难题. 尽管上海气候潮湿,空气湿度高达30gHO/m,熔炼区气/渣接触面积有5m大,但几个昼夜的重熔过程中,低氢控制技术使重熔与天气和季节无关.使用冷渣料对低氢控制没有明显影响.电渣锭中的氢含量都不超过2×10~,大部分在1.4 ×10以下.数十个大锻件,包括直径为2000mm的汽轮机低压转子,完全取消扩氢退火后无一发现白点.(4)低铝控制技术¨扫除了电渣重熔法生产汽轮机转子的障碍.汽轮机转子中的铝不允许超过0.010%(质量分数),而电渣重熔获得低铝非常困难.当用低铝电极重熔时,总是发生增铝,因为渣中含有大量铝.当电极中的铝超过0.010%(质量分数)时,重熔过程中更难以将其降至0.010%以下.用自主研发的低铝,低氧,低硫兼得的重熔工艺技术'"批量生产的高,中,低压汽轮机转子,铝均控制在0.005%~0.007% 之间,氧,硫均在25×10以下,大部分为20X10-.'.30年来,200t级电渣炉一直在生产运行,在完成国家重点建设项目的攻关任务中做出了一个又一个重大贡献,不断受到国内外专家的关注和推崇.主要产品有:(1)炉子建成首先是生产秦山核电站核岛大锻件用电渣锭.1981年10月10日重熔出127t核电用电渣锭,1983年10月31日和11月18日连续两次生产出205t和207t核电用电渣锭,到1984年底共生产核电用电渣锭24根,锭重多在(130~170)t之间,完成了秦山核电站核岛大锻件所需大钢锭的生产任务.用电渣锭成套生产的蒸发器和稳压器等核电大锻件,经有关部门5大类35项材料内在质量严格测试,技术性能符合设计要求,综合质量达到ASME标准,通过国家级鉴定和验收.秦山核电站1991年l2月15日并网发电,提前两年达到年发电设计能力.20年过去了,作为"国之光荣",秦山核电站至今运行情况良好.(2)此后,相继批量生产了300MW发电机转子,300MW一600MW汽轮机高.中压和低压转子,560t加氢反应器等大锻件,全部通过国家级鉴定和验收.(3)进入21世纪,凭借技术优势,批量生产了核潜艇堆内构件,三峡工程710MW水轮机导叶轴头,1000MW核电站堆内构件,1000MW超超临界汽轮机转子等高合金大锻件,获得了巨大29No.1January2011《大型铸锻件》HEA VYCASTINGANDFORGING的经济效益.一个国家的钢铁工业发展和冶金技术水平,既要看钢的产量,品种和质量,还要看能生产多大的钢锭和大钢锭的质量有多高.巨型钢锭的生产技术反应了一个国家重工业的发展水平和科学技术的攻坚能力,也是一个企业实力和等级水平的象征.作为中国的自主原创技术,200t级电渣炉开辟了生产优质巨型钢锭的新方法,新途径,因对世界特种熔炼技术的重大贡献,曾于1988年在美国举行的第九届国际真空冶金会议(9thICVM)上获大奖(图8).在我国的工业现代化发展过程中,由中国人独创,从研究开发到付诸工业生产应用并达到世界领先地位,在国际上获奖的重大项目还为数不多.图8的奖牌Figure8Themedia(9thICVM)2.3其它大型电渣炉此外,还有一些见诸于苏联文献的苏联建造大型电渣炉的报道.如,1979~1980年在新克拉马托尔斯克机器制造厂(HKM3)安装了~iiiri?15o型电渣炉¨...据称,该电渣炉由3台单相变压器供电,总功率为(12—14)MV A(4800kV AX3).液渣启动,采用上部加大的漏斗形结晶器(Q)3360mm).上部加大处为熔化部分,下部为成型部分(O2550mm),其截面积等于自耗电极的总截面积或者大20%.渣量(11~12)t.结晶器加大处装有钢液面传感器,还有供注入或排出液渣用的孔眼.熔炼过程中向金属熔池和渣池吹入惰性气体.可熔炼直径(1800~2700)mm,重(80—200)t的电渣锭和外径(1800~2700)mm, 内径(600~800)mm的空心锭,并可同时熔炼3 个重(30—60)t的电渣锭.采用7根电极操作,熔炼80t锭时电极直径为650mm,熔炼200t锭时电极直径为1000mm.重熔时电极不进给,短网也不动,只有结晶器上移.苏联出口朝鲜千里马钢厂的200t电渣炉也是这种炉型结构,但是根30本无法开炉炼钢,请中国专家去也爱莫能助.又如,YUI一108型电渣炉,变压器容量为3 500kV A×3(单相),可熔炼2500mm/100t的空心锭和实心锭;日丹诺夫重型机器厂(TM)的YlII-100型电渣炉J,变压器容量为2500kV AX3(单相),可熔炼O2300mm/120t的空心锭和实心锭,等等.但是30年过去了,至今也未见那些炉子投人生产使用的报道.3大型化的新进展(2008年以后)为了满足市场急需,提升企业核心竞争力,上海重型机器厂有限公司2008年着手投建结晶器直径为37001Tim的450t电渣炉.450t电渣锭相当于(6oo一700)t电炉锭,覆盖了当前世界上所有最大吨位的锻件用钢锭.历时一年,于2009 年4月建成(图9),5月5日热调试成功,现已投入试运行.2009年开炉重熔11炉,根据锻件需要,现已顺利重熔出220t,320t的核电压力容器用电渣锭.450t电渣炉的产品对象主要是百万千瓦级核电机组的核岛锻件,汽轮机低压转子,管板和大型支撑辊等超大型锻件.此外,第一重型机械集团公司的120t电渣炉从2010年5月已开始调试;东北特钢正在大连基地上马100t电渣炉(从奥地利Inteco公司引进),计划在2011年7月投入运行;无锡桥联集团的300t电渣浇注炉已从2009年开始设计(由乌克兰巴顿电焊研究所的Elmet-Roll-MedovarGroup 承担),还有一些单位正在筹建200t和400t电渣炉.尤为可喜的是,通裕重工股份有限公司通过技术改革,实现了电渣重熔技术的提升和跨越. 2009年4月冶炼出第三代核电AP1000主管道用超低碳控氮不锈钢(SA376TP316LN)72t电渣锭,而且是一次成功;2009年生产的几根75t电渣锭,锭高4.1nl,锭子上下成分一致,底部质量,顶部补缩和低倍组织优良,洁净度高.[H]=1XlO,『O1=17×10I¨,[S]=20×10I¨.2010年4,5月,通裕重工又率先顺利生产出一套第三代核电AP1000主管道用超低碳控氮不锈钢(SA376 TP316LN)大型电渣锭8根.这不仅是国内也是世界上首次成套生产出AP1000主管道用核级超低碳控氮不锈钢大型电渣锭.AP1000主管道是我国引进AP1000核电技术项目中唯一没有引进国外技术的核岛关键设备,被称之为核电站的"主动脉",属于核1级设备.AP1000主管道用超低碳控氮不锈钢大型电渣锭的生产技术是《大型铸锻件》HEA VYCASTINGANDF0RGINGNO.1January201】AP1000主管道制造的核心技术,是主管道制造的限制性环节.AP1000主管道用超低碳控氮不锈钢大型电渣锭成套生产成功,解决了我国第三代核电主管道国产化的瓶颈制约问题,对于我国大力发展核电事业是一个不小的贡献.迄今为止,通裕重工已生产(70~82)t的大型电渣锭近20 根,质量稳定.据报道,Et本,德国,意大利以及欧洲其他一些工业发达国家近年也在陆续投建250t,150t, 145t,120t,110t,100t大型电渣炉.Figure9450tESRfurnaceatremelting4大型电渣炉值得注意的几个问题电渣炉相对于电弧炉等其他熔炼设备而言是比较简单的,但由于设备容量的大型化而引发的一些问题则不容忽视.世界上好几台大型电渣炉都不成功的教训是深刻的.根据笔者从事200t级电渣炉技术工作30年的实践,认为大型电渣炉至少以下几方面值得认真注意:4.1电渣重熔工艺设计是灵魂设备是正常生产的基本保障,对生产工艺有关键性影响.所谓"工欲善其事,必先利其器",在某种意义上甚至可以说设备比生产工艺本身还重要.其实生产设备是根据生产工艺而设计的,它在各方面的工作性能必须要满足生产工艺的要求,需要两者的和谐统一,完美结合.并且设备要有很强的适应性,要能充分满足生产工艺所涉及的调整范围.好些大型电渣炉不好用,甚至无法重熔生产,常常是缺少工艺设计.重熔工艺是生产电渣锭的各种过程参数,规范程序和操作方法.重熔工艺设计是全面规划和具体描述电渣重熔生产实施意图的过程,是电渣炉设计中的"灵魂".电渣炉还没有形成标准化,系列化.大型电渣炉的工业化生产,也才仅仅40年短暂时间.奥地利Inteco公司总裁W.Holzgruber博士说,技术上突破100t的电渣炉仅有德国萨尔钢厂和中国上海重型机器厂两家.可想而知,大型电渣重熔特别是100t以上的炉子的工业生产实践经验是极其有限的.这种本来是生产小锭的特种熔炼技术,炉容量十倍百倍地扩大,使得很多工艺因素复杂化,这不是一个简单的数量增加,而是跨越,质的飞跃.科学上的新发现可以通过论文和网络技术很快地在全世界范围内传播开来,知识全球共享,但新的工艺技术却是企业的Know-how(专有技术),是企业的看家本领,是企业的核心竞争力,往往具有知识产权,具有独占性,保密程度很高.如果没有掌握大型电渣重熔的工艺技术,工艺设计又从何谈起?如果设备设计者对重熔工艺茫然无知,那这种由没有灵魂的设计建造的设备怎么可能好用?苏联本是电渣重熔技术的发源地,但是苏联的大型电渣炉并不成功,其主要原因就在于苏联没有掌握大型电渣重熔工艺技术.对此,IO.B. BaTam教授,A.F.~oFaqeHKO博士都曾向笔者证实,并一再称赞中国200t电渣重熔技术的先进性.美国康萨克公司(ConsarcCorp.)也不掌握大型电渣重熔工艺技术.尽管康萨克电渣炉设备特别是供电部分做得还不错,但康萨克大型电渣炉注定是不好用的.康萨克公司总裁R.J.Roberts博士曾称赞中国的200t级电渣炉"是一个很好的设计".奥地利Inteco公司称,他们2008年开始设计的一台250t电渣炉,采用的是3~4根(60—80)t 的自耗电极.可以想象,电极的制备不是件容易的事,支撑电极的结构也不会轻便,变压器容量也会非常之大.因为该公司还为意大利FOMAS锻造厂设计了一台结晶器直径为2050mm的120t 电渣炉,计划于2011年2月投产,也采用同样的方案,变压器容量有30000kV A之大,超过30年前苏联建造的结晶器直径为3360mm的200t电渣炉变压器容量的两倍.我国东北特钢在2009年也向该公司引进了一台类似结构的100t电渣炉.这些炉子都还没有建成,祝愿它们都能顺利投产.20世纪80年代,中国的200t级电渣炉之所以能一次调试成功就重熔出合格的90t转子电渣锭,第二次调试就重熔出合格的127t核电电渣锭,炉子建成3年就生产出核电蒸发器用205t电渣锭,是因为200t级电渣炉是根据我国电渣冶金的开山祖师朱觉教授及刘海洪教授的工艺思想进31No.1January2011《大型铸锻件》HEA VYCASTINGANDFORGING行设计的,是建立在100t电渣炉的工程实践和生产经验的基础上的.中国的450t电渣炉从设计制造到安装调试仅只一年时间,也是一次调试成功就投入生产运行.如果没有200t级电渣炉2O 多年的技术开发和生产经验,那是不可想象的. 中国的200t级电渣炉和450t电渣炉的成功说明,工艺思想的确是电渣炉的灵魂.4.2设备是产品之母,工艺是产品之父产品的制造过程,都必须利用一定的设备通过一定的工艺才能实现.设备是产品之母,工艺是产品之父.即使炉子好用,也还有个会不会用的问题.因此,必须全面掌握熔炼软技术和一系列检测技术.如电制度,渣制度,温度制度,速度制度,启动技术,换电极技术,抽锭技术,高均匀性控制技术,低氢控制技术,低氧控制技术,低铝控制技术,脱氧技术,补缩技术,脱锭技术,炉气分析技术,炉渣分析技术,熔池检测技术等.必须强化气氛可控,重熔过程可控和凝固过程可控,提高过程控制水平,才能稳定可靠地生产出合格产品. 不掌握这些专有技术,在生产中,在质量上都会产生很大的迷茫,困惑和麻烦.比如,电渣重熔首先要造渣,上海重型机器厂的200t级电渣炉5t渣料,用时75min,钢锭底部质量良好以至在生产筒体锻件时无需切除;可是一些炉子1t渣料,通常要用150min,钢锭底部质量还不尽如人意.又如,电渣重熔结束前要进行补缩,有的20t电渣锭补缩折腾好几个小时,结果钢锭顶部不是包了一包渣就是存在暗缩孔.至于低氢控制问题,那更是普遍存在的了.而设备设计和销售单位往往并不具备这些专有技术.长期以来,我们习惯更多地依赖科研机构和大学,但近百年世界产业发展的历史表明,真正起作用的技术几乎都来自企业(比如,通讯领域的贝尔,汽车领域的福特,飞机领域的波音和空客,化工领域的杜邦和拜耳,机床领域的西门子,计算机领域的IBM,英特尔,微软, 等等).道理很简单,实际熔炼时开发的技术和生产现场积累的经验才是真实可靠的,才是有实用价值的.4.3特大电流问题大型电渣炉是特大电流用电设备,有的甚至高达100kA.因此,炉子短网电气特性就显得非常重要,否则功率因数不高,有功分量的效率太低,会给熔炼造成很大困难.导体的感抗量是由导体本身磁通变化引起的自感和由相邻导体磁通变化所引起的互感的几何32和.为了降低大电流网路感抗,提高功率因数(cos),减少无功损耗,有的采用双极串联供电,通过平行布线和交错布线,使电流回路互相靠近, 外部磁场大大抵消.我国200t级电渣炉和450t电渣炉就采用了这种办法,cos~p可高达0.80—0.93.由于电感与电流频率成正比,所以采用低频电源可以降低短网大电流所引起的感抗损失,提高功率因数.德国莱宝公司(LeyboldAG)制造的电渣炉大都采用低频供电.比如,由莱宝公司设计制造的萨尔钢厂的160t电渣炉就是(0~10) Hz的低频电源,达到较高的功率因数.采用同轴布置或同轴电缆是减少短网电抗,提高功率因数的又一方案.美国康萨克公司。
- 1、下载文档前请自行甄别文档内容的完整性,平台不提供额外的编辑、内容补充、找答案等附加服务。
- 2、"仅部分预览"的文档,不可在线预览部分如存在完整性等问题,可反馈申请退款(可完整预览的文档不适用该条件!)。
- 3、如文档侵犯您的权益,请联系客服反馈,我们会尽快为您处理(人工客服工作时间:9:00-18:30)。
大型电渣重熔值得注意的几个问题No.1January2011《大型铸锻件》HEA VYCASTINGANDFORGING大型电渣重熔值得注意的几个问题向大林(上海重型机器厂有限公司,上海200245)摘要:大型电渣重熔作为生产100t以上直至300t重大锻件用巨型钢锭的理想方法,正在被更多的人们所关注.本文回顾了电渣重熔的大型化缘起和发展.根据200t级电渣炉的实践经验,讨论了大型电渣重熔一些值得注意的问题,如设备与工艺,特大电流短网,低氢控制,均匀性控制等.关键词:大型电渣重熔;200t级电渣炉;设备与工艺;大电流短网;低氢控制;均匀性控制中图分类号:TFI4文献标识码:B SomeProblemsMeritingAttentioninLarge—scaleESRXiangDalinAbstract:Large—scaleESRisbeingspreadasanidealprocessofmanufacturinggiganticingotsfor100tupto3O Otmonoblockforgings.Originanddevelopmentoflarge—scaleESRwerelookedbackinthispaper.Someproblemsmeritingattentioninlarge—scaleESR,suchasequipmentandtechnology,excessivecurrentshoanet,lowhydrogencontr ol,homo-geneitycontroletc.,werediscussedonthebasisofproductionpracticeofthe200t-classESRfurnace.Keywords:large—scaleESR;200t-classESRfurnace;equipmentandtechnology;excessivecurrentshortnet;lo whydrogencontrol;homogeneitycontrol随着重大型装备向高参数,大容量发展,大锻件的尺寸,吨位也越来越大,如第三代核电AP1000反应堆压力容器法兰接管段筒体需要600t以上的钢锭来制造,汽轮机低压转子交货尺寸长11in,直径最大达2.8Ill,锻件重量达365t,钢锭重量要达到700t.而且锻件的质量和性能要求越来越高,锻件报废的风险也不断加大.钢锭的冶金质量是获得优质大锻件的基础和先决条件,在大锻件生产中起关键性作用.为了保证大锻件质量,降低废品率,生产高均匀性,高纯净度金属材料的电渣重熔越来越受到青睐.近些年,国内外都在纷纷上马大型电渣炉生产大锻件用钢锭.但电渣重熔本是一种生产小锭的特种熔炼技术,而且是在20世纪50年代末,60年代初才发展起来的.苏联巴顿电焊研究所(MH—TaneKTpOCBapKHHM.E.O.HaTOHa)把电渣焊的相似过程移植到冶金领域,1958年5月,在德聂伯特殊钢厂(3aBO~《)Inerapo—cnei~cTanb>>)建立了第一台工业电渣炉(P909型),生产直径500mm,重500kg的电渣锭,电渣重熔技术才开始实际工业应用叫.迄今为止,电渣重熔只有5O多年短暂历史.50多年来,电渣重熔的大型化颇费周折,获收稿日期:2O10—1O—2626得成功的案例并不多,这个现象引人深思,令人费解.本文通过对电渣重熔大型化发展过程的简要回顾,结合笔者从事200t级电渣炉技术工作30 年的实践经验,提出一些值得注意的问题并加以讨论,供大型电渣炉的同行参考.1大型化的开端——10Ot电渣炉(1965年)钢锭的生产通常分为两步,即熔炼和浇铸,而电渣重熔则把熔炼和浇铸两道工序合二为一.在同一个金属模内,两道工序同时进行,同时完成, 而且锭模是强制水冷.电渣重熔过程中,金属在渣池中以薄膜形式微量熔化,渣/钢反应接触面大,渣温高,渣池活跃,金属受到熔渣强烈有效的精炼净化.在重熔和铸锭同时进行的过程中,钢水始终不接触耐火材料,不接触空气,免受耐火材料污染和二次氧化.特别是,钢锭凝固条件优越, 是在强制冷却的,很陡的温度梯度条件下进行,具有定向渐进结晶特点.因此,在炉外精炼还不普遍也不发达的当时,电渣重熔的出现,显示出强大的生命力,各国竞相开发,纷纷采用.20世纪60 年代,电渣重熔迅速发展成为包括我国在内的世界各国生产高纯净度,高均匀性,耐高温高压,耐腐蚀磨损,抗冲击疲劳,抗中子辐照等质量要求苛刻的金属材料的主要冶金方法.《大型铸锻件》HEA VYCASTINGANDFORGINGNo.1January2011中国科技人员睿智卓识,对这一新生事物表现出极大的敏感性.电渣重熔既从内部创造了精炼净化金属的良好条件,又从外部杜绝了夹杂物的来源,尤其具有对于结晶至关重要的优越的冷却条件,而且它把熔炼和铸锭两道工序合二为一, 为解决当今世界上大钢锭的"纯净度"和"均匀性"两大冶金质量难题提供了将两者紧密结合的最佳条件.同时,电渣重熔设备简单,投资很少,工艺灵活,适应性,可控性强,操作易于掌握,质量可靠性高,经济合理有效.这些都是其他冶金方法无可比拟的.因此,电渣重熔问世不久,他们就迅速将这种本来是生产小钢锭的技术创造性地引人大型铸锻件行业,用以生产大锻件用优质大型钢锭. 1965年,很多国家包括一些工业发达国家刚刚开始起步研究电渣重熔技术,世界电渣炉的容量还仅仅在几吨的范围,在沈鸿及林宗棠的倡导和组织下,上海重型机器厂就已建成了100t的3相大型电渣炉(图1).这是世界上最早的大型电渣炉,也是当时世界上最大的电渣炉.其结晶器直径为1500mm和2100mln两种,内胆为钢质,是由3 节叠合而成的固定式长结晶器(1650mm×3).图1100t电渣炉Figure1100tESRfurnace重熔启动用自耗电极炉内化渣.渣料中常常有30%~50%的一次返回渣,渣化清即用A1块对炉渣进行预脱氧,渣池深度(350~380)mm.重熔过程中控制熔化速度,并用Al粉或/和ca.si 粉对炉渣进行脱氧.同时每隔(2~3)h取渣样和钢样分析,根据分析结果随时调整脱氧制度.自耗电极由原有1t小电弧炉生产,以小拼大,用50多炉乃至100多炉电极重熔成一根大型电渣锭. 3根自耗电极夹持在同一个升降机构上,由一台3 相炉用变压器(7500kV A)向3根电极供电同时重熔.所夹持的3根自耗电极同时上升或同时下降.自耗电极经车削加工而成,带螺纹接头.电极与电极通过电极头螺纹连接,和电弧炉石墨电极的连接方法相仿(图2).接电极时无需停电,边连接边送进,熔炼过程照样进行,可生产50t至100t大型电渣锭.设备于1965年初安装,1965年4月开始热调试,用1500mm结晶器于1965年6月29日熔炼出55t电渣锭.同年9月27 日,用2100mm结晶器熔炼出第一根100t电渣锭(60CrMnMo,Q2025mm×4050mm,图3). 1965年共生产了4根100t重的电渣锭.截止1972年11月,共熔炼生产了46根大型电渣锭, 钢种有60CrMnMo,35MnMoV,34CrMnMo,34CrNiMo,34CrNi3Mo,30CrMnMoNb,9Cr2Mo, 37SiMn2MoV,34CrMolA,34CrNi3MoV等. Figure2Consumptiveelectrodes100t电渣炉把当时世界上的电渣锭重量提高了两个数量级,并且解决了上海重型机器厂120MN水压机缺乏大钢锭的无米之炊问题,为制造我国当时最大的轧机2300mln冷轧机支撑辊做出了积极贡献.由于自耗电极需要机械加工,工序太繁杂,金属损耗大,生产成本高,特别是后来发现重熔至螺丝接头处时有小块电极金属脱落掉入金属熔池, 使锻件超声波探伤通不过而报废.这和20世纪30年代美国霍普金斯(R.K.Hopkins)用管状自耗电极熔炼时,重熔金属中不时发现有未熔化的管子电极碎片的情况相类似].此外,二次回路的压降和电感损失都较大,变压器容量的利用率和电效率都较低,钢内胆结晶器在叠合处常常发生局部熔化粘锭,使用寿命短,也不安全.因此,该炉于1972年底停止生产.27No.1January2011《大型铸锻件》HEA VYCASTINGANDFORGINGFigure3A100tESRingot100t电渣炉在世界上首开了电渣重熔大型化的先河,对大型电渣重熔的设备和工艺进行了开创性的尝试和探索,积累了极其宝贵的实践经验.2大型化的典型——160t电渣炉(1971年)和200t级电渣炉(1981年)2.1萨尔钢厂160t电渣炉1971年,西德萨尔钢厂(Saarstah1)建成结晶器直径2300mm的160t电渣炉,1980年l0月生产出第一根160t电渣锭.厂方称,用普通方法制造大锻件,技术上遇到的困难和经济上遭受的损失,使得在已经具备大型熔炼和浇铸手段的情况下被迫上了电渣炉.这座电渣炉(图4)设四个机架,四组彼此独立的供电系统分别对各机架供电.每组供电系统有一台变压器经可控硅变频装置输出(0~10)Hz的低频电供重熔用,以降低大电流二次回路的感抗,提高功率因数.自耗电极由130t电弧炉熔炼,经DH提升脱气处理之后浇铸而成.当使用f2j2300mm,【2j1700mm结晶器时,4根电极同时重熔.当改换成1300mm,(2j1000mm结晶器时,则采用单电极重熔,通过更换电极和抽锭操作,能生产长达(5—6)m的电渣锭,相应的锭重为160t,90t和50t,30t.2.2上海重型机器厂200t电渣炉20世纪70年代,我国第一座核电站秦山核电站开始筹建,秦山核电大锻件需要360t重的电炉钢锭.为了经济而可靠地向核电站提供核电大锻件,在深入研究了大锻件生产的主要质量问题28Figure4160tESRfumaceatremehing和特殊性,认真总结了上海重型机器厂20世纪60年代100t电渣炉的生产实践经验的基础上, 在朱觉教授的精心指导下,上海重型机器厂于1981年创建了世界上最大的200t级电渣炉(图5,图6,图7),并于1983年10月31日生产出第一根205t电渣锭.炉子设3个机架,呈等边三角形布置,每个机架的电极支臂上夹持呈串联形式的两根自耗电极.3个机架各由一台单相变压器供电,6根电极构成3相双极串联回路.自耗电极由40t电弧炉熔炼,经RH循环脱气处理之后浇铸而成.炉子装备了干燥空气保护,除尘和烟气净化设施.重熔过程中交错更换电极,根据锻件需要,可通过抽锭生产240t((2j2730mm×5200mm)以内的任意重量的电渣锭.若更换成直径3300mm的结晶器,则可生产300t重的电渣锭.就重量上说,240t电渣锭相当于400t电炉锭,可生产200t重的锻件;300t电渣锭相当于500t电炉锭,可生产250t重的锻件.该电渣炉还可用于单相重熔,生产不同直径,各种吨位的中小型电渣锭.炉子建成后,针对重熔工艺的关键技术展开了全方位,多层面的深入系统的研究,攻克了一系列重大技术难题,主要有:(1)均匀性控制技术解决了用成分有差异的若干炉号,数十根电极,通过几个昼夜重熔成一根200t电渣锭的成分均匀性问题.(2)大功率,快熔速,高冷却和强脱氧工艺为获得高质量巨型电渣锭提供了重要保证.大功率供电,渣温高,冶金反应的动力学条件好,精炼净化效果强.虽然熔速高达5t/h以上,但由于有《大型铸锻件》HEA VYCASTINGANDFORGINGNo.1January2011Figure5200t—classESRfurnaceatremelting图6核电用207t电渣锭Figure6A207tESRingotfornuclearpower图7核电用205t电渣锭Figure7A205tESRingotfornuclearpower高速强制冷却,使得熔池浅,成分均匀,组织致密. 强制脱氧使渣池始终保持低氧位(FeO≤0.3%), 高冶金性能.因此,200t级电渣炉生产的电渣锭热塑性良好,锻压时一次压下量达1000mm也不开裂.电渣锭中心的密度与锭边缘密度一致.锭中心的二次枝晶间距仅为2mm.氧化物0.5级,硫化物找不到.直径为2113的锻件,超声波探伤起始灵敏度1.1mm也能通过J.(3)低氢控制技术解决了高湿度气候条件下长时间重熔获得低氢巨型电渣锭的难题. 尽管上海气候潮湿,空气湿度高达30gHO/m,熔炼区气/渣接触面积有5m大,但几个昼夜的重熔过程中,低氢控制技术使重熔与天气和季节无关.使用冷渣料对低氢控制没有明显影响.电渣锭中的氢含量都不超过2×10~,大部分在1.4 ×10以下.数十个大锻件,包括直径为2000mm的汽轮机低压转子,完全取消扩氢退火后无一发现白点.(4)低铝控制技术¨扫除了电渣重熔法生产汽轮机转子的障碍.汽轮机转子中的铝不允许超过0.010%(质量分数),而电渣重熔获得低铝非常困难.当用低铝电极重熔时,总是发生增铝,因为渣中含有大量铝.当电极中的铝超过0.010%(质量分数)时,重熔过程中更难以将其降至0.010%以下.用自主研发的低铝,低氧,低硫兼得的重熔工艺技术'"批量生产的高,中,低压汽轮机转子,铝均控制在0.005%~0.007% 之间,氧,硫均在25×10以下,大部分为20X10-.'.30年来,200t级电渣炉一直在生产运行,在完成国家重点建设项目的攻关任务中做出了一个又一个重大贡献,不断受到国内外专家的关注和推崇.主要产品有:(1)炉子建成首先是生产秦山核电站核岛大锻件用电渣锭.1981年10月10日重熔出127t核电用电渣锭,1983年10月31日和11月18日连续两次生产出205t和207t核电用电渣锭,到1984年底共生产核电用电渣锭24根,锭重多在(130~170)t之间,完成了秦山核电站核岛大锻件所需大钢锭的生产任务.用电渣锭成套生产的蒸发器和稳压器等核电大锻件,经有关部门5大类35项材料内在质量严格测试,技术性能符合设计要求,综合质量达到ASME标准,通过国家级鉴定和验收.秦山核电站1991年l2月15日并网发电,提前两年达到年发电设计能力.20年过去了,作为"国之光荣",秦山核电站至今运行情况良好.(2)此后,相继批量生产了300MW发电机转子,300MW一600MW汽轮机高.中压和低压转子,560t加氢反应器等大锻件,全部通过国家级鉴定和验收.(3)进入21世纪,凭借技术优势,批量生产了核潜艇堆内构件,三峡工程710MW水轮机导叶轴头,1000MW核电站堆内构件,1000MW超超临界汽轮机转子等高合金大锻件,获得了巨大29No.1January2011《大型铸锻件》HEA VYCASTINGANDFORGING的经济效益.一个国家的钢铁工业发展和冶金技术水平,既要看钢的产量,品种和质量,还要看能生产多大的钢锭和大钢锭的质量有多高.巨型钢锭的生产技术反应了一个国家重工业的发展水平和科学技术的攻坚能力,也是一个企业实力和等级水平的象征.作为中国的自主原创技术,200t级电渣炉开辟了生产优质巨型钢锭的新方法,新途径,因对世界特种熔炼技术的重大贡献,曾于1988年在美国举行的第九届国际真空冶金会议(9thICVM)上获大奖(图8).在我国的工业现代化发展过程中,由中国人独创,从研究开发到付诸工业生产应用并达到世界领先地位,在国际上获奖的重大项目还为数不多.图8的奖牌Figure8Themedia(9thICVM)2.3其它大型电渣炉此外,还有一些见诸于苏联文献的苏联建造大型电渣炉的报道.如,1979~1980年在新克拉马托尔斯克机器制造厂(HKM3)安装了~iiiri?15o型电渣炉¨...据称,该电渣炉由3台单相变压器供电,总功率为(12—14)MV A(4800kV AX3).液渣启动,采用上部加大的漏斗形结晶器(Q)3360mm).上部加大处为熔化部分,下部为成型部分(O2550mm),其截面积等于自耗电极的总截面积或者大20%.渣量(11~12)t.结晶器加大处装有钢液面传感器,还有供注入或排出液渣用的孔眼.熔炼过程中向金属熔池和渣池吹入惰性气体.可熔炼直径(1800~2700)mm,重(80—200)t的电渣锭和外径(1800~2700)mm, 内径(600~800)mm的空心锭,并可同时熔炼3 个重(30—60)t的电渣锭.采用7根电极操作,熔炼80t锭时电极直径为650mm,熔炼200t锭时电极直径为1000mm.重熔时电极不进给,短网也不动,只有结晶器上移.苏联出口朝鲜千里马钢厂的200t电渣炉也是这种炉型结构,但是根30本无法开炉炼钢,请中国专家去也爱莫能助.又如,YUI一108型电渣炉,变压器容量为3 500kV A×3(单相),可熔炼2500mm/100t的空心锭和实心锭;日丹诺夫重型机器厂(TM)的YlII-100型电渣炉J,变压器容量为2500kV AX3(单相),可熔炼O2300mm/120t的空心锭和实心锭,等等.但是30年过去了,至今也未见那些炉子投人生产使用的报道.3大型化的新进展(2008年以后)为了满足市场急需,提升企业核心竞争力,上海重型机器厂有限公司2008年着手投建结晶器直径为37001Tim的450t电渣炉.450t电渣锭相当于(6oo一700)t电炉锭,覆盖了当前世界上所有最大吨位的锻件用钢锭.历时一年,于2009 年4月建成(图9),5月5日热调试成功,现已投入试运行.2009年开炉重熔11炉,根据锻件需要,现已顺利重熔出220t,320t的核电压力容器用电渣锭.450t电渣炉的产品对象主要是百万千瓦级核电机组的核岛锻件,汽轮机低压转子,管板和大型支撑辊等超大型锻件.此外,第一重型机械集团公司的120t电渣炉从2010年5月已开始调试;东北特钢正在大连基地上马100t电渣炉(从奥地利Inteco公司引进),计划在2011年7月投入运行;无锡桥联集团的300t电渣浇注炉已从2009年开始设计(由乌克兰巴顿电焊研究所的Elmet-Roll-MedovarGroup 承担),还有一些单位正在筹建200t和400t电渣炉.尤为可喜的是,通裕重工股份有限公司通过技术改革,实现了电渣重熔技术的提升和跨越. 2009年4月冶炼出第三代核电AP1000主管道用超低碳控氮不锈钢(SA376TP316LN)72t电渣锭,而且是一次成功;2009年生产的几根75t电渣锭,锭高4.1nl,锭子上下成分一致,底部质量,顶部补缩和低倍组织优良,洁净度高.[H]=1XlO,『O1=17×10I¨,[S]=20×10I¨.2010年4,5月,通裕重工又率先顺利生产出一套第三代核电AP1000主管道用超低碳控氮不锈钢(SA376 TP316LN)大型电渣锭8根.这不仅是国内也是世界上首次成套生产出AP1000主管道用核级超低碳控氮不锈钢大型电渣锭.AP1000主管道是我国引进AP1000核电技术项目中唯一没有引进国外技术的核岛关键设备,被称之为核电站的"主动脉",属于核1级设备.AP1000主管道用超低碳控氮不锈钢大型电渣锭的生产技术是《大型铸锻件》HEA VYCASTINGANDF0RGINGNO.1January201】AP1000主管道制造的核心技术,是主管道制造的限制性环节.AP1000主管道用超低碳控氮不锈钢大型电渣锭成套生产成功,解决了我国第三代核电主管道国产化的瓶颈制约问题,对于我国大力发展核电事业是一个不小的贡献.迄今为止,通裕重工已生产(70~82)t的大型电渣锭近20 根,质量稳定.据报道,Et本,德国,意大利以及欧洲其他一些工业发达国家近年也在陆续投建250t,150t, 145t,120t,110t,100t大型电渣炉.Figure9450tESRfurnaceatremelting4大型电渣炉值得注意的几个问题电渣炉相对于电弧炉等其他熔炼设备而言是比较简单的,但由于设备容量的大型化而引发的一些问题则不容忽视.世界上好几台大型电渣炉都不成功的教训是深刻的.根据笔者从事200t级电渣炉技术工作30年的实践,认为大型电渣炉至少以下几方面值得认真注意:4.1电渣重熔工艺设计是灵魂设备是正常生产的基本保障,对生产工艺有关键性影响.所谓"工欲善其事,必先利其器",在某种意义上甚至可以说设备比生产工艺本身还重要.其实生产设备是根据生产工艺而设计的,它在各方面的工作性能必须要满足生产工艺的要求,需要两者的和谐统一,完美结合.并且设备要有很强的适应性,要能充分满足生产工艺所涉及的调整范围.好些大型电渣炉不好用,甚至无法重熔生产,常常是缺少工艺设计.重熔工艺是生产电渣锭的各种过程参数,规范程序和操作方法.重熔工艺设计是全面规划和具体描述电渣重熔生产实施意图的过程,是电渣炉设计中的"灵魂".电渣炉还没有形成标准化,系列化.大型电渣炉的工业化生产,也才仅仅40年短暂时间.奥地利Inteco公司总裁W.Holzgruber博士说,技术上突破100t的电渣炉仅有德国萨尔钢厂和中国上海重型机器厂两家.可想而知,大型电渣重熔特别是100t以上的炉子的工业生产实践经验是极其有限的.这种本来是生产小锭的特种熔炼技术,炉容量十倍百倍地扩大,使得很多工艺因素复杂化,这不是一个简单的数量增加,而是跨越,质的飞跃.科学上的新发现可以通过论文和网络技术很快地在全世界范围内传播开来,知识全球共享,但新的工艺技术却是企业的Know-how(专有技术),是企业的看家本领,是企业的核心竞争力,往往具有知识产权,具有独占性,保密程度很高.如果没有掌握大型电渣重熔的工艺技术,工艺设计又从何谈起?如果设备设计者对重熔工艺茫然无知,那这种由没有灵魂的设计建造的设备怎么可能好用?苏联本是电渣重熔技术的发源地,但是苏联的大型电渣炉并不成功,其主要原因就在于苏联没有掌握大型电渣重熔工艺技术.对此,IO.B. BaTam教授,A.F.~oFaqeHKO博士都曾向笔者证实,并一再称赞中国200t电渣重熔技术的先进性.美国康萨克公司(ConsarcCorp.)也不掌握大型电渣重熔工艺技术.尽管康萨克电渣炉设备特别是供电部分做得还不错,但康萨克大型电渣炉注定是不好用的.康萨克公司总裁R.J.Roberts博士曾称赞中国的200t级电渣炉"是一个很好的设计".奥地利Inteco公司称,他们2008年开始设计的一台250t电渣炉,采用的是3~4根(60—80)t 的自耗电极.可以想象,电极的制备不是件容易的事,支撑电极的结构也不会轻便,变压器容量也会非常之大.因为该公司还为意大利FOMAS锻造厂设计了一台结晶器直径为2050mm的120t 电渣炉,计划于2011年2月投产,也采用同样的方案,变压器容量有30000kV A之大,超过30年前苏联建造的结晶器直径为3360mm的200t电渣炉变压器容量的两倍.我国东北特钢在2009年也向该公司引进了一台类似结构的100t电渣炉.这些炉子都还没有建成,祝愿它们都能顺利投产.20世纪80年代,中国的200t级电渣炉之所以能一次调试成功就重熔出合格的90t转子电渣锭,第二次调试就重熔出合格的127t核电电渣锭,炉子建成3年就生产出核电蒸发器用205t电渣锭,是因为200t级电渣炉是根据我国电渣冶金的开山祖师朱觉教授及刘海洪教授的工艺思想进31No.1January2011《大型铸锻件》HEA VYCASTINGANDFORGING行设计的,是建立在100t电渣炉的工程实践和生产经验的基础上的.中国的450t电渣炉从设计制造到安装调试仅只一年时间,也是一次调试成功就投入生产运行.如果没有200t级电渣炉2O 多年的技术开发和生产经验,那是不可想象的. 中国的200t级电渣炉和450t电渣炉的成功说明,工艺思想的确是电渣炉的灵魂.4.2设备是产品之母,工艺是产品之父产品的制造过程,都必须利用一定的设备通过一定的工艺才能实现.设备是产品之母,工艺是产品之父.即使炉子好用,也还有个会不会用的问题.因此,必须全面掌握熔炼软技术和一系列检测技术.如电制度,渣制度,温度制度,速度制度,启动技术,换电极技术,抽锭技术,高均匀性控制技术,低氢控制技术,低氧控制技术,低铝控制技术,脱氧技术,补缩技术,脱锭技术,炉气分析技术,炉渣分析技术,熔池检测技术等.必须强化气氛可控,重熔过程可控和凝固过程可控,提高过程控制水平,才能稳定可靠地生产出合格产品. 不掌握这些专有技术,在生产中,在质量上都会产生很大的迷茫,困惑和麻烦.比如,电渣重熔首先要造渣,上海重型机器厂的200t级电渣炉5t渣料,用时75min,钢锭底部质量良好以至在生产筒体锻件时无需切除;可是一些炉子1t渣料,通常要用150min,钢锭底部质量还不尽如人意.又如,电渣重熔结束前要进行补缩,有的20t电渣锭补缩折腾好几个小时,结果钢锭顶部不是包了一包渣就是存在暗缩孔.至于低氢控制问题,那更是普遍存在的了.而设备设计和销售单位往往并不具备这些专有技术.长期以来,我们习惯更多地依赖科研机构和大学,但近百年世界产业发展的历史表明,真正起作用的技术几乎都来自企业(比如,通讯领域的贝尔,汽车领域的福特,飞机领域的波音和空客,化工领域的杜邦和拜耳,机床领域的西门子,计算机领域的IBM,英特尔,微软, 等等).道理很简单,实际熔炼时开发的技术和生产现场积累的经验才是真实可靠的,才是有实用价值的.4.3特大电流问题大型电渣炉是特大电流用电设备,有的甚至高达100kA.因此,炉子短网电气特性就显得非常重要,否则功率因数不高,有功分量的效率太低,会给熔炼造成很大困难.导体的感抗量是由导体本身磁通变化引起的自感和由相邻导体磁通变化所引起的互感的几何32和.为了降低大电流网路感抗,提高功率因数(cos),减少无功损耗,有的采用双极串联供电,通过平行布线和交错布线,使电流回路互相靠近, 外部磁场大大抵消.我国200t级电渣炉和450t电渣炉就采用了这种办法,cos~p可高达0.80—0.93.由于电感与电流频率成正比,所以采用低频电源可以降低短网大电流所引起的感抗损失,提高功率因数.德国莱宝公司(LeyboldAG)制造的电渣炉大都采用低频供电.比如,由莱宝公司设计制造的萨尔钢厂的160t电渣炉就是(0~10) Hz的低频电源,达到较高的功率因数.采用同轴布置或同轴电缆是减少短网电抗,提高功率因数的又一方案.美国康萨克公司。