我国催化裂化工艺技术进展_许友好
我国催化裂化工艺技术研究现状及发展趋势

催化裂化技术主要具有投资低、产品方案灵活、操作压力低、轻质油产率高、重油转化率高以及原料适应性宽等特征,是原油二次加工重要的生产技术。
自1942年发展以来,取得了较大的发展和创新。
全球催化裂化发展主要增长点在中国,目前已达210Mt/a的加工能力。
随着原料品质的变差,对生产产品的要求不断提高,催化裂化技术面临前所未有的挑战。
1 反应器发展现状1.1 提升管反应器传统单提管反应器结构简单,配置等径直管型提升管,催化剂从单侧进,预提升段通入预提升蒸汽主要采取环管式和直管式。
提升管反应器较流化床反应器而言,缩短了反应时间,提升了产品选择性,轻油产率大大提高。
同时焦炭产率大幅降低,明显提高了掺渣比例。
但由于原油日益劣质化和重质化,传统提升管反应器也存在很多不足。
针对提升管径向分布不均和固相浓度低问题,形成了变径提升管反应器;针对原料来源广泛和性质复杂等问题,形成了多段进料提升管反应器。
1.2 下行式反应器在提升管反应器内,存在径向分布不均、催化剂逆重力场流动、返混严重以及固相颗粒跟随性差等问题,往往表现出“环-核”流动结构。
因此,为突破传统提升管反应器局限,形成了下行式反应器,实现了油剂接触均匀、无返混、无偏流分布以及混合迅速等优势。
该反应器保证了高裂解温度,裂解油和催化剂接触时间短,结焦量得到有效控制,最终提高了反应目标产物收率。
2 反应机理研究进展2.1 以生产化工原料为目的2.1.1 催化裂解技术(DCC)DCC装置在国际上使用较早,在催化裂化多产低碳烯烃技术方向仍处于世界领先水平。
近年来,在深入研究乙烯和丙烯生成化学的基础上,认为引发催化裂解链的反应路径存在多元性特征。
经五配位正碳离子中间过渡态,原料烃分子可以引发单分子裂化反应,经三配位正碳离子中间过渡态,原料烃分子可以引发双分子裂化反应。
2.1.2 催化裂解增强型技术(DCC-plus)研究丙烯生成反应,认为汽油中烯烃二次裂解和重油一次裂解共同作用下,行了了丙烯。
催化裂化过程芳烃转化及生焦关系探索
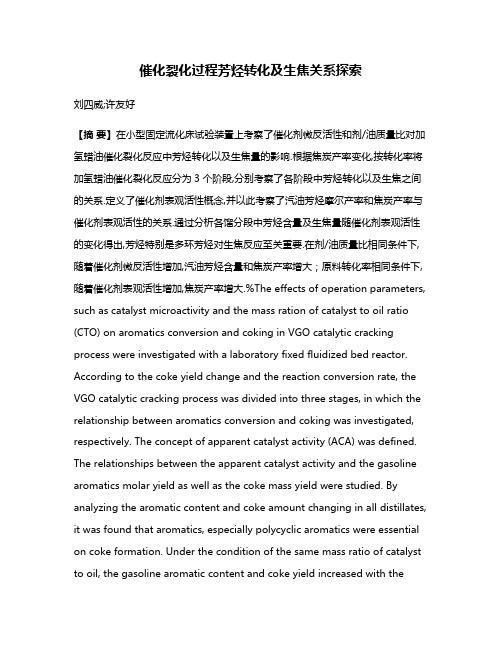
催化裂化过程芳烃转化及生焦关系探索刘四威;许友好【摘要】在小型固定流化床试验装置上考察了催化剂微反活性和剂/油质量比对加氢蜡油催化裂化反应中芳烃转化以及生焦量的影响.根据焦炭产率变化,按转化率将加氢蜡油催化裂化反应分为3个阶段,分别考察了各阶段中芳烃转化以及生焦之间的关系.定义了催化剂表观活性概念,并以此考察了汽油芳烃摩尔产率和焦炭产率与催化剂表观活性的关系.通过分析各馏分段中芳烃含量及生焦量随催化剂表观活性的变化得出,芳烃特别是多环芳烃对生焦反应至关重要.在剂/油质量比相同条件下,随着催化剂微反活性增加,汽油芳烃含量和焦炭产率增大;原料转化率相同条件下,随着催化剂表观活性增加,焦炭产率增大.%The effects of operation parameters, such as catalyst microactivity and the mass ration of catalyst to oil ratio (CTO) on aromatics conversion and coking in VGO catalytic cracking process were investigated with a laboratory fixed fluidized bed reactor. According to the coke yield change and the reaction conversion rate, the VGO catalytic cracking process was divided into three stages, in which the relationship between aromatics conversion and coking was investigated, respectively. The concept of apparent catalyst activity (ACA) was defined. The relationships between the apparent catalyst activity and the gasoline aromatics molar yield as well as the coke mass yield were studied. By analyzing the aromatic content and coke amount changing in all distillates, it was found that aromatics, especially polycyclic aromatics were essential on coke formation. Under the condition of the same mass ratio of catalyst to oil, the gasoline aromatic content and coke yield increased with theincrease of catalyst microactivity. Under the condition of the same conversion rate, the coke yield increased with the increase of apparent catalyst activity.【期刊名称】《石油学报(石油加工)》【年(卷),期】2013(029)001【总页数】6页(P145-150)【关键词】催化裂化;微反活性;催化剂表观活性;芳烃;焦炭【作者】刘四威;许友好【作者单位】中国石化石油化工科学研究院,北京100083;中国东方电气集团有限公司中央研究院,四川成都611731;中国石化石油化工科学研究院,北京100083【正文语种】中文【中图分类】TE624.4裂化反应过程包含部分原料的重质化,其中烷烃、烯烃以及环烷烃可以通过环化、烷基化、脱氢等反应逐步转化成芳烃,芳烃可经脱烷基、断侧链等反应向小分子烃转变,也可在催化剂孔道内脱氢缩合生成大分子芳烃以及焦炭,具体哪个方向占优要看原料油性质、催化剂类型、操作条件等因素影响。
催化裂化工艺及催化剂的技术进展

催化裂化工艺及催化剂的技术进展催化裂化工艺和催化剂技术在炼油工业中占有重要地位,是提高石油利用率的主要途径。
因为炼油厂原料使用的差异性,导致产品的分布状况也有所不同,因此催化裂化工艺和催化剂技术的发展更为多样化。
本文对催化裂化工艺和催化裂化催化剂技术的进展进行了详细的介绍,希望能为同行业者提供有利的帮助和借鉴。
标签:催化裂化;催化剂;技术进展目前,我国的进行在不断地进步,人们的生活水平也在逐渐地提高,石油行业也发展起来,同时也给环境带来诸多问题,因此,在利用石油资源时一定要重视环境保护的问题,以便为清洁燃料的生产提供更多的有利条件。
在石油资源的市场应用中,与催化剂相结合,能够提高轻汽油的生产效率,催化裂化装置与市场工艺相结合,能够促使装置规模迅速发展,在炼油厂轻质油产品的生产中,催化裂化起着重要作用,促进催化裂化工艺及催化剂技术的开发和生产。
1 简析催化裂化工艺技术进展1.1 分析多产异构烷烃的催化裂化工艺技术多产异构烷烃的催化裂化工艺技术主要根据与串联改造后的提升管反应装置相符合的技术标准,有效地将提升管反应装置分为两个不同的部分,其中一个区域在温度和催化剂油的比例均处于高水平的条件下进行反应,就苛刻度而言,比平时要高很多,重质原油处理后生产的烯烃较快;在另一个区域,当提升管处于非常高的水平时,催化剂在到达该区域时将结合冷却介质,以便达到反应温度能够降低的程度,并延长反应时间,特别芳烃的作用功效非常之大。
MIP工艺技术用于提高二次反应的强度,并有效控制氢转移反应。
除此之外,还能够不断提高和改善产品的性能和分布。
1.2 分析双提升管FCC工艺技术想要对产品分布的科学以及合理性进行有效保障,实现有关材料的加工和生产任务,有必要对双提升管FCC工艺技术进行了全方位的研究,这样能够促进工业化的发展和进步。
在应用双提升管FCC工艺技术的过程中,将两种材料放入两个不一样的管子中,以便在不同温度下,保障产品的较好分布。
浅谈中国催化裂化工艺流程的新进展
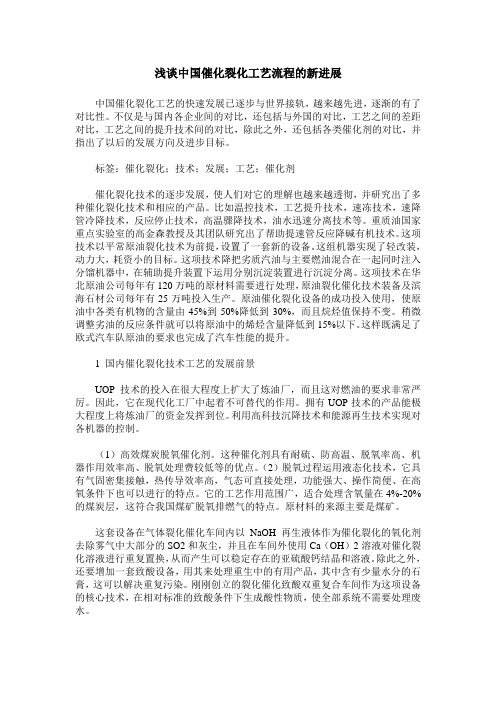
浅谈中国催化裂化工艺流程的新进展中国催化裂化工艺的快速发展已逐步与世界接轨,越来越先进,逐渐的有了对比性。
不仅是与国内各企业间的对比,还包括与外国的对比,工艺之间的差距对比,工艺之间的提升技术间的对比,除此之外,还包括各类催化剂的对比,并指出了以后的发展方向及进步目标。
标签:催化裂化;技术;发展;工艺;催化剂催化裂化技术的逐步发展,使人们对它的理解也越来越透彻,并研究出了多种催化裂化技术和相应的产品。
比如温控技术,工艺提升技术,速冻技术,速降管冷降技术,反应停止技术,高温骤降技术,油水迅速分离技术等。
重质油国家重点实验室的高金森教授及其团队研究出了帮助提速管反应降碱有机技术。
这项技术以平常原油裂化技术为前提,设置了一套新的设备。
这组机器实现了轻改装,动力大,耗资小的目标。
这项技术降把劣质汽油与主要燃油混合在一起同时注入分馏机器中,在辅助提升装置下运用分别沉淀装置进行沉淀分离。
这项技术在华北原油公司每年有120万吨的原材料需要进行处理,原油裂化催化技术装备及滨海石材公司每年有25万吨投入生产。
原油催化裂化设备的成功投入使用,使原油中各类有机物的含量由45%到50%降低到30%,而且烷烃值保持不变。
稍微调整劣油的反应条件就可以将原油中的烯烃含量降低到15%以下。
这样既满足了欧式汽车队原油的要求也完成了汽车性能的提升。
1 国内催化裂化技术工艺的发展前景UOP技术的投入在很大程度上扩大了炼油厂,而且这对燃油的要求非常严厉。
因此,它在现代化工厂中起着不可替代的作用。
拥有UOP技术的产品能极大程度上将炼油厂的资金发挥到位。
利用高科技沉降技术和能源再生技术实现对各机器的控制。
(1)高效煤炭脱氧催化剂。
这种催化剂具有耐硫、防高温、脱氧率高、机器作用效率高、脱氧处理费较低等的优点。
(2)脱氧过程运用液态化技术,它具有气固密集接触,热传导效率高,气态可直接处理,功能强大、操作简便、在高氧条件下也可以进行的特点。
它的工艺作用范围广,适合处理含氧量在4%-20%的煤炭层,这符合我国煤矿脱氧排燃气的特点。
催化裂化重油加氢(HAR)技术开发和工业实践

HAR 技 术的核心 是对 FGO 中的多环 芳烃进
收 稿 日 期 :20181220;修 改 稿 收 到 日 期 :20190428。 作 者 简 介 :刘涛,硕士,研究员,主要从事重油加氢工艺研究工作。 通 讯 联 系 人 :刘 涛 ,Email:liutao.ripp@sinopec.com。 基 金 项 目 :中 国 石 油 化 工 股 份 有 限 公 司 合 同 项 目 (S110146)。
石科院在总结多年加氢处理催化剂研究开发 经验的基础上,提 出 了 FGO 加 氢 催 化 剂 开 发 的 具 体要求和开发思路:① 选 择 芳 环 加 氢 功 能 强、活 性 高的金属体系;②开 发 具 有 合 适 孔 道 结 构 的 载 体, 使催化剂 具 有 较 高 的 有 效 反 应 表 面,使 反 应 物 分 子容易接 近 活 性 中 心 反 应 和 脱 附,提 高 金 属 利 用 率;③催化剂或载体 通 过 适 当 表 面 改 性,产 生 一 定 量的 B 酸,使 容 易 吸 附 的 易 结 焦 前 身 物 通 过 加 氢 反应后快 速 脱 附;④ 尽 量 简 化 催 化 剂 制 备 工 艺 过 程,以 缩 短 生 产 周 期,降 低 生 产 成 本。 最 终,通 过 对载体、助 剂、金 属 组 元 及 负 载 量 等 的 研 究 探 讨, 开发了 FGO 加氢专用催化剂 RDA1。 12 犎犃犚 技术工艺条件研究
浅谈中国催化裂化工艺流程新进展
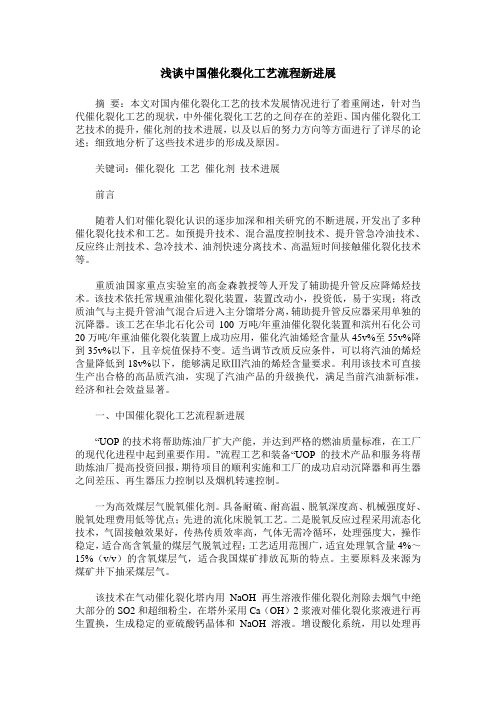
浅谈中国催化裂化工艺流程新进展摘要:本文对国内催化裂化工艺的技术发展情况进行了着重阐述,针对当代催化裂化工艺的现状,中外催化裂化工艺的之间存在的差距、国内催化裂化工艺技术的提升,催化剂的技术进展,以及以后的努力方向等方面进行了详尽的论述;细致地分析了这些技术进步的形成及原因。
关键词:催化裂化工艺催化剂技术进展前言随着人们对催化裂化认识的逐步加深和相关研究的不断进展,开发出了多种催化裂化技术和工艺。
如预提升技术、混合温度控制技术、提升管急冷油技术、反应终止剂技术、急冷技术、油剂快速分离技术、高温短时间接触催化裂化技术等。
重质油国家重点实验室的高金森教授等人开发了辅助提升管反应降烯烃技术。
该技术依托常规重油催化裂化装置,装置改动小,投资低,易于实现;将改质油气与主提升管油气混合后进入主分馏塔分离,辅助提升管反应器采用单独的沉降器。
该工艺在华北石化公司100万吨/年重油催化裂化装置和滨州石化公司20万吨/年重油催化裂化装置上成功应用,催化汽油烯烃含量从45v%至55v%降到35v%以下,且辛烷值保持不变。
适当调节改质反应条件,可以将汽油的烯烃含量降低到18v%以下,能够满足欧Ⅲ汽油的烯烃含量要求。
利用该技术可直接生产出合格的高品质汽油,实现了汽油产品的升级换代,满足当前汽油新标准,经济和社会效益显著。
一、中国催化裂化工艺流程新进展“UOP的技术将帮助炼油厂扩大产能,并达到严格的燃油质量标准,在工厂的现代化进程中起到重要作用。
”流程工艺和装备“UOP的技术产品和服务将帮助炼油厂提高投资回报,期待项目的顺利实施和工厂的成功启动沉降器和再生器之间差压、再生器压力控制以及烟机转速控制。
一为高效煤层气脱氧催化剂。
具备耐硫、耐高温、脱氧深度高、机械强度好、脱氧处理费用低等优点;先进的流化床脱氧工艺。
二是脱氧反应过程采用流态化技术,气固接触效果好,传热传质效率高,气体无需冷循环,处理强度大,操作稳定,适合高含氧量的煤层气脱氧过程;工艺适用范围广,适宜处理氧含量4%~15%(v/v)的含氧煤层气,适合我国煤矿排放瓦斯的特点。
浅谈催化裂化工艺及催化剂的技术进展

浅谈催化裂化工艺及催化剂的技术进展催化裂化工艺及催化剂的技术发展至今经过了几十年的时间,该种技术在工业领域中得到了广泛的应用,并且在未来的发展前景客观。
基于此本文结合国内外催化裂化工艺及催化剂的技术进展,阐述当代催化裂化工艺及催化剂的特点和具体技术应用。
标签:催化裂化工艺;催化剂;能源开发石油化学工业作为化学工业的重要组成部分是近代发达国家的重要工业,然而20世纪70年代后由于原油价格的上涨而导致石油的发展速度急剧下降,而催化裂化工艺由于其拥有着较低的投资操作成本、高转化率以及原材料适应性强发展成为了实际炼油过程中的核心工艺,而且经过数十年的发展其技术比较成熟稳定,成为了炼化重油的一种较为重要的手段。
1 催化裂化工艺的技术进展1.1 当代催化裂化工艺的特点分析当代化工催化裂化工艺的特点如下:①技术稳定,可持续性应用;催化裂化工艺(英文缩写RFCC)一般由再生系统、分馏系统、吸收-稳定系统三部分组成,是石油二次加工的主要方法之一。
在高温和催化剂的作用下,使重质油发生裂化反应,转变为裂化气、汽油和柴油等的过程。
虽然目前世界对于重油提炼的工艺趋于成熟稳定,但就目前环境问题来讲各项技术仍有待提高,重油提炼出现了原材料的价格问题、环境问题、规格问题、石油化工的发展问题。
但是,催化裂化工艺对于环境保护法律规定的要求已经基本满足,使得此项技术未来可以取得长足的发展空间;②应用广泛;石油仍然是目前世界所需的重要能源,对于石油加工的新工艺就显得尤为重要,发达国家对于石油工业的生产水平已经占据前列,我国从20世纪60年代开始着手钻研石油工業也逐步迈入世界顶尖行列,目前我国自主研制的石油催化裂化工艺基本全方位覆盖本国石油行业,排入世界前列。
MGD和MIP工艺、催化汽油改制技术、催化裂化组合工艺、用添加剂强化的催化裂化工艺等已经被我国灵活运用到生产、生活等各个领域。
随着我国自主研究人员的不断努力,我国开发的催化裂化工艺可以有效的为各个企业取得优秀的经济效益,以及减轻原有重油炼制手段对于环境的危害。
催化裂化过程反应化学的进展
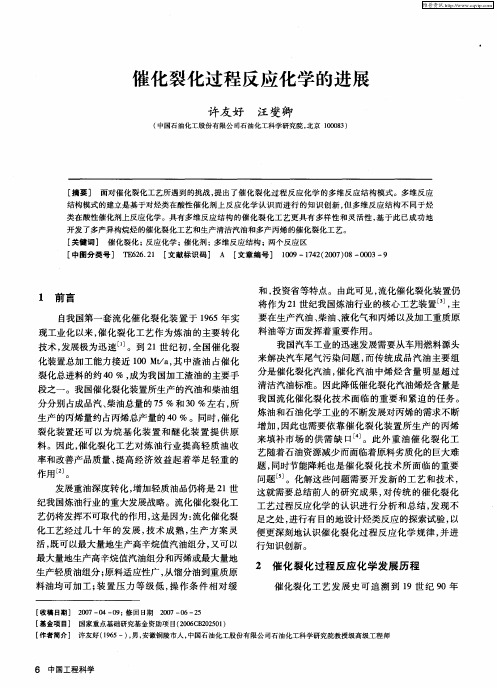
发展重油深度转化 , 增加轻质油品仍将是 2 世 1
纪我 国炼油 行业 的重 大发 展战 略 。流化催 化裂 化工
艺仍将发挥不可取代的作用 , 这是因为: 流化催化裂
化 工艺经 过 几 十 年 的 发 展 , 术 成 熟 , 产 方 案 灵 技 生 活, 既可 以最大 量地 生产 高辛 烷值 汽油 组分 , 可 以 又
许友好 汪 燮 卿
( 中国石 油化工股份有限公司石油化工学研究院 , 北京 10 8 ) 0 0 3
[ 摘要 ] 面对催 化裂 化工艺所 遇到的挑 战 , 出了催化裂 化过 程反应 化学 的多维反应 结构模 式。多维反应 提 结构模式的建立是基于对烃类在酸性催化 剂上反应 化学认 识 而进行 的知识创 新 , 但多维反 应结 构不 同于烃
类 在酸性催化剂上反应 化学。具 有多维反应 结构 的催 化裂 化工 艺更具有 多样性 和灵 活性 , 于此 已成功地 基 开发 了多产异 构烷 烃的催化裂化 工艺和生产 清洁汽油和多产丙烯 的催化裂化工 艺。
[ 关键词] 催化裂化 ;反应 化学 ; 催化剂 ;多维反应 结构 ; 两个反应 区 [ 中图分类号] T/ 62 [ F 2 . 1 文献标识码 ] A [ 5 文章编号 ] 10 0 9—14 ( 07 0 00 9 7 2 2 0 ) 8— 0 3—
由氢转移反应将负氢离子转移到正碳离子上中断了烃链的裂化反应从而造成汽油产率大幅度地增加汽油中的烯烃含量降低而烷烃含量增加汽油的辛烷值明显降低焦炭产率有所增加一120世纪60年代后期为适应高活性高选择性沸石催化剂而开发出提升管催化裂化工艺
维普资讯
催 化裂化过程反应化学 的进 展
1 前 言
自我 国第 一 套 流化 催 化 裂 化装 置 于 16 95年 实
许友好:“中国石化科研环境10年巨变让我受益良多”
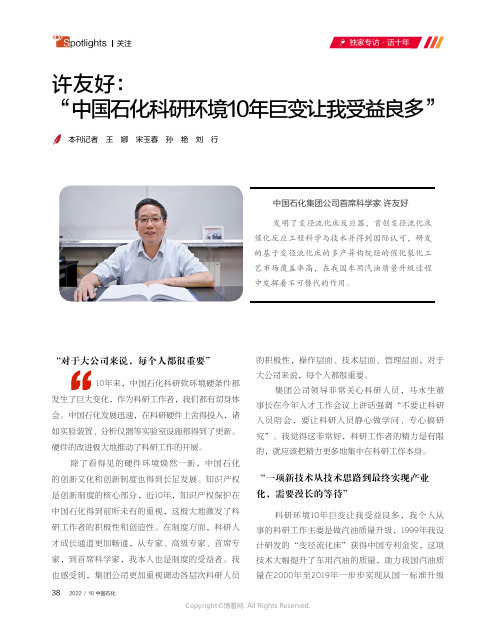
“对于大公司来说,每个人都很重要”10年来,中国石化科研软环境硬条件都发生了巨大变化,作为科研工作者,我们都有切身体会。
中国石化发展迅速,在科研硬件上舍得投入,诸如实验装置、分析仪器等实验室设施都得到了更新。
硬件的改进极大地推动了科研工作的开展。
除了看得见的硬件环境焕然一新,中国石化的创新文化和创新制度也得到长足发展。
知识产权是创新制度的核心部分,近10年,知识产权保护在中国石化得到前所未有的重视,这极大地激发了科研工作者的积极性和创造性。
在制度方面,科研人才成长通道更加畅通,从专家、高级专家、首席专家,到首席科学家,我本人也是制度的受益者。
我也感受到,集团公司更加重视调动各层次科研人员的积极性,操作层面、技术层面、管理层面,对于大公司来说,每个人都很重要。
集团公司领导非常关心科研人员,马永生董事长在今年人才工作会议上讲话强调“不要让科研人员陪会,要让科研人员静心做学问、专心搞研究”。
我觉得这非常好,科研工作者的精力是有限的,就应该把精力更多地集中在科研工作本身。
“一项新技术从技术思路到最终实现产业化,需要漫长的等待”科研环境10年巨变让我受益良多,我个人从事的科研工作主要是做汽油质量升级,1999年我设计研发的“变径流化床”获得中国专利金奖,这项技术大幅提升了车用汽油的质量,助力我国汽油质量在2000年至2019年一步步实现从国一标准升级许友好:“中国石化科研环境10年巨变让我受益良多” 本刊记者 王 娜 宋玉春 孙 艳 刘 行中国石化集团公司首席科学家 许友好 发明了变径流化床反应器,首创变径流化床催化反应工程科学与技术并得到国际认可,研发的基于变径流化床的多产异构烷烃的催化裂化工艺市场覆盖率高,在我国车用汽油质量升级过程中发挥着不可替代的作用。
关注382022 / 10 中国石化到国六标准,到2021年7月1日,随着车用汽油国六排放标准实施,标志着我国汽车标准全面进入国六时代,基本实现与欧美发达国家接轨。
浅析催化裂化工艺及催化剂的技术进展

浅析催化裂化工艺及催化剂的技术进展摘要:随着科学技术的发展,催化裂化工艺的技术进展水平也越来越高,催化裂化工艺主要有满足清洁燃料生产要求的技术和多效的催化裂化工艺以及重油催化裂化技术等,这些催化裂化技术在国内外都有一定的发展。
除此之外,催化裂化催化剂也有较明显的发展,但这些工艺仍需要面对一些挑战。
关键词:催化裂化工艺;催化剂;技术进展1催化裂化工艺技术进展1.1MIP工艺技术这项工艺技术主要运用了串联改造后的提升管反应装置,依靠与之匹配的技术条件,对其进行有效划分,形成两个不同的区域部分,其中一个区域进行反应的条件为温度和剂油比都拥有很高的水平,在苛刻度方面,相较于普通变得更高,处理完重质原油以后所产生的烯烃速度更快;而另一区域在提升管处于很高的高度之时,等待催化剂到达该区域以后,便与冷却介质融合到一块,降低反应温度,延长反应时间,尤其针对芳烃而言,拥有一定的作用功效。
利用该工艺技术,提高了二次反应强度,有效控制氢转移反应的同时,不断完善产品的有关性质和分布情况。
1.2双提升管FCC工艺技术基于保证产品分布科学合理性的目的,并且完成相关各类材料的加工生产任务,针对该工艺技术的研究在全球范围得以开展,有利于工业化的发展与进步。
运用这种工艺技术的过程中,在不同的两根管之中放入两类材料,从而基于各自不同的温度下,确保产品的分布处于良好状态。
从相关研究中不难获悉,完善提升管工艺技术的过程中,实际上相较于传统工艺技术而言并无显著差异,仅在温度和剂油比两个参数方面获得了更高的效果,让轻催化汽油处于另一根提升管之内予以回炼处理,确保丙烯产出率提升到更为理想的水平。
结合企业的具体炼油需要,依靠此工艺技术完成不同产品的分布工作。
例如,基于确保汽油与气体发挥出较高产出率的目的,使柴油、馏分再次回到原来的提升管实施回炼。
当苛刻度处于较高水平时予以裂化处理,以便满足产品分布的规定。
1.3FDFCC工艺技术国内的汽油、柴油领域的发展中均需要催化裂化装置,其已经占据了油品生产领域的很大比例。
我国催化裂化工艺技术进展

我国催化裂化工艺技术进展催化裂化工艺技术是一种将重质烃类裂解为轻质烃类和汽油等燃料的重要手段。
在我国,随着石油化工行业的快速发展,催化裂化工艺技术也取得了显著的进步。
本文将简要回顾我国催化裂化工艺技术的发展历程,介绍技术创新与应用情况,并展望未来的发展前景。
自20世纪50年代以来,我国催化裂化工艺技术经历了从引进到自主研发的过程。
早期,我国从国外引进了一批先进的催化裂化装置和技术,在消化吸收的基础上,逐渐开始自主创新。
到20世纪80年代,我国已成功开发出具有自主知识产权的催化裂化工艺技术,并在大型工业装置上得到应用。
进入21世纪,我国催化裂化工艺技术水平进一步提升,已成为世界催化裂化工艺技术的重要研发和应用大国。
近年来,我国催化裂化工艺技术在技术创新和应用方面取得了许多重要成果。
在催化剂的种类和性能方面,通过优化制备工艺和组分设计,成功开发出多种高效、环保型催化剂。
这些催化剂在提高产品收率、降低能源消耗、减少污染物排放等方面具有显著优势。
在反应器设计方面,我国已成功开发出多套具有自主知识产权的反应器设计。
这些反应器在提高原料适应性、优化产品分布、降低能源消耗等方面表现出色。
例如,某新型反应器采用独特的结构设计,有效提高了催化剂的利用率和产品的分离效果,降低了装置的运行成本。
展望未来,我国催化裂化工艺技术将继续深入研究和技术创新。
随着环保要求的日益严格,开发高效、环保型催化裂化工艺技术将成为重要方向。
通过优化催化剂和反应器设计,降低污染物排放,提高资源利用率,实现绿色生产。
市场对燃料油和化工产品的需求将持续增长,因此催化裂化工艺技术的研究和应用将更加注重产品结构的优化和多样性的拓展。
例如,通过引入新的反应条件和原料,开发生产高附加值化学品的技术,提高企业的经济效益。
随着智能化和自动化的快速发展,催化裂化工艺技术将更加注重信息技术和自动化技术的应用。
通过建立自动化控制系统和实时监测分析系统,提高装置的运行效率和安全性,实现生产过程的智能化和信息化。
组合工艺提升重油催化裂化加工水平

石油化工一、前言针对国际原油市场高硫高酸及重质原油成本低廉的优势,对国内现有炼油装置进行适应性改造,进一步提高对高硫、高酸及重质原油的加工能力,可显著降低炼油企业原油成本,提高企业经济效益。
催化裂化作为重油转化的重要工艺之一,在多产轻质油特别是高辛烷值汽油和化工原料方面起着不可替代的作用。
如何加工这些重质、劣质原料油,实现目标产品最大化,始终是催化裂化工艺技术研究的主要方向。
二、重质油加工现状炼油行业内的“重质油”一般是指常规原油中沸点高于500℃的重质部分和相对密度大于0.934的重质原油以及天然沥青。
大量的实验研究表明,根据分子结构的转化性能可以将重质油分子结构区分为“易转化(烷基链、环烷烃)部分”和“难转化(芳香环)部分”。
“易转化(烷基链、环烷烃)部分”通过催化裂化可高效转化为汽油、柴油、乙烯、丙烯等目的产品;“难转化(芳香环)部分”在催化裂化反应中不能发生开环分解,倾向于发生缩合反应生成焦炭,特别是当原料中的多环芳烃含量过高时,或加工催化循环油时,造成焦炭产率大幅度升高,轻质油品收率降低,更严重时将不能用于催化裂化工艺加工。
目前,众多工艺方法和催化剂的进步在很大程度上提高了催化裂化装置的重质油转化率。
但是由于重质油馏程分布范围很宽,不同结构及组成的重油适宜的最优转化条件也不相同,所以仅按照一套操作条件对重质油进行加工是不够的,实际应用中难以实现目标产品最大化。
三、重油催化裂化工艺技术研究进展针对重质油高效转化的技术难题,石油炼制领域的研究者开展了大量卓有成效的研究工作和工业实践,提出多种组合工艺进行重质油转化的理念。
1.LTAG技术催化裂化轻循环油加氢——催化裂化组合生产高辛烷值汽油或轻质芳烃技术(LCO To Aromatics and Gasoline,简称LTAG技术)是中国石化石油化工科学研究院开发的将劣质催化裂化轻循环油(LCO)转化为高辛烷值催化裂化汽油或轻质芳烃(BTX)的技术。
中国炼油创新技术MIP的开发策略及启示
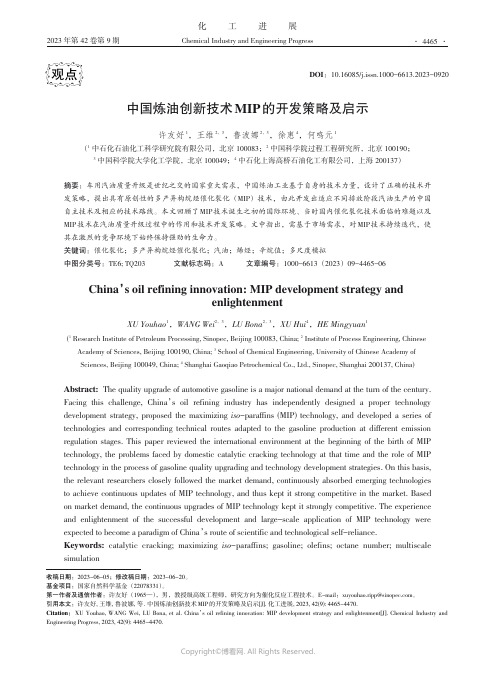
化工进展Chemical Industry and Engineering Progress2023 年第 42 卷第 9 期中国炼油创新技术MIP 的开发策略及启示许友好1,王维2,3,鲁波娜2,3,徐惠4,何鸣元1(1 中石化石油化工科学研究院有限公司,北京 100083;2 中国科学院过程工程研究所,北京 100190;3中国科学院大学化工学院,北京 100049;4 中石化上海高桥石油化工有限公司,上海 200137)摘要:车用汽油质量升级是世纪之交的国家重大需求,中国炼油工业基于自身的技术力量,设计了正确的技术开发策略,提出具有原创性的多产异构烷烃催化裂化(MIP )技术,由此开发出适应不同排放阶段汽油生产的中国自主技术及相应的技术路线。
本文回顾了MIP 技术诞生之初的国际环境、当时国内催化裂化技术面临的难题以及MIP 技术在汽油质量升级过程中的作用和技术开发策略。
文中指出,需基于市场需求,对MIP 技术持续迭代,使其在激烈的竞争环境下始终保持强劲的生命力。
关键词:催化裂化;多产异构烷烃催化裂化;汽油;烯烃;辛烷值;多尺度模拟中图分类号:TE6; TQ203 文献标志码:A 文章编号:1000-6613(2023)09-4465-06China ’s oil refining innovation: MIP development strategy andenlightenmentXU Youhao 1,WANG Wei 2,3,LU Bona 2,3,XU Hui 4,HE Mingyuan 1(1 Research Institute of Petroleum Processing, Sinopec, Beijing 100083, China; 2 Institute of Process Engineering, Chinese Academy of Sciences, Beijing 100190, China; 3 School of Chemical Engineering, University of Chinese Academy of Sciences, Beijing 100049, China; 4 Shanghai Gaoqiao Petrochemical Co., Ltd., Sinopec, Shanghai 200137, China)Abstract: The quality upgrade of automotive gasoline is a major national demand at the turn of the century. Facing this challenge, China ’s oil refining industry has independently designed a proper technology development strategy, proposed the maximizing iso -paraffins (MIP) technology, and developed a series of technologies and corresponding technical routes adapted to the gasoline production at different emission regulation stages. This paper reviewed the international environment at the beginning of the birth of MIP technology, the problems faced by domestic catalytic cracking technology at that time and the role of MIP technology in the process of gasoline quality upgrading and technology development strategies. On this basis, the relevant researchers closely followed the market demand, continuously absorbed emerging technologies to achieve continuous updates of MIP technology, and thus kept it strong competitive in the market. Based on market demand, the continuous upgrades of MIP technology kept it strongly competitive. The experience and enlightenment of the successful development and large-scale application of MIP technology were expected to become a paradigm of China ’s route of scientific and technological self-reliance.Keywords: catalytic cracking; maximizing iso -paraffins; gasoline; olefins; octane number; multiscale simulation观点DOI :10.16085/j.issn.1000-6613.2023-0920收稿日期:2023-06-05;修改稿日期:2023-06-20。
生产清洁汽油组分并增产丙烯的催化裂化工艺
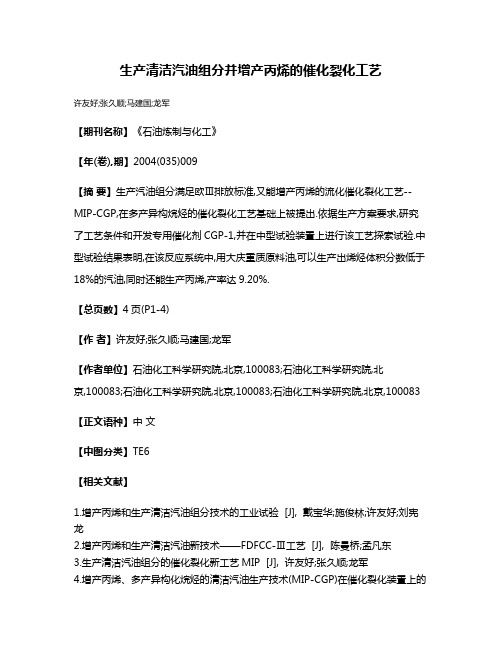
生产清洁汽油组分并增产丙烯的催化裂化工艺
许友好;张久顺;马建国;龙军
【期刊名称】《石油炼制与化工》
【年(卷),期】2004(035)009
【摘要】生产汽油组分满足欧Ⅲ排放标准,又能增产丙烯的流化催化裂化工艺--MIP-CGP,在多产异构烷烃的催化裂化工艺基础上被提出.依据生产方案要求,研究了工艺条件和开发专用催化剂CGP-1,并在中型试验装置上进行该工艺探索试验.中型试验结果表明,在该反应系统中,用大庆重质原料油,可以生产出烯烃体积分数低于18%的汽油,同时还能生产丙烯,产率达9.20%.
【总页数】4页(P1-4)
【作者】许友好;张久顺;马建国;龙军
【作者单位】石油化工科学研究院,北京,100083;石油化工科学研究院,北
京,100083;石油化工科学研究院,北京,100083;石油化工科学研究院,北京,100083【正文语种】中文
【中图分类】TE6
【相关文献】
1.增产丙烯和生产清洁汽油组分技术的工业试验 [J], 戴宝华;施俊林;许友好;刘宪龙
2.增产丙烯和生产清洁汽油新技术——FDFCC-Ⅲ工艺 [J], 陈曼桥;孟凡东
3.生产清洁汽油组分的催化裂化新工艺MIP [J], 许友好;张久顺;龙军
4.增产丙烯、多产异构化烷烃的清洁汽油生产技术(MIP-CGP)在催化裂化装置上的
应用 [J], 杨健;谢晓东;蔡智
5.生产清洁汽油组分并增产丙烯的催化裂化工艺(CGP) [J], 无
因版权原因,仅展示原文概要,查看原文内容请购买。
国内FCC工艺进展及问题(中国石油)-20160519-许友好
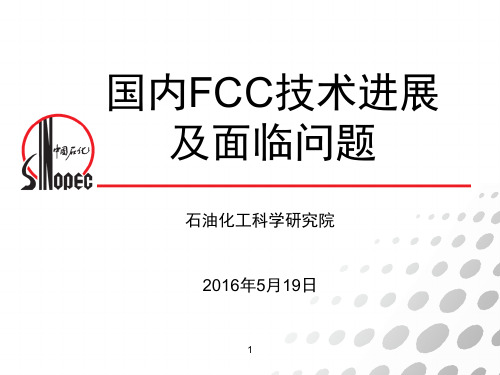
经济效应极其显著,千万吨炼油厂税后利润约为4亿
2016年11月28日 24
应用推广社会效益(1000万吨/年)
基础流程 一 1 2 5 二 8 原料 原油 甲醇 天然气 外购氢气(自煤制氢) 产品 汽油 93#国五汽油 94#国六汽油 9 10 0#柴油(国 V) 0#柴油(国 VI) 999.66 920 3.72 27.84 0 906.82 240.61 240.61 0.00 276.9 IHCC 1007.86 920 12.94 21.82 5 917.48 309.97 0.00 309.97 0 256.94 增量 8.2 0 9.22 -6.02 5 10.66 69.36 -240.61 309.97 -276.9 256.94
多产汽油方案:IHCC液体产品增加8.56百分点,且汽油产率超过50% 多产轻质油方案:IHCC液体产品增加10.04百分点
应用效果
原料中的碳氢有效利用率
工艺类型 标定方案 原料油 原料 100.0 EC 87.26 79.83 85.26 12.19 100.0 87.52 89.64 91.70 产率 FCC 多产汽油 碳含量 氢含量 产率 IHCC 多产轻质油 碳含量 氢含量 12.19+ 0.49
0 40
50
60
70 转化 率/%
80
90
100
当转化率大于一定值后,焦炭产率急剧增 加,原料越重,对应的转化率越低
8
试验最佳转化率区间
12.8 茂名加氢重油
大庆蜡油
9.0
12.4
焦炭选择性 /%
12.0
11.6 11.2
偏离最佳 转化率区 间 正好落在 最佳转化 率区间
6.0
我国催化裂化设备工艺发展现状及未来趋势

我国催化裂化设备工艺发展现状及未来趋势摘要:催化裂化设备工艺在炼油方面至关重要。
我国催化剂的制备技术已取得了长足的进步,国产催化剂在渣油裂化能力和抗金属污染等方面均已达到或超过国外的水平。
在减少焦炭、取出多余热量、催化剂再生、能量回收等方面的技术有了较大进展,催化裂化设备工艺将取得更大的发展。
关键词:催化裂化;设备工艺技术;发展现状;未来趋势0 引言在我国石油资源中,炼油工业必须走向深加工的路线,这是由于我国原油大部分偏重,且轻质油品含量低所决定的。
近几十年来我国催化裂化的技术水平逐步提高,油量也不断提升,且处于世界领先地位。
同时我国在催化剂的制备方面也有很大进步,甚至在许多方面都超过国外的先进水平。
我国石油资源中,原油大部分偏重,轻质油品含量低,这就决定了炼油工业必须走深加工的路线。
近十几年来,催化裂化掺炼渣油量在不断上升,已居世界领先地位。
催化剂的制备技术已取得了长足的进步,国产催化剂在渣油裂化能力和抗金属污染等方面均已达到或超过国外的水平。
在减少焦炭、取出多余热量、催化剂再生、能量回收等方面的技术有了较大发展。
1 现代催化裂化工艺设备发展现状及趋势催化裂化是最重要的重质油轻质化过程之一,这是因为:热裂化因技术落后而被淘汰;焦化适合减压渣油;加氢裂化技术先进,产品收率高,质量好但设备投资大,操作费用高,氢气来源有困难。
因此催化裂化成为了油轻质化的主要手段。
商品汽油有80%、柴油有33%是来自催化裂化技术的。
同时我国原油加工能力每年2.7亿吨,其中催化裂化超过1亿吨/年。
催化裂化是现代化炼油厂用来改质重质瓦斯油和渣油的核心技术,是炼厂获取经济效益的一种重要方法。
影响催化裂化未来发展的重要因素是:原油价格、满足环保要求、新燃料规格、石油化工原料需求和渣油加工。
环保法规已成为催化裂化工艺技术发展的主要推动力。
已从简单解决诸如汽油、柴油、液化气、抗金属等其中的一、二个问题转向要同时解决多个矛盾的组合。
- 1、下载文档前请自行甄别文档内容的完整性,平台不提供额外的编辑、内容补充、找答案等附加服务。
- 2、"仅部分预览"的文档,不可在线预览部分如存在完整性等问题,可反馈申请退款(可完整预览的文档不适用该条件!)。
- 3、如文档侵犯您的权益,请联系客服反馈,我们会尽快为您处理(人工客服工作时间:9:00-18:30)。
《中国科学》杂志社
SCIENCE CHINA PRESS
我国催化裂化工艺技术进展
许友好*
中国石化石油化工科学研究院, 北京 100083 *通讯作者, E-mail: xuyouhao.ripp@ 收稿日期: 2013-07-14; 接受日期: 2013-08-30; 网络版发表日期: 2013-11-01 doi: 10.1360/032013-233
年开发了 MIP 工艺技术, 并迅速得到大范围应用[4, 5]; 2007 年又开发了 IHCC/HSCC 技术, 现正处于工业试 验前期[6]. 从我国催化裂化工艺由无到有的发展经验来看 , 真正实现完全自力更生开发催化裂化技术 , 闯出一 条独特的具有中国特色的发展 , 有 3 个重要因素 [7]: 第一重要因素是必须有一个强有力的领导核心 , 能 够高效地组织各方面的力量 , 因而自开始阶段即能 从工艺研究、工程设计与施工、关键设备制造和装置 生产几方面齐头并进地同时展开工作 , 从而节省大 量的时间, 迅速达到较高的技术水平; 第二重要因素 是在关键的技术节点上必须有领军人物 , 如我国早 期催化裂化工艺设计领军人物陈俊武院士、 工艺研究 与开发领军人物武宝琛博士、 催化剂研究与开发领军 人物闵恩泽院士, 这 3 位杰出的科学家为我国催化裂 化技术发展做出了杰出贡献, 在其带领下, 形成了强 有力的研究开发和工程设计团队 ; 第三重要因素是 无数技术人员和生产操作人员的无私奉献 . 在自主
产率分布 (%)
汽油性质
烯烃 芳烃 MON
a) 抚顺二厂第一套装置的标定数据; b) 高桥分公司渣油催化裂化装置标定数据
入大气中. 再生器烧焦所用的空气由主风机供给, 大 部分空气分成两路进辅助燃烧室 , 以较高的线速通 过分布板小孔, 进入再生器密相床层, 与催化剂接触 进行烧焦; 少量的空气经增压机增压, 增压后送到密 相提升管, 作提升空气用. 密相流化催化裂化装置加 工大庆蜡油时典型的产物分布和汽油产品性质列于 表 1[7]. 兰州炼油厂于 1965 年 12 月建成了我国第一套 3 kt/a 的微球催化剂生产装置, 生产出合格的微球催 化剂. 随后, 微球催化剂应用于我国第一套催化裂化 装置, 并取得满意的工业应用结果. 随着催化裂化装 置的增多以及加工能力的增加, 1970、1976 和 1978 年 相继在长岭炼油厂、 齐鲁石化公司催化剂厂和石油六 厂建成投产年产分别为 6、4.5 和 2 kt 的微球催化剂 生产装置, 从而形成了我国 4 个裂化催化剂制备基地[9].
图1
密相床催化裂化反应-再生系统示意图
中国科学: 化学
2014 年
第 44 卷
第1期
表1
不同类型反应器催化裂化装置典型的产物分布及产品性质
密相流化 a) 无定形硅铝 0.8410 0.15 467 100 1.48 11.6 44.20 35.50 6.00 1.22 100.00 64.50 92.34 54.8 8.4 82.2 提升管 a) 沸石 0.8722 0.13 493 82 1.42 10.92 49.63 31.30 5.35 1.38 100.00 68.70 92.65 29.6 10.6 77.3 +4.20 +0.31 25.2 +2.2 4.9 变化幅度 提升管 b) 沸石 0.8967 4.0 515 5.5 3.79 15.44 44.14 22.57 4.64 0.65 8.92 0.50 100.00 72.79 82.15 43.1 / 79.2 变径提升管 b) 沸石 0.8966 4.68 497 1.15 2.88 14.63 49.28 21.22 3.04 8.64 0.31 100.00 75.74 85.13 34.3 14.8 80.2 +2.95 +2.98 8.8 +1.0 变化幅度
关键词 流化催化裂化 提升管 变径串联提升管 催化裂解 高选择性催化裂化
1
引言
20 世纪 50 年代以来, 我国催化裂化工艺技术取 得了跨越式发展, 催化裂化装置实现了从无到有, 研 究方式实现了从跟踪模仿到自主创新的转变 . 到目 前为止 , 国内催化裂化工艺技术水平处于国际先进 水平, 已有 150 多套不同类型的催化裂化装置建成投 产 , 处理量已接近 150 Mt/a, 其中渣油含量占 40%. 从我国催化裂化技术发展历程来看, 1965 年实现了催 化裂化工艺的工业化 , 催化裂化技术的开发处于起 步阶段, 典型的成就是建立石油二厂 0.6 Mt/a 密相输 送流化催化裂化装置 , 实现了从无到有的质的飞跃 ; 1971~1985 年开发渣油催化裂化技术, 催化裂化技术 的开发处于跟踪阶段[1], 典型的成就是沸石催化剂的 提升管催化裂化工艺的开发、 快速流化床烧焦罐再生 技术的开发和渣油催化裂化工艺技术的开发 ; 1986~ 1990 年开始进行催化裂解技术的开发 , 标志着我国 催化裂化技术开发进入自主创新阶段[2, 3]; 随后, 1998
摘要
自我国第一套流化催化裂化装置于 1965 年实现工业化以来, 先后开发出沸石催
化剂-提升管催化裂化、渣油催化裂化、催化裂解、变径串联提升管催化裂化和正在开发 的高选择性催化裂化; 经历了催化裂化装置从无到有, 技术水平由低到高, 装置规模和加 工能力从小到大, 研究思路从跟踪模仿到自主创新, 取得了巨大的成就, 已跻身国际先进 水平. 到目前为止, 全国催化裂化装置总加工能力已达到近 150 Mt/a, 其中渣油占催化裂 化总进料约 40%, 所生产的汽油和柴油组分分别占全国汽油和柴油成品总量的 70%和 30%左右, 所生产的丙烯量约占全国丙烯总产量的 40%. 同时, 此催化裂化装置还可为烷 基化装置和醚化装置提供原料. 这些成果对我国炼油行业加工重质原料、 提高轻质油收率 和改善产品质量, 进而提高经济效益起着举足轻重的作用.
反应器类型 催化剂 大庆蜡油性质 操作条件
密度 (20 ℃ , g/cm3) 残炭 (%) 反应 (提升管出口) 温度 (℃ ) 回炼比 (%) 干气 液化气 汽油 柴油 油浆 焦炭 损失 合计 转化率 总液收
+26 18 0.06 0.68 +5.43 4.20
18 4.35 0.91 0.81 +5.14 1.35 1.60 0.28
2
密相流化床催化裂化工艺
1941 年 2 月 11 日, 流化催化裂化工艺正式诞生, 随后开发出第二代、三代催化裂化技术, 1952 年开发 出第四代流化催化裂化技术 . 我国的第一套密相流 化催化裂化装置于 1962 年开始设计, 1965 年 5 月 5 日第一套 0.6 Mt/a 同高并列式密相流化催化裂化装置 在抚顺石油二厂建成投产, 其在处理能力、产品收率 和产品质量等方面均达到了设计目标 , 顺利地实现 了试生产一次成功 . 这表明这套完全由国内自行设 计、自行制造设备、自行施工的催化裂化装置设计是 先进的, 设备制造的质量是可靠的, 工程质量是优良 的. 这是在石油部卓有成效的组织下, 调动了石油部 内部各方面的力量 , 开展石油部内外单位的大力协 作, 加速了科研、 设计、 设备试制及必要的国外订货、 施工建设和生产准备等一系列工作的步伐 , 在短短 的 3 年时间内实现了从无到有的质的飞跃. 这套催化 裂化装置的建成和投产标志着我国炼油工业达到了 一个新阶段 , 大大缩短了我国与西方发达国家在炼 油领域的差距, 为我国随后全面发展炼油新工艺、新 技术提供了宝贵的经验 , 同时也推动了我国炼油工 业的设备和仪表制造技术的快速发展. 密相流化催化裂化反应-再生系统设备主要包括 反应器和再生器, 两者并列安装于构架上, 底部用 U 形管相连接, 如图 1 所示. 新鲜原料和回炼油混合后 进入加热炉加热至 300~330 ℃ , 然后送到反应器的 进料喷嘴, 在蒸汽雾化下喷入稀相提升管, 与来自再 生器的催化剂接触, 发生气化和反应, 随后油气和催 化剂一起从进料弯管被送到密相流化床反应器床层 内, 继续进行反应, 此时油气线速约为 1.2 m/s. 大约
3
3.1
沸石催化剂的提升管催化裂化工艺的开发
沸石催化剂的提升管催化裂化工艺的开发
20 世纪 60 年代中期, 由美国石油公司首先成功 开发了沸石催化剂的提升管催化裂化工艺 . 与密相 流化床催化裂化工艺相比 , 其具有轻质油收率高 ( 尤
其是汽油产率大幅度增加)、 生产方案灵活等优点, 从 而很快地取代了密相流化床催化裂化工艺 , 为沸石 催化剂工业应用提供更加适宜的反应器 . 石油化工 科学研究院于 1973 年建成了一套处理量为 0.24 t/d 的中型提升管催化裂化装置 , 并在这套中型装置上 进行了多种沸石催化剂和不同类型的原料油评价试 验 , 为大型工业化提升管催化裂化装置的设计和开 工提供了有用的工艺设计基础数据 . 在取得满意的 试验结果和工业装置所需的设计基础数据后 , 石油 化工科学研究院与玉门石油管理局炼油厂、 石油化工 规划设计院等单位合作, 于 1974 年 8 月首先将玉门 炼油厂 0.12 Mt/a 同高并列装置改造成我国第一套高 低并列式提升管催化裂化装置 , 取得满意的工业试 验结果, 其反应-再生部分工艺流程如图 2 所示. 随后, 石油化工科学研究院与石油化工规划设计院、 抚顺石 油二厂合作 , 将抚顺石油二厂的流化床催化裂化装 置改造成提升管催化裂化装置 , 使其处理能力提高 到 0.9 Mt/a, 沸石催化剂的提升管催化裂化装置加工 大庆蜡油时典型的产物分布和汽油产品性质见表 1. 此后 , 国内所有的改造或新建的催化裂化装置均采 用提升管反应器 , 迄今已有上百套提升管催化裂化 装置. 与此同时, 进行了稀土 X 型沸石催化剂的研究
许友好: 我国催化裂化工艺技术进展
创新阶段 , 科技人员的个人素质在寻找正确的研究 方向上已上升为第一重要因素 , 行政干预可能起到 相反的作用 . 爱因斯坦总结自己的科学生涯经验后 感叹到 : 提出一个问题往往比解决一个问题更重要 , 解决一个问题也许仅是一个数学或实验上的技能而 已 , 而提出新的问题 , 新的可能性 , 从新的角度去看 旧的问题, 却需要创新性的想象力, 并标志着科学的 真正进步. 侯祥麟曾经指出: 大的创新必须有新的思 维, 光靠号召、 光靠投入不见得就能引出新的思维来; 至于要靠领导确定任务 , 企图用行政命令加以实现 , 得到创新, 恐怕只会起到相反的效果[8].