催化裂化的工艺特点及基本原理
催化裂化原理
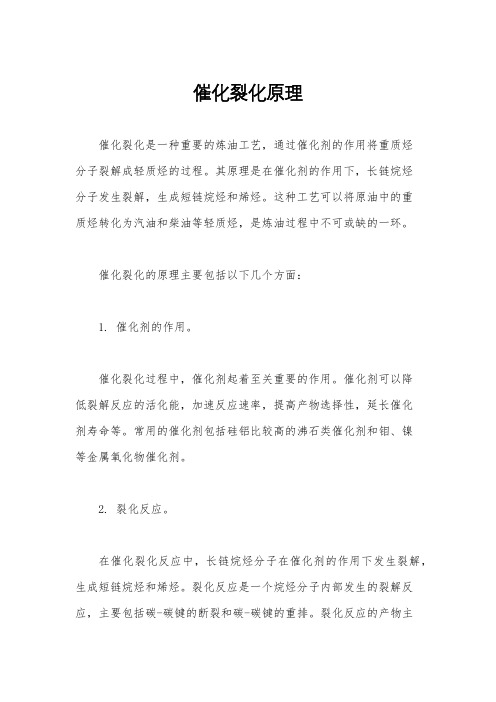
催化裂化原理催化裂化是一种重要的炼油工艺,通过催化剂的作用将重质烃分子裂解成轻质烃的过程。
其原理是在催化剂的作用下,长链烷烃分子发生裂解,生成短链烷烃和烯烃。
这种工艺可以将原油中的重质烃转化为汽油和柴油等轻质烃,是炼油过程中不可或缺的一环。
催化裂化的原理主要包括以下几个方面:1. 催化剂的作用。
催化裂化过程中,催化剂起着至关重要的作用。
催化剂可以降低裂解反应的活化能,加速反应速率,提高产物选择性,延长催化剂寿命等。
常用的催化剂包括硅铝比较高的沸石类催化剂和钼、镍等金属氧化物催化剂。
2. 裂化反应。
在催化裂化反应中,长链烷烃分子在催化剂的作用下发生裂解,生成短链烷烃和烯烃。
裂化反应是一个烷烃分子内部发生的裂解反应,主要包括碳-碳键的断裂和碳-碳键的重排。
裂化反应的产物主要是烷烃、烯烃和芳烃。
3. 反应条件。
催化裂化的反应条件包括温度、压力、催化剂种类和用量等。
通常情况下,催化裂化反应需要在较高的温度下进行,以提高反应速率和产物选择性。
此外,适当的压力和催化剂的选择也对裂化反应的效果有重要影响。
4. 产物分离。
催化裂化反应产生的混合气体需要进行分离和纯化,以得到所需的轻质烃产品。
通常采用的分离技术包括精馏、萃取、吸附等,以获得高纯度的汽油和柴油产品。
5. 催化剂再生。
在催化裂化过程中,催化剂会因受到焦炭和烃类物质的污染而失活,需要进行再生。
催化剂再生是通过热氧化或化学氧化等方法将焦炭烧除,恢复催化剂的活性和选择性,延长催化剂的使用寿命。
总的来说,催化裂化是一种重要的炼油工艺,通过催化剂的作用将重质烃分子裂解成轻质烃,可以提高原油的利用率,生产出更多的汽油和柴油产品。
催化裂化的原理涉及催化剂的作用、裂化反应、反应条件、产物分离和催化剂再生等多个方面,需要综合考虑和控制,以实现高效、稳定的生产过程。
催化裂化工艺与工程

催化裂化工艺与工程引言催化裂化工艺与工程是石油炼制领域中的重要技术,其通过催化剂的作用,将重油分子裂解为较轻的产品。
催化裂化工艺在石油化工行业中具有广泛应用,可以生产出汽油、液化气和轻质石脑油等产品,对石油资源的高效利用具有重要意义。
催化裂化反应原理1.催化裂化反应介质:常见的催化剂是硅铝酸盐,其具有高的表面积和一定的酸性。
催化剂通过提供活性中心,促进了重油分子的裂解反应。
2.催化裂化反应机理:重油中的长链烷烃在催化剂的作用下发生裂解,产生较短的烷烃和芳烃。
裂解过程中产生了大量的烯烃和芳烃,这些物质是石油下游加工的重要原料。
催化裂化工艺流程1.原料预处理:重油首先需要进行预处理,包括去除硫、氮等杂质,以减小对催化剂的毒化作用。
2.催化裂化反应:重油在裂化装置中与催化剂接触,发生裂解反应。
在裂化过程中,需要严格控制反应温度、压力和催化剂的用量,以提高产品的收率和质量。
3.分离工序:裂化反应产生的产物包括汽油、液化气、轻质石脑油等组分,这些组分需要经过分离工序进行提取。
主要包括精馏、吸附和深度处理等步骤。
4.催化剂再生:经过一段时间的使用,催化剂表面会产生积炭和失活,需要进行再生。
催化剂再生的过程包括热氧化和酸洗等步骤,以恢复催化剂的活性。
5.产品处理:裂化产物需要进一步进行加工和改性,以获得符合市场需求的成品。
催化裂化工程设计1.反应器设计:反应器是催化裂化装置的核心部分,设计合理的反应器可以提高反应效率和产物质量。
反应器设计考虑因素包括反应器类型、反应器尺寸、反应器温度和压力等。
2.催化剂选择:催化剂的选择是催化裂化工程设计中的重要一环。
催化剂的性能直接影响反应的效果和产物的质量。
选择合适的催化剂需要考虑其活性、稳定性和成本等因素。
3.热力学和动力学模型:对催化裂化反应进行热力学和动力学模拟,可以预测反应过程中的表现和优化操作条件。
4.安全性考虑:催化裂化工程设计需要考虑装置的安全性。
石油化工装置涉及高温、高压和易燃易爆物质,需要进行安全分析和设计,以确保操作的安全性和稳定性。
催化裂解工艺(DCC)

催化裂解工艺(DCC)1.工艺原理:催化裂解工艺(DCC)是以重质油为原料、利用择形催化反应制取气体烯烃的新技术。
其中催化裂解Ⅰ型(DCC-Ⅰ)以生产最大量丙烯为主要目的,催化裂解Ⅱ型(DCC-Ⅱ)以生产最大量异丁烯和异戊烯、兼产丙烯和高辛烷值优质汽油为目的。
它们所加工的原料可以是蜡油、蜡油掺渣油或二次加工油以及常压渣油,实现了炼油工艺向石油化工的延伸,开创了一条以重质油为原料直接制取低碳烯烃的新途径,达到国际先进水平。
由于目的产品不同,DCC-Ⅰ和DCC-Ⅱ两者采用的反应器型式、催化剂类型和工艺操作条件都不相同,其差别列于表1。
从表1可见,DCC-Ⅱ的反应时间、反应温度、剂油比及注水量均低于DCC-Ⅰ。
表1:DCC-Ⅰ和DCC-Ⅱ工艺的主要差别DCC-ⅠDCC-Ⅱ反应器型式提升管十床层提升管催化剂CRP CIP反应温度,℃540-580500-530剂油比9-156-9注水量,m%15-256-10产品分布,m%H2~C211.91 5.59C3~C442.2234.49C5+汽油26.6039.00柴油 6.609.77重油 6.07 5.84焦炭 6.00 4.31损失0.60 1.00合计100.00100.00烯烃产率,m%丙烯21.0314.29总丁烯14.0314.65异丁烯 5.13 6.13总戊烯--9.77异戊烯-- 6.77异丁烯/总丁烯0.360.42异戊烯/总戊烯--0.69汽油性质RONC99.396.4MONC84.782.5催化裂解利用择形催化反应原理,将重质原料油选择性裂化成低碳气体烯烃,其丙烯产率是常规FCC的3倍以上。
异丁烯和异戊烯产率也达到FCC的3倍以上。
催化裂解工艺开辟了一条制取低碳烃的新途径。
1.1催化裂解的一般特点①催化裂解是碳正离子反应机理和自由基反应机理共同作用的结果,其裂解气体产物中乙烯所占的比例要大于催化裂化气体产物中乙烯的比例。
②在一定程度上,催化裂解可以看作是高深度的催化裂化,其气体产率远大于催化裂化,液体产物中芳烃含量很高。
催化裂化机理及特点

催化裂化机理及特点催化裂化是一种通过加热和催化剂的作用将长链烃分子裂解为短链烃分子的重要工艺。
催化裂化机理及特点主要包括以下几个方面:一、催化裂化机理1.构造反应:长链烃分子在裂化过程中首先发生构造反应,通过裂解碳-碳键,形成相对较短的碳链碳烃和烯烃。
2.重排反应:长链烃分子中的骨架碳骨架会经历一系列重排反应,使得产物中更多的是相对稳定的异构体和环状化合物。
3.脱氢反应:重排反应过程中,长链分子中的烃基可能失去氢原子,从而形成烯烃,增加了催化裂化的产物中烯烃的含量。
4.脱氢裂解反应:在高温高压下,部分碳链碳烃可以发生脱氢裂解反应,形成更短的链长烃烃烃烃、烯烃和芳香烃。
二、催化裂化特点1.催化裂化具有高选择性:在催化剂的影响下,催化裂化反应主要发生在长链烃分子中的弱键和缺陷位置,使得产物中的碳链长度相对较短,同时产生更多的异构体和环状化合物。
2.催化裂化反应速度快:催化剂的存在提高了反应活性,使得裂化反应可以在相对低的温度和压力下进行,加快了反应速度。
3.催化裂化可以产生高附加值的产品:催化裂化使得重质燃料油转化为轻质烃类产品,其中包括汽油、炼厂气、润滑油基础油等,这些产品有较高的附加值。
4.催化裂化可以降低能源消耗:通过催化裂化将重质原油转化为较轻质产品,如汽油和炼厂气,不仅提供了更多的高附加值产品,还减少了对原油的需求,降低了能源消耗。
5.催化裂化可以调节产品分布:通过不同的催化剂组合和反应条件,可以调节催化裂化产物的碳链长度分布,以满足市场需求,提高产品经济效益。
总之,催化裂化是一种高效、高选择性的炼油工艺,通过加热和催化剂的作用,将长链烃分子裂解为短链烃分子,产生高附加值产品,并降低能源消耗。
催化裂化机理和特点的深入研究对于提高炼油工艺的效率和降低能源消耗具有重要意义。
催化催化裂化技术

催化催化裂化技术催化裂化技术是一种重要的炼油工艺,可以将重质石油馏分转化为高附加值的轻质产品。
本文将从催化裂化技术的原理、应用和发展前景等方面进行探讨,以期为读者提供对该技术的全面了解。
一、催化裂化技术的原理催化裂化技术是通过催化剂的作用将重质石油馏分分解为较轻的产品。
其主要原理是在高温和高压的条件下,将原料油与催化剂接触,使其发生裂化反应。
这种反应可以将长链烃分子裂解成短链烃分子,从而提高汽油和燃料油的产率。
催化裂化反应主要分为两个阶段:热裂化和催化裂化。
在热裂化阶段,原料油在高温下分解成烃气和液体烃。
然后,在催化剂的作用下,烃气和液体烃进一步反应,生成较轻的产品,如汽油、液化气和柴油等。
二、催化裂化技术的应用催化裂化技术在炼油行业中具有广泛的应用。
首先,它可以提高汽油的产率。
由于汽车的普及,对汽油的需求量不断增加。
催化裂化技术可以将重质石油馏分转化为轻质的汽油,从而满足市场需求。
催化裂化技术可以生产出高质量的柴油。
在催化裂化过程中,石油馏分中的硫、氮和金属等杂质可以得到有效去除,从而提高柴油的质量。
这对于减少柴油排放的污染物具有重要意义。
催化裂化技术还可以生产出液化气、石脑油和石化原料等产品。
这些产品在化工、冶金和化肥等行业中具有广泛的应用。
三、催化裂化技术的发展前景随着能源需求的增加和石油资源的日益枯竭,催化裂化技术在未来的发展前景十分广阔。
一方面,随着汽车工业的高速发展,对汽油的需求将持续增加,催化裂化技术将成为满足市场需求的重要手段。
另一方面,随着环境保护意识的提高,对燃料油质量的要求也越来越高。
催化裂化技术可以提高燃料油的质量,减少对环境的污染,因此在未来的发展中具有重要的作用。
随着科技的不断进步,催化剂的研发和改进也将推动催化裂化技术的发展。
新型的催化剂可以提高反应的选择性和活性,从而提高产品的产率和质量。
催化裂化技术作为一种重要的炼油工艺,在提高石油产品产率和质量方面具有重要的作用。
催化裂化的工艺特点及基本原理

催化裂化的工艺特点及基本原理催化裂化是一种重要的石油加工工艺,其开发和应用对于提高石油产业发展水平具有重要的意义。
催化裂化工艺的特点和基本原理如下:一、工艺特点:1.高选择性:催化裂化工艺可以将石油馏分中的大分子烃化合物按照其碳数分解为较低碳数的烃化合物,其中可选择的烃化合物主要是汽油和液化气。
因此,催化裂化可以提高汽油和液化气产率,达到更好的操作经济效益。
2.产物分布广:催化裂化反应不仅可以生成汽油和液化气,还可以生成较低碳数的烃化合物,如乙烯、丙烯等。
因此,催化裂化反应可以提供多种不同碳数的烃化合物,满足不同需求。
3.增塔体积积极:催化裂化工艺采用固定床反应器,反应器内填充了催化剂颗粒,因此反应器体积较大。
大体积的反应器可以增加催化裂化反应的容量,提高石油裂解速率,并且还可以增加反应过程的稳定性和可控性。
4.废气利用:催化裂化反应产生的废气中含有非常丰富的烃化合物和能量,可以通过适当的处理和回收利用,从而得到更好的经济效益,并减少对环境的污染。
二、基本原理:催化裂化反应是通过催化剂的作用来进行的,其基本原理如下:1.裂解反应:石油中的长链烃化合物在催化剂的作用下发生热裂解反应,将大分子烷烃分解成较小分子的烃化合物。
这种反应是一个链状反应过程,会生成一系列的短链烃化合物和碳氢烃中间体。
2.重排反应:短链烃化合物和碳氢烃中间体在催化剂的作用下发生重排反应,重新组合成不同碳数的烃化合物。
3.芳构化反应:在催化裂化过程中,由于催化剂特殊的性质,烃化合物还会发生芳构化反应,生成芳烃类化合物,如苯、甲苯等。
4.积碳反应:由于裂化过程产生的碳元素会在催化剂表面析出,形成碳黑,导致催化剂失活。
因此,催化裂化还需要定期对催化剂进行再生,以保持其活性。
综上所述,催化裂化工艺具有高选择性、广泛的产物分布、增塔体积积极和废气利用等特点。
其基本原理包括裂解反应、重排反应、芳构化反应和积碳反应。
催化裂化工艺的开发和应用有助于提高石油产业的经济效益和环境可持续性。
简述催化裂化工艺原理
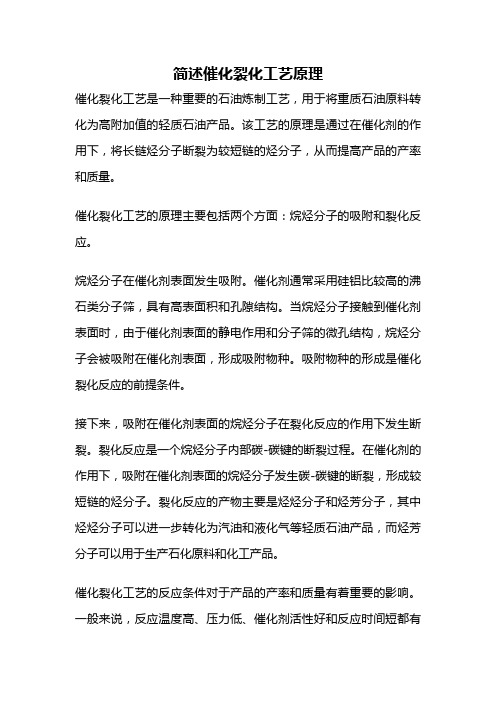
简述催化裂化工艺原理催化裂化工艺是一种重要的石油炼制工艺,用于将重质石油原料转化为高附加值的轻质石油产品。
该工艺的原理是通过在催化剂的作用下,将长链烃分子断裂为较短链的烃分子,从而提高产品的产率和质量。
催化裂化工艺的原理主要包括两个方面:烷烃分子的吸附和裂化反应。
烷烃分子在催化剂表面发生吸附。
催化剂通常采用硅铝比较高的沸石类分子筛,具有高表面积和孔隙结构。
当烷烃分子接触到催化剂表面时,由于催化剂表面的静电作用和分子筛的微孔结构,烷烃分子会被吸附在催化剂表面,形成吸附物种。
吸附物种的形成是催化裂化反应的前提条件。
接下来,吸附在催化剂表面的烷烃分子在裂化反应的作用下发生断裂。
裂化反应是一个烷烃分子内部碳-碳键的断裂过程。
在催化剂的作用下,吸附在催化剂表面的烷烃分子发生碳-碳键的断裂,形成较短链的烃分子。
裂化反应的产物主要是烃烃分子和烃芳分子,其中烃烃分子可以进一步转化为汽油和液化气等轻质石油产品,而烃芳分子可以用于生产石化原料和化工产品。
催化裂化工艺的反应条件对于产品的产率和质量有着重要的影响。
一般来说,反应温度高、压力低、催化剂活性好和反应时间短都有利于提高产品的产率。
此外,催化裂化工艺还需要添加适量的催化剂再生剂,以保证催化剂的活性和稳定性。
催化裂化工艺在石油炼制中具有广泛的应用。
通过该工艺可以将重质石油原料转化为高附加值的轻质石油产品,如汽油、柴油和液化气等。
同时,催化裂化工艺还可以提高石油产品的产率和质量,减少燃料的消耗和环境污染。
催化裂化工艺是一种重要的石油炼制工艺,通过在催化剂的作用下将重质石油原料转化为轻质石油产品。
该工艺的原理是在催化剂表面发生烷烃分子的吸附和裂化反应,从而提高产品的产率和质量。
催化裂化工艺在石油炼制中具有广泛的应用,为能源行业的发展做出了重要的贡献。
简述催化裂化工艺原理
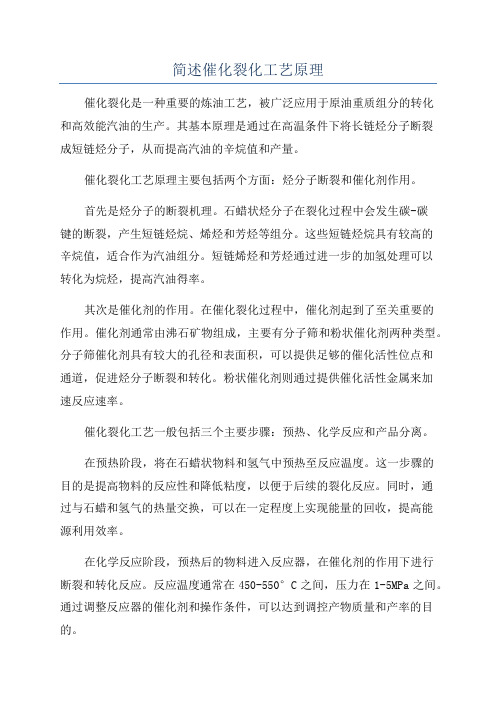
简述催化裂化工艺原理催化裂化是一种重要的炼油工艺,被广泛应用于原油重质组分的转化和高效能汽油的生产。
其基本原理是通过在高温条件下将长链烃分子断裂成短链烃分子,从而提高汽油的辛烷值和产量。
催化裂化工艺原理主要包括两个方面:烃分子断裂和催化剂作用。
首先是烃分子的断裂机理。
石蜡状烃分子在裂化过程中会发生碳-碳键的断裂,产生短链烃烷、烯烃和芳烃等组分。
这些短链烃烷具有较高的辛烷值,适合作为汽油组分。
短链烯烃和芳烃通过进一步的加氢处理可以转化为烷烃,提高汽油得率。
其次是催化剂的作用。
在催化裂化过程中,催化剂起到了至关重要的作用。
催化剂通常由沸石矿物组成,主要有分子筛和粉状催化剂两种类型。
分子筛催化剂具有较大的孔径和表面积,可以提供足够的催化活性位点和通道,促进烃分子断裂和转化。
粉状催化剂则通过提供催化活性金属来加速反应速率。
催化裂化工艺一般包括三个主要步骤:预热、化学反应和产品分离。
在预热阶段,将在石蜡状物料和氢气中预热至反应温度。
这一步骤的目的是提高物料的反应性和降低粘度,以便于后续的裂化反应。
同时,通过与石蜡和氢气的热量交换,可以在一定程度上实现能量的回收,提高能源利用效率。
在化学反应阶段,预热后的物料进入反应器,在催化剂的作用下进行断裂和转化反应。
反应温度通常在450-550°C之间,压力在1-5MPa之间。
通过调整反应器的催化剂和操作条件,可以达到调控产物质量和产率的目的。
最后,在产品分离阶段,通过一系列的分离操作,将裂化产物中的不同组分分离出来。
主要的分离方式包括蒸馏、吸附和萃取等。
其中,蒸馏是最主要的分离手段,可以将产物按烃碳数分为不同的馏分,进一步提纯和精制。
催化裂化工艺具有许多优点。
首先,可以将重质石油产品转化为高辛烷值的汽油,提高产品附加值和经济效益。
其次,可以通过调整催化剂和操作条件,实现灵活生产不同品质和组分的汽油。
再者,催化裂化可以与其他炼油工艺相结合,如加氢裂化、重整和烷基化等,进行综合重整和分子设计,进一步提高汽油产率和质量。
fcc 工艺

fcc 工艺
FCC工艺是指流体催化裂化工艺(Fluid Catalytic Cracking Process)的简称。
这是一种常见的炼油工艺,用于将重质石
油馏分转化为高附加值的轻质产品,如汽油和液化石油气。
该工艺的基本原理是在高温下,将重质石油馏分与催化剂一起进入反应器中,经过裂化反应,将长链烃分子分解为较短的烃烷和烯烃。
这些轻质烃烷和烯烃可以用作汽油和石油气等产品的原料。
FCC工艺的主要特点是反应过程连续性好、转化率高、产品
烃烷和烯烃分布广、操作灵活性强。
它可以适应不同种类和质量的石油原料,产出适应市场需求的各类产品。
在FCC工艺中,催化剂起到了关键的作用。
催化剂通常由沸石、金属氧化物等组成,能够促进烃烷分子的裂化反应。
同时,催化剂还能吸附和去除反应中产生的硫、氮等杂质,提高产品质量。
总的来说,FCC工艺在炼油行业中起到了重要的作用,可以
高效地转化重质石油馏分,提供供应市场需求的产品。
催化裂化工艺介绍
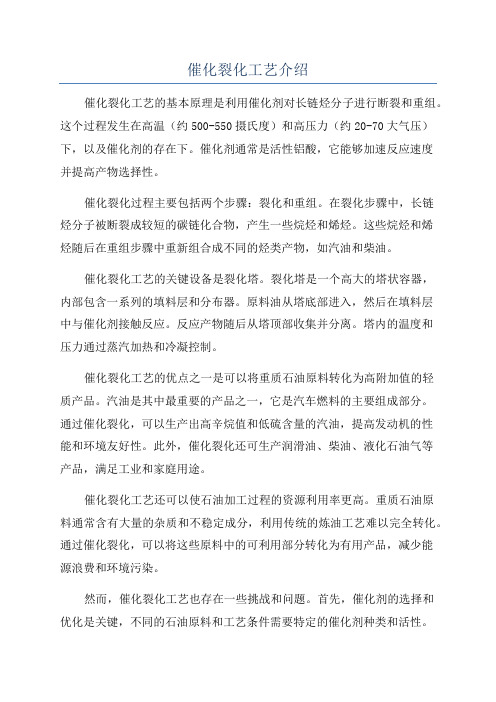
催化裂化工艺介绍催化裂化工艺的基本原理是利用催化剂对长链烃分子进行断裂和重组。
这个过程发生在高温(约500-550摄氏度)和高压力(约20-70大气压)下,以及催化剂的存在下。
催化剂通常是活性铝酸,它能够加速反应速度并提高产物选择性。
催化裂化过程主要包括两个步骤:裂化和重组。
在裂化步骤中,长链烃分子被断裂成较短的碳链化合物,产生一些烷烃和烯烃。
这些烷烃和烯烃随后在重组步骤中重新组合成不同的烃类产物,如汽油和柴油。
催化裂化工艺的关键设备是裂化塔。
裂化塔是一个高大的塔状容器,内部包含一系列的填料层和分布器。
原料油从塔底部进入,然后在填料层中与催化剂接触反应。
反应产物随后从塔顶部收集并分离。
塔内的温度和压力通过蒸汽加热和冷凝控制。
催化裂化工艺的优点之一是可以将重质石油原料转化为高附加值的轻质产品。
汽油是其中最重要的产品之一,它是汽车燃料的主要组成部分。
通过催化裂化,可以生产出高辛烷值和低硫含量的汽油,提高发动机的性能和环境友好性。
此外,催化裂化还可生产润滑油、柴油、液化石油气等产品,满足工业和家庭用途。
催化裂化工艺还可以使石油加工过程的资源利用率更高。
重质石油原料通常含有大量的杂质和不稳定成分,利用传统的炼油工艺难以完全转化。
通过催化裂化,可以将这些原料中的可利用部分转化为有用产品,减少能源浪费和环境污染。
然而,催化裂化工艺也存在一些挑战和问题。
首先,催化剂的选择和优化是关键,不同的石油原料和工艺条件需要特定的催化剂种类和活性。
其次,裂化塔的设计和操作也需要专业知识和经验,以确保正常运行和高效产物分离。
总之,催化裂化工艺是一种重要的石油加工技术,能够将重质石油原料转化为高附加值的轻质产品。
它提高了原油的利用率,增加了汽车燃料和化工原料的供应。
但该工艺也面临着一些挑战和问题,需要不断的研究和改进。
催化裂化工艺技术

催化裂化工艺技术催化裂化工艺技术是炼油行业中常用的一种重要技术,通过这种技术可以将较长碳链的石油馏分转化为更短碳链的产品。
本文将介绍催化裂化工艺技术的基本原理、工艺流程以及应用范围。
催化裂化工艺技术的基本原理是在高温、高压、催化剂存在的条件下,将较长碳链的石油馏分分解成较短碳链的产品。
其中,催化剂起到了重要的作用,它可以提高反应速率、降低反应温度和压力,并且还可以选择性地抑制一些副反应的发生,提高产品质量。
催化裂化工艺技术的工艺流程主要包括预处理、进料与裂化反应、分离与回收以及产品处理等几个步骤。
首先,在预处理过程中,将原油经过加热、除水和脱硫等处理,以去除其中的杂质和硫化物。
然后,将预处理过后的原油送入反应器中,与催化剂一起进行裂化反应。
在分离与回收过程中,通过减压蒸馏、凝结、吸附等方法,将裂化反应产生的气体、液体和固体分离出来,并回收利用其中的有用产品。
最后,对产品进行处理,例如对汽油进行加氢、重整等处理,以提高其品质。
催化裂化工艺技术广泛应用于石油炼制、化工、燃料添加剂等领域。
在石油炼制过程中,催化裂化可以将重质原油转化为轻质石油产品,以满足市场对汽油、柴油等轻质产品的需求。
另外,催化裂化还可以生产出各种化工原料,如丙烷、乙烯等。
此外,催化裂化在燃料添加剂领域也有着广泛的应用,它可以使燃料燃烧更充分,减少排放物的产生,提高环境友好性。
然而,催化裂化工艺技术也存在一些挑战和问题。
首先,催化剂的选择和制备对于反应效果有着重要的影响,因此需要进行大量的实验和研究。
其次,催化裂化反应过程中会产生大量的热量,需要进行适当的能量调节和热量回收。
此外,催化剂的寿命也是一个重要的问题,随着反应的进行,催化剂会失去活性,需要定期更换。
综上所述,催化裂化工艺技术是一种重要的炼油技术,通过将较长碳链的石油馏分转化为较短碳链的产品,满足市场对轻质石油产品的需求。
催化裂化技术的原理基于催化剂的存在,其工艺流程主要包括预处理、裂化反应、分离与回收以及产品处理等几个步骤。
(完整版)催化裂化工艺介绍
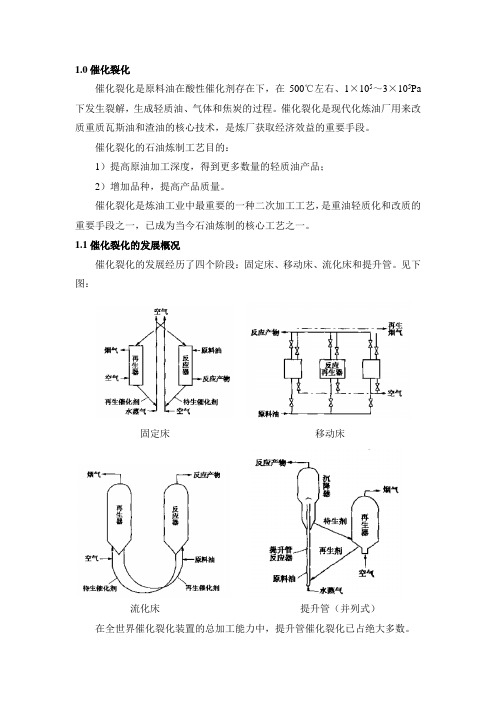
1.0催化裂化催化裂化是原料油在酸性催化剂存在下,在500℃左右、1×105~3×105Pa 下发生裂解,生成轻质油、气体和焦炭的过程。
催化裂化是现代化炼油厂用来改质重质瓦斯油和渣油的核心技术,是炼厂获取经济效益的重要手段。
催化裂化的石油炼制工艺目的:1)提高原油加工深度,得到更多数量的轻质油产品;2)增加品种,提高产品质量。
催化裂化是炼油工业中最重要的一种二次加工工艺,是重油轻质化和改质的重要手段之一,已成为当今石油炼制的核心工艺之一。
1.1催化裂化的发展概况催化裂化的发展经历了四个阶段:固定床、移动床、流化床和提升管。
见下图:固定床移动床流化床提升管(并列式)在全世界催化裂化装置的总加工能力中,提升管催化裂化已占绝大多数。
1.2催化裂化的原料和产品1.2.0原料催化裂化的原料范围广泛,可分为馏分油和渣油两大类。
馏分油主要是直馏减压馏分油(VGO),馏程350-500℃,也包括少量的二次加工重馏分油如焦化蜡油等,以此种原料进行催化裂化称为馏分油催化裂化。
渣油主要是减压渣油、脱沥青的减压渣油、加氢处理重油等。
渣油都是以一定的比例掺入到减压馏分油中进行加工,其掺入的比例主要受制于原料的金属含量和残炭值。
对于一些金属含量低的石蜡基原有也可以直接用常压重油为原料。
当减压馏分油中掺入渣油使通称为RFCC。
以此种原料进行催化裂化称为重油催化裂化。
1.2.1产品催化裂化的产品包括气体、液体和焦炭。
1、气体在一般工业条件下,气体产率约为10%-20%,其中含干气和液化气。
2、液体产物1)汽油,汽油产率约为30%-60%;这类汽油安定性较好。
2)柴油,柴油产率约为0-40%;因含较多芳烃,所有十六烷值较低,由重油催化裂化得到的柴油的十六烷值更低,这类柴油需经加氢处理。
3)重柴油(回炼油),可以返回到反应器内,已提高轻质油收率,不回炼时就以重柴油产品出装置,也可作为商品燃料油的调和组分。
4)油浆,油浆产率约为5%-10%,从催化裂化分馏塔底得到的渣油,含少量催化剂细粉,可以送回反应器回炼以回收催化剂。
催化裂化装置基本原理
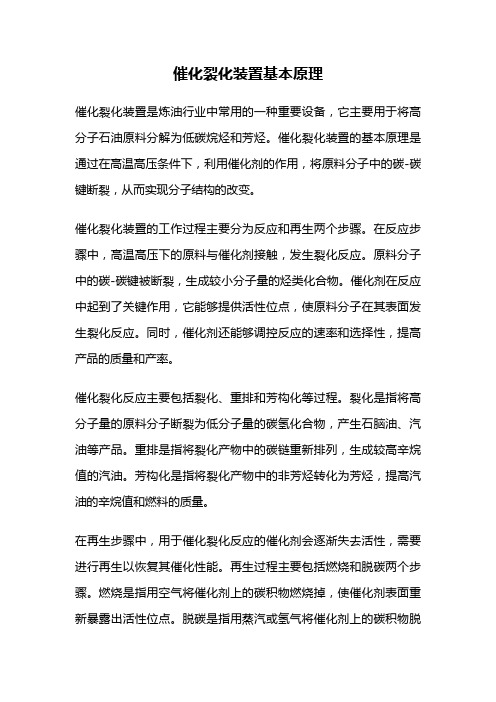
催化裂化装置基本原理催化裂化装置是炼油行业中常用的一种重要设备,它主要用于将高分子石油原料分解为低碳烷烃和芳烃。
催化裂化装置的基本原理是通过在高温高压条件下,利用催化剂的作用,将原料分子中的碳-碳键断裂,从而实现分子结构的改变。
催化裂化装置的工作过程主要分为反应和再生两个步骤。
在反应步骤中,高温高压下的原料与催化剂接触,发生裂化反应。
原料分子中的碳-碳键被断裂,生成较小分子量的烃类化合物。
催化剂在反应中起到了关键作用,它能够提供活性位点,使原料分子在其表面发生裂化反应。
同时,催化剂还能够调控反应的速率和选择性,提高产品的质量和产率。
催化裂化反应主要包括裂化、重排和芳构化等过程。
裂化是指将高分子量的原料分子断裂为低分子量的碳氢化合物,产生石脑油、汽油等产品。
重排是指将裂化产物中的碳链重新排列,生成较高辛烷值的汽油。
芳构化是指将裂化产物中的非芳烃转化为芳烃,提高汽油的辛烷值和燃料的质量。
在再生步骤中,用于催化裂化反应的催化剂会逐渐失去活性,需要进行再生以恢复其催化性能。
再生过程主要包括燃烧和脱碳两个步骤。
燃烧是指用空气将催化剂上的碳积物燃烧掉,使催化剂表面重新暴露出活性位点。
脱碳是指用蒸汽或氢气将催化剂上的碳积物脱除,以保证催化剂的活性和稳定性。
催化裂化装置的设计和操作需要考虑多个因素。
首先是选择合适的催化剂,催化剂的选择应根据原料的性质和产品的要求进行优化。
其次是控制反应的温度、压力和空速等工艺参数,以达到最佳的反应效果。
此外,催化裂化装置还需要考虑原料的预处理、氢气的补充和废热的回收利用等问题,以提高装置的效率和经济性。
催化裂化装置在炼油工业中具有重要的地位和广泛的应用。
通过裂化反应,可以将高分子的重质石油原料转化为轻质燃料和化工原料,满足市场对汽油、柴油和石脑油等产品的需求。
同时,催化裂化装置还可以提高石油产品的质量,减少环境污染物的排放,具有良好的经济和环境效益。
催化裂化装置是一种利用催化剂作用进行石油原料分解的重要设备。
催化裂化的工艺特点及基本原理
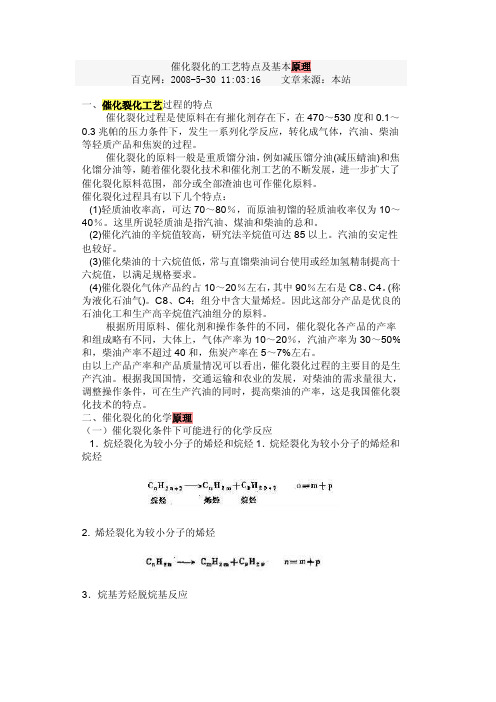
催化裂化的工艺特点及基本原理百克网:2008-5-30 11:03:16 文章来源:本站一、催化裂化工艺过程的特点催化裂化过程是使原料在有摧化剂存在下,在470~530度和0.1~0.3兆帕的压力条件下,发生一系列化学反应,转化成气体,汽油、柴油等轻质产品和焦炭的过程。
催化裂化的原料一般是重质馏分油,例如减压馏分油(减压蜻油)和焦化馏分油等,随着催化裂化技术和催化剂工艺的不断发展,进一步扩大了催化裂化原料范围,部分或全部渣油也可作催化原料。
催化裂化过程具有以下几个特点:(1)轻质油收率高,可达70~80%,而原油初馏的轻质油收率仅为10~40%。
这里所说轻质油是指汽油、煤油和柴油的总和。
(2)催化汽油的辛烷值较高,研究法辛烷值可达85以上。
汽油的安定性也较好。
(3)催化柴油的十六烷值低,常与直馏柴油词台使用或经加氢精制提高十六烷值,以满足规格要求。
(4)催化裂化气体产品约占10~20%左右,其中90%左右是C8、C4。
(称为液化石油气)。
C8、C4;组分中含大量烯烃。
因此这部分产品是优良的石油化工和生产高辛烷值汽油组分的原料。
根据所用原料、催化剂和操作条件的不同,催化裂化各产品的产率和组成略有不同,大体上,气体产率为10~20%,汽油产率为30~50%和,柴油产率不超过40和,焦炭产率在5~7%左右。
由以上产品产率和产品质量情况可以看出,催化裂化过程的主要目的是生产汽油。
根据我国国情,交通运输和农业的发展,对柴油的需求量很大,调整操作条件,可在生产汽油的同时,提高柴油的产率,这是我国催化裂化技术的特点。
二、催化裂化的化学原理(一)催化裂化条件下可能进行的化学反应1.烷烃裂化为较小分子的烯烃和烷烃1.烷烃裂化为较小分子的烯烃和烷烃2. 烯烃裂化为较小分子的烯烃3.烷基芳烃脱烷基反应4.烷基芳烃侧链断裂5.环烷烃裂化为烯烃假如环烷烃中仅有单环,则环不打开:6.氢转移反应如:环烷烃+烯烃→芳香烃+烷烃7.异构化反应:烷烃→异构烷烃烯烃→异构烯烃8.芳构化反应烯烃环化脱氢生成芳香烃,如:9.缩合反应单环芳烃可缩台成稠环芳烃,最后可缩合成焦炭,并放出氢气,使烯烃饱和。
催化裂化的工艺特点及基本原理

催化裂化的工艺特点及基本原理催化裂化是一种重要的炼油工艺,主要用于将重质石油馏分裂解为较轻的馏分,以增加汽油和其他高附加值产品的产量。
其工艺特点和基本原理如下:工艺特点:1.选择性:催化裂化能够选择性地将重质石油馏分中的长链烃破裂成较短的烃烷和烃烯。
这种选择性能使得催化裂化工艺可以得到较高品质和较高产率的汽油。
2.灵活性:催化裂化工艺可以通过控制反应条件(如温度、压力、催化剂活性等)来实现不同产品的选择性改变。
这使得生产者可以根据市场需求对产品进行灵活调整。
3.高产率:催化裂化能够将重质石油馏分中的大分子烃分解为较小的分子,从而增加汽油的产率。
此外,催化裂化还能产生其他高附加值产品,如液化石油气(LPG)、石脑油和柴油等。
4.能源效率:催化裂化可以在较低的温度和压力下进行,从而节约能源。
此外,催化裂化还可以利用石油馏分中的热和压力来驱动反应,节约能源成本。
基本原理:催化裂化是通过在催化剂的作用下将石油馏分中的长链烃分子破裂成较短的烃烷和烃烯的过程。
其基本原理包括以下几个方面:1.热裂解和催化裂解:石油馏分中的长链烃在高温条件下会发生热裂解,即分子内部键的断裂,生成较短的碳链。
催化裂化是在催化剂的作用下,将热裂解过程中产生的碳链进行选择性破裂。
2.催化剂的作用:催化剂在催化裂化反应中起到重要作用。
催化剂通常由多孔介质和活性组分组成,活性组分一般为酸性物质,如氧化铝、硅铝酸盐等。
催化剂能够吸附和解离烃分子,使其在催化剂表面发生分解反应,从而实现分子的破裂和选择性转化。
3.反应条件的控制:反应温度、压力、空速和催化剂活性等条件对催化裂化反应的效果具有重要影响。
通常情况下,较高的温度和较低的压力利于反应进行,但过高的温度会导致过度裂解和产生过多的烃烯。
因此,在实际生产中,需要综合考虑反应的产率、选择性和经济性,确定合适的反应条件。
4.产物分离和处理:催化裂化反应产生的产物通常是气体、液体和固体混合物,需要通过分离和处理工艺进行产品回收和提纯。
我国催化裂化工艺技术进展

我国催化裂化工艺技术进展一、本文概述催化裂化(FCC)作为一种重要的石油加工技术,在我国石油工业中占据着举足轻重的地位。
随着科技的不断进步和环保要求的日益严格,我国催化裂化工艺技术也在持续发展和创新。
本文旨在全面概述我国催化裂化工艺技术的最新进展,包括技术原理、工艺流程、催化剂研发、设备改进以及环保措施等方面的内容。
通过对这些方面的深入探讨,本文旨在展示我国催化裂化工艺技术在提高石油资源利用效率、促进石油工业可持续发展以及减少环境污染等方面的积极贡献。
本文还将对催化裂化工艺技术的发展趋势进行展望,以期为相关领域的科研人员和企业提供有益的参考和借鉴。
二、催化裂化工艺技术的基本原理催化裂化(Catalytic Cracking)是一种重要的石油加工过程,主要目的是将重质烃类转化为更有价值的轻质产品,如汽油、煤油和柴油等。
其基本原理是利用催化剂加速烃类分子在高温高压环境下的热裂解反应,使长链烃类断裂成较短的链烃,从而改善产品的品质和产量。
催化裂化工艺主要包括热裂化和催化裂化两个阶段。
热裂化是在没有催化剂的情况下,通过高温使烃类分子发生热裂解,生成较小的烃分子。
然而,这个过程的选择性较差,会产生大量的裂化气和焦炭,导致产品收率较低。
催化裂化则是在热裂化的基础上引入催化剂,通过催化剂的选择性吸附和表面酸性,使得烃类分子在较低的温度下就能发生裂解,同时提高裂解的选择性和产品的收率。
催化剂的活性、选择性和稳定性对催化裂化过程的影响至关重要。
在催化裂化过程中,烃类分子首先被催化剂表面的酸性位点吸附,然后在催化剂的作用下发生裂解反应。
生成的较小烃分子随后从催化剂表面脱附,进入气相,最后通过冷凝和分离得到所需的产品。
随着科技的不断进步,我国的催化裂化工艺技术也在不断发展。
新型的催化剂、反应器和工艺条件的优化等技术的发展,使得催化裂化过程的效率和选择性得到了显著提高,为我国石油工业的发展做出了重要贡献。
三、我国催化裂化工艺技术的现状我国催化裂化工艺技术自上世纪五十年代引进至今,经历了从引进消化到自主创新的发展历程,目前已经形成了具有自主知识产权的催化裂化工艺技术体系。
催化裂化工艺介绍
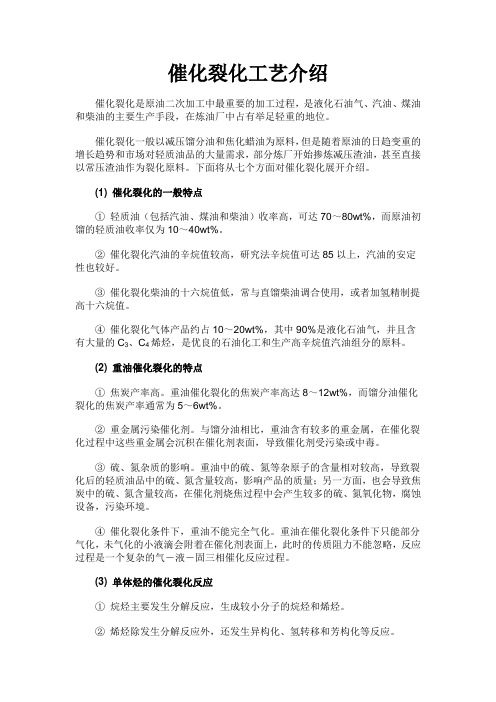
催化裂化工艺介绍催化裂化是原油二次加工中最重要的加工过程,是液化石油气、汽油、煤油和柴油的主要生产手段,在炼油厂中占有举足轻重的地位。
催化裂化一般以减压馏分油和焦化蜡油为原料,但是随着原油的日趋变重的增长趋势和市场对轻质油品的大量需求,部分炼厂开始掺炼减压渣油,甚至直接以常压渣油作为裂化原料。
下面将从七个方面对催化裂化展开介绍。
(1) 催化裂化的一般特点①轻质油(包括汽油、煤油和柴油)收率高,可达70~80wt%,而原油初馏的轻质油收率仅为10~40wt%。
②催化裂化汽油的辛烷值较高,研究法辛烷值可达85以上,汽油的安定性也较好。
③催化裂化柴油的十六烷值低,常与直馏柴油调合使用,或者加氢精制提高十六烷值。
④催化裂化气体产品约占10~20wt%,其中90%是液化石油气,并且含有大量的C3、C4烯烃,是优良的石油化工和生产高辛烷值汽油组分的原料。
(2) 重油催化裂化的特点①焦炭产率高。
重油催化裂化的焦炭产率高达8~12wt%,而馏分油催化裂化的焦炭产率通常为5~6wt%。
②重金属污染催化剂。
与馏分油相比,重油含有较多的重金属,在催化裂化过程中这些重金属会沉积在催化剂表面,导致催化剂受污染或中毒。
③硫、氮杂质的影响。
重油中的硫、氮等杂原子的含量相对较高,导致裂化后的轻质油品中的硫、氮含量较高,影响产品的质量;另一方面,也会导致焦炭中的硫、氮含量较高,在催化剂烧焦过程中会产生较多的硫、氮氧化物,腐蚀设备,污染环境。
④催化裂化条件下,重油不能完全气化。
重油在催化裂化条件下只能部分气化,未气化的小液滴会附着在催化剂表面上,此时的传质阻力不能忽略,反应过程是一个复杂的气-液-固三相催化反应过程。
(3) 单体烃的催化裂化反应①烷烃主要发生分解反应,生成较小分子的烷烃和烯烃。
②烯烃除发生分解反应外,还发生异构化、氢转移和芳构化等反应。
③环烷烃可以发生开环反应生成链状烯烃,也可以发生氢转移反应生成芳香烃。
④芳香烃不发生开环反应,只发生断侧链反应,且断裂的位置主要发生在侧链同芳香环连接的键上。
石油加工中的催化裂化工艺
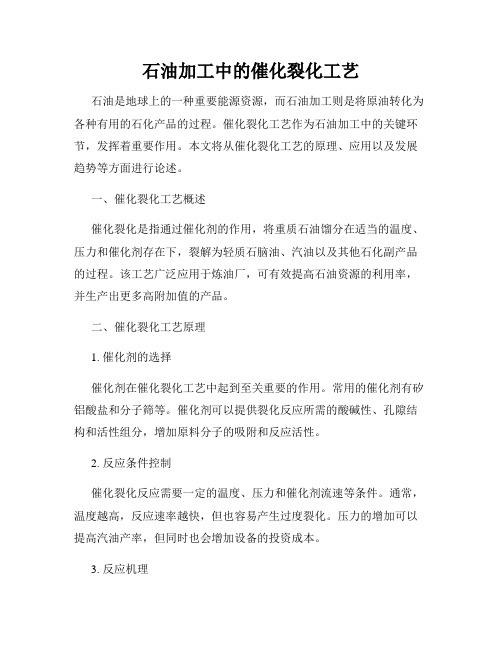
石油加工中的催化裂化工艺石油是地球上的一种重要能源资源,而石油加工则是将原油转化为各种有用的石化产品的过程。
催化裂化工艺作为石油加工中的关键环节,发挥着重要作用。
本文将从催化裂化工艺的原理、应用以及发展趋势等方面进行论述。
一、催化裂化工艺概述催化裂化是指通过催化剂的作用,将重质石油馏分在适当的温度、压力和催化剂存在下,裂解为轻质石脑油、汽油以及其他石化副产品的过程。
该工艺广泛应用于炼油厂,可有效提高石油资源的利用率,并生产出更多高附加值的产品。
二、催化裂化工艺原理1. 催化剂的选择催化剂在催化裂化工艺中起到至关重要的作用。
常用的催化剂有矽铝酸盐和分子筛等。
催化剂可以提供裂化反应所需的酸碱性、孔隙结构和活性组分,增加原料分子的吸附和反应活性。
2. 反应条件控制催化裂化反应需要一定的温度、压力和催化剂流速等条件。
通常,温度越高,反应速率越快,但也容易产生过度裂化。
压力的增加可以提高汽油产率,但同时也会增加设备的投资成本。
3. 反应机理催化裂化反应中,重油组分在催化剂的存在下经历裂解反应,生成轻质石脑油和汽油等产品。
裂化反应主要通过破坏C-C键和C-H键实现,生成碳烯烃、烷烃等中间体,随后通过裂解生成轻质石脑油和汽油等产物。
三、催化裂化工艺应用1. 汽油生产催化裂化工艺主要用于汽油的生产。
通过控制裂化反应的条件和催化剂的选择,可以获得不同辛烷值的汽油产品,使其符合市场需求。
2. 石脑油生产石脑油是一种重要的石化副产品,广泛用于合成橡胶、树脂、溶剂等行业。
催化裂化工艺可以将重质石油馏分经过裂解反应,生成大量的石脑油。
3. 各种石化副产品生产除了汽油和石脑油外,催化裂化工艺还能生产出许多其他石化副产品,如润滑油、石油蜡、煤油等。
这些产品具有广泛的应用领域,满足了人们对不同石化产品的需求。
四、催化裂化工艺发展趋势1. 提高石化产品质量随着社会的进步和环保要求的提高,催化裂化工艺正朝着提高产品质量的方向发展。
- 1、下载文档前请自行甄别文档内容的完整性,平台不提供额外的编辑、内容补充、找答案等附加服务。
- 2、"仅部分预览"的文档,不可在线预览部分如存在完整性等问题,可反馈申请退款(可完整预览的文档不适用该条件!)。
- 3、如文档侵犯您的权益,请联系客服反馈,我们会尽快为您处理(人工客服工作时间:9:00-18:30)。
教案叶蔚君5.1催化裂化的工艺特点及基本原理[引入]:先提问复习,再从我国催化裂化汽油产量所占汽油总量的比例引入本章内容。
[板书]:催化裂化一、概述1、催化裂化的定义、反应原料、反应产物、生产目的[讲述]:1.催化裂化的定义(重质油在酸性催化剂存在下,在470~530O C的温度和0.1~0.3MPa的条件下,发生一系列化学反应,转化成气体、汽油、柴油等轻质产品和焦炭的过程。
)、反应原料:重质油;(轻质油、气体和焦炭)、(轻质油);[板书]2.催化裂化在炼油厂申的地位和作用:[讲述]以汽油为例,据1988年统计,全世界每年汽油总消费量约为6.5亿吨以上,我国汽油总产量为1750万吨,从质量上看,目前各国普通级汽油一般为90-92RON、优质汽油为96-98RON,我国1988年颁布车用汽油指标有两个牌号,其研究法辛烷值分别为不低于90和97。
但是,轻质油品的来源只靠直接从原油中蒸馏取得是远远不够的。
一般原油经常减压蒸馏所提供的汽油、煤油和柴油等轻质油品仅有10-40%,如果要得到更多的轻质产品以解决供需矛盾,就必须对其余的生质馏分以及残渣油进行二次加工。
而且,直馏汽油的辛烷值太低,一般只有40-60MON,必须与二次加工汽油调合使用。
国内外常用的二次加工手段主要有热裂化、焦化、催化裂化和加氢裂化等。
而热裂化由于技术落后很少发展,而且正逐渐被淘汰,焦化只适用于加工减压渣油,加氢裂化虽然技术上先进、产品收率高、质量好、灵活性大,但设备复杂,而且需大量氢气,因此,技术经济上受到一定限制,所以,使得催化裂化在石油的二次加工过程中占居着重要地位(在各个主要二次加工工艺中居于首位)。
特别是在我国,车用汽油的组成最主要的是催化裂化汽油,约占近80%。
因此,要改善汽油质量提高辛烷值,首先需要把催化裂化汽油辛烷值提上去。
目前我国催化裂化汽油辛烷值RON偏低,必须采取措施改进工艺操作,提高催化剂质量,迅速赶上国际先进水平。
[板书]3催化裂化过程具有以下几个特点[讲述](1)轻质油收率高,可达70%-80%,而原料初馏的轻质油收率仅为10%~40%。
所说轻质油是指汽抽、煤油和柴油的总和。
(2)催化汽油的辛烷值较高,研究法辛烷值可达85以上。
汽油的安定性也较好。
(3)催化柴油的十六烷值低,常与直馏柴油调合使用或经加氢精制提高十六烷值。
(4)催化裂化气体产品产率约为10%~20%左右,其中90%左右是C3,C4(称为液化石油气)。
C3、C4组分中合大量烯烃。
因此这部分产品是优良的石油化工原料及生产高辛烷值汽油组分的原料。
气体产率为10%~20%,汽油产率为30%-50%,柴油产率不超过40%,焦炭产率在5%~7%左右。
催化裂化过程的主要目的是生产汽油,根据我国国情,交通运输和农业的发展,对柴油的需求量很大,通过调整操作条件或采用新的工艺技术,可在生产汽油的同时,尽可能提高柴抽的产率,这也是我国催化裂化技术的一大特点。
[板书]4.催化裂化的发展概况5.催化裂化的发展方向:[讲述]:继续改进工艺、设备、催化剂技术,尽可能多地转化劣质重油;提高轻质产品收率。
对我国而言,特别要在保证长周期运转上下功夫。
继续研究开发多产低碳烯烃的工艺,为发展石油化工和清洁燃料组分的生产提供原料。
利用其反应机理,继续研究开发能满足市场产品需求的催化裂化工艺和催化剂。
为清洁生产,研究开发减少排放的工艺、催化剂、添加剂以及排放物的无害化处理。
同步发展催化裂化与其它工艺的组合优化。
过程模拟和计算机应用。
新催化材料的开发和应用。
[引入]催化裂化汽油原料和产品[板书]二、催化裂化的原料和产品1、原料:馏分油、渣油[讲述]馏分油(直馏重馏分油/直馏减压馏分油VGO馏程是350~500o C、热加工产物——焦化蜡油/减粘裂化馏出油、润滑油溶剂精制的抽出油)、渣油(减压渣油、脱沥青的减压渣油、加氢处理重油等,常掺入到减压馏分油中进行加工,当减压馏分油中掺入渣油时则通称为RFCC)。
评价指标:馏分组成、烃类族组成、残炭、含硫含氮化合物、金属等。
[板书]2、产品:气体、液体产物、焦炭[讲述]气体(干气、液化气)、液体产物(汽油、柴油、重柴油/回炼油、油浆/澄清油)、焦炭。
[引入]催化裂化原料是如何进行反应而得到产品的?[板书]三、烃类的催化裂化反应[小结]:一、烃类的催化裂化基本反应:(一)烷烃(以分解反应为主);(二)烯烃(分解反应、异构化反应——骨架异构/双键位移异构/几何结构、氢转移反应、芳构化反应——脱氢);(三)环烷烃(分解、氢转移、异构化);(四)芳香烃(烷基侧链断裂、脱氢、焦化)[提问]:为什么催化的汽油辛烷值高,而柴油的十六烷值低呢?[回答]要点:从裂化可能进行的化学反应上看,可知异构成分、芳香烃较多,而正构烷烃少)再把辛烷值、十六烷值的概念重新复习一遍。
[板书]二、石油馏分的催化裂化反应机理各种烃类之间的竞争吸附和对反应的阻滞作用、复杂的平行-顺序反应。
不同烃类分子在催化剂表面上的吸附能力不同,其顺序如下: 稠环芳烃>稠环环烷烃>烯烃>单烷塞单环芳烃>单环环烷烃>烷烃同类分子,相对分予质量越大越容易被吸附。
按烃类化学反应速度顺序排列,大致如下:烯烃>大分子荜烷基侧链的单环芳烃>异构烷烃和环烷烃>小分子单烷基侧链的单环芳烃>正构烷烃>稠环芳烃[讨论]催化裂化的理想原料是什么?为什么?讨论结束请学生回答问题[小结]环烷烃有一定的吸附能力,又具适宜的反应速度,因此可以认为,富含环烃的石油馏分应是催化裂化的理想原料[引入]催化裂化反应的催化剂结构和组成如何?应该在使用中注意些什么? [板书]四、催化裂化催化剂1、裂化催化剂的种类(无定形硅酸铝、分子筛系列)、组成(活性中心Al2O3,Si02、其他添加剂)和结构(八面沸石笼);[板书]2.裂化催化剂的使用性质:活性、选择性、稳定性抗重金属污染性质。
[讲述]活性、选择性、稳定性抗重金属污染性质对催化剂的影响。
[板书]3.工业用分子筛裂化催化剂的种类:4.裂化催化剂的失活与再生:[讲述]失活原因(水热失活、结焦失活、中毒失活)、裂化催化剂的再生(主要是烧焦)再生操作的主要影响因素(T、氧分压、再生剂含碳量、再生器的结构形式、再生时间)[归纳、提问、总结]以提问的方式梳理本次课的内容5.2催化裂化工业装置(工艺流程)[引入]:先提问复习,再引入提问:催化裂化的工艺流程由哪几个部分组成、主要设备是什么、现有哪些新技术?[板书]5-2催化裂化工业装置(工艺流程)一、生产中几个常用的基本观念(一)转化率和回炼操作[版书并讲解]1转化率:原料转化为产品的百分率。
总转化率=(气体+汽油+焦炭)/(新鲜原料油)x100%[讲述]真正意义的转化率应该是原料油量减去末转化油的量与原料油量之比,称为重油转化率,一般在实验室使用。
[版书]2.回炼操作[讲述]回炼操作又叫循环裂化。
由于新鲜原料经过一次反应后不能都变成要求的产品,还有一部分和原料油馏程相近的中间馏分。
把这部分中间馏分送回反应器重新进行反应就叫回炼操作。
这部分中间馏分油就叫做回炼油(或称循环油)。
如果这部分循环油不去回炼而作为产品送出装置,这种操作叫单程裂化。
[版书并讲解]单程转化率=(气体+汽油+焦炭)/(总进料)x100%=总转化率/(1+回炼化)式中回炼比是回炼油(包括回炼油浆)与新鲜原料质量之比,即: [版书并讲解]回炼比=(回炼油十回炼油浆)/新鲜原料回炼比的大小由原料性质和生产方案决定。
通常,多产汽油方案采用小回炼比,多产柴油方案用大回炼比。
[举例]总转化率、单程转化率的计算[板书](二)空速和反应时间[讲述]在床层流化催化裂化中?常用空速表示原料油与催化剂的接触时间。
其定义是每小时进入反应器的原料油量与反应器内催化剂藏量之比。
其定义是每小时进入反应器的原料油量与反应器内催化剂藏量之比[板书](三)剂油比:剂油比为5~10[讲述]催化剂循环量与总进料量之比称为剂油比,用c/o表示:在同一条件下,剂油比大,表明原料油能与更多的催化剂接触,单位催化剂上的积炭少,催化剂失活程度小,从而使转化率提高。
但剂油比增大会便焦炭产率增加,剂油比太小,增加热裂化反应的比例,使产品质量变差。
高剂油比操作对改善产品分布和产品质量都有利,实际生产中剂油比为5~10[板书](四)反应温度470~520o C[讲述]如前所述,石油馏分的催化裂化反应总体上是强吸热反应,欲便反应过程顺利进行,必须提供热量使之在一定温度条件下进行。
工业生产中石油馏分是在提升管反应器中进行的,由于反应过程申吸收热量和器壁散热,反应器进口和出口的温度是不相同的,进口温度高于出口大约20~30。
C。
所谓反应温度通常是指提升管出口温度,根据所加工的原料和生产方案的不同,反应温度在470~520。
C左右。
通常,原料越重应采用较高的反应温度,处理轻质原料采用较低的反应温度;以多产柴油为目的,应采用较低的反应温度,以生产汽油和液化气为主要目的则应采用较高的反应温度。
[版书]二、催化裂化装置的工艺流程(一)反应—再生系统[投影]高低并列式提升管催化裂化装置反应—再生系统的工艺流程。
[讲述]1.工艺流程新鲜原料(减压馏分油或重油)经过一系列换热后与回炼油混合,进入加热炉预热到200-300的温度,由原料油喷嘴以雾化状态喷入提升管反应器下部,与来自再生器的高温催化剂接触并立即气化,油气与雾化蒸汽及预提升蒸汽一起携带着催化剂以5-8m/s的线速向上流保证催化剂在两器间按正常流向循环以及再生器有良好的流化状况是催化裂化装置的技术关键,除设计时准确无误外,正确操作也非常重要。
2、主要设备的结构和作用特点3、着重于反应-再生的新技术[板书](二)分馏系统[讲述]分馏系统的作用是将反应-再生系统的产物进行初步分离,得到部分产品和半成品。
由反应-再生系统来的高温油气进入催化分馏塔下部,经装有挡板的脱过热段脱过热后进入分馏段,经分馏后得到富气、粗汽油、轻柴油、重柴油、回炼油和油浆。
富气和粗汽油去吸收稳定系统;轻、重柴油经提、换热或冷却后出装置;回炼油返回反应-再生系统进行回炼;油浆的一部分送反应-再生系统回炼,另一部分经换热后循环回分馏塔。
将轻柴油的一部分经冷却后送至再吸收塔作为吸收剂,吸收了C3、C4组分的轻柴油再返回分馏塔。
为了取走分馏塔的过剩热量以使塔内气、液负荷分布均匀,在塔的不同位置分别设有4个循环回流:顶循环回流、一中段回流、二中段回流和油浆循环回流。
[板书]1工艺流程:吸收-稳定系统包括吸收塔、解吸塔、再吸收塔、稳定塔以及相应的冷换设备。
2主要设备的结构和作用特点[板书](三)吸收-稳定系统[板书]工艺流程[讲述]由分馏系统油气分离器出来的富气经气体压缩机升压后,冷却并分出凝缩油,压缩富气进入吸收塔底部,粗汽油和稳定汽油作为吸收剂由塔顶进入,吸收了C3、C4的富吸收油由塔底抽出送至解吸塔顶部。