硅酸盐水泥的制备
简述硅酸盐水泥的凝结硬化过程与特点
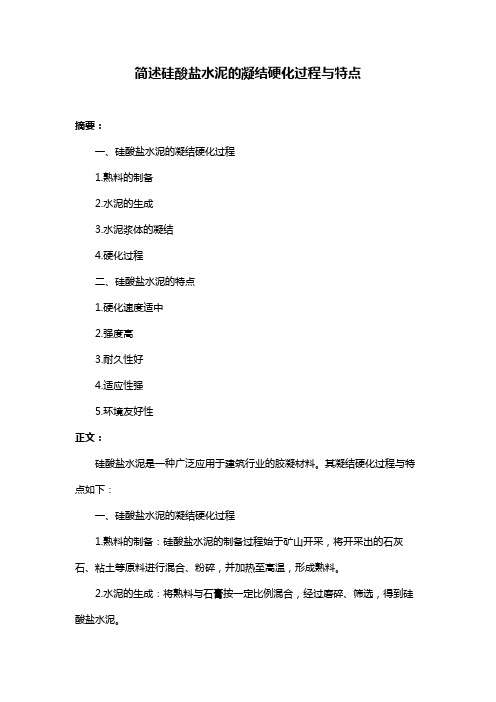
简述硅酸盐水泥的凝结硬化过程与特点摘要:一、硅酸盐水泥的凝结硬化过程1.熟料的制备2.水泥的生成3.水泥浆体的凝结4.硬化过程二、硅酸盐水泥的特点1.硬化速度适中2.强度高3.耐久性好4.适应性强5.环境友好性正文:硅酸盐水泥是一种广泛应用于建筑行业的胶凝材料。
其凝结硬化过程与特点如下:一、硅酸盐水泥的凝结硬化过程1.熟料的制备:硅酸盐水泥的制备过程始于矿山开采,将开采出的石灰石、粘土等原料进行混合、粉碎,并加热至高温,形成熟料。
2.水泥的生成:将熟料与石膏按一定比例混合,经过磨碎、筛选,得到硅酸盐水泥。
3.水泥浆体的凝结:当水泥与水混合时,水泥中的硅酸盐矿物与水发生水化反应,生成具有粘性的水泥浆体。
随着水化反应的进行,浆体逐渐凝结,形成凝胶体。
4.硬化过程:在水泥浆体凝结的基础上,水泥中的硅酸盐矿物不断水化,形成水化硅酸钙(CSH)凝胶。
这种凝胶具有很高的强度和耐久性,随着时间的推移,硬化过程逐渐完成。
二、硅酸盐水泥的特点1.硬化速度适中:硅酸盐水泥的硬化速度适中,有利于施工操作。
在正常条件下,水泥浆体在拌和水后约30分钟开始凝结,12小时内达到一定强度。
2.强度高:硅酸盐水泥具有较高的早期和后期强度,能满足不同工程结构对抗压强度的要求。
3.耐久性好:硅酸盐水泥硬化后,其水化产物具有良好的抗侵蚀性、抗渗透性、抗碳化性,使建筑物具有较好的耐久性。
4.适应性强:硅酸盐水泥在不同环境下均能保持良好的性能,适用于多种工程结构,如混凝土、砂浆等。
5.环境友好性:硅酸盐水泥生产过程中,采用低碳、环保的生产工艺,有利于减少环境污染。
综上所述,硅酸盐水泥以其优良的性能在建筑行业中得到广泛应用。
硅酸盐水泥的生产工艺及发展进展
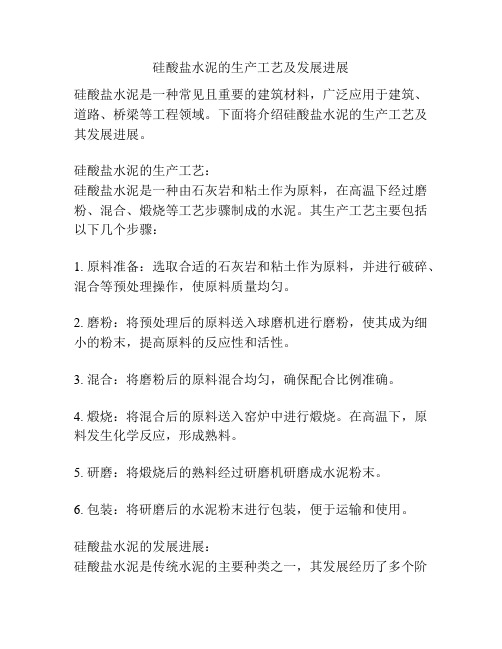
硅酸盐水泥的生产工艺及发展进展硅酸盐水泥是一种常见且重要的建筑材料,广泛应用于建筑、道路、桥梁等工程领域。
下面将介绍硅酸盐水泥的生产工艺及其发展进展。
硅酸盐水泥的生产工艺:硅酸盐水泥是一种由石灰岩和粘土作为原料,在高温下经过磨粉、混合、煅烧等工艺步骤制成的水泥。
其生产工艺主要包括以下几个步骤:1. 原料准备:选取合适的石灰岩和粘土作为原料,并进行破碎、混合等预处理操作,使原料质量均匀。
2. 磨粉:将预处理后的原料送入球磨机进行磨粉,使其成为细小的粉末,提高原料的反应性和活性。
3. 混合:将磨粉后的原料混合均匀,确保配合比例准确。
4. 煅烧:将混合后的原料送入窑炉中进行煅烧。
在高温下,原料发生化学反应,形成熟料。
5. 研磨:将煅烧后的熟料经过研磨机研磨成水泥粉末。
6. 包装:将研磨后的水泥粉末进行包装,便于运输和使用。
硅酸盐水泥的发展进展:硅酸盐水泥是传统水泥的主要种类之一,其发展经历了多个阶段,不断优化改进。
以下是硅酸盐水泥的主要发展进展:1. 早期硅酸盐水泥的发展:早期硅酸盐水泥主要是通过人工磨制,生产效率低且产品质量不稳定。
2. 自动化生产:随着科技的发展,硅酸盐水泥的生产过程逐渐实现了自动化和机械化。
这大大提高了生产效率和产品质量稳定性。
3. 先进的生产工艺:近年来,人们不断探索和改进硅酸盐水泥的生产工艺。
例如,采用新型特种窑炉和高效煅烧工艺,可以降低能耗、减少排放,提高产品质量。
4. 绿色硅酸盐水泥的研发:随着环保意识的增强,人们开始研发绿色环保的硅酸盐水泥。
例如,引入废弃物渣滓作为原料,以减少资源浪费和环境污染。
5. 加入新功能材料:为了满足工程建设的需求,人们不断研发新功能材料的硅酸盐水泥。
例如,加入高强度增强纤维可以提高水泥的抗压强度和耐久性。
总的来说,硅酸盐水泥的生产工艺经历了从传统到现代化的演变,不断实现自动化和绿色环保。
随着科技的发展和需求的变化,硅酸盐水泥的应用和生产工艺还将继续发展和创新。
硅酸盐水泥配料及生料制备

硅酸盐水泥配料及生料制备一、生料及配料的基本概念1 生料1.1 定义:由石灰质原料、粘土质原料、少量校正原料(有时还加入矿化剂、晶种等,立窑生产时还要加煤)按比例配合,粉磨到一定细度的物料。
1.2 分类:生料粉和生料浆两种。
(1)、生料粉:干法生产用的生料。
一般水分≤1%。
据生料中是否含煤又分为三种:白生料:出磨生料中不含煤。
干法回转窑及采用白生料法煅烧的立窑用。
黑生料:出磨生料中含有煅烧所需的全部煤。
采用全黑生料法煅烧的立窑用。
半黑生料:出磨生料中只含有煅烧所需煤的一部分。
采用半黑生料法煅烧的立窑用。
(2)、生料浆:湿法生产所用的生料。
一般含水分32%~40%左右。
2 配料的概念及常用计算式2.1 概念1、定义:根据水泥品种、原燃料品质、工厂具体生产条件等选择合理的熟料矿物组成或率值,并由此计算所用原料及燃料的配合比,称为生料配料,简称配料。
2、配料计算的目的:(1)设计(2)生产3、配料应遵循的基本原则:(1)烧出的熟料具有较高的强度和良好的物理化学性能。
(2)配制的生料易于粉磨和煅烧;(3)生产过程易于控制,便于生产操作管理,尽量简化工艺流程。
并结合工厂生产条件,经济、合理地使用矿山资源。
2,2 配料计算中的常用基准1、干燥基准:用干燥状态物料(不含物理水)作计算基准,简称干基。
如不考虑生产损失,有:各种干原料之和=干生料(白生料)2、灼烧基准:生料经灼烧以后去掉烧失量之后,处于灼烧状态,以灼烧状态作计算基准称为灼烧基准。
如不考虑生产损失,有:灼烧生料+煤灰(掺入熟料中的)=熟料3、湿基准:用含水物料作计算基准时称为湿基准,简称湿基。
4、基准间的转换:(1)干基转灼烧基:式中:A——干基物料成分(%)L——干基物料烧失量(%)(2)干基转湿基:式中:w——物料含水量(%)2,3 熟料热耗与煤耗1、热耗:生产1kg熟料所消耗的热量。
符号q,单位kj/kg;2、煤耗:生产1kg熟料所消耗的煤的质量。
水泥工艺生产硅酸盐水泥的原料及配料计算
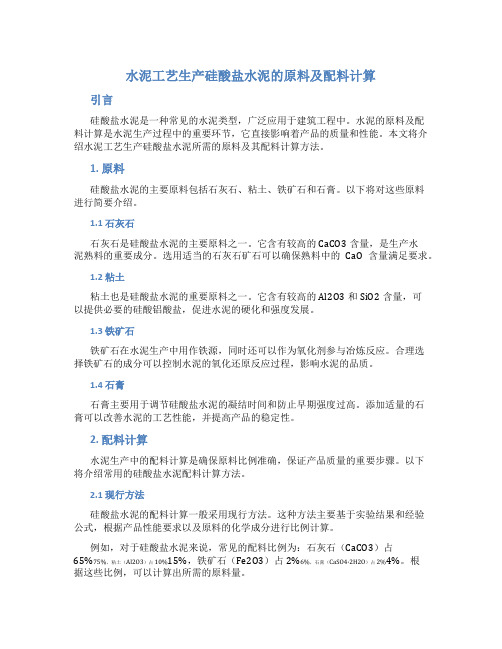
水泥工艺生产硅酸盐水泥的原料及配料计算引言硅酸盐水泥是一种常见的水泥类型,广泛应用于建筑工程中。
水泥的原料及配料计算是水泥生产过程中的重要环节,它直接影响着产品的质量和性能。
本文将介绍水泥工艺生产硅酸盐水泥所需的原料及其配料计算方法。
1. 原料硅酸盐水泥的主要原料包括石灰石、粘土、铁矿石和石膏。
以下将对这些原料进行简要介绍。
1.1 石灰石石灰石是硅酸盐水泥的主要原料之一。
它含有较高的CaCO3含量,是生产水泥熟料的重要成分。
选用适当的石灰石矿石可以确保熟料中的CaO含量满足要求。
1.2 粘土粘土也是硅酸盐水泥的重要原料之一。
它含有较高的Al2O3和SiO2含量,可以提供必要的硅酸铝酸盐,促进水泥的硬化和强度发展。
1.3 铁矿石铁矿石在水泥生产中用作铁源,同时还可以作为氧化剂参与冶炼反应。
合理选择铁矿石的成分可以控制水泥的氧化还原反应过程,影响水泥的品质。
1.4 石膏石膏主要用于调节硅酸盐水泥的凝结时间和防止早期强度过高。
添加适量的石膏可以改善水泥的工艺性能,并提高产品的稳定性。
2. 配料计算水泥生产中的配料计算是确保原料比例准确,保证产品质量的重要步骤。
以下将介绍常用的硅酸盐水泥配料计算方法。
2.1 现行方法硅酸盐水泥的配料计算一般采用现行方法。
这种方法主要基于实验结果和经验公式,根据产品性能要求以及原料的化学成分进行比例计算。
例如,对于硅酸盐水泥来说,常见的配料比例为:石灰石(CaCO3)占65%75%,粘土(Al2O3)占10%15%,铁矿石(Fe2O3)占2%6%,石膏(CaSO4·2H2O)占2%4%。
根据这些比例,可以计算出所需的原料量。
在配料计算中,还需要考虑原料的含水率、季节变化等因素,以确保配料的准确性和稳定性。
2.2 计算示例假设要生产1000吨硅酸盐水泥,按照常见的配料比例:石灰石65%、粘土10%、铁矿石4%、石膏4%计算。
首先,计算石灰石的用量:石灰石用量 = 1000吨 * 65% = 650吨然后,计算粘土的用量:粘土用量 = 1000吨 * 10% = 100吨接下来,计算铁矿石的用量:铁矿石用量 = 1000吨 * 4% = 40吨最后,计算石膏的用量:石膏用量 = 1000吨 * 4% = 40吨3. 结论水泥工艺生产硅酸盐水泥的原料及配料计算是保证产品质量的关键环节。
第三节 硅酸盐水泥的生产工艺

(5) 液相的形成与熟料的烧结 液相的形成(1250~1280℃)
液相的组成:由氧化铁、氧化铝、氧化 钙、氧化镁和碱及其他组分 最低共熔温度:物料在加热过程中,两种或两种以上组分 开始出现液相的温度称为最低共熔温度。
其大小与组分的性质与数目有关。
液相量:液相量与组分的性质、含量、温度等因素 有关(一般为20~30%) 。液相多形成C3S容 易,但过多,会造成转窑内结圈,立窑内 结炉瘤等。
(1) 使熟料中的C3S和C2S呈介稳态存在,减少C3S分解, 防止β-C2S向γ-C2S转化而降低水硬活性,提高熟 料质量;防止MgO晶体长大,有利于水泥安定性 ;急冷熟料晶粒小,活性高;C3A主要呈玻璃体, 抗硫酸盐性能提高; (2) 改善熟料的易磨性; (3)回收熟料带走的热量,预热二次空气,提高窑的热 效率; (4)便于熟料运输、贮存与粉磨。
破碎:就是依靠外力(主要是机械力),克服固体物料内 聚力,将大块物料变成小块物料的过程。 破碎的方法: a)压碎 b)磨碎 c) 劈碎 d) 折碎 e)冲击破碎
根据破碎后物料粒度的大小,将破碎分为粗碎、
中碎和细碎三种。
入料粒度(mm) 粗碎 中碎 300 ~ 900 100 ~ 350 出料粒度(mm) 100 ~ 350 20 ~ 100
应能充分进行,必须使烧成带有一定的高度,还要 将煤的粒度、鼓风压力和通风情况加以综合考虑。 但是机立窑中料球如果在烧成带停留时间过长,易 产生过烧,引起结大块、炼边、甚至架窑,反而影 响产质量,增加不必要的能耗。 过短,将漏生。
(3) 冷却带 该带物料温度低于1300℃。在该带中,高温 熟料与从窑下鼓入的冷空气进行热交换,空气被 加热后进入烧成带供燃料燃烧之用。
C-S-A-F四元系统,不同温度下,液相的计算公式:
硅酸盐水泥生产工艺流程

硅酸盐水泥生产工艺流程水泥生产原料及配料、硅酸盐水泥熟料的矿物组成、硅酸盐水泥生产工艺流程、硅酸盐水泥生产的原料水泥生产原料及配料:生产硅酸盐水泥的主要原料为石灰原料和粘土质原料,有时还要根据燃料品质和水泥品种,掺加校正原料以补充某些成分的不足,还可以利用工业废渣作为水泥的原料或混合材料进行生产。
ﻫ1、石灰石原料石灰质原料是指以碳酸钙为主要成分的石灰石、泥灰岩、白垩和贝壳等。
石灰石是水泥生产的主要原料,每生产一吨熟料大约需要1.3吨石灰石,生料中80%以上是石灰石。
ﻫ2、黏土质原料黏土质原料主要提供水泥熟料中的、、及少量的。
天然黏土质原料有黄土、黏土、页岩、粉砂岩及河泥等。
其中黄土和黏土用得最多。
此外,还有粉煤灰、煤矸石等工业废渣。
黏土质为细分散的沉积岩,由不同矿物组成,如高岭土、蒙脱石、水云母及其它水化铝硅酸盐。
3、校正原料当石灰质原料和黏土质原料配合所得生料成分不能满足配料方案要求时(有的含量不足,有的和含量不足)必须根据所缺少的组分,掺加相应的校正原料(1)硅质校正原料含80%以上ﻫ(2)铝质校正原料含30%以上ﻫ(3)铁质校正原料含 50%以上硅酸盐水泥熟料的矿物组成:硅酸盐水泥熟料的矿物主要由硅酸三钙()、硅酸二钙( )、铝酸三钙( )和铁铝酸四钙( )组成。
硅酸盐水泥生产工艺流程:1、破碎及预均化(1)破碎水泥生产过程中,大部分原料要进行破碎,如石灰石、黏土、铁矿石及煤等。
石灰石是生产水泥用量最大的原料,开采后的粒度较大,硬度较高,因此石灰石是生产水泥用量最大的原料,开采后的粒度较大,硬度较高,因此石灰石的破碎在水泥厂的物料破碎中占有比较重要的地位。
ﻫ破碎过程要比粉磨过程经济而方便,合理选用破碎设备和和粉磨设备非常重要。
在物料进入粉磨设备之前,尽可能将大块物料破碎至细小、均匀的粒度,以减轻粉磨设备的负荷,提高黂机的产量。
物料破碎后,可减少在运输和贮存过程中不同粒度物料的分离现象,有得于制得成分均匀的生料,提高配料的准确性。
第四节硅酸盐水泥的生料制备

炉渣、煤矸石、矾土
Al2O3>30%
11
一、水泥生产的主要原料
4、低品位原料和工业废渣的利用 低品位原料:指那些化学成分、杂质含量 与物理性能等不符合一般水泥生产要求的
原料。如:低品位石灰质原料。
工业废渣:主要指煤矸石、石煤、粉煤灰、
炉渣等。
12
一、水泥生产的主要原料
4、低品位原料和工业废渣的利用
19
破碎类型
允许物料含 水泥厂常用破碎设备一览表 水(%) 破碎原理 破碎比 i
适宜破碎的物料
颚式、旋转式、 颚旋式破碎机 细碎颚式破碎机
挤压 挤压
3~ 6 8 ~10 10 ~15(双转 子30 ~40 ) 10 ~40 10 ~20 10 ~30 50 ~200
<10 <10
石灰石、熟料、石膏 石灰石、熟料、石膏
25
三、原料破碎与烘干、输送与储存
2、烘干
烘干方法
单独烘干 烘干兼粉磨 回转烘干机
烘干设备
悬浮烘干机
流态化烘干机
立式烘干塔
26
三、原料破碎与烘干、输送与储存
2、烘干 ◇单独烘干系统:回转烘干机
27
三、原料破碎与烘干、输送与储存
2、烘干 ◇单独烘干系统:逆流式烘干机
28
三、原料破碎与烘干、输送与储存
天然低品位矿物 煤矿生产废渣 低碳煤 乙炔生产废渣 煤粉燃烧后粉状灰烬
CaO
石 煤 煤矸石 电石渣 粉煤灰
以SiO2、Al2O3 为主,少量 Fe2O3、 CaO Ca(OH)2 以SiO2、 Al2O3为主
炉渣
锅炉煤灰渣
一、水泥生产的主要原料
4、低品位原料和工业废渣的利用
名 称 玄武岩 矿物特征 一种分布较广的 火成岩 化学成分 类似粘土,但Fe2O3、 R2O偏高 应用 代替粘土质 原料
硅酸盐水泥生产工艺

硅酸盐水泥生产工艺水泥生产工艺要点:两磨一煅烧一、硅酸盐水泥生产方法分类立窑生产工艺过程硅酸盐水泥生产的原料1.硅酸盐水泥的主要成分硅酸三钙(3CaO·SiO2)、硅酸二钙(2CaO·SiO2)、铝酸三钙(3CaO·AI2O3)、铁铝酸四钙(4CaO·AI2O3·Fe2O3)其中:CaO 62~67%;SiO220~24%;AI2O34~7%;Fe2O32~6%。
2.硅酸盐水泥生产的主要原料(1)石灰质原料:以碳酸钙为主要成分的原料,是水泥熟料中CaO的主要来源。
如石灰石、白垩、石灰质泥灰岩、贝壳等。
一吨熟料约需1.4~1.5吨石灰质干原料,在生料中约占80%左右。
石灰质原料的质量要求(2)粘土质原料:含碱和碱土的铝硅酸盐,主要成分为SiO2,其次为AI2O3,少量Fe2O3,是水泥熟料中SiO2、AI2O3、Fe2O3的主要来源。
粘土质原料主要有黄土、粘土、页岩、泥岩、粉砂岩及河泥等。
一吨熟料约需0.3~0.4吨粘土质原料,在生料中约占11~17%。
一般情况下SiO2含量60~67%,AI2O3含量14~18%。
(3)主要原料中的有害成分①MgO:影响水泥的安定性。
水泥熟料中要求MgO<5%,原料中要求MgO<3%。
②碱含量(K2O、Na2O):对正常生产和熟料质量有不利影响。
水泥熟料中要求R2O<1.3%,原料中要求R2O<4%。
③P2O5:水泥熟料中含少量的P2O5对水泥的水化和硬化有益。
当水泥熟料中P2O5含量在0.3%时,效果最好,但超过1%时,熟料强度便显著下降。
P2O5含量应限制。
④TiO2:水泥熟料中含有适量的TiO2,对水泥的硬化过程有强化作用。
当TiO2含量达0.5~1.0%,强化作用最显著,超过3%时,水泥强度就要降低。
如果含量继续增加,水泥就会溃裂。
因此在石灰石原料中应控制TiO2<2.0%。
3. 硅酸盐水泥生产的辅助原料(1)校正原料①铁质校正原料:补充生料中Fe2O3的不足,主要为硫铁矿渣和铅矿渣等。
一种高抗蚀硅酸盐水泥的制备方法[发明专利]
![一种高抗蚀硅酸盐水泥的制备方法[发明专利]](https://img.taocdn.com/s3/m/23532c6283d049649a66582f.png)
专利名称:一种高抗蚀硅酸盐水泥的制备方法
专利类型:发明专利
发明人:陈敬,马树立,王九龙,张宇,王营和,王玉和,王海雨,李竹勤
申请号:CN201910976318.6
申请日:20191015
公开号:CN110818290A
公开日:
20200221
专利内容由知识产权出版社提供
摘要:本发明提供一种高抗蚀硅酸盐水泥的制备方法,属于无机材料技术领域,将硅酸盐水泥熟料、粉煤灰、胶凝材料、石膏经单独研磨后混合或共同混合后研磨,获得高抗蚀硅酸盐水泥,其中,所用硅酸盐水泥熟料的制备方法为:将粘土质原料、钙质原材料和铁质原料烘干,混合,研磨,获得生料;烧结生料和矿化剂,冷却,获得硅酸盐水泥熟料;其中,在烧结之前或烧结过程中将包含珍珠岩和三氧化二锑的矿化剂加入到生料粉末中。
本发明硅酸盐水泥熟料的制备方法能够提高硅酸盐水泥熟料的易烧性,增加熟料的结晶度,改善熟料在不同龄期的抗折和抗压强度;本发明制得的高抗蚀硅酸盐水泥具有良好的工作性能、较高的抗压强度和较高的抗侵蚀性能,耐久性能良好。
申请人:大同冀东水泥有限责任公司
地址:037000 山西省大同市口泉新东街
国籍:CN
代理机构:北京睿博行远知识产权代理有限公司
代理人:龚家骅
更多信息请下载全文后查看。
- 1、下载文档前请自行甄别文档内容的完整性,平台不提供额外的编辑、内容补充、找答案等附加服务。
- 2、"仅部分预览"的文档,不可在线预览部分如存在完整性等问题,可反馈申请退款(可完整预览的文档不适用该条件!)。
- 3、如文档侵犯您的权益,请联系客服反馈,我们会尽快为您处理(人工客服工作时间:9:00-18:30)。
硅酸盐水泥的制备1概述水泥是指加水拌和成塑性浆体后,能胶结砂、石等适当材料并能在空气和水中硬化的粉状水硬性胶凝材料。
水泥品种繁多,按其主要水硬性物质,可分为硅酸盐水泥、铝酸盐水泥、硫铝酸盐水泥、铁铝酸盐水泥等系列,其中以硅酸盐系列水泥生产量最大,应用最为广泛。
按其性能和用途不同,又可分为通用水泥、专用水泥和特性水泥三大类。
由硅酸盐水泥熟料、0~5%石灰石或粒化高炉矿渣、适量石膏磨细制成的水硬性胶凝材料,称为硅酸盐水泥。
硅酸盐水泥分两种类型,不掺加混合材料的称I型硅酸盐水泥,其代号为P⋅I。
在硅酸盐水泥熟料粉磨时掺加不超过水泥质量5%石灰石或粒化高炉矿渣混合材料的称∏型硅酸盐水泥,其代号为P⋅∏。
2硅酸盐水泥生产原燃料及配料生产硅酸盐水泥的主要原料为石灰原料和粘土质原料,有时还要根据燃料品质和水泥品种,掺加校正原料以补充某些成分的不足,还可以利用工业废渣作为水泥的原料或混合材料进行生产。
(1)石灰石原料石灰质原料是指以碳酸钙为主要成分的石灰石、泥灰岩、白垩和贝壳等。
石灰石是水泥生产的主要原料,每生产一吨熟料大约需要1.3吨石灰石,生料中80%以上是石灰石。
(2)黏土质原料黏土质原料主要提供水泥熟料中的SiO2、Al2O3、及少量的Fe2O3。
天然黏土质原料有黄土、黏土、页岩、粉砂岩及河泥等。
其中黄土和黏土用得最多。
此外,还有粉煤灰、煤矸石等工业废渣。
黏土质为细分散的沉积岩,由不同矿物组成,如高岭土、蒙脱石、水云母及其它水化铝硅酸盐。
(3)校正原料当石灰质原料和黏土质原料配合所得生料成分不能满足配料方案要求时(有的SiO2含量不足,有的Al2O3和Fe2O3含量不足)必须根据所缺少的组分,掺加相应的校正原料,校正原料有以下三种:(a)硅质校正原料含SiO280%以上(b)铝质校正原料含Al2O330%以上(c)铁质校正原料含Fe2O350%以上3硅酸盐类水泥的生产3.1硅酸盐水泥的生产过程硅酸盐水泥的生产过程就是“两磨一烧”。
第一步,将原料按一定比例配料并磨细得到生料;第二步,将生料煅烧使之部分熔融,冷却后形成熟料;第三步,将熟料与适量的石膏、混合材料共同磨细即为硅酸盐水泥。
其主要生产过程如下:3.1.1破碎及预均化(1)破碎水泥生产过程中,大部分原料要进行破碎,如石灰石、黏土、铁矿石及煤等。
石灰石是生产水泥用量最大的原料,开采后的粒度较大,硬度较高,因此石灰石是生产水泥用量最大的原料,开采后的粒度较大,硬度较高,因此石灰石的破碎在水泥厂的物料破碎中占有比较重要的地位。
破碎过程要比粉磨过程经济而方便,合理选用破碎设备和和粉磨设备非常重要。
在物料进入粉磨设备之前,尽可能将大块物料破碎至细小、均匀的粒度,以减轻粉磨设备的负荷,提高磨机的产量。
物料破碎后,可减少在运输和贮存过程中不同粒度物料的分离现象,有得于制得成分均匀的生料,提高配料的准确性。
(2)原料预均化预均化技术就是在原料的存、取过程中,运用科学的堆取料技术,实现原料的初步均化,使原料堆场同时具备贮存与均化的功能。
原料预均化的基本原理就是在物料堆放时,由堆料机把进来的原料连续地按一定的方式堆成尽可能多的相互平行、上下重叠和相同厚度的料层。
取料时,在垂直于料层的方向,尽可能同时切取所有料层,依次切取,直到取完,即“平铺直取”。
意义:(1)均化原料成分,减少质量波动,以利于生产质量更高的熟料,并稳定烧成系统的生产。
(2)扩大矿山资源的利用,提高开采效率,最大限度扩大矿山的覆盖物和夹层,在矿山开采的过程中不出或少出废石。
(3)可以放宽矿山开采的质量和要求,降低矿山的开采成本。
(4)对黏湿物料适应性强。
(5)为工厂提供长期稳定的原料,也可以在堆场内对不同组分的原料进行配料,使其成为预配料堆场,为稳定生产和提高设备运转率创造条件。
(6)自动化程度高。
3.1.2生料制备水泥生产过程中,每生产1吨硅酸盐水泥至少要粉磨3吨物料(包括各种原料、燃料、熟料、混合料、石膏),据统计,干法水泥生产线粉磨作业需要消耗的动力约占全厂动力的60%以上,其中生料粉磨占30%以上,煤磨占约3%,水泥粉磨约占40%。
因此,合理选择粉磨设备和工艺流程,优化工艺参数,正确操作,控制作业制度,对保证产品质量、降低能耗具有重大意义。
3.1.3生料均化新型干法水泥生产过程中,稳定入窖生料成分是稳定熟料烧成热工制度的前提,生料均化系统起着稳定入窖生料成分的最后一道把关作用。
采用空气搅拌,重力作用,产生“漏斗效应”,使生料粉在向下卸落时,尽量切割多层料面,充分混合。
利用不同的流化空气,使库内平行料面发生大小不同的流化膨胀作用,有的区域卸料,有的区域流化,从而使库内料面产生倾斜,进行径向混合均化。
3.1.4预热分解把生料的预热和部分分解由预热器来完成,代替回转窑部分功能,达到缩短回窑长度,同时使窑内以堆积状态进行气料换热过程,移到预热器内在悬浮状态下进行,使生料能够同窑内排出的炽热气体充分混合,增大了气料接触面积,传热速度快,热交换效率高,达到提高窑系统生产效率、降低熟料烧成热耗的目的。
预热器的主要功能是充分利用回转窑和分解炉排出的废气余热加热生料,使生料预热及部分碳酸盐分解。
为了最大限度提高气固间的换热效率,实现整个煅烧系统的优质、高产、低消耗,必需具备气固分散均匀、换热迅速和高效分离三个功能。
3.1.4水泥熟料的烧成生料在旋风预热器中完成预热和预分解后,下一道工序是进入回转窑中进行熟料的烧成。
在回转窑中碳酸盐进一步的迅速分解并发生一系列的固相反应,生成水泥熟料中的C3A、C4AF、C2S等矿物。
随着物料温度升高近1300℃时,C3A、C4AF、C2S等矿物会变成液相,溶解于液相中的C2S和CaO进行反应生成大量C3S(熟料)。
熟料烧成后,温度开始降低。
最后由水泥熟料冷却机将回转窑卸出的高温熟料冷却到下游输送、贮存库和水泥磨所能承受的温度,同时回收高温熟料的显热,提高系统的热效率和熟料质量。
5、水泥粉磨水泥粉磨是水泥制造的最后工序,也是耗电最多的工序。
其主要功能在于将水泥熟料(及胶凝剂、性能调节材料等)粉磨至适宜的粒度(以细度、比表面积等表示),形成一定的颗粒级配,增大其水化面积,加速水化速度,满足水泥浆体凝结、硬化要求。
3.2水泥熟料的形成过程硅酸盐水泥熟料的矿物组成主要为:硅酸三钙3CaO·SiO2(C3S)(37~60%),硅酸二钙2CaO·SiO2(C2S)(15~37%),铝酸三钙3CaO·Al2O3(C3A)(7~15%),铁铝酸四钙4CaO·Al2O3·Fe2O3(C4AF)(10~18%)。
除四种主要成分外,水泥中尚含有少量游离CaO、MgO、SO3、及碱(K2O、Na2O)这些均为有害成分,国家标准中有严格限止。
3.2.1水分蒸发在入窑生料中都含有一定量的水分,干法窑生料含水分一般不超过1%,立窑和立波尔窑生料约含水分12%~15%,湿法窑的料浆水分通常为30%~40%,生料入窑后,物料温度逐渐升高,当温度升高到100~150℃时,生料中水分全部被排除,这一过程称为干燥过程。
每1kg水分蒸发潜热高达2257kJ(100℃),因而湿法生产料浆的水分为35%左右时,每生产1kg熟料用于蒸发水分的热量高达2100kJ,占总热耗的35%以上,因而降低料浆水分或过滤成料块,可以降低熟料热耗,增加窑的产量。
3.2.1粘土矿物脱水粘土矿物的化合水有两种,一种以OH-离子状态存在于晶体结构中,称为晶体配位水;一种以水分子状态吸附在晶层结构间,称为晶层间水或层间吸附水。
伊利石的层间水因风化程度而异,层间水在100℃左右即可脱去,而配位水则必须高达400~600℃才能脱去。
生料干燥后,继续被加热,温度上升较快,当温度升到500℃时,粘土中的主要组成矿物高岭土发生脱水分解反应,其反应式为A12O3·2SiO2·2H2O→A12O3·2SiO2+2H2O高岭土进行脱水分解反应时,在失去化学结合水的同时,本身晶体结构也受到破坏,生成无定形偏高岭土。
因此,高岭土脱水后的活性较高,当继续加热到970~1050℃时,由无定形物质转换成晶体莫来石,同时放出热量。
蒙脱石和伊利石脱水后,仍然具有晶体结构,因而它们的活性较高岭土差。
伊利石脱水时还伴随有体积膨胀,而高岭土和蒙脱石则是体积收缩,所以立窑和立波尔窑生产时,不宜采用以伊利石为主导矿物的粘土,否则料球的热稳定性差,入窑后会引起炸裂、严重影响窑内通风。
粘土矿物脱水分解反应是个吸热过程,每1kg高岭土在450℃时吸热为934kJ,但因粘土质原料在配合料中的含量较少,所以其吸热反应不显著。
3.2.3碳酸盆分解脱水后的物料,温度继续升至600℃左右时,生料中的碳酸盐开始分解,主要是石灰石中的碳酸钙和原料中夹杂的碳酸镁进行分解,其反应如下:MgCO3==MgO+CO2CaCO3==CaO+CO21.碳酸盐分解反应的特点(1)可逆反应。
受系统温度和周围介质中CO2的分压影响较大,在CaCO3的分解反应中,CO2分压、CO2浓度和分解温度之间存在着一定关系,如CO2分压和温度处于平衡状态,使反应向正向或逆向进行,所以为了使分解顺利进行,必须保持较高的反应温度,降低周围介质中CO2分压或减少CO2浓度。
(2)强吸热反应。
碳酸盐分解时,需要吸取大量的热量,是熟料形成过程中消耗热量最多的一个工艺过程,每1kg纯碳酸钙在200℃时分解吸热为1767kJ,900℃时为1658kJ,可用下式计算生成每1kg熟料时用于CaCO3分解所需的热量Q:Q=KABq式中:K—干生料消耗定额(Kg/Kg熟料),取1.5kg/kg熟料;A-配合料中石灰石含量(%),取85%;B-石灰石中CaCO3的含量(%),取95%;q-纯CaCO3,900℃时分解吸热,为1658kJ/kg。
则Q=1.5×85%×95%×1658=2008kJ/kg熟料由计算可知,碳酸钙分解所需热量约占湿法生产总热耗的1/3,约占悬浮预热预分器或预分解窑的1/2,因此,为保证碳酸钙分解反应能完全地进行,必须供给足够的热量。
(3)反应的起始温度较低,约在600℃时就有CaCO3进行分解反应,但速度非常缓慢,至894℃时,分解放出的CO2分压达0.1MPa,分解速度加快,1100~1200℃时,分解速度极为迅速,由试验可知,温度每增加50℃,分解速度常数约增加1倍,分解时间约缩短50%。
2.碳酸钙的分解过程碳酸钙的分解有以下五个过程:二个传热过程——热气流向颗粒表面传热,热量以传导方式由表面向分解面的传热过程。
一个化学反应过程——分解面上CaCO3分解并放出CO2。