轮子及其气压棒的检验标准
工器具检验检查标准

1次/ 半年
序 号
工器 具名 称
工器 具类 别
基本要求
检验/检查标准
周期
备注
6。安全帽的颜色、10go标记要统 一规定,以区别其它单位。
7。不得在安全帽内再佩戴其他帽 子。
璃钢帽W3。5年)。
2
安全
+H-市
安全 用具
1.必须使用有效期内合格的安全
3.不可使用有破损的绝缘靴.
1。产品标识及定期检验合格标识 应清晰齐全。
2。靴底的防滑花纹磨损应不超过50%,不能磨透露出绝缘层。
3。绝缘靴整体各处应无裂纹、无 漏洞、无气泡、无灼伤、无划痕等 损伤。
1次/ 半年
序 号
工器 具名 称
工器 具类 别
基本要求
检 身内.
工器 具类 别
基本要求
检验/检查标准
周期
备注
能将挂钩直接勾在安全绳上,应勾 在安全带的挂环上。
7。安全带严禁打结使用,使用中要 避开尖锐的构件。
4。金属酉己件表面应光洁、无裂纹、 无严重锈蚀和目测可见的变形,配 件边缘应呈圆弧形.
5。金属卡环(钩)必须有保险装置, 且操作要灵活。
6.钩体和钩舌的咬□必须完整,两 者不得偏斜。
1次/ 半年
序 号
工器 具名 称
工器 具类 别
基本要求
检验/检查标准
周期
备注
5。防坠器规格长度有3m、5m、10m、15m、20m、30m等,应根 据现场情况正确选用.
5.防坠器吊绳应无断股、无霉变、 无磨损。
6.防坠器壳体应无变形、无裂纹、 无缺损.
7.金属卡钩必须有保险装置,且操 作灵活.
国家轮胎耐磨检测标准

国家轮胎耐磨检测标准
本标准规定了轮胎耐磨性能的检测方法和技术要求。
适用于各类轮胎产品的耐磨性能检测。
1.轮胎规格与结构检测
检测轮胎的规格尺寸、结构类型、胎面花纹深度等参数,以确保符合设计要求。
2.材料质量检测
对轮胎的主要材料进行质量检测,包括橡胶、纤维和钢丝等材料的质量和性能,以确保其符合设计要求。
3.轮胎耐磨性能检测
通过在标准条件下进行磨耗试验,检测轮胎的耐磨性能。
磨耗试验包括干磨试验、湿磨试验和滑磨试验等。
4.耐久性能检测
通过模拟实际使用条件下的耐久性试验,检测轮胎的耐久性能。
试验包括高速耐久试验、恶劣路况耐久试验等。
5.抗疲劳性能检测
通过疲劳试验检测轮胎的抗疲劳性能,以评估轮胎在使用过程中的疲劳寿命。
6.抗湿滑性能检测
通过湿滑试验检测轮胎的抗滑性能,以评估轮胎在雨天或潮湿路面的抓地力。
7.抗静电性能检测
通过静电试验检测轮胎的抗静电性能,以评估轮胎在使用过程中的安全性能。
8.轮胎气压与充气压力检测
检测轮胎的气压和充气压力,以确保符合设计要求,保证轮胎的正常使用。
9.轮胎滚动阻力检测
通过滚动阻力试验检测轮胎的滚动阻力,以评估轮胎在使用过程中的燃油经济性。
10.轮胎生热性能检测
通过生热试验检测轮胎在使用过程中的生热性能,以评估轮胎的安全性能和使用寿命。
轮胎检测方案
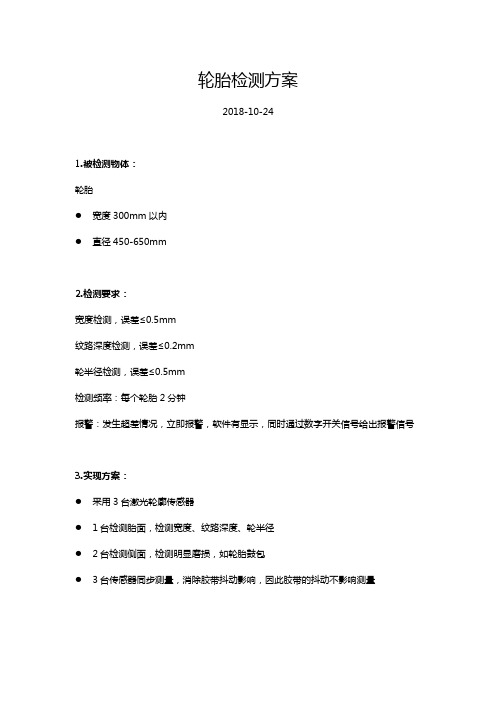
轮胎检测方案
2018-10-24
1.被检测物体:
轮胎
●宽度300mm以内
●直径450-650mm
2.检测要求:
宽度检测,误差≤0.5mm
纹路深度检测,误差≤0.2mm
轮半径检测,误差≤0.5mm
检测频率:每个轮胎2分钟
报警:发生超差情况,立即报警,软件有显示,同时通过数字开关信号给出报警信号
3.实现方案:
●采用3台激光轮廓传感器
●1台检测胎面,检测宽度、纹路深度、轮半径
●2台检测侧面,检测明显磨损,如轮胎鼓包
●3台传感器同步测量,消除胶带抖动影响,因此胶带的抖动不影响测量
4.性能指标:
宽度误差:≤0.5mm
纹路深度检测误差:≤0.2mm
轮半径检测误差:≤0.5mm
缺陷检测:视缺陷程度而定,暂不能确定
检测频率:每秒检测1次
2个传感器距离胶带的安装距离:650mm
报警:发生超差情况,立即报警,软件有显示,同时通过数字开关信号给出报警信号图形显示:轮胎面3D轮廓实施显示,各测量要素实时显示
传感器防护等级:IP67,适合恶劣的工业环境
电源:220V 8A
4.实现示意图
4.系统构成:
激光传感器3台
传输线3套
采集同步控制器1套
(注:用户需要提供双千兆网口工业计算机)
5.软件系统
可以根据客户要求,设计专用的软件和界面(费用另计)。
汽车轮毂试验的三个标准和分析过程

汽车轮毂试验的三个标准和分析过程一有关汽车轮毂的三个试验标准根据国内和国际标准化组织(ISO) 的规定,汽车轮毂必须满足三个典型试验的要求。
有关的国内标准与ISO 的标准是一致的,国外不同国家的标准可能不完全一样,但是基本方面还是一致的,只是具体载荷大小有所差别。
在国内,这三个试验对应的标准分别是:1. 车轮动态弯曲疲劳和径向疲劳试验方法- QCT221其中包含了动态弯曲和径向载荷两个疲劳试验标准。
2. 车轮冲击试验方法- GBT15704其中包含了轮毂冲击试验的标准。
下面简单介绍这三个试验标准。
标准1:汽车轻合金车轮的性能要求和试验方法QC/T221—1997前言本标准是根据1995 年标准制修订计划安排组织制定的。
本标准在制订过程中,参照采用了美国SFI、日本JASO 等有关标准。
本标准由机械工业部汽车工业司提出。
本标准由全国汽车标准化技术委员会归口。
本标准由广东南海中南铝合金轮毂有限公司负责起草、立中车轮制造有限公司参加起草。
本标准主要起草人:雷铭君。
1 范围本标准规定了汽车轻合金车轮的动态弯曲疲劳性能、动态径向疲劳性能要求及试验方法。
本标准适用于全部或部分轻合金制造的汽车车轮。
2 试验项目2.1 动态弯曲疲劳试验;2.2 动态径向疲劳试验。
3 试验样品弯曲疲劳和径向疲劳试验用的车轮应是未经试验或未使用过的新成品车轮,每个车轮只能做一次试验。
4 动态弯曲疲劳试验4.1 试验设备试验台应有一个旋转装置,车轮可在一固定不变的弯矩作用下旋转,或是车轮静止不动,而承受一个旋转弯曲力矩作用(见图1)4.2 试验程序4.2.1 准备工作根据车轮在车辆上安装的实际情况,按规定的扭矩最低值的115%,将车轮紧固在试验装置的支承面上,螺母不允许加润滑剂。
调整车轮位置后,将轮辋的轮缘夹紧到试验夹具上。
试验的连接件和车轮的配合面应去除多余的堆聚物、灰尘或杂质。
车轮的螺栓和螺母在试验过程中可再次紧固。
加载系统应保持规定的载荷,误差不超过±2.5%。
轮胎检测及项目参照标准(科标化工)
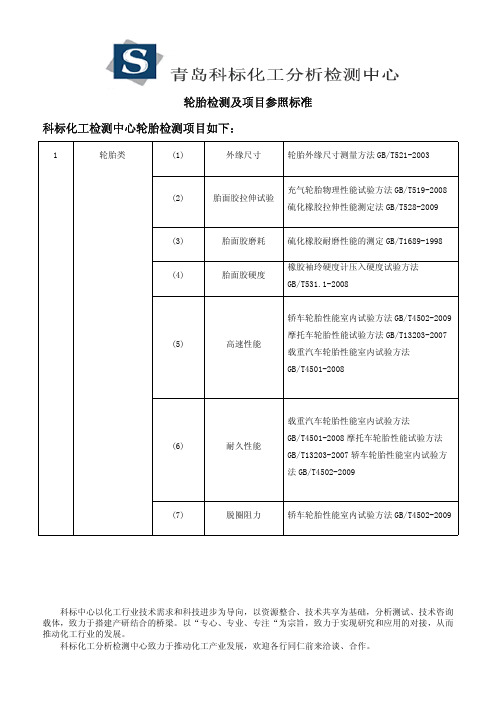
动态弯曲疲劳
乘用车车轮性能要求和试验方法 GB/T5334-2005 商用车辆车轮性能要求和试 验方法 GB/T5909-1995
冲击试验
轿车车轮冲击试验方法 GB/T15704-1995
低气压项目 轿车轮胎性能室内试验方法 GB/T4502-2009
科标中心以化工行业技术需求和科技进步为导向,以资源整合、技术共享为基础,分析测试、技术咨询 载体,致力于搭建产研结合的桥梁。以“专心、专业、专注“为宗旨,致力于实现研究和应用的对接,从而 推动化工行业的发展。
部分参数
力车内胎 GB/T1703-2008
全部参数
压配式实心轮胎技术规范 GB/T16623-2008
全部参数
充气轮胎轮辋实心轮胎 GB/T10824-2008
物理性能
轿车翻新轮胎 GB/T14646-2007
物理性能 性能要求 性能要求 冲击试验
载重汽车翻新轮胎 GB7037-2007
商用车辆车轮性能要求和试验方法 GB/T5909-2009 乘用车车轮性能要求和试验方法 GB/T5334-2005
科标化工分析检测中心致力于推动化工产业发展,欢迎各行同仁前来洽谈、合作。
2
乘用车轮胎
3
轿车轮胎
轻型车辆用新的 4
子午线充气轮胎
新充气斜交轮胎 5
和某些特殊轮胎
全部参数
乘用车轮胎 GSO 51/52/53/2007 关于批准汽 车及其拖车用充气轮胎的统一要求 ECER30
全部参数
轿车轮胎 GB9743-2007
全部参数 全部参数 全部参数
农业轮胎技术条件 GB/T1192-2008 内胎标准 SNI06-6700-2002 汽车轮胎内胎 JIS D 4231-1995
轮胎气密性试验机测试要求以及结果标准

轮胎气密性试验机的测试要求和结果标准1.测试条件1.1初始空气压如下表:1.2室内温度要求:1.2.1室内的储存区域,平均温度维持在21℃±3℃。
1.2.2测试期间的平均室内温度为21℃±0.6℃。
1.2.3每日的室内温度变化为21℃±3℃。
2.测试准备2.1使用涂装钢圈且RIM的Bead Seat部必须没有熔接段差,损坏、凹凸存在。
2.2将Clamp in Valve组装于RIM上且把Valve Core取出。
2.3检查要使用的压力计、测试开始空气压的80%~120%范围、以5kPa以下的刻度作检测,并调整至符合试验开始空气压的1%的误差范围内,记录检测结果并作保存。
2.4把检测完后的压力计以Seal Tape贴附住。
2.5轮胎安装前在胎唇区域和轮辋涂抹用胎唇润滑油,建议使用植物油或是皂基的润滑油。
2.6以规定的轮辋安装轮胎,但固定胎唇座时轮胎内充气压力不可超过275kPa(40psi)。
3.测试顺序3.1作RIM与TIRE组装,须注意不要造成TIRE BEAD部损伤。
3.2将组装有压力计的T型特殊Valve以Seal Tape等装置于RIM Valve上。
3.3以T型特殊Valve的空气注入Valve来作TIRE 内压的充填。
3.4轮胎的胎唇部或者钢圈气门嘴、T型特殊气门嘴、压力计等的接合部位,请使用肥皂水来确定是否有无漏气。
3.5将轮胎充气到超过试验压力大约15kPa(2psi)的值后,将轮胎和轮辋组合体在实验室环境温度(18~36℃)下停放24~26小时,让轮胎成长。
3.6待组装轮胎成长后浸入水中45分钟(每间隔10分钟确认一次,确认时间为5分钟),以确保样品无试水漏气现象。
3.7在确认轮胎不会漏气后,将气门嘴盖上盖子,而且轮胎应保持在相同的平面上,避免引起新的漏气。
3.8在试水漏气检查后,轮胎要放置在静置漏气实验室内停放48~50小时,然后才开始记录测试初始压力。
渔轮产品通用检验标准
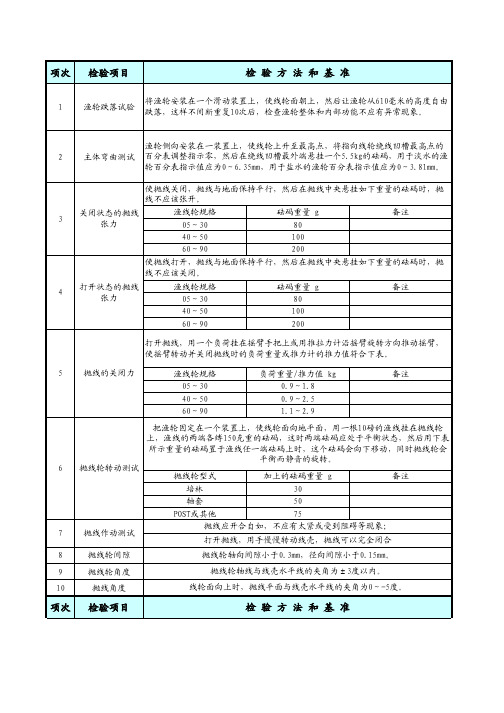
4
打开状态的抛线 张力
渔线轮规格 05~30
砝码重量 g 80
备注
40~50
100
60~90
200
打开抛线,用一个负荷挂在摇臂手把上或用推拉力计沿摇臂旋转方向推动摇臂, 使摇臂转动并关闭抛线时的负荷重量或推力计的推力值符合下表。
5 抛线的关闭力
渔线轮规格 05~30 40~50 60~90
负荷重量/推力值 kg 0.9~1.8 0.9~2.5 1.1~2.9
力及刹车紧度设置:
45
刹车紧度和最小 刹车力
渔线轮规格 05~10 20 30 40~50 60 70~90
最小刹车力kg 2.7 4.1 4.5 5.4 6.3 7.7
30%刹车紧度kg 0.91 1.36 1.5 1.81 2.09 2.54
将渔轮固定在一个滑动装置上,线轮载满渔线,模拟正常钓鱼的状况,依不同速
27 摇臂的转动间隙 使线壳固定不动,扳动摇臂,转动方向的间隙变化应小于2度。
28
摇臂的晃动量
将渔轮固定在一装置上,旋紧摇臂盖,用百分表测量摇臂手把端内侧的晃动量, 其值应小于2.0mm。
29
摇臂的左右互换 性
摇臂从左右两边锁紧后都能灵活转动,且不可与其他部位干涉。
将渔轮固定在一装置上,反动钮OFF,在摇臂手把上加载下表所示的负荷时,不应 发生铆钉滑落、损坏或摇臂明显变形、松动等。
23
线轮轴向位置
调整钮调至最松,使线轮上升至最高位置时,用0.5kg的力沿轴向往外拉线轮,线 轮裙部与线壳中心圆台的重合高度应大于0.5mm。
项次 检验项目
检验方法和基准
以约100RPM速度转动,手把转动应灵活,无滞涩感或异音; 24 手把装配特性
脚轮的测试方法及要求
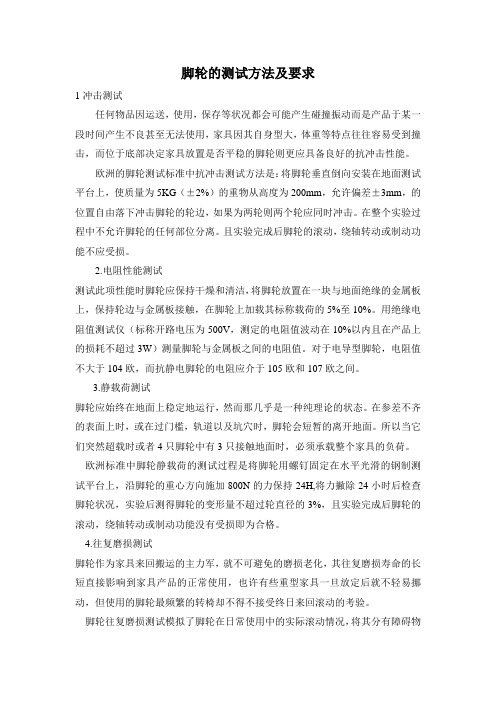
脚轮的测试方法及要求1冲击测试任何物品因运送,使用,保存等状况都会可能产生碰撞振动而是产品于某一段时间产生不良甚至无法使用,家具因其自身型大,体重等特点往往容易受到撞击,而位于底部决定家具放置是否平稳的脚轮则更应具备良好的抗冲击性能。
欧洲的脚轮测试标准中抗冲击测试方法是:将脚轮垂直倒向安装在地面测试平台上,使质量为5KG(±2%)的重物从高度为200mm,允许偏差±3mm,的位置自由落下冲击脚轮的轮边,如果为两轮则两个轮应同时冲击。
在整个实验过程中不允许脚轮的任何部位分离。
且实验完成后脚轮的滚动,绕轴转动或制动功能不应受损。
2.电阻性能测试测试此项性能时脚轮应保持干燥和清洁,将脚轮放置在一块与地面绝缘的金属板上,保持轮边与金属板接触,在脚轮上加载其标称载荷的5%至10%。
用绝缘电阻值测试仪(标称开路电压为500V,测定的电阻值波动在10%以内且在产品上的损耗不超过3W)测量脚轮与金属板之间的电阻值。
对于电导型脚轮,电阻值不大于104欧,而抗静电脚轮的电阻应介于105欧和107欧之间。
3.静载荷测试脚轮应始终在地面上稳定地运行,然而那几乎是一种纯理论的状态。
在参差不齐的表面上时,或在过门槛,轨道以及坑穴时,脚轮会短暂的离开地面。
所以当它们突然超载时或者4只脚轮中有3只接触地面时,必须承载整个家具的负荷。
欧洲标准中脚轮静载荷的测试过程是将脚轮用螺钉固定在水平光滑的钢制测试平台上,沿脚轮的重心方向施加800N的力保持24H,将力撇除24小时后检查脚轮状况,实验后测得脚轮的变形量不超过轮直径的3%,且实验完成后脚轮的滚动,绕轴转动或制动功能没有受损即为合格。
4.往复磨损测试脚轮作为家具来回搬运的主力军,就不可避免的磨损老化,其往复磨损寿命的长短直接影响到家具产品的正常使用,也许有些重型家具一旦放定后就不轻易挪动,但使用的脚轮最频繁的转椅却不得不接受终日来回滚动的考验。
脚轮往复磨损测试模拟了脚轮在日常使用中的实际滚动情况,将其分有障碍物测试和无障碍物测试两种,将其脚轮正确安装好放至测试平台上,每个测试脚轮负载300N,测试频率为(6-8)次/min,一个测试周期包括前进1M和折回反向1M的一个来回运动,在有障碍物(金属障碍物,宽50mm,高2mm-3mm)的测试平台上测试5000次(H型脚轮)或30000次(W型脚轮)。
滚轮型式试验检验内容要求与方法

检验项目
标准要求
检验结果
结论
1
滚轮外径(mm)
滚轮外径偏差应符合企业规定的要求
3
滚轮轮体硬度
邵尔(A)
橡胶硬度应符合企业规定的要求
4
外观质量
滚轮表面不允许有气泡、砂眼,裂痕等缺陷,应手感光滑,无粘手现象,色泽应均匀。
5
疲劳试验
疲劳试验应符合企业规定的要求,试验后滚轮应没有脱胶现象和开裂现象。但加载压力至少应为800N,试验运行时间至少应为250小时。
2.申请单位应向型式试验机构提供二个滚轮的试验样品。
二、型式试验的内容要求与方法应符合下表的要求:
项目
编号
检验内容与要求
检验方法
1
滚轮外径偏差应符合企业规定的要求
用尺测量
2
滚轮橡胶硬度应符合企业规定的要求
用邵尔橡胶硬度计测量轮子表面上均布的3点,取平均值。
3
滚轮表面不允许有气泡、砂眼,裂痕等缺陷,应手感光滑,无粘手现象,色泽应均匀。
检验日期
检验依据
《自动扶梯和自动人行道型式试验规程》
技术参数
材料:
外径(mm):
轮厚(mm):
适用自动扶梯、自动人行道速度(m/s):
抽
样
抽样方式:
抽样地点:
抽样数/抽样基数:
抽样单位:
检
验
结
论
检验单位名称(盖章)
批准:审核:编制:
日期:日期:日期:
滚轮型式试验报告
报告编号:
共2页
第2页
检验项目及结果汇总
目测
4
疲劳试验应符合企业规定的要求,试验后滚轮应没有脱胶现象和开裂现象。但加载压力至少应为800N,试验运行时间至少应为250小时。
轮胎产品型式试验项目及检测依据
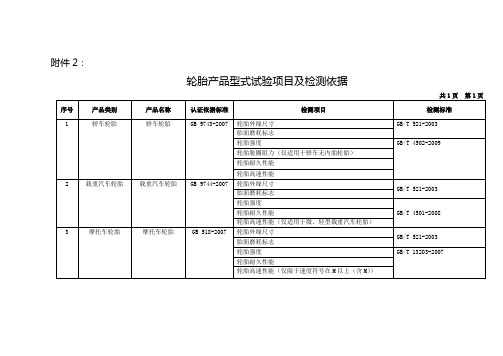
轮胎高速性能(仅限于速度符号在M以上(含M))
附件2:
轮胎产品型式试验项目及检测依据
共1页第1页
序号
产品类别
产品名称
认证依据标准
检测项目
检测标准
1
轿车轮胎
轿车轮胎
GB 9743-2007
轮胎外缘尺寸
GB/T 521-2003
胎面磨耗标志
轮胎强度
GB/T 4502-2009
轮胎脱圈阻力(仅适用于Байду номын сангаас车无内胎轮胎)
轮胎耐久性能
轮胎高速性能
2
载重汽车轮胎
载重汽车轮胎
GB 9744-2007
轮胎外缘尺寸
GB/T 521-2003
胎面磨耗标志
轮胎强度
GB/T 4501-2008
轮胎耐久性能
轮胎高速性能(仅适用于微、轻型载重汽车轮胎)
3
摩托车轮胎
摩托车轮胎
GB 518-2007
轮胎外缘尺寸
GB/T 521-2003
胎面磨耗标志
轮胎强度
GB/T 13203-2007
CEN-37-中文-96版脚轮检验标准
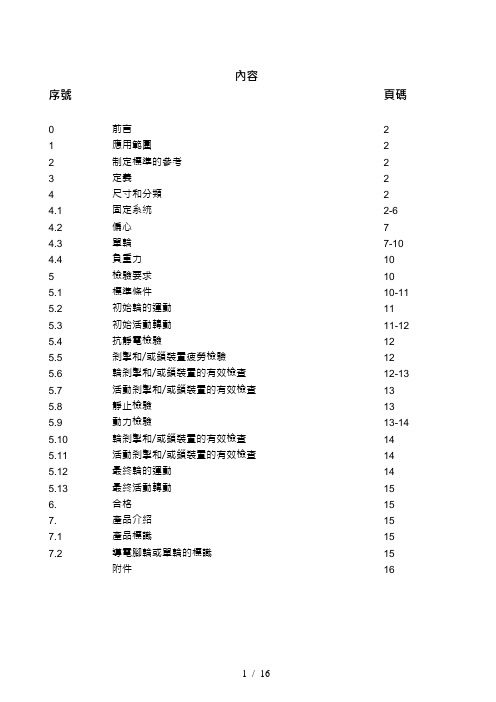
內容序號頁碼0 前言 21 應用範圍 22 制定標準的參考 23 定義 24 尺寸和分類 24.1 固定系統2-6 4.2 偏心7 4.3 單輪7-104.4 負重力105 檢驗要求10 5.1 標準條件10-11 5.2 初始輪的運動11 5.3 初始活動轉動11-12 5.4 抗靜電檢驗12 5.5 剎掣和/或鎖裝置疲勞檢驗12 5.6 輪剎掣和/或鎖裝置的有效檢查12-13 5.7 活動剎掣和/或鎖裝置的有效檢查13 5.8 靜止檢驗13 5.9 動力檢驗13-14 5.10 輪剎掣和/或鎖裝置的有效檢查14 5.11 活動剎掣和/或鎖裝置的有效檢查14 5.12 最終輪的運動145.13 最終活動轉動156. 合格157. 產品介紹15 7.1 產品標識15 7.2 導電腳輪或單輪的標識15附件160. 前言此草擬歐洲標準定名為CEN/TC 324 “腳輪和單輪〞。
1. 應用範圍該草擬歐洲標準規定了技術要求、恰當的尺寸与檢驗要求。
該草擬歐洲標準適用於手動或電動腳輪和單輪( 包括附件),其速度不超過1.1米/秒( 4公里/小時)。
用於家具、辦公椅、學院、醫院的床与駕駛配件的腳輪和單輪不包括在內。
2. 制定標準的參考本草擬歐洲標準包含有已指定日期和非指定日期的參考資料与其它文刊的題要。
這些制定標準的參考資料將在下文中適當地引述。
有效的指定日期參考資料由最新更改版本引正,非指定日期的參考資料由最後版本引正。
prEN .... 腳輪和單輪:詞匯、推荐符號与多種語言字典。
prEN .... 腳輪和單輪:檢驗設備和程序3. 定義為制定本草擬歐洲標準,prEN參考資料內的定義与推荐符號全部適用。
4. 尺寸与分類一個腳輪特徵如下:-固定系統( 4.1 )-偏心( 4.2 )-單輪( 4.3 )-負重力( 4.4 )4.1 固定系統固定系統包括底板、固體柄把与單個螺栓固定裝置。
4.1.1 底板通過分類將底板區分開來,包括帶三個固定孔的三角形底板和帶四個固定孔的長方形底板。
福来轮、万向轮检验标准

雨雪痕迹;
要转储等信息,反馈 SQE,判定是否可以让步接 收。
编号:
备注
第5步
第6步 第7步 第8步 第9步
开箱检查
外观检验 目检 尺寸检验 游标卡尺 材质检验 委外 转动灵活 性
G、如没有合格证或检验记录,则整体检验合
格后不予入库,并反馈采购经理,待补齐后再
8、确认内包装中是否具有合格证或附带规定格式检验记录, 入库。
确认标示的信息是否与送货单不一致。
H、如出现数量、规格型号标记、供应商商标
9、确认包装箱标示的数量是否与实物一致。
不一致问题,则停止检验并反馈采购经理和
10、福来轮、万向轮保持架上是否有标识,标识内容包括规格
SQE。待落实情况后处理。
型号标记、供应商商标,规格型号标识和供应商商标是否与送 I、如出现标识内容不包含规格型号标记、供
备注
变更标记
变更申请单号
检验员/SQE 确认及日期
拟制/ 日期 审核/ 日期
批准/ 日期
福来轮、万向轮检验标准(指导部分)
操作步骤 检验项目 检测设备
详细操作方法及内容
标准要求、注意事项
第 1 步 资料审查 第 2 步 标准确认
1、随产品附有本次订单的随行文件,文件包括合格证或检验 a、如果未提供随行文件,则检验完毕后不予入 记录(内容应至少包括外观、尺寸、转动灵活性、材质证明)库,待补齐并经质检员确认数据真实性后入库。
零部件名称 适用范围
福来轮、万向轮检验标准(总则)
福来轮、万向轮 通用
编号:
主 部件
要
组
成
保持架、转动部件、
包装方式
避光包装材料袋装,每袋重量 应低于 30KG.
脚轮的测试方法及要求
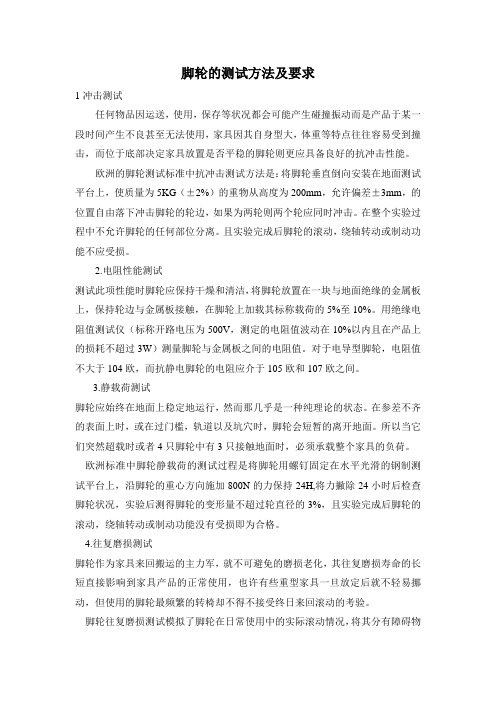
脚轮的测试方法及要求1冲击测试任何物品因运送,使用,保存等状况都会可能产生碰撞振动而是产品于某一段时间产生不良甚至无法使用,家具因其自身型大,体重等特点往往容易受到撞击,而位于底部决定家具放置是否平稳的脚轮则更应具备良好的抗冲击性能。
欧洲的脚轮测试标准中抗冲击测试方法是:将脚轮垂直倒向安装在地面测试平台上,使质量为5KG(±2%)的重物从高度为200mm,允许偏差±3mm,的位置自由落下冲击脚轮的轮边,如果为两轮则两个轮应同时冲击。
在整个实验过程中不允许脚轮的任何部位分离。
且实验完成后脚轮的滚动,绕轴转动或制动功能不应受损。
2.电阻性能测试测试此项性能时脚轮应保持干燥和清洁,将脚轮放置在一块与地面绝缘的金属板上,保持轮边与金属板接触,在脚轮上加载其标称载荷的5%至10%。
用绝缘电阻值测试仪(标称开路电压为500V,测定的电阻值波动在10%以内且在产品上的损耗不超过3W)测量脚轮与金属板之间的电阻值。
对于电导型脚轮,电阻值不大于104欧,而抗静电脚轮的电阻应介于105欧和107欧之间。
3.静载荷测试脚轮应始终在地面上稳定地运行,然而那几乎是一种纯理论的状态。
在参差不齐的表面上时,或在过门槛,轨道以及坑穴时,脚轮会短暂的离开地面。
所以当它们突然超载时或者4只脚轮中有3只接触地面时,必须承载整个家具的负荷。
欧洲标准中脚轮静载荷的测试过程是将脚轮用螺钉固定在水平光滑的钢制测试平台上,沿脚轮的重心方向施加800N的力保持24H,将力撇除24小时后检查脚轮状况,实验后测得脚轮的变形量不超过轮直径的3%,且实验完成后脚轮的滚动,绕轴转动或制动功能没有受损即为合格。
4.往复磨损测试脚轮作为家具来回搬运的主力军,就不可避免的磨损老化,其往复磨损寿命的长短直接影响到家具产品的正常使用,也许有些重型家具一旦放定后就不轻易挪动,但使用的脚轮最频繁的转椅却不得不接受终日来回滚动的考验。
脚轮往复磨损测试模拟了脚轮在日常使用中的实际滚动情况,将其分有障碍物测试和无障碍物测试两种,将其脚轮正确安装好放至测试平台上,每个测试脚轮负载300N,测试频率为(6-8)次/min,一个测试周期包括前进1M和折回反向1M的一个来回运动,在有障碍物(金属障碍物,宽50mm,高2mm-3mm)的测试平台上测试5000次(H型脚轮)或30000次(W型脚轮)。
工器具检验检查标准(干货分享)

附件1
工器具检验/检查标准
序号
工器具名称
工器具类别
基本要求
检验/检查标准
周期
备注
1
安全帽
安全用具
1.必须使用有效期内合格的安全帽,使用前应根据自己头型将帽箍调至适当位置,避免过松或过紧。
2。将帽衬衬带位置调节好并系牢,帽衬的顶端与帽壳内顶之间应保持20-50mm的空间。
3。安全帽的下颏带必须扣在颏下,并系牢,松紧要适度,以防帽子滑落、碰掉.
3.锯片防护罩应完好齐全,且安装牢固可靠。
4.外壳金属部分应无明显缺损,有表面涂层的应无起层和剥落现象。
5。外壳塑料部分及握柄应无气泡、无裂痕、无灼伤、无变形、无影响安全使用的灼伤等缺陷。
6。电源线、电源插头均完好无损伤.
7.电源开关应操作正常、灵活.
8。锯片紧固螺栓及压板应无松动,锯片外观应无缺口、无缺齿、无裂纹等损伤。底板应平整无变形.1年/次8Fra bibliotek防坠器
安全用具
1.必须使用有效期内合格的防坠器。使用时必须高挂低用,悬挂在使用者上方坚固钝边的结构物上。
2。使用防坠器进行倾斜作业时,原则上倾斜度不超过30度,30度以上必须考虑能否撞击到周围物体或采取其它措施。
3。防坠器关键零部件已特种处理过,使用时不需加润滑剂。
4.防坠器安全绳严禁扭结使用。严禁拆卸改装。雨天使用后须用干布擦干安全绳再收回机壳内。不使用时应在干燥少尘的地方存放.
1.产品标识及定期检验合格标识应清晰齐全。
2.靴底的防滑花纹磨损应不超过50%,不能磨透露出绝缘层.
3.绝缘靴整体各处应无裂纹、无漏洞、无气泡、无灼伤、无划痕等损伤。
4.工频耐压试验(15kV、1min)。
轮胎成品检验的普通检验流程

步骤序号
检验项目
检验方法
判定标准
1
外观检查
目视检查
轮胎表面应平整量
使用测量工具
轮胎尺寸应符合产品规格要求
3
重量检查
使用电子秤
轮胎重量应符合产品规格要求
4
气压测试
使用气压表
轮胎气压应符合产品规格要求,且无漏气现象
5
平衡性测试
使用平衡机
轮胎动平衡性能应符合产品规格要求
6
耐磨性测试
使用耐磨试验机
轮胎耐磨性能应符合产品规格要求
7
耐久性测试
进行耐久性试验
轮胎耐久性应符合产品规格要求,无异常磨损或损坏
8
标记检查
目视检查
轮胎标记应清晰、准确,符合相关标准
起重工具检查和试验周期质量参考标准
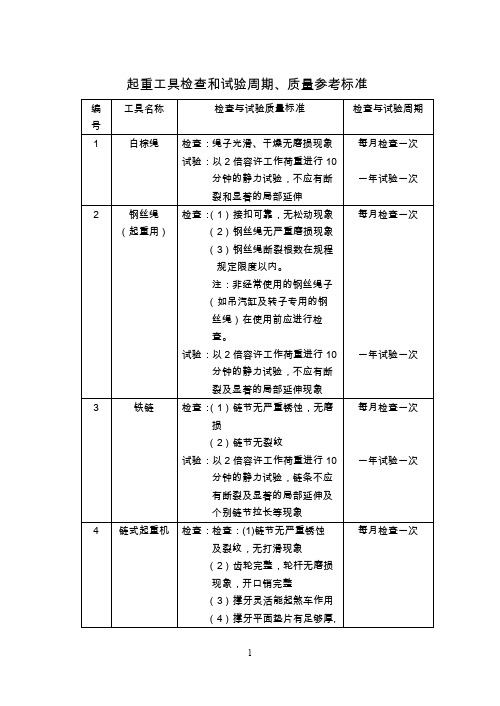
(4)吊钩无裂纹变形
(5)滑轮滑杆无磨损现象
(6)滚筒突缘高度至少应比最
外层绳索的表面高出该绳索的
一个直径.吊钩放至最低位置
时,滚筒上至少剩有5圈绳索,
绳索固定点良好
(7)机械转动部分防护罩完整,
开关及电机外壳接地良好
(8)卷扬限制器在吊钩升起距
起重构架300毫米时自动停止
六个月检查一次
(3)使用前应进行
状况和部件,并测量构架挠曲
度
(2)一般的定期试验,以1.1
倍容许工作荷重进行10分
钟的静力试验
定期试验:常用的一年进行一次;不常用的,每三年进行一次
9
千斤顶
检查:(1)顶重头形状能防止物件的
滑动
(2)螺旋或齿条千斤顶,防止螺杆或齿条脱离丝扣的装置良好
(3)螺纹磨损率不超过20%
(4)螺旋千斤顶,自动制动装
11
安全带
检查:(1)绳索无脆裂断股现象
(4)皮带各部接扣及铆接处完
整牢固
试验:以225公斤重物悬吊5分钟,
无损伤或局部延伸现象
每月检查一次
六个月试验一次
起重工具检查和试验周期
质量参考标准
批准:
审核:
断根数在规程规定范围以内
(2)吊钩无裂纹及变形,销子
及滚珠轴承良好
(3)滚筒突缘高度至少比最外
层绳索表面高出该绳索的一
个直径.吊钩放在最低位置时
滚筒上至少剩有5圈绳索,绳
索固定点良好
(4)齿轮箱良好,轴承无严重
磨损
(5)葫芦链节无严重锈蚀裂纹
齿轮完整,轮杆无磨损现象,
(一)一年试验检查一次
(二)结合大小修进行检查
(4)棕绳光滑无任何断裂现象
- 1、下载文档前请自行甄别文档内容的完整性,平台不提供额外的编辑、内容补充、找答案等附加服务。
- 2、"仅部分预览"的文档,不可在线预览部分如存在完整性等问题,可反馈申请退款(可完整预览的文档不适用该条件!)。
- 3、如文档侵犯您的权益,请联系客服反馈,我们会尽快为您处理(人工客服工作时间:9:00-18:30)。
用手 模
成 品√ 椅
①、各规格汽压棒 行程尺寸误差为
5PCS
用卷
卷
√
±3mm
/批 尺量 尺
②、中心管外径为:
2
尺 寸
Ø28mm+0mm/- 0.03mm 外管外径
为:
5PCS /批
Ø50mm±0.2mm
用游 标卡 尺量
游 标 卡 尺
√
③、各规格外管长 5PCS 用卷 卷 度误差为:±2mm /批 尺量 尺
烤漆颜色、亮度与样品 一致,无碰伤、掉漆现
√
象
③、轮子主轴、卡簧无
电镀脱层、生锈、发黄
√
现象
④、轮子四周削边整齐
平滑,用手触、轮子主轴直径为
√
10.9mm-11.1mm
2
尺 寸
②、轮子主轴长度为 22mm±1mm
5PCS/ 批
测量
卡尺
√
③、轮片、轮轴用手转
√
动灵活无异声
√
①、棒芯不可有漏
气现象
②、棒芯与外管配
合要吻合,不可有
功 晃动现象
3
能 结
③、汽压棒组件与
构 环规检验缩度
±1.5mm
④、汽压棒寿命测 试升降、旋转12万 次无损坏、无漏气
(Ⅱ)
(Ⅱ)
5PCS /批
1次/6 个月
试压
用成 椅组 装试
用卷 尺量 环规
座椅 旋转 测试
√
成 椅
√
卷
尺 环
√
规
测
试√
机
标准
20N
轮子检验及其测试标准
品号
通用
检 序验 号项
目
1
外 观
检验标准
①、轮子颜色、纹路、 表面处理效果与样品一 致,无裂纹、流痕、发 白等现象
允收 水准 抽样 方式
(Ⅱ)
CRI:0
MAJ :1.0
MIN:4.0
不良类型
检验方 检验 C
法
工具 R MAJ
MIN
I
目视
手感 对照合
样板
√
格样板
②、轮子表面清洁干净,
1PCS /批
椅背 强度 测试 标准
静
压
测
√
试
机
拉
背
测√
试
机
⑧、通过冲击测试 后无漏气、严重变 形、损坏等现象, 功能性200磅,证明 性300磅。
1PCS /批
用冲 击测 试机 测
冲 击 测√ 试 机
注意:汽杆 级数为 SGS 或 TUV 钢印 标志为 CLASS1 — —3级 测 试不得少 于 400N+ —
不良类型
检
检
序验 号项
检验标准
抽样 检验 验 方式 方法 工
目
具
C
R MAJ
MIN
I
①、外管表面烤漆 处理与样品一致,
参照 样
无严重刮花、碰伤 之现象
限度 样品
品
√
②、外管底部焊接
外 要牢固,不可漏焊、
1 观 假焊、组装成椅执 (Ⅱ) 目测 无
√
行座椅落下测试看
焊接边无开裂现象
③、汽压棒组件不 可有毛刺、刮手现 象
①、轮子外形、结构与
对照合格
样品一致
(Ⅱ)
样板
样板
√
②、轮子主轴与轮子塑
30磅沙
胶部位组合紧密,30磅 沙袋吊起主轴1分钟主
袋吊起 沙袋
√
主轴1分 30磅
轴无脱落现象
钟
5PCS/
用合格椅
③、轮子主轴与五爪轮 批
功 孔配合紧密,轮子组装
3
能 结
轻松,吊起5磅沙袋1分 钟轮子脱落
脚试装轮 椅脚
子,吊起5 沙袋
√
环
4
保 测
送测或供方提供证明
√
试
√
磅沙袋1 5磅
分钟
构 ④、组装成椅300磅冲击 5PCS/
测试轮子无结构损坏
批
冲击测 试标准
测试 机
√
⑤、寿命测试10万次轮 子无结构、功能损坏(其 中障碍2000次无障碍 98000次)
1次/6 个月
椅轮耐 久性测 试标准
测试 机√
⑥、刹车轮在15度的坡 度上无滑动
5PCS/ 批
成椅组 装
坡度 板
⑤、组立成椅后, 汽压棒升降功能要
灵活,以底盘锥孔
用成
为中心点,15cm 为 5PCS 椅组 成 半径内静压50KG /批 装测 椅
√
重物执行分段下降
试
操作,汽压棒满足 分段下降要求
⑥、汽压棒承受压 力须符合订单要求
5PCS /批
用静 压测 试机 测
⑦、通过拉背测试 后无漏气、严重变 形、损坏等现象, 功能性200磅,证明 性300磅。