PCB全制程简介
PCB全制程

PCB制造流程及说明一. PCB演变1.1 PCB扮演的角色PCB的功能为提供完成第一层级构装的组件与其它必须的电子电路零件接合的基地以组成一个具特定功能的模块或成品所以PCB在整个电子产品中扮演了整合连结总其成所有功能的角色也因此时常电子产品功能故障时最先被质疑往往就是PCB图1.1是电子构装层级区分示意1。
2 PCB的演变1.早于1903年Mr. Albert Hanson首创利用"线路"(Circuit)观念应用于电话交换机系统它是用金属箔予以切割成线路导体将之黏着于石蜡纸上上面同样贴上一层石蜡纸成了现今PCB的机构雏型见图1.22. 至1936年Dr Paul Eisner真正发明了PCB的制作技术也发表多项专利而今日之print-etch (photo image transfer)的技术就是沿袭其发明而来的1。
3 PCB种类及制法在材料层次制程上的多样化以适合不同的电子产品及其特殊需求以下就归纳一些通用的区别办法来简单介绍PCB的分类以及它的制造方法1。
3。
1 PCB种类A。
以材质分a. 有机材质酚醛树脂玻璃纤维/环氧树脂PolyamideBT/Epoxy等皆属之b。
无机材质铝Copper Inver—copperceramic等皆属之主要取其散热功能B。
以成品软硬区分a。
硬板Rigid PCBb。
软板Flexible PCB 见图1。
3c.软硬板Rigid—Flex PCB 见图1。
4C。
以结构分a。
单面板见图1。
5b。
双面板见图1。
6c。
多层板见图1.7D。
依用途分通信/耗用性电子/军用/计算机/半导体/电测板,见图1.8 BGA.另有一种射出成型的立体PCB因使用少不在此介绍1。
3。
2制造方法介绍A. 减除法其流程见图1.91资料收藏http://www。
maihui。
net PCB收藏天地PCB制造流程及说明B. 加成法又可分半加成与全加成法见图1.10 1.11C. 尚有其它因应IC封装的变革延伸而出的一些先进制程本光盘仅提及但不详加介绍因有许多尚属机密也不易取得或者成熟度尚不够本光盘以传统负片多层板的制程为主轴深入浅出的介绍各个制程再辅以先进技术的观念来探讨未来的PCB走势二。
pcb流程简介全制程

表面处理
表面处理是PCB制造中的重要环节,主要目的是提高 PCB的可靠性和性能。
输标02入题
表面处理工艺包括镀金、镀银、喷锡等。镀金可以增 强导电性能和耐腐蚀性,镀银可以提高焊接性能,喷 锡则可以提高可焊性和耐热性。
01
03
在表面处理过程中,需要注意防止表面氧化、变色和 脱落等问题。
05
02
制作
将设计好的PCB图转换为实际电路板, 需要进行覆铜、钻孔、电镀等处理。
03
检测
对制作好的电路板进行检测,包括外 观检测、电气性能检测等,确保质量 合格。
04
组装
将电子元器件焊接到电路板上,完成 PCB的组装。
02
PCB设计
原理图设计
总结词
原理图设计是PCB流程的起始阶段,主要任务是创建电路原理图,将电路的功 能需求转化为图形表示。
确保使用的原材料质量合格, 无缺陷且符合设计要求。
生产过程监控
对PCB制造过程中的各个环节 进行严格监控,确保工艺参数
符合标准。
成品检验
对完成的PCB进行全面的质量 检查,包括外观、尺寸、电气
性能等。
环境条件控制
确保生产环境满足温湿度、清 洁度等要求,以降低品质风险
。
可靠性评估方法
寿命测试
模拟实际使用环境,对 PCB进行长时间运行测试 ,评估其寿命和稳定性。
详细描述
PCB布线是电路板设计的最后阶段,它需要考虑布线的长度、宽度、弯曲半径等 因素,以确保电路的电气性能和可靠性。同时,布线还需要考虑制造工艺的要求 ,以确保生产的可行性和效率。
03
PCB材料选择与处
PCB流程简介-全制程
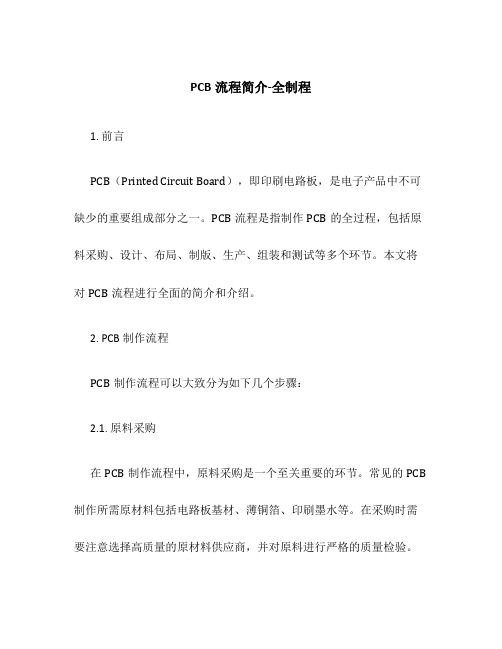
PCB流程简介-全制程1. 前言PCB(Printed Circuit Board),即印刷电路板,是电子产品中不可缺少的重要组成部分之一。
PCB流程是指制作PCB的全过程,包括原料采购、设计、布局、制版、生产、组装和测试等多个环节。
本文将对PCB流程进行全面的简介和介绍。
2. PCB制作流程PCB制作流程可以大致分为如下几个步骤:2.1. 原料采购在PCB制作流程中,原料采购是一个至关重要的环节。
常见的PCB 制作所需原材料包括电路板基材、薄铜箔、印刷墨水等。
在采购时需要注意选择高质量的原材料供应商,并对原料进行严格的质量检验。
2.2. 设计和布局PCB设计是整个流程中重要的阶段之一。
在这个阶段,设计师会使用专业的电路设计软件,根据电子产品的功能要求和电路原理图进行PCB电路板的设计和布局。
设计师需要考虑电路板的大小、层次、电路连接、电源布局等因素,并与其他硬件模块进行兼容性和接口匹配的设计。
2.3. 制版制版是将PCB设计文件转化成实际可用的制板文件的过程。
在这个阶段,设计师会将PCB设计文件输出为Gerber文件,并将Gerber文件发送给制板厂家。
制板厂家会根据Gerber文件进行图形的翻版和制版,最终得到制版后的电路板。
2.4. 生产和组装生产和组装是将制版的电路板进行生产和组装的过程。
在这个阶段,制板厂家会采用先进的生产工艺和设备,将电路板上的电子元器件和连接线进行焊接和组装。
生产和组装的目标是将电路板上的各个元器件正确地安装到预定位置,并确保电路板的良好连接和可靠性。
2.5. 测试和质检测试和质检是确保PCB质量和性能的关键环节。
在这个阶段,制板厂家会进行全面的测试和质检,包括电气测试、可靠性测试和功能测试等。
只有通过了严格的测试和质检,才能确保PCB的质量和可靠性。
3. PCB制作的注意事项在PCB制作流程中,需要注意以下几个重要的事项:3.1. 设计准则在进行PCB设计和布局时,应遵循一些设计准则,如规避电源干扰、保持信号完整性、合理布局元器件和线路等。
PCB流程及制程简介
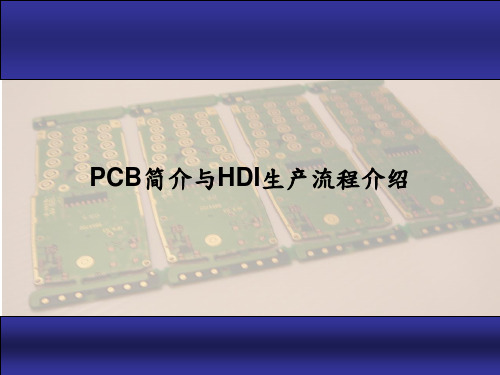
剪边(CNC裁板)-完成压合的板子其边缘都会有溢胶,必须用剪床裁掉以便在后续制程 中作业 方便及避免造成人员的伤害,剪边最好沿着边缘直线内1公分处切下,切太多会 造成电镀夹点 的困扰,最好再用磨边机将四个角落磨圆及边缘毛头磨掉,以减少板子 互相间的刮伤及对槽液 的污染。或者现在很普遍直接以CNC成型机做裁边的作业
氧化路板铜面与胶片结合强度的制程,氧化后的板子表面生成了一层黑色的绒毛层。
10.铆合
PP板
内层板
针对又可能发生的层间移动的多层板而采用 的制程。将多片已经氧化的内层线路板中间 放上夹层胶片后用铆钉将其铆合起来,讲究 正反铆、对称铆的原则。 所谓胶片是由铆钉胶合玻璃纤维布组成,它 在加热的情况下可再软化,再经加热、加压 后硬化,硬化后就不可再软化,胶片的主要 作用是作为线路板的绝缘层和粘合介质。
5. 剥锡-去除做为蚀刻阻剂的
37. 外层AOI
检测外层线路
37. 防焊绿油
用印刷机通过丝网在板表面刷上一层感光油墨,并用烤箱烤干
38. 防焊曝光
39. 防焊显影
40. 文字印刷
40. 化镍金
–其是在被催化的銅面上沉積兩層金屬的製程。利用金低接 觸電阻及不易氧化的特性,對線路提供良好的傳導及保護; 鎳層則是焊錫時之焊點並提供銅金中間緩衝層,避免銅和金 互相的擴散或遷移。
同内层2 为得到良好质量的蚀刻图形,就要确保抗蚀层与基板 表面牢固的结合,要求基板表面无氧化层、油污、灰尘、指印 以及其他的污物。因此在涂布抗蚀层前首先要对板进行表面清 洗并使铜箔表面达到一定的粗化层度
19.干膜压膜
在板表面加热后贴一层感光贴膜,为曝光准备
20.干膜曝光
同4内层曝光
21.次外层显影 22 .AOI 23.棕化 24.叠合 25. 压合 26. x-ray定位孔 27.修边
PCB成型制程介绍
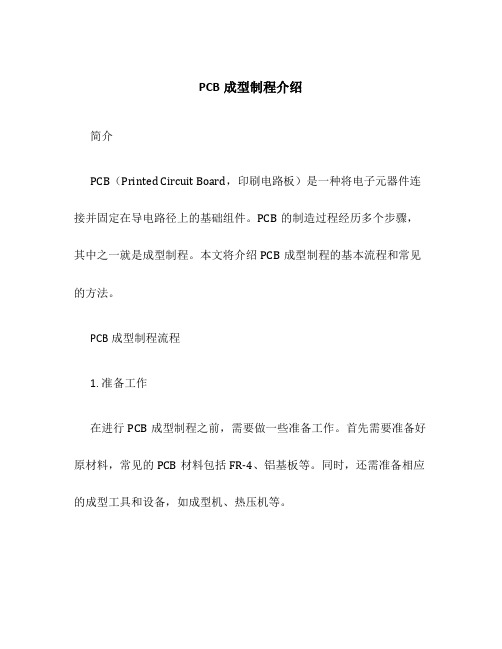
PCB成型制程介绍简介PCB(Printed Circuit Board,印刷电路板)是一种将电子元器件连接并固定在导电路径上的基础组件。
PCB的制造过程经历多个步骤,其中之一就是成型制程。
本文将介绍PCB成型制程的基本流程和常见的方法。
PCB成型制程流程1. 准备工作在进行PCB成型制程之前,需要做一些准备工作。
首先需要准备好原材料,常见的PCB材料包括FR-4、铝基板等。
同时,还需准备相应的成型工具和设备,如成型机、热压机等。
2. 色板制作色板制作是PCB制程的第一步,它用于制作出PCB中的导线层。
色板通常由铜材料制成,通过化学腐蚀或机械加工的方式形成导线图案。
3. 铺铜层铺铜层是为了增加PCB的导电性能。
铜层可以通过压铜、电镀等方式添加在色板上,形成一个可导电的层。
4. 成型成型是PCB制程中的关键步骤之一,它通过加热和施加压力将PCB 材料压制成所需的形状。
不同的成型工艺有不同的方法,下面将介绍常见的两种成型方法。
(1) 热压成型热压成型是一种常见的PCB成型方法。
它使用热压机将PCB材料加热到一定温度,然后施加一定的压力,使其在模具的作用下变形成所需的形状。
这种方法可以在较短的时间内实现高质量的成型效果。
(2) 塑料注塑成型塑料注塑成型是另一种常见的PCB成型方法。
它使用注塑机将熔化的塑料注入到模具中,然后在高压下使其冷却和固化成为所需的形状。
这种方法适用于需要复杂形状的PCB成型,但时间和成本相对较高。
5. 钻孔钻孔是为了在PCB上开孔以供电子元器件的焊接。
钻孔工艺有自动和手动两种,通常使用钻针将孔钻出。
电镀是一种常见的PCB制程方法,它通过将金属沉积在PCB上来提高其导电性和耐蚀性。
电镀通常使用电解沉积的方式进行,常见的金属包括铜、金、锡等。
7. 丝网印刷丝网印刷是一种用于印刷PCB上的标记、文字或图案的方法。
它通过在PCB上放置一个丝网模板和墨水,然后用刮刀将墨水刮平,形成所需的标记。
PCB制作工艺流程简介
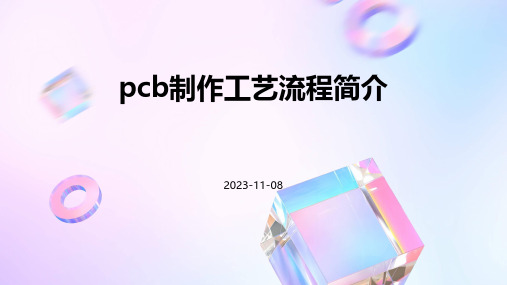
2023-11-08•pcb制作概述•pcb设计•pcb制作的前期准备•pcb制作过程•pcb制作完成后的处理目•pcb制作中的注意事项及常见问题•pcb制作的发展趋势及未来展望录01 pcb制作概述pcb基本概念Printed Circuit BoardPCB是印刷电路板,是一种用于将电子器件连接在一起的基板,通常由绝缘材料制成。
电路板组成PCB通常由导电层、绝缘层和支撑层组成,其中导电层用于传输电信号,绝缘层用于隔离导电层,支撑层则用于支撑整个电路板。
设计电路图制作裸板光绘与刻板将铜箔粘贴在绝缘材料上,形成导电层。
使用光绘机将电路图绘制在铜箔上,形成电路图形。
03pcb制作流程简介02 01根据产品需求,使用EDA设计软件绘制电路图。
通过蚀刻工艺将不需要的铜箔去除,形成所需的电路图形。
蚀刻与去膜在电路导线上沉积一层锡/金,以提高导电性能和耐腐蚀性。
沉锡/金在电路板上涂抹阻焊剂,以防止焊接时短路。
印阻焊剂对电路板进行成型和钻孔加工,以满足实际应用需求。
成型与钻孔pcb制作流程简介实现电子设备的小型化和高效化PCB是实现电子设备内部器件连接的关键部件,其制作质量直接影响到电子设备的性能和可靠性。
pcb制作的重要性保障电子设备的稳定性和安全性PCB的制作质量直接关系到电子设备的稳定性和安全性,因为一旦出现短路或信号干扰等问题,就可能导致设备故障或损坏。
提升电子设备的品质和降低成本优秀的PCB制作工艺可以提高电子设备的品质和性能,同时降低制作成本和时间成本,提高市场竞争力。
02 pcb设计03优化板型结构PCB设计应优化板型结构,提高电路板的机械强度、电气性能和散热性能。
pcb设计基本原则01确保电路功能正常PCB设计应确保电路的功能正常,满足原始电路设计的要求。
02减少信号干扰为了减少信号干扰,PCB设计应尽量选择低噪声的器件,同时避免器件之间的相互干扰。
pcb设计流程PCB检查与优化对设计好的PCB进行检查,确保没有错误和不合理的地方,并进行优化改进。
pcb制程简介-备课讲稿

06
pcb制程案例分析
ห้องสมุดไป่ตู้
案例一:某公司pcb制程改造案例
1 2 3
背景介绍
某公司在进行pcb生产时遇到了诸多问题,如生 产效率低下、产品质量不稳定等,需要进行制程 改造。
改造内容
通过对原有制程进行分析,该公司引入了新的生 产设备和工艺,对原有的浸锡、清洗等环节进行 了优化。
废弃物处理问题
总结词
废弃物的处理是PCB制程中不可避免的问题,如何有效地处理这些废弃物是PCB企业需要解决的重要问题。
详细描述
在PCB制程中,会产生大量的废弃物,包括废水、废气、废渣等。这些废弃物不仅会对环境造成污染,还会对操 作人员的身体健康造成危害。因此,需要采取有效的措施来处理这些废弃物,如建立废弃物处理设施、加强废弃 物分类和回收等。
电路板结构
PCB由基板、导电层和绝缘层构成,其中导电层是用于连接电子元 件的金属层,而绝缘层则是用于隔离导电层的非金属层。
电路板类型
根据使用需求,PCB可分为单面板、双面板、多层板等不同类型。
pcb制程的必要性
实现电子设备的小型化和轻量化
01
PCB可以将电子元件连接起来,实现特定功能,从而降低了设
。
特点
适用于大批量生产,可控制电路图 形和连接点大小,但电镀溶液需要 定期处理。
步骤
将PCB放入电镀溶液中,通过电流 作用实现金属沉积。
喷射镀(spray plating)
定义
通过喷射方式将金属颗粒附着在PCB上形成电路 和元件连接点。
特点
适用于小批量生产,可快速制造复杂电路图形, 但金属附着不均匀。
随着技术的发展,出现了 半自动的PCB制程设备, 提高了生产效率。
PCB各工序知识介绍

PCB各工序知识介绍PCB(Printed Circuit Board)是电子产品中不可或缺的一个组成部分,它承载着电子元器件,并提供了连接和支持这些元器件所需的电路。
在PCB制造的过程中,有多个关键的工序需要进行,以确保PCB的质量和可靠性。
接下来将详细介绍各个PCB工序的知识。
1.原材料准备:PCB的主要原材料是铜箔和基板。
铜箔作为PCB的导电层,负责连接电子元器件。
而基板则提供了支持和固定元器件的平台。
在原材料准备阶段,需要对铜箔进行切割和整平,以及对基板进行加工和预处理。
2.印制制作:在印制制作工序中,需要使用特殊的设备将电路图案打印到基板上。
这通常通过使用光刻技术和蚀刻技术来实现。
首先,将电路图案通过光阻材料覆盖在基板上,然后通过光刻曝光将电路图案暴露出来。
最后,使用蚀刻液将未覆盖的铜箔部分蚀刻掉,从而形成电路。
3.钻孔和插件:在钻孔和插件阶段,需要在PCB上钻孔来安装连接器和其他组件。
首先,根据设计要求在特定位置进行钻孔。
然后,使用钢钻头将孔径扩大,并进行外层导电层的拍孔。
最后,通过钻孔加工进行多孔插件,以容纳各种组件。
4.金属化和保护:金属化和保护工序是为了提高PCB的导电性能和保护电路。
首先,将电路表面进行金属化处理,通常是通过镀金或镀锡来实现。
这样可以增强电路的导电性能,并提供耐腐蚀的保护层。
然后,通过打印或喷涂方式施加保护层,如防焊膜、阻焊膜和丝印标识,以保护电路免受外界环境的侵害和损坏。
5.焊接和装配:在焊接和装配阶段,将电子元器件与PCB进行连接。
这个过程通常是通过使用焊锡来实现的。
首先,在PCB上涂上焊膏,并将元器件放置在正确的位置上。
然后,通过加热焊接区域,使焊膏熔化并形成连接。
最后,通过质量检测,确保焊接的质量和可靠性。
6.电测试和品质检验:在PCB制造的最后阶段,需要进行电测试和品质检验,以确保PCB的功能和质量。
电测试包括测试电路的连通性、导通和绝缘性能。
品质检验则包括外观检查、尺寸测量、绝缘电阻测试等。
比较全的PCB生产工艺流程介绍

比较全的PCB生产工艺流程介绍PCB(Printed Circuit Board)是现代电子产品中不可或缺的一部分,它起到了组织电子元件、连接电路的作用。
下面是一个较全的PCB生产工艺流程介绍。
1.原料准备:PCB生产的原材料主要包括基板材料、导电层材料、覆盖层材料以及焊接材料等。
各种材料需要经过质量检验和筛选。
2.设计:PCB的设计一般是通过电脑辅助设计(CAD)软件进行的。
在设计过程中,需要考虑电路布局、元件安装位置、线路走向等因素。
3.版图制作:根据PCB设计图,进行版图制作。
版图制作包括各种工艺参数的设置,如层间距、线宽、线间距等。
4.印制制作:通过光刻工艺,将设计的电路图形透过掩膜映射到基板上,涂覆光敏化剂,并暴光照射,形成导电图形。
5.蚀刻:将覆盖着光敏化剂的基板浸入蚀刻液中,通过化学反应去除未曝光的光敏化剂,暴露出需要保留的导电层。
6.电镀:在蚀刻后的导电层上进行金属电镀,一般使用铜。
铜层的厚度和均匀性对PCB的性能有重要影响。
7.钻孔:根据PCB设计要求,在特定位置进行钻孔。
钻孔通常使用电脑控制的机械钻床进行。
8.电镀:进行表面处理,保护导电层不被氧化。
常用的表面处理方法包括阻焊、镀金、喷锡等。
9.特殊工艺:一些PCB可能需要特殊的工艺,如层压、压线、贴膜等。
这些工艺的目的是提高PCB的性能和可靠性。
10.组件装配:将PCB上的元件进行焊接,通常使用锡膏和热风或烙铁进行。
11.测试:对PCB进行测试,确保其正常工作。
常见的测试方法有连通性测试、功能性测试等。
12.包装和发货:将已经测试过的PCB进行包装,并按照订单要求进行发货。
总结:以上是一个较全的PCB生产工艺流程介绍。
PCB生产工艺复杂,需要多个环节的配合和准确的操作。
每个环节都非常重要,影响着PCB的质量和可靠性。
随着技术的不断进步,PCB生产工艺也在不断改进,以满足不断变化的市场需求。
PCB板生产工艺和制作流程详解

PCB板生产工艺和制作流程详解1. 设计:PCB板的设计是整个制作流程的第一步。
设计师根据电路原理图进行PCB板的布线设计,确定电子元件的安装位置和连接方式。
2. 确定材料:根据设计要求,确定PCB板的基板材料。
常用的基板材料有FR-4玻璃纤维胶片、铝基板、陶瓷基板等。
3. 印制电路:在基板上通过化学腐蚀或机械加工的方法,将设计好的电路图案印制到基板表面。
这一步通常使用光刻技术,将电路图案转移到光刻胶上,然后在化学溶液中去除未曝光的部分。
4. 镀金属化:PCB板上的电路图案通常需要镀上一层金属,以增加导电性。
通常使用的金属化方法包括电镀、喷镀等。
5. 安装元件:在PCB板上进行元件的安装,通常采用表面贴装技术(SMT)或插件式焊接技术。
6. 焊接:通过波峰焊接、回流焊接或手工焊接等方法,将元件与PCB板焊接在一起。
7. 清洗和检验:清洗焊接后的PCB板,去除残留的焊膏和污垢。
然后进行电测试和可视检查,确保PCB板的质量。
8. 包装:对已经检验合格的PCB板进行包装,便于运输和存储。
PCB板的生产工艺和制作流程是复杂而精细的,每一个步骤都需要高度的专业知识和技术。
随着电子技术的发展,PCB板的制作工艺也在不断地更新和完善,以适应更多样化的电子产品需求。
PCB板(Printed Circuit Board)是一种用于支撑和连接电子元件的导电板。
PCB板是现代电子设备中必不可少的部分,它们被广泛应用于手机、计算机、汽车电子、医疗设备等各个领域。
生产PCB板的工艺和制作流程包括以下几个步骤:1. 设计:PCB板的设计是整个制作流程的第一步。
设计师根据电路原理图进行PCB板的布线设计,确定电子元件的安装位置和连接方式。
设计师需要考虑电路的复杂度、电路板的尺寸以及元件的布局等因素,以确保电路的性能和可靠性。
2. 确定材料:根据设计要求,确定PCB板的基板材料。
常用的基板材料有FR-4玻璃纤维胶片、铝基板、陶瓷基板等。
PCB全制程及相关基础知识介绍

VRS确认: 全称为Verify Repair Station,确认系统
目的: 通过与AOI连线,将每片板子的测试资料传给V.R.S,并由 人工对AOI的测试缺点进行确认
注意事項: VRS的确认人员不光要对测试缺点进行确认,另外就是对 一些可以直接修补的确认缺点进行修补
压板
棕化
铆合
叠板
压膜(LAMINATION): 目的: 将经处理之基板铜面透过热压 方式贴上抗蚀干膜 主要原物料:干膜(Dry Film) 溶劑顯像型 半水溶液顯像型 干膜 鹼水溶液顯像型 水溶性乾膜主要是由於其組成 中含有機酸根,會與強碱反應 使成為有機酸的鹽類,可被水 溶掉。
压膜前
压膜后
曝光(EXPOSURE): 目的: 经光源作用将原始底片上的图像转 移到感光底板上
UV光
主要原物料:底片 内层所用底片为负片,即白色透光部 分发生光聚合反应, 黑色部分则因 不透光,不发生反应(白线黑底),外 层所用底片刚好与内层相反,底片为 正片
曝光前
曝光后
显影(DEVELOPING): 目的: 用碱液作用将未发生化学反 应之干膜部分冲掉 主要原物料:Na2CO3 使用将未发生聚合反应之干 膜冲掉,而发生聚合反应之 干膜则保留在板面上作为蚀 刻时之抗蚀保护层
VRS确认
目的: 对内层生产板进行检查,挑出异常板并进行处理 收集品质资讯,及时反馈处理,避免重大异常发生
CCD冲孔:
目的: 利用CCD对位冲出检验作业之定位孔及铆钉孔 主要原物料:冲头 注意事项: CCD冲孔精度直接影响铆合对准度,故机台精度定期确认非 常重要
PCB生产流程介绍
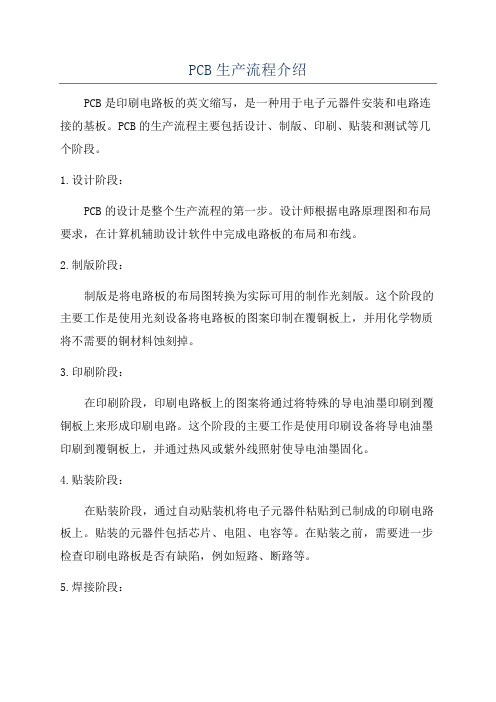
PCB生产流程介绍PCB是印刷电路板的英文缩写,是一种用于电子元器件安装和电路连接的基板。
PCB的生产流程主要包括设计、制版、印刷、贴装和测试等几个阶段。
1.设计阶段:PCB的设计是整个生产流程的第一步。
设计师根据电路原理图和布局要求,在计算机辅助设计软件中完成电路板的布局和布线。
2.制版阶段:制版是将电路板的布局图转换为实际可用的制作光刻版。
这个阶段的主要工作是使用光刻设备将电路板的图案印制在覆铜板上,并用化学物质将不需要的铜材料蚀刻掉。
3.印刷阶段:在印刷阶段,印刷电路板上的图案将通过将特殊的导电油墨印刷到覆铜板上来形成印刷电路。
这个阶段的主要工作是使用印刷设备将导电油墨印刷到覆铜板上,并通过热风或紫外线照射使导电油墨固化。
4.贴装阶段:在贴装阶段,通过自动贴装机将电子元器件粘贴到已制成的印刷电路板上。
贴装的元器件包括芯片、电阻、电容等。
在贴装之前,需要进一步检查印刷电路板是否有缺陷,例如短路、断路等。
5.焊接阶段:在焊接阶段,通过波峰焊接机将贴装完成的电子元器件与印刷电路板焊接在一起。
焊接的方法通常有浸锡法和无铅焊接法两种。
焊接完成后,需要进行视觉检测和电气性能测试,以确保焊接的质量和可靠性。
6.测试阶段:在测试阶段,对已制成的印刷电路板进行电气性能测试,以确保其功能正常。
测试方法包括功能测试、电气测试和可靠性测试等。
7.包装阶段:以上是PCB的主要生产流程介绍。
每个阶段都需要严格的操作和控制,以确保PCB的质量和性能。
同时,随着科技的进步,PCB的生产流程也在不断发展和改进,以满足日益复杂的电子产品需求。
PCB制程介绍
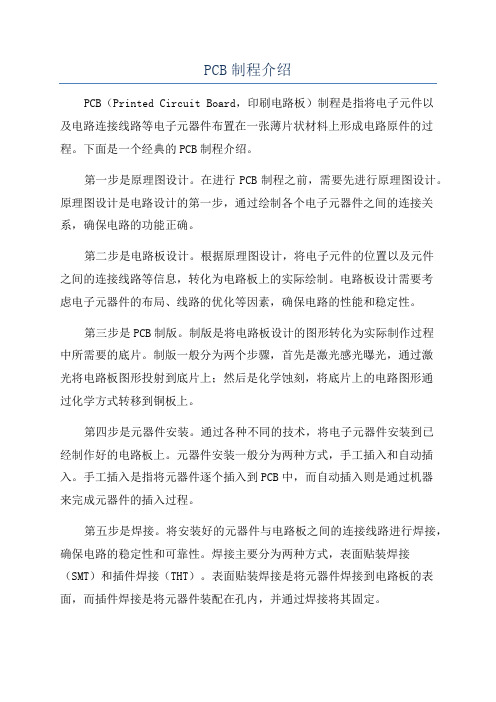
PCB制程介绍PCB(Printed Circuit Board,印刷电路板)制程是指将电子元件以及电路连接线路等电子元器件布置在一张薄片状材料上形成电路原件的过程。
下面是一个经典的PCB制程介绍。
第一步是原理图设计。
在进行PCB制程之前,需要先进行原理图设计。
原理图设计是电路设计的第一步,通过绘制各个电子元器件之间的连接关系,确保电路的功能正确。
第二步是电路板设计。
根据原理图设计,将电子元件的位置以及元件之间的连接线路等信息,转化为电路板上的实际绘制。
电路板设计需要考虑电子元器件的布局、线路的优化等因素,确保电路的性能和稳定性。
第三步是PCB制版。
制版是将电路板设计的图形转化为实际制作过程中所需要的底片。
制版一般分为两个步骤,首先是激光感光曝光,通过激光将电路板图形投射到底片上;然后是化学蚀刻,将底片上的电路图形通过化学方式转移到铜板上。
第四步是元器件安装。
通过各种不同的技术,将电子元器件安装到已经制作好的电路板上。
元器件安装一般分为两种方式,手工插入和自动插入。
手工插入是指将元器件逐个插入到PCB中,而自动插入则是通过机器来完成元器件的插入过程。
第五步是焊接。
将安装好的元器件与电路板之间的连接线路进行焊接,确保电路的稳定性和可靠性。
焊接主要分为两种方式,表面贴装焊接(SMT)和插件焊接(THT)。
表面贴装焊接是将元器件焊接到电路板的表面,而插件焊接是将元器件装配在孔内,并通过焊接将其固定。
第六步是测试和调试。
在完成元器件的安装和焊接之后,需要对整个电路进行测试和调试,确保电路的功能正常。
测试和调试主要根据电路的设计要求,对各个元器件进行测试和参数调整,以达到预定的性能要求。
第七步是包装和组装。
在测试和调试完成之后,将整个电路板进行包装和组装。
包装和组装主要是将电路板安装在相应的外壳或者机械结构中,确保电路的安全和稳定。
以上是一个经典的PCB制程介绍。
PCB制程是电子产品制造的重要环节,通过合理的制程设计和执行,可以保证电路的性能和可靠性,同时也能提高产品的制造效率和降低成本。
PCB工艺流程全面介绍

PCB工艺流程全面介绍Printed Circuit Board(PCB)是一种用于支持电子组件的载体,被广泛应用于各种电子设备中。
PCB的质量和性能直接影响设备的可靠性和性能。
了解PCB的制造过程对于设计工程师和制造工程师来说都是非常重要的。
本文将全面介绍PCB 的制造工艺流程,包括设计、原料准备、成型、去电镀、印刷、表面处理、检测以及最后的组装测试等环节。
1. PCB设计PCB设计是PCB制造的第一步,设计工程师通过软件将电路图绘制到PCB板上,并做好规划布局以保证电路的良好连接和信号传输。
在设计过程中需要考虑到板子的尺寸、层数、阻抗控制、焊盘、连接孔、线宽等参数。
2. 原料准备PCB制造的原料主要包括基材、铜箔、耐热胶、光敏胶等。
基材主要有FR-4、CEM-1、CEM-3等。
铜箔用于形成线路,耐热胶用于覆盖铜箔,光敏胶用于制作外层图形。
3. 成型成型是将基材、铜箔等原料通过一系列工艺加工成为预定形状的过程。
与预设的设计文件一致。
4. 去电镀去电镀是将已经镀铜的线路上的残留铜除去,保证线路干净平整。
这个环节是PCB工艺中的关键步骤之一。
5. 印刷印刷是在PCB板上印上文字、标志或者特殊图形等内容。
通常使用丝印墨或喷印技术进行印刷。
6. 表面处理表面处理是在PCB的焊盘上涂覆一层保护层以防止氧化。
常见的表面处理方式包括HASL、金手指、沉金等。
7. 检测检测是在PCB制造的各个环节都会进行的步骤,其目的是确保PCB的质量和性能符合设计要求。
常见的检测手段包括目视检查、X射线检测、自动光学检测等方法。
8. 组装测试完成以上工艺后,PCB将进行组装测试,包括插件、焊接、功能测试等环节。
只有通过这些环节的测试,PCB才能被认为是合格的产物。
综上所述,PCB工艺流程包括设计、原料准备、成型、去电镀、印刷、表面处理、检测以及组装测试等多个环节。
每个环节都有其独特的工艺要求和关键步骤。
只有严格按照工艺流程操作,才能保证PCB的质量和性能。
PCB工艺流程简介
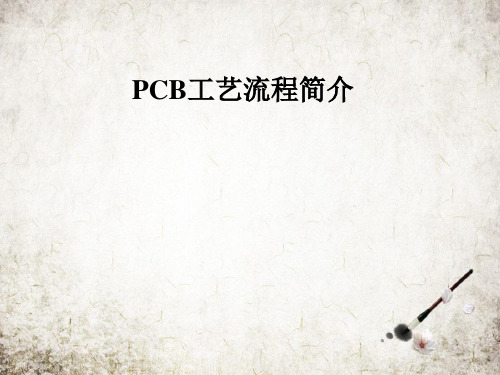
一次銅
☺ 流程介绍:
外层线路
前处理
压膜
曝光
显影
☺ 目的:
利用光化学原理,将线路图形通过以感光材料转形式移到 印制板上,形成一种抗蚀或抗电镀的掩膜图像。
外层线路
☺ 前处理(Pre-treatment):
制程目的:去除铜面上的污染物,增加铜面粗糙度,提高抗蚀或 抗电镀掩膜与板面的附着力。 主要设备:针刷磨板机 主要物料:刷轮
铜为2—4OZ的碱性直蚀板; AQ-3058:主要用于电厚镍金板。
外层线路
☺ 曝光(Exposure):
制程目的: 通过底片进行图形转移,在干膜上曝出客戶所需的线路图形。 主要设备:曝光机 主要物料:底片
➢ 外层所用底片与内层相反, 为负片,底片黑色为线路,白色 为底板(白底黑线) ➢ 白色的部分紫外光透射过去, 干膜发生聚合反应,不能被显 影液洗掉
重要的原物料:刷轮
除胶渣/化学沉铜/全板电镀
☺ 除胶渣(Desmear):
smear形成原因:鑽孔時造成的高溫超過玻璃化轉移溫度
(Tg值),而形成融熔狀,產生膠渣。
Desmear之目的:裸露出各層需互連的銅環,另膨松劑
可改善孔壁結構,增強電鍍銅附著力。
重要的原物料:KMnO4(除膠劑)
除胶渣/化学沉铜/全板电镀
☺ 目的:
将铜层厚度镀至客户所需求的厚度
镀锡
图形电镀
☺ 二次镀铜:
目的:將显影后的裸露 铜面的厚度加厚,以达到客 戶所要求的銅厚。 重要原物料:铜球、
电镀药水
乾膜
铜厚FA监控
二次銅
图形电镀
☺ 镀锡:
目的:在鍍完二次銅的 表面镀上一层锡保护,做为 蚀刻时的保护剂。 重要原物料:锡条、
PCB制程工艺简要介绍

PCB制程工艺简要介绍1. PCB(Printed Circuit Board)制程工艺简介PCB制程工艺是指将电路图设计转化成实际的电路板的过程。
在制程工艺中,通过一系列的步骤,包括设计、绘制、制造、组装和测试,将电路原型制造出来。
本文将从设计、制造和组装三个方面对PCB制程工艺进行简要介绍。
2.PCB设计PCB设计是将电路图转化为PCB板图的过程。
设计人员根据电路原理图进行布局和布线,在布局过程中,需要考虑电路元件的摆放位置、信号的传导路径、电子元器件之间的连接方式,以及电路板的尺寸等因素。
在布线过程中,需要考虑信号的走线方式、电路板的层数、电子元器件的引脚数等要素。
通过CAD软件辅助设计,生成PCB板图文件。
3.PCB制造a.基材选择:根据电路板的要求,选择合适的基材。
常用的基材有FR-4(玻璃纤维复合材料)、铝基板(采用铝作为散热材料)等。
b.压敏膜:在制造过程中,需要使用压敏膜来保护电路板。
压敏膜可以防止化学液体腐蚀、污染和物理损伤。
c.图形化:将PCB板图通过光绘技术转化为图像。
通过光敏感物质和紫外线曝光,将图形转移到覆盖在基材上的粘合剂上。
d.蚀刻:在制造中最关键的步骤之一、通过化学腐蚀的方法,将覆盖在基材上的铜层进行镀蚀,形成电路路径和金属引脚。
不需要的部分将被蚀刻掉。
e.成品分离:将制造好的电路板从基材上切割下来,形成独立的电路板。
4.PCB组装PCB组装是将元器件安装到印制线路板上的过程。
根据电路原理图和BOM表(元器件清单),选择合适的元器件,并通过自动贴片机将元器件焊接到PCB板上。
组装完成后,还需要进行一系列的测试和检查,以确保电路板的质量和可靠性。
总结:PCB制程工艺是将电路图设计转化为实际电路板的过程,涵盖了设计、制造和组装三个方面。
在设计中,通过布局和布线确定电路板的元件摆放和信号传导路径。
在制造中,通过选择合适的基材、图形化、蚀刻和成品分离等步骤,制造出电路板。
PCB工艺流程全面介绍

PCB工艺流程全面介绍1. 设计阶段PCB设计是整个PCB制造过程的第一步。
在这一阶段,工程师首先根据电路原理图进行布线设计,确定电路的连接和布局。
然后利用CAD软件完成电路板的布局设计,包括元器件的位置和连接方式等。
2. 制作阶段PCB制作包括制版、印刷、腐蚀和钻孔等工序。
首先在铜箔基板上涂覆一层光敏胶,然后将设计好的图案用UV曝光到光敏胶上,形成一个图案。
接着用化学溶剂将未曝光的部分去除,再进行铜板腐蚀,去掉多余的铜箔。
最后进行钻孔、镀锡等步骤,完成电路板的制作。
3. 检查阶段在制作完成后,需要进行丝印、检查和打磨等工序,确保电路板的质量符合要求。
同时还需要进行电气性能测试,以及外观和尺寸的检查。
4. 组装阶段组装阶段包括贴片和焊接等工序。
首先需要将元器件(如电阻、电容等)贴上PCB板上的焊盘,然后通过波峰焊或热风烙铁等方式进行焊接,固定元器件并形成电气连接。
5. 测试阶段最后需要进行电路板的功能测试,确保电路的正常工作。
如果有缺陷或问题,需要修复或更换不合格的元器件。
综上所述,PCB工艺流程包括设计、制作、检查、组装和测试等多个环节,需要严格按照流程进行,以确保电路板的质量和性能。
PCB(Printed Circuit Board)即印刷电路板,在电子产品中发挥着至关重要的作用。
PCB工艺流程的全面介绍涉及到PCB的制造和组装过程。
下文将继续介绍PCB制造和组装的详细内容。
6. 表面处理在PCB制造的过程中,常见的表面处理包括有机保护膜、喷镀油、喷镀锡等。
有机保护膜的作用是保护电路板不受环境条件的影响,防止电路板受到潮气、化学气体的侵蚀。
喷镀油的作用是在PCB表面形成一层保护膜,以提高PCB的防潮性。
而喷镀锡则是为了提高焊接操作的精度和可靠度。
7. 组装PCB组装是将已经制作好的PCB板和电子元器件组合成为功能完整的整体。
这个组装的过程有时候包括两个阶段:表面组装(SMT)和插件组装(THT)。
- 1、下载文档前请自行甄别文档内容的完整性,平台不提供额外的编辑、内容补充、找答案等附加服务。
- 2、"仅部分预览"的文档,不可在线预览部分如存在完整性等问题,可反馈申请退款(可完整预览的文档不适用该条件!)。
- 3、如文档侵犯您的权益,请联系客服反馈,我们会尽快为您处理(人工客服工作时间:9:00-18:30)。
压膜前
压膜后
8
2. 内层流程
2.3 压膜(Film lamination):
贴膜时,先从干膜上剥下聚乙烯保护膜,然后在加热加压的条件下将干膜抗蚀剂 粘贴在基板上。干膜中的抗蚀剂层受热后变软,流动性增加,借助于热压轮的压 力和抗蚀剂中粘结剂的作用完成贴膜.
压膜前
压膜中
压膜后
Dry Film Structure Base Film (PE)基膜
型号
7628 1506 2116 1080 106
胶含量
42±3% 48 ±3% 52 ±3% 62 ±3% 72 ±3%
压合厚度(inch)
0.00745 0.00619 0.00459 0.00277 0.00210
23
4. 压合流程
4.4 叠板
目的: 将预叠合好的内层板,胶片等板叠
成待压多层板的形式 主要原物料: 铜箔 电镀铜皮;按厚度可分为 1/3OZ(代号T) 1/2OZ(代号H) 1OZ(代号1) RCC(覆树脂铜皮)等
UV光 曝光前
负片底片
曝光后
10
2. 内层流程
2.4 曝光(Exposure):
干膜(dry film)的构造见右图, 1968年由杜邦公司开发出来这 种感旋旋光性聚合物的干膜 后,PCB的制作就进入另一纪元, 到1984年末杜邦的专利到期后 日本的HITACHI也有自己的品 牌问世.
目前碱水溶液显像型为主 制程步骤: 压膜─停置─曝光─停
压 力
可叠多层
热板
钢板 牛皮纸 承载盘
压合机
25
4. 压合流程
4.6 后处理
目的: 经剖半;打靶;捞边;磨边等工序对压合之多层板进行初步外形处理,以便
后工序生产品质控制要求(板厚测量等),并提供后工序加工之工具 孔(打靶时完成) 主要原物料:钻头;铣刀
剖半
X-Ray钻靶
捞边
磨边 26
5. 钻孔流程
3
1. 裁板流程
1.1 裁板介绍:
依制前设计单位,根据材料利用率等的原则, 依照制定下来的材料型号、尺寸进行选材, 裁切的过程。
主要原物料:基板;锯片 基板由铜箔和绝缘层(介电层)压合而成,依
要求有不同板厚规格,依铜厚可分为 H/H;1oz/1oz;2oz/2oz等种类,也有1/H等 基板正反面不对称铜厚的规格
2.6 蚀刻(Etch):
利用蚀刻药液,将显影后露出 的铜蚀刻掉(铜没有膜的保 护),形成内层线路图形 主要原物料:蚀刻药液 (HCl,H2O2,或者NaClO3 , H2O2)
蚀刻前
双氧水/盐酸反应式
蚀刻后
Cu+CuCl2 → 2CuCl 2CuCl+H2O2+HCl → CuCl2+2H2O 净反应: 3H2O2 + 6HCl + 3Cu → 3CuCl2 + 6H2O
干膜感光树脂层
Protection Film (PET) 保护膜
感
光
树
脂
层
干膜结构
9
2. 内层流程
2.4 曝光(Exposure):
经光源作用将原始底片上的图像转移到感光底 板上 主要原物料:底片
内层所用底片为负片,即白色透光部分,因为紫 外光可以穿透过去,干膜发生光聚合反应, 黑色 部分则因不透光, 干膜不发生反应。
补线
割线
开始
AOI扫描
不良
否
是
VRS
NG
否
是
检修或报废
续流
结束
19
4. 压合流程
4.1 压合流程:
棕化
铆合
叠板
压合
后处理
压合,是将铜箔(Copper)、胶片(Prepreg)与氧化处理后的内层线 路板压合在一起的过程。
叠合
压合结构
压合机
20
4. 压合流程
4.1 棕化:
目的: (1)粗化铜面,增加与树脂接触表面积 (2)增加铜面对流动树脂之湿润性 (3)使铜面钝化,避免发生不良反应 主要原物料:棕化药液 注意事项:棕化膜很薄,极易发生擦花问题,操作时需注意操作手势
5L
多种;
树脂据交联状况可分为:
A阶(完全未固化);B阶(半固化);C阶(完全固化)
2L
三类,生产中使用的全为B阶状态的P/P
3L
铆合后(空铆)
4L
5L 铆钉
22
4. 压合流程
4.3 铆合(铆合;预叠)
PP(Prepreg,半固化片)简介,它是由玻璃布含浸树脂而形成,树脂处于半固化状态, 压合加热时,树脂会转化成液体,并进一步固化。
根据生产线设备的制程能力,进行产品的排版设计,设计单位通常根据材料的最佳 利用率来决定Working panel的尺寸,以降低成本。
锯片
基板(CCL)
48“ Raw Material : Sheet Size
FR-4: 玻璃纤维+环氧树脂
纬向(非机械方向)
36“,40”,42“
5
2. 内层流程
2.1 流程介绍:
裁板
前处理
压膜
曝光
DES
底片(Art work)
利用影像转移原理制作内层线路,也是就是把底片上的图形 转移到产品上的过程。
DES为显影(Develop);蚀刻(Etch);去膜(Strip film)连线简称
6
2. 内层流程
2.2 前处理(Pre-treat):
前处理方式有刷磨,化学法 (微蚀)等 目的: 去除铜面上的污染物,增加 铜面粗糙度,以利于后续的 压膜制程 主要原物料:刷轮,硫酸-双 氧水等
Layer 1 Layer 2 Layer 3 Layer 4 Layer 5 Layer 6
24
4. 压合流程
4.5 压合
目的:通过热压方式将叠合板压成多层板,使得胶片中的树脂变成液体, 填充线路中的间隙,并把多层板牢牢地结合起来,压合过程,需要控 制温度,压力,真空度等。
主要原物料:牛皮纸;钢板
17
3. 内层检验流程
3.3 AOI检验:
全称为Automatic Optical Inspection,自动 光学检测 目的:
通过光学反射原理将图像回馈至设备处理,与 设定的逻辑判断原则或资料图形相比较,找出 缺点位置 注意事项:
由于AOI所用的测试方式为逻辑比较,一定会存 在一些误判的缺点,故需通过人工加以确认
去膜前
去膜后
干膜被移除掉
15
3. 内层检验流程
3.1 流程介绍: CCD冲孔
AOI检验
VRS确认
对内层生产板进行检验,挑出异常板并进行处理,进行检修或者报废 (X-out等),避免流到后站,增加不必要的成本。 收集品质讯息,及时反馈,分析概述,避免重大异常发生
16
3. 内层检验流程
3.2 CCD冲孔: 利用CCD对位冲出检验作业之定位孔及铆钉孔 主要原物料:冲头 注意事项: CCD冲孔精度直接影响铆合对准度,故机台精度定期确认非 常重要
置─显像
11
2. 内层流程
2.4 曝光(Exposure):
曝光机种类:
手动与自动 平行光与非平行光
非平行光与平行光的差异,平 行光可降低Under-Cut.做细 线路(4mil以下)非得用平行光 之曝光机.
LDI镭射直接曝光
镭射直接感光之设备与感光方 式.是利用特殊之感光膜 coating在板面,不需底片直接 利用镭射扫描曝光.其细线可 做到2mil以内
PCB流程
本处介绍传统通孔板PCB流程,不介绍HDI(高密度互联板)的PCB流程
一般负片流程:
发料/裁板→内层→黑棕化/压合→钻孔→ Deburr / Desmear +PTH / 一次铜→外层干膜→二次铜→防焊→加工→成型→测试→成检 → OQC →包装
一般正片流程:
发料/裁板→内层→黑棕化/压合→钻孔→ Deburr / 水平 Desmear + PTH / 水平电镀铜→正片干膜 →防焊→加工→成型→测试 →成检→ OQC →包装
5.1 生产流程
目的:在板面上钻出层与层之间线路连接的通孔,孔径通常从 0.15mm~6.5mm,其中0.15,0.2mm的相对比较少;主力钻针基本在 0.25,~0.5mm之间。
利用铆钉将多张内层板钉在一起,以避免后续
铆钉机
加工时产生层间滑移,现在也有热熔的方式把
铆钉
多层板组合在一起;
2L
更高层次的会采用Pin压合(通常14层以上);
主要原物料:铆钉;P/P
3L
P/P(PREPREG):由树脂和玻璃纤维布组成,据
4L
玻璃布种类可分为1060;1080;2116;7628等
注意事项: 避免板边巴里(Burr)影响品质(掉屑,刮伤
等),裁切后进行磨边,圆角处理 考虑材料的涨缩影响,裁切板送下制程前进行
烘烤(此根据PCB厂产品类别进行安排) 裁切须注意材料的机械方向一致的原则
4
1. 裁板流程
1.2 裁板作业:
买进来的常规材料的尺寸基本上是36*48,40*48,42*48英寸;
铜箔SEM
表面处理前
刷磨法
铜箔 绝缘层
前处理后. 内层流程
2.3压膜(Film lamination):
将经处理之基板铜面透过热压方式贴 上抗蚀干膜
主要原物料:干膜(Dry Film)
溶剂显像型 半水溶液显像型 碱水溶液显像型
水溶性干膜主要是由于其组成中含有 干膜 机酸根,会与强碱反应使成为有机酸 的盐类,可被水溶掉。
PCB制造流程简介
1
内容
1. 裁板流程 ………………….……………………………………….…..……….. 3 2. 内层流程 ………………….……………………………………..…..…...…….. 6 3. 内层检验流程 ……………….…………………………..…........................... 16 4. 压合流程 …………….……………………………………………................... 20 5. 钻孔流程 ………….………………………………………………...…..…….… 27 6. 电镀流程 ……………….………………………………………….…............... 34 7. 外层流程 ……………….…………………………..….................................. 39 8. 电镀二铜流程 ………………….…………………………………..…………… 44 9. 外层检验流程 …….……………………………………………....................... 49 10. 防焊流程 ………….…………………………………………….…..….……… 55 11. 成型流程 ……………….………………………………………………........... 67 12. 电测流程 ……………….………………………………………………........... 69 13. 表面处理流程 ……………….………………………………….……............. 74 14. 成品检验流程 ……………….…………………………..…......................... 100 15. 包装流程 ……………….…………………………..…................................ 104 16. 未来趋势 ……………….…………………………..…................................ 105