磨损的定义及分类
摩擦与磨损

表面摩擦与磨损一、摩擦与磨损的定义摩擦的定义是:两个相互接触的物体在外力的作用下发生相对运动或者相对运动趋势时,在切相面见间产生切向的运动阻力,这一阻力又称为摩擦力。
磨损的定义是:任一工作表面的物质,由于表面相对运动而不断损失的现象。
据估计消耗在摩擦过程中的能量约占世界工业能耗的30%。
在机器工作过程中,磨损会造成零件的表面形状和尺寸缓慢而连续损坏,使得机器的工作性能与可靠性逐渐降低,甚至可能导致零件的突然破坏。
人类很早就开始对摩擦现象进行研究,取得了大量的成果,特别是近几十年来已在一些机器或零件的设计中考虑了磨损寿命问题。
在零件的结构设计、材料选用、加工制造、表面强化处理、润滑剂的选用、操作与维修等方面采取措施,可以有效地解决零件的摩擦磨损问题,提高机器的工作效率,减少能量损失,降低材料消耗,保证机器工作的可靠性。
二、摩擦的分类及评价方法在机器工作时,零件之间不但相互接触,而且接触的表面之间还存在着相对运动。
从摩擦学的角度看,这种存在相互运动的接触面可以看作为摩擦副。
有四种摩擦分类方式:按照摩擦副的运动状态分类、按照摩擦副的运动形式分类、按照摩擦副表面的润滑状态分类、按照摩擦副所处的工况条件分类。
这里主要以根据摩擦副之间的状态不同分类,摩擦可以分为:干摩擦、边界摩擦、流体摩擦和混合摩擦,如图2-1所示。
图2-1 摩擦状态1、干摩擦当摩擦副表面间不加任何润滑剂时,将出现固体表面直接接触的摩擦(见图2-1a),工程上称为干摩擦。
此时,两摩擦表面间的相对运动将消耗大量的能量并造成严重的表面磨损。
这种摩擦状态是失效,在机器工作时是不允许出现的。
由于任何零件的表面都会因为氧化而形成氧化膜或被润滑油所湿润,所以在工程实际中,并不存在真正的干摩擦。
2 、边界摩擦当摩擦副表面间有润滑油存在时,由于润滑油与金属表面间的物理吸附作用和化学吸附作用,润滑油会在金属表面上形成极薄的边界膜。
边界膜的厚度非常小,通常只有几个分子到十几个分子厚,不足以将微观不平的两金属表面分隔开,所以相互运动时,金属表面的微凸出部分将发生接触,这种状态称为边界摩擦(见图2-1b)。
常见的磨损分类、定义以及它们发生的条件
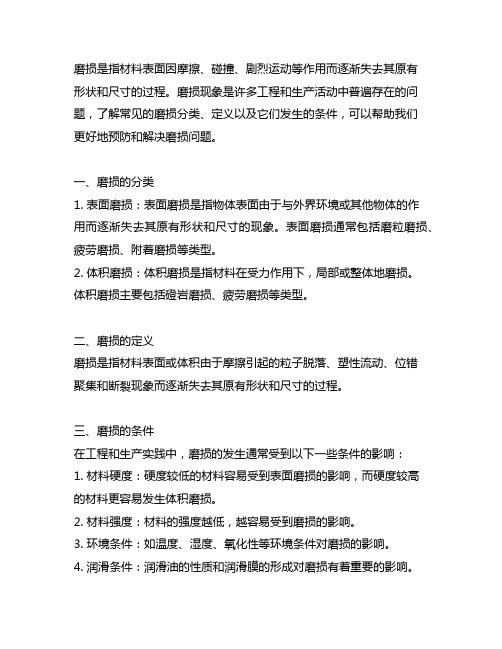
磨损是指材料表面因摩擦、碰撞、剧烈运动等作用而逐渐失去其原有形状和尺寸的过程。
磨损现象是许多工程和生产活动中普遍存在的问题,了解常见的磨损分类、定义以及它们发生的条件,可以帮助我们更好地预防和解决磨损问题。
一、磨损的分类1. 表面磨损:表面磨损是指物体表面由于与外界环境或其他物体的作用而逐渐失去其原有形状和尺寸的现象。
表面磨损通常包括磨粒磨损、疲劳磨损、附着磨损等类型。
2. 体积磨损:体积磨损是指材料在受力作用下,局部或整体地磨损。
体积磨损主要包括磴岩磨损、疲劳磨损等类型。
二、磨损的定义磨损是指材料表面或体积由于摩擦引起的粒子脱落、塑性流动、位错聚集和断裂现象而逐渐失去其原有形状和尺寸的过程。
三、磨损的条件在工程和生产实践中,磨损的发生通常受到以下一些条件的影响:1. 材料硬度:硬度较低的材料容易受到表面磨损的影响,而硬度较高的材料更容易发生体积磨损。
2. 材料强度:材料的强度越低,越容易受到磨损的影响。
3. 环境条件:如温度、湿度、氧化性等环境条件对磨损的影响。
4. 润滑条件:润滑油的性质和润滑膜的形成对磨损有着重要的影响。
5. 负载条件:负载大小和方向对磨损的发生和发展有着重要影响。
6. 表面粗糙度:表面粗糙度的大小和形状对磨损的发生和发展也有着重要的影响。
通过对常见的磨损分类、定义以及它们发生的条件的了解,我们可以更好地预防和解决磨损问题,提高材料的使用寿命和性能。
磨损是材料表面或体积由于摩擦引起的粒子脱落、塑性流动、位错聚集和断裂现象而逐渐失去原有形状和尺寸的过程。
磨损的发生对工程和生产活动而言是不可避免的,但我们可以通过控制磨损的条件和采取相应的预防措施来减少磨损带来的损失。
一、磨损的分类1. 表面磨损表面磨损是指物体表面由于与外界环境或其他物体的作用而逐渐失去其原有形状和尺寸的现象。
表面磨损主要包括以下几种类型:- 磨粒磨损:在材料表面受到磨料颗粒的作用下,材料表面的微观形貌逐渐改变,最终形成磨损痕迹。
摩擦磨损
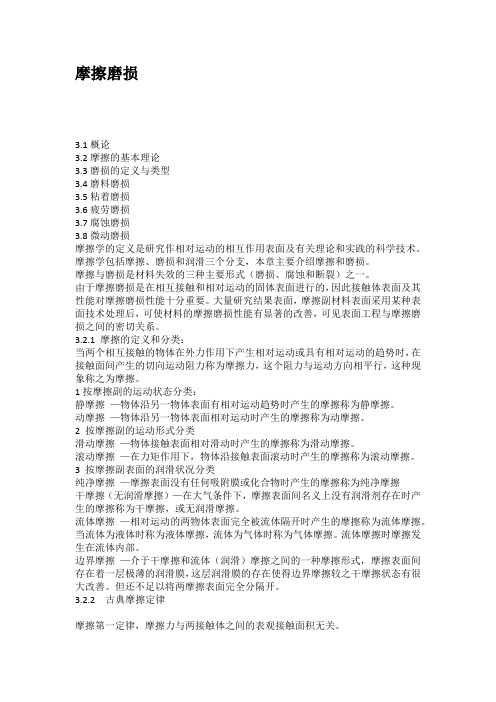
摩擦磨损3.1概论3.2摩擦的基本理论3.3磨损的定义与类型3.4磨料磨损3.5粘着磨损3.6疲劳磨损3.7腐蚀磨损3.8微动磨损摩擦学的定义是研究作相对运动的相互作用表面及有关理论和实践的科学技术。
摩擦学包括摩擦、磨损和润滑三个分支,本章主要介绍摩擦和磨损。
摩擦与磨损是材料失效的三种主要形式(磨损、腐蚀和断裂)之一。
由于摩擦磨损是在相互接触和相对运动的固体表面进行的,因此接触体表面及其性能对摩擦磨损性能十分重要。
大量研究结果表面,摩擦副材料表面采用某种表面技术处理后,可使材料的摩擦磨损性能有显著的改善,可见表面工程与摩擦磨损之间的密切关系。
3.2.1 摩擦的定义和分类:当两个相互接触的物体在外力作用下产生相对运动或具有相对运动的趋势时,在接触面间产生的切向运动阻力称为摩擦力,这个阻力与运动方向相平行,这种现象称之为摩擦。
1按摩擦副的运动状态分类:静摩擦—物体沿另一物体表面有相对运动趋势时产生的摩擦称为静摩擦。
动摩擦—物体沿另一物体表面相对运动时产生的摩擦称为动摩擦。
2 按摩擦副的运动形式分类滑动摩擦—物体接触表面相对滑动时产生的摩擦称为滑动摩擦。
滚动摩擦—在力矩作用下,物体沿接触表面滚动时产生的摩擦称为滚动摩擦。
3 按摩擦副表面的润滑状况分类纯净摩擦—摩擦表面没有任何吸附膜或化合物时产生的摩擦称为纯净摩擦干摩擦(无润滑摩擦)—在大气条件下,摩擦表面间名义上没有润滑剂存在时产生的摩擦称为干摩擦,或无润滑摩擦。
流体摩擦—相对运动的两物体表面完全被流体隔开时产生的摩擦称为流体摩擦。
当流体为液体时称为液体摩擦,流体为气体时称为气体摩擦。
流体摩擦时摩擦发生在流体内部。
边界摩擦—介于干摩擦和流体(润滑)摩擦之间的一种摩擦形式,摩擦表面间存在着一层极薄的润滑膜,这层润滑膜的存在使得边界摩擦较之干摩擦状态有很大改善。
但还不足以将两摩擦表面完全分隔开。
3.2.2 古典摩擦定律摩擦第一定律,摩擦力与两接触体之间的表观接触面积无关。
磨损及磨损理论

第一节 概 述
任何机器运转时,相互接触的零件之间都将因相对运动而产 生摩擦,而磨损正是由于摩擦产生的结果。由于磨损,将造成 表层材料的损耗,零件尺寸发生变化,直接影响了零件的使用 寿命。从材料学科特别是从材料的工程应用来看,人们更重视 研究材料的磨损。据不完全统计,世界能源的1/3~1/2消耗 于摩擦,而机械零件80%失效原因是磨损。
表表面面存存在在明明显显粘粘着着痕痕迹迹和和材材料料转转移移,,有有较较大大粘粘着着坑坑块,块在,高在速高重速 载重下载,下大,量大摩量擦摩热擦使热表使面表焊面合焊,合撕,脱撕后脱留后下留片下片片粘片着粘坑着。坑。
黏黏着着坑坑密密集集,,材材料料转转移移严严重重,,摩摩擦擦副副大大量量焊焊合合,,磨磨损急损剧急增剧加增,加, 摩摩擦擦副副相相对对运运动动受受到到阻阻碍碍或或停停止止。。 材材料料以以极极细细粒粒状状脱脱落落,,出出现现许许多多““豆豆斑斑””状状凹凹坑坑。。
所以磨损是机器最常见、最大量的一种失效方式。据调查轮,胎压联痕(SEM 邦德国在1974年钢铁工业中约有30亿马克花费在维修上,其5中000X) 直接由于磨损造成的损失占47%,停机修理所造成的损失与磨损 直接造成的损失相当,如果再加上后续工序的影响,其经济损失 还需加上10%一20%。
摩擦痕迹 (350X)
此时虽然摩擦系数增大,但是磨损却很小,材料迁移也不显著。通常 在金属表面具有氧化膜、硫化膜或其他涂层时发生轻微粘着摩损。
(2)涂抹:
粘着结合强度大于较软金属抗剪切强度,小于较硬金属抗剪切强度。 剪切破坏发生在离粘着结合面不远的较软金属浅层内,软金属涂抹在硬 金属表面。这种模式的摩擦系数与轻微磨损差不多,但磨损程度加剧。
(3)磨损比
第6章 磨损与腐蚀失效分析汇总

金属表面 发生局部 塑性变形
磨粒嵌入金属 表面,切割金 属表面
表面被 划伤
特点 • 普遍存在于机件中; • 磨损速度较大,0.5~5 μm/h 防止措施 • 提高表面硬度(从选材方面); • 减少磨粒数量(从工作状况方面)。
(3)疲劳磨损的特征及判断。 它会引起表面金属小片状脱落,在金属表 面形成一个个麻坑,麻坑的深度多在几微 米到几十微米之间。 特点 产生接触疲劳的零件表面上出现许多针状 或痘状的凹坑,称麻点,故得名麻点磨损, 亦称疲劳磨损。 接触疲劳是裂纹形成和扩展的过程。
• 在化工、石油化工、轻工、能源、交通等 行业中,约60%的失效与腐蚀有关。化工与 石油化工行业腐蚀失效所占比例更高一些。 如近年来(1995 ~ 2000年)国内先后四次对石 化企业的压力容器使用情况进行调查,其中 对失效原因调查统计认为,在使用中因腐蚀 产生严重缺陷及材质劣化,是近年来引起容 器报废的主要原因。
6.2 腐蚀失效分析
6.2.1 腐蚀及腐蚀失效 1. 腐蚀的概念
腐 蚀 介 质
耐 蚀 金 属
(1)腐蚀的定义。 • 金属与环境介质发生化学或电化学作用,导致金 属的损坏或变质。OR在一定环境中,金属表面或界 面上进行的化学或电化学多相反应,结果使金属转 入氧化或离子状态。 (2)腐蚀介质。 • 通常不把所有的介质都称为腐蚀介质。例如,空 气、淡水、油脂等虽然对金属材料均有一定的腐蚀 作用,但并不称为腐蚀介质。一般仅把腐蚀性较强 的酸、碱、盐的溶液称为腐蚀介质。
• 腐蚀不仅损耗了地球的资源,而且因腐蚀而造成 的生产停顿、产品质量下降,甚至人身事故等损 失,更是无法估量。分析、材料腐蚀及控制的研究 给予了前所未有的关注。 (2)腐蚀介质。 • 通常不把所有的介质都称为腐蚀介质。例如,空 气、淡水、油脂等虽然对金属材料均有一定的腐蚀 作用,但并不称为腐蚀介质。一般仅把腐蚀性较强 的酸、碱、盐的溶液称为腐蚀介质。
磨损的定义是什么(精)

磨损的定义是什么?1.磨粒磨损由于摩擦表面的硬质突出物或从外部进入摩擦表面的硬质颗粒,对摩擦表面起到切削或刮擦作用,从而引起表层材料脱落的现象,称为魔粒磨损。
这种磨损是最常见的一种磨损方式,应想办法减轻这种磨损发生。
为减轻磨粒磨损,除加入好的润滑油,还应当合理选择摩擦副的材料,降低表面的粗糙度值以及加装防护密度装置等。
2.黏着磨损当摩擦副受到较大压力作用时,由于表面不平,其顶峰接触点受到高压力作用而产生弹、塑性变形,附在摩擦表面的吸附膜破裂、温升后使金屑的顶峰塑性面牢固地黏着并熔焊在一起,形成冷焊结点。
在摩擦表面相对滑动时,材料便从一个表面转移到另一个表面,成为表面凸起,促使摩擦表面进一步磨损。
这种由于黏着作用引起的磨损,称为黏着磨损。
黏着磨损按程度不同分为五级:轻微磨损、涂抹、擦伤、撕脱、咬死。
如汽缸与活塞环、曲轴与轴瓦、轮齿合表面等,皆可能出现不同黏着程度的磨损。
涂抹、擦伤、撕脱又称为胶合,往往发生于高速、重载的场合。
合理低选择配对材料,采用表面处理(如表面热处理、喷镀、化学处理等),限制摩擦表面的温度,控制压强及采用含有油性极压添加剂的润滑剂等,都可以减轻黏着磨损。
3.疲劳磨损疲劳磨损(点蚀)两摩擦表面为点或线接触时.由于局部的弹性变形形成了小的接触区。
这些小的接触区形成的摩擦副如果受变化接触应力的作用,则在其反复作用下,表层将产生裂纹。
随着裂纹的扩展与相互连接,表层金属脱落,形成许多月纠‘形的浅坑,这种现象称为疲劳磨损,也称点蚀。
合理地选择材料及材料的硬度(硬度高则抗疲劳磨损能力强)。
选择黏度高的润滑油,加入极压添加剂及减小摩擦面的粗糙度值等,可以提高抗疲劳磨损的能力。
4腐蚀磨损在摩擦过程中.摩擦面与周围介质发生化学或电化学反应而产生物质损失的现象.称为腐蚀磨损。
腐蚀磨损可分为氧化磨损、特殊介质腐蚀磨损、气蚀磨损等。
腐蚀也可以在没有摩擦的条件下形成,这种情况常发生于钢铁类零件.如化工管道、泵类零件、柴油机缸套等。
刀具磨损报告作业指导

刀具磨损报告作业指导引言概述:刀具磨损是制造业中常见的问题,它直接影响着生产效率和产品质量。
为了及时识别和解决刀具磨损问题,制定刀具磨损报告作业指导是必要的。
本文将从刀具磨损的定义、原因、检测方法、解决方案以及预防措施等方面进行详细阐述。
一、刀具磨损的定义1.1 刀具磨损的概念:刀具磨损指的是刀具表面与工件接触时,由于摩擦和热量的作用,刀具表面逐渐磨损、磨蚀的过程。
1.2 刀具磨损的分类:刀具磨损可分为刀尖磨损、刀脚磨损和刀片磨损等多种类型。
1.3 刀具磨损的影响:刀具磨损会导致切削力增加、加工表面质量下降、加工精度降低等问题,从而影响生产效率和产品质量。
二、刀具磨损的原因2.1 切削温度过高:高速切削时,由于切削温度过高,刀具表面易于磨损。
2.2 切削速度过快:过高的切削速度会导致刀具表面的磨损加剧。
2.3 切削材料不匹配:切削材料与工件材料不匹配时,易导致刀具磨损。
三、刀具磨损的检测方法3.1 目视检测法:通过观察刀具表面的颜色、光泽等变化,判断刀具是否磨损。
3.2 量测检测法:采用显微镜、测微计等工具,测量刀具表面的磨损量。
3.3 动态监测法:利用传感器等设备,实时监测刀具的磨损情况。
四、刀具磨损的解决方案4.1 刀具润滑:合理选择切削液,提供良好的润滑和冷却效果,减少切削温度,降低刀具磨损。
4.2 刀具涂层:采用合适的刀具涂层,能够有效增加刀具的硬度和耐磨性,延长刀具使用寿命。
4.3 切削参数优化:合理调节切削速度、进给量和切削深度等参数,减少刀具磨损。
五、刀具磨损的预防措施5.1 定期维护:定期对刀具进行清洁、润滑和检查,及时更换磨损严重的刀具。
5.2 刀具贮存:正确存放刀具,避免刀具之间的相互碰撞和受潮等问题,保证刀具的质量。
5.3 刀具选择:根据工件材料和加工要求,选择合适的刀具材料和结构,提高刀具的耐磨性和切削效率。
结论:刀具磨损是制造业中常见的问题,但通过正确的刀具磨损报告作业指导,可以及时识别和解决刀具磨损问题。
摩擦学第五章磨损ppt课件
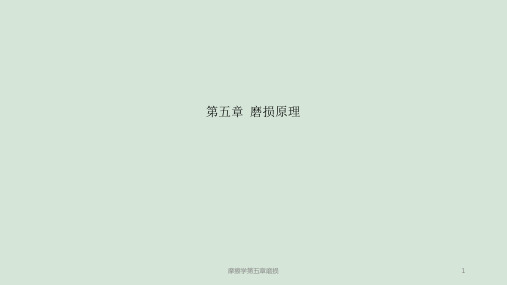
实际的磨损现象大都是多种类型磨损同时存在;或磨损状态随工 况条件的变化而转化。
摩擦学第五章磨损
9
第二节 粘着磨损
一、定义及其过程
1、定义:
(1) 在摩擦副中,相对运动的摩擦表面之间,由于粘着现象产生材料转移
此外,磨损率与滑动速度无关。
摩擦学第五章磨损
22
金属的粘着磨损的磨损系数
润滑状况 相同 无润滑 15X10-4
金属/金属
相容
部分相容和 部分不相容
不相容
金属/ 非金属
5X10-4
1X10-4 0.15X10-4 1.7X10-6
润滑不良 30X10-5 10X10-5
润滑良好 润滑极好
30X10-6 10X10-7
假定磨屑半径 ,产生磨屑的概率 ,则滑动 距离磨损体积:
摩擦学第五章磨损
21
分析
粘着磨损的体积磨损率与法向载荷N (或正压力p)成正比,而与软金属材 料的屈服强度(或布氏硬度HB值)成反比。
当正压力
时,会使磨损加剧,产生胶合或咬死。
因此,在设计时应保证正压力不超过材料的布氏硬度的三分之一。
体积磨损率随着粘着磨损的磨损系数的增大而增大,而后者主要取决于摩 擦表面的润滑状况和两滑动金属相互牢固地粘着的趋向。
相溶性好的材料 材料塑性越高,粘着磨损越严重
脆性材料的抗粘着能力比塑性材料高 脆性材料:正应力引起,最大正应力在表面,损伤浅, 磨屑也易脱落,不堆积在表面。 塑性材料:剪应力引起,最大剪应力离表面某一深度, 损伤深。
摩擦学第五章磨损
25
三、防止和减轻粘着磨损的措施
磨损及磨损理论

粘着结合强度比两基体金属的抗剪强度都高,切应力高于粘着结合强度。 剪切破坏发生在摩擦副金属较深处,表面呈现宽而深的划痕。
此时表面将沿着滑动方向呈现明显的撕脱,出现严重磨损。如果滑动继 续进行,粘着范围将很快增大,摩擦产生的热量使表面温度剧增,极易出现 局部熔焊,使摩擦副之间咬死而不能相对滑动。 这种破坏性很强的磨损形式,应力求避免。
所以磨损是机器最常见、最大量的一种失效方式。据调查, 轮胎压痕(SEM 5000X) 联邦德国在1974年钢铁工业中约有30亿马克花费在维修上,其中 直接由于磨损造成的损失占47%,停机修理所造成的损失与磨损 直接造成的损失相当,如果再加上后续工序的影响,其经济损失 还需加上10%一20%。
摩擦痕迹 (350X)
1.6
磨损过程的一般规律:
1、磨损过程分为三个阶段:
表面被磨平, 实际接触面 积不断增大, 表面应变硬 化,形成氧 化膜,磨损 速率减小。
随磨损的增长,磨耗 增加,表面间隙增大, 表面质量恶 化,机件快速失效。
斜率就是磨损速率,唯一稳定值; 大多数机件在稳定磨损阶段(AB 段)服役; 磨损性能是根据机件在此阶段 的表现来评价。
(3)磨损比
冲蚀磨损过程中常用磨损比(也有称磨损率)来度 量磨损。
Hale Waihona Puke 材料的冲蚀磨损量(g或μ m 3) 磨损比= 造成该磨损量所用的磨料量(g)
它必须在稳态磨损过程中测量,在其它磨损阶段 中所测量的磨损比将有较大的差别。 不论是磨损量、耐磨性和磨损比,它们都是在一 定实验条件或工况下的相对指标,不同实验条件或 工况下的数据是不可比较的。
当材料产生塑性变形时,法向载荷W与较软材料的屈服极限σy之间的关系:
(1)
当摩擦副产生相对滑动,且滑动时每个微凸体上产生的磨屑为半球形。 其体积为(2/3)πa3,则单位滑动距离的总磨损量为:
简述磨损的概念及减少零件磨损的措施

简述磨损的概念及减少零件磨损的措施磨损是一种涉及物体局部形状发生变化的过程,在很多物理活动中都有其存在。
磨损的定义是指介质的摩擦、压缩、剪切、扩展等活动对接触表面产生的影响,使当前物体表面形状发生变化。
本文旨在简要介绍磨损概念及减少零件磨损的相关措施。
一、磨损概念磨损本身是一种自然现象,是指物体表面局部或整体形状发生变化的不可逆转的结果。
主要分为可预测磨损和不可预测磨损。
可预测磨损是指其影响因素可以用数学模型表达,磨损量可以根据因素来计算和推断的磨损;不可预测磨损是指由于系统的复杂性而无法用数学模型表达其影响因素,无法根据因素预测磨损量。
二、减少零件磨损的措施1.选择正确的材料使用正确的材料对减少零件磨损具有重要作用,选用适当的摩擦系数、抗磨性、耐热性、耐化学腐蚀性等参数的材料更有利于减少零件磨损。
2.采用调整载荷来减少磨损调整载荷是指在物体接触运动、压缩变形等物理状态下,把一定的载荷放在接触表面,以改变表面形状及摩擦能量,从而减少摩擦和磨损。
3.改善表面改善表面是把摩擦剂和表面镀层应用在零件表面,使表面更光滑,以改善摩擦条件,从而有效减少零件的磨损。
4.采用滑动支撑采用滑动支撑技术是将滑动支撑装在接触表面,以减少摩擦力,并使表面形状稳定,有效地减少磨损。
5.采用润滑技术润滑技术是一种利用润滑剂把接触表面涂上润滑膏,使摩擦面之间形成一层润滑油膜,以减轻接触表面之间的摩擦力,从而减少磨损。
总之,磨损是一种不可逆转的过程,要想减少磨损,就需要采取正确的对策,包括正确的选择材料、调整载荷、改善表面、采用滑动支撑、润滑技术等。
只有做到这一点,才能真正有效地减少零件磨损。
设备磨损规律与故障规律
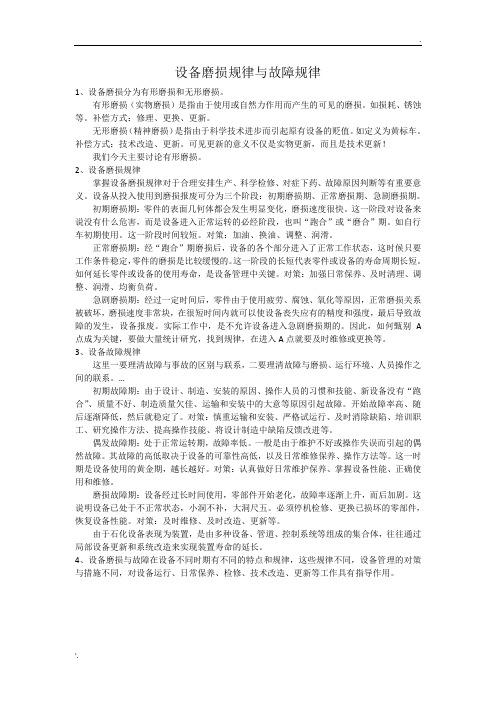
.'. 设备磨损规律与故障规律1、设备磨损分为有形磨损和无形磨损。
有形磨损(实物磨损)是指由于使用或自然力作用而产生的可见的磨损。
如损耗、锈蚀等。
补偿方式:修理、更换、更新。
无形磨损(精神磨损)是指由于科学技术进步而引起原有设备的贬值。
如定义为黄标车。
补偿方式:技术改造、更新。
可见更新的意义不仅是实物更新,而且是技术更新!我们今天主要讨论有形磨损。
2、设备磨损规律掌握设备磨损规律对于合理安排生产、科学检修、对症下药、故障原因判断等有重要意义。
设备从投入使用到磨损报废可分为三个阶段:初期磨损期、正常磨损期、急剧磨损期。
初期磨损期:零件的表面几何体都会发生明显变化,磨损速度很快。
这一阶段对设备来说没有什么危害,而是设备进入正常运转的必经阶段,也叫“跑合”或“磨合”期。
如自行车初期使用。
这一阶段时间较短。
对策:加油、换油、调整、润滑。
正常磨损期:经“跑合”期磨损后,设备的各个部分进入了正常工作状态,这时候只要工作条件稳定,零件的磨损是比较缓慢的。
这一阶段的长短代表零件或设备的寿命周期长短。
如何延长零件或设备的使用寿命,是设备管理中关键。
对策:加强日常保养、及时清理、调整、润滑、均衡负荷。
急剧磨损期:经过一定时间后,零件由于使用疲劳、腐蚀、氧化等原因,正常磨损关系被破坏,磨损速度非常块,在很短时间内就可以使设备丧失应有的精度和强度,最后导致故障的发生,设备报废。
实际工作中,是不允许设备进入急剧磨损期的。
因此,如何甄别A 点成为关键,要做大量统计研究,找到规律,在进入A点就要及时维修或更换等。
3、设备故障规律这里一要理清故障与事故的区别与联系,二要理清故障与磨损、运行环境、人员操作之间的联系。
…初期故障期:由于设计、制造、安装的原因、操作人员的习惯和技能、新设备没有“跑合”、质量不好、制造质量欠佳、运输和安装中的大意等原因引起故障。
开始故障率高、随后逐渐降低,然后就稳定了。
对策:慎重运输和安装、严格试运行、及时消除缺陷、培训职工、研究操作方法、提高操作技能、将设计制造中缺陷反馈改进等。
材料力学性能第七章金属的磨损ppt课件

➢ 根据剥落裂纹起始位置及形态不同,分为:
➢ (1) 麻点剥落(点蚀)
➢ (2) 浅层剥落
➢
(3) 深层剥落(表面压碎)
46
2. 接触应力
➢ 两物体相互接触时,在表面上产生的局部压入应力称 为接触应力,也称为赫兹应力。
➢ 线接触(齿轮)与点接触(滚珠轴承)
上图为温度对胶合磨损的影响,可以看出, 当表面温度达到临界值(约80℃)时, 磨损量 和摩擦系数都急剧增加。
17
润滑油、润滑脂的影响
在润滑油、润滑脂中加人油性或极压添加剂能提高润 滑油膜吸附能力及油膜强度,能成倍地提高抗粘着磨 损能力。
油性添加剂是由极性非常强的分子组成,在常温条件 下,吸附在金属表面上形成边界润滑膜,防止金属表 面的直接接触,保持摩擦面的良好润滑状态。
磨损是一个复杂的系统工程
6
机件正常运行的磨损过程
(a)磨损量与 时间或行程关系曲线;
(b)磨损速率与 时间或行程关系曲线
7
3. 磨损的分类方法
粘着磨损 磨粒磨损
冲蚀磨损 疲劳磨损 微动磨损 腐蚀磨损
8
§7.2 磨损模型
一、粘着磨损 1. 磨损机理 ➢定义:在滑动摩擦条件下,当摩擦副相对滑动速 度较小(钢小于1m/s)时发生的, ➢原因:缺乏润滑油,摩擦副表面无氧化膜,且单 位法向载荷很大,σ接触>σs又称咬合磨损
36
主轴转速 : 60r/min ~ 12000r/min
主轴转速示值准确度: ± 2r/min
高温炉温度范围: 室温~ 800℃;
高温炉密封性能: 在连续充入氮气(纯度
99.9%以上)的条件下,炉内 氧气含量应能达到1%以下。 最大负荷:
第三章 磨损及磨损理论
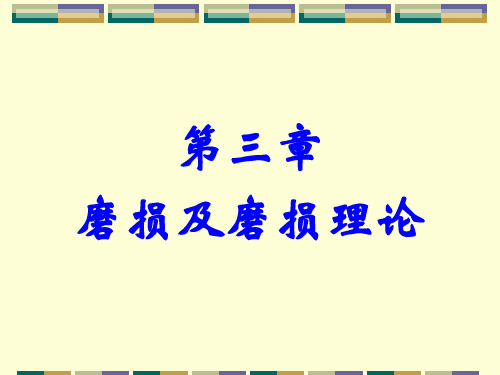
c.材料的组织结构和表面处理
多相金属比单相金属的抗粘着磨损能力高;金 属中化合物相比单相固溶体的粘着倾向小。
通过表面处理技术在金属表面生成硫化物、磷 化物或氯化物等薄膜可以减少粘着效应,同时 表面膜限制了破坏深度,提高抗粘着磨损的能 力。
d.元素周期表中的B族元素,如锗、银、镉、铟、 锡、锑、铊、铅、铋与铁的冶金相容性差,抗 粘着磨损性能好。而铁与A族元素组成的摩擦副 粘着倾向大。
b. 相同金属或冶金相溶性大的材料摩擦副易发生 粘着磨损。异种金属或冶金相溶性小的材料摩 擦副抗粘着磨损能力较高。金属与非金属摩擦 副抗粘着磨损能力高于异种金属摩擦副。
应避免使用同种金属或冶金相溶性大的金属组成 摩擦副。
冶金的相(互)溶性:两种金属能在固态互相溶解的性能。 摩擦的相(互)溶性:一定配对材料在发生摩擦和磨损时抵 抗粘着的性能。 一般,冶金相溶性好的金属摩擦副,其摩擦相溶性就差, 相同金属摩擦副,摩擦互溶性最差。
③ 速度的影响
随着滑动速度的变化,磨损类型由一种形式转变为另一种 形式。 如图(a)所示,当摩擦速度很低时,主要是氧化磨损,出 现Fe2O3的磨屑,磨损量很小。 随速度的增大,氧化膜破裂,金属的直接接触,转化为粘 着磨损,磨损量显著增大。 滑动速度再高,摩擦温度上升,有利于氧化膜形成,又转 为氧化磨损,磨屑为Fe3O4,磨损量又减小。 如摩擦速度再增大,将再次转化为粘着磨损,磨损量又开 始增加。
它们不产生切削作用,因此Ks值明显减小。
图(b)是滑动速度保持一定而改变载荷所得到的钢对钢磨
损实验结果。
载荷小产生氧化磨损, 磨屑主要是Fe2O3;
当载荷达到W0后, 磨屑是FeO、Fe2O3 和Fe3O4的混合物。 载荷超过临界载荷Wc以后, 便转入危害性的粘着磨损。
第五章 磨损的定义、分类、

1923 - 2002
一、磨损的定义
(1) 磨损是相对运动中所产生的现象,因而橡胶 表面老化、材料腐蚀等非相对运动中的现象不 属于磨损研究的范畴; (2)磨损发生在运动物体材料表面,其它非表面 材料的损失或破坏,不包括在磨损范围之内; (3) 磨损是不断损失或破坏的现象,损失包括直 接耗失材料和材料的转移(材料从一个表面转移 到另一个表面上去),破坏包括产生残余变形, 失去表面精度和光泽等。不断损失或破坏则说 明磨损过程是连续的、有规律的,而不是偶然 的几次。
单位 时间 符 号
单 位 μm或 mm mm3 g 或mg
mm3/h或 mg/h mm3/m 或mg/m
名 称
符 号
单 位
h/mm h/mg或 h/mm3 1/mm 1/mg或 1/mm3
Wl Wv 或V Ww
耐磨性
& W −1
W-1
& Wt & Wl
相对耐 磨性
ε
单位 距离
磨损的评定 冲蚀磨损率Ev=
第一节 粘着磨损的定义和分类 粘着磨损过程: 粘着磨损实际上是相互接触表面上的微凸体不断地形 成粘着结点和结点断裂而导致摩擦表面破坏并形成磨 屑的过程。 粘着磨损发生: 粘着磨损不仅在干摩擦状态下会发生,而且在边界润 滑条件下以及润滑不当时也会出现。如在齿轮、轴承 及液压元件表面等也会发生粘着磨损。 Why? 齿轮、涡轮、刀具、模具、轴承等零件的失效都与粘 着磨损有关。 粘着磨损是一种常见的磨损形式,约占磨损中 的25%。
我国仅冶金矿山、农机、煤炭、电力和建材五个部门的不完全 统计,每年仅由于磨料磨损而需要补充的备件就达100万吨钢 材,相当于15-20亿元。 耐磨钢铁件耐磨钢铁件主要用于冶金、电力、建材、建
磨料磨损
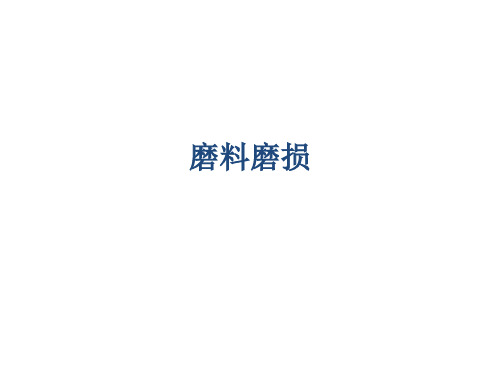
二、多次塑变导致断裂的磨损机理
(犁皱或微观压入)
✓ 当磨粒滑过表面时,除了切削外,大部分磨 粒只把材料推向前面或两旁。这些材料受到 很大的塑性形变,却没有脱离母体,同时在 沟底及沟槽附近的材料也受到较大的变形。
✓ 犁沟时一般可能有一部分材料被切削而形成 切屑,一部分则未被切削而形成塑变,被推 向两侧和前缘。
分类Ⅱ 艾弗莱,1975,磨料磨损的性质 1) 纯流体冲蚀 2) 冲击冲蚀:指流体所带的固体颗粒对金属表面进行冲击。 3) 冲刷磨损:指平行流体的硬颗粒的低应力磨料磨损。 4) 切削式磨料磨损: 5) 高应力研磨磨料磨损 6) 凿削式磨料磨损 7) 冲刷腐蚀磨损
分类Ⅲ 磨料的固定状态 1) 自由磨料 2) 固定磨料
✓ 微观切削磨损是材料表面磨损的主要机理;
✓ 磨料和表面接触时发生切削的概率不大;
✓ 磨粒形状成圆钝时,或犁沟的过程中磨粒的棱角 而不是棱边对着运动方向时,或磨粒和表面间夹 角太小,或表面材料塑性很高时,磨粒沿表面滑 过后只犁出一条沟,把材料推向两边或前面,不 形成切屑;
✓ 对于松散的自由磨粒,大约90%以上的磨粒,发 生滚动,只能压出印痕;
L H B2
4
法向载荷 被磨材料硬度
压痕直径
沟槽的截面积 沟槽深度
Ag
1 2
Bt
1 4
B2tg
L tg H
WV
Ag
S
L S tg H
被迁移的沟槽体积
单位滑动距离材料的迁移:
WV S
Ag
K1B2 K2t 2
磨粒的形状系数
表明: 单位滑动距离材料的迁移与磨沟的宽度 平方或与磨沟的深度平方成正比
✓低周应变疲劳:材料在超过其弹性极限的 周期性重复应力作用下产生的破坏现象。 扩大了“疲劳”的含义。
摩擦和磨损

的种
类
(1) 种类
对磨 损表 面外 观的 描述
磨损 机理
点蚀 磨损
胶合 磨损
擦伤 磨损
……
粘着 磨损
疲劳 磨损
冲蚀 磨损
腐蚀 磨损
磨料 磨损
……
§1-4 摩擦与磨损
2. 磨损种类 (2)磨损机理下的几种磨损及影响因素
1)粘着磨损(最普通的磨损)
当摩擦表面的不平度的尖峰相互作用的各点发生粘着后,在相对滑动时, 材料从运动副的一个表面转移到另一个表面,故而形成粘着磨损。
影响因素:①表面硬度↑,产生疲劳裂纹的危险性越小;②提高表面质量, 对零件的疲劳寿命有显著改善;③与加入的润滑油的粘度和压力有关,高 压下的润滑油能在接触区起到均化应力的作用,可提高抗疲劳磨损的能力; 油的粘度过低,则易于挤入疲劳裂缝中,在被封闭的裂缝中受高压而促进 疲劳裂纹的扩展,因此,高粘度的油有利于提高抗疲劳能力 。
影响因素:①硬度↑,耐磨性↑;
②磨粒的平均尺寸↑,磨损就越严重; ③磨粒的硬度越高,磨损就越严重。
§1-4 摩擦与磨损
2. 磨损种类
(2)磨损机理下的几种磨损及影响因素
3)疲劳磨损
当做滚动或滑动的高副受到反复作用的应力(如滚动轴承运转或齿轮传 动)时,如果应力超过材料的接触疲劳强度,就会在零件表面或一定深度 处形成疲劳裂纹,随着裂纹的扩展与相互连接,造成许多微粒从零件表面 上脱落下来,致使表面上出现许多月牙形浅坑,叫做疲劳磨损,也称疲劳 点蚀或简称点蚀。
磨损会影响机器的精度,强敌工作的可靠性,甚至促使机器提前报废。
§1-4 摩擦与磨损
1. 磨损过程
磨
损 量 Q
磨 合
稳定磨损
剧烈磨损
简述磨损

简述磨损佳木斯大学材料成型一班磨损是物体或零件相互接触并相对运动的系统的一种材料消耗现象,受摩擦工况条件,环境和材料自身因素的影响。
磨损是各种机器零部件失效的主要形式(过量变形、断裂、磨损和腐蚀)之一,了解摩擦磨损知识和抗磨材料,对正确地选择和使用材料是非常重要的。
磨损作为一种现象,普遍存在于生产和生活中,其中一类是机器零件接触导致磨损;另一类是机器在工作环境中与外界介质相接触时导致磨损。
磨损消耗着机器运转能量,缩短零部件使用寿命,造成能量和材料的消耗;此外,机器零件的接触磨损会使零部件配合间隙增大,导致噪声大、灰分或水分跑、冒、滴、漏等多种污染,导致生产环境、生活环境恶劣。
据统计,世界上能源的30%~50%消耗于摩擦和磨损。
对材料来说,约80%的零件失效是磨损引起的,在各类磨损中,磨料磨损又占有重要的地位,在金属磨损总量中占50%以上。
磨损不仅引起设备零件失效,导致工件更换和维修频繁、设备工作效率降低,而且消耗了大量的能源和材料。
为此,减少摩擦和磨损,提高资源利用效率,力争以最少的资源消耗获得最大的经济和社会收益。
由磨损定义可知,磨损是一种十分复杂的微观动态过程,影响因素甚多,因此关于磨损的分类方法也较多。
(1)按照表面接触性质不同的磨损分类:金属—磨料磨损、金属—金属磨损、金属—液体磨损;(2)按照环境和介质不同的磨损分类:干磨损、湿磨损、液体磨损;(3)按照磨损机制不同的磨损分类:磨料磨损、微动磨损、冲击磨损、接触疲劳磨损、腐蚀磨损、冲蚀磨损、粘着磨损等。
其中,磨料磨损在实际工矿中存在的形式最多,产生的材料消耗及其它经济损失最多。
1、影响磨损的因素:(1)材料性能钢中的非塑性夹杂物等冶金缺陷,对疲劳磨损有严重的影响。
如钢中的氮化物、氧化物、硅酸盐等带棱角的质点,在受力过程中,其变形不能与基体协调而形成空隙,构成应力集中源,在交变应力作用下出现裂纹并扩展,最后导致疲劳磨损早期出现。
因此,选择含有害夹杂物少的钢(如轴承常用净化钢),对提高摩擦副抗疲劳磨损能力有着重要意义。
异常磨损的定义和分类标准

异常磨损的定义和分类标准异常磨损是指机械设备在使用过程中遭受的非正常磨损现象。
正常磨损是设备在正常条件下使用后逐渐产生的损耗,而异常磨损则是由于使用条件、材料质量、操作错误、设备设计缺陷等因素引起的磨损加剧或磨损形式不正常的现象。
分类标准如下:1.磨损形式:(1)表面磨损:主要发生在设备表面的磨损,通常是由于材料之间的摩擦引起的,如摩擦磨损、磨粒磨损等。
(2)内部磨损:主要发生在设备内部的磨损,通常是由于材料内部的应力、温度和流体等因素引起的,如疲劳磨损、腐蚀磨损等。
2.磨损类型:(1)表面磨损:-磨刮磨损:主要由于磨料、硬颗粒等异物在设备表面滑动刮擦而导致的磨损,如砂粒磨损、金属屑磨损等。
-磨杂质磨损:主要由于杂质、材料缺陷等引起的磨损,如焊接缺陷磨损、夹杂物磨损等。
-氧化磨损:主要由于氧化反应导致设备表面发生氧化腐蚀而引起的磨损。
(2)内部磨损:-疲劳磨损:主要由于材料受到交变应力作用,经过一段时间后出现裂纹并扩展引起的磨损。
-腐蚀磨损:主要由于酸碱、氧化剂等介质的腐蚀作用引起的磨损。
-磨损疲劳:主要由于交变应力与材料的磨损作用相结合而导致的磨损疲劳。
3.磨损程度:(1)轻微磨损:主要表现为设备表面光洁度下降,无大面积磨损或损伤。
(2)中等磨损:设备表面出现局部明显磨损或损伤。
(3)严重磨损:设备表面出现大面积磨损或损伤,可能出现裂纹或材料脱落等现象。
4.磨损原因:(1)材料因素:材料的硬度、强度、耐磨性等性能差异导致磨损程度的差异。
(2)使用条件:设备操作温度、湿度、压力等因素对磨损速度有直接影响。
(3)操作错误:错误的操作和维护方式会导致设备磨损加剧,如润滑不及时、过度负荷运转等。
(4)设备设计缺陷:设备在设计阶段存在的设计不合理、结构缺陷等问题可能导致异常磨损。
(5)环境因素:环境中的粉尘、腐蚀性气体、湿度等因素也会引起设备异常磨损。
总结起来,异常磨损是机械设备在使用过程中遭受的非正常磨损现象,根据磨损形式、类型、程度以及磨损原因等因素进行分类。
- 1、下载文档前请自行甄别文档内容的完整性,平台不提供额外的编辑、内容补充、找答案等附加服务。
- 2、"仅部分预览"的文档,不可在线预览部分如存在完整性等问题,可反馈申请退款(可完整预览的文档不适用该条件!)。
- 3、如文档侵犯您的权益,请联系客服反馈,我们会尽快为您处理(人工客服工作时间:9:00-18:30)。
磨损的定义及分类
磨损:是物体或零件相互接触并相对运动的系统中发生的一种现象,这种现象普遍的存在于生产生活中。
磨损消耗了机器运转的能量,使机器零部件使用寿命缩短,造成材料的消耗。
磨损的结果是零部件几何尺寸(体积)变小,零部件失去原有设计所规定的功能而失效。
失效包括完全丧失原定功能;功能降低和有严重损伤或隐患,继续使用会失去可靠性及安全性。
磨损的分类:按照表面破坏机理特征,磨损可以分为磨粒磨损、粘着磨损、表面疲劳磨损、腐蚀磨损和微动磨损等。
前三种是磨损的基本类型,后两种只在某些特定条件下才会发生。
磨粒磨损:物体表面与硬质颗粒或硬质凸出物(包括硬金属)相互摩擦引起表面材料损失。
磨粒磨损主要出现在以下两种情况:一是粗糙而坚硬的表面贴着软表面滑动;另一种情况是由游离的坚硬粒子在两个摩擦面之间滑动而产生的磨损。
粘着磨损:摩擦副相对运动时,由于固相结合作用的结果,造成接触面金属损耗,因为机械零件的表面从宏观上是光滑的,而微观尺度(从显微镜下观察)总是粗糙不平的,所以,当两个表面粘合时,受力的地方只是那些表面上比较高的凸点。
表面疲劳磨损:两接触表面在交变接触压应力的作用下,材料表面因疲劳而产生物质损失。
表面疲劳磨损是表面或亚表面中裂纹形成以及疲劳裂纹扩展的过程。
腐蚀磨损:零件表面在摩擦的过程中,表面金属与周围介质发生化学或电化学反应,因而出现的物质损失。
微动磨损:两接触表面间没有宏观相对运动,但在外界变动负荷影响下,有小振幅的相对振动(小于100μm),此时接触表面间产生大量的微小氧化物磨损粉末,因此造成的磨损称为微动磨损。
东臻科技专业解决冶金、化工、电力、钢铁等行业机械设备磨损问题,咨询电话。