配料计算及物料平衡表
物料平衡计算公式
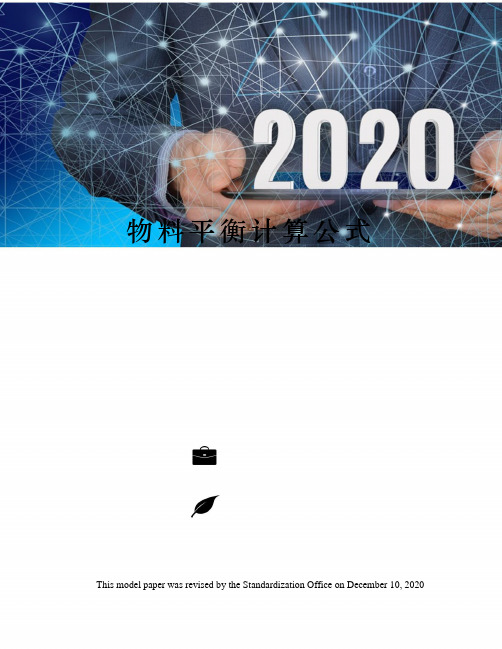
物料平衡计算公式This model paper was revised by the Standardization Office on December 10, 2020物料平衡计算公式:每片主药含量理论片重=测得颗粒主药百分含量1.原辅料粉碎、过筛的物料平衡物料平衡范围: %~100 %物料平衡= %100⨯+ac b a-粉筛前重量(kg) b-粉筛后重量(kg) c-不可利用物料量(kg)2.制粒工序的物料平衡物料平衡范围: %~ %制粒工序的物料平衡=a d cb ++×100% 制粒工序的收率=ab ×100% a-制粒前所有原辅料总重(kg) b-干颗粒总重(kg)c-尾料总重(kg) d-取样量(kg)3.压片工序的物料平衡范围: %~ %压片工序的物料平衡=ad c b ++×100% 压片工序的收率=ab ×100%a-接收颗粒重量(kg) b-片子重量(kg)c-取样重量(kg) d-尾料重量(kg)4.包衣工序的物料平衡包衣工序的物料平衡范围: %~ %包衣工序的物料平衡 = b a ed c +++包衣工序的收率 = b a c+a-素片重量(kg) b-包衣剂重量(kg) c-糖衣片重量(kg) d-尾料重量(kg) e-取样量(kg)5.内包装工序物料平衡内包装工序物料平衡范围: %~ %包材物料平衡=%100⨯++++A a dc b Ba- PTP 领用量(kg) b- PTP 剩余量(kg) A- PVC领用量(kg) B- PVC 剩余量(kg) c-使用量(kg) d-废料量(kg)片剂物料平衡=%100⨯++a dc ba :领用量(Kg)b :产出量(Kg)c :取样量(Kg)d :废料量(Kg)6.外包装工序的物料平衡包装材料的物料平衡范围:100%包装材料物料平衡=%100⨯+++ea d cb e-上批结存 a-领用量 b-使用量 c-剩余量 d-残损量7.生产成品率成品率范围:90%~102%片剂收率= %100⨯++a dc ba-计划产量 b-入库量 c-留样量 d-取样量 1.粉碎过筛和称配岗位物料平衡检查:配料量╳100% 粉碎过筛后原辅料总重(物料平衡范围应控制在~%)2.制粒干燥、整粒总混岗位物料平衡检查:总混后重量+不良品╳100%干颗粒净重+润滑剂+崩解剂(物料平衡范围应控制在~%)3.充填抛光岗位物料平衡检查:胶囊总重+细粉+不良品+废胶囊壳重量╳100%颗粒总重+胶囊壳重量(物料平衡范围应控制在~%)4.铝塑内包岗位物料平衡检查:(成品板总重/平均每板重量+不良品)×规格(粒/板)╳100%胶囊领用量/平均胶囊重(物料平衡范围应控制在~%)5.总物料平衡检查:成品产量╳100%理论产量(物料平衡范围应控制在97~100%)。
生料磨物料平衡计算
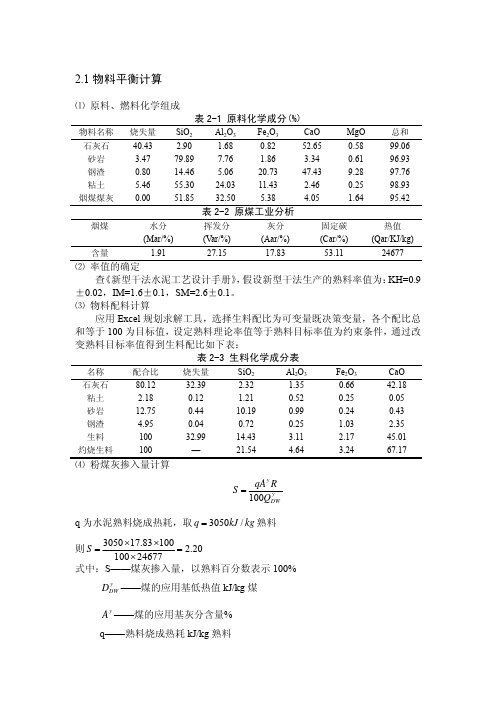
2.2 热量平衡计算
2.2.1 原始资料
表 2-6 热平衡的原始资料
名称 入磨物料水分(%) 出料物料水分(%)
入磨物料温度(℃) 出磨物料温度(℃) 入磨热气体温度(℃) 出磨热气体温度(℃)
—
SiO2 2.32 1.21 10.19 0.72 14.43 21.54
Al2O3 1.35 0.52 0.99 0.25 3.11 4.64
Fe2O3 0.66 0.25 0.24 1.03 2.17 3.24
CaO 42.18 0.05 0.43 2.35 45.01 67.17
S = qA y R 100QDyW
L——入磨热风量 Nm3 / h
C——入磨热风平均比热 kJ / Nm3 ⋅ ℃,在 0℃—450℃时为 1.435kg/ Nm 3 T1——入磨热风温度 240℃ ② 粉磨机工作时发热 Q2 = 3559ωηη1κf = 3559 × 4200 × 0.9 × 0.9 × 0.7 × 0.7 = 5932781.82kJ / h
q 为水泥熟料烧成热耗,取 q = 3050kJ / kg 熟料
则 S = 3050×17.83×100 = 2.20 100× 24677
式中:S——煤灰掺入量,以熟料百分数表示 100%
DDyW ——煤的应用基低热值 kJ/kg 煤
Ay ——煤的应用基灰分含量% q——熟料烧成热耗 kJ/kg 熟料
K钢渣 = 1.505× 4.95% = 0.0745t / t熟料
根据干料中饱含水分,湿物料的消耗定额为:
物料平衡计算表

规格:
投料量 规格
批号或生产日期:
次品量 合格量 收率(合格量/投料量×100%)
物料平衡率= 总 结 论 原 因 分 析 属正常偏差 车间部长:
异 常 偏 差 处 理
技师: 审批意见:
年ቤተ መጻሕፍቲ ባይዱ
月
日
车间部长:
年
月
日
(正常偏差时异常偏差处理栏不填)
品控员:
年
月
日
备注:
物 料 平 衡 计 算 表
SOR-SC-01-01 品名:
生产工序 和 面 半 成 品 生 产 线 半成品成型 醒发成型 烘焙 (蒸制) 成型 本批投料量① 本品取样量③ ③+④ 物料平衡率= 包装规格 投料量① 配送入库数② 留样数③ 包 装 线 残次品数④ 项目 发放数 实际使用数 报废数 收率= 销毁数 剩余数 物料平衡率 属异常偏差 年 处 理 意 见 月 日 名称 ①×规格 ×100%= ×100%= 标签及含有标签内容的包装物情况 包装膜 kg Kg Kg kg kg 包装袋 只 只 只 只 只 包装盒 只 只 只 只 只 标签 张 张 张 张 张 本批次品量② 本批实际合格产量④
高炉冶炼物料平衡计算
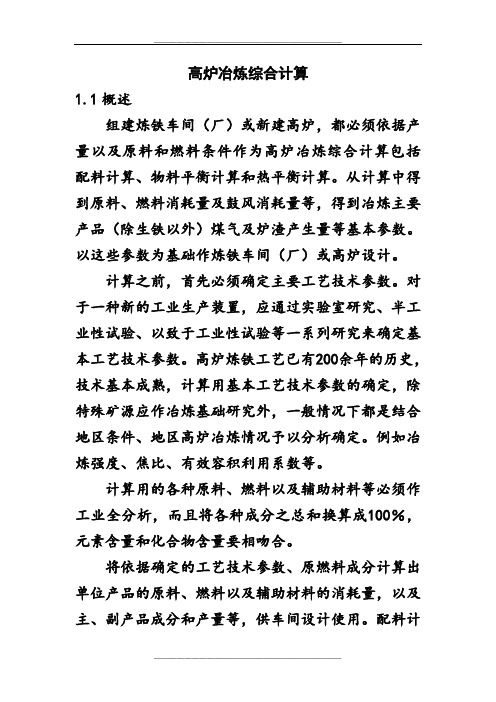
高炉冶炼综合计算1.1概述组建炼铁车间(厂)或新建高炉,都必须依据产量以及原料和燃料条件作为高炉冶炼综合计算包括配料计算、物料平衡计算和热平衡计算。
从计算中得到原料、燃料消耗量及鼓风消耗量等,得到冶炼主要产品(除生铁以外)煤气及炉渣产生量等基本参数。
以这些参数为基础作炼铁车间(厂)或高炉设计。
计算之前,首先必须确定主要工艺技术参数。
对于一种新的工业生产装置,应通过实验室研究、半工业性试验、以致于工业性试验等一系列研究来确定基本工艺技术参数。
高炉炼铁工艺已有200余年的历史,技术基本成熟,计算用基本工艺技术参数的确定,除特殊矿源应作冶炼基础研究外,一般情况下都是结合地区条件、地区高炉冶炼情况予以分析确定。
例如冶炼强度、焦比、有效容积利用系数等。
计算用的各种原料、燃料以及辅助材料等必须作工业全分析,而且将各种成分之总和换算成100%,元素含量和化合物含量要相吻合。
将依据确定的工艺技术参数、原燃料成分计算出单位产品的原料、燃料以及辅助材料的消耗量,以及主、副产品成分和产量等,供车间设计使用。
配料计算也是物料平衡和热平衡计算的基础。
依据质量守恒定律,投入高炉物料的质量总和应等于高炉排出物料的质量总和。
物料平衡计算可以验证配料计算是否准确无误,也是热平衡计算的基础。
物料平衡计算结果的相对误差不应大于0.25%。
常用的热平衡计算方法有两种。
第一种是根据热化学的盖斯定律,即按入炉物料的初态和出炉物料的终态计算,而不考虑炉内实际反应过程。
此法又称总热平衡法。
它的不足是没有反应出高炉冶炼过程中放热反应和吸热反应所发生的具体空间位置,这种方法比较简便,计算结果可以判断高炉冶炼热工效果,检查配料计算各工艺技术参数选取是否合理,它是经常采用的一种计算方法。
第二种是区域热平衡法。
这种方法以高炉局部区域为研究对象,常将高炉下部直接还原区域进行热平衡计算,计算其中热量的产生和消耗项目,这比较准确地反应高炉下部实际情况,可判断炉内下部热量利用情况,以便采取相应的技术措施。
水泥配料计算和全厂物料平衡
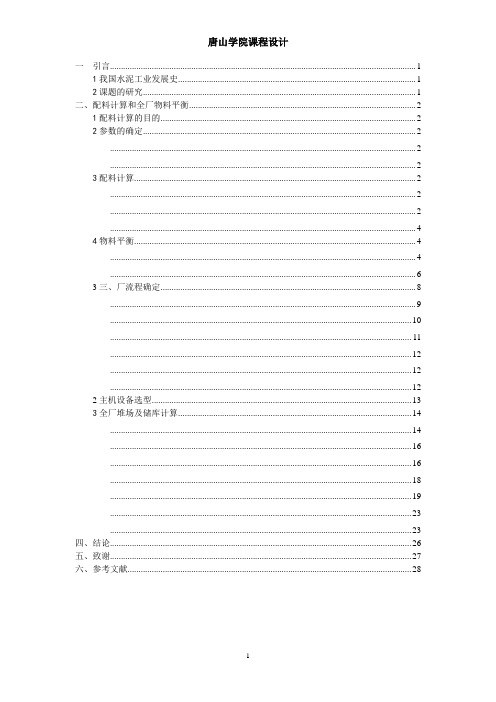
一引言 (1)1我国水泥工业发展史 (1)2课题的研究 (1)二、配料计算和全厂物料平衡 (2)1配料计算的目的 (2)2参数的确定 (2) (2) (2)3配料计算 (2) (2) (2) (4)4物料平衡 (4) (4) (6)3三、厂流程确定 (8) (9) (10) (11) (12) (12) (12)2主机设备选型 (13)3全厂堆场及储库计算 (14) (14) (16) (16) (18) (19) (23) (23)四、结论 (26)五、致谢 (27)六、参考文献 (28)一引言1我国水泥工业发展史我国是世界上的水泥生产大国,产量世界第一,但产品结构与国际市场水泥产品需求结构差距较大,其中新型干法水泥产量仅占35%,65%的水泥为落后的立窑、湿法窑和小型中空窑生产。
用新型干法水泥生产技术逐步取代传统技术,发挥产品质量高、热耗、能耗低、环保水平高等优点,已经成为世界水泥工业发展的唯一方向,水泥生产消耗大量不可再生资源和能源并对环境造成极大的破坏[1]。
2004年我国水泥总产量达到97亿吨,每年的水泥生产电耗超过800亿千瓦时,煤耗占全国煤炭总产量的10%,年消耗石灰石约7.5亿~9亿吨;另一方面,我国水泥产品的结构以325和425强度等级为主,水泥性能和混凝土的耐久性较差,混凝土工程结构常常建成10年或20年就开始大修甚至拆除重建、与其他先进国家的水平相差较大[2]。
同时,据不完全统计,我国煤炭、电力、化工等行业排出的各种废渣在7亿吨以上,粉煤灰、钢渣等都是量大、面广且利用率仍较低的大宗工业废渣。
而大量废渣的堆积不仅占用良田,部分粉尘飘入大气中污染空气,其中某些重金属或少量放射性有毒物质可能经过雨水渗入地下污染水源等造成“二次”污染。
因此,研究新型干法水泥生产工艺,实现水泥低环境负荷化和高性能化,已成为实现水泥工业可持续发展和循环经济发展的迫切任务。
以预分解窑为代表的新型干法水泥生产技术是国际公认的代表当代技术发展水平的水泥生产方法[3]。
物料平衡计算公式:
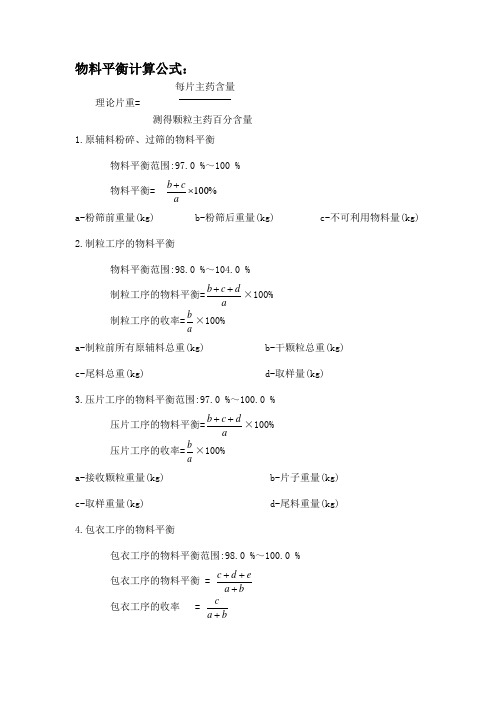
物料平衡计算公式:每片主药含量理论片重=测得颗粒主药百分含量1.原辅料粉碎、过筛的物料平衡物料平衡范围:97.0 %~100 %物料平衡= %100⨯+ac b a-粉筛前重量(kg) b-粉筛后重量(kg) c-不可利用物料量(kg)2.制粒工序的物料平衡物料平衡范围:98.0 %~104.0 %制粒工序的物料平衡=a d cb ++×100% 制粒工序的收率=ab ×100% a-制粒前所有原辅料总重(kg) b-干颗粒总重(kg)c-尾料总重(kg) d-取样量(kg)3.压片工序的物料平衡范围:97.0 %~100.0 %压片工序的物料平衡=a d cb ++×100% 压片工序的收率=ab ×100% a-接收颗粒重量(kg) b-片子重量(kg)c-取样重量(kg) d-尾料重量(kg)4.包衣工序的物料平衡包衣工序的物料平衡范围:98.0 %~100.0 %包衣工序的物料平衡 =ba e d c +++ 包衣工序的收率 =b ac +a-素片重量(kg) b-包衣剂重量(kg) c-糖衣片重量(kg) d-尾料重量(kg) e-取样量(kg)5.内包装工序物料平衡内包装工序物料平衡范围:99.5 %~100.0 %包材物料平衡=%100⨯++++Aa d cb B a- PTP 领用量(kg) b- PTP 剩余量(kg) A- PVC 领用量(kg) B- PVC 剩余量(kg) c-使用量(kg) d-废料量(kg)片剂物料平衡=%100⨯++ad c b a :领用量(Kg) b :产出量(Kg)c :取样量(Kg)d :废料量(Kg)6.外包装工序的物料平衡包装材料的物料平衡范围:100%包装材料物料平衡=%100⨯+++ea d cb e-上批结存 a-领用量 b-使用量 c-剩余量 d-残损量7.生产成品率成品率范围:90%~102%片剂收率= %100⨯++ad c b a-计划产量 b-入库量 c-留样量 d-取样量1.粉碎过筛和称配岗位物料平衡检查:配料量╳100%粉碎过筛后原辅料总重(物料平衡范围应控制在99.8~100.2%)2.制粒干燥、整粒总混岗位物料平衡检查:总混后重量+不良品╳100%干颗粒净重+润滑剂+崩解剂(物料平衡范围应控制在99.0~100.0%)3.充填抛光岗位物料平衡检查:胶囊总重+细粉+不良品+废胶囊壳重量╳100%颗粒总重+胶囊壳重量(物料平衡范围应控制在96.0~101.0%)4.铝塑内包岗位物料平衡检查:(成品板总重/平均每板重量+不良品)×规格(粒/板)╳100%胶囊领用量/平均胶囊重(物料平衡范围应控制在98.0~101.0%)5.总物料平衡检查:成品产量╳100%理论产量(物料平衡范围应控制在97~100%)。
(完整版)物料平衡计算公式:
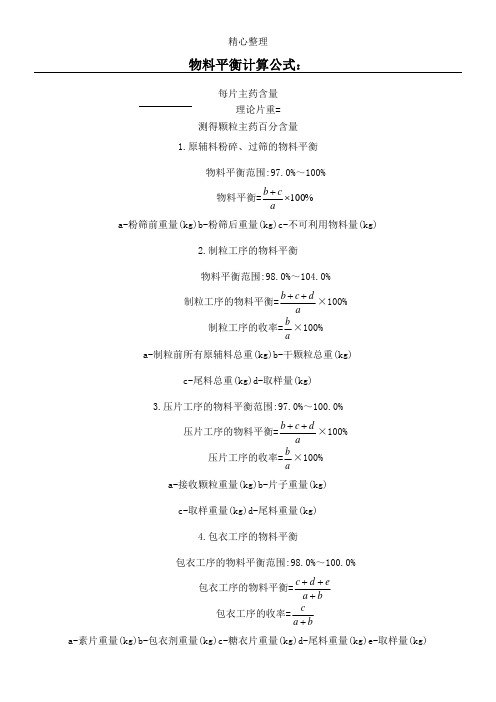
物料平衡计算公式:
每片主药含量
理论片重=
测得颗粒主药百分含量
1.原辅料粉碎、过筛的物料平衡
物料平衡范围:97.0%~100% +c b
c-取样重量(kg)d-尾料重量(kg)
4.包衣工序的物料平衡
包衣工序的物料平衡范围:98.0%~100.0%
包衣工序的物料平衡=b
a e d c +++ 包衣工序的收率=b
a c + a-素片重量(kg)b-包衣剂重量(kg)c-糖衣片重量(kg)d-尾料重量(kg)e-取样量(kg)
5.内包装工序物料平衡
内包装工序物料平衡范围:99.5%~100.0%
包材物料平衡=%100⨯++++A
a d c
b B a-PTP 领用量(kg)b-PTP 剩余量(kg)A-PVC 领用量(kg)
B-PVC 剩余量(kg)c-使用量(kg)d-废料量(kg)
片剂物料平衡=%100⨯++d c b
粉碎过筛后原辅料总重
(物料平衡范围应控制在99.8~100.2%)
2.制粒干燥、整粒总混岗位物料平衡检查:
总混后重量+不良品
╳100%
干颗粒净重+润滑剂+崩解剂
(物料平衡范围应控制在99.0~100.0%)
3.充填抛光岗位物料平衡检查:
胶囊总重+细粉+不良品+废胶囊壳重量
╳100%
颗粒总重+胶囊壳重量
(物料平衡范围应控制在96.0~101.0%)
4.铝塑内包岗位物料平衡检查:
(成品板总重/平均每板重量+不良品)×规格(粒/板)
╳100%。
物料平衡计算公式
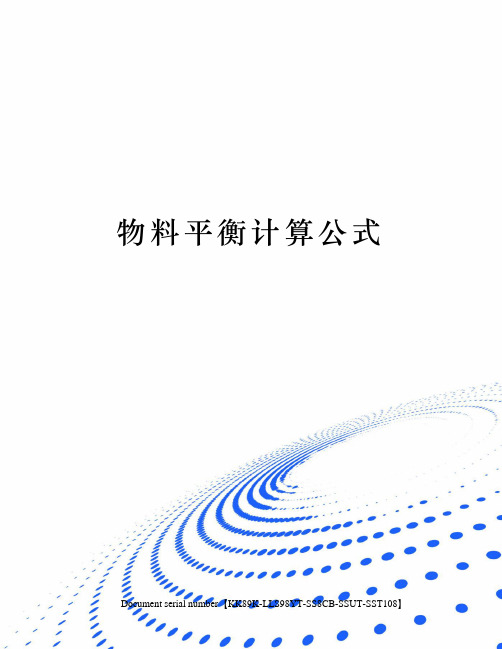
物料平衡计算公式 Document serial number【KK89K-LLS98YT-SS8CB-SSUT-SST108】物料平衡计算公式:每片主药含量理论片重=测得颗粒主药百分含量1.原辅料粉碎、过筛的物料平衡物料平衡范围:97.0%~100%物料平衡=%100⨯+ac b a-粉筛前重量(kg)b-粉筛后重量(kg)c-不可利用物料量(kg)2.制粒工序的物料平衡物料平衡范围:98.0%~104.0%制粒工序的物料平衡=a d cb ++×100% 制粒工序的收率=ab ×100% a-制粒前所有原辅料总重(kg)b-干颗粒总重(kg)c-尾料总重(kg)d-取样量(kg)3.压片工序的物料平衡范围:97.0%~100.0%压片工序的物料平衡=a d cb ++×100% 压片工序的收率=ab ×100% a-接收颗粒重量(kg)b-片子重量(kg)c-取样重量(kg)d-尾料重量(kg)4.包衣工序的物料平衡包衣工序的物料平衡范围:98.0%~100.0%包衣工序的物料平衡=b a e dc +++ 包衣工序的收率=ba c + a-素片重量(kg)b-包衣剂重量(kg)c-糖衣片重量(kg)d-尾料重量(kg)e-取样量(kg)5.内包装工序物料平衡内包装工序物料平衡范围:99.5%~100.0%包材物料平衡=%100⨯++++Aa d cb B a-PTP 领用量(kg)b-PTP 剩余量(kg)A-PVC 领用量(kg) B-PVC 剩余量(kg)c-使用量(kg)d-废料量(kg)片剂物料平衡=%100⨯++ad c b a :领用量(Kg)b :产出量(Kg)c :取样量(Kg)d :废料量(Kg)6.外包装工序的物料平衡包装材料的物料平衡范围:100%包装材料物料平衡=%100⨯+++ea d cb e-上批结存a-领用量b-使用量c-剩余量d-残损量7.生产成品率成品率范围:90%~102%片剂收率=%100⨯++ad c b a-计划产量b-入库量c-留样量d-取样量1.粉碎过筛和称配岗位物料平衡检查:配料量╳100%粉碎过筛后原辅料总重(物料平衡范围应控制在99.8~100.2%)2.制粒干燥、整粒总混岗位物料平衡检查:总混后重量+不良品╳100%干颗粒净重+润滑剂+崩解剂(物料平衡范围应控制在99.0~100.0%)3.充填抛光岗位物料平衡检查:胶囊总重+细粉+不良品+废胶囊壳重量╳100%颗粒总重+胶囊壳重量(物料平衡范围应控制在96.0~101.0%)4.铝塑内包岗位物料平衡检查:(成品板总重/平均每板重量+不良品)×规格(粒/板)╳100%胶囊领用量/平均胶囊重(物料平衡范围应控制在98.0~101.0%)5.总物料平衡检查:成品产量╳100%理论产量(物料平衡范围应控制在97~100%)。
水泥厂配料计算

一、物料平衡式:(不考虑生产损失) 1、干石灰石+干粘土+干铁粉=干生料2、灼烧石灰石+灼烧粘土+灼烧铁粉=灼烧生料=熟料3、灼烧生料+煤灰(掺入熟料中的)=熟料4、熟料的率值 KH=(C-1.65*A-0.35F)/2.8S SM=S/(A+F) IM=A/F 2.5 熟料的率值 一、石灰饱和系数: 公式:KH=232328.235.0065.1SiO O Fe Al CaO --意义:水泥熟料中的总CaO 含量扣除饱和酸性氧化物所需要的氧化钙后,所剩下的与二氧化硅化合的氧化钙的含量与理论上二氧化硅全部化合成硅酸三钙所需要的氧化钙含量的比值。
简言之。
KH 表示熟料中二氧化硅被氧化钙饱和成硅酸三钙的程度。
取值:0.87~0.96二、硅 率:公式: n(SM)= 含义: 反映了熟料中硅酸盐矿物、熔剂、矿物的相对含量。
取值: 三、铝 率:公式: p(IM)=3232O Fe O Al含义:说明熟料中C3A 、C4AF 的相对含量。
反映液相的性质。
(C3A 产生的液相粘度大;C4AF 产生的液相粘度小.) 取值:0.9~1.9 配料计算 配料方法1、尝试误差法先按假定的原料配合比计算熟料的组成。
若计算结果不符合要求,则调整原料的配合比再进行重复计算直至符合要求为止。
2、递减试凑法从假定的熟料化学成分中依次递减假定配分比的原料组分,试凑至符合要求为止。
3、酸碱滴定法根据已确定的生料碳酸盐滴定值和实际测得石灰石、粘土的滴定值按规定的公式作简单的计算,较快地得出各种原料的配合比 4、烧失量法水泥生料的烧失量一般为34~36%。
预先确定的生料烧失量数,按实测石灰石烧失量及实测粘土烧失量,计算原料的配合比。
配料计算实例已知原料、燃料的有关分析数据如表4-10、4-11,假设用窑外分解窑以三种原料配合进行生产,要求熟料的三个率值为:KH =0.89±0.02、SM =2.1±0.1、IM =1.3±0.1,单位熟料热耗为q=3350kj/kg 熟料,试计算原料的配合比。
物料平衡计算公式
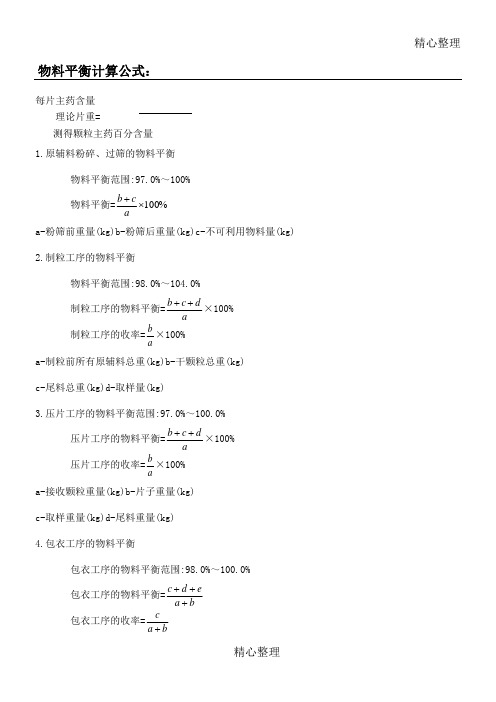
精心整理
物料平衡计算公式:
每片主药含量
理论片重=
测得颗粒主药百分含量
1.原辅料粉碎、过筛的物料平衡
物料平衡范围:97.0%~100%
a-2.a-c-3.a-c-取样重量(kg)d-尾料重量(kg)
4.包衣工序的物料平衡
包衣工序的物料平衡范围:98.0%~100.0%
包衣工序的物料平衡=
b a e d
c +++ 包衣工序的收率=b
a c +
a-素片重量(kg)b-包衣剂重量(kg)c-糖衣片重量(kg)d-尾料重量(kg)e-取样量(kg)
5.内包装工序物料平衡
内包装工序物料平衡范围:99.5%~100.0%
包材物料平衡=%100⨯++++A
a d c
b B a-PTP 领用量(kg)b-PTP 剩余量(kg)A-PVC 领用量(kg)
B-PVC 剩余量(kg)c-使用量(kg)d-废料量(kg)
a c 6.e-7.a-1.配料量
╳100%
粉碎过筛后原辅料总重
(物料平衡范围应控制在99.8~100.2%)
2.制粒干燥、整粒总混岗位物料平衡检查:
总混后重量+不良品
╳100%
干颗粒净重+润滑剂+崩解剂
(物料平衡范围应控制在99.0~100.0%) 3.充填抛光岗位物料平衡检查:
胶囊总重+细粉+不良品+废胶囊壳重量
╳100%
颗粒总重+胶囊壳重量
(物料平衡范围应控制在96.0~101.0%) 4.
5.。
物料平衡计算公式:
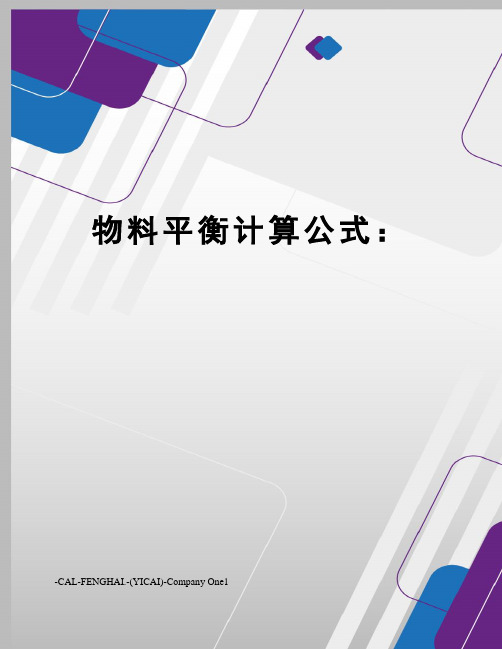
物料平衡计算公式:-CAL-FENGHAI.-(YICAI)-Company One1物料平衡计算公式:每片主药含量理论片重=测得颗粒主药百分含量1.原辅料粉碎、过筛的物料平衡物料平衡范围: %~100 %物料平衡= %100⨯+ac b a-粉筛前重量(kg) b-粉筛后重量(kg) c-不可利用物料量(kg)2.制粒工序的物料平衡物料平衡范围: %~ %制粒工序的物料平衡=a d cb ++×100% 制粒工序的收率=ab ×100% a-制粒前所有原辅料总重(kg) b-干颗粒总重(kg)c-尾料总重(kg) d-取样量(kg)3.压片工序的物料平衡范围: %~ %压片工序的物料平衡=a d cb ++×100% 压片工序的收率=ab ×100% a-接收颗粒重量(kg) b-片子重量(kg)c-取样重量(kg) d-尾料重量(kg)4.包衣工序的物料平衡包衣工序的物料平衡范围: %~ %包衣工序的物料平衡 =b a e dc +++ 包衣工序的收率 =ba c +a-素片重量(kg) b-包衣剂重量(kg) c-糖衣片重量(kg) d-尾料重量(kg) e-取样量(kg)5.内包装工序物料平衡内包装工序物料平衡范围: %~ %包材物料平衡=%100⨯++++Aa d cb B a- PTP 领用量(kg) b- PTP 剩余量(kg) A- PVC 领用量(kg)B- PVC 剩余量(kg) c-使用量(kg) d-废料量(kg)片剂物料平衡=%100⨯++ad c b a :领用量(Kg) b :产出量(Kg)c :取样量(Kg)d :废料量(Kg)6.外包装工序的物料平衡包装材料的物料平衡范围:100%包装材料物料平衡=%100⨯+++ea d cb e-上批结存 a-领用量 b-使用量 c-剩余量 d-残损量7.生产成品率成品率范围:90%~102%片剂收率= %100⨯++ad c b a-计划产量 b-入库量 c-留样量 d-取样量1.粉碎过筛和称配岗位物料平衡检查:配料量╳100%粉碎过筛后原辅料总重(物料平衡范围应控制在~%)2.制粒干燥、整粒总混岗位物料平衡检查:总混后重量+不良品╳100%干颗粒净重+润滑剂+崩解剂(物料平衡范围应控制在~%)3.充填抛光岗位物料平衡检查:胶囊总重+细粉+不良品+废胶囊壳重量╳100%颗粒总重+胶囊壳重量(物料平衡范围应控制在~%)4.铝塑内包岗位物料平衡检查:(成品板总重/平均每板重量+不良品)×规格(粒/板)╳100%胶囊领用量/平均胶囊重(物料平衡范围应控制在~%)5.总物料平衡检查:成品产量╳100%理论产量(物料平衡范围应控制在97~100%)。
物料平衡计算公式
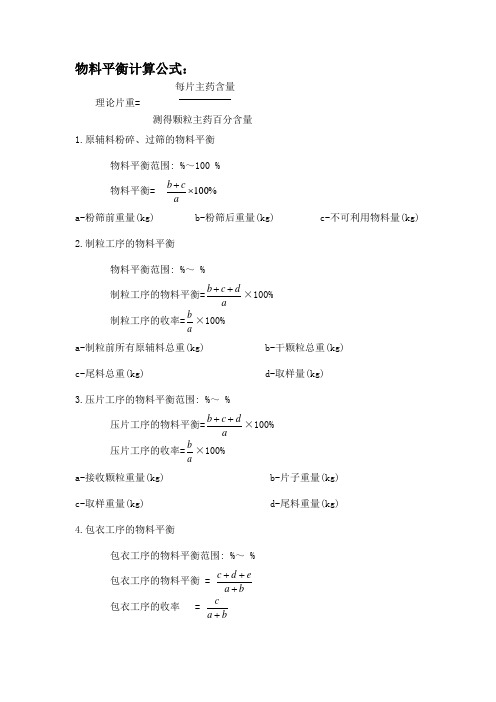
物料平衡计算公式:每片主药含量理论片重=测得颗粒主药百分含量1.原辅料粉碎、过筛的物料平衡物料平衡范围: %~100 %物料平衡= %100⨯+ac b a-粉筛前重量(kg) b-粉筛后重量(kg) c-不可利用物料量(kg)2.制粒工序的物料平衡物料平衡范围: %~ %制粒工序的物料平衡=a d cb ++×100% 制粒工序的收率=ab ×100% a-制粒前所有原辅料总重(kg) b-干颗粒总重(kg)c-尾料总重(kg) d-取样量(kg)3.压片工序的物料平衡范围: %~ %压片工序的物料平衡=a d cb ++×100% 压片工序的收率=ab ×100% a-接收颗粒重量(kg) b-片子重量(kg)c-取样重量(kg) d-尾料重量(kg)4.包衣工序的物料平衡包衣工序的物料平衡范围: %~ %包衣工序的物料平衡 =ba e d c +++ 包衣工序的收率 =b ac +a-素片重量(kg) b-包衣剂重量(kg) c-糖衣片重量(kg) d-尾料重量(kg) e-取样量(kg)5.内包装工序物料平衡内包装工序物料平衡范围: %~ %包材物料平衡=%100⨯++++Aa d cb B a- PTP 领用量(kg) b- PTP 剩余量(kg) A- PVC 领用量(kg) B- PVC 剩余量(kg) c-使用量(kg) d-废料量(kg)片剂物料平衡=%100⨯++ad c b a :领用量(Kg) b :产出量(Kg)c :取样量(Kg)d :废料量(Kg)6.外包装工序的物料平衡包装材料的物料平衡范围:100%包装材料物料平衡=%100⨯+++ea d cb e-上批结存 a-领用量 b-使用量 c-剩余量 d-残损量7.生产成品率成品率范围:90%~102%片剂收率= %100⨯++ad c b a-计划产量 b-入库量 c-留样量 d-取样量1.粉碎过筛和称配岗位物料平衡检查:配料量╳100%粉碎过筛后原辅料总重(物料平衡范围应控制在~%)2.制粒干燥、整粒总混岗位物料平衡检查:总混后重量+不良品╳100%干颗粒净重+润滑剂+崩解剂(物料平衡范围应控制在~%)3.充填抛光岗位物料平衡检查:胶囊总重+细粉+不良品+废胶囊壳重量╳100%颗粒总重+胶囊壳重量(物料平衡范围应控制在~%)4.铝塑内包岗位物料平衡检查:(成品板总重/平均每板重量+不良品)×规格(粒/板)╳100%胶囊领用量/平均胶囊重(物料平衡范围应控制在~%)5.总物料平衡检查:成品产量╳100%理论产量(物料平衡范围应控制在97~100%)。
配料计算及物料平衡表.ppt

烧失量
SiO2
Al2O3
Fe2O3
CaO
34.68612 2.232976 0.841532 0.408268 43.64302
MgO
其他
0.79154 0.716552
合计 配合比 83.32 0.8332
粘土
0.47263 11.46241 1.96753 0.59947 0.08003 0.09815 0.41978 15.1 0.151
一般率值的波动范围: KH:目标值±0.01~0.02 n:目标值±0.1 p:目标值±0.1
白生料配料计算实例(尝试拼凑法)
一、原料及煤灰化学成分
名称 石灰石
烧失量 41.63
SiO2 2.68
Al2O3 1.01
Fe2O3 0.49
CaO 52.38
MgO 0.95
其他
合计
0.86
100
(三)、熟料热耗与煤耗
热耗:生产1kg熟料所消耗的热量。符号q,单位 kJ/kg;
煤耗:生产1kg熟料所消耗的煤的质量。符号p, 单位kg/kg
P
q
Qne t.ar
式中:Qnet,ar——煤的应用基低位发热量(kJ/kg)
(四)、煤灰掺入量
GA
P Aar S 100
式中:GA——熟料中煤灰的掺入量(%); Aar——煤的收到基灰分含量(%); S——煤灰沉落于熟料中的百分率(%)。一般取
S=100。
(五)、理论料耗
理论料耗KT:不计生产损失和物料水分的情况下, 生产每千克熟料所消耗的干生料量。
生产方式及煅烧工艺不同,计算公式不同。 例:回转窑白生料的理论料耗:
KT
100 GA 100 L白
物料平衡计算公式:
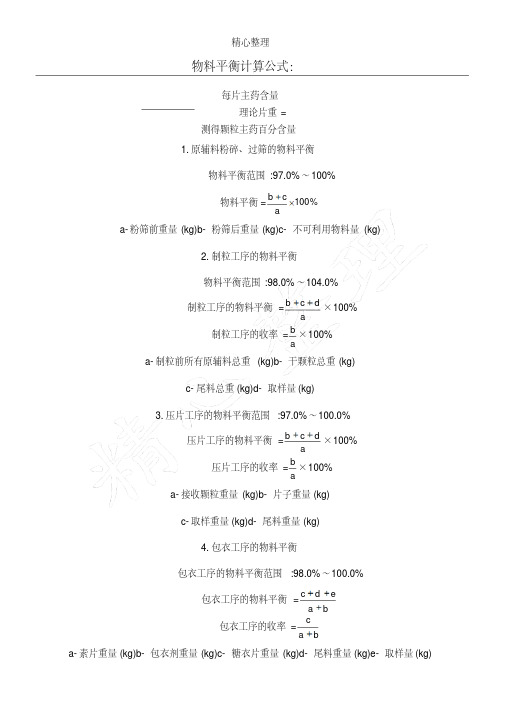
精心整理
物料平衡计算公式:
每片主药含量
理论片重=
测得颗粒主药百分含量
1.原辅料粉碎、过筛的物料平衡
物料平衡范围:97.0%~100%
物料平衡=%
100a c b
a-粉筛前重量(kg)b-粉筛后重量(kg)c-不可利用物料量(kg)
2.制粒工序的物料平衡
物料平衡范围:98.0%~104.0%
制粒工序的物料平衡=a d c b
×100% 制粒工序的收率=a b
×100%
a-制粒前所有原辅料总重(kg)b-干颗粒总重(kg)
c-尾料总重(kg)d-取样量(kg)
3.压片工序的物料平衡范围:97.0%~100.0%
压片工序的物料平衡=a d c b
×100% 压片工序的收率=a b
×100%
a-接收颗粒重量(kg)b-片子重量(kg)
c-取样重量(kg)d-尾料重量(kg)
4.包衣工序的物料平衡
包衣工序的物料平衡范围:98.0%~100.0%
包衣工序的物料平衡=
b a e d
c 包衣工序的收率=b a
c
a-素片重量(kg)b-包衣剂重量(kg)c-糖衣片重量(kg)d-尾料重量(kg)e-取样量(kg)。
物料平衡计算

一、配料计算 率值的确定在一定的工艺条件下,熟料中各氧化物的含量和彼此之间的比例关系的系数即率值是水泥生产质量控制的基本要素,国内外水泥厂都把率值作为控制生产的主要指标。
目前,我国主要采用石灰饱和系数(KH )、硅率(n )、铝率(p )三个率值。
对于新型干法水泥生产工艺,水泥熟料率值大致范围为:KH = 0.86~0.91,n = 2.2~2.6 ,p = 1.3 ~1.8,根据设计工艺条件设定三个率值为:KH = 0.89±0.01,n = 2.60±0.10, p =1.60±0.10 原始数据表2-1 原燃料化学成分(%)熟料热耗确定本次设计熟料热耗取3100 KJ/Kg 。
干原料的配合比计算 (1)煤灰掺入量计算 G a=qA y s Q dw y×R=3100×25.92×10023001×100=3.4934%式中: S ——煤灰掺入量,以熟料百分数表示(100%) Q dw y——煤的应用基低热值(kJ/kg 煤)G a ——煤的应用基灰分含量(%)q ——熟料烧成热耗(kJ/kg 熟料)R ——煤灰沉落度(%),当窑后有电收尘且窑灰入窑时取100%, (2)配比以尝试误差法计算各原料配合比,作EXCEL 表格计算,如下:煤灰的参入量 A G =3.4934%,则灼烧生料的配合比为100-3.4934%=96.5066%, 以此计算熟料的化学成分:则熟料的率值计算如下:KH =232328.235.065.1SiO O Fe O Al CaO -- = 65.5319−1.65∗5.1634−0.35∗3.41642.8∗22.4288 =0.8888n = 32322O Fe O Al SiO +=22.42885.1634+3.4164= 2.6141p =3232O Fe O Al = 5.16343.4164 =1.5114 由上表得知熟料三率值均在要求范围内,即可认为配料计算结果符合要求。
管材原料计算列出输入输出物料平衡表

氯乙烯:0.0084 千克/小时
引发剂:0.0017 克/小时
悬浮剂 0.00035 千克/小时
它们是她的化身,在每一个夜晚,她都和它们约会,将那些悄悄话告诉它们
缓冲剂 0.00075 千克/小时
1cq0f2c9a
1)进料
去离子水:0.717 千克/小时
氯乙烯:0.448 千克/小时
引发剂:0.00015 千克/小时
悬浮剂 0.00035 千克/小时
缓冲剂 0.00075 千克/小时
它们是她的化身,在每一个夜晚,她都和它们约会,将那些悄悄话告诉它们
(2)出料
去离子水:0.68 千克/小时
聚氯乙烯:0.427 千克/小时
1 聚合釜物料衡算
它们是她的化身,在每一个夜晚,她都和它们约会,将那些悄悄话告诉它们
去离子水纯度 100%
氯乙烯纯度 99%
悬浮剂(聚乙烯醇)97%
引发剂(过氧化二碳酸二异丙醇)97%
缓冲剂(磷酸氢二钠)99%
消泡剂(邻苯二甲酸二丁酯)99%
它们是她的化身,在每一个夜晚,她都和它们约会,将那些悄悄话告诉它们
此表用来描述和识别所有进入体系和离开
体系的物料。表中列出了已知量和要求解的未知
它们是她的化身,在每一个夜晚,她都和它们约会,将那些悄悄话告诉它们
量,有时还列出经过导出和计算的有关数据。
2.5.3 物料衡算
生产任务:1 天 10 千克
每天生产量:10 千克
每小时生产量:10/24=0.417 千克/小时
量在数值上太大,计算起来不方便,则可先按 100
它们是她的化身,在每一个夜晚,她都和它们约会,将那些悄悄话告诉它们
千克或 100 摩尔原料(也可按任何别的方便的数 量)出发进行计算。算出产品产量后,与实际产
SC-203物料平衡计算表

包装线
包装规格
10╳10ml
╳40盒
标签及含有标签内容的包装物情况
名称
项目
标签
纸盒
说明书
纸箱
交库件数
件
本批取样留样数
10盒
发放数
张
个
张
个
本批零头产品数
盒
实际使用数
张
个
张
个
合箱
合箱批号
盒数(盒)
报废数
张
个
张
个
销毁数
张
个
张
个
剩余数
张
个
张
个
数据平衡
平衡□
平衡□
平衡□
平衡□
总结论
属正常偏差属异常偏差
车间工艺员: 年 月 日
物料平衡计算表
SOR-SC-203-00
品名:阿胶浆口服液规格:10ml批号:日期:20年月日
生产线
投入量
产出量
主料名称
投料量ห้องสมุดไป่ตู้
总配制量
理论产量
本批产量
支③
阿胶
支①
蜂蜜
低聚果糖
乳酸亚铁
灯检不良品
支④
投入的不良品量
支②
包装废弃物
支⑤
总计:①+②= 支
总计:③+④+⑤= 支
物料平衡率=
产出量
×100%=
×100%=
异常偏差处理
原因分析
车间工艺员: 年 月 日
处
理
意
见
车间副主任:年 月 日
审批意见:
质管员: 年 月 日
(正常偏差时异常偏差处理栏不填)
备注:
- 1、下载文档前请自行甄别文档内容的完整性,平台不提供额外的编辑、内容补充、找答案等附加服务。
- 2、"仅部分预览"的文档,不可在线预览部分如存在完整性等问题,可反馈申请退款(可完整预览的文档不适用该条件!)。
- 3、如文档侵犯您的权益,请联系客服反馈,我们会尽快为您处理(人工客服工作时间:9:00-18:30)。
0.0313 1.6316 1.0506
89
19
02
熟料
22.369 5.3677
1
09
54
八、计算率值
Fe2O3 3.129352 0.094796 3.224148
CaO 65.47242 0.143135 65.61555
MgO 1.371167 0.019148 1.390315
其他 1.833509 0.199636 2.033145
一般率值的波动范围: KH:目标值±0.01~0.02 n:目标值±0.1 p:目标值±0.1
白生料配料计算实例(尝试拼凑法)
一、原料及煤灰化学成分
名称 石灰石
烧失量 41.63
SiO2 2.68
Al2O3 1.01
Fe2O3 0.49
CaO 52.38
MgO 0.95
其他
合计
0.86
100
熟料热耗:
3095 kJ/kg
煤热值:
25360 kJ/kg
标准煤耗=
熟料热耗/煤热值=
六、计算煤灰掺入量
0.122043 kg煤/kg熟料
GA=P*A*S/100=
3.138935 %
七、计算熟料化学成分(%)
成分
灼烧生 0.9686
料
11
SiO2
20.737 47
Al2O3
4.3171 52
煤灰
工艺设计的依据,正常生产的前提
KH= CaO 1.65 Al2 03 0.35Fe2O3
0.87~0.96
2.8SiO2
n(SM)=
1.7~2,7 p(IM)= 0.9~1.9
SiO2 Al2O3 Fe2O3
Al2O3 Fe2O3
配料应遵循的基本原则:
1、烧出的熟料具有较高的强度和良好的物理化 学性能;
湿基准:
基准间的转换:
A——干基物料成分(%)
L——干基物料烧失量(%)
w——物料含水量(%)
干基转灼烧基 灼烧基成分(%)=
A 100 100 L
干基转湿基:
湿基成分=
100 干基成分
100 w
煤的基准
应用基 分析基 干燥基 可燃基
送到分析室时的状态进行分析的结果 空气干燥 不含任何水分 不含水分和灰分
S=100。
(五)、理论料耗
理论料耗KT:不计生产损失和物料水分的情况下, 生产每千克熟料所消耗的干生料量。
生产方式及煅烧工艺不同,计算公式不同。 例:回转窑白生料的理论料耗:
KT
100 GA 100 L白
式中: KT——理论料耗; L白——白生料的烧失量(%)。
§3-2 配料方案的选择
(%) 干基 湿基
物料量(t)
干基
湿基
时日 年 时 日 年
全厂主机设备表
车间名称 主机 型号、规格、性能 数量 备注 名称
kg湿铁粉/kg熟 料
kg湿原煤/kg熟 料
十三、计算湿物料配合比
湿物料总石+湿粘土+湿铁粉= 湿粘土 湿铁粉
配比(%) 82.58006 15.59605 1.823893
1.586871
物料平衡表
物料 名称
物料 配比
水分 生产 消耗定额 (%) 损失 (kg/kg熟料
2、配制的生料易于粉磨和煅烧; 3、生产过程中易于控制,便于生产操作管理, 尽量简化工艺流程,并结合工厂生产条件、经济、 合理地使用矿山资源。
(二)配料计算中的常用基准及换算
干燥基准: 如不考虑生产损失,有: 各种干原料之和=干生料(白生料)
灼烧基准: 如不考虑生产损失,有: 灼烧生料+煤灰(掺入熟料中的)=熟料
(三)、熟料热耗与煤耗
热耗:生产1kg熟料所消耗的热量。符号q,单位 kJ/kg;
煤耗:生产1kg熟料所消耗的煤的质量。符号p, 单位kg/kg
P
q
Qne t.ar
式中:Qnet,ar——煤的应用基低位发热量(kJ/kg)
(四)、煤灰掺入量
GA
P Aar S 100
式中:GA——熟料中煤灰的掺入量(%); Aar——煤的收到基灰分含量(%); S——煤灰沉落于熟料中的百分率(%)。一般取
水泥工艺学课程设计 配料计算及物料平衡计算
(一)生料及配料的基本概念
一、生料 ➢ 定义:由石灰质原料、粘土质原料、少量校正
原料(有时还加入矿化剂)按比例配合,粉磨到 一定细度的物料。 ➢ 干法生料含水量 ≤1%
生料粉:是否含煤分为三种:
白生料:出磨生料中不含煤。干法回转窑及采用 白生料法煅烧的立窑用。
十、计算实物煤耗 P’= P/(1-煤生产损失)= 0.1258kg煤/kg熟料
十一、计算干基实际消耗定额 干石灰石= HS*X/(1-石灰石生产损失)=1.2973
kg干石灰石/kg熟料 干粘土= HS*Y/(1-粘土生产损失)=0.2351 kg干
粘土/kg熟料 干铁粉= HS*Z/(1-铁粉生产损失)=0.0246 kg干
成分 SiO2 Al2O3
Fe2O3
CaO
MgO
其他
合计
21.40
名称
95 4.457057 3.230764 67.59415 1.415602 1.892927
100
五、计算熟料标准煤耗(kg煤/kg熟料)
煤的工业分析
挥发分 固定碳 灰分
热值
29.77% 41.82% 25.72%
25360 kJ/kg
粘土
3.13
75.91
13.03
3.97
0.53
0.65
2.78
100
铁粉
3.89
10.99
4.95
68.68
4.07
1.73
5.69
100
煤灰
51.98
33.47
3.02
4.56
0.61
6.36
100
二、假设原料配比
石灰石: 粘土: 铁粉=
83.32
:
15.10
:
1.58
三、计算白生料化学成分
名称 石灰石
铁粉/kg熟料
十二、计算湿基实际消耗定额
湿石灰 石=
干石灰石/(1-石灰石含水率)=
湿粘土= 干粘土/(1-粘土含水率)=
湿铁粉= 干铁粉/(1-铁粉含水率)=
湿原煤= 实物煤耗/(1-原煤含水率)=
1.310439 0.247489 0.028943 0.136758
kg湿石灰石/kg 熟料
kg湿粘土/kg熟 料
烧失量
SiO2
Al2O3
Fe2O3
CaO
34.68612 2.232976 0.841532 0.408268 43.64302
MgO
其他
0.79154 0.716552
合计 配合比 83.32 0.8332
粘土
0.47263 11.46241 1.96753 0.59947 0.08003 0.09815 0.41978 15.1 0.151
铁粉
0.061462 0.173642 0.07821 1.085144 0.064306 0.027334 0.089902 1.58 0.0158
白生料 35.22021 13.86903 2.887272 2.092882 43.78735 0.917024 1.226234
100
1
四、计算灼烧基生料化学成分
配料方案:既熟料的矿物组成或熟料的三 率值。
配料方案的选择:选择合理的熟料矿物组 成,即确定熟料的三率值KH、n 、p。
一、确定配料方案的依据
水泥品种 原料品质 燃料品质 生料细度﹑均匀性﹑易烧性 生产窑型和生产方法
二、熟料率值的选择
三个率值要互相匹配,吻合,不能只强调某 一率值而忽视其他两个。
合计 96.86106 3.138935
100
KH= 0.888
SM= 2.604
IM= 1.665
经检验三率值均符合要求
九、计算熟料料耗 1、理论料耗 HL=(100-GA)/(100-生料烧失量)=1.4952kg生 料/kg熟料 2、实际料耗 HS=HL/(1-生产损失)=1.5103 kg生料/kg熟 料
黑生料:出磨生料中含有煅烧所需的全部煤。采 用全黑生料法煅烧的立窑用。
半黑生料:出磨生料中只含有煅烧所需煤的一部 分。采用半黑生料法煅烧的立窑用
二、配料
1、概念 配料:根据水泥品种、强度等级﹑原燃料品质、
工厂具体生产条件等选择合理的熟料矿物组成或 率值,并由此计算所用原料及燃料的配合比,称 为生料配料,简称配料。 配料的目的: 确定各原料的数量比例,以保证生 产符合要求的水泥熟料