模具CNC加工标准参考
模具部CNC编程及加工工作标准
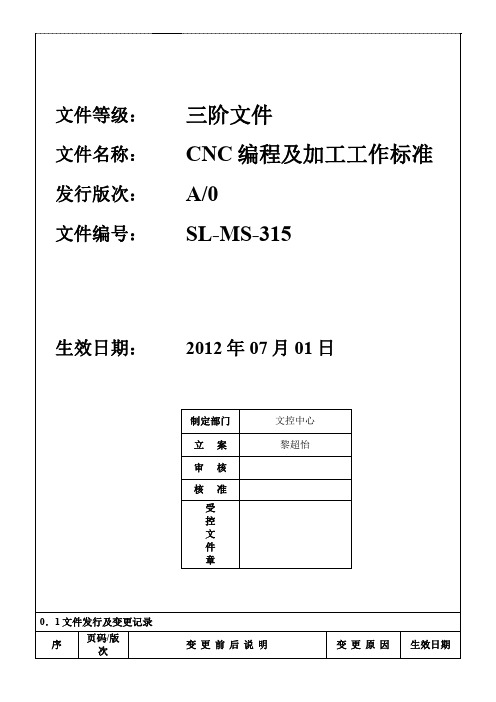
5.2.2.3 产品表面有利角要求,可用局部加工的方法来保证,而这种加工方法就需要对面做一些修改。
5.2.3 刀具大小和类型的选择:
5.2.3.1 尽可能用最大的刀开粗,且要减少抬刀。
5.2.3.2 二次开粗,要先对第一把刀开粗后转角及凹坑的余量进行分析,刀具应可能满刀切削,并要防止夹刀。二次开粗应做局部开粗,防止重复开粗加工。
d.对于超过2㎜的后模骨位,做2件铜公,粗公火花位0.20㎜/S,精公0.07㎜/S,胶位少的骨位,也只做一件精公;
5.1.4 多种设备都可加工的工件
5.1.4.1 根据各个工位的工作量进行调配。
5.1.4.2 根据各个工位的时间进行调配。
5.1.4.3 根据各个工位的成本进行调配。
5.1.5 电极零件图及总装图的输出;
5.2.5.2铣铜公时,¢12合金刀FS=3000MM\MIN 左右,S=4000-6000 R\MIN,球头合金刀FS=3000MM\MIN左右,S=8000R\MIN以上。
5.3 NC加工
5.3.1 备铜公和刀具:
5程式单和开料单给NC操作员后,操作员应立即将开料单给师傅,并要求其在铜公背面打孔攻牙
页 码
1
2
3
4
5
6
7
8
9
10
11
12
13
14
15
版 次
A/0
A/0
A/0
A/0
页 码
版 次
1、目的
为了规范CNC拆分铜公、编写程式、NC加工各环节的工作,确保下道工序的进程及整套模具质量,特制订《CNC编程及加工工作标准》
IML模具CNC加工要求
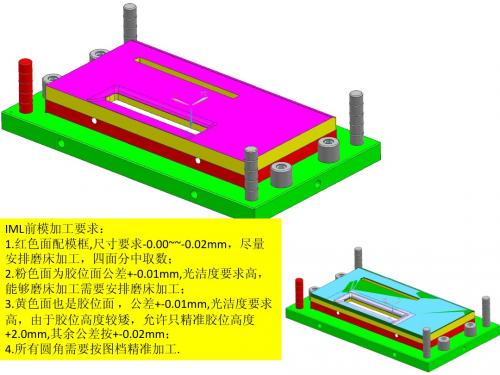
IML后模模板加工要求:(模架厂开粗留料0.5/单边) 1.粉色面为胶位面公差+-0.01mm,光洁度要求高。 2.加工以导柱பைடு நூலகம்取数; 3.圆角加工不到需要EDM加工接顺NC面; 4.所有圆角需要按图档精准加工.
IML后模镶件加工要求: 1.绿色面配模框,设计间隙单边0.05,加工时单边0.025MM,确保间隙配合,四面分中取数; 2.其余面为胶位面公差+-0.01mm,光洁度要求高, 能够磨床加工需要安排磨床加工; 3.镶件上红色面为非工作面,公差+-0.05; 4.所有圆角需要按图档精准加工; 5.灰色工件厚度磨床加工,其余没有尺寸要求.
模具CNC加工标准参考

2.8.4注意加工完之成品保护以断裂、磨耗等更换。
3其他:
3.1本作业标准每年九月,由责任单位负责召集有关单位检讨,并将检讨结果送事业单位主管审核。
3.2审核完成后,呈群主管核准,保存于制造单位,公布后立即实施,修订时亦同。
2.6素材备料应以长宽实际尺寸预留2mm为限。
2.7 加工电极基准的方式:
2.7.1侧壁与底面不同时精修(刀具刃部与端面同时切削会震动)。
2.7.2先精加工侧壁再精加工底面(如上图所示)。
2.8其它(注意事项)
2.8.1加工前先利用一次元确认加工物之X、Y、Z有无过切。
2.8.2注意加工前校模时毛边的清理,以免寻边造成误差。
G24 X600 Y400 Z400 I0 J0 K[V3003-11]
M03 S32000
G04 P30
M07
M56
G72 $1101
G0 Z50
M02
2.5.4.1主程序要有加工过负荷检机能。
2.5.4.2主程序要有主轴上升机能。
2.5.4.3主程序要有CNC形状控制机能。
2.5.4.4主程序要有干涉机能设定。
M98 P8011
M98 P8012
G91 G28 Z0
M319
M30
2.5.1.1刀具使用完成后,须再次测刀长之后,才可将其放回刀仓内(破损检出)。
2.5.1.2有交换台之机械,即有主程序,也有子程序;无交换台的只有主程序。
2.5.2V55(参照附件二)
(主程序)
G91 G28 Z0
M98 P9810
#1=#7
#17=#23
#32=1
M98P8100
24条CNC模具加工工艺标准:模仁、镶件、斜顶、滑块等

24条CNC模具加工工艺标准:模仁、镶件、斜顶、滑块等1. 工艺员编工艺卡工艺员编工艺卡时要在工艺卡中详细注明加工预留量、预留量的方位、粗糙度要求及注意事项。
加工工艺流程卡编写原则:在能保证精度、质量的前提下,优先采用加工效率高的设备。
铣床、CNC、磨床的加工效率比线切割、电脉冲要快,尤其是电脉冲加工效率最慢。
图纸上的尺寸不能随意更改(只有技术员能改)。
2. 加工预留量原则需要热处理加工的工件,热处理前外形备料尺寸单边加0.25mm的磨床余量,模仁、镶件需要CNC粗加工的部分,单边预留余量0.2mm,钳工铣床粗铣外形单边预留余量0.3-0.5mm,线割后需要磨床加工的工件,成型部位单边预留0.05mm,外形开粗单边预留0.1mm的磨削余量;CNC精加工、电脉冲后要镜面抛光,单边留0.03mm的抛光余量。
3. 加工精度要求模具尺寸的制造精度应在0.005~0.02mm范围内;垂直度要求在0.01~0.02mm范围内;同轴度要求在0.01~0.03mm范围内;动、定模分型面的上、下两平面的平行度要求在0.01~0.03mm范围内。
合模后,分型面之间的间隙小于所成型塑料的溢边值。
其余模板配合面的平行度要求在0.01~0.02mm范围内;固定部分的配合精度一般选用0.01~0.02mm范围内;小芯子如果无对插要求或对尺寸影响不大可取双边0.01~0.02mm的间隙配合;滑动部分的配合精度一般选用H7/e6、H7/f7、H7/g6三种。
注意:镜面上如有做了挂靠台阶的镶件,配合不能太紧,否则在镶件从正面往后退敲打时,用来敲打的工具易碰坏镜面,如不影响产品尺寸,可取双边0.01~0.02mm的间隙配合。
4. CNC拆电极的原则模具型腔型芯应先拆外观主体电极,再拆其他主体电极,最后拆局部电极;定模外观电极要考虑整体加工,对CNC清角不到的地方,采用线切割清角,以便定模外观面完整,无接痕;动模深度相差不大的加强筋、筋片、柱子能一起加工的尽量做在一个电极上;比较深的筋片要做镶件,要单独做电极侧打,以防电脉冲时积碳;动模电极尽量不要CNC铣好之后还要线切割清角,如要,应将电极分解拆开或直接采用线切割;动模的筋部和筋位或者柱子的间隔超过35mm,应当分开做,节约铜料。
CNC加工检验标准

CNC加工检验标准文件编号:XHL-WI-041发行日期:2020-8-1审核版本:1.0编制者:XXX批准者。
1.0 目的本标准旨在规范CNC加工产品的加工标准及检验标准,为判定者提供可靠的依据。
2.0 适用范围本标准适用于本公司以及外协厂的CNC加工工件的可靠性验证和外观检验。
3.0 检验项目及定义3.1 刀纹:由于刀具磨损或摆动产生的纹路,通常有触感,呈浪状。
3.2 碰伤:由于操作不当产生碰撞或跌落行程塌陷状。
3.3 气孔、砂眼:由于铸造密度不够,形成不规则孔状缺陷或蜂窝状黑点。
3.4 擦伤:由于操作不当产品发生摩擦形成条状缺陷,或由于刀具附有残留切削废料形成螺旋线状缺陷。
3.5 段差(台阶):由于刀路斜接不顺畅,形成台阶状缺陷。
3.6 毛刺:由于刀具径向作用力导致局部切削废料未脱离工件形成锯齿状或条状缺陷。
3.7 缺料:由于刀具磨损后切削作用力过大导致产品薄弱处崩边或缺肉。
3.8 烂牙:由于攻丝底径偏小或偏大、底孔歪斜、丝锥磨损导致螺纹局部紊乱、无螺纹、牙型不符。
3.9 压伤:由于加工治具存有切削残渣或受外力影响,将杂质压入产品内部呈凹陷状缺陷。
3.10 裂纹:由于铸造致密度不够或刀具磨损导致切削作用力过大造成薄弱处呈撕裂状缺陷。
3.11 切削不良:由于产品在治具固定位置发生偏移或刀具相对坐标发生变化造成切削量过大或偏小;包括过切或少切,其中少切也叫多料。
3.12 孔偏:由于定位不当或加强柱歪斜,甚至压铸产品缩水不均导致孔位与该孔所在加强柱中心发生偏离。
3.13 倒角不良:由于装配或安全因素对产品锐边进行工艺倒角,若图面无特殊要求按照C0.2±0.1管控,螺纹倒角须保证攻丝披锋不高出螺丝柱顶面(即披锋高度要低于倒角高度)。
倒角不良分两种状况:a、倒角过大,由于刀具或程序控制存有吃刀过深,造成倒角偏大或倒角偏小;倒角后存有锐边或翻边披锋;b、倒角不均(倒角大小边),由于产品变形,或治具装夹存有松动,导致倒角宽度存有不规则形状,治具装夹松动常伴随振刀纹路出现。
CNC加工标准(草稿)

三CNC编程的依据1 CNC加工委托单(付图)注明2 模具材料、加工要求、加工顺序3 机床参数,刀具参数,切削数据4 EDM数据。
四CNC 编程流程1 认真分析模具的结构及产品,导出需加工的部件.2.导入加工部件。
3.①认真检查模型分中情况(可用模胚查看方法检查),需多面加工的考虑清楚加工面的顺序,工件的装夹方式(压板或底板),确定基准摆放方向,需要垫高加工的要在CNC加工程序单上注明,。
②认真检查模具的碰穿面,擦穿面,分型面,料位面,避空面,装配面,EDM面的位置,模型中所要加工的R角大小,尖角位置,需要做加工辅佐面的要清楚并先做好导入加工图型以便加工,认真留意加工委托单上的加工要求。
做到心中有数,用刀具大小,加工方式,余量控制心中有个大概的轮廓。
4首要加工模具R角位置,R角加工注意问题:①清楚材料高度,底部预留0.3—0。
5mm 余量。
②单边避空0.2mm。
③用大飞刀加工。
④使用等高加工方式.5一次粗加工.加工方式:①平行区域区域清除模型——相对简单模型适用.②偏置区域清除模型——常用开粗。
开粗余量控制侧壁0。
35-0。
5mm,底部0.15—0。
3mm.热处理材料总体;0.5mm。
6二次开粗加工。
加工方式:①偏置残留加工--建议使用:安全性高,加工均匀,残留计算准确。
②等高二次加工-—对于简单模型适用,加工均匀,加工时间短,计算时间快。
③平行开粗加工-—相对简单弧面模型,加工时间短,进给量可适当大,计算时间最快。
7曲面中光加工(大部分模具需中光)。
加工方式:①等高精加工——常用中光加工.②平行精加工——常用中光加工③三维偏置精加工等等。
.认真检测好开粗时的残留余量,部位。
适用合理的加工方式从而保证中光加工的均匀,余量的一致.曲面余量控制0.05-0。
12mm之间平面中光加工.加工方式①平行平坦面加工①偏置平坦面加工.中光平面时注意侧面的预留余量,底部余量0.05—0.08mm.8 曲面精光加工。
模具CNC加工工艺_模具CNC加工工艺有哪些
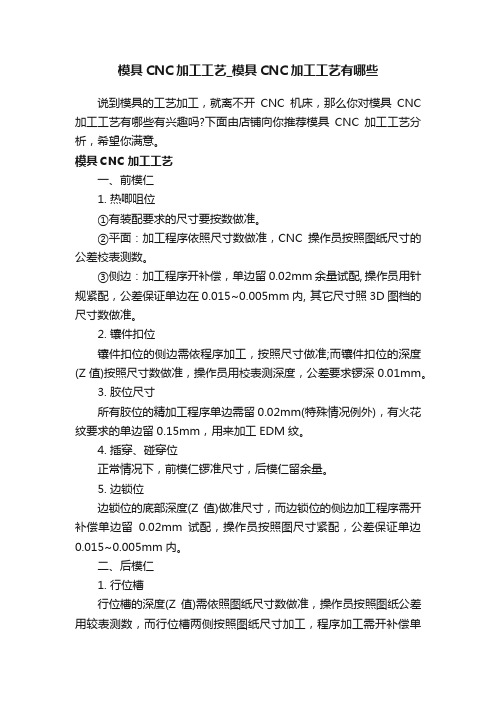
模具CNC加工工艺_模具CNC加工工艺有哪些说到模具的工艺加工,就离不开CNC机床,那么你对模具CNC 加工工艺有哪些有兴趣吗?下面由店铺向你推荐模具CNC加工工艺分析,希望你满意。
模具CNC加工工艺一、前模仁1. 热唧咀位①有装配要求的尺寸要按数做准。
②平面:加工程序依照尺寸数做准,CNC操作员按照图纸尺寸的公差校表测数。
③侧边:加工程序开补偿,单边留0.02mm余量试配, 操作员用针规紧配,公差保证单边在0.015~0.005mm内, 其它尺寸照3D图档的尺寸数做准。
2. 镶件扣位镶件扣位的侧边需依程序加工,按照尺寸做准;而镶件扣位的深度(Z值)按照尺寸数做准,操作员用校表测深度,公差要求锣深0.01mm。
3. 胶位尺寸所有胶位的精加工程序单边需留0.02mm(特殊情况例外),有火花纹要求的单边留0.15mm,用来加工EDM纹。
4. 插穿、碰穿位正常情况下,前模仁锣准尺寸,后模仁留余量。
5. 边锁位边锁位的底部深度(Z值)做准尺寸,而边锁位的侧边加工程序需开补偿单边留0.02mm试配,操作员按照图尺寸紧配,公差保证单边0.015~0.005mm内。
二、后模仁1. 行位槽行位槽的深度(Z值)需依照图纸尺寸数做准,操作员按照图纸公差用较表测数,而行位槽两侧按照图纸尺寸加工,程序加工需开补偿单边留0.02mm余量试配,操作员用块规紧配,公差保证单边0.015~0.005mm内。
2. 镶件扣位镶件扣位侧边需按照图纸尺寸数做准,而底部的深度(Z值)都按照尺寸数做准,操作员用校表测数,公差要求锣深0.01mm。
3. 模框孔位(藏CORE位)编程员做光刀程序,需开补偿单边留0.02mm余量,开补偿操作员按照图纸尺寸数测量,单边锣大0.005~0.01mm,方便装配。
4. 胶位尺寸所有胶位精加工留余量0.02mm(特殊要求例外)。
5. 插穿、碰穿位正常情况下后模需多留+0.02~0mm余量,后模仁配行位的位置需按照尺寸数做准,而行位相配后模仁的位置需多留余量。
实用CNC加工参数设置标准

倍数(l/d)
参数比例
转数S 100%70%60%50%↓
进给率F 100%70%60%50%↓
Ar(切深)100%70%60%50%↓
A 级
B 级
C 级
D 级
E 级
F 级
0.00250.01外观型腔面非外观型腔
面分型面1-5倍6倍7倍8-10倍一.刀具悬伸长度应选择刀具直径的2~3倍,使用D/L (刀长/刀径)>5的刀具时,NC 文件要进行分段加工,对长度与直径比(l/d)超过5倍的刀具在加工中应降低转速与进给率,并减少吃刀量,具体数据见下表二.球刀加工时应根据工件不同要求进行参数选择,参阅《模具加工工艺规范》《刀径深度位移落差表》选择
模具加工工艺规范
加工工艺要求CAD 输入精度
0.0020.0050.01CAM 精度(Cimatrion)模具及精公电极0.01(透明件0.0025)
0.01电极粗公电极
0.02CAM 精度(Cam-tool)模具及精公电极0.01
0.05电极粗公电极
0.05切削参数按
粗糙度设定平优化)粗公电极
0.01 (III)0.01 (III)精公电极0.002 (I)0.005(透明件 0.002
0.0030.0050.005 (III)0.0020.0050.008 (III)0.02 (III)中公电极
0.003\\0.005 (III)外观型腔面
0.002 (I) 0.005(透明件0.0020.005
刀长与加工参数调整原则:
工工艺改进专业系统
四.切削参数计算常用公式。
2020年模具模架加工CNC作业指导书参照模板
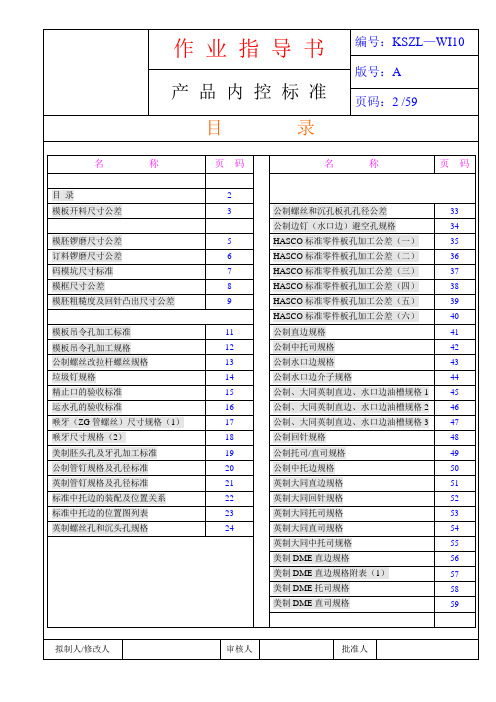
XXXX模架有限公司
XXXX模架有限公司
XXXX模架有限公司XXXX模架有限公司
XXXX模架有限公司
XXXX模架有限公司
XXXX模架有限公司
XXXX模架有限公司
XXXX模架有限公司
XXXX模架有限公司
XXXX模架有限公司
XXXX模架有限公司
XXXX模架有限公司
XXXX模架有限公司
XXXX模架有限公司
XXXX模架有限公司
XXXX模架有限公司
XXXX模架有限公司
XXXX模架有限公司
XXXX模架有限公司
XXXX模架有限公司
XXXX模架有限公司
XXXX模架有限公司
XXXX模架有限公司
XXXX模架有限公司
XXXX模架有限公司
XXXX模架有限公司
XXXX模架有限公司
XXXX模架有限公司
XXXX模架有限公司
XXXX模架有限公司
XXXX模架有限公司
XXXX模架有限公司
XXXX模架有限公司
XXXX模架有限公司
XXXX模架有限公司
XXXX模架有限公司
XXXX模架有限公司
XXXX模架有限公司
XXXX模架有限公司
XXXX模架有限公司。
CNC加工检验标准

生产制造CNC加工检验标准1)变形:合格放置平稳或装配后无错位,离壳间隙在0.2MM以下,不影响外观.不合格放置不平稳,装配有组合不严或影响其他组装,间隙超0.2MM均不可接受.2)缩水合格轻微缩水,正面在30CM距离以内才能发现,或侧边不明显处,可接受(客户特殊要求除外合格轻微缩水,正面在20CM距离以内才能发现或侧边不明显处,手感轻微,可接受(客户特殊除外)不合格严重缩水,用手可以明显感到不平,影响装配,影响外观.3)色差合格在同样环境下与样板无明显差别均可接受.不合格在同样环境下与样板有明显差异或同批产品有颜色差异或同一产品各部分有明显颜色差异均不可接受.4)披锋合格表面或边缘无毛刺,光滑接缝处0.2MM但无刺手现象,工艺需作改善.合格表面或边缘光滑无任何毛边,毛刺;披锋<0.1MM无刺手现象但工艺需作改善.不合格表面边缘刺手,影响外观均不可接收.5)碰伤合格整机外观无任何碰伤边缘掉油现象.合格正面轻微碰伤,喷油或可以覆盖碰伤痕迹,不明显影响外观,侧面/底面碰伤较重喷油或能见轻微碰伤痕迹. 不允许任何碰伤.不合格成品机外壳有明显碰伤,变形,影响外观.6)喷油合格喷油面均匀,无灰尘,发亮,油粒,表面无明显夹水纹.吸附力:用3M SCOTHCH 810胶纸,将喷油干透之产品表面贴紧5-10分钟后撕开, 油漆无脱落现象为合格,(方法:将胶纸一端倾斜约45度撕开)表面硬度:待干后24小时,用手指甲背在其表面轻刮,若出现刮花痕迹和轻微痕迹,如果可用手轻轻抹去其轻微痕迹(或用去污水轻轻一擦痕迹便消除)为合格.颜色与样板一样(或与样板有少许差异,但须整套色一致不合格喷油面不均匀,一部分粗糙,一部分光亮,喷油面有灰尘,油粒,明显夹水纹.吸附力:表面硬度达不到要求. 颜色与样板差异较大,或整套颜色不一致.7)丝印合格塑胶:表面丝印位置,字体,颜色与样板或工程图纸一致.吸附力:用3M SCOTCH 810胶纸,在丝印好的塑胶表面贴紧后撕开,(方法:将胶纸一端倾斜约45度角撕开,连续3次丝印无脱落现象为合格耐磨度:用沙胶笔擦30次以上不掉油为合格.电子元件:丝印颜色清晰,色环易辨认浸,UC36洗板水浸3秒后不掉色环,极性标识清楚,规格丝印清晰易识别.合格丝印有轻微断缺,连接,能够辨别丝印内容.电子元件色环极性标识,有少许断缺,但可以辨认其极性,浸UC36洗板水约3秒后丝印不掉可接受.不合格塑胶表面丝印模糊,丝印移位,颜色与工程图纸或样板不一致,丝印色坏,字体变形丝印有毛边,重叠,连接,断缺,气泡.塑胶表面丝印达不到吸附力,耐磨度要求.电子元件色环丝印不全,少色环,不能辨认其颜色,不能辨认其极性或规格.受.8)错位合格成品装配错位不超过0.2MM且不影响其他组装外观.合格成品装配错位不超过0.1MM且不影响外观.不合格错位超过0.2MM影响整机外观。
cnc加工标准
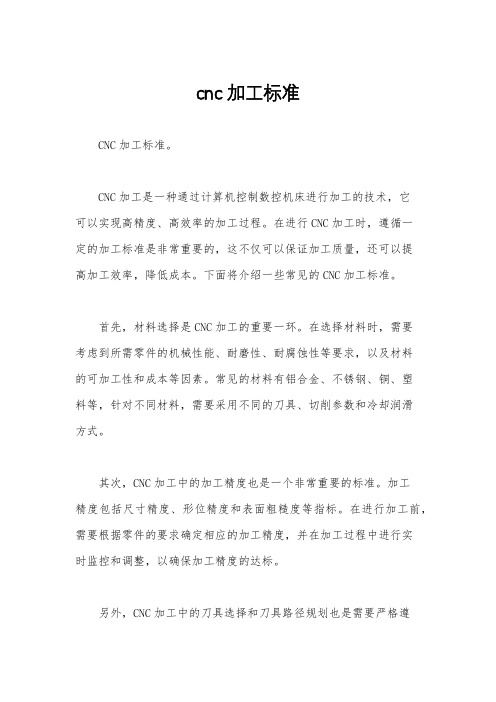
cnc加工标准CNC加工标准。
CNC加工是一种通过计算机控制数控机床进行加工的技术,它可以实现高精度、高效率的加工过程。
在进行CNC加工时,遵循一定的加工标准是非常重要的,这不仅可以保证加工质量,还可以提高加工效率,降低成本。
下面将介绍一些常见的CNC加工标准。
首先,材料选择是CNC加工的重要一环。
在选择材料时,需要考虑到所需零件的机械性能、耐磨性、耐腐蚀性等要求,以及材料的可加工性和成本等因素。
常见的材料有铝合金、不锈钢、铜、塑料等,针对不同材料,需要采用不同的刀具、切削参数和冷却润滑方式。
其次,CNC加工中的加工精度也是一个非常重要的标准。
加工精度包括尺寸精度、形位精度和表面粗糙度等指标。
在进行加工前,需要根据零件的要求确定相应的加工精度,并在加工过程中进行实时监控和调整,以确保加工精度的达标。
另外,CNC加工中的刀具选择和刀具路径规划也是需要严格遵循的标准之一。
合理的刀具选择可以提高加工效率和加工质量,而合理的刀具路径规划可以减少切削时间,降低生产成本。
同时,刀具的使用寿命和刀具的更换也需要按照标准程序进行,以保证加工质量和安全生产。
此外,CNC加工中的工艺文件和加工参数的编制也是至关重要的。
在进行CNC加工前,需要编制详细的工艺文件,包括加工工序、刀具选择、切削参数、加工顺序等内容,并根据实际情况进行不断修订和完善。
加工参数的选择也需要根据材料的特性和加工精度的要求进行科学合理的确定。
最后,CNC加工中的质量检验和记录也是不可或缺的一环。
在零件加工完成后,需要进行严格的质量检验,包括尺寸测量、外观检查、材料成分分析等,以确保零件的质量符合要求。
同时,需要对加工过程中的各项数据进行记录和归档,以便日后的追溯和分析。
总之,CNC加工标准是保证加工质量和提高加工效率的重要保障。
只有严格遵循相关标准,才能够确保CNC加工过程中的各个环节都能够达到预期的效果,从而满足客户的需求,提升企业的竞争力。
CNC加工参数表(工厂经验精髓)

CNC加工参数表(工厂经验精髓)机材切钢削速率/速度参考表刀具425R3 R55 3R1 25R55 2R1 2550R8.2 R50 201R 6R111 6R.8 012R 11R1 21R2.80 216 R0R1 58R4 6R 3R52. 5R42 R135. R2 11.R5.75 1R0.05 1 21 8 06 5 4 3.5 22 .51 1 10R2 1R005 .8R2 R805 .R61 60.5R型类转速进给率4000-050 4000-***** 540 0300 ***-*****- ***-***** 0 03000-***** 00-0120 4000 03006 ***-***** 0 *****-00 0380 *****-20 0***** 00-***** ***** 0 080-1200 3000 ***-***** 0 ***** 0320 03000 200-2805 ***-***** 0 2500-***** 2500-3000 0003 0030-305 *****-***** 0-***-***** 0-***-***** 0032-002 800 5020-00302 ***-***** -5002-***** 00-0003 0040 ***-***** 0 030-0***** 00 3000-***** 000 *****-500 ***** 3000-403 ***** ***-*****-0加深工度.500-8. 0.5-.0 8.300-. 0.2 05.-0.75 03-..5 00.510 2.0.3-0.4-0 5 .03.0-4 0..5 1.3-0.03 5.10 502-..3 0.01-05.20.21-0.15加工距间备注L01、09B2 L001B70/、9B2/B312(加长杆)延L010、70B/B29/B12(3加延长) L9杆5、6B/5B87 95、LB65B/87/1L52(斜度B7带5 L)202(≤1B0) L589、5B 3L89B5、3L8 2B4、/B503L 41(B0100) ≤铣精面B平7≤0钨钢刀R305 2.0R.4 1.R053. 10R.2高机钢速切削材速率/ 速度参考刀具4表R05.粗1 08-*****粗23 0-2800 中03 00033-0 精0 粗000-3503 中04 05-***** 精中粗050 0光面45平00 粗4 0004-050中5500 中精6 00-00700精中5 00 精0 中7 000粗7精000-0008 6中50 精精065 00中70 0 精0中0008精中9005-00100精中1010 0精精1 0200精*****精1400 0 精1800 0精1 0008精6 000精700 精280 00950- 精01000 0精*****精 1 5020 13精500 精*****精4000 1 精1450 ***** 0精中2700精7中200 精中8000 中精0800 精中95 00精中9 50 精0类型精中中精中精中精精速转1100 01300 ***-***** ***** 300 020000进率300给-3400 0200-3208 0003 0202-2500 02000 1400 502 3000 00300加工深度0.1-.15 00.-1.0210 .0-90.12 0.600.0-80. 0-0.085 .00-2.050 .0020.-400.02-0 .30加工间距备注L05B、≤03L4 5B≤、22钨刀钢L5 、B≤12 L775B(≤2)1普通机钢材切削速/率速度参考刀具表0R64 0R3 5525 R23R.8025R0.8 2R0.0 4610.4 R16R8 12R 60R5 120R1 08R4 6R 35R.25 R2 43R.5 1R2 11620 25 1 10 286 10 0R5. 80R.5类型粗粗粗中精中精中精中精中精中精中中精精中精中中精精中精中精精精精精中精中中精精中精中精中精速转*****-00 *****-500 2100-6001 000-1201 ***-*****0 13-0015-00 ***-***** -4001-100 ***-***** 0-1060 0140-***** 0031-50 0***-***** 01800-1 *****-0 ***-*****-026 0-0200 2580-30 2000-5022 0-250 0120-1400 1400-1500 05100-***** 00-***** 0 08000给进率1200-180 *****-0***** -0610 02100-400 6010-80 0*****-400 00-680 9000-***** 0-0*****-12 0 ***-*****-1 02-0601 08001-200 100-1400 000810-001 000-1200 008-***** 20-***-***** -***** 080-1000 00-8006 00-7800 400-*****- ***** 06-00 5006-00 00-340 400-500 250-350 000-***** 200 0200 00 *****-0 800 *****-0 03002 0-040 600 002-4000 3000-300 3600-04300 030-0300 *****-4003每次加深工或度间距0.81.5(深度) 0.--1.2(深度)5 .0-5.10深() 度0.-0.84深度()0 2-..20(5深) 度.0-046.(深)度02-0..24深() 度.30-0.6深度) 0.(2深(度) 03-.05.(度深) .150(度深)0.3 50-4.(间距)0. 820.-5(3距) 0间2-0..2(5距) 0.3间-.40(5距间)0 1.8-.20(5距间)0.16- .230间距( 0).1-5.2(0距)间0 .310.1-7(间) 距.12-001.6间()距0. -101.3(间)距0 .05-0.(1侧) 0刃05.0-1.(侧刃)00.-05.(侧1) 0刃.1-0.1 0.51-.01 0.28-001 0.06-..100 .51-0.0 0.21-05.02备注L203 200LL150/ 13L0L 30/0250L钻(铣杆刀) 1L05/2L02(铣钻杆) L刀120L1/582L0(0铣刀杆)钻L 10/L1710(钻铣刀杆)舍弃刀舍片刀片舍弃弃刀片L75舍1弃刀片钢刀钨钢刀钨钢刀钨钢刀钨钨刀钨钢刀钢钢刀白白钢刀钢刀白钨刀钢钨刀钢钨刀钨钢钢刀钨刀钢钨刀钢01-0..12 .20-.25 001.5-.022 0.-5.60 01.50.2 0-.40.- 0.1550.18 0.-30-4.0 .1-2.0150.0.3-0.1210. -1.120 .00-08.1 0.0-600. 8.05-0.0700 05 0.1-0..15 00.-08. 10.80-.100 0.-6.100.0 50.1 0.-500-. 0.15-0.0080. 5-0.07 0.00-4.06 00.2-0004 0..-01. 0.22-5.3 00.7-102.2 .052-0.30.170.2-2 .2-0025 .015-0..1 9.0-2.2050 1.-5.09 101.50.-8 1.0-0.15 101.50-18. 01-..051B27L 7(B5≤84 )精平面铣钢钨杆L刀615细耕作(≤90)B 钨刀钢钨钢刀杆31(B≤70) 钨钢0 刀钢钨刀杆116B≤5(0 )90、BL50 80、LB3 L45、B030≤ 38、L≤22B 50LB≤、4 L510B≤12、L 50、≤B1 L752、B70≤L7 0、≤B60 L0、6≤B50L 5、0B≤04L50、B≤35 L 50B≤、3 0L5、0≤B22 L0、B≤148 L40、≤B41 50、LB≤21L 0、钨钢刀5B ≤1 L210、B0≤06 L100、B6≤0L 00、1B≤50 L01、0≤B50L 01、0≤B0 410L0B、≤04CNC 钢料加工参数表因为铁材与铜材基本特性不同,所以必须因应材料的特性,改变切削进给率,转速切削量。
CNC模具加工要求

5.1 在编写路径前应把所要加工的工件图形放至标原点。
5.2 编制路径时,曲面、线条等的公差尽量设定在曲面为0.01mm线条为
0.005mm范围内。
30/89
5.3 认真检查所要绘的图是否漏绘细小的不引起注意的地方。
5.4 要反复检查所做的刀具路径是否产生过量或者加工面的少选。
5.5 产品清角时应把刀具设定为从大到小。
间隙,刀具的名字为D6R0.5-0.3,直径为5.7,圆角为0.5,
见下图所示:
46/89
2.1.9设定一个标准的刀库与加工参数,编程员在编写电极程序前应熟
悉此刀库及参数表(见附表一、附表二、附表三、附表四)
附表一 :
附表二 :
47/89
附表三 :
附表四 :
48/89
2.2 钢料加工标准
2.2.1 胶位尺寸标准:所有胶位、钢料编程都加工到数(特殊要求例
• 3-4考虑加工.(要
方便加工,防止变
形)
此面加强防止加工变形
7/89
3.拆电极需注意和考虑的问题:
• 3-5有无斜度,无
斜度需要自己加
斜度.
两头面需拔斜度方便加工防
止 刀 柄 撞 骨 位 变 形
8/89
3.拆电极需注意和考虑的问题:
修 补 后
• 3-6曲面整齐
清晰,避免很多
碎面,曲面需修
剪整齐.
引起变形
23/89
4.电极多处共用时的拆分顺序
• 4-1在铜料不浪
费的情况下,尽
量连到一起
• 电极多处使用时
尽量采用平移
• 其次使用旋转
• 最次使用镜像
24/89
4.电极多处共用时的拆分顺序
CNC加工编程参数
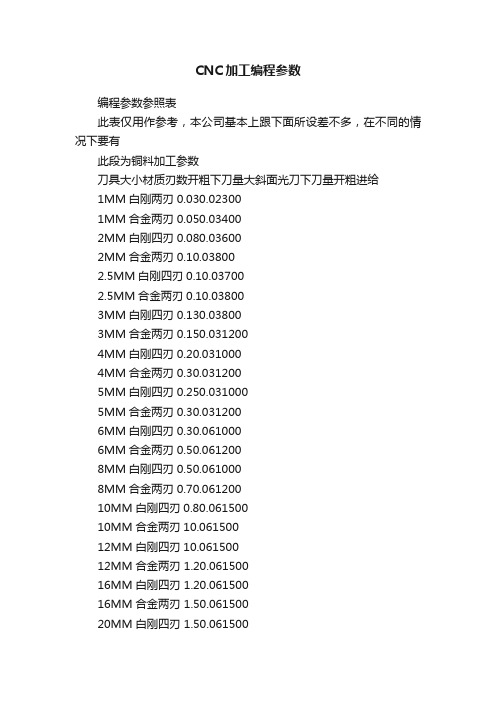
CNC加工编程参数编程参数参照表此表仅用作参考,本公司基本上跟下面所设差不多,在不同的情况下要有此段为铜料加工参数刀具大小材质刃数开粗下刀量大斜面光刀下刀量开粗进给1MM白刚两刃0.030.023001MM合金两刃0.050.034002MM白刚四刃0.080.036002MM合金两刃0.10.038002.5MM白刚四刃0.10.037002.5MM合金两刃0.10.038003MM白刚四刃0.130.038003MM合金两刃0.150.0312004MM白刚四刃0.20.0310004MM合金两刃0.30.0312005MM白刚四刃0.250.0310005MM合金两刃0.30.0312006MM白刚四刃0.30.0610006MM合金两刃0.50.0612008MM白刚四刃0.50.0610008MM合金两刃0.70.06120010MM白刚四刃0.80.06150010MM合金两刃10.06150012MM白刚四刃10.06150012MM合金两刃 1.20.06150016MM白刚四刃 1.20.06150016MM合金两刃 1.50.06150020MM白刚四刃 1.50.06150020MM合金两刃 1.50.06150025MM白刚四刃 1.50.06150025MM合金两刃 1.50.061500飞刀刀具刀具大小材质刃数开粗下刀量大斜面光刀下刀量开粗进给R6合金刀粒两刃0.450.151500R8合金刀粒两刃0.50.21500R10合金刀粒两刃0.60.2150012R0.4合金刀粒一刃0.70.1120016R0.4合金刀粒两刃0.70.1150020R0.4合金刀粒两刃0.70.1150025R0.8合金刀粒两刃10.1150030R5合金刀粒两刃0.60.31600球刀刀具刀具大小直径材质刃数开粗下刀量斜面光刀下刀量R0.51MM合金两刃0.020.02R11MM合金两刃0.040.05R1.53MM合金两刃0.060.07R24MM合金两刃0.150.1R2.55MM合金两刃0.20.1R36MM合金两刃0.30.12R48MM合金两刃0.30.12R510MM合金两刃0.50.15R612MM合金两刃0.50.15R816MM合金两刃0.60.2R1020MM合金两刃0.60.2编程参数参照表此表仅用作参考,本公司基本上跟下面所设差不多,在不同的情况下要有此段为钢料加工参数刀具大小材质刃数开粗下刀量大斜面光刀下刀量开粗进给2MM白刚四刃0.020.034002MM合金两刃0.040.035002.5MM白刚四刃0.020.034002.5MM合金两刃0.040.035003MM白刚四刃0.030.034003MM合金两刃0.050.036004MM白刚四刃0.050.036004MM合金两刃0.050.036005MM白刚四刃0.050.036005MM合金两刃0.050.038006MM白刚四刃0.060.066006MM合金两刃0.060.068008MM白刚四刃0.080.068008MM合金两刃0.10.06110010MM白刚四刃0.10.0680010MM合金两刃0.150.06110012MM白刚四刃0.130.07120012MM合金两刃0.150.07130016MM白刚四刃0.150.11300 16MM合金两刃0.20.11300 20MM白刚四刃0.20.11200 20MM合金两刃0.250.11200 25MM白刚四刃0.20.11200 25MM合金两刃0.250.131200飞刀刀具刀具大小材质刃数开粗下刀量大斜面光刀下刀量开粗进给R6合金刀粒两刃0.40.151500 R8合金刀粒两刃0.40.21500 R10合金刀粒两刃0.50.21500 12R0.4合金刀粒一刃0.20.11200 16R0.4合金刀粒两刃0.250.11500 20R0.4合金刀粒两刃0.30.11500 25R0.8合金刀粒两刃0.30.21500 30R5合金刀粒两刃0.50.31600 40R6合金刀粒两刃0.50.31500 63R5合金刀粒六刃0.60.31300球刀刀具刀具大小直径材质刃数开粗下刀量斜面光刀下刀量R11MM合金两刃0.030.03 R1.53MM合金两刃0.060.07R24MM合金两刃0.150.1 R2.55MM合金两刃0.20.1 R36MM合金两刃0.30.12 R48MM合金两刃0.30.12 R510MM合金两刃0.50.15 R612MM合金两刃0.50.15 R816MM合金两刃0.60.2 R1020MM合金两刃0.60.2下要有不同的改变光平面进给光斜面进给开粗转数光刀转数15030050006000150400550060002005004000450020050042005000200600350040002006004000450020060035004000200650400045002506003000350025065035004000250600300035003006503500400025060028003200300700300040002506002200250030080022003000300600220025004008002200300030060022002500400800220030004008001200120045010001200150040080010001000450100012001200400800800-100800450100010001000光平面进给光斜面进给开粗转数光刀转数150025003000150021002500150020002500500110022003000600120018003000600120018003000600130018002800700120016002000开粗进给光斜面进给开粗转数光刀转数300350550060006005004500450070060042004500110090040004500120080040004200150012003000380015001300300035001700150026003000180015002500300018001500250030001800150025002800下要有不同的改变光平面进给光斜面进给开粗转数光刀转数光侧面进给斜面转速2004503000320025050032003500200450300032002505003200350020045025002800250500260030002004502200250025050025003000250500180025003006502200280025050015002200300600200025002506001300230030080030080018002300300800300600120020002508004008001800200025080030080012001600250800400800150018002508004008007001200230400450100080012002504004008006001000200300450100060010002003004008005008002002504501000500800200250光平面进给光斜面进给开粗转数光刀转数15002500300015002100250015002000250050011002200300060012001800300060012001800300060013001800280070012001600200080012001600200010001200700-10001500开粗进给光斜面进给开粗转数光刀转数40040035004500 70060035004000 110090035004000 120080035004000 1500120025003000 1500130025003000 1700130022002800 1800150022002800 1800150020002600 1800150018002300。
CNC加工检验标准

加工余量
1)光刀位≤0.02mm;
2)插穿面在凸边留≤0.05mm;
3)待EDM位≤0.15mm,水平底面≤0.05mm;
4)深腔开粗位≤0.35mm。
5
数据检测
1)加工误差≤0.03mm(单边);
2)位置公差≤0.03mm。
6
完成程度
1)完成CNC程式单要求全部项目;
2)图纸要求附加项目。
1目的:明确CNC的加工标准及检验标准。
2适用范围:适用于本公司及外协厂的CNC加工。
3定义:无
4权责:公司及外协厂的CNC加工工件必须按照《CNC加工检验标准》进行检验。
5内容:
序号
检验内容
检验标准
1
光洁度
1)分型面及料位曲面加工扇形高度h≤0.001mm;
2)避空位曲面加工扇形高度h=0.003mm~0.005mm;
3)平面加工无明显刮伤圆刀纹。
4)精加工面无明显弹刀痕;
5)曲面光刀后无水波纹;
6)进刀点进刀痕级差≤0.02mm;
7)R角位加工顺滑,不出现阶梯状刀纹。
2
接刀痕
工件加工时接刀位置级差≤0.02mm。
3
清角位
1)精加工部分无弹刀纹,顺滑过度;
2)精加工部分接刀位级差≤0.0
CNC加工标准
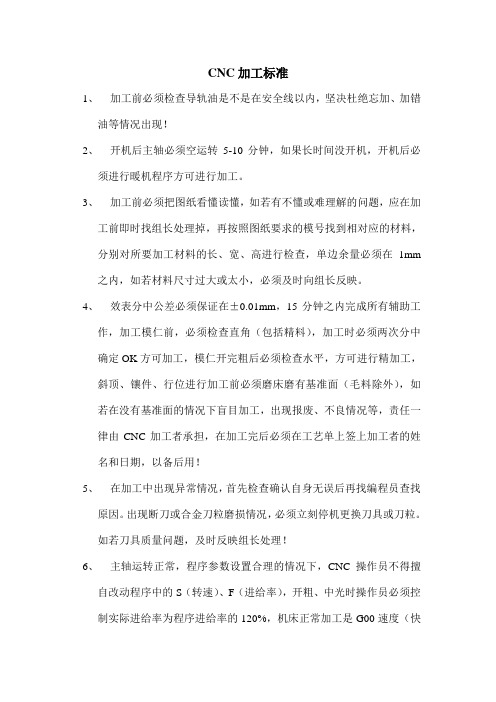
CNC加工标准1、加工前必须检查导轨油是不是在安全线以内,坚决杜绝忘加、加错油等情况出现!2、开机后主轴必须空运转5-10分钟,如果长时间没开机,开机后必须进行暖机程序方可进行加工。
3、加工前必须把图纸看懂读懂,如若有不懂或难理解的问题,应在加工前即时找组长处理掉,再按照图纸要求的模号找到相对应的材料,分别对所要加工材料的长、宽、高进行检查,单边余量必须在1mm 之内,如若材料尺寸过大或太小,必须及时向组长反映。
4、效表分中公差必须保证在±0.01mm,15分钟之内完成所有辅助工作,加工模仁前,必须检查直角(包括精料),加工时必须两次分中确定OK方可加工,模仁开完粗后必须检查水平,方可进行精加工,斜顶、镶件、行位进行加工前必须磨床磨有基准面(毛料除外),如若在没有基准面的情况下盲目加工,出现报废、不良情况等,责任一律由CNC加工者承担,在加工完后必须在工艺单上签上加工者的姓名和日期,以备后用!5、在加工中出现异常情况,首先检查确认自身无误后再找编程员查找原因。
出现断刀或合金刀粒磨损情况,必须立刻停机更换刀具或刀粒。
如若刀具质量问题,及时反映组长处理!6、主轴运转正常,程序参数设置合理的情况下,CNC操作员不得擅自改动程序中的S(转速)、F(进给率),开粗、中光时操作员必须控制实际进给率为程序进给率的120%,机床正常加工是G00速度(快速移动)必须为100%,精加工时,操作员必须控制实际进给率为程序的50%,以保证其光洁度。
7、在生产加工中,改模的铜公、改模模仁优先加工,其次为新模,新模模仁、滑块优先加工,其中钢料需外发淬火先开粗,相对应的加工此模铜公,铜公中铜打铜、线割、整公优先加工。
铜公精(F)粗(R)字码必须分清楚,线割铜公的字码必须打在铜公的底部,以免铜公需线割避空,把字码锣掉,给火花机加工带来不方便。
8、CNC操作员必须按照《模具加工工艺流程》加工,模具主管所安排的生产加工顺序,不得私自改变或调整,改模模仁,铜公及异常加工、未经批准私自加工严惩不贷。
模具加工工艺标准
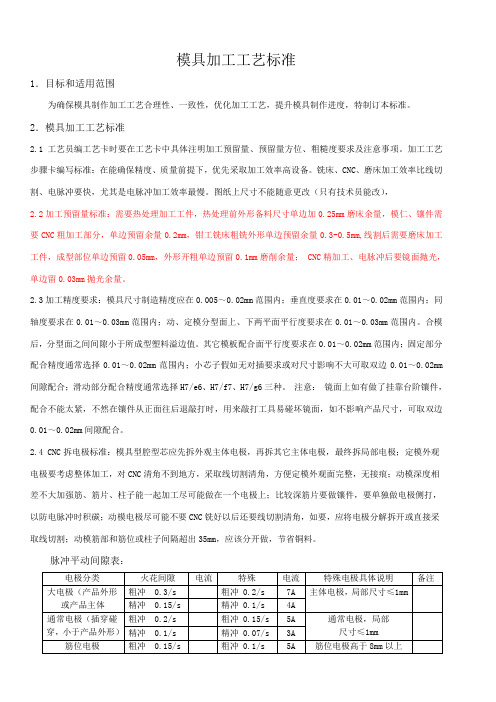
模具加工工艺标准1.目标和适用范围为确保模具制作加工工艺合理性、一致性,优化加工工艺,提升模具制作进度,特制订本标准。
2.模具加工工艺标准2.1工艺员编工艺卡时要在工艺卡中具体注明加工预留量、预留量方位、粗糙度要求及注意事项。
加工工艺步骤卡编写标准:在能确保精度、质量前提下,优先采取加工效率高设备。
铣床、CNC、磨床加工效率比线切割、电脉冲要快,尤其是电脉冲加工效率最慢。
图纸上尺寸不能随意更改(只有技术员能改),2.2加工预留量标准:需要热处理加工工件,热处理前外形备料尺寸单边加0.25mm磨床余量,模仁、镶件需要CNC粗加工部分,单边预留余量0.2mm,钳工铣床粗铣外形单边预留余量0.3-0.5mm,线割后需要磨床加工工件,成型部位单边预留0.05mm,外形开粗单边预留0.1mm磨削余量; CNC精加工、电脉冲后要镜面抛光,单边留0.03mm抛光余量。
2.3加工精度要求:模具尺寸制造精度应在0.005~0.02mm范围内;垂直度要求在0.01~0.02mm范围内;同轴度要求在0.01~0.03mm范围内;动、定模分型面上、下两平面平行度要求在0.01~0.03mm范围内。
合模后,分型面之间间隙小于所成型塑料溢边值。
其它模板配合面平行度要求在0.01~0.02mm范围内;固定部分配合精度通常选择0.01~0.02mm范围内;小芯子假如无对插要求或对尺寸影响不大可取双边0.01~0.02mm 间隙配合;滑动部分配合精度通常选择H7/e6、H7/f7、H7/g6三种。
注意:镜面上如有做了挂靠台阶镶件,配合不能太紧,不然在镶件从正面往后退敲打时,用来敲打工具易碰坏镜面,如不影响产品尺寸,可取双边0.01~0.02mm间隙配合。
2.4 CNC拆电极标准:模具型腔型芯应先拆外观主体电极,再拆其它主体电极,最终拆局部电极;定模外观电极要考虑整体加工,对CNC清角不到地方,采取线切割清角,方便定模外观面完整,无接痕;动模深度相差不大加强筋、筋片、柱子能一起加工尽可能做在一个电极上;比较深筋片要做镶件,要单独做电极侧打,以防电脉冲时积碳;动模电极尽可能不要CNC铣好以后还要线切割清角,如要,应将电极分解拆开或直接采取线切割;动模筋部和筋位或柱子间隔超出35mm,应该分开做,节省铜料。
- 1、下载文档前请自行甄别文档内容的完整性,平台不提供额外的编辑、内容补充、找答案等附加服务。
- 2、"仅部分预览"的文档,不可在线预览部分如存在完整性等问题,可反馈申请退款(可完整预览的文档不适用该条件!)。
- 3、如文档侵犯您的权益,请联系客服反馈,我们会尽快为您处理(人工客服工作时间:9:00-18:30)。
2.7 加工電極基準的方式:
2.7.1側壁與底面不同時精修(刀具刃部與端面同時切削會震動)。
2.7.2先精加工側壁再精加工底面(如上圖所示)。
2.8其它(注意事項)
2.8.1加工前先利用一次元確認加工物之X、Y、Z有無過切。
2.8.2注意加工前校模時毛邊的清理,以免尋邊造成誤差。
座標號即可,主程式名稱定義為O8001 O8002... ... O8011 O8012共12工位.
%
O0401(P1)(子程式名稱定義為O0401 O0402... ... O0411 O0412共12工位)
N1
#1=1(NT1)(第一把加工刀具對應刀庫中的刀具號,如T6在庫中3號,調用
改為#1=3)
#1=#7
#17Байду номын сангаас#23
#32=1
M98P8100
N8
M98P401(8)
IF[#8EQ0]GOTO990
IF[#8GT40]GOTO999
#33=108
#1=#8
#17=#24
#32=1
M98P8100
N9
M98P401(9)
IF[#9EQ0]GOTO990
IF[#9GT40]GOTO999
#33=109
N608
#3000=116(NOT HAVE #1)
N666
M99
%
附件二: SNC-64/V55加工程式
%
O8500(G54 P1主程式)
M743G90G17G40G80
N1
M98P500(1)
IF[#1EQ0]GOTO501
IF[#1GT15]GOTO502(刀具庫為15把刀,故當#1大於15號時即跳轉)
N7
#7=7(NT7)
#23=8700(S)
N8
#8=8(NT8)
#24=8800(S)
N9
#9=9(NT9)
#25=8900(S)
N10
#10=10(NT10)
#26=9000(S)
N11
#11=11(NT11)
#27=9100(S)
N12
#12=12(NT12)
#28=9200(S)
N13
#13=13(NT13)
#33=111
#1=#11
#17=#27
#32=1
M98P8100
N12
M98P401(12)
IF[#12EQ0]GOTO990
IF[#12GT40]GOTO999
#33=112
#1=#12
#17=#28
#32=1
M98P8100
N13
M98P401(13)
IF[#13EQ0]GOTO990
IF[#13GT40]GOTO999
(a)優先工作(priority)。
(b)已準備好的工作(ready)。
(c)跳過(skip、reserv)。
2.5.3.2舊的機械:只有座標設定,沒有加工順序先後。
2.5.4F-MACH 644:
(主程式)
G25
G57 H901
G90 G0 X0 Y0
Z50
G728
M166
G984 E2L0 R0.04
M3S5000
IF[#32EQ#0]GOTO603
IF[#32NE#136]GOTO603
G90G54.1P#32X0Y0
IF[#17NE#135]GOTO604
IF[#17LT3500]GOTO605
IF[#1NE#134]GOTO602
IF[#1EQ#0]GOTO608
G43H#1Z100.M3S#17
N5
M98P500(5)
IF[#5EQ0]GOTO990
IF[#5GT15]GOTO999
#33=#33*10+5
#1=#5
#17=#21
#32=54
M98P8100
N6
M98P500(6)
IF[#6EQ0]GOTO990
IF[#6GT15]GOTO999
#33=#33*10+6
#1=#6
#17=#22
%
O8100(子程式)
#134=#1
#135=#17
#136=#32
#137=#33
IF[#1EQ#0]GOTO601
T#1
M6
G49
G91G28Z0
IF[#1NE#134]GOTO602
IF[#1EQ#0]GOTO608
IF[#1EQ#138]GOTO101
/G65P9611H#1
N101
#138=#1
#33=#33*10+1(重新定義#33值)
#32=54(坐標系採用G54.G55,故#32=54或55)
M98P8100
N2
M98P500(2)
IF[#2EQ0]GOTO990
IF[#2GT15]GOTO999
#33=#33*10+2
#1=#2
#17=#18
#32=54
M98P8100
N3
M98P500(3)
M98P8100 (調用子程式O8100)
N2
M98P401(2)
IF[#2EQ0]GOTO990
IF[#2GT40]GOTO999
#33=102
#1=#2
#17=#18
#32=1
M98P8100
N3
M98P401(3)
IF[#3EQ0]GOTO990
IF[#3GT40]GOTO999
#33=103
G24 X600 Y400 Z400 I0 J0 K[V3003-11]
M03 S32000
G04 P30
M07
M56
G72 $1101
G0 Z50
M02
2.5.4.1主程式要有加工過負荷檢機能。
2.5.4.2主程式要有主軸上升機能。
2.5.4.3主程式要有CNC形狀控制機能。
2.5.4.4主程式要有干涉機能設定。
#17=8100(S)(第一把刀具之轉速如設為11000轉,則17=11000)
N2
#2=2(NT2)
#18=8200(S)
N3
#3=3(NT3)
#19=8300(S)
N4
#4=4(NT4)
#20=8400(S)
N5
#5=5(NT5)
#21=8500(S)
N6
#6=6(NT6)
#22=8600(S)
G91 Y-200
M98 P8500 (G54)
G91 G28 Z0
M98 P9820
M98 P9810
G91 Y-200
M98 P8600(G55)
M30
2.5.3SNC64(參照附件二)
2.5.3.1新的機器有:
2.5.3.1.1EROWA座倉。
2.5.3.1.2要有座標設定動作。
2.5.3.1.3加工順序為:
#1=#5
#17=#21
#32=1
M98P8100
N6
M98P401(6)
IF[#6EQ0]GOTO990
IF[#6GT40]GOTO999
#33=106
#1=#6
#17=#22
#32=1
M98P8100
N7
M98P401(7)
IF[#7EQ0]GOTO990
IF[#7GT40]GOTO999
#33=107
1用途
在模具加工時,使每位CNC操作人員能有所遵循依據,以達到加工統一化為目的。
2作業內容
2.1依圖面(水孔)位置,確認模仁、滑塊、入子等加工方向。
2.2夾持方式採用:壓條、EROWA、虎鉗,依工件之適用性選擇最佳夾持方式。
2.2.1壓條:注意床台平面之毛邊與鐵屑之清理,及壓條高度之調整。
2.2.2EROWA:注意EROWA孔中之清潔,以免使鋼球受損,並確認有無鎖緊。
2.8.3注意加工完之毛邊處理,避免下製程人員困擾與割傷。
2.8.4注意加工完之成品保護以防止撞傷等受損現象發生。
2.8.5注意任何加工中之異常處理,如刀具斷裂、磨耗等更換。
3其他:
3.1本作業標準每年九月,由責任單位負責召集有關單位檢討,並將檢討結果送事業單位主管審核。
3.2審核完成後,呈群主管核准,保存於製造單位,公佈後立即實施,修訂時亦同。
#32=54
M98P8100
N7
M98P500(7)
IF[#7EQ0]GOTO990
IF[#7GT15]GOTO999
M743G90G17G40G80
N1
M98P401(1)(調用一號坐標副程式)
IF[#1EQ0]GOTO501
IF[#1GT40]GOTO502
#33=101 (令#33等於101,為M198調用P值賦值,2號工位為201,3號工位
301類推)
#32=1 (令#32等於1,為G54.1P#32之#32賦值,2號工位為"2",3號工位"3"類推)
#29=9300(S)
N14
#14=14(NT14)
#30=9400(S)
N15
#15=15(NT15)(最多可一次加工15把刀)
#31=9500(S)
N16
#16=41(END)(此句用來結束加工用)
M99
%
備註:副程式名稱定義為O0401 O0402... ... O0411 O0412共12工位.
#33=115
#1=#15
#17=#31
#32=1