全抛釉瓷砖生产过程,别开口喊贵!
一篇文章看懂瓷砖生产全过程,每个环节都清清楚楚
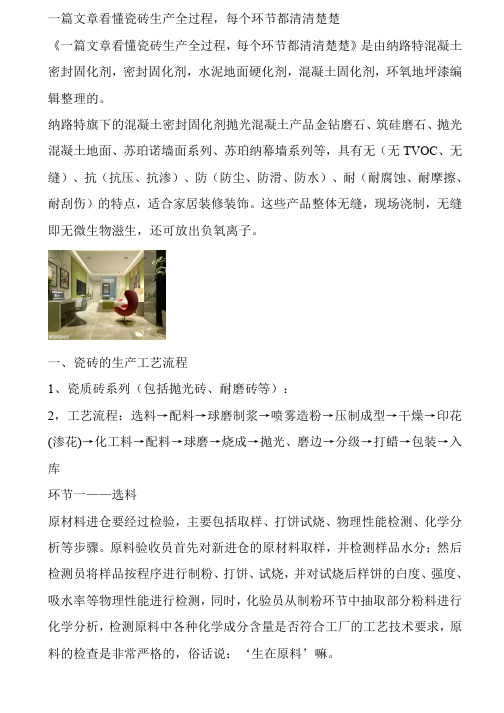
一篇文章看懂瓷砖生产全过程,每个环节都清清楚楚《一篇文章看懂瓷砖生产全过程,每个环节都清清楚楚》是由纳路特混凝土密封固化剂,密封固化剂,水泥地面硬化剂,混凝土固化剂,环氧地坪漆编辑整理的。
纳路特旗下的混凝土密封固化剂抛光混凝土产品金钻磨石、筑硅磨石、抛光混凝土地面、苏珀诺墙面系列、苏珀纳幕墙系列等,具有无(无TVOC、无缝)、抗(抗压、抗渗)、防(防尘、防滑、防水)、耐(耐腐蚀、耐摩擦、耐刮伤)的特点,适合家居装修装饰。
这些产品整体无缝,现场浇制,无缝即无微生物滋生,还可放出负氧离子。
一、瓷砖的生产工艺流程1、瓷质砖系列(包括抛光砖、耐磨砖等):2,工艺流程:选料→配料→球磨制浆→喷雾造粉→压制成型→干燥→印花(渗花)→化工料→配料→球磨→烧成→抛光、磨边→分级→打蜡→包装→入库环节一——选料原材料进仓要经过检验,主要包括取样、打饼试烧、物理性能检测、化学分析等步骤。
原料验收员首先对新进仓的原材料取样,并检测样品水分;然后检测员将样品按程序进行制粉、打饼、试烧,并对试烧后样饼的白度、强度、吸水率等物理性能进行检测,同时,化验员从制粉环节中抽取部分粉料进行化学分析,检测原料中各种化学成分含量是否符合工厂的工艺技术要求,原料的检查是非常严格的,俗话说:‘生在原料’嘛。
环节二——粉料制备粉料制备包括配料——球磨——过筛除铁——泥浆均化——喷雾干燥制粉——料仓陈腐等过程。
首先是根据工艺配方单(包括加水量)对相应的原料进行称重配料(是按一定的比例);然后将配好的原料加入球磨机进行研磨成浆,球磨机内按照工艺要求配好研磨介质——球石,目的是使各种块状、粗细不等的原料经研磨破碎后充分均匀混合,一方面能促进坯料在烧成过程中的物化反应,降低烧成温度,另一方面也有利于原料中杂质的分离;球磨后的泥浆经检测符合工艺质量要求放入浆池中,途中要进行过筛除铁。
过筛是为了除去球磨时没有磨细的粗颗粒和一些杂质;除铁是因为铁影响瓷砖的白度,而且会在瓷砖表面形成黑点、熔洞、杂质等缺陷,所以必须经过多道严格除铁;泥浆经过过筛除铁后,要不断的搅拌均化,是使泥浆组成更均匀,改善泥浆流动性能,增加后期制成的泥料的可塑性,提高坯体强度,减少成型、烧成时的开裂等。
全抛釉瓷砖生产进程别开口喊贵

全抛釉瓷砖的生产进程,别开口喊贵!《全抛釉瓷砖的生产进程,别开口喊贵!》是由纳路特混凝土密封固化剂,密封固化剂,水泥地面硬化剂,混凝土固化剂,环氧地坪漆编辑整理的。
全抛釉采纳世界先进的3D喷墨技术,通过色料和墨水的运用,将天然石材的纹理和色感传神还原,釉面纹理仿真度达到百分之95以上,自然神韵跃然于瓷砖之上,层次丰硕,颜色多变,立体感强。
置身家中也能体味大自然的隽美。
此刻,小编就为大伙儿讲解全抛釉产品的生产工艺流程,一路来深切了解吧。
纳路特旗下的混凝土密封固化剂抛光混凝本地货物金钻磨石、筑硅磨石、抛光混凝土地面、苏珀诺墙面系列、苏珀纳幕墙系列等,具有无(无TVOC、无缝)、抗(抗压、抗渗)、防(防尘、防滑、防水)、耐(耐侵蚀、耐摩擦、耐刮伤)的特点,适合家居装修装饰。
这些产品整体无缝,现场浇制,无缝即无微生物滋长,还可放出负氧离子。
全抛釉瓷砖的生产工艺流程第1道:原料开采、贮存陶瓷原料来自矿山、土壤,属天然原料,能够直接在矿山中挖掘:可塑性原料:黑泥、白泥等,决定了瓷砖的基础寿命;脊性原料:石英等,决定了瓷砖的各类性能;溶剂原料:长石等,决定了瓷砖的活力与韧性。
第2道:原料进厂检测瓷砖生产对原料化学成份及矿物组成都有严格的要求,因此在大量的原料进入厂区的堆场前都要进行一系列严格的分析、查验。
一:用先进的化学分析仪器分析原料的7大成份、可塑性指标、白度指标等;第二步:用快速磨打出浆料,检测其流动性、触变性;第三步:用激光粒径分析仪检测其球磨细度;第四步:按生产工艺用液压机压制成试样饼;第五步:放进电炉里烧成,检测其烧结程度、收缩指数等,以判定阻碍瓷砖成品外观的黑点、起泡、开裂、黑心等氧化物的多少;经检测合格的原料就能够进厂了,但是大自然直接开采的这些原料由于气候天气、形成时刻、层次结构等因素,它们是不稳固的,因此必需通过均化。
第3道:原料储蓄(均化、陈腐)均化,是原料通过机械运动搅拌均匀的一道工序;陈腐,指把混合好的泥料放置一段时刻,使泥料之间充分反映,使水分更均匀。
全抛釉瓷砖生产工艺

全抛釉瓷砖生产工艺全抛釉瓷砖是一种具有耐磨、耐酸碱腐蚀、易清洁、色彩丰富等特点的装饰材料,广泛应用于室内地面和墙面的装饰。
其生产工艺一般包括原料准备、制浆、模压、干燥、烧结、釉料制备、釉施打印、烧成等步骤。
首先,原料的准备是全抛釉瓷砖生产工艺的首要步骤。
原料主要包括石英砂、长石、白度高的粘土等。
这些原料首先经过初步混合,然后进一步研磨成细粉。
接下来是制浆的步骤。
将细粉原料与水进行混合,搅拌成糊状物,使其成为适合模压的浆料。
然后是模压的步骤。
将制浆得到的糊状物倒入模具中,通过振动和压实使其成型。
模具的选择可以根据需求定制,例如不同的纹理、尺寸、形状等。
完成模压后,瓷砖需要进行干燥。
通常采用自然干燥或加热干燥的方式,使瓷砖中的水分逐渐蒸发,使其表面达到合适的硬度。
接下来是烧结的步骤。
将干燥的瓷砖放入炉内进行高温烧结,使其成为坚硬的瓷质。
烧结的温度一般在1000℃以上,具体的烧结时间和温度根据不同的瓷砖种类而定。
完成烧结后,需要进行釉料的制备。
釉料一般由颜料、助剂、玻璃粉等材料组成。
这些材料经过粉碎、搅拌、过滤等步骤,最终得到稳定的釉料。
然后是釉施打印的步骤。
将釉料均匀地施加在瓷砖表面,并通过打印技术在釉面上添加图案、色彩等装饰元素。
打印的技术包括丝网印刷、数码喷墨等。
最后是烧成的步骤。
将釉施打印的瓷砖放入炉中进行二次高温烧结,使釉料与瓷砖充分融合,形成光滑、坚固的表面。
以上就是全抛釉瓷砖生产工艺的主要步骤。
通过这些步骤的操作,可以生产出各式各样的全抛釉瓷砖,满足不同消费者的需求。
同时,全抛釉瓷砖还可以根据市场需求进行创新和改进,提高产品的质量和设计性。
全抛釉瓷砖生产过程中常见技术问题及解决方法

1前言全抛釉瓷砖是一种可以在釉面进行抛光工序的特殊瓷砖,集仿古砖和抛光砖的优点于一身。
全抛釉瓷砖的釉面如抛光砖般光滑亮洁,同时其釉面花色如仿古砖般图案丰富,色彩厚重或绚丽,花纹各式各样,深受业界和广大消费者的喜爱。
随着装饰手段的多样化和工艺技术的不断进步,其市场份额占有率也逐步提高。
但是在全抛釉瓷砖实际生产过程中因受工艺因素影响,常见有针孔、熔洞,耐磨度不够,凹釉,砖型不好,耐酸碱,辊棒印等问题。
下面主要就全抛釉瓷砖生产过程中的上述这些常见技术问题进行探究,并提出了合理化的解决方法。
2全抛釉瓷砖生产过程中常见技术问题及解决方案全抛釉釉面出现针孔、熔洞的原因可以从以下几个方面考虑:砖坯粉料成型、釉料、淋釉、烧成等考虑。
2.1.1砖坯粉料成型方面a.配方或者选材不合理,导致烧失量过大,始熔点过高或者过低,不能和釉料始熔点相匹配。
b.球磨加工不够精细,过筛除铁不彻底,导致杂质郭惠法,熊超圆,陈光(清远市简一陶瓷有限公司,清远511500)因其独特的仿石材效果以及优越的物理性能,从出现以来,一直是家装行业的宠儿。
全抛釉瓷砖的产品质量与生产过程中各项工艺流程紧密相连,本文结合实际生产,从生产工艺角度,对全抛釉瓷砖的生产过程中常见技术问题进行探究,并提出了合理化的解决方法。
技术问题;解决方案针孔,可以加强过筛除铁。
c.压机压制后,砖坯表面有粉团或者假颗粒或者纤维状状杂质存在,调整粉料颗粒级配,必要时在压机进料口加多筛网,砖坯表面的纤维杂质可以在干燥窑加装喷火枪烧掉。
d.磨坯过深,导致坯体表面有小孔,适当磨浅即可。
e.压机压力过大,导致烧成时排气困难。
f.坯体有低温杂质造成,如低温煤粉,或者低温大颗粒。
g.坯体干燥落脏。
2.1.2釉料方面a.面釉中铝含量过低,或配方不合理,导致面釉耐火度或始熔点不能匹配烧成条件,目前多数陶瓷厂要求面釉中铝含量要达到30%以上。
b.和面釉相比,抛釉配方对于针孔的影响较小,一般要求抛釉硅铝总量要达到55%以上,从而提高配方的稳定性,生产实践中,当生产出现针孔时外加氧化铝浆也是有效措施之一。
瓷砖中全抛釉瓷砖的生产工艺流程,全抛釉瓷砖与抛光砖区别
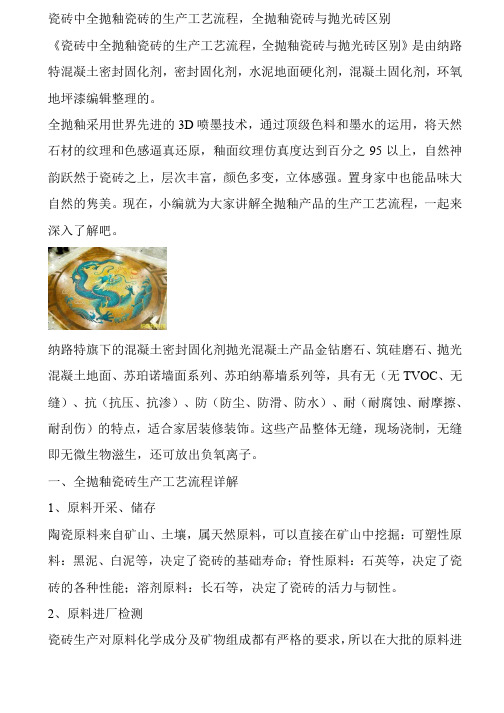
瓷砖中全抛釉瓷砖的生产工艺流程,全抛釉瓷砖与抛光砖区别《瓷砖中全抛釉瓷砖的生产工艺流程,全抛釉瓷砖与抛光砖区别》是由纳路特混凝土密封固化剂,密封固化剂,水泥地面硬化剂,混凝土固化剂,环氧地坪漆编辑整理的。
全抛釉采用世界先进的3D喷墨技术,通过顶级色料和墨水的运用,将天然石材的纹理和色感逼真还原,釉面纹理仿真度达到百分之95以上,自然神韵跃然于瓷砖之上,层次丰富,颜色多变,立体感强。
置身家中也能品味大自然的隽美。
现在,小编就为大家讲解全抛釉产品的生产工艺流程,一起来深入了解吧。
纳路特旗下的混凝土密封固化剂抛光混凝土产品金钻磨石、筑硅磨石、抛光混凝土地面、苏珀诺墙面系列、苏珀纳幕墙系列等,具有无(无TVOC、无缝)、抗(抗压、抗渗)、防(防尘、防滑、防水)、耐(耐腐蚀、耐摩擦、耐刮伤)的特点,适合家居装修装饰。
这些产品整体无缝,现场浇制,无缝即无微生物滋生,还可放出负氧离子。
一、全抛釉瓷砖生产工艺流程详解1、原料开采、储存陶瓷原料来自矿山、土壤,属天然原料,可以直接在矿山中挖掘:可塑性原料:黑泥、白泥等,决定了瓷砖的基础寿命;脊性原料:石英等,决定了瓷砖的各种性能;溶剂原料:长石等,决定了瓷砖的活力与韧性。
2、原料进厂检测瓷砖生产对原料化学成分及矿物组成都有严格的要求,所以在大批的原料进入厂区的堆场前都要进行一系列严格的分析、检验。
首先,用先进的化学分析仪器分析原料的7大成分、可塑性指标、白度指标等;第二步,用专业的快速磨打出浆料,检测其流动性、触变性;第三步,用激光粒径分析仪检测其球磨细度;第四步,按生产工艺用液压机压制成试样饼;第五步,放进电炉里烧成,检测其烧结程度、收缩指数等,以判断影响瓷砖成品外观的黑点、起泡、开裂、黑心等氧化物的多少。
经检测合格的原料就能进厂了,然而大自然直接开采的这些原料由于气候天气、形成时间、层次结构等因素,它们是不稳定的,因此必须经过均化。
3、原料储备(均化、陈腐)均化,是原料通过机械运动搅拌均匀的一道工序;陈腐,指把混合好的泥料放置一段时间,使泥料之间充分反应,使水分更均匀。
全抛釉瓷砖的生产工艺

全抛釉瓷砖的生产工艺
全抛釉瓷砖是将釉料均匀地涂覆在整个瓷砖表面,然后在高温下进行烧制而成的。
其生产工艺主要包括以下几个步骤:
1.瓷砖基材制备:选用高质量的瓷土、石英、长石等原料,按一
定比例混合,然后经过成型、干燥等工序制成瓷砖基材。
2.底釉施工:将一种白色或浅色釉料均匀地涂覆在瓷砖表面,形
成一层底釉。
底釉的作用是增加瓷砖表面的光泽度,提高釉层与基材之间的附着力。
3.装饰釉施工:将颜色、花纹等装饰釉料均匀地涂覆在底釉上,
形成瓷砖的装饰层。
装饰釉的颜色、花纹可以根据需求来选择和设计。
4.烧制:将经过装饰釉施工的瓷砖放入窑炉中进行高温烧制,通
常烧制温度在1180-1250℃之间。
烧制过程中,瓷砖表面的釉料会融化、流淌,形成均匀的玻璃状釉层,与瓷砖基材紧密结合。
5.后处理:烧制完成后,瓷砖需要经过冷却、检验、分类、包装
等后处理工序。
其中检验是非常重要的一步,要检查瓷砖的表面光泽度、颜色、花纹、尺寸等是否符合要求。
以上是全抛釉瓷砖的生产工艺,这种工艺能够生产出表面光滑、光泽度高、色彩丰富的瓷砖,具有良好的防污、耐磨、易清洁等特点。
瓷砖生产流程

瓷砖生产流程
瓷砖是一种常见的建筑材料,广泛应用于室内和室外装饰。
瓷
砖的生产流程经历了多个环节,包括原料处理、成型、烧制、装饰
和包装等步骤。
首先,瓷砖的生产需要使用多种原料,主要包括粘土、石英砂、长石和其他添加剂。
这些原料经过精确的配比和混合后,形成了瓷
砖的坯料。
坯料的质量对瓷砖的成品质量有着重要的影响。
接下来,坯料通过成型机器进行成型。
成型的方式主要有干压
成型和浇注成型两种。
在成型过程中,需要根据设计要求制作出不
同规格和花色的瓷砖产品。
成型完成后,瓷砖需要进行烧制。
烧制是整个生产流程中最为
关键的环节之一。
瓷砖在高温窑炉中进行烧制,经过一系列的热处
理过程,使得瓷砖的物理性能得到提升,同时也赋予了瓷砖特有的
色泽和纹理。
烧制完成后,瓷砖需要进行装饰。
装饰的方式多样,可以通过
釉料的涂覆、釉下彩的绘制等方式进行。
装饰的目的是为了提升瓷
砖的外观质感,使其更具装饰性和美观性。
最后,经过装饰的瓷砖产品需要进行包装。
包装的方式通常是采用纸箱包装或托盘包装,以保护瓷砖在运输和搬运过程中不受损坏。
总的来说,瓷砖的生产流程经过原料处理、成型、烧制、装饰和包装等多个环节。
每个环节都需要精心操作和严格控制,以确保最终生产出高质量的瓷砖产品。
这些瓷砖产品不仅可以满足建筑装饰的需求,同时也在美化人们的生活环境中发挥着重要的作用。
全抛釉的生产工艺

全抛釉的生产工艺
全抛釉工艺是一种现代瓷砖生产技术,采用全抛釉工艺生产出来的瓷砖表面光滑,色彩鲜艳,花纹细腻,质感逼真,具有很高的装饰性和实用性。
全抛釉工艺的生产过程主要分为原料准备、成型、干燥、上釉、烧制等几个工序。
首先是原料准备,根据产品需求选择合适的原料,主要包括粘土、石英石、矿物颜料等。
这些原料经过精细的加工和配比,确保了产品的质量和性能。
然后是成型工序,将原料通过挤压成型机进入线切割机进行切割,形成瓷坯。
然后经过热压缩成型,使瓷坯的外观平整,大小一致。
成型后的瓷坯经过抛光处理,使瓷砖表面更加光滑。
接着是干燥工序,将成型后的瓷坯放入干燥室进行干燥处理,以去除水分,提高瓷砖的密度和强度。
然后是上釉工序,将已经干燥的瓷坯送入喷釉机,通过高压喷枪将釉料均匀喷涂在瓷砖表面,形成一层厚度均匀的釉层。
釉料主要由矿石、氧化物和颜料等组成,可以根据需要调整颜色、材质和光泽度等。
最后是烧制工序,将已经上釉的瓷坯放入烧窑进行高温烧制,使其达到应有的力学性能和表面光洁度。
烧制温度通常在1200℃-1300℃之间,烧制时间根据产品要求和材料性能不同,
一般在8-24小时。
全抛釉工艺的优点是瓷砖表面光滑、色彩鲜艳,不易受污染,易于清洁和保养。
由于上釉均匀,瓷砖表面不会出现釉层厚度不均匀、颜色不一致的现象。
同时,全抛釉瓷砖采用的是完全人工控制的技术,能够提供更多的选择和个性化定制。
总之,全抛釉工艺是一种高技术含量的现代瓷砖生产工艺,它不仅提供了更好的装饰效果和使用体验,还为设计师和消费者提供了更多的选择空间,推动了瓷砖行业的发展。
全抛釉生产流程

全抛砖生产工艺流程
根据生产产品要求,将先备用好的泥、砂、石、土等原料混合调整好后,对原料进行加工制成泥浆,首先原料装罐球磨,球磨达到要求后放入浆池,
制粉时再将泥浆泵到喷雾干燥塔制成成型粉料,再转到料仓进行陈腐,生产
时将制好的料仓粉料转到压机压制成型,干燥窑烘干,烘干要达到干燥标准
要求,可以后进入釉线生产:砖坯施釉、印花、烧成、磨边、抛光、打蜡、
分选后打包入库。
工艺流程图:
原料配料→球磨→浆池→喷雾塔喷粉→料仓陈腐→
压机成型→干燥烘干→施釉印花→烧成→磨边→抛光→打蜡→分级→打包→入库。
全抛釉瓷砖的生产工艺

全抛釉瓷砖的生产工艺
全抛釉瓷砖是一种采用全抛釉工艺生产的瓷砖产品,其生产工艺大致分为以下几个步骤:
1. 原料准备:根据产品需求,选择适当的瓷砂、高岭土、长石等原材料,并按照一定的比例进行搅拌混合。
2. 瓷砖成型:将混合好的原料通过压制机或注塑机进行成型。
一般采用大型压机将混合好的原料压制成固定尺寸的坯体。
也可以采用注塑机进行成型,将原料注入模具中并加压成形。
3. 瓷砖干燥:将成型的瓷砖坯体放置在通风良好的场所,使其逐渐干燥。
这个过程中,要控制好干燥的速度和时间,以免出现开裂等问题。
4. 胚体修整:对干燥好的瓷砖坯体进行修整。
这个步骤主要是利用机械设备对瓷砖的四周进行修整,使其形状更加规整。
5. 上釉:在瓷砖坯体表面上涂上一层釉料。
全抛釉瓷砖需要涂抹两层釉料,一层是基础釉,用于填充瓷砖表面的细微凹凸;另一层是浮釉,用于增加瓷砖表面的光泽和颜色。
6. 釉料烧成:将上釉的瓷砖坯体放入窑炉中进行高温烧制。
这个过程中,瓷砖
坯体中的矿石物质和釉料会发生化学反应,形成玻化层和釉面。
烧制温度通常在1000C以上,具体温度和时间根据瓷砖的要求进行调控。
7. 切割和打磨:将烧制好的瓷砖坯体进行切割,根据产品规格和尺寸进行个性化定制。
切割后还需要进行打磨,以使瓷砖表面更加光滑。
8. 包装和质检:对成品瓷砖进行外包装,以防止瓷砖在运输过程中受损。
同时还需进行严格的质量检查,确保产品符合标准要求。
以上就是全抛釉瓷砖的生产工艺的主要步骤,不同的生产厂家可能会有略微不同的工序和技术,但整体的生产流程大致相似。
瓷砖生产工艺流程
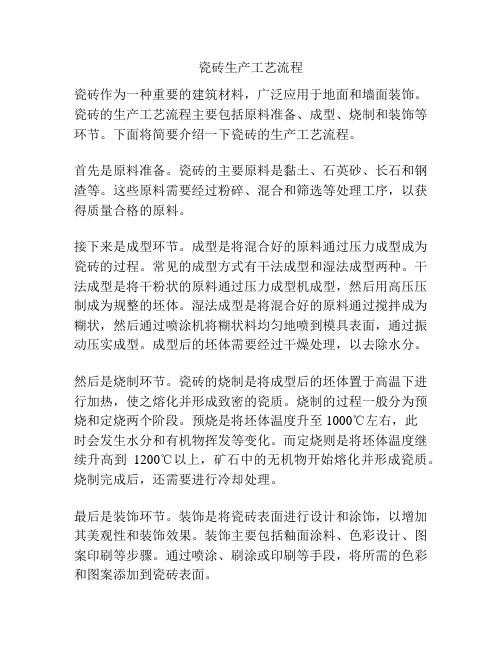
瓷砖生产工艺流程瓷砖作为一种重要的建筑材料,广泛应用于地面和墙面装饰。
瓷砖的生产工艺流程主要包括原料准备、成型、烧制和装饰等环节。
下面将简要介绍一下瓷砖的生产工艺流程。
首先是原料准备。
瓷砖的主要原料是黏土、石英砂、长石和钢渣等。
这些原料需要经过粉碎、混合和筛选等处理工序,以获得质量合格的原料。
接下来是成型环节。
成型是将混合好的原料通过压力成型成为瓷砖的过程。
常见的成型方式有干法成型和湿法成型两种。
干法成型是将干粉状的原料通过压力成型机成型,然后用高压压制成为规整的坯体。
湿法成型是将混合好的原料通过搅拌成为糊状,然后通过喷涂机将糊状料均匀地喷到模具表面,通过振动压实成型。
成型后的坯体需要经过干燥处理,以去除水分。
然后是烧制环节。
瓷砖的烧制是将成型后的坯体置于高温下进行加热,使之熔化并形成致密的瓷质。
烧制的过程一般分为预烧和定烧两个阶段。
预烧是将坯体温度升至1000℃左右,此时会发生水分和有机物挥发等变化。
而定烧则是将坯体温度继续升高到1200℃以上,矿石中的无机物开始熔化并形成瓷质。
烧制完成后,还需要进行冷却处理。
最后是装饰环节。
装饰是将瓷砖表面进行设计和涂饰,以增加其美观性和装饰效果。
装饰主要包括釉面涂料、色彩设计、图案印刷等步骤。
通过喷涂、刷涂或印刷等手段,将所需的色彩和图案添加到瓷砖表面。
总的来说,瓷砖的生产工艺流程包括原料准备、成型、烧制和装饰等环节。
这些环节需要严格按照工艺要求进行操作,以保证瓷砖的质量和装饰效果。
而瓷砖的生产工艺流程也在不断创新和改进中,以满足人们对于瓷砖的多样化需求。
生料高耐磨全抛釉及其设备制作方法与制作流程

本技术公开了生料高耐磨全抛釉及其制备方法,由以下原料按照重量份数组成:钾长石28~38份、高岭土4~7份、烧滑石5~10份、白云石5~10份、碳酸钡16~22份、烧氧化锌5~8份、熔融石英10~18份、刚玉微粉3~12份、含锂矿物1~5份、外加剂5~10份。
本技术引入了刚玉颗粒和熔融石英颗粒,保证了部分原有耐磨颗粒的存在,而且还生成了大量的钙长石和钡长石微晶,提高了釉面耐磨性;另外在全抛釉中加入了含锂矿物,使得全抛釉在低温下就产生液相,由于锂元素离子半径小,形成的玻璃网络紧密,从而也提高了釉面耐磨性。
技术要求1.生料高耐磨全抛釉,其特征在于,由以下原料按照重量份数组成:钾长石28~38份、高岭土4~7份、烧滑石5~10份、白云石5~10份、碳酸钡16~22份、烧氧化锌5~8份、熔融石英10~18份、刚玉微粉3~12份、含锂矿物1~5份、外加剂5~10份。
2.根据权利要求1所述的生料高耐磨全抛釉,其特征在于:所述的含锂矿物是锂辉石、透锂长石或锂霞石的一种或几种混合。
3.根据权利要求1所述的生料高耐磨全抛釉,其特征在于:所述的外加剂是硅溶胶。
4.根据权利要求1到3任一项所述的生料高耐磨全抛釉的制备方法,其特征在于,包括以下步骤:(1)除外加剂外的各种原料按照配比准确称量加入球磨机内进行混合球磨,球磨完在放浆池中按照比例加入外加剂,充分均匀搅拌为成釉,陈腐备用;(2)砖坯料依次进行球磨、过筛、除铁、造粒、压制成型、干燥、喷水施底釉、印花或喷墨加彩、淋所述的生料高耐磨全抛釉、烧成、抛釉;所述的烧成温度为1160~1180℃下,最高温度保温时间为8~10分钟,烧成总用时为50~60分钟的。
生料高耐磨全抛釉及其制备方法技术领域本技术涉及建筑陶瓷釉料技术领域,尤其涉及一种生料高耐磨全抛釉及其制备方法。
背景技术全抛釉砖是一种可以对喷墨打印等加彩的底釉施全抛釉面釉后进行抛光的一种特殊釉。
全抛釉砖集抛光砖与大理石砖优点于一体,釉面如抛光砖般光洁亮丽,同时其釉面花色如大理石砖般图案丰富,色彩厚重或绚丽。
瓷砖产品的生产工艺

产品的生产工艺流程图一、抛光砖生产工艺流程图:1、原料:抛光砖的花色稳定最主要来自于坯体及原料本身的稳定,所以对原料的选择和使用成为了抛光砖产品生产的第一道门户,也是最重要的环节,抛光砖产品主要原料种类:坭、砂、石、化工料。
2、球磨:球磨工序就是把各种原料按照一定的配比,通过球磨机的转动及研磨体的研磨,变成浆状物质的过程。
3、制粉:制粉工序也属于原料加工的辅助工序,通过加热,使球磨工序制备的浆料变成粉料的过程。
4、压制:通过压机的压制,使制粉工序生产的粉料变成抛光砖半成品的过程5、干燥:压机压制的抛光砖半成品通过干燥窑,把水份蒸发,使其半成品的强度提高,能够符合运输或印花时不产生开裂。
6、印花:无机颜料通过花网印在干燥后的砖坯表面,使颜料渗进砖坯内部的过程就被称为印花;最终在抛光后,颜料的颜色又能够重新显现在砖坯表面,这就是渗花抛光砖被称为“渗花”的来源。
7、烧成:从原料到烧成,共经历了五道大的工序,付诸了生产大部分人员的心血,最终是否有所收获,就取决于烧成工序的烧成结果,抛光砖产品需要很高的温度烧成,通常都是在1200摄氏度左右。
8、抛光:烧成后的半成品表面是没有图案的,需要把表层拨开,图案才能够显现出来。
故而需要有抛光工序对半成品进行加工。
通常抛光的厚度都保持在0.6~1.2毫米左右。
抛光后的光度可达到60度以上.。
9、分选:为了使不合格的产品不流入仓库和消费者手中,必须对抛光后的抛光砖进行分选。
通过分选,根据花色的异同,把相同花色的产品归为一个色别,并且把不符合内控分选标准的产品挑选出,作为不合格产品进行处理。
10、超洁亮:超洁亮的使用材料是高科技纳米无机材料,制作过程需要通过两次研磨和抛光,工艺控制复杂困难,它的工艺原理是: 纳米材料(液态)施在抛光砖的表面,通过磨头在表面进行研磨和抛光,使纳米材料充分填充在砖表面的毛孔内部,达到防污和增加亮度的目的。
二、全抛釉生产工艺流程图:1、原料:釉面砖的质量稳定最主要来自于坯体及原料本身的稳定,所以对原料的选择和使用成为了釉面砖产品生产的第一道门户,也是最重要的环节,釉面砖产品主要原料种类:坭、砂、石、化工料。
抛釉砖的生产工艺流程

抛釉砖的生产工艺流程
《抛釉砖的生产工艺流程》
抛釉砖是一种非常常见的建筑材料,用于室内和室外的装饰工程。
其生产工艺流程包括以下几个步骤:
1. 原料准备:抛釉砖的主要原料包括粘土、石英砂、煤粉和各种化学添加剂。
这些原料要经过精确的配比和混合,确保产品的质量和性能。
2. 成型:经过原料准备后,将混合好的材料送入成型机进行成型。
成型机通过挤压和振动的方法将原料压制成砖形,并在成型过程中进行定型和压花处理。
3. 干燥:新成型的抛釉砖需要进行自然晾晒和人工干燥。
在这个过程中,要控制好温度和湿度,确保产品无裂纹和变形。
4. 烧制:干燥后的抛釉砖送入烧窑进行高温烧制。
在烧制的过程中,砖坯会经历预热、烧成和冷却等多个阶段,确保产品的物理性能和表面光泽。
5. 抛釉:烧制好的砖坯送入抛釉线进行表面处理。
通过喷涂或浸泡的方式,将各种颜色的釉料均匀地涂抹在砖表面,并经过高温烧结,形成坚固的釉面。
6. 包装:经过抛釉处理的砖坯进行检验,合格后进行包装和装箱。
包装时要注意防水防潮,确保产品在运输和存储中不受损
坏。
以上就是抛釉砖的生产工艺流程,每个步骤都需要严格控制和操作,确保产品质量和性能达到标准要求。
抛釉砖因其美观、耐磨、易清洁等特点,在建筑装饰领域得到了广泛的应用。
抛釉砖制作工艺流程

抛釉砖制作工艺流程嘿,朋友们!今天咱就来讲讲抛釉砖制作工艺流程,这可有意思啦!你想想看,一块平平无奇的原材料,是怎么摇身一变成为那漂亮又实用的抛釉砖呢?那就跟着我一起来探秘吧!首先,得有好的原料呀,就像做饭得有新鲜的食材一样。
这些原料被精心挑选,然后混合在一起,就像是给它们来了一场大聚会。
接着,它们被送进一个大机器里,被压呀压,就变成了一块一块的砖坯。
这砖坯就像是还没打扮的小姑娘,虽然有模有样了,但还不够漂亮呢!接下来,就是给砖坯化妆的时候啦!它们会被送进一个神奇的地方,喷上一层又一层的釉料。
这釉料可神奇了,就像给砖坯穿上了一件华丽的外衣。
而且这外衣可不是随便穿的,得均匀,得漂亮,得让每一块砖都美美的。
然后呢,砖坯就被送进窑里啦!这窑就像是一个大火炉,把砖坯烤得热乎乎的。
在这高温的烘烤下,釉料和砖坯紧紧地融合在一起,变得坚不可摧。
这就像是一场考验,只有经过了这场考验,才能成为真正的抛釉砖。
等砖从窑里出来,哇塞,那简直就像变魔术一样,变得亮晶晶、光闪闪的。
它们被工人们仔细地检查,有一点点瑕疵都不行哦!就像我们出门得打扮得整整齐齐一样,这些抛釉砖也得完美无缺才能走向市场。
你说这制作抛釉砖是不是很神奇?从一块普通的原料到一块漂亮的抛釉砖,这中间经历了多少道工序呀!每一道工序都像是一场冒险,都需要工人们的精心呵护和认真对待。
你再想想,我们家里的地板、墙壁,那些漂亮的抛釉砖,都是经过了这么多步骤才来到我们身边的。
它们不仅仅是一块砖,更是工人们的心血和汗水呀!所以呀,我们在使用抛釉砖的时候,可一定要好好珍惜它们,别轻易地去破坏它们。
因为它们背后的故事,真的很值得我们去尊重和敬佩呢!这就是抛釉砖制作工艺流程,是不是很有趣?是不是让你对那些平时不起眼的砖有了新的认识?哈哈!。
抛釉砖的生产工艺流程

抛釉砖的生产工艺流程
抛釉砖是一种常用的建筑用砖,具有良好的耐久性和美观性。
它的生产工艺流程相对较为复杂,包括原料准备、成型、烧制和抛釉等环节。
下面我将详细介绍抛釉砖的生产工艺流程。
首先是原料准备。
抛釉砖的主要原料是黏土和石英砂。
黏土可以提供砖体的黏结性,而石英砂则能够增加砖体的强度。
在原料准备阶段,需要对黏土和石英砂进行筛选和混合,确保其质量合格。
接下来是成型阶段。
在这一阶段,将准备好的原料与适量的水混合,制成泥浆状。
然后将泥浆通过成型机进行成型,常见的成型机有真空外排型和挤压型。
成型机通过挤出、拉伸和压实等工艺,将泥浆压制成形成具有一定形状和尺寸的砖坯。
然后是烧制阶段。
成型后的砖坯需要进行烧制,以使其具有一定的强度和稳定性。
烧制是将砖坯置于烧窑中,通过高温处理,使其发生一系列物理、化学反应,最终转变为具有一定力学性能的砖体。
烧制的温度和时间可以根据砖体的要求进行调节,一般烧制温度在1000℃-1300℃之间。
最后是抛釉阶段。
经过烧制的砖体可以进行抛釉处理,以改善其表面的光泽和外观。
抛釉是将砖体表面涂上一层抛釉料,并进行干燥和烧结的过程。
抛釉料可以根据需要选择不同的颜色和质感,以满足不同的设计要求。
砖体经过抛釉后,其表面会变得光滑、亮丽,具有一定的防水和防污性能。
以上就是抛釉砖的生产工艺流程。
整个流程需要经过原料准备、成型、烧制和抛釉等多个环节,每个环节都需要严格控制和操作,以保证最终产品的质量和性能。
抛釉砖以其美观、实用和耐久的特点,在建筑装饰中得到广泛应用。
瓷质抛光砖生产工艺
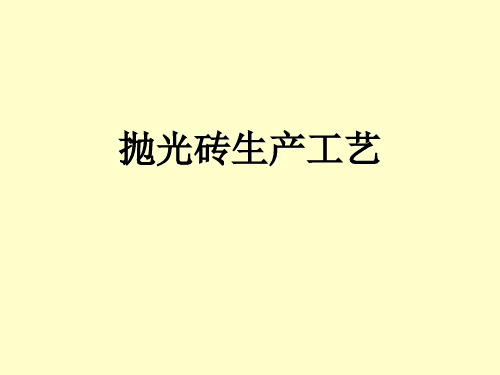
八)、釉线或印花
砖坯出了干燥窑之后通过釉线进入烧成窑,根据不同的产 品,釉线上会有不同的作用,对于普通的微粉砖釉线只是 作为输送带而已,如果是生产渗花砖,则需要在釉线处进 行印花和喷水。如果是生产象莽岩这类产品则需要在釉线 上进行喷透明釉。
九)、烧
成
1、砖坯进入烧成窑之后通过高温让砖坯进行瓷化,一般来 说烧成的温度在1250度以上,根据不同的配方和冲压次数 温度也有所不同。 2、烧成时间根据冲压次数以及公司的窑炉产能的考核决定。 3、窑炉的产量主要也是看冲压次数以及窑炉的长度。 4、窑炉在烧成过程中需要调节窑炉的烧成温度,温度曲线、 窑炉的气氛、以及急冷管的开度。调节以上参数可控制砖 的吸水率、砖的平整度、抗折强度、滞后变形以及砖面的 针孔、防污。 5、现有4条行业最长窑炉329米,上下温差一般不超过过3℃, 确保每件砖坯的性能稳定而优秀。
二)、球
磨
1、球磨机对坭砂料进行球磨,球磨时间一般在15--20小时。 球磨介质主要是中高铝球石。 2、球磨过程中需要对球磨机里面的树根或者杂物进行打捞, 预防部分有机物磨碎后混入浆料而造成针孔或溶洞。 3、球磨合格后工艺质检进行浆料的检测,细度标准(250筛 余)0.8~1.0%,浆料水分32~35%,流速30~60秒,比重 1.69~1.72。大部分石英颗粒的粒径小于40微米。 4、以上工艺标准都满足要求之后才可以放浆入浆池。浆池 搅拌机不停对浆料进行搅拌,预防浆料沉淀。 5、我公司现有16台100吨球磨机,研磨细度及球磨效果均为 行业内最好,充分保证生产质量。
抛光砖生产工艺
一、陶瓷的分类 二、抛光砖的生产原料 三、抛光砖的生产工艺流程及具体内容 四、抛光超洁亮介绍 五、瓷砖印花的第三次革命----喷墨印花技术 六、抛光砖后时代的终结者----全抛釉产品介 绍 七、新产品介绍 八、我司部分优势设备介绍
全抛釉的生产工艺及性能研究

远泰陶瓷化工有限公司研发的全抛釉釉层SEM
晶体也是常见的晶体之一,硬度在4~5级之间
度上可以提高釉面的硬度和抗热震性能。
有文献研究表明[1],引入煅烧α-氧化铝可以在一定程度上提升釉面的硬度。
实践表明,选用
α-氧化铝,添加量在0%~15%的范围内
影响全抛釉透明度的同时,可以提高釉面耐磨性能
入过多的煅烧α-氧化铝,会使全抛釉的高温黏度增大釉层透明度降低,严重影响喷墨色彩的呈现。
全抛釉的膨胀系数及砖型的控制
通常在生产过程中,全抛釉料的热膨胀系数较面釉为了保持瓷砖(600mm×1200mm、800mm×800。
- 1、下载文档前请自行甄别文档内容的完整性,平台不提供额外的编辑、内容补充、找答案等附加服务。
- 2、"仅部分预览"的文档,不可在线预览部分如存在完整性等问题,可反馈申请退款(可完整预览的文档不适用该条件!)。
- 3、如文档侵犯您的权益,请联系客服反馈,我们会尽快为您处理(人工客服工作时间:9:00-18:30)。
全抛釉瓷砖的生产过程,别开口喊贵!《全抛釉瓷砖的生产过程,别开口喊贵!》是由纳路特混凝土密封固化剂,密封固化剂,水泥地面硬化剂,混凝土固化剂,环氧地坪漆编辑整理的。
全抛釉采用世界先进的3D喷墨技术,通过色料和墨水的运用,将天然石材的纹理和色感逼真还原,釉面纹理仿真度达到百分之95以上,自然神韵跃然于瓷砖之上,层次丰富,颜色多变,立体感强。
置身家中也能品味大自然的隽美。
现在,小编就为大家讲解全抛釉产品的生产工艺流程,一起来深入了解吧。
纳路特旗下的混凝土密封固化剂抛光混凝土产品金钻磨石、筑硅磨石、抛光混凝土地面、苏珀诺墙面系列、苏珀纳幕墙系列等,具有无(无TVOC、无缝)、抗(抗压、抗渗)、防(防尘、防滑、防水)、耐(耐腐蚀、耐摩擦、耐刮伤)的特点,适合家居装修装饰。
这些产品整体无缝,现场浇制,无缝即无微生物滋生,还可放出负氧离子。
全抛釉瓷砖的生产工艺流程第1道:原料开采、储存陶瓷原料来自矿山、土壤,属天然原料,可以直接在矿山中挖掘:可塑性原料:黑泥、白泥等,决定了瓷砖的基础寿命;脊性原料:石英等,决定了瓷砖的各种性能;溶剂原料:长石等,决定了瓷砖的活力与韧性。
第2道:原料进厂检测瓷砖生产对原料化学成分及矿物组成都有严格的要求,所以在大批的原料进入厂区的堆场前都要进行一系列严格的分析、检验。
一:用先进的化学分析仪器分析原料的7大成分、可塑性指标、白度指标等;第二步:用快速磨打出浆料,检测其流动性、触变性;第三步:用激光粒径分析仪检测其球磨细度;第四步:按生产工艺用液压机压制成试样饼;第五步:放进电炉里烧成,检测其烧结程度、收缩指数等,以判断影响瓷砖成品外观的黑点、起泡、开裂、黑心等氧化物的多少;经检测合格的原料就能进厂了,然而大自然直接开采的这些原料由于气候天气、形成时间、层次结构等因素,它们是不稳定的,因此必须经过均化。
第3道:原料储备(均化、陈腐)均化,是原料通过机械运动搅拌均匀的一道工序;陈腐,指把混合好的泥料放置一段时间,使泥料之间充分反应,使水分更均匀。
只有经过均化、陈腐处理后的原料,才可以进行生产加工,才能保证批量生产的稳定。
开采均化、进厂均化、加工(泥浆)后均化,三步缺一不可。
第4道:配料技术人员手上掌握了一份配料清单,成熟的配料配方单一般要通过实验室反复多次小试,生产线中试对板,才能进入大生产。
配料员拿到技术人员下达的配料清单后即开始配料,各种原料通过大型铲车加到喂料机里再通过输送带进入球磨机。
第5道:配方确定的原则(1)坯料和釉料的组成应满足产品的物理、化学性质和使用要求;(2)拟定配方时应考虑生产工艺及设备条件;(3)了解各种原料对产品性质的影响;(4)拟定配方时应考虑经济上的合理性以及资源是否丰富、来源是否稳定等。
第6道:放浆入池(除铁)检测合格的浆料进入浆池内备用,浆池入口处设置除铁装置对浆料进行除铁。
第7道:浆料过筛、除铁(1)浆料进入过筛系统,把不符合要求的粗颗粒分离后返回球磨,直到合格为止;(2)浆料经过除铁后把原料中有危害产品质量的铁、钛等杂质基本除掉。
采用高磁性电磁棒吸附铁屑,铁含量低于百分之0.1,确保烧制后的坯体没有黑色杂质,砖体纯净。
第8道:浆料储备(均化陈腐)过筛除铁后的浆料进入浆池储备并均化陈腐。
喷雾造粒:浆料流入喷雾干燥塔进行干燥脱水,此工序的原理是利用柱塞泵的压力将浆料喷入约10米高的空间,喷成雾状,在热风的作用下干燥脱水,浆料变成一个个直径0.5㎜-2㎜不等的粉料颗粒。
第9道:粉料检测(颗粒度、水分)喷雾干燥形成的粉料需检测合格后,才可进入下一道工序。
第10道:粉料检测项目:(1)粉料颗粒级配检测,颗粒级配即粒度分布,是指粉料中各种粒径的颗粒所占的比例;(2)粉料水分的检测,一般瓷砖粉料水分控制在百分之6-7,这种颗粒有非常好的流动性。
第11道:粉料过筛粉料经过过筛,避免不符合粒度要求的颗粒进入下一道工序,以保障产品的质量。
第12道:粉料入料仓储备(均化陈腐)喷雾干燥后的粉料有一定的温度,且水份也不均匀,所以粉料一般需均化陈腐48小时后方可使用。
(1)陈腐时间太短,水份不均匀产品易产生夹层;(2)陈腐时间太长,强度差,流动性差,不易填满压机模腔。
第13道:粉料入压机储料仓粉料由输送带输送进入压机料斗,为压制砖坯做好准备。
第14道:砖坯机压成型压机料斗中的粉料通过布料格栅布料,供压砖机压制成型,压制过程分三步:一:轻压排气;第二步:加压再排气;第三步:将压力加至终。
压制到符合密度要求的坯体,整个过程要非常精细。
首先,填料要均匀;其次,压制时间与速度要非常准确,通过电脑进行控制;然后脱模也是要非常准确,否则容易出现开裂。
不同压机吨位压制不同尺寸的产品,这决定了坯体的厚度、尺寸、密度、硬度等不同参数。
压机的吨位直接决定了瓷砖的密度及硬度。
第15道:砖坯干燥机压成型后的砖坯含有一定的水分,即便是极小的水分,都会影响到砖坯的强度,因此,砖坯随即被送进干燥窑进行干燥。
经过干燥的砖坯,含水率由百分之七降到了百分之零点五左右。
干燥窑的长短,决定着瓷砖的水分干燥程度。
超长320米辊道干燥窑,不仅能让砖坯的水分含量低于百分之零点五,并且烧制不会出现变形。
第16道:砖坯冷却(表面清洁)干燥后的砖坯要经过冷却,并进行表面清洁,方可进入下一道工序。
第17道:砖坯喷水砖坯在上底釉前需要喷水,其作用是:(1)使坯温降低到施釉所需要的温度,打通坯面上的毛细孔;(2)加强坯、釉结合性,减少生产缺陷,如缩釉等。
第18道:淋底釉淋底釉是将釉浆打入位于钟罩淋釉器上方的高位罐,通过釉槽和筛网格的缓冲作用,使釉浆通过光滑的钟罩,均匀的如静静的瀑布一样覆盖在坯体的表面。
施釉量可以通过供釉量和输送带的速度进行调整。
淋釉后的砖坯表面光滑,为下一步高度精细的印花工序打好基础。
第19道:表面装饰表面装饰工序就是通常说的印花工序,全抛釉产品表面颜色和花纹、图案都非常丰富逼真。
就目前来说,印花技术主要有三种:丝网印花、胶辊印花、喷墨打印,不同的印花技术呈现出的产品表面效果大不相同。
(1)丝网印花:丝网印花是将预先配好的印花釉通过丝网的毛细网孔转印到釉坯上,印花丝网上的图案决定了瓷砖的图案。
(2)胶辊印花:胶辊印花是将预先设计好的图案用激光打孔的方式雕刻在圆形的胶辊上,大型的胶辊通过准确的转动和转速,将从下方经过的釉坯一片片地滚压,图案就转印到了釉坯的表面,由于每次砖在胶辊下面通过时的位置略有不同,因此胶辊印花出来的产品图案是有少许的不同的,这样生产出来的产品就更具天然的效果了。
(3)喷墨打印:喷墨打印技术是通过高性能的喷墨印刷机,把电脑预设的图案直接喷印在釉坯表面。
喷墨技术由于是凌空喷印,因此,其花纹图案可以是立体凹凸的,让瓷砖的触感真实,图案栩栩如生。
世界先进的意大利西斯特姆喷墨打印机,生产出来的全抛釉产品图案花色瑰丽自然、色彩丰富。
第20道:施面釉全抛釉产品表面有一层透明的面釉,使全抛釉产品呈现出如水晶般的璀璨炫丽。
第21道:烧成施过面釉的砖坯由输送带送到辊道窑进行烧成,辊道窑的主要燃料可以使用柴油、天然气或发生炉煤气,烧成温度可达1200℃以上。
可以从整个温度的变化把窑炉分成三个带:预热带、烧成带、冷却带,每个带的烧成时间、温度都是通过电脑严格控制的。
经过高温烧成的砖坯发生了质的变化,此时就成了真正意义上的瓷砖。
品牌厂家采用超长宽体节能辊道窑,瓷砖烧制时间比一般厂家要长,确保砖体完全瓷化,像瓷碗一样密实,硬度高、耐磨!第22道:砖坯冷却烧成完成后,从辊道窑出来的瓷砖温度很高,需要经过冷却,才可以进入下一道工序。
第23道:磨边定尺冷却后的瓷砖进入磨边工序,将各边的尺寸标准化。
磨边工序由两组机械完成,每个平行边磨边完成后,瓷砖90°转向,进行另一平行边的作业。
第24道:弹性抛光完成磨边定尺后,瓷砖在输送线上进入粗抛机,将砖面磨削平滑,然后进中抛,从粗抛至中抛,可以抛去砖坯厚度0.1-0.2㎜,从中抛机出来的砖,其光滑程度有点像哑光砖。
精抛机的作用更确切的说像是上光机,砖坯经过精抛机,表面光滑如镜,光泽度可以达到60°左右。
抛光的工作原理是通过不同的目数磨头转动,达到磨削、抛光瓷砖的目的,一般磨头的目数从24目开始至1500目甚至更高。
第25道:超洁亮防污为了提高防污能力,要在瓷砖的表面均匀的涂上一层纳米防污剂,也就是通常所说的超洁亮。
防污剂可以阻止施工过程中水泥浆对瓷砖表面的渗入,另外也会防止日常生活中墨水、茶水等造成的污染。
超洁亮防污还可以提升瓷砖的光泽度(达到90°以上)。
第26道:吹干抛光、超洁亮防污过程中,要用到大量的水对瓷砖进行冲刷,故此工序完成后,砖体附着有很多水分,需要将瓷砖吹干才可进行下一步的处理工序。
第27道:检验分级对吹干后的瓷砖进行检验分级。
质检人员首先对产品变形度、边直度进行检测,再按不同色号将瓷砖分类,根据表面质量情况进行分级。
品牌厂家采用比国家标准严格很多的企业标准,质检人员受过培训,产品分级过程非常的严格和谨慎,对每一片砖都进行严苛的质量检验,保证产品在平整度、尺寸偏差以及色差等指标符合国标的内控指标,确保产品的高品质。
第28道:上蜡、贴膜上蜡前先将瓷砖上所有的污渍彻底清理干净,再用打蜡机将液体蜡均匀涂于砖面上,待瓷砖表面晾干后,再在瓷砖表面贴上一层贴膜。
给瓷砖打蜡能去污上光,增加美观,又可防虫、防潮、防开裂、减少外界对瓷砖的腐蚀和磨损,延长瓷砖使用寿命。
给瓷砖表面贴膜能保护瓷砖不被刮花。
第29道:包装、入库分级过后的产品即可进入自动打包工序,按照不同的产品和尺寸,分设了不同的打包片数,大而重的瓷砖片数少,小而精的瓷砖片数较多,主要是为了库存、运输、购买整箱数的方便。
包装好后的瓷砖即可入库存放,并严格按照产品类别、型号、等级、色号分区存放。
质检人员对入库产品还要进行定期抽检,把好产品出厂前的一道质量关。
上一个:下一个:。