煤炭液化技术
煤的液化技术
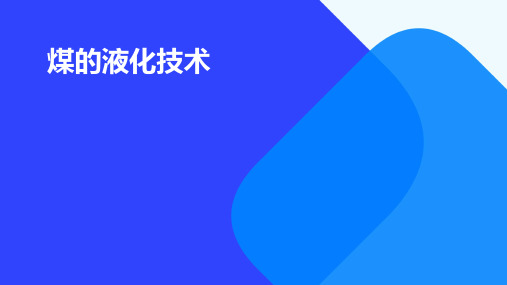
市场发展前景
1 2 3
替代石油资源
随着石油资源的日益枯竭,煤液化技术作为一种 替代石油的能源资源,具有广阔的市场前景。
满足环保要求
煤液化技术能够降低煤炭燃烧过程中的污染物排 放,符合环保要求,有助于推动清洁能源市场的 发展。
对煤液化技术企业给予税收优惠政策,降低企业税负,提高市场 竞争力。
THANKS FOR WATCHING
感谢您的观看
出口潜力
煤液化产品如柴油、汽油等可作为燃料或化工原 料,具有较大的出口潜力,有助于提升我国能源 产业的国际竞争力。
政策支持与推动
产业政策引导
政府通过制定产业政策,鼓励和支持煤液化技术的研发和应用, 推动产业健康发展。
资金扶持
政府提供资金扶持,支持企业进行技术研发和产业化推广,减轻 企业负担。
税收优惠
润滑油
煤液化过程中产生的润滑油具有 优良的润滑性能和稳定性,可用 于机械设备的润滑。
民用燃料
燃气
通过煤液化技术得到的液化石油气可作为居民生活和商业用 途的燃气。
供暖
煤液化燃料可用于集中供暖和家庭采暖,提高居民生活质量 。
化工原料
乙烯
煤液化技术可以生产乙烯等化工原料 ,进一步用于生产塑料、合成纤维等 高分子材料。
该技术最早由南非开发,主要 产品是柴油和航空煤油等。
间接液化技术的优点是工艺流 程相对简单,对原料煤的适应 性较强,但转化效率较低,且 催化剂消耗较大。
合成气液化
合成气液化是指将合成气在一定 条件下转化为液体燃料的过程。
该技术通常采用费托合成工艺, 将合成气在催化剂作用下转化为
煤炭液化技术包括煤炭直接液化和煤炭间接液化

成绩中国矿业大学2011 级本科课程考试试卷考试科目学科前沿讲座考试时间2014年12月学生姓名彭玉斌学生学号06112931所在院系化工学院任课教师周敏教授等多名教师题目:煤炭液化技术煤炭液化技术摘要;煤炭液化技术包括煤炭直接液化和煤炭间接液化,是属于洁净煤技术的一种。
文章简要论述了煤炭直接接液化技术和煤炭间接液化技术的化学反应机理和化学反应过程;回顾了液化技术的发展历史,国外煤液化技术的发展状况;介绍了我国煤碳液化的现状;展望今后煤炭液化的发展方向。
关键字:煤炭;直接液化;间接液化所谓煤炭液化是指,固体煤炭通过化学加工过程,使其转化成为液体燃料、化工原料和产品的先进洁净煤技术。
根据不同的加工路线,煤炭液化可分为直接液化和间接液化两大类。
1煤炭直接液化概述煤与石油都是由碳、氢、氧为主的元素组成的天然有机矿物燃料。
只是煤中氢含量及H/C原子比,较石油相比要低很多。
要将煤转化为液体产物,必须在适当的温度、氢压、溶剂和催化剂的条件下,将煤中的大分子裂解为小分子,进而加氢稳定,降低H/C原子比,从而得到液体产物。
1.1煤直接液化的化学反应一般认为煤直接液化的过程是煤在溶剂、催化剂和高压氢气存在下,随着温度的升高,煤开始在溶剂中膨胀形成胶体体系。
煤进行局部溶解,并发生煤有机质的分裂、解聚,同时在煤有机质与溶剂间进行氢分配,于350~400℃左右生成沥青质含量较高的高分子物质。
在此过程中主要发生煤的热解、自由基加氢稳定、自由基缩合以及氮、氧、硫元素杂元素的脱除等一系列反应。
其主要反应是自由基的生成和加氢稳定。
自由基稳定后可生成分子量小的馏分油,分子量大的沥青烯,及分子量更大前沥青烯。
前沥青烯可进一步分解为分子量较小的沥青烯、馏分油和烃类气体。
同样沥青烯通过加氢可进一步生成馏分油和烃类气体。
如果煤的自由基得不到氢而它的浓度又很大时,这些自由基碎片就会互相结合而生成分子量更大的化合物甚至生成焦炭。
图1表示了煤热解产生自由基以及溶剂向自由基供氢、溶剂和前沥青烯、沥青烯加氢的过程:1.2煤直接液化技术的发展历程煤直接加氢液化一般是在较高温度,高压,氢气(或CO+H2, CO+H2O)、催化剂和溶剂作用下,将煤进行解聚、裂解加氢,直接转化为液体油的加工过程。
煤炭液化技术
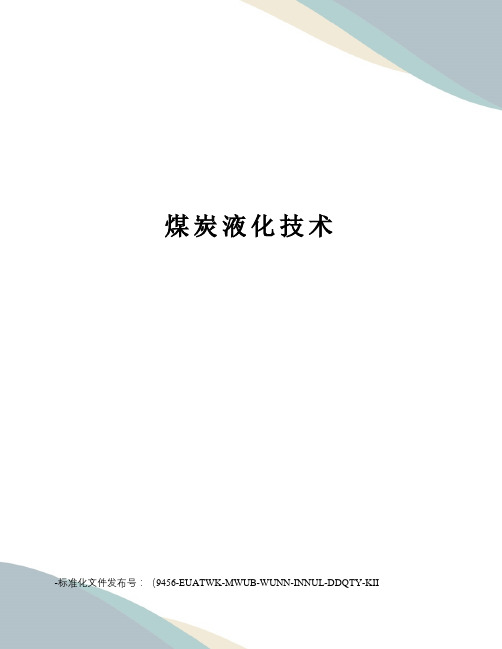
煤炭液化技术-标准化文件发布号:(9456-EUATWK-MWUB-WUNN-INNUL-DDQTY-KII煤炭液化技术[编辑本段]煤炭液化技术煤炭液化是把固体煤炭通过化学加工过程,使其转化成为液体燃料、化工原料和产品的先进洁净煤技术。
根据不同的加工路线,煤炭液化可分为直接液化和间接液化两大类:一、直接液化直接液化是在高温(400℃以上)、高压(10MPa以上),在催化剂和溶剂作用下使煤的分子进行裂解加氢,直接转化成液体燃料,再进一步加工精制成汽油、柴油等燃料油,又称加氢液化。
1、发展历史煤直接液化技术是由德国人于1913年发现的,并于二战期间在德国实现了工业化生产。
德国先后有12套煤炭直接液化装置建成投产,到1944年,德国煤炭直接液化工厂的油品生产能力已达到423万吨/年。
二战后,中东地区大量廉价石油的开发,煤炭直接液化工厂失去竞争力并关闭。
70年代初期,由于世界范围内的石油危机,煤炭液化技术又开始活跃起来。
日本、德国、美国等工业发达国家,在原有基础上相继研究开发出一批煤炭直接液化新工艺,其中的大部分研究工作重点是降低反应条件的苛刻度,从而达到降低煤液化油生产成本的目的。
目前世界上有代表性的直接液化工艺是日本的NEDOL工艺、德国的IGOR工艺和美国的HTI工艺。
这些新直接液化工艺的共同特点是,反应条件与老液化工艺相比大大缓和,压力由40MPa降低至17~30MPa,产油率和油品质量都有较大幅度提高,降低了生产成本。
到目前为止,上述国家均已完成了新工艺技术的处理煤100t/d级以上大型中间试验,具备了建设大规模液化厂的技术能力。
煤炭直接液化作为曾经工业化的生产技术,在技术上是可行的。
目前国外没有工业化生产厂的主要原因是,在发达国家由于原料煤价格、设备造价和人工费用偏高等导致生产成本偏高,难以与石油竞争。
2、工艺原理煤的分子结构很复杂,一些学者提出了煤的复合结构模型,认为煤的有机质可以设想由以下四个部分复合而成。
煤炭液化技术
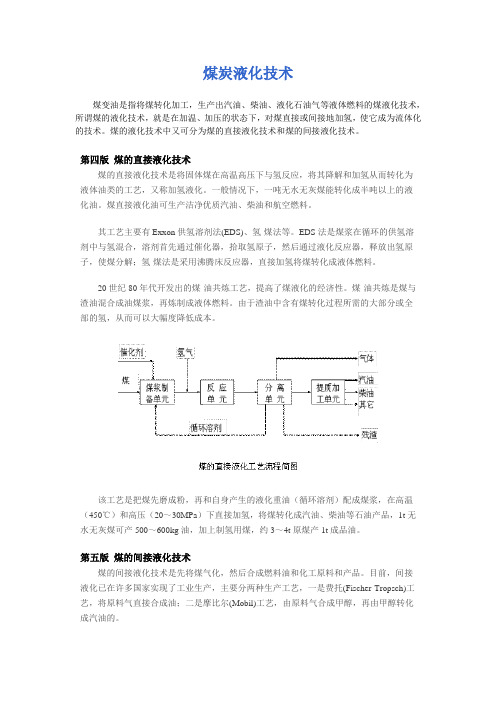
煤炭液化技术煤变油是指将煤转化加工,生产出汽油、柴油、液化石油气等液体燃料的煤液化技术,所谓煤的液化技术,就是在加温、加压的状态下,对煤直接或间接地加氢,使它成为流体化的技术。
煤的液化技术中又可分为煤的直接液化技术和煤的间接液化技术。
第四版煤的直接液化技术煤的直接液化技术是将固体煤在高温高压下与氢反应,将其降解和加氢从而转化为液体油类的工艺,又称加氢液化。
一般情况下,一吨无水无灰煤能转化成半吨以上的液化油。
煤直接液化油可生产洁净优质汽油、柴油和航空燃料。
其工艺主要有Exxon供氢溶剂法(EDS)、氢-煤法等。
EDS法是煤浆在循环的供氢溶剂中与氢混合,溶剂首先通过催化器,拾取氢原子,然后通过液化反应器,释放出氢原子,使煤分解;氢-煤法是采用沸腾床反应器,直接加氢将煤转化成液体燃料。
20世纪80年代开发出的煤-油共炼工艺,提高了煤液化的经济性。
煤-油共炼是煤与渣油混合成油煤浆,再炼制成液体燃料。
由于渣油中含有煤转化过程所需的大部分或全部的氢,从而可以大幅度降低成本。
该工艺是把煤先磨成粉,再和自身产生的液化重油(循环溶剂)配成煤浆,在高温(450℃)和高压(20~30MPa)下直接加氢,将煤转化成汽油、柴油等石油产品,1t无水无灰煤可产500~600kg油,加上制氢用煤,约3~4t原煤产1t成品油。
第五版煤的间接液化技术煤的间接液化技术是先将煤气化,然后合成燃料油和化工原料和产品。
目前,间接液化已在许多国家实现了工业生产,主要分两种生产工艺,一是费托(Fischer-Tropsch)工艺,将原料气直接合成油;二是摩比尔(Mobil)工艺,由原料气合成甲醇,再由甲醇转化成汽油的。
煤间接液化工艺先把煤全部气化成合成气(氢气和一氧化碳),然后再在催化剂存在下合成为汽油。
约5~7t煤产1t油。
间接液化工艺特点:1. 适用煤种比直接液化广泛;2. 可以在现有化肥厂已有气化炉的基础上实现合成汽油;3. 反应压力为3MPa,低于直接液化,反应温度为550℃,高于直接液化;4. 油收率低于直接液化,需5-7t煤出1t油,所以产品油成本比直接液化高出较多。
煤炭液化技术

煤炭液化定义
煤炭液化技术是把固体煤炭通 过化学加工过程,使其转化成 为液体燃料、化工原料和产品 的先进洁净煤技术。
煤炭液化技术简介
煤直接液化技术是由德国人于1913年发现的。德国煤炭直 接液化工厂的油品生产能力已达到423万吨/年。二战后, 中东地区大量廉价石油的开发,煤炭直接液化工厂失去竞 争力并关闭。 70年代初期,由于世界范围内的石油危机,煤炭液化技术 又开始活跃起来。日本、德国、美国等工业发达国家,在 原有基础上相继研究开发出一批煤炭直接液化新工艺。目 前世界上有代表性的直接液化工艺是日本的NEDOL工艺、 德国的IGOR工艺和美国的HTI工艺。
煤炭液化技术分类
1.煤炭直接液化工艺 2.煤炭间接液化工艺
直接液化
直接液化是在高温(400℃以上)、高压 (10MPa以上),在催化剂和溶剂作用下使 煤的分子进行裂解加氢,直接转化成液体 燃料,再进一步加工精制成汽油、柴油等
燃料油,又称加氢液化。源自直接液化流程图间接液化
间接液化技术是先将煤全部气 化成合成气,然后以煤基合成 气(一氧化碳和氢气)为原料, 在一定温度和压力下,将其催 化合成为烃类燃料油及化工原 料和产品的工艺,包括煤炭气 化制取合成气、气体净化与交 换、催化合成烃类产品以及产 品分离和改制加工等过程。
间接液化流程图
煤炭液化是解决中国多煤、少油、缺气能源国情的 重要途径,而煤液化多联产技术是煤液化的发展模 式,是提高能源利用率的重要途径,是发展煤炭循 环经济的重要措施,我们应给予充分的肯定与重视。
煤的直接液化

4、操作条件 温度和压力是影响煤直接液化反应进行的 两个因素,也是直接液化工艺两个最重要 的操作条件。 煤的液化反应是在一定温度下进行的,不 同工艺的所采用的温度大体相同,一般为 440~460º C。当温度超过450º C时,煤转化 率和油产率增加较少,而气产率增多,因 此会增加氢气的消耗量,不利于液化。
2、直接液化的溶剂 在煤液化过程中,溶剂起着溶解煤、溶 解气相氢向煤或催化剂表面扩散、供氢或 传递氢、防止煤热解的自由基碎片缩聚等 作用。 煤的直接液化必须有溶剂存在,这也是 与加氢热解的根本区别。 通常认为在煤的直接液化过程中,溶 剂能起到如下作用:
a)将煤与溶剂制成浆液的形式便于工艺过程 的输送。同时溶剂可以有效地分散煤粒、 催化剂和液化反应生成的热产物,有利于 改善多相催化液化反应体系的动力学过程。 b)依靠溶剂能力使煤颗粒发生溶胀和软化, 使其有机质中的键发生断裂。 c) 溶解部分氢气,作为反应体系中活性氢的 传递介质;或者通过供氢溶剂的脱氢反应 过程,可以提供煤液化需要的活性氢原子。
d)在有催化剂时,促使催化剂分散和萃取出 在催化剂表面上强吸附的毒物。 在煤液化工艺中,通常采用煤直接液化后 的重质油作为溶剂,且循环使用,因此又 称为循环溶剂。
3、催化剂 选用合适的催化剂对煤的直接液化至关重要, 一直是技术开发的热点之一,也是控制工艺成 本的重要因素。 催化剂的作用机理,有两种观点:(1)催化剂 的作用是吸附气体中的氢分子,并将其活化成 为易被煤的自由基团接受的活性氢;(2)催化 剂是使煤中的桥键断裂和芳环加氢的活性提高, 或是使溶剂加氢生成可向煤转移氢的供氢体等。
对压力而言,理论上压力越高对反应越有 利,但这样会增加系统的技术难度和危 险性,降低生产的经济性,因此,新的 生产工艺都在努力降低压力条件。 早期液化反应(如德国工艺)压力 高达 30~70MPa ,目前常用的反应压力 已经降到了 17~25MPa ,大大减少了设 备投资和操作费用。
煤炭直接液化技术总结
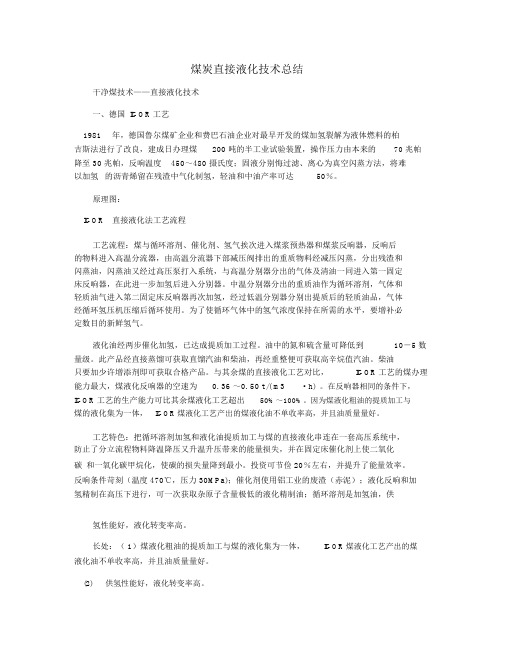
煤炭直接液化技术总结干净煤技术——直接液化技术一、德国 IGOR工艺1981年,德国鲁尔煤矿企业和费巴石油企业对最早开发的煤加氢裂解为液体燃料的柏吉斯法进行了改良,建成日办理煤200 吨的半工业试验装置,操作压力由本来的70 兆帕降至 30 兆帕,反响温度450~480 摄氏度;固液分别悔过滤、离心为真空闪蒸方法,将难以加氢的沥青烯留在残渣中气化制氢,轻油和中油产率可达50%。
原理图:IGOR直接液化法工艺流程工艺流程:煤与循环溶剂、催化剂、氢气挨次进入煤浆预热器和煤浆反响器,反响后的物料进入高温分流器,由高温分流器下部减压阀排出的重质物料经减压闪蒸,分出残渣和闪蒸油,闪蒸油又经过高压泵打入系统,与高温分别器分出的气体及清油一同进入第一固定床反响器,在此进一步加氢后进入分别器。
中温分别器分出的重质油作为循环溶剂,气体和轻质油气进入第二固定床反响器再次加氢,经过低温分别器分别出提质后的轻质油品,气体经循环氢压机压缩后循环使用。
为了使循环气体中的氢气浓度保持在所需的水平,要增补必定数目的新鲜氢气。
液化油经两步催化加氢,已达成提质加工过程。
油中的氮和硫含量可降低到10-5 数量级。
此产品经直接蒸馏可获取直馏汽油和柴油,再经重整便可获取高辛烷值汽油。
柴油只要加少许增添剂即可获取合格产品。
与其余煤的直接液化工艺对比,IGOR工艺的煤办理能力最大,煤液化反响器的空速为0. 36 ~0. 50 t /( m3·h)。
在反响器相同的条件下,IGOR工艺的生产能力可比其余煤液化工艺超出50%~100%。
因为煤液化粗油的提质加工与煤的液化集为一体,IGOR煤液化工艺产出的煤液化油不单收率高,并且油质量量好。
工艺特色:把循环溶剂加氢和液化油提质加工与煤的直接液化串连在一套高压系统中,防止了分立流程物料降温降压又升温升压带来的能量损失,并在固定床催化剂上使二氧化碳和一氧化碳甲烷化,使碳的损失量降到最小。
投资可节俭 20%左右,并提升了能量效率。
煤炭液化技术复习资料

第三章1.什么是煤炭直接液化?定义:煤经化学加工转化成洁净的便于运输和使用的液体燃料、化学品或化工原料的一种先进的洁净煤技术.煤在氢气和催化剂作用下,通过加氢裂化转变为液体燃料的过程称为直接液化。
2.煤炭直接液化的途径是什么?如何实施?途径:煤先经加氢裂解等过程转化为液化油,再提质加工得到成品油.具体实施:先热解反应产生自由基碎片再由自由基碎片加氢得到的油再经脱杂(S,N,O等杂原子),缩合反应得到成品油。
3.煤炭直接液化反应有哪些?主要反应是什么?煤的热解反应自由基碎片的加氢反应脱杂原子反应缩合反应4.什么是自由基碎片?在直接液化过程中,煤的大分子结构首先受热分解,而使煤分解成以结构单元缩合芳烃为单个分子的独立的自由基碎片5.自由基碎片加氢反应中氢的来源是什么?哪些是主要来源?供给自由基的氢源主要有:(1)外界供给的氢在催化剂作用下变为活性氢;(2)溶剂可供给的或传递的氢;(3)煤本身可供应的氢(煤分子内部重排、部分结构裂解或缩聚形成的氢);(4)化学反应生成的氢,如CO和H2O反应生成的氢等.6.煤直接液化研究中油,沥青烯,前沥青烯,残渣是如何定义的?(1)油:可溶于正己烷的物质(2)沥青烯:不溶于正己烷而溶于苯(3)前沥青烯:不溶于苯而溶于四氢呋喃或吡啶(4)残渣:不溶于四氢呋喃或吡啶的物质7.描述煤炭直接液化反应的历程?首先,煤在溶剂中膨胀形成胶体系统,有机质进行局部溶解,发生煤的解体破坏,350~400℃左右发生分解、加氢、解聚、聚合以及脱杂原子等一系列反应,生成沥青质含量很多的高分子物质。
当温度达到450~480℃时,溶剂中氢的饱合程度增加,使氢重新分配程度也相应增加,从而使煤加氢液化过程逐步加深,使高分子物质(沥青质)转变为低分子产物-油和气。
这个过程中也是存在分解、加氢、解聚、聚合以及脱杂原子等一系列反应1)先裂解后加氢。
2)反应以顺序进行为主。
虽然在反应初期有少量气体和轻质油生成,不过数量不多。
煤直接液化工艺流程

煤直接液化工艺流程
《煤直接液化工艺流程》
煤直接液化是一种将煤直接转化成液体燃料的技术,被广泛应用于煤炭资源的高效利用和清洁能源的生产。
其工艺流程是一个复杂的化工过程,需要多种设备和技术的配合,下面将对其工艺流程进行说明。
首先,煤炭的预处理是整个工艺流程的第一步。
煤炭首先经过破碎、磨矿和筛分等步骤,使得煤炭颗粒的大小和形状更适合后续的反应和转化过程。
然后,煤质的选煤是非常关键的一步,通过密度分离、气浮和湿选等技术,将煤中的灰分和硫分等杂质进行分离,提高煤质的纯度。
接下来是煤的干馏。
将经过预处理的煤炭送入干馏炉中,利用高温和缺氧环境进行反应,将煤转化成气体和液体产物。
在此过程中,煤中的碳、氢、氧、氮等元素都将发生化学变化,产生气化气体和焦油等产品。
然后,气化气体进一步处理。
气化气体中含有一定量的一氧化碳和氢气,在进一步利用前,需要经过净化和变换等步骤,去除其中的杂质并转化成合成气,以便后续的加氢和合成反应。
最后是合成。
通过控制合成气的压力和温度,利用催化剂将合成气经过合成反应,生成液体燃料和化工产品。
整个煤直接液化工艺流程中,合成反应是决定产物品质的关键步骤。
总的来说,煤直接液化是一个复杂而又高效的技术,通过一系列工艺流程将煤炭转化成清洁高效的液体燃料。
随着技术的不断进步和设备的不断完善,相信煤直接液化技术将会在未来发挥更加重要的作用。
煤制油

煤制油煤制油包括直接液化和间接液化两种工艺技术路线。
1.煤炭直接液化技术煤在高压和一定温度下直接与氢气反应生成液体燃料油的工艺技术称为直接液化。
煤炭直接液化主要产品为汽油、柴油、航空煤油、石脑油、LPG(液化石油气),另外还可以提取BTX(苯、甲苯、二甲苯),副产品有硫磺、氨或尿素等。
直接液化工艺的产品中,柴油的比例在60~70%,汽油和LPG占40~30%左右。
直接液化的工艺主要有Exxon供氢溶剂法(EDS)。
氢-煤法等。
EDS法是煤浆在循环的供氢溶剂中与氢混合,溶剂首先通过催化器,拾取氢原子,然后通过液化反应器,释放出氢原子,使煤分解。
氢-煤法是采用沸腾床反应器,直接加氢将煤转化成液体燃料。
直接液化过程流程现代煤炭直接液化技术提高了产品质量,特别是通过液化后的提质加工工艺,使液化油通过加氢精制、重整、加氢裂化,可得到合格的汽油、柴油或航空煤油。
尤其是柴油的凝点很低,可以在高寒地区使用,所得航空煤油的比重较大,同样容积的油箱可使飞机的续航距离增加。
2. 煤炭间接液化技术间接液化是把煤炭先气化再合成,煤在高温下与氧气和水蒸气反应生成合成反应气(CO+H2),合成反应气再经F-T合成催化反应合成液体燃料及其化学品。
煤炭间接液化主要产品为汽油、柴油、航空煤油、石脑油、LPG、以及乙烯、丙稀等重要化工原料,副产品有α烯烃、硬蜡、氨、醇、酮、焦油、硫磺、煤气等。
间接液化的产品品种是可以变通的,即可以生产油品,又可以根据市场需要加以调节,生产高附加值、价格高、市场紧缺的化工产品。
对中国的石油产品市场而言,以优质石脑油和高质量柴油、烯烃、LPG 和石蜡等产品为好。
另外烯烃的价值较高,LPG也是市场紧俏物资。
此外我国石蜡生产和销售市场上,高熔点微晶蜡缺口较大,高品位润滑油也是国内比较紧缺的。
因此,汽油、柴油与高附加值的润滑油、微晶蜡等市场紧缺的产品并举,可以作为合成油产品的主攻方向。
间接液化在可控制的条件下进行合成,获得的柴油的十六烷值达70,且低硫、无芳烃,既可直接供给环保要求高的地区使用,也可作为优质油与其它油品调配。
【知识】煤炭液化工艺

煤制油关键技术:煤炭液化2014-03-01化化网煤化工煤炭液化是把固态状态的煤炭通过化学加工,使其转化为液体产品(液态烃类燃料,如汽油、柴油等产品或化工原料)的技术。
煤炭通过液化可将硫等有害元素以及灰分脱除,得到洁净的二次能源,对优化终端能源结构、解决石油短缺、减少环境污染具有重要的战略意义。
煤炭液化是将煤经化学加工转化成洁净的便于运输和使用的液体燃料、化学品或化工原料的一种先进的洁净煤技术。
煤炭液化方法包括直接液化和间接液化。
煤直接液化煤在氢气和催化剂作用下,通过加氢裂化转变为液体燃料的过程称为直接液化。
裂化是一种使烃类分子分裂为几个较小分子的反应过程。
因煤直接液化过程主要采用加氢手段,故又称煤的加氢液化法。
比较著名的直接液化工艺有:溶剂精炼法(SRC-1、SRC-2),供氢溶剂法(EDS)、氢煤法(H-Coal )、前苏联可燃物研究所法(NTN)、德国液化新工艺、日澳褐煤液化、煤与渣油联合加工法、英国的溶剂萃取法和日本的溶剂分离法等,它们在工艺和技术上都取得了不同程度的突破。
直接液化是目前可采用的最有效的液化方法。
在合适的条件下,液化油收率超过70%(干燥无矿物质煤)。
如果允许热量损失和其它非煤能量输入的话,现代液化工艺总热效率(即转化成最终产品的输入原料的热值比例,%)一般为60-70%。
煤间接液化间接液化是以煤为原料,先气化制成合成气,然后,通过催化剂作用将合成气转化成烃类燃料、醇类燃料和化学品的过程。
煤炭间接液化技术主要有:南非Sasol公司的F-T合成技术、荷兰Shell 公司的SMDS技术、Mobil公司的MTG合成技术等。
还有一些先进的合成技术,如丹麦TopsФe公司的Tigas法和美国Mobil公司的STG法等。
煤炭液化的可行性主要决定于液化工艺的经济性。
这需要大量的品位低、价格低的煤炭,且石油和天然气缺乏或成本较高。
也就是说,未来石油价格的上涨将引起人们重新对煤炭液化技术的极大兴趣,并可能导致大规模的商业化煤炭液化生产。
煤间接液化与直接液化技术的比较及缺点

煤间接液化与直接液化技术的比较及缺点一.煤间接液化介绍煤的间接液化技术是先将煤全部气化成合成气,然后以合成气为原料,在一定温度、压力和催化剂存在下,通过F-T合成为烃类燃料油及化工原料和产品的工艺。
包括煤气化制取合成气、催化合成烃类产品以及产品分离和改制加工等过程。
煤炭间接液化技术主要有南非的萨索尔(Sasol)费托合成法、美国的Mobil(甲醇制汽油法)和荷兰SHELL的中质馏分合成(SMDS)间接液化工艺。
F-T合成的特点是:合成条件较温和,无论是固定床、流化床还是浆态床,反应温度均低于350℃,反应压力2.0-3.0MPa;转化率高,如SASOL 公司SAS工艺采用熔铁催化剂,合成气的一次通过转化率达到60%以上,循环比为2.0时,总转化率即达90%左右。
二.煤直接液化介绍煤的直接液化是煤在适当的温度和压力下,催化加氢裂化生成液体烃类及少量气体烃,脱除煤中氮、氧和硫等杂原子的转化过程。
煤化工监理目前国内外的主要工艺有:1.美国HTI工艺该工艺是在两段催化液化法和H-COAL工艺基础上发展起来的,采用近十年来开发的悬浮床反应器和HTI拥有专利的铁基催化剂(GelCatTM)。
反应温度420~450℃,反应压力17MPa;采用特殊的液体循环沸腾床反应器,达到全返混反应器模式;催化剂是采用HTI专利技术制备的铁系胶状高活性催化剂。
在高温分离器后面串联一台加氢固定床反应器,对液化油进行在线加氢精制。
2.日本NEDOL工艺该工艺由煤前处理单元、液化反应单元、液化油蒸馏单元及溶剂加氢单元等4个主要单元组成。
反应压力17M~19MPa,反应温度为430~465℃;催化剂采用合成硫化铁或天然硫铁矿。
离线加氢方式3.德国煤液化新工艺(IGOR工艺)1981年,德国鲁尔煤矿公司和费巴石油公司对最早开发的煤加氢裂解为液体燃料的柏吉斯法进行了改进,建成日处理煤200吨的半工业试验装置,操作压力由原来的70MPa降至30MPa,反应温度450~480℃,固液分离改过滤、离心为真空闪蒸方法,将难以加氢的沥青烯留在残渣中气化制氢,轻油和中油产率可达50%。
煤的液化原理及应用现状

煤的液化原理及应用现状1. 煤的液化原理煤的液化是指将固体煤炭转化为液体燃料的过程。
液化煤技术是利用化学反应将煤炭转化为可以燃烧的液体燃料,以满足能源需求。
下面是煤的液化原理的一些关键点:•加热:将煤炭加热到高温。
高温有助于打破煤炭的化学键,使其分解为较小的分子。
•催化剂:使用催化剂促进液化反应。
催化剂能够降低反应的活化能,提高反应速率。
•溶剂:使用合适的溶剂来使煤炭与催化剂接触,并促进反应的进行。
•氢气:向反应体系中加入氢气,可以提高液化反应的效率并降低产物中的杂质含量。
2. 煤的液化应用现状煤的液化技术已经在工业生产中得到广泛应用。
下面是煤的液化应用现状的一些主要方面:2.1 燃料煤的液化产物可以用作燃料,用于替代传统的石油燃料。
液化煤燃料的热值高,可以用于发电、汽车燃料等领域。
液化煤燃料还可以降低燃烧产生的污染物排放。
2.2 化工原料煤的液化产物可以用作化工原料,在合成某些化学产品时起到重要作用。
例如,液化煤产物可以用于合成合成氨、甲醇等化学品。
2.3 煤基化学品煤的液化技术还可以用于生产煤基化学品。
通过煤的液化过程,可以获得具有高附加值的煤基化学品,例如煤油、煤焦油等。
2.4 国内外应用现状在中国,煤的液化技术已经得到了广泛的应用。
中国是全球煤炭资源最丰富的国家之一,因此煤的液化技术在中国具有重要意义。
国外一些发达国家也在开展煤的液化研究,并将其应用于能源转化和化工领域。
3. 结论煤的液化技术可以将固体煤炭转化为液体燃料或化工原料,具有广泛的应用前景。
煤的液化在燃料和化工行业发挥着重要作用,能够提高能源的利用效率,减少环境污染。
随着煤炭资源的减少和环境保护意识的增强,煤的液化技术将会得到更广泛的应用和研究。
煤炭加工中的煤炭液化技术及应用

政策支持与推动煤炭液化技术发展的建议
柴油等。
煤炭液化与生物 质能技术的结合: 利用煤炭液化技 术生产生物质能 产品,如生物柴 油、生物乙醇等。
煤炭液化与氢能 技术的结合:利 用煤炭液化技术 生产氢能产品, 如氢气、氢燃料
电池等。
煤炭液化与碳捕 获与封存技术的 结合:利用煤炭 液化技术生产低 碳产品,如二氧 化碳、甲烷等。
添加标题
添加标题
航空燃料:煤炭液化技术可以生产出高热值、低挥发性的航空燃料,提高飞行安全性。
船舶燃料:煤炭液化技术可以生产出低硫、低灰分的船舶燃料,降低船舶排放对环境的影响。
工业燃料:煤炭液化技术可以生产出高热值、低挥发性的工业燃料,提高工业生产效率。
间接液化燃料的应用
燃料电池:将煤炭液化燃 料转化为电能,用于电动 汽车、便携式电子设备等
领域。
航空燃料:将煤炭液化燃 料转化为航空燃料,用于 飞机燃料,降低对石油的
依赖。
化工原料:将煤炭液化 燃料转化为化工原料, 用于生产塑料、橡胶、
纤维等化工产品。
供热燃料:将煤炭液化燃 料转化为供热燃料,用于 家庭、商业和工业供热,
减少对天然气的依赖。
煤炭液化与其他技术的结合应用
煤炭液化与石油 化工技术的结合: 利用煤炭液化技 术生产石油化工 产品,如汽油、
法。
生物质液化法:通过生物质 气化、合成气净化、合成油 等步骤将生物质转化为液体 燃 料 , 如 瑞 典 Va t t e n f a l l
《煤的液化技术》课件

01
合成气液化工艺是指将合成 气冷却到低温条件下,通过 物理方法将其液化成液体燃
料的过程。
02
该工艺需要使用高效制冷系 统和精密的分离技术,以确 保合成的液体燃料纯度和品
质。
03
合成气液化工艺的产物为高 品质的液体燃料,如航空煤 油等,具有较高的经济价值
和环保性能。
04
煤液化技术的发展趋势与 挑战
03
煤的液化工艺类型
直接液化工艺
直接液化工艺是指将煤在氢气和催化剂的作用下,通过加氢裂化转变为液体燃料的 过程。
该工艺需要高温、高压的反应条件,同时对原料煤的品质要求较高,通常使用褐煤 、长焰煤等年轻煤种。
直接液化工艺的产物为液体燃料,如柴油、汽油等,具有较高的能源密度和环保性 能。
间接液化工艺
国际煤的液化技术应用案例
该案例展示了国际上煤液化技术的先进性和成熟度。 案例二:ExxonMobil煤液化技术
ExxonMobil公司是全球最大的石油和天然气生产商之一,同时也拥有先进的煤液化技术。
国际煤的液化技术应用案例
01
02
代表性项目为美国煤炭巨头皮博迪公司的煤液化项目,采用 ExxonMobil直接液化技术,年产油品数十万吨。
间接液化工艺是指先将煤转化为 合成气,再通过催化剂作用将合
成气转化为是将煤气化生成合成气,第二 步是将合成气催化转化为液体燃
料。
间接液化工艺的产物同样为液体 燃料,但可以通过调整合成气转 化催化剂的种类和反应条件,生
产不同种类的液体燃料。
合成气液化工艺
煤资源有限,且分布不均,需要 寻求其他可替代的能源资源。
高能耗与高碳排放
煤液化过程中能耗高,碳排放量大 ,需要采取措施降低能耗和碳排放 。
- 1、下载文档前请自行甄别文档内容的完整性,平台不提供额外的编辑、内容补充、找答案等附加服务。
- 2、"仅部分预览"的文档,不可在线预览部分如存在完整性等问题,可反馈申请退款(可完整预览的文档不适用该条件!)。
- 3、如文档侵犯您的权益,请联系客服反馈,我们会尽快为您处理(人工客服工作时间:9:00-18:30)。
煤炭液化技术[编辑本段] 煤炭液化技术煤炭液化是把固体煤炭通过化学加工过程产品的先进洁净煤技术。
根据不同的加工,使其转化成为液体燃料路线,煤炭液化可分为直接、化工原料和液化和间接液化两大类:一、直接液化直接液化是在高温(400℃以上)、高压(10MPa以上),在催化剂和溶剂作用下使煤的分子进行裂解加氢,直接转化成液体燃料,再进一步加工精制成汽油、柴油等燃料油,又称加氢液化。
1、发展历史煤直接液化技术是由德国人于1913 年发现的,并于二战期间在德国实现了工业化生产。
德国先后有12套煤炭直接液化装置建成投产,到1944年,德国煤炭直接液化工厂的油品生产能力已达到423万吨/年。
二战后,中东地区大量廉价石油的开发,煤炭直接液化工厂失去竞争力并关闭。
70年代初期,由于世界范围内的石油危机,煤炭液化技术又开始活跃起来。
日本、德国、美国等工业发达国家,在原有基础上相继研究开发出一批煤炭直接液化新工艺,其中的大部分研究工作重点是降低反应条件的苛刻度,从而达到降低煤液化油生产成本的目的。
目前世界上有代表性的直接液化工艺是日本的NEDOL 工艺、德国的IGOR工艺和美国的HTI工艺。
这些新直接液化工艺的共同特点是,反应条件与老液化工艺相比大大缓和,压力由40MPa降低至17~30MPa,产油率和油品质量都有较大幅度提高,降低了生产成本。
到目前为止,上述国家均已完成了新工艺技术的处理煤100t/d 级以上大型中间试验,具备了建设大规模液化厂的技术能力。
煤炭直接液化作为曾经工业化的生产技术,在技术上是可行的。
目前国外没有工业化生产厂的主要原因是,在发达国家由于原料煤价格、设备造价和人工费用偏高等导致生产成本偏高,难以与石油竞争。
2、工艺原理煤的分子结构很复杂,一些学者提出了煤的复合结构模型,认为煤的有机质可以设想由以下四个部分复合而成。
第一部分,是以化学共价键结合为主的三维交联的大分子,形成不溶性的刚性网络结构,它的主要前身物来自维管植物中以芳族结构为基础的木质素。
第二部分,包括相对分子质量一千至数千,相当于沥青质和前沥青质的大型和中型分子,这些分子中包含较多的极性官能团,它们以各种物理力为主,或相互缔合,或与第一部分大分子中的极性基团相缔合,成为三维网络结构的一部分。
第三部分,包括相对分子质量数百至一千左右,相对于非烃部分,具有较强极性的中小型分子,它们可以分子的形式处于大分子网络结构的空隙之中,也可以物理力与第一和第二部分相互缔合而存在。
第四部分,主要为相对分子质量小于数百的非极性分子,包括各种饱和烃和芳烃,它们多呈游离态而被包络、吸附或固溶于由以上三部分构成的网络之中。
煤复合结构中上述四个部分的相对含量视煤的类型、煤化程度、显微组成的不同而异。
上述复杂的煤化学结构,是具有不规则构造的空间聚合体,可以认为它的基本结构单元是以缩合芳环为主体的带有侧链和多种官能团的大分子,结构单元之间通过桥键相连,作为煤的结构单元的缩合芳环的环数有多有少,有的芳环上还有氧、氮、硫等杂原子,结构单元之间的桥键也有不同形态,有碳碳键、碳氧键、碳硫键、氧氧键等。
从煤的元素组成看,煤和石油的差异主要是氢碳原子比不同。
煤的氢碳原子比为0.2~1,而石油的氢碳原子比为 1.6~2,煤中氢元素比石油少得多。
煤在一定温度、压力下的加氢液化过程基本分为三大步骤。
(1)、当温度升至300℃以上时,煤受热分解,即煤的大分子结构中较弱的桥键开始断裂,打碎了煤的分子结构,从而产生大量的以结构单元为基体的自由基碎片,自由基的相对分子质量在数百范围。
(2)、在具有供氢能力的溶剂环境和较高氢气压力的条件下、自由基被嘉庆得到稳定,成为沥青烯及液化油分子。
能与自由基结合的氢并非是分子氢(H2),而应是氢自由基,即氢原子,或者是活化氢分子,氢原子或活化氢分子的来源有:①煤分子中碳氢键断裂产生的氢自由基;②供氢溶剂碳氢键断裂产生的氢自由基;③氢气中的氢分子被催化剂活化;④化学反应放出的氢。
当外界提供的活性氢不足时,自由基碎片可发生缩聚反应和高温下的脱氢反应,最后生成固体半焦或焦炭。
(3)、沥青烯及液化油分子被继续加氢裂化生成更小的分子。
3、工艺过程直接液化典型的工艺过程主要包括煤的破碎与干燥、煤浆制备、加氢液化、固液分离、气体净化、液体产品分馏和精制,以及液化残渣气化制取氢气等部分。
氢气制备是加氢液化的重要环节,大规模制氢通常采用煤气化及天然气转化。
液化过程中,将煤、催化剂和循环油制成的煤浆,与制得的氢气混合送入反应器。
在液化反应器内,煤首先发生热解反应,生成自由基“碎片”,不稳定的自由基“碎片”再与氢在催化剂存在条件下结合,形成分子量比煤低得多的初级加氢产物。
出反应器的产物构成十分复杂,包括气、液、固三相。
气相的主要成分是氢气,分离后循环返回反应器重新参加反应;固相为未反应的煤、矿物质及催化剂;液相则为轻油(粗汽油)、中油等馏份油及重油。
液相馏份油经提质加工(如加氢精制、加氢裂化和重整)得到合格的汽油、柴油和航空煤油等产品。
重质的液固淤浆经进一步分离得到重油和残渣,重油作为循环溶剂配煤浆用。
煤直接液化粗油中石脑油馏分约占15%-30%,且芳烃含量较高,加氢后的石脑油馏分经过较缓和的重整即可得到高辛烷值汽油和丰富的芳烃原料,汽油产品的辛烷值、芳烃含量等主要指标均符合相关标准(GB17930-1999),且硫含量大大低于标准值(≤0.08%),是合格的优质洁净燃料。
中油约占全部直接液化油的50%-60%,芳烃含量高达70%以上,经深度加氢后可获得合格柴油。
重油馏分一般占液化粗油的10%-20%,有的工艺该馏分很少,由于杂原子、沥青烯含量较高,加工较困难,可以作为燃料油使用。
煤液化中油和重油混合经加氢裂化可以制取汽油,并在加氢裂化前进行深度加氢以除去其中的杂原子及金属盐。
4、工艺特点(1)液化油收率高。
例如采用HTI工艺,神华煤的油收率可高达63%-68%;(2)煤消耗量小,一般情况下,1吨无水无灰煤能转化成半吨以上的液化油,加上制氢用煤,约3-4吨原料产1吨液化油。
(3)馏份油以汽、柴油为主,目标产品的选择性相对较高;(4)油煤浆进料,设备体积小,投资低,运行费用低;(5)反应条件相对较苛刻,如德国老工艺液化压力甚至高达70MPa,现代工艺如IGOR 、HTI、NEDOL 等液化压力也达到17-30MPa,液化温度430-470℃;(6)出液化反应器的产物组成较复杂,液、固两相混合物由于粘度较高,分离相对困难;(7)氢耗量大,一般在6%-10%,工艺过程中不仅要补充大量新氢,还需要循环油作供氢溶剂,使装置的生产能力降低。
5、国内技术发展我国从70年代末开始煤炭直接液化技术研究。
煤炭科学研究总院北京煤化所对近30个煤种在0.1 吨/日装置上进行了50 多次运转试验,开发了高活性的煤液化催化剂,进行了煤液化油的提质加工研究,完成了将煤的液化粗油加工成合格的汽油、柴油和航空煤油的试验。
“九五”期间分别同德国、日本、美国有关部门和公司合作完成了神华、黑龙江依兰、云南先锋建设煤直接液化厂的预可行性研究。
在开发形成“神华煤直接液化新工艺”的基础上,我公司建成了投煤量6t/d的工艺试验装置,于2004 年10月开始进行溶剂加氢、热油连续运转,并于2004 年12 月16日投煤,进行了23小时投料试运转,打通了液化工艺,取得开发成果。
经过近一年的时间进行装置的改造,装置于2005年10月29日开始第二次投煤试验,经过近18天(412小时)的连续平稳运转,完成了预定的试验计划,于11 月15日顺利停车,试验取得了成功。
经统计,试验期间共配制煤浆206 吨,共消耗原煤105吨(其中干燥无灰基煤85 吨);共制备863 催化剂油浆44吨。
我公司位于鄂尔多斯的使用神华自己技术的直接液化项目的先期工程于2004 年8月25日正式开工建设。
二、间接液化煤的间接液化技术是先将煤全部气化成合成气,然后以煤基合成气(一氧化碳和氢气)为原料,在一定温度和压力下,将其催化合成为烃类燃料油及化工原料和产品的工艺,包括煤炭气化制取合成气、气体净化与交换、催化合成烃类产品以及产品分离和改制加工等过程。
1、发展历史1923年,德国化学家首先开发出了煤炭间接液化技术。
40 年代初,为了满足战争的需要,德国曾建成9个间接液化厂。
二战以后,同样由于廉价石油和天然气的开发,上述工厂相继关闭和改作它用。
之后,随着铁系化合物类催化剂的研制成功、新型反应器的开发和应用,煤间接液化技术不断进步,但由于煤炭间接液化工艺复杂,初期投资大,成本高,因此除南非之外,其它国家对煤炭间接液化的兴趣相对于直接液化来说逐渐淡弱。
煤炭间接液化技术主要有三种,即的南非的萨索尔(Sasol)费托合成法、美国的Mobil甲醇制汽油法)和正在开发的直接合成法。
目前,煤间接液化技术在国外已实现商业化生产,全世界共有3家商业生产厂正在运行,它们分别是南非的萨索尔公司和新西兰、马来西亚的煤炭间接液化厂。
新西兰煤炭间接液化厂采用的是Mobil液化工艺,但只进行间接液化的第一步反应,即利用天然气或煤气化合成气生产甲醇,而没有进一步以甲醇为原料生产燃料油和其它化工产品,生产能力 1.25 万桶/天。
马来西亚煤炭间接液化厂所采用的液化工艺和南非萨索尔公司相似,但不同的是它以天然气为原料来生产优质柴油和煤油,生产能力为50万吨/年。
因此,从严格意义上说,南非萨索尔公司是世界上唯一的煤炭间接液化商业化生产企业南非萨索尔公司成立于50年代初,1955年公司建成第一座由煤生产燃料油的S asol-1厂。
70 年代石油危机后,1980年和1982年又相继建成Sasol-2 厂和Sasol- 3厂。
3个煤炭间接液化厂年加工原煤约4600 万t,产品总量达768万t,主要生产汽油、柴油、蜡、氨、乙烯、丙烯、聚合物、醇、醛等113种产品,其中油品占60%,化工产品占40%。
该公司生产的汽油和柴油可满足南非28%的需求量,其煤炭间接液化技术处于世界领先地位。
此外,美国SGI公司于80年代末开发出了一种新的煤炭液化技术,即LFC(煤提油)技术。
该技术是利用低温干馏技术,从次烟煤或褐煤等非炼焦煤中提取固态的高品质洁净煤和液态可燃油。
美国SGI公司于1992 年建成了一座日处理能力为1000t的次烟煤商业示范厂。
2、工艺原理费托合成(Fisher-Tropsch Sythesis)合成是指CO在固体催化剂作用下非骏相氢化生成不同链长的烃类(C1~C25)和含氧化合物的反应。
该反应于1923年由F. Fischer和H.Tropsch首次发现后经Fischer等人完善,并于1936 年在鲁尔化学公司实现工业化,费托(F-T)合成因此而得名。